铜化学抛光剂配方分析
铜抛光剂配方配比
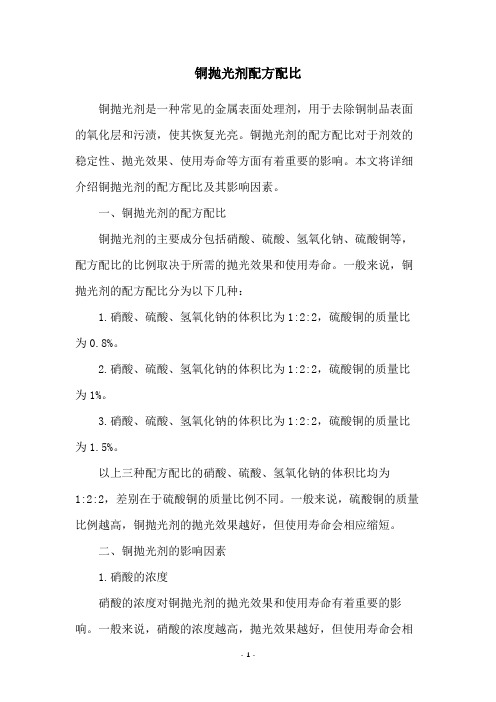
铜抛光剂配方配比铜抛光剂是一种常见的金属表面处理剂,用于去除铜制品表面的氧化层和污渍,使其恢复光亮。
铜抛光剂的配方配比对于剂效的稳定性、抛光效果、使用寿命等方面有着重要的影响。
本文将详细介绍铜抛光剂的配方配比及其影响因素。
一、铜抛光剂的配方配比铜抛光剂的主要成分包括硝酸、硫酸、氢氧化钠、硫酸铜等,配方配比的比例取决于所需的抛光效果和使用寿命。
一般来说,铜抛光剂的配方配比分为以下几种:1.硝酸、硫酸、氢氧化钠的体积比为1:2:2,硫酸铜的质量比为0.8%。
2.硝酸、硫酸、氢氧化钠的体积比为1:2:2,硫酸铜的质量比为1%。
3.硝酸、硫酸、氢氧化钠的体积比为1:2:2,硫酸铜的质量比为1.5%。
以上三种配方配比的硝酸、硫酸、氢氧化钠的体积比均为1:2:2,差别在于硫酸铜的质量比例不同。
一般来说,硫酸铜的质量比例越高,铜抛光剂的抛光效果越好,但使用寿命会相应缩短。
二、铜抛光剂的影响因素1.硝酸的浓度硝酸的浓度对铜抛光剂的抛光效果和使用寿命有着重要的影响。
一般来说,硝酸的浓度越高,抛光效果越好,但使用寿命会相应缩短。
因此,在制备铜抛光剂时,应根据所需的抛光效果和使用寿命选择合适的硝酸浓度。
2.硫酸的浓度硫酸的浓度对铜抛光剂的稳定性和使用寿命有着重要的影响。
一般来说,硫酸的浓度越高,铜抛光剂的稳定性越好,但使用寿命会相应缩短。
因此,在制备铜抛光剂时,应根据所需的使用寿命选择合适的硫酸浓度。
3.氢氧化钠的浓度氢氧化钠的浓度对铜抛光剂的抛光效果和使用寿命有着重要的影响。
一般来说,氢氧化钠的浓度越高,抛光效果越好,但使用寿命会相应缩短。
因此,在制备铜抛光剂时,应根据所需的抛光效果和使用寿命选择合适的氢氧化钠浓度。
4.硫酸铜的质量比硫酸铜的质量比对铜抛光剂的抛光效果和使用寿命有着重要的影响。
一般来说,硫酸铜的质量比越高,铜抛光剂的抛光效果越好,但使用寿命会相应缩短。
因此,在制备铜抛光剂时,应根据所需的抛光效果和使用寿命选择合适的硫酸铜质量比。
铜电解抛光药水配方
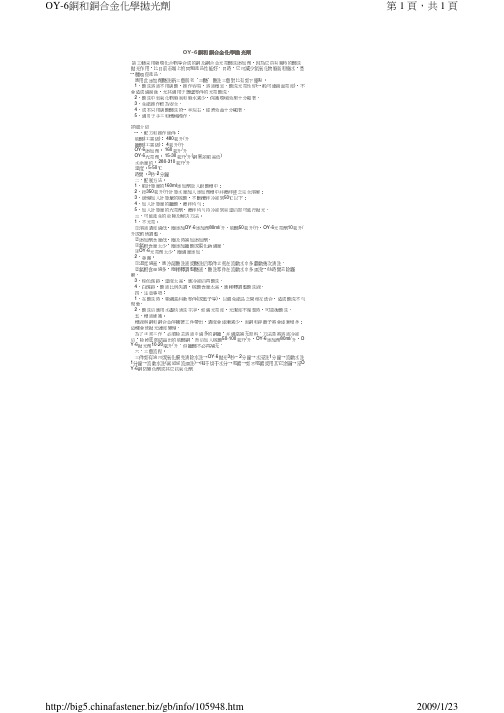
OY-6銅和銅合金化學銅和銅合金化學拋拋光劑該工藝采用雜環化合物等合成的銅及銅合金光亮酸洗添加劑,因為它具有獨特的酸洗拋光作用,比目前市場上的同類產品性能好。
同時,它可減少氮氧化物廢氣和廢水,是一種環保產品。
應用此添加劑酸洗新工藝與老“三酸”酸洗工藝對比有如下優點:1、酸洗溶液不用硝酸,操作容易,溶液穩定。
酸洗光亮性好(一般可達鏡面亮度),不會造成過腐蝕,尤其適用于薄壁零件的光亮酸洗。
2、酸洗中氮氧化物廢氣和廢水減少,保護環境效果十分顯著。
3、生產操作較為安全。
4、成本只用硝酸酸洗的一半左右,經濟效益十分顯著。
5、適用于手工和機械操作。
詳細介紹一、配方和操作條件:硫酸(工業級): 480毫升/升鹽酸(工業級): 4毫升/升OY-6添加劑: 160毫升/升OY-6光亮劑: 15-30毫升/升(銅質差取高值)水余量約: 280-310毫升/升溫度:5-50℃時間:3秒-2分鐘二、配制方法:1、取計算量的160ml 添加劑放入耐酸槽中;2、按350毫升/升計算水量加入添加劑槽中并攪拌使之完全溶解;3、緩慢加入計算量的硫酸,不斷攪拌冷卻到50℃以下;4、加入計算量的鹽酸,攪拌均勻;5、加入計算量的光亮劑,攪拌均勻待冷卻到室溫后即可進行拋光。
三、可能產生的故障及解決方法:1、不光亮:①溶液濃度過低,應添加OY-6添加劑80ml/升、硫酸50毫升/升,OY-6光亮劑10毫升/升或酌情調整。
②添加劑含量低,應及時補加添加劑。
③氯根含量太少,應添加鹽酸或氯化鈉適量。
