4.3流延成型技术
流延成型法
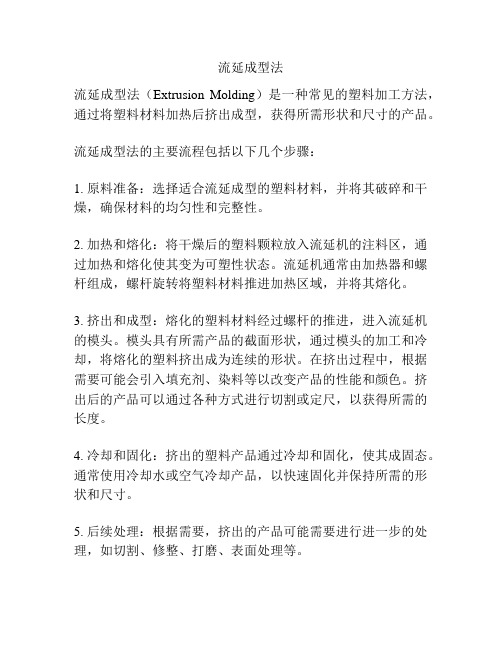
流延成型法
流延成型法(Extrusion Molding)是一种常见的塑料加工方法,通过将塑料材料加热后挤出成型,获得所需形状和尺寸的产品。
流延成型法的主要流程包括以下几个步骤:
1. 原料准备:选择适合流延成型的塑料材料,并将其破碎和干燥,确保材料的均匀性和完整性。
2. 加热和熔化:将干燥后的塑料颗粒放入流延机的注料区,通过加热和熔化使其变为可塑性状态。
流延机通常由加热器和螺杆组成,螺杆旋转将塑料材料推进加热区域,并将其熔化。
3. 挤出和成型:熔化的塑料材料经过螺杆的推进,进入流延机的模头。
模头具有所需产品的截面形状,通过模头的加工和冷却,将熔化的塑料挤出成为连续的形状。
在挤出过程中,根据需要可能会引入填充剂、染料等以改变产品的性能和颜色。
挤出后的产品可以通过各种方式进行切割或定尺,以获得所需的长度。
4. 冷却和固化:挤出的塑料产品通过冷却和固化,使其成固态。
通常使用冷却水或空气冷却产品,以快速固化并保持所需的形状和尺寸。
5. 后续处理:根据需要,挤出的产品可能需要进行进一步的处理,如切割、修整、打磨、表面处理等。
流延成型法的优点包括生产效率高、生产周期短、成本低、适用于生产大批量产品等。
它在日常生活中广泛应用于制造各种塑料制品,如塑料板材、水管、电缆护套、薄膜、包装材料等。
流延成型工艺及添加助剂作用
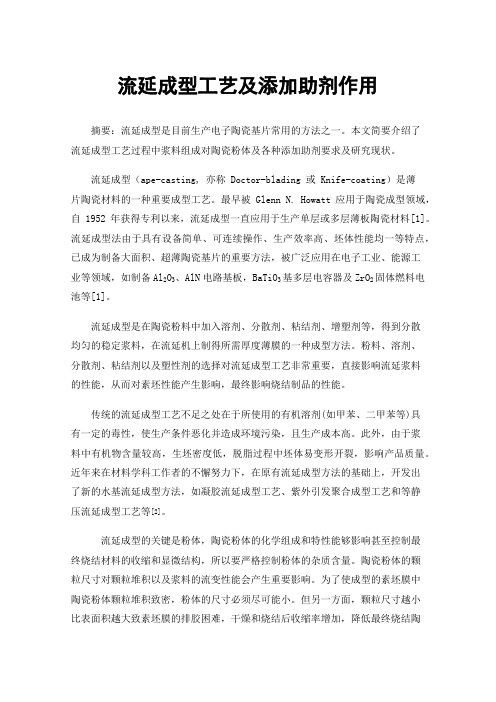
流延成型工艺及添加助剂作用摘要:流延成型是目前生产电子陶瓷基片常用的方法之一。
本文简要介绍了流延成型工艺过程中浆料组成对陶瓷粉体及各种添加助剂要求及研究现状。
流延成型(ape-casting, 亦称 Doctor-blading 或 Knife-coating)是薄片陶瓷材料的一种重要成型工艺。
最早被 Glenn N. Howatt应用于陶瓷成型领域,自1952年获得专利以来,流延成型一直应用于生产单层或多层薄板陶瓷材料[1]。
流延成型法由于具有设备简单、可连续操作、生产效率高、坯体性能均一等特点,已成为制备大面积、超薄陶瓷基片的重要方法,被广泛应用在电子工业、能源工业等领域,如制备Al2O3、AlN电路基板,BaTiO3基多层电容器及ZrO2固体燃料电池等[1]。
流延成型是在陶瓷粉料中加入溶剂、分散剂、粘结剂、增塑剂等,得到分散均匀的稳定浆料,在流延机上制得所需厚度薄膜的一种成型方法。
粉料、溶剂、分散剂、粘结剂以及塑性剂的选择对流延成型工艺非常重要,直接影响流延浆料的性能,从而对素坯性能产生影响,最终影响烧结制品的性能。
传统的流延成型工艺不足之处在于所使用的有机溶剂(如甲苯、二甲苯等)具有一定的毒性,使生产条件恶化并造成环境污染,且生产成本高。
此外,由于浆料中有机物含量较高,生坯密度低,脱脂过程中坯体易变形开裂,影响产品质量。
近年来在材料学科工作者的不懈努力下,在原有流延成型方法的基础上,开发出了新的水基流延成型方法,如凝胶流延成型工艺、紫外引发聚合成型工艺和等静压流延成型工艺等[2]。
流延成型的关键是粉体,陶瓷粉体的化学组成和特性能够影响甚至控制最终烧结材料的收缩和显微结构,所以要严格控制粉体的杂质含量。
陶瓷粉体的颗粒尺寸对颗粒堆积以及浆料的流变性能会产生重要影响。
为了使成型的素坯膜中陶瓷粉体颗粒堆积致密,粉体的尺寸必须尽可能小。
但另一方面,颗粒尺寸越小比表面积越大致素坯膜的排胶困难,干燥和烧结后收缩率增加,降低最终烧结陶瓷的体密度。
流延法成型

流延法成型
流延法成型是一种常见的塑料加工方法,其原理是将高温的塑料料通过挤压或拉伸的方式制成薄膜或板材。
这种方法通常需要使用专门的机器和设备,如流延机、热管、挤出机等。
通过流延法成型,可以制造出各种不同形状和尺寸的塑料制品,如塑料袋、塑料薄膜、塑料管道、塑料板材等。
而且,这种方法制造的产品具有较高的强度和优良的物理特性,具有广泛的应用价值。
流延法成型在化工、食品、医药等领域中得到广泛应用,如制造食品包装袋、药品包装袋、化妆品包装袋等。
同时,它也为环保事业做出了贡献,如制造生物降解塑料袋等,减少了对环境的污染。
总的来说,流延法成型是一种重要的塑料加工技术,具有广泛的应用前景和重要的社会意义。
- 1 -。
塑料薄膜流延成型技术

塑料薄膜流延成型技术
塑料薄膜流延成型技术
塑料薄膜流延成型技术是一种无模制造技术,它可以让原料被加热,加压,挤压,拉伸,压缩和热塑成型。
