各种硅酸盐水泥的标准
硅酸盐水泥标号
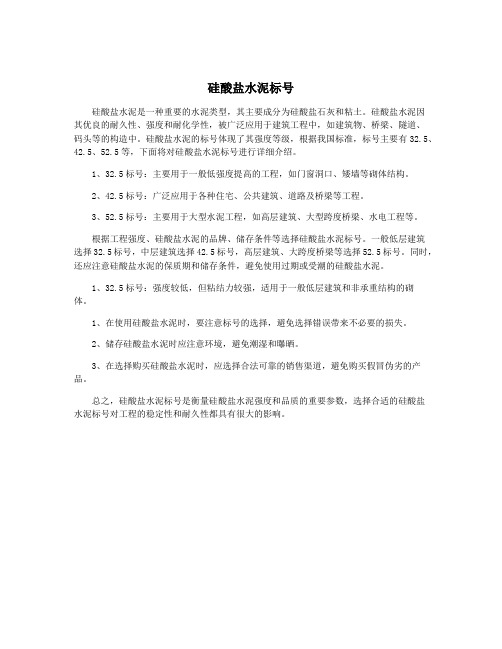
硅酸盐水泥标号
硅酸盐水泥是一种重要的水泥类型,其主要成分为硅酸盐石灰和粘土。
硅酸盐水泥因
其优良的耐久性、强度和耐化学性,被广泛应用于建筑工程中,如建筑物、桥梁、隧道、
码头等的构造中。
硅酸盐水泥的标号体现了其强度等级,根据我国标准,标号主要有32.5、42.5、52.5等,下面将对硅酸盐水泥标号进行详细介绍。
1、32.5标号:主要用于一般低强度提高的工程,如门窗洞口、矮墙等砌体结构。
2、42.5标号:广泛应用于各种住宅、公共建筑、道路及桥梁等工程。
3、52.5标号:主要用于大型水泥工程,如高层建筑、大型跨度桥梁、水电工程等。
根据工程强度、硅酸盐水泥的品牌、储存条件等选择硅酸盐水泥标号。
一般低层建筑
选择32.5标号,中层建筑选择42.5标号,高层建筑、大跨度桥梁等选择52.5标号。
同时,还应注意硅酸盐水泥的保质期和储存条件,避免使用过期或受潮的硅酸盐水泥。
1、32.5标号:强度较低,但粘结力较强,适用于一般低层建筑和非承重结构的砌
体。
1、在使用硅酸盐水泥时,要注意标号的选择,避免选择错误带来不必要的损失。
2、储存硅酸盐水泥时应注意环境,避免潮湿和曝晒。
3、在选择购买硅酸盐水泥时,应选择合法可靠的销售渠道,避免购买假冒伪劣的产品。
总之,硅酸盐水泥标号是衡量硅酸盐水泥强度和品质的重要参数,选择合适的硅酸盐
水泥标号对工程的稳定性和耐久性都具有很大的影响。
通用硅酸盐水泥的国家标准

28d ≥42.5 ≥52.5 ≥62.5
≥42.5
≥27.0 ≥10.0
≥52.5
≥15.0 ≥15.0
≥32.5
≥19.0
≥21.0
≥23.0
≥42.5
≥52.5
抗折强度
3d ≥3.5 ≥4.0 ≥4.0 ≥5.0 ≥5.0 ≥5.5 ≥3.5 ≥4.0
≥4.0
28d ≥6.5 ≥7.0 ≥8.0
Page:
品渣硅酸 盐水泥
火山灰质 硅酸盐 水泥
粉煤灰硅 酸盐水 泥
复合硅酸 盐水泥
代号
P·I P·Ⅱ P·O P·S·A P·S·B
P·P
P·F P·C
通用硅酸盐水泥的国家标准
熟料+石膏
100 ≥95 ≥95 ≥80 且 <95 ≥50 且 <80 ≥30 且 <50
Page:
通用硅酸盐水泥的国家标准
5、合格品与不合格品 凡检验结果符合GB175-2007的7.1、7.3.1、7.3.2、7.3.3 的规定为合格品。
• 凡检验结果不符合GB175-2007的7.1、7.3.1、7.3.2、 7.3.3中的任何一项技术要求为合格品。
Page:
≥60且 <80
粒化高炉 矿渣
≤5 -
>20且 ≤50b
>50且 ≤70b
-
组分 火山灰质 混合材料
>5且≤20a
-
-
>20且 ≤40c
粉煤灰
-
-
-
≥60且 <80
-
≥50且 <80
-
>20且 ≤40d
>20且≤50e
钢渣道路硅酸盐水泥标准
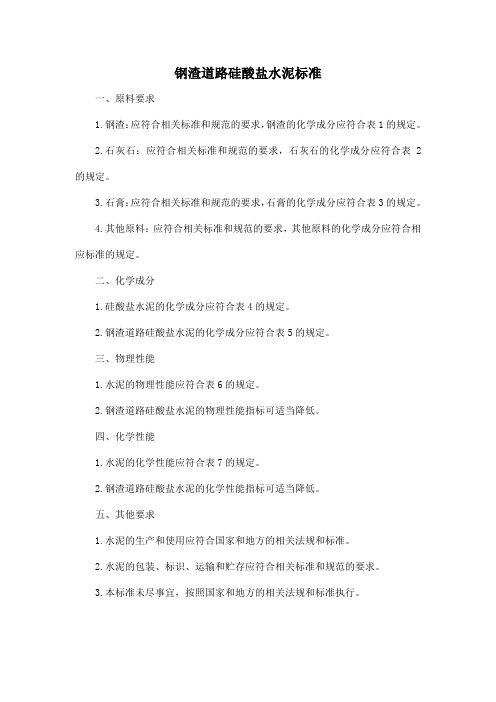
钢渣道路硅酸盐水泥标准
一、原料要求
1.钢渣:应符合相关标准和规范的要求,钢渣的化学成分应符合表1的规定。
2.石灰石:应符合相关标准和规范的要求,石灰石的化学成分应符合表2的规定。
3.石膏:应符合相关标准和规范的要求,石膏的化学成分应符合表3的规定。
4.其他原料:应符合相关标准和规范的要求,其他原料的化学成分应符合相应标准的规定。
二、化学成分
1.硅酸盐水泥的化学成分应符合表4的规定。
2.钢渣道路硅酸盐水泥的化学成分应符合表5的规定。
三、物理性能
1.水泥的物理性能应符合表6的规定。
2.钢渣道路硅酸盐水泥的物理性能指标可适当降低。
四、化学性能
1.水泥的化学性能应符合表7的规定。
2.钢渣道路硅酸盐水泥的化学性能指标可适当降低。
五、其他要求
1.水泥的生产和使用应符合国家和地方的相关法规和标准。
2.水泥的包装、标识、运输和贮存应符合相关标准和规范的要求。
3.本标准未尽事宜,按照国家和地方的相关法规和标准执行。
六种水泥细度标准

六种水泥细度标准
六种水泥细度标准如下:
1.硅酸盐水泥:比表面积应大于300m²/kg;
2.普通硅酸盐水泥:比表面积应大于350m²/kg;
3.矿渣硅酸盐水泥:比表面积应大于300m²/kg;
4.火山灰质硅酸盐水泥:比表面积应大于280m²/kg;
5.粉煤灰硅酸盐水泥:比表面积应大于280m²/kg;
6.复合硅酸盐水泥:比表面积应大于350m²/kg。
水泥细度是指水泥颗粒的粗细程度,它是影响水泥性能的重要因素之一。
水泥颗粒越细,其比表面积越大,与水反应的表面积越大,硬化后的强度也越高。
因此,水泥细度的控制对于保证水泥质量至关重要。
以上六种水泥细度标准是针对不同类型的水泥而定的,符合国家标准要求。
普通硅酸盐水泥强度等级有42
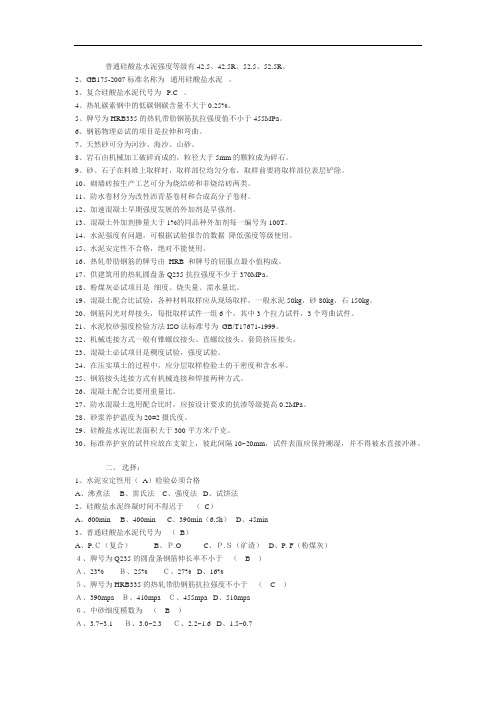
普通硅酸盐水泥强度等级有42.5、42.5R、52.5、52.5R。
2、GB175-2007标准名称为通用硅酸盐水泥。
3、复合硅酸盐水泥代号为P.C 。
4、热轧碳素钢中的低碳钢碳含量不大于0.25%。
5、牌号为HRB335的热轧带肋钢筋抗拉强度值不小于455MPa。
6、钢筋物理必试的项目是拉伸和弯曲。
7、天然砂可分为河沙、海沙、山砂。
8、岩石由机械加工破碎而成的,粒径大于5mm的颗粒成为碎石。
9、砂、石子在料堆上取样时,取样部位均匀分布,取样前要将取样部位表层铲除。
10、砌墙砖按生产工艺可分为烧结砖和非烧结砖两类。
11、防水卷材分为改性沥青基卷材和合成高分子卷材。
12、加速混凝土早期强度发展的外加剂是早强剂。
13、混凝土外加剂掺量大于1%的同品种外加剂每一编号为100T。
14、水泥强度有问题,可根据试验报告的数据降低强度等级使用。
15、水泥安定性不合格,绝对不能使用。
16、热轧带肋钢筋的牌号由HRB 和牌号的屈服点最小值构成。
17、供建筑用的热轧圆盘条Q235抗拉强度不少于370MPa。
18、粉煤灰必试项目是细度、烧失量、需水量比。
19、混凝土配合比试验,各种材料取样应从现场取样,一般水泥50kg,砂80kg,石150kg。
20、钢筋闪光对焊接头,每批取样试件一组6个,其中3个拉力试件,3个弯曲试件。
21、水泥胶砂强度检验方法ISO法标准号为GB/T17671-1999。
22、机械连接方式一般有锥螺纹接头、直螺纹接头、套筒挤压接头。
23、混凝土必试项目是稠度试验,强度试验。
24、在压实填土的过程中,应分层取样检验土的干密度和含水率。
25、钢筋接头连接方式有机械连接和焊接两种方式。
26、混凝土配合比要用重量比。
27、防水混凝土选用配合比时,应按设计要求的抗渗等级提高0.2MPa。
28、砂浆养护温度为20±2摄氏度。
29、硅酸盐水泥比表面积大于300平方米/千克。
30、标准养护室的试件应放在支架上,彼此间隔10~20mm,试件表面应保持潮湿,并不得被水直接冲淋。
各种硅酸盐水泥的标准

各种硅酸盐水泥的标准各种硅酸盐水泥的标准通用硅酸盐水泥《通用硅酸盐水泥标准》由国家质量监督检验检疫总局和国家标准化管理委员会于2021年11月9日发布,2021年6月1日起实施,标准个性编号GB175-2021。
该标准自实施之日起代替之前三个水泥标准,分别为:GB175-1999《硅酸盐、普通硅酸盐水泥》、GB1344-1999《矿渣硅酸盐水泥、火山灰质硅酸盐水泥》、GB12958-1999《复合硅酸盐水泥》。
其与欧洲水泥标准EN197-1:2000《通用波特兰水泥》的一致性为非等效。
与GB175-1999、GB1344-1999、GB12958-1999相比,GB175-2021标准作了28项修改,主要取消了普通水泥中32.5水泥等级,限制了混合材品种,调整了部分水泥的混合材掺材量,增加了氯离子的限量要求,严格了包装水泥重量要求等。
