粉磨系统
联合粉磨系统介绍2010-3s-1

天津水泥工业设计研究院有限公司
9
V-
S联EP合AR粉AT磨O 系统流程B
R
天津水泥工业设计研究院有限公司
10
振兴联合粉磨系统
辊压机 TRP140/140
600t/h
V选 TPS160 160000m3/h
旋风筒 6DC1525 180000 m3/h
循环风机 M4-73-15 No.18F
180000 m3/h
26~28 18~22
200~240
200~300
~4000
~4000
天津水泥工业设计研究院有限公司
2
◆ 辊压机发展概况
1977年:Clausthal大学Schonert教授申请专利 1985年:第一台样机投产
●规格不断大型化,对粒度的适应性提高; ●耐磨性能不断改善,使用寿命延长; ●液压系统可靠性提高,故障率降低; ●系统不断改进,辊压机作用得到充分体现。
L/D 利弊
>1
① 边缘效应小; ② 辊宽方向受力好; ③ 辊子偏斜量大,但目前
从液压系统的调节上 已经解决。
<1
① 边缘效应大; ② 辊宽方向受力
差; ③ 辊子偏斜量小
。
天津水泥工业设计研究院有限公司
4
压力与辊压机的出力:
PR=2Sinβ×D×B ×V ×PT
(PR-需用功率, PT-挤压力)
辊压机的规格系数:
设计
实际
86
84
5
5
9
4
7
170
170
3300
3480
30.2
29.3
7.6
7.1
17.6
16.8
12
●系统运行指标先进,是比较满意的辊压机系统之一; ●半成品≥1800cm2/g,R80mm=20~30%, R45mm=50%,全部入磨影响粉磨效率; ●系统比较复杂,通风电耗较高;
水泥制作工艺中用的到一些主要设备介绍 。

水泥制作工艺中用的到一些主要设备介绍一、石灰石破碎机:(图一所示)石灰石主要成分是碳酸钙(CaCO3)。
石灰和石灰石大量用做建筑材料,也是许多工业的重要原料。
专业生产厂家提供石灰石破碎机,在石灰石破碎机生产方面已经有多年的制造经验,目前已经成功用于多条石灰石生产线,有技术先进的破碎工程师,可以根据用户的要求设计成套的石灰石破碎系统,提供该系统的前期设计咨询,以及设计安装,和石灰石破碎系统系调试,试产,已及工人的培训一整套完善的售前,售中,售后流程.产品特点:该设备运行性能稳定可靠,工艺简化,结构简单,维修方便。
生产能力大,锤头使用寿命长。
广泛适用于花岗岩、玄武岩、石灰岩、河卵石、水泥熟料、石英石、铁矿石、铝矾土等多种矿物的细式破碎。
工作原理工作时,该机在电机的带动下,转子高速旋转,物料进入第一破碎腔破碎与转子上的板锤撞击破碎,然后进入第二细碎腔进行粉碎,最后从出料口排出。
工艺流程石灰石破碎系统系:粉碎法,系将含CaCO3在90%以上的白石用雷蒙磨或其它高压磨经粉碎、分级、分离,而制得的成品。
包装:塑料袋包装,每袋净重50公斤。
储运注意事项储存于干燥的库房中。
运输中防止袋破。
不得与液体酸类共储混运。
图一二、水泥窑系统(图二所示)(图二)水泥窑是水泥生产的主要设备,由生料烧成熟料的整个过程都在窑内完成,最简单的回转窑是干法中空窑。
生料粉由窑尾加入,煤粉用一次风由窑头喷入并在窑内燃烧,这里的火焰温度达1800—2000℃。
生料在窑内不断向窑头流动,湿度也逐渐升高,经过烘干、脱水、预热、分解,到1300°C左右时出现液相,在火焰下面升高到1450°C烧成熟料,然后冷却到1300~1100℃离开回转窑落入单筒冷却机,冷却到100—150℃左右卸到熟料输送机运至熟料破碎机,破碎后入库贮存。
三、回转窑系统:(图三所示)(图三)回转窑是由钢板卷制的圆筒,内砌耐火砖,由装车简体上的轮带和下面的托轮支承,用装在窑身上的大齿圈传动。
辊压机及粉磨系统计算
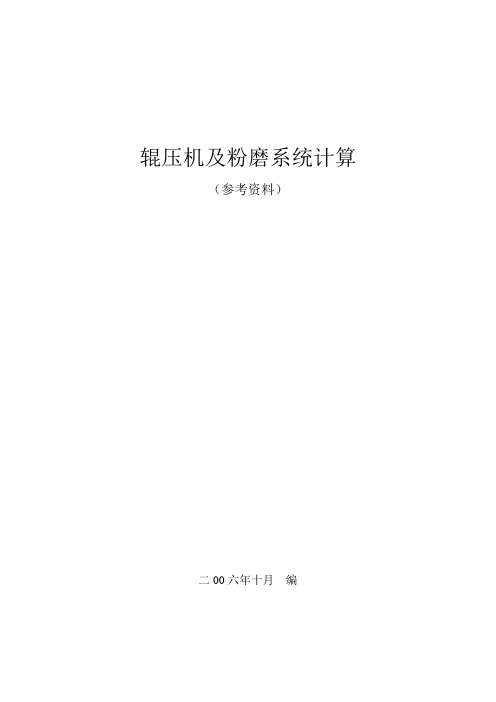
辊压机及粉磨系统计算(参考资料)二00六年十月编目录一、磨机计算 (2)1.磨机需要功率: (2)2.磨机单位功耗: (2)3.磨机单位需要功率: (3)4.磨机生产能力: (4)二、辊压机计算 (5)1.辊压机通过量: (5)2.辊压机功率 (6)3.辊压机料饼单位功耗: (7)三、选粉机计算 (10)1.选粉机能力 (10)2.循环负荷及选粉效率 (12)四、辊压粉磨系统计算 (13)1.辊压粉磨系统产量 (13)2.辊压粉磨系统电耗 (14)3.辊压机循环量及循环次数 (16)4.辊压机增产节能效果 (18)五、计算实例 (20)例1、计算预粉磨及联合粉磨系统产量及电耗 (20)例2、计算增加辊压机后单位电耗及增产效益 (21)例3、计算增加辊压机前后磨机能力就及电耗 (23)例4、计算磨机功率及生产能力 (24)六、辊压机与磨机配套 (25)一、磨机计算1.磨机需要功率:P T=P0·K1 ------------------------------------------------------(1)P0=0.184×D i×V i×n×φ×(6.16-5.75φ)P T─磨机需要功率,kw;P0─磨机理论功率,kw;D i=D g-2δD i─磨机有效内径,m;D g =4~5m,δ=0.08mD g─磨机公称直径,m;D g =3~4m,δ=0.07mV i─磨机有效容积,m3;n─磨机转速,r/min;n=32×D-0.5φ─研磨体填充率,%;一般28~30%(γ=4.5t/m3计)γ─钢球容重,t/m3;K1─动力系数,水泥磨、生料磨,大中型:K1 =1.25;中小型:K1 =1.35;2.磨机单位功耗:为计算磨机生产能力,应先计算出磨机单位功耗。
