2019精品金属压力加工车间设计车间平面布置及立面尺寸化学
新车间平面规划图及说明
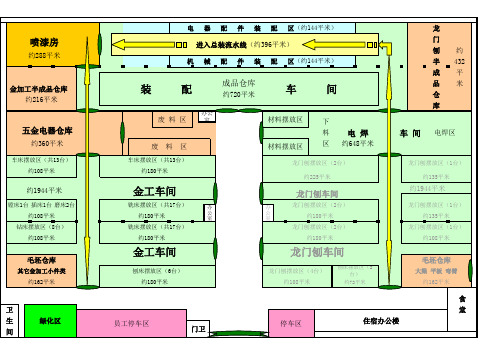
新厂区平面规划图详细说明(个人意见仅供参考)新厂区如何合理利用?不是随意的给他一个地盘,就有他来分配调整!要有统筹安排意识,新厂区的利用不能马虎,要有多个方案的比对研究,确定合理性方案的实施!新厂区的规划要注意以下几个问题:生产布局规划第一、整体决策性:要考虑的是总部如何设立部门!这个方案决定了整个企业的管理程序化问题,能不能改变以往老式的管理观念,就要从这次的整体规划中体现!如:总部要以销售、采购、技术为核心,以此严律销售、管制物资、技术革新、品质监控、售后服务、奠定生产!(属于六加一产业链管理模式),这就决定了新厂区的利用为生产!那就要把成熟的产品、批量生产的产品搬入新厂区!以大产量主导生产;相应的金加工及龙门刨也要搬入!确定新厂区的生产完整性!第二、现场规划性:要考虑的是新厂区的规划长期性、稳定性;这个也尤为重要,一但确定就不要再做轻易的改变!如:当新厂区规划好以后,是否做为长期生产部属,稳定生产产量,再按照现场的实际区域设定厂区布局,必须考虑全面。
上图《新厂区平面规划图》中所显示的分布区域为:金工车间、龙门刨车间、电焊车间、装配车间及金加工半成品仓库、龙门刨半成品仓库、小件类毛坯仓库、大件类毛坯仓库、五金电器仓库、成品仓库和喷漆房等。
第三、设备流程性:厂区布局要根据产品的配套生产性能,生产设备的流程性进行设定摆放,才能够发挥作用,体现出设备流程管理的最大优势。
金工车间生产区主要以生产小件类为主,根据设备流程性能及产能,配相应产量(生产计划)进行小件类量化管理;龙门刨车间生产区主要以生产大件类为主,也可以根据设备流程性能及产能,配相应产量(生产计划)进行大件类量化管理;这些生产都服务于装配流水线!电焊车间也一样控制相应产量,服务整体流水线的合理生产!新厂区、新开端、新流程、新观念,为了改变现在混乱的局面,这个才是我们公司崭新的要点!第四、管理程序性:以上图《新厂区平面规划图》中所显示:龙门刨车间的大件类可从南丰铸件车间直接推过来,进入计划生产;施行生产领料制,金工车间的小件类由外协直接运至小件毛坯仓库进行计划领料生产,大件类以相同的方式进行合理生产;当金工、龙门刨车间按计划生产好的配件成品进入相应的半成品仓库后,再由装配按计划控制半成品出库量;整体以生产目标制按计划进行相应配件产品的生产,按计划领料生产控制所有设备进行量化管理,以此达到生产管理目标制!第五、生产流水线性:首先由毛坯件作为流水线的开始,大件类进入龙门刨车间进行量化生产(计划生产量、设备定值量(生产领料量)、最大产能量、目标控制量等),电焊车间将焊好的脚架同样在龙门刨车间刨好后进入总装流水线,作为总装流水线的第一道工序;金工车间小件类与龙门刨车间生产同步进行生产,同样进行量化生产,当金工车间产品配件生产一批结束后,进入机械配件装配区进行配件装配,当机械配件装配结束,总装流水线的第一道工序也已完成,然后进入第二道机械装配,第二道工序结束后进入第三道电机装配,第四道电器装配,第五、第六道等,最后进入道喷漆工序,喷漆批灰可以在第一道完成后进行!注:整道工序还待确定!总装流水线适用于除圆弧机(超大型)以外的任何机型!它可以减少人员、质量稳定、快速生产、提高产能。
金属压力加工车间设计车间设计概述

对金属压力加工车间的废弃物进行分类收集和处理,可回收利用的 废弃物应进行回收利用。
废弃物处置
对于不可回收利用的废弃物,应按照相关规定进行安全处置,避免 对环境造成不良影响。
废弃物管理制度
建立完善的废弃物管理制度,明确废弃物的分类、收集、运输和处理 等环节的责任和要求。
06
金属压力加工车间设计 案例分析
设计案例三:某铜加工企业轧制车间设计
总结词
灵活性、可持续性
详细描述
该轧制车间设计充分考虑了生产灵活性的需求,可根据市场 需求调整产品规格和产量。同时,设计注重可持续性,采用 了资源回收、能源再利用等措施,降低生产成本和环境影响 。
谢谢观看
安全原则
确保操作安全
设计时应充分考虑操作过程中的 安全问题,如设备布局、操作空 间、安全防护措施等,以降低操 作风险。
预防事故发生
