甲醇合成设备要点
甲醇装置简介和重点部位及设备(通用版)

( 安全技术 )单位:_________________________姓名:_________________________日期:_________________________精品文档 / Word文档 / 文字可改甲醇装置简介和重点部位及设备(通用版)Technical safety means that the pursuit of technology should also include ensuring that peoplemake mistakes甲醇装置简介和重点部位及设备(通用版)一、装置简介(一)装置发展及类型以一氧化碳和氢为原料合成甲醇的生产技术始于20世纪20年代。
到50年代末,我国已掌握了甲醇和合成甲醇催化剂的制备技术。
60年代未,我国又实现了合成氨和合成甲醇的联合生产(简称联醇),联醇技术降低了合成氨和甲醇的生产成本。
20世纪60年代,世界上,低压法合成甲醇新工艺技术实现了工业化。
低压法由于其能耗低,逐步取代了原来的高压法合成甲醇工艺,并得到了快速发展。
80年代初,我国研制的低压合成甲醇催化剂已达到国际水平。
联醇工艺技术是合成氨生产过程中,利用合成氨原料气中一氧化碳、二氧化碳与氢气同时生产甲醇。
联醇工艺技术由于生产方式灵活、工艺简单、原料利用率高、成本低、效益好,在我国中型合成氨装置得到普遍的推广。
甲醇生产一般以天然气、轻油、重油、煤及某些加工过程中产生的尾气为原料。
制得的原料气通过净化,得到一氧化碳、二氧化碳与氢气,经合成生成甲醇。
典型的流程包括原料气制备、原料气净化、甲醇合成和粗甲醇精馏等工序。
甲醇装置生产工艺所采用的原料气制备与净化工艺,与合成氨装置相同或相类似。
原料气制备工艺类型一般有:煤(焦)固定床气化工艺;煤(焦)气流床气化工艺;渣油、水煤浆部分氧化制气工艺;烃类(轻油、天然气)蒸汽转化制气工艺。
气体净化工艺类型也与合成氨原料气净化工艺类型相同,一般根据原料气的组成不同而采用不同的脱硫、变换、脱碳工艺技术。
甲醇合成设备
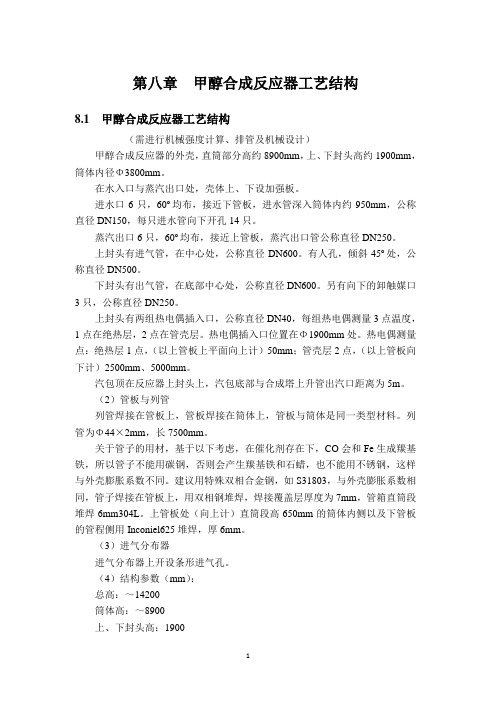
第八章甲醇合成反应器工艺结构8.1甲醇合成反应器工艺结构(需进行机械强度计算、排管及机械设计)甲醇合成反应器的外壳,直筒部分高约8900mm,上、下封头高约1900mm,筒体内径Φ3800mm。
在水入口与蒸汽出口处,壳体上、下设加强板。
进水口6只,60o均布,接近下管板,进水管深入筒体内约950mm,公称直径DN150,每只进水管向下开孔14只。
蒸汽出口6只,60o均布,接近上管板,蒸汽出口管公称直径DN250。
上封头有进气管,在中心处,公称直径DN600。
有人孔,倾斜45o处,公称直径DN500。
下封头有出气管,在底部中心处,公称直径DN600。
另有向下的卸触媒口3只,公称直径DN250。
上封头有两组热电偶插入口,公称直径DN40,每组热电偶测量3点温度,1点在绝热层,2点在管壳层。
热电偶插入口位置在Φ1900mm处。
热电偶测量点:绝热层1点,(以上管板上平面向上计)50mm;管壳层2点,(以上管板向下计)2500mm、5000mm。
汽包顶在反应器上封头上,汽包底部与合成塔上升管出汽口距离为5m。
(2)管板与列管列管焊接在管板上,管板焊接在筒体上,管板与筒体是同一类型材料。
列管为Φ44×2mm,长7500mm。
关于管子的用材,基于以下考虑,在催化剂存在下,CO会和Fe生成羰基铁,所以管子不能用碳钢,否则会产生羰基铁和石蜡,也不能用不锈钢,这样与外壳膨胀系数不同。
建议用特殊双相合金钢,如S31803,与外壳膨胀系数相同,管子焊接在管板上,用双相钢堆焊,焊接覆盖层厚度为7mm,管箱直筒段堆焊6mm304L。
上管板处(向上计)直筒段高650mm的筒体内侧以及下管板的管程侧用Inconiel625堆焊,厚6mm。
(3)进气分布器进气分布器上开设条形进气孔。
(4)结构参数(mm):总高:~14200筒体高:~8900上、下封头高:1900筒体内径:Φ3800绝热层高度:480列管管长:7500列管管径:Φ44×2管心距:51管数:4309根换热面积(以外径计算):4348m2(5)催化剂装填上管板上部绝热层:0.7854×3.82×0.48=5.44m3列管内冷却层:0.7854×0.042×7.5×4309=40.61m3总计46.06 m3催化剂型号:国产C307或XNC98铜基催化剂,粒度Φ5×5mm。
甲醇合成装置优化运行总结
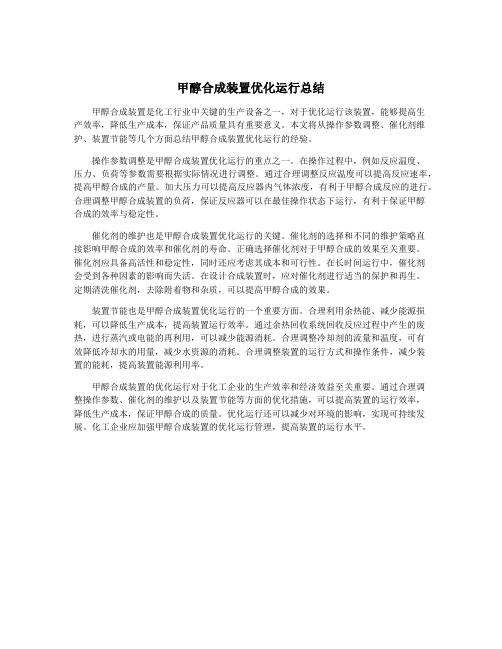
甲醇合成装置优化运行总结甲醇合成装置是化工行业中关键的生产设备之一,对于优化运行该装置,能够提高生产效率,降低生产成本,保证产品质量具有重要意义。
本文将从操作参数调整、催化剂维护、装置节能等几个方面总结甲醇合成装置优化运行的经验。
操作参数调整是甲醇合成装置优化运行的重点之一。
在操作过程中,例如反应温度、压力、负荷等参数需要根据实际情况进行调整。
通过合理调整反应温度可以提高反应速率,提高甲醇合成的产量。
加大压力可以提高反应器内气体浓度,有利于甲醇合成反应的进行。
合理调整甲醇合成装置的负荷,保证反应器可以在最佳操作状态下运行,有利于保证甲醇合成的效率与稳定性。
催化剂的维护也是甲醇合成装置优化运行的关键。
催化剂的选择和不同的维护策略直接影响甲醇合成的效率和催化剂的寿命。
正确选择催化剂对于甲醇合成的效果至关重要。
催化剂应具备高活性和稳定性,同时还应考虑其成本和可行性。
在长时间运行中,催化剂会受到各种因素的影响而失活。
在设计合成装置时,应对催化剂进行适当的保护和再生。
定期清洗催化剂,去除附着物和杂质,可以提高甲醇合成的效果。
装置节能也是甲醇合成装置优化运行的一个重要方面。
合理利用余热能、减少能源损耗,可以降低生产成本,提高装置运行效率。
通过余热回收系统回收反应过程中产生的废热,进行蒸汽或电能的再利用,可以减少能源消耗。