WW0=W i×(10/(P80)1/2-10/(F80)1/2)×C1×C2×C3×C4×C5×C6(2)W0─磨机单位功耗,kwh/t;W i─物料功指数(易磨性),kwh/t;各种物料W i值如下:石灰石:8~14;生料:7~12;熟料:14~19;辊压后熟料:12~13 P80─成品80%通过筛孔的粒径,μm;P80与比表面积的关系如表1F80─入磨物料80%通过筛孔的粒径,μm;F80与粉磨系统的关系如表2C1~C6为各种修正系数表3为计算方便C1~C6乘积,未加辊压机取“1.4”,增加辊压机取“1.33”。
辊压机联合粉磨工艺系统分析

辊压机联合粉磨工艺系统分析辊压机联合粉磨(或半终粉磨)工艺系统,其技术核心在本质上属于“分段粉磨”。
目前,国内水泥制成工序广泛应用由辊压机+打散分级机(动态分级设备)或V型选粉机(静态分级设备)+管磨机开路(或配用高效选粉机组成双闭路)组成的联合粉磨工艺系统(或由辊压机+V型选粉机(静态分级设备)+高效选粉机+管磨机组成的半终粉磨工艺系统),在实际运行过程中,由于各线生产工艺流程及设备配置、物料粉磨特性、水份等方面因素不尽相同,导致系统产量、质量及粉磨电耗等技术经济指标也参差不齐,本文拟对水泥联合粉磨单闭路(管磨机为开路)及双闭路系统(或半终粉磨系统)中各段常出现的工艺技术与设备故障模式进行探讨分析,并提出了相应的解决办法,仅供粉磨工程技术人员在日常工作中参考,文章中谬误之处恳望予以批评指正:一、辊压机系统故障模式:辊压机挤压效果差故障原因1:1. 被挤压物料中的细粉过多,辊压机运行辊缝小,工作压力低影响分析:辊压机作为高压料床(流动料床)粉磨设备,其最大特点是挤压力高(>150Mpa),粉磨效率高,是管磨机的3-4倍,预处理物料通过量大,能够与分级和选粉设备配置用于生料终粉磨系统。
但由于产品粒度分布窄、颗粒形貌不合理及凝结时间过快、标准稠度需水量大与混凝土外加剂相容性差等工作性能参数方面的原因,国内水泥制备工艺未采用辊压机终粉磨系统,辊压机只在水泥联合粉磨系统中承担半终粉磨(预粉磨)的任务,经施以双辊之间的高压力挤压后的物料,其内部结构产生大量的晶格裂纹及微观缺陷、<2.0mm及以下颗粒与<80um细粉含量增多(颗粒裂纹与粒度效应),分级后的入磨物料粉磨功指数显著下降(15-25%),易磨性明显改善;因后续管磨机一仓破碎功能被移至磨前,相当于延长了管磨机细磨仓,从而大幅度提高了系统产量,降低粉磨电耗。
但辊压机作业过程中对入机物料粒度及均匀性非常敏感,粒状料挤压效果好、粉状料挤压效果差,即有“挤粗不挤细”的料床粉磨特性;当入机物料中细粉料量多时会造成辊压机实际运行辊缝小,主电机出力少,工作压力低,若不及时调整,则挤压效果会变差、系统电耗增加。
如何提高磨粉系统的粉磨效率

粉磨系统的合理性是和设备选 型、 工艺布置以及各仓磨粉 的能 力相关的 ,粉磨效率会受 到多方面的影响 ,如磨机的物料性质、 粒 度、 温度 、 易磨性 、 以及成品的细度 、 水分等因素。其次 , 研磨体 的装 载量 、 级配 、 填充率和通风等工艺参数也会对粉磨效率造成影 响。 最 后, 磨机的磨仓长度、 隔板形式以及衬板形式 和通孔率、 篦孔大小等 机械结构问题等也会影响粉末效率 。 只有综合考虑上述因素才 能够 使得磨机效率得 以提高 , 从 而达到高产 、 优产的目的。 只有在结构上 保证设备具有合理性 , 并使得设备具有高适应性 、 简单性 , 对物料进 行严格 的筛选 , 并提高设备的可靠性 , 才能够在减少过粉磨的 同时 获得 较 高 的产 品 比表 面积 以及颗 粒 级 配 。 1物料性质 同粉磨效率的关系 1 . 1有效控制物料粒度以及成品细度 磨机产量会受到入磨物料粒度 的影响 , 当粒度过大时 , 研磨体 的研 磨作 用 以及 冲击 就无 法 适 应 , 在 磨机 的一 仓 中需 要 加 入 大量 大 钢球 , 用 以提高研磨体 的冲击 。 在一定程度上 , 一仓起到主要的破碎 作用 , 这样会使得粉磨过程的失衡 , 造成不合理的粉磨过程。 从实质 上讲磨机利用率较低 , 物料粒度越大 , 在人磨时设备效率就会越低 , 就会造成磨机产量 的下降。 因此人磨物料粒度应 当小于 2 5 a r m, 粒度 的减小就使得相同装载量 的前提下 , 装在钢球的直径更小 、 装载量 更多 , 钢球的总表面积就会越大 , 粉磨效率便越高 。 1 . 2有效控制易磨性 根据相关物料实验结果可 以看 出, 物料 的结晶性能越好结构越 密集 的研磨越困难 , 各种矿物的组成以及冷却会直接影响熟料易磨 性 ,从实际的应用 中能够分析出 , P值越高 、 K H值越高的熟料较容 易研磨 , C 3 S多且 C 4 A F 少 的熟料以及冷却快的熟料易磨性较高 , 相 反则易磨性差 。而混合料 的粉磨中 , 粒化高炉矿渣若水淬条件好那 么结 构就 会 较 为 疏 松 , 便 具 有 良好 的 易磨 性 , 若 水 淬条 件 差 则 易磨