通过合理的设计,减少事故发生 的可能性,如设置紧急出口、安 全警示标识等。
效率原则
提高生产效率
优化设备布局,减少物料搬运距离, 提高生产流程的连续性和自动化程度 。
降低能耗
直接挤压机
将加热好的坯料放入挤压筒中,通过挤压轴施加 压力,使坯料通过模具挤出成所需断面形状的制 品。
反向挤压机
挤压轴施加的压力与坯料进入挤压筒的方向相反, 使坯料在挤压过程中受到较大的摩擦力,制品精 度较高。
连续挤压机
采用连续挤压工艺,可实现连续、高效的生产, 主要用于铝、铜等有色金属的挤压加工。
废气排放标准
02
确保废气排放符合国家和地方的环境标准,定期监测废气中的
污染物浓度,确保达标排放。
废气处理效率
03
提高废气处理设备的效率,减少有害物质的排放量,降低对环
精选压力加工车间设计方案

[时间]/[产品]
生铁(万吨)
粗钢(万吨)
钢材(万吨)
大型型钢(万吨)
中小型型钢(万吨)
钢筋(万吨)
盘条(线材)(万吨)
热轧薄板(万吨)
中厚宽钢带(万吨)
无缝钢管(万吨)
2001年
1ห้องสมุดไป่ตู้,554.25
15,163.44
16,067.61
226.17
663.09
3,109.71
1.2.2 总图运输
1.2.2.1 总图 总图——总平面布置——车间相互位置的关系。 从总图上可以了解企业内各车间和构筑物间的相互关系、所在位置、地形和方位,运输方法和距离等。 1. 企业的组成 生产车间:生产主线;指直接生产各种加工产品的 车间. 如 型材,管材,板带,棒线生产车间,锻造件 及模压件生产车间等。
1.4.1 主要任务
(2)组织任务 研究车间生产劳动组织,确定职工人数及编制,制定劳动定额等。(3)经济任务 计算及制定基本建设投资额,生产预算,计划单位产品成本及综合技术经济指标等。
1.4.2 工艺说明书的编制
设计说明书——重要的设计文件。1. 总论——原则说明以下问题(1)车间设计年产量、钢与合金的品种、规格和范围等。(2)原料、材料、动力、燃料来源,市场情况。(3)本车间与同类车间比较具有那些特点——设计特点。(4)车间劳动组织、建设投资,经济效益和社会效益。(5)目前建设的内容和远景发展规划。
满足生产操作及安全要求;节省投资:做到技术上可行,经济上合理;施工方便,留有发展余地。
1.2.2 总图运输
企业外运——原辅材料、燃料、成品; (运输方式主要有铁路、水路、公路)企业内运——原辅材料、燃料、半成品、成品、废料、废渣等。(内运主要有辊道、行车、运输 小车、升降设备等)综合性的大、中型加工企业的运输量相当大,一般是年产量的3~4倍。
2019精品金属压力加工车间设计环境保护化学
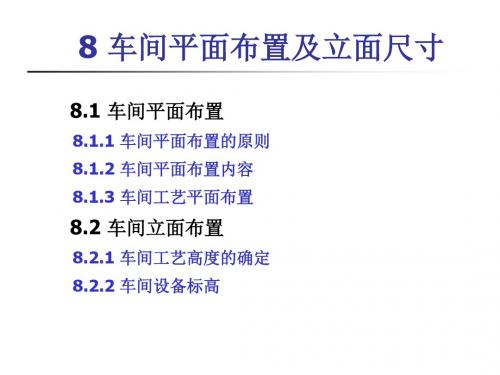
8.1 车间平面布置
8.1.1 车间平面布置的原则 8.1.2 车间平面布置内容 8.1.3 车间工艺平面布置
8.2 车间立面布置
8.2.1 车间工艺高度的确定 8.2.2 车间设备标高
8.1 车间平面布置
车间平面布置:
主要指设备和设施按选定的生产工艺流程确定平 面位置,平面布置的合理与否对于:
3#A 3#B 4#
吐丝机 Laying Head
水箱
Water Boxes
夹送辊
Pinch Roll
STELMOR冷却线 STELMOR Cooling Line
集卷 Reform Station
往P/F线 to P/F Line
H型钢轧制 工艺流程图
宝钢5m宽厚板轧机工艺平面布置图
1
8
16
17 18
柱距——相邻两柱间的中心距——常用标准柱距6、9、 12、24m。
长度——取决于工艺布置,车间占地面积。
8.1.3 车间工艺平面布置
2、车间工艺平面布置的绘制(参见P187~204) ① 图纸幅面: 0#、1#、2#、3#、4# ② 图面的一般规定 ③ 施工设计工艺平面布置图规定 ④ 图例
8.1.2 车间平面布置内容
3. 车间内通路的布置
1) 车间主要通路:车间内部运输通路,如电气台车通路, 过跨小车等;
2) 车间次要通路:用于运输材料、备品备件、设备检修 及仓库场地的通路等。如成品库内设火车通路,车间 的端面或侧面开设大门,作为汽车通路等。
3) 人行通路及防火通路.