它可以制成多种多样的塑料薄膜产品,具有较高的精度,较厚的层次感和良好的耐磨性能。
塑料薄膜流延成型技术的优势在于,它可以制造出厚度可调、宽度可调、颜色可调和形状可调等多种多样的塑料薄膜产品。
它还具有低成本、快速生产、无模具、切割容易等优势。
塑料薄膜流延成型技术的应用非常广泛,它可以用于制造各种类型的塑料薄膜,如热塑性塑料薄膜、压敏性塑料薄膜、水性塑料薄膜、高分子长丝塑料薄膜等。
它可以用于制造包装薄膜、家用电器外壳、电子元件封装、贴片绝缘层、膜型涂层等。
塑料薄膜流延成型技术的生产工艺比较复杂,需要精密的控制,以保证产品质量。
在工艺过程中,应注意温度和湿度的控制,并且在拉伸、压缩、热塑成型等过程中,要控制好塑料薄片的厚度和宽度,以保证产品质量。
塑料薄膜流延成型技术是一种高精度的无模制造技术,它可以用于制造各种类型的塑料薄膜产品,应用非常广泛,具有较高的精度和良好的耐磨性能。
流延成型工艺

流延成型工艺嘿,朋友们!今天咱来聊聊流延成型工艺,这可真是个有意思的玩意儿呢!你看啊,流延成型就好像是一位神奇的魔法师,能把那些不起眼的原材料变得有模有样。
想象一下,一堆粉末或者液体,在经过这个工艺之后,就能变成薄如蝉翼、平整光滑的薄片,是不是很神奇?它的过程其实也不难理解。
就像是我们包饺子的时候擀面皮一样,把材料均匀地铺开。
只不过流延成型更精细、更专业啦!先把材料调配好,让它们乖乖地融合在一起,形成一种可以流动的状态。
然后呢,通过一个特殊的装置,让这些材料像小河流一样缓缓地流淌出来,均匀地铺在一个平面上。
等它们冷却固化了,嘿,一张完美的薄片就诞生啦!流延成型工艺的好处可多了去了。
它可以做出非常薄而且均匀的制品,这可不是随便什么方法都能做到的哦!而且它的精度很高,能满足各种精细的要求。
这就好比是一个能工巧匠,一点点地雕琢出精美的作品。
比如说,在电子行业,那些薄薄的薄膜,很多都是通过流延成型做出来的呀!没有它,我们的手机、电脑可能就没那么好用啦!还有在医疗领域,一些特殊的材料也需要用这个工艺来制作呢。
那怎么才能做好流延成型呢?这可得有点技巧啦!首先,材料的选择很重要,就像做菜选食材一样,得挑好的。
然后,工艺参数得把握好,温度啦、流速啦,都得恰到好处,不然可就做不出好东西咯!而且啊,设备也得维护好,不然关键时刻掉链子可不行。
流延成型工艺虽然厉害,但也不是没有挑战的呀!比如说,有时候材料会不听话,出现气泡啊、厚度不均匀啊之类的问题。
这就像是路上遇到的小怪兽,得想办法打败它们。
还有啊,不同的材料有不同的脾气,得慢慢摸索它们的习性,才能让它们乖乖听话。
不过没关系呀,咱不怕挑战!只要我们认真研究,不断尝试,肯定能把流延成型工艺玩得团团转。
让它为我们创造出更多更好的产品,让我们的生活变得更加丰富多彩。
总之呢,流延成型工艺就是这样一个既有趣又有用的东西。
它就像一个隐藏在工业世界里的小秘密,等待着我们去发现和探索。
车衣4.0薄膜流延工艺

车衣4.0薄膜流延工艺全文共四篇示例,供读者参考第一篇示例:车衣4.0薄膜流延工艺是当前汽车行业中的一项重要技术,它可以为汽车提供保护,提高汽车的外观和耐用性。
薄膜流延工艺是指将涂料在一个适当的基材表面上流延成薄膜的一种生产工艺,通过这种方法可以将各种类型的汽车薄膜制作成车衣,并将其应用在汽车表面,起到保护车漆、提高汽车外观等作用。
车衣4.0薄膜流延工艺是一种高科技、高精密的生产工艺,它的特点是能够制作出较薄的汽车薄膜,而且对基材的要求也较高,需要选用具有较好机械性能和表面平整度的基材。
目前,市场上广泛应用的基材有聚氯乙烯(PVC)、聚乙烯(PE)、聚丙烯(PP)等材料。
车衣4.0薄膜流延工艺的制作流程大致可以分为以下几个步骤。
首先是将涂料通过流延机喷涂在基材表面,形成一层均匀的薄膜。
接着经过烘干和冷却,将薄膜固化并附着在基材上。
对固化后的薄膜进行剪裁和包装,制成成品车衣。
车衣4.0薄膜流延工艺的优点是可以实现薄膜的连续生产,生产效率高,且可以根据客户的需求定制不同规格和颜色的车衣。
车衣薄膜的附着性、耐候性和耐磨性也比较优秀,能够保护汽车表面免受风吹雨淋、紫外线等自然因素的侵害。
在实际应用中,车衣4.0薄膜流延工艺被广泛应用于汽车改装、汽车保养等领域。
通过为汽车表面添加车衣薄膜,可以提高汽车的抗刮擦能力,延长车漆的使用寿命,使汽车外观更加时尚美观。
车衣薄膜还具有一定的防晒效果,可以有效减少紫外线对汽车表面的侵害,延长汽车的使用寿命。
车衣4.0薄膜流延工艺是一种先进的制备技术,它为汽车行业提供了一种新颖、轻便、环保的汽车保护产品。
