生产单元布局完整版
生产车间如何进行布局
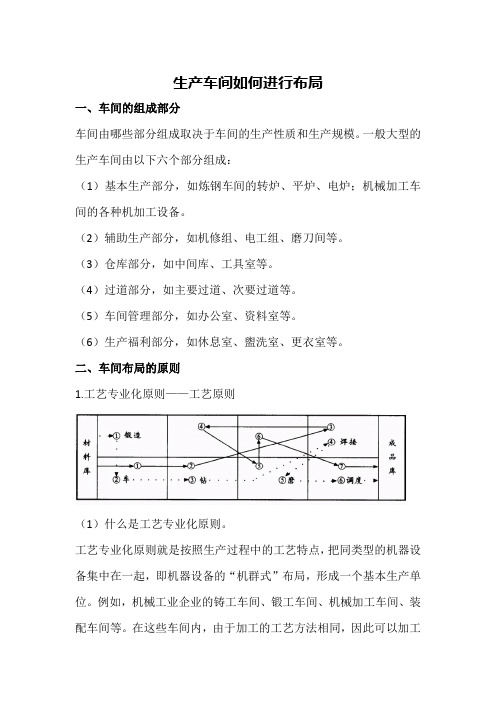
生产车间如何进行布局一、车间的组成部分车间由哪些部分组成取决于车间的生产性质和生产规模。
一般大型的生产车间由以下六个部分组成:(1)基本生产部分,如炼钢车间的转炉、平炉、电炉;机械加工车间的各种机加工设备。
(2)辅助生产部分,如机修组、电工组、磨刀间等。
(3)仓库部分,如中间库、工具室等。
(4)过道部分,如主要过道、次要过道等。
(5)车间管理部分,如办公室、资料室等。
(6)生产福利部分,如休息室、盥洗室、更衣室等。
二、车间布局的原则1.工艺专业化原则——工艺原则(1)什么是工艺专业化原则。
工艺专业化原则就是按照生产过程中的工艺特点,把同类型的机器设备集中在一起,即机器设备的“机群式”布局,形成一个基本生产单位。
例如,机械工业企业的铸工车间、锻工车间、机械加工车间、装配车间等。
在这些车间内,由于加工的工艺方法相同,因此可以加工多种多样的产品。
(2)工艺专业化原则的优点。
①车间对产品品种的适应性强。
②由于同种设备集中在一起,可以充分利用设备和生产面积,提高设备负荷系数。
③便于工艺管理。
④生产控制灵活性较强,便于生产任务连续进行。
(3)工艺专业化原则的缺点。
①当零件加工工序较多时,需要由不同的车间来完成,因而加工路线长,往返运输多,生产周期长。
②在制品数量增多,流动资金占用量增大。
③各车间之间的联系和协作关系复杂,影响各项管理工作的协调一致。
(4)适用范围。
按工艺专业化原则的车间工艺布局,多用于单件小批生产条件。
2.对象专业化原则——对象原则(1)什么是对象专业化原则。
对象专业化原则就是把加工对象的全部或大部分工艺过程集中在一个生产单位中,组成以产品或零件为对象的生产单位。
例如,机械工业企业的齿轮车间、标准件车间、发动机车间等。
(2)优点。
①机器设备按零件或产品的工艺流程布置,缩短了产品的加工路线,节约了运输费用,减少了仓库和生产面积。
②缩短了生产周期,减少了在制品数量和流动资金的占用量。
③减少了车间之间的联系,便于各项管理工作。
工厂及生产线布局
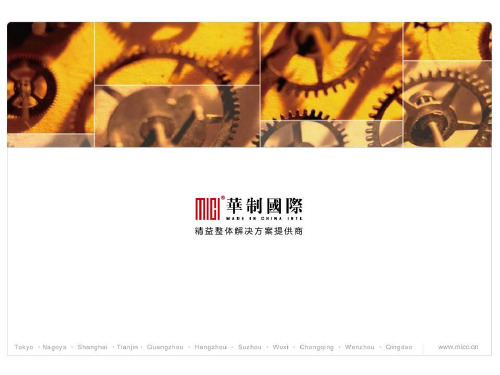
X
X X
将类似的加工工序归类,在上例中,产品A与C属于同一产品族,B与C?
