混合烷烃脱氢装置原料比例调整丙烯塔热泵系统改造技术方案探讨
丙烯塔 热泵精馏 塔效率低的原因

丙烯塔热泵精馏塔效率低的原因下载温馨提示:该文档是我店铺精心编制而成,希望大家下载以后,能够帮助大家解决实际的问题。
文档下载后可定制随意修改,请根据实际需要进行相应的调整和使用,谢谢!并且,本店铺为大家提供各种各样类型的实用资料,如教育随笔、日记赏析、句子摘抄、古诗大全、经典美文、话题作文、工作总结、词语解析、文案摘录、其他资料等等,如想了解不同资料格式和写法,敬请关注!Download tips: This document is carefully compiled by the editor. I hope that after you download them, they can help yousolve practical problems. The document can be customized and modified after downloading, please adjust and use it according to actual needs, thank you!In addition, our shop provides you with various types of practical materials, such as educational essays, diary appreciation, sentence excerpts, ancient poems, classic articles, topic composition, work summary, word parsing, copy excerpts,other materials and so on, want to know different data formats and writing methods, please pay attention!热泵精馏技术是一种能有效提高塔效率的分离方法,但在实际应用中,我们常常会发现丙烯塔热泵精馏塔效率并不高,这引起了很多工程师和研究人员的关注。
丙烷脱氢制丙烯工艺流程设计与过程优化

丙烷脱氢制丙烯工艺流程设计与过程优化一、引言丙烯是一种重要的化工原料,在塑料、橡胶、合成纤维等领域有广泛的应用。
目前,丙烷脱氢制丙烯是一种主要的工艺路线。
本文将对丙烷脱氢制丙烯的工艺流程进行设计,并进行过程优化,以提高丙烯的产率和质量。
二、工艺流程设计1. 原料准备将纯度高于99%的丙烷作为原料,通过去除杂质和水分的处理,确保原料的纯净度。
经过预处理后,将丙烷送至反应器进行下一步的反应处理。
2. 反应器设计反应器是丙烷脱氢制丙烯的核心装置,其设计需考虑反应的温度、压力和催化剂的选择等因素。
常用的反应器类型有固定床反应器和流化床反应器。
选择合适的反应器类型,能够提高反应的效率和稳定性。
3. 催化剂选择催化剂在丙烷脱氢制丙烯过程中起到关键作用。
常用的催化剂有氧化铬、氯化铝、磷酸锆等。
催化剂的选择需考虑其活性、稳定性和成本等因素。
同时,催化剂的负载方式和用量也需要进行合理设计。
4. 反应条件控制在丙烷脱氢制丙烯的过程中,控制反应的温度和压力是至关重要的。
合适的反应温度和压力能够提高产率和选择性。
此外,还需进行适当的氢气调节,以实现良好的反应平衡。
5. 产物分离与纯化在反应结束后,需要对产物进行分离和纯化。
常用的分离方法有升华、蒸馏、吸附和萃取等。
通过合理的分离和纯化工艺,能够获得高纯度的丙烯产品。
三、过程优化1. 温度优化通过研究不同温度下反应的影响,寻找最适合的反应温度。
过高或过低的温度都可能导致丙烯产率的下降或副反应的发生。
通过合理控制温度,能够提高丙烯的产率和选择性。
2. 压力优化压力对丙烷脱氢反应的影响主要体现在平衡转化率上。
通过调节反应器的压力,可以使反应接近平衡,提高丙烯产率。
3. 催化剂优化催化剂的性能直接影响到反应的效果。
通过优化催化剂的配方和负载方式,提高催化剂的活性和稳定性,可以提高丙烯的产率和质量。
4. 废物处理在丙烷脱氢制丙烯的过程中,会产生一定量的废物和副产物。
合理设计废物处理方案,将废物进行回收利用或安全处理,不仅可以降低环境污染,还能减少资源浪费。
PDH技术简介及新型应用研究

PDH技术简介及新型应用研究丙烷脱氢技术简介及国内应用现状01、丙烷脱氢技术原理原料丙烷在专用催化剂的作用下,脱氢生成丙烯与副产品氢气。
反应式:该反应为强吸热过程,也是平衡反应,所以,提高温度和降低压力有利于脱氢反应的进行,从而获得较高的丙烷转化率。
02、国外主流丙烷脱氢技术存在问题丙烷脱氢技术主要有霍尼韦尔UOP催化脱氢连续移动床工艺和荷兰CBI循环多反应器系统工艺,2种技术都有较明显的缺点。
UOP工艺缺点:对装置原料丙烷的纯度要求高(丙烷纯度95%,且硫含量要低),单程转化率和选择性略低。
CBI工艺缺点:反应器设置较多,间歇操作,操作复杂;装置操作压力高,能耗较大;催化剂寿命短,且使用的催化剂含铬,对环境有污染。
新型丙烷脱氢技术开发现状及特点01、技术研发背景及简介目前国内已经投产的丙烷脱氢项目所用催化剂几乎全部被国外公司垄断。
国产化的新型高效丙烷脱氢制丙烯催化剂,对于打破国外技术垄断、实现国产化具有重要的意义。
中国石油大学重质油实验室李春义教授课题组开发出新型丙烷/异丁烷脱氢(ADHO)技术,并工业化试验取得成功,填补了国内空白。
该技术特点为:采用无毒、无腐蚀、非贵金属催化剂,并配套设计了高效循环流化床反应器,且成功实现生产过程连续进行。
02、ADHO技术优点(1)原料不需要预处理即可直接进装置反应,省去了脱硫、脱砷、脱铅等复杂过程;(2)既适用于丙烷、异丁烷单独脱氢,也适用于丙烷与丁烷混合脱氢;(3)反应与催化剂再生连续进行,效率高;(4)催化剂无毒,对环境无污染;(5)催化剂为难熔氧化物,无腐蚀性,有利于装置长周期安全稳定运行;(6)催化剂机械强度高,剂耗低等。
03、ADHO主要技术指标烯烃16%;反应方式为循环流该技术烷烃转换率为80%,氢气收率4%,C4化床反应,温度为600℃。
参考同类装置,该装置能耗为12600MJ/t左右。
某炼油厂应用该技术可行性分析丙烷脱氢装置原料为丙烷,产品为丙烯,副产氢气。
丙烷脱氢制丙烯技术研究
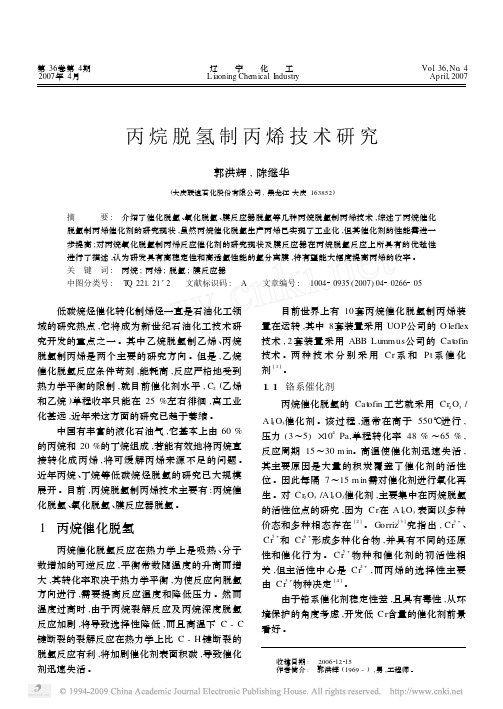
第36卷第4期辽 宁 化 工Vol.36,No.4 2007年4月L iaoning Che m ical I ndustry Ap ril,2007丙烷脱氢制丙烯技术研究郭洪辉,陈继华(大庆联谊石化股份有限公司,黑龙江大庆163852)摘 要: 介绍了催化脱氢、氧化脱氢、膜反应器脱氢等几种丙烷脱氢制丙烯技术,综述了丙烷催化脱氢制丙烯催化剂的研究现状,虽然丙烷催化脱氢生产丙烯已实现了工业化,但其催化剂的性能需进一步提高;对丙烷氧化脱氢制丙烯反应催化剂的研究现状及膜反应器在丙烷脱氢反应上所具有的优越性进行了描述,认为研发具有高稳定性和高透氢性能的氢分离膜,将有望能大幅度提高丙烯的收率。
