粉末注射成型技术的特点
粉末注塑和粉末冶金工艺介绍
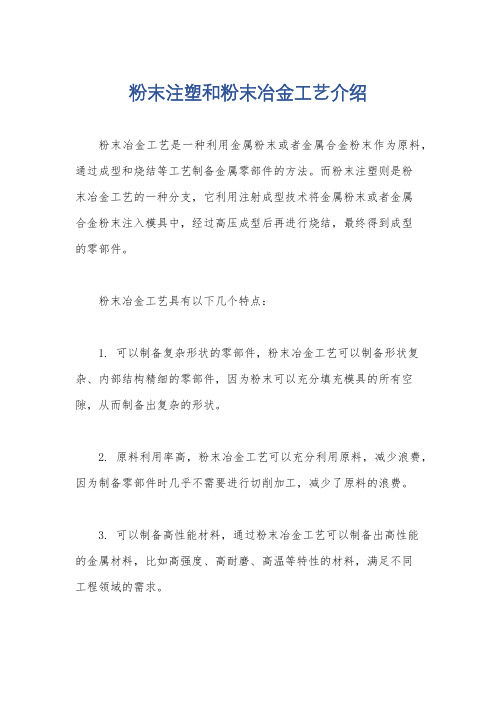
粉末注塑和粉末冶金工艺介绍
粉末冶金工艺是一种利用金属粉末或者金属合金粉末作为原料,通过成型和烧结等工艺制备金属零部件的方法。
而粉末注塑则是粉
末冶金工艺的一种分支,它利用注射成型技术将金属粉末或者金属
合金粉末注入模具中,经过高压成型后再进行烧结,最终得到成型
的零部件。
粉末冶金工艺具有以下几个特点:
1. 可以制备复杂形状的零部件,粉末冶金工艺可以制备形状复杂、内部结构精细的零部件,因为粉末可以充分填充模具的所有空隙,从而制备出复杂的形状。
2. 原料利用率高,粉末冶金工艺可以充分利用原料,减少浪费,因为制备零部件时几乎不需要进行切削加工,减少了原料的浪费。
3. 可以制备高性能材料,通过粉末冶金工艺可以制备出高性能
的金属材料,比如高强度、高耐磨、高温等特性的材料,满足不同
工程领域的需求。
粉末注塑作为粉末冶金工艺的一种应用,具有以下特点:
1. 成本低,相比传统的金属加工工艺,粉末注塑可以减少原材
料浪费和加工成本,从而降低零部件的制造成本。
2. 生产效率高,粉末注塑可以批量生产零部件,提高生产效率,适用于大规模生产。
3. 可以制备复杂形状的零部件,粉末注塑技术可以制备出复杂
形状的零部件,满足不同工程领域对零部件形状的需求。
总的来说,粉末冶金工艺和粉末注塑技术在制备金属零部件方
面具有独特的优势,可以满足不同领域对于零部件性能和形状的需求,有着广泛的应用前景。
211172531_金属粉末注射成形技术发展探究

金属粉末注射成形技术发展探究顾海峰摘要:金属粉末注射成形(Metal powder injection molding,MIM)技术,是一种新型的近净成形技术,主要用来生产形状小、结构复杂的零部件。
文章针对MIM技术的发展应用进行探究,综述了MIM工艺流程和技术特点、气雾化粉末与水雾化粉末的对比、MIM技术的应用现状、MIM工艺中的常见问题及解决对策,以期促进MIM技术进一步发展。
关键词:MIM技术;工艺流程;应用现状;问题;解决对策MIM技术起源于20世纪70年代,由美国学者首次开发成功。
到了80年代,关于MIM技术的理论和应用研究活动广泛开展,这一时期脱脂工艺用时明显缩短,产品尺寸精度得以提高。
进入21世纪,随着新材料、新工艺的出现,MIM向着产业化发展,解决了难熔金属基复合材料的加工问题。
在金属材料加工领域,人类追求金属零件一体成形的梦想从未停止,MIM技术是当今金属零件制造的顶尖技术,被誉为“金属加工技术的未来”。
以下结合现有研究成果,对MIM技术的发展与应用进行探讨。
1 MIM工艺流程和技术特点1.1 MIM工艺流程MIM工艺流程为:金属粉末+粘结剂→混炼制粒→注射成形→脱脂→烧结→后处理→成品。
主要材料和关键工艺介绍如下。
1.1.1 金属粉末理论上,满足粉末冶金要求的金属,均能用在MIM工艺中。
目前常用的金属粉末有:①低合金钢,如Fe-2Ni、Fe-8Ni;②不锈钢,如304L、440C、17-4PH;③硬质合金,如WC-6Co;④重合金,如W-Ni-Fe、W-Cu;⑤钛合金,如TiAl、Ti-6Al-4V、TiMo;⑥新型合金,如Fe-Al-Si、无Ni奥氏体不锈钢。
制备金属粉末,主要方法有雾化法、羰基法、电解法、还原法、研磨法等。
实践证实,粉末粒度大小、粉末之间的摩擦力,均会影响混料的均匀度。
粉末粒度越小、摩擦力越小,混料均匀度越高,有助于提高工艺质量。
1.1.2 粘结剂MIM工艺中,对粘结剂的要求为:粘度与熔点低,固化性、流动性、湿润性好,各组分不会分离,不会与金属粉末发生反应,分解温度高于混料温度、成形温度,且产物无毒无害、可循环使用。
MIM(金属材料粉末注塑成型)技术介绍

精心整理
MIM(金属粉末注塑成型)技术介绍
?????MIM 是将现代塑料注射成形技术引入粉末冶金领域而形成的一种全新的金属零部件近净成形加工技术,是近年来粉末冶金学科和工业领域中发展十分迅猛的一项高新技术。
MIM 的工艺步骤是:首先选取符合MIM MIM ????1????2~1.6μm ????3度高,工序简单,可实现连续大批量生产;?
