异丁烷制异丁烯技术综述
异丁烷与异丁烯的分离-概述说明以及解释

异丁烷与异丁烯的分离-概述说明以及解释1.引言1.1 概述概述部分的内容:异丁烷与异丁烯是一对常见的有机化合物,它们在工业生产中具有重要的应用价值。
异丁烷是一种无色气体,具有较低的沸点和可燃性,在化工领域广泛用于溶剂、燃料和润滑剂等方面。
异丁烯则是一种无色液体,具有较高的沸点和双键的存在,常用作合成橡胶、塑料和溶剂等。
由于它们在性质上的相似性,使得在工业分离过程中面临着一些挑战。
本文将重点探讨异丁烷与异丁烯的分离问题,分析现有的分离方法并对其进行评价。
同时,本文还将展望未来的研究方向,以期对解决异丁烷与异丁烯分离问题提供一定的参考。
不同的分离方法具有各自的特点和适用范围,包括蒸馏、吸附、萃取等。
然而,由于异丁烷与异丁烯在物理性质上的相似性,传统的分离方法往往效果不佳,存在分离度低、能耗高等问题。
因此,对异丁烷与异丁烯分离问题的研究和探索具有重要的理论和应用意义。
总之,本文将通过对异丁烷与异丁烯的性质进行分析,介绍现有的分离方法,并对其进行评价和展望。
同时,将探讨未来研究方向,以期为解决该分离问题提供可行的解决方案。
文章结构是指文章的组织框架,通常包括引言、正文和结论三个部分。
每个部分又可以分为不同的子部分,以便更好地组织和呈现文章内容。
在本文中,文章结构如下:1. 引言1.1 概述1.2 文章结构1.3 目的2. 正文2.1 异丁烷的性质2.2 异丁烯的性质2.3 异丁烷与异丁烯的分离方法3. 结论3.1 总结异丁烷与异丁烯的分离问题3.2 对分离方法的评价和展望3.3 未来研究方向1.3 目的本文的目的是探讨异丁烷与异丁烯的分离方法,以解决工业生产中常见的分离难题。
具体来说,我们将对异丁烷和异丁烯的性质进行研究和分析,以了解它们之间的差异和相互作用。
根据性质的不同,我们将研究和比较各种分离方法,包括物理方法和化学方法。
我们将关注这些方法的效率、成本、环境友好性以及工业应用的可行性。
同时,我们也将评价当前已知的分离方法的优缺点,并展望未来可能的研究方向。
异丁烯的生产工艺与技术路线的选择

异丁烯的生产工艺与技术路线的选择2.1 异丁烯生产工艺发展概述目前,生产异丁烯的原料主要来源于石脑油蒸汽裂解制乙烯装置的副产C4馏分、炼油厂流化催化裂解(FCC)装置的副产C4馏分和Halcon法环氧丙烷合成中的副产叔丁醇(TBA)。
各种C4馏分中异丁烯的含量有所不同。
在C4馏分中,由于异丁烯和正丁烯的沸点只相差0.6℃,相对挥发度仅相差0.022℃,因此采用一般的物理方法很难将其分离,但由于异丁烯的化学活性仅次于丁二烯,所以工业上一般利用其化学活性来进行分离。
20世纪80年代以前,异丁烯主要通过硫酸萃取法进行生产,少数采用Halcon 共氧化联产法进行。
硫酸萃取法技术成熟,工业上已经沿用40多年,但该方法的反应选择性不理想,设备腐蚀严重,存在废酸回收处理等问题,而Halcon共氧化法局限性较大,只有在大规模联产环氧丙烷和叔丁醇时才能使用。
进入20世纪80年代,异丁烯的生产纷纷转向技术经济更为合理的甲基叔丁基醚(MTBE)裂解法和树脂水合脱水法工艺。
