“浮纤”原因和解决方法
增强塑料制品浮纤现象的产生原因

增强塑料制品浮纤现象的产生原因知道了浮纤产生的原因及过程,我们不难制定出解决浮去问题的方案1. 注射温度: 除热敏性塑料外,一般增强塑料的料筒温度均比非增强塑料的温度高出10~30℃,玻纤含量高的,温度应适当提高些,含量低的可略低些. 料筒温度的增加,有利与将低熔体粘度,提高充模性能,改善制品表面光洁度,提高纤维的分散性和减小取向性.料筒温度的提高,对制品的冲击性能影响不大,而对成型收缩率有所影响,趋于降低,同时物料的降解因素增加,色泽变深. 为了减少螺杆对纤维所产生的剪切作用,提高物料的塑化情况,要求料筒加料段温度略高些(比压缩段低),使物料在此阶段预热.2. 注射压力: 注射压力对纤维的充模有着重要影响.注射压力高有利于充模,纤维分散性好,制品收缩率下降,但剪切应力增加,取向性明显,易发生翘取变形,制品脱模困难,并可能导致溢边问题. 注射压力的选择与制品的璧厚,浇口尺寸等因素有关外,还与玻纤含量有关.一般纤维含量高,注射压力大,纤维长度长,注射压力也要求大些.3. 注射速度注射速度的提高有利于玻璃纤维增强塑料的快速充满模腔.在快速注射过程中,一部分纤维沿物料流动方向作快速轴向运动,这对于提高纤维的分散性,减少取向性,改善接缝强度显然是有利的,所得制品的表观光洁度较好,但如果注射速度过快,在喷嘴口和浇口处易发生"喷射"现象,造成制品局部表观的不光洁,在浇口附近有块状鲁思的缺陷,这在选择注射速度时应加以注意.4. 模具温度对玻纤增强塑料而言,采用较高的模具温度可缩小模具与熔体闲的温差,提高熔体的充模能力.防止制品中纤维淤积.鲁思,改善制品表观光洁度,增加熔接痕的熔接缝强度,同时对减少取向,防止制品的变形也有利.但随着模具温度的提高,不可避免的造成了成型周期长,生产率下降,和成型收缩率增加等问题. 模具温度除了与树脂品种,模具结构等有关外,还与纤维情况有关,通常纤维含量大,充模有困难的情况下.模具温度应适当提高些.5.螺杆转速与背压在玻璃纤维的增强塑料的塑化过程中,要求螺杆转速不易过高,以免减切作用过大而给玻璃纤维带来伤害,特别是长纤维,易出现长短不均现象,进而使制品不稳定或同一制品各点强度不一. 为使纤维能均匀的分散于熔体中,提高物料的流动性,以得到外观理想,机械物理性能均匀的制品,可用提高螺杆背压的方法,但背压的提高对长纤的剪切作用较大,物料易过热变色降解.这是背压选择时应注意的问题,通常比非增强塑料略高些就行了.纖維種類有許多,如玻璃纖維,碳纖,硼纖,金属纖維等,目的用以補強塑膠的強度,但纖維與塑膠畢竟不是相同材質,他們的流动性存在著差異,對塑膠熔體的融合性便有所差異,所以两相介面間存在著相容性問題.1.質量密度的差異会造成流动充填時,有某種分離的趋势,会造成浮纖现象.2.射出時的磨擦剪力会造成局部黏度的差異,黏度小的地方抓不住纖維時,纖維便会向製品表面逐漸累積,造成浮纖现象.3.成品表面絕大部份是由于噴泉效应所形成,纖維由内部向表面流去,模具面較冷,瞬間冻結流动层,纖維便凝固在表层,若與塑料的結合性不高時,便会有明顯的浮纖现象.玻璃纤维增强制品浮纤现象比较常见,会严重影响制品外观及喷涂作业。
浮纤产生原机理

浮纤产生原机理浮力纤维(Floating Fiber)是一种介于沉陷纤维和浮行纤维之间的新材料。
相对于沉陷纤维需要通过加重物才能使其沉降到目标层,而浮行纤维又需要自然浮升到表层,浮力纤维则可以在水域内保持在理想的层次上。
浮力纤维主要应用于海洋工程、环境保护和水上交通工具等领域。
那么,浮力纤维是如何产生的呢?首先,浮力纤维的产生需要依赖于材料的密度分布。
浮力纤维是由特殊的聚合物制成,这种聚合物的密度分布是非常关键的。
一般来说,浮力纤维的密度分布要求在纤维的一端相对较高,而另一端相对较低。
这样一来,纤维的重心会偏向较低密度的一端,从而使得整个纤维产生了一个向上的浮力。
其次,浮力纤维的密度分布需要精确控制。
为了达到理想的浮力效果,制造浮力纤维的厂家需要在材料的制作过程中进行密度分布的调整。
一种常用的方法是在聚合物中添加密度调节剂,通过控制这些密度调节剂的含量和分布来实现纤维的浮力调整。
密度调节剂可以通过控制纤维表面的吸附量来调节浮力纤维的密度分布,从而实现纤维的浮力调整。
此外,浮力纤维的形状也对其产生浮力起到一定的影响。
通常情况下,浮力纤维采用的是空心或多孔的结构。
这种结构可以减少纤维的质量,并增大纤维与水的接触面积,从而增加了纤维所受到的浮力。
此外,纤维的形状也可以通过对纤维表面进行改变来实现浮力的调整。
例如,可以通过加工纤维表面的形状,使其在水中受到的浮力增大或减小,从而实现纤维的浮力调整。
最后,浮力纤维的浮力还受到水的密度和温度的影响。
根据阿基米德原理,浮力纤维在水中的浮力与水的密度和纤维的体积有关。
因此,水的密度和温度变化都会影响浮力纤维的浮力。
一般来说,当水的密度较大或温度较低时,浮力纤维所受到的浮力也会增大;反之,当水的密度较小或温度较高时,浮力纤维所受到的浮力会减小。
综上所述,浮力纤维产生的原机理主要包括聚合物的密度分布、密度调节剂的使用、纤维的形状以及水的密度和温度等因素的影响。