????4、产品质量稳定、性能可靠,制品的相对密度可达95%~99%,可进行渗碳、淬火、回火等热处理。
产品强度、硬度、延伸率等力学性能高,耐磨性好,耐疲劳,组织均匀;?
国际上普遍认为MIM技术的发展将会导致零部件成形与加工技术的一场革命,被誉为“21世纪最热门的零部件的成形技术”。
?
MIM技术优势
MIM与传统粉末冶金相对比?
?MIM可以制造复杂形状的产品,避免更多的二次机加工。
?
?MIM产品密度高、耐蚀性好、强度高、延展性好。
?
?MIM可以将2个或更多PM产品组合成一个MIM产品,节省材料和工序。
?
MIM与机械加工相对比?
??MIM设计可以节省材料、降低重量。
???MIM可以将注射后的浇口料重复破碎使用,不影响产品性能,材料利用率高。
粉末注射成型

金属粉末注射成型(MIM)
比较项目 零件相对密度 零件拉伸强度 Байду номын сангаас末注射成形 粉末冶金 精密铸造 98% 高 86% 低 98% 高 机加工 100% 高 冲压 100% 高
零件表面光洁度
零件微小化能力 零件薄壁能力 零件复杂程度 零件设计宽容度 批量生产能力 适应材质范围 供货能力
医疗机械用零件:如牙矫形架、剪刀、镊子; 军用零件:导弹尾翼、枪支零件、弹头、药型罩、 引信用零件; 电气用零件:微型马达、电子零件、传感器件; 电气汽车零件:门锁体、螺栓、安全气囊零件等。
谢谢观看!
陶瓷粉末注射成型(CIM)
成型工艺:
粉末 粘结剂 分散剂 润滑剂 产品检测 混合 除气、制粒 注射
烧结
脱脂
金属粉末注射成型(MIM)
成型工艺:
粉末
粘结剂
注射成型 脱粘
烧结
金属粉末注射成型(MIM)
应用特点: 模具成本很高,尤其对于大批量生产,模具需要用 高硬耐磨材料制造,材料成本很高;
配料成本高,工艺步骤多、过程要求高;
高
高 高 高 高 高 高 高
中
中 中 低 中 高 高 高
中
低 中 中 中 中 中-高 中
高
中 低 高 中 中-高 高 低
高
高 高 低 低 高 中 高
表1-1 粉末注射成形工艺与传统批量工业化零件加工工艺的比较
金属粉末注射成型(MIM)
应用领域:
计算机及其辅助设施零件; 日用器具:如手表零件、照相机零件等;
粉末注射成型
粉末注射成型(Powder Injection Molding)
金属粉末的注射成型

具有极高的表面积和活性,能够提高 材料的力学性能和电磁性能,为金属 粉末注射成型的发展提供了新的方向 。
材料性能与成型工艺的关系
1 2 3
流动性
金属粉末的流动性直接影响注射成型的充模能力 和制件质量,流动性好的粉末有利于提高制件的 光洁度和尺寸精度。
压缩性
金属粉末的压缩性决定了其在模具内的填充密度 和制件的致密度,压缩性好的粉末能够提高制件 的机械性能。
医疗器械领域
制造个性化医疗器械和植入物,满足医疗行业对个性化、高性能 和高安全性的需求。
感谢您的观看
THANKS
注射成型操作
将混合料加热至流动状态,注入 模具中,在压力和温度的作用下, 混合料填充模具并硬化定型。
后处理
脱脂
烧结
通过加热或化学方法将粘结剂从金属粉末 中分解、去除,以获得纯净的金属制品。
将脱脂后的金属粉末制品在高温下进行烧 结,使金属粉末颗粒之间形成冶金结合, 提高制品的强度和性能。
热处理
表面处理
度和复杂度。
新型粘结剂的开发
02
研究新型粘结剂,以提高金属粉末的粘结效果,降低成型难度
和成本。
连续注射成型技术
03
开发连续注射成型技术,实现金属粉末的连续加工,提高生产
效率和降低能耗。
新材料的应用与开发
高性能金属粉末
研究开发高性能金属粉末,如钛合金、镍基高温 合金等,以满足高端制造业的需求。
复合材料的应用
详细描述
粉末流动性问题通常表现为注射压力不足、填充不均匀、成 型时间延长等。为了解决这一问题,可以采用改善粉末粒度 分布、降低粉末含水量和加入润滑剂等方法,以提高粉末的 流动性。
成型精度问题
注射成型不锈钢粉末工艺参数
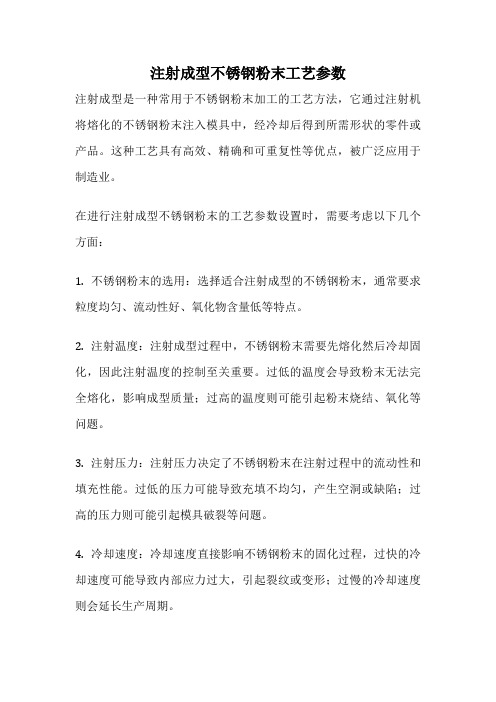
注射成型不锈钢粉末工艺参数