随着汽车行业的不断发展,车衣薄膜的市场需求也会不断增长,相信在未来的发展中,车衣4.0薄膜流延工艺将会得到更加广泛的应用和推广。
第二篇示例:车衣4.0薄膜流延工艺是一种先进的汽车表面防护技术,通过将特制的薄膜材料涂覆在汽车车身表面,形成一层坚固耐磨的保护膜,可以有效抵御外界因素对车身的损害,延长汽车的使用寿命,保持车身漆面的光泽和颜色。
流延成型技术

凝胶流延成型工艺
水基凝胶流延成型工艺是利用有机单体的聚合原理进行流延 成型。该法是将陶瓷粉料分散于含有有机单体和交联剂的水 溶液中,制备出低粘度且高固相体积分数的浓悬浮体(<50 %体积分数),然后加引发剂和催化剂,在一定的温度条件 下引发有机单体聚合,使悬浮体粘度增大,从而导致原位凝 固成型,得到具有一定强度、可进行机加工的坯体。水基凝 胶流延成型所使用的浆料由陶瓷粉末、有机单体、交联剂、 溶剂、分散剂、塑性剂等组分配制而成。
粉末处理工艺
煅烧温度与球磨时间:球磨工艺不仅减小了平均粒径,而且也使粒 径分布区域变窄。 粒 度 分 析
原始粉料 煅烧 球磨 烘干 过筛 实验用粉料
0.70
SEM分 析
原始粉 末 1200℃煅烧 1250℃煅烧
100
0.65
1200℃煅烧未球磨
煅烧后球磨40h
0.60
80
平均粒径 /μm
百 分 数 /%
沉积率RSH(%)
分散剂对ZrO2浆料粘度的影响
粉料和溶剂恒定时,浆料粘度与分散 剂浓度呈非线性关系。随着分散剂用 量的增加,分散剂对颗粒的静电位阻 作用增强,浆料的流动性明显改善, 粘度也不断下降,直至达到最低粘度。 继续增加分散剂用量,浆料的粘度又 有所增加,这是因为出现过饱和吸附 的情况,过量的分散剂分子相互桥联 成网络结构,极大地限制了颗粒的运 动,再加上离子强度的增加,从而使 浆料粘度升高。故每种分散剂用量均 有一个最佳范围,使浆料粘度达到最 低,此时分散剂在颗粒表面的吸附达 到了饱和,分散剂大分子在粒子外围 形成一壳层,使分散体系靠静电位阻 的作用达到稳定。
脱脂
烧结
水基流延成型工艺
水基流延成型工艺使用水基溶剂替代有机溶剂,由 于水分子是极性分子,而粘结剂、增塑剂和分散剂 等是有机添加剂,与水分子之间存在相容性的问题, 因此在添加剂的选择上,需选择水溶性或者能够在 水中形成稳定乳浊液的有机物以确保得到均一稳定 的浆料。同时还应在保证浆料稳定悬浮的前提下, 使分散剂的用量尽量地少,同时在保证素坯强度和 柔韧性的前提下使粘结剂、增塑剂等的有机物的用 量尽可能少。
流延成型技术

流延成型技术嘿,咱今儿就来说说这流延成型技术!这玩意儿可神奇了呢!你想啊,就像咱平时做面条似的,把那一团面给擀成薄薄的一片,这流延成型技术差不多也是这个道理。
只不过呢,它不是做面条,而是用来制造各种材料的。
流延成型技术啊,就像是一个神奇的魔法师,能把那些原材料变得平平整整、规规矩矩的。
它能让那些材料乖乖地按照我们想要的形状和厚度来成型。
你说神奇不神奇?比如说,在制造陶瓷的时候,流延成型技术就能大显身手啦!它能让陶瓷的坯体变得又薄又均匀,就像是给陶瓷穿上了一件合身的衣服一样。
这样做出来的陶瓷制品,质量那可是杠杠的!再想想看,如果没有流延成型技术,那我们好多东西都没办法做得那么精致呢!就好比盖房子没有了砖头,做饭没有了锅,那可不行呀!流延成型技术还特别的灵活呢!它可以根据不同的需求,调整材料的配方和工艺参数,就像是一个聪明的厨师,可以根据不同人的口味来调整菜肴的味道一样。
这样就能制造出各种各样符合我们要求的产品啦!而且哦,流延成型技术在很多领域都有着广泛的应用呢!不光是陶瓷,在电子材料、生物医学等领域也都能看到它的身影。
它就像是一个无处不在的小精灵,默默地为我们的生活和科技进步做着贡献。
你说,这么厉害的技术,我们能不好好了解了解吗?要是咱也能掌握这门技术,那岂不是很牛?说不定还能自己动手做出一些好玩的东西来呢!流延成型技术啊,真的是一项非常有意义的技术。
它让我们的生活变得更加丰富多彩,让那些原本普通的材料变得神奇起来。
它就像是一束光,照亮了我们追求更好生活的道路。
咱可不能小瞧了这流延成型技术,它虽然看起来不起眼,但却有着大作用呢!它就像是一个默默奉献的幕后英雄,虽然不被大多数人所熟知,但却一直在为我们的生活和科技发展努力着。
所以啊,我们要好好感谢流延成型技术,感谢它为我们带来的一切便利和美好。
让我们一起为流延成型技术点赞吧!。
流延成型工艺流程

流延成型工艺流程一、流延成型的准备阶段。
1.1 原料的选择。
流延成型啊,这原料的选择可太重要了。
