汽车制动系统计算
制动系统计算说明书

制动器的计算分析整车参数2、制动器的计算分析前制动器制动力前制动器规格为ɸ310×100mm,铸造底板,采用无石棉摩擦片,制动调整臂臂长,气室有效面积。
当工作压力为P=6×105Pa时,前制动器产生的制动力:F1=2*A c*L/a*BF*ɳ*R/R e*P桥厂提供数据在P=6×105Pa时,单个制动器最大制动力为F1=3255kgf以上各式中:A c—气室有效面积L—调整臂长度a—凸轮基圆直径BF—制动器效能因数R—制动鼓半径R e—车轮滚动半径ɳ—制动系效率P—工作压力后制动器制动力后制动器规格为ɸ310×100mm,铸造底板,采用无石棉摩擦片,制动调整臂臂长,气室有效面积。
当工作压力为P=6×105Pa时,前制动器产生的制动力:F2=2*A c*L/a*BF*ɳ*R/R e*P桥厂提供数据在P=6×105Pa时,单个制动器最大制动力为F2 =3467kgf满载制动时的地面附着力满载制动时的地面附着力是地面能够提供给车轮的最大制动力,正常情况下制动气制动力大于地面附着力是判断整车制动力是否足够的一个标准。
地面附着力除了与整车参数有关之外,还与地面的附着系数有关,在正常的沥青路面上制动时,附着系数ϕ值一般在~之间,我们现在按照路面附着系数为来计算前后地面附着力:Fϕ前=G×ϕ+G×ϕ2满1=2200×+6000××=2002kgfFϕ后=G满2×ϕ-G×ϕ23800×××==1487kgf因为前面计算的前后制动器最大制动力分别为F1=3255kgfF2=3467kgf3、制动器热容量、比摩擦力的计算分析单个制动器的比能量耗散率的计算分析前制动器的衬片面积A1=2×πR1××L1=式中(L1=100mm摩擦片的宽度w1=110°)后制动器的衬片面积A2=2×πR2××L2=式中(L2=100m m 摩擦片的宽度w2=)比能量耗散率e1=β=e2=β=上式中:G—满载汽车总质量V1—制动初速度,计算时取V1=18m/sβ—满载制动力分配系数t—制动时间,计算时取t=鼓式制动器的比能量耗散率以不大于mm2为宜,故该制动器的比能量耗散率满足要求。
最大制动减速度计算公式
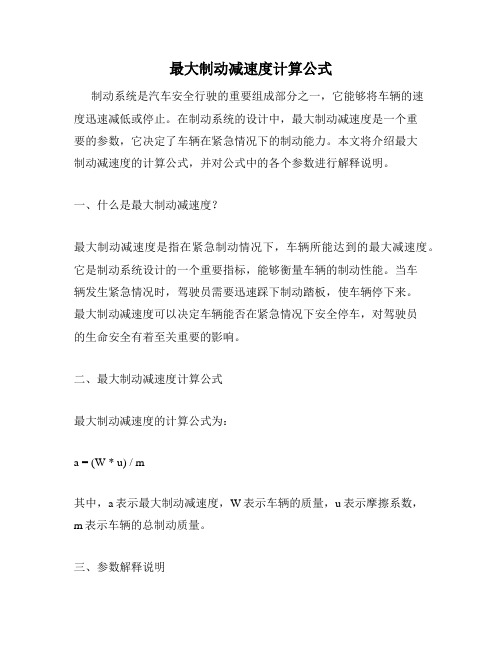
最大制动减速度计算公式制动系统是汽车安全行驶的重要组成部分之一,它能够将车辆的速度迅速减低或停止。
在制动系统的设计中,最大制动减速度是一个重要的参数,它决定了车辆在紧急情况下的制动能力。
本文将介绍最大制动减速度的计算公式,并对公式中的各个参数进行解释说明。
一、什么是最大制动减速度?最大制动减速度是指在紧急制动情况下,车辆所能达到的最大减速度。
它是制动系统设计的一个重要指标,能够衡量车辆的制动性能。
当车辆发生紧急情况时,驾驶员需要迅速踩下制动踏板,使车辆停下来。
最大制动减速度可以决定车辆能否在紧急情况下安全停车,对驾驶员的生命安全有着至关重要的影响。
二、最大制动减速度计算公式最大制动减速度的计算公式为:a = (W * u) / m其中,a表示最大制动减速度,W表示车辆的质量,u表示摩擦系数,m表示车辆的总制动质量。
三、参数解释说明1. 车辆质量(W):车辆质量是指车辆自身的重量,包括车身、发动机、底盘、车轮等组成部分的重量。
它是最大制动减速度计算公式中的一个重要参数,可以直接影响到车辆的制动性能。
2. 摩擦系数(u):摩擦系数是指制动器与车轮之间的摩擦力。
它与制动器的设计、材料、工艺以及路面的状况等因素有关。
摩擦系数越大,制动器对车轮的制动能力越大,车辆的制动性能也就越好。
3. 车辆总制动质量(m):车辆总制动质量是指车辆在制动过程中所需施加的总制动力与重力的比值。
它的数值范围为0至1,数值越大,表示车辆所受的制动力越大,车辆的制动性能也就越好。
四、实例分析假设一辆小轿车的质量为1000kg,摩擦系数为0.7,车辆总制动质量为0.8。
根据最大制动减速度计算公式,可以得到最大制动减速度的数值:a = (1000 * 0.7) / 0.8 = 875 m/s²根据计算结果可知,该小轿车在紧急制动情况下的最大减速度为875m/s²。
这个数值较大,表示车辆具备较好的制动性能,能够在紧急情况下迅速停车,保证驾驶员的安全。
汽车制动系统计算

制动液储油壶容量的要求如下:
1、液储油壶总容量应大于或等于制动器所需要的容量。
(1)盘式制动器所需的储油壶容量:Vpmax
2
4
d
2 p
2 np
( p1
P2
p3)
103
式中: Vpmax—两侧盘式制动器所需的储油壶容量(cm3)
dp—盘式制动器轮缸直径
△p1—盘式制动器摩擦衬块的极限磨损量。
后
2
制 动
器
制动鼓内径mm 分泵直径mm 行车效能因数 驻车效能因数
驻车拉杆机构杠杆比
3
踏 板
真 空 4助 力 器
制动踏板杠杆比
尺寸 助力比 总泵类型 总泵缸径mm 第一腔行程mm
第二腔行程mm
驻
5
车 系
统
驻车手柄杠杆比
质量 m(kg)
车轮滚动 半径
Rd(mm)
©版权归江淮汽车股份有限公司所有 未经授权禁止复制
第 11 页,共 13 页
制动系统方案设计计算说明书
mz (1.72.5)m
P201-NAM-SD-DP-G3-2
对管路布置为X型的主缸,主缸第1、2室行程相同,有:
mz1
mz2
1 2
mz
对管路布置为II型的主缸,主缸第1、2室行程不相同,有:
mz1
n1
1
d
2 1
mz 2
n2
2
d
2 2
2 .
