romax 齿轮箱振动分析
基于Romax的变速箱建模及模态分析
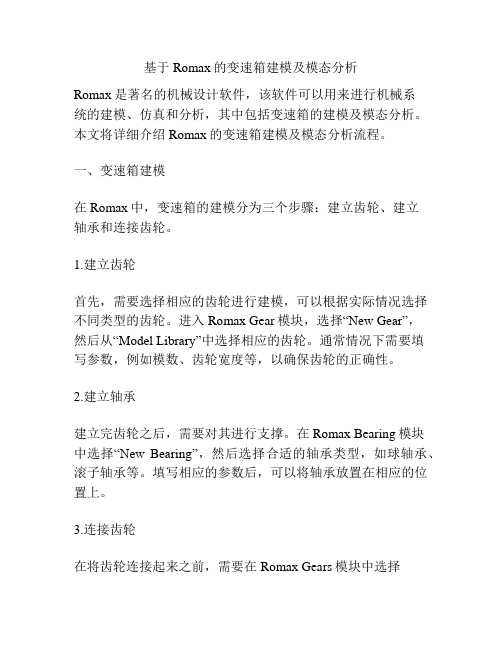
基于Romax的变速箱建模及模态分析Romax是著名的机械设计软件,该软件可以用来进行机械系统的建模、仿真和分析,其中包括变速箱的建模及模态分析。
本文将详细介绍Romax的变速箱建模及模态分析流程。
一、变速箱建模在Romax中,变速箱的建模分为三个步骤:建立齿轮、建立轴承和连接齿轮。
1.建立齿轮首先,需要选择相应的齿轮进行建模,可以根据实际情况选择不同类型的齿轮。
进入Romax Gear模块,选择“New Gear”,然后从“Model Library”中选择相应的齿轮。
通常情况下需要填写参数,例如模数、齿轮宽度等,以确保齿轮的正确性。
2.建立轴承建立完齿轮之后,需要对其进行支撑。
在Romax Bearing模块中选择“New Bearing”,然后选择合适的轴承类型,如球轴承、滚子轴承等。
填写相应的参数后,可以将轴承放置在相应的位置上。
3.连接齿轮在将齿轮连接起来之前,需要在Romax Gears模块中选择“New Shaft Assembly”,然后选择正确的轴承类型。
然后在“New Gear”中选择齿轮并放置到相应的位置上,最后将齿轮进行连接。
二、模态分析在建立完变速箱的三维模型之后,就可以进入模态分析。
Romax使用有限元方法来预测变速箱的固有频率和固有振型,以便确定变速箱的可靠性和稳定性。
1.建立模态分析模型模态分析模型需要包括整个变速箱的结构,包括轴、齿轮、轴承、支撑等所有部分。
在Romax中,可以使用“Create New Model”来建立模态分析模型。
在建立模型时需要将齿轮和轴承等等加入到模型中。
2.设置分析参数确定好模态分析模型之后,需要设置一些分析参数,如边界条件、网格密度、模型尺寸和接触范围等等。
设置完这些参数后,可以使用FEA技术进行模态分析。
3.模态分析结果模态分析结果可以得到变速箱的固有频率和固有振型,这些结果可以用来判断变速箱的稳定性和可靠性。
同时,也可以进一步优化设计,以提高变速箱的实际性能。
齿轮箱振动的故障诊断与分析

其倍频 处 能量 集 中且 数 值 较 大. 据 齿 轮 箱 各 类 根
零件损 坏 比例 的统 计 , 轮失 效 占 6 , 次依 次 齿 0 其
为轴 承 1 %、 1 、 体 7 、 固件 3 、 封 9 轴 O 箱 紧 油 1 因此 , %. 确定 进 一 步 的研 究 方 向 为 齿 轮 振 动 信
频率/ Hz
图 1 测点 1 径 向 ) 速 度 频 谱 图 ( 加
F g 1 Ac ee a in s e t u o a u i g p i t1 i. c lr t p c r m fme s r o n o n ( a il ie t n r d a r c i ) d o
4 #机 架 齿轮 箱连 接 螺栓 断 裂事 故 , 重 影 响到该 严 产 线 的正常 生产 , 其后 , 轮 箱螺 栓 断 裂事 故频 频 齿 发生 , #机架 齿 轮箱 在 1 4 ~5架 中振 动 最为 明显 , 造 成长 时 间停 机 抢 修 , 给企 业 生 产 带来 了一 定 的
动 的 激励 源. 立 齿 轮 箱 螺 栓 的 有 限 元模 型 , 模 拟 工况 下 计 算 得 出螺 栓 的第 3阶 固 有 频 率 与 齿 轮 箱 振 动 主 建 在 频 率相 近 , 成 共 振 是 致 使 螺 栓 断裂 的 主要 原 因. 过 这 种 分 析 计算 方法 , 栓 断 裂 事 故 得 到 了 有 效 的 控 制 . 形 通 螺
第 1 2期
安 妮 , : 轮 箱 振 动 的 故 障 诊 断 与分 析 等 齿
的激励源 , 障齿 轮 的振 动信 号 表现 为 回转 频率 对 故 啮合频率及其倍频 的调制 , 对于其频谱 而言 , 其谱 线 是 以啮合频率 为 中心 , 以故 障齿 轮 的转频 为
基于Romax的电动汽车齿轮箱优化设计
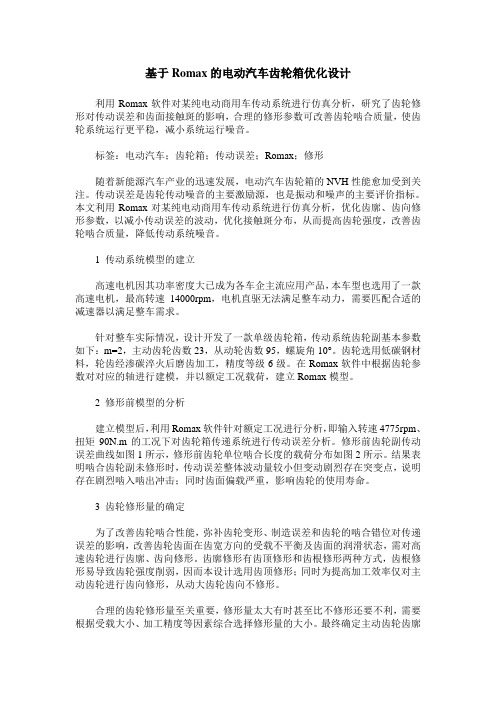
基于Romax的电动汽车齿轮箱优化设计利用Romax软件对某纯电动商用车传动系统进行仿真分析,研究了齿轮修形对传动误差和齿面接触斑的影响,合理的修形参数可改善齿轮啮合质量,使齿轮系统运行更平稳,减小系统运行噪音。
标签:电动汽车;齿轮箱;传动误差;Romax;修形随着新能源汽车产业的迅速发展,电动汽车齿轮箱的NVH性能愈加受到关注。
传动误差是齿轮传动噪音的主要激励源,也是振动和噪声的主要评价指标。
本文利用Romax对某纯电动商用车传动系统进行仿真分析,优化齿廓、齿向修形参数,以减小传动误差的波动,优化接触斑分布,从而提高齿轮强度,改善齿轮啮合质量,降低传动系统噪音。
1 传动系统模型的建立高速电机因其功率密度大已成为各车企主流应用产品,本车型也选用了一款高速电机,最高转速14000rpm,电机直驱无法满足整车动力,需要匹配合适的减速器以满足整车需求。
针对整车实际情况,设计开发了一款单级齿轮箱,传动系统齿轮副基本参数如下:m=2,主动齿轮齿数23,从动轮齿数95,螺旋角10°。
齿轮选用低碳钢材料,轮齿经渗碳淬火后磨齿加工,精度等级6级。
在Romax软件中根据齿轮参数对对应的轴进行建模,并以额定工况载荷,建立Romax模型。
2 修形前模型的分析建立模型后,利用Romax软件针对额定工况进行分析,即输入转速4775rpm、扭矩90N.m的工况下对齿轮箱传递系统进行传动误差分析。
修形前齿轮副传动误差曲线如图1所示,修形前齿轮单位啮合长度的载荷分布如图2所示。
结果表明啮合齿轮副未修形时,传动误差整体波动量较小但变动剧烈存在突变点,说明存在剧烈啮入啮出冲击;同时齿面偏载严重,影响齿轮的使用寿命。
3 齿轮修形量的确定为了改善齿轮啮合性能,弥补齿轮变形、制造误差和齿轮的啮合错位对传递误差的影响,改善齿轮齿面在齿宽方向的受载不平衡及齿面的润滑状态,需对高速齿轮进行齿廓、齿向修形。
齿廓修形有齿顶修形和齿根修形两种方式,齿根修形易导致齿轮强度削弱,因而本设计选用齿顶修形;同时为提高加工效率仅对主动齿轮进行齿向修形,从动大齿轮齿向不修形。
RomaxDesigner自编教程(减速器、变速箱动态分析)

一、行业软件介绍1、MASTA(英国SMT技术公司)MASTA 是当今世界上功能最强,覆盖面最宽,技术最深,实用性最强的传动系统选配、设计/开发、制造一体化大型专用软件系统。
MASTA 软件应用涵盖了舰船(包括工业齿轮箱、风电齿轮箱等)、车辆(包括变速器、驱动桥和分动器)和航空领域。