注射成型是一种常用于不锈钢粉末加工的工艺方法,它通过注射机将熔化的不锈钢粉末注入模具中,经冷却后得到所需形状的零件或产品。
这种工艺具有高效、精确和可重复性等优点,被广泛应用于制造业。
在进行注射成型不锈钢粉末的工艺参数设置时,需要考虑以下几个方面:
1. 不锈钢粉末的选用:选择适合注射成型的不锈钢粉末,通常要求粒度均匀、流动性好、氧化物含量低等特点。
2. 注射温度:注射成型过程中,不锈钢粉末需要先熔化然后冷却固化,因此注射温度的控制至关重要。
过低的温度会导致粉末无法完全熔化,影响成型质量;过高的温度则可能引起粉末烧结、氧化等问题。
3. 注射压力:注射压力决定了不锈钢粉末在注射过程中的流动性和填充性能。
过低的压力可能导致充填不均匀,产生空洞或缺陷;过高的压力则可能引起模具破裂等问题。
4. 冷却速度:冷却速度直接影响不锈钢粉末的固化过程,过快的冷却速度可能导致内部应力过大,引起裂纹或变形;过慢的冷却速度则会延长生产周期。
5. 模具温度:模具温度的控制可以影响注射成型的充填性能和成品的表面质量。
过低的温度可能导致粉末凝固不完全,产生毛刺或瑕疵;过高的温度则可能引起粉末烧结或氧化。
6. 固化时间:固化时间是指不锈钢粉末在模具中冷却固化所需的时间。
固化时间过短可能导致产品未完全固化,无法保持所需形状;固化时间过长则会增加生产周期。
在实际操作中,需要根据具体的不锈钢粉末材料和产品要求进行工艺参数的优化调整。
通过合理的工艺参数设置,可以实现不锈钢粉末注射成型工艺的高效、精确和稳定性,为制造业提供优质的不锈钢零件和产品。
金属粉末注射成型

案例四:电子产品制造
总结词
微型化、高精度、轻量化
详细描述
金属粉末注射成型在电子产品制造中发挥着重要作用,尤其 在微型化、高精度和轻量化方面具有显著优势。例如,用于 制造手机、平板电脑等消费电子产品的金属结构件和连接件 等。
05
结论
金属粉末注射成型的重要性和应用前景
金属粉末注射成型是一种重要的金属加 工技术,具有高精度、高效率、低成本 等优点,广泛应用于汽车、航空航天、
未来发展方向
新材料研究与应用
随着新材料技术的不断发展,未来将有更 多具有优异性能的金属粉末应用于金属粉
末注射成型工艺。Βιβλιοθήκη 环保与可持续发展随着环保意识的提高,未来金属粉末注射 成型将更加注重环保和可持续发展,减少
生产过程中的废弃物和能耗。
智能化与自动化
通过引入先进的传感器、控制系统和人工 智能技术,实现金属粉末注射成型的智能 化和自动化,提高生产效率和产品质量。
探索金属粉末注射成型与其他 先进制造技术的结合,实现优 势互补,提高整体制造水平。
ABCD
加强新材料的研发和应用, 以满足市场需求和推动产 业升级。
加强国际合作和技术交流,引 进先进技术和理念,推动金属 粉末注射成型技术的全球发展 。
THANK YOU
型产品。
1970年代
随着粘结剂喷射和脱脂技术的 发展,金属粉末注射成型技术
逐渐成熟。
1980年代至今
金属粉末注射成型技术不断发 展和完善,应用领域不断扩大
。
应用领域
电子通讯
如连接器、端子、 线圈架等;
医疗器械
如手术器械、牙科 器械等;
汽车零件
如发动机零件、变 速器零件、刹车系 统零件等;
粉末注射成型

粉末注射成型
粉末注射成型(Powder Injection Moulding,简称PIM)是一种将金属或陶瓷粉末通过加工制造成零件的技术。
这
个过程类似于传统的塑料注射成型,但使用的是金属或陶
瓷粉末。
整个过程包括以下步骤:
1. 材料准备:选择合适的金属或陶瓷粉末,并按照特定的
配方制备成所需的粉末混合物。
2. 注射成型:将粉末混合物装入注射机中,并通过高压将
粉末推入模具中。
模具通常是具有所需形状的两个半球体。
3. 球芯去除:等到粉末充填到模具后,球芯会自动脱落并
迅速冷却固化。
4. 焙烧:固化的零件需要经过焙烧过程,以去除残留的有
机物,并增加材料的密度和强度。
5. 精加工:将焙烧后的零件进行必要的后续加工,例如打磨、抛光等。
6. 检测和质量控制:对成品进行检测,确保其符合规定的
尺寸和质量标准。