树脂脱水法的主要缺点是C4馏分中异丁烯单程转化率低(将增加进一步提取1-丁烯的难度),采用多段水合可提高转化率,但能耗较高。
MTBE裂解法生产异丁烯收率和选择性均较高,工艺过程简单,投资费用较低,适宜于大规模生产。
80年代后期,新建的从裂解C4馏分中分离出异丁烯的生产装置,绝大部分采用此法进行生产。
进入90年代,又开发出异构化生产异丁烯的生产技术。
目前,MTBE裂解法和异构化法已经成为世界上生产异丁烯的两种最主要的方法。
2.2 异丁烯的几种生产工艺2.2.1甲基叔丁基醚(MTBE)裂解法甲基叔丁基醚(MTBE)裂解制异丁烯是20世纪70年代末期研究开发成功的一种生产异丁烯的重要方法。
和其它方法相比,该技术具有对设备无腐蚀,对环境无污染,工艺流程合理,操作条件缓和,能耗低,产品纯度高,装置规模灵活性大,可以根椐市场需求生产MTBE或异丁烯等特点,自开发成功至今一直是国内外生产异丁烯最主要的方法之一。
异丁烷脱氢制异丁烯 ppt课件
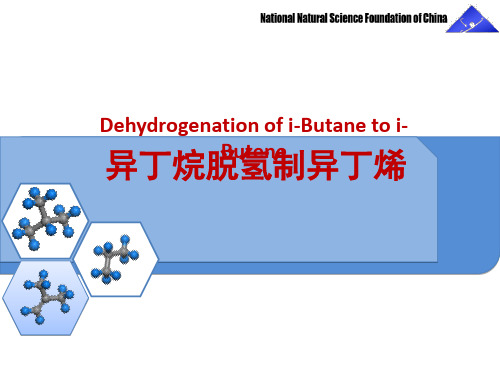
异丁烷脱Bu氢ten制e 异丁烯
主要内容
1
背景
1. 背景
1.背景
① 我国异丁烯几乎全部来自催化裂化和乙烯装置。 ② 2010年国内异丁烯供给量可望达到270万-280万吨。 ③ 2007年FCC副产异丁烯约120万吨,2010年约160万吨 ④ 2005年来自乙烯裂解的异丁烯近70万吨,2010年超过110万吨。
烷烃分子C-H键的选择性活化 如何实现选择性活化C-H键?
① 关键是催化剂 ② 硫化前,分解 ③ 硫化后,脱氢
硫化前后催化剂脱氢性能对比
解决催化剂问题,是解决C-H键选择性活化的关键。
需要解决的关键问题
烷烃分子C-H键的选择性活化 C-H键是如何选择性活化的?
反应物+活性位 吸附
表面中间物种 表面反应
1.背景
混合馏分异丁烯化工利用途径 ① 生产MTBE ② 生产叔丁醇 ③ 生产甲基丙烯酸甲酯MMA ④ 生产聚丁烯,用作润滑油添加剂。 ⑤ 生产对叔辛基酚(对叔辛基酚甲醛
树脂,橡胶硫化剂;与环氧乙烷一 起生产辛基酚聚氧乙烯醚) ⑥ 异戊二烯
1.背景
高纯异丁烯
纯度高于99.5%
高纯度异丁烯生产
① 硫酸叔丁基酯法 ② MTBE法(改性Al2O3、180oC、0.3-0.6MPa) ③ 叔丁醇法
消费领域
2007年
2008年
2010年
抗氧剂,农、医药中间体
1.95
1.95
2.1
丁基橡胶
4.17
4.98
12.0
高活性聚异丁烯
1.50
1.50
4.0
合计
7.62
异丁烷化工利用技术现状及发展趋势

异丁烷化工利用技术现状及发展趋势2017-01-23原《石油石化行业资讯》,您身边的石化咨询专家,专注石油石化行业,提供炼油与化工工艺、设备、安环、信息技术方面的资讯与服务。
催化裂化装置副产的混合C4中异丁烷的含量高达45.5%,多数企业将异丁烷直接作为液化气出售。
随着国内炼油装置及催化裂化装置规模的不断扩大,未来异丁烷的产能将进一步提高,如何提高异丁烷的经济效益逐渐成为C4资源综合利用的热点。