标准修订编制说明自1953年我国第一个统一的水泥标准诞生至今,我国通用硅酸盐水泥标准已经历了4次修订.1996年我国开始了强度检验方法等同采用ISO标准的研究,1999年颁布了以新强度检验方法标准为核心的六大通用水泥标准,这标志着我国水泥标准已完全与国际接轨.在1998~1999年修订GB175,GB1344,GB12958三项标准时,主要是配合我国水泥强度检验方法与国际接轨,在原92版标准的基础上只对水泥强度检验方法和强度标号进行了修订,大部分内容维持了92版标准.这样现行标准在实施中一些问题就显现出来,针对这些问题,中国建材院水泥新材所于2021年开始修订水泥标准,现已完成报批稿.现行标准在使用中出现的问题1,关于三项标准的整合GB175-1999\GB1344-1999\GB12958-1999按照国家标准化管理委员会对国家标准进行清理整顿的要求,同时参考欧洲水泥标准EN197-1:2000《通用波特兰水泥》,此次修订将三项标准合并为一个标准,统称为通用硅酸盐水泥2,关于定义和组成按照GB/T1.1-2000《标准化工作导则》的要求,定义中不能包含要求,水泥组分的含量不能在定义中体现.3,关于普通硅酸盐水泥的名称及取消普通32.5水泥的理由我国普通硅酸盐水泥是五十年代初学习苏联标准而得名的.由于普通硅酸盐水泥性能是硅酸盐熟料起主导作用,混合材起辅助作用,而少量的混合材对于节能,环保等方面有明显的社会经济效益,其使用量约占70%.近几年来,新型水泥生产工艺不断发展,水泥熟料质量的不断提高,粉磨技术的不断进步,为水泥中多掺混合材创造了条件,因此水泥品种设置和强度等级不匹配的问题愈来愈突出,绝大部分水泥企业按标准规定加入混合材实际是无法生产出32.5等级的普通水泥,如果不突破混合材掺量就肯定是富裕强度很大,甚至超出二个强度等级,由于水泥产品附加值很低,这样一来水泥企业损失很大.根据调查结果分析,生产P.O42.5水泥,最大混合材掺加量可以达到26%,平均水平20%;生产P.O32.5水泥,最大混合材掺量可以达到48%,平均28%.因此强度等级与混合材掺量不匹配也是我国普通水泥混合材使用混乱的主要原因.同时,生产水泥熟料需要消耗大量资源,能源,还排放大量有害气体,因此我们希望水泥企业能生产出高品质的水泥熟料,再依据不同工程的需要生产不同品种的水泥.4,关于混合材种类及允许掺量确定通用硅酸盐水泥允许使用混合材的原则:1)保证水泥质量;2)有利于水泥产品质量的管理;3)混合材量大,面广;4)对人体无害.部分水泥的混合材掺量进行了调整,具体见标准.5,关于石膏种类增加了混合石膏.6,关于助磨剂用量1%改为0.5%7,关于技术指标的一些调整.1 本标准与欧洲水泥标准ENV197-1:2000《通用波特兰水泥》的一致性为非等效.2 标准的全文强制改为条文强制.如:碱含量,细度作为选择性指标.3 增加了通用硅酸盐水泥的定义.定义:以硅酸盐水泥熟料,适量的石膏,或/和混合材料制成的水硬性胶凝材料.4 将组分与材料合并为一章原版GB175-1999,GB1344-1999,GB12958-1999第4章,本版第4章.4.1 普通硅酸盐水泥中"掺活性混合材料时,最大掺量不超过15%.其中允许用不超过水泥质量5%的窑灰或不超过水泥质量10%的非活性混合材料来代替"改为"活性混合材料掺加量为>5%且≤20%",其中允许用不超过水泥质量5%且符合本标准4.2.5条的窑灰或不超过水泥质量8%且符合本标准4.2.3条的非活性混合材料代替."_4.2 将矿渣硅酸盐水泥中矿渣掺加量由"20%~70%"改为">20%且≤70%",并分为A型和B 型.A型矿渣掺量>20%且≤50%.代号P.S.A;B型矿渣掺量>50%且≤70%,代号P.S.B;4.3 将火山灰质硅酸盐水泥中火山灰质混合材料掺量由"20%~50%"改为">20%且≤40%";4.4 将复合硅酸盐水泥中混合材料总掺加量由"应大于15%,但不超过50%"改为">20%且≤50%"4.5 材料中增加了粒化高炉矿渣粉;4.6 取消了复合硅酸盐水泥中允许掺加粒化精炼铬铁渣,粒化增钙液态渣,粒化碳素铬铁渣,粒化高炉钛矿渣等混合材料及符合附录A新开辟的混合材料,并将附录A取消;1 我国现行标准中规定了不同品种水泥混合材料的掺加量超过允许掺量为不合格品,但标准中没有明确混合材料掺加量的测定方法,从而引起了广泛的争议.2 混合材掺量作为合格判定项目产生在GB175-1999和GB1345-1999标准中,不合格品判定条款中规定"凡水泥细度……或混合材掺加量超过最大限量时……为不合格品".这一条款产生于1984年.当时我国刚刚进行改革开放,水泥年产量接近14000万吨,严重供不应求.为了满足经济建设的需要小水泥工业得到了很大的发展,但多数立窑熟料质量差,生产水泥时大都需要依靠掺混合材来改善水泥的安定性,针对这一情况为了防止水泥中混合材的超标,1984年修订时将混合材超量作为水泥不合格判定依据之一.当时既没有可供全国统一使用的混合材测定方法标准,也没有在产品标准中规定的试验方法,然而标准实施后并没有出现如今的问题,主要是当时政府对企业具有无可代替的管束力,只要标准规定,行业主管部门就可以通过行政手段,或制定条例,规程对企业进行干预,所以这一规定对保证我国水泥质量,促进水泥质量提高起到了重要作用.在今天行业主管职能只限于宏观调空的情况下来执行这一规定,确实存在没有统一方法的困难,虽然各地技术监督部门为了查处水泥中混合材掺量超标问题,采取自选测试方法,指定检测机构的测定结果作为合格判定,甚至处罚的依据.但由于缺乏执法的依据,受罚水泥企业并不服气,而且抱怨很多.因此这一规定已经不在适应我国当前的实际情况,应该进行修订.3 混合材对水泥性能的影响世界各国对通用水泥品种的划分都是以水泥中混合材品种变化和掺加量多少来规定的.这是由于混合材品种和掺加量的变化,会对水泥的性能产生影响.同一种混合材,掺量对水泥性能的影响是渐变的,相同种类的混合材对水泥性能的影响在品质内涵或影响程度上存在较大的差别,正因为可以掺入不同特性的混合材来调整硅酸盐水泥的性能,使得硅酸盐水泥具有更广泛的性能特点和更广泛的适用范围.为了合理使用具有不同性能特点的水泥,世界各国标准都把混合材引起性能变化范围基本相同的水泥划分为一个品种.我国现行标准的品种划分,基本上是建立在上世纪六十年代和七十年代的试验基础上.3.1 矿渣掺量与强度的关系掺加矿渣混合材料对于混合粉磨和分别粉磨的变化规律一致.对于3天,7天抗压强度,随掺量增加呈明显下降趋势,只是在掺量大于50%后,强度下降幅度略微缓和;而对于28天抗压强度,随掺量增加呈下降趋势,但掺量大于35%后强度下降幅度更为明显.矿渣掺量大于50%后性能变化加剧.>50且≤70b>20且≤50b≥50且20且≤40≥60且20且≤40火山灰硅酸盐水泥水泥熟料质量的提高影响水泥性能的变化,而混合材品种与掺量的不同对水泥性能又有很大的影响,但水泥性能随混合材掺量的变化规律与上世纪60~70年代的试验研究结果基本一致.5 增加了M类混合石膏,取消了A类硬石膏(原版GB175-1999,GB1344-1999,GB12958-1999中第3章,本版第4.2.2.1条)4.2.2.1 天然石膏:应符合GB/T 5483中规定的G类或M类二级(含)以上的石膏或4.2.2.2 工业副产石膏:工业生产中以硫酸钙为主要成分的副产物.采用工业副产石膏时,应经过试验验证,证明对水泥现行标准中规定水泥可以使用符合相关标准要求的二水石膏和硬石膏.但在水泥实际生产中,为了改善硬石膏与外加剂的适应性,一般多和二水石膏混合用,形成实际上使用的混合石膏;同时以混合石膏形态存在的脱硫石膏也开始广泛用于水泥生产.因此本标准增加允许"混合石膏"种类用于水泥生产.