通过合理控制和调整这些因素,可以实现对浮力纤维的浮力进行精确调整。
塑胶产品表面浮纤处理方法

塑胶产品表面浮纤处理方法塑胶产品在生产过程中,由于各种原因,表面可能会出现浮纤现象,这不仅影响了产品的美观度,还会影响产品的质量和使用寿命。
因此,对于塑胶产品表面浮纤的处理方法,需要进行一定的了解和掌握。
我们需要了解浮纤的成因。
浮纤是由于塑胶材料在注塑过程中,由于温度、压力等因素的影响,导致塑胶材料表面出现纤维状物质。
这些纤维状物质会附着在产品表面,影响产品的美观度和质量。
针对浮纤现象,我们可以采取以下几种处理方法:1. 机械处理法机械处理法是指通过机械设备对塑胶产品表面进行处理,去除浮纤。
这种方法适用于浮纤较少的情况,可以采用打磨、抛光等方式进行处理。
但是,对于浮纤较多的情况,机械处理法效果不佳。
2. 化学处理法化学处理法是指通过化学药品对塑胶产品表面进行处理,去除浮纤。
这种方法适用于浮纤较多的情况,可以采用溶解、腐蚀等方式进行处理。
但是,化学处理法需要注意药品的选择和使用方法,以免对产品造成损害。
3. 热处理法热处理法是指通过加热对塑胶产品表面进行处理,去除浮纤。
这种方法适用于浮纤较少的情况,可以采用热风枪、火焰等方式进行处理。
但是,热处理法需要注意温度的控制和操作的安全性。
4. 光学处理法光学处理法是指通过光学设备对塑胶产品表面进行处理,去除浮纤。
这种方法适用于浮纤较少的情况,可以采用激光、光纤等方式进行处理。
但是,光学处理法需要注意设备的选择和操作的安全性。
针对塑胶产品表面浮纤的处理方法,我们可以根据具体情况选择不同的处理方法。
在生产过程中,我们需要注意控制温度、压力等因素,以减少浮纤的产生。
同时,对于浮纤现象的处理,需要注意安全性和产品质量,以确保产品的美观度和使用寿命。
23节浮纤Glass fiber streaks

在模具表面凝结过快,由于流动方向遭到配向影响, 及流动速度与冷却速度的变化,及致玻璃纤维排列 不良,一些竖立,一些斜立,再也不会嵌入到熔体 内,出现玻璃纤维浮出表面的现象。 2.浮纤原因分析:
因料温太低、或模温太低、或困气等因素,两 股料流前锋相遇时,会在交叉的地方导致表面材质 不规则,结果就会形成熔接线与亮面线,影响产品 外观与产品的工程结构。
注塑成型不良 原因分析与改善对策
第二十三节 浮纤Glass fiber streaks
一、浮纤不良品图片(喷射浮纤):
1
一、浮纤不良品图片(伴有熔接线、困气): 2
Hale Waihona Puke 浇口熔接线区域 浮纤明显
一、浮纤不良品图片(晒纹面浮纤):
3
良品
不良品 (填充 末端)
困气处浮纤 明显
二、浮纤不良描述(浮纤产品往往表面泛白) : 4
⑹ 产品壁厚差异大,过渡明显,收缩造成玻纤 刺出树脂界面。
⑺ 产品筋位设计紊乱熔体流向,造成玻纤取向
三、浮纤不良对策:
6
被打乱,形成浮纤,尤其垂直流动方向的筋位设计。 2.工艺条件对策:
⑴ 增加保压及保压时间; ⑵ 减少计量行程,垫量在5-10㎜;
⑶ 提高射出速度;注意困气。 ⑷ 升高料温,检查喷嘴温度是否足够; ⑸ 升高模温;
⑶ 考虑玻璃纤维和基体的相溶性,对玻纤进行 表面处理,如加入一些偶联剂和接枝物;
⑷ 加入润滑剂,润滑剂主要考虑到玻纤的分散 问题,及一些润滑剂本身具有外润滑作用,在成型 时容易跑到产品表面来形成光滑的一层。
三、浮纤不良对策:
8
⑸ 适当加入一定量的水口料,可以减弱浮纤的
“浮纤”原因和解决方法

“浮纤”现象是玻纤外露造成的;白色的玻纤在塑料熔体充模流动过程中浮露于外表;待冷凝成型后便在塑件表面形成放射状的白色痕迹;当塑件为黑色时会因色泽的差异加大而更加明显..其形成的原因主要有以下几个方面..首先;在塑料熔体流动过程中;由于玻纤与树脂的流动性有差异;而且质量密度也不同;使两者具有分离的趋势;密度小的玻纤浮向表面;密度大的树脂沉入内里;于是形成了玻纤外露现象;其次;由于塑料熔体在流动过程中受到螺杆、喷嘴、流道及浇口的摩擦剪切力作用;会造成局部粘度的差异;同时又会破坏玻纤表面的界面层;熔体粘度愈小;界面层受损愈严重;玻纤与树脂之间的粘结力也愈小;当粘结力小到一定程度时;玻纤便会摆脱树脂基体的束缚;逐渐向表面累积而外露;再则;塑料熔体注入型腔时;会形成“喷泉”效应;即玻纤会由内部向外表流动;与型腔表面接触;由于模具型面温度较低;质量轻冷凝快的玻璃纤维被瞬间冻结;若不能及时被熔体充分包围;就会外露而形成“浮纤”.主要问题要解决相容和材料间的结合改善“浮纤”现象的措施方法是在成型材料中加入相容剂、分散剂和润滑剂等添加剂;包括硅烷偶联剂、马来酸酐接枝相容剂;南京塑泰相容剂、硅酮粉、脂肪酸类润滑剂及一些国产或进口的防玻纤外露剂等;通过这些添加剂来改进玻纤和树脂之间的界面相容性;提高分散相和连续相的均匀性;增加界面粘接强度;减少玻纤与树脂的分离;从而改善玻纤外露现象;液体硅烷偶联剂;就存在加入后难以分散;塑料容易结块成团的问题;会造成设备喂料不均匀;玻纤含量分布不均匀;进而导致制品的力学性能不均匀浇注系统设计的基本原则是流道截面宜大;流程宜平直而短..