④OY-6光亮劑太少,應適量添加。
2、發霧:①溫度過高,應冷卻酸洗液或酸洗后零件立刻在流動水中多翻動幾次清洗。
②氯根含量過多,應稀釋調整酸液,酸洗零件在流動水中多漂洗一些時間去除霧膜。
3、棕色斑跡,溫度太高,應冷卻后再酸洗。
4、白斑跡,酸液比例失調,硫酸含量太高,應稀釋調整酸洗液。
四、注意事項:1、在酸洗時,要適當抖動零件(或籃子等),以避免產品之間相互迭合,造成酸洗不勻現象。
铜及铜合金化学及电化学抛光

铜及铜合金化学及电化学抛光:化学抛光(1)普通型化学抛光溶液配方及工艺规范见表1。
(2)清洁型化学抛光溶液①工艺流程。
上夹具一超声波脱脂一热水洗一三级逆流漂洗一除膜一化学抛光一流动水洗一无铬钝化一流动水洗一封闭干燥一成品下架。
②清洁型化学抛光溶液配方及工艺规范硫酸(H2S04)450mL/L表1铜及铜合金化学抛光工艺规范配方工艺规范12345硫酸(H2S04,密度1.84g/mL)/(mL/L)250~280400~500硝酸(HN03,密度1.50g/mL,质量分数)/%40~50 mL/L106~829.5~6.440~60g/L磷酸(H3P04,密度1.70g/mL,质量分数)/%5440~5070.5~95.6冰醋酸(CH3CO OH)/%3035~45铬酐(Cr03)/(g/L)180~200盐酸(HCl,密度1.19g/mL)/(mL/L)3尿素/(g/L)40~60明胶/(g/L)1~2聚乙二醇/(g/L)1~2温度/℃20~4055~6540~6025~45<40时间/min0.2~33~53~101~215~30s用途适用于比较精密度高的制品适用于钢及黄铜制品适用于铜和黄铜制品,降低温度至20℃,可抛光白铜制品适用于铜铁组合制品适用于黄铜制品添加剂70mL/LO P乳化剂1.0mL/L温度40℃时间l5s③抛光液各成分对抛光质量的影响a·硫酸。
主要作用是溶解剥离铜及其合金表面的氧化膜,与抛光添加剂A配合使用,可起到光亮整平作用。
硫酸浓度高时,抛光速度快,表面光亮度好。
但浓度过高时,抛光效果会变差。
硫酸浓度低时,抛光速度慢,光亮度差。
b·抛光添加剂。
抛光添加剂分为A、B两组分。
A为添加剂,B为调整剂。
添加剂A是抛光液的主要组成部分,能起到促进反应速度和提高光亮度的作用。
添加剂A含量高时,抛光速度快,光亮度好,但含量再高时,无明显作用。
含量低时,抛光速度慢,抛光表面达不到镜面光泽。
3m抛光液配方分析
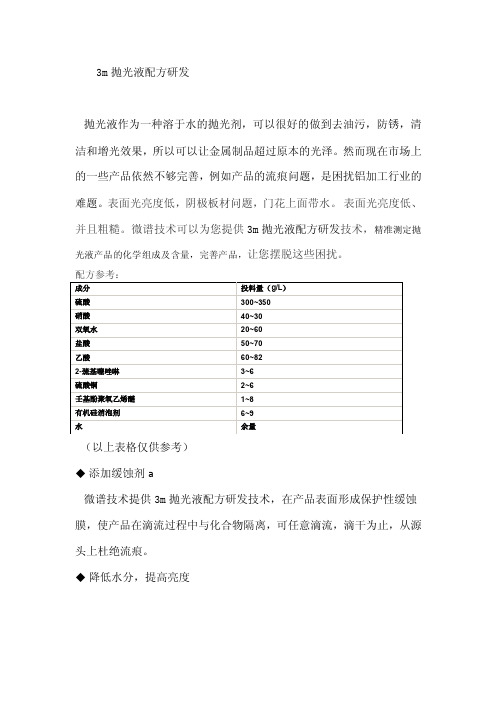
3m抛光液配方研发
抛光液作为一种溶于水的抛光剂,可以很好的做到去油污,防锈,清洁和增光效果,所以可以让金属制品超过原本的光泽。
然而现在市场上的一些产品依然不够完善,例如产品的流痕问题,是困扰铝加工行业的难题。
表面光亮度低,阴极板材问题,门花上面带水。
表面光亮度低、并且粗糙。
微谱技术可以为您提供3m抛光液配方研发技术,精准测定抛光液产品的化学组成及含量,完善产品,让您摆脱这些困扰。
(以上表格仅供参考)
◆添加缓蚀剂a
微谱技术提供3m抛光液配方研发技术,在产品表面形成保护性缓蚀膜,使产品在滴流过程中与化合物隔离,可任意滴流,滴干为止,从源头上杜绝流痕。
◆降低水分,提高亮度
研究表明,当三酸比例一定时,产品的亮度与抛光液含水量成反比,那么含水量越高,亮度越低,微谱技术提供3m抛光液配方研发技术,可以有效提高了抛光材的亮度。
添加缓蚀剂b
微谱技术提供3m抛光液配方研发技术,有效延缓、抑制了硝酸的分解,降低黄烟的溢出,从而保证硝酸浓度在一个合理的范围内波动,提升成品率。
微谱技术,之所以优秀的三大理由:
○因为权威,所有优秀。
微谱技术有着一个专们属于自己的实验室,最权威的检测结果,,绝对是您的首选!