就像咱们做菜,得选新鲜的食材一样。
这原料得有合适的粒度、纯度之类的。
比如说陶瓷流延成型,那陶瓷粉末的质量得过关啊,要是粉末里面杂质太多,就像一锅粥里混进了沙子,那做出来的成品质量肯定好不了。
而且不同的产品需求,原料的成分比例也得好好琢磨,可不能稀里糊涂的。
1.2 添加剂的调配。
添加剂在流延成型里那就是“神助攻”。
像分散剂啊,它能让原料均匀地分散开,就像把一群调皮捣蛋的小孩子给安排得井井有条。
增塑剂呢,能让坯体有一定的柔韧性,不然那坯体硬邦邦的,很容易就裂了,这就好比人要是太死板,在生活里就容易碰壁。
这些添加剂的量得拿捏得准,多了少了都不行,那真得有点“过犹不及”的意思。
二、流延成型的关键操作。
2.1 浆料的制备。
这浆料制备可是个精细活。
先把原料和添加剂按照比例混合起来,然后加入溶剂。
这个搅拌的过程就像跳舞一样,得有节奏。
搅拌得不够,原料混合不均匀,搅拌得太猛了,又可能会引入气泡。
气泡在流延成型里那就是“眼中钉”,有了气泡,做出的产品就可能有孔洞,就像漂亮的脸蛋上长了麻子,多难看啊。
2.2 流延过程。
流延的时候,就像给地面铺地毯似的。
把制备好的浆料倒在流延机的载带上,然后通过刮刀控制厚度。
刮刀就像一把神奇的梳子,把浆料梳理成均匀的一层。
这厚度的控制可不能马虎,得精确到毫米甚至更小的单位。
要是厚度不均匀,那做出来的产品尺寸就不达标,就像盖房子,墙砌歪了,这房子能结实吗?2.3 干燥处理。
干燥这一步也很关键。
就像把洗过的衣服晾干一样,得把流延后的坯体里的溶剂给除掉。
但是干燥的速度得控制好,太快了,坯体可能会开裂,这就叫“欲速则不达”;太慢了呢,又会影响生产效率。
而且干燥的环境也得注意,湿度啊温度啊都得合适,不然坯体可能会受潮或者变形。
三、流延成型的后期处理。
3.1 坯体的脱模。
坯体干燥好了之后,就要脱模了。
流延(涎)法——塑料热成型片材生产技术
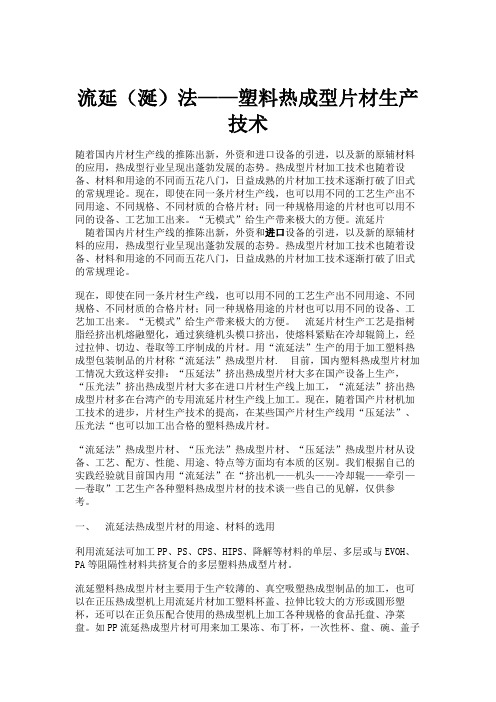
流延(涎)法——塑料热成型片材生产技术随着国内片材生产线的推陈出新,外资和进口设备的引进,以及新的原辅材料的应用,热成型行业呈现出蓬勃发展的态势。
热成型片材加工技术也随着设备、材料和用途的不同而五花八门,日益成熟的片材加工技术逐渐打破了旧式的常规理论。
现在,即使在同一条片材生产线,也可以用不同的工艺生产出不同用途、不同规格、不同材质的合格片材;同一种规格用途的片材也可以用不同的设备、工艺加工出来。
“无模式”给生产带来极大的方便。
流延片随着国内片材生产线的推陈出新,外资和进口设备的引进,以及新的原辅材料的应用,热成型行业呈现出蓬勃发展的态势。
热成型片材加工技术也随着设备、材料和用途的不同而五花八门,日益成熟的片材加工技术逐渐打破了旧式的常规理论。
现在,即使在同一条片材生产线,也可以用不同的工艺生产出不同用途、不同规格、不同材质的合格片材;同一种规格用途的片材也可以用不同的设备、工艺加工出来。
“无模式”给生产带来极大的方便。
流延片材生产工艺是指树脂经挤出机熔融塑化,通过狭缝机头模口挤出,使熔料紧贴在冷却辊筒上,经过拉伸、切边、卷取等工序制成的片材。
用“流延法”生产的用于加工塑料热成型包装制品的片材称“流延法”热成型片材. 目前,国内塑料热成型片材加工情况大致这样安排:“压延法”挤出热成型片材大多在国产设备上生产,“压光法”挤出热成型片材大多在进口片材生产线上加工,“流延法”挤出热成型片材多在台湾产的专用流延片材生产线上加工。
现在,随着国产片材机加工技术的进步,片材生产技术的提高,在某些国产片材生产线用“压延法”、压光法“也可以加工出合格的塑料热成片材。
“流延法”热成型片材、“压光法”热成型片材、“压延法”热成型片材从设备、工艺、配方、性能、用途、特点等方面均有本质的区别。
我们根据自己的实践经验就目前国内用“流延法”在“挤出机——机头——冷却辊——牵引——卷取”工艺生产各种塑料热成型片材的技术谈一些自己的见解,仅供参考。
流延膜成型工艺及设备介绍

流延膜成型工艺及设备介绍引言流延膜成型工艺是一种常见的塑料薄膜制备技术,广泛应用于包装、建筑、农业等行业。
本文将介绍流延膜成型的工艺流程以及相关设备。
流延膜成型工艺流延膜成型工艺是通过将熔融的塑料料坯通过流通槽流动,在一对冷却辊的夹持下进行拉伸成膜。
具体工艺流程如下:1.塑料颗粒的预处理:将原料塑料颗粒进行干燥、筛选等预处理工序,确保颗粒的干燥和均匀性,以便提高成膜质量。
2.挤出:将预处理后的塑料颗粒通过挤出机加热熔化,形成熔融的塑料料坯。