应采用粗短的主流道、分流道和粗大浇口;浇口可以是薄片式、扇形及环形;亦可采用多浇口形式;以使料流混乱、玻纤扩散、减少取向性..而且要求有良好的排气功能;能及时排出因玻纤表面处理剂挥发产生的气体;以免造成熔接不良、缺料及烧伤等缺陷.另外需要注意的是;“浮纤”易于在塑件壁厚较大的部位出现;这是因为熔体在该处流动速度梯度较大;熔体流动时其中心速度高;而靠近型腔壁面处速度低;使得玻纤浮露的趋势加剧;相对速度更慢;发生滞留堆积而形成“浮纤”..因此;应尽量使塑件各处壁厚均匀;并避免尖角、缺口;保证熔体流动顺畅;由于玻纤增强塑料的熔融指数比非增强塑料低30%~70%;流动性较差;因此料筒温度较一般情况应高出10~30℃..提高料筒温度;可使熔体粘度降低;改善流动性;避免填充及熔接不良;而且有利于加大玻纤分散性和减小取向性;获得较低的制品表面粗糙度..但料筒温度并不是越高越好;温度过高会加大尼龙聚合物氧化和降解的趋势;轻微时会发生颜色变化;严重时则产生焦化发黑..在设置料筒温度时;应使加料段温度比常规要求略高些;稍低于压缩段即可;以利用其预热效果;降低螺杆对玻纤所产生的剪切作用;减少局部粘度的差异及对玻纤表面的破坏;保证玻纤与树脂之间的粘结强度模具与熔体之间的温差不宜太大;防止熔体充填时玻纤遇冷在表面淤积;形成“浮纤”;因此需采用较高的模具温度;这对于提高熔体充模性能、增加熔接痕强度、改善制品表面光洁度、减少取向和变形也是有利的..但模具温度愈高;冷却时间愈久;成型周期延长;生产率降低;而且成型收缩率加大;故也不是越高越好.采用高料温、高模温、高压、高速、低螺杆转速注射;对改善“浮纤”现象比较有利。
“浮纤”原因和解决方法

“浮纤”原因和解决方法浮纤,又称为浮球纤维,指纺织品中出现的细丝状或球状杂质。
浮纤主要由于纤维束破裂或纤维弯折而产生,它不仅会影响纺织品的质量和外观,还可能在织物工艺中堵塞喷水孔、堵塞毛细管或堵塞喷嘴等,严重会导致设备故障和停工,给纺织生产带来一系列问题。
浮纤主要有以下几个原因:1.纤维工艺设备问题:纤维工艺设备存在异物残留、杂质堵塞等问题,导致纤维束在过程中受到不必要的损坏和污染。
2.纺纱工艺问题:纤维预处理、纺纱工艺参数不当,尤其是纺纱机速度过快、张力不均匀等因素,容易导致纤维的弯曲和打结,从而产生浮纤。
3.纤维品质问题:原料纤维的质量不良、长度不均、含杂率过高等问题,会增加纤维断裂和弯曲的可能性,从而产生浮纤。
对于浮纤问题的解决方法,可以从以下几个方面进行改进和优化:1.加强设备维护和清洁:定期检查和维护设备,清理设备中的异物和杂质,保障设备正常运行,减少纤维在生产过程中的损伤和污染。
2.优化纺纱工艺参数:合理设置纺纱工艺参数,控制纺纱机的速度和张力,保持纤维的均匀拉伸,减少纤维的弯曲和打结,降低浮纤的发生率。
3.提高纤维品质:加强对纤维原料的采购和品质控制,选择优质的纤维原料,减少纤维条带中的杂质和断裂纤维,从源头上控制浮纤的发生。
4.加强质量控制和检测:建立完善的质量检测体系,对纺织品进行严格的检测和筛选,及时发现并处理浮纤问题,确保产品的合格出厂。
5.培训和教育:加强员工培训和教育,提高他们的纤维品质意识和质量控制能力,使他们能够主动发现和解决浮纤问题。
总之,浮纤问题的解决需要从设备维护、纺纱工艺优化、纤维品质改进以及质量控制等多个方面进行综合治理。
只有通过完善和改进纺织生产工艺,提高纤维品质,加强质量控制和员工培训等措施,才能有效地减少浮纤的发生,提高纺织品的质量和合格率,促进纺织工业的健康发展。
玻纤知识与浮纤解决方法探讨

玻纤知识与浮纤解决方法探讨第一部分:玻纤知识:1、玻纤分类根据长度分类,可分为连续玻璃纤维、短玻璃纤维(定长玻璃纤维)和长玻璃纤维(let)。
连续玻璃纤维是我国使用最广泛的玻璃纤维,俗称长纤维。
具有代表性的制造商包括巨石、泰山、兴旺等。
固定长度的玻璃纤维通常被称为“短纤维”。
国外改性厂和国内一些企业普遍采用。
代表性制造商包括PPG、OCF和国内CPIC。
巨石泰山也有一些零件,但质量不令人满意。
Let最近在中国兴起。
代表性制造商包括PPG、CPIC和巨石。
目前,国内金发女郎和苏州合昌产量较大。
捷士杰、温州君儿、南京巨龙正在开发中,也有小批量生产从碱金属含量分可分为无碱,低中高,通常改性增强用无碱,也就是e玻纤,国内改性一般使用e玻纤。
2、玻纤的应用:玻璃纤维增强塑料的原理主要是因为玻璃纤维/树脂界面上的连接必须将作用在模塑件上的力传递给玻璃纤维。
因此,玻璃纤维的长度完全用于树脂加固,但树脂基体中玻璃纤维的长度必须满足一定的要求,即玻璃纤维的临界长度,玻璃纤维的临界长度(即从基材向纤维传递力的最小长度)在0.3~0.6mm之间。
临界长度仅与剪切力和玻璃纤维单丝直径有关。
上述临界长度是指最终产品中玻璃纤维的长度。
对于塑料颗粒,该长度在0.6~0.8mm之间。
从理论上讲,临界长度与玻璃纤维的原始长度无关,如果将玻璃纤维的长度控制在该范围内,则产品的机械性能和表面外观最佳且最平衡。
如果长度过长,机械性能会增加,但产品表面会变得粗糙和翘曲。