○因为认可,所以优秀。
微谱技术出具的数据和报告都是经过大量的实验和论证的,因此也获得了国内外专业检测机构和跨国公司的认可。
○因为专业,所以优秀。
微谱技术拥有来自各大行业的专业分析团队,具有相关CMA 检测认证。
铜布线化学机械抛光技术分析
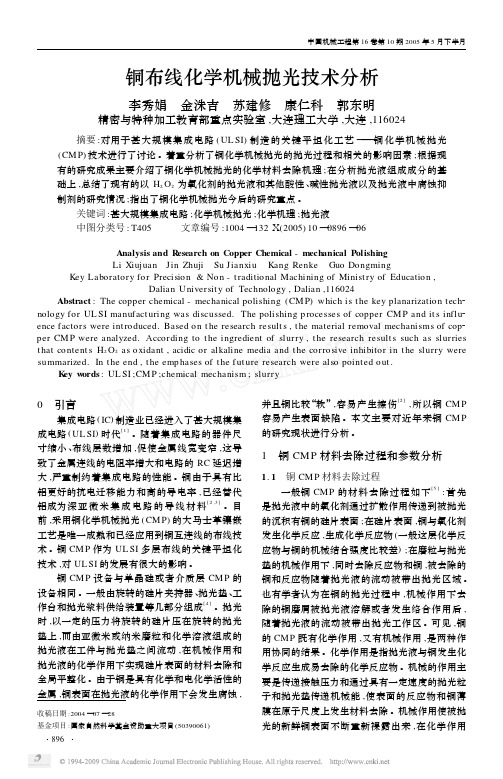
·896 ·
并且铜比较“软”,容易产生擦伤[2] ,所以铜 CM P 容易产生表面缺陷 。本文主要对近年来铜 CM P 的研究现状进行分析 。
1 铜 CM P 材料去除过程和参数分析
1. 1 铜 CM P 材料去除过程 一般铜 CM P 的材料去除过程如下[5] : 首先
中国机械工程第 16 卷第 10 期 2005 年 5 月下半月
铜布线化学机械抛光技术分析
李秀娟 金洙吉 苏建修 康仁科 郭东明
精密与特种加工教育部重点实验室 ,大连理工大学 ,大连 ,116024
摘要 :对用于甚大规模集成电路 ( UL SI) 制造的关键平坦化工艺 ———铜化学机械抛光 (CM P) 技术进行了讨论 。着重分析了铜化学机械抛光的抛光过程和相关的影响因素 ;根据现 有的研究成果主要介绍了铜化学机械抛光的化学材料去除机理 ;在分析抛光液组成成分的基 础上 ,总结了现有的以 H2 O2 为氧化剂的抛光液和其他酸性 、碱性抛光液以及抛光液中腐蚀抑 制剂的研究情况 ;指出了铜化学机械抛光今后的研究重点 。
铜布线化学机械抛光技术分析 ———李秀娟 金洙吉 苏建修等
的配合下 ,使材料去除过程能继续下去 。抛光中
凸的表面抛光速度快 ,凹的表面抛光速度低 ,这样
最终实现表面的全局平整化 。
1. 2 影响因素分析
在铜 CM P 的过程中 ,如果机械的因素较强 ,
则铜薄膜表面容易出现擦伤 ,而且抛光下来的产
2. 1 物理机理 在物理机理方面 ,铜 CM P 和其他材料 CM P
具有类似的机理 。目前有大量的学者从机械的角 度研究影响 CM P 的材料去除模式 。除了上述的 唯象学描述外 ,根据不同的压力和速度条件下硅 片与抛光垫间所处的接触状态的不同 ,已经提出 了接触模型[9 ] 、流体模型[10 ,11 ] , 以及流体和接触 同时作用的混合模型[12] 。目前认为半接触的混 合模型与实际情况比较符合 ,更容易被接受 。但 是 ,还没有更合理的模型揭示 CM P 的材料去除 机理 。 2. 2 化学机理
四川铜化学抛光工艺的配方
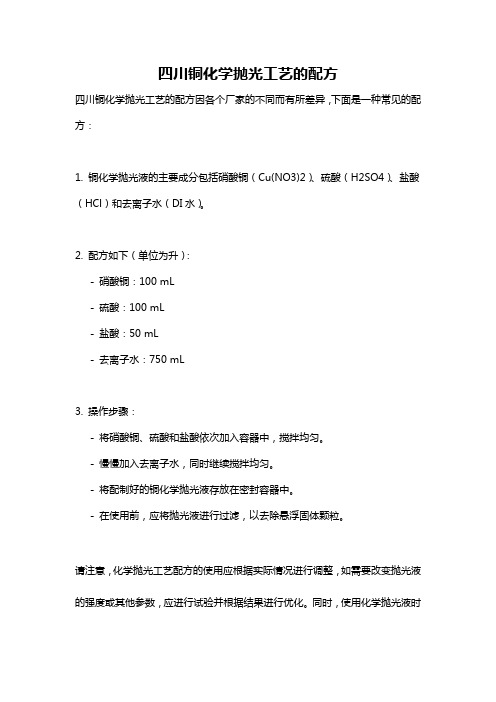
四川铜化学抛光工艺的配方
四川铜化学抛光工艺的配方因各个厂家的不同而有所差异,下面是一种常见的配方:
1. 铜化学抛光液的主要成分包括硝酸铜(Cu(NO3)2)、硫酸(H2SO4)、盐酸(HCl)和去离子水(DI水)。
2. 配方如下(单位为升):
- 硝酸铜:100 mL
- 硫酸:100 mL
- 盐酸:50 mL
- 去离子水:750 mL
3. 操作步骤:
- 将硝酸铜、硫酸和盐酸依次加入容器中,搅拌均匀。
- 慢慢加入去离子水,同时继续搅拌均匀。
- 将配制好的铜化学抛光液存放在密封容器中。
- 在使用前,应将抛光液进行过滤,以去除悬浮固体颗粒。
请注意,化学抛光工艺配方的使用应根据实际情况进行调整,如需要改变抛光液的强度或其他参数,应进行试验并根据结果进行优化。
同时,使用化学抛光液时
要注意安全操作,佩戴适当的防护设备,避免对人体和环境造成损害。
环保型铜材抛光液MS0308-1最新说明书
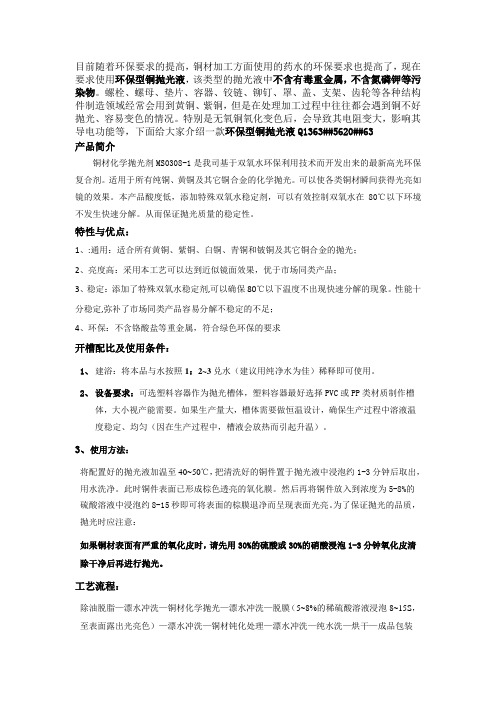
目前随着环保要求的提高,铜材加工方面使用的药水的环保要求也提高了,现在要求使用环保型铜抛光液,该类型的抛光液中不含有毒重金属,不含氮磷钾等污染物。
螺栓、螺母、垫片、容器、铰链、铆钉、罩、盖、支架、齿轮等各种结构件制造领域经常会用到黄铜、紫铜,但是在处理加工过程中往往都会遇到铜不好抛光、容易变色的情况。
