潜在失效模式及后果分析程序
潜在失效模式及后果分析程序(PFMEA).
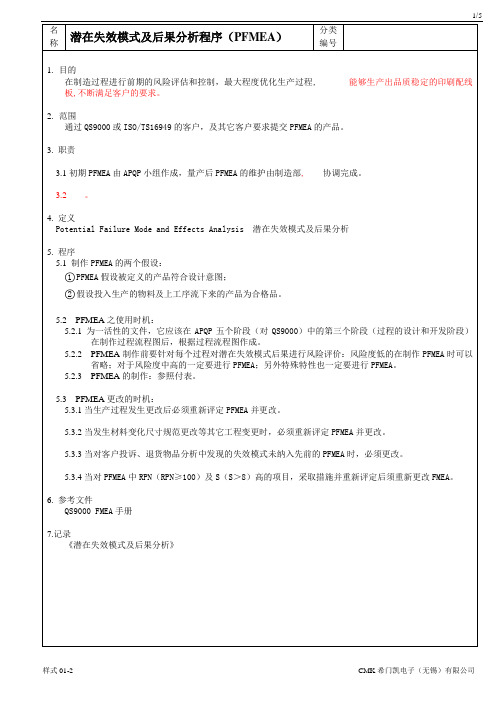
样式 01-2
CMK 希门凯电子(无锡)有限公司
将重要特性转化成潜在不良模式
失效模式是对该特定的过程/产品特性不合理由的详细 描述
识别其潜在的失效后果
是
失效后果以不符合产品功能或过程作业功能要求的方式 描述,如果该失效涉及不符合政府法规的潜在因素或对 产品相关操作人员安全的潜在影响则必须加以指出.
是否有其它的 潜在失效模式 检查是否有遗漏了其它的潜在失效模式.
否
判定严重度
按照严重度评分标准,评估严重度.
分级
按照严重度分级基准分类.
确认潜在不良原因
原因必须以某种可以改正或控制的方式加以描述, 避免模 棱两可的语句.
判定频度数
按照频度数评分标准,评估频度数.
A
样式 01-2
CMK 希门凯电子(无锡)有限公司
3/5
名 称
潜在失效模式及后果分析程序( 潜在失效模式及后果分析程序(PFMEA) )
高:现有控制在后道工序或中间检查中(在制造过程完成之前)几乎肯定能发现存在的缺陷。 3-4 现有控制在后道工序或中间检查中(在制造过程完成之前)几乎肯定能发现存在的缺陷。 - 非常高/早期:现有控制几乎是在制造过程中, 非常高 早期:现有控制几乎是在制造过程中,在产品移动到下一工序或别的部门前肯定能发 早期 1-2 - 现缺陷的存在。 现缺陷的存在。
追踪
样式 01-2
CMK 希门凯电子(无锡)有限公司
4/5
名 称
潜在失效模式及后果分析程序( 潜在失效模式及后果分析程序(PFMEA) )
分类 编号
付表-2
严重度、频度、探测度定级表
1、严重度定级标准 、 失效后果的严重度
定级
非常高:潜在的失效模式可能会导致生产现场失效( ) 或构成安全性危害, ,或构成安全性危害 非常高:潜在的失效模式可能会导致生产现场失效(9) 或构成安全性危害,或不符合某项 , 9-10 - 政府法规的要求 高:由于失效的性质导致顾客高度不满意。可能会导致后续产品加工过程的严重中断或导致 由于失效的性质导致顾客高度不满意。 产品不能满足其销售规范。会导致顾客投诉和产品退货。在顾客进行最终产品试验过程中, - 产品不能满足其销售规范。会导致顾客投诉和产品退货。在顾客进行最终产品试验过程中, 7-8 该种失效有可能被查出来。 该种失效有可能被查出来。 中等:失效会引起顾客有些不满意且可能导致顾客投诉。为适应该种材料, 中等:失效会引起顾客有些不满意且可能导致顾客投诉。为适应该种材料,顾客可能需要对 可能导致顾客投诉 5-6 - 他们的过程进行修改或调整。 他们的过程进行修改或调整。 低:失效只会引起外观的轻微不良或顾客轻微的恼怒。顾客将注意到产品或产品加工只有一 失效只会引起外观的轻微不良或顾客轻微的恼怒。 3-4 - 些轻微劣化或不便。 些轻微劣化或不便。 微弱:顾客合理地认为该失效的微弱性对产品或其加工不会引起任何实质性后果。 微弱:顾客合理地认为该失效的微弱性对产品或其加工不会引起任何实质性后果。顾客甚至 1-2 - 可能注意不到这种失效。 可能注意不到这种失效。 2、频度定级标准 、 失效的频度 非常高:失效几乎总是不可避免的。需要开发其他过程步骤以解决失效问题。 非常高:失效几乎总是不可避免的。需要开发其他过程步骤以解决失效问题。 高:类似的过程曾有过重复失效的发生。该过程不处于统计受控状态。 类似的过程曾有过重复失效的发生。该过程不处于统计受控状态。 中等:类似的过程曾经有过偶尔失效,但比例不大。过程是处于统计受控状态。 类似的过程曾经有过偶尔失效,但比例不大。过程是处于统计受控状态。 非常低:类似的过程只有个别或极个别的失效发生。 非常低:类似的过程只有个别或极个别的失效发生。 极低:不太可能有失效发生。几乎同样的过程从未发生有关的失效。 极低:不太可能有失效发生。几乎同样的过程从未发生有关的失效。过程处于统计受控状态 或已采取了防错措施。 或已采取了防错措施。 3、探测度定级标准 、 缺陷被发现的可能性及其在过程中的位置 绝对的不确定:现有控制不会或不能发现存在的缺陷。 绝对的不确定:现有控制不会或不能发现存在的缺陷。 定级 9-10 - 定级 9-10 - 7-8 - 5-6 - 3-4 - 1-2 -
潜在的失效模式与后果分析(FMEA)精选全文
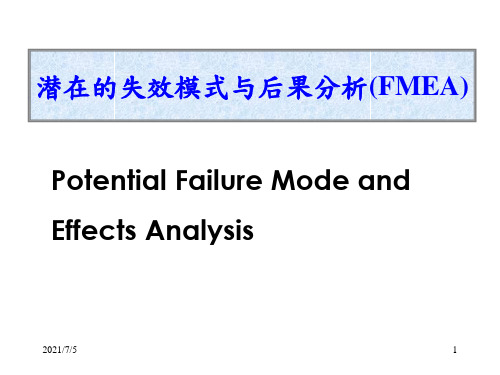
太短功能 :支撑架总成生产方法 (焊接)潜在失效模式 :
设计目标骑乘至少3000小时
不需保养, 及10000
小时的骑乘寿命适应99.5%男性成人
舒适的骑乘其它功能 :容易骑用潜在失效模式驾驶困难踩踏困难功能 :提供可靠的交通潜在失效模式链条经常损坏轮胎经常需要保养功能:提供舒适的交通潜在失效模式座椅位置令骑乘者
2021/7/5
19
FMEA的实施
FMA(失效模式分析)
FMEA(潜在失效模式及后果分析)
失效已经产生
失效还未产生,可能发生,但不是一定要发生
核心:纠正
核心:预防
诊断已知的失效
评估风险和潜在失效模式的影响开始于产品设计和工艺开发活动之前
指引开发和生产
指引贯穿整个产品周期
FMA:Failure Mode Analysis
2021/7/5
18
FMEA的实施
●及时性●它是一个事前的行为,而不是一个事后的行为。●事先花时间很好地进行综合的FMEA分析,能够容易、低成本地对产品或过程进行修改,从而减轻事后修改的危机。●FMEA能够减少或消除因修改而带来更大的机会。适当地应用FMEA是一个相互作用的过程,永无止境。● FMEA是一个动态的文件。● FMA是一种事后行为,是对产品/过程已经发生的失效 模式分析其产生的原因,评估其后果采取纠正措施的一种活动。●类似项目的FMA是FMEA的重要的输入参考资料。