成组原则布置优缺点 优点 1. 2. 3. 由于产品成组,设备利用率较高 流程通顺,运输距离较短,搬运 量少 有利于发挥班组合作精神 1. 2. 缺点 需要较高的生产控制水平以平衡 各单元之间的生产流程 如果单元之间流程不平衡,需要中 间储存,增加了单元之间的物料搬 运 班组成员需要掌握所有作业的技 能 减少使用专用设备的机会 有产品原则布置和工艺原则布置 的缺点
生产设施布置 服务设施布置
工厂总 体布置
车间内 部布置
服务设施 总体布置
服务设施 内部布置
4、设施布置的方法
1) 基本思路: 物料搬运占生产周期和生产成本的比重 很大; 尽量使物流较大的经济活动单元靠近, 以减少搬运距离和搬运量
2)具体方法
含义:
方法1:物料流向图法
按原材料进厂、零部件加工、产品装配等环节总体流动方向,绘制物料 流向图,来布置各车间、仓库和设施的相互位置。
预测,估算生产 能力及需求量 确定设施要求生 产能力及需求量 总体规划及总布 置图
O 预规划 Ⅰ.确定需求
规 划 顺 序
Ⅱ.总体规划 Ⅲ.详细规划
制定进度表 和网络图
做详细规划及详 细布置图
Ⅳ.规划设施 V 试运行
规划时间
施工,安装, 试车及总结
设施规划与设计阶段结构
3、设施布置种类,形势和类型
布置种类
车床 钻床 装配 车床 钻床
磨床
焊接 钻床 装配
滚齿 压机 压机 钻床
装配
平衡 装配 焊接 仓 库
仓 库
铣床 压机 磨床
分析产品族
加工流程
P/N
单元式生产布局CELLProduction

单元式生产布局CELLProduction单元生产方式的基本目的就是消除浪费,该生产模式主要消除七大浪费中的搬运浪费、等待浪费、生产线平衡浪费。
可有效的降低生产成本,提高质量及工作效率。
档即用网向您推荐如下的“单元式生产布局”的干货文档。
小伙伴们万万不可错过,原版文档下载方法参照文章底部说明~ 文档整理逻辑如下-->1.传统组装线设计精益组装线布局的目的:·按照节拍时间, 生产优质产品Quality products produced at takt time·有效利用人力 Productive utilization of people–装配工只做装配 Assembleproduct only–按节拍分配任务达到高生产力Highoperator productivity through loading to takttime–工人能完成整个流程 Operatorto complete the full process·物料/工人流畅 Flow of material and operators–优化工位以方便摆放零件?物料?工具Workstations optimized for presentation of parts, materials, and tools–工位设计减少走动Workstation design minimizes operator movements·信息即时反馈 Immediate flow of information /feedback·问题立即暴露 Immediately expose problems生产线布置方式:(1)U型线 U - Shaped Line最少走动;工人间的平衡;避免产生孤岛;多工序作业;促进沟通;按灯识别异常;WS负责所有物料需求;节拍变,你也变。