合理调整冷却剂的流量和温度,可有效降低冷却水的用量,减少水资源的消耗。
合理调整装置的运行方式和操作条件,减少装置的能耗,提高装置能源利用率。
甲醇合成装置的优化运行对于化工企业的生产效率和经济效益至关重要。
通过合理调整操作参数、催化剂的维护以及装置节能等方面的优化措施,可以提高装置的运行效率,降低生产成本,保证甲醇合成的质量。
优化运行还可以减少对环境的影响,实现可持续发展。
化工企业应加强甲醇合成装置的优化运行管理,提高装置的运行水平。
甲醇合成装置优化运行总结
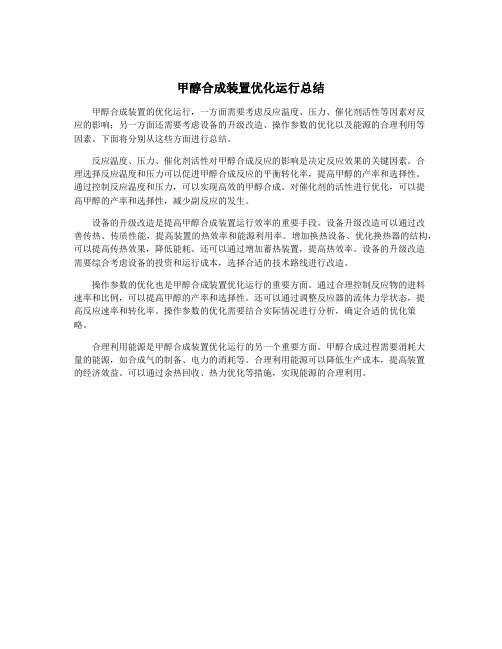
甲醇合成装置优化运行总结
甲醇合成装置的优化运行,一方面需要考虑反应温度、压力、催化剂活性等因素对反
应的影响;另一方面还需要考虑设备的升级改造、操作参数的优化以及能源的合理利用等
因素。
下面将分别从这些方面进行总结。
反应温度、压力、催化剂活性对甲醇合成反应的影响是决定反应效果的关键因素。
合
理选择反应温度和压力可以促进甲醇合成反应的平衡转化率,提高甲醇的产率和选择性。
通过控制反应温度和压力,可以实现高效的甲醇合成。
对催化剂的活性进行优化,可以提
高甲醇的产率和选择性,减少副反应的发生。
设备的升级改造是提高甲醇合成装置运行效率的重要手段。
设备升级改造可以通过改
善传热、传质性能,提高装置的热效率和能源利用率。
增加换热设备、优化换热器的结构,可以提高传热效果,降低能耗。
还可以通过增加蓄热装置,提高热效率。
设备的升级改造
需要综合考虑设备的投资和运行成本,选择合适的技术路线进行改造。
操作参数的优化也是甲醇合成装置优化运行的重要方面。
通过合理控制反应物的进料
速率和比例,可以提高甲醇的产率和选择性。
还可以通过调整反应器的流体力学状态,提
高反应速率和转化率。
操作参数的优化需要结合实际情况进行分析,确定合适的优化策
略。
合理利用能源是甲醇合成装置优化运行的另一个重要方面。
甲醇合成过程需要消耗大
量的能源,如合成气的制备、电力的消耗等。
合理利用能源可以降低生产成本,提高装置
的经济效益。
可以通过余热回收、热力优化等措施,实现能源的合理利用。
甲醇合成的工艺流程和设备
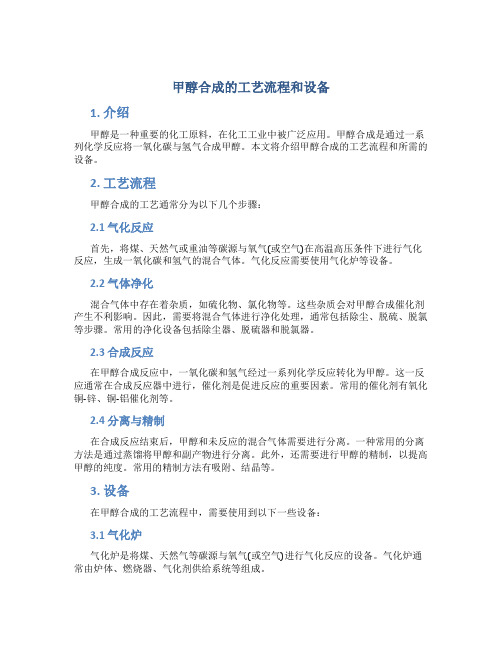
甲醇合成的工艺流程和设备1. 介绍甲醇是一种重要的化工原料,在化工工业中被广泛应用。
甲醇合成是通过一系列化学反应将一氧化碳与氢气合成甲醇。
本文将介绍甲醇合成的工艺流程和所需的设备。
2. 工艺流程甲醇合成的工艺通常分为以下几个步骤:2.1 气化反应首先,将煤、天然气或重油等碳源与氧气(或空气)在高温高压条件下进行气化反应,生成一氧化碳和氢气的混合气体。
气化反应需要使用气化炉等设备。
2.2 气体净化混合气体中存在着杂质,如硫化物、氯化物等。
这些杂质会对甲醇合成催化剂产生不利影响。
因此,需要将混合气体进行净化处理,通常包括除尘、脱硫、脱氯等步骤。
常用的净化设备包括除尘器、脱硫器和脱氯器。
2.3 合成反应在甲醇合成反应中,一氧化碳和氢气经过一系列化学反应转化为甲醇。
这一反应通常在合成反应器中进行,催化剂是促进反应的重要因素。
常用的催化剂有氧化铜-锌、铜-铝催化剂等。
2.4 分离与精制在合成反应结束后,甲醇和未反应的混合气体需要进行分离。
一种常用的分离方法是通过蒸馏将甲醇和副产物进行分离。
此外,还需要进行甲醇的精制,以提高甲醇的纯度。
常用的精制方法有吸附、结晶等。
3. 设备在甲醇合成的工艺流程中,需要使用到以下一些设备:3.1 气化炉气化炉是将煤、天然气等碳源与氧气(或空气)进行气化反应的设备。
气化炉通常由炉体、燃烧器、气化剂供给系统等组成。
3.2 除尘器除尘器用于去除混合气体中的固体颗粒物,以保证合成反应的正常进行。
除尘器可以采用重力沉淀、过滤等原理进行操作。
3.3 脱硫器脱硫器主要用于去除混合气体中的硫化物。
常用的脱硫方法有化学吸收脱硫、物理吸附脱硫等。
3.4 脱氯器脱氯器用于去除混合气体中的氯化物。
脱氯通常采用物理吸附或化学吸收的方式进行。
3.5 合成反应器合成反应器是进行甲醇合成反应的设备。
合成反应器通常由反应罐体、催化剂床层等组成。
3.6 分离设备分离设备主要用于将合成反应产物中的甲醇和副产物进行分离。
甲醇合成的工艺流程和设备

甲醇合成的工艺流程和设备甲醇合成是一种重要的工业化学反应,它是通过一系列的工艺流程和设备来完成的。
下面将详细介绍甲醇合成的工艺流程和设备。
第一步是气体净化。
原料气体主要是天然气或煤气,其中含有一些杂质,如硫化氢、二氧化碳、氨等。
这些杂质会对后续的合成反应产生不利影响,因此需要通过气体净化来去除。
气体净化主要包括硫化氢去除、二氧化碳去除和氨去除等步骤。
硫化氢可以通过催化氧化反应转化为硫,二氧化碳可以通过碱性溶液吸收,氨可以通过酸性溶液吸收。
第二步是合成气的制备。
合成气是甲醇合成的重要原料,它是一种混合气体,主要由一氧化碳和氢气组成。
合成气的制备一般采用催化剂转化法或气化法。
催化剂转化法是将天然气或煤气与蒸汽在催化剂的作用下反应生成合成气。
气化法是将煤、石油等碳质原料在高温、高压条件下气化生成合成气。
第三步是甲醇的合成。
合成气进入甲醇合成反应器后,经过一系列的反应生成甲醇。
甲醇合成一般采用低温高压条件下的催化反应。
常用的催化剂有铜-锌氧化物、铜-铝氧化物等。
甲醇合成反应的主要反应是一氧化碳和氢气生成甲醇。
反应温度一般在200-300摄氏度,压力一般在10-30兆帕。
甲醇的合成反应是一个平衡反应,需要通过适当的操作控制反应条件和催化剂的选择来提高甲醇的产率和选择性。
气体净化装置主要包括硫化氢去除器、二氧化碳去除器和氨去除器等。
硫化氢去除器通常采用催化氧化法,其中含有催化剂床层。
二氧化碳去除器采用碱性溶液吸收法,溶液中加入碱性物质,如钠碱。
氨去除器采用酸性溶液吸收法,溶液中加入酸性物质,如硫酸。
合成气制备装置主要包括催化转化装置和气化装置。
催化转化装置中含有催化剂床层,通过催化反应将天然气或煤气转化为合成气。