目前,异丁烷化工利用的路线主要有3条:1)异丁烷与C3~5烯烃进行烷基化反应生成烷基化油;2)异丁烷与丙烯进行共氧化反应生产环氧丙烷(PO)并联产叔丁醇(TBA)或甲基叔丁基醚(MTBE);3)异丁烷脱氢制异丁烯。
相对于异丁烯、正丁烯等C4烯烃,异丁烷的化工利用较为困难,并且无论哪一种利用路线,都存在技术难度高和投资额大等问题。
因而,对异丁烷的化工利用路线进行分析,以找到一条适宜的路线,对提高企业的经济效益具有重要的意义。
1、异丁烷烷基化1.1 技术现状异丁烷烷基化技术比较成熟,目前世界各大型装置的生产路线基本仍以硫酸法和氢氟酸法为主。
虽然液体酸烷基化工艺的烷基化油收率高、选择性好,但硫酸法工艺废酸排放量大,环境污染严重;氢氟酸是易挥发的剧毒化学品,一旦泄漏会给环境和周围生态系统造成严重危害。
此外,液体酸烷基化工艺都存在生产设备腐蚀等问题。
因此,国外主要生产企业对传统的烷基化技术不断进行改进,与传统硫酸法相比,新硫酸法在反应温度和烷烯比等工艺条件方面有所改进,烷基化油的辛烷值和蒸气压有所提高,生产过程的废物量减少,硫酸用量大幅减少且分离净化过程得到了简化。
具有代表性的改进型硫酸法工艺是Lummus公司的CDAlky低温硫酸烷基化工艺。
该工艺比传统的硫酸法酸耗量减少50%以上,烷基化产物的辛烷值至少提高1个单位,而且不需要中和及水洗,由于简化了流程而使整套装置的投资和公用工程消耗大幅降低。
近年来,以固体酸和离子液体为催化剂的烷基化工艺也成为相关企业的关注焦点。
异丁烷脱制异丁烯的技术

稳定性实验
P t - Sn-K/γ-Al2O3催化 剂异丁 烷转化 率和异 丁烯选 择 性
稳定性实验
P t - Sn-K/γ-Al2O3催化 剂异丁 烯收率 和副产 物收率
5、总 结
1 国内催化裂化石油气中的异丁烷绝大部分作为民用液化石油气燃 料,而其他用途的用量不到总量的5% ,我国对异丁烷的使用还 处在初级阶段,新的用途还有待开发。
游产品的开发利用,全球性异丁烯资源不足的矛盾日益突出。传统
来源的异丁烯已不能满足需求。因此,扩大异丁烯的来源,增加异
丁烯的产量,已成为全球石油化工发展的当务之急。
1、生产需求
· 炼油厂的副产物主要由C4-C6链烷烃组成,这些副产物一直作为 低价值的燃料使用,化工利用率低。因此,探讨C4-C6烃深加工途径 ,以C4-C6为原料开发化工产品,合理利用该资源,具有十分重要的 意义。
4、实验成果
(2)异丁烷脱氢工艺实验
异丁烷脱氢实验装置图
4、实验成果
(2)异丁烷脱氢工艺实验 实 验 催 化 剂 采 用 自 制 P t - Sn-K/γ-Al2O3催 化 剂
外观:黄色球状,规格Φ3mm
催化剂性质
载体
比表面积m2/g
γ-Al2 O3(Sn)
95
孔容ml/g 0.79
孔半径nm 16.6
异丁烷脱氢制异丁烯典型工艺介绍
(2)Lummus公司的Catofin工艺 由正丁烷脱氢生产丁二烯的工艺技术上发展而来,1986年首套装
置工业化。 技术特点:一套装置至少由三台反应器组成,间歇再生反应系统。
异丁烷转化率较高,采用氧化铬\ 氧化铝催化体系。
异丁烷脱氢制异丁烯的技术

