基于工业4.0的轴承合套机械系统设计
YE254-【课设】轴承套加工工艺及钻Φ4孔专用夹具设计【外径42,长40】说明书改
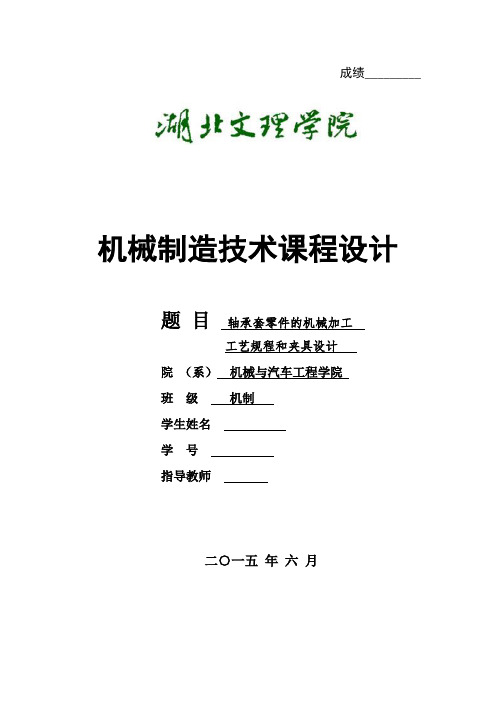
成绩_________机械制造技术课程设计题目轴承套零件的机械加工工艺规程和夹具设计院(系)机械与汽车工程学院班级机制学生姓名学号指导教师二○一五年六月轴承套零件的机械加工工艺规程和夹具设计摘要:本设计是基于轴承套零件的加工工艺规程及一些工序的专用夹具设计。
轴承套零件的主要加工表面是外圆及孔系。
一般来说,保证平面的加工精度要比保证孔系的加工精度容易。
因此,本设计遵循先面后孔的原则。
并将孔与平面的加工明确划分成粗加工和精加工阶段以保证孔系加工精度。
主要加工工序安排是先以孔系定位加工出平面,在后续工序中除个别工序外均用顶平面和工艺孔定位加工其他孔系与平面。
夹具选用专用夹具,夹紧方式多选用手动夹紧,夹紧可靠,机构可以不必自锁。
因此生产效率较高。
适用于大批量、流水线上加工。
能够满足设计要求。
关键词:轴承套类零件,加工工艺,专用夹具,设计目录第一章零件的分析 (4)1.1零件的作用 (4)1.2 零件的工艺分析 (4)1.3零件生产类型的选择 (5)第二章确定毛坯类型绘制毛坯简图 (7)2.1 选择毛坯 (7)2.2 确定毛坯的尺寸公差和加工余量 (7)2.3 绘制毛坯-零件合图 (7)第三章工艺过程设计 (9)3.1定位基准的选择 (9)3.2零件各表面加工方法的选择 (9)3.3加工阶段的划分 (10)3.4工序顺序安排 (11)3.5 热处理工序及辅助工序的安排 (11)3.6确定总的工艺路线 (12)3.7工艺装备的选择 (13)第四章精车φ22H7内孔和φ42左端面机械加工工序设计 (15)4.1 工序简图的绘制 (15)4.2工序余量的确定 (15)4.3工序尺寸的确定 (16)4.4切削用量的确定 (16)4.5时间定额估算 (18)第五章钻φ4孔专用夹具设计 (19)5.1 夹具设计任务 (19)5.2 拟订夹具结构方案与绘制夹具草图 (19)5.3 绘制夹具装配总图 (19)5.4 夹具装配图上标注尺寸、配合和技术要求 (20)5.5 夹具专用零件图设计绘制 (21)总结 (22)致谢 (23)参考文献 (24)第一章零件的分析1.1零件的作用题目给出的零件是轴承套。
轴承套工艺设计说明书-第5组标准版
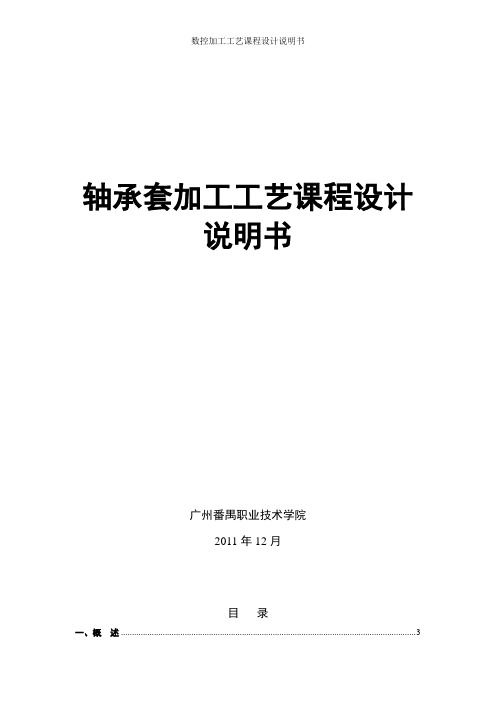
轴承套加工工艺课程设计说明书广州番禺职业技术学院2011年12月目录一、概述 (3)二、零件工艺分析 (5)三、确定毛坯 (6)轴承套的工艺路线如下:下料→车两端面→粗车各外圆→精车各外圆,车槽,倒角→检验77.1 工序设计 (11)7.2 机床选择 (11)参考文献 (14)一、概述套筒类零件的加工工艺根据其功用、结构形状、材料和热处理以及尺寸大小的不同而异。
就其结构形状来划分,大体可以分为短套筒和长套筒两大类。
一般套筒类零件在机械加工中的主要工艺问题是保证内外圆的相互位置精度(即保证内、外圆表面的同轴度以及轴线与端面的垂直度要求)和防止变形。
套筒类零件的外圆表面多以过盈或过渡配合与机架或箱体孔相配合起支承作用。
内孔主要起导向作用或支承作用,常与运动轴、主轴、活塞、滑阀相配合。
有些套筒的端面或凸缘端面有定位或承受载荷的作用。
套筒类零件虽然形状结构不一,但仍有共同特点和技术要求,根据使用情况可对套筒类零件的外圆与内孔提出如下要求1)内孔与外圆的精度要求外圆直径精度通常为IT5~IT7,表面粗糙度Ra 为5~0.63um,要求较高的可达0.04 um;内孔作为套类零件支承或导向的主要表面,要求内孔尺寸精度一般为IT6~117,为保证其耐磨性要求,对表面粗糙度要求较高(Ra=2.5~0.16 um)。
有的精密套筒及阀套的内孔尺寸精度要求为IT4~II5,也有的套筒(如油缸、气缸缸筒)由于与其相配的活塞上有密封圈,故对尺寸精度要求较低,一般为II'8—ITc),但对表面粗糙度要求较高,Ra一般为2.5~1.6um。
2)几何形状精度要求通常将外圆与内孔的几何形状精度控制在直径公差以内即可;对精密轴套有时控制在孔径公差的1/2~1/3,甚至更严。
对较长套筒除圆度有要求以外,还应有孔的圆柱度要求。
为提高耐磨性,有的内孔表面粗糙度要求为Ral.6-0.1 um,有的高达Ra0.025um。
套筒类零件外圆形状精度一般应在外径公差内,表面粗糙度Ra为3.2~0.4um。
轴承套课程设计说明书