气化装置一般采用煤气化炉或石油气化炉,通过高温、高压条件下将煤或石油气化生成合成气。
甲醇合成反应器是甲醇合成的核心设备。
反应器一般采用垂直的压力容器,内部装有催化剂床层。
合成气经过加热后进入反应器,与催化剂发生反应生成甲醇。
年产10万吨煤合成甲醇工厂设计要点

年产10万吨煤合成甲醇工厂设计要点煤合成甲醇工厂设计要点煤合成甲醇工厂是利用煤作为原料制备甲醇的生产设备。
煤作为一种丰富的化石燃料,具有储量大、价格低廉以及可再生的特点,因此利用煤来生产甲醇具有较大的经济和环境优势。
下面我们将介绍设计一个年产10万吨煤合成甲醇工厂的要点。
1. 工艺选择煤合成甲醇工厂的工艺选择对于整个工厂的设计有至关重要的影响。
目前常见的工艺路线有间接法、直接法和半直接法等。
在选择工艺路线时需要考虑甲醇产率、甲醇纯度、能耗和设备投资等因素,综合比较各种工艺路线的优势和劣势,选择适合的工艺路线。
2. 原料处理煤是煤合成甲醇工厂的主要原料,但煤中含有许多杂质,如灰分、硫分、氮分等,需要进行原料处理。
原料处理的主要目的是去除杂质,提高煤的纯度,减少后续工艺过程中的能耗和设备磨损。
原料处理的主要工艺包括煤炭碎煤、煤炭洗选、煤泥脱水等。
3. 反应和分离煤合成甲醇的反应过程是核心环节,主要包括原料气化、合成气净化、合成气变换和甲醇合成等。
在反应过程中,需要注意反应温度、反应压力、反应速率等参数的控制,以保证反应的高效进行。
在分离过程中,主要包括甲醇的分离和副产物的回收利用。
4. 能源利用煤合成甲醇工厂需要大量的能源供应,包括煤炭燃烧产生的热能、原料气化产生的合成气以及电力等。
在能源利用上需要考虑能源的高效利用和节能减排。
通过合理设计能源系统,进行余热回收、废气处理和烟气排放控制等措施,以减少能源消耗和环境污染。
5. 设备选型煤合成甲醇工厂设备的选型对于工艺的高效运行和产品质量的保证至关重要。
设备选型需要考虑设备的质量、性能、可靠性和维修保养等方面。
此外,还需要考虑设备的运行安全和环境保护要求,选择符合国家标准和行业规范的设备。
6. 自动化控制煤合成甲醇工厂的生产过程复杂,需要进行自动化控制来实现对生产过程的监控和调控。
自动化控制系统可以实现对设备运行状态、工艺参数和产品质量等方面的实时监测和调节,提高生产效率和产品质量。
甲醇合成的生产工艺流程及主要设备

任务1 甲醇合成的工艺条件
二、压力 压力也是甲醇合成反应过程的重要工艺条件之一。从热力学分析,甲醇
合成是体积缩小的反应,因此增加压力对平衡有利,可提高甲醇平衡产 率。在高压下,因气体体积缩小了,则分子之间互相碰撞的机会和次数 就会增多,甲醇合成反应速率也就会因此加快。因而,无论对于反应的 平衡或速率,提高压力总是对甲醇合成有利。但是,合成压力不是单纯 由一个因素来决定的,它与选用的催化剂、温度、空间速度、碳氢比等 因素都有关系。而且,甲醇平衡浓度也不是随压力的增加而成比例的增 加,当压力提高到一定程度也就不再往上增加。
上一页 下一页 返回
任务1 甲醇合成的工艺条件
另外,空速增大到一定程度后,催化床温度将不能维持。在甲醇合成生 产中,空速一般控制在10000~30000h-1之间。
综上所述,影响甲醇合成反应过程的工艺条件有温度、压力、气体组成、 空速等因素,在具体情况下,针对一定的目标,都可以找到该因素的最 佳或较佳条件,然而这些因素间又是互相有联系的。
任务1 甲醇合成的工艺条件
生产中合理的氢碳比应比化学计量比略高些,按化学计量比值,f值或 M值约为2,实际上控制得略高于2,即通常保持略高的氢含量。过量 的氢对减少羰基铁的生成与高级醇的生成,及延长催化剂寿命起着有益 的作用。
此外,原料气中含有一定量的CO2,可以减少反应热量的放出,利于 床层温度控制,同时还抑制二甲醚的生成。
三、低压法甲醇合成工艺流程 近年来,甲醇的合成,大多采用铜系低温高活性催化剂,可在5MPa
低压下将(CO+H2)合成气体或含有CO2的(CO+H2) 合成气 进行合成,并得到较高的转化率。
上一页 下一页 返回
任务2 甲醇合成的工艺流程
1.ICI低压法甲醇合成工艺流程 1966年,英国ICI公司在成功地开发了铜基低压甲醇合成催化剂
甲醇生产工艺流程及设备认知 甲醇合成反应器的选用
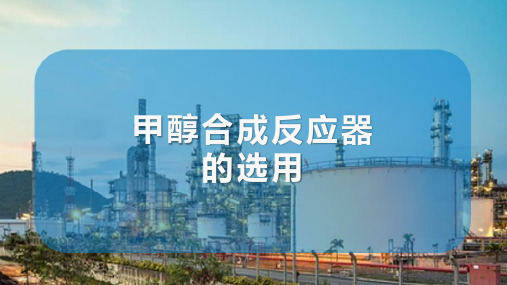
冷激式绝热反应器的温度分布如图
反应器的结构
02
列管式等温反应器
温度易于控制,单 程转化率较高,循 环气量小,能量利 用较经济,反应器 生产能力大,设备 结构紧凑。
03
反应器的材质
反应器的材质
合成气中含有氢和一氧化碳
氢气在高温高压下会和钢材发生脱碳反应,降低钢材的性能; 一氧化碳在高温高压下易和铁发生作用生成五羰基铁,引起
设备的腐蚀
小
结
生产工艺对反应器的要求 反应器的结构 反应器的材质
02
反应器的结构
反应器的结构
根据反应热移出方式不同,可分为绝热式和等温式两大类; 根据冷却方式不同,可分为直接冷却的冷激式和间接冷却 的列管式两大类。
反应器的结构
01
冷激式绝热反应器
结构简单,催化剂 装填方便,生产能 力大,但要有效控 制反应温度,避免 过热现象发生
反应器的结构
01
冷激式绝热反应器
甲醇合成反应器 的选用
甲醇通过什么原料制取? 生产原理是什2 反应器的结构 03 反应器的材质
01
生产工艺对反应器的要求
生产工艺对反应器的要求
合成反应器及时将反应放出的热量移出; 充分利用合成塔的容积,尽量多装催化剂; 合成塔的流体阻力小,结构必须简单、紧凑、坚固、气密性好; 尽量组织热量交换,充分利用反应余热,降低能耗; 合成反应器应能防腐蚀; 便于操作控制和工艺参数调节。
甲醇合成装置工艺流程及关键控制点分析简介
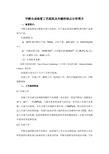
甲醇合成装置工艺流程及关键控制点分析简介一、装置简介:甲醇合成装置是以煤基合成气为原料,生产满足要求的MTO级甲醇产品和氢气产品。
(1)装置能力:a)MTO级甲醇日产量:5500t,小时产量:229.167t(以100%CH3OH 计)。