(2)直型线 Straight Line当产品结构和物料展示能够保证时使用生产线的速度由产品的移动速度决定随时掌握装配进展已经设立了工人区已经定义了交接区(交接指挥棒)按使用次序安排物料非整合分装(预装)按配套供料必须建立信息与反馈系统(3)开放式平行线布局 Parallel(Open Room) Layout 2.工位设计工位设计原理:标准化作业 Standard operations适当面积 Appropriate size零件排列 Part arrangement工具标准化 T ool standardization工具放置 Tool placement目视控制 Visual controls工人走动 Operator motions质量控制 Quality controls物料补充 Replenishment工位送料设计:3.物料展示 Material Presentation线上双箱系统:配套供料系统:4.物料补充 Material Resupply实施线上送料员(水蜘蛛) 系统:步骤1: 确定工位标准化作业步骤2: 识别待送零件步骤3: 制定物料展示系统步骤4: 做好分料箱 / 配套箱步骤5: 设计及制定线上送料员分料车和分料单步骤6: 设计及建造超市5.物料储存 Material Storage。
生产线布局(超详细)【精品课件】.ppt
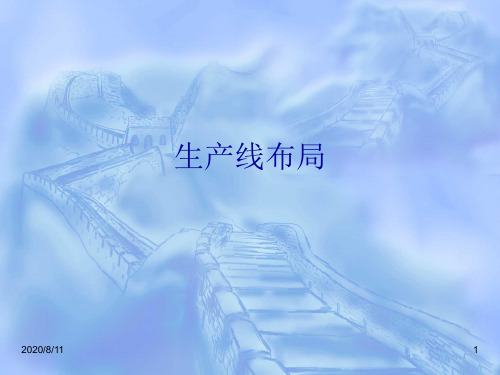
2020/8/11
12
鉴别七大浪费
六、来自工序不当的浪费
工作本身产生的浪费,当机器不正常运作而使操作人员 需要花额外时间,或当操作人员出于习惯或花了过多的 时间使清洁工作超过了规格的要求。
多余的检查也是过程浪费的另一个表现形式。
2020/8/11
13
鉴别七大浪费
七、不需要的动作的浪费
人们在工作设置中经常将工作中的动作搞混乱,实际做的动 作和工作要求的动作往往是不同的。
生产线布局
2020/8/11
1
精益生产五项基本原则
• 价值 (VALUE) : 决定于客户是否愿意为了它而付钱。
• 价值流 (VALUE STREAM) : 从产品设计到客户服务的所有
活动的描述和鉴别,都需要消除非增值活动。
• 流畅 (FLOW) : 消除所有工序的阻滞使价值流“流畅”而没有
中断。
作为一个确定的目的,工作是要作为一组精确的动作来考虑 的,哪些是增值的,那些是不增值的。
一个人在每天的恒定的工作中(例如一个很忙的人)可能实 际上只是很少一部分是增值工作。
工作中的不需要的动作被认为是浪费的,不增值的。
2020/8/11
14
生产布局前的准备工作
▪ 产能评估 ▪ 生产线顺流 ▪ 库存周转评估
1. 采用了看板管理,拉动生产方式 2. 车间布局U型布局; 3. 不同类型的机器摆放在一块; 4. 实现了单件流的生产; 5. 机器小型化 ; 6. 工序中间很少甚至没有库存; 7. 实现了作业标准化; 8. 对工人实行了多技能培训; 9. 具有完善的作业改善活动制度
2020/8/11
3
看谁摘的果子最多!
6
产生更严重的成本连锁反应……
生产线布局(超详细)_图文
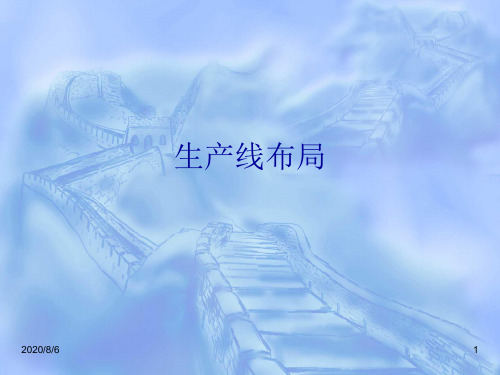
工艺原则布局
权重代码 密切程度
A
绝对必要
E
特别重要
I
重要
O
普通的
U
不重要的
X
不予考虑的
2020/8/6
线代号
29
工艺原则布局
▪ 医院相关图
1
3
5
2
4
6
2020/8/6
30
工艺原则布局
▪ 医院总体合理布局图
1
4
65
2
3
2020/8/6
31
工艺原则布局
▪ 布局方法 设部门或工艺有n个
布局方案=n!