2021/7/5
22
良好FMEA之具备事项
FMEA是早期预防失效及错误发生的最重要且最有效的方法之一。一个良好的FMEA必须具备: 1. 确认已知及潜在失效模式 2. 确认每一失效模式的后果和原因 3. 依据风险顺序(严重度、频度及探测度)采取措施 4. 提供问题改正行动及跟催
10FMEA潜在失效模式及后果分析程序
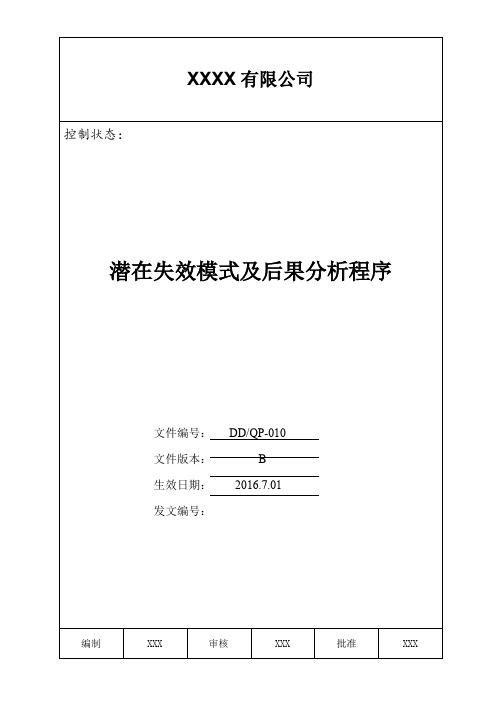
潜在失效模式及后果分析流程图1. 目的认可并评价在设计和制造过程中潜在的失效模式,分析其后果,评估其风险,从而预先采取措施,消除或减少失效发生的机会,有效地提高产品质量和可靠性,达到顾客满意。
2. 适用范围适用于新的或更改后的产品/过程的策划设计阶段,对构成产品的各子系统、零部件,对构成过程和服务的各个过程的潜在失效模式及后果进行分析的活动。
3. 术语和定义3.1 DFMEA:设计潜在失效模式和后果分析,是指产品设计人员采用的一门分析技术,在最大范围内保证充分地考虑失效模式及其相关的后果起因/机理,DFMEA以最严密的形式总结了工程技术人员进行产品设计时的指导思想。
3.2 PFMEA:过程潜在失效模式和后果分析,主要是由负责制造的工程师/多方论证小组采用的一种分析技术,用来保证在可能的范围内已充分地考虑到并指明潜在失效模式及其相关的起因或机理。
4. 职责4.1技术部职责4.1.1 组织由负责过程设计、制造、装配、售后服务、质量及可靠性等方面的专家成立多方论证小组。
4.1.2负责计算风险顺序数RPN,并编制《风险顺序数序列表》。
4.1.3负责对FMEA的输出整理归档。
4.2 多方论证小组职责4.2.1负责收集与PFMEA相关数据资料。
4.2.2负责进行PFMEA分析、评审、效果跟踪和确认。
5. 工作程序5.1 DFMEA5.1.1 由技术部组织设计人员、工艺人员、销售部、质量部、采购部相关人员成立多方论证小组,报管理者代表批准。
5.1.2多方论证小组根据设计任务书的设计要求和预期的工艺流程,对设计方案进行分析评审,分析产品在设计结构中的每一个关键部位、结构的风险,并确定需执行DFMEA的高风险的零部件/子系统/系统。
5.1.3 多方论证小组对确定为高风险的部位、结构进行DFMEA,并记录于表格《潜在的失效模式及后果分析(DFMEA)》,当顾客或公司要求对中等风险的部位、结构进行DFMEA 时,按确定的步骤实施。
FMEA潜在失效模式及后果分析管理程序
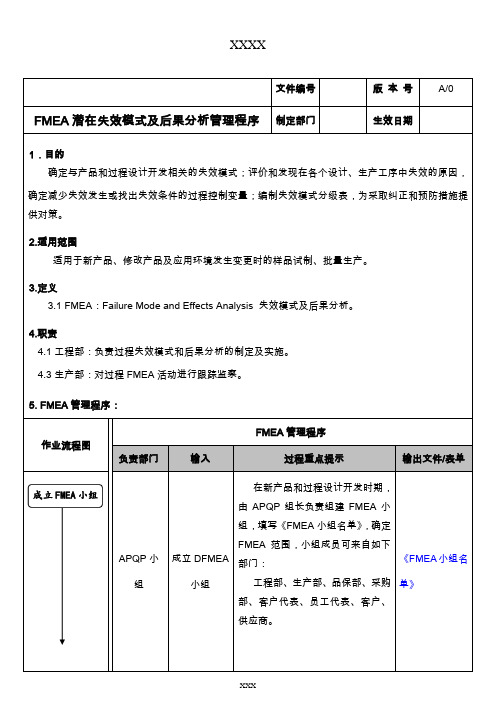
XXX
XXXX
文件编号
版本号
A/0
FMEA 潜在失效模式及后果分析管理程序 制定部门
生效日期
FMEA 分析
FMEA 分析小组应当建立一个 过程流程图,识别每步操作相关的 产品/过程特性,结合 DFMEA,图 样和设计记录,内外部不符合历史, 质量与可靠性历史等信息来源制定 《FMEA》。
PFMEA 分析
评定准则可参考 PFMEA 严重度 评定准则表:
FMEA 严重度评定准则表参照《FMEA 管理手册》
FMEA 分析
14.分类:作为识别与确定特殊 特性的重要工具,小组应在PFMEA 分析中识别并确定过程特殊特性, 并以《APQP管理程序》规定的符号
XXX
XXXX
文件编号
FMEA 潜在失效模式及后果分析管理程序 制定部门
XXX
XXXX
文件编号
版本号
A/0
FMEA 潜在失效模式及后果分析管理程序 制定部门
生效日期
描述失效的影响,尽可能采用表 达顾客关注和感受的词汇。如:操 作者眼睛受伤害,零件破损将机器 损坏,外观不良,无法装配,等等。 对最终顾客的影响应使用与产品或 系统的性能有关的术语来描述,例 如噪声、振动、工作不正常、停止 工作、工作不稳定、操作力过大、 异味、性能衰退、观外不良、褪色, 等等。
式是指:过程不能达到过程功能要 求或过程设计意图的问题的表现形 式。一般情况下,它是指按规定的 操作规范进行操作时的潜在的失效 问题,但由于过程设计中对技术与 能力考虑不足而造成的失效,或容 易产生误操作的问题也是潜在失效 模式考虑的范围。潜在失效模式应 当用专业的技术术语描述,不必描 述成顾客能够注意到的现象。在进 行 FMEA 时应当假定即将接收的零 件/材料是正确的。
质量管理培训手册潜在失效模式及后果分析FMEA

开始
图例
活动
内部接口明确
开始
活动
结束 过程
判断
活动 判断
记录 人流物流
信息流
10.01.2024
结束
程序
目标明确吗 定义过程或活动了吗 过程的输入是什么 职责明确了吗 使用哪些控制方法 配置了哪些资源
输出是什么
记录
判据的标准和方法
记录
怎样证明输出达到目标 并且可以持续提高
用文字把上面这些问题的 做法按规定的格式写下来
10.01.2024
34
控制计划方法论
控制计划
Control Plan
控制计划的制定和实施可以统一策划 小组成员的行动
控制计划的制定可以提高策划小组成 员发现问题;分析问题;处理问题的能力
控制计划是策划小组与其他项目策划 小组交流的一种渠道
10.01.2024
35
控制计划方法论
控制计划
Control Plan
这就是
程序文件 作业指导 29
把取得的成果规范化 形成标准化合适的管 理文件成为大家共同 遵守的法则保持成果
10.01.2024
30
控制计划
Control Plan
控制计划 Control Plan
среда, 10 января 2024 г.