b)日输出氢气量:15456 Nm3,小时输出量644Nm3,(以99.5% H2计)。
(2)年操作小时:8000小时。
(3)专利技术来源:装置引进英国DPT(Davy Process Technology)公司的工艺包和JMC(Johnson Matthey Catalyst)催化剂。
(4)装置主要由以下几个工艺单元组成:压缩工序、合成工序、精馏工序、氢回收工序、蒸汽冷凝液回收工序、甲醇裂解制氢二、工艺流程简述2.1压缩工序压缩工序合成气压缩机和循环气压缩机。
来自界区(低温甲醇洗)的煤基合成气~30℃、~5.2MPaG,与膜分离来的富氢气混合后,依次进入合成气分离器、合成气压缩机,并在合成气压缩机中增压到~7.8MPaG。
增压后的合成气进入合成气净化预热器,用蒸汽加热并喷入锅炉给水以水解其中的COS,然后进入合成气净化槽,脱除残留的对合成催化剂有毒害的微量组份。
合成气净化槽中装填有净化催化剂。
2.2 合成工序甲醇合成回路由两个串联在一起的蒸汽上升式反应塔组成。
这种串联方式比传统流程在催化剂与设备投资上要更为经济。
甲醇合成塔为径向流反应器,气体通过装填在壳侧的催化剂,发生甲醇合成反应。
反应器内温度由管内上升的蒸汽控制。
副产蒸汽过热后送出界区。
来自合成气压缩机的净化后的合成气分为两股,其中大部分合成气和循环气混合,经过合成回路1号中间换热器加热后,进入1号甲醇合成塔进行甲醇合成反应。
甲醇合成反应在~280℃、~7.46MPaG下,在催化剂的作用下进行,该反应为放热反应。
主要的两个反应如下:CO + 2H2→ CH3OH + QCO2 + 3H2 → CH3OH + H2O + Q反应热副产~2.1MPaG的中压饱和蒸汽,经1号甲醇合成汽包分离后,进入装置内蒸汽总管。
甲醇的技术装备与设施
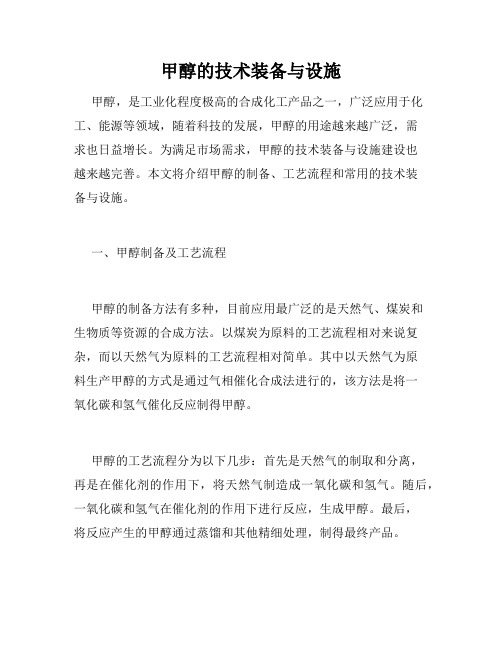
甲醇的技术装备与设施甲醇,是工业化程度极高的合成化工产品之一,广泛应用于化工、能源等领域,随着科技的发展,甲醇的用途越来越广泛,需求也日益增长。
为满足市场需求,甲醇的技术装备与设施建设也越来越完善。
本文将介绍甲醇的制备、工艺流程和常用的技术装备与设施。
一、甲醇制备及工艺流程甲醇的制备方法有多种,目前应用最广泛的是天然气、煤炭和生物质等资源的合成方法。
以煤炭为原料的工艺流程相对来说复杂,而以天然气为原料的工艺流程相对简单。
其中以天然气为原料生产甲醇的方式是通过气相催化合成法进行的,该方法是将一氧化碳和氢气催化反应制得甲醇。
甲醇的工艺流程分为以下几步:首先是天然气的制取和分离,再是在催化剂的作用下,将天然气制造成一氧化碳和氢气。
随后,一氧化碳和氢气在催化剂的作用下进行反应,生成甲醇。
最后,将反应产生的甲醇通过蒸馏和其他精细处理,制得最终产品。
二、甲醇的技术装备与设施1. 合成反应装置合成反应装置是甲醇制备工艺的核心设备之一,通常包括加气管、催化剂层和冷却水管等附件,它们的结构设计和装配工艺对甲醇合成反应的效果有重要影响。
目前从合成装置技术方面来看,常用的有固定床反应器、移动床反应器,流化床反应器等。
2. 精馏装置精馏装置是使甲醇精馏纯化、去除杂质的重要设备,包括粗精馏器、回流塔、精馏塔、加热系统、冷却系统等部分。
甲醇的精馏过程非常复杂,因此精馏塔的结构和操作控制至关重要。
通常采用的装置有常压塔、减压塔、等压塔和蒸汽回流塔等,其中蒸汽回流塔是目前甲醇精馏的主要方式。
3. 生产储罐生产储罐是指用于储存甲醇的设备,通常采用圆柱形或球形储罐,包括罐壁、罐盖、进气口、排出口、抽气口和检查孔等部分,有一定的环保和安全措施。
甲醇的储存需要安全性强且环保的设施,以免对人体和环境造成危害。
4. 废气回收设备甲醇合成过程会产生大量的废气,包括一氧化碳、二氧化碳、甲烷、氢气等物质。
因此,甲醇生产场地需要配置废气回收设备,用于收集和处理废气,减少对环境的污染和腐蚀。
甲醇合成的工艺流程和设备

甲醇合成的工艺流程和设备工艺流程:1. 一氧化碳和氢气的制备:首先,通过煤炭气化或天然气重整等方法制备一氧化碳和氢气,然后进行净化和分离处理,得到高纯度的一氧化碳和氢气。
2. 催化反应:将一氧化碳和氢气送入反应器中,在一定的温度和压力条件下,通过催化剂的作用发生一系列反应,将一氧化碳和氢气转化为甲醇。
3. 分离纯化:将反应产物中的甲醇、水蒸汽和未反应的一氧化碳、氢气等组分进行分离和纯化处理,得到高纯度的甲醇产品。
设备:1. 一氧化碳和氢气制备装置:包括气化炉、重整炉、净化器、分离塔等设备。
2. 催化反应器:通常采用固定床反应器,内部填充有高效催化剂,能够保证反应物的充分接触和反应。
3. 分离纯化装置:包括精馏塔、萃取塔、膜分离装置等,用于将反应产物中的各种组分进行分离和纯化处理。
以上是甲醇气相合成的工艺流程和设备,通过精心设计和优化,可以实现甲醇的高效生产,满足不同行业的需求。
甲醇气相合成是一种复杂的化学工艺过程,涉及到高温高压、催化剂选择、反应器设计等多个方面的技术问题。
在甲醇的生产过程中,存在一系列的技术挑战,包括反应的选择性和产率问题、催化剂的稳定性和寿命等。
针对这些挑战,科学家和工程师们提出了许多解决方案,并对工艺流程和设备进行了深入的研究和优化。
在工艺流程方面,甲醇气相合成主要包括气体净化、气体反应和产物分离三个阶段。
首先,气体净化要求将一氧化碳和氢气分离、净化并去除其它杂质;然后在反应阶段,一氧化碳和氢气在一定的温度、压力和催化剂存在下发生反应,生成甲醇;最后在产物分离阶段,需要对反应产物中的甲醇、水蒸汽、未反应的一氧化碳、氢气等组分进行分离、纯化和回收。
这些工艺环节都需要设计合适的设备和优化的操作条件,以保证甲醇高效产出且质量优良。
对于设备的选择和设计,首先需要考虑气体净化部分的设备选型,包括气化炉、重整炉、净化器和分离塔等。
这些设备需要具备耐高温、高压、耐腐蚀等特性,同时还要保证反应物料的净化和分离效果。
粗甲醇合成—甲醇合成设备(煤制甲醇课件)
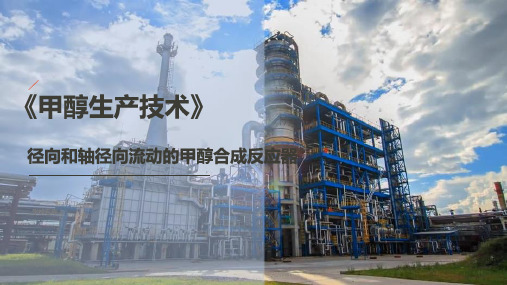