3.进料和涂布:熔融的塑料料坯通过流通槽进入成膜区域,同时在上方的涂布器中加入适量的添加剂,如抗静电剂、防霉剂等,以增加膜的功能性。
4.成膜:塑料料坯在冷却辊的夹持下进行拉伸,形成薄膜状。
辊的转速和温度的控制对成膜速度和薄膜厚度有重要影响。
5.冷却:成膜后的薄膜通过冷却辊的冷却作用,使其快速降温固化,保持形状和机械性能。
6.拉伸:冷却后的薄膜经过拉伸辊进行预拉伸,以提高薄膜的透明度、强度和尺寸稳定性。
7.收卷:拉伸后的薄膜经过辊筒的引导,被卷取到薄膜卷筒中。
流延膜成型设备流延膜成型设备是流延膜生产过程中的核心设备,主要包括挤出机、流通槽、冷却辊、涂布器、拉伸辊和收卷机等。
1.挤出机:挤出机是将固态塑料颗粒加热熔化,并通过螺杆将熔融物质推送到流通槽中的设备。
挤出机的型号和规格根据生产需要进行选择。
2.流通槽:流通槽是塑料料坯流动的通道,通常由不锈钢制成。
其长度和宽度可根据生产需求进行调整,以控制成膜速度和薄膜厚度。
3.冷却辊:冷却辊通常由铸铁或铜制成,通过辊的内部流动的冷却介质降温,使薄膜快速降温固化。
冷却辊的转速和温度可以通过控制系统进行调节。
4.涂布器:涂布器用于在薄膜成膜区域上方添加添加剂。
涂布器有不同种类,可根据生产需要选择,如喷雾式涂布器和擦拭式涂布器等。
5.拉伸辊:拉伸辊用于对成膜后的薄膜进行预拉伸,以提高薄膜的透明度、强度和尺寸稳定性。
拉伸辊的尺寸和数量可根据生产需求进行选择。
陶瓷流延成型工艺

陶瓷流延成型工艺
近年来,陶瓷制造业发展迅速,随之而来的是对于陶瓷流延成型工
艺的不断完善和应用。
这种工艺可以有效地提高陶瓷制品的质量和稳
定性,在工业领域中广泛应用。
下面,我们将对这种工艺进行详细的
介绍和分析。
一、工艺流程
陶瓷流延成型工艺是一种连续制造工艺,大体分为材料制备、搅拌、
过滤、成型、干燥、硬化、烧结等多个环节。
首先,制造人员需要选
取合适的陶瓷原料,并进行粉碎、混合、搅拌等工作,制成均匀的浆料。
接着,将浆料倒入流延机中,依照预设的模具尺寸和几何形状进
行成型。
此时,陶瓷坯体从模具中不间断推出,经过干燥后再进行硬化、烧结,最终制成成品陶瓷。
二、工艺优点
相比于传统陶瓷成型工艺,陶瓷流延成型具有如下优点:
1. 陶瓷坯体的形状稳定性好,表面光整,不会出现开裂、变形等现象。
2. 成品陶瓷具有高强度、高密度、高韧性等优良物理性能。
3. 浆料处理和成型过程中不需要使用高压,无需消耗大量人力物力,
具有较高的成型效率。
4. 可以制造出细致度小、形状异样的不规则陶瓷制品,且可以控制制品的尺寸精度和表面质量。
三、工艺应用
陶瓷流延成型工艺的应用广泛,涉及到陶瓷制造的各个领域。
例如,在航空航天领域中,流延成型可以用于制造高温陶瓷热结构件、超声速飞行器传感器等高性能要求的陶瓷部件,具有重要的应用价值。
另外,该工艺还可以用于制造陶瓷基合成材料、陶瓷感应器件等。
总之,随着陶瓷流延成型技术逐渐成熟,它的应用将会得到更广泛的推广和应用。
【精品文章】一种重要的薄片陶瓷材料成型工艺:流延成型
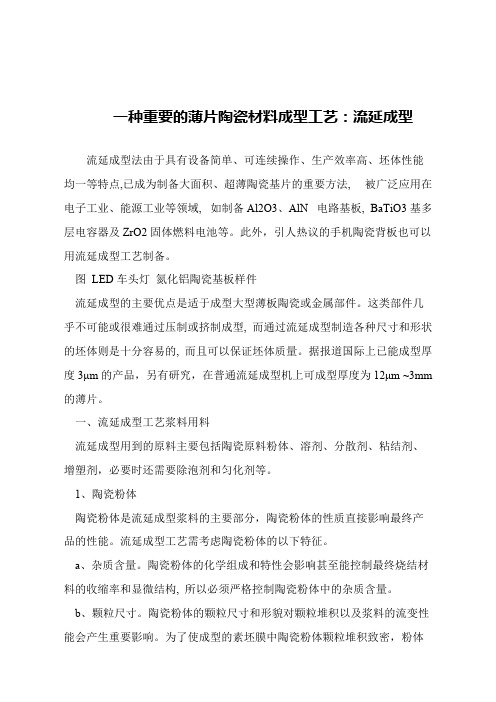
一种重要的薄片陶瓷材料成型工艺:流延成型
流延成型法由于具有设备简单、可连续操作、生产效率高、坯体性能均一等特点,已成为制备大面积、超薄陶瓷基片的重要方法, 被广泛应用在电子工业、能源工业等领域, 如制备Al2O3、AlN 电路基板, BaTiO3基多层电容器及ZrO2固体燃料电池等。
此外,引人热议的手机陶瓷背板也可以用流延成型工艺制备。
图LED车头灯氮化铝陶瓷基板样件
流延成型的主要优点是适于成型大型薄板陶瓷或金属部件。
这类部件几乎不可能或很难通过压制或挤制成型, 而通过流延成型制造各种尺寸和形状的坯体则是十分容易的, 而且可以保证坯体质量。
据报道国际上已能成型厚度3μm的产品,另有研究,在普通流延成型机上可成型厚度为12μm ~3mm 的薄片。
一、流延成型工艺浆料用料
流延成型用到的原料主要包括陶瓷原料粉体、溶剂、分散剂、粘结剂、增塑剂,必要时还需要除泡剂和匀化剂等。
1、陶瓷粉体
陶瓷粉体是流延成型浆料的主要部分,陶瓷粉体的性质直接影响最终产品的性能。
流延成型工艺需考虑陶瓷粉体的以下特征。
a、杂质含量。
陶瓷粉体的化学组成和特性会影响甚至能控制最终烧结材料的收缩率和显微结构, 所以必须严格控制陶瓷粉体中的杂质含量。
b、颗粒尺寸。
陶瓷粉体的颗粒尺寸和形貌对颗粒堆积以及浆料的流变性能会产生重要影响。
为了使成型的素坯膜中陶瓷粉体颗粒堆积致密,粉体。