关 键 词: 丙烷;丙烯;脱氢;膜反应器中图分类号: T Q221.21+2 文献标识码: A 文章编号: 10040935(2007)04026605 低碳烷烃催化转化制烯烃一直是石油化工领域的研究热点,它将成为新世纪石油化工技术研究开发的重点之一。
其中乙烷脱氢制乙烯、丙烷脱氢制丙烯是两个主要的研究方向。
但是,乙烷催化脱氢反应条件苛刻,能耗高,反应严格地受到热力学平衡的限制,就目前催化剂水平,C2(乙烯和乙烷)单程收率只能在25%左右徘徊,离工业化甚远,近年来这方面的研究已趋于萎缩。
中国有丰富的液化石油气,它基本上由60%的丙烷和20%的丁烷组成,若能有效地将丙烷直接转化成丙烯,将可缓解丙烯来源不足的问题。
近年丙烷、丁烷等低碳烷烃脱氢的研究已大规模展开。
目前,丙烷脱氢制丙烯技术主要有:丙烷催化脱氢、氧化脱氢、膜反应器脱氢。
1 丙烷催化脱氢丙烷催化脱氢反应在热力学上是吸热、分子数增加的可逆反应,平衡常数随温度的升高而增大,其转化率取决于热力学平衡,为使反应向脱氢方向进行,需要提高反应温度和降低压力。
然而温度过高时,由于丙烷裂解反应及丙烷深度脱氢反应加剧,将导致选择性降低,而且高温下C-C 键断裂的裂解反应在热力学上比C-H键断裂的脱氢反应有利,将加剧催化剂表面积碳,导致催化剂迅速失活。
丙烷无氧脱氢制丙烯工艺和催化剂的研究进展_刘乔

·714·
石油化工 PETROCHEMICAL TECHNOLOGY
2014 年第 43 卷
艺,其中丙烷脱氢制丙烯工艺的研究备受关注,已 成为当代石油化工领域的一个重大课题。
本文概述了目前已工业化的丙烷无氧脱氢制 丙烯技术,对常用的Cr系和Pt系催化剂进行了介 绍,重点介绍了Pt系催化剂上丙烷无氧脱氢制丙烯 的反应机理以及Pt系催化剂的结构、制备方法、失
Company
Temperature/℃
Pressure/kPa
Catalyst
Reactor
UOP Lummus
550-650
138
560-620
30
PtSn/Al2O3 Cr2O3/Al2O3
Moving bed Fixed bed
Krupp-Uhde
500
415
PtSn/ZnAl2O4
Fixed bed
气里分离催化剂粉尘的问题。
除上述常见的几种脱氢工艺外,还有尚未实
现工业化的无机膜催化脱氢工艺[8]。该工艺利用不
同物种在反应器内扩散速率不同的特点克服动力学
平衡限制,同时催化剂还可保持高的活性和选择
性,在较宽的温度范围内,使用多孔膜反应器的丙
烯收率高于固定床反应器,且大于丙烯的平衡收
率。该工艺虽然尚未实现工业化,但其应用前景可
对cr系催化剂的研究主要集中在丙烷脱氢的活性位点上cr化合物的数量与催化剂的初始活性相关但主活性中心是cr的活性位决定11温下催化剂的活性位易被丙烷或反应中间体裂解生成的碳覆盖生成积碳导致催化剂迅速失活因此要在短周期内15min左右对催化剂进行氧化除碳因此增加了操作成本
2014 年第 43 卷第 6 期
Linde-BASF Snamprogetti
化学工程工艺在丙烷脱氢工艺的研究与应用技术

化学工程工艺在丙烷脱氢工艺的研究与应用技术摘要:现阶段丙烷脱氢(PHD)国际上主要有两种主流工艺。
UOP公司的Oleflex工艺为UOP公司专利技术,在压力大于0.1 MPa、温度580~650 ℃、铂催化剂作用下进行丙烷脱氢、分离和精馏,得到聚合级丙烯产品。
反应中不用氢气或水蒸气作稀释剂,故可降低能耗和操作费用。
分为反应、回收和催化剂再生三部分。
另一种ABB公司的Lumms- Catofin工艺Catofin工艺是美国ABB Lummus公司开发的C3~C5 烷烃脱氢生产单烯烃技术,该工艺分为反应、压缩、回收和精制4个工段,本文主要研究解析丙烷脱氢工艺中的CATOFIN反应工艺过程。
关键词:化学工程;工艺;丙烷脱氢;丙烯一、工艺原理CATOFIN工艺是在固定床的铬-铝催化剂上将丙烷转化为丙烯。
属于高温裂解裂化工艺,经过优化选择性、转换率和能量损耗之间的关系,选择的反应条件约为600℃、绝对压力0.05MPa。
生成了目标产品丙烯及副产品氢气。
二、影响脱氢反应的因素1温度的影响空气或烃入口温度的增加会导致反应器底部床层温度增加,这加剧了丙烷的转化,并使选择性降低,增加了焦炭的生成。
温度影响的大小将随着催化剂的老化和活性而改变。
在反应器热量平衡控制过程中,务必注意温度对积炭的影响。
如果催化剂床未处在热平衡,并且床层温度逐渐增加,那么积炭的不成比例增加能导致床层温度以较快增长的速率上升,累积影响最终使温度失控。
因此,在连续生产中,当注意到有床层温度增加的趋势时,生产装置应作出迅速的调整来修正反应器热量平衡。
2液空时速液空时速是总的烃进料流量除以在循环的给定时刻与进料接触的催化剂总数量。
液空时速不是通常可被装置操作人员用来进行装置控制的过程变量。
然而,在低负荷条件下操作会导致液空时速降低。
一般来说,液空时速的增加对温度的增加有反作用。
液空时速的增加会降低焦炭的产生。
增加液空时速也能降低转化率而且降低丙烯的瞬时产率。
45万吨年丙烷脱氢制丙烯(PDH)装置工艺操作规程(UOP_C3_Oleflex_工艺)

45万吨/年丙烷脱氢制丙烯(PDH)装置工艺技术规程(UOP C3 Oleflex 工艺)2018年11月13日目录1 预处理工段 (1)2 丙烷脱氢反应工段 (1)3 催化剂再生工段 (4)4 冷箱分离工段 (8)5 SHP工段 (9)6 精馏工段 (9)7 PSA工段 (10)8 全厂系统(蒸汽凝液系统) (12)9 丙烷低温储罐及其辅助系统 (12)10 中间罐区 (13)11 火炬 (14)12 空压站及氮气辅助系统 (17)13 本项目涉及的主要化学反应 (19)1 预处理工段来自新鲜丙烷进料加热器(21E0601)新鲜丙烷原料先进入进料保护床(21D0101-1/2),在此用树脂吸附剂除去氮化物和有机金属化合物。
这两台保护床可以通过调整进出料管道来改变两台保护床的前后。
接着丙烷原料流过汞脱除器(21D0102)除汞,然后进入进料干燥器(21D0103-1/2))以脱除原料中水分(原料中如果含水将在分离系统结冰,就可能堵塞系统。
这两台干燥器一般在系统开车时用来干燥进料,正常运行时可不用。
进料干燥器装填分子筛以从丙烷中脱除水分。
进料干燥器设计为每周再生一次,再生用干燥的丙烷气来完成,丙烷在进料干燥再生蒸发器(21E0120)中用蒸汽先加热到60℃,然后用原料干燥再生过热器(21E0122)加热到232℃左右,以与丙烷进料相反的方向进入进料干燥器去再生干燥床层,然后进入进料干燥再生冷凝器(21E0102),被冷凝后送到进料干燥再生收集器(21D0104),在此水与再生丙烷分离,丙烷用进料干燥再生泵(21P0101)输送到在线操作的干燥器入口,废水送至反应工段与含硫废液混合后一并送至含硫/盐污水处理装置处理。