内冷冷管连续换热式甲醇合成反应器
催化剂筐是合成塔的内件的核心部件。催化剂筐的外面包有玻璃纤维(或石 棉)保温层,以防止催化剂筐大量散热。上部设有催化剂筐盖,下部有筛孔板, 在筛孔板上放有一层不锈钢网,避免放置在上面的催化剂漏下。在催化剂筐里装 有数根冷管,冷管是由内冷管、中冷管及外冷管所组成的三套管,其中内冷管与 中冷管下端的环缝用满焊焊死,另一端敞开,这样可以使内冷管与中冷管间形成 一层很薄的不流动的滞气层从而起到隔热作用,这样呢,进塔气体自下向上通过 内冷管时,则不与中心管与外冷管内的气体进行换热,故而冷气的温升很小,内 冷管仅起输送气体的作用。冷气经中冷管与外冷管的环隙自上向下流动的过程, 与外部催化剂床层进行热交换作用,带走催化剂床层的热量。
热交换器
开工加热器是为了保证催化剂的升温还原,
内冷冷管连续换热式甲醇合成反应器
使学生掌握不同的内冷冷管连续 换热式甲醇合成反应器的结构及 工原理。
教学目的
教学
重点:三套管并流型甲醇合成反应器内流 程,其他内冷冷管反应器内流体流程。 难点:三套管并流型甲醇合成反应器结构。
教学重点与难点
内冷冷管连续换热式甲醇合成反应器
使学生掌握不同的连续换热式催 化剂筐的结构及换热原理。
教学目的
教学
重点:连续换热式催化剂筐的结构及换 热原理 难点:流体在催化剂筐内的流动方式。
教学重点与难点
连续换热式催化剂筐
根据合成塔内流体流动方式和换热方式不同将合成塔分为以下三类:
连续换热式
合成塔
多段换热式
径向式
连续换热式催化剂筐
根据换热介质的的不同将连续换热式催化剂筐进行分类
连续换热式催化剂筐
催化剂床层的实 际温度分布
甲醇合成的主要设备
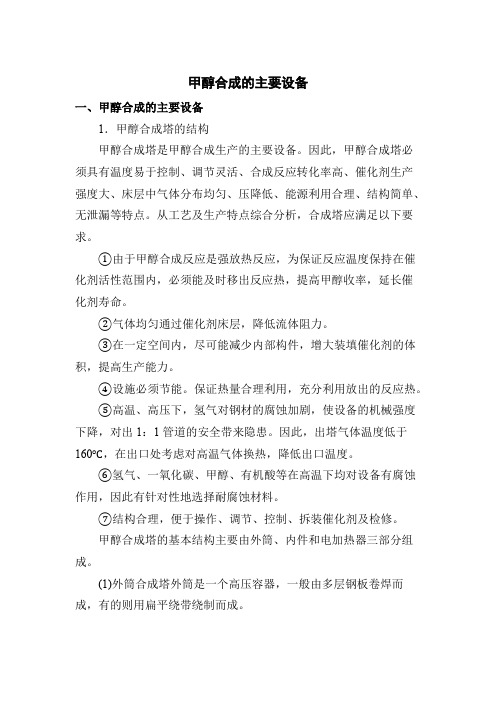
甲醇合成的主要设备一、甲醇合成的主要设备1.甲醇合成塔的结构甲醇合成塔是甲醇合成生产的主要设备。
因此,甲醇合成塔必须具有温度易于控制、调节灵活、合成反应转化率高、催化剂生产强度大、床层中气体分布均匀、压降低、能源利用合理、结构简单、无泄漏等特点。
从工艺及生产特点综合分析,合成塔应满足以下要求。
①由于甲醇合成反应是强放热反应,为保证反应温度保持在催化剂活性范围内,必须能及时移出反应热,提高甲醇收率,延长催化剂寿命。
②气体均匀通过催化剂床层,降低流体阻力。
③在一定空间内,尽可能减少内部构件,增大装填催化剂的体积,提高生产能力。
④设施必须节能。
保证热量合理利用,充分利用放出的反应热。
⑤高温、高压下,氢气对钢材的腐蚀加剧,使设备的机械强度下降,对出1:1管道的安全带来隐患。
因此,出塔气体温度低于160℃,在出口处考虑对高温气体换热,降低出口温度。
⑥氢气、一氧化碳、甲醇、有机酸等在高温下均对设备有腐蚀作用,因此有针对性地选择耐腐蚀材料。
⑦结构合理,便于操作、调节、控制、拆装催化剂及检修。
甲醇合成塔的基本结构主要由外筒、内件和电加热器三部分组成。
(1)外筒合成塔外筒是一个高压容器,一般由多层钢板卷焊而成,有的则用扁平绕带绕制而成。
(2)内件内件由催化剂筐和换热器两部分组成。
催化剂筐是填装催化剂进行合成反应的组合件。
换热器分两类,一是为满足开车时催化剂活性温度,对原料气进行加热的需要,可采用电加热器;二是对进出催化剂床层的反应气体进行热交换,以达到工艺生产要求。
①催化剂筐。
甲醇合成塔内件的设计主要是催化剂筐的设计,它的形式与结构需尽可能实现催化剂床层内最佳温度分布,一般连续冷管有自热式和外冷式两种结构。
自热式是利用反应热,用冷原料气为冷却剂,使催化剂床层降温,原料气体同时被加热。
自热式又分为单管逆流、双套管并流、三套管并流、单管并流以及U形管式。
外冷式是冷却剂采用其他介质进行冷却。
②换热器。
换热器的作用是回收合成气反应后的热量及提高冷原料气的温度。
甲醇合成的工艺流程和设备

甲醇合成的工艺流程和设备甲醇是一种重要的化工原料,广泛应用于化工、医药、食品等领域。
甲醇的合成工艺流程主要包括天然气制甲醇和煤制甲醇两种。
以下将以天然气制甲醇为例,介绍甲醇的合成工艺流程和设备。
1. 甲醇合成工艺流程甲醇的合成主要通过气相合成法进行,该方法通过一系列复杂的催化反应将一氧化碳和氢气合成甲醇。
具体的工艺流程如下:- 天然气→天然气净化→变化转换反应→合成气→合成气净化→合成气改质→甲醇合成→甲醇回收2. 甲醇合成设备甲醇合成设备主要包括催化反应器、冷凝器、分离塔等:- 催化反应器:将一氧化碳和氢气催化反应生成甲醇,需要具有较高的反应活性和选择性。
- 冷凝器:用于冷却和凝结合成气中的甲醇,使其形成液体甲醇。
- 分离塔:用于将液体甲醇从残余的气相中分离出来,保证甲醇的纯度和回收率。
3. 甲醇生产过程甲醇生产过程主要包括天然气的催化转变、合成气的制备、甲醇的合成和甲醇的回收等环节。
整个过程需要耗费大量的热能和电能,因此需要具备较为完备的能源设施和配套设备。
总的来说,甲醇的合成工艺流程较为复杂,需要涉及多个催化反应和分离过程,所需要的设备也比较繁杂。
企业在进行甲醇合成生产时,需要充分考虑到工艺流程和设备配置,确保生产过程的高效稳定。
甲醇是一种重要的化学品,其合成工艺的复杂性和对能源的依赖性使得甲醇工业在全球范围内备受关注。
天然气制甲醇是目前全球最为主流的甲醇生产工艺。
下面将详细介绍甲醇的合成工艺流程和设备,以及在甲醇生产过程中可能出现的关键技术和挑战。
4. 甲醇合成过程甲醇的合成工艺主要涉及以下几个过程:4.1 天然气制备合成气首先,天然气需要在天然气净化设备中进行净化处理,去除其中的硫化氢、二氧化碳和水等杂质。
通过石灰石和干燥剂的吸附、脱硫等处理,可使天然气达到合成气制备的要求。
然后,经催化转化反应,天然气中的甲烷和水蒸气进行高温反应,生成一氧化碳和氢气,形成合成气。
4.2 合成气的制备合成气是由一氧化碳和氢气所组成的气体混合物,它是甲醇合成的重要中间产物。
甲醇合成塔的产气原理

甲醇合成塔的产气原理甲醇合成塔是一种用于合成甲醇的重要设备。
甲醇合成塔的产气原理主要涉及三个步骤:脱氢、气相反应和冷却净化。