8.1.2 车间平面布置内容
8.1.3 车间工艺平面布置
3.车间组成
通常由原料跨,加热炉跨,主轧跨,精整跨和成品跨组 成,外加轧辊、导卫加工跨,有的车间还有专门的主 电机跨。 跨间布置——取决于工艺流程,轧机组成及地形条件 等。 (1)“丁”字形布置:原料与成品跨与主轧跨垂直布 置。
标准化加工车间平面布置图(草稿)

中天建设集团西南公司项目工厂化车间标准当前的建筑施工管理仍显粗放,老一辈技术工人身上的计算、策划能力,对工序的严谨,对质量的较真的态度,既很少在新一代“建筑工人”的身上得到遗传,也很少在管理人员中得到继承。
现实中靠工人“素质”实现施工效率和质量稳定显得十分的困难。
那么在全民质量意识觉醒之前,在建筑行业工业化拼装时代来临之前,构件(材料)的工厂化加工和作业面的流水施工这一“工业化管理模式”的应用,应该是当前提高施工效率和产品质量的有效方法之一。
工厂化加工,是施工现场标准化施工的一个环节,在工厂化加工的流程中,上游是施工各环节原材料或半成品的标准化、量化,下游是作业面施工的程序化、局部拼装化,最终要解决的是在劳动力紧缺、素质下降的整体环境下,如何提高施工效率,稳定的提供高质量的建筑产品。
工厂化加工的范围可结合不同工程类型,不同施工工艺有针对性的开展,在施工过程中需设立了五个标准化加工车间,五个标准加工车间共同的特征是:设立固定的原材料堆放区和加工车间;配备专用的加工设备和辅助设施;设立专门的加工岗位和人员;最后也是最重要的是结合作业面工序的分解,识别、量化了实施工厂化加工的构件(材料)。
注:根据项目场地的实际情况,加工车间可放置在施工楼层内。
标准化的施工深化图一、一、标准化的施工深化图1、模板配模及下料:分顶板模板配模图和木模施工的梁、飘板、横竖向线条配模图。
2、钢筋加工及绑扎:钢筋加工和料单,按单位范围原料分类别堆放,采用吊笼吊装;定型化吊笼焊制6只。
小型构件加工车间现场厨卫间下沉板支模应用3、填充墙体:先绘制砌体组砌图;再根据砌体组砌图绘制电源管配管图;根据电源管布置确定包管配砖做法中的砌体切割砖。
4、管道井二次深化排列图:原设计电子版图纸和二次深化管线排列图。
项目管道井平面布置图二、标准化的加工车间木工加工车间一)一)木工加工车间配备精密木工加工车一台,通过前期计算,对所有梁、板模板按部位进行下料,对非标板材进行了统筹利用,实现两大功能:一是作业面模板的统一下料和集中领用;二是利用余料废料统一加工土建、水电班组的各类预埋箱盒。
年产25000吨铝型材挤压车间工艺设计.doc

年产25000吨铝型材挤压车间工艺设计一、绪论随着时代的进步,材料的应用也发生着变化。
因铝合金铝合金型材具有强度高、重量轻、稳定性强、耐腐蚀性强、可塑性好、变形量小、无污染、无毒、防火性强,使用寿命长(可达50—100年),回收性好,可回炉重炼等优点,应用受到日益关注。
尤其在建筑方面,铝合金型材现已广泛应用于各种商业及民用建筑,有着不可替代的重要地位。
而在铝合金型材中应用最广泛的就是6063铝合金。
6063铝合金的成份位于Al—Mg2Si—Si的三相区,它的主要合金组元是Mg和Si,而且Mg和Si首先形成Mg2Si相,淬火状态和自然时效状态都有很高的塑性。
人工时效的 6O63台金挤压材,抗拉强度为 240MPa,屈服强度为 220MPa,延伸率为 l1%。
该合金可以在高温下进行高速变形,由于其淬火敏感性低,可以在挤压机上直接风冷淬火。
生产的制品表面光洁,可省去专门的抛光工序。
能进行各种颜色的阳极氧化着色。
由于该合金主要用于建筑、装饰等,所以对 Fe、Cu等杂质元素的控制较为严格,以保证其抗蚀性。
另外,在可热处理强化的合金中,其可焊性属于上等,可以铁焊、气焊、电阻焊,电弧焊。