MASTA 包含两部分:设计分析部分和齿轮制造部分,针对车辆,还有整车匹配部分。
设计分析部分包含三个方面的功能:建模或设计功能,分析功能,优化功能。
这三方面的功能都覆盖三个层面:零件,部件或称子系统,总成或称系统2、Romax Designer(英国Romax公司)Romax 是一家集软件工具开发和传动项目咨询为一体的公司,在传动领域有超过十二年以上的经验;总部设在英国,在欧洲、美国、日本、韩国、澳洲、印度等均开办有办事处。
由Romax 公司积累多年经验开发的Romax Designer 主要应用于齿轮传动系统虚拟样机的设计和分析,在传动系统设计领域享有盛誉,目前已成为齿轮传动领域事实的行业标准。
Romax 用来建立齿轮传动系统虚拟样机模型,还包括详细部件强度和可靠性分析,及传动系统振动噪声分析,大大加速传动系统的设计和开发流程。
在Romax 中,考虑结构柔性,同时考虑更多实际情况,如装配误差及轴承间隙、预载等。
Romax Designer 应用很广,其中包括汽车、船舶、工程机械、风力发电、工业、轴承以及航空航天等领域的齿轮传动系统的设计。
3、KISSSOFT HIRNWARE (瑞士软件)KISSSOFT 是一款用于机械传动设计分析的软件,计算操作过程简便,计算结果精确。
对于各类零件如齿轮、弹簧、链轮、花键、键、轴承等很多的零件提供了计算方法,类似于中国的机械设计手册,功能十分齐全。
唯一不足的是该软件计算整个系统传动时,操作性、结果不如Romax 和Masta 详细方便。
4、MDESIGN (德国软件)机械传动设计软件大牛MDESIGN,包括类似中国的机械设计手册,集成MATHCAD的机械计算程序包,标准零件库,齿轮,轴,花键,轴承计算,齿轮计算包括齿轮箱设计,齿轮设计,行星轮设计,包括使用标准进行计算强度已经有限元计算强度。
ROMAX齿轮动力学分析和优化资料

万方数据
学校代号:10731 学 号:122080201078 密 级:公开
兰州理工大学硕士学位论文
基于 ROMAX 的齿轮箱动力学分析及 优化
学位申请人姓名: 导师姓名及职称: 培 养 单 位: 专 业 名 称: 论文提交日期 : 论文答辩日期 : 答辩委员会主席:
王彬 郭润兰 教授 黄华 副教授 机电工程学院 机械制造及其自动化 2015 年 4 月 15 日 2015 年 6 月 9 日 余生福 正高级工程师
万方数据
Dynamic Analysis and Optimization of the Gearbox Based on ROMAX by WANG Bin
B.E. (Lanzhou University of Technology) 2011
A thesis submitted in partial satisfaction of the Requirements for the degree of Master of Engineering in
学校代号 10731 分 类 号 TH131
学 号 122080201078
密级
公开
硕士学位论文
基于 ROMAX 的齿轮箱动力学分 析及优化设计
学位申请人姓名 培养单位 导师姓名及职称 学科专业 研究方向 论文提交日期
王彬 机电工程学院 郭润兰 教授 黄华 副教授 机械制造及其自动 先进制造技术 2015 年 4 月 15 日
Mechanical Manufacture and Automation in the
School of Mechanical and Electronical Engineering of
Lanzhou University of Technology
某型齿轮箱传动系统的噪声与振动分析

某型齿轮箱传动系统的噪声与振动分析随着科技的进步和人们对质量要求的提高,噪声和振动问题已经成为工业界面临的一个重要挑战。
对于某型齿轮箱传动系统来说,噪声和振动不仅会对设备的正常运行产生负面影响,还会对操作人员的健康和环境造成潜在风险。
因此,对齿轮箱传动系统的噪声与振动特性进行深入分析和优化是十分必要的。
首先,要了解齿轮箱传动系统中噪声和振动的产生机制。
齿轮箱主要由齿轮、轴、轴承等组成,当这些部件在工作过程中发生相对运动时,就会产生振动。
而由于材料、摩擦、结构等因素的限制,这种振动会以声波的形式传播出来,产生噪声。
齿轮、轴、轴承等部件的质量、结构、加工精度等都会对振动和噪声产生影响,因此,在设计和制造过程中应该注重提高部件的质量和加工精度,减少不必要的振动和噪声。
其次,齿轮箱传动系统噪声和振动的分析方法主要由试验和数值模拟两部分组成。
试验方法通常使用振动传感器和声学传感器来测量实际工作状态下的振动和噪声数据。
通过对实测数据的分析,可以了解不同工况下齿轮箱振动和噪声的变化规律,找出可能存在的问题和改进措施。
数值模拟方法则通过建立齿轮、轴、轴承等部件的有限元模型,并结合运动学和动力学分析方法,计算出齿轮箱在不同工况下的振动和噪声情况。
通过数值模拟可以在设计阶段就预测和评估齿轮箱的性能,提前采取相应的改进措施。
齿轮箱传动系统的噪声和振动问题涉及到多个方面的因素。
首先,振动和噪声的源头主要包括齿轮啮合、轴承摩擦、轴向不稳定等。
齿轮啮合时会产生周期性的振动和噪声,当齿轮啮合配合不良或齿轮质量不合格时,啮合过程中会产生不规则的振动和噪声。
轴承摩擦和轴向不稳定则会导致齿轮箱产生高频振动和噪声。
其次,传动系统的结构和材料也会对振动和噪声产生影响。
合理设计传动系统的结构和加强件的连结,选择合适的材料和表面处理方法,可以有效地减少振动和噪声的产生。
再次,传动系统的工作工况也会对噪声和振动产生不同程度的影响。
根据传动系统的工况,合理调整传动比、转速和负载等参数,可以减少振动和噪声的幅度和频率。
齿轮与齿轮箱振动噪声机理分析及控制

齿轮与齿轮箱振动噪声机理分析及控制写在前面噪声是指发声体做无规则振动时发出的声音。
声音由物体的振动产生,以波的形式在一定的介质(如固体、液体、气体)中进行传播。
一、齿轮振动的实例1齿轮轮毂的振动齿轮传递扭矩首先从轴传至轮毂,由轮毂传递到轮齿,再由主动轮轮齿传递到被动轮轮毂和轴系。
在传递过程中,由于受到轴向激励力的作用,齿轮轮毂产生轴向振动。
另外,由于啮合力的作用,轮毂也会产生横向和沿周向的振动。
2轴承及轴承座的振动齿轮系统通过轴系安置于轴承及其轴承座上,由于齿轮本体的轴向和周向振动必引起轴承支承系统的振动,相反,外界干扰力(如螺旋桨的轴承力)也可能通过轴承传递给齿轮系统。
3齿轮箱的振动齿轮的振动由轴系传到齿轮箱,激励箱体振动,从而辐射出噪声。