特别是无氧铜氧化变色后,会导致其电阻变大,影响其导电功能等,下面给大家介绍一款环保型铜抛光液Q1363##5620##63产品简介铜材化学抛光剂MS0308-1是我司基于双氧水环保利用技术而开发出来的最新高光环保复合剂。
适用于所有纯铜、黄铜及其它铜合金的化学抛光。
可以使各类铜材瞬间获得光亮如镜的效果。
本产品酸度低,添加特殊双氧水稳定剂,可以有效控制双氧水在80℃以下环境不发生快速分解。
从而保证抛光质量的稳定性。
特性与优点:1、:通用:适合所有黄铜、紫铜、白铜、青铜和铍铜及其它铜合金的抛光;2、亮度高:采用本工艺可以达到近似镜面效果,优于市场同类产品;3、稳定:添加了特殊双氧水稳定剂,可以确保80℃以下温度不出现快速分解的现象。
性能十分稳定,弥补了市场同类产品容易分解不稳定的不足;4、环保:不含铬酸盐等重金属,符合绿色环保的要求开槽配比及使用条件:1、建浴:将本品与水按照1:2~3兑水(建议用纯净水为佳)稀释即可使用。
2、设备要求:可选塑料容器作为抛光槽体,塑料容器最好选择PVC或PP类材质制作槽体,大小视产能需要。
如果生产量大,槽体需要做恒温设计,确保生产过程中溶液温度稳定、均匀(因在生产过程中,槽液会放热而引起升温)。
3、使用方法:将配置好的抛光液加温至40~50℃,把清洗好的铜件置于抛光液中浸泡约1-3分钟后取出,用水洗净。
此时铜件表面已形成棕色透亮的氧化膜。
然后再将铜件放入到浓度为5-8%的硫酸溶液中浸泡约8-15秒即可将表面的棕膜退净而呈现表面光亮。
为了保证抛光的品质,抛光时应注意:如果铜材表面有严重的氧化皮时,请先用30%的硫酸或30%的硝酸浸泡1-3分钟氧化皮清除干净后再进行抛光。
化学抛光液成分分析-抛光液配方原理及生产技术工艺

化学抛光液成分分析,抛光原理及配方技术开发导读:本文详细介绍了抛光液的研究背景,理论基础,参考配方等,本文中的配方数据经过修改,如需更详细资料,可咨询我们的技术工程师。
化学抛光液,用于不锈钢电解抛光。
禾川化学引进尖端配方解剖技术,致力于化学抛光液成分分析,配方还原,研发外包服务,为抛光液相关企业提供一整套配方技术解决方案。
1 背景经过机械抛光后的铝合金工件虽然已经获得光亮的表面,但若将机械抛光后的工件直接进行阳极氧化,所得到的只是一个平滑的表面而得不到反光系数较高的膜层,所以经机械抛光后的工件还必须进行化学抛光或电抛光,以除去工件表面在机械抛光时所形成的晶体变形层,从而获得光亮、细致的表面。
铝合金的化学抛光可分为碱性抛光和酸性抛光两种。
酸性化学抛光的主要原料是磷酸、硫酸、硝酸、乙酸、氟化氢铵等。
由这些基本原料根据加工目的的不同可以组成很多配方,在化学抛光中仅有这些基本原料组成的配方并不能很好地满足生产要求,还需要有目的的在抛光溶液中添加一些旨在提高其光泽度和平滑度的添加物质。
这些添加物质可分为两大类:一是无机盐;二是有机物。
无机盐中采用的最多的是银、铜、镍、铬等,有机物有甘油、草酸、柠檬酸、氨基酸等。
禾川化学通过多年沉积,运用精细化工的复配技术, 做了小试和应用试验, 研制了一种铝合金化学抛光液配方技术;化学抛光可以认为是在一个特定条件下的光面化学侵蚀过程,其结果是需要获得一个平滑而光亮的表面,但并不是所有的铝合金材料都可以得到这个效果,一般而言,化学抛光的质量随铝合金各组分的不同而异,含铜及锌的铝合金抛光效果较差,而高硅铝则完全不适合化学抛光,通常是铝的纯度越高,抛光效果越好,抛光后的反射率越高。
样品分析检测流程:样品确认—物理表征前处理—大型仪器分析—工程师解谱—分析结果验证—后续技术服务。
有任何配方技术难题,可即刻联系禾川化学技术团队,我们将为企业提供一站式配方技术解决方案!化学抛光广泛应用于:一是铝合金经喷砂或拉丝后旨在对其表面进行光泽处理的加工;二是经机械抛光后的工件进行化学二次研磨以消除抛光时的抛光纹理,得到平滑而均匀的光亮表面,在理想状态下化学抛光可以做到比电解抛光更为平滑光亮的镜面效果;三是铝合金工件在进行纹理蚀刻前或在阳极氧化前为了获得一个基本的光度(或称为底光)而进行的加工。
铜材化学抛光处理方法_概述及解释说明