▪ 使用范围:
• 批量小 • 体积大
▪ 布局特点
• 以产品为中心 • 不考虑物流成本和复杂程度
2020/8/6
18
工艺原则布局
▪ 定义:
• 将相似的设备或功能集中放在一起的布局方式 • 也称车间布局,如车床车间
▪ 使用范围
• 生产设备密集型 • 设备专业性 • 自动化程度高 • 资本密集型 • 产品重量轻
2020/8/6
次数
1 1 2 3 4 5 6 7 8
23 175 50
0
45 0 30 100 75 17 88
20
678 200 20 25 90 80 90 125 99 180 5 0 25 0 180 187
347 103 7
21
▪ 玩具厂各车间年物流成本示意图
2020/8/6
22
工艺原则布局
1. 采用了看板管理,拉动生产方式 2. 车间布局U型布局; 3. 不同类型的机器摆放在一块; 4. 实现了单件流的生产; 5. 机器小型化 ; 6. 工序中间很少甚至没有库存; 7. 实现了作业标准化; 8. 对工人实行了多技能培训; 9. 具有完善的作业改善活动制度
第四章生产与运作系统的布局共24页
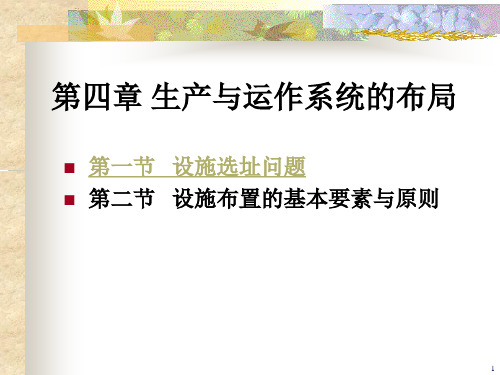
j1
i1
9
设施选址方法的实例见 [例4-1]、 [例4-2]
10
二、目前设施选址的发展趋
➢ 工业园区和工业中心 ➢ 企业群体布局,靠近仓储设施和服务设施 ➢ 企业生产运作全球化 ➢ 向郊区发展 ➢ 选址要注意有利于生态环境控制 ➢ 选址应适应动态、长期、均衡的发展 ➢ 设施选址普遍应用多目标规划和计算机技
地理位置 1 3 3 2 2 4 4 1 1
气候 1 1 1 4 4 2 2 3 3
生活 1 2 2 3 3 4 4 1 1
科技依托 1 1 1 2 2 3 3 4 4
总分
78
112
97
83
8
厂址位置选择的方法-线性规划法
某企业有n个可供选择的厂址,需供应m个目标市场
设 Xi: i工厂的产量 (i=1‥‥‥ n)
最方便。
➢发展合理性
16
厂区布置的目标
➢ 最短的运输路线 ➢ 最大的灵活性 ➢ 面积的最有效利用 ➢ 最良好的工作环境 ➢ 最合理的发展余地
17
车间布置
所谓车间布置就是按一定的原则、正 确地确定车间内部各组成单位(工段、 班组)及工作地,设备机床之间的相互 位置,从而使它能组成一个有机整体, 实现车间的具体功能和任务。
75
10
70
15
必要 必要
90
必要
原方案: 数控机床 车铣床 总装台 检验组 工具组 磨床 新方案: 工具组 车铣床 总装台 数控机床 磨床 检验组
表中的数字表示ABC三种产品由一个工序至另一个工序往返的 距离单位与重量单位之积的总和。数字越大说明往返越多,此数字 为工序的从至数。
从至数越大说明工序相关性越重要。 由以上可得出以下结论:
生产线布局(超详细)_图文
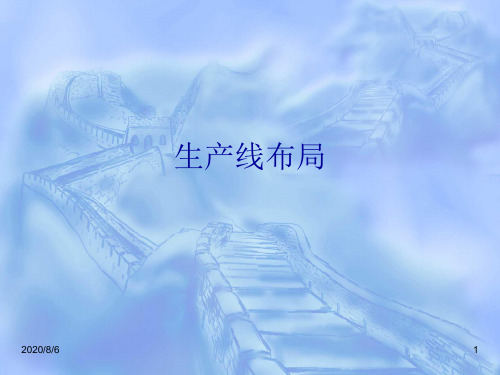
次数
1 1 2 3 4 5 6 7 8
23 175 50
0
45 0 30 100 75 17 88
20
678 200 20 25 90 80 90 125 99 180 5 0 25 0 180 187
347 103 7
21
▪ 玩具厂各车间年物流成本示意图
2020/8/6
22
工艺原则布局
2020/8/6
12
鉴别七大浪费
六、来自工序不当的浪费