氧化铬/Al2O3 500~600 常压以上 9h(3再生)
45~55
50
40~45
91~94
91以上
91~95
异丁烷脱氢生产异丁烯工艺汇总表
4、实验成果
(1)C4烯烃原料的净化
MTBE醚后碳四和MTBE裂解生产纯异丁烯中含有二甲醚、MTBE、 甲醇、叔丁醇、水等氧化物杂质。甲醇制烯烃(MTO)副产的碳四中 含有CO、CO2、二甲醚、甲醇、水等氧化物杂质。
对Pt-Sn-K/γ-Al2O3催化剂异丁烷脱氢反应的影响。
反应温度实验
异丁烷转化率,% 异丁烯选择性,%
100 90 80 70 60 50 40 30 0
100
90
560℃
80
580℃
600℃
70
620℃
640℃
60
50
40
30
50
100
150
200
250
300
反应时间,min
反应温度对异丁烷转化率和异丁烯选择性的影响
10
5
5
0
0
0
1
2
3
4
5
6
氢烷比(mol)
氢烷比对异丁烯收率和副产物收率的影响
4、实验成果
(2)异丁烷脱氢工艺实验
(Ⅳ) 稳定性实验 实验条件:
压力:0.1MPa, 反应温度:580℃, 进料组成:H2/ i-C4H10=2(V) , 进料空速:总空速GHSV=2000h-1,GHSV(i-C4H10)=667h-1, 考察Pt-Sn-K/γ-Al2O3催化剂稳定性。
异丁烷直接脱氢反应研究较早,较为深入,已经实现了工业化生产, 但在选择性和催化剂积炭问题上还有待于进一步开发。
异丁烷脱氢制异丁烯

3.异丁烷脱氢
异丁烷脱氢
烟气
原料 去分离系统 洗 涤 罐 沉 淀 罐 反应器
再 生 器
发 生 蒸 汽
燃料 污 油 预热炉 空气
异丁烷脱氢
装置构成: ♥ 反应再生部分 ♥ 反应气体水洗部分
♥ 烟气洗涤部分
♥ 富气压缩及吸收稳定部分 ♥ 气体分离部分(包括脱丙烷塔、脱异丁烷塔,但不包括 丙烯塔)。
600oC
0 200 400
o
焦炭
600
800
1000
Temperature( C)
异丁烷脱氢
脱氢后干气组成 烃 H2 甲烷 乙烷 乙烯 含量,wt% 51.98 36.14 8.91 2.97 烃
醚化后C4组成 含量,wt% 90.75 6.20 1.20 0.95 0.90
异丁烷 正丁烷 反2-丁烯 1-丁烯 顺2-丁烯
③ 只有选择性活化C-H键,才能得
到相应的烯烃。
需要解决的关键问题
烷烃分子C-H键的选择性活化 如何实现选择性活化C-H键?
① 关键是催化剂 ② 硫化前,分解 ③ 硫化后,脱氢
硫化前后催化剂脱氢性能对比
解决催化剂问题,是解决C-H键选择性活化的关键。
需要解决的关键问题
烷烃分子C-H键的选择性活化 C-H键是如何选择性活化的?
催化剂 高活性 低成本 无毒性
长期稳 态运行
需要解决的关键问题 1. 背景 拟开展的工作
研究新型高活性、非贵金属、环保型烷 烃脱氢制烯烃催化剂,解决烷烃脱氢制
烯烃C-H键选择性活化问题。
研究与新型催化剂配套的循环流化床反
应器,解决气固两相高效接触问题。
需要解决的关键问题
烷烃分子C-H键的选择性活化 为什么要选择性活化C-H键?