10.01.2024
31
控制计划方法论
控制计划
Control Plan
26
9 将流程图转化为程序图
输入
流程设计和流程图
Process Design and Process Flow Chart
开始 过程 活动 判断 记录
输出
10.01.2024
潜在失效模式后果分析FMEA控制程序
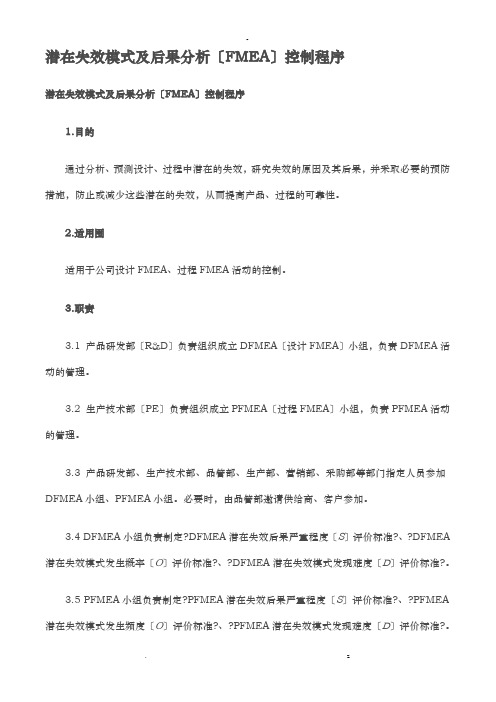
潜在失效模式及后果分析〔FMEA〕控制程序潜在失效模式及后果分析〔FMEA〕控制程序1.目的通过分析、预测设计、过程中潜在的失效,研究失效的原因及其后果,并采取必要的预防措施,防止或减少这些潜在的失效,从而提高产品、过程的可靠性。
2.适用围适用于公司设计FMEA、过程FMEA活动的控制。
3.职责3.1 产品研发部〔R&D〕负责组织成立DFMEA〔设计FMEA〕小组,负责DFMEA活动的管理。
3.2 生产技术部〔PE〕负责组织成立PFMEA〔过程FMEA〕小组,负责PFMEA活动的管理。
3.3 产品研发部、生产技术部、品管部、生产部、营销部、采购部等部门指定人员参加DFMEA小组、PFMEA小组。
必要时,由品管部邀请供给商、客户参加。
3.4 DFMEA小组负责制定?DFMEA潜在失效后果严重程度〔S〕评价标准?、?DFMEA 潜在失效模式发生概率〔O〕评价标准?、?DFMEA潜在失效模式发现难度〔D〕评价标准?。
3.5 PFMEA小组负责制定?PFMEA潜在失效后果严重程度〔S〕评价标准?、?PFMEA 潜在失效模式发生频度〔O〕评价标准?、?PFMEA潜在失效模式发现难度〔D〕评价标准?。
4.工作程序4.1 设计FMEA的开发实施DFMEA实施的时机.1 按APQP的方案进展DFMEA。
.2 在出现以下情况时,DFMEA小组应在产品零件图纸设计之前进展DFMEA活动:① 开发新产品/产品更改;② 产品应用的环境发生变化;③ 材料或零部件发生变化。
DFMEA实施前的准备工作① 产品研发部〔R&D〕牵头成立DFMEA〔设计FMEA〕小组,生产技术部、品管部、生产部、营销部、采购部等部门指定人员参加DFMEA小组,必要时,由品管部邀请供给商、客户参加。
② 在DFMEA活动实施前,DFMEA小组应制定出?DFMEA潜在失效后果严重程度〔S〕评价标准?、?DFMEA潜在失效模式发生概率〔O〕评价标准?、?DFMEA潜在失效模式发现难度〔D〕评价标准?。
PFMEA程序文件

PFMEA程序文件一、目的PFMEA(过程潜在失效模式及后果分析)程序文件的制定旨在识别和评估产品制造或服务提供过程中潜在的失效模式及其可能产生的后果,确定能够消除或减少潜在失效发生机会的措施,以提高过程的质量和可靠性,预防缺陷的产生,并在产品或服务的开发过程中优化资源配置。
二、适用范围本程序适用于公司内所有新产品开发、现有产品改进以及生产过程变更时的过程潜在失效模式及后果分析。
三、职责分工1、项目团队负责组建 PFMEA 小组,并指定小组负责人。
2、 PFMEA 小组负责收集相关信息,进行过程潜在失效模式及后果分析。
3、设计、工艺、生产、质量等相关部门负责提供技术支持和数据资料。
4、管理层负责对 PFMEA 结果进行评审和批准。
四、工作程序1、组建 PFMEA 小组项目团队根据项目需求,从设计、工艺、生产、质量、采购等相关部门选取具备专业知识和经验的人员组成 PFMEA 小组。
明确小组负责人的职责和权限,确保小组工作的顺利开展。
2、确定分析对象和范围PFMEA 小组根据项目目标和产品特点,确定需要进行潜在失效模式及后果分析的过程。
明确分析的范围,包括过程的起点和终点,以及涉及的工序和操作。
3、收集相关信息小组收集与分析对象相关的技术文件、图纸、规范、以往的故障数据、类似产品的 PFMEA 报告等信息。
与相关部门和人员进行沟通,了解过程的实际运行情况和存在的问题。
4、识别潜在失效模式小组成员运用头脑风暴法,对每个过程步骤可能出现的失效模式进行讨论和识别。
失效模式应具体、清晰地描述,例如“零件尺寸超差”、“焊接强度不足”等。
5、分析潜在失效后果针对每个识别出的失效模式,分析其可能对产品性能、功能、安全性、客户满意度等方面产生的后果。
后果的描述应包括对内部和外部客户的影响,如“导致产品无法装配”、“引起客户投诉”等。
6、评估严重度(S)根据失效后果的严重程度,使用既定的评分标准对严重度进行评估。
严重度评分通常为 1 到 10 分,10 分为最严重。
潜在失效模式及后果分析管理程序
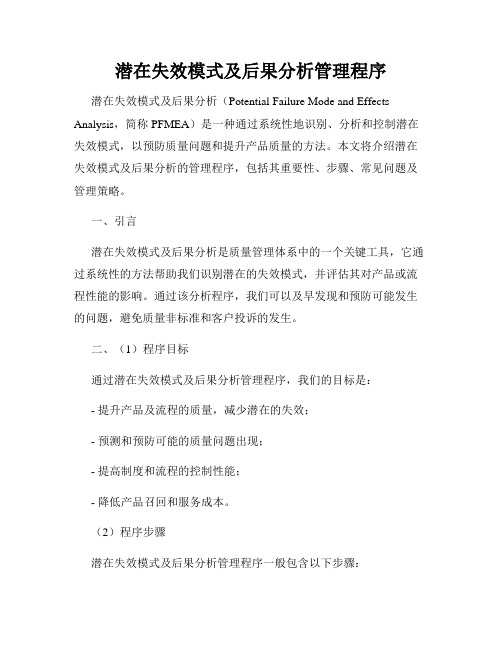
潜在失效模式及后果分析管理程序潜在失效模式及后果分析(Potential Failure Mode and Effects Analysis,简称PFMEA)是一种通过系统性地识别、分析和控制潜在失效模式,以预防质量问题和提升产品质量的方法。
本文将介绍潜在失效模式及后果分析的管理程序,包括其重要性、步骤、常见问题及管理策略。
一、引言潜在失效模式及后果分析是质量管理体系中的一个关键工具,它通过系统性的方法帮助我们识别潜在的失效模式,并评估其对产品或流程性能的影响。
通过该分析程序,我们可以及早发现和预防可能发生的问题,避免质量非标准和客户投诉的发生。
二、(1)程序目标通过潜在失效模式及后果分析管理程序,我们的目标是:- 提升产品及流程的质量,减少潜在的失效;- 预测和预防可能的质量问题出现;- 提高制度和流程的控制性能;- 降低产品召回和服务成本。
(2)程序步骤潜在失效模式及后果分析管理程序一般包含以下步骤:1. 确定分析对象:选择需要进行分析的产品或流程。