同时,单独使用硬石膏会引起水泥与部分减水剂的不适应,造成急凝,瞬凝现象,因此本标准取消了水泥中允许使用硬石膏的规定.6 助磨剂允许掺量由"不超过水泥质量的1%"改为"不超过水泥质量的0.5%";7 普通水泥强度等级中取消了32.5和32.5R;普通32.5水泥混合材掺量超标的客观原因是:水泥熟料质量的提高及粉磨技术的不断进步,为水泥中多掺混合材料创造了条件,因此水泥品种设置和强度等级不匹配的问题越来越突出,绝大部分水泥企业按标准规定加入混合材料实际是无法生产出32.5等级的普通硅酸盐水泥,如不突破混合材掺量就肯定是富裕强度很大,甚至超出二个等级,由于水泥附加值很低,这样一来水泥企业损失很大.同时生产水泥熟料需要消耗大量资源,能源,还排放大量有害气体.取消普通硅酸盐水泥32.5强度等级,将水泥品种划分为两个层次,如果用户需要高强度等级的水泥主要选择P.Ⅰ,P.Ⅱ,P.O;需要低强度等级水泥主要选择P.S,P.C,P.F,8 将矿渣硅酸盐水泥,火山灰质硅酸盐水泥,粉煤灰硅酸盐水泥和复合硅酸盐水泥中"熟料中的氧化镁含量"改为"水泥中的氧化镁含量",其中要求P.S.A型,P.F型,P.P型,P.C型水泥中的氧化镁含量不大于6.0%,并加注b说明"如果水泥中氧化镁含量大于6.0%时,应进行水泥压蒸试验并合格".S.B型无要求.氧化镁含量超标造成的破坏XRD实验结果9 增加了氯离子限量的要求,即水泥中氯离子含量不大于0.06%说明:由于水泥混凝土中氯离子含量会引起钢筋锈蚀,从而导致混凝土开裂破坏.欧洲所有品种小于0.1%.对予应力应严格控制;日本:普通水泥小于0.035%,早强,超早强,中热,低热,抗硫酸盐等小于0.02%,其它品种没有规定.其他国家没有规定._钢筋的腐蚀――电化学反应过程钢筋混凝土结构中的钢筋腐蚀主要是电化学腐蚀,这是由于混凝土空隙中的水分通常以饱和的氢氧化钙的溶液形式存在,其中还含有一些氢氧化钠和氢氧化钙,pH值为12.5.在这样的强碱性的环境中,钢筋表面形成钝化膜,它是厚度为2×10-9- 6×10-9m 的水化氧化物(nFe203·mH2O),阻止钢筋进一步腐蚀.但是,当钢筋表面的钝化膜受到破坏,成为活化态时,钢筋就容易腐蚀.呈活化态的钢筋表面所发生的腐蚀反应的电化学机理是,当钢筋表面有水分存在时,就发生铁电离的阳极反应和溶液中氧还原的阴极反应,相互以等速度进行,其反应式如下:阳极反应 2Fe-4e-→2Fe2+阴极反应 O2+2H2O+4e-→4OH-腐蚀过程的全反应是阳极反应和阴极反应的组合,在钢筋表面析出氢氧化亚铁,其反应式为2Fe+02+2H20→2Fe2++4OH-→2Fe(0H)24Fe(OH)2+02+2H2O→4Fe(OH)3该化合物被溶解氧化后生成氢氧化铁Fe(OH)3,并进一步生成nFe2O3·mH2O (红锈),一部分氧化不完全的变成Fe304(黑锈),在钢筋表面形成锈层.红锈体积可大到原来体积的4倍,黑锈体积可大到原来的两倍.铁锈体积膨胀,对周围混凝土产生压力,将使混凝土沿钢筋方向开裂,进而使保护层成片脱落,而裂缝及保护层的剥落又进一步导致钢筋更剧烈的腐蚀.氯离子很容易引起钢筋锈蚀,有三种理论解释氯离子锈蚀的电化学作用.(1)氧化膜理论――钢筋在碱性介质中生成氧化膜,可以保护钢筋不受侵蚀,氯离子比其它离子(例如硫酸根离子)更容易通过膜的缺陷或孔隙穿透氧化膜.另一种意见认为氯离子能分散氧化膜使之更宜穿透,引起锈蚀.(2)吸附理论――氯离子吸附于钢筋表面,促进金属离子的水化,因而使金属更容易溶解.(3)过渡络合物理论――按照这个理论,氯离子生成氯化铁,氯化铁自阳极扩散从而破坏Fe(0H)2保护层,使腐蚀继续进行.氯化铁在电极不远处转化为氢氧化铁沉淀,氯离子自阳极传导更多的铁离子.现场的经验及研究表明,对于受氯离子污染的已建结构,0.026%的氯离子浓度足以破坏钝化膜而引起钢筋的破坏.其主要反应式如下,反应最终产物氢氧化铁Fe(0H)3即是铁锈. 2Fe-4e-→2Fe2+Fe2+ +2C1-+4H20→FeC12·4H20FeC12·4H20→2Fe(OH)2↓+2C1-+2H++2H204Fe(OH)2+02+2H2O→4Fe(OH)3↓10 将各强度等级的普通硅酸盐水泥的强度指标改为和硅酸盐水泥一致,将各强度等级复合硅酸盐水泥的强度指标改为和矿渣硅酸盐水泥,火山灰质硅酸盐水泥,粉煤灰硅酸盐水泥一致;11 增加了45μm方孔筛筛余不大于30%作为选择性指标;6.3.4细度(选择性指标)硅酸盐水泥和普通硅酸盐水泥以比表面积表示,不小于300m2/kg;矿渣硅酸盐水泥,火山灰质硅酸盐水泥,粉煤灰硅酸盐水泥和复合硅酸盐水泥以筛余表示,80μm方孔筛筛余不大于10%或45μm方孔筛筛余不大于30%.水泥磨得越细,水泥水化速度越快,强度越高.但与此对应的是水泥需水量增大,干缩增大,施工性能变差等负面影响.在熟料矿物组成,水泥组成固定的情况下,这些就只有通过水泥细度在一定范围内调细度的作用由产品质量保证向性能调控作用转变.增加了选择水泥组分试验方法的原则和定期校核要求.由生产者按GB/T12960或选择准确度更高的方法进行.在正常生产情况下,生产者应至少每月对水泥组分进行校核,年平均值应符合本标准第4.1条的规定,单次检验值应不超过本标准规定最大限量的2%.为保证组分测定结果的准确性,生产者应采用适当的生产程序和适宜的方法对所选方法的可靠性进行验证,并将经验证的方法形成文件.13 将"按0.50水灰比和胶砂流动度不小于180mm来确定用水量"的规定的适用水泥品种扩大为火山灰质硅酸盐水泥,粉煤灰硅酸盐水泥,复合硅酸盐水泥和掺火灰质混合材料的普通硅酸盐水泥 .___ 按GB/T17671进行.但火山灰质硅酸盐水泥,粉煤灰硅酸盐水泥,复合硅酸盐水泥和掺火山灰质混合材料的普通硅酸盐水泥在进行胶砂强度检验时,其用水量按0.50水灰比和胶砂流动度不小于180mm来确定.当流动度小于180mm时,须以0.01的整倍数递增的方法将水灰比调整至胶砂流动度不小于180mm.胶砂流动度试验按GB/T2419进行,其中胶砂制备按GB/T17671进行.14 编号与取样中增加了年生产能力"200万吨以上"的级别.200万吨以上,不超过4000吨为一编号;_____ 120万吨~200万吨,不超过2400吨为一编号;说明:上述对于生产企业的约束,工程依然按照验收规程进行检验,即袋装200吨,散装500吨为一个批号.15 将"出厂水泥应保证出厂强度等级,其余技术要求应符合本标准有关要求"改为"经确认水泥各项技术指标及包装质量符合要求时方可出厂. "16 增加了出厂检验项目.出厂检验项目为6.1,6.3.1,6.3.2,6.3.3条.17 取消了废品判定.18 不合格判定中取消了细度和混合材料掺加量的规定,将判定规则改为"检验结果符合本标准6.1,6.3.1,6.3.2,6.3.3条技术要求为合格品.检验结果不符合本标准6.1,6.3.1,6.3.2,6.3.3条中任何一项技术要求为不合格品. "19 检验报告中增加了"合同约定的其他技术要求 ".20 交货与验收中增加了"水泥安定性仲裁检验时,从水泥取样之日起10天以内完成.如超过10天进行安定性检验不合格,则为不合格."21 包装标志中将"且应不少于标志质量的98% "改为"且应不少于标志质量的99% ".22 包装标志中将"火山灰质硅酸盐水泥,粉煤灰硅酸盐水泥和复合硅酸盐水泥的两侧印刷采用黑色."改为"火山灰质硅酸盐水泥,粉煤灰硅酸盐水泥和复合硅酸盐水泥的两侧印刷采用黑色或蓝色."本文来自: 中国质量热讯社区 [url][/url]中国质量热讯 -质量技术监督人士的网络家园!试说明生产硅酸盐水泥时为什么必须掺入适量石膏?水泥熟料中的铝酸三钙遇水后,水化反应的速度最快,会使水泥发生瞬凝或急凝。
通用硅酸盐水泥取样标准