MPS3350B立式磨生料粉磨系统操作流程

现在就此粉磨系统做一简要介绍, 仅供同行参考。 足并确认无其它主机设备启动的情况下 , 给磨 1MP 3 5 B立式磨 系统生 产及 主要设 备 S3 0 主电机, 喂料系统, 除渣系统发出启动命令 , 一 然 1 工 艺流程简介 . 1 后辅传电机会按照设计好的启磨时间先带动 M S 30 式磨 生料 粉 磨 系统 是烘 干 , P 35 B立 选 磨盘运转 , 然后启动主电机启磨 , 启动磨辅传 粉和输送功能于一体的紧凑系统。我公司采用砂 布料时,可提前拉风至正常操作风量的 8%, 5 随时根据主传电机电流及磨压 岩, 铁粉, 石灰石, 粉煤灰四组分配料。这四种料从 等主传启动后 , 各自的料仓下来由 4台给料机经 4台电子皮带秤 差进行调整, 热风的供风量也是同步加入。 2 2人 口负压 计量后 ,现经 19 9 m米皮 带 ,8 2 m米输送 机经过 三 道锁风阀后进 人立密, 落在转动的料盘上, 在离心 合理 的风速 ( 过人 口负压来 控 制 ) 以 通 可 力的作用下向磨盘边缘移动, 并受到磨辊的碾压而 形成良好的内部循环,使磨盘上的料层稳定 , 粉碎,粉碎后的物料被风环处高速上升的气流带 粉磨效率高, 我公司利用窑尾废气作为烘干热 起, 大颗粒直接落到磨盘上重新粉磨 , 气流中的物 源 , 同时循环风阀门 10 0% ̄, 两者共同成为人 料经旋转的分离器选粉后, 不合格的粗粉分离下来 密风量的来源, 口负压可通过调节开度及热 人 经锥斗落到磨盘中央重新粉磨( 此过程称内循环 ) 风阀门的开度来调节。负压值控制在 8 1t a磨 , -0 b, u 细粉随气流一起出磨 , 在旋风简和系统收尘装置中 机运行 较平稳 。 收集下来 , 即为合格生料。 还有少量的物料通过风 2 3磨机 出 口温度 环落 下 , 舌 , 输送设 备重 新输 入磨 内 经 啼 刮出 通过 出磨气体 温度是衡 量烘 干过程 是否 正常 的综 2℃ 否则软 连接 粉磨( 此过程称为外循环 )如此循环反复, , 在研磨 合 性指 标。 出磨 风温不 许超过 1O , 的同时 , 物料充分与热气流进行热交换 , 从而被烘 要受损失。我公司出磨气体温度控制在 8 ℃左右, 5 干, 得到符合粒度要求 , 含水量小于0 %的产品。 温度高因采用石灰石, 。5 砂岩, 铁粉, 粉煤灰四组分配 用于立磨烘干的热风来 自于窑尾气 , 管路上设有冷 料中粉煤灰不易形成稳定料层, 磨机振动明显。温 风 阀和热风炉 ( 没有窑尾 废气时使 用 )工 作流程见 度低则出磨物料水份大, 。 易挂生料库壁。
【探究】辊压机联合粉磨系统的操作控制

【探究】辊压机联合粉磨系统的操作控制天津振兴水泥有限公司二线水泥粉磨系统采用TRP1400×1400辊压机联合粉磨系统。
该系统于2004年5月建成,几年的生产实践证明该系统年运转率可达80%以上,月最高运转率达96%以上。
本文仅就该系统的生产经验进行介绍。
1工艺流程物料经皮带秤由混料皮带输送至喂料斗提,经1.4 m皮带进入稳料承重仓内,物料从小仓底部卸出以料柱形式进入辊压机,被辊压过的料饼经喂料斗提进入V型选粉机打散分选,经循环风机风选后(实际生产过程中根据磨机能力通过循环风机阀门来控制入磨物料量)的细颗粒被六筒旋风收尘器收集,粗料落入称重仓重新喂入辊压机循环辊压,使物料得到挤压破碎再与新物料一起入斗式提升机进入V型选粉机分选,细颗粒入磨,粗颗粒再次被挤压破碎,周而复始;出V型选粉机的细颗粒被六筒旋风收尘器收集,通过下料溜子入磨粉磨,物料通过出磨斗提进入O-sepa选粉机分选,成品经布袋收尘器收集入库,粗颗粒经回粉皮带入磨继续粉磨。
表1是该系统设备的相关参数。
2参数控制与运行调整2.1 物料粒度的控制辊压机对物料的粒度要求比较严格,粒度过大或过小都会影响系统的正常运转。
如果物料细粉较多,则物料通过辊压机速度就快,形不成足够的料饼,物料受到的压力小,导致辊压后的物料成品率低,影响台产;物料粒度过大时容易造成辊压机产生振动或跳停,因此在正常生产过程中要注意保持熟料仓的料位,避免因物料离析形成的物料颗粒变化对生产产生影响。
2.2 研磨体级配的调整由于物料经辊压破碎后,入磨物料的粒度(比表面积)已经达到160~200 m2/kg,达到了不带辊压机的闭路粉磨系统的粉磨能力,因此磨内研磨体级配要进行合理优化。
最初按设计给定的级配进行生产,出磨水泥细度在0.1%~0.2%之间(0.08 mm方孔筛),现场取样做循环负荷测定,过粉磨现象严重。
2008年利用大修机会对级配重新进行调整(表2),调整后出磨水泥细度在0.7%~1.0%之间,磨机产量明显提高。
粉磨工艺

粉磨作业的基本流程(一)、基本概念粉磨流程又称为粉磨系统。
它对粉磨作业的产量、质量、电耗、投资、维护管理费用等都有十分重要的影响。