2 丙烷脱氢反应工段(1)原料预热及反应自冷箱分离工段回收冷量后的原料丙烷送至热联合进料换热器(21E0201-1/2/3/4)内与出反应器的粗产品气进行换热进一步提高进料温度同时降低粗产品的温度。
丙烯-丙烷分馏塔再沸器的配管

_____________________________________________________信息记录材料2019年6月第20卷第6期[综述•谕團丙烯-丙烷分f留塔再沸器的配管童伟(中国石化工程建设有限公司北京100101)【摘要】本文主要介绍了丙烷脱氢装置中丙烯-丙烷分馆塔再沸器的布置、配管及其优点.该塔底再沸器的配管以再沸器配管设计规定和工艺要求作为依据,同时结合再沸器管道应力要求以及再沸器的类型,综合考虑合理设计再沸器配管使其既能满足工艺和应力计算的要求,也能尽可能让再沸器配管简单紧凑,以节省材料和占地空间。
【关键词】丙烯-丙烷分馅塔再沸器;配管设计;应力要求.【中图分类号】TQ31【文献标识码】A【文章编号】1009-5624(2019)06-0021-03 The Piping of t he reboiler of p ropylene-propane fractionatorTong Wei.SINOPEC E ngineering Incorporation,Beijing100101,China[Abstract】This paper mainly introduces the arrangement,piping and advantages of reboiler of propylene-propane fractionator in propane dehydrogenation unit The piping of the reboiler at the bottom of the tower is based on the design requirements and process requirements of the reboiler piping.Considering the stress requirements of the reboiler piping and the type of the reboilei;the reasonable design of the reboiler piping can not only meet the requirements of process and stress calculation,but also make the reboiler piping as simple and compact as possible to save material and space.【Key words】Reboiler of propylene-propane fractionator;P iping;The stress requirements1引言丙烯是重要的化工原料,主要应用于生产聚丙烯(PP)、环氧丙烷(P0)、丙烯睛(AN)、丙烯酸(AA)等化工产品,终端应用涉及包装、建筑、汽车、纺织、日化等诸多领域。
POX装置原料结构调整的影响研究及解决方案
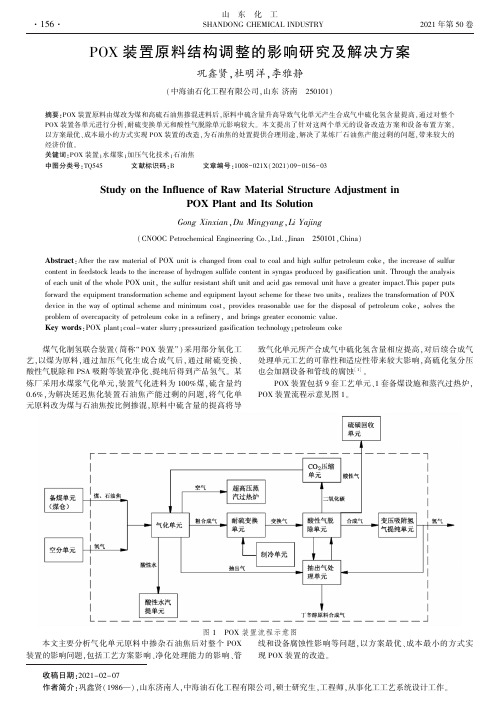
PSA 提纯单元,改造后虽然合成气中硫含量增加,但由于
合成气先经酸性气脱除单元后再进入 PSA 提纯单元,因而不会
对其造成影响。 制冷单元,根据对酸性气脱除单元的核算结
果,改造后冷量增加 10%以内,利用原有冰机即可满足要求,因
而不需要改造。
CO2 压缩单元和酸性水汽提单元,气化单元处理能力未变
化,基本无影响,不需要改造。
· 158·
3) 增加精密过滤器 1 台。
改造前后酸性气脱除单元进硫磺回收单元酸性气组成对
比见表 3。
表 3 掺入石油焦前后酸性气参数对比
名称
原设计
掺入石油焦后酸性气成分
操作压力 / MPa( G)
0.12
0.12
操作温度 / ℃
约 30
约 30
CO 2
62.72
48.89
COS
0.43
0.43
操作流量 / ( kmol / h)
Gong Xinxian,Du Mingyang,Li Yajing
( CNOOC Petrochemical Engineering Co.,Ltd.,Jinan 250101,China)
Abstract:After the raw material of POX unit is changed from coal to coal and high sulfur petroleum coke, the increase of sulfur
· 156·
山 东 化 工
SHANDONG CHEMICAL INDUSTRY 2021 年第 50 卷
POX 装置原料结构调整的影响研究及解决方案
巩鑫贤,杜明洋,李雅静
国内丙烷脱氢装置发展现状
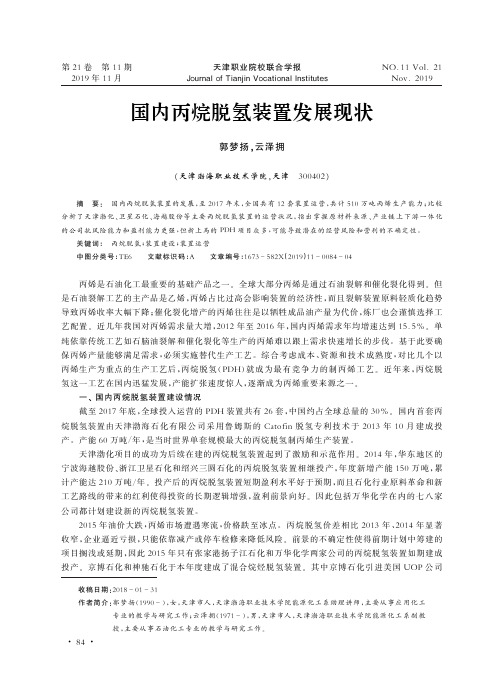
第21卷㊀第11期2019年11月天津职业院校联合学报J o u r n a l o f T i a n j i nV o c a t i o n a l I n s t i t u t e s N O.11V o l .21N o v .2019国内丙烷脱氢装置发展现状郭梦扬,云泽拥(天津渤海职业技术学院,天津㊀300402)摘㊀要:㊀国内丙烷脱氢装置的发展,至2017年末,全国共有12套装置运营,共计510万吨丙烯生产能力;比较分析了天津渤化㊁卫星石化㊁海越股份等主要丙烷脱氢装置的运营状况,指出掌握原材料来源㊁产业链上下游一体化的公司抗风险能力和盈利能力更强,但新上马的P D H 项目众多,可能导致潜在的经营风险和营利的不确定性.关键词:㊀丙烷脱氢;装置建设;装置运营中图分类号:T E 6㊀㊀文献标识码:A ㊀㊀文章编号:1673-582X (2019)11-0084-04收稿日期:2018-01-31作者简介:郭梦扬(1990-),女,天津市人,天津渤海职业技术学院能源化工系助理讲师,主要从事应用化工专业的教学与研究工作;云泽拥(1971-),男,天津市人,天津渤海职业技术学院能源化工系副教授,主要从事石油化工专业的教学与研究工作.丙烯是石油化工最重要的基础产品之一.全球大部分丙烯是通过石油裂解和催化裂化得到.但是石油裂解工艺的主产品是乙烯,丙烯占比过高会影响装置的经济性,而且裂解装置原料轻质化趋势导致丙烯收率大幅下降;催化裂化增产的丙烯往往是以牺牲成品油产量为代价,炼厂也会谨慎选择工艺配置.近几年我国对丙烯需求量大增,2012年至2016年,国内丙烯需求年均增速达到15.5%.单纯依靠传统工艺如石脑油裂解和催化裂化等生产的丙烯难以跟上需求快速增长的步伐.基于此要确保丙烯产量能够满足需求,必须实施替代生产工艺.