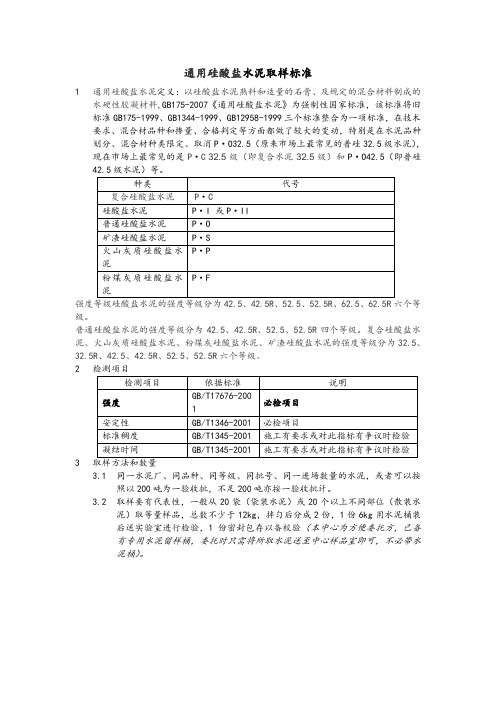
通用硅酸盐水泥取样标准
1通用硅酸盐水泥定义:以硅酸盐水泥熟料和适量的石膏、及规定的混合材料制成的水硬性胶凝材料,GB175-2007《通用硅酸盐水泥》为强制性国家标准,该标准将旧标准GB175-1999、GB1344-1999、GB12958-1999三个标准整合为一项标准,在技术要求、混合材品种和掺量、合格判定等方面都做了较大的变动,特别是在水泥品种划分、混合材种类限定、取消P〃O32.5(原来市场上最常见的普硅32.5级水泥),现在市场上最常见的是P〃C 32.5级(即复合水泥32.5级)和P〃O42.5(即普硅
级。
普通硅酸盐水泥的强度等级分为42.5、42.5R、52.5、52.5R四个等级。
复合硅酸盐水泥、火山灰质硅酸盐水泥、粉煤灰硅酸盐水泥、矿渣硅酸盐水泥的强度等级分为32.5、32.5R、42.5、42.5R、52.5、52.5R六个等级。
2检测项目
3
3.1同一水泥厂、同品种、同等级、同批号、同一进场数量的水泥,或者可以按
照以200吨为一验收批,不足200吨亦按一验收批计。
3.2取样要有代表性,一般从20袋(袋装水泥)或20个以上不同部位(散装水
泥)取等量样品,总数不少于12kg,拌匀后分成2份,1份6kg用水泥桶装
后送实验室进行检验,1份密封包存以备校验(本中心为方便委托方,已备
有专用水泥留样桶,委托时只需将所取水泥送至中心样品室即可,不必带水
泥桶)。
硅酸盐水泥的规格

硅酸盐水泥的规格硅酸盐水泥的规格根据不同国家和地区的标准而有所不同。
以下是常见的硅酸盐水泥规格:1. 欧洲标准:Cements conforming to European Standard EN 197-1。
- CEM I: Portland cement。
- CEM III: Blastfurnace cement。
- CEM IV: Pozzolanic cement。
2.美国标准:ASTMC150。
- Type I: Normal Portland cement。
- Type IA: Normal air-entraining Portland cement。
- Type II: Moderate sulfate resistance Portland cement。
- Type IIA: Moderate sulfate resistance air-entraining Portland cement。
- Type III: High early strength Portland cement。
- Type IIIA: High early strength air-entraining Portland cement。
- Type IV: Low heat of hydration Portland cement。
- Type V: High sulfate resistance Portland cement。
3.中国标准:GB175-2007。
-32.5级硅酸盐水泥。
-42.5级硅酸盐水泥。
-52.5级硅酸盐水泥。
其中,数字表示硅酸盐水泥的抗压强度等级。
例如,32.5级硅酸盐水泥的28天抗压强度为32.5MPa。
通用硅酸盐水泥-GB-175-2007
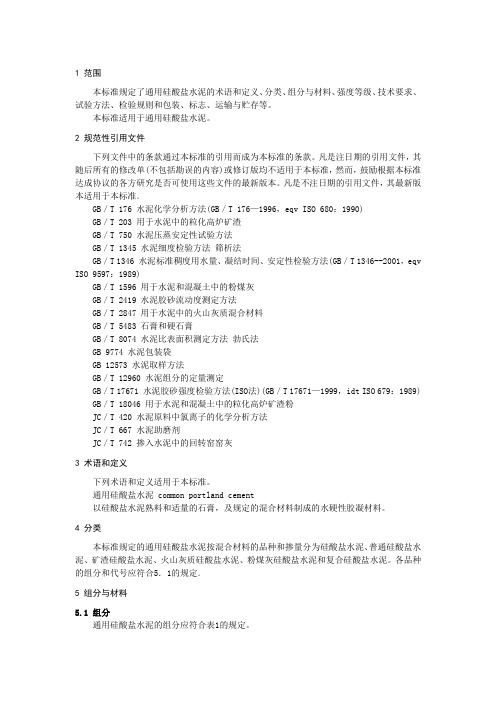
1 范围本标准规定了通用硅酸盐水泥的术语和定义、分类、组分与材料、强度等级、技术要求、试验方法、检验规则和包装、标志、运输与贮存等。
本标准适用于通用硅酸盐水泥。
2 规范性引用文件下列文件中的条款通过本标准的引用而成为本标准的条款。
凡是注日期的引用文件,其随后所有的修改单(不包括勘误的内容)或修订版均不适用于本标准,然而,鼓励根据本标准达成协议的各方研究是否可使用这些文件的最新版本。
凡是不注日期的引用文件,其最新版本适用于本标准。
GB/T 176 水泥化学分析方法(GB/T 176—1996,eqv ISO 680:1990)GB/T 203 用于水泥中的粒化高炉矿渣GB/T 750 水泥压蒸安定性试验方法GB/T 1345 水泥细度检验方法筛析法GB/T 1346 水泥标准稠度用水量、凝结时间、安定性检验方法(GB/T 1346--2001,eqv ISO 9597:1989)GB/T 1596 用于水泥和混凝土中的粉煤灰GB/T 2419 水泥胶砂流动度测定方法GB/T 2847 用于水泥中的火山灰质混合材料GB/T 5483 石膏和硬石膏GB/T 8074 水泥比表面积测定方法勃氏法GB 9774 水泥包装袋GB 12573 水泥取样方法GB/T 12960 水泥组分的定量测定GB/T 17671 水泥胶砂强度检验方法(ISO法)(GB/T 17671—1999,idt ISO 679:1989) GB/T 18046 用于水泥和混凝土中的粒化高炉矿渣粉JC/T 420 水泥原料中氯离子的化学分析方法JC/T 667 水泥助磨剂JC/T 742 掺入水泥中的回转窑窑灰3 术语和定义下列术语和定义适用于本标准。
通用硅酸盐水泥 common portland cement以硅酸盐水泥熟料和适量的石膏,及规定的混合材料制成的水硬性胶凝材料。
4 分类本标准规定的通用硅酸盐水泥按混合材料的品种和掺量分为硅酸盐水泥、普通硅酸盐水泥、矿渣硅酸盐水泥、火山灰质硅酸盐水泥、粉煤灰硅酸盐水泥和复合硅酸盐水泥。
gb 75-2007 通用硅酸盐水泥标准
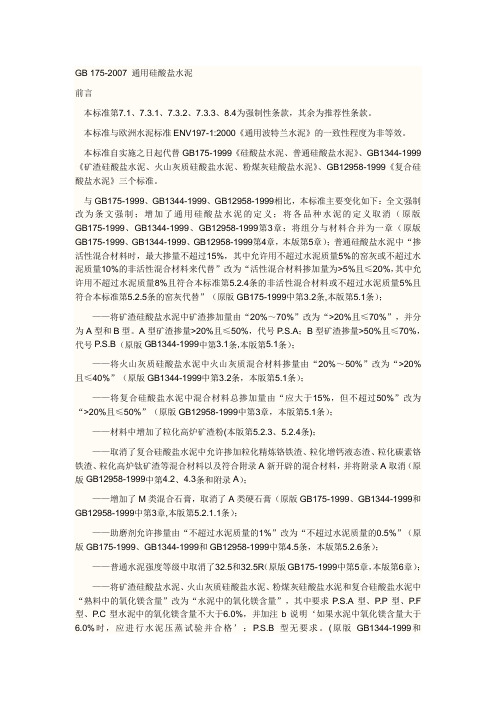
GB 175-2007 通用硅酸盐水泥前言本标准第7.1、7.3.1、7.3.2、7.3.3、8.4为强制性条款,其余为推荐性条款。
本标准与欧洲水泥标准ENV197-1:2000《通用波特兰水泥》的一致性程度为非等效。
本标准自实施之日起代替GB175-1999《硅酸盐水泥、普通硅酸盐水泥》、GB1344-1999《矿渣硅酸盐水泥、火山灰质硅酸盐水泥、粉煤灰硅酸盐水泥》、GB12958-1999《复合硅酸盐水泥》三个标准。
与GB175-1999、GB1344-1999、GB12958-1999相比,本标准主要变化如下:全文强制改为条文强制;增加了通用硅酸盐水泥的定义;将各品种水泥的定义取消(原版GB175-1999、GB1344-1999、GB12958-1999第3章;将组分与材料合并为一章(原版GB175-1999、GB1344-1999、GB12958-1999第4章,本版第5章);普通硅酸盐水泥中“掺活性混合材料时,最大掺量不超过15%,其中允许用不超过水泥质量5%的窑灰或不超过水泥质量10%的非活性混合材料来代替”改为“活性混合材料掺加量为>5%且≤20%,其中允许用不超过水泥质量8%且符合本标准第5.2.4条的非活性混合材料或不超过水泥质量5%且符合本标准第5.2.5条的窑灰代替”(原版GB175-1999中第3.2条,本版第5.1条);——将矿渣硅酸盐水泥中矿渣掺加量由“20%~70%”改为“>20%且≤70%”,并分为A型和B型。