流延成型法
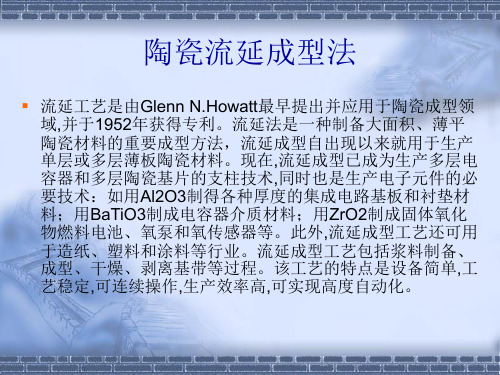
0 0
2
4
6
8
pH值
10
12
14
内,沉积率低于15%,浆料的分散稳定性更 好。另一方面,在pH>12时,沉积率均有所
增加。这是因为加入了较多的NaOH,引起
离子强度的增加,双电层厚度减小,由于范
德华力的作用,陶瓷颗粒相互靠近,从而影
响浆料的稳定性,使沉积率增加。
分散剂对ZrO2浆料粘度的影响
▪ 粉料和溶剂恒定时,浆料粘度与分散
流延成型溶剂
▪ 选择溶剂的基本原则为:必须能溶解其它添加成分,包括分散剂、 粘结剂和增塑剂等;在浆料中能保持化学稳定性,不与粉料发生 化学反应;易于挥发与烧除;使用安全卫生和对环境污染少。最 常用的溶剂分为有机溶剂和水两大类。因用有机溶剂所得的浆料 粘度低,溶剂挥发快,干燥时间短,所以流延法制膜中使用有机 溶剂较多,但使用有机溶剂存在易燃和有毒的缺点,而用水作溶 剂则具有成本低、使用安全卫生和便于大规模生产等优点,其缺 点是:对粉料颗粒的湿润性能较差、挥发速度慢和干燥时间长;浆 料除气困难,气泡的存在会影响素坯的质量;水基浆料所用粘结 剂多为乳状液,品种较少使粘结剂的选择受到限制。溶剂对粉料 的湿润性能主要与其表面张力有关,表面张力越小,对粉料颗粒 的湿润性能越好。有机溶剂的表面张力比水要低得多,所以其湿 润性能比水好。混合溶剂的表面张力和介电常数等综合性能较单 一组分要好,且沸点低,对分散剂、粘结剂和塑性剂的溶解性能 也较佳。研究表明,所谓“动力学溶剂”(小分子如乙醇)和 “热力学溶剂”(酯、酮)的混合物是最有效的。为确保干燥过 程中同时挥发,流延浆中常用二元共沸混合物。最常用的有乙醇/ 甲乙酮、乙醇/三氯乙烯、乙醇/水和三氯乙烯/甲乙酮等。
流延陶瓷片基元件用途
4.3流延成型技术
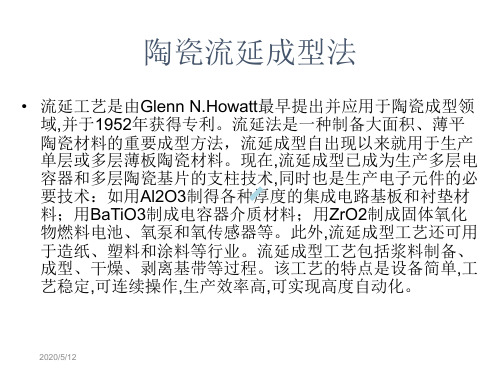
水基流延成型工艺优缺点
• 水基流延成型具有价格低廉,无毒性,不易燃等优 点,但也存在一些问题:a)蒸发速度低;b)所需的 粘结剂浓度高;c)氢键引起陶瓷粉末团聚导致絮凝 ;d)浆料对工艺参数变化敏感,不易成型表面致密 光滑的陶瓷膜;e)坯体结合不充分,干燥易起泡开 裂,脆性大,易弯曲变形;f)缺陷引起应力集中, 导致烧结开裂。目前,水基流延成型的研究主要应 用于Al2O3, ZrO2等少数的氧化物陶瓷,对TiC也 有研究。
50
位增大,静电稳定作用增强,有利于稳定分
40
散。相反,浆料电动电位降低,颗粒容易团
30
聚。由于加入不同分散剂后浆料等电点并不
相同,因此不同分散剂的最佳pH范围也有
20
所不同。比较三条曲线可知,磷酸三丁酯和
10
松油醇作分散剂时,其沉积率均在25%以上
0
。而三乙醇胺作分散剂时,在9.5<pH<11范
0
工艺稳定,可连续操作,生产效率高,可实现高度自动化。
溶剂
粘结剂
陶瓷粉料 球磨
混磨 真空除泡 粘度调节 流延成型 干燥
分散剂
增塑剂
传统的非水基流延成型已经较为成熟,在陶瓷领域有广泛的应用,如用流延成 型制备氧化铝陶瓷膜、制备ALN膜、制备YSZ膜、流延成型制备陶瓷燃料电池 电解质膜等,也可以制备包含有晶须的复合陶瓷膜。 传统的流延成型工艺不足之处在于所使用的有机溶剂(如甲苯、二甲苯等)具有 一定的毒性,使生产条件恶化并造成环境污染,且生产成本较高。此外,由于浆 料中有机物含量较高,素坯密度低,脱脂过程中坯体易变形开裂,影响产品质
2020/5/12
陶瓷流延成型法
• 流延成型的具体工艺过程是将陶瓷粉末与分散剂、 粘结剂和增塑剂在溶剂中混合,形成均匀稳定悬浮 的浆料。成型时浆料从料斗下部流至基带之上,通 过基带与刮刀的相对运动形成坯膜,坯膜的厚度由 刮刀控制。将坯膜连同基带一起送入烘干室,溶剂 蒸发,有机结合剂在陶瓷颗粒间形成网络结构,形 成具有一定强度和柔韧性的坯片,干燥的坯片连同 基带一起卷轴待用。在储存过程中使残留溶剂分布 均匀,消除湿度梯度。然后可按所需形状切割、冲 片或打孔。最后经过脱脂烧结得到成品。
陶瓷薄片的流延成型工艺概述

陶瓷薄片的流延成型工艺概述
宋占永;董桂霞;杨志民;马舒旺
【期刊名称】《材料导报》
【年(卷),期】2009(023)009
【摘要】概述了流延成型工艺的特点及发展历程,比较了水基流延成型与传统流延成型技术的优缺点.针对特定的流延成型工艺过程进行了详细的介绍和理论分析,同时介绍了几种新型的流延工艺.最后对流延成型技术的研究和应用进行了展望,并提出了自己的见解.