异丁烷脱氢制异丁烯的技术教学提纲
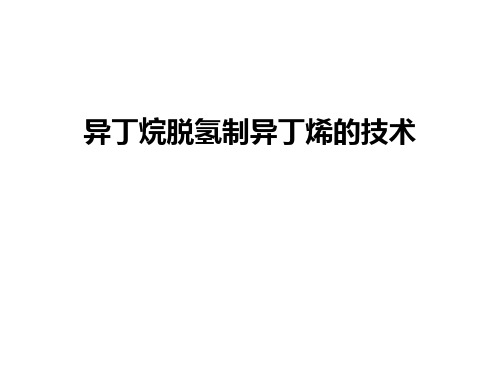
性。
3、异丁烷脱氢生产异丁烯工艺
Oleflex工艺流程图
3、异丁烷脱氢生产异丁烯工艺
异丁烷脱氢制异丁烯典型工艺介绍
(2)Lummus公司的Catofin工艺 由正丁烷脱氢生产丁二烯的工艺技术上发展而来,1986年首套装
置工业化。 技术特点:一套装置至少由三台反应器组成,间歇再生反应系统。
3、异丁烷脱氢生产异丁烯工艺
俄罗斯的FBD-4工艺流程图
3、异丁烷脱氢生产异丁烯工艺
异丁烷脱氢制异丁烯典型工艺介绍
(5)Linde A.G公司的Linde工艺 1982年中试,1998年西班牙第一套装置 技术特点:与Star工艺相似,唯一不同是不加蒸汽稀释剂。
3、异丁烷脱氢生产异丁烯工艺
Linde工艺流程图
wt% 0.11 3.22 1.78 34.83 10.91 17.01 14.70 5.06 11.28 0.43 0.20 0.48
2、工艺改进
原工艺
混合C4 抽余液
改进工艺
异丁烯
MTBE 醚化装置
液化气 燃料直接燃烧
异丁烷脱氢 装置
异丁烷
丁烷异构化 装置
混合C4
MTBE 醚化装置
异丁烯
醚后C4
冷 凝 罐 冷凝水
收 液 罐
湿式流量计 储 液 罐
4、实验成果
❖ 异丁烷直接脱氢反应研究较早,较为深入,已经实现了工业化生产, 但在选择性和催化剂积炭问题上还有待于进一步开发。
3、异丁烷脱氢生产异丁烯工艺
异丁烷脱氢制异丁烯典型工艺介绍
(1)Uop公司的Oleflex工艺 80年代开发,1990年实现工业化。 技术特点:采用移动床反应器,设计装置处量大,Pt为催化活性
- 1、下载文档前请自行甄别文档内容的完整性,平台不提供额外的编辑、内容补充、找答案等附加服务。
- 2、"仅部分预览"的文档,不可在线预览部分如存在完整性等问题,可反馈申请退款(可完整预览的文档不适用该条件!)。
- 3、如文档侵犯您的权益,请联系客服反馈,我们会尽快为您处理(人工客服工作时间:9:00-18:30)。
异丁烷制异丁烯技术综述摘要:以异丁烷为原料制取异丁烯是解决异丁烯短缺和异丁烷浪费的双赢方法。
本文简要介绍了异丁烷脱氢的反应机理;异丁烷脱氢催化剂:铂系催化剂、铬系催化剂、钒系催化剂和杂多酸催化剂,目前Cr系催化剂和Pt系催化剂是异丁烷脱氢技术中主要应用的催化剂;异丁烷脱氢工艺,主要包括UOP 公司的Oleflex工艺、Lummus公司的Catofin工艺、Phillips公司的STAR工艺、俄罗斯的FBD-4工艺、以及Linde公司的Linde工艺,其中工业化最多的为Oleflex工艺、Catofin工艺和FBD-4工艺,经验也比较丰富。
我国的异丁烷脱氢技术全部从国外引进,近期,中国石油大学自主研发的新型丙烷/丁烷脱氢(ADHO)技术开车成功,填补了我国在该技术领域的空白,为我国异丁烷脱氢产业带来了更为广阔的前景。
关键词:异丁烷脱氢,异丁烯,脱氢机理,脱氢催化剂,脱氢工艺1 前言我国C4资源丰富,但是C4利用率很低,仅有7.8%,与发达国家相比有很大的差距。