综合考虑成本㊁资源和技术成熟度,对比几个以丙烯生产为重点的生产工艺后,丙烷脱氢(P D H )就成为最有竞争力的制丙烯工艺.近年来,丙烷脱氢这一工艺在国内迅猛发展,产能扩张速度惊人,逐渐成为丙烯重要来源之一.一㊁国内丙烷脱氢装置建设情况截至2017年底,全球投入运营的P D H 装置共有26套,中国约占全球总量的30%.国内首套丙烷脱氢装置由天津渤海石化有限公司采用鲁姆斯的C a t o f i n 脱氢专利技术于2013年10月建成投产.产能60万吨/年,是当时世界单套规模最大的丙烷脱氢制丙烯生产装置.天津渤化项目的成功为后续在建的丙烷脱氢装置起到了激励和示范作用.2014年,华东地区的宁波海越股份㊁浙江卫星石化和绍兴三圆石化的丙烷脱氢装置相继投产,年度新增产能150万吨,累计产能达210万吨/年.投产后的丙烷脱氢装置短期盈利水平好于预期,而且石化行业原料革命和新工艺路线的带来的红利使得投资的长期逻辑增强,盈利前景向好.因此包括万华化学在内的七八家公司都计划建设新的丙烷脱氢装置.2015年油价大跌,丙烯市场遭遇寒流,价格跌至冰点.丙烷脱氢价差相比2013年㊁2014年显著收窄,企业逼近亏损,只能依靠减产或停车检修来降低风险.前景的不确定性使得前期计划中筹建的项目搁浅或延期,因此2015年只有张家港扬子江石化和万华化学两家公司的丙烷脱氢装置如期建成投产.京博石化和神驰石化于本年度建成了混合烷烃脱氢装置.其中京博石化引进美国U O P 公司的O l e f l e x混合脱氢技术,建成了国内首套C3/C4混合烃脱氢装置,年产丙烯11.6万吨,异丁烯10.4万吨.生产的丙烯可以达到环氧级纯度要求.2016年,丙烯价格从年初回暖到持续走强,P D H装置利润一路飘红.河北海伟石化的50万吨/年丙烷脱氢是实现美国鲁姆斯工艺完全国产化的首套装置,于7月中旬试车成功.宁波福基石化公司一期66万吨P D H在2016年10月投产.齐翔腾达公司的低碳混合烷烃脱氢装置也于本年度8月建成,生产M T B E和丙烯.2017年,丙烷脱氢产能增长速度明显放缓,仅有东明石化投产一套混合烷烃脱氢装置.空档期的产生基于三方面原因:一是丙烷脱氢装置规模大,投资高,建设周期相对较长.经过2014~2016年产能的集中释放后,特别是2015年的不利态势令投资者持观望态度,后续产能承继乏力;二是丙烷脱氢的核心技术和原料丙烷基本依赖进口,行业准入门槛较高,有能力上马新项目的企业相对有限;三是近年来丙烯市场需求的高增长拉动了丙烯新增产能,除传统油制丙烯外,国内煤制烯烃㊁甲醇制烯烃的产能扩张势头迅猛(图1),企业对于新建丙烷脱氢项目的盈利性存在犹疑.截至2017年12月,国内共建成丙烷脱氢(包括混烷脱氢)装置12套(图2),总产能达510万吨/年.其中,纯丙烷脱氢装置产能占全部的90%,混烷脱氢占10%.图1㊀2013~2016年不同工艺制丙烯产能对比㊀㊀㊀图2㊀国内丙烷脱氢装置统计(万吨,套)二㊁国内丙烷脱氢装置运营情况(一)天津渤化丙烷脱氢装置天津渤化石化有限公司是由天津渤海化工集团有限责任公司出资组建的全资国有子公司,从事丙烷脱氢制丙烯的生产经营活动.丙烷脱氢项目总投资44.85亿元,建设规模为年产60万吨丙烯,于2013年10月12日正式投产.该装置采用A B BL u mm u s的C a t o f i n循环多反应器工艺,循环固定床反应器中的氧化铬-氧化铝催化剂将丙烷转化为丙烯,未反应的丙烷循环使用.C a t o f i n技术可以生产聚合级丙烯,是世界上丙烷脱氢的主流技术之一.装置的原料需求量约为每年70万吨,均采用进口丙烷.渤海化工集团下属的天津渤化化工进出口公司负责丙烷进口业务,与美国T a r g aR e s o u r c e s公司签订了长期协议,可保证原料供应充足.所产丙烯的50%内供给渤化集团自有的15万吨的环氧丙烷装置和两套22.5万吨的丁辛醇装置;剩余50%对外销售给山东的丁辛醇和环氧丙烷工厂.2013年,丙烷脱氢装置处于试生产阶段,产量较低.2014年整体装置负荷不高,10月~12月因故障停工,全年仅完成了产能的一半.2015和2016年,装置超负荷运转.特别是2015年产量达到70.36万吨,实现销售额42.46亿元.其下游的环氧丙烷和丁辛醇装置也达到了满负荷运转.(二)浙江卫星丙烷脱氢装置卫星石化作为国内产能最大的丙烯酸生产商之一,致力于完善C3产业链,依托上下游产业配套,提升核心竞争力,形成差异化的竞争优势.丙烷脱氢作为C3产业链的龙头,是卫星石化产业前向一体化的关键.该装置采用美国U O P公司的O l e f l e x丙烷脱氢制丙烯技术,是U O P技术在国内的第一套建成装置.建设规模为年产45万吨丙烯,2014年8月底打通全部流程,产出合格产品.卫星石化的全资子公司浙江卫星能源有限公司负责以丙烷为原料生产丙烯,36万吨配套供应卫星石化丙烯酸及酯装置,其余9万吨外售.2014年8月丙烷脱氢装置开车成功后,进入试生产阶段.2014年11月中旬,生产的丙烯可内供下游装置.2014年共生产丙烯9.87万吨,其中63%用于下游丙烯酸及酯生产,其余丙烯对外销售,实现销售收入23633万元.2015年2月底,丙烷脱氢装置试生产趋于稳定,产量逐步提升,年底达满负荷生产.但是2015年原油价格大幅下跌造成卫星石化原料与产品库存双重减值.下游生产装置受到成本㊁区域㊁环保等多重因素的影响频繁检修或停产,卫星石化公司经历了创立以来的首次亏损.为进一步发挥P D H安全阀 的功能,公司非公开发行募资建设年产30万吨聚丙烯项目,2015年11月平湖基地启动年产聚丙烯项目建设,提高自产丙烯的内部消化比例.丙烯与丙烷二者价格差距较大时,选择以销售丙烯为主;当两者价差缩小,则选择销售聚丙烯为主,可以充分调节原材料价格波动对公司经营状况的影响,强化产业协同㊁增强整体盈利稳定性,实现卫星石化从丙烯酸及酯的行业困境中突围.2016年卫星石化的经营状况同比2015年出现较大的增长.在行业逐渐启稳的背景下,丙烷脱氢装置按满负荷安排生产与检修作业计划,全年始终保持较高的开工负荷.市场认可度的提升及丙烯-丙烷价差的回升,丙烯产品获利能力逐步提高,毛利比同期增加8570.40万元,毛利率增长14.17%.卫星能源公司2016年实现盈利1.62亿元,经济效益良好,获取良好的投资回报.2016年10月卫星石化公司完成30万吨聚丙烯装置建设并产出合格产品,P D H二期与技术方签订协议并开工建设.卫星石化公司上游石化产业基础日趋巩固,形成了以丙烷为原料到丙烯酸,并深加工成为高分子材料的特色产业链,实现了上下游装置集中,原料㊁产品全部管道输送的布局,装置内能源循环利用,成本最低.C3全产业链优势突出,综合竞争力逐年增强.(三)宁波海越丙烷脱氢装置宁波海越新材料有限公司由浙江海越股份有限公司(控股)㊁宁波银商投资有限公司㊁宁波万华石化投资有限公司共同出资组建,负责实施包括60万吨/年丙烷脱氢装置在内的138万吨/年丙烷和混合碳四利用项目.