如果长度太短,机械性能将不足。
为了控制玻璃纤维的长度,我们应该从调整螺旋结构和速度开始。
如果玻璃纤维的长度和直径控制在400,效果最好。
3.评价玻璃纤维质量的主要指标:第一个指标:玻璃纤维拉伸过程中使用的表面活性剂。
表面活性剂处理剂通常被称为润湿剂。
润湿剂主要是偶联剂和成膜剂,以及一些润滑剂、抗氧化剂、乳化剂、抗静电剂等。
成膜剂的组成和其他添加剂的种类对玻璃纤维有决定性的影响。
玻纤外露的原因和解决方法分析

玻纤外露的原因和解决方法分析一直以来,为了提高产品的强度和耐温性等性能,使用玻纤来对塑料进行增强改性成了一个非常不错的选择。
大量事实也证明了玻纤所带来的良好性能。
但是,玻纤与塑料本身就是两种不同的材料,自然也就产生了二者的相容性问题。
玻纤外露(或叫浮纤)就是二者相容性问题的直接体现。
而玻纤外露也是加纤材料注塑加工过程中经常碰到且困扰诸多朋友们的一个问题。
那么玻纤外露究竟是怎么产生的呢?可能一些朋友没有见过直接的玻纤,简而言之,从玻纤的形态上来说玻纤有长纤和短纤之分,是一束一束的,是白色的(具体的这里就不多讲了)。
加纤料就是将玻纤和树脂共混造粒而成的。
在射胶的时候,料的流动是类似于液体的流动方式。
大家应该看过河流里面,在河流里有一些树枝等杂物时,经常会在沿岸边有一些这类依附河岸而停留。
如果在注塑中,就是玻纤外露。
这是因为玻纤相对于塑料的流动性要差很多,而塑料在模具中的流动是从夹层中间往前流,俩边往外翻动的方式流动的,所以流动性最好的肯定是跑到最前面,而流动性不好的就会停留在模具表面(注:这段话是借用别的朋友的话,在此表示感谢)。
同时,玻纤有促进结晶的作用,而PP、PA都属于结晶性材料。
结晶快冷却就快;冷却快,玻纤就难以被树脂束缚和掩盖住,那么就容易产生玻纤外露。
原因弄清了,那么咱们就该去解决了,对吧?目前通常的解决办法主要有以下几种:一、材料方面:1、考虑玻璃纤维和基体的相容性,对玻纤进行表面处理,如加入一些偶联剂和接枝物;2、加入润滑剂,润滑剂主要是考虑到玻纤的分散问题以及一些润滑剂本身具有外润滑作用,在成型时候容易跑到制品表面来形成光滑的一层。
3、还有其他一些填充剂也有改善的效果,这里就不再一一列举。
二、注塑加工方面:1、提高料温和模温;2、高压高速;3、采用快速冷热成型技术(RHCM)。
因为如果熔融塑料在接触模壁时固化太快,玻璃纤维就无法被完全包覆,即产生表面浮纤现象。
而对于RHCM成型,由于高模温使得型腔界面处玻璃纤维完全可以被塑料熔体包覆,且由于该部位处于熔融状态,使得玻璃纤维的定向趋于一致,保证了收缩均匀性,进而保证了成型品质。
塑胶产品表面浮纤处理方法

塑胶产品表面浮纤处理方法
塑胶制品在生产加工过程中,往往会出现表面浮纤的现象,这会直接影响制品的外观和品质。
为了解决这个问题,我们可以采用以下几种处理方法:
1. 使用表面处理剂:在制品表面涂布一层表面处理剂,可以有效地减少浮缎的产生。
常用的表面处理剂有硅烷偶联剂、磷酸酯等。
2. 采用防浮缩微珠:将一定数量的防浮缩微珠加入塑料中,可以改变塑料的密度,从而减少浮缎的产生。
3. 调整生产工艺:在生产过程中,加强温度控制和冷却速度,可以有效地减少浮缎的产生。
4. 自然浸润:将制品浸入水中,可以通过自然浸润的方式将浮缎排除,同时可以增强制品表面的光泽度。
以上是几种常见的塑胶产品表面浮缎处理方法,具体应根据不同情况选择合适的处理方式。
- 1 -。
如何改善浮纤
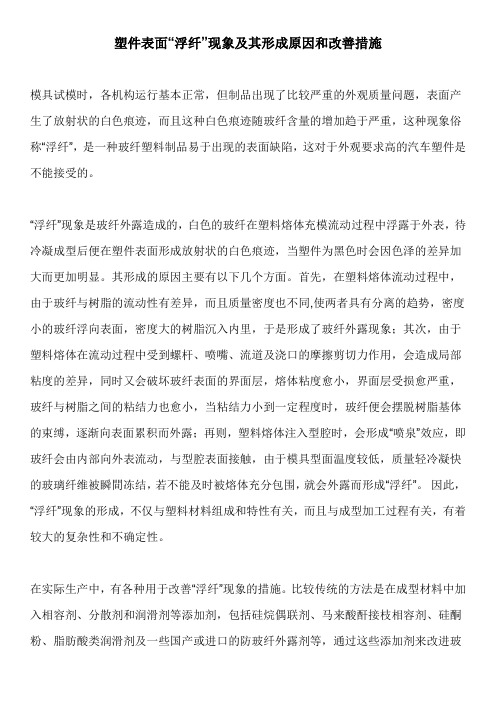
塑件表面“浮纤”现象及其形成原因和改善措施模具试模时,各机构运行基本正常,但制品出现了比较严重的外观质量问题,表面产生了放射状的白色痕迹,而且这种白色痕迹随玻纤含量的增加趋于严重,这种现象俗称“浮纤”,是一种玻纤塑料制品易于出现的表面缺陷,这对于外观要求高的汽车塑件是不能接受的。
“浮纤”现象是玻纤外露造成的,白色的玻纤在塑料熔体充模流动过程中浮露于外表,待冷凝成型后便在塑件表面形成放射状的白色痕迹,当塑件为黑色时会因色泽的差异加大而更加明显。
其形成的原因主要有以下几个方面。
首先,在塑料熔体流动过程中,由于玻纤与树脂的流动性有差异,而且质量密度也不同,使两者具有分离的趋势,密度小的玻纤浮向表面,密度大的树脂沉入内里,于是形成了玻纤外露现象;其次,由于塑料熔体在流动过程中受到螺杆、喷嘴、流道及浇口的摩擦剪切力作用,会造成局部粘度的差异,同时又会破坏玻纤表面的界面层,熔体粘度愈小,界面层受损愈严重,玻纤与树脂之间的粘结力也愈小,当粘结力小到一定程度时,玻纤便会摆脱树脂基体的束缚,逐渐向表面累积而外露;再则,塑料熔体注入型腔时,会形成“喷泉”效应,即玻纤会由内部向外表流动,与型腔表面接触,由于模具型面温度较低,质量轻冷凝快的玻璃纤维被瞬間冻结,若不能及时被熔体充分包围,就会外露而形成“浮纤”。
因此,“浮纤”现象的形成,不仅与塑料材料组成和特性有关,而且与成型加工过程有关,有着较大的复杂性和不确定性。
在实际生产中,有各种用于改善“浮纤”现象的措施。