在美国,C4利用率为80%~90%,西欧为60%,日本为64%。
据调查显示,我国炼厂副产的碳四馏分中含有大量的异丁烷,而国内对异丁烷的利用缺乏足够的重视,C4馏分除了少量用于烷基化外,绝大部分仍作为民用燃料直接消耗,未得到有效利用。
因此,合理利用C4资源,将其进行深加工,制备出国内需要的化工原料单体,是石油化工领域面临的一项迫切的任务。
异丁烯没有天然来源,主要来自催化裂化液化石油气中的C4组分、石脑油蒸汽裂解制乙烯中副产的C4烯烃和天然气中的C4组分。
随着石油化工技术的发展,异丁烯已成为除乙烯、丙烯以外重要的基础石油化工原料[i],可广泛用于合成丁基橡胶、聚异丁烯、甲基丙烯酸甲酯等化工产品[ii],也可用于合成无铅、含氧、低芳烃和高辛烷值汽油的优良调和组分甲基叔丁基醚(MTBE)和乙基叔丁基醚(ETBE)。
近年来,异丁烯下游产品的急剧发展导致我国对异丁稀的需求也在逐年增加,传统的合成异丁烯的方法很难满足这种快速增长的需求。
相反我国异丁烷的来源广泛,价格低廉,工业利用不足,把异丁烷做为高附加值来利用显得十分必要,异丁烷脱氢制备异丁烯不仅可以解决我国异丁烯短缺的问题,也可解决异丁烷用于燃料的浪费问题。
2 异丁烷脱氢反应概述异丁烷脱氢是指在一定的温度和压力下,在叔碳原子和一个伯碳原子上发生碳氢键的断裂形成碳碳双键,其脱氢方法可分为三种:直接脱氢、氧化脱氢和膜催化反应脱氢。
2.1 异丁烷直接脱氢直接脱氢法即异丁烷在非氧化气氛中直接脱氢,为防止催化剂结焦可选择氢气做为稀释剂。
其反应方程式为:△H°=120kJ/mol直接脱氢反应为强吸热反应,且是体积增大的反应,根据热力学原理,反应需要在高温、低压下才能具有良好旳转化率。
但是高温下催化剂容易发生裂解、烯烃聚合等副反应使催化剂积炭和结焦从而使催化剂失活。
工业上通常采用逐步加热的方式对催化剂进行脱氢,这样可以在较高转化率的情况下增加催化剂的单程周期,达到一个最优的经济效益。
但该方法催化剂的用量和循环量较大,工业上耗能较大。
2.2 异丁烷氧化脱氢氧化脱氢即异丁烷在氧化气氛下进行脱氢,其反应方程式如下:该反应属于放热反应,不存在热力学限制性问题,反应温度较低,解决了催化剂的能耗和高温下反应的积炭问题[iii],但氧化脱氢的产物比较复杂,不同的氧浓度产生不同的产物。
因此,催化反应高度氧化和催化剂稳定性是限制其工业化发展的根本因素。
2.3 异丁烷膜催化脱氢对于可逆的脱氢反应,利用膜催化反应可以将氢气从反应体系中选择性移除,从而打破热力学平衡的限制。
近年来,用于异丁烷脱氢的膜反应器主要有钯膜、钯合金膜、介孔氧化铝或氧化硅膜等,但介孔膜对氢气的选择透过性较低,且对反应空速有一定限制。
而钯、钯合金等致密膜对氢气的选择透过性高、膜通量大,因此受到研究者的广泛关注。
异丁烷膜催化脱氢反应的关键在于寻找一种选择性高且耐高温的膜,现正处于研宄阶段,还面临许多有待解决的问题。
2.4 异丁烷三种脱氢方法比较异丁烷直接脱氢法由于需要在高温条件下反应能耗较大,但在合适的催化剂和条件下可以达到很好的选择性而普遍被工业化所采用;异丁烷氧化脱氢法虽然能耗低但由于产物的分布难于控制、选择性差,目前还处于进一步研究阶段;异丁烷膜催化反应脱氢法,现在只是处于探索阶段,离实现工业化还有很远的距离。