本次铝型材挤压车间工艺设计采用6063铝合金进行挤压生产。
二、本次设计的意义本次课程设计任务是完成年产量不少于5000吨的挤压车间工艺设计,通过设计可以加深我对挤压车间整个生产流程的认识以及对铝合金性能、生产工艺、挤压设备等有更加深入的了解。
这次课程设计还让初次感受到要创办一间工厂需要考虑多方面的因素(如设备的选购、生产工艺的安排及其具体参数、人员及工作时间的分配等),从中锻炼了我考虑问题的周密性,使我在以后的工作中更加地细致。
因此,本次课程设计对于大四的毕业生来说有着重要的意义。
三、生产任务1.本车间任务本次设计的任务是完成年产量不少于5000吨的挤压车间工艺设计,完成的型材的品种有:幕墙、纱窗、卷廉门和扣板材。
所用的挤压材料是6063铝合金。
化工设计竞赛4-车间平立面图
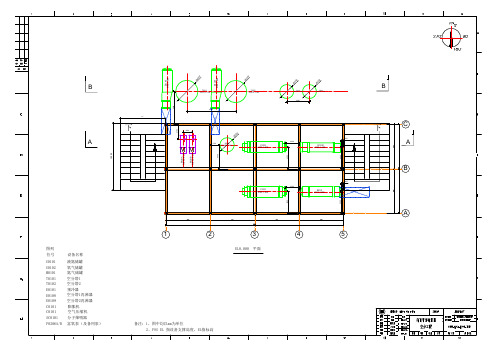
8000
下
A
E0108 Ø EL 1.800
6000
2700
检修区 检修区
0 0 0 4 Ø
T0101 POS EL 1.000
9000
E0109
Ø EL 1.800
0 0 0 4 Ø
T0102 POS EL 1.000
1600
MM
0 0 5 2
Ø
1700
S0101
POS EL 1.500
C0103 Ø EL 1.800
2、POS EL 指设备支撑高度,EL指标高
ERSITY
湘
图列 位号 S0102 M0101 T0101 T0102 E0108 E0109
设备名称 氧气储罐 氮气储罐 空分塔1 空分塔2 空分塔1再沸器 空分塔2再沸器
EL 2.700
E0108
EL 0.200
T0201 T0201
EL 32.000 EL 31.000
8000
8000
8000
1
2
3
4
EL6.000 平面
C
下
A
B
A
A
5
ERSITY
湘
检修区 检修区 检修区 检修区
图列
位号
设备名称
E0102
换热器
TAN UNIV
E0103
换热器
潭大
E0104
换热器
E0105
换热器
备注:1、图中均以mm为单位
2、POS EL 指设备支撑高度,EL指标高
10000 E0106 Ø EL 13.800 E0107 Ø EL 13.800
XIANG
学
金属压力加工车间设计01 车间设计概述

编制详细的施工说明,包括施工方法、材料选用、施工注意事项等, 确保施工质量符合设计要求。
03
车间设计的要素
工艺流程设计
工艺流程设计
根据产品需求和生产工艺要求,合理规划生产流 程,确保生产过程高效、顺畅。
工艺流程图绘制
使用流程图等工具,清晰地展示生产过程中的各 个工序和操作步骤。
工艺流程优化
生产能力的适应性
车间设计应考虑生产能力 的需求,合理配置设备和 人员,提高生产效率。
安全性原则
作业安全
车间设计应充分考虑作业 安全,合理配置安全设施, 如防护栏、安全门、报警 装置等。
设备安全
设备设计应符合安全标准, 确保操作人员在使用过程 中不会发生意外伤害。
消防安全
车间应设置合理的消防通 道和消防设施,提高应对 火灾等突发情况的能力。
环保设施
配备相应的环保设施,如废气处理装置、噪音控制设备等,确保生 产过程符合环保要求。
安全与环保培训
对员工进行安全与环保培训,提高员工的安全意识和环保意识。
人机工程学考虑
工作台设计
根据人体工学原理,合理设计工作台的高度、倾斜度等,提高员工 操作舒适度。
照明设计
选用适当的照明设备和灯具,保证工作区域的照明质量,减轻员工 眼睛疲劳。
02
根据生产需求,设计合理的工艺流程,确定设备布置和工艺管
道走向。
建筑结构设计
03
进行车间的建筑结构设计,包括主体结构、承重体系、维护结
构等,确保结构安全、经济合理。