≤95.7
性 能
空载失效制动 制后动失减效速制度动(距m/离s2)
(70km/h)
(m)
≥2.2 ≤95.7
制前动失减效速制度动(距m/离s2)
≥2.2
制动系统车重计算

制动系统车重计算
制动系统车重计算是车辆设计和工程中一个非常重要的环节。
车辆的总重量直接影响着制动系统的设计和性能,因此在进行制动系统车重计算时需要考虑多个因素。
车辆的基本重量是进行制动系统车重计算的关键因素之一。
车辆的基本重量包括车身重量、底盘重量、动力总成重量等。
这些重量需要准确测量和计算,以确保在设计制动系统时考虑到车辆整体的重量分布情况。
车辆的额定载重量也是进行制动系统车重计算时必须考虑的因素。
额定载重量是指车辆设计时所规定的最大载重量,超过这个载重量将会对制动系统造成严重影响。
因此,在进行车重计算时,需要考虑到车辆额定载重量,并确保制动系统能够应对额定载重量下的制动需求。
车辆的使用环境也会影响制动系统车重计算。
例如在不同的道路条件下,车辆的制动性能需求会有所不同。
在湿滑路面或者急转弯情况下,车辆对制动系统的要求会更高。
因此,在进行车重计算时,需要考虑到车辆的使用环境,以确保制动系统在各种情况下都能够正常工作。
车辆的行驶速度也会对制动系统车重计算产生影响。
高速行驶时,车辆的制动距离会更长,对制动系统的要求也会更高。
因此,在进
行车重计算时,需要考虑到车辆的最大行驶速度,以确保制动系统在高速行驶时也能够正常工作。
制动系统车重计算是车辆设计中一个至关重要的环节。
在进行车重计算时,需要考虑车辆的基本重量、额定载重量、使用环境和行驶速度等因素,以确保制动系统能够满足各种情况下的制动需求。
只有在对车辆的车重计算进行全面考虑和分析的基础上,才能设计出安全可靠的制动系统,保障车辆和乘客的安全。
制动强度的定义及计算公式。什么是轴荷转移现象。
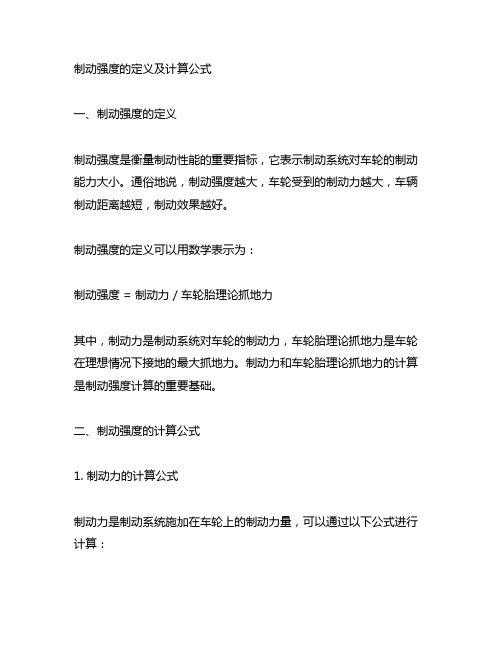
制动强度的定义及计算公式一、制动强度的定义制动强度是衡量制动性能的重要指标,它表示制动系统对车轮的制动能力大小。
通俗地说,制动强度越大,车轮受到的制动力越大,车辆制动距离越短,制动效果越好。
制动强度的定义可以用数学表示为:制动强度 = 制动力 / 车轮胎理论抓地力其中,制动力是制动系统对车轮的制动力,车轮胎理论抓地力是车轮在理想情况下接地的最大抓地力。
制动力和车轮胎理论抓地力的计算是制动强度计算的重要基础。
二、制动强度的计算公式1. 制动力的计算公式制动力是制动系统施加在车轮上的制动力量,可以通过以下公式进行计算:制动力 = 制动器输出力 - 滑移力 - 惯性力其中,制动器输出力是制动系统的输出力,滑移力是车轮因抱死而发生的滑动力,惯性力是车轮滚动时的惯性力。
2. 车轮胎理论抓地力的计算公式车轮胎理论抓地力是车轮在理想情况下接地的最大抓地力,可以通过以下公式进行计算:车轮胎理论抓地力 = 车轮胎附着系数× 车轮垂荷其中,车轮胎附着系数是车轮在不同路面情况下的附着系数,车轮垂荷是车辆在制动时车轮所受的垂直载荷。
制动强度的计算公式为:制动强度 = (制动器输出力 - 滑移力 - 惯性力) / (车轮胎附着系数× 车轮垂荷)通过这个公式,可以计算出车辆在不同路况和制动情况下的制动强度,为制动性能的评价提供了科学的依据。
三、轴荷转移现象在车辆行驶过程中,通过悬挂系统的作用,车辆的重心会发生位置变化,造成车轮的垂向载荷也发生变化,这种现象被称为轴荷转移。
轴荷转移会影响车辆在制动时的稳定性和性能。
当车辆制动时,前轮上的垂向载荷会增加,后轮上的垂向载荷会减小,这会影响车辆的抓地力分布,降低车辆的制动稳定性和制动效果。
轴荷转移现象的计算公式可以表示为:前轮轴荷转移率 = (前轮制动力× 车辆重心高度) / (车轮距)后轮轴荷转移率 = (后轮制动力× 车辆重心高度) / (车轮距)通过这些公式,可以计算出车辆在制动时前后轮的轴荷转移率,为制动性能的优化提供了重要的参考依据。
自动计算制动力矩的公式很好用
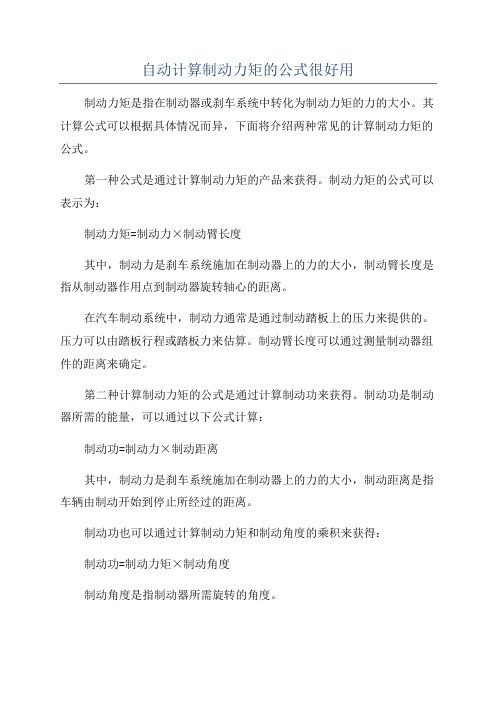
自动计算制动力矩的公式很好用
制动力矩是指在制动器或刹车系统中转化为制动力矩的力的大小。
其计算公式可以根据具体情况而异,下面将介绍两种常见的计算制动力矩的公式。
第一种公式是通过计算制动力矩的产品来获得。