比较传统的方法是在成型材料中加入相容剂、分散剂和润滑剂等添加剂,包括硅烷偶联剂、马来酸酐接枝相容剂、硅酮粉、脂肪酸类润滑剂及一些国产或进口的防玻纤外露剂等,通过这些添加剂来改进玻纤和树脂之间的界面相容性,提高分散相和连续相的均匀性,增加界面粘接强度,减少玻纤与树脂的分离,从而改善玻纤外露现象,其中有的使用效果较好,但是大多价钱不菲,增加了生产成本,而且对材料的力学性能也会有影响,例如较常用的液体硅烷偶联剂,就存在加入后难以分散,塑料容易结块成团的问题,会造成设备喂料不均匀,玻纤含量分布不均匀,进而导致制品的力学性能不均匀。
注塑产品浮纤的名词解释

注塑产品浮纤的名词解释注塑技术是一种常用于制造塑料产品的方法,通过将熔化的塑料注入模具中,使塑料在模具中冷却凝固,最终形成所需的产品。
在注塑过程中,浮纤是一个重要的名词,它是常常被提及的。
那么,什么是浮纤,它在注塑产品中扮演着怎样的角色呢?首先,我们来解释一下浮纤的意思。
浮纤全称为浮纤实物,它是指注塑过程中产生的实际物质,通常是指形成在塑料产品表面的细小纤维状物质。
这些纤维可能由于原料的选择、模具的设计和加工条件等原因而产生。
浮纤通常是塑料注塑产品中出现的常见缺陷,因此在注塑生产中需要采取措施来控制和减少浮纤的生成。
接下来,我们来谈一谈浮纤在注塑产品中的影响。
由于浮纤通常是与塑料产品表面粘附的纤维状物质,它会对产品的外观质量产生一定的影响。
当产品表面出现浮纤时,会使得产品的表面不光滑,甚至可能出现粗糙或不均匀的情况。
这会影响产品的美观度,并可能降低产品的附加值。
除了外观质量的影响,浮纤还可能对产品的性能产生一定的影响。
在一些特定的应用领域中,产品的表面质量是非常重要的,如汽车内饰件、电子产品外壳等。
这些产品的外观质量直接影响着用户的体验感和消费欲望。
因此,控制浮纤的生成对于满足用户需求和提高产品竞争力是非常关键的。
那么,如何控制和减少浮纤的生成呢?首先,我们需要从原料的选择和处理入手。
选择粒径较小、分散性好的原料,并进行充分的预干燥和混合,可以有效降低浮纤的生成。
其次,模具的设计和加工条件也是影响浮纤生成的重要因素。
合理设计模具结构,避免出现过小的孔隙和死角,同时控制注塑速度和温度等加工参数,有助于减少浮纤的产生。
此外,采用一些辅助措施也可以帮助控制和减少浮纤的生成。
例如,在注塑过程中添加一些防浮纤剂,能够改善塑料的流动性和熔体的黏性,从而减少浮纤的形成。
另外,注塑设备的维护保养也是非常重要的,定期清洗和检查设备,保证设备的正常运行,有助于降低浮纤的产生。
总之,浮纤是注塑产品中常见的缺陷之一,它对产品的外观质量和性能都会产生一定的影响。
玻纤知识与浮纤解决方法探讨

玻纤知识与浮纤解决方法探讨第一部分:玻纤知识:1、玻纤分类从长度分类分可以分连续玻纤、短玻纤(定长玻纤)和长玻纤(LET),连续玻纤是国内目前应用最广的玻纤,就是通常说的“长纤”,代表厂家有巨石,泰山、兴旺等。
定长玻纤就是通常说的“短纤”,一般是外资改性厂与国内部分企业在用,代表厂家有PPG,OCF及国内的CPIC,巨石泰山也有少部分,但质量不如人意。
LET是最近在国内兴起的,代表厂家有PPG,CPIC及巨石,目前国内金发和苏州和昌产量较大,杰事杰及温州俊尔,南京聚隆在开发当中,也有小批量生产从碱金属含量分可分为无碱,低中高,通常改性增强用无碱,也就是E玻纤,国内改性一般使用E玻纤。
2、玻纤的应用:玻纤增强塑料的原理主要是由于玻纤/树脂界面上连接必然是使作用到模塑件上的力传导到玻纤上,因此玻纤的长度被充分利用,起到树脂增强的目的,但玻纤在树脂基体中长度必须满足一定的要求,这就是临界玻纤长度,玻璃纤维的临界纤维长度(即可将力从基材传递给纤维的最小长度)在0.3~0.6mm之间,临界长度只与剪切力与玻纤单丝直径有关,上面的临界长度是指玻纤在最终产品里的长度,如是果是塑料粒子里话,此长就就在0.6~0.8mm 之间,从理论上讲,临界长度与玻纤的原始长度没有关系,如果增强产品把玻纤的长度都控制在这个范围的话,此时产品的力学性能与表面外观都是最好的,最平衡的,如果长度过长,力学性能上升,但制品表面会变粗糙与翘曲,如果长度过短,就会导致力学性能不足。
要控制玻纤的长度应该从调整螺杆结构及转速入手,如果玻纤长径控制在400效果最佳。
3、评价玻纤好坏的主要指标:第一个指标:玻纤在拉丝过程中所使用的表面活性处理剂。
表面活性处理剂也就是通常所说的浸润剂,浸润剂主要是偶联剂与成膜剂,另外还有一些润滑剂、抗氧剂、乳化剂、抗静电剂等,成膜剂的成分与其它助剂的种类对玻纤有决定性的影响,所以在选择玻纤时就根据基料与成品要求选择合适的玻纤。
浮纤原因和解决方法
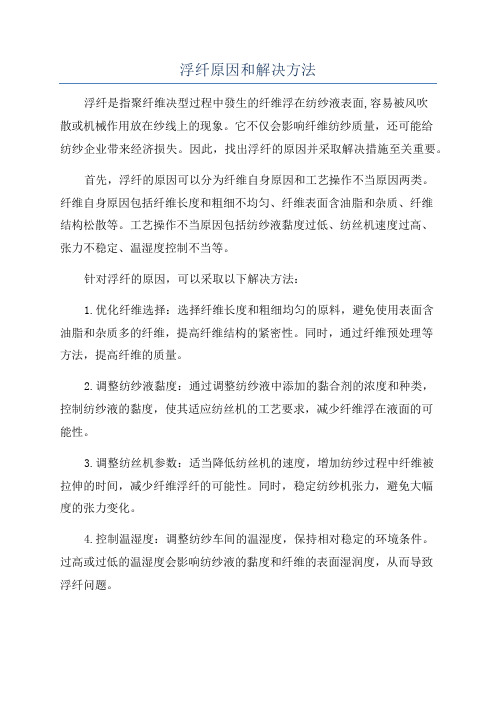
浮纤原因和解决方法浮纤是指聚纤维决型过程中發生的纤维浮在纺纱液表面,容易被风吹散或机械作用放在纱线上的现象。
它不仅会影响纤维纺纱质量,还可能给纺纱企业带来经济损失。
因此,找出浮纤的原因并采取解决措施至关重要。
首先,浮纤的原因可以分为纤维自身原因和工艺操作不当原因两类。
纤维自身原因包括纤维长度和粗细不均匀、纤维表面含油脂和杂质、纤维结构松散等。