施工图设计
详细设备布置
根据初步设计的总体布局和工艺流程,进行设备的具体布置设计, 明确设备型号、规格、安装位置等。
施工图纸绘制
金属压力加工车间设计生产方案选择

酸、碱或化学处理过程中的溶解损失。 与材质,处理液,表面积和处理工艺等有关。 钢的溶损比有色金属大,通常为:0.3~2%。
(3)切损:
切头尾和切边等几何废料损失(含切试样)。 与坯料种类、规格、材质、交货状态(定尺或非定 尺)和轧制方法及工艺装备水平有关。
3.2 金属平衡表的编制
(3)切损:
关,通常为1%左右。
普碳<1% 合金钢:1%~3%
3.2 金属平衡表的编制
2. 确定综合成材率的方法
通常调研国内外同类厂家近三年实际生产报表 的基础上,结合本设计的工艺装备状况取“平 均先进水平”。
在编制平衡表时,通常先确定各品种的综合成 材率,再确定原料量,然后按各废品损失比例 确定各废品损失量,最后按原料总量,成品总 量以及各废品总量算出总的成材率和各项损失 比。
在全国范围内统一的标准,用代号“GB”表示。 部颁标准 指国家标准中暂时未包括的产品标准和其他
技术规定,或只用于本专业范围内的标准。YB 企业标准 指在尚无国家标准和部颁标准的情况下由企
业制定的标准。QB
3.1 生产方案选择
4. 产品标准和技术条件
内容包括—— 规格标准;性能标准;试验标准;交货标准。
无缝管生产工艺
5) 钢管生产方案
热轧无缝管生产方法——
自动式轧管机组,皮尔格轧管机组,连续式轧管机组, 狄舍尔轧管机组, 三辊轧管机组等。
挤压——薄壁,质量好,生产率低,成本高,消耗 大。
5) 钢管生产方案
埋弧直缝焊管
2) 焊管:直缝连续焊;螺旋焊;UOE直缝焊。 焊管以带钢卷或钢板为坯料,采用不同的方法焊 接而成。 工序:
生产工艺流程: 坯料加热轧制冷却剪切矫直检查包装入库
第8章+车间平面布置ppt课件
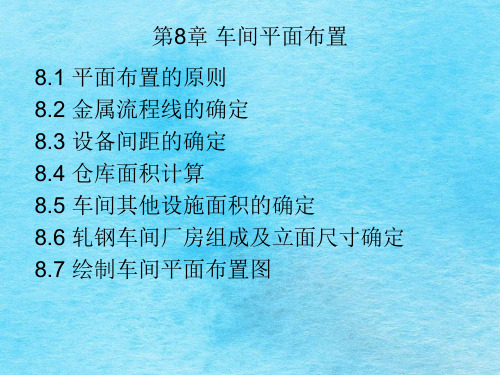
8.3 设备间距的确定
设计车间平面布置图时,首先要做出包 括主要生产工段、辅助生产工段、仓库、 实验室、动力系统、生活间及办公室等部 分在内的平面布置图,而且同时要做几个 方案加以比较分析,最后确定一个较好的 方案。生产设备布置没有一定的规定。
7〕剪切设备至冷床的距离取决于剪切后轧 件的最大长度,一般冷床直接安放在剪切 设备之后,而且在冷床能力大于锯切机能 力情况下,通常可采用稍大于定尺后轧件 最大长度。但当小型型材定尺长度很长时, 剪切设备至冷床的距离要小得多,只要很 好考虑有足够的操作面积和较好的劳动条 件就可以。
8〕车间内通路的布置
第8章 车间平面布置
8.1 平面布置的原则 8.2 金属流程线的确定 8.3 设备间距的确定 8.4 仓库面积计算 8.5 车间其他设施面积的确定 8.6 轧钢车间厂房组成及立面尺寸确定 8.7 绘制车间平面布置图
车间平面布置主要指设备和设施按选 定的生产工艺流程确定平面位置,平面布 置的合理与否对于设备生产能力的发挥、 工人操作安全、生产周期的长短及生产率 的高低有着很大的影响,在平面布置时应 当从实际出发求得最大合理的布置。
(5〕考虑将来的发展,要留有余地。
8.2 金属流程线的确定
金属流线指生产各类产品由原料到成品 的工艺流程线,把所选定的设备与设施布 置在相应工序的工艺流程线上,同时要考 虑中间的堆料场地以及运输等。
常用的金属流程线如图8-1所示。
1〕直线式
从生产的连续性及运输等方面看是最合 理的。因此,常用于连轧机以及初轧机等。 但这种生产流程受到厂房的长度限制,因 为厂房愈长所铺设的管道也愈长,故经济 上是不合理的,建设投资要大, 一般认为 厂房最好不超过500米长。
金属压力加工车间设计生产方案选择