制动力矩的公式可以表示为:
制动力矩=制动力×制动臂长度
其中,制动力是刹车系统施加在制动器上的力的大小,制动臂长度是指从制动器作用点到制动器旋转轴心的距离。
在汽车制动系统中,制动力通常是通过制动踏板上的压力来提供的。
压力可以由踏板行程或踏板力来估算。
制动臂长度可以通过测量制动器组件的距离来确定。
第二种计算制动力矩的公式是通过计算制动功来获得。
制动功是制动器所需的能量,可以通过以下公式计算:
制动功=制动力×制动距离
其中,制动力是刹车系统施加在制动器上的力的大小,制动距离是指车辆由制动开始到停止所经过的距离。
制动功也可以通过计算制动力矩和制动角度的乘积来获得:
制动功=制动力矩×制动角度
制动角度是指制动器所需旋转的角度。
需要注意的是,计算制动力矩时,对于不同的应用和系统,可能涉及到不同的额外因素。
例如,汽车制动系统还需要考虑阻力系数、速度、摩擦系数等因素。
此外,制动力矩的大小也受到制动器设计、制动力的大小以及制动系统的特性等因素的影响。
因此,在实际应用中,需要根据具体情况来选择合适的计算公式和参数。
总结起来,制动力矩的计算公式可以通过计算制动力与制动臂长度的乘积或计算制动功来获得。
但需要根据具体应用和系统的要求来选择合适的公式和参数,并考虑其他因素的影响。
制动系统设计自动计算表格excel

制动系统设计自动计算表格excel.制动系统是车辆最重要的安全部件之一,它直接影响到车辆的制动性能和安全性。
因此,设计一个优秀的制动系统是汽车制造商必须关注和重视的问题。
制动系统设计需要涉及到很多参数,包括车辆重量、轮胎、制动器类型、主缸直径及比例、制动片直径及厚度等多种因素。
对于车辆制造厂商和设计师来说,准确计算这些参数是必不可少的。
我们可以借助excel表格来进行自动计算以更快更准确地获得结果。
首先,制动系统设计需要准确的车辆重量值,这可以通过测量方式得到。
然后,我们需要选择合适的轮胎,并根据制造商提供的数据表格确定轮胎的摩擦系数。
接下来,我们需要选择制动器类型和规格,包括弹簧制动器、液压制动器或电磁制动器等。
根据制动器类型和规格,我们需要计算制动力矩,并以此计算所需的制动器数目。
在选择主缸时,我们需要根据制动器的数量、大小和所需的制动力矩来确定主缸的直径和比例。
为此,我们需要借助公式计算主缸的有效直径,以确保制动力分配到每个制动器。
同时,我们还需要选择合适的制动片直径和厚度,并使用公式计算出制动距离和制动时间。
在车辆行驶过程中,由于轮胎和地面摩擦力随着车速、车重和路面情况的变化而变化,因此我们需要在计算表格中考虑这些因素。
我们可以使用Vlookup和If函数等excel函数进行自动计算。
除了上述关键参数之外,还需要考虑一些其他因素,如制动系统的故障时刻、刹车盘和刹车片磨损速度等。
为此,我们需要在表格中进行连续的轮毂速度、制动压力和刹车片厚度的计算。
这些数据可以用来判断刹车片何时需要更换,从而保证车辆制动性能始终处于最佳状态。
总之,设计一款高性能的制动系统需要仔细考虑多种因素。
使用Excel表格可以简化这些计算,并确保结果的准确性。
通过自动计算表格,我们可以更加快速、准确地设计出适合特定车辆的制动系统,提高车辆的安全性和性能。
制动系统设计自动计算表格excel
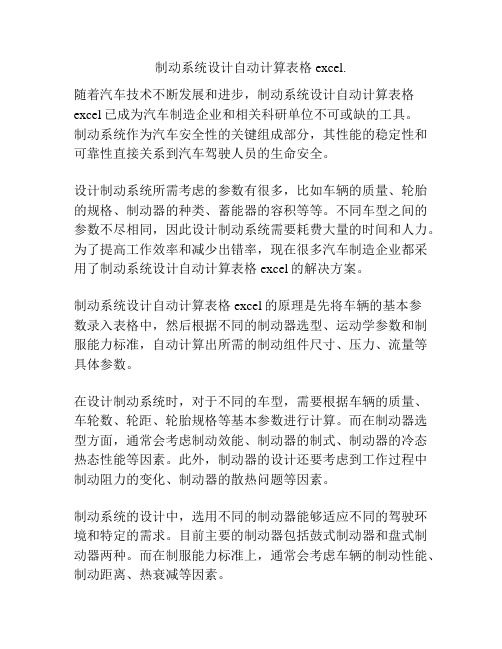
制动系统设计自动计算表格excel.随着汽车技术不断发展和进步,制动系统设计自动计算表格excel已成为汽车制造企业和相关科研单位不可或缺的工具。
制动系统作为汽车安全性的关键组成部分,其性能的稳定性和可靠性直接关系到汽车驾驶人员的生命安全。
设计制动系统所需考虑的参数有很多,比如车辆的质量、轮胎的规格、制动器的种类、蓄能器的容积等等。
不同车型之间的参数不尽相同,因此设计制动系统需要耗费大量的时间和人力。
为了提高工作效率和减少出错率,现在很多汽车制造企业都采用了制动系统设计自动计算表格excel的解决方案。
制动系统设计自动计算表格excel的原理是先将车辆的基本参数录入表格中,然后根据不同的制动器选型、运动学参数和制服能力标准,自动计算出所需的制动组件尺寸、压力、流量等具体参数。
在设计制动系统时,对于不同的车型,需要根据车辆的质量、车轮数、轮距、轮胎规格等基本参数进行计算。