2. 制定团队:组建跨职能团队,包括设计师、工程师、生产经理及质量专家等。
3. 制定流程图:绘制分析对象的流程图,详细记录每个操作步骤。
4. 识别潜在失效模式:根据流程图,识别可能存在的失效模式,以及导致其发生的原因。
5. 评估失效后果:评估每种潜在失效模式对产品或流程性能的影响,确定其后果等级。
6. 制定预防控制措施:针对每种潜在失效模式,制定相应的预防控制措施,以降低失效发生的概率。
7. 实施控制措施:在生产或流程中实施预防控制措施。
8. 监控效果:对实施的控制措施进行监控,并评估其效果。
9. 持续改进:根据实施和监控结果,进行持续改进,提升产品或流程的质量和性能。
(3)常见问题及管理策略在潜在失效模式及后果分析管理过程中,常见的问题包括:- 遗漏潜在失效模式:由于团队成员的专业背景和经验不同,可能会遗漏一些潜在失效模式。
解决方案是广泛征求团队成员的意见,并进行多层次的复查。
FMEA潜在失效模式分析管理程序

FMEA潜在失效模式分析管理程序FMEA潜在失效模式分析管理程序(IATF16949-2016)1.目的:确定潜在失效模式与评定其影响的严重程度。
确定关键特性与重要特性。
对潜在的过程缺陷进行排序。
帮助我们集中力量免除对过程的担心,防止问题的发生。
2.范围:适用于公司所有新产品、产品更改以及应用或环境有变化的沿用零件(包括:产品交付给客户后的抱怨(投诉)或退货的产品)。
3.定义:PFMEA:是英文Process Failure Mode and Effects Analysis 的缩写,即过程失效模式及后果分析,是一种表格化的系统方法,用来帮助我们思维,以确定失效模式及其影响,并通过周期性的FMEA分析,以此来获得产品品质的持续改进。
4.权责:4.1APQP小组:负责初期产品生产过程潜在的失效模式及后果分析的作成和评审。
4.2生产部:负责统筹量产后FMEA的维护。
4.3各部门:参与产品生产过程潜在的失效模式及后果分析,并进行评审。
5.内容:5.1 制作PFMEA的三个假设:①PFMEA假设被定义的产品将符合设计意图;②假设投入生产的物料为合格品;③假设操作人员是经培训合格的。
5.2 PFMEA之使用时机:5.2.1 PFMEA为一活性的文件,它应该在APQP五个阶段中的第三个阶段(过程的设计和开发阶段)在制作过程流程图后,根据过程流程图作成。
5.2.2 PFMEA的制作:5.2.2.1讨论并填表:APQP小组成员对相应工序进行讨论,评估出现的几率、可查性、严重程度等项目。
根据评分结果拟定改善措施,负责人及实施日期。
填写相应的FMEA表格。
由指定的改善措施负责人组织,在规定的时间内实施具体的改善行动。
5.2.2.2 评估改善行动:根据计划,由APQP组长召集改善措施的评估会。
依据改善效果决定是否还需要进行下一轮FMEA。
5.2.2.2 FMEA制作流程:5.3 FMEA更改的时机:5.3.1 当生产过程发生更改后必须重新评定FMEA并更改。
IATF16949-2016潜在失效模式和后果分析程序
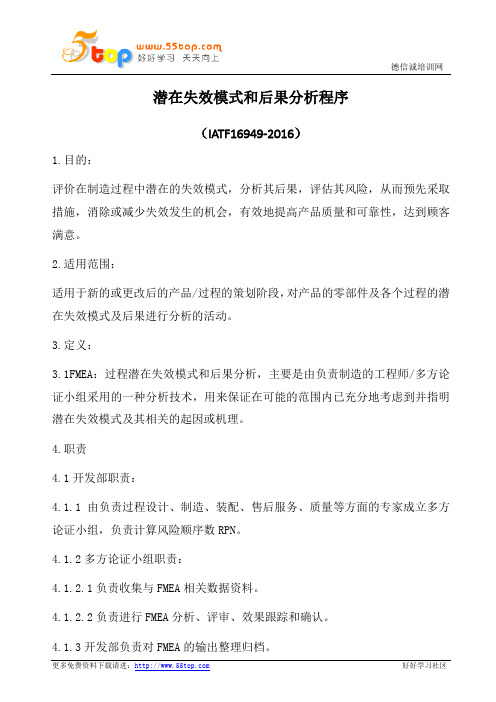
潜在失效模式和后果分析程序(IATF16949-2016)1.目的:评价在制造过程中潜在的失效模式,分析其后果,评估其风险,从而预先采取措施,消除或减少失效发生的机会,有效地提高产品质量和可靠性,达到顾客满意。
2.适用范围:适用于新的或更改后的产品/过程的策划阶段,对产品的零部件及各个过程的潜在失效模式及后果进行分析的活动。
3.定义:3.1FMEA:过程潜在失效模式和后果分析,主要是由负责制造的工程师/多方论证小组采用的一种分析技术,用来保证在可能的范围内已充分地考虑到并指明潜在失效模式及其相关的起因或机理。
4.职责4.1开发部职责:4.1.1由负责过程设计、制造、装配、售后服务、质量等方面的专家成立多方论证小组,负责计算风险顺序数RPN。
4.1.2多方论证小组职责:4.1.2.1负责收集与FMEA相关数据资料。
4.1.2.2负责进行FMEA分析、评审、效果跟踪和确认。
4.1.3开发部负责对FMEA的输出整理归档。
5.作业流程5.1开展FMEA的时机FMEA旨在及早识别出潜在的失效,因此FMEA应在以下情况下开展:5.1.1在产品、过程设计概念形成,设计方案初步确定时开始FMEA;5.1.2在产品、过程设计的各个重要阶段,对FMEA进行评审、修改;5.1.3在如产品、过程设计文件完成之后完成FMEA工作;5.1.4在进行产品、过程设计修改时对FMEA进行重新评审和修改。
5.2FMEA活动的实施5.2.2多方论证小组根据过程流程图、特殊特性清单、产品技术要求、过程特性参数、制造和装配的要求等和现有的FMEA资料对过程潜在失效模式及后果进行分析。
5.3按下列要求填写FMEA表格:5.3.1FMEA编号:按过程号编号。
5.3.2项目名称:填入所分析项目的名称。
如零件/系统;5.3.3设计责任部门:填入产品设计部门和/或小组名称。
5.3.4编制者:填入负责编制的人员姓名、电话及所在部门名称。
5.3.5车型年:填入设计将要应用或影响的车辆年/项目(如已知)。
潜在失效模式及后果分析控制程序

潜在失效模式及后果分析控制程序潜在失效模式及后果分析(Failure Mode and Effects Analysis,简称FMEA)是一种用于系统分析和控制的工具。
通过对系统中可能发生的潜在失效模式进行分析,确定失效的潜在原因和后果,并根据风险程度制定相应的控制措施,以提高系统的稳定性和可靠性。
下面将详细介绍FMEA的控制程序和相关事项,以确保其有效性和可行性。