粉末注射成型技术具有许多优点,例如可以生产形状复杂的零件,材料利用率高,生产效率高等。
它被广泛应用于汽车、医疗器械、工具等领域的零部件制造。
《金属粉末注射成型》课件

金属粉末的压缩性对注射成型的充模过程和制件 质量有重要影响,压缩性好的粉末能够减小注射 压力和注射时间,提高生产效率。
松装密度与流动性关系
松装密度较高的粉末具有较好的流动性,有利于 提高制件的致密度和减小内应力。
热物理性能
金属粉末的热物理性能如熔点、热导率、热膨胀 系数等对注射成型的加热、冷却和制件性能有较 大影响,选择合适的热物理性能有助于优化注射 成型工艺和提高制件性能。
随着市场需求的多样化,金属粉末注射成 型技术将更加注重定制化和个性化生产, 满足不同客户的需求。
05
金属粉末注射成型工 艺优化
工艺参数优化
温度控制
优化温度参数,确保金属粉末在熔融和冷却过程中的 温度分布均匀,提高成型质量。
压力调整
合理设置注射和压制压力,以获得更好的密度和强度 。
注射速度与时间
优化注射速度和时间,确保金属粉末均匀填充模具并 减少内部缺陷。
科植入物等。
其他
金属粉末注射成型还可应用于 电子产品、珠宝等领域,生产
小型、复杂的金属零件。
02
金属粉末注射成型原 理
粉末制备
01
02
03
原材料选择
根据产品需求选择合适的 金属粉末,如不锈钢、钛 合金、镍基合金等。
粉末制备方法
通过化学或物理方法将原 材料细化成微米级粉末, 确保粉末的纯度、粒度和 流动性。
烧结与后处理
烧结
在保护气氛下将注射成型的金属零件 进行烧结,使金属粉末颗粒间形成冶 金结合,提高零件的强度和致密度。
后处理
根据需要,对烧结后的零件进行热处 理、机加工、表面处理等后处理操作 ,以满足产品性能和使用要求。
03
金属粉末注射成型材 料
PIM粉末注射成形概述

PIM粉末注射成形概述:注射成型车间连续烧结炉设备结构图真空烧结炉粉末注射成形(Powder Injection Molding,PIM)由金属粉末注射成形(Metal Injection Molding,MIM)与陶瓷粉末注射成形(Ceramics Injection Molding,CIM)两部分组成,它是一种新的金属、陶瓷零部件制备技术,它是将塑料注射成形技术引入到粉末冶金领域而形成的一种全新的零部件加工技术。
MIM的基本工艺步骤是:首先选取符合MIM要求的金属粉末和黏结剂,然后在一定温度下采用适当的方法将粉末和黏结剂混合成均匀的喂料,经制粒后再注射成形,获得成形坯(Green Part),再经过脱脂处理后烧结致密化成为最终成品(White Part)。
粉末注射成形技术的特点:粉末注射成形能像生产塑料制品一样,一次成形生产形状复杂的金属、陶瓷零部件。
该工艺技术利用注射方法,保证物料充满模具型腔,也就保证了零件高复杂结构的实现。
以往在传统加工技术中,对于复杂的零件,通常是先分别制作出单个零件,然后再组装;而在使用PIM技术时,可以考虑整合成完整的单一零件,这样大大减少了生产步骤,简化了加工程序。
1、与传统的机械加工、精密铸造相比,制品内部组织结构更均匀;与传统粉末冶金压制∕烧结相比,产品性能更优异,产品尺寸精度高,表面光洁度好,不必进行再加工或只需少量精加工。
金属注射成形工艺可直接成形薄壁结构件,制品形状已能接近或达到最终产品要求,零件尺寸公差一般保持在±0.10%~±0.30%水平,特别对于降低难以进行机械加工的硬质合金的加工成本、减少贵重金属的加工损失尤其具有重要意义。
2、零部件几何形状的自由度高,制件各部分密度均匀、尺寸精度高,适于制造几何形状复杂、精度密高及具有特殊要求的小型零件(0.2~200g)。
3、合金化灵活性好,对于过硬、过脆、难以切削的材料或原料铸造时有偏析或污染的零件,可降低制造成本。
金属粉末注射成型技术
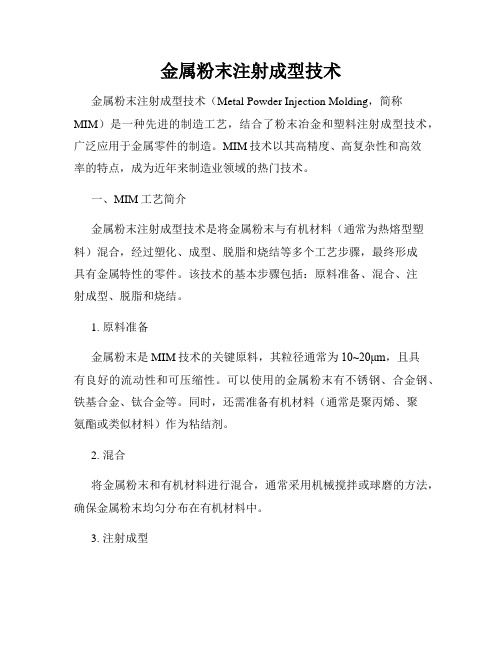
金属粉末注射成型技术金属粉末注射成型技术(Metal Powder Injection Molding,简称MIM)是一种先进的制造工艺,结合了粉末冶金和塑料注射成型技术,广泛应用于金属零件的制造。