而在制动器选型方面,通常会考虑制动效能、制动器的制式、制动器的冷态热态性能等因素。
此外,制动器的设计还要考虑到工作过程中制动阻力的变化、制动器的散热问题等因素。
制动系统的设计中,选用不同的制动器能够适应不同的驾驶环境和特定的需求。
目前主要的制动器包括鼓式制动器和盘式制动器两种。
而在制服能力标准上,通常会考虑车辆的制动性能、制动距离、热衰减等因素。
制动系统设计自动计算表格excel不仅可以有效提高制动系统设计的效率,还可以降低设计错误率。
在使用制动系统设计自动计算表格excel时,只需要输入车辆的基本参数和选用的制动器,就可以自动计算出所需的制动组件尺寸、压力、流量等具体参数。
这不仅可以节省设计时间,还可以保证设计的准确性和可靠性。
总而言之,制动系统设计自动计算表格excel是目前汽车制造企业和科研单位不可或缺的工具。
其可以有效提高工作效率,降低制动系统设计过程中可能存在的错误率和风险,保证了汽车制动系统的稳定性和可靠性,可以更好地保障驾驶人员的生命安全。
汽车制动系统计算
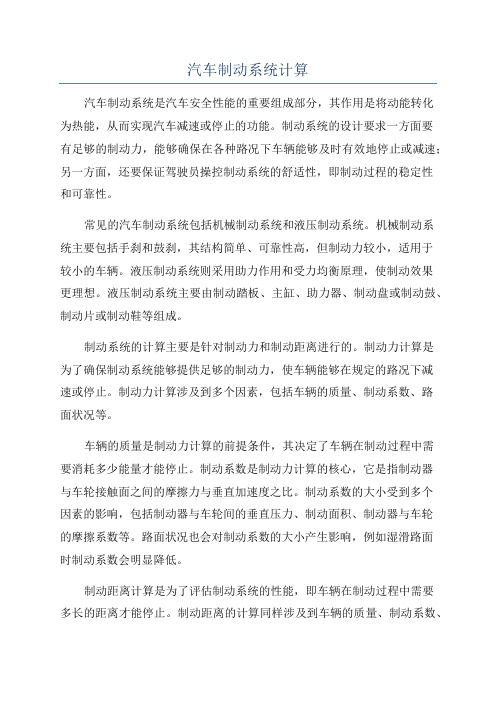
汽车制动系统计算汽车制动系统是汽车安全性能的重要组成部分,其作用是将动能转化为热能,从而实现汽车减速或停止的功能。
制动系统的设计要求一方面要有足够的制动力,能够确保在各种路况下车辆能够及时有效地停止或减速;另一方面,还要保证驾驶员操控制动系统的舒适性,即制动过程的稳定性和可靠性。
常见的汽车制动系统包括机械制动系统和液压制动系统。
机械制动系统主要包括手刹和鼓刹,其结构简单、可靠性高,但制动力较小,适用于较小的车辆。
液压制动系统则采用助力作用和受力均衡原理,使制动效果更理想。
液压制动系统主要由制动踏板、主缸、助力器、制动盘或制动鼓、制动片或制动鞋等组成。
制动系统的计算主要是针对制动力和制动距离进行的。
制动力计算是为了确保制动系统能够提供足够的制动力,使车辆能够在规定的路况下减速或停止。
制动力计算涉及到多个因素,包括车辆的质量、制动系数、路面状况等。
车辆的质量是制动力计算的前提条件,其决定了车辆在制动过程中需要消耗多少能量才能停止。
制动系数是制动力计算的核心,它是指制动器与车轮接触面之间的摩擦力与垂直加速度之比。
制动系数的大小受到多个因素的影响,包括制动器与车轮间的垂直压力、制动面积、制动器与车轮的摩擦系数等。
路面状况也会对制动系数的大小产生影响,例如湿滑路面时制动系数会明显降低。
制动距离计算是为了评估制动系统的性能,即车辆在制动过程中需要多长的距离才能停止。
制动距离的计算同样涉及到车辆的质量、制动系数、道路状况等因素。
制动距离的计算可以根据牛顿第二定律和运动学公式来进行,其中制动时间、制动段速度和制动段长度等参数需要进行实际测量或估算。
为了确保汽车制动系统的安全性和可靠性,制动力和制动距离的计算结果可以作为制动系统设计和制造的依据。
制动力应该保证在各种路况下都能够满足要求,并且具有一定的安全余量。
制动距离的计算结果可以与制动距离标准进行比较,以评估制动系统的性能是否合格。
总之,汽车制动系统的计算是保证汽车行驶安全的重要环节。
制动系统设计自动计算表格excel
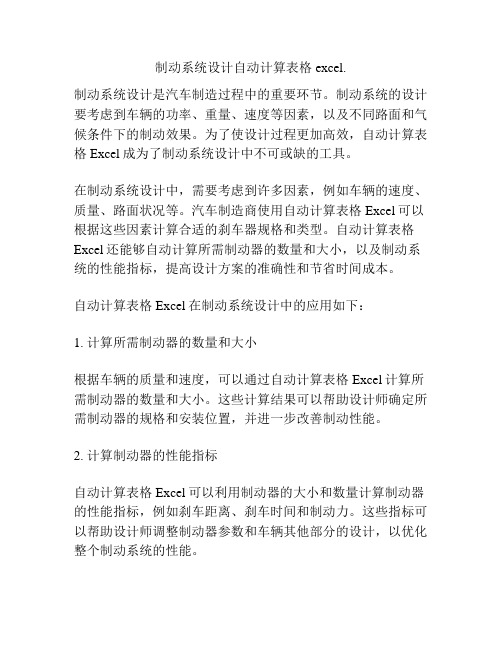
制动系统设计自动计算表格excel.制动系统设计是汽车制造过程中的重要环节。
制动系统的设计要考虑到车辆的功率、重量、速度等因素,以及不同路面和气候条件下的制动效果。
为了使设计过程更加高效,自动计算表格Excel成为了制动系统设计中不可或缺的工具。
在制动系统设计中,需要考虑到许多因素,例如车辆的速度、质量、路面状况等。
汽车制造商使用自动计算表格Excel可以根据这些因素计算合适的刹车器规格和类型。
自动计算表格Excel还能够自动计算所需制动器的数量和大小,以及制动系统的性能指标,提高设计方案的准确性和节省时间成本。
自动计算表格Excel在制动系统设计中的应用如下:1. 计算所需制动器的数量和大小根据车辆的质量和速度,可以通过自动计算表格Excel计算所需制动器的数量和大小。
这些计算结果可以帮助设计师确定所需制动器的规格和安装位置,并进一步改善制动性能。
2. 计算制动器的性能指标自动计算表格Excel可以利用制动器的大小和数量计算制动器的性能指标,例如刹车距离、刹车时间和制动力。