另外,齿轮在箱内振动的辐射声激励箱体,使箱体形成二次辐射噪声,这类噪声大部在中低频范围内。
齿轮箱体本身的振动也直接产生辐射声。
4齿轮的振动在啮合过程中,轮齿先由一点接触而扩展到线接触,或一次实现线接触,使得接触力大小、方向改变,产生机械冲击振动,从而辐射出噪声。
这类噪声呈现高频冲击的形式,其典型的齿轮振动时程曲线示于图2。
轮齿啮合时不断变化的啮合力,既激发齿轮的强烈振动,即各个轮齿的响应很大,也激发了齿轮箱箱体较弱的振动。
通常认为齿轮产生噪声的主要原因是轮齿之间的相对位移。
这类噪声源产生的噪声可以用付氏变换法把噪声表示为稳定频率的分量的集合。
图1 齿轮啮合振动及噪声传播图2 齿轮振动时程曲线二、齿轮振动噪声产生的机理1齿轮啮合激励产生的噪声齿轮的轮齿在啮合时因传动误差产生交变力,在交变力作用下产生线性及扭转响应,使齿轮产生振动辐射出噪声。
这是一种主要的噪声源,接触力变化越大,则齿轮相应的振动响应越大。
另外,齿轮的周节差产生的由复杂的或调制频率及其倍频组成的噪声,含有重复的基频(轴频),频率很低。
由于周节差产生了不规则的脉冲序列。
这种脉冲序列包括了众多的频率成份,但还不能认为是宽带随机噪声。
齿轮箱专用振动信号分析方法

齿轮箱专用振动信号分析方法齿轮箱振动信号的特点是频率成分复杂,存在大量的调制现象,并且齿轮箱(特别是行星齿轮箱)内部的故障信号传递路径长,冲击脉冲比较弱,易受其他信号干扰,被幅值大的转动轴振动信号掩盖,基本的频谱分析有时效果不理想,需要根据结构特点,采用一些专用的分析方法一、多轴系阶比跟踪技术计算阶比跟踪技术(Computed Order Tracking)对齿轮箱分析非常适用,特别是变速齿轮箱的低速轴分析,由于转速低,测量5-10个转动周期需要耗时很长,加上转速变动,如果不做阶比跟踪采集,得到的振动信号直接做FFT,频谱存在非常严重的“模糊”现象(谱线相互重叠,不清晰,不便于故障识别和分析)。
图1:阶比跟踪采样图2:普通频谱分析图3:计算阶比跟踪分析图4:计算阶比跟踪分析局部放大(啮合频率和边带明显)齿轮箱类设备因为有多个齿轮轴,采用多轴系阶比跟踪分析,很多时候分析结果非常直观,直接从不同转轴的阶比跟踪采样波形就能得到故障信息。
图5:中间轴故障图6:输出轴故障二、齿轮箱振动分析Circular图技术下面三张图分别是一个齿轮箱输入轴(高速)、中间轴、输出轴(低速)的Circular图,三个轴的转速比是1:3:5。
可以直观的看到输出轴存在故障。
图7:输入轴振动Circular图图8:中间轴振动Circular图图9:输出轴振动Circular图下图是一个行星齿轮箱的齿圈故障时的振动Circular图。
该行星齿轮箱有三个行星轮。
图10:齿圈有1个断齿时的Circular图三、阶比包络谱技术包络分析对于齿轮箱及其内部的滚动轴承故障分析和故障定位非常有效,包络分析可以有效提取齿轮箱、轴承部件存在缺陷时的高频冲击脉冲信号,但是如果齿轮箱转速不稳定,存在转速变动,这种冲击信号的周期也是随转速变动的,直接进行包络分析效果不好。
采用阶比包络分析技术可以消除转速波动的影响,得到非常清晰的诊断图谱。
图11:频谱分析图12:普通包络分析图13:阶比包络分析四、阶比边带能量比技术齿轮箱振动信号频谱最基本的特征是啮合频率和转轴边带信号。
齿轮箱振动信号分析和故障诊断ppt课件

齿轮传动 (r/min)
1495
1457
1402
涡轮传动 (r/min)
1498
1345
1252
970
方差 0.1970 0.0742 0.0822 0.0019
0.0341
0.0764 0.0385
偏度 -0.0108 0.1928 -0.1391 -0.6687 -7.175e-04 -0.0224 0.0027
齿轮传动振动信号功率谱(1402r/min) 涡轮传动振动信号功率谱(1498r/min)
涡轮传动振动信号功率谱(1345r/min) 涡轮传动振动信号功率谱(1252r/min)
涡轮传动振动信号功率谱(970r/min)
总结
1、在时域中,我们往往很难对齿轮箱的振动信号的 时域波形图直接进行有效分析,只能通过计算信号的的 方差、偏度、峰度和均方根值等统计数学指标,使我们 能够对信号波形有一个初步大致的认识。通过对不同输 入转速下的振动信号比较,其时域特征并不能明显的做 出区分判断。
32维分解 a=zeros(32,1); for ii=1:32 for jj=1:n
%求每个尺度对应能量占总能量的百分比 sum1=0; for ii=1:32 sum1=sum1+a(ii); end b=zeros(32,1); for ii=1:32 b(ii,1)=a(ii,1)/sum1; end b=b'; l1(i,2:1:33)=b(1,:);
选用Morlet小波函数,把振动信号在Morlet小波下进行 尺度为32的分解,经过连续Morlet小波变换可得到振动信号 的尺度-能量关系。
程序如下:
clc clear close all hidden %%********************************读数据 l1=zeros(7,33); for i=1:7
Romax在变速箱设计及优化方面的主要应用

图1 传递误差分析
实用文档
图2 齿轮啮合特性分析界面
实用文档
图3 齿轮啮合特性分析界面
实用文档
图4 齿轮单位啮合长度的载荷分布
实用文档
图5 齿轮谐次响应
实用文档
图6 齿轮传递误差(26.15-13.72=12.43um)
实用文档
由图4可以看出,齿轮所受载荷在齿向分布上存在严重的分布齿优化界面:
实用文档
Romax 软件内嵌动力学分析模块如下图所示,可以完成齿轮箱系统 固有频率及固有振型的求解,通过 振动噪声分析模块可以查看求解结 果。利用动力学分析模块可求解动力模块传动系统在各档工况下的前几 阶固有频率。
实用文档
分别对变速箱壳体及变速箱齿轮传动系统进行模态分析,分 析界面如下图所示:
齿轮传动系统模态分析
因此我们可以采用第一部分所讲的齿廓修形作为减小轮齿 啮合激励的有效手段,用于消除轮齿的啮入和啮出冲击并最大 限度地减小齿轮传动误差的波动,实现减小振动的目标。可通 过齿轮修形以减小齿轮传递误差,并对传递误差的仿真结果与 测量结果进行对比,验证两者的关联性。
目前对于齿轮箱啸叫的研究,主要集中在应该如何使传 递误差减小的方面。
实用文档
最终建立完成的三维模型如下图所示:
实用文档
换挡机构建立完成后,建立工况,设置每个工况下的载荷:
实用文档
1.2 齿轮强度分析
以1档输出齿轮为例进行分析。分析结果如下图所示, 轮齿弯 曲应力、接触应力如图:.