MIM技术以其高精度、高复杂性和高效率的特点,成为近年来制造业领域的热门技术。
一、MIM工艺简介金属粉末注射成型技术是将金属粉末与有机材料(通常为热熔型塑料)混合,经过塑化、成型、脱脂和烧结等多个工艺步骤,最终形成具有金属特性的零件。
该技术的基本步骤包括:原料准备、混合、注射成型、脱脂和烧结。
1. 原料准备金属粉末是MIM技术的关键原料,其粒径通常为10~20μm,且具有良好的流动性和可压缩性。
可以使用的金属粉末有不锈钢、合金钢、铁基合金、钛合金等。
同时,还需准备有机材料(通常是聚丙烯、聚氨酯或类似材料)作为粘结剂。
2. 混合将金属粉末和有机材料进行混合,通常采用机械搅拌或球磨的方法,确保金属粉末均匀分布在有机材料中。
3. 注射成型混合料经过塑化,放入注射成型机中进行注射成型。
注射成型机通过加热熔融的混合料,并将其注入模具中,在一定的温度和压力下形成所需的零件形状。
4. 脱脂注射成型后,零件经过脱脂工艺,将有机材料从混合料中去除。
通常使用热处理或溶剂处理方法进行脱脂。
5. 烧结脱脂后的零件被置于特定的高温环境中,金属粉末与有机材料经过烧结而成。
在烧结过程中,金属颗粒之间发生冶金结合,形成致密的金属零件。
二、MIM技术的优势金属粉末注射成型技术相比其他金属加工方式具有以下几个显著优势:1. 复杂形状MIM技术可以制造复杂形状的金属零件,包括细小孔洞、薄壁结构、内部腔体等。
这种高精度和高复杂性的加工能力,使得MIM技术在航空航天、医疗器械、汽车零部件等领域得到广泛应用。
2. 材料多样性MIM技术可以使用多种金属粉末制造零件,涵盖广泛的金属材料,包括不锈钢、合金钢、铁基合金、钛合金等。
这使得MIM技术具有较大的材料选择范围,满足不同应用领域对材料性能的需求。
金属粉末注射成型技术(MIM)

金属粉末注射成型技术(Metal Powder Injection Molding,简称MIM)是将现代塑料注射成形技术引入粉末冶金领域而形成的一门新型粉末冶金近净形成形技术。
其基本工艺过程是:首先将固体粉末与有机粘结剂均匀混练,经制粒后在加热塑化状态下(~150℃)用注射成形机注入模腔内固化成形,然后用化学或热分解的方法将成形坯中的粘结剂脱除,最后经烧结致密化得到最终产品。
与传统工艺相比,具有精度高、组织均匀、性能优异,生产成本低等特点,其产品广泛应用于电子信息工程、生物医疗器械、办公设备、汽车、机械、五金、体育器械、钟表业、兵器及航空航天等工业领域。
因此,国际上普遍认为该技术的发展将会导致零部件成形与加工技术的一场革命,被誉为“当今最热门的零部件成形技术”和“21世纪的成形技术”。
美国加州Parmatech公司于1973年发明,八十年代初欧洲许多国家以及日本也都投入极大精力开始研究该技术,并得到迅速推广。
特别是八十年代中期,这项技术实现产业化以来更获得突飞猛进的发展,每年都以惊人的速度递增。
到目前为止,美国、西欧、日本等十多个国家和地区有一百多家公司从事该工艺技术的产品开发、研制与销售工作。
日本在竞争上十分积极,并且表现突出,许多大型株式会社均参与MIM工业的推广,这些公司包括有太平洋金属、三菱制钢、川崎制铁、神户制钢、住友矿山、精工--爱普生、大同特殊钢等。
目前日本有四十多家专业从事MIM产业的公司,其MIM工业产品的销售总值早已超过欧洲并直追美国。
到目前为止,全球已有百余家公司从事该项技术的产品开发、研制与销售工作,MIM技术也因此成为新型制造业中最为活跃的前沿技术领域,被世界冶金行业的开拓性技术,代表着粉末冶金技术发展的主方向MIM技术金属粉末注射成型技术是集塑料成型工艺学、高分子化学、粉末冶金工艺学和金属材料学等多学科透与交叉的产物,利用模具可注射成型坯件并通过烧结快速制造高密度、高精度、三维复杂形状的结构零件,能够快速准确地将设计思想物化为具有一定结构、功能特性的制品,并可直接批量生产出零件,是制造技术行业一次新的变革。
MIM金属粉末注射成型技术简介

MIM金属粉末注射成型技术简介MIM(Metal Injection Molding)金属粉末注射成型技术是一种将金属粉末与聚合物混合并注射成型的成型工艺。