工艺操作不当原因包括纺纱液黏度过低、纺丝机速度过高、张力不稳定、温湿度控制不当等。
针对浮纤的原因,可以采取以下解决方法:1.优化纤维选择:选择纤维长度和粗细均匀的原料,避免使用表面含油脂和杂质多的纤维,提高纤维结构的紧密性。
同时,通过纤维预处理等方法,提高纤维的质量。
2.调整纺纱液黏度:通过调整纺纱液中添加的黏合剂的浓度和种类,控制纺纱液的黏度,使其适应纺丝机的工艺要求,减少纤维浮在液面的可能性。
3.调整纺丝机参数:适当降低纺丝机的速度,增加纺纱过程中纤维被拉伸的时间,减少纤维浮纤的可能性。
同时,稳定纺纱机张力,避免大幅度的张力变化。
4.控制温湿度:调整纺纱车间的温湿度,保持相对稳定的环境条件。
过高或过低的温湿度会影响纺纱液的黏度和纤维的表面湿润度,从而导致浮纤问题。
5.设备维护保养:定期对纺纱设备进行检修和保养,保证设备的正常运转。
同时,加强员工的培训和管理,提高操作技能,减少操作不当造成的浮纤问题。
通过以上综合解决方法,可以有效地解决纺纱过程中出现的浮纤问题。
但需要注意的是,不同纺纱工艺和设备的特点不同,可能需要根据具体情况制定具体的解决方案。
因此,纺纱企业应密切关注浮纤问题,进行系统的实验和改进,以提升纤维纺纱质量和降低生产成本。
注塑成型之产品常见不良
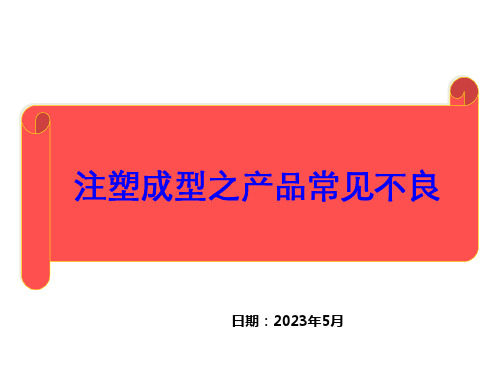
产品不良说明: 熔接线处困气图示说明,黑色产品困气“烧白” 。
注塑成型产品不良图片
12
13. 烧黑(深肋骨处困气)
14. 表面烧焦(尖拐角处困气)
上壳拐角困气/ 烧焦
底壳亮面
产品不良说明: 深肋骨处困气图示,说明,白色产
品困气“烧黑” 。追下排气镶件或 “扁顶”
产品不良说明: 晒纹面光泽不一,底壳在保压未
浇口
产品不良说明:
◎浇口过小,材料剪切大,降解; ◎注射速度过快; ◎料温过高或滞留时间过长; ◎浇口堵塞,出现熔体破裂。 ◎热流道与螺杆料筒内有杂料; ◎颜料耐热性差等。
表层剥离改善的顺序:
检查塑料种类与级别→检查胶料是否污染 →升高模具温度→升高成型温度→物料是 否干燥充分→降低注射速度→缩短浇口长 度→减小注射压力→改变浇口位置→采用 大孔浇口→加大机台喷嘴直径。
注塑成型产品不良图片
32
37. 太阳斑、消光斑、 应力痕、 喷射气痕、雾斑等:
点浇口
点浇口
产品不良说明: 在浇口周边出现的圆环,显现成暗淡的日冕痕(消光斑点)或斑痕。
主要原因是: 浇口偏细,注射速度过高。
注塑成型产品不良图片
38. 浇口晕、雾斑等:
33
潜顶针 浇口背面
点浇口
产品不良说明:
产品浇口处出现斑纹和混浊,通常由于熔 体注入模腔时,造成“熔体破裂”所致。 对策:浇口尺寸,流道优化;浇口处太薄, 对面加圆弧胶位;调整注射速度;提高模 温与料温等。
注塑成型产品不良图片
21
23.浮纤(喷射浮纤)
23.浮纤(困气处浮纤)
浇口
产品不良说明: 若料温或模温太低,含纤塑料凝结过快,出现玻璃纤维浮出表面的现象。
玻纤尼龙出现“浮纤”问题的解决方案
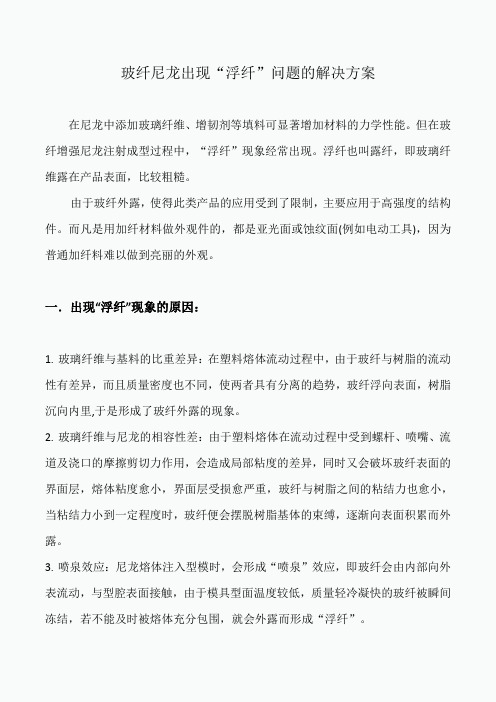
玻纤尼龙出现“浮纤”问题的解决方案在尼龙中添加玻璃纤维、增韧剂等填料可显著增加材料的力学性能。
但在玻纤增强尼龙注射成型过程中,“浮纤”现象经常出现。
浮纤也叫露纤,即玻璃纤维露在产品表面,比较粗糙。
由于玻纤外露,使得此类产品的应用受到了限制,主要应用于高强度的结构件。
而凡是用加纤材料做外观件的,都是亚光面或蚀纹面(例如电动工具),因为普通加纤料难以做到亮丽的外观。
一.出现“浮纤”现象的原因:1.玻璃纤维与基料的比重差异:在塑料熔体流动过程中,由于玻纤与树脂的流动性有差异,而且质量密度也不同,使两者具有分离的趋势,玻纤浮向表面,树脂沉向内里,于是形成了玻纤外露的现象。
2.玻璃纤维与尼龙的相容性差:由于塑料熔体在流动过程中受到螺杆、喷嘴、流道及浇口的摩擦剪切力作用,会造成局部粘度的差异,同时又会破坏玻纤表面的界面层,熔体粘度愈小,界面层受损愈严重,玻纤与树脂之间的粘结力也愈小,当粘结力小到一定程度时,玻纤便会摆脱树脂基体的束缚,逐渐向表面积累而外露。
3.喷泉效应:尼龙熔体注入型模时,会形成“喷泉”效应,即玻纤会由内部向外表流动,与型腔表面接触,由于模具型面温度较低,质量轻冷凝快的玻纤被瞬间冻结,若不能及时被熔体充分包围,就会外露而形成“浮纤”。
因此,综上所述,“浮纤”现象的形成,不仅与塑料材料组成和特性有关,而且与成型加工过程有关,有着较大的复杂性和不确定性。
二.出现“浮纤”的解决方案1.模具方面:将产品外观面刻意做成亚光面或蚀纹面,减少玻纤外露的视觉反应。
2.改善玻纤与尼龙的相容性:在成型材料中加入相容剂、分散剂和润滑剂等添加剂,包括硅烷偶联剂、马来酸酐接枝相容剂、脂肪酸类润滑剂及一些国产或进口的防玻纤外露剂等,通过这些添加剂来改进玻纤与树脂间的相容性,提高分散的均匀性,增加界面粘结强度,减少玻纤与树脂的分离,从而改善玻纤外露现象。
如研究表明,在基体中添加相容剂,改性后材料玻纤在基体中相容性较未添加材料明显提高。
玻纤增强尼龙(PA)出现“浮纤”影响油漆喷涂怎么办?