首先,FMEA的控制程序应该包括以下几个关键步骤:1.选择分析对象:确定需要进行FMEA的系统、过程或子系统。
应根据系统的重要性和风险程度来选择,确保资源的合理分配。
2.建立团队:组建一个多学科的团队,包括相关的专业人员和利益相关者。
例如,工程师、产品经理、质量管理人员等,以确保分析的全面性和准确性。
3.识别失效模式:对于选定的系统,通过头脑风暴、经验或专业知识等方法,识别可能的失效模式。
要考虑机械、电气、软件、环境等多个方面的潜在失效。
4. 评估风险程度:对于每个失效模式,评估其可能性、严重性和检测能力,并计算出风险优先级数(Risk Priority Number,简称RPN)。
5.制定控制措施:根据风险程度和优先级,制定适当的控制措施。
例如,修改设计、更换零部件、增加检测设备等。
6.实施控制措施:根据制定的控制措施,实施相应的改进措施。
确保控制措施的可行性和有效性。
其次,在FMEA的控制程序中,还需要注意以下几个事项:1.及时性:FMEA应与产品或系统的开发、设计和生产过程同步进行,确保在系统投入使用之前发现和修复潜在问题。
2.精确性:在进行FMEA时,应尽量详细和准确地描述潜在失效模式、原因和后果,以避免信息的误解和处理的偏差。
3.综合性:FMEA应对系统的各个方面进行考虑,包括硬件、软件、人员、环境等,以确保全面的分析和控制。
4.持续性:FMEA应持续进行,及时跟踪系统的演化和变化,以保持对潜在失效的控制,并及时识别新的失效模式。
潜在失效模式及后果分析

潜在失效模式及后果分析潜在失效模式及后果分析(Process Failure Mode and Effects Analysis,简称Process FMEA)是一种用于评估和减少过程中的潜在失效模式及其后果的方法。
它是一种系统的、综合的方法,可以帮助组织识别和纠正可能导致质量问题或安全问题的过程中的潜在问题。
在进行过程FMEA之前,需要明确具体的过程,包括每个步骤、输入、输出、关键参数等。
然后根据这些信息,通过以下的步骤进行潜在失效模式及后果分析:1.建立团队:选择合适的团队成员,包括过程的相关专家和从业人员。
确保代表了不同职能和领域的人员。
2.定义过程:清楚地定义需要进行FMEA的过程。
确保团队对过程的理解一致。
3.识别失效模式:识别过程中可能发生的所有失效模式。
这些失效模式可以是物理的、功能性的、电子的等等。
4.评估失效严重性:评估每个失效模式的严重性。
这可以通过影响质量、安全、环境或成本等方面的标准来确定。
5.评估失效频率:评估每个失效模式的发生频率。
这可以通过统计数据、历史记录、专家意见等来确定。
6.评估失效检测程度:评估每个失效模式的检测程度。
这可以通过使用现有的控制和检测方法,并考虑其有效性和可靠性来确定。
7.计算风险优先数(RPN):根据失效严重性、频率和检测程度来计算每个失效模式的风险优先数。
风险优先数是通过将这些因素的等级相乘得到的。
8.制定改进措施:对于具有较高风险优先数的失效模式,制定相应的改进措施。
这可以包括改进过程、加强控制、提高检测方法等。
9.实施改进措施:根据制定的改进措施,进行相应的改进。
这可能需要调整过程、培训员工、更新标准操作程序等。
10.追踪和监控:持续追踪和监控改进的效果。
确保改进措施有效并持续改进。
通过进行潜在失效模式及后果分析,可以帮助组织识别和纠正过程中的潜在问题,以减少质量问题的发生,提高效率和可靠性,并降低成本和风险。
它也可以帮助组织制定相应的控制和预防措施,以确保过程能够持续满足质量和安全要求。
潜在失效模式及后果分析程序
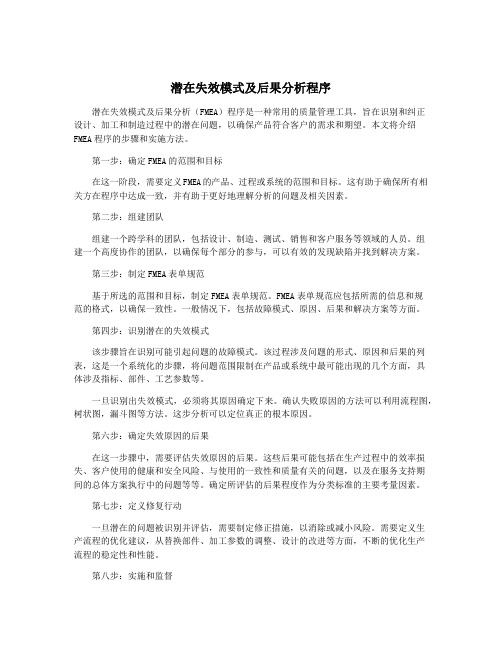
潜在失效模式及后果分析程序潜在失效模式及后果分析(FMEA)程序是一种常用的质量管理工具,旨在识别和纠正设计、加工和制造过程中的潜在问题,以确保产品符合客户的需求和期望。
本文将介绍FMEA程序的步骤和实施方法。
第一步:确定FMEA的范围和目标在这一阶段,需要定义FMEA的产品、过程或系统的范围和目标。
这有助于确保所有相关方在程序中达成一致,并有助于更好地理解分析的问题及相关因素。
第二步:组建团队组建一个跨学科的团队,包括设计、制造、测试、销售和客户服务等领域的人员。
组建一个高度协作的团队,以确保每个部分的参与,可以有效的发现缺陷并找到解决方案。
第三步:制定FMEA表单规范基于所选的范围和目标,制定FMEA表单规范。
FMEA表单规范应包括所需的信息和规范的格式,以确保一致性。
一般情况下,包括故障模式、原因、后果和解决方案等方面。
第四步:识别潜在的失效模式该步骤旨在识别可能引起问题的故障模式。
该过程涉及问题的形式、原因和后果的列表,这是一个系统化的步骤,将问题范围限制在产品或系统中最可能出现的几个方面,具体涉及指标、部件、工艺参数等。
一旦识别出失效模式,必须将其原因确定下来。
确认失败原因的方法可以利用流程图,树状图,漏斗图等方法。
这步分析可以定位真正的根本原因。
第六步:确定失效原因的后果在这一步骤中,需要评估失效原因的后果。
这些后果可能包括在生产过程中的效率损失、客户使用的健康和安全风险、与使用的一致性和质量有关的问题,以及在服务支持期间的总体方案执行中的问题等等。
确定所评估的后果程度作为分类标准的主要考量因素。
第七步:定义修复行动一旦潜在的问题被识别并评估,需要制定修正措施,以消除或减小风险。
需要定义生产流程的优化建议,从替换部件、加工参数的调整、设计的改进等方面,不断的优化生产流程的稳定性和性能。
第八步:实施和监督实施和监督是最后一步,它涉及将所确定的解决方案引入到生产流程中、并监督其执行情况。