这种工艺结合了传统金属粉末冶金和塑料注射成型技术的优势,可以生产出复杂形状、高精度和高强度的金属零件。
MIM工艺的基本原理是将金属粉末与适当比例的聚合物混合,并在高温下注射进模具中。
注射后,模具中的混合物经过固化和烧结两个步骤。
首先,在固化阶段,聚合物在高温下固化成强度较低的绿坯。
然后,在烧结阶段,通过加热使聚合物燃烧脱除,金属粉末颗粒在密实的绿坯中结合成金属零件。
MIM工艺具有以下几个优点。
首先,它可以实现复杂形状的金属零件的制作,包括内腔、细槽和细孔等特殊结构。
其次,MIM可以生产出精度高、表面光滑的零件。
此外,在同样强度要求下,MIM制件的重量通常比传统制造工艺更轻。
最后,MIM工艺适用于大批量生产,可以实现高效率、低成本的生产。
MIM工艺的主要应用领域包括电子、汽车、医疗、军工等行业。
在电子领域,MIM可以制作出细小的电子器件,如连接器、电池片和耳机插头等。
在汽车领域,MIM可以制作出复杂的发动机零件、传动系统部件和刹车系统组件等。
在医疗领域,MIM可以制作出高精度的人工关节、牙科器械和手术工具等。
在军工领域,MIM可以制作出高强度、耐磨的武器部件和飞行器部件等。
然而,MIM工艺也存在一些限制。
首先,MIM工艺的设备和材料成本较高,需要更高的投资。
其次,MIM的制造周期较长,通常需要数周至数月的时间。
最后,MIM工艺的材料种类有限,只适用于可烧结金属粉末,如不锈钢、合金钢和钛合金等。
总的来说,MIM金属粉末注射成型技术是一种高效、精密和经济的金属制造工艺。
随着对金属零件的需求不断增加,MIM有望在各行业中得到更广泛的应用。
未来,随着新材料的发展和工艺改进,MIM技术将进一步提升零件的性能和质量,为各行业的发展带来更多的机遇和挑战。
2024年金属粉末注射成型技术(2篇)

2024年金属粉末注射成型技术金属粉末注射成型技术(MetalPowderInjectionMolding,简称MIM)是将现代塑料喷射成形技术引入粉末冶金领域而形成的一门新型粉末冶金近净形成形技术。
其基本工艺过程是:首先将固体粉末与有机粘结剂均匀混练,经制粒后在加热塑化状态下(~150℃)用喷射成形机注入模腔内固化成形,然后用化学或热分解的方法将成形坯中的粘结剂脱除,最后经烧结致密化得到最终产品。
与传统工艺相比,具有精度高、组织均匀、性能优异,生产成本低等特点,其产品广泛应用于电子信息工程、生物医疗器械、办公设备、汽车、机械、五金、体育器械、钟表业、兵器及航空航天等工业领域。
因此,国际上普遍认为该技术的发展将会导致零部件成形与加工技术的一场革命,被誉为“当今最热门的零部件成形技术”和“21世纪的成形技术”。
美国加州Parmatech公司于1973年发明,八十年代初欧洲许多国家以及日本也都投入极大精力开始研究该技术,并得到迅速推广。
特别是八十年代中期,这项技术实现产业化以来更获得突飞猛进的发展,每年都以惊人的速度递增。
到目前为止,美国、西欧、日本等十多个国家和地区有一百多家公司从事该工艺技术的产品开发、研制与销售工作。
日本在竞争上十分积极,并且表现突出,许多大型株式会社均参与MIM工业的推广,这些公司包括有太平洋金属、三菱制钢、川崎制铁、神户制钢、住友矿山、精工--爱普生、大同特殊钢等。
目前日本有四十多家专业从事MIM产业的公司,其MIM工业产品的销售总值早已超过欧洲并直追美国。
到目前为止,全球已有百余家公司从事该项技术的产品开发、研制与销售工作,MIM技术也因此成为新型制造业中最为活跃的前沿技术领域,被世界冶金行业的开拓性技术,代表着粉末冶金技术发展的主方向MIM技术。
金属粉末喷射成型技术是集塑料成型工艺学、高分子化学、粉末冶金工艺学和金属材料学等多学科透与交叉的产物,利用模具可喷射成型坯件并通过烧结快速制造高密度、高精度、三维复杂形状的结构零件,能够快速准确地将设计思想物化为具有一定结构、功能特性的制品,并可直接批量生产出零件,是制造技术行业一次新的变革。
金属粉末注塑成型技术
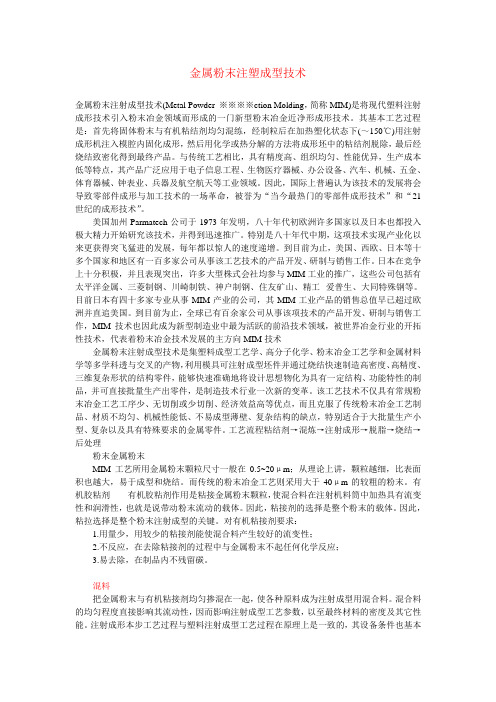