玻纤增强尼龙(PA)出现“浮纤”影响油漆喷涂怎么办?在尼龙中添加玻璃纤维、增韧剂等共混材料的力学性能.结果表明随玻纤含量的增加,材料的拉伸强度、弯曲强度有大幅度的提高,冲击强度则较为复杂,增韧剂加入,材料的韧性大幅度的提高.添加30%~35%的玻纤,8%~12%的增韧剂,材料的综合力学性能最佳。
PA66增强尼龙系列:具有优良的耐磨性、耐热性及电性能,机械强度高,能自熄,尺寸稳定性良好,广泛应用于汽车工业产品、纺织产品、泵叶轮和一级精密工程部件。
PA6增强尼龙系列:具有良好的耐磨性、耐热性、耐油性及耐化学药品性,还大大降低了原材料的吸水率和收缩率,具有优良的尺寸稳定性及优异的机械强度。
由此增强尼龙用于各大行业,就PA6+GF的应用来看:PA6+GF15%---用于生产汽车散热隔栏、轮饰盖、冷却液壶、蓄电器外壳等;PA6+GF25%---用于生产汽车风扇支架、轮饰盖、油箱盖、门拉手、高位刹车灯等;PA6+GF30%---用于生产汽车组合开关、天线座、空滤外壳、门外拉手、灯体、盖板、发动机隔板等;PA6+GF60%---用于生产汽车高强度部件、倒车镜壳体支架、一般可以替代金属产品等;PA6+GF10%+M20%---用于生产油箱盖、发动机盖板、门外拉手、轮饰盖、耐磨低收缩不不变形部件等;PA6+GF20%+M25%---用于生产汽车电子冷却风扇、门外拉手、小型盖板、发动机外壳等;PA6+M30/35/40%---用于生产汽车加油门小盖、空气滤板、倒车镜壳体、线束固定座等。
关注艾邦高分子,回复“尼龙”或者“玻纤”查看更多增强尼龙成型生产中容易出现一些问题,包括因熔融粘度大造成的充填困难、因混炼不均造成的性能变化以及制品表面烧焦、浮纤、料花、翘曲变形等等。
特别是3C产品表面质量,对于外观要求越来越高。
“浮纤”现象是玻纤增强尼龙在注射成型过和中,经常出现的表面质量问题,一直困扰着塑料制品的生产制造。
浮纤浮纤也叫露纤。
浮纤的原因和解决对策
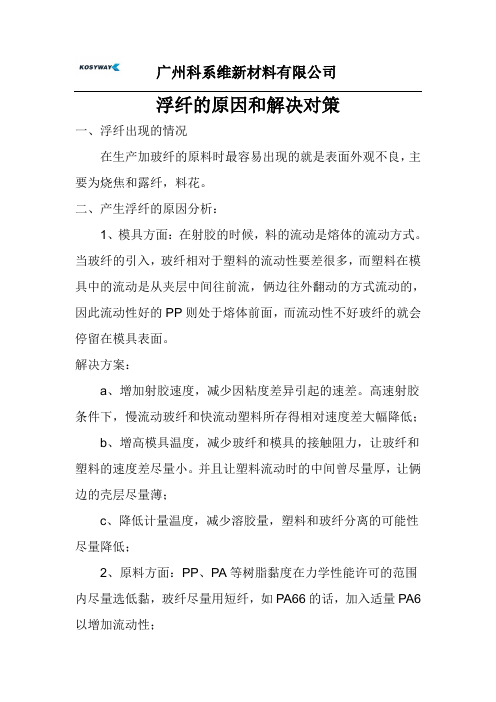
浮纤的原因和解决对策
一、浮纤出现的情况
在生产加玻纤的原料时最容易出现的就是表面外观不良,主要为烧焦和露纤,料花。
二、产生浮纤的原因分析:
1、模具方面:在射胶的时候,料的流动是熔体的流动方式。
当玻纤的引入,玻纤相对于塑料的流动性要差很多,而塑料在模具中的流动是从夹层中间往前流,俩边往外翻动的方式流动的,因此流动性好的PP则处于熔体前面,而流动性不好玻纤的就会停留在模具表面。
解决方案:
a、增加射胶速度,减少因粘度差异引起的速差。
高速射胶条件下,慢流动玻纤和快流动塑料所存得相对速度差大幅降低;
b、增高模具温度,减少玻纤和模具的接触阻力,让玻纤和塑料的速度差尽量小。
并且让塑料流动时的中间曾尽量厚,让俩边的壳层尽量薄;
c、降低计量温度,减少溶胶量,塑料和玻纤分离的可能性尽量降低;
2、原料方面:PP、PA等树脂黏度在力学性能许可的范围内尽量选低黏,玻纤尽量用短纤,如PA66的话,加入适量PA6以增加流动性;
3、加工工艺方面:a、适当提高螺杆剪切力;b、注射速度调高,螺杆速度可以调到70%-90%;c、增大注射压力;d、整个螺杆回缩1-2MM,防止浇口浮纤;e、对于复杂制件采取分级注塑。
4、助剂方面:提高玻纤的流动性,增强玻纤与树脂的结合能力,是最有有效的办法,如加些硅酮、分散剂之类的助剂。
以下是一个解决方案仅供参考:
硅酮0.5~0.8%+分散剂0.8%,可以有效增加产品的光度和降低螺杆扭矩。
玻纤的分类及应用(不错)

玻纤知识与浮纤解决方法探讨第一部分:玻纤知识:1、玻纤分类从长度分类分可以分连续玻纤、短玻纤(定长玻纤)和长玻纤(LET),连续玻纤是国内目前应用最广的玻纤,就是通常说的“长纤”,代表厂家有巨石,泰山、兴旺等。
定长玻纤就是通常说的“短纤”,一般是外资改性厂与国内部分企业在用,代表厂家有PPG,OCF及国内的CPIC,巨石泰山也有少部分,但质量不如人意。
LET是最近在国内兴起的,代表厂家有PPG,CPIC及巨石,目前国内金发和苏州和昌产量较大,杰事杰及温州俊尔,南京聚隆在开发当中,也有小批量生产从碱金属含量分可分为无碱,低中高,通常改性增强用无碱,也就是E玻纤,国内改性一般使用E玻纤。
2、玻纤的应用:玻纤增强塑料的原理主要是由于玻纤/树脂界面上连接必然是使作用到模塑件上的力传导到玻纤上,因此玻纤的长度被充分利用,起到树脂增强的目的,但玻纤在树脂基体中长度必须满足一定的要求,这就是临界玻纤长度,玻璃纤维的临界纤维长度(即可将力从基材传递给纤维的最小长度)在0.3~0.6mm之间,临界长度只与剪切力与玻纤单丝直径有关,上面的临界长度是指玻纤在最终产品里的长度,如是果是塑料粒子里话,此长就就在0.6~0.8mm之间,从理论上讲,临界长度与玻纤的原始长度没有关系,如果增强产品把玻纤的长度都控制在这个范围的话,此时产品的力学性能与表面外观都是最好的,最平衡的,如果长度过长,力学性能上升,但制品表面会变粗糙与翘曲,如果长度过短,就会导致力学性能不足。