A型矿渣掺量>20%且≤50%,代号P.S.A;B型矿渣掺量>50%且≤70%,代号P.S.B(原版GB1344-1999中第3.1条,本版第5.1条);——将火山灰质硅酸盐水泥中火山灰质混合材料掺量由“20%~50%”改为“>20%且≤40%”(原版GB1344-1999中第3.2条,本版第5.1条);——将复合硅酸盐水泥中混合材料总掺加量由“应大于15%,但不超过50%”改为“>20%且≤50%”(原版GB12958-1999中第3章,本版第5.1条);——材料中增加了粒化高炉矿渣粉(本版第5.2.3、5.2.4条);——取消了复合硅酸盐水泥中允许掺加粒化精炼铬铁渣、粒化增钙液态渣、粒化碳素铬铁渣、粒化高炉钛矿渣等混合材料以及符合附录A新开辟的混合材料,并将附录A取消(原版GB12958-1999中第4.2、4.3条和附录A);——增加了M类混合石膏,取消了A类硬石膏(原版GB175-1999、GB1344-1999和GB12958-1999中第3章,本版第5.2.1.1条);——助磨剂允许掺量由“不超过水泥质量的1%”改为“不超过水泥质量的0.5%”(原版GB175-1999、GB1344-1999和GB12958-1999中第4.5条,本版第5.2.6条);——普通水泥强度等级中取消了32.5和32.5R(原版GB175-1999中第5章,本版第6章);——将矿渣硅酸盐水泥、火山灰质硅酸盐水泥、粉煤灰硅酸盐水泥和复合硅酸盐水泥中“熟料中的氧化镁含量”改为“水泥中的氧化镁含量”,其中要求P.S.A型、P.P型、P.F 型、P.C型水泥中的氧化镁含量不大于6.0%,并加注b说明‘如果水泥中氧化镁含量大于6.0%时,应进行水泥压蒸试验并合格’;P.S.B型无要求。
通用硅酸盐水泥标准
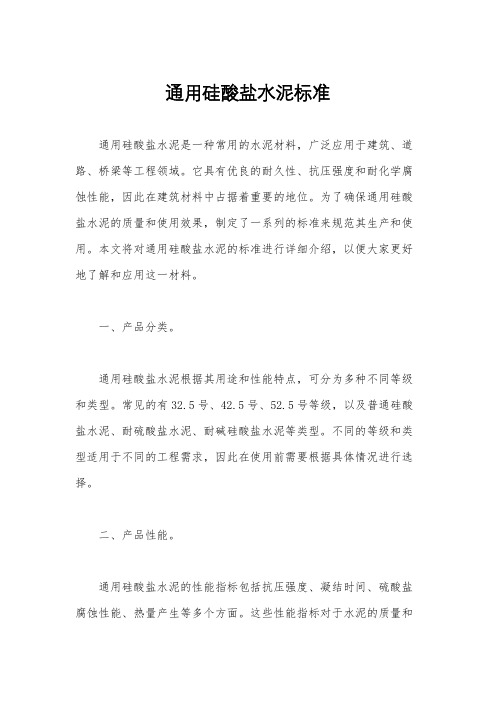
通用硅酸盐水泥标准通用硅酸盐水泥是一种常用的水泥材料,广泛应用于建筑、道路、桥梁等工程领域。
它具有优良的耐久性、抗压强度和耐化学腐蚀性能,因此在建筑材料中占据着重要的地位。
为了确保通用硅酸盐水泥的质量和使用效果,制定了一系列的标准来规范其生产和使用。
本文将对通用硅酸盐水泥的标准进行详细介绍,以便大家更好地了解和应用这一材料。
一、产品分类。
通用硅酸盐水泥根据其用途和性能特点,可分为多种不同等级和类型。
常见的有32.5号、42.5号、52.5号等级,以及普通硅酸盐水泥、耐硫酸盐水泥、耐碱硅酸盐水泥等类型。
不同的等级和类型适用于不同的工程需求,因此在使用前需要根据具体情况进行选择。
二、产品性能。
通用硅酸盐水泥的性能指标包括抗压强度、凝结时间、硫酸盐腐蚀性能、热量产生等多个方面。
这些性能指标对于水泥的质量和使用效果至关重要,生产厂家和使用者都需要严格遵守相关标准要求,确保产品的质量稳定和可靠。
三、生产工艺。
通用硅酸盐水泥的生产工艺主要包括原料选用、熟料烧成、水泥磨矿等多个环节。
在生产过程中,需要严格控制原料配比、烧成温度、磨矿粒度等关键参数,以确保产品的化学成分和物理性能符合标准要求。
此外,生产过程中还需要对废气排放、能源消耗等环保和节能问题进行严格控制,以减少对环境的影响。
四、质量控制。
通用硅酸盐水泥的质量控制涉及原料质量、生产工艺、成品检测等多个方面。
在原料采购和使用过程中,需要对原料进行严格把关,确保其化学成分和物理性能符合要求。
在生产过程中,需要建立健全的质量管理体系,对关键环节进行监控和控制。
此外,还需要对成品进行全面检测,确保产品的质量稳定和可靠。
五、使用规范。
通用硅酸盐水泥的使用规范涉及到施工工艺、养护要求、使用环境等多个方面。
在施工过程中,需要严格按照设计要求和施工工艺进行操作,确保水泥的使用效果。
在养护过程中,需要注意环境温度、湿度等因素,以确保水泥的早期强度和耐久性。
此外,还需要对使用环境进行评估,选择合适的水泥类型和等级。
水泥国家标准GB175_1999
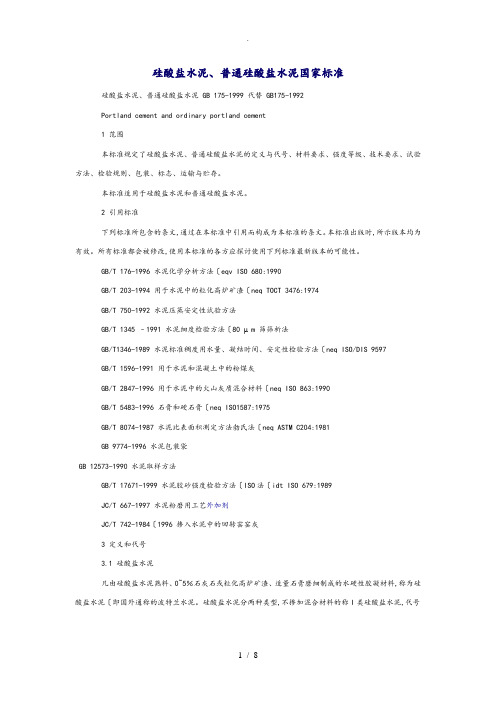
硅酸盐水泥、普通硅酸盐水泥国家标准硅酸盐水泥、普通硅酸盐水泥 GB 175-1999 代替 GB175-1992Portland cement and ordinary portland cement1 范围本标准规定了硅酸盐水泥、普通硅酸盐水泥的定义与代号、材料要求、强度等级、技术要求、试验方法、检验规则、包装、标志、运输与贮存。
本标准适用于硅酸盐水泥和普通硅酸盐水泥。
2 引用标准下列标准所包含的条文,通过在本标准中引用而构成为本标准的条文。
本标准出版时,所示版本均为有效。
所有标准都会被修改,使用本标准的各方应探讨使用下列标准最新版本的可能性。
GB/T 176-1996 水泥化学分析方法〔eqv ISO 680:1990GB/T 203-1994 用于水泥中的粒化高炉矿渣〔neq TOCT 3476:1974GB/T 750-1992 水泥压蒸安定性试验方法GB/T 1345 –1991 水泥细度检验方法〔80 µm 筛筛析法GB/T1346-1989 水泥标准稠度用水量、凝结时间、安定性检验方法〔neq ISO/DIS 9597GB/T 1596-1991 用于水泥和混凝土中的粉煤灰GB/T 2847-1996 用于水泥中的火山灰质混合材料〔neq ISO 863:1990GB/T 5483-1996 石膏和硬石膏〔neq ISO1587:1975GB/T 8074-1987 水泥比表面积测定方法勃氏法〔neq ASTM C204:1981GB 9774-1996 水泥包装袋GB 12573-1990 水泥取样方法GB/T 17671-1999 水泥胶砂强度检验方法〔ISO法〔idt ISO 679:1989JC/T 667-1997 水泥粉磨用工艺外加剂JC/T 742-1984〔1996 掺入水泥中的回转窑窑灰3 定义和代号3.1 硅酸盐水泥凡由硅酸盐水泥熟料、0~5%石灰石或粒化高炉矿渣、适量石膏磨细制成的水硬性胶凝材料,称为硅酸盐水泥〔即国外通称的波特兰水泥。
《通用硅酸盐水泥》的标准
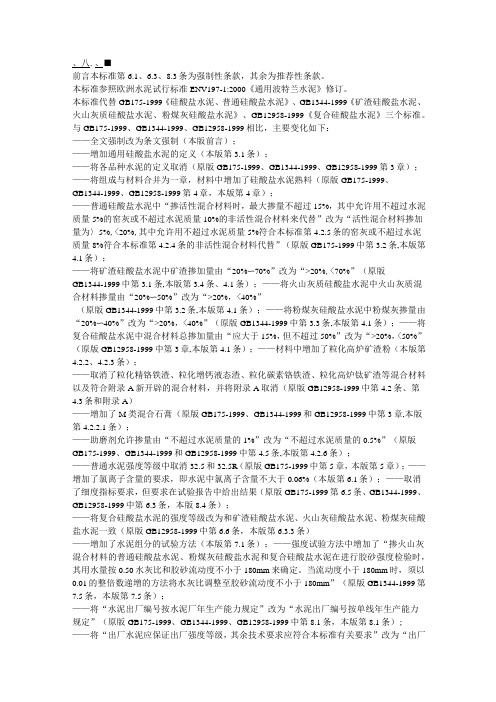
、八.、■前言本标准第6.1、6.3、8.3条为强制性条款,其余为推荐性条款。
本标准参照欧洲水泥试行标准ENV197-1:2000《通用波特兰水泥》修订。
本标准代替GB175-1999《硅酸盐水泥、普通硅酸盐水泥》、GB1344-1999《矿渣硅酸盐水泥、火山灰质硅酸盐水泥、粉煤灰硅酸盐水泥》、GB12958-1999《复合硅酸盐水泥》三个标准。
与GB175-1999、GB1344-1999、GB12958-1999相比,主要变化如下:——全文强制改为条文强制(本版前言);——增加通用硅酸盐水泥的定义(本版第3.1条);——将各品种水泥的定义取消(原版GB175-1999、GB1344-1999、GB12958-1999第3章);——将组成与材料合并为一章,材料中增加了硅酸盐水泥熟料(原版GB175-1999、GB1344-1999、GB12958-1999第4章,本版第4章);——普通硅酸盐水泥中“掺活性混合材料时,最大掺量不超过15%,其中允许用不超过水泥质量5%的窑灰或不超过水泥质量10%的非活性混合材料来代替”改为“活性混合材料掺加量为〉5%,<20%,其中允许用不超过水泥质量5%符合本标准第4.2.5条的窑灰或不超过水泥质量8%符合本标准第4.2.4条的非活性混合材料代替”(原版GB175-1999中第3.2条,本版第4.1条);——将矿渣硅酸盐水泥中矿渣掺加量由“20%〜70%”改为“>20%,<70%”(原版GB1344-1999中第3.1条,本版第3.4条、4.1条);——将火山灰质硅酸盐水泥中火山灰质混合材料掺量由“20%〜50%”改为“>20%,<40%”(原版GB1344-1999中第3.2条,本版第4.1条);——将粉煤灰硅酸盐水泥中粉煤灰掺量由“20%〜40%”改为“>20%,<40%”(原版GB1344-1999中第3.3条,本版第4.1条);——将复合硅酸盐水泥中混合材料总掺加量由“应大于15%,但不超过50%”改为“>20%,<50%”(原版GB12958-1999中第3章,本版第4.1条);——材料中增加了粒化高炉矿渣粉(本版第4.2.2、4.2.3条);——取消了粒化精铬铁渣、粒化增钙液态渣、粒化碳素铬铁渣、粒化高炉钛矿渣等混合材料以及符合附录A新开辟的混合材料,并将附录A取消(原版GB12958-1999中第4.2条、第