水泥厂的粉磨作业有生料、水泥和煤粉三部分。
本书只介绍生料和水泥的粉磨流程,关于煤的粉磨流程见“硅酸盐工业热工过程及设备”一书。
一、基本概念开路系统:在粉磨过程中,物料一次通过磨机后即为产品,如图2—48所示,称为开路系统。
闭路系统:在粉磨过程中,物料出磨后经过分级设备选出产品,粗料返回磨内重磨,如图2—49所示,称为闭路系统。
系统级数:粉磨物料通过一个磨制得成品的称为一级系统。
粉磨物料先后通过两个磨制得成品的称为二级系统。
循环负荷率:循环负荷率K是指选粉机的回料量T与成品量Q之比,见图2—49以百分数表示。
设 F——选粉机的喂料量(吨/时);T——选粉机的回料量(吨/时):Q——选粉机的成品量(吨/时);a——选粉机的喂料细度(通过某一筛孔的百分数);b——选粉机的回料细度(通过某一筛孔的百分数):c——选粉机成品的细度(通过某一筛孔的百分数)。
根据物料平衡得F=T+QF·a=T·b+Q·c二式联立得(T+Q)a=T·b+Q·cT(a-b)=Q(c-a)(2—47) 各种不同粉磨系统的循环负荷率一般在下述范围内:一级闭路水泥磨 K=150~300%二级闭路水泥磨(短磨) K=300~600%一级闭路干法生料磨 K=200~450%风扫生料磨 K=50~150%一级闭路湿法生料磨 K=50~300%循环负荷率与磨机的长度有关,磨机愈长,出磨物料的细度愈细(a值愈大),循环负荷率愈低。
选粉效率:选粉效率E是指选粉后成品中所含细粉量与选粉机喂料中细粉量之比。
以百分数表示,其计算公式如下:(2—48)生产实践中常用筛余的百分数表示.如以a′、b′、c′分别表示相应子a、b、c某一筛孔的筛余百分数,则(2—49)选粉效率的高低与选粉机的分级性能和循环负荷率的大小有关。
水泥粉磨系统堵料原因及解决措施

2019年第6期0前言近些年来,辊压机水泥部分终粉磨系统以其适应性强、操控方便、产能高、电耗低等特点在国内水泥行业中得到广泛认可,目前绝大多数水泥辊压机粉磨系统未配置热风供给,利用熟料一定的温度,通过选粉系统充分热交换来烘干混合材,使水泥成品满足质量要求。
但是部分现场由于采用水分较高的工业废渣加之受当地气候环境的影响,致使入水泥磨物料综合水分偏高,出现个别环节堵料的现象。
在此就祁连山某现场水泥粉磨系统堵料问题从设计的角度进行分析,提出解决方案,供大家参考。
1项目背景祁连山某水泥有限公司2016年改造水泥粉磨系统,通过新增辊压机TRP180-120(2×1250kW )与原有的Φ4.2m×13.5m (3350kW )水泥磨组成双圈流水泥部分终粉磨系统,部分终粉磨系统流程图见图1。
图1部分终粉磨系统流程图投产两年来系统产量为250~260t/h ,系统综合电耗~29.5kWh/t 。
自2019年该系统开始采用脱硫石膏替代天然石膏,同时混合材中采用水分5%~6%选矿废渣,导致生产P·C32.5R 时水泥入磨综合水分1.41%。
出现新鲜料进入辊压机循环斗提的溜子处堵料的现象,每班均需要人工清理,部分环节观察孔出现水珠结露的现象,负责辊压机、中间仓、入料环节的收尘器有糊袋的现象,收尘器回灰溜子、辊压机系统选粉机的粗粉回料溜子等地方也有堵料现象,需要人工定期去敲打振动疏通。
分析现场生产中控操作画面、部分原始数据,我们从设计的角度出发,认为通过少量的调整和改造,能够一定程度上解决水泥粉磨生产辊压机环节的频繁堵料问题。
2主要思路和具体做法该系统水泥粉磨环节物料水分的蒸发主要依赖熟料温度和粉磨环节的做功热来实现。
现场熟料入粉磨系统温度110℃。
生产P·C32.5R 水泥时物料综合水分为1.4%。
针对现有条件,主要考虑从以下方面着手:(1)水分排出主要通过各个收尘器风机烟囱排出系统。
水泥磨粉DCS控制系统-可用
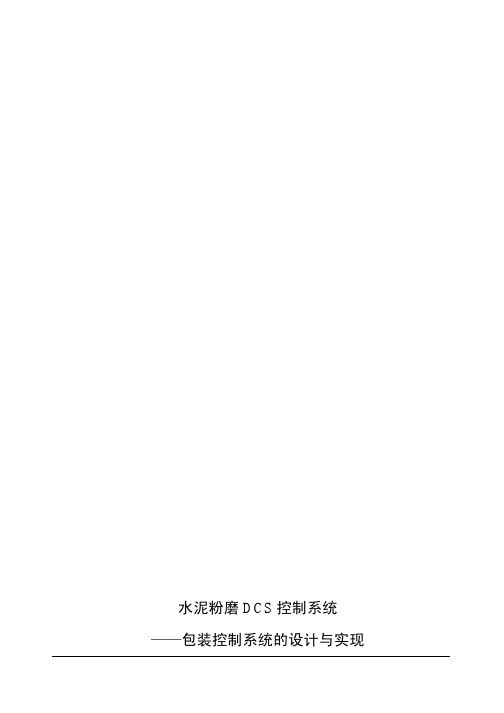
水泥粉磨DCS控制系统——包装控制系统的设计与实现摘要ABSTRACT1概述2方案论证2.1 集散控制系统的简介集散控制系统(Distributed Control System)是以微处理器为基础的集中分散型控制系统。
集中控制系统是进行集中管理的,而系统的体系结构是分布式的,总体上是一种分布结构的控制系统。
DCS控制系统有以下特点:⑴DCS系统作为计算机控制系统中较为完善和成熟的技术,能够对分布于较大范围内的执行机构进行控制,并采用集中管理、分散控制的策略。
⑵DCS系统编程灵活,可以方便地实现历史数据存储、动态显示、报表打印等功能。
⑶DCS可采用组态软件,容易组态,系统集成方便,可靠性高。
2.2 Industial IT控制系统简介Industrial IT系统是ABB公司推出的一种全能综合型开放控制系统,该系统融传统的DCS和PLC优点于一体并支持多种国际现场总线标准。
它既具备DCS的复杂模拟回路调节能力、友好的人机界面(HMI)及方便的工程软件,同时又具有与高档PLC指标相当的高速逻辑和顺序控制性能。
系统既可连接常规I/O,又可连接Remote I/O及Profibus、FF、CAN、Modbus等各种现场总线设备。