工作本身产生的浪费,当机器不正常运作而使操作人员 需要花额外时间,或当操作人员出于习惯或花了过多的 时间使清洁工作超过了规格的要求。
多余的检查也是过程浪费的另一个表现形式。
2020/8/6
13
鉴别七大浪费
七、不需要的动作的浪费
人们在工作设置中经常将工作中的动作搞混乱,实际做的动 作和工作要求的动作往往是不同的。
2020/8/6
15
生产线布局类别
▪ 定位原则布局 ▪ 工艺原则布局 ▪ 产品原则布局 ▪ 成组技术(单元式)布局
2020/8/6
16
定位原则布局
▪ 定义:
• 将原材料和设备按照使用次序和移动的难易程度 在产品的四周进行生产
▪ 起源
• 19世纪初亨利福特的汽车装配线
2020/8/6
17
定位原则布局
2020/8/6
9
不合格品
率高
库
机器故障率高
调整时间太长
存
水
设备能力不平衡
缺勤率高
备件供应不及时
平
采购周期太长 技术服务 工人技能差 后勤服务差
不及时
图 17-1 库存水平高掩盖的管理问题多
生产管理培训教程生产系统布局

PART 3
生产系统布局的要素
设施布置
物料搬运:合理规划物料搬 运路线,提高生产效率
生产设备:选择合适的生产 设备,满足生产需求
空间布局:合理安排生产空 间,提高生产效率和员工舒
适度
安全设施:设置必要的安全 设施,保障员工安全
工艺流程
原材料准备:确保原材料的质量和数量 生产过程:按照工艺流程进行生产,确保产品质量 质量控制:对生产过程中的产品质量进行监控和检验 成品包装:对产品进行包装,确保产品的外观和质量 仓储物流:对产品进行仓储和物流管理,确保产品的安全和及时交付
提高产品质量: 合理的布局可以 提高产品质量, 减少不良品
提高员工满意度 :合理的布局可 以提高员工满意 度,降低员工流 失率
生产系统布局的原则
效率原则:提高生产效率,降低生产成本 安全原则:确保生产安全,防止事故发生 环保原则:减少环境污染,实现可持续发展 灵活性原则:适应市场需求变化,提高生产灵活性 经济性原则:合理利用资源,降低生产成本 美观性原则:保持生产环境整洁美观,提高员工工作满意
到预期目标
优化过程中的注意事项
考虑生产流程的合理性和 效率
确保设备布局的合理性和 效率
考虑物料和人员流动的合 理性和效率
考虑生产环境的安全性和 环保性
考虑生产系统的可扩展性 和灵活性
考虑生产系统的维护和保 养
优化后的评估与调整
评估标准:生产效 率、成本、质量、 安全等
调整方法:根据评 估结果,对生产系 统布局进行优化调 整
效率最大化
优点:提高生 产效率、降低 成本、提高产
品质量
应用:适用于 多种生产类型, 如流水线生产、 批量生产、单
件生产等
注意事项:合 理规划、优化 配置、定期维 护和更新设备、
04生产系统布局
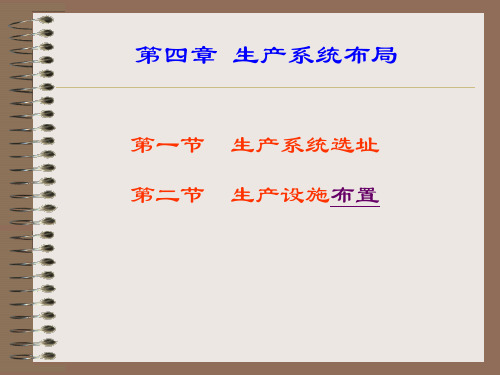
现有工厂 生产能力 和备选工厂 (台/月)
A
2800
B
2Байду номын сангаас00
X
2400
Y
2400
各仓库的需求(台/月)
到仓库的单位运费(元)
U
V
W
10
24
36
20
16
14
30
22
12
40
30
8
2200
1400
2600
第一节 生产系统选址
[解]首先,假定X选中,其解如下表。月总发运费用为: 2200×10+1400×16+200×14+2400×12 = 76000