铜材化学抛光处理方法概述及解释说明1. 引言1.1 概述本文旨在对铜材化学抛光处理方法进行综述和解释说明。
化学抛光作为一种表面处理技术,在铜材领域具有广泛的应用。
通过有效地去除铜材表面的氧化层、污渍和不规则凸起等,能够提高铜材的表面质量,使其达到特定的要求,适用于多个工业领域。
1.2 文章结构本文将分为五个部分来讨论铜材化学抛光处理方法。
首先,在引言部分中我们将对文章的框架做简要描述。
接着,在第二部分中,我们将介绍铜材化学抛光前的准备工作以及常用的化学抛光方法,并探讨如何选择和优化抛光参数。
在第三部分中,我们将详细解析化学抛光过程及机理,并解释不同抛光液成分的作用机制,同时介绍表面质量评价的方法。
第四部分将以实际应用与案例研究为重点,介绍铜材化学抛光在工业界常见应用领域,并分享一些成功的系统优化案例。
最后,在第五部分中,我们将总结本文的核心发现,并展望未来铜材化学抛光处理方法的研究方向与挑战。
1.3 目的本文旨在全面介绍铜材化学抛光处理方法,通过对抛光前的准备工作、常用的化学抛光方法以及抛光参数的选择和优化等方面的探讨,帮助读者更好地理解这一表面处理技术。
同时,通过解析化学反应机理和不同抛光液成分的作用机制,提供关于铜材化学抛光过程的深入理解。
此外,通过实际应用与案例研究,读者将了解到铜材化学抛光在不同领域中的应用情况,并能够借鉴成功的系统优化案例。
最后,本文还将指出研究方向与挑战,并为未来进一步开展相关研究提供展望。
2. 铜材化学抛光处理方法:2.1 抛光前的准备工作:在进行铜材化学抛光之前,需要做一些准备工作以确保最佳抛光效果。
首先,需要清洗铜材表面,以去除油脂、污垢和氧化物等杂质。
常见的清洗方法包括机械清洗、超声波清洗和溶剂清洗等。
接下来,使用研磨纸或砂带对铜材表面进行打磨,以去除粗糙度和不均匀性。
2.2 常用的化学抛光方法:铜材化学抛光是一种通过与铜材表面发生化学反应来去除表面氧化物的方法。
铜件化学抛光配方
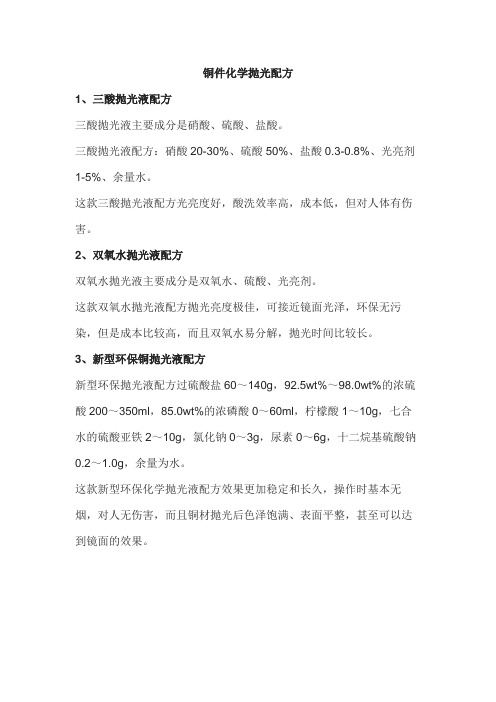
铜件化学抛光配方
1、三酸抛光液配方
三酸抛光液主要成分是硝酸、硫酸、盐酸。
三酸抛光液配方:硝酸20-30%、硫酸50%、盐酸0.3-0.8%、光亮剂1-5%、余量水。
这款三酸抛光液配方光亮度好,酸洗效率高,成本低,但对人体有伤害。
2、双氧水抛光液配方
双氧水抛光液主要成分是双氧水、硫酸、光亮剂。
这款双氧水抛光液配方抛光亮度极佳,可接近镜面光泽,环保无污染,但是成本比较高,而且双氧水易分解,抛光时间比较长。
3、新型环保铜抛光液配方
新型环保抛光液配方过硫酸盐60~140g,92.5wt%~98.0wt%的浓硫酸200~350ml,85.0wt%的浓磷酸0~60ml,柠檬酸1~10g,七合水的硫酸亚铁2~10g,氯化钠0~3g,尿素0~6g,十二烷基硫酸钠0.2~1.0g,余量为水。
这款新型环保化学抛光液配方效果更加稳定和长久,操作时基本无烟,对人无伤害,而且铜材抛光后色泽饱满、表面平整,甚至可以达到镜面的效果。
铜及其合金化学抛光工艺研究
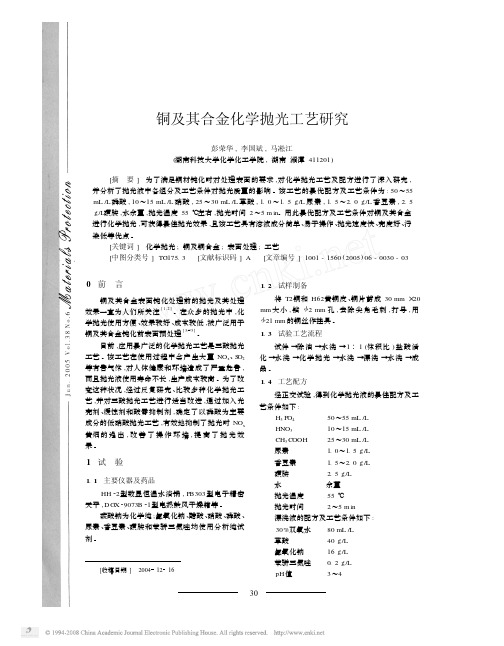
30 铜及其合金化学抛光工艺研究彭荣华,李国斌,马凇江(湖南科技大学化学化工学院,湖南湘潭411201)[摘 要] 为了满足铜材钝化时对处理表面的要求,对化学抛光工艺及配方进行了深入研究,并分析了抛光液中各组分及工艺条件对抛光质量的影响。
该工艺的最优配方及工艺条件为:50~55mL /L 磷酸,10~15mL /L 硝酸,25~30mL /L 草酸,1.0~1.5g/L 尿素,1.5~2.0g/L 香豆素,2.5g /L 磺胺,水余量,抛光温度55℃左右,抛光时间2~5m in 。
用此最优配方及工艺条件对铜及其合金进行化学抛光,可获得最佳抛光效果,且该工艺具有溶液成分简单、易于操作、抛光速度快、亮度好、污染低等优点。