一期投资80亿元,于2014年9月2日产出合格丙烯产品.该装置采用A B B L u mm u s的C a t o f i n工艺和高效的P S+H GM催化剂,具有丙烷转换率高㊁丙烯选择性好㊁原料适应性强及装置在线率高等优点.产品丙烯直接通过码头和陆路外销至下游企业.2014年,宁波海越丙烷脱氢装置投料试车后,装置稳定性较差,一直未正式投产.2015年5月丙烷脱氢装置通过考核和标定转入正式生产.装置的生产能力㊁工艺指标㊁产品质量等主要标定结果均优于专利商的设计保证值,实际运行情况均达预期效果.但是2015年初,国际原油继2014年后继续快速下跌,丙烷脱氢装置负荷较低,且开停工频繁,导致单位能耗及生产成本上扬.进入9月份后,丙烯价格下滑40%左右,P D H装置运行时间和运行负荷大幅降低,开始发生亏损.2016年度石化行业景气度有所提高,宁波海越的装置利用率上升,销售收入大幅增加.全年丙烯营业利润较上年增长679%,大幅减亏.公司仍处在主业转型后的基础巩固阶段,面临丙烷原料长约和人民币贬值的压力,成本居高不下,经济效益受到影响.宁波海越丙烷脱氢装置原料为进口丙烷,年进口量在80万吨左右.公司提前与国外丙烷供应商签订了长期丙烷供应协议,2016年全年丙烷进口长约均价为452美元/吨,而同期丙烷现货均价为333美元/吨.长约和现货价格长期倒挂,导致丙烯的生产成本高于同类装置.针对价差对P D H装置经济效益的严重影响,宁波海越采取调整计价方式或到货周期,追加现货采购,拓展丙烷贸易渠道等措施降低原料成本.目前宁波海越的138万吨/年丙烷和混合碳四利用项目只建设完成一期工程,但是产品受单一㊁链条短,且产品储罐库容有限的影响,在产品价格大幅向下波动时,抗风险能力较差.因此,海越股份公司拟适时启动二期项目建设,扩建产品库容,在碳三碳四深加工产业链延伸发展,增加抗波动能力,不断提升企业竞争力,打造持续成长的生产清洁能源产品和化工新材料的新型石化企业.三㊁结语根据对各丙烷脱氢装置运营状况的分析可知:(1)丙烷与丙烯的价差决定了P D H装置的运营成本,掌握原材料来源㊁保障原材料采购的公司盈利能力更强;(2)以P D H装置为龙头构建产业链上下游一体化的公司抗风险能力更强,利润率更高;(3)具有石化产业背景的公司生产管理水平高,装置稳定性好,投资回报较快;(4)各公司2016业绩表现亮眼,2017上半年利润水平提升,纷纷加速丙烷脱氢二期工程的投建,亦吸引了社会资金上马新的P D H项目,可能存在潜在的经营风险和营利的不确定性.参考文献:[1]雷燕湘.世界丙烯及其衍生物发展现状与趋势[J].当代石油石化,2007,(04).[2]周一峰.D H能源股份有限公司发展战略研究[D].南京:南京理工大学,2014.[3]周保国.丙烷脱氢制丙烯技术的工业化应用[J].乙烯工业,2011,(02).D o m e s t i cD e v e l o p m e n t S t a t u s o fP r o p a n eD e h y d r o g e n a t i o nD e v i c e sG U O M e n g-y a n g,Y U NZ e-y o n g(T i a n j i nB o h a iV o c a t i o n a lT e c h n o l o g y C o l l e g e,T i a n j i n,300402)A b s t r a c t:F o r t h e d e v e l o p m e n t o f d o m e s t i c p r o p a n e d e h y d r o g e n a t i o nd e v i c e s,t h e r e a r e12s e t s o f d e v i c e s i no p e r a t i o n t i l l t h e e n do f2017,w i t h t o t a l p r o d u c t i o n c a p a b i l i t y:5.1m i l l i o n t o n s p r o p y l e n e.T h e s t a t u s o f o p e r a t i o n s t a t u s i n c l u d i n g T i a n j i nB o h a iC h e m i c a l,S a t e l l i t e P e t r o c h e m i c a l,H a i y u e s h a r e s a n d s o o na r e c o m p a r e d a n d a n a l y z e dh e r e i n a n d i n d i c a t e d t h a t t h e c o m p a n i e s c o n t r o l t h e s o u r c e s o fm aGt e r i a l s a n d f o r m e d i n t e g r a t e dc o m p a n y i n c l u d i n g u p s t r e a ma n dd o w n s t r e a mi n d u s t r i a l c h a i nh a v em o r e p o w e r f u l c a p a b i l i t y a g a i n s t r i s k sw i t hb i g p r o f i t a b i l i t y.H o w e v e r,t o om a n y n e wPD H p r o j e c t sm a y l e a d t o p o t e n t i a l o p e r a t i o n r i s k a n du n c e r t a i n t y o f p r o f i t.K e y w o r d s:P r o p a n eD e h y d r o g e n a t i o n;c o n s t r u c t i o no f d e v i c e s;o p e r a t i o no f d e v i c e s。
丙烷脱氢技术与应用研究
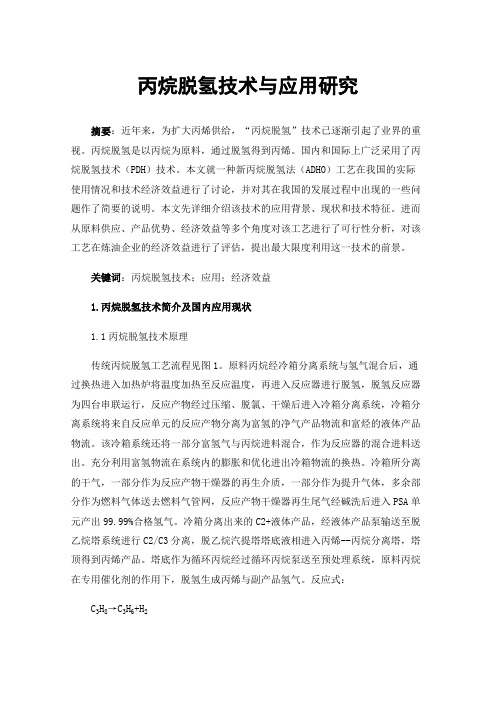
丙烷脱氢技术与应用研究摘要:近年来,为扩大丙烯供给,“丙烷脱氢”技术已逐渐引起了业界的重视。
丙烷脱氢是以丙烷为原料,通过脱氢得到丙烯。
国内和国际上广泛采用了丙烷脱氢技术(PDH)技术。
本文就一种新丙烷脱氢法(ADHO)工艺在我国的实际使用情况和技术经济效益进行了讨论,并对其在我国的发展过程中出现的一些问题作了简要的说明。
本文先详细介绍该技术的应用背景、现状和技术特征。