要控制玻纤的长度应该从调整螺杆结构及转速入手,如果玻纤长径控制在400效果最佳。
3、评价玻纤好坏的主要指标:第一个指标:玻纤在拉丝过程中所使用的表面活性处理剂。
表面活性处理剂也就是通常所说的浸润剂,浸润剂主要是偶联剂与成膜剂,另外还有一些润滑剂、抗氧剂、乳化剂、抗静电剂等,成膜剂的成分与其它助剂的种类对玻纤有决定性的影响,所以在选择玻纤时就根据基料与成品要求选择合适的玻纤。
- 1、下载文档前请自行甄别文档内容的完整性,平台不提供额外的编辑、内容补充、找答案等附加服务。
- 2、"仅部分预览"的文档,不可在线预览部分如存在完整性等问题,可反馈申请退款(可完整预览的文档不适用该条件!)。
- 3、如文档侵犯您的权益,请联系客服反馈,我们会尽快为您处理(人工客服工作时间:9:00-18:30)。
“浮纤”原因和解决方法(总
3页)
-CAL-FENGHAI.-(YICAI)-Company One1
-CAL-本页仅作为文档封面,使用请直接删除
“浮纤”现象是玻纤外露造成的,白色的玻纤在塑料熔体充模流动过程中浮露于外表,待冷凝成型后便在塑件表面形成放射状的白色痕迹,当塑件为黑色时会因色泽的差异加大而更加明显。
其形成的原因主要有以下几个方面。
首先,在塑料熔体流动过程中,由于玻纤与树脂的流动性有差异,而且质量密度也不同,使两者具有分离的趋势,密度小的玻纤浮向表面,密度大的树脂沉入内里,于是形成了玻纤外露现象;
其次,由于塑料熔体在流动过程中受到螺杆、喷嘴、流道及浇口的摩擦剪切力作用,会造成局部粘度的差异,同时又会破坏玻纤表面的界面层,熔体粘度愈小,界面层受损愈严重,玻纤与树脂之间的粘结力也愈小,当粘结力小到一定程度时,玻纤便会摆脱树脂基体的束缚,逐渐向表面累积而外露;
再则,塑料熔体注入型腔时,会形成“喷泉”效应,即玻纤会由内部向外表流动,与型腔表面接触,由于模具型面温度较低,质量轻冷凝快的玻璃纤维被瞬间冻结,若不能及时被熔体充分包围,就会外露而形成“浮纤”.
主要问题要解决相容和材料间的结合
改善“浮纤”
现象的措施方法是在成型材料中加入相容剂、分散剂和润滑剂等添加剂,包括硅烷偶联剂、马来酸酐接枝相容剂,南京塑泰相容剂、硅酮粉、脂肪酸类润滑剂及一些国产或进口的防玻纤外露剂等,通过这些添加剂来改进玻纤和树脂之间的界面相容性,提高分散相和连续相的均匀性,增加界面粘接强度,减少玻纤与树脂的分离,从而改善玻纤外露现象,液体硅烷偶联剂,就存在加入后难以分散,塑料容易结块成团的问题,会造成设备喂料不均匀,玻纤含量分布不均匀,进而导致制品的力学性能不均匀浇注系统设计的基本原则是流道截面宜大,流程宜平直而短。
应采用粗短的主流道、分流道和粗大浇口,浇口可以是薄片式、扇形及环形,亦可采用多浇口形式,以使料流混乱、玻纤扩散、减少取向性。
而且要求有良好的排气功能,能及时排出因玻纤表面处理剂挥发产生的气体,以免造成熔接不良、缺料及烧伤等缺陷.
另外需要注意的是,“浮纤”易于在塑件壁厚较大的部位出现,这是因为熔体在该处流动速度梯度较大,熔体流动时其中心速度高,而靠近型腔壁面处速度低,使得玻纤浮露的趋势加剧,相对速度更慢,发生滞留堆积而形成“浮纤”。
因此,应尽量使塑件各处壁厚均匀,并避免尖角、缺口,保证熔体流动顺畅,由于玻纤增强塑料的熔融指数比非增强塑料低30%~70%,流动性较差,因此料筒温度较一般情况应高出10~30℃。
提高料筒温度,可使熔体粘度降低,改善流动性,避免填充及熔接不良,而且有利于加大玻纤分散性和减小取向性,获得较低的制品表面粗糙度。
但料筒温度并不是越高越好,温度过高会加大尼龙聚合物氧化和降解的趋势,轻微时会发生颜色变化,严重时则产生焦化发黑。
在设置料筒温度时,应使加料段温度比常规要求略高些,稍低于压缩段即可,以利用其预热效果,降低螺杆对玻纤所产生的剪切作用,减少局部粘度的差异及对玻纤表面的破坏,保证玻纤与树脂之间的粘结强度
模具与熔体之间的温差不宜太大,防止熔体充填时玻纤遇冷在表面淤积,形成“浮纤”,因此需采用较高的模具温度,这对于提高熔体充模性能、增加熔接痕强度、改善制品表面光洁度、减少取向和变形也是有利的。
但模具温度愈高,冷却时间愈久,成型周期延长,生产率降低,而且成型收缩率加大,故也不是越高越好.采用高料温、高模温、高压、高速、低螺杆转速注射,对改善“浮纤”现象比较有利。