金属粉末注塑成型技术金属粉末注射成型技术(Metal Powder ※※※※ction Molding,简称MIM)是将现代塑料注射成形技术引入粉末冶金领域而形成的一门新型粉末冶金近净形成形技术。
其基本工艺过程是:首先将固体粉末与有机粘结剂均匀混练,经制粒后在加热塑化状态下(~150℃)用注射成形机注入模腔内固化成形,然后用化学或热分解的方法将成形坯中的粘结剂脱除,最后经烧结致密化得到最终产品。
与传统工艺相比,具有精度高、组织均匀、性能优异,生产成本低等特点,其产品广泛应用于电子信息工程、生物医疗器械、办公设备、汽车、机械、五金、体育器械、钟表业、兵器及航空航天等工业领域。
因此,国际上普遍认为该技术的发展将会导致零部件成形与加工技术的一场革命,被誉为“当今最热门的零部件成形技术”和“21世纪的成形技术”。
美国加州Parmatech公司于1973年发明,八十年代初欧洲许多国家以及日本也都投入极大精力开始研究该技术,并得到迅速推广。
特别是八十年代中期,这项技术实现产业化以来更获得突飞猛进的发展,每年都以惊人的速度递增。
到目前为止,美国、西欧、日本等十多个国家和地区有一百多家公司从事该工艺技术的产品开发、研制与销售工作。
日本在竞争上十分积极,并且表现突出,许多大型株式会社均参与MIM工业的推广,这些公司包括有太平洋金属、三菱制钢、川崎制铁、神户制钢、住友矿山、精工--爱普生、大同特殊钢等。
目前日本有四十多家专业从事MIM产业的公司,其MIM工业产品的销售总值早已超过欧洲并直追美国。
到目前为止,全球已有百余家公司从事该项技术的产品开发、研制与销售工作,MIM技术也因此成为新型制造业中最为活跃的前沿技术领域,被世界冶金行业的开拓性技术,代表着粉末冶金技术发展的主方向MIM技术金属粉末注射成型技术是集塑料成型工艺学、高分子化学、粉末冶金工艺学和金属材料学等多学科透与交叉的产物,利用模具可注射成型坯件并通过烧结快速制造高密度、高精度、三维复杂形状的结构零件,能够快速准确地将设计思想物化为具有一定结构、功能特性的制品,并可直接批量生产出零件,是制造技术行业一次新的变革。
金属的粉末注射成型技术
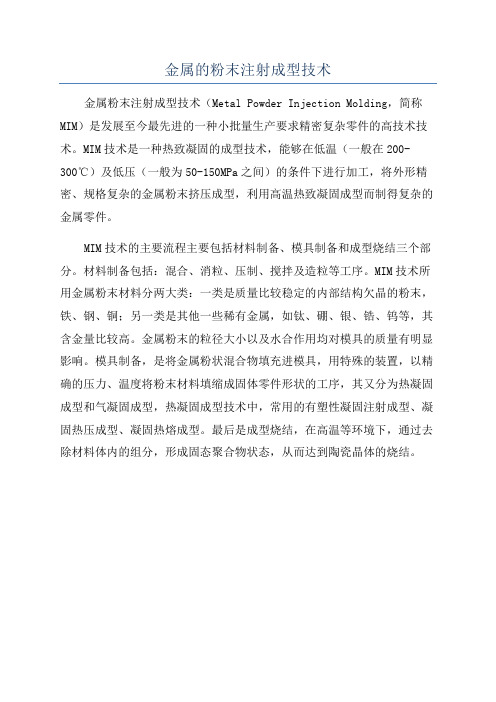
金属的粉末注射成型技术
金属粉末注射成型技术(Metal Powder Injection Molding,简称MIM)是发展至今最先进的一种小批量生产要求精密复杂零件的高技术技术。
MIM技术是一种热致凝固的成型技术,能够在低温(一般在200-300℃)及低压(一般为50-150MPa之间)的条件下进行加工,将外形精密、规格复杂的金属粉末挤压成型,利用高温热致凝固成型而制得复杂的金属零件。
MIM技术的主要流程主要包括材料制备、模具制备和成型烧结三个部分。
材料制备包括:混合、消粒、压制、搅拌及造粒等工序。
MIM技术所用金属粉末材料分两大类:一类是质量比较稳定的内部结构欠晶的粉末,铁、钢、铜;另一类是其他一些稀有金属,如钛、硼、银、锆、钨等,其含金量比较高。
金属粉末的粒径大小以及水合作用均对模具的质量有明显影响。
模具制备,是将金属粉状混合物填充进模具,用特殊的装置,以精确的压力、温度将粉末材料填缩成固体零件形状的工序,其又分为热凝固成型和气凝固成型,热凝固成型技术中,常用的有塑性凝固注射成型、凝固热压成型、凝固热熔成型。
最后是成型烧结,在高温等环境下,通过去除材料体内的组分,形成固态聚合物状态,从而达到陶瓷晶体的烧结。
金属粉末注射成型技术
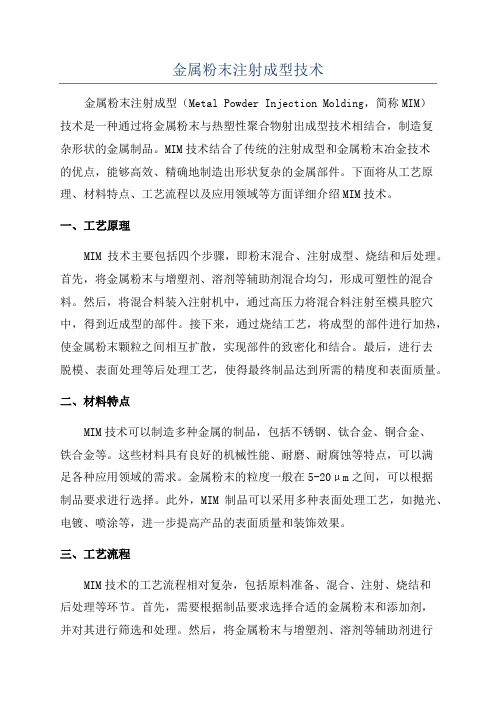
金属粉末注射成型技术金属粉末注射成型(Metal Powder Injection Molding,简称MIM)技术是一种通过将金属粉末与热塑性聚合物射出成型技术相结合,制造复杂形状的金属制品。
MIM技术结合了传统的注射成型和金属粉末冶金技术的优点,能够高效、精确地制造出形状复杂的金属部件。
下面将从工艺原理、材料特点、工艺流程以及应用领域等方面详细介绍MIM技术。
一、工艺原理MIM技术主要包括四个步骤,即粉末混合、注射成型、烧结和后处理。
首先,将金属粉末与增塑剂、溶剂等辅助剂混合均匀,形成可塑性的混合料。