这些指标可以帮助设计师调整制动器参数和车辆其他部分的设计,以优化整个制动系统的性能。
3. 完成刹车管道设计刹车管道是制动系统的重要组成部分。
自动计算表格Excel可以在综合考虑各项参数的基础上进行刹车管道的设计,避免人为的误差和洛克式使用,提高设计的精度和可靠性。
4. 数据处理和可视化自动计算表格Excel还可以对已有数据进行分析和处理,获取更多的有价值的信息。
此外,还能将计算结果以图表和图形的形式呈现出来,直观、生动地展示制动系统的性能和设计优化效果。
总之,自动计算表格Excel对制动系统设计有着重要的作用,从计算所需制动器的数量和大小到计算制动器的性能指标,一直到完成刹车管道设计,最后对设计结果可视化处理。
设计师可以充分利用Excel工具,精细化完成制动系统效率的高品质设计作品。
同时,还需要注意根据实际情况进行合理的调整和改进,以实现优秀的汽车制动系统的设计目标。
汽车列车制动率计算公式
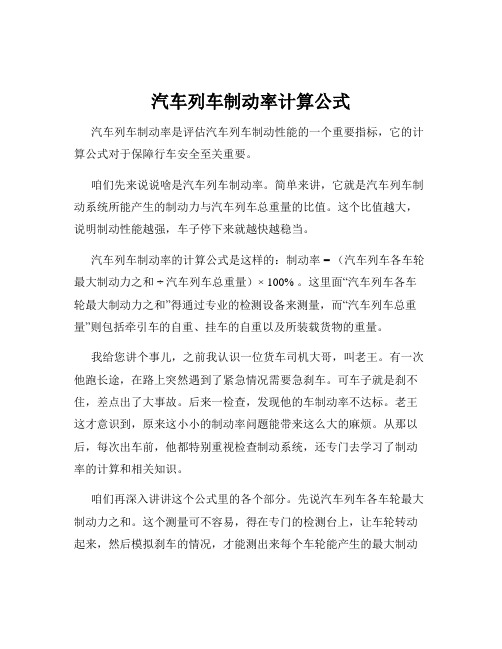
汽车列车制动率计算公式汽车列车制动率是评估汽车列车制动性能的一个重要指标,它的计算公式对于保障行车安全至关重要。
咱们先来说说啥是汽车列车制动率。
简单来讲,它就是汽车列车制动系统所能产生的制动力与汽车列车总重量的比值。
这个比值越大,说明制动性能越强,车子停下来就越快越稳当。
汽车列车制动率的计算公式是这样的:制动率 = (汽车列车各车轮最大制动力之和 ÷汽车列车总重量)× 100% 。
这里面“汽车列车各车轮最大制动力之和”得通过专业的检测设备来测量,而“汽车列车总重量”则包括牵引车的自重、挂车的自重以及所装载货物的重量。
我给您讲个事儿,之前我认识一位货车司机大哥,叫老王。
有一次他跑长途,在路上突然遇到了紧急情况需要急刹车。
可车子就是刹不住,差点出了大事故。
后来一检查,发现他的车制动率不达标。
老王这才意识到,原来这小小的制动率问题能带来这么大的麻烦。
从那以后,每次出车前,他都特别重视检查制动系统,还专门去学习了制动率的计算和相关知识。
咱们再深入讲讲这个公式里的各个部分。
先说汽车列车各车轮最大制动力之和。
这个测量可不容易,得在专门的检测台上,让车轮转动起来,然后模拟刹车的情况,才能测出来每个车轮能产生的最大制动力。
而且,不同的车轮、不同的制动系统,产生的制动力可能都不一样。
再看汽车列车总重量。
这可不是简单地把牵引车和挂车的自重加一加就行的,还得考虑车上货物的重量。
有时候,司机为了多装货多挣钱,就会超载。
可这一超载,不仅违法,还会让制动率下降,刹车效果大打折扣。
在实际应用中,不同类型的汽车列车,制动率的要求也不一样。
比如,重型货车的制动率要求就比轻型货车高。
这也是为了适应它们不同的行驶条件和载重情况。
还有啊,制动率不是一成不变的。
随着车辆的使用,制动系统会磨损,制动力会下降;车辆的维护保养情况也会影响制动率。
所以,定期检查和维护制动系统,确保制动率符合标准,是每个司机都不能忽视的重要工作。
制动系统计算

0.35
参考值
0.76
2.2 22.22
34 54 23.81 0.5 0.5 5.5 4.1 139.4 8.2 5.35 292
292
8 8 0 0
参考值
设计值 设计值 设计值 设计值 参考值 参考值 设计值 设计值 设计值 设计值 设计值 测量值 测量值 参考值 参考值 参考值 参考值
感载比例阀 空载拐点液压 满载拐点液压 空、满载拐点后输出比例
制动强度 前轴的利用附着系数
ψf=β *z/((Lr+z*hg)/L)
后轴的利用附着系数 《汽车理论》P93
ψr=(1-β)*z/((Lfz*hg)/L)
0
0
0.1
0.120939392
0.2
0.229854052
0.3
0.328452434
0.4
0.418133981
0 0.078949692 0.166664565 0.264690108 0.374957835
空载
地面摩擦系数
前后轮制动力比值
前轮制动器制动力Fμ1
后轮制动器制动 力Fμ2
0
0
0
0
0.1
1.005297011
647.5259396 644.1140604
0.2
1.116613419
1362.802053 1220.477947
0.3
1.241014799
2145.82834
1729.09166
0
0