FMEA潜在失效模式及后果分析控制程序
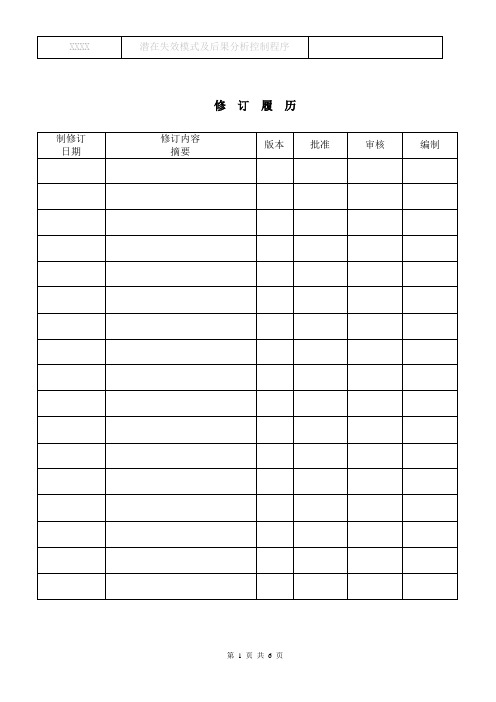
修订履历1.0目的:发现、评价限公司制造过程中潜在的失效以及进行其后果分析,找到能够避免或减少这些潜在失效发生的措施,以便最大限度的确保产品能满足顾客的要求和期望。
2.0范围:公司生产的产品以下的情况,需要进行潜在失效模式与后果分析(简称:FMEA)。
2.1汽车相关的产品或者组件需要实施2.2根据顾客的要求实施2.3品质、技术部门部长指示需要实施的情况3.0权责:3.1 FMEA的分析、措施实施的跟踪、最终报告的作成、以后的修改:工程部门3.2 相关纠正/预防措施的实施:各责任部门4.0 定义:FMEA:是Failrue Mode And Effect Analysis的缩写,意思为潜在失效模式与后果分析。
分为设计FMEA(DFMEA)和过程FMEA(PFMEA)。
5.0作业内容:5.1实施的时期因为公司没有产品的设计和开发,故设计FMEA不适用,仅实施过程FMEA。
在产品的工程设计开始以后到作业标准完成之间作成PFMEA。
在新产品开发和工程变更时的以下时期应进行PFMEA分析:(1)在可行性阶段或之前;(2)在生产用工装到位之前;(3)考虑到从单个部件到总成的所有的制造工序;5.2实施部门由工程部门指定担当者组织,需要的时候由相关各个部门参加,共同参与PFMEA 分析。
5.3实施步骤5.3.1 PFMEA的前提(1) PFMEA假定所设计的产品能够满足设计的要求;(2) PFMEA不依靠改变设计来克服过程中的薄弱环节;5.3.2确认工艺流程图已经完成,按照工艺流程图的工艺顺序填写入《潜在过程失效及后果分析(PFMEA)》的表格。
5.3.3 FMEA分析的严重度(S)、频度(O)、探测度(D)的评价按照第6.0项评价细则进行评价。
5.3.4计算出风险顺序数(RPN),是严重度(S)、频度(O)和探测度(D)的乘积。
严重度(S)×频度(O)×探测度(D) = RPN5.3.5采取措施当RPN>100时,或即使RPN值不大于100的情况仍然需要按照RPN的由大到小的顺序,根据需要采取措施,值大的应优先采取对策。
FMEA潜在失效模式及后果分析管理程序

FMEA潜在失效模式及后果分析管理程序FMEA(Failure Mode and Effects Analysis)是一种系统性的方法,用于识别和评估产品或过程的潜在失效模式及其可能引起的后果。
FMEA可以帮助组织预防或最小化潜在失效对产品质量、安全性和可靠性的影响。
下面是一个FMEA潜在失效模式及后果分析管理程序的示例,确保在组织中有效实施FMEA。
一、引言该程序旨在确保组织对产品或过程进行系统性的失效模式及后果分析(FMEA),以评估潜在失效的风险,并采取适当的预防措施。
二、定义1. FMEA:Failure Mode and Effects Analysis,是一种识别和评估潜在失效模式及其可能引起的后果的方法。
2.潜在失效模式:指在产品或过程中可能发生的具体失效模式。
3.后果:指潜在失效模式发生后产生的影响。
三、程序内容1.确定FMEA的范围和目标:明确进行FMEA的产品或过程范围,以及FMEA的目标是为了什么。
例如,产品的质量改进、安全性提升、故障率降低等。
2.组建FMEA团队:确保组建具有相关领域知识和技能的跨部门团队。
团队成员应包括产品设计、工艺工程、质量控制等相关专业人士。
3.制定FMEA计划:制定详细的FMEA计划,包括时间表、任务分配和所需资源等。
4.进行FMEA分析:a.识别潜在失效模式:收集和分析产品或过程中可能出现的失效情况。
b.评估失效后果:针对每个潜在失效模式,评估其可能引起的后果,包括质量、安全、可靠性和法规符合性等方面。
c.确定风险优先级:通过综合评估潜在失效模式的严重性、发生概率和探测能力,确定每个潜在失效的风险优先级。
d.制定预防措施:针对高风险优先级的潜在失效模式,制定相应的预防措施,以减少或消除潜在失效的风险。
e.实施预防措施:组织相关部门或人员实施制定的预防措施,并跟踪措施的有效性。
f.更新FMEA文档:在FMEA过程中产生的所有数据和分析结果都应及时记录和更新FMEA文档。
潜在失效模式及后果分析管理程序
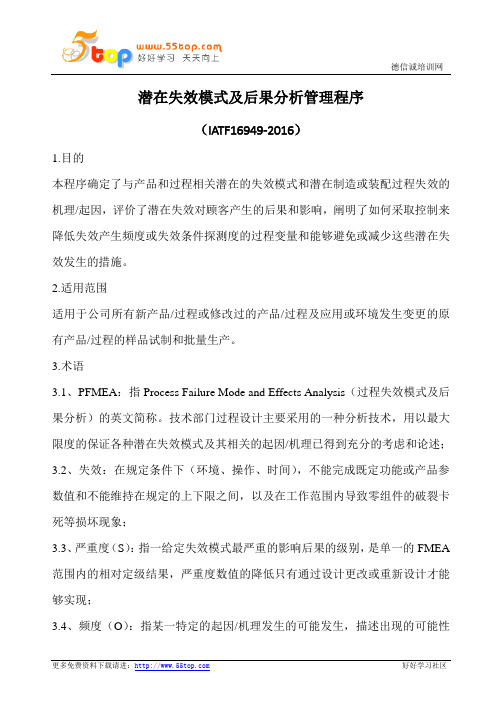
潜在失效模式及后果分析管理程序(IATF16949-2016)1.目的本程序确定了与产品和过程相关潜在的失效模式和潜在制造或装配过程失效的机理/起因,评价了潜在失效对顾客产生的后果和影响,阐明了如何采取控制来降低失效产生频度或失效条件探测度的过程变量和能够避免或减少这些潜在失效发生的措施。
2.适用范围适用于公司所有新产品/过程或修改过的产品/过程及应用或环境发生变更的原有产品/过程的样品试制和批量生产。
3.术语3.1、PFMEA:指Process Failure Mode and Effects Analysis(过程失效模式及后果分析)的英文简称。
技术部门过程设计主要采用的一种分析技术,用以最大限度的保证各种潜在失效模式及其相关的起因/机理已得到充分的考虑和论述;3.2、失效:在规定条件下(环境、操作、时间),不能完成既定功能或产品参数值和不能维持在规定的上下限之间,以及在工作范围内导致零组件的破裂卡死等损坏现象;3.3、严重度(S):指一给定失效模式最严重的影响后果的级别,是单一的FMEA 范围内的相对定级结果,严重度数值的降低只有通过设计更改或重新设计才能够实现;3.4、频度(O):指某一特定的起因/机理发生的可能发生,描述出现的可能性的级别数具有相对意义,但不是绝对的;3.5、不易探测度(D):指在零部件离开制造工序或装配之前,利用第二种现行过程控制方法找出失效起因/机理过程缺陷或后序发生的失效模式的可能性的评价指标;或者用第三种过程控制方法找出后序发生的失效模式的可能性的评价指标;3.6、风险优先数(RPN):指严重度数(S)和频度数(O)及不易探测度数(D)三项数字之乘积。