系统具备高度的灵活性和极好的扩展性,无论是小型生产装置的控制,还是超大规模的全厂一体化控制,甚至对于跨厂的管理控制应用,Industrial IT都能应付自如。
系统分为两级:操作管理级(操作站OS、工程师站ES及网关GS)和过程控制级(过程站PS及现场控制器AC800F)。
在操作管理级上不仅实现传统的控制系统监控操作功能(预定义及自由格式动态画面显示、趋势显示、弹出式报警及操作指导信息、报表打印、硬件诊断等),而且完成配方管理及数据交换等管理功能。
过程控制级实现包括复杂控制在内的各种回路调节(各种PID、比值、Simith……)和高速逻辑控制、顺序控制以及批量间歇控制功能。
每个过程站PS支持5个机架单元,可配置44个I/O模件(1408个I/0点),PS过程站的CPU模件、电源及系统网络接口均可冗余。
浅谈水泥粉磨增加辊压机系统的提产节能改造

l 一 熟 料 仓 ;2 - 石 膏 仓 ;3 - 混 合 材 料 ;4 一 除铁 器 ; 5 一 水 泥 磨 ;6 - 出磨 斗 提 ;7 - 选 粉 机 ;8 - 收 尘机 ;9 一 收 尘器排风机。 图 1 球 磨 闭 路 粉 磨 系 统 流 程 图 表 1 球 磨 系统 主 机 参 数
1 一 辊 压 机 ;2 一 v 型分 级 机 ;3 一 旋 风 分 离 器 ;4 一 循 环 风 机 ;5 - 收 尘器 ;6 - 收尘 排 风 机 ;7 - 水泥磨。 图 2 辊压机 ( 联合 ) 粉 磨 系统 工 艺 流 程 图
前端 增加 辊 压 机 系统 ,对入 磨 物 料进 行 破 碎 , 以 减 轻 磨 机 粉 磨 负 荷 ,主 要 设 备 情 况 如 表 2 。
选
寺匀 ( D E V E L O P M E M G u I D E T 0 B u I L D I N G M A T E R I A L S )
ቤተ መጻሕፍቲ ባይዱ
浅 谈 水 泥 粉 磨 增 加 辊 压 机 系 统 的 提 产 节 能 改 造
李 志 强 ,盛 赵 宝 , 杨 旺 生 , 张 提 提
0 引 言
辊压机 自 2 0世 纪 8 0年 代 引 入 国 内 至 今 , 经
历 了 3 0多 年 的 发 展 ,无 论 在 装 备 还 是 技 术 方 面 均 取 得 到 了长 足 的进 步 [ 1 ] ,在 水 泥 粉 磨 系 统 中 ,辊 压
一
机 以能 量 利 用 率 高 、破 碎 后 物 料 易 磨 性 好 等 特 点 得 到 了广 泛应 用 [ 2 1 ,在 水 泥 粉 磨 系 统 设 计 中基 本 成
辊压机联合粉磨系统问题分析及技改措施

辊压机联合粉磨系统问题分析及技改措施摘要:为了降低综合生产成本,满足日益激烈的水泥市场,进行了一系列的技术改造和工艺参数的优化,最终实现了P·O42.5水泥台时产量、电耗达标,设备运转率高的目标,保证了水泥产品的稳定,为公司销售拓宽市场奠定了良好的基础。
关键词:辊压机;联合粉磨;压力;分级;结构;级配;降耗;一、概述某公司5 000t/d熟料生产线水泥粉磨系统是由辊压机和?4.2m×13m球磨机组成的双闭路粉磨系统承担,投产后,受系统工艺设计等因素影响,系统堵料,设备空转时间长,设备故障多,水泥电耗高,产量低,制约了水泥销售和产品质量。
为了降低综合生产成本,满足日益激烈的水泥市场,我公司受邀对该系统进行了一系列的技术改造和工艺参数的优化,最终实现了P·O42.5水泥台时产量、电耗达标,设备运转率高的目标,保证了水泥产品的稳定,为公司销售拓宽市场奠定了良好的基础。
二、存在问题及技改措施1.技改工艺流程。
原工艺流程:熟料、脱硫石膏及混合材等按一定比例配料后,经带式输送机、配合料提升机、辊压机中间仓,经过辊压后的物料由混合料提升机送入V型选粉机,粗料返回经喂料小仓入辊压机循环辊压,细料由旋风分离器分离后入球磨机中粉磨。
辊压机系统的废气经循环风机分别进入V型选粉机和闭路球磨机系统的高效水平涡流选粉机。
粉煤灰出库经喂料计量设备按水泥配比要求通过空气输送斜槽、提升机和V型选粉机入磨,选出的粗粉入磨粉磨,成品水泥随气流进入袋收尘器,收下的水泥成品由空气输送斜槽送至水泥库。
(1)存在问题及技改措施:由于脱硫石膏、高炉矿渣水分偏大,物料频繁在入辊压机中间仓的下料溜子处堵料,物料流动性不好造成中间仓下料不畅,只能靠岗位工活动棒阀维持生产。
系统频繁堵料造成磨机止料频繁,岗位工清堵劳动强度加大,磨机空转时间长,后滑履瓦温度升高,造成磨机调停,影响了产质量及设备的稳定运行。
通过论证,混合料提升机最大提升量为1 000t/h,拆除配合料提升机后,能够满足配料站物料和出辊压机物料的提升量,且物料直接进V型选粉机后可以将水分随气流带走,减少细粉量。
水泥粉磨系统开、停机操作

水泥粉磨系统开、停机操作设备分组:根据工艺和有关设备的操作要求,系统内设备分成若干组,各组内设备之间、各组之间有联锁关系。
当需要启动某组设备时,操作员只要在屏幕上选择该组,该组内设备就会依次启动或依次停车,使整个系统操作更加安全、快捷、省时。
水泥粉磨系统的分组一般是:稀油站组、水泥库顶输送组、水泥入库输送组、系统排风机及除尘器组、(选粉机组)、磨机组、辊压机组、磨机喂料组、原料及熟料输送组。