制动器制动力的计算公 式 Fμ 1=2*BF1*PI()/4*d1*d1* P1*r1/Rf
《汽车制动理论与设计 》P26
在此处假设前后制动器 轮缸液压值相等,且前 后轮缸液压无损失。
制动相对压力计算公式

制动相对压力计算公式在汽车制动系统中,制动相对压力是一个重要的参数,它直接影响着制动力的大小和分配情况。
因此,了解和计算制动相对压力是非常重要的。
本文将介绍制动相对压力的概念,并给出其计算公式。
1. 制动相对压力的概念。
制动相对压力是指制动器工作时的压力与制动器工作时的最大压力之间的比值。
在汽车制动系统中,制动相对压力可以用来描述不同制动器工作时的压力大小,从而实现制动力的合理分配。
通常情况下,制动相对压力越大,对应的制动力也就越大。
2. 制动相对压力的计算公式。
制动相对压力的计算公式如下:P = (p1 + p2) / Pmax。
其中,P表示制动相对压力,p1和p2分别表示两个制动器的工作压力,Pmax表示制动器工作时的最大压力。
3. 制动相对压力的影响因素。
制动相对压力的大小受到多种因素的影响,主要包括制动器的设计参数和工作状态等。
首先,制动器的设计参数对制动相对压力有着直接的影响。
例如,制动器的工作面积、摩擦系数等参数都会影响到制动相对压力的大小。
通常情况下,设计参数越大,制动相对压力也就越大。
其次,制动器的工作状态也会对制动相对压力产生影响。
例如,当制动器处于高温状态时,摩擦系数会发生变化,从而导致制动相对压力的变化。
因此,在实际应用中,需要对制动器的工作状态进行考虑,以确保制动相对压力的准确计算。
4. 制动相对压力的应用。
制动相对压力的准确计算对于汽车制动系统的设计和优化具有重要意义。
首先,通过合理计算制动相对压力,可以实现制动力的合理分配,从而提高制动系统的性能和稳定性。
其次,制动相对压力的计算结果还可以用来指导制动器的选择和调整,以满足不同工况下的制动需求。
此外,制动相对压力的计算还可以为汽车制动系统的故障诊断和维护提供参考。
通过监测和分析制动相对压力的变化,可以及时发现制动系统的故障,并采取相应的维护措施,以确保汽车制动系统的正常运行。
5. 结语。
制动相对压力是汽车制动系统中一个重要的参数,它直接影响着制动力的大小和分配情况。
制动系统设计自动计算表格excel

制动系统设计自动计算表格excel.制动系统设计是机械、汽车、航空等领域中非常重要的部分,因为它直接关系到车辆和飞行器的安全性。
随着科技的快速发展,拟定制动系统设计计划的同时自动计算制动系统参数也成为了一个不可或缺的步骤。
这些计算往往会涉及到制动器动力学、热力学等方面。
Excel可以被用于自动计算制动系统参数。
用户可以使用Excel创建一个工作表,可以根据制动器的几何尺寸、材料特性以及工作条件计算出制动力和制动器的温度分布等参数。
此外,也可以利用Excel进行参数变化的可视化。
下面是一些在制动系统设计自动计算表格Excel中需要考虑的要素:1. 制动力制动器产生的制动力取决于制动器的尺寸、材质和工作条件。
为了计算制动器的刹车力,可以采用下面的公式:F=μN其中,μ是材料的摩擦系数,N是垂直于制动盘面积的力的大小。
计算中需要注意的是,μ取决于制动器和制动盘之间的面压力及其变化量。
2. 制动器的温度分布制动器在工作过程中会受到摩擦产生的热量的影响。
因此,计算制动器的温度分布是设计制动系统的重要部分。
这个参数主要取决于热传导方程、制动器几何尺寸和热介质的温度及换热系数。
在Excel中,通过建立表格和运用由折线图和散点图所组成的多个图表工具可以计算出制动器的温度分布,并且可视化展示制动器的特点和表现。
3. 制动盘和制动器的耐久性制动盘和制动器之间的接触表面产生的每一次摩擦都会引起对制动盘和制动器的磨损。
因此,在设计制动系统时,需要考虑制动器和制动盘的材料特性、工作条件,以及垂直力和轴向力对制动盘和制动器的影响。
Excel中的绘图功能可以帮助用户更好地检测这些参数的变化量和轨迹。
在本文中,我们简单介绍了制动系统设计自动计算表格Excel 中需要考虑的相关参考内容。
通过对制动力、制动器温度和制动盘和制动器的耐久性的计算和可视化展示,可以更好地验证制动系统的性能,并且为实践应用提供更好的参考。
三轴以上的汽车制动力计算
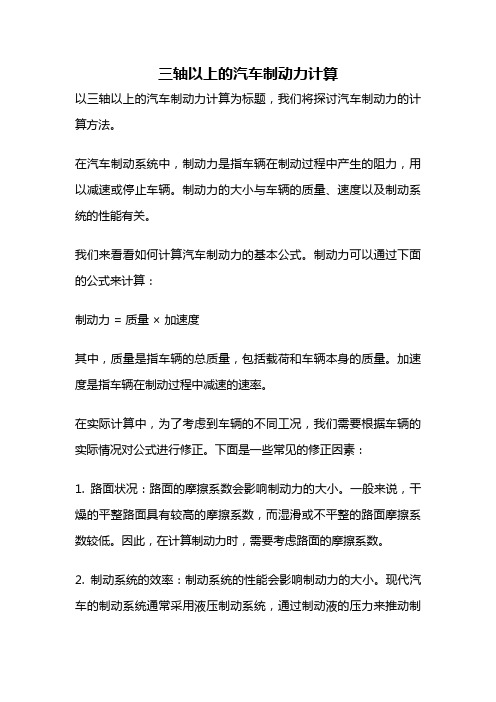