【总页数】4页(P43-46)
【作者】宋占永;董桂霞;杨志民;马舒旺
【作者单位】北京有色金属研究总院先进电子材料研究所,北京,100088;北京有色金属研究总院先进电子材料研究所,北京,100088;北京有色金属研究总院先进电子材料研究所,北京,100088;北京有色金属研究总院先进电子材料研究所,北
京,100088
【正文语种】中文
【中图分类】TQ17
【相关文献】
1.流延法制备FeNiMnO4热敏陶瓷薄片 [J], 方道来
2.薄片陶瓷材料凝胶流延成型(Gel—Tape—Casting)工艺研究 [J], 向军辉;黄勇
3.工艺条件对薄片陶瓷材料凝胶流延成型的影响 [J], 向军辉;黄勇;谢志鹏;杨金龙;马春雷
4.流延法制备陶瓷薄片的研究进展 [J], 李冬云;乔冠军;金志浩
5.电子陶瓷基板及薄片陶瓷器件的快速凝固流延成型方法 [J],
因版权原因,仅展示原文概要,查看原文内容请购买。
- 1、下载文档前请自行甄别文档内容的完整性,平台不提供额外的编辑、内容补充、找答案等附加服务。
- 2、"仅部分预览"的文档,不可在线预览部分如存在完整性等问题,可反馈申请退款(可完整预览的文档不适用该条件!)。
- 3、如文档侵犯您的权益,请联系客服反馈,我们会尽快为您处理(人工客服工作时间:9:00-18:30)。
凝胶流延成型工艺
水基凝胶流延成型工艺是利用有机单体的聚合原理进行流延 成型。该法是将陶瓷粉料分散于含有有机单体和交联剂的水 溶液中,制备出低粘度且高固相体积分数的浓悬浮体(<50 %体积分数),然后加引发剂和催化剂,在一定的温度条件 下引发有机单体聚合,使悬浮体粘度增大,从而导致原位凝 固成型,得到具有一定强度、可进行机加工的坯体。水基凝 胶流延成型所使用的浆料由陶瓷粉末、有机单体、交联剂、 溶剂、分散剂、塑性剂等组分配制而成。
流延成型溶剂
选择溶剂的基本原则为:必须能溶解其它添加成分,包括分散剂、 粘结剂和增塑剂等;在浆料中能保持化学稳定性,不与粉料发生 化学反应;易于挥发与烧除;使用安全卫生和对环境污染少。最 常用的溶剂分为有机溶剂和水两大类。因用有机溶剂所得的浆料 粘度低,溶剂挥发快,干燥时间短,所以流延法制膜中使用有机 溶剂较多,但使用有机溶剂存在易燃和有毒的缺点,而用水作溶 剂则具有成本低、使用安全卫生和便于大规模生产等优点,其缺 点是:对粉料颗粒的湿润性能较差、挥发速度慢和干燥时间长;浆 料除气困难,气泡的存在会影响素坯的质量;水基浆料所用粘结 剂多为乳状液,品种较少使粘结剂的选择受到限制。溶剂对粉料 的湿润性能主要与其表面张力有关,表面张力越小,对粉料颗粒 的湿润性能越好。有机溶剂的表面张力比水要低得多,所以其湿 润性能比水好。混合溶剂的表面张力和介电常数等综合性能较单 一组分要好,且沸点低,对分散剂、粘结剂和塑性剂的溶解性能 也较佳。研究表明,所谓“动力学溶剂”(小分子如乙醇)和 “热力学溶剂”(酯、酮)的混合物是最有效的。为确保干燥过 程中同时挥发,流延浆中常用二元共沸混合物。最常用的有乙醇/ 甲乙酮、乙醇/三氯乙烯、乙醇/水和三氯乙烯/甲乙酮等。
流延等静压复合成型工艺
流延等静压复合成型工艺是以非水基和水基流延成型工艺为 基础的工艺过程,它把流延成型工艺和等静压成型工艺有效 的结合起来,以提高素坯的成型密度和烧结密度,工艺过程 较为简单,易于陶瓷膜的工业化生产。由于流延素坯本身制 备工艺的限制,其浆料固含量较低,虽然通过增大粒径,可 以提高浆料固含量和提高素坯密度,但粉体粒子粒径过大, 其烧结性能就会下降,反而会导致烧结膜材密度下降。另一 方面在素坯干燥过程中,因溶剂的挥发,粘结剂和塑性剂难 以在干燥前填充溶剂挥发留下的气孔,从而在素坯表面和内 部留有许多凹坑和孔洞,使素坯结构疏松,密度较低,而单 层流延膜由于厚度较小,不能采用一些非常规烧结手段(如 热压烧结),只能采用无压烧结,加上烧结过程中大量有机 添加剂的烧除,很难获得致密的流延烧结膜材。因素坯密度 较低,结构疏松但延展性较好,故对素坯采用等静压二次成 型提高素坯成型密度,将提高烧结膜材密度。
陶瓷流延成型法
流延工艺是由Glenn N.Howatt最早提出并应用于陶瓷成型领 域,并于1952年获得专利。流延法是一种制备大面积、薄平 陶瓷材料的重要成型方法,流延成型自出现以来就用于生产 单层或多层薄板陶瓷材料。现在,流延成型已成为生产多层电 容器和多层陶瓷基片的支柱技术,同时也是生产电子元件的必 要技术:如用Al2O3制得各种厚度的集成电路基板和衬垫材 料;用BaTiO3制成电容器介质材料;用ZrO2制成固体氧化 物燃料电池、氧泵和氧传感器等。此外,流延成型工艺还可用 于造纸、塑料和涂料等行业。流延成型工艺包括浆料制备、 成型、干燥、剥离基带等过程。该工艺的特点是设备简单,工 艺稳定,可连续操作,生产效率高,可实现高度自动化。
增塑剂 单体溶液 球磨 混合 交联剂 分散剂 陶瓷粉末 催化剂 惰性气体保护 真空除泡 流延 聚合成型 引发剂 加热
凝胶流延成型工艺
有机单体的选择原则是:粘度低、溶液稳定性好、流动性好; 经聚合反应能够形成长链状聚合物;形成的聚合物具有一定 的强度,保证成型后的素坯能够进行切片、冲孔等加工作业。 用于凝胶流延成型的有机单体有:2-羟乙基甲基丙烯酸酯 (HEMA)、甲基丙烯酸(MA)、丙烯酰胺(AM)、甲基 丙烯酰胺(MAM)等。凝胶流延成型工艺的优点在于可以 极大地降低浆料中有机物的使用量,提高浆料的固相含量, 因而提高素坯的密度和强度,同时大大减轻环境污染,并显 著降低生产成本。目前凝胶流延成型工艺已经应用于研制氧 化铝陶瓷薄片及燃料电池YSZ等领域。