一、开车前的准备本系统的全部设备,在启动前,都应作认真的调整检查。
这必须作为一条制度,在以后的生产中严格执行。
1.润滑设备和润滑油量的检查及调整(检查调整的根据是《设备润滑油表》) ,设备的润滑对保证设备的长期安全运转,起着关键性的作用。
润滑油量应达到设备的要求,既不能过多,也不能过少。
油量过多,会引起设备发热;油量过少,设备会因缺油而损坏。
另一方面,要定期检查、补充、更换润滑油。
用油的品种、标号不能错,而且要保证油中无水无杂质。
主要检查项目有以下几点:A.水泥磨主轴承稀油站的油量要恰当,油路要畅通。
B.水泥磨减速机稀油站、滑履油站油量要恰当,油路要畅通。
C.辊压机系统的稀油站、液压站油量要恰当,油路要畅通。
D.所有设备的传动装置,包括减速机、电动机、连轴器等润滑点要加好油。
E.所有设备轴承、活动部件及传动链条等部分要加好油。
F.所有电动执行机构要加好油。
G.检查润滑油是否变质,确定换油与否。
H.箱(机)底部所有放油(水)孔,拧紧堵孔螺栓。
2.设备内部、人孔门、检查门的检查与密封在设备启动前,要对设备内部进行全面检查,清除安装或检修时掉在设备内的杂物,以防止设备运转时卡死或损坏设备,造成不必要的损失。
在设备内部检查完后,将所有人孔门、检修门关闭并严格密封,防止生产时漏风、漏料、漏油等。
3.闸门及各物料定量给料机进口单层棒闸,要开到适当的位置,保证物料的畅通4.重锤翻板阀的检查与调整,所有重锤翻板阀要根据磨机不同负荷进行调整,重锤位置调整要恰当,使翻板阀受到适当的力时,能自动灵活地打开,松手后能关闭严密5.所有阀门的开闭方向及开度的确认6.1 所有的手动阀门在设备启动前,都应打到适当的位置7.2 所有的电动阀门,首先在现场确认能否灵活打开,阀轴与连杆是否松动,然后由中央控制室进行遥控操作,确认中控与现场的开闭方向是否一致,开度与指示是否正确。
年产100万t矿渣微粉生产线立磨系统热工计算及配置
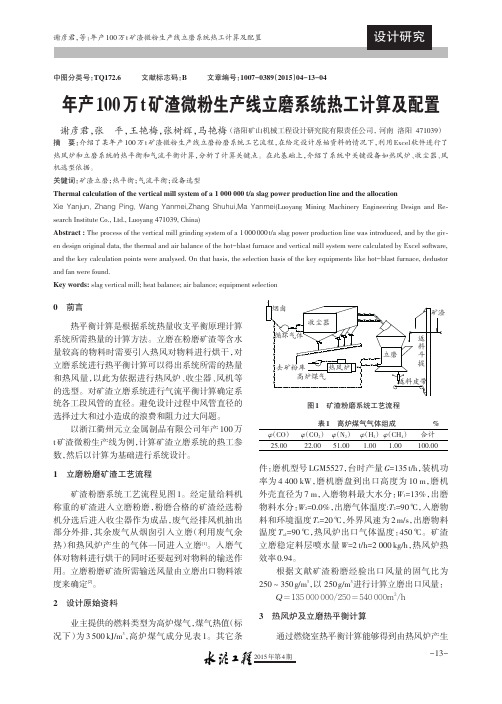
Key words: slag vertical mill; heat balance; air balance; equipment selection
0
前言
热平衡计算是根据系统热量收支平衡原理计算
系统所需热量的计算方法。立磨在粉磨矿渣等含水
量较高的物料时需要引入热风对物料进行烘干,对
search Institute Co., Ltd., Luoyang 471039, China)
Abstract : The process of the vertical mill grinding system of a 1 000 000 t/a slag power production line was introduced, and by the giv⁃
9765.88 kJ
100 m3 煤气化学热和显热
热烟气显热
燃烧用空气显热
高炉煤气化学热:
损失热量
图2
q DW = 3 500 × 100 = 350 000kJ
煤气
燃烧室热量收支项目图
表2
组成
以 100 m3 高炉煤气为基准烟气组成计算表
燃烧所需理论空气量/kmol
O2
N2
0.56
2.52
物质的量/kmol
CO
100×25%/22.4=1.12
CO2
100×22%/22.4=0.98
N2
100×51%/22.4=2.28
H2
100×1%/22.4=0.045
CH4
100×1%/22.4=0.045
合计
4.46
空气过量系数
1.2
辊压机生料终粉磨操作手册课件

目录
• 辊压机生料终粉磨系统简介 • 操作前准备 • 操作步骤 • 常见故障及排除方法 • 维护与保养
01 辊压机生料终粉磨系统简介
系统组成
给料系统
负责将物料均匀送入辊压机,保证连续、稳 定地供料。
卸料装置
辊压机主机
由两个相向转动的辊子组成,通过高压作用 将物料压缩成密实的料饼。
谢谢聆听
主机振动过大
总结词
主机振动过大可能是由于安装基础不牢固、轴承损坏、齿轮磨损等原因引起的。
详细描述
主机振动过大不仅会影响设备寿命,还会导致粉磨效率和质量下降。为了解决这 个问题,需要检查设备安装基础是否牢固,轴承和齿轮的磨损情况,并及时更换 损坏的部件。
粉磨效率低
总结词
粉磨效率低可能是由于物料硬度过高、研磨体配置不当、通 风不畅等原因引起的。
启动前的准备工作
确保物料准备充足,满足生产需求。
检查设备周围环境是否清洁,确保设备运行环境 良好。
确保设备操作人员熟悉操作规程,具备操作资格 。
安全注意事项
操作人员必须穿戴好劳动保护用品,确保人身 安全。
严禁在设备运行过程中进行维修、检查等作业 ,确保作业安全。
设备运行过程中,应定期检查设备运行状况, 确保设备安全运行。
05 维护与保养
日常维护保养
每日检查
检查辊压机各部件是否正常,润滑系统是否良好,是 否有异常声音或振动。
清洁
保持辊压机表面清洁,无灰尘、杂物,防止对生产造 成影响。
紧固
检查并紧固各连接螺栓、螺母等紧固件,确保设备安 全稳定运行。
定期检查与维修
01
定期对辊压机进行全面检查,包括轴承、齿轮、润 滑系统等关键部位。