4.3条和附录A)——增加了M类混合石膏(原版GB175-1999、GB1344-1999和GB12958-1999中第3章,本版第4.2.2.1条);——助磨剂允许掺量由“不超过水泥质量的1%”改为“不超过水泥质量的0.5%”(原版GB175-1999、GB1344-1999和GB12958-1999中第4.5条,本版第4.2.6条);——普通水泥强度等级中取消32.5和32.5R(原版GB175-1999中第5章,本版第5章);——增加了氯离子含量的要求,即水泥中氯离子含量不大于0.06%(本版第6.1条);——取消了细度指标要求,但要求在试验报告中给出结果(原版GB175-1999第6.5条、GB1344-1999、GB12958-1999中第6.3条,本版8.4条);——将复合硅酸盐水泥的强度等级改为和矿渣硅酸盐水泥、火山灰硅酸盐水泥、粉煤灰硅酸盐水泥一致(原版GB12958-1999中第6.6条,本版第6.3.3条)——增加了水泥组分的试验方法(本版第7.1条);——强度试验方法中增加了“掺火山灰混合材料的普通硅酸盐水泥、粉煤灰硅酸盐水泥和复合硅酸盐水泥在进行胶砂强度检验时,其用水量按0.50水灰比和胶砂流动度不小于180mm来确定。
gb175-2024通用硅酸盐水泥标准

gb175-2024通用硅酸盐水泥标准GB175-2024通用硅酸盐水泥标准是中国国家标准,对硅酸盐水泥的技术要求、试验方法、标记、包装、运输和质量证明等进行了详细的规定。
以下是对该标准内容的详细介绍:一、产品分类及技术要求:GB175-2024将硅酸盐水泥分为32.5级、42.5级和52.5级三个等级。
每个等级的硅酸盐水泥都有其特定的技术要求,如化学成分、强度等。
1.化学成分:硅酸盐水泥必须符合特定的化学成分要求,包括主要成分氧化钙(CaO)、二氧化硅(SiO2)、三氧化二铝(Al2O3)、三氧化二铁(Fe2O3)等。
2.强度:对于三个等级的硅酸盐水泥,GB175-2024对其强度也有明确的要求。
其中,32.5级硅酸盐水泥的28天抗压强度不低于32.5MPa,42.5级硅酸盐水泥的28天抗压强度不低于42.5MPa,52.5级硅酸盐水泥的28天抗压强度不低于52.5MPa。
3.物理性能:GB175-2024还对硅酸盐水泥的物理性能进行了详细的要求,包括比表面积、试验时间等。
二、试验方法:为了保证硅酸盐水泥的质量,GB175-2024还规定了一系列的试验方法,以确保硅酸盐水泥的化学成分、物理性能和强度等达到标准要求。
例如,试验方法包括化学分析、物理性能试验和强度试验等。
1.化学分析:硅酸盐水泥的化学成分可以通过化学分析方法来确定,如用化学试剂和设备对硅酸盐水泥样品进行定性和定量分析。
2.物理性能试验:物理性能试验包括比表面积测定、主要矿物组成分析等。
比表面积测定可通过比表面积测定仪进行实验。
3.强度试验:强度试验主要包括抗压强度和抗折强度试验。
通过在一定的条件下对硅酸盐水泥样品进行加载,以测定其抗压强度和抗折强度。
三、标记、包装、运输和质量证明:为了保证硅酸盐水泥的质量和正常使用,GB175-2024还对硅酸盐水泥的标记、包装、运输和质量证明等进行了规定。
1.标记:硅酸盐水泥包装上必须标有生产厂家的名称、商标、产品牌号、生产日期、质量等级等。
通用硅酸盐水泥GB完整版
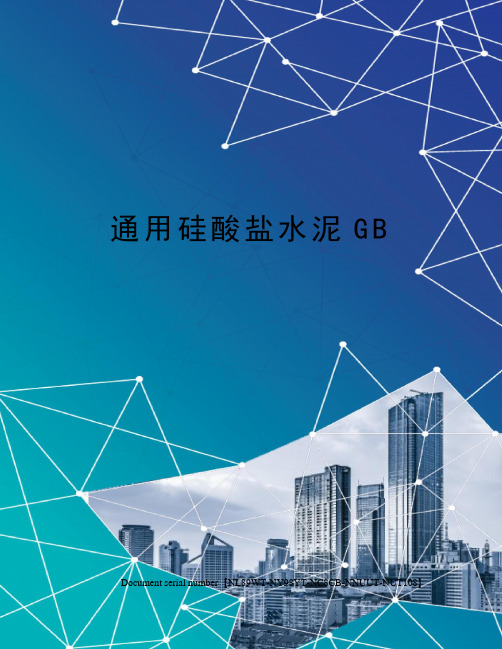
通用硅酸盐水泥G BDocument serial number【NL89WT-NY98YT-NC8CB-NNUUT-NUT108】《通用硅酸盐水泥》GB175-2007?通则前言本标准第、7.3.1、、、为强制性条款,其余为推荐性条款。
本标准与欧洲水泥标准ENV197-1:2000《通用波特兰水泥》的一致性程度为非等效。
本标准自实施之日起代替GB175-1999《硅酸盐水泥、普通硅酸盐水泥》、GB1344-1999《矿渣硅酸盐水泥、火山灰质硅酸盐水泥、粉煤灰硅酸盐水泥》、GB12958-1999《复合硅酸盐水泥》三个标准。
与GB175-1999、GB1344-1999、GB12958-1999相比,本标准主要变化如下:全文强制改为条文强制;增加了通用硅酸盐水泥的定义;将各品种水泥的定义取消(原版GB175-1999、GB1344-1999、GB12958-1999第3章;将组分与材料合并为一章(原版GB175-1999、GB1344-1999、GB12958-1999第4章,本版第5章);普通硅酸盐水泥中“掺活性混合材料时,最大掺量不超过15%,其中允许用不超过水泥质量5%的窑灰或不超过水泥质量10%的非活性混合材料来代替”改为“活性混合材料掺加量为>5%且≤20%,其中允许用不超过水泥质量8%且符合本标准第条的非活性混合材料或不超过水泥质量5%且符合本标准第条的窑灰代替”(原版GB175-1999中第条,本版第条);——将矿渣硅酸盐水泥中矿渣掺加量由“20%~70%”改为“>20%且≤70%”,并分为A型和B型。
A型矿渣掺量>20%且≤50%,代号;B型矿渣掺量>50%且≤70%,代号(原版GB1344-1999中第条,本版第条);——将火山灰质硅酸盐水泥中火山灰质混合材料掺量由“20%~50%”改为“>20%且≤40%”(原版GB1344-1999中第条,本版第条);——将复合硅酸盐水泥中混合材料总掺加量由“应大于15%,但不超过50%”改为“>20%且≤50%”(原版GB12958-1999中第3章,本版第条);——材料中增加了粒化高炉矿渣粉(本版第5.2.3、条);——取消了复合硅酸盐水泥中允许掺加粒化精炼铬铁渣、粒化增钙液态渣、粒化碳素铬铁渣、粒化高炉钛矿渣等混合材料以及符合附录A新开辟的混合材料,并将附录A取消(原版GB12958-1999中第、条和附录A);——增加了M类混合石膏,取消了A类硬石膏(原版GB175-1999、GB1344-1999和GB12958-1999中第3章,本版第5.2.1.1条);——助磨剂允许掺量由“不超过水泥质量的1%”改为“不超过水泥质量的%”(原版GB175-1999、GB1344-1999和GB12958-1999中第条,本版第5.2.6条);——普通水泥强度等级中取消了和(原版GB175-1999中第5章,本版第6章);——将矿渣硅酸盐水泥、火山灰质硅酸盐水泥、粉煤灰硅酸盐水泥和复合硅酸盐水泥中“熟料中的氧化镁含量”改为“水泥中的氧化镁含量”,其中要求型、型、型、型水泥中的氧化镁含量不大于%,并加注b说明‘如果水泥中氧化镁含量大于%时,应进行水泥压蒸试验并合格’;型无要求。
- 1、下载文档前请自行甄别文档内容的完整性,平台不提供额外的编辑、内容补充、找答案等附加服务。
- 2、"仅部分预览"的文档,不可在线预览部分如存在完整性等问题,可反馈申请退款(可完整预览的文档不适用该条件!)。
- 3、如文档侵犯您的权益,请联系客服反馈,我们会尽快为您处理(人工客服工作时间:9:00-18:30)。
通用硅酸盐水泥《通用硅酸盐水泥标准》由国家质量监督检验检疫总局和国家标准化管理委员会于2007年11月9日发布,2008年6月1日起实施,标准个性编号GB175-2007。
该标准自实施之日起代替之前三个水泥标准,分别为:GB175-1999《硅酸盐、普通硅酸盐水泥》、GB1344-1999《矿渣硅酸盐水泥、火山灰质硅酸盐水泥》、GB12958-1999《复合硅酸盐水泥》。
其与欧洲水泥标准EN197-1:2000《通用波特兰水泥》的一致性为非等效。
与GB175-1999、GB1344-1999、GB12958-1999相比,GB175-2007标准作了28项修改,主要取消了普通水泥中32.5水泥等级,限制了混合材品种,调整了部分水泥的混合材掺材量,增加了氯离子的限量要求,严格了包装水泥重量要求等。