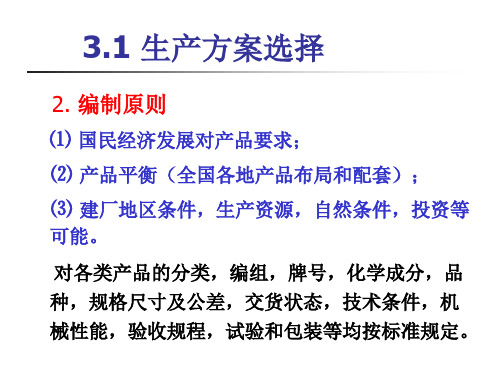
普碳<1% 合金钢:1%~3%
3.2 金属平衡表的编制
2. 确定综合成材率的方法
通常调研国内外同类厂家近三年实际生产报表 的基础上,结合本设计的工艺装备状况取“平 均先进水平”。
在编制平衡表时,通常先确定各品种的综合成 材率,再确定原料量,然后按各废品损失比例 确定各废品损失量,最后按原料总量,成品总 量以及各废品总量算出总的成材率和各项损失 比。
产品 名称
产品方案表
钢种
规格 代表 mm 规格mm
年生产计划
t/a
%
金属平衡表
轧 机及产
钢锭
品名称
t%
原料
成品
初轧坯 连铸坯 钢坯 钢材
t %t % t % t %
废料
切头及 烧损 废品 t %t %
3.1 生产方案选择
3. 计算产品的选择
有代表性——产量大,品种、规格、状态、工艺特点 均具有代表性;
3.2 金属平衡表的编制
(1)烧损:
金属在高温状态下的氧化损失(含炉内及成型过 程的二次氧化)。与材质,坯料种类,炉型和加 热制度等有关。 钢的烧损比有色金属大,通常为0.5~3%,对于 推钢式炉加热钢锭为2~3%;连铸坯为1~2%; 步进式炉加热炉连铸坯(钢坯)为0.5~1.5%。
3.2 金属平衡表的编制
无缝管生产工艺
5) 钢管生产方案
热轧无缝管生产方法——
自动式轧管机组,皮尔格轧管机组,连续式轧管机组, 狄舍尔轧管机组, 三辊轧管机组等。
挤压——薄壁,质量好,生产率低,成本高,消 耗大。
5) 钢管生产方案
埋弧直缝焊管
2) 焊管:直缝连续焊;螺旋焊;UOE直缝焊。 焊管以带钢卷或钢板为坯料,采用不同的方法焊 接而成。 工序:
- 1、下载文档前请自行甄别文档内容的完整性,平台不提供额外的编辑、内容补充、找答案等附加服务。
- 2、"仅部分预览"的文档,不可在线预览部分如存在完整性等问题,可反馈申请退款(可完整预览的文档不适用该条件!)。
- 3、如文档侵犯您的权益,请联系客服反馈,我们会尽快为您处理(人工客服工作时间:9:00-18:30)。
8.1.2 车间平面布置内容
6) 过渡式——用于布置多台相同设备的车间,如精整线。 7) 分枝式——用于主设备不多而品种规格多的车间。
将相同或相似的工艺过程组合,如管、棒、型车间可 以分管材生产线及型棒生产线等。
8.1.2 车间平面布置内容
8.2.1 车间工艺高度的确定
吊车轨面标高(H)—— 地面(±0.0)至吊车轨道面的高度。 其取决于设备高度,检修和操作所需要的空间, 吊车类型及被吊物件的尺寸,车间通风及照明要 求和车间投资等。 当H↑,厂房越高,通风照明条件越好,投资↑。
8.2.1 车间工艺高度的确定
在车间吊车要越过的最高设备高度已知情况下则:
23
4
56
7
9 10 11 12
13
14
15
1.板坯二次切割线;2.连续式加热炉;3.高压水除鳞箱;4.精轧机;5.加速冷却装 置; 6.热矫直机;7.宽冷床; 8.特厚板冷床; 9.检查修磨台架; 10.超声波探 伤装置; 11.切头剪; 12.双边剪和剖分剪; 13.定尺剪;14.横移修磨台架; 15.冷矫直机; 16.压力矫直机; 17.热处理线; 18.涂漆线
车间设备标高—— 设备工作面标高,一般以轧制线标高为基准。
其取决于: 1. 工艺要求——无缝管车间运输靠管子自由滚动,故每个
设备标高各异。 2. 检修方便——辊道高出车间地面。 3. 操作方便——平均身高——操作面高度 600~800mm。
H=h1+h2+h3+h4+h5
h1——自地坪算起在吊车行走范围内最高设备或其他物件; h2——被吊物件与最高设备间的安全距离,取400~500mm h3——被吊最大物件的高度,例如集装箱高度; h4——吊具高度; h5——吊钩极限位置至轨面距离。