3 异丁烷脱氢反应机理异丁烷脱氢反应过程中,在催化剂表面除了会发生异丁烷脱氢主反应外,还会发生裂解、异构化、芳构化、烷基化、聚合、结焦等副反应,其反应网络如图1所示:图1 异丁烷脱氢反应网络随着催化剂种类的不同,异丁烷直接脱氢的反应机理也不尽相同。
一般情况下,自由基机理和碳正离子机理是脱氢反应中可能发生的两种机理。
3.1 自由基机理自由基机理即反应物以均裂方式脱去氢原子,其反应过程[iv]如下:式中,M为催化剂上的金属原子或金属离子;N为催化剂上的金属原子或金属离子,或者催化剂表面上存在的氧原子[O]或·O一。
自由基机理对催化剂有着一定的要求,那就是其能够提供具有未配对电子的活性中心,而这些活性中心则需要具有较强的成键能力以及较多的暴露。
如此,这些活性中心就可以与C-H上的H原子相接触,并发生作用,金属(如铂、镍、铜等)、硫化物以及氧化物催化剂都可以满足此反应机理。
3.2 碳正离子机理碳正离子机理即反应物以异裂方式脱去和,其反应过程[i]如下:式中M为催化剂表面金属离子活性中心。
该机理对反应物和催化剂都有着一定的要求。
对反应物分子来说,要求其容易发生极化而产生Cδ+-Hδ-。
而对催化剂来说,在其上需要包含有着较强极化作用力的金属离子M n+,以便以脱去H-,同时为了以接受H+,还需要包含具有显著电荷效应的O2-。
显而易见,此类机理与酸碱催化非常类似。
4 异丁烷脱氢催化剂异丁烷脱氢是一个较强的吸热过程,受动力学控制的,高温有利于提高收率,但高温下催化剂易于失活;较低的氢压对脱氢有利,但实际操作中为抑制结焦和清除积炭又需要临氢环境,故实现该过程有一定的难度。
目前异丁烷脱氢的催化剂主要可以分为FBD-4工艺为代表的铬系催化剂和以UOP Oleflex 工艺为代表的铂系催化剂。
此外,近年来对钒系催化剂和杂多酸催化剂的研究也有所增加。
4.1 铂系催化剂铂作为优良的脱氢催化剂的活性组分,在烷烃催化脱氢领域占据重要的地位。
以铂为活性中心催化异丁烷脱氢具有选择性高,催化活性持久等优点。
负载型的单金属Pt催化剂对低碳烷烃的脱氢效果差,易催化烷烃发生异构化和氢解反应,烯烃选择性低,此时Pt在催化剂表面以Pt4或Pt6簇形式存在。
向Pt基催化剂体系中加入Sn等金属组分,可以有效催化C-H键发生断裂,丁烯的选择性显著提高[v]。
Cortright 等[vi]将Sn组分加入到Pt/L-分子筛中,使其与Pt组分形成Pt-Sn合金颗粒,催化剂表面上Pt聚集体的尺寸得到降低,Pt簇上的异构化及氢解反应在一定程度上受到抑制。
现普遍认为,贵金属催化的脱氢反应活性位是尽可能少的Pt原子;而氢解和异构化反应因为需要连续脱氢,要求催化剂表面上至少有几个邻近的Pt原子。
Sn的加入使催化剂表面Pt 颗粒被分隔成较小的Pt原子簇,减少了碳氢化合物在Pt上的多点吸附,从而抑制了氢解反应和异构化反应,提高了低碳烷烃的脱氢选择性。
Cortright 等[vi]通过离子交换法制备了K-Pt/SiO2和K-Sn-Pt/SiO2催化剂。