下面将详细介绍这些步骤。
首先是脱氢步骤。
在甲醇合成过程中,甲烷和水蒸气通过催化剂床层进行接触,催化剂床层中的催化剂会促使甲烷和水蒸气发生脱氢反应,生成CO和H2。
这个步骤是甲醇合成的关键步骤,也是产气的起始步骤。
其次是气相反应步骤。
在催化剂床层中,CO和H2与来自脱氢反应的甲烷和水蒸气一起进一步发生反应。
这些反应产生的主要产物是甲醇(CH3OH)和副产物(如二甲醚、甲基丙烯酸等)。
这个步骤是甲醇合成的核心步骤,通过控制反应温度、催化剂种类和反应压力等参数,可以实现高效率的甲醇合成。
最后是冷却净化步骤。
在气相反应后,产生的气体中含有一些固体颗粒和液滴,还有部分未反应的甲醇蒸汽。
为了净化产气,必须对产气进行冷却和净化处理。
首先通过冷却器将产气冷却到较低的温度,使一部分液态甲醇和水分凝结成液滴;然后通过净化设备去除固体颗粒,并将未反应的甲醇回收利用。
甲醇合成塔的产气原理可以归纳为以下几点:1. 脱氢反应:甲烷和水蒸气在催化剂床层上发生脱氢反应,生成CO和H2。
2. 气相反应:CO和H2与来自脱氢反应的甲烷和水蒸气一起进一步发生反应,产生甲醇和副产物。
3. 冷却净化:产气通过冷却器冷却,并经过净化设备去除固体颗粒和未反应的甲醇蒸汽。
甲醇合成塔的产气原理是一个复杂的过程,需要合理控制各个步骤的条件和参数,以提高甲醇的产率和纯度。
此外,还需要注意催化剂的选择和催化剂床层的维护,以保证甲醇合成塔的正常运行和长久稳定的产气效果。
煤制甲醇工艺与设备概述
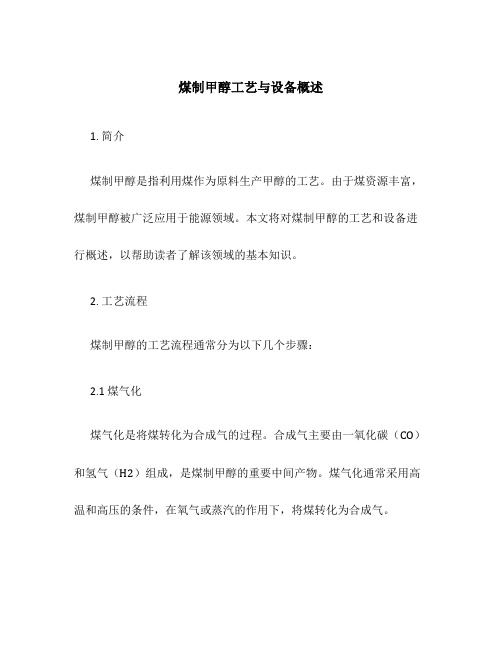
煤制甲醇工艺与设备概述1. 简介煤制甲醇是指利用煤作为原料生产甲醇的工艺。
由于煤资源丰富,煤制甲醇被广泛应用于能源领域。
本文将对煤制甲醇的工艺和设备进行概述,以帮助读者了解该领域的基本知识。
2. 工艺流程煤制甲醇的工艺流程通常分为以下几个步骤:2.1 煤气化煤气化是将煤转化为合成气的过程。
合成气主要由一氧化碳(CO)和氢气(H2)组成,是煤制甲醇的重要中间产物。
煤气化通常采用高温和高压的条件,在氧气或蒸汽的作用下,将煤转化为合成气。
2.2 合成气净化由于煤气化过程中产生的合成气中含有杂质和硫化物等物质,需要通过净化工艺去除这些杂质。
常见的净化工艺包括冷却、洗涤、吸附等。
2.3 甲醇合成甲醇合成是将合成气通过催化剂催化反应,生成甲醇的过程。
常见的催化剂有铜锌铝催化剂和铁锆催化剂等。
甲醇合成反应通常在中温和中压下进行。
2.4 甲醇净化甲醇合成后,需要进行进一步的净化工艺,以去除残留的杂质和不纯物质。
常见的甲醇净化工艺包括蒸馏、吸附和冷凝等。
3. 设备介绍煤制甲醇的设备包括煤气化设备、合成气净化设备、甲醇合成设备和甲醇净化设备。
3.1 煤气化设备煤气化设备通常包括气化炉、气化反应器和气化器。
气化炉是将煤转化为合成气的核心设备,常见的气化炉包括固定床气化炉和流化床气化炉。
气化反应器主要用于气体化学反应,将煤转化为合成气。
气化器用于提供气化反应所需的热量。
3.2 合成气净化设备合成气净化设备通常包括冷却器、洗涤塔和吸附塔。
冷却器用于降低合成气的温度,以便进行后续的净化工艺。
洗涤塔用于去除合成气中的硫化物和杂质,常见的洗涤液包括水和胺溶液。
吸附塔用于吸附合成气中的二氧化碳和其他杂质。
3.3 甲醇合成设备甲醇合成设备通常包括加氢器、催化剂床和换热器。
加氢器用于将合成气中的一氧化碳和二氧化碳转化为甲醇。
催化剂床用于催化甲醇合成反应。
换热器用于提供反应所需的热量。
3.4 甲醇净化设备甲醇净化设备通常包括蒸馏塔、吸附塔和冷凝器。
甲醇合成装置优化运行总结
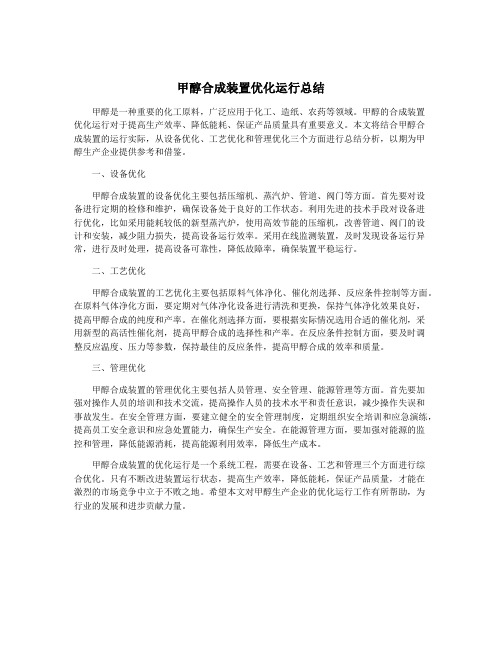
甲醇合成装置优化运行总结甲醇是一种重要的化工原料,广泛应用于化工、造纸、农药等领域。
甲醇的合成装置优化运行对于提高生产效率、降低能耗、保证产品质量具有重要意义。
本文将结合甲醇合成装置的运行实际,从设备优化、工艺优化和管理优化三个方面进行总结分析,以期为甲醇生产企业提供参考和借鉴。
一、设备优化甲醇合成装置的设备优化主要包括压缩机、蒸汽炉、管道、阀门等方面。
首先要对设备进行定期的检修和维护,确保设备处于良好的工作状态。
利用先进的技术手段对设备进行优化,比如采用能耗较低的新型蒸汽炉,使用高效节能的压缩机,改善管道、阀门的设计和安装,减少阻力损失,提高设备运行效率。
采用在线监测装置,及时发现设备运行异常,进行及时处理,提高设备可靠性,降低故障率,确保装置平稳运行。
二、工艺优化甲醇合成装置的工艺优化主要包括原料气体净化、催化剂选择、反应条件控制等方面。
在原料气体净化方面,要定期对气体净化设备进行清洗和更换,保持气体净化效果良好,提高甲醇合成的纯度和产率。
在催化剂选择方面,要根据实际情况选用合适的催化剂,采用新型的高活性催化剂,提高甲醇合成的选择性和产率。
在反应条件控制方面,要及时调整反应温度、压力等参数,保持最佳的反应条件,提高甲醇合成的效率和质量。
三、管理优化甲醇合成装置的管理优化主要包括人员管理、安全管理、能源管理等方面。
首先要加强对操作人员的培训和技术交流,提高操作人员的技术水平和责任意识,减少操作失误和事故发生。
在安全管理方面,要建立健全的安全管理制度,定期组织安全培训和应急演练,提高员工安全意识和应急处置能力,确保生产安全。
在能源管理方面,要加强对能源的监控和管理,降低能源消耗,提高能源利用效率,降低生产成本。
甲醇合成装置的优化运行是一个系统工程,需要在设备、工艺和管理三个方面进行综合优化。
只有不断改进装置运行状态,提高生产效率,降低能耗,保证产品质量,才能在激烈的市场竞争中立于不败之地。
希望本文对甲醇生产企业的优化运行工作有所帮助,为行业的发展和进步贡献力量。
甲醇厂合成操作规程内容(3篇)
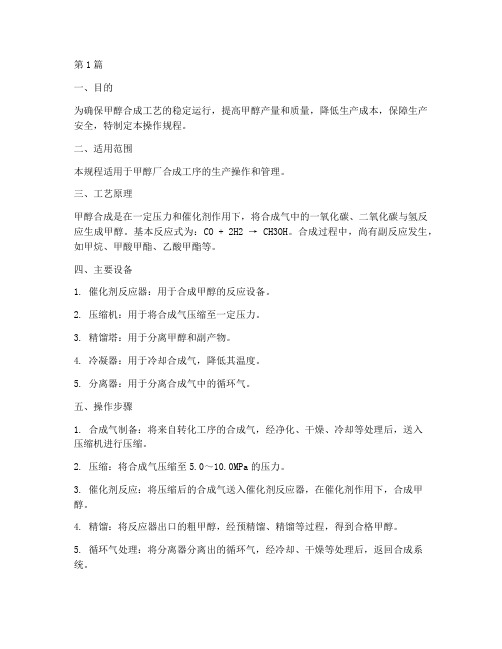
第1篇一、目的为确保甲醇合成工艺的稳定运行,提高甲醇产量和质量,降低生产成本,保障生产安全,特制定本操作规程。