工厂
生产能力 (吨/月)
P
到各仓库单位运费(元)
Q
X
Y
A
2400
15
27
48
51
B
2400
27
12
24
27
C
1800
45
24
9
15
第一节 生产系统选址
[解]首先,假定X选中,其解如下表。月总运输费用为: 2100×15 + 2100×12 + 300×24 + 1800×9 = 80100
工厂
A B C 需求
160
140
环境污染法规
50
30
40
30
税收稳定性
50
30
40
30
合
计
1100
840
900
800
第一节 生产系统选址
[例2]加权评分:考虑在某城市的高速发展区域新开设一医疗诊所, 其相关因素及权重如下表,求该选址的加权评分。
生产过程的布局ppt课件
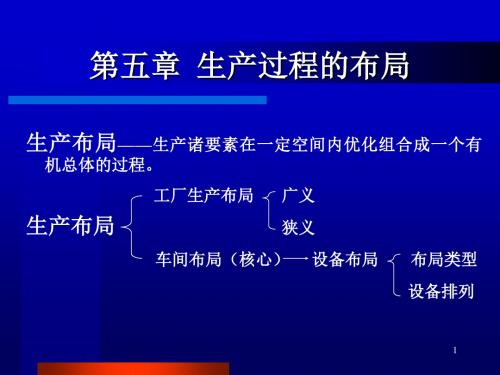
What 何为
How 如何
Why 为何 Who 何人
Where 何地
When 何时
2.用“ECRS”或“四巧”技术——改进流程(P183)
3.从备选方法或方案中选优
11
四.流程的时间分析
1.流程时间的构成 2.流程时间的计算和制订 (1)某工序平均生产时间(生产周期)的计算
单件小批生产 成批生产 大量生产 (2)制订生产时间标准的方法 制订同意的辅助生产时间标准 制订不同的辅助生产时间宽放系数
白线:距离为1
料
铣
红线:距离≥2
料—车:1×2=2;车—铣:1×3=3
钻
刨
铣—车:1×2=2;铣—检:1×1=1
移动距离=标准基数+合计超出单位
车
检
=18+8 =26(标准单位)
8
现重新多行排列如下:
料
车
移动距离
=18+0
铣
刨
=18 (标准单位)
钻
检
9
第六章 生产过程的流程分析
生产流程——生产对象从原材料起至最后转换成为成
3
四.设备位置的排列
1.设备单行排列 ——交接表法(交叉表、从至图)
例:某金加工车间,加工ABCD四种零件,所需设备(工 作地)单行排为:料库—铣床—钻床—刨床—车床—检验, 各零件加工工艺路线如下: A: 料—刨—铣—检 B: 料—车—铣—刨—检 C: 料—铣—车—刨—钻—检 D: 料—车—铣—车—铣—钻—检
6
至 从
料车铣刨钻检
∑
料
211
4
车
31
4
铣
2
1115
刨
1
第三章 生产系统的合理布置22页PPT
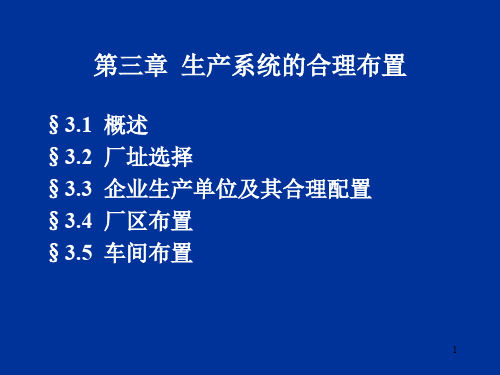
8
§3.3企业生产单位及其合理 配置
一 影响企业生产单位构成的因素 二 典型制造企业的生产单位 三 企业生产单位合理配置的原则
9
一 影响企业生产单位构成的因素
生产单位:企业中包含一定生产力要素, 实现一定功能并占据一定空间 位置的子系统即为生产单位。
1 产品:产品品种、结构特点、工艺特点 与生产规模
17
一 车间布置
所谓车间布置就是按一定的原则、 正确地确定车间内部各组成单位(工段、 班组)及工作地,设备机床之间的相互 位置,从而使它能组成一个有机整体, 实现车间的具体功能和任务。
18
二 车间总体布置
1 基本生产部分 2 辅助生产部分 3 仓库部分 4 过道部分 5 车间管理部分 6 生活福利部分
20 12 19750
址 乙
414000 260000 154000 20000
20 13 22000
6
厂址选择(分级加权法)
影响因素