3.7、顾客:一般是指“最终使用者”,但也可以是随后或下游的制造或装配工序,维修工序或政府法规;4.职责4.1、技术部负责过程失效模式及后果分析(PFMEA)的制定与管理。
5.依据标准5.1、本程序依据IA TF16949:2016质量管理体系中标准条款8.1、8.1.1、8.1.2、8.3、8.3.1、8.3.1.1、8.3.2.3、8.3.3、8.3.3.1、8.3.3.2、8.3.3.3、8.3.4、8.3.4.1、8.3.4.2、8.3.4.3、8.3.4.4、8.3.6、8.3.6.1编制。
潜在失效模式后果分析FMEA控制程序

潜在失效模式后果分析FMEA控制程序潜在失效模式后果分析(Failure Mode and Effects Analysis, FMEA)是一种系统化的方法,用于评估和控制潜在失效模式及其对系统、产品或过程的影响。
以下是FMEA控制程序的一般步骤和相关考虑事项。
1.确定分析的范围和目标:明确需要进行FMEA的系统、产品或过程范围,以及分析的目标,如识别潜在失效模式、评估后果等。
2.组建FMEA团队:成立由跨职能团队组成的FMEA团队,包括设计、制造、质量等相关部门和人员。
在团队成员中确定一个负责人。
3.识别潜在失效模式:对系统、产品或过程进行全面的分析,识别可能出现的潜在失效模式,并列出所有潜在失效模式。
4.评估失效后果:对每个潜在失效模式进行评估,考虑其对系统、产品或过程的影响。
评估标准可以包括安全性、可靠性、维修性、可用性和环境影响等方面。
5.确定失效频率:评估每个潜在失效模式发生的频率或概率。
这可以通过历史数据、经验知识和专家判断等方法来获得。
6.确定探测能力:评估当前探测或检测系统对失效模式的能力,以及探测到失效模式后能否及时采取相应控制措施。
7.计算风险优先级数(RPN):根据失效模式的后果、发生频率和探测能力来计算风险优先级数。
通常使用一个简单的公式:RPN=后果×频率×探测。
8.制定控制措施:对具有较高风险优先级数的失效模式,制定并实施相应的控制措施,以减少或消除潜在风险。
9.重新评估和追踪:定期重新评估已采取控制措施的失效模式,追踪其效果并及时调整控制程序。
10.修订和更新:根据实施控制措施的效果和经验教训,以及新的信息和要求,修订和更新FMEA控制程序。
在FMEA控制程序中1.缺陷的严重程度:评估失效模式对系统、产品或过程的影响程度,包括安全性、可靠性等方面。
2.失效发生的频率:评估失效模式发生的概率或频率,以便更准确地评估潜在风险。
3.探测控制能力:评估当前的探测系统、检测方法或控制措施是否能够及时发现和控制失效模式。
潜在失效模式及后果分析FMEA控制程序
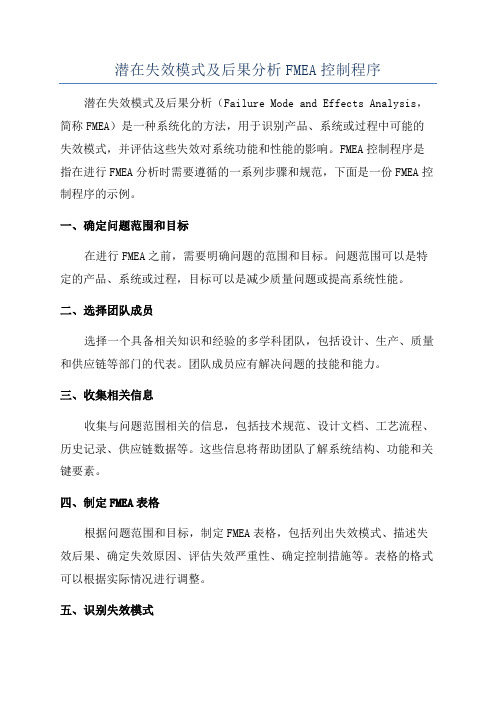
潜在失效模式及后果分析FMEA控制程序潜在失效模式及后果分析(Failure Mode and Effects Analysis,简称FMEA)是一种系统化的方法,用于识别产品、系统或过程中可能的失效模式,并评估这些失效对系统功能和性能的影响。
FMEA控制程序是指在进行FMEA分析时需要遵循的一系列步骤和规范,下面是一份FMEA控制程序的示例。
一、确定问题范围和目标在进行FMEA之前,需要明确问题的范围和目标。
问题范围可以是特定的产品、系统或过程,目标可以是减少质量问题或提高系统性能。
二、选择团队成员选择一个具备相关知识和经验的多学科团队,包括设计、生产、质量和供应链等部门的代表。
团队成员应有解决问题的技能和能力。
三、收集相关信息收集与问题范围相关的信息,包括技术规范、设计文档、工艺流程、历史记录、供应链数据等。
这些信息将帮助团队了解系统结构、功能和关键要素。
四、制定FMEA表格根据问题范围和目标,制定FMEA表格,包括列出失效模式、描述失效后果、确定失效原因、评估失效严重性、确定控制措施等。
表格的格式可以根据实际情况进行调整。
五、识别失效模式团队成员按照经验和知识识别可能的失效模式。
失效模式可以是产品功能缺陷、系统故障、质量不符合要求等。
团队成员可以使用头脑风暴、故障模式与影响分析(FMEA)会议等方法来识别失效模式。
六、描述失效后果对于每个失效模式,团队成员应详细描述其潜在的后果。
后果可以包括安全风险、功能损失、效率下降、成本增加等。
描述后果时,可以使用图表、图像、文字说明等形式。
七、确定失效原因团队成员需要分析和确定导致每个失效模式的原因。
原因可能包括设计缺陷、生产工艺问题、供应链质量问题等。
团队成员可以使用因果图、5W1H法(即What、Why、When、Where、Who、How)等方法确定失效原因。
八、评估失效严重性对于每个失效模式,团队成员需要评估其对系统功能和性能的严重性。
评估可以基于潜在的后果、出现的频率、影响的程度等。
- 1、下载文档前请自行甄别文档内容的完整性,平台不提供额外的编辑、内容补充、找答案等附加服务。
- 2、"仅部分预览"的文档,不可在线预览部分如存在完整性等问题,可反馈申请退款(可完整预览的文档不适用该条件!)。
- 3、如文档侵犯您的权益,请联系客服反馈,我们会尽快为您处理(人工客服工作时间:9:00-18:30)。
1.