[关键词] 化学抛光;铜及铜合金;表面处理;工艺[中图分类号]TG175.3 [文献标识码]A [文章编号]1001-1560(2005)06-0030-03 [收稿日期] 200412160 前 言铜及其合金表面钝化处理前的抛光及其处理效果一直为人们所关注[1,2]。
在众多的抛光中,化学抛光使用方便、效果较好、成本较低,被广泛用于铜及其合金钝化前表面预处理[3~5]。
目前,应用最广泛的化学抛光工艺是三酸抛光工艺。
该工艺在使用过程中会产生大量NO x 、S O 2等有害气体,对人体健康和环境造成了严重危害,而且抛光液使用寿命不长,生产成本较高。
为了改变这种状况,经过反复研究、比较多种化学抛光工艺,并对三酸抛光工艺进行适当改进,通过加入光亮剂、缓蚀剂和酸雾抑制剂,确定了以磷酸为主要成分的低硝酸抛光工艺,有效地抑制了抛光时NO x 黄烟的逸出,改善了操作环境,提高了抛光效果。
1 试 验1.1 主要仪器及药品HH 22型数显恒温水浴锅,P B303型电子精密天平,DGX 29073B 21型电热鼓风干燥箱等。
碳酸钠为化学纯;氢氧化钠、醋酸、硝酸、磷酸、尿素、香豆素、磺胺和苯骈三氮唑均使用分析纯试剂。
LR-303环保铜抛光剂
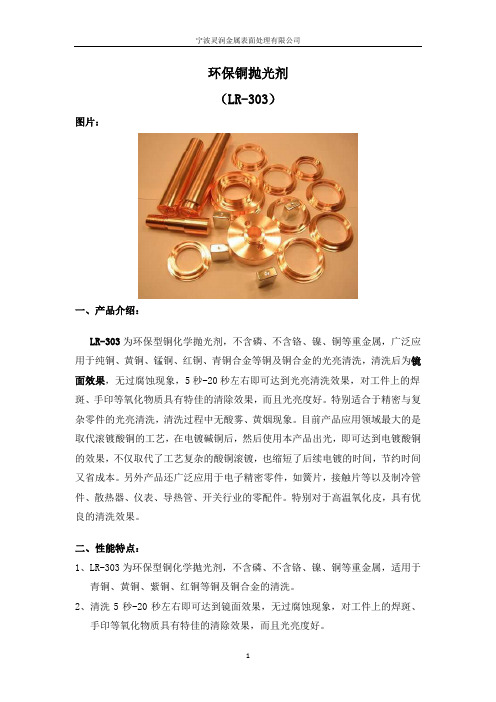
环保铜抛光剂(LR-303)图片:一、产品介绍:LR-303为环保型铜化学抛光剂,不含磷、不含铬、镍、铜等重金属,广泛应用于纯铜、黄铜、锰铜、红铜、青铜合金等铜及铜合金的光亮清洗,清洗后为镜面效果,无过腐蚀现象,5秒-20秒左右即可达到光亮清洗效果,对工件上的焊斑、手印等氧化物质具有特佳的清除效果,而且光亮度好。
特别适合于精密与复杂零件的光亮清洗,清洗过程中无酸雾、黄烟现象。
目前产品应用领域最大的是取代滚镀酸铜的工艺,在电镀碱铜后,然后使用本产品出光,即可达到电镀酸铜的效果,不仅取代了工艺复杂的酸铜滚镀,也缩短了后续电镀的时间,节约时间又省成本。
另外产品还广泛应用于电子精密零件,如簧片,接触片等以及制冷管件、散热器、仪表、导热管、开关行业的零配件。
特别对于高温氧化皮,具有优良的清洗效果。
二、性能特点:1、LR-303为环保型铜化学抛光剂,不含磷、不含铬、镍、铜等重金属,适用于青铜、黄铜、紫铜、红铜等铜及铜合金的清洗。
2、清洗5秒-20秒左右即可达到镜面效果,无过腐蚀现象,对工件上的焊斑、手印等氧化物质具有特佳的清除效果,而且光亮度好。
3、特别适合于精密与复杂零件的光亮清洗,清洗过程中无酸雾、黄烟现象。
二、工艺流程:除油脱脂→流动清洗→LR-303环保铜抛光剂→水洗→电镀或浸铜保护剂→流水清洗→烘干三、使用方法:1.建浴:2.使用方法:A.小件产品(面积小重量轻):可以制作网状的篮子一个,将产品盛入篮子内进行清洗,清洗时将篮子适当抖动,以避免产品之间相互迭合,造成酸洗不匀现象。
B.有孔状或凹槽的产品:制作夹具或四方篮子一个,将产品用夹具撑好,或将产品放在篮子内有呈有规则的摆放,凹槽朝下,可以避免取出时有残留药液。
然后提到槽内进行浸泡清洗,时间以光亮程度为标准,清洗时要适当的摇动,保证清洗的均匀性。
C.大面积铜板:配备喷淋设备,按产品的规格设计喷淋槽子一个,将产品摆放在固定的位置,以药液喷洒的形式对产品进行清洗,这种方式特别适合正规的厂家的清洗生产线,喷洗以后直接用清水冲洗干净。
铜及铜合金环保型化学抛光工艺新探

高产 品 质量 、 延长 使用 寿命 、 改善 装饰 效 果 和表 面 性 能[ ] 1 .抛 光 是 物体 表 面尤 其 是金 属 表 面处 理 常 用 的 方 法之 一. 目前广 泛使 用 的抛光 方法 有机 械抛 光 、 学抛 光 、 化 电解抛 光 、 声波抛 光 、 超 流体抛 光 、 磁力 抛光 等
艺 的开发 一直 为人 们所关 注[ 本文 以 H。 HN 为 主配方 , 过对配 方 体 系进行 优 化 , 发 了一种 污 1 引. 0 一 O。 通 开 染小 、 光效果 好 的化学 抛光 液 , 抛 同时具 有工 艺稳 定 、 护方 便等 特点 , 维 可使 铜及铜 合金 的制 件达 到镜 面光 亮 的水平 并提 高其 抗变 色性 和耐腐 蚀性 能.