地理条件 气候 交通运输 资源 能源供应 水源 排水 扩展余地 环境保护 安全 生活条件 协作 劳动力来源 产品销售 料场 投资费用 总计
权数
可供选择的厂址
甲
乙
丙
丁
19
三 工作地布置的类型及原则
类型:1 工艺专业化布置 2 对象专业化布置 3 定位布置 4 成组单元布置
原则:1 符合生产过程流向 2 便于运输 3 创造安全、良好的工作环境 4 便于工人操作和工作地(工具、图纸、工位器具) 的布置 5 充分利用车间面积 6 充分考虑机床精度和工作特点
20
四 工作地(设备)布置的技术和方法
2 企业规模:规模∝生产单位数量、大小 3 生产专业化水平和协作化水平 4 企业的生产技术水平 5 企业的环境条件
- 1、下载文档前请自行甄别文档内容的完整性,平台不提供额外的编辑、内容补充、找答案等附加服务。
- 2、"仅部分预览"的文档,不可在线预览部分如存在完整性等问题,可反馈申请退款(可完整预览的文档不适用该条件!)。
- 3、如文档侵犯您的权益,请联系客服反馈,我们会尽快为您处理(人工客服工作时间:9:00-18:30)。
生产单元布局
HEN system office room 【HEN16H-HENS2AHENS8Q8-HENH1688】
工艺专业化布局和产品专业化布局
1. 机群式布置,这个概念与厂区布置的工艺专业化是相同的,只是工艺的概念更小一些,指把同种类型的设备和人员集中布置在一个地方。
这种布置方式常常用于用同样的设备来制造和装配各种不同的部件。
比较是用于品种多产量小的生产类型。
其特点是:同类设备集中,加工技术单一,生产系统柔性大;加工对象多,工艺路线差别大,物料搬运有交叉,难以使工件搬动自动化;在各工序之间成批搬运,加工周期长;周转环节多,不易管理。
车间门
计划管理简单,生产易控制;但加工线应变能力差,缺乏柔性。
2. 工件加工中的运送路线要短;
3. 车间内要留出足够的通到面积,通道要直;
4. 充分保证生产用面积,提高利用率;
5. 设备布置要保证安全。
传统生产线的弊端
直线型生产线的生产方式下,人员在一个周期内的来回时间及行走距离较多,如图2 所示。
某个单元生产周期不能够得到合理限制造成整个系统的周期过长,产品成本增加,如局部环节出现问题会影响整个生产线的连续性,形成在制品堆积的严重现象。
面向产品族的“制造单元”
制造单元是以柔性设备为核心的若干台设备的组合,将这些设备按照每一个产品“族”相类同的工艺顺序排列,在制造单元内完成制造这些产品/零件族的全部过程。
制造单元不是针对每一个零件的,这样就不是精益制造了。
制造单元起码有以下几个特征和功能:
a)面向一个“产品/零件族”。
“族”是一组形状和制造过程相同或相似
的零件。
因而精益的制造单元是柔性的,大大地减少了由于换型造成的
生产停滞。
b)
c)制造单元内的设备顺序是按工艺流程排列的,考虑到零件进出单元方向
的一致性,经常排列成U形,所以又称其为U形单元,从而保证了 >物
流的流程距离最短,而消除了多种形式的浪费。
d)
e)工件在制造单元中按流程顺序自然流转,从而简化了管理,节省了信息
的传递和信息流距离。
f)制造单元内的工人是多能的,单元团队的成员之间是相互支持和相互替
代的,使更加发挥工人和团队的积极性,
g)所以建立制造单元是实行精益生产的关键步骤之一。
单元生产模式是一种基于追求无浪费理念,以工作单元(机械设备、生产人员和在制品