标准修订编制说明自1953年我国第一个统一的水泥标准诞生至今,我国通用硅酸盐水泥标准已经历了4次修订.1996年我国开始了强度检验方法等同采用ISO标准的研究,1999年颁布了以新强度检验方法标准为核心的六大通用水泥标准,这标志着我国水泥标准已完全与国际接轨.在1998~1999年修订GB175,GB1344,GB12958三项标准时,主要是配合我国水泥强度检验方法与国际接轨,在原92版标准的基础上只对水泥强度检验方法和强度标号进行了修订,大部分内容维持了92版标准.这样现行标准在实施中一些问题就显现出来,针对这些问题,中国建材院水泥新材所于2004年开始修订水泥标准,现已完成报批稿.现行标准在使用中出现的问题1,关于三项标准的整合GB175-1999\GB1344-1999\GB12958-1999按照国家标准化管理委员会对国家标准进行清理整顿的要求,同时参考欧洲水泥标准EN197-1:2000《通用波特兰水泥》,此次修订将三项标准合并为一个标准,统称为通用硅酸盐水泥2,关于定义和组成按照GB/T1.1-2000《标准化工作导则》的要求,定义中不能包含要求,水泥组分的含量不能在定义中体现.3,关于普通硅酸盐水泥的名称及取消普通32.5水泥的理由我国普通硅酸盐水泥是五十年代初学习苏联标准而得名的.由于普通硅酸盐水泥性能是硅酸盐熟料起主导作用,混合材起辅助作用,而少量的混合材对于节能,环保等方面有明显的社会经济效益,其使用量约占70%.近几年来,新型水泥生产工艺不断发展,水泥熟料质量的不断提高,粉磨技术的不断进步,为水泥中多掺混合材创造了条件,因此水泥品种设置和强度等级不匹配的问题愈来愈突出,绝大部分水泥企业按标准规定加入混合材实际是无法生产出32.5等级的普通水泥,如果不突破混合材掺量就肯定是富裕强度很大,甚至超出二个强度等级,由于水泥产品附加值很低,这样一来水泥企业损失很大.根据调查结果分析,生产P.O42.5水泥,最大混合材掺加量可以达到26%,平均水平20%;生产P.O32.5水泥,最大混合材掺量可以达到48%,平均28%.因此强度等级与混合材掺量不匹配也是我国普通水泥混合材使用混乱的主要原因.同时,生产水泥熟料需要消耗大量资源,能源,还排放大量有害气体,因此我们希望水泥企业能生产出高品质的水泥熟料,再依据不同工程的需要生产不同品种的水泥.4,关于混合材种类及允许掺量确定通用硅酸盐水泥允许使用混合材的原则:1)保证水泥质量;2)有利于水泥产品质量的管理;3)混合材量大,面广;4)对人体无害.部分水泥的混合材掺量进行了调整,具体见标准.5,关于石膏种类增加了混合石膏.6,关于助磨剂用量1%改为0.5%7,关于技术指标的一些调整.标准的内容1 本标准与欧洲水泥标准ENV197-1:2000《通用波特兰水泥》的一致性为非等效.2 标准的全文强制改为条文强制.如:碱含量,细度作为选择性指标.3 增加了通用硅酸盐水泥的定义.定义:以硅酸盐水泥熟料,适量的石膏,或/和混合材料制成的水硬性胶凝材料.4 将组分与材料合并为一章原版GB175-1999,GB1344-1999,GB12958-1999第4章,本版第4章.4.1 普通硅酸盐水泥中"掺活性混合材料时,最大掺量不超过15%.其中允许用不超过水泥质量5%的窑灰或不超过水泥质量10%的非活性混合材料来代替"改为"活性混合材料掺加量为>5%且≤20%",其中允许用不超过水泥质量5%且符合本标准4.2.5条的窑灰或不超过水泥质量8%且符合本标准4.2.3条的非活性混合材料代替."_4.2 将矿渣硅酸盐水泥中矿渣掺加量由"20%~70%"改为">20%且≤70%",并分为A型和B 型.A型矿渣掺量>20%且≤50%.代号P.S.A;B型矿渣掺量>50%且≤70%,代号P.S.B;4.3 将火山灰质硅酸盐水泥中火山灰质混合材料掺量由"20%~50%"改为">20%且≤40%"; 4.4 将复合硅酸盐水泥中混合材料总掺加量由"应大于15%,但不超过50%"改为">20%且≤50%"4.5 材料中增加了粒化高炉矿渣粉;4.6 取消了复合硅酸盐水泥中允许掺加粒化精炼铬铁渣,粒化增钙液态渣,粒化碳素铬铁渣,粒化高炉钛矿渣等混合材料及符合附录A新开辟的混合材料,并将附录A取消;说明:1 我国现行标准中规定了不同品种水泥混合材料的掺加量超过允许掺量为不合格品,但标准中没有明确混合材料掺加量的测定方法,从而引起了广泛的争议.2 混合材掺量作为合格判定项目产生的历史背景在GB175-1999和GB1345-1999标准中,不合格品判定条款中规定"凡水泥细度……或混合材掺加量超过最大限量时……为不合格品".这一条款产生于1984年.当时我国刚刚进行改革开放,水泥年产量接近14000万吨,严重供不应求.为了满足经济建设的需要小水泥工业得到了很大的发展,但多数立窑熟料质量差,生产水泥时大都需要依靠掺混合材来改善水泥的安定性,针对这一情况为了防止水泥中混合材的超标,1984年修订时将混合材超量作为水泥不合格判定依据之一.当时既没有可供全国统一使用的混合材测定方法标准,也没有在产品标准中规定的试验方法,然而标准实施后并没有出现如今的问题,主要是当时政府对企业具有无可代替的管束力,只要标准规定,行业主管部门就可以通过行政手段,或制定条例,规程对企业进行干预,所以这一规定对保证我国水泥质量,促进水泥质量提高起到了重要作用.在今天行业主管职能只限于宏观调空的情况下来执行这一规定,确实存在没有统一方法的困难,虽然各地技术监督部门为了查处水泥中混合材掺量超标问题,采取自选测试方法,指定检测机构的测定结果作为合格判定,甚至处罚的依据.但由于缺乏执法的依据,受罚水泥企业并不服气,而且抱怨很多.因此这一规定已经不在适应我国当前的实际情况,应该进行修订.3 混合材对水泥性能的影响世界各国对通用水泥品种的划分都是以水泥中混合材品种变化和掺加量多少来规定的.这是由于混合材品种和掺加量的变化,会对水泥的性能产生影响.同一种混合材,掺量对水泥性能的影响是渐变的,相同种类的混合材对水泥性能的影响在品质内涵或影响程度上存在较大的差别,正因为可以掺入不同特性的混合材来调整硅酸盐水泥的性能,使得硅酸盐水泥具有更广泛的性能特点和更广泛的适用范围.为了合理使用具有不同性能特点的水泥,世界各国标准都把混合材引起性能变化范围基本相同的水泥划分为一个品种.我国现行标准的品种划分,基本上是建立在上世纪六十年代和七十年代的试验基础上.3.1 矿渣掺量与强度的关系掺加矿渣混合材料对于混合粉磨和分别粉磨的变化规律一致.对于3天,7天抗压强度,随掺量增加呈明显下降趋势,只是在掺量大于50%后,强度下降幅度略微缓和;而对于28天抗压强度,随掺量增加呈下降趋势,但掺量大于35%后强度下降幅度更为明显.矿渣掺量大于50%后性能变化加剧.>50且≤70b>20且≤50b矿渣≥30且<50≥50且20且≤40粉煤灰≥60且20且≤40火山灰质混合材料≥60且<80熟料+石膏P·P代号火山灰硅酸盐水泥水泥熟料质量的提高影响水泥性能的变化,而混合材品种与掺量的不同对水泥性能又有很大的影响,但水泥性能随混合材掺量的变化规律与上世纪60~70年代的试验研究结果基本一致.5 增加了M类混合石膏,取消了A类硬石膏(原版GB175-1999,GB1344-1999,GB12958-1999中第3章,本版第4.2.2.1条)4.2.2.1 天然石膏:应符合GB/T 5483中规定的G类或M类二级(含)以上的石膏或混合石膏.4.2.2.2 工业副产石膏:工业生产中以硫酸钙为主要成分的副产物.采用工业副产石膏时,应经过试验验证,证明对水泥性能无害.说明:现行标准中规定水泥可以使用符合相关标准要求的二水石膏和硬石膏.但在水泥实际生产中,为了改善硬石膏与外加剂的适应性,一般多和二水石膏混合用,形成实际上使用的混合石膏;同时以混合石膏形态存在的脱硫石膏也开始广泛用于水泥生产.