进而从原料供应、产品优势、经济效益等多个角度对该工艺进行了可行性分析,对该工艺在炼油企业的经济效益进行了评估,提出最大限度利用这一技术的前景。
关键词:丙烷脱氢技术;应用;经济效益1.丙烷脱氢技术简介及国内应用现状1.1丙烷脱氢技术原理传统丙烷脱氢工艺流程见图1。
原料丙烷经冷箱分离系统与氢气混合后,通过换热进入加热炉将温度加热至反应温度,再进入反应器进行脱氢,脱氢反应器为四台串联运行,反应产物经过压缩、脱氯、干燥后进入冷箱分离系统,冷箱分离系统将来自反应单元的反应产物分离为富氢的净气产品物流和富烃的液体产品物流。
该冷箱系统还将一部分富氢气与丙烷进料混合,作为反应器的混合进料送出。
充分利用富氢物流在系统内的膨胀和优化进出冷箱物流的换热。
冷箱所分离的干气,一部分作为反应产物干燥器的再生介质,一部分作为提升气体,多余部分作为燃料气体送去燃料气管网,反应产物干燥器再生尾气经碱洗后进入PSA单元产出99.99%合格氢气。
冷箱分离出来的C2+液体产品,经液体产品泵输送至脱乙烷塔系统进行C2/C3分离,脱乙烷汽提塔塔底液相进入丙烯--丙烷分离塔,塔顶得到丙烯产品。
塔底作为循环丙烷经过循环丙烷泵送至预处理系统,原料丙烷在专用催化剂的作用下,脱氢生成丙烯与副产品氢气。
反应式:C3H8→C3H6+H2ΔH=+124.3kJmol-1该反应为强吸热过程,也是平衡反应,所以,提高温度和降低压力有利于脱氢反应地进行,从而获得较高的丙烷转化率,但是过高的反应温度导致结焦问题加剧。
丙烷脱氢制丙烯项目的技术经济对比分析
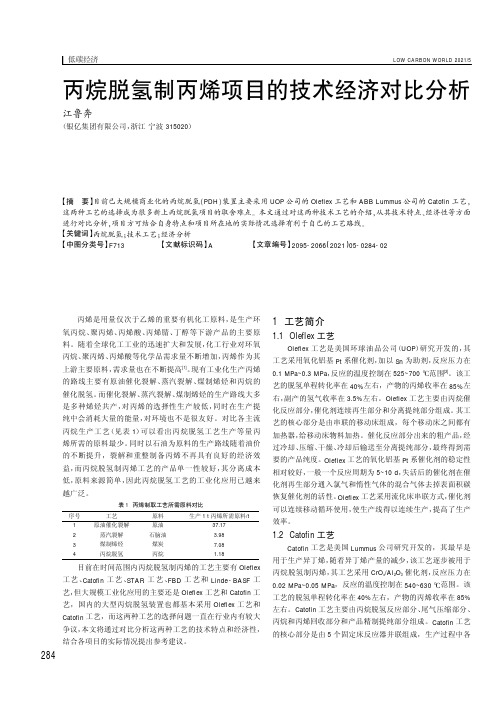
丙烷脱氢制丙烯项目的技术经济对比分析江鲁奔(银亿集团有限公司,浙江宁波315020)【摘要】目前已大规模商业化的丙烷脱氢(PDH)装置主要采用UOP公司的Oleflex工艺和ABB Lummus公司的Catofin工艺,这两种工艺的选择成为很多新上丙烷脱氢项目的取舍难点。
本文通过对这两种技术工艺的介绍,从其技术特点、经济性等方面进行对比分析,项目方可结合自身特点和项目所在地的实际情况选择有利于自己的工艺路线。
【关键词】丙烷脱氢;技术工艺;经济分析【中图分类号】F713【文献标识码】A【文章编号】2095-2066(2021)05-0284-02丙烯是用量仅次于乙烯的重要有机化工原料,是生产环氧丙烷、聚丙烯、丙烯酸、丙烯腈、丁醇等下游产品的主要原料。
随着全球化工工业的迅速扩大和发展,化工行业对环氧丙烷、聚丙烯、丙烯酸等化学品需求量不断增加,丙烯作为其上游主要原料,需求量也在不断提高[1]。
现有工业化生产丙烯的路线主要有原油催化裂解、蒸汽裂解、煤制烯烃和丙烷的催化脱氢。
而催化裂解、蒸汽裂解、煤制烯烃的生产路线大多是多种烯烃共产,对丙烯的选择性生产较低,同时在生产提纯中会消耗大量的能量,对环境也不是很友好。
对比各主流丙烷生产工艺(见表1)可以看出丙烷脱氢工艺生产等量丙烯所需的原料最少。
同时以石油为原料的生产路线随着油价的不断提升,裂解和重整制备丙烯不再具有良好的经济效益,而丙烷脱氢制丙烯工艺的产品单一性较好,其分离成本低,原料来源简单,因此丙烷脱氢工艺的工业化应用已越来越广泛。
目前在时间范围内丙烷脱氢制丙烯的工艺主要有Oleflex 工艺、Catofin工艺、STAR工艺、FBD工艺和Linde-BASF工艺,但大规模工业化应用的主要还是Oleflex工艺和Catofin工艺,国内的大型丙烷脱氢装置也都基本采用Oleflex工艺和Catofin工艺,而这两种工艺的选择问题一直在行业内有较大争议,本文将通过对比分析这两种工艺的技术特点和经济性,结合各项目的实际情况提出参考建议。
Oleflex丙烷脱氢工艺技术工业应用的改进
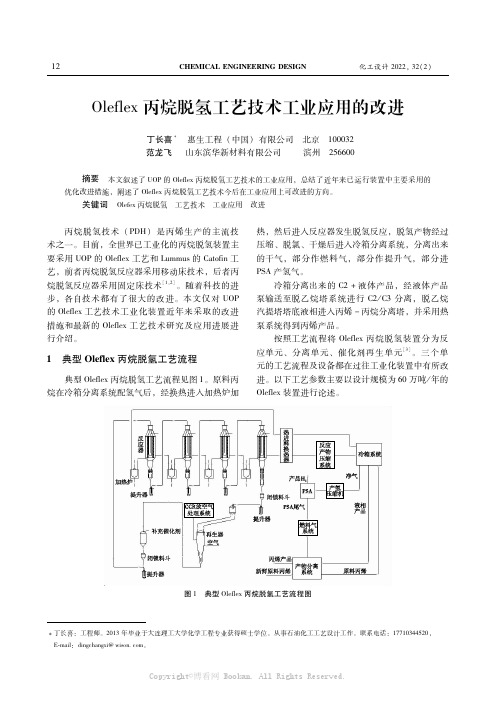
CHEMICALENGINEERINGDESIGN化工设计2022,32(2)Oleflex丙烷脱氢工艺技术工业应用的改进丁长喜 惠生工程(中国)有限公司 北京 100032 范龙飞 山东滨华新材料有限公司 滨州 256600 摘要 本文叙述了UOP的Oleflex丙烷脱氢工艺技术的工业应用,总结了近年来已运行装置中主要采用的优化改进措施,阐述了Oleflex丙烷脱氢工艺技术今后在工业应用上可改进的方向。
关键词 Olefex丙烷脱氢 工艺技术 工业应用 改进丁长喜:工程师。
2013年毕业于大连理工大学化学工程专业获得硕士学位。
从事石油化工工艺设计工作。
联系电话:17710344520,E mail:dingchangxi@wison com。
丙烷脱氢技术(PDH)是丙烯生产的主流技术之一。
目前,全世界已工业化的丙烷脱氢装置主要采用UOP的Oleflex工艺和Lummus的Catofin工艺,前者丙烷脱氢反应器采用移动床技术,后者丙烷脱氢反应器采用固定床技术[1,2]。
随着科技的进步,各自技术都有了很大的改进。
本文仅对UOP的Oleflex工艺技术工业化装置近年来采取的改进措施和最新的Oleflex工艺技术研究及应用进展进行介绍。
1 典型Oleflex丙烷脱氢工艺流程典型Oleflex丙烷脱氢工艺流程见图1。
原料丙烷在冷箱分离系统配氢气后,经换热进入加热炉加热,然后进入反应器发生脱氢反应,脱氢产物经过压缩、脱氯、干燥后进入冷箱分离系统,分离出来的干气,部分作燃料气,部分作提升气,部分进PSA产氢气。
冷箱分离出来的C2+液体产品,经液体产品泵输送至脱乙烷塔系统进行C2/C3分离,脱乙烷汽提塔塔底液相进入丙烯-丙烷分离塔,并采用热泵系统得到丙烯产品。
按照工艺流程将Oleflex丙烷脱氢装置分为反应单元、分离单元、催化剂再生单元[3]。
三个单元的工艺流程及设备都在过往工业化装置中有所改进。
以下工艺参数主要以设计规模为60万吨/年的Oleflex装置进行论述。
丙烷脱氢制丙烯技术进展

综述专论化工科技,2006,14(4):62~66SCIENCE &T ECHNO LOGY IN CHEM ICA L I NDU ST RY收稿日期:2006-03-15作者简介:苏建伟(1972-),男,河南镇平人,乌鲁木齐石油化工公司炼油厂工程师,主要从事催化重整、催化裂解、烃类的选择性氧化等方面的研究工作。
丙烷脱氢制丙烯技术进展苏建伟1,牛海宁2(1.乌鲁木齐石油化工公司炼油厂,新疆乌鲁木齐830019;2.抚顺市环境保护局信息中心,辽宁抚顺113006)摘 要:综述了丙烷脱氢制备丙烯各催化体系反应机理,探讨了丙烷脱氢制备丙烯工艺流程的进展和最新研究成果,在此基础上指出了该领域今后的发展方向。
关键词:丙烷;丙烯;脱氢中图分类号:T Q 221.21+2 文献标识码:A 文章编号:1008-0511(2006)04-0062-05丙烯是从石油中获得的无色可燃气态烃,大量用于制取树脂、纤维、弹性体以及其它化学产品,近年来世界丙烯需求增长率一直高于乙烯[1]。
2003年全球丙烯产量约为5760万t,大约67%的丙烯为乙烯裂解副产,其余部分为炼油厂催化裂化工艺和丙烷脱氢生产。