3 、 HNO ,9wt ) 浓硫 酸 ( S 9 ) s 6 、 H O ,8wt 等均 为工 业 级试 剂 , 直接 按 体 积 量
取 使用 ; 光过程 中使 用 的抛光 布 由上海 双弘 针织 品有 限公 司提供 , 的损 耗 量 、 光量 通 过 上海 精 科 电 抛 铜 抛 子 天平 进行 称量 . 条及铜 条卷 的抛 光 效果 通 过 肉眼 、 星 S 5 铜 三 T5 0型数 码 相 机 、 日本 岛津 uv一5 0型 紫 25
基 金 项 目 : 徽 省 自然科 学青 年基 金 资 助 项 目( 04 66 0 ) 安 徽 省 自然 科 学 研 究 基 金 资 助 项 目( j0 20 2 安 1000q5 ; k 1a 3 ) 2 作 者 简 介 : 飞 云 ( 9 4 ) 男 , 徽 阜 阳人 , 士 研 究 生 . 周 1 8一 , 安 硕 通讯作者 : 高建 纲 (9 8) 男 , 1 7一 , 山东 莱 阳人 , 教 授 , 士 副 博
铜化学抛光剂配方分析

铜化学抛光剂配方分析一.背景化学抛光液广泛应用于金属表面处理,科标技术专业从事化学抛光液配方分析、配方检测、配方还原、成分分析,科标技术为金属表面处理企业提供整套配方改进技术方案;化学抛光与机械抛光、电化学抛光相比,它不需要通电和挂具。
因此,可以抛光形状复杂的制品 ,并且生产效率高。
化学抛光得到光亮表面 ,提高了铜及铜合金的装饰效果和表面性能。
目前国内大多使用铬酐型和硝酸(盐)型的化学抛光液,危害人体健康 ,并污染环境。
因此,近年来国内外对铜及铜合金的抛光进行大量的研究,开发了各种污染小、抛光效果好的环保型抛光液。
通过对各种化学抛光工艺如三酸型、H2O2-H2SO4型、H2O2-HNO3型、H2O2-HAc型、以及K2CrO7-H2SO4型等抛光效果及环境影响的比较 ,找到了抛光效果好、污染小的化学抛光液 ,即以 H2O2-H2SO4型为基础配方 ,研究了化学抛光的添加剂,使抛光效果达到或接近镜面光亮的水平。
二.化学抛光液的开发2.1工艺流程化学除油-----热水洗-----冷水洗------化学抛光-----冷水洗-----5% H2SO4脱膜----冷水洗-----转入下道工序2.2抛光液基础配方通过对各种不同类型化学抛光液效果比较 ,并反复试验 ,获得了铜及铜合金光亮抛光新工艺 ,其工艺配方如下:H2O2 (30 %) ,ml/L 450纯水 490添加剂A 60T ,°C 45~50t ,s 30~100本工艺中无硝酸或硝酸盐 ,在酸洗过程中不产生 NOx黄烟 ,有利于操作和环保 ,对铜件腐蚀特别小 ,适用于各种铜基零件。
由于成份简单 ,控制方便 ,添加剂由 A、B两个组份组成 ,A为开缸剂 ,B为补充剂。
平时添加补充时 ,应按 B剂∶H2O2 = 1∶6(体积比)混合后 ,再加到槽液中 ,原则上应不亮即加 ,少加、勤加。
对于磷青铜件 ,可在抛光液中再加 10 %(体积比)的氟化氢铵。
ZJ-504铜材多功能抛光光亮剂

ZJ-504 铜材多功能抛光光亮剂ZJ-504光亮剂本产品采用优质的表面活性剂及缓蚀剂、酸雾抑制剂等合制而成,具有独特的酸洗抛光作用,比目前市场上的同类产品相比,抛光液性能稳定,可以反复使用及回收利用,而且具有配制方便,使用简单等特点;另外,氮氧化物废气及废水量少且易于控制,因此是接近环保型的产品。
光亮剂新工艺与老“三酸”酸抛光工艺对比有如下优点:1、酸洗溶液不用硝酸,操作容易,溶液稳定。
酸洗光亮性好(一般可达半镜面亮度),不会造成过腐蚀,尤其适用于薄壁零件的光亮酸洗。
2、酸洗中氮氧化物废气和废水减少,保护环境效果十分显著。
3、生产操作较为安全。
4、成本只用硝酸酸洗的 30%-50%左右,经济效益十分显著。
5、适用于手工和机械操作。
6、适应范围宽:之前市面上销售的光亮剂,有的应用黄铜上有良好的效果,有的在纯铜方面有很好的效果,但是很多光亮剂在磷青铜、锡青铜、铍青铜等铜合金上很难得到良好的效果,但是我中心研究的本产品,不仅能在黄铜和纯铜上取得良好的效果,更为显著的效果是在磷青铜、铍青铜、锡青铜上的成绩。
一、配方和操作条件:参数参数范围按体积百分比配置项目硫酸(工业级d=1.84) 400 毫升/升40%盐酸(工业级d=1.18) 5-10 毫升/升5‰硝酸钠(工业级)70 克/升(或硝酸 60 毫升)7%Zj-504光亮剂20-40毫升/升(铜质差取高值) 2%水余量约500毫升/升50-58%温度5-40℃5-40℃PH ≥1 ≥1处理方法浸泡浸泡时间 3 秒-2 分钟 3 秒-2 分钟搅拌不需要不需要过滤不需要不需要二、配制方法:1、取计算量的硝酸钠放入耐酸槽中;2、按 450 毫升/升计算水量加入添加剂槽中并搅拌使之完全溶解;3、缓慢加入计算量的硫酸,不断搅拌冷却到 50℃以下;4、加入计算量的盐酸,搅拌均匀;5、加入计算量的光亮剂和规定体积的水,搅拌均匀待冷却到室温后即可进行抛光。
三、可能产生的故障及解决方法:1、不光亮:①溶液浓度过低,应添加硝酸钠50克/升、硫酸50毫升/升,zj-504光亮剂10毫升/升或酌情调整。
- 1、下载文档前请自行甄别文档内容的完整性,平台不提供额外的编辑、内容补充、找答案等附加服务。