湖南铁道职业技术学院课程设计说明书设计题目:设计“轴承套”零件的机械加工工艺规程班别:数控加工111设计者:李孝伟指导教师:刘慎玖评定成绩:设计日期 2013年4月20日至4月26日目录设计任务书课程设计说明书正文序言一、零件的分析............................................................... (4)(一)零件的作用 (4)(二)零件的工艺分析 (4)二、工艺规程设计 (5)(一)确定毛坯的制造形式 (5)(二)基面的选择 (5)(三)工艺路线的拟定 (5)(四)机械加工余量、工序尺寸及毛坯尺寸的确定 (8)(五)确定切削用量及基本工时 (9)三、课程设计心得体会 (13)四、结束语 (14)五、参考文献 (15)设计任务书湖南铁道职业技术学院机械制造工艺学课程设计任务书设计题目:设计“轴承套”零件的机械加工工艺规程及工艺装置(生产纲领:100件)设计内容:1.产品零件图 1张2.产品毛坯图 1张3.机械加工工艺过程卡 1份4.机械加工工序卡片 1套5.课程设计说明书 1份班别:数控加工111设计者:李孝伟指导教师:刘慎玖2013 年 4 月 26 日课程设计说明书正文序言机械制造工艺学课程设计是在我们学完了大学的全部基础课、技术基础课以及大部分专业课之后进行的。
这是我们在进行毕业设计之前对所学各课程的一次深入的综合性的链接,也是一次理论联系实际的训练。
因此,它在我们的大学学习生活中占有十分重要的地位。
就我个人而言,我希望能通过这次课程设计对自己未来将从事的工作进行一次适应性训练,从中锻炼自己分析问题、解决问题的能力,为今后参加国家的现代化建设打下一个良好的基础。
由于能力所限,设计尚有许多不足之处,恳请各位老师给予指教。
一、零件的分析(一)零件的功用及结构分析轴承套广泛应用于轻负荷便于拆装的地方,有许多轴承在装配和拆卸中会遇到困难,特别在箱体内部轴承的装配受到条件限制,应用轴承套解决了装配和拆卸的难题。
典型机械零件数控加工项目教程(第2版)课件:轴承套的加工与调试
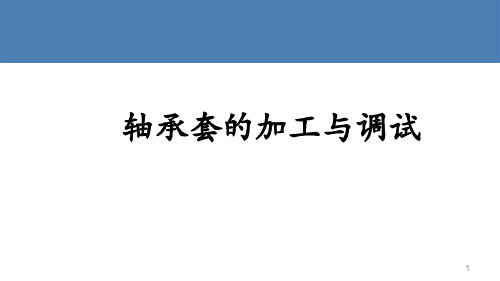
最大回转直径 最大加工长度 定位精度 刀位数 刀杆规格
360 500 0.005 4 20*20
装夹方式
装夹要求 定位:确定零件在机床中的位置 夹紧:保证加工时零件不产生位移
装夹时伸出长度怎么来确定? 在满足加工要求前提下,约短越好。 零件总长+切断刀宽度+8
右端加工装夹方式 三爪卡盘装夹 优点:装夹方便、可靠 缺点:容易在表面夹出痕迹
孔径小于刀杆直径+退刀 量,退刀时,发生碰撞
四、内孔车刀退刀时撞工件
可能出现的问题
处理方法
从第二个加工件起,减 小退刀量,或者选择直径 略小的刀杆
第二个起加内 孔退刀量
五、内孔出现锥度
问题描述
零件Φ30内孔前后尺寸不一 致,外端尺寸较大
问题分析
刀杆安装倾斜,没有保证刀尖在最前面。 刀杆刚性差或伸出长度过大,出现让刀现象。 垫刀片伸出太长。
参数选择
内孔车刀的刚性相对 外圆较差,故内孔的 切削参数小于外圆的 用量
刀具选择
工序 刀号
刀杆规格
刀片规格
T01
加工 T02
右端
CNMG090408-PR DCLNL2020M09
CCMT090404-PF
T03 C6-RF20-45065B N2-0300-0001-CF
加工
T01
左端
DCLNL2020M09 CNMG090408-PR
加工内 转速 切深 容 (r/min) (mm)
进给 (mm/
r)
粗车 1600 2.5 0.25
精车
切断 切槽
2500 1000
0.5 0.15 0.15
精车 2500 0.5 0.15
轴承套加工工艺设计规程与油孔夹具工艺设计工序卡片
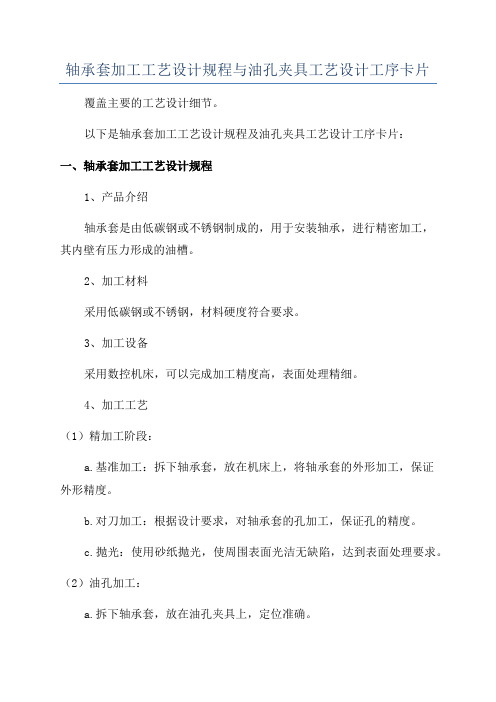
轴承套加工工艺设计规程与油孔夹具工艺设计工序卡片覆盖主要的工艺设计细节。
以下是轴承套加工工艺设计规程及油孔夹具工艺设计工序卡片:
一、轴承套加工工艺设计规程
1、产品介绍
轴承套是由低碳钢或不锈钢制成的,用于安装轴承,进行精密加工,
其内壁有压力形成的油槽。
2、加工材料
采用低碳钢或不锈钢,材料硬度符合要求。
3、加工设备
采用数控机床,可以完成加工精度高,表面处理精细。
4、加工工艺
(1)精加工阶段:
a.基准加工:拆下轴承套,放在机床上,将轴承套的外形加工,保证
外形精度。
b.对刀加工:根据设计要求,对轴承套的孔加工,保证孔的精度。
c.抛光:使用砂纸抛光,使周围表面光洁无缺陷,达到表面处理要求。
(2)油孔加工:
a.拆下轴承套,放在油孔夹具上,定位准确。
b.进行铣削,完成油孔加工,保证油孔的精度。
c.抛光:使用砂纸抛光,使油孔表面光洁无缺陷,达到表面处理要求。
(3)清洗:
a.使用清洗液,将加工过的轴承套进行清洗,清除残留的油脂和污垢。
b.使用空气吹扫,将清洗出来的污垢和气体吹除。
1、工序卡片介绍。
轴承座(1)4×M5螺纹底孔加工专机总体结构、夹具及其液压系统设计
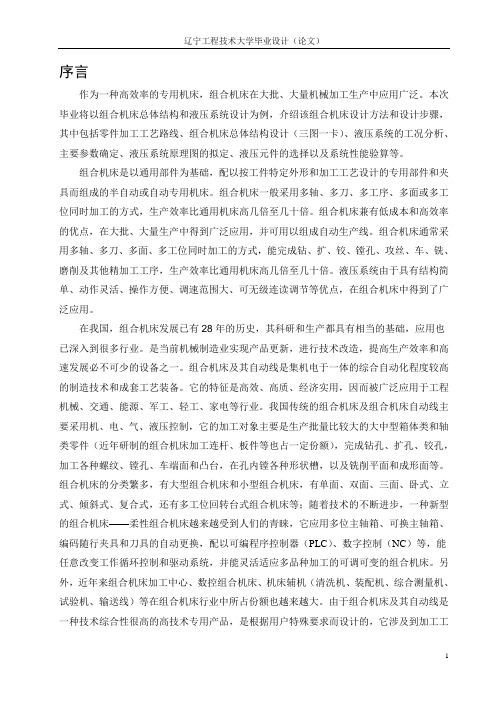
序言作为一种高效率的专用机床,组合机床在大批、大量机械加工生产中应用广泛。
本次毕业将以组合机床总体结构和液压系统设计为例,介绍该组合机床设计方法和设计步骤,其中包括零件加工工艺路线、组合机床总体结构设计(三图一卡)、液压系统的工况分析、主要参数确定、液压系统原理图的拟定、液压元件的选择以及系统性能验算等。
组合机床是以通用部件为基础,配以按工件特定外形和加工工艺设计的专用部件和夹具而组成的半自动或自动专用机床。
组合机床一般采用多轴、多刀、多工序、多面或多工位同时加工的方式,生产效率比通用机床高几倍至几十倍。
组合机床兼有低成本和高效率的优点,在大批、大量生产中得到广泛应用,并可用以组成自动生产线。