二、适用范围本规程适用于甲醇厂合成工序的生产操作和管理。
三、工艺原理甲醇合成是在一定压力和催化剂作用下,将合成气中的一氧化碳、二氧化碳与氢反应生成甲醇。
基本反应式为:CO + 2H2 → CH3OH。
合成过程中,尚有副反应发生,如甲烷、甲酸甲酯、乙酸甲酯等。
四、主要设备1. 催化剂反应器:用于合成甲醇的反应设备。
2. 压缩机:用于将合成气压缩至一定压力。
3. 精馏塔:用于分离甲醇和副产物。
4. 冷凝器:用于冷却合成气,降低其温度。
5. 分离器:用于分离合成气中的循环气。
五、操作步骤1. 合成气制备:将来自转化工序的合成气,经净化、干燥、冷却等处理后,送入压缩机进行压缩。
2. 压缩:将合成气压缩至5.0~10.0MPa的压力。
3. 催化剂反应:将压缩后的合成气送入催化剂反应器,在催化剂作用下,合成甲醇。
4. 精馏:将反应器出口的粗甲醇,经预精馏、精馏等过程,得到合格甲醇。
5. 循环气处理:将分离器分离出的循环气,经冷却、干燥等处理后,返回合成系统。
六、操作指标1. 压力:合成气压力为5.0~10.0MPa。
2. 温度:催化剂反应器温度为230~260℃。
3. 催化剂活性:催化剂活性不低于设计值。
4. 甲醇产量:根据生产计划进行调整。
七、注意事项1. 严格控制合成气成分,确保催化剂活性。
2. 严格操作,防止催化剂中毒。
3. 定期检查设备,确保设备完好。
4. 严格执行安全技术操作规程,确保生产安全。
八、事故处理1. 催化剂中毒:发现催化剂中毒现象时,应立即停止生产,更换催化剂。
2. 压缩机故障:发现压缩机故障时,应立即停止生产,排除故障。
3. 精馏塔故障:发现精馏塔故障时,应立即停止生产,排除故障。
九、安全要求1. 严格执行国家有关安全生产法律法规。
2. 加强员工安全教育培训,提高安全意识。
3. 定期进行安全检查,确保生产安全。
国内外甲醇合成反应器比较与探讨
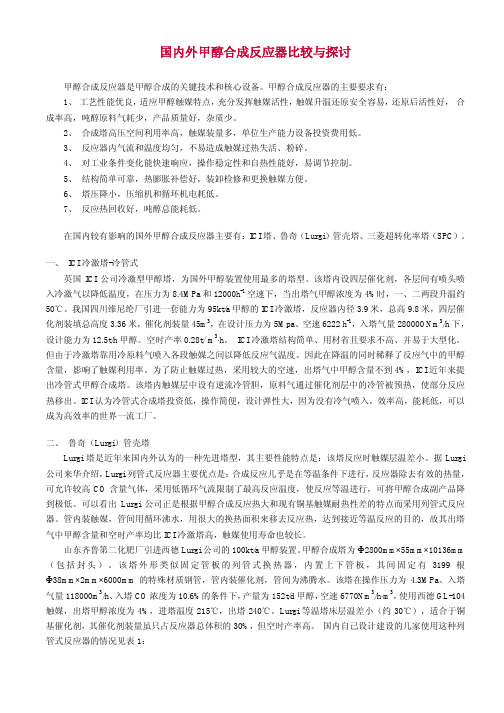
用温度。 5、投资大。据报导陕西榆林年产 3 万吨甲醇装置,实际总投资为 9600 万元。
三、 三菱超转化率塔(SPC) 这是近年来引起人们注意的甲醇合成塔。由日本三菱气体化学公司研制。该塔为双套管式。日产 520 吨
在国内较有影响的国外甲醇合成反应器主要有:ICI 塔、鲁奇(Lurgi)管壳塔、三菱超转化率塔(SPC)。
一、 ICI 冷激塔-冷管式 英国 ICI 公司冷激型甲醇塔,为国外甲醇装置使用最多的塔型。该塔内设四层催化剂,各层间有喷头喷
入冷激气以降低温度,在压力为 8.4MPa 和 12000h-1 空速下,当出塔气甲醇浓度为 4%时,一、二两段升温约 50℃。我国四川维尼纶厂引进一套能力为 95kt/a 甲醇的 ICI 冷激塔,反应器内径 3.9 米,总高 9.8 米,四层催 化剂装填总高度 3.36 米,催化剂装量 45m3,在设计压力为 5Mpa、空速 6222 h-1,入塔气量 280000 Nm3/h 下, 设计能力为 12.5t/h 甲醇。空时产率 0.28t/ m3·h。 ICI 冷激塔结构简单、用材省且要求不高、并易于大型化。 但由于冷激塔靠用冷原料气喷入各段触媒之间以降低反应气温度。因此在降温的同时稀释了反应气中的甲醇 含量,影响了触媒利用率。为了防止触媒过热,采用较大的空速,出塔气中甲醇含量不到 4%,ICI 近年来提 出冷管式甲醇合成塔。该塔内触媒层中设有逆流冷管胆,原料气通过催化剂层中的冷管被预热,使部分反应 热移出。ICI 认为冷管式合成塔投资低,操作简便,设计弹性大,因为没有冷气喷入,效率高,能耗低,可以 成为高效率的世界一流工厂。
二、 鲁奇(Lurgi)管壳塔 Lurgi 塔是近年来国内外认为的一种先进塔型,其主要性能特点是:该塔反应时触媒层温差小。据 Lurgi
- 1、下载文档前请自行甄别文档内容的完整性,平台不提供额外的编辑、内容补充、找答案等附加服务。
- 2、"仅部分预览"的文档,不可在线预览部分如存在完整性等问题,可反馈申请退款(可完整预览的文档不适用该条件!)。
- 3、如文档侵犯您的权益,请联系客服反馈,我们会尽快为您处理(人工客服工作时间:9:00-18:30)。
第八章甲醇合成反应器工艺结构
8.1甲醇合成反应器工艺结构
(需进行机械强度计算、排管及机械设计)
甲醇合成反应器的外壳,直筒部分高约8900mm,上、下封头高约1900mm,筒体内径Φ3800mm。
在水入口与蒸汽出口处,壳体上、下设加强板。
进水口6只,60o均布,接近下管板,进水管深入筒体内约950mm,公称直径DN150,每只进水管向下开孔14只。
蒸汽出口6只,60o均布,接近上管板,蒸汽出口管公称直径DN250。
上封头有进气管,在中心处,公称直径DN600。
有人孔,倾斜45o处,公称直径DN500。
下封头有出气管,在底部中心处,公称直径DN600。
另有向下的卸触媒口3只,公称直径DN250。
上封头有两组热电偶插入口,公称直径DN40,每组热电偶测量3点温度,1点在绝热层,2点在管壳层。
热电偶插入口位置在Φ1900mm处。
热电偶测量点:绝热层1点,(以上管板上平面向上计)50mm;管壳层2点,(以上管板向下计)2500mm、5000mm。
汽包顶在反应器上封头上,汽包底部与合成塔上升管出汽口距离为5m。
(2)管板与列管
列管焊接在管板上,管板焊接在筒体上,管板与筒体是同一类型材料。
列管为Φ44×2mm,长7500mm。
关于管子的用材,基于以下考虑,在催化剂存在下,CO会和Fe生成羰基铁,所以管子不能用碳钢,否则会产生羰基铁和石蜡,也不能用不锈钢,这样与外壳膨胀系数不同。
建议用特殊双相合金钢,如S31803,与外壳膨胀系数相同,管子焊接在管板上,用双相钢堆焊,焊接覆盖层厚度为7mm,管箱直筒段堆焊6mm304L。
上管板处(向上计)直筒段高650mm的筒体内侧以及下管板的管程侧用Inconiel625堆焊,厚6mm。
(3)进气分布器
进气分布器上开设条形进气孔。
(4)结构参数(mm):
总高:~14200
筒体高:~8900