实用文档
一档输出齿轮强度分析结果如下表所示:
实用文档
1.3 齿形优化过程
由于轴、轴承、齿轮的变形及受载,必然 导致轮齿变形及错位,减小单位啮合长度的最大载 荷及传递误差(减小啮合噪声),对轮齿进行齿向 及齿形修形,这样可以有效减小啮合线单位长度上 的载荷,减小载荷突变,可减小啮合噪声。
romax齿轮箱振动分析要点
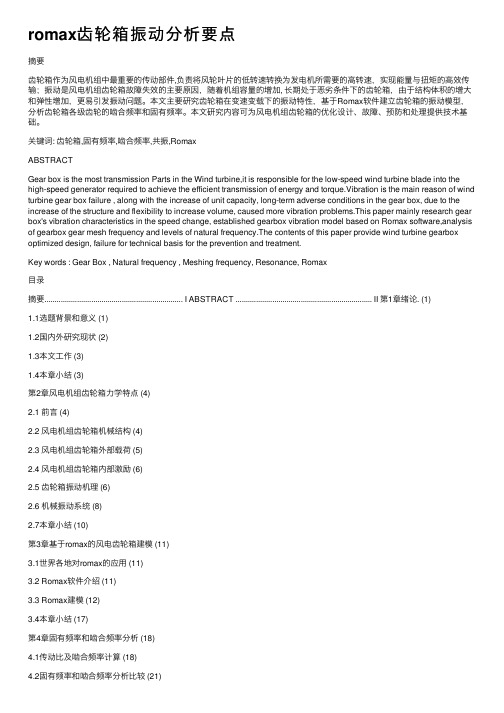
romax齿轮箱振动分析要点摘要齿轮箱作为风电机组中最重要的传动部件,负责将风轮叶⽚的低转速转换为发电机所需要的⾼转速,实现能量与扭矩的⾼效传输;振动是风电机组齿轮箱故障失效的主要原因,随着机组容量的增加, 长期处于恶劣条件下的齿轮箱,由于结构体积的增⼤和弹性增加,更易引发振动问题。
本⽂主要研究齿轮箱在变速变载下的振动特性,基于Romax软件建⽴齿轮箱的振动模型,分析齿轮箱各级齿轮的啮合频率和固有频率。
本⽂研究内容可为风电机组齿轮箱的优化设计、故障、预防和处理提供技术基础。
关键词: 齿轮箱,固有频率,啮合频率,共振,RomaxABSTRACTGear box is the most transmission Parts in the Wind turbine,it is responsible for the low-speed wind turbine blade into the high-speed generator required to achieve the efficient transmission of energy and torque.Vibration is the main reason of wind turbine gear box failure , along with the increase of unit capacity, long-term adverse conditions in the gear box, due to the increase of the structure and flexibility to increase volume, caused more vibration problems.This paper mainly research gear box's vibration characteristics in the speed change, established gearbox vibration model based on Romax software,analysis of gearbox gear mesh frequency and levels of natural frequency.The contents of this paper provide wind turbine gearbox optimized design, failure for technical basis for the prevention and treatment.Key words : Gear Box , Natural frequency , Meshing frequency, Resonance, Romax⽬录摘要.................................................................... I ABSTRACT ................................................................... II 第1章绪论. (1)1.1选题背景和意义 (1)1.2国内外研究现状 (2)1.3本⽂⼯作 (3)1.4本章⼩结 (3)第2章风电机组齿轮箱⼒学特点 (4)2.1 前⾔ (4)2.2 风电机组齿轮箱机械结构 (4)2.3 风电机组齿轮箱外部载荷 (5)2.4 风电机组齿轮箱内部激励 (6)2.5 齿轮箱振动机理 (6)2.6 机械振动系统 (8)2.7本章⼩结 (10)第3章基于romax的风电齿轮箱建模 (11)3.1世界各地对romax的应⽤ (11)3.2 Romax软件介绍 (11)3.3 Romax建模 (12)3.4本章⼩结 (17)第4章固有频率和啮合频率分析 (18)4.1传动⽐及啮合频率计算 (18)4.2固有频率和啮合频率分析⽐较 (21)4.3本章⼩结 (22)第5章结论和展望 (23)5.1结论 (23)5.2展望 (23)参考⽂献 (24)致谢 (25)第1章绪论1.1 选题背景和意义在⼈类越来越渴望清洁能源和环保能源的⼤时代背景下,风电作为⼀种新兴的清洁能源,受到全世界⼈类的⼴泛关注。
齿轮箱中齿轮故障与振动分析
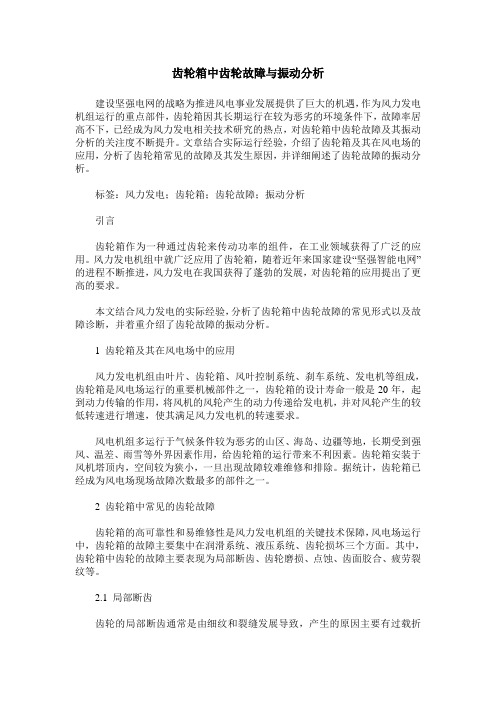
齿轮箱中齿轮故障与振动分析建设坚强电网的战略为推进风电事业发展提供了巨大的机遇,作为风力发电机组运行的重点部件,齿轮箱因其长期运行在较为恶劣的环境条件下,故障率居高不下,已经成为风力发电相关技术研究的热点,对齿轮箱中齿轮故障及其振动分析的关注度不断提升。
文章结合实际运行经验,介绍了齿轮箱及其在风电场的应用,分析了齿轮箱常见的故障及其发生原因,并详细阐述了齿轮故障的振动分析。
标签:风力发电;齿轮箱;齿轮故障;振动分析引言齿轮箱作为一种通过齿轮来传动功率的组件,在工业领域获得了广泛的应用。
风力发电机组中就广泛应用了齿轮箱,随着近年来国家建设“坚强智能电网”的进程不断推进,风力发电在我国获得了蓬勃的发展,对齿轮箱的应用提出了更高的要求。
本文结合风力发电的实际经验,分析了齿轮箱中齿轮故障的常见形式以及故障诊断,并着重介绍了齿轮故障的振动分析。
1 齿轮箱及其在风电场中的应用风力发电机组由叶片、齿轮箱、风叶控制系统、刹车系统、发电机等组成,齿轮箱是风电场运行的重要机械部件之一,齿轮箱的设计寿命一般是20年,起到动力传输的作用,将风机的风轮产生的动力传递给发电机,并对风轮产生的较低转速进行增速,使其满足风力发电机的转速要求。
风电机组多运行于气候条件较为恶劣的山区、海岛、边疆等地,长期受到强风、温差、雨雪等外界因素作用,给齿轮箱的运行带来不利因素。
齿轮箱安装于风机塔顶内,空间较为狭小,一旦出现故障较难维修和排除。