组合机床通常采用多轴、多刀、多面、多工位同时加工的方式,能完成钻、扩、铰、镗孔、攻丝、车、铣、磨削及其他精加工工序,生产效率比通用机床高几倍至几十倍。
液压系统由于具有结构简单、动作灵活、操作方便、调速范围大、可无级连读调节等优点,在组合机床中得到了广泛应用。
在我国,组合机床发展已有28年的历史,其科研和生产都具有相当的基础,应用也已深入到很多行业。
是当前机械制造业实现产品更新,进行技术改造,提高生产效率和高速发展必不可少的设备之一。
组合机床及其自动线是集机电于一体的综合自动化程度较高的制造技术和成套工艺装备。
它的特征是高效、高质、经济实用,因而被广泛应用于工程机械、交通、能源、军工、轻工、家电等行业。
我国传统的组合机床及组合机床自动线主要采用机、电、气、液压控制,它的加工对象主要是生产批量比较大的大中型箱体类和轴类零件(近年研制的组合机床加工连杆、板件等也占一定份额),完成钻孔、扩孔、铰孔,加工各种螺纹、镗孔、车端面和凸台,在孔内镗各种形状槽,以及铣削平面和成形面等。
组合机床的分类繁多,有大型组合机床和小型组合机床,有单面、双面、三面、卧式、立式、倾斜式、复合式,还有多工位回转台式组合机床等;随着技术的不断进步,一种新型的组合机床——柔性组合机床越来越受到人们的青睐,它应用多位主轴箱、可换主轴箱、编码随行夹具和刀具的自动更换,配以可编程序控制器(PLC)、数字控制(NC)等,能任意改变工作循环控制和驱动系统,并能灵活适应多品种加工的可调可变的组合机床。
轴承套的加工设计
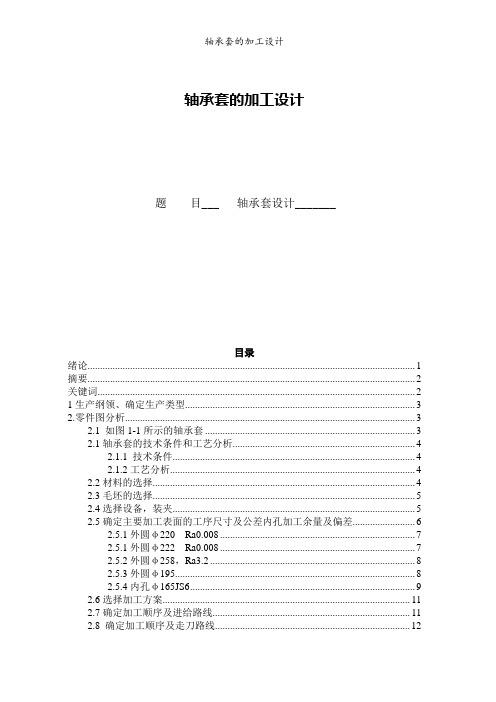
轴承套的加工设计题目___ 轴承套设计_______目录绪论 (1)摘要 (2)关键词 (2)1生产纲领、确定生产类型 (3)2.零件图分析 (3)2.1 如图1-1所示的轴承套 (3)2.1轴承套的技术条件和工艺分析 (4)2.1.1 技术条件 (4)2.1.2工艺分析 (4)2.2材料的选择 (4)2.3毛坯的选择 (5)2.4选择设备,装夹 (5)2.5确定主要加工表面的工序尺寸及公差内孔加工余量及偏差 (6)2.5.1外圆φ220 Ra0.008 (7)2.5.1外圆φ222 Ra0.008 (7)2.5.2外圆φ258,Ra3.2 (8)2.5.3外圆φ195 (8)2.5.4内孔φ165JS6 (9)2.6选择加工方案 (11)2.7确定加工顺序及进给路线 (11)2.8 确定加工顺序及走刀路线 (12)2.9切削用量的选择 (12)3拟定精密轴承套加工工艺过程卡片 (13)3.1确定工件原点 (13)3.2 精密轴承套加工工艺过程卡片 (13)3.3编写加工程序及说明 (16)总结............................................................................................... 错误!未定义书签。
致谢................................................................................................. 错误!未定义书签。
参考文献. (21)绪论机械制造业的竞争,其实就是数控技术的竞争,这种竞争是全方位的。
目前,随着国内数控机床用量的剧增,特别是随着高刚度整体铸造床伸、高速运算数控系统和主轴运平衡等新技术的采用以及刀具材料的不断发展,现代切削加工朝着高速、高精度和强力切削方向发展。
数控技术是制造业实现自动化、柔性化、集成化生产的基础,数控技术的应用是提高制造业产品质量和劳动生产率必不可少的重要手段。
轴承衬套自动化装配机的设计
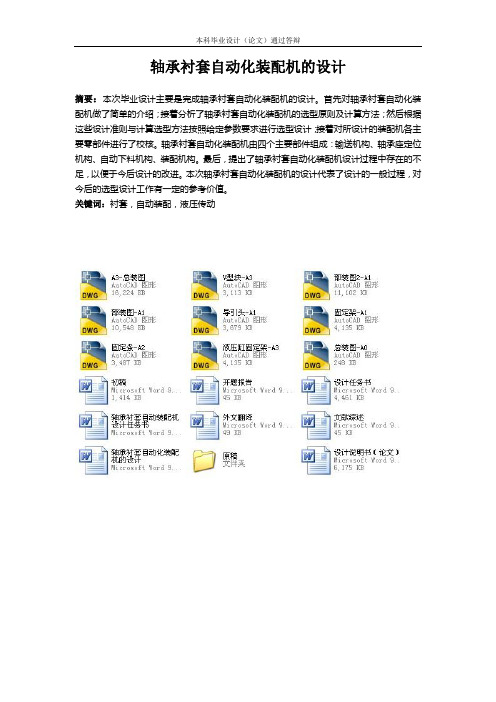
轴承衬套自动化装配机的设计摘要:本次毕业设计主要是完成轴承衬套自动化装配机的设计。
首先对轴承衬套自动化装配机做了简单的介绍;接着分析了轴承衬套自动化装配机的选型原则及计算方法;然后根据这些设计准则与计算选型方法按照给定参数要求进行选型设计;接着对所设计的装配机各主要零部件进行了校核。
轴承衬套自动化装配机由四个主要部件组成:输送机构、轴承座定位机构、自动下料机构、装配机构。
最后,提出了轴承衬套自动化装配机设计过程中存在的不足,以便于今后设计的改进。
本次轴承衬套自动化装配机的设计代表了设计的一般过程,对今后的选型设计工作有一定的参考价值。
关键词:衬套,自动装配,液压传动Bearing Bush Automated Assembly Machine DesignAbstract: The design is completed for graduation bearing bush automated assembly machine design. Firstly, bearing bush automated assembly machine is introduced. Secondly, the bearing bush automated assembly machine selection principle and method of calculation are analyzed. Then