因此本标准增加允许"混合石膏"种类用于水泥生产.同时,单独使用硬石膏会引起水泥与部分减水剂的不适应,造成急凝,瞬凝现象,因此本标准取消了水泥中允许使用硬石膏的规定.6 助磨剂允许掺量由"不超过水泥质量的1%"改为"不超过水泥质量的0.5%";7 普通水泥强度等级中取消了32.5和32.5R;说明:普通32.5水泥混合材掺量超标的客观原因是:水泥熟料质量的提高及粉磨技术的不断进步,为水泥中多掺混合材料创造了条件,因此水泥品种设置和强度等级不匹配的问题越来越突出,绝大部分水泥企业按标准规定加入混合材料实际是无法生产出32.5等级的普通硅酸盐水泥,如不突破混合材掺量就肯定是富裕强度很大,甚至超出二个等级,由于水泥附加值很低,这样一来水泥企业损失很大.同时生产水泥熟料需要消耗大量资源,能源,还排放大量有害气体.取消普通硅酸盐水泥32.5强度等级,将水泥品种划分为两个层次,如果用户需要高强度等级的水泥主要选择P.Ⅰ,P.Ⅱ,P.O;需要低强度等级水泥主要选择P.S,P.C,P.F,P.P等.8 将矿渣硅酸盐水泥,火山灰质硅酸盐水泥,粉煤灰硅酸盐水泥和复合硅酸盐水泥中"熟料中的氧化镁含量"改为"水泥中的氧化镁含量",其中要求P.S.A型,P.F型,P.P型,P.C型水泥中的氧化镁含量不大于6.0%,并加注b说明"如果水泥中氧化镁含量大于6.0%时,应进行水泥压蒸试验并合格".S.B型无要求.氧化镁含量超标造成的破坏XRD实验结果压蒸实验前后9 增加了氯离子限量的要求,即水泥中氯离子含量不大于0.06%说明:由于水泥混凝土中氯离子含量会引起钢筋锈蚀,从而导致混凝土开裂破坏.欧洲所有品种小于0.1%.对予应力应严格控制;日本:普通水泥小于0.035%,早强,超早强,中热,低热,抗硫酸盐等小于0.02%,其它品种没有规定.其他国家没有规定._钢筋的腐蚀――电化学反应过程钢筋混凝土结构中的钢筋腐蚀主要是电化学腐蚀,这是由于混凝土空隙中的水分通常以饱和的氢氧化钙的溶液形式存在,其中还含有一些氢氧化钠和氢氧化钙,pH值为12.5.在这样的强碱性的环境中,钢筋表面形成钝化膜,它是厚度为2×10-9- 6×10-9m 的水化氧化物(nFe203·mH2O),阻止钢筋进一步腐蚀.但是,当钢筋表面的钝化膜受到破坏,成为活化态时,钢筋就容易腐蚀.呈活化态的钢筋表面所发生的腐蚀反应的电化学机理是,当钢筋表面有水分存在时,就发生铁电离的阳极反应和溶液中氧还原的阴极反应,相互以等速度进行,其反应式如下:阳极反应2Fe-4e-→2Fe2+阴极反应O2+2H2O+4e-→4OH-腐蚀过程的全反应是阳极反应和阴极反应的组合,在钢筋表面析出氢氧化亚铁,其反应式为2Fe+02+2H20→2Fe2++4OH-→2Fe(0H)24Fe(OH)2+02+2H2O→4Fe(OH)3该化合物被溶解氧化后生成氢氧化铁Fe(OH)3,并进一步生成nFe2O3·mH2O (红锈),一部分氧化不完全的变成Fe304(黑锈),在钢筋表面形成锈层.红锈体积可大到原来体积的4倍,黑锈体积可大到原来的两倍.铁锈体积膨胀,对周围混凝土产生压力,将使混凝土沿钢筋方向开裂,进而使保护层成片脱落,而裂缝及保护层的剥落又进一步导致钢筋更剧烈的腐蚀.氯离子很容易引起钢筋锈蚀,有三种理论解释氯离子锈蚀的电化学作用.(1)氧化膜理论――钢筋在碱性介质中生成氧化膜,可以保护钢筋不受侵蚀,氯离子比其它离子(例如硫酸根离子)更容易通过膜的缺陷或孔隙穿透氧化膜.另一种意见认为氯离子能分散氧化膜使之更宜穿透,引起锈蚀.(2)吸附理论――氯离子吸附于钢筋表面,促进金属离子的水化,因而使金属更容易溶解.(3)过渡络合物理论――按照这个理论,氯离子生成氯化铁,氯化铁自阳极扩散从而破坏Fe(0H)2保护层,使腐蚀继续进行.氯化铁在电极不远处转化为氢氧化铁沉淀,氯离子自阳极传导更多的铁离子.现场的经验及研究表明,对于受氯离子污染的已建结构,0.026%的氯离子浓度足以破坏钝化膜而引起钢筋的破坏.其主要反应式如下,反应最终产物氢氧化铁Fe(0H)3即是铁锈.2Fe-4e-→2Fe2+Fe2+ +2C1-+4H20→FeC12·4H20FeC12·4H20→2Fe(OH)2↓+2C1-+2H++2H204Fe(OH)2+02+2H2O→4Fe(OH)3↓10 将各强度等级的普通硅酸盐水泥的强度指标改为和硅酸盐水泥一致,将各强度等级复合硅酸盐水泥的强度指标改为和矿渣硅酸盐水泥,火山灰质硅酸盐水泥,粉煤灰硅酸盐水泥一致;11 增加了45μm方孔筛筛余不大于30%作为选择性指标;6.3.4细度(选择性指标)硅酸盐水泥和普通硅酸盐水泥以比表面积表示,不小于300m2/kg;矿渣硅酸盐水泥,火山灰质硅酸盐水泥,粉煤灰硅酸盐水泥和复合硅酸盐水泥以筛余表示,80μm方孔筛筛余不大于10%或45μm方孔筛筛余不大于30%.说明:水泥磨得越细,水泥水化速度越快,强度越高.但与此对应的是水泥需水量增大,干缩增大,施工性能变差等负面影响.在熟料矿物组成,水泥组成固定的情况下,这些就只有通过水泥细度在一定范围内调整.细度的作用由产品质量保证向性能调控作用转变.增加了选择水泥组分试验方法的原则和定期校核要求.7.1 组分由生产者按GB/T12960或选择准确度更高的方法进行.在正常生产情况下,生产者应至少每月对水泥组分进行校核,年平均值应符合本标准第4.1条的规定,单次检验值应不超过本标准规定最大限量的2%.为保证组分测定结果的准确性,生产者应采用适当的生产程序和适宜的方法对所选方法的可靠性进行验证,并将经验证的方法形成文件.13 将"按0.50水灰比和胶砂流动度不小于180mm来确定用水量"的规定的适用水泥品种扩大为火山灰质硅酸盐水泥,粉煤灰硅酸盐水泥,复合硅酸盐水泥和掺火灰质混合材料的普通硅酸盐水泥.7.5 强度___ 按GB/T17671进行.但火山灰质硅酸盐水泥,粉煤灰硅酸盐水泥,复合硅酸盐水泥和掺火山灰质混合材料的普通硅酸盐水泥在进行胶砂强度检验时,其用水量按0.50水灰比和胶砂流动度不小于180mm来确定.当流动度小于180mm时,须以0.01的整倍数递增的方法将水灰比调整至胶砂流动度不小于180mm.胶砂流动度试验按GB/T2419进行,其中胶砂制备按GB/T17671进行.14 编号与取样中增加了年生产能力"200万吨以上"的级别.200万吨以上,不超过4000吨为一编号;_____ 120万吨~200万吨,不超过2400吨为一编号;说明:上述对于生产企业的约束,工程依然按照验收规程进行检验,即袋装200吨,散装500吨为一个批号.15 将"出厂水泥应保证出厂强度等级,其余技术要求应符合本标准有关要求"改为"经确认水泥各项技术指标及包装质量符合要求时方可出厂. "16 增加了出厂检验项目.出厂检验项目为6.1,6.3.1,6.3.2,6.3.3条.17 取消了废品判定.18 不合格判定中取消了细度和混合材料掺加量的规定,将判定规则改为"检验结果符合本标准6.1,6.3.1,6.3.2,6.3.3条技术要求为合格品.检验结果不符合本标准6.1,6.3.1,6.3.2,6.3.3条中任何一项技术要求为不合格品. "19 检验报告中增加了"合同约定的其他技术要求".20 交货与验收中增加了"水泥安定性仲裁检验时,从水泥取样之日起10天以内完成.如超过10天进行安定性检验不合格,则为不合格."21 包装标志中将"且应不少于标志质量的98% "改为"且应不少于标志质量的99% ".22 包装标志中将"火山灰质硅酸盐水泥,粉煤灰硅酸盐水泥和复合硅酸盐水泥的两侧印刷采用黑色."改为"火山灰质硅酸盐水泥,粉煤灰硅酸盐水泥和复合硅酸盐水泥的两侧印刷采用黑色或蓝色."本文来自: 中国质量热讯社区[url][/url]中国质量热讯-质量技术监督人士的网络家园!试说明生产硅酸盐水泥时为什么必须掺入适量石膏?水泥熟料中的铝酸三钙遇水后,水化反应的速度最快,会使水泥发生瞬凝或急凝。