三轴以上的汽车制动力计算以三轴以上的汽车制动力计算为标题,我们将探讨汽车制动力的计算方法。
在汽车制动系统中,制动力是指车辆在制动过程中产生的阻力,用以减速或停止车辆。
制动力的大小与车辆的质量、速度以及制动系统的性能有关。
我们来看看如何计算汽车制动力的基本公式。
制动力可以通过下面的公式来计算:制动力 = 质量× 加速度其中,质量是指车辆的总质量,包括载荷和车辆本身的质量。
加速度是指车辆在制动过程中减速的速率。
在实际计算中,为了考虑到车辆的不同工况,我们需要根据车辆的实际情况对公式进行修正。
下面是一些常见的修正因素:1. 路面状况:路面的摩擦系数会影响制动力的大小。
一般来说,干燥的平整路面具有较高的摩擦系数,而湿滑或不平整的路面摩擦系数较低。
因此,在计算制动力时,需要考虑路面的摩擦系数。
2. 制动系统的效率:制动系统的性能会影响制动力的大小。
现代汽车的制动系统通常采用液压制动系统,通过制动液的压力来推动制动器。
制动系统的效率可以通过制动器的设计和制动液的压力来调节。
3. 轮胎的状况:轮胎是车辆与路面之间的唯一接触点,轮胎的状况会影响制动力的大小。
磨损严重的轮胎或胎压不足的轮胎会减少制动力的传递效果。
除了以上的修正因素,还有一些其他因素也会影响制动力的大小,比如车辆的空气阻力、坡度、风阻等。
这些因素都需要在具体计算中进行考虑。
总的来说,计算汽车制动力是一个复杂的过程,需要考虑多个因素的综合影响。
在实际应用中,可以通过模拟仿真或实验测试等手段来得到更准确的制动力数值。
在现代汽车制动系统中,制动力的计算是非常重要的。
合理计算制动力可以帮助设计师评估制动系统的性能,确保车辆的安全性和可靠性。
此外,制动力的计算也可以用于优化车辆的制动系统设计,提高制动效果。
随着汽车制动技术的不断进步,制动力的计算方法也在不断完善。
未来,随着电动汽车和自动驾驶技术的发展,制动力的计算将面临更多的挑战和机遇。
以三轴以上的汽车制动力计算为标题,我们介绍了汽车制动力的计算方法以及影响制动力的因素。
- 1、下载文档前请自行甄别文档内容的完整性,平台不提供额外的编辑、内容补充、找答案等附加服务。
- 2、"仅部分预览"的文档,不可在线预览部分如存在完整性等问题,可反馈申请退款(可完整预览的文档不适用该条件!)。
- 3、如文档侵犯您的权益,请联系客服反馈,我们会尽快为您处理(人工客服工作时间:9:00-18:30)。
主缸工作行程计算式: m
kv (n1d121 n2d222) dm2
V1、V2、Vm—前、后制动器工作缸工作容积和主缸的工作容积;
d1、d2、dm—前、后制动器工作缸直径和主缸直径; δ1、δ2、δm—前、后制动器活塞工作行程和主缸活塞工作行程
2
制动距离,可用以下公式计算:
S
1 3.6
(t1
t2 ) v 2
v2 25.92 jmax
式中:t1—制动机构滞后时间,即踩下制动踏板克服回位弹簧力并消除制动蹄片
与制动鼓间的间隙所需的时间
t2—制动器制动力增长过程所需的时间 v—制动初速度,km/h
t1+t2—制动器作用时间 ,一般在0.2-0.9s
第 1 页,共 13 页
制动系统方案设计计算说明书
2 .整
车
空载制动 (80km/h)
项目
冷态制动距离-O型 (m)
制动减速度 (m/s2)
法规要求 ≤61.2 ≥5.0
制 动 安
满载制动 (80km/h)
冷态制动距离-O型 (m)
制动减速度 前失(效m制/s动2)距离
≤1.2 ≥5.0
全
(m)
对液压制动系统,GB7258-2004规定,达到规定的制动减速度的75%时的制动协调
时间不得超过0.35秒,所以
t1
t2 2
最大值近似取0.35秒。
©版权归江淮汽车股份有限公司所有 未经授权禁止复制
第 6 页,共 13 页
制动系统方案设计计算说明书
P201-NAM-SD-DP-G3-2
(
3对
于a.
2、在满载状态下,地面附着系数为0.8,标杆管路压力达到12MPa,方案管路压力达到 10MPa,选配方案管路压力达到11MPa,制动器发生抱死,此时前轴早于后轴抱死,整车保持稳 定性。
2前
、
f
F Xb 1 FZ 1
z
1 L
(b
zh
g
)
式
r
FXb 2 FZ 2
(1 )z
1
(
—L
a
zh
g
)
中
f ——
驻坡度
≥18%
.