据统计,齿轮箱已经成为风电场现场故障次数最多的部件之一。
2 齿轮箱中常见的齿轮故障齿轮箱的高可靠性和易维修性是风力发电机组的关键技术保障,风电场运行中,齿轮箱的故障主要集中在润滑系统、液压系统、齿轮损坏三个方面。
其中,齿轮箱中齿轮的故障主要表现为局部断齿、齿轮磨损、点蚀、齿面胶合、疲劳裂纹等。
2.1 局部断齿齿轮的局部断齿通常是由细纹和裂缝发展导致,产生的原因主要有过载折断、疲劳折断、随机断裂等原因。
其中,过载折断是由于轴承损坏、外部冲击等原因,导致作用在齿轮上的应力持续较大,超过了齿轮的极限承受应力导致;疲劳折断多因为齿轮材料不佳,导致齿轮长期运行在交变应力下,产生长期疲劳,裂纹不断扩展,最终断裂;随机断裂的原因较多,比如有硬物进入齿轮啮合区、齿轮根部突遇外力冲击等。
齿轮箱振动信号分析及故障检测与诊断

齿轮箱振动信号分析及故障检测与诊断摘要:随着企业对机械设备的科学管理与维护的需求日益迫切,而齿轮箱在大型机械设备中更是得到广泛应用,对齿轮箱运行状态是否故障的检测和诊断成为企业的一大忧患。
最常用的对齿轮箱故障的检测便是通过对其四个不同部位加装加速度传感器,这种方法能在齿轮箱不停机的时候进行,便捷且节约时间。
本文则阐述了如何通过分析传感器采集到的振动信号,来检测和诊断齿轮箱的运行状态。
关键词:齿轮箱、故障诊断、特征统计值、相关性分析、机器学习随着科学技术的提高,各种机械设备的出现,人们对机械设备的管理与维护有着日益迫切的需求。
优质的机械维护不仅能降低企业运行的成本,更能提高机械的生产效率,因此为保障机械的安全与长久运行,企业也愈发重视对设备运行的监测。
在大型的旋转机械设备中,齿轮箱的应用十分频繁,在汽车、风机等中都屡见不鲜,但也极易损坏。
利用加速度传感器采集到的振动信号,然后根据振动信号进行分析,得出其是否故障或处于何种故障状态。
如何对振动信号的进行科学分析也自然成为备受关注的一大问题。
一、基于振动信号的主要特征统计值的故障检测模型首先,我们通过安装在正常运行的齿轮箱的四个不同部位的加速度传感器,采集正常状态下齿轮箱的振动信号。
对于出现不同故障的齿轮箱,我们同样采用安装加速度传感器的方式,采集各种故障状态下的振动信号数据。
当我们通过加速度传感器得到了大量振动信号后,可先对原始数据进行可视化处理(画出正态分布图像),直接观察正常状态下与不同故障状态下的振动信号的差异。
为了进一步的分析差异与规律,可计算出各组数据的主要统计特征值,并绘制正常状态下与不同故障状态下振动信号的平均值、峰值、峰度、偏度的折线图来呈现差异。
通过分析各项特征统计值的差异大小,最终确定用来描述差异的特征值。
但是由于传感器的振动信号数据庞大且无序,直接观察原始数据计算得到的统计特征值难以判断齿轮箱是否处于故障状态,故需要对原始数据进行一定的处理。
基于Romax的电动车减差速器振动特性分析
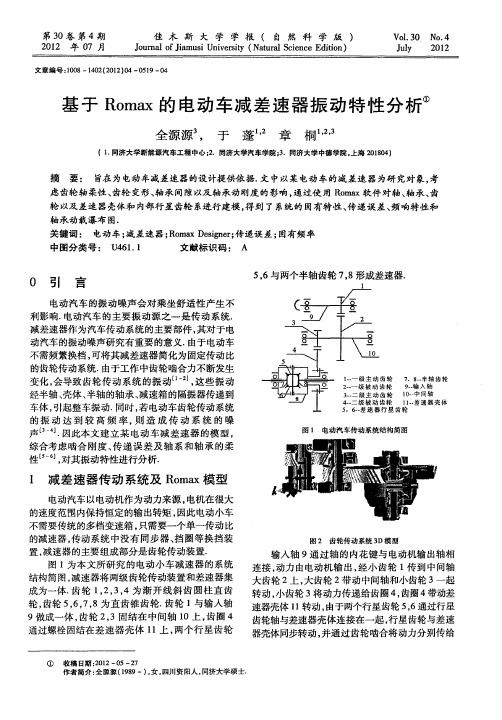
56 , 与两个半轴齿轮 7 8 , 形成差速器.
7 一半 轴 齿 轮 .8 9- -输入 轴 l - 间轴 0- 中
l一 】 差速 器壳 体 齿轮
图 1 电动汽车传动 系统结构 简图
1 减差 速 器传 动 系统 及 R ma 型 o x模
电动汽车以电动机作为动力来源 , 电机在很大 的速 度 范 围内保 持恒 定 的输 出转 矩 , 因此 电动小 车 不需要传统的多档变速箱 , 只需要一个单一传动 比 的减速 器 , 动 系统 中没 有 同 步器 、 圈 等换 挡 装 传 挡 置, 减速器的主要组成部分是齿轮传动装置. 图 1为本 文 所 研究 的 电 动小 车 减 速 器 的 系统 结构简图, 减速器将两级齿轮传动装置和差速器集 成 为一体 . 轮 12 3, 渐 开 线 斜 齿 圆 柱 直 齿 齿 , , 4为 轮, 齿轮 56 7 8为直齿锥齿轮. 轮 1与输入轴 , ,, 齿 9做 成一 体 , 轮 2, 齿 3固结 在 中 间 轴 1 0上 , 圈 4 齿 通过螺栓固结在差速器壳 体 l 上 , 1 两个行星齿轮
Ro l sa ei l Di tnc nTe t om e hFr SAPo To hlf ri u h t P n o f ot o np ts af1 i i nl
图 5 50 rm n 6 0/ i 一级齿轮副传递误差 曲线
第3 O卷 第 4期
21 年 O 月 02 7
佳 木 斯 大 学 学 报 ( 自 然 科 学 版 ) Ju f i u i nv ̄ t N tr ce c dt n omM o a s U ie i Jm y( auM S i eE io ) n i
Vo. 0 No. 13 4
带式输送机齿轮箱的振动噪声与对策

带式输送机齿轮箱的振动噪声与对策带式输送机齿轮箱是带式输送机传动系统中非常重要的组成部分,它的工作状态直接影响到整个输送机的运行效率和稳定性。
随着带式输送机的使用时间不断增长,齿轮箱的振动和噪声问题也逐渐凸显出来。
对于这一问题,我们需要对齿轮箱的振动噪声进行深入分析,并提出有效的对策措施,以确保带式输送机的正常运行。
一、齿轮箱振动噪声问题的分析1. 齿轮箱振动噪声的原因齿轮箱在工作过程中会受到很大的载荷和冲击力,同时受到不同传动零部件之间的摩擦和碰撞,这些因素都会导致齿轮箱振动和噪声的产生。
齿轮箱的设计和制造质量、润滑状态、使用环境等方面的问题也会对振动噪声产生影响。
2. 齿轮箱振动噪声的危害齿轮箱振动噪声不仅会给运行人员带来不适,还会影响整个输送机设备的稳定性和运行效率。
长期以来,振动噪声还会对齿轮箱的使用寿命造成影响,甚至会导致部件的损坏,对设备的安全性产生潜在威胁。
二、齿轮箱振动噪声对策措施为了解决带式输送机齿轮箱振动噪声的问题,我们需要综合考虑从齿轮箱的设计、制造、安装、使用和维护等方面,采取有效的对策措施。
1. 齿轮箱的设计和制造对于齿轮箱的设计和制造,我们需要选用高质量的齿轮箱零部件和材料,确保其制造精度和装配质量。
需要做好齿轮箱的减振设计,采用合理的减振措施,减少振动源的产生。
2. 齿轮箱的安装和使用在齿轮箱的安装和使用过程中,需要严格按照设备制造商的规定来安装和调整齿轮箱,保证齿轮箱和其他传动部件之间的配合准确度。
需要做好齿轮箱的润滑工作,以减少齿轮箱的摩擦和磨损,降低振动和噪声的产生。