P206:各车间具体高度。
8.2.2 车间设备标高
柱距——相邻两柱间的中心距——常用标准柱距6、9、 12、24m。
长度——取决于工艺布置,车间占地面积。
8.1.3 车间工艺平面布置
2、车间工艺平面布置的绘制(参见P187~204) ① 图纸幅面: 0#、1#、2#、3#、4# ② 图面的一般规定 ③ 施工设计工艺平面布置图规定 ④ 图例
“丁”字形布置对于主轧跨的采光,通风; 原料和成品跨行车利用; 轧辊导卫间、主电室、水处理等其他辅助设施的布置 上都优于平行跨布置。 原料和成品运输如果采用平行跨更为方便。
8.2 车间立面布置
根据工艺要求确定车间的工艺高度和所有设备 工作面高度,为建筑设计者进行厂房剖面,立 面设计提供参数,并为设备基础和安装提供依 据。
8.1.2 车间平面布置内容
2) 直线横移式——与(1)类同,利用管材自由滚动, 多用于管材车间及型材车间的冷床布置。
3) 曲折式——占地小,投资较小;用于厂房长度受 限,跨间较多的中小型车间。
8.1.2 车间平面布置内容
4) 放射式——用于一个机组加工后半成品进入两个 或两个以上相同机组继续加工的车间,如高速线 材轧机。
8.1.3 车间工艺平面布置
3.车间组成
通常由原料跨,加热炉跨,主轧跨,精整跨和成品跨组 成,外加轧辊、导卫加工跨,有的车间还有专门的主 电机跨。 跨间布置——取决于工艺流程,轧机组成及地形条件 等。 (1)“丁”字形布置:原料与成品跨与主轧跨垂直布 置。
8.1.3 车间工艺平面布置
(2)平行跨布置:原料与成品跨与主轧跨平行布置。
4. 仓库设施的布置 原 则
1) 物流畅通,便于运输,原料库与成品库可布置在车间头 尾或同跨。可“丁”字形布置或平行布置——取决于地形, 原料(或成品)厂,运输方式。 2) 仓库面积保证正常生产,避免因“空库”或“涨库”而 停工。 3) 应考虑仓库的利用系数——安全通道,吊运不到的面积, 检修,标记,包装,清理面积。 4) 垛高不超过地坪负荷。 5) 其他方面的特殊要求及经济核算(如称量)等。
8 车间平面布置及立面尺寸
8.1 车间平面布置
8.1.1 车间平面布置的原则 8.1.2 车间平面布置内容 8.1.3 车间工艺平面布置
8.2 车间立面布置
8.2.1 车间工艺高度的确定 8.2.2 车间设备标高
8.1 车间平面布置
车间平面布置:
主要指设备和设施按选定的生产工艺流程确定平 面位置,平面布置的合理与对于:
通常,由于由原料至成品生产的工序多,流 程长,设备复杂,一种布置形式很难满足生 产工艺的要求,因此大多数根据工艺要求采 用组合形式。
8.1.2 车间平面布置内容
2. 生产设备布置 车间平面布置图包括主要生产工段,辅助生产工
段,仓库,实验室,动力系统,生活间和办公室 等。 车间工艺平面布置则包括主、辅生产工段和仓库 等。 对于平面布置,应做几个方案,经比较后确定一 个较好的方案。
3#A 3#B 4#
吐丝机 Laying Head
水箱
Water Boxes
夹送辊
Pinch Roll
STELMOR冷却线 STELMOR Cooling Line
集卷 Reform Station
往P/F线 to P/F Line
H型钢轧制 工艺流程图
宝钢5m宽厚板轧机工艺平面布置图
1
8
16
17 18
8.1.2 车间平面布置内容
原料库面积 (F) 计算
式中:
F = 24AnKt / K1QH
A——主设备平均小时产量t/h;
Kt——金属消耗(投料量)系数 Kt=1 / 成材率
K1——仓库利用系数,轧机:K1=0.7, 有色金属:K1=0.4; n——存放天数,一般7~10天,通常按大、中修考虑,直接轧制, 热装酌减。