分散剂和pH值对氧化锆浆料稳定性的影响
80 4 6 8
pH值
随着pH值的改变,沉积率均有较大变化。 这是因为调节浆料pH值使其接近或远离等 三乙醇胺 磷 酸三丁酯 电点(isoelectric point, IEP),会相应的引 松油醇 起浆料电动电位的减少或增大,根据静电稳 定理论,pH值远离等电点时,浆料电动电 位增大,静电稳定作用增强,有利于稳定分 散。相反,浆料电动电位降低,颗粒容易团 聚。由于加入不同分散剂后浆料等电点并不 相同,因此不同分散剂的最佳pH范围也有 所不同。比较三条曲线可知,磷酸三丁酯和 松油醇作分散剂时,其沉积率均在25%以上。 而三乙醇胺作分散剂时,在9.5<pH<11范围 内,沉积率低于15%,浆料的分散稳定性更 10 12 14 好。另一方面,在pH>12时,沉积率均有所 增加。这是因为加入了较多的NaOH,引起 离子强度的增加,双电层厚度减小,由于范 德华力的作用,陶瓷颗粒相互靠近,从而影 响浆料的稳定性,使沉积率增加。
传统的非水基流延成型已经较为成熟,在陶瓷领域有广泛的应用,如用流延成 型制备氧化铝陶瓷膜、制备ALN膜、制备YSZ膜、流延成型制备陶瓷燃料电池 电解质膜等,也可以制备包含有晶须的复合陶瓷膜。 传统的流延成型工艺不足之处在于所使用的有机溶剂(如甲苯、二甲苯等)具有 一定的毒性,使生产条件恶化并造成环境污染,且生产成本较高。此外,由于浆 料中有机物含量较高,素坯密度低,脱脂过程中坯体易变形开裂,影响产品质 量。针对上述缺点,研究人员开始尝试用水基溶剂体系替代有机溶剂体系。
沉积率RSH(%)
分散剂对ZrO2浆料粘度的影响
粉料和溶剂恒定时,浆料粘度与分散 剂浓度呈非线性关系。随着分散剂用 量的增加,分散剂对颗粒的静电位阻 作用增强,浆料的流动性明显改善, 粘度也不断下降,直至达到最低粘度。 继续增加分散剂用量,浆料的粘度又 有所增加,这是因为出现过饱和吸附 的情况,过量的分散剂分子相互桥联 成网络结构,极大地限制了颗粒的运 动,再加上离子强度的增加,从而使 浆料粘度升高。故每种分散剂用量均 有一个最佳范围,使浆料粘度达到最 低,此时分散剂在颗粒表面的吸附达 到了饱和,分散剂大分子在粒子外围 形成一壳层,使分散体系靠静电位阻 的作用达到稳定。
水基流延成型工艺优缺点
水基流延成型具有价格低廉,无毒性,不易燃等优 点,但也存在一些问题:a)蒸发速度低;b)所需的 粘结剂浓度高;c)氢键引起陶瓷粉末团聚导致絮凝; d)浆料对工艺参数变化敏感,不易成型表面致密光 滑的陶瓷膜;e)坯体结合不充分,干燥易起泡开裂, 脆性大,易弯曲变形;f)缺陷引起应力集中,导致 烧结开裂。目前,水基流延成型的研究主要应用于 Al2O3, ZrO2等少数的氧化物陶瓷,对TiC也有研 究。
0 10 20 30 40
0.55
60
40
0.50
20
0.45
0
0.40
0.0 0.2 0.4 0.6 0.8 1.0 1.2 1.4 1.6 1.8 2.0 2.2
球磨时 间 /h
平均粒径 /μ m
流延成型稳定浆料的制备
在流延成型工艺中,稳定浆料的制备是成型低缺陷高质量陶 瓷坯片的关键。浆料制备过程中产生的缺陷难以通过后续工 艺步骤的调整来消除,粉料颗粒在流延浆料中的分散性和均 匀性直接影响素坯的质量及烧结特性,从而影响烧结致密性、 气孔率和机械强度等一系列特性。因此,在成型过程中,控 制浆料中颗粒的作用力,以便排除团聚体,改善浆料的流变 学性质对于坯体的成型和坯体性质的优化至关重要。为了制 备结构均匀的高固相含量浆料,必须了解粉料颗粒在浆料中 的受力情况,采用合适的评价指标,考察不同分散剂及其用 量、浆料pH值、粘结剂、增塑剂以及球磨时间等因素对浆料 粘度和稳定性的影响规律,为制备稳定分散的浆料提供依据。
流延陶瓷片基元件用途 1陶瓷单层
A电容器 B压电陶瓷 C电子陶瓷
2多层陶瓷部件
A多层平板式传感器 B固体氧化物燃料电池(SOFC)
3.2厚膜成型工艺 陶瓷片基元件总生产流程图
溶剂 陶瓷粉料 分散剂 球磨 增塑剂 粘结剂 混磨 真空除泡 粘度调节 流延成型 干燥
目前得到广泛应用的流延成形工艺为非水基流延成型工艺,即传统的流延工艺,其工艺 包括浆料制备、球磨、脱泡、成型、干燥、剥离基带等工序。该工艺的特点是设备简单, 工艺稳定,可连续操作,生产效率高,可实现高度自动化。
陶瓷流延成型法
流延成型的具体工艺过程是将陶瓷粉末与分散剂、 粘结剂和增塑剂在溶剂中混合,形成均匀稳定悬浮 的浆料。成型时浆料从料斗下部流至基带之上,通 过基带与刮刀的相对运动形成坯膜,坯膜的厚度由 刮刀控制。将坯膜连同基带一起送入烘干室,溶剂 蒸发,有机结合剂在陶瓷颗粒间形成网络结构,形 成具有一定强度和柔韧性的坯片,干燥的坯片连同 基带一起卷轴待用。在储存过程中使残留溶剂分布 均匀,消除湿度梯度。然后可按所需形状切割、冲 片或打孔。最后经过脱脂烧结得到成品。
粉末处理工艺
煅烧温度与球磨时间:球磨工艺不仅减小了平均粒径,而且也使粒 径分布区域变窄。 粒 度 分 析
原始粉料 煅烧 SEM分 析
原始粉 末 1200℃煅烧 1250℃煅烧
100
球磨
烘干
过筛
实验用粉料
0.70
0.65
1200℃煅烧未球磨
煅烧后球磨40h
80
0.60
平均粒径 /μ m
百 分 数 /%
高分子量的聚合物分子(多为二亲共聚物) 以其非溶性基团锚固在固体颗粒的表面, 其可溶性基团向介质中充分伸展,充当 稳定部分,阻碍颗粒沉降,起到稳定浆 料的作用,即空间位阻稳定
空间位阻稳定示意图 Schematic diagram of steric stabilization