3. 齿轮箱的维护和监测定期对带式输送机的齿轮箱进行维护和检测工作也是至关重要的。
在运行过程中,及时清洁齿轮箱,及时更换润滑油和密封件,排查齿轮箱的工作状态和振动噪声情况,确保其正常运行。
4. 振动噪声监测与控制技术利用振动噪声监测与控制技术来对齿轮箱的振动噪声进行实时监测和控制,及时发现齿轮箱的异常振动和噪声,并采取相应措施进行处理,确保齿轮箱的正常运行。
齿轮箱振动信号频谱分析与故障诊断
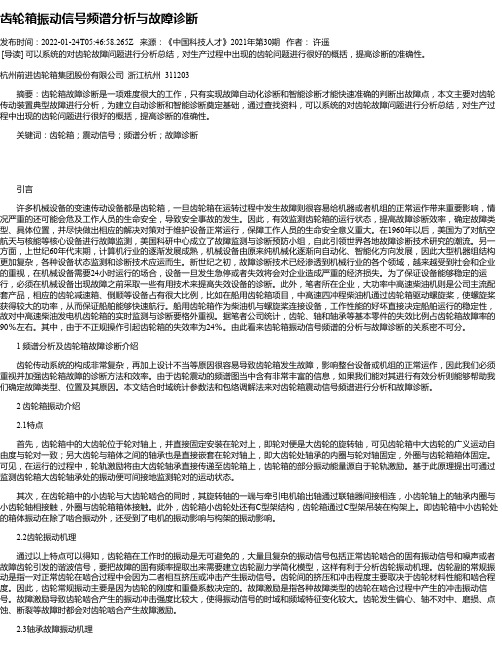
齿轮箱振动信号频谱分析与故障诊断发布时间:2022-01-24T05:46:58.265Z 来源:《中国科技人才》2021年第30期作者:许遥[导读] 可以系统的对齿轮故障问题进行分析总结,对生产过程中出现的齿轮问题进行很好的概括,提高诊断的准确性。
杭州前进齿轮箱集团股份有限公司浙江杭州 311203摘要:齿轮箱故障诊断是一项难度很大的工作,只有实现故障自动化诊断和智能诊断才能快速准确的判断出故障点,本文主要对齿轮传动装置典型故障进行分析,为建立自动诊断和智能诊断奠定基础,通过查找资料,可以系统的对齿轮故障问题进行分析总结,对生产过程中出现的齿轮问题进行很好的概括,提高诊断的准确性。
关键词:齿轮箱;震动信号;频谱分析;故障诊断引言许多机械设备的变速传动设备都是齿轮箱,一旦齿轮箱在运转过程中发生故障则很容易给机器或者机组的正常运作带来重要影响,情况严重的还可能会危及工作人员的生命安全,导致安全事故的发生。
因此,有效监测齿轮箱的运行状态,提高故障诊断效率,确定故障类型、具体位置,并尽快做出相应的解决对策对于维护设备正常运行,保障工作人员的生命安全意义重大。
在1960年以后,美国为了对航空航天与核能等核心设备进行故障监测,美国科研中心成立了故障监测与诊断预防小组,自此引领世界各地故障诊断技术研究的潮流。
另一方面,上世纪60年代末期,计算机行业的逐渐发展成熟,机械设备由原来纯机械化逐渐向自动化、智能化方向发展,因此大型机器组结构更加复杂,各种设备状态监测和诊断技术应运而生。
新世纪之初,故障诊断技术已经渗透到机械行业的各个领域,越来越受到社会和企业的重视,在机械设备需要24小时运行的场合,设备一旦发生急停或者失效将会对企业造成严重的经济损失。
为了保证设备能够稳定的运行,必须在机械设备出现故障之前采取一些有用技术来提高失效设备的诊断。
此外,笔者所在企业,大功率中高速柴油机则是公司主流配套产品,相应的齿轮减速箱、倒顺等设备占有很大比例,比如在船用齿轮箱项目,中高速四冲程柴油机通过齿轮箱驱动螺旋桨,使螺旋桨获得较大的功率,从而保证船舶能够快速航行。
RomaxDesigner--十个实例分析中文翻译

扭矩分配不均是由于下述弹性变形:齿的弯曲和接触变形;齿轮轴的扭曲和弯曲;齿廓和箱体的变形;滚子轴承的接触变形。采用传统有限元工具分析这些结构的组合和接触变形相当困难。
本例中设计空间巨大且是多维的,不可能手动的产生和检验每一种齿轮设计。螺旋角、压力角、模数、齿宽每种各十个变化值的组合可产生10000种候选设计。因此,唯一的方法就是使用高级优化设计方法实现各个参数的优化。
RomaxDesigner采用自动人工智能方法的搜索引擎来实现齿轮优化设计。图1结果显示了在优化中同时减少弯曲应力和接触应力所碰到的矛盾。
l 详细的齿轮几何结构模型
l 安装在带径向和轴向间隙的滚针轴承上的同步齿轮
l 外壳柔性的影响
各个齿的表面均作了基于平均制造公差的齿端修缘和鼓形量的修形。预测得到了驱动、滑行工况下的各种传动误差变化规律。同时使用旋转记码器(如图2)和Romax自行研制的设备测量了准静态传动误差,并作了相关对比。如图3预计和实验结果有很好的相关性。在滑行工况下的传动误差可以通过修改齿轮副安装误差和齿端修形而减小到可以接受的级别。
新轴承供应商提供的输入轴滚子轴承(如图1)过早失效。Romax承担该项项目检测两个轴承制造商的设计和制造品质,以确定其失效原因。
为了确定真实的制造质量,对新、旧和失效轴承作了详尽的测量。结果显示其中一个制造商设计的轴承有滚子端和挡边的接触结构,这种结构不能承受过高的轴向载荷,引起了滚子端(如图2)在短期内磨损。
各种复杂的轴/轴承布置形式的可靠性可通过使用RomaxDesigner独特全面的分析能力而得到准确的预测。
齿轮箱震动大的原因

齿轮箱震动大的原因
齿轮箱震动大的原因可能有以下几种:
1.齿轮制造或组装不当:齿轮的质量分布不均匀,造成不平衡,
从而引起振动。
2.齿轮配合不良:齿轮的啮合间隙不正确或齿轮副的配合不良会
导致振动增加。
3.齿轮损伤:齿轮表面磨损、剥落、疲劳裂纹等损伤会导致不正
常振动。
4.轴承故障:轴承损坏、润滑不良或装配不当都可能导致振动异
常。
5.轴弯曲:轴的弯曲或变形会导致轴承不稳定,引起振动。
6.油液问题:油液腐化、污染或不合适的润滑油会影响齿轮箱的
正常运行,引起振动。
7.转子不平衡:如果转子(如电机转子)存在不平衡,会导致振
动问题。
8.轴承支撑刚度不足:轴承支撑刚度不足会影响系统的稳定性,
产生振动。
9.齿轮箱结构松动:固定螺栓松动或齿轮箱的结构失稳会导致振
动异常。
10.过载运行:超负荷运行会导致齿轮箱振动过大,影响正常工
作。
11.齿轮箱使用环境:温度、湿度、尘埃等使用环境因素也可能
影响齿轮箱振动。
12.操作不当:操作人员不正确的使用或保养齿轮箱可能导致振
动异常。
为了避免齿轮箱震动过大,需要定期进行维护保养和检查,确保齿轮箱的结构和机械元件处于良好状态,并使用合适的润滑油和操作规范,以确保其正常运行。
如果出现震动异常的情况,应及时进行振动分析检测,排查问题,找出原因并进行相应的维修和校正。
齿轮箱振动简易诊断的方法

齿轮箱振动简易诊断的方法由于齿轮箱结构复杂,频率成分多,齿轮箱简易振动诊断方法一般应具备时域分析和频谱分析两种测试处理和分析手段,并在长期定时定点检测的基础上进行。
齿轮箱简易诊断方法一般由振动测试参数和简易诊断仪器选择、结构分析、测点选择、测试时间间隔选择、建立特征参数档案、判断标准选择和制定、定时或调整时间间隔进行振动测试、趋势分析、仪器定期标定九个部分组成。
齿轮箱简易诊断一般以箱体振动速度的测量作为首要选择的参数,振动速度的均方根值就是振动烈度,是检测中的重要指标,可配置手持式振动仪进行测试,也可以配置传感器为振动加速度的手持式振动仪进行测试,但测试效果不如采用振动速度传感器好。