然后,将混合料装入注射机中,通过高压力将混合料注射至模具腔穴中,得到近成型的部件。
接下来,通过烧结工艺,将成型的部件进行加热,使金属粉末颗粒之间相互扩散,实现部件的致密化和结合。
最后,进行去脱模、表面处理等后处理工艺,使得最终制品达到所需的精度和表面质量。
二、材料特点MIM技术可以制造多种金属的制品,包括不锈钢、钛合金、铜合金、铁合金等。
这些材料具有良好的机械性能、耐磨、耐腐蚀等特点,可以满足各种应用领域的需求。
金属粉末的粒度一般在5-20μm之间,可以根据制品要求进行选择。
此外,MIM制品可以采用多种表面处理工艺,如抛光、电镀、喷涂等,进一步提高产品的表面质量和装饰效果。
三、工艺流程MIM技术的工艺流程相对复杂,包括原料准备、混合、注射、烧结和后处理等环节。
首先,需要根据制品要求选择合适的金属粉末和添加剂,并对其进行筛选和处理。
然后,将金属粉末与增塑剂、溶剂等辅助剂进行混合,形成可塑性的混合料。
接下来,将混合料装入注射机中,通过高压力将混合料注射至模具腔穴中。
然后,将近成型的部件进行烧结,使其实现致密化和结合。
最后,通过去脱模、除渣、表面处理等后处理工艺,得到最终的金属部件。
四、应用领域MIM技术的应用领域非常广泛,包括电子通讯、汽车工业、医疗器械、军工等领域。
在电子通讯领域,MIM技术可以制造小型高精度的连接器、插件等零部件,满足电子设备不断减小体积和提高性能的需求。
- 1、下载文档前请自行甄别文档内容的完整性,平台不提供额外的编辑、内容补充、找答案等附加服务。
- 2、"仅部分预览"的文档,不可在线预览部分如存在完整性等问题,可反馈申请退款(可完整预览的文档不适用该条件!)。
- 3、如文档侵犯您的权益,请联系客服反馈,我们会尽快为您处理(人工客服工作时间:9:00-18:30)。
粉末注射成型技术的特点
MIM作为一种制造高质量精密零件的近净成形技术,具有常规和机加工方法比拟的优势。
MIM能制造许多具有复杂形状特征的零件:如各种外部切槽,外螺纹,锥形外表面,交叉通孔、盲孔,四台与键销,加强筋板,表面滚花等等,具有以上特征的零件都是无法用常规粉末冶金方法得到的。
由于通过MIM制造的零件几乎不需要再进行机加工,所以减少了材料的消耗,因此在所要求生产的复杂形状零件数量高于一定值时,MIM就会比机加工方法更为经济。
MIM和精密铸造成形能力的比较
粉末注射成型的优点:
能像生产塑料制品一样,一次成形生产形状复杂的金属、陶瓷等零件部件产品成本低、光洁度好、精度高(±0.3%~±0.1%),一般无需后续加工产品强度,硬度,延伸率等力学性能高,耐磨性好,耐疲劳,组织均匀原材料利用率高,生产自动化程度高,工序简单,可连续大批量生产无污染,生产过程为清洁工艺生产
粉末注射成型
粉末注射成型材料应用
较新MIM材料体系应用
常用MIM产品应用
几种粉末注射成型材料的基本性能
粉末注射形成技术与其他成形工艺技术比较
粉末注射成型工艺与传统批量工业与自动化零件加工、冲压、锻造、精密铸造、粉末冶金相比,具有极其明显的优势。
零件薄壁能力高中中低高
零件复杂程度高低中高低
零件设计宽容度高中中中低
批量生产能力高高中中-高高
适应材质范围高高中-高高中
供货能力高高中低高
粉末注射成型工艺流程图
适用材料及性能
材料
密度硬度拉伸强度伸长率
g/cm 3 洛氏MPa %
铁基合金MIM-2200(烧结态)
7.65
45HRB 290 40 MIM-2200(烧结态)50HRC 380 20 MIM-2700(烧结态)
7.65
69HRB 440 26 MIM-2700(碳氮共渗)55HRC 830 9 MIM-4650(烧结态)7.55 90HRB 700 11 MIM-4650(热处理态)7.55 48HRC 1655 2 MIM-8620(烧结态)7.5 85HRB 445 20 MIM-8620(热处理态)7.5 35HRC 800-1300 5-9
不锈钢
MIM - 316L (烧结态)7.8 67HRB 520 50
MIM-304L(烧结态)7.75 60HRB 500 70。