据Chem Sys -tems 分析,未来丙烯供应短缺还将加剧。
由于现有来源不敷需要,20世纪90年代开发的丙烷催化脱氢制丙烯新工艺已成为第三位的丙烯来源。
我国有着丰富的石油和天然气资源,其中含有大量的丙烷,如油田气中丙烷约占6%,液化石油气中约占60%,湿天然气中可达15%[2],炼厂气中也含有一定量的丙烷。
它们一般是作为燃料使用或者放空烧掉,资源浪费较大,采用催化脱氢的方法,能有效地利用现有资源使之转变为有用的烯烃。
丙烷脱氢制丙烯的关键在于研制高活性、高选择性和高稳定性的脱氢催化剂。
当前丙烷脱氢制丙烯的工艺主要有临氢脱氢、氧化脱氢两种。
1 丙烷临氢脱氢单纯从裂解工艺获得丙烯已不能满足市场对丙烯的需求,所以开发扩大丙烯来源的生产工艺近年成为热点。
年产50万吨丙烷脱氢制丙烯工艺设计
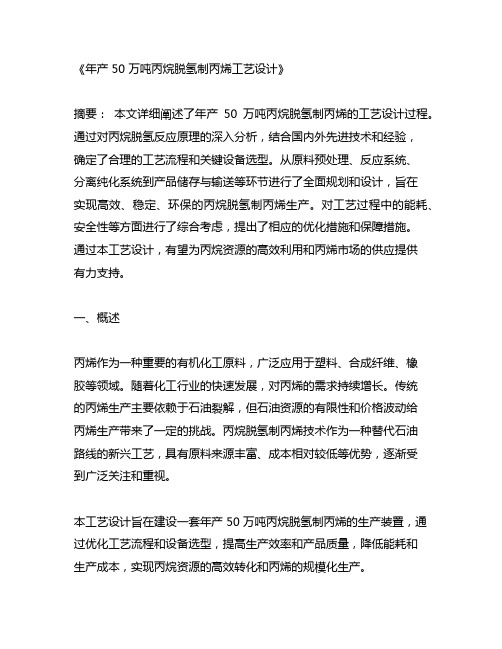
《年产 50 万吨丙烷脱氢制丙烯工艺设计》摘要:本文详细阐述了年产50 万吨丙烷脱氢制丙烯的工艺设计过程。
通过对丙烷脱氢反应原理的深入分析,结合国内外先进技术和经验,确定了合理的工艺流程和关键设备选型。
从原料预处理、反应系统、分离纯化系统到产品储存与输送等环节进行了全面规划和设计,旨在实现高效、稳定、环保的丙烷脱氢制丙烯生产。
对工艺过程中的能耗、安全性等方面进行了综合考虑,提出了相应的优化措施和保障措施。
通过本工艺设计,有望为丙烷资源的高效利用和丙烯市场的供应提供有力支持。
一、概述丙烯作为一种重要的有机化工原料,广泛应用于塑料、合成纤维、橡胶等领域。
随着化工行业的快速发展,对丙烯的需求持续增长。
传统的丙烯生产主要依赖于石油裂解,但石油资源的有限性和价格波动给丙烯生产带来了一定的挑战。
丙烷脱氢制丙烯技术作为一种替代石油路线的新兴工艺,具有原料来源丰富、成本相对较低等优势,逐渐受到广泛关注和重视。
本工艺设计旨在建设一套年产 50 万吨丙烷脱氢制丙烯的生产装置,通过优化工艺流程和设备选型,提高生产效率和产品质量,降低能耗和生产成本,实现丙烷资源的高效转化和丙烯的规模化生产。
二、工艺原理丙烷脱氢制丙烯的反应原理主要是丙烷在催化剂的作用下发生脱氢反应,生成丙烯和氢气。
反应方程式如下:C₃H₈ → C₃H₆ + H₂该反应是一个吸热反应,需要在高温、低压的条件下进行。
选择合适的催化剂是实现丙烷脱氢反应高效进行的关键。
目前,常用的催化剂主要有 Pt、Cr 等贵金属催化剂和非贵金属催化剂。
三、工艺流程设计(一)原料预处理系统原料丙烷首先经过压缩和冷却,去除其中的水分、杂质等,使其达到工艺要求的纯度和压力。
然后进入丙烷储罐进行储存,以便后续的连续稳定供应。
(二)反应系统反应系统采用固定床反应器,反应器内装填高效的催化剂。
丙烷和氢气在反应器中逆流接触,进行脱氢反应。
反应温度控制在适宜的范围内,通过加热炉和换热器等设备进行精确调控。
- 1、下载文档前请自行甄别文档内容的完整性,平台不提供额外的编辑、内容补充、找答案等附加服务。
- 2、"仅部分预览"的文档,不可在线预览部分如存在完整性等问题,可反馈申请退款(可完整预览的文档不适用该条件!)。
- 3、如文档侵犯您的权益,请联系客服反馈,我们会尽快为您处理(人工客服工作时间:9:00-18:30)。
混合烷烃脱氢装置原料比例调整丙烯塔热泵系统改造技术方案探讨摘要:文章以某石油化工有限公司25万吨/年混合烷烃脱氢装置改造为例,介绍了混合脱氢装置的工艺流程及技术特点,着重论述了当装置原料比例调整,适当降低碳四原料、最大化增加丙烷原料时,丙烯塔热泵系统所面临的瓶颈,并给出了相关的改造方案及建议,为今后同类装置的改造方案提供了借鉴。
关键词:混合烷烃脱氢;碳三;碳四;丙烷;丁烷;丙烯塔热泵;1.概述混合烷烃脱氢制烯烃技术近年来广受关注,是指有两种及以上烷烃在一套装置内同时进行脱氢反应,其可以根据需求,更改进料中不同种类烷烃的配比,生产不同的产品结构,从而更好的适应市场需求,达到经济效益的最大化。
其中,丙烷脱氢制丙烯,异丁烷脱氢制异丁烯是混合烷烃脱氢技术应用最广的两个领域[1]。
在国内,丙烯主要用于生产聚丙烯,占到了丙烯需求量的70%以上,近十年来,随着聚丙烯消费年均增长量达17.59%,丙烯供需缺口不断加大[2]。
异丁烯的醚化反应生产的甲基叔丁基醚(Methyl tert-butyl ether, MTBE),是国内常用的汽油添加剂,以改善汽油的冷启动特性、加速性能及辛烷值分布,然而因其具有一定的毒性,且可以与水融合,容易渗入土壤,污染地下水质,美国等一些国家和地区已经禁用了MTBE,国内对于MTBE的禁用也逐步提上了日程,这无论对于MTBE的出口,还是国内市场,都将产生很大的影响[3-5]。
烷烃脱氢工艺最早由美国UOP公司和英国ICI公司联合设计并进行工业化推广应用[6],目前国外已经实现工业化且比较成熟的工艺主要有:美国UOP公司的Oleflex工艺、Lummus公司的Catofin工艺、Phillips公司的Star工艺、意大利Snamprogetti与俄罗斯Yarsintez共同研发的FBD-4工艺以及德国Linde公司开发的Linde工艺[7]。
山东某石油化工有限公司25万吨/年混合烷烃脱氢装置采用美国UOP公司Oleflex混合烷烃脱氢专利技术,以丙烷、丁烷为原料生产聚合级丙烯和异丁烯产品,同时副产氢气等,异丁烯进一步在装置内生产MTBE产品。
近期由于C3、C4原料和产品市场发生较大变化,丙烯产品价格有明显优势,该公司提出希望在当前混合烷烃脱氢装置的基础上,调整进料比例,适当降低碳四原料,提高碳三进料比例,同时结合操作参数的调整进行优化,增加丙烯产量及节能降耗,以达到改善装置经济效益目的。
1.装置系统简介混合脱氢装置由碳三原料预处理、碳四原料预处理、混合烷烃脱氢反应、碳四异构化、产物分离、异丁烯醚化及公用工程等单元组成,其工艺流程如下图所示。
外购原料碳四依次经C4精制单元、氧化物脱除单元(ORU)、烯烃饱和单元(CSP)、异构化单元后,与经进料脱丙烷塔处理后的原料碳三和来自丙烷—丙烯塔的循环丙烷混合后进入冷箱系统,汽化并与循环氢混合后进入脱氢反应单元,从反应器出来的液体产品经反应产物压缩机压缩、脱氯、干燥、冷箱系统分离后送至SHP选择性加氢反应器进行选择加氢反应。
出SHP的液体产品依次送至脱乙烷塔、产物脱丙烷塔、丙烯塔。
产物脱丙烷塔塔底碳四送至醚化反应,异丁烯和甲醇合成生成精MTBE和粗MTBE。
丙烯塔顶聚合级丙烯作为产品出装置。
其中脱氢反应单元采用的是UOP的Oleflex工艺,进料烷烃(主要是丙烷和异丁烷)在脱氢反应单元内的催化剂作用下发生催化脱氢反应,生产丙烯、异丁烯以及副产物氢气。
单元内设置了三台固定床反应器,反应器间设置加热炉为各级反应器的进料加热。