calculation based on these design criteria and selection method of parameters in accordance with the requirements of a given type design are done. Then designed machine on the main components are checked. Bearing bush automated assembly machine consists of four main components: transport sector, bearing positioning mechanism, automatic unloading mechanism, assembly body. Finally, the deficiencies of the bearing bush automated assembly machine design process proposed, in order to facilitate the future design improvements. The bearing bushing design of automated assembly machine represents of the general process of design, selection of design work on the future of some reference value.Key words: bush, auto assembly, hydraulic transmission目录第一章绪论 (1)1.1设计解决的问题 (1)1.2设计时注意的问题 (1)1.2.1 具有足够的推力(即推出力) (1)1.2.2 保证工件准确定位 (1)1.2.3 具有足够的强度和刚度 (1)第二章轴承衬套自动化装配机的概述 (2)2.1轴承衬套自动化装配机的应用 (2)2.2轴承衬套自动化装配机的特点 (2)2.3轴承衬套自动化装配机的发展状况 (2)2.4轴承衬套自动化装配机的工作原理 (3)第三章总体方案的确定 (4)3.1设计内容 (4)3.1.1设计任务 (4)3.1.2设计要求 (4)3.2设计方案的构想 (4)第四章总体方案的设计计算 (6)4.1衬套装配摩擦力计算 (6)4.2 预设导引缸型号及推力 (7)4.2.1 液压缸安装方式选择 (7)4.2.2 导引缸选型 (7)4.3 顶出缸的推力计算及选型 (8)4.4 夹紧缸推力计算及型号选用 (8)4.5 驱动缸推力计算及型号选用 (8)4.5.1 计算驱动缸的推力 (8)4.5.2 驱动缸的选择 (10)4.6 分配器缸推力计算及型号选用 (10)第五章刚度和强度校核 (11)5.1 销轴强度校核 (11)5.2 活塞杆稳定性校核 (11)5.3 支架强度校核 (12)第六章液压系统的设计 (14)6.1 设计要求 (14)6.1.1 设备工况及要求 (14)6.1.2 设备工作程序 (14)6.1.3 控制与连续要求 (14)6.1.4 执行元件工艺参数 (14)6.1.5 工作循环时间顺序图 (14)6.2 系统方案设计 (15)6.2.1 确定回路方式 (15)6.2.2 确定系统工作压力 (15)6.2.3 液压泵类型的确定 (15)6.3 液压元件的计算与选择 (15)6.3.1 主要液压元件的计算与选择 (15)6.3.1.1 液压缸的性能参数计算 (15)6.3.1.2 液压泵的性能参数计算 (15)6.3.1.3 电动机的选择 (16)6.3.1.4 电磁换向阀的选择 (16)6.3.1.5 溢流阀的选择 (16)6.3.1.6 单向阀的选择 (16)6.3.1.7 单向节流阀的选择 (17)6.3.2 液压辅助元件的选择与计算 (17)6.3.2.1 油管的选择 (17)6.3.2.2 过滤器的选择 (17)6.3.2.3 压力表的选择 (17)6.3.2.4 油箱容积的计算 (17)6.4 拟定液压原理图 (18)6.5 液压控制系统的分析 (18)6.5.1 液压系统动作顺序表 (19)6.5.2 系统工作过程 (19)6.5.3 PLC控制命令 (19)第七章结论 (21)7.1 设计的主要成果 (21)7.2 存在的主要问题 (21)7.3 进一步研究的建议 (21)参考文献 (22)致谢 (23)附录图纸列表 (24)第一章 绪论随着社会的发展和技术的进步,衬套材质及其装配方式有了明显的变化和改进。
中小型圆锥滚子轴承套圈套塔复合锻造
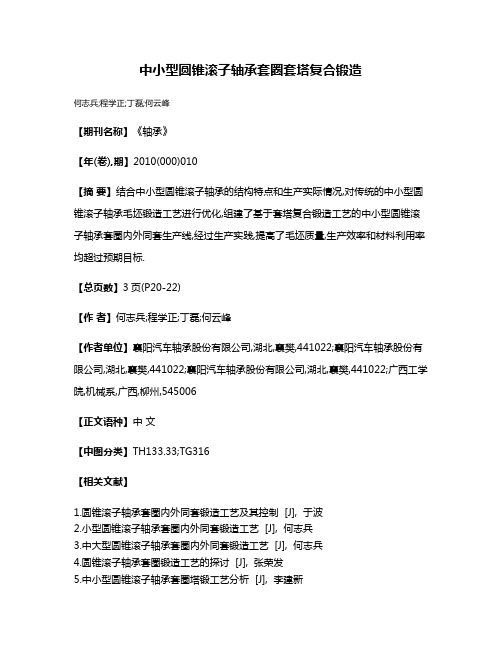
中小型圆锥滚子轴承套圈套塔复合锻造
何志兵;程学正;丁磊;何云峰
【期刊名称】《轴承》
【年(卷),期】2010(000)010
【摘要】结合中小型圆锥滚子轴承的结构特点和生产实际情况,对传统的中小型圆锥滚子轴承毛坯锻造工艺进行优化,组建了基于套塔复合锻造工艺的中小型圆锥滚子轴承套圈内外同套生产线,经过生产实践,提高了毛坯质量,生产效率和材料利用率均超过预期目标.