- 2、"仅部分预览"的文档,不可在线预览部分如存在完整性等问题,可反馈申请退款(可完整预览的文档不适用该条件!)。
- 3、如文档侵犯您的权益,请联系客服反馈,我们会尽快为您处理(人工客服工作时间:9:00-18:30)。
铜化学抛光剂配方分析
一.背景
化学抛光液广泛应用于金属表面处理,科标技术专业从事化学抛光液配方分析、配方检测、配方还原、成分分析,科标技术为金属表面处理企业提供整套配方改进技术方案;化学抛光与机械抛光、电化学抛光相比,它不需要通电和挂具。
因此,可以抛光形状复杂的制品 ,并且生产效率高。
化学抛光得到光亮表面 ,提高了铜及铜合金的装饰效果和表面性能。
目前国内大多使用铬酐型和硝酸(盐)型的化学抛光液,危害人体健康 ,并污染环境。
因此,近年来国内外对铜及铜合金的抛光进行大量的研究,开发了各种污染小、抛光效果好的环保型抛光液。
通过对各种化学抛光工艺如三酸型、H2O2-H2SO4型、H2O2-HNO3型、H2O2-HAc型、以及K2CrO7-H2SO4型等抛光效果及环境影响的比较 ,找到了抛光效果好、污染小的化学抛光液 ,即以 H2O2-H2SO4型为基础配方 ,研究了化学抛光的添加剂,使抛光效果达到或接近镜面光亮的水平。
二.化学抛光液的开发
2.1工艺流程
化学除油-----热水洗-----冷水洗------化学抛光-----
冷水洗-----5% H2SO4脱膜----冷水洗-----转入下道工序
2.2抛光液基础配方
通过对各种不同类型化学抛光液效果比较 ,并反复试验 ,获得了铜及铜合金光亮抛光新工艺 ,其工艺配方如下:
H2O2 (30 %) ,ml/L 450
纯水 490
添加剂A 60
T ,°C 45~50
t ,s 30~100
本工艺中无硝酸或硝酸盐 ,在酸洗过程中不产生 NOx黄烟 ,有利于操作和环保 ,对铜件腐蚀特别小 ,适用于各种铜基零件。
由于成份简单 ,控制方便 ,添加剂由 A、B两个组份组成 ,A为开缸剂 ,B为补充剂。
平时添加补充时 ,应按 B剂∶H2O2 = 1∶6(体积比)混合后 ,再加到槽液中 ,原则上应不亮即加 ,少加、勤加。
对于磷青铜件 ,可在抛光液中再加 10 %(体积比)的氟化氢铵。
2.3反应机理及工艺条件
铜及铜合金的化学抛光过程一般可分浸蚀、光亮、过腐蚀三个阶段。
在抛光过程的浸蚀阶段 ,由于金属处于活化状态 ,金属表面不同部位的电化学和物理化学性质的不同导致金属表面的不均匀溶解 ,于是产生腐蚀表面。
随着抛光过程的进行 ,金属表面逐渐由活化状态变为钝化状态 ,此时抛光过程进入光亮阶段。
由于金属表面凹凸部位的钝化程度不同 ,凸处相对凹处的高度活性和金属离子由凸处向抛光液的高速扩散 ,以及新抛光液高速向凸处的扩散 ,导致凸起部份的优先溶解。
另外 ,金属表面凸起部位所形成的钝化膜的不完整和多孔性 ,也加速了凸起部分的溶解 ,结果浸蚀的金属表面被光亮表面所代替。
随着抛光时间的延长 ,金属表面的钝化状态被打破 ,产生过腐蚀的金属表面。
(1)添加剂 A、B
A剂、B剂均由硫酸、表面活性剂、H2O2稳定剂、氧化剂等组成。
硫酸主要溶解 CuO ,其含量过高会产生过腐蚀;太低 ,则表面易形成白色条纹 ,必须选择合适的含量。
H2O2在溶液中不稳定 ,特别是在含铜离子的抛光液中分解更为严重。
提高H2O2的稳定性是能否批量生产的关键。
因此 ,必须在抛光液中加入稳定剂 ,使H2O2分解减缓或停止。
一般使用醇类与其它物质互配来稳定H2O2。
表面活性剂有缓蚀和抑制酸雾能力 ,也可提高零件的表面光亮度。
(2) H2O2:
抛光液中的主要氧化剂 ,与硫酸联合作用 ,使制品表面光亮。
H2O2浓度太低 ,抛光效果差; H2O2浓度过高 ,则会在酸洗后产生粗糙的粉红色铜层。
(3)温度:
抛光液温度对抛光后的粗糙度和光亮度有很大影响 ,一般随温度升高 ,其粗糙度和光亮度增加。
但温度过高 ,会导致过腐蚀 ,产生麻点 ,并且温度过高 , H2O2分解加快。
适宜的温度范围为 45~50°C。
(4)抛光时间
抛光时间随温度的升高而缩短 ,抛光时间短 ,则抛不亮;过长 ,又会产生麻点。
为了获得镜面光亮度 ,抛光应采取短时、多次的抛光方式 ,每抛一次 ,都要脱膜和水洗一次。
(5)搅拌
在抛光时要求对溶液进行搅拌或抖动零件。
一般的操作方法是 ,把零件放入抛光液 ,稍后再抖动零件 ,这样可保证获得高质量的抛光表面。
在配制抛光液的过程中 ,需使用纯水才能达到最佳效果 ,新配制的抛光液 ,第一批零件的抛光时间较长 ,但以后的抛光速度就很快了。
二.参考抛光液配方
组分投料量(g/L)
硫酸350~400
硝酸30~50
双氧水30~100
盐酸40~80
乙酸20~50
2-巯基噻唑啉1~3
硫酸铜1~10
壬基酚聚氧乙烯醚5~10
有机硅消泡剂1~3
水余量
三.市面常见抛光液的种类:
硅材料抛光液、蓝宝石抛光液、砷化镓抛光液、铌酸锂抛光液、锗抛光液、集成电路多次铜布线抛光液、集成电路阻挡层抛光液、研磨抛光液、电解抛光液、不锈钢电化学抛光液,不锈钢抛光液、石材专用纳米抛光液、氧化铝抛光液、铜化学抛光液、铝合金抛光液、镜面抛光液、铜抛光液、玻璃研磨液、蓝宝石研磨液、酸性抛光液、铝材抛光液、金刚石抛光液、钻石抛光液、单晶体钻石研磨液、抛光膏。