水泥厂粉磨系统的节能降耗措施

水泥厂的生产工艺主要是两磨一烧,生料和水泥磨的电力消耗约占水泥厂电力消耗的2/3 左右,占水泥成本的1/3 左右,要大幅度降低电耗,降低成本,提高市场竟争力,必须加强日常生产管理,采用新技术,新工艺来大幅度提高磨机产量,降低单位产量电力消耗,达到提高经济效益的目的。
以下从工艺、电气、设备、运行等多角度谈一下,降低磨机电耗的措施。
一、从工艺角度降低电耗的措施1.磨机的设计与选择是关键因素一般而言,以大磨机取代小磨机,可以增产节电,用效率高的粉磨机取代效率低的球磨机,也可收到显著的节能效果,如立磨、辊压磨、挤压磨、高细磨等,它们的效率都比球磨机高。
2.降低入磨物料粒度,采用“多碎少磨”工艺改造可降低粉磨电耗系统。
在生产实际中入磨粒度不是越小越好,当把入磨平均粒径降低到10mm 以下时,对于磨机产量的增加并不明显。
入磨物料粒度不宜过小,因随着破碎产品粒度的减少,破碎单位产品所消耗的功率在增长。
对于特定的物料而言,进入磨机的粒度存在一个最佳值,在这一点物料的碎、磨能耗最低,根据经验,最佳入磨粒度一般为0.005D(D为磨机筒体有效内径)左右。
原因是当入磨物料小于一定粒径后,即使再减小入磨粒径,增产的效果也不会明显。
特别是对于闭路系统,管磨机至少设为两仓,大球仓是破碎而不是研磨。
当物料小于一定粒径后,只要一仓的级配合理、仓长到位,物料进入二仓完全能够达到所需粒径要求。
3.严格控制物料水分,使入磨物料平均水分在0.5%~1.5%。
若水分大,细粉易糊在研磨体,衬板和隔仓板的篦孔上,使粉磨效率降低,磨机产量降低,当水分达到5%左右时,磨机基本上不能进行工作。
但水分偏低时易出现静电效应,形成静电吸附,从而影响磨机产量,这也是大型水泥磨机粉磨回转窑熟料时,在磨内喷水的原因之一,实践证明入磨物料平均水分在 1.0%左右为宜。
4.控制入磨物料温度水泥磨物料温度高,将对水泥磨的产量、质量、能耗产生较大影响。
入磨物料温度高,物料带入磨内大量热量,加之磨机在研磨时,大部分机械能将转为热能,致使磨内温度较高,而物料的易磨性随温度的升高而降低。
水泥粉磨系统主机设备知识培训

2.3辊压机的应用 辊压机除了用于水泥生料和熟料的粉磨外,还可以用 于煤炭金属矿石,化工原料的脆性物料的粉磨。 辊压机在预粉磨流程中已经取得了明显的经济效益, 即节能25%,但根据国内外大量实验研究获得辊压机在 混合粉磨流程,半终粉磨流程和完全终粉磨流程中可以 获得更显著的经济效益,如全终的电耗可比传统粉磨节 省35%~50%。 2.4辊压机的稳定工作运行条件 ①、喂入的物料粒度应小于工作辊缝,借以形成较密实的料 层,但在高压料层粉碎的可以发生单颗粒破碎的部分除 外。 ②、喂入的物料应具有一定的料压,借以保证物料连续的喂 入辊间,形成较密实的料层、但设计参数,喂料粒度, 粉磨要求相应综合改变后可以免除该项要求。 ③、粉磨时应具有足够大的挤压粉碎力,不过该力对于不同
的粘度下降或变质; 油管:送油 油箱:存油的地方 仪表:对油站的温度、压力、油位进行监控 加热器:当环境温度偏低时,润滑油的粘度发生变化,达 不到设备润滑要求,这就需要对润滑油进行加热; 控制箱:油站通过控制箱来开关油站,同时通过仪表数据 传输给PLC对油站的油压、油温油位等进行连锁保护; 阀门:根据不同设备的润滑要求不同,通过阀门来调节 油量的大小和压力的大小,满足设备的润滑,阀门分进过 滤器阀门(排油用)、短路阀(油不经冷却器)、进冷却 器阀、出冷却器阀、溢流阀(直接回油箱阀)、供各润滑 点的阀门等。 控制要求:
出库物料的除铁问题必须重视,往往是铁块或其它
金属杂质对细碎机造成致命的伤害。 增设预破碎后,球磨机内部结构也要进行相应调整, 尤其是一仓应以提高研磨能力为目标。 有的厂曾尝试过 提高磨机转速来提高产量,但效果不好。从理论上分析, 加预破碎后入磨物料粒度降低,一仓的破碎作用与研磨作 用已退居次要地位。磨速提高,研磨体提升高度增加,破 碎能力增大而研磨能力降低,这显然不符合要求。 采用预破碎系统进行提高磨机产量的改造,低投资是 其最大优势,它主要适合于磨机辅助设备和输送设备富裕 能力有限,以及大幅度升级成本效益不合理的厂家。 2.2.2预粉磨 预粉磨是指球磨机前增设一台粉磨设备,使原有的粉 磨系统大幅度增产的措施。 用于预粉磨的设备主要有短球磨、辊磨、辊压机、筒 辊磨等。上述四种预粉磨设备的能量利用率由低到高依次 为短球磨、辊磨、筒辊磨、辊压机。
- 1、下载文档前请自行甄别文档内容的完整性,平台不提供额外的编辑、内容补充、找答案等附加服务。
- 2、"仅部分预览"的文档,不可在线预览部分如存在完整性等问题,可反馈申请退款(可完整预览的文档不适用该条件!)。
- 3、如文档侵犯您的权益,请联系客服反馈,我们会尽快为您处理(人工客服工作时间:9:00-18:30)。
粉磨系统
• 中卸提升循环磨系统 • (1)工艺流程:物料从磨头喂入,选粉机的回料
分别从磨头、磨尾回入粗磨仓和细磨仓,磨中出 料,经提升机提至选粉机分选。 • 大部分回料(一般占2/3)回入细磨仓,其余部分 回料入粗磨仓,目的是为了改善冷料的流动性, 同时也有利于磨内的物料平衡。 • 粗、细磨分开有利于最佳配球,过粉磨少,粉磨 效率高。