的物流系统)为基本组成,对生产线合理布置,进行单一或多品种的生产方式。
单元式生产
可根据人员配备情况将生产线分为单人、多人循环类型,即U 型布置。
单元生产方式的基本目的就是消除浪费,该生产模式主要消除七大浪费中的搬运浪费、等待浪费、生产线平衡浪费。
同时可有效的降低生产成本,提高质量及工作效率,增强系的柔性能力
通常单元式生产线采用U 型或C 型生产线的模式,在这种生产线模式中设备和工作地点按照流程步骤的顺序紧密配置,这样能够减少不必要的人员走动和物料的搬运时间,使得生产线的运行更加顺畅,U 型生产线的最大特征就是实现生产线的平衡,该生产线为了减少工作人员由于生产线布局不当所造成的行走时间浪费现象,把生产的投入点,即原材料的放置点与半成品或成品的产出点的位置,尽可能的缩短其二者间距离,叫做“IO 一致”原则
构建制造单元需要有以下技术的支持:
利用成组技术(Group?Technology)的相似性原则,将产品和零件分成为若干“族”。
在这个过程中,采用成组技术分类编码是必要的。
但是很多企业径直采用目测和经验的方法分类,也取得可行的效果。
利用工艺和聚类分析等方法形成与零件族工艺设备相对应的设备组。
这个过程可以凭经验完成,最好用专业的应用软件实现。
绘制产品族的价值流图(valuestreammapping)。
价值流图是借鉴日本的经验在美国广泛应用的一种识别浪费的方法。
利用价值流图分析现行过程存在的过程停滞和浪费,计算不增值过程所占用的过程时间。
按照分析结果重新设计。
在车间现场按经过优化的族的工艺流程布置设备组,形成U形或直线的生产单元。
不断的进行工艺路线的改进和优化,不断的进行制造单元设备类型和位置的调整。
将工程技术人员的办公桌安放在各个制造单元的中央,加快对现场问题的反应速度
为了方便的构建和调整制造单元,布置精益制造单元的厂房采用整体地基,准备在任何地方安置设备,而设备也放在简易的可移动拖架上,多数并不与地面固定。
在美国和的许多实践打消了关于设备精度、和寿命的所有疑虑。
水、电、气的管道从设备上空下来。
设备的位置排列:
1. 单行排列:例:某金加工车间,加工ABCD四种零件,所需设备(工作地)单行排为:料库—铣床—钻床—刨床—车床—检验,各零件加工工艺路线如下:
A: 料—刨—铣—检
B: 料—车—铣—刨—检
C: 料—铣—车—刨—钻—检
D: 料—车—铣—车—铣—钻—检
2. 设备的多行排列:
柔性化的设备
,实现精益制造的设备是便于更换或调整的柔性化设备。
在柔性设备上,更换产品只需要很少的时间,以至于可以大大地降低所谓“经济规模”的阈值。
各种数控设备,特别是数控加工中心和柔性制造系统FMS是拉式生产系统首选的柔性设备。
注意首推数控设备并不是由于它们是“自动化”
的,而是看中了它们“柔性化”的特征。
用普通的设备加式的快速换装的模具系统、或在前苏联过的成组夹具或组合夹具,也是效果很好的柔性化设备方案。
相反,刚性自动化设备最能体现大量生产方式的优势,但用他们进行精益的小批量甚至单件流生产、而又企图获得高效率和低成本是不可能的。
因而,在向精益企业转变过程中,体积庞大而不易搬动、需要按批量作业的“超大设备”成为新的浪费而失去它的生命力。
在国内外进行精益企业改造过程中,并没有一开始就进行大规模设备更新的。
但是必须不断地进行制造技术的改进,用新的柔性自动化的设备替代普通的通用设备,逐渐形成出面向“大规模定制生产”的敏捷制造环境。