上、下封头高:1900
筒体内径:Φ3800
绝热层高度:480
列管管长:7500
列管管径:Φ44×2
管心距:51
管数:4309根
换热面积(以外径计算):4348m2
(5)催化剂装填
上管板上部绝热层:0.7854×3.82×0.48=5.44m3
列管内冷却层:0.7854×0.042×7.5×4309=40.61m3
总计46.06 m3
催化剂型号:国产C307或XNC98铜基催化剂,粒度Φ5×5mm。
(因还原后,催化剂体积收缩,催化剂的收缩全部在绝热层,上管板上方催化剂落入列管中。
还原后体积约42.88m3。
绝热层催化剂装填高度视催化剂收缩率而定。
)
(6)开工喷射器
合成塔催化剂还原升温时,靠开工喷射器加入中压蒸汽进行,中压蒸汽经开工喷射器后,带动锅炉水循环,使催化剂温度逐渐上升,其规格为Φ273mm/Φ108mm/Φ168mm,L=2624mm,材质为Q345R。
8.2结构描述
甲醇合成反应器类似于一个立式副产蒸汽的管壳式固定管板换热器,管板与壳体之间直接焊接,无法兰连接。
反应器结构简图见附图。
反应器的上下封头,采用半球封头。
上封头合成气入口处设置气体分布器。
绝热层催化剂上部填装Φ10mm耐火球,装填高度为200mm。
下管板下面(以下管板下面往下计)装填Φ10mm耐火球300mm,再往下装填Φ25mm耐火球。
列管内装填催化剂,列管与管板的连接为贴胀加强度焊。
反应器的壳层筒体上端设有6根蒸汽出口管,下端有6根水进口管,为防止汽阻及加强换热管的固定,反应器的壳层设有支承挡圈。
催化剂的装卸口分别设置在反应器的侧封头上。
基础设计数据、接管管表、设计要求、件号对照表见下列各表。
基础设计数据
基础设计图纸接管口表
基础设计技术要求
基础设计件号对照表
第九章甲醇合成反应器设备建议
9.1对设计标准的建议
甲醇合成反应器的设备设计、制造、检验,建议参考下列有关标准:
TSG R0004-2009《固定式压力容器安全技术监察规程》
GB150.1~150.4-2011《压力容器》标准
GB151-1999《管壳式换热器》标准
NB/T47015-2011《压力容器焊接规程》
NB/T47014-2011《承压设备焊接工艺评定》
GB713-2009《锅炉和压力容器用钢板》标准
GB13296-2007《锅炉、热交换器用不锈钢无缝钢管》标准
GB-T 1220-2007《不锈钢棒》标准
GB24511-2009《承压设备用不锈钢钢板及钢带》标准
JB/T4730-2005《压力容器无损检测》规程
NB/T47008-2010《承压设备用碳素钢和低合金钢锻件》规程
HG/T20615-2009《钢制管法兰》
9.2对材质选择的建议
甲醇合成反应器的材质根据介质特性及操作温度、压力等选择,其基本选择原则为:
(1)合成气中有H2,根据H2的操作压力与温度,应考虑氢腐蚀影响。
(2)合成气中有CO、CO2和H2O,其中CO还可能与Fe、Ni等生成羰基铁、羰基镍,所以在选材时,要考虑避免生成羰基化物。
管程操作介质为合成气,壳程操作介质为水蒸汽。
对合成反应器的材质作如下建议:
(1)上下封头15CrMoR
(2)管板:20MnMo+S30403
(3)换热管:S31803
(4)筒体:Q345R
(5)合成气进口分布器:304不锈钢
合成气出口管:15CrMo
装、卸触媒孔:15CrMo
筒体加强管:15CrMo
(6)堆焊焊条牌号及堆焊厚度:
在上管板与上封头内侧用Inconel625堆焊,厚6mm。
9.3对焊接方式的建议
(1)封头与筒体之间的焊接
建议采用氩弧焊打底的全熔透焊接方式。
15CrMoR之间、15CrMoR与CrMo 之间、15CrMoR与Q345R之间的焊接均应在另一侧做清根处理,并经磁粉检测合格后方可焊接。
(2)换热管与管板的焊接
采用贴胀加强焊连接,并采用先胀后焊的方法。
(3)管板表面及上封头内侧下部堆焊双相不锈钢
先将待堆焊表面进行机加工,经超声波检测合格后,先堆焊过渡层,然后中间清除应力热处理,清洗表面后,再堆焊盖面层,然后进行机加工,表面液体渗透检测,超声波检测堆焊层熔合质量,最后再以超声波测厚仪对堆焊层的厚度进行测量。
9.4对制造、检验要求的建议
甲醇合成反应器的制造、检验及试验规范按GB150.1~150.4-2011、HG/T20583-2011及“甲醇合成反应器技术条件”的要求进行。
第十章合成工序其它设备
10.1合成工序其它设备
合成工艺其它设备见下表。
10.2工艺设备数据表
10.3 合成工序其它设备结构简图
10.3.1 汽包
B
A
C
N1
N10
N5
2
汽包简图
汽包 基础设计数据
汽包管口表
汽包件号对照表
10.3.2入塔气换热器
水冷器简图见附图6。
气-气换热器热负荷
换热器冷热流体状态
换热器
换热器
换热器
10.3.3水冷器
水冷器简图见附图7。
水冷器热负荷
换热器
固定管板水冷器
基础设计数据
*注:该组成为质量组成。
固定管板水冷器
基础设计图纸接管口表
固定管板水冷器
10.3.4 甲醇分离器
N5,N7,N9
N6,N8,N10
甲醇分离器简图
甲醇分离器 基础设计数据
甲醇分离器管口表
甲醇分离器
10.3.5 闪蒸槽
闪蒸槽简图
闪蒸槽管口表
10.3.6 循环压缩机
循环压缩机主要参数:
后期110%负荷时,循环气量37.5×104Nm3/h,出口压力5.65MPaG,压差0.65MPa;后期100%负荷时,循环气量34.1×104Nm3/h,出口压力5.65MPaG,压差0.60MPa;后期50%负荷、初期100%负荷时,循环气量29.0×104Nm3/h,出口压力5.25MPaG,压差0.6MPa;初期50%负荷时,循环气量24.0×104Nm3/h,出口压力4.85MPaG,压差0.6MPa;初期110%负荷时,循环气量32.0×104Nm3/h,出口压力5.45MPaG,压差0.6MPa。
在催化剂升温还原阶段,压缩机运行状态保持恒定,保证入塔还原气流量≥2.7×104Nm3/h。
压缩机不同工况下循环气体组成:。