【总页数】3页(P20-22)
【作者】何志兵;程学正;丁磊;何云峰
【作者单位】襄阳汽车轴承股份有限公司,湖北,襄樊,441022;襄阳汽车轴承股份有限公司,湖北,襄樊,441022;襄阳汽车轴承股份有限公司,湖北,襄樊,441022;广西工学院,机械系,广西,柳州,545006
【正文语种】中文
【中图分类】TH133.33;TG316
【相关文献】
1.圆锥滚子轴承套圈内外同套锻造工艺及其控制 [J], 于波
2.小型圆锥滚子轴承套圈内外同套锻造工艺 [J], 何志兵
3.中大型圆锥滚子轴承套圈内外同套锻造工艺 [J], 何志兵
4.圆锥滚子轴承套圈锻造工艺的探讨 [J], 张荣发
5.中小型圆锥滚子轴承套圈塔锻工艺分析 [J], 李建新
因版权原因,仅展示原文概要,查看原文内容请购买。
(整理)全自动深沟球轴承装配机结构设计毕业设计

摘要:本设计是综合深沟球轴承装配的各个步骤,根据现代机械自动化控制原理而设计的。
是一台针对深沟球轴承的综合装配机械,能够实现深沟球轴承从外环、内环、钢珠的单体到轴承装配体的步骤。
解决了由于手工装配带来的诸如清洁度、装配精度和锈蚀等许多问题。
本机械大量的运用了PLC控制液压气压元件实现运动,机构较为复杂。
本设计是只针对机械结构部分的设计,主要由以下几部分组成:1.入钢珠装置;2分钢珠装置;3入保持器及保持器组合装置;4铆接装置;5铆接检测装置;6轴承传送装置。
关键词:入钢珠分钢珠保持器检测装置传送装置Abstract:This design is compeleted by synthesizing each process of assembling the deep groove ball bearing and by following the modern mechanical automation control theory.It is one integrated assembling machine specially for deep groove ball bearing, and it can carry out all the process of the deep groove ball bearing, from the monomer like the outer ring, the inner rim and the steel ball to the assembled bearing.It solves many problems, such as the cleanliness, the assembly precision and the corrosion which is caused by manual setting.This machine utilizes massive PLC controlled hydraulic and barometric pressure parts to achieve movement,thus the framework is much more complex..This design is only for the mechanical part and is mainly composed by the following several parts:1.the steel ball entering installment;2.the steel ball separating equipment;3.the retainer entering and retainer aggregate unit;4.the riveting device;5.the riveting detector set;6.the bearing transport unit.Key Words:Steel ball entering; Steel ball separating; Retainer; Detector set; Transport unit毕业设计(论文)原创性声明和使用授权说明原创性声明本人郑重承诺:所呈交的毕业设计(论文),是我个人在指导教师的指导下进行的研究工作及取得的成果。
“工业4.0”背景下的自动化制造技术-最新文档
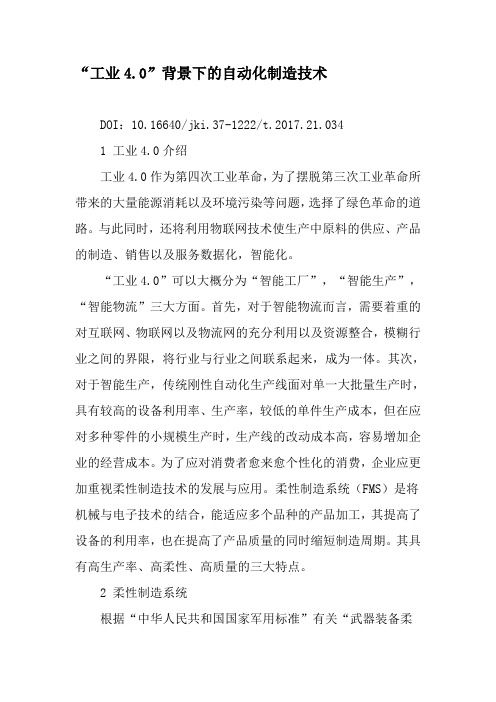
“工业4.0”背景下的自动化制造技术DOI:10.16640/jki.37-1222/t.2017.21.0341 工业4.0介绍工业4.0作为第四次工业革命,为了摆脱第三次工业革命所带来的大量能源消耗以及环境污染等问题,选择了绿色革命的道路。
与此同时,还将利用物联网技术使生产中原料的供应、产品的制造、销售以及服务数据化,智能化。
“工业4.0”可以大概分为“智能工厂”,“智能生产”,“智能物流”三大方面。
首先,对于智能物流而言,需要着重的对互联网、物联网以及物流网的充分利用以及资源整合,模糊行业之间的界限,将行业与行业之间联系起来,成为一体。
其次,对于智能生产,传统刚性自动化生产线面对单一大批量生产时,具有较高的设备利用率、生产率,较低的单件生产成本,但在应对多种零件的小规模生产时,生产线的改动成本高,容易增加企业的经营成本。
为了应对消费者愈来愈个性化的消费,企业应更加重视柔性制造技术的发展与应用。
柔性制造系统(FMS)是将机械与电子技术的结合,能适应多个品种的产品加工,其提高了设备的利用率,也在提高了产品质量的同时缩短制造周期。
其具有高生产率、高柔性、高质量的三大特点。
2 柔性制造系统根据“中华人民共和国国家军用标准”有关“武器装备柔性制造系统术语”的定义,柔性制造系统是?悼丶庸ど璞浮⑽锪洗⒃俗爸煤图扑慊?控制系统组成的自动化制造系统,并包括多个柔性制造单元(FMC),能够根据制造任务或者环境变化迅速的做出调整。
,适用于多品种、中小批量的生产。
柔性制造系统的主要目的一是为了解决机械制造生产技术灵活性的问题二是为了提高产品的质量。
三是为了缩短周期。
为了适应市场需求,柔性制造系统的发展方向应大致分为以下四点:(1)积极开发经济型的FMS。
企业追求的是效益,在遇到需要企业的升级换代时,较高的成本容易使得企业在面对升级设备上出现犹豫不决的情况,这容易导致企业在市场竞争中处于劣势。