2
P201-NAM-SD-DP-G3-2
设计要求
Z1
图1 整车受力简图
—
ZL2
—a
—b
—hg
—G
—m
—
©版权归江淮汽车股份有限公司所有 未经授权禁止复制
第 2 页,共 13 页
制动系统方案设计计算说明书
P201-NAM-SD-DP-G3-2
整
车
Fif
Z1
G L
b hg
Fir
n1、n2—前、后制动器单侧油缸数目(仅对盘式制动器而言)
Kv—考虑软管膨胀时的主缸容积系数,汽车设计推荐:轿车 =1.1,货车 =1.3
其中 要根据制动器的类型、参考同类车型确定,对鼓式制动器:汽车设计推荐δ=2-2.5mm;汽车工 程手册推荐3.5-5.5(考虑软管膨胀量及磨损间隙不能自调的影响),公司目前车型均可实现间隙
pv is 1)
式中: Fv0—真空助力器最大助力点输出力;
Pv—真空压力,对汽油车,QC/T307-1999规定的试验真空度为66.7±1.3KPa,柴油
车装有独立的真空泵,一般可达90 Kpa;
D—膜片有效直径;
此时,主缸输出力 Fvo
d
2 m
p
/
4
由此得出膜片有效直径的计算公式:D
d
2 m
d22 4
n2
BF2
r2 R
©版权归江淮汽车股份有限公司所有 未经授权禁止复制
第 3 页,共 13 页
制动系统方案设计计算说明书
根 据 表5 各管路压力下前后制动器制动力
压强 MPa
1
标杆
F if
Fir
方案
Fif
Fir
2
3
4
5
6 7
8
9
10
11
12
此 时 表6 制动力分配系数和同步附着系数
名称
代号
p
(is 1)
pv is
注:采用双膜片时,D2=两个膜片直径的平方和
注:上述计算中P值选取为在1.1附着系数路面前后轮均抱死所需的最大压力;
©版权归江淮汽车股份有限公司所有 未经授权禁止复制
第 10 页,共 13 页
制动系统方案设计计算说明书
P201-NAM-SD-DP-G3-2
2 .
油缸容积计算式为:V 1d2 4
r ——
a ——
b——
整
z—
车
图3 利用附着系数与制动强度的关系曲线
©版权归江淮汽车股份有限公司所有 未经授权禁止复制
第 5 页,共 13 页
制动系统方案设计计算说明书
P201-NAM-SD-DP-G3-2
根据GB 12676-1999制动法规要求: 1)当制动强度z处于0.2~0.8之间时,制动强度z≥0.1+0.85(φ-0.2)。 2)当制动强度z处于0.15~0.3之间时,各轴的附着系数利用曲线位于由φ=z+0.08和φ=z0.08确定的两条平行于理想附着系数利用曲线之间,其中后轴附着系数利用曲线允许与直线φ =z-0.08相交; 3)当制动强度z处于0.3~0.5和0.5~0.61之间时,分别满足公式φ≤z+0.08和φ≤2× (z-0.21) 由上图可以得出结论:当制动强度z处于0.3~0.5和0.5~0.61之间时,标杆满载前轴利用 附着系数不满足法规要求,必须通过ABS电磁阀调节制动力分配,才能满足法规要求。P201方 案前制动器对标,也须通过ABS电磁阀调节制动力分配。
动的
情式 中
jmax p g
Fu—前后轴总制动力 φs—路面滑动附着系数
φp—路面峰值附着系数
路面峰值附着系数的利用,决定于ABS的匹配,且其值大于路面滑动附着系数;在法
规要求的最大踏板力作用下,制动器制动力应远大于任何路面附着系数下的地面制动
(力;所以,可按jm式ax s g
近似计算制动减速度。
第 7 页,共 13 页
制动系统方案设计计算说明书
P201-NAM-SD-DP-G3-2
踏板力
油压
前轴
后轴
空载减速度 空载制动距
离 满载减速度 满载制动距
离
各个方案均满足法规对失效制动的要求。(GB12676,减速度大于2.2m/s²,制动距离小于
©版权归江淮汽车股份有限公司所有 未经授权禁止复制
制动液储油壶容量的要求如下:
1、液储油壶总容量应大于或等于制动器所需要的容量。
(1)盘式制动器所需的储油壶容量:Vpmax
2
4
d
2 p
2 np
( p1
P2
p3)
103
式中: Vpmax—两侧盘式制动器所需的储油壶容量(cm3)
dp—盘式制动器轮缸直径
△p1—盘式制动器摩擦衬块的极限磨损量。
2( 1
在制动稳定性符合法规要求、制动器制动力足够的情况下,车辆的制动减速度主要
取决于路面附着系数及利用,装有ABS的制动系统可以很好的利用路面的峰值附着系数,
所以可以获得更大的制动减速度。在不考虑滚动阻力、风阻等的情况下车辆可获得的最
大减速度可用以下公式表示:
制
动在
jmax Fu / m
车制
jmax s g
制动系统方案设计计算说明书
2 、2
.2 .
P201-NAM-SD-DP-G3-2
车型
载荷
轴距 质心距前 L(mm) 轴距离
质心距后 轴距离
质心高度
a(mm) b(mm)
hg(mm)
空载
2
满载
.
序 号
前
1
制 动
器
项目
结构 分泵直径mm 制动盘外径mm 摩擦片有效半径mm
表2 设计方案参数
标杆
方案
结构
真空助力器在其最大助力点以上曲线工作时,输出力与输入力的比值将大大小于助
力比,将引起踏板力的迅速增加,在一般路面上紧急制动时,要求在最大助力点以下段
曲线工作。对普通型单膜片真空助力器,在不考虑复位弹簧力、助力器的机械效率及主
缸推杆截面积的影响时,真空助力器最大助力点输出力可用下式表示:
Fvo
D2 4(is
△p2—盘式制动器摩擦衬块与制动盘单面间隙。 △p3—盘式制动器摩擦衬块的厚度公差。
np—盘式制动器单侧油缸数目
(2)鼓式制动器所需的储油壶容量:Vgmax
2
4
d
2 g
4 ( g1
g2
g3 ) 103
式中: Vgmax—两侧鼓式制动器所需的储油壶容量(cm3)
dg—鼓式制动器轮缸直径
△g1—鼓式制动器摩擦衬片的极限磨损量
后
2
制 动
器
制动鼓内径mm 分泵直径mm 行车效能因数 驻车效能因数
驻车拉杆机构杠杆比
3
踏 板
真 空 4助 力 器
制动踏板杠杆比
尺寸 助力比 总泵类型 总泵缸径mm 第一腔行程mm
第二腔行程mm
驻
5
车 系
统
驻车手柄杠杆比
质量 m(kg)
车轮滚动 半径
Rd(mm)
©版权归江淮汽车股份有限公司所有 未经授权禁止复制
Z2
G L
a hg
前 、
F1 2p1
d12 4
n1
BF1
r1 R
其 中