H——堆放高度m,与坯料种类,规格,吊车型式有关,见表8-3。
Q——单位空间存放量t/m3,与坯料种类规格有关。
8.1.2 车间平面布置内容
8.1.2 车间平面布置内容
成品库面积 (F) 计算
计算公式和原料库面积相同,但:
1)Kt=1 2) K1: 钢: K1=0.7;有色金属:K1=0.35~0.4 3)n: 钢材公司有库 n=5~7天,无库n=7~10天; 有色金属 n=15天。 4)H参见表8-4
4. 节省投资,并为将来发展留有余地。
8.1.2 车间平面布置内容
1. 金属流线的确定 金属流线——生产各类产品由原料到成品的工艺 流程线。 把所选定的设备与设施布置在相应工序的工艺流 程线上,同时要考虑中间的堆料场地以及运输等。
8.1.2 车间平面布置内容
常用的金属流程线: 1) 直线式——金属流线畅通,操作方便;厂房长, 占地大,管线敷设长投资大; 从生产的连续性及运输等方面看是最合理的。主 要用于连轧机,初轧机,中厚板轧机。一般不超 过500m长。
8.1.2 车间平面布置内容
3. 车间内通路的布置
1) 车间主要通路:车间内部运输通路,如电气台车通路, 过跨小车等;
2) 车间次要通路:用于运输材料、备品备件、设备检修 及仓库场地的通路等。如成品库内设火车通路,车间 的端面或侧面开设大门,作为汽车通路等。
3) 人行通路及防火通路.
8.1.2 车间平面布置内容
加热炉区 Furnace Area
粗轧机组 Roughing Mill
中轧机组 Intermediate Mill
保温辊道
Insulated Roller Table
夹送辊
Pinch Roll
预精轧机组 Prefinishing Mill
侧活套 Sidelooper
1H 2V 3H 4V 5H 6V
靠主跨厂房的一侧。 4)生产设备的间距除了考虑工艺要求外,还要考虑安装操作、
检修等要求。 5)轧制中心线布置应考虑保证操作侧有足够的操作空间.
8.1.2 车间平面布置内容
6)设备离厂房的两端和两边柱脚应留出一定距离,以便吊运, 安装,检修。
7)操作室,生活间,控制室等辅助设施应尽量布置在两跨之间 或两端。
C&C剪
C&C Shear
7H 8V 9H 10V 11H 12V
13H 14V
立活套 Uploopers
精轧机组 Finishing Mill
2#A 2#B
水箱
Water Box
C&D剪 C&D Shear 侧活套 Sidelooper
水箱 Water Boxes
减定径机 Reducing and Sizing Mill
8.1.2 车间平面布置内容
5. 其他设施的布置 操纵台位置确定原则:
面积大小和位置主要根据操作人员的工作条件和设备的 机械化自动化程度的高低来决定: 位置靠近被控设备中心。节省导线,便于观察—≯15
米 共用操纵台——被控设备中部或偏向主要设备; 不占车间的有效面积——无特殊要求时布置在柱列间。
8.1.2 车间平面布置内容
8.1.2 车间平面布置内容
中间库面积 (F) 计算
F = ATK/q
式中: A——该机组平均日产量, t/天; T——生产周期时间,天; K——主设备与各精整设备产量不平衡系数; q——单位面积平均堆放量 t/m2, 取成品库1/2。 实际上,中间仓库钢材的储存量可以考虑按轧机3~5天的平均日产量 计算。对于合金钢厂可按轧机的8~10天的产量计算。有色金属中间 再制料堆放天数为2~3天,面积利用系数为0.40
8.1.2 车间平面布置内容
宝钢初轧产线工艺流程
初轧产线工艺流程
钢锭 均热 钢锭称量 1#初轧 2#初轧
热火焰清理
剪切
钢坯称量
板、大方、矩 形材的精整
6VH连轧
飞剪 热锯
冷床冷却