(2)发展更高效的FMC。
汽车轴承端盖组合机床的设计

第1章汽车主轴轴承盖机加工艺全套图纸请加:2298262081.1确定生产纲领、生产类型、工艺特征首先要分析、被加工零件,通过认真阅读被加工零件图样,研究被加工零件的用途,尺寸、形状、材料、硬度、重量,加工部位的结构和加工精度及表面粗糙度要求等内容。
通过对产品装配图样和有关工艺资料的分析,充分认识被加工零件在产品中的地位和作用,从而来确定机车轴承盖的机械加工工艺,使它保证各种加工要求和经济精度。
1、由N=3000~4000件/年,知道了零件的生产纲领。
2、生产类型的确定——为大批量生产。
3、该工件的工艺特性。
针对工件的结构形状及正常的经济精度和位置精度的分析可知结构工艺性十分复杂。
而且工件是大批量生产,可采用高效专用机床及自动化生产线进行生产,可以广泛采用高效专用夹具、复合刀具、专用量具及自动检查装置(按流水线、自动线排列设备),因此在实际加工中我们采用组合机床进行加工。
这样容易保证加工精度,提高生产率,使产品成本相对降低,提高产品的经济效益。
1.2确定毛坯及材料的选择1.2.1确定毛坯及材料的选择(1) 查阅零件图和技术要求及机构工艺性可知此工件采用42CrMo材料,根据零件加工工艺性及零件尺寸精度,我们在选择毛坯的加工方法时要综合分析零件的轮廓,尺寸精度、形状、位置、加工表面技术要求,最终确定了采用模锻件来制造毛坯,精度等级为2级。
分析零件的材料特征,查《机械制造设计手册》退火/回火硬度—HB217,而零件的技术要求硬度为HB241—258,则要对零件进行调质处理。
(2) 确定零件毛坯尺寸查工艺手册毛坯尺寸 L=440+2X3.25 B=235+2X3.25 H=92+2X2而半圆环槽(表1—53)按锻件确定R=115+2.75(3) 材料的重量计算查零件的比重7.75g/m3M=446.5X96X241.5X7.75=78㎏由此确定毛坯的技术要求1)锻件无明显裂纹缺陷2)未注圆角R3~R53)零件硬度HB241~2851.2.2确定工艺路线(1)根据零件结构工艺性和经济精度,按照粗精加工分开原则,工序集中原则,来确定机械加工工序的安排顺序。
轴承套机械加工工-轴承套加工工艺及钻Φ8孔夹具设计
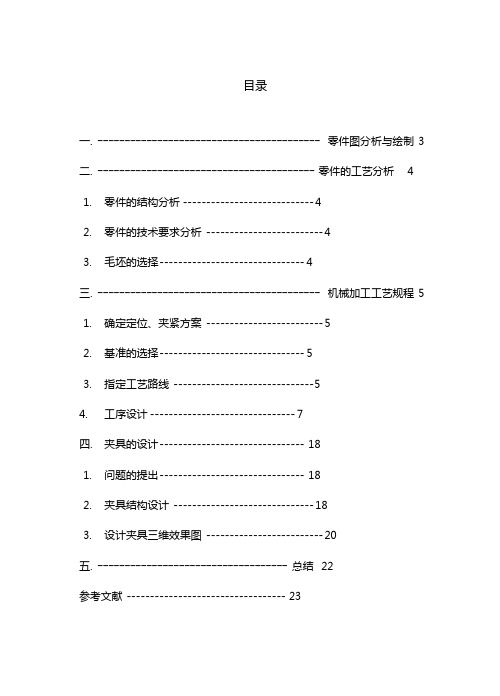
目录一. ----------------------------------------- 零件图分析与绘制3二. ---------------------------------------- 零件的工艺分析 41.零件的结构分析 ---------------------------- 42.零件的技术要求分析------------------------- 43.毛坯的选择------------------------------- 4三. ----------------------------------------- 机械加工工艺规程51.确定定位、夹紧方案------------------------- 52.基准的选择------------------------------- 53.指定工艺路线 ------------------------------ 54.工序设计 ------------------------------- 7四.夹具的设计------------------------------- 181.问题的提出------------------------------- 182.夹具结构设计------------------------------ 183.设计夹具三维效果图------------------------- 20五. ----------------------------------- 总结22参考文献 ---------------------------------- 23第一章零件的分析1.1零件图的分析与绘制该零件为轴承套,主要作用为配合紧定螺丝,以达到内圈周向、轴向固定的目的, 广泛应用于轻负荷便于拆装的地方, 其内圈内孔是间隙配合,一般只用于轻载、无冲 击的场合,同时它可以调整紧松使许多箱体的加工精度得到放宽使箱体加工的工效大 大提高。
轴承套加工课程设计

轴承套加工课程设计一、课程设计背景随着机械制造行业的快速发展,轴承套作为一种重要的机械零部件,在各种机械设备中得到广泛应用。
因此,轴承套加工技术的研究和开发具有重要的意义。
本课程设计旨在通过对轴承套加工技术进行研究和实践,提高学生的实际操作能力和创新能力。
二、课程设计目标1.了解轴承套加工技术的基本原理和流程;2.掌握数控车床加工轴承套的操作方法;3.熟练掌握刀具选择、夹具调整等相关技术;4.培养学生的实际操作能力和创新能力。
三、课程设计内容1.理论部分(1)轴承套加工技术基础知识;(2)数控车床基本操作;(3)数控编程基础知识。
2.实践部分(1)数控车床编程及调试;(2)刀具选择及夹具调整;(3)轴承套加工实验。
四、教学方法1.理论讲授:通过课堂讲解、PPT演示等方式,让学生了解轴承套加工技术的基本原理和流程。
2.实践操作:通过实验课的形式,让学生亲自操作数控车床,进行编程、调试和加工轴承套的实际操作。
五、教学过程1.理论部分(1)轴承套加工技术基础知识:讲解轴承套的定义、分类及加工流程。
(2)数控车床基本操作:介绍数控车床的基本构造和操作方法。
(3)数控编程基础知识:介绍数控编程的语法规则和常用指令。
2.实践部分(1)数控车床编程及调试:学生根据给定的轴承套图纸进行编程,并进行调试。
(2)刀具选择及夹具调整:学生根据加工要求选择合适的刀具,并对夹具进行调整。
(3)轴承套加工实验:学生按照要求进行轴承套加工,并对加工结果进行检验和评价。
六、教学评估1.理论考核:通过闭卷考试等方式,对学生掌握的理论知识进行评估。
2.实践考核:对学生的实际操作能力进行考核,包括编程、调试和加工轴承套的能力。
七、教学资源1.教材:《数控技术基础》、《机械制造工艺学》等;2.实验室设备:数控车床、刀具、夹具等;3.参考资料:轴承套加工相关图纸、加工工艺流程等。