评价在制造过程中潜在的失效模式,分析其后果,评估其风险,从而预先采取措施,消除
或减少失效发生的机会,有效地提高产品质量和可靠性,达到顾客扌两丿意。
2. 适用范围:
适用于新的或更改后的产品/过程的策划阶段,对产品的零部件及各个过程的潜在失效模式及后果进行分析的活动。
3. 定义:
3.1 FMEA:过程潜在失效模式和后果分析,主要是由负责制造的工程师/多方论
证小组采用的一种分析技术,用来保证在可能的范围内已充分地考虑到并指明潜在失效模
式及其相关的起因或机理。
4. 职责
4.1开发部职责:
4.1.1由负责过程设计、制造、装配、售后服务、质量等方面的专家成立多方论证小组,负责
计算风险顺序数RPN
4.1.2多方论证小组职责:
4.121负责收集与FMEAS关数据资料。
4.1.2.2负责进行FMEA分析、评审、效果跟踪和确认。
4.1.3开发部负责对FMEA勺输出整理归档。
5. 作业流程
5.1开展FMEA勺时机FMEA旨在及早识别出潜在的失效,因此FMEA应在以下情况下开
展:
5.1.1在产品、过程设计概念形成,设计方案初步确定时开始FMEA
5.1.2在产品、过程设计的各个重要阶段,对FMEAJ行评审、修改;
5.1.3在如产品、过程设计文件完成之后完成FMEAC作;
5.1.4在进行产品、过程设计修改时对FMEAS行重新评审和修改。
5.2 FMEA活动的实施
5.2.2多方论证小组根据过程流程图、特殊特性清单、产品技术要求、过程特性参数、制造和
装配的要求等和现有的FMEA&料对过程潜在失效模式及后果进行分析。
5.3按下列要求填写FMEA表格:
5.3.1 FMEA 编号:按过程号编号。
5.3.2项目名称:填入所分析项目的名称。
如零件/系统;
533设计责任部门:填入产品设计部门和/或小组名称。
534编制者:填入负责编制的人员姓名、电话及所在部门名称。
5.3.5车型年:填入设计将要应用或影响的车辆年/项目(如已知)。
5.3.6关键日期:填入初次FMEA预定完成的日期,该日期不应超过产品加工图完成的日期。
5.3.7 FMEA日期:填入编制FMEA初稿的日期及最新修订的日期。
5.3.8主要参加人:填写执行此项工作的各责任部门和负责人(或参与人)。
5.3.9设计功能要求:简单描述被分析的产品或零件的功能和使用特性,若设计中包括许多具
有不同失效模式的特性,应把这些行性作为独立的一项列出处理。
5.4 潜在失效模式:是指零部件可能发生的不符合设计功能的失效形式,是对具体特性不
符合要求的描述,它可能是引发上一级系统失效的起因,也可
能是下一级零部件失效的后果。
在FMEA准备中,应假定提供的零件/材料是合格
的。
5.5 潜在失效后果:是指失效模式对顾客感受到的功能的影响。
在这里,顾客可以是下一
道工序、后续工序或工位、代理商、最终用户。
当评价潜在失效后果时,应依据顾客可能注意到的或经历的情况来描述失效的后果。
对最终用户来说失效的后果应一律用产品或系统的性能来描述(如噪音、工
作不正常、发热、外观不良、不起作用、间歇性工作等);若顾客是下一道工序、后续工序或工位,失效的后果应用过程/工序性能来描述(如无法紧固、不匹配、无法安装、加工余量过大或过小、危害操作者、损坏设备等)。
5.6严重度(S):是指潜在的失效模式对顾客的影响后果的严重程度的评价指标,严重度仅
适用于失效的后果。
评价指标分为“ T到“10”级,按严重程度依次递增。
评价准
则见表1。
表1严重度(S)评价准则
5.7级别:对零部件、半成品或成品的一些特殊的设计特性进行分级(如关键、重要)。
如在FMEA中确定了某一级别,技质部根据需要制定相应的控制计戈叽
5.8潜在失效起因/机理:是指失效是怎么发生的,并依据易于纠正或控制的方式来描述。
针
对每一个潜在失效模式,尽可能在广、深的范围内列出所有能想象到的失效原因,以便采取针对性的纠正措施。
5.9频度(O):是指具体的失效起因/机理发生的频率。
频度的分级重在其含义而不是具体
的数值。
评价指标分为“ 1”到“10”级,按严重程度依次递增。
评价
准则见表2
表2:频度(O)评价准则
5.10设计控制:列出预防措施、设计确认/验证或其他活动,这些活动的完成或承诺将确
保该设计对于所考虑的失效模式和/或机理来说是充分的。
现行的控制方法是指已经用于或正用于相同或相似设计中的方法。
应尽可能的把重点放在设计控制的改进上,如在技质部进行新系统试验、或创建新的系统模型化运算法等。
有两种类型的设计控制特性可以考虑:
5.10.1预防:预防起因/机理或失效模式的发生,或减少它们的频度;
5.10.2探测:在该项目投产前,以任何解析的或物理的方式,查出失效或失效模式的或起因/
机理。
如有可能,优先选用第一种的预防控制方法,让预防控制方法作为设计意图
的一部分,因为其将影响到最初的频度;最初的探测度将基于失效起因/机理探测或
对失效模式探测的设计控制。
5.11测度(D):是指零部件、半成品、成品、在安装使用前,利用现行设计的控制方法找出
失效起因/机理过程缺陷的可能性的评价指标;或利用控制方法找出后续发生的实效模式的可能性的评价指标。
评价等级分为“1”到
“ 10”级,按严重程度递增。
评价准则见表“ 3”。
表3:探测度(D)评价准则
5.12风险顺序数(RPN:风险顺序数是严重度(S)、频度(O)和探测度(D)的乘积。
即:RPN=S O X Db RPN取值在1-1000之间,对设计中所有担心的事项可以用RPN值来排序,研发工程师负责计算风险顺序数RPN输出
〈产品设计/过程设计风险评估表〉。
5.12.1当RPN> 50 (或依顾客要求)时,应采取改进措施。
5.12.2不管风险顺序数是多少,当S>8时,都要采取改进措施。
5.13措施失效模式按RPN值排出先后次序后,应首先对排在最前面的问题和最关键的项目采
取纠正措施。
任何建议措施的目的都是为了减少严重度、频度和探测度的数值。
如果对某一特定原因无建议措施,那么就在该栏中填写“无”,予以明确。
应考虑以下措施。
5.13.1为了减小失效发生的可能性,需要修改设计。
5.13.2有修改设计,才能减小严重度数。
5.13.3为了增加探测的可能性,需要修改设计。
5.13.4积极的纠正措施是制订永久性的改进措施,以及采用统计过程控制(SPC
方法制订预防缺陷发生的措施。
5.14 目标完成日期:填入建议措施的部门和个人,已及预定完成的日期。
5.15 措施:当实施一项措施后,简要记录具体的措施和生效日期。
5.16 结果:当明确了纠正措施后,估算并记录措施后的严重度、频度和探测度,计算并记
录纠正后的RPN fi。
如未采取什么纠正措施,将措施后的RPN栏和对应的取值栏目空
白即可。
所有纠正后的RPN fi都应评审,而且如果有必要考虑进一步的措施。
5.17 追踪:
5.18.1 应负责保证所有的建议措施已被实施或已妥善地落实。
5.18.2 FMEA是一个动态文件,它不仅应体现最新的设计水平,还应体现最新的有关纠正措
施,包括产品正式投产后发生的设计更改和措施。
5.19 FMEA的管理:完成的FMEA由综合部负责归档保管,如须分发、更改和回收按《文件
管理程序》规定执行。
6. 支持文件与相关表单
6.1 FMEA 分析表。