因齿轮箱结构复杂,传递途径多,所以有条件的情况下可以采用对振动速度或加速度进行频谱分析作为检测参数,配置带简易频谱分析的数据采集器和相应的离线振动分析软件系统进行分析。
数据采集器可以代替便携式测振仪进行定期巡检,又具有简易频谱分析的功能,是齿轮箱故障诊断较好的简易诊断仪器。
振动烈度:必备,测量振动速度的均方根值,配置手持式振动仪进行测试。
根据相应的判别标准制定相应的警告界限值和故障界限值。
振动速度或加速度的频谱分析:有条件的情况下选配,测量振动速度或加速度的幅值谱,配置带简易频谱分析和检测的数据采集器和相应的离线振动分析软件系统进行测试分析。
根据相应的判别标准和特征频率等制定相应的频谱窄带警告界限值和故障界限值。
首先要对齿轮箱的结构进行认真细致的分析,重点是分析轴承座的部位,并分析哪些轴和齿轮是高速重载,以帮助确定测点的布置;分析电动机的转速和各传动链齿轮的齿数、传动比,以帮助确定各轴的转频、啮合频率;分析各轴承座等滚动轴承的型号,以帮助确定各滚动轴承的通过频率。
轴承座附近是天然的最佳测点。
齿轮箱中轴或轴承发生故障,其振动信号经过齿轮、轴和轴承传递到轴承座,再通过箱体传递到测点位置,振动信号在传递过程中幅值要衰减,高频成分幅值衰减比低频成分快得多。
- 1、下载文档前请自行甄别文档内容的完整性,平台不提供额外的编辑、内容补充、找答案等附加服务。
- 2、"仅部分预览"的文档,不可在线预览部分如存在完整性等问题,可反馈申请退款(可完整预览的文档不适用该条件!)。
- 3、如文档侵犯您的权益,请联系客服反馈,我们会尽快为您处理(人工客服工作时间:9:00-18:30)。
摘要齿轮箱作为风电机组中最重要的传动部件,负责将风轮叶片的低转速转换为发电机所需要的高转速,实现能量与扭矩的高效传输;振动是风电机组齿轮箱故障失效的主要原因,随着机组容量的增加, 长期处于恶劣条件下的齿轮箱,由于结构体积的增大和弹性增加,更易引发振动问题。
本文主要研究齿轮箱在变速变载下的振动特性,基于Romax软件建立齿轮箱的振动模型,分析齿轮箱各级齿轮的啮合频率和固有频率。
本文研究内容可为风电机组齿轮箱的优化设计、故障、预防和处理提供技术基础。
关键词: 齿轮箱,固有频率,啮合频率,共振,RomaxABSTRACTGear box is the most transmission Parts in the Wind turbine,it is responsible for the low-speed wind turbine blade into the high-speed generator required to achieve the efficient transmission of energy and torque.Vibration is the main reason of wind turbine gear box failure , along with the increase of unit capacity, long-term adverse conditions in the gear box, due to the increase of the structure and flexibility to increase volume, caused more vibration problems.This paper mainly research gear box's vibration characteristics in the speed change, established gearbox vibration model based on Romax software,analysis of gearbox gear mesh frequency and levels of natural frequency.The contents of this paper provide wind turbine gearbox optimized design, failure for technical basis for the prevention and treatment.Key words : Gear Box , Natural frequency , Meshing frequency, Resonance, Romax目录摘要 (I)ABSTRACT (II)第1章绪论 (1)1.1选题背景和意义 (1)1.2国内外研究现状 (2)1.3本文工作 (3)1.4本章小结 (3)第2章风电机组齿轮箱力学特点 (4)2.1 前言 (4)2.2 风电机组齿轮箱机械结构 (4)2.3 风电机组齿轮箱外部载荷 (5)2.4 风电机组齿轮箱内部激励 (6)2.5 齿轮箱振动机理 (6)2.6 机械振动系统 (8)2.7本章小结 (10)第3章基于romax的风电齿轮箱建模 (11)3.1世界各地对romax的应用 (11)3.2 Romax软件介绍 (11)3.3 Romax建模 (12)3.4本章小结 (17)第4章固有频率和啮合频率分析 (18)4.1传动比及啮合频率计算 (18)4.2固有频率和啮合频率分析比较 (21)4.3本章小结 (22)第5章结论和展望 (23)5.1结论 (23)5.2展望 (23)参考文献 (24)致谢 (25)第1章绪论1.1 选题背景和意义在人类越来越渴望清洁能源和环保能源的大时代背景下,风电作为一种新兴的清洁能源,受到全世界人类的广泛关注。
美国,德国,日本等国家都在积极地研究风电这一清洁、高效的发电方式。
在中国,风电也在蓬勃发展,金风,华锐,明阳这些企业已经走在了科研的前列,而东方汽轮机厂,华能也新建了风电厂。
从九十年代到2007年,我国风电机组装机总容量已超过560万kW,风电机组共计6469台,分布在全国22个省、市和自治区。
目前已装机的风电机组中,大部分采用的是水平轴结构,并采用齿轮箱作为风轮与发电机之间的传动部件。
齿轮箱负责将风轮叶片的低转速转换为发电机所需要的高转速,实现能量与扭矩的高效传输。
因此,齿轮箱是风电机组中最重要的传动部件。