碳四异构化单元中设置异构化反应器,来自罐区的丁烷经过氧化物脱除、CSP加氢饱和后,进入至异构化反应器,在异构化反应器内,进料中的正丁烷在催化剂作用下发生异构化反应,生成异丁烷,反应转化率约为60%,生成的异丁烷与经原料预处理后的丙烷组成联合进料,通过冷箱系统换热后输送至脱氢反应单元。
冷箱系统位于脱氢反应单元的下游,其进料分为两股,一股来自于脱氢反应单元的出料—脱氢产物,另一股来自于丙烯-丙烷塔的塔釜产物—循环丙烷。
脱氢产物中主要有丙烯、异丁烯以及大量的副产物氢气,为了避免加重下游装置的负荷,循环物料过多等问题,需在冷箱系统中将副产物氢气进行深冷分离。
冷箱系统中设置了两级透平机,为其提供深冷环境,设置了低、中、高位分离罐和级间换热器,达到液化的烃类和氢气分离效果。
冷箱系统分离出来的氢气一部分循环返回至脱氢反应单元,起到控制反应器床层压力以及保护催化剂床层的左右,一部分输送至界区外进行氢气提纯。
产物分离单元包括脱乙烷塔汽提段、精馏段、产物脱丙烷塔、丙烯-丙烷塔三台精馏塔和一台热泵精馏塔组成,主要作用是将C3、C4分离,丙烷和丙烯分离。
产物脱丙烷塔塔釜的C4及以上组分进入后续的异丁烯醚化单元,丙烯-丙烷塔的塔顶产品丙烯纯度达到聚合级,作为产品外送,塔釜的丙烷则循环回脱氢反应单元。
异丁烯醚化单元即MTBE精制单元,其进料来自产物分离单元中的产物脱丙烷塔的塔釜C4及以上组分,其中的异丁烯和来自罐区的甲醇混合后,进入醚化反应器,在催化剂的作用下进行催化醚化反应,生成MTBE粗产品,MTBE粗产品经脱轻塔、脱重塔进一步精制,脱除轻组分和重组分后,得到MTBE精制产品。
混合脱氢装置工艺流程长、原料复杂、循环物流多、单元设备品种多,原料比例及产品比例的调整,各个单元对整个装置生产能力的制约不尽相同,其中又以丙烯塔热泵系统对其的影响最为显著,本文针对这一情况,对丙烯塔热泵系统着重进行了分析和研究,并给出了相关的改造方案和建议。
1.方案分析及研究3.1 丙烯塔进料浓度影响分析根据企业提供的生产运行数据,通过详细模拟计算,得出的模拟结果与实际运行数据吻合较好。
依据模拟计算结果,针对丙烯进料浓度变化和系统裕量进行了针对性的分析。
其中丙烷—丙烯分离塔设计值及相关生产运行数据如下表所示:表1 丙烷—丙烯分离塔设计值及相关生产运行数据维持丙烯塔进料量不变,调整进料中丙烯丙烷比例,分析不同丙烯浓度对设计的影响。
通过图1气液相负荷与进料组成关系图可以看出,将丙烯浓度自23%逐步升高至30%时,在保持各进料浓度下塔顶、塔底产品质量合格的情况下,通过模拟计算得出,随着丙烯浓度的升高,丙烯塔液相负荷保持不变,气相负荷由12410kmol/h提高到12510kmol/h,提高幅度不到1%。
通过图2压缩机功率与进料组成关系图可以看出,随着丙烯进料浓度的增加,而压缩机功率仅仅由5920KW 增加到5980KW,几乎没有增加。
通过图3回流比与进料组成关系图中可以看出,回流比与丙烯进料组成是成反相关,随着进料组成的升高,回流比逐渐降低,当进料组成由23%升高到30%时,回流比则由32.5降低到25,降低了23%。
通过图4丙烯产量与进料组成关系图可以看出,随着丙烯进料组成的提高,丙烯产量也随之提高,自376.97kmol/h提高至484.18kmol/h,增加28.4%。
以上说明,在热泵压缩机总功率保持不变、总进料流量不变的情况下,通过提高进料的丙烯浓度,可以增加丙烯产量,而丙烯塔气液相负荷、塔回流量、压缩机功率几乎都没有改变,回流比反而降低。
同时根据测算,当进料浓度升高至26%以内,热泵压缩机、丙烷泵和丙烯丙烷回流泵均可满足操作,进料浓度升高至30%时,丙烷泵仍能满足操作。
图1 气液相负荷与进料组成关系图 2 压缩机功率与进料组成关系图3 回流比与进料组成关系图4 丙烯产量与进料组成关系3.2 丙烯产品纯度调整影响丙烯塔热泵系统由丙烯精馏塔系和丙烯热泵压缩机构成,是脱氢装置产出丙烯产品和脱氢反应器循环进料的单元,也是非常重要的单元。
当前该企业对丙烷丙烯分离塔控制指标为:丙烯产品中丙烯含量≥99.7%mol、塔釜丙烷中丙烯含量≤1.5%mol。
而国家标准对聚合级丙烯产品的纯度要求是99.5%mol,非99.7%,如果用99.7%mol的产品当作99.5%纯度的价格进行销售,无疑是不经济也是不必要的,控制产品纯度恰好达到要求是最为经济合算的策略。
当前实际操作中丙烯浓度高于控制指标较多,如果使丙烯产品质量刚好合规,通过适当降低回流量便可实现,结果是节省部分压缩机功率,降低能耗,也为丙烯产能的提高留出了余量。
通过进行模拟计算得出,将塔顶丙烯浓度自99.73%下调至99.56%mol、塔底丙烷浓度自99.24%下降至99.19%后,丙烯塔的回流比下降8%,而压缩机总功率降低6%,则一年可节省6%的蒸汽用量,其所获得的节能效益还是很客观的。
如保持压缩机目前运行功率不变、进料浓度不变,则丙烯塔的进料量有6%的提升幅度,使得丙烯产品仍可以满足99.5%的纯度要求。
3.3 热泵压缩机组影响分析丙烯塔热泵循环就是逆向卡诺循环,它将回收塔顶流体的低温热通过压缩机做功,使其温位升高作为塔底热源使用,从而节约能源和操作费用。
丙烯热泵系统主要由压缩机、冷凝器、节流阀和蒸发器四部分组成,其中压缩机是热泵系统中的关键设备,其负荷的大小直接影响着丙烯-丙烷塔的产能,丙烯的产量。
本装置热泵压缩机额定功率为6710 KW,额定转数为5200 r/min,根据现场操作反馈,当前运行实际转速仅为4950 r/min,其距额定转速还有一些空间,说明还具有一定的负荷提升余量,然而由于此汽轮机形式采用的是背压式,蒸汽透平背压的弹性不够,因此缺少进一步提升转速的条件,成为了提升产能的制约因素。
针对此种情况,对本热泵压缩机进行增容改造,尽可能的提升其流量和负荷,通过与压缩机厂家沟通,提出以下三种改造方案:1)只更换转子,不更换驱动机组。
此种方案改造量最小,然而由于受限于驱动机功率,在不更换驱动机组的情况下,压缩机入口流量仅能提高约为4%;2)既更换转子,又更换驱动机组。
此种方案可以利旧基础及底座,利旧干气密封本体,利旧支撑及推力轴承,然而由于受限于马赫数及机壳宽度,压缩机入口流量能提高约为7%;3)更换驱动机组及压缩机本体,增加一级叶轮,由原背压式汽轮机改为凝汽式汽轮机,压缩机入口流量可以提高30%,功率由6710 KW提高至8998 KW,转速由5203 r/min降为4476 r/min。
此种改造方案,由于凝汽式汽轮机与背压式汽轮机构造差距较大,改为凝汽式汽轮机之后,需要对其基础进行重新核算和局部改造,同时也需要对底座、联轴器、联轴器护罩等部位进行更新。
综合考虑以上三种改造方案,建议在热泵压缩机透平背压管网处增设蒸汽冷凝器,或将原背压式汽轮机透平更换为全凝或半凝汽式透平,改善蒸汽透平背压操作弹性,提升压缩机转速,从而增加热泵压缩机的入口流量和负荷,提高装置的产能。
3.4 投入产出变化由上表可以看出,原料调整后与原设计相比,由于进料组成变化,C3原料增多,C4原料减少,甲醇用量减少,导致了总进料年投入费用降低了2047万元。