• 某公司水泥生产工艺流程图
粉磨系统
• 开、闭路的特点
开路流程: 优点是:流程简单,设备少,投资少,操作简便。
缺点是:由于物料全部达到细度要求后才能出磨,以备 磨细的物料在磨内出现过粉磨现象,并形成缓冲电层, 妨碍粗了进一步磨细,从而降低了粉磨效率,增加电耗。
闭路流程: 优点:将合格细粉即时选出,减少了过粉磨现象,产量
比同规格的开路磨提高15%~25%。产品粒度较均齐, 颗粒组成较理想。磨制水泥时3 ~ 30um的颗粒较多, 强度较高。磨制生料时较大颗粒少,可使熟料中游离石 灰含量较少。产品细度易于调节。使用于生产不同细度 要求的水泥。散热面积大,磨内温度较低。 缺点:流程复杂、设备多、投资大、厂房高、操作麻烦、 维修工作量大。
并画图说明。
粉磨系统
• 简化提升循环磨系统 • (1)工艺流程:是一种气体净化系统和选
粉系统合一的流程,将粗粉分离和选粉任 务结合在一起,既接受提升机的喂料,又 接受出磨气体由气力提升的粉尘,从而使 整个系统大大简化。该流程尾卸和中卸磨 均可应用,以尾卸为例,如图。
简化提升循环磨系统
粉磨系统
• 立式磨系统 • (1)工艺流程: • 它是根据料床粉磨原理,通过相对运动的
粉磨系统
• 干法生料粉磨系统 :
风扫磨系统 尾卸提升循环磨系统 中卸提升循环磨系统 简化提升循环磨系统 立式磨系统 选粉烘干系统
风扫磨系统
粉磨系统
• 风扫磨系统 • (1)工艺流程:物料和热气流一同进入磨
内,一面粉磨,一面烘干。粉磨到一定细 度的物料由热气流扫出磨机并借助气力提 升至粗粉分离器中,分选出的粗粉回磨重 新粉磨,细粉由细粉分离器收回作为成品。 如果原料水分小,烘干用风量比风扫或提 升需风量少,则有部分回风回入磨机或磨 尾,提升管中再进行循环。
粉磨系统
• 水泥粉磨系统
开路长磨和中长磨
水 泥
闭路长磨和中长磨
粉 磨
闭路中线磨
系 统
辊压机系统
立式磨系统
作业:
• 1、简述球磨机的工作原理。 • 2、研磨体在磨机中有几种运动状态?各有
何特点? • 3、简述球磨机的分类。 • 4、磨机规格如何表示? • 5、简述闭路粉磨和开路粉磨各有何优点,
磨辊、磨盘碾磨装置来粉磨物料的机械。
立式磨系统
粉磨系统
• 立式磨系统 • (2)优点: • 入磨粒度大(一般为40~100mm,甚至可达
120mm); • 烘干能力强(可烘干水分8% ~ 10%甚至20%的
原料); • 电耗低; • 粉磨效率高、产量高、噪音低、控制方便、运转
率高等。 • 目前在水泥工业特别是生产粉磨中被广泛运用。
物料返回磨内重磨的流程为
闭路流程。
粉成品
T
Q
Q
F
• 开路粉磨系统:出磨水泥即是成品。
• 特点:系统简单,投资省,厂房小。
• 缺点:过粉磨现象严重,粉磨效率低,单位电耗 大,球耗高,特别不适应高标号水泥的生产。
物料
不合格物料 回磨
闭路粉磨
选粉机 合格物料为成品
粉磨系统
• 尾卸提升循环磨系统 • (1)工艺流程:和风扫磨的基本区别在于
烘干粉磨后的物料由尾端卸出后用提升机 送入选粉机。热气流经磨机尾端的卸料罩 抽出并通过收成设备排除。
粉磨系统
• 尾卸提升循环磨系统
• (2)特点: • 这种系统的通风阻力较大。一般允许进料端风速
为3~4m/s。 • 利用窑尾废气能烘干水分为4% ~ 5%的物料,若
粉磨系统
• 选分烘干系统 • 工艺流程:它是一种磨外烘干系统。烘干介质通
入选粉机而不入进磨。但是为了提高烘干兼粉磨 系统的效果,也有在磨内通风的基础上,同时进 入选粉烘干的。这种系统实质上已经是磨内磨外 同时烘干的系统了。 • 干法生料烘干兼粉磨系统还有:带有粒式烘干塔 的粉磨系统及带有预破碎的烘干兼粉磨系统。
粉磨系统
• 风扫磨系统 • (2)特点: • 风扫磨的长径比小,进料中空轴大,磨尾没有出
料笓板,故通风阻力小。 • 利用窑尾废气,可烘干水分8%的物料;若另设热
源,入磨物料水分15%。本系统粉磨效率较低, 单位理论功的产量比提升循环磨低15%-20%。 • 现代化的大型风扫磨烘干能力大,系统简单,维 修工作量小,操作容易,又能充分利用窑尾废热, 近年来又重新得到发展,以出现了 5.8m×14.75m、产量约350t/h的大型风扫磨。
粉磨系统
粉磨系统
• 1、粉磨系统概念: • 按一定粉磨流程配置的主机及辅机组
成的系统称作粉磨系统。
生料
• 2、水泥厂的粉磨作业有三部分 水 泥
煤粉
粉磨系统
• 3、开、闭路流程
开路流程:
在粉磨过程中,物料仅通过 磨机一次,卸出来即为成品
的流程为开路流程。
闭路流程:
物料出磨后经分级设备分选, 合格的细粉为成品,偏粗的
中卸提升循环磨系统
粉磨系统
• 中卸提升循环磨系统 • (2)特点:大部分热风(一般占80%~
90%)从磨头进,小部分热风从磨尾进。 如利用窑尾废气可烘干水分为6% ~ 7%的 物料;若另设热源,可烘干水分为14%的 物料。
• 这种系统从烘干作用来说,是风扫磨和尾 卸提升循环磨相结合;从粉磨作用来说实 际上相当于两级闭路。适用于大型化。