八、教学成果通过本课程设计,学生可以掌握轴承套加工技术的基本原理和流程,熟练掌握数控车床加工轴承套的操作方法,并具备刀具选择、夹具调整等相关技术。
深沟球轴承自动装配机合套系统的机械结构设计

深沟球轴承自动装配机合套系统的机械结构设计赵春辉【摘要】主要研究深沟球轴承自动装配机中合套系统的机械结构,主要研究的模块有六个:外圈进料机内圈进料机构、检测机构、中转机构、机械手机构和滚珠进料机构.根据轴承装配的要求及各机构的运动形式,通过三维建模建立模型对各模块进行机械结构设计.【期刊名称】《装备制造技术》【年(卷),期】2018(000)001【总页数】3页(P68-70)【关键词】深沟球轴承自动装配机;合套系统;机械结构设计【作者】赵春辉【作者单位】无锡技师学院(立信中专),江苏无锡 214153【正文语种】中文【中图分类】TH1220 引言本市很多轴承厂是微型轴承制造公司。
这些企业轴承的产量很大,传统的手工装配效率太低,因此研制自动装配线成为提高生产率的一个重要方面[1]。
针对某企业生产的型号为619/9的深沟球轴承,研究该轴承自动装配机中的合套系统,以有效地提高其自动装配的精度和速度[2]。
619/9型常用参数见表1.它的尺寸见图1.表1619 /9型轴承基本参数型号内径d/mm 外径D/mm 宽度B/mm 倒角/mm 619/9 7 20 6 0.3图1 深沟球轴承本文主要阐述深沟球轴承自动装配机合套系统的设计,其结构构成如图2所示,该系统是自动装配机的第一大部分,主要完成深沟球轴承三大基础件(外圈、内圈及滚动体)装配位置的确定,研究该系统的目的在于保证和稳定该类产品的品质、提高生产效率,以适应国际市场的激烈竞争[3-4]。
1 合套系统的基本组成结构轴承合套系统主要的模块:内外圈的进料模块、内外圈的合套模块、滚动体(滚珠等)的入料模块。
这三大模块中,共有8个主要机构协同运动进行本设备的合套运动。
该合套系统就要求完成的以下功能:(1)内、外圈进入所需的位置。
(2)内、外圈尺寸的测量。
(3)机械手自动夹紧定位。
(4)根据游隙自动输送滚珠。
(5)自动送料。
总体的模块如下图2所示。
图2 深沟球轴承自动装配机合套系统总体模块合套装置的总体机械部分见图3,其主要由外圈进料机构、内圈进料机构、检测机构等机构构成[5]。
轴承套零件机械加工工艺分析
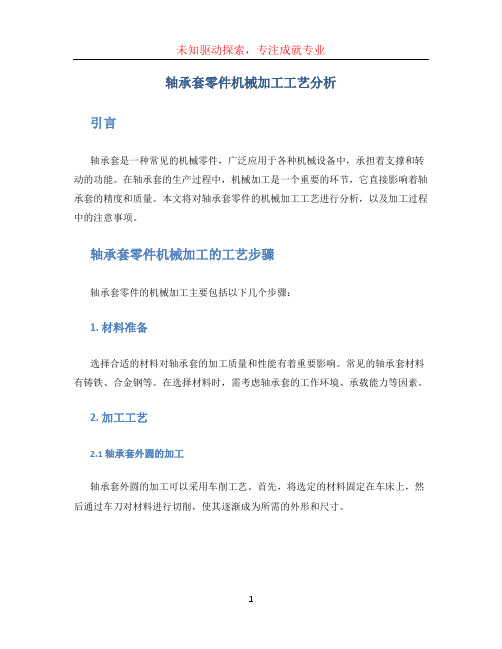
轴承套零件机械加工工艺分析引言轴承套是一种常见的机械零件,广泛应用于各种机械设备中,承担着支撑和转动的功能。
在轴承套的生产过程中,机械加工是一个重要的环节,它直接影响着轴承套的精度和质量。
本文将对轴承套零件的机械加工工艺进行分析,以及加工过程中的注意事项。
轴承套零件机械加工的工艺步骤轴承套零件的机械加工主要包括以下几个步骤:1. 材料准备选择合适的材料对轴承套的加工质量和性能有着重要影响。
常见的轴承套材料有铸铁、合金钢等。
在选择材料时,需考虑轴承套的工作环境、承载能力等因素。
2. 加工工艺2.1 轴承套外圆的加工轴承套外圆的加工可以采用车削工艺。
首先,将选定的材料固定在车床上,然后通过车刀对材料进行切削,使其逐渐成为所需的外形和尺寸。
2.2 轴承套内孔的加工轴承套的内孔加工一般采用铰削工艺。
在铰削过程中,先使用钻孔机将轴承套预先钻出合适的孔径,然后再使用铰刀将孔径加工到所需精度和形状。
3. 表面处理轴承套的表面处理是为了提高其外观质量和耐腐蚀性。
常见的表面处理方式包括镀镍、镀铬等。
这些处理方式可以使轴承套表面看起来更光滑,提高其美观度,并且能够提高其耐腐蚀性,延长使用寿命。
4. 检验与质量控制对于加工好的轴承套,需要进行严格的检验和质量控制,以确保其符合设计要求和标准。
常用的检验手段包括尺寸测量、外观检查、硬度测试等。
通过这些检验手段,可以及时发现和纠正加工过程中的问题,确保轴承套的质量达到要求。
加工过程中的注意事项在轴承套零件的机械加工过程中,需要注意以下几个方面:1. 加工精度控制轴承套是一个精密零件,其加工精度对整个机械设备的性能和寿命都有着重要影响。
因此,在加工过程中,需要控制好加工精度,保证轴承套的尺寸和形状满足设计要求。
2. 切削参数控制在轴承套的切削过程中,切削参数的选择和控制是非常重要的。
合理选择切削速度、进给速度和切削深度等参数,可以降低切削力,避免切削过程中的振动和变形,提高加工质量。
轴承内环分解工装的设计
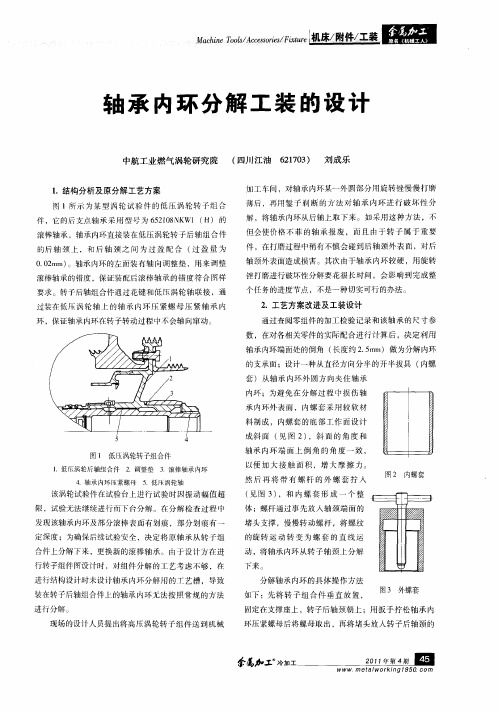
2 .工艺方案改进及工装设计
通过查阅零组件的加工检验记录 和该 轴承 的尺寸参
环 ,保证轴 承内环在转子转动过程中不会轴 向窜动 。
数 ,在对各相关零件的实际配合进行计 算后 ,决定 利用 轴承 内环端面处的倒角 ( 长度约 2 5 m)做 为分解 内环 .m 的支承面 ;设 汁一种从直径方 向分半 的开半拔 具 ( 内螺 套 )从轴承 内环 外 圆方 向夹住 轴承
1 .结构分析及原分解工艺方案
图 1所示 为某 型涡 轮试 验件 的低 压 涡轮转 子组 合 件 ,它的后支点轴承 采用 型号为 6 2 0 N W1( 5 18 K H) 的
解 ,将轴 承内环从后轴上取 下来。如采用这 种方 法,不 但会使价 格不 菲 的轴 承 报废 ,而且 由于转 子 属于 重要 件 ,在打磨过程 中稍有不慎会碰 到后轴颈外 表 面,对后 轴颈外表 面造成损害 。其次 由于轴 承 内环较 硬 ,用旋转
汽车覆盖件尤其是外板件 ,其形状 、尺寸精度要求
研发 了 G C结构 面编程软件及 自动化程序后置 。 WN
较高 ,而覆盖件 模具 尤 其是 高级 汽车 的覆 盖件 ( 外板 件)尺寸公差 、形状精度的要求 更高 ,如果按照一般 的 加工工艺 ,难 以保证模具的装配和型 面精 度。长城汽车 精工模具技术有限公司是一家大型的模具公 司 ,为了在 同行业竞争 中立于前列 ,通过高精度 的机 床设备 ,合理
内环 ;为避免在 分解 过程 中损伤 轴
承 内环外 表面 ,内螺 套采用 较 软材
料制成 ,内螺 套的底 部工作 面设 计