他们认为Sn的加入还有利于沉积炭从活性位到载体的转移、减小了炭在金属表面沉积的比例[vii]。
高温下金属颗粒的烧结是此类催化剂失活的主要原因,而Sn的加入可以降低失活速率,提高催化剂的稳定性。
此外,钾的加入使K-Sn-Pt/SiO2具有较高的异丁烷脱氢速率,这是因为钾在提高异丁烷分子吸附稳定性的同时,增加了吸附态异丁烷发生氢脱除的活性位的数目。
然而,林励吾等[viii]认为Pt-Sn/γ-Al2O3催化剂中存在两种活性中心,分别为直接锚定在γ-Al2O3载体上的P活性位和锚定在γ-Al2O3上SnO x表面上的Pt活性位,即Pt-SnO x-γ-Al2O3“夹心”结构。
前者有利于催化烃类发生氢解反应,后者有利于催化烷烃发生脱氢反应。
Sn的加入促进了Pt组分从直接锚定状态向“夹心”结构转化。
负载型Pt基催化剂的脱氢活性与载体的酸碱性密切相关[ix]。
若采用酸性载体如γ-Al2O3、分子筛等,Pt基催化剂催化脱氢效果不佳,酸性位易催化烷烃发生异构化和裂解反应,而裂解过程生成了大量积炭,因此需要对催化剂进行频繁再生,从而缩短了催化剂的寿命。
若采用中性或非酸性载体,如具有弱酸性、高热稳定性的镁铝尖晶石、锌铝尖晶石可以抑制在酸性位上发生裂解等副反应,提高烯烃选择性。
Rennard 等[x]发现在丙烷和异戊烷脱氢时,Pt/MgAl2O4经过六次反应-再生循环后,催化剂表面Pt的分散度依然较好。
为了改善催化剂的酸性质,使其更有利于发生脱氢反应,通常加入碱性金属降低催化剂酸性、稳定载体结构。
Rodríguez 等[xi]研究表明,向Pt-Sn/SiO2新鲜剂中加入的K主要集中在载体上,虽然K的加入并未提高Pt的分散度、改善异丁烷催化脱氢活性,但明显改善了异丁烷脱氢的选择性,异丁烯选择性几乎达到100%。
Tasbihi 等[xii]认为,Li,K等碱金属的加入明显改善了Pt-Sn/Al2O3的活性、稳定性和选择性。
催化剂的制备方法也会对Pt基催化剂的催化性能产生影响。
Bocanegra等[xiii]通过高温固相反应法和共沉淀法两种方法制备了弱酸性、能高度分散金属的镁铝尖晶石。
研究表明,高温固相反应法制备的MgAl2O4具有较高的酸性、良好的金属分散能力、以此载体制备的Pt基催化剂显示了更高的催化活性。
除上述载体外,Mg(Al)O 由于适度的碱性和较高的热稳定性也得到了广泛关注。
Siddiqi 等[xiv]采用类水滑石焙烧的方法合成了系列Pt/Mg(Ga)(Al)O催化剂并对其进行了表征,发现载体中Ga的引入促进了水滑石的分解而形成混合氧化物。
大部分Ga3+以八面体配位的形式存在于载体中,小部分在Pt/Mg(Ga)(Al)O 的预还原过程中被从Pt颗粒表面溢流到载体上的H还原为Ga,进一步与Pt纳米颗粒相互作用形成Pt-Ga合金。
随着Ga/Pt的升高,催化剂的丙烷脱氢活性先升高后降低,在Ga/Pt=5.4时最大,此时烯烃选择性也最高,接近100%,这主要是表面Pt 金属颗粒的减小和催化剂表面Ga引起的电子效应的影响。
负载型Pt基催化剂为贵金属催化剂,因为其价格昂贵使其应用受到一定的限制。
如何提高Pt原子的利用率,有效降低贵金属催化剂的成本具有重要的现实意义。