风电齿轮箱具有质量大、重心高等特点,随着风电机组装机容量的不断增大,轮毂高度逐渐增加,齿轮箱受力变得复杂化,这就造成有些齿轮箱可能在设计上存在缺陷。
一般风电机组都安装在高山、荒野、海滩、海岛等风口处,受无规律的变向变负荷的风力作用以及强阵风的冲击,常年经受酷暑严寒和极端温差的影响,加之所处自然环境交通不便,齿轮箱安装在塔顶的狭小空间内,一旦出现故障,修复非常困难。
由于齿轮箱长期处于这样的恶劣条件下,会出现粘附磨损、腐蚀磨损、表面疲劳磨损、微动磨损和气蚀等失效形式,轻则导致润滑油失效,重则轴、轴承、轮齿的断裂,导致风电机组的停机[5]。
在变速变载这样的情况下,还会出现轮齿折断、齿面点蚀等的情况。
根据国际上有关机构对25台实际运行机组在3个月时间段的故障统计,机组各部件故障造成发电量损失见图1,齿轮箱是风电机组中故障率最高的部件,其主要失效形式为轮齿折断、齿面点蚀、齿面胶合、齿面磨损、齿面塑性变形[6]。
图1-1 风电机组故障所造成的发电量损失估计上述齿轮箱失效形式主要由风电机组所承受的变速、变载的复杂作用力引起,其故障特点皆可通过齿轮箱的振动信息表征出来。
因此,分析大型风电机组齿轮箱的振动特点,对于判断零件的失效原因,明确故障部位,并对齿轮箱进行优化设计具有指导意义。
1.2国内外研究现状1.2.1 国外研究现状由于人类认识到风能是清洁、可再生能源,因此世界的风力发电工业正以不同的方式提高风力发电的经济性,各国的公司也都在想方设法提高现有的技术水平,选择最优秀的设计方案。
对振动特性的研究和应用,美国、德国已经走在了世界的前列。
在国外,已经把齿轮的振动和噪声问题作为评价一个齿轮装置好坏的重要因素[7]。
齿轮的振动和噪声问题这个问题引起了世界范围内的广泛关注。
而对齿轮箱的振动模型的建立及其仿真系统已经在德、美这些发达国家中指导并应用在风力的发电当中了,对于齿轮箱的固有频率和啮合频率的研究已经处于世界前沿,使用了如有限元法、使用计算机软件等有效的手段,对影响齿轮箱振动的因素分析比较透彻,并能有效地减小这些影响因素,从而为风电机组齿轮箱的故障分析和判断提供了非常好的平台。
1.2.2 国内研究现状国内由于风力发电机行业本身起步较晚,很多风电技术还不成熟,处于探索阶段。
对于齿轮箱振动特性的分析还处于起步状态,在国内风力发电机上的运用还比较少。
目前我国还没有相关的振动标准,对整个齿轮箱系统模型进行了模态分析和动态响应分析,得出了齿轮箱的固有特性和箱体表面的振动响应曲线,而对成果的检验和应用还没有完善的技术。
但是,我们国家已经有企业致力于这方面的研究,通过建立各种模型,对轮齿进行受力分析,在变速变载的情况下研究振动特性,分析各种型号的固有频率、啮合频率等等已经有了很大的进步了.我国很多企业引进国外成熟技术,吸收消化,以提高国产化机组的制造技术。
采用与国外公司合作生产的方式引进技术,并允许国外风电机组制造厂商在我国投资设厂。
国内有关的风电机组制造、生产企业,已研制出、1.5Mw机组的关键部件,如齿轮箱和叶片等,并且750Kw的机组其本地化率已达到90%,还有如江苏千鹏公司,建立了该齿轮箱的直齿圆柱齿轮三维接触有限元模型和整个齿轮箱系统有限元模型,对直齿圆柱齿轮进行了接触分析,得到了直齿圆柱齿轮的综合啮合刚度激励,同时对整个齿轮箱系统模型进行了模态分析和动态响应分析,得出了齿轮箱的固有特性和箱体表面的振动响应曲线。
通过齿轮箱声压和声强实验,预测了该齿轮箱噪声值,且验证了有限元分析的有效性和准确性。
而在应用这方面国家也正在不遗余力地研究,相信在十年之内,我国的风电技术会引领世界[8]。
1.3 本文工作齿轮箱是风电机组主传动系统最主要的振动部位,本文对风电机组齿轮箱的振动特性进行深入研究,分析齿轮箱各级齿轮的固有频率与啮合频率之间的关系,主要研究内容如下:(1)分析风电机组齿轮箱的机械结构振动问题作了一些介绍,然后对齿轮箱的重要性,产生故障的原因,故障的类型等等作了一些详尽的阐述。
(2)在变速变载的情况下,,对机械振动系统特别是固有动态产生比较大的影响.选取了一组风电机组齿轮箱的数据作为参考,作了一些计算,计算了各级轮系的传动比,然后在风轮转速为15,22.34,85,128,306,457六种速度下分别计算了主轴,太阳轮,中间轮,高速轴的转速同步频率;行星级、中间级、高速级的啮合频率及10%的浮动范围。
(3)系统学习Romax软件, 并基于该软件建立齿轮箱振动模型。
分析变速、变载情况下齿轮箱的各阶振型和固有频率。
(4)对齿轮箱的固有频率和啮合频率进行比较分析,得到了共振区,指出在实际应用中应该尽量避开这些共振区。
1.4本章小结本章对风电机组振动特性的选题背景和意义作了一些阐述,并介绍了一些国内外研究现状,然后介绍了本文所要进行的工作,并介绍了主要研究内容。
第2章风电机组齿轮箱力学特点2.1 前言风电齿轮箱是一个复杂的弹性机械系统。
齿轮啮合时轮齿的弹性变形、时变啮合刚度、啮入出冲击、齿侧间隙、制造误差等都对轮齿静动力接触特性、系统动态性能、系统传动精度等有很大影响。
齿轮箱同时承受由原动机和负载引入的外部激励和由时变啮合刚度、齿轮传动误差和啮合冲击所引起的内部激励,其振动受轴、齿轮、轴承、等多种振动的影响,具有高度的非线性特点及耦合效应。
要综合考虑上述因素,用解析法难以全面描述其动力模型,其求解过程也极为繁杂,用实验方法可以测量系统的模态和响应,但难以直接测量齿轮接触区动态接触特性,也无法在设计阶段预估其动态特性并修改设计加以改善。
因此,有必要结合试验分析数据,研究齿轮系统动态特性综合数值分析方法,开发齿轮系统振动冲击数值仿真软件,实现它的动态响应分析[9]。
2.2 风电机组齿轮箱机械结构图2-1 风电齿轮箱机械结构图使用齿轮箱,可以将风电机转子上的较低转速、较高转矩,转换为用于发电机上的较高转速、较低转矩。
风电机上的齿轮箱,通常在转子及发电机转速之间具有单一的齿轮比。
对于600千瓦或750千瓦机器,齿轮比大约为1比50。
齿轮箱的结构包括输出轴、齿轮箱盖、大齿轮、小齿轮和齿轮箱,所述的齿轮箱内设有至少二个卡位,挡油罩上设有与卡位相对应的定位,挡油罩通过定位设置在齿轮箱的卡位上,齿轮箱盖上设有与挡油罩接合口相匹配的压圈,挡油罩与齿轮箱盖构成小齿轮和大齿轮的传动腔室.齿轮箱以三点支撑,输入为空心轴,采用锁紧盘,联接在主轴上,其余两点通过对称分布于前箱体扭力臂两端上的支座、弹性套联接在机舱底座上。