成斜 面 ( 网 2 ,斜 面 的角 度 和 见 )
- 1、下载文档前请自行甄别文档内容的完整性,平台不提供额外的编辑、内容补充、找答案等附加服务。
- 2、"仅部分预览"的文档,不可在线预览部分如存在完整性等问题,可反馈申请退款(可完整预览的文档不适用该条件!)。
- 3、如文档侵犯您的权益,请联系客服反馈,我们会尽快为您处理(人工客服工作时间:9:00-18:30)。
Design of Bearing Sleeve Mechanical System Based on Industry 4.0 JIN Duting
( Zhejiang Institute of Mechanical & Electrical Engineering, Hangzhou 310051, China ) Abstract:In view of the fact that the existing bearing splicing machine is intelligent and the degree of automation is not high, it can not meet the needs of modern intelligent manufacturing and the change trend of the bearing market “increased demand for types and reduction of total demand”, designing the bearing system based on industry 4.0 by combining modular design and virtual simulation. The system includes inner and outer raceway feeding transmission module, clamping transmission module, inner raceway deviation measurement module, outer raceway deviation measurement module, multi-layer inner/outer raceway placement module, assembly module and installation module. Among them, the installation module is mainly divided into the down-pressing part, push-pressing part and pull-out part. Each module coordinates to complete the inner and outer rings of two types of bearings without interference. Therefore, the system realizes the full automatic bearing fitting, and at the same time realizes the model customization in a small range (6202 and 6203). When changing the model demand, the automatic on-line switching production is realized. Key words:sleeve mechanical system;raceway deviation measurement module;internal and external loop module;installation module;model customi期 第 46 卷
持架与滚动体的合套,再将其放置于内外圈合套 环节,汇入装配线。浙江万向特种轴承有限公司 研制半自动圆锥滚子轴承合套机[5]在十分钟内实 行工装更换,切换型号完成内外圈合套,减员同 时提高生产效益。西安海红轴承厂等轴承企业也 在轴承内外圈合套环节自动化程度和装配效益 上进行了多项研究[6]。国外 SKF、TIMKEN、NSK 等企业,在轴承内外圈合套上已经实现高度自动 化[7],其中,SKF 的轴承生产线,可快速完成人 工更换工装以切换生产线合套型号,保证各型号 合套质量同时最大程度上提高市场响应速度。
系统。系统包括内外圈进料传输模块、内外圈夹取传递模块、内圈滚道偏差值测量模块、外圈滚道偏差
值测量模块、多层式内/外圈放置模块、内外圈合套模块、安装模块。其中安装模块主要分为下压部分、
推压部分和拨动部分。模块装配完毕后,虚拟仿真显示,各模块协调配合可完成两种型号轴承内外圈合
套,互相不产生干涉。因此,系统实现轴承全自动合套,同时小范围(6202 和 6203)内实现型号订制,
机械 2019 年第 10 期 第 46 卷
机械
·73·
基于工业 4.0 的轴承合套机械系统设计
金杜挺
(浙江机电职业技术学院,浙江 杭州 310051)
摘要:针对现有轴承合套机智能化、自动化程度不高,无法满足现代化智能制造的需求和轴承市场“种
类需求增加,总量需求减少”变化趋势,结合模块化设计与虚拟仿真,设计基于工业 4.0 的轴承合套机械
国内轴承企业内外圈合套工序是手工、半 自动化操作[1],难以满足先进制造业对轴承质 量等各项参数的要求[2]。因此,部分企业在轴
承内外圈合套工序进行了一些研究[3]:浙江新 昌双菱轴承研制的轴承自动装配线[4]一定程度 上提高了轴承装配效率,但仍需装配工人完成保
———————————————
收稿日期:2019-05-05 作者简介:金杜挺(1992-),男,浙江金华人,硕士,助教,主要研究方向为智能制造技术。
改变型号需求时,全自动在线切换生产。
关键词:合套机械系统;滚道偏差值测量模块;内外圈合套模块;安装模块;型号订制
中图分类号:TP271+.2;TH133.3 文献标志码:A
doi:10.3969/j.issn.1006-0316.2019.10.013
文章编号:1006-0316 (2019) 10-0073-09