多晶硅刻蚀特性的研究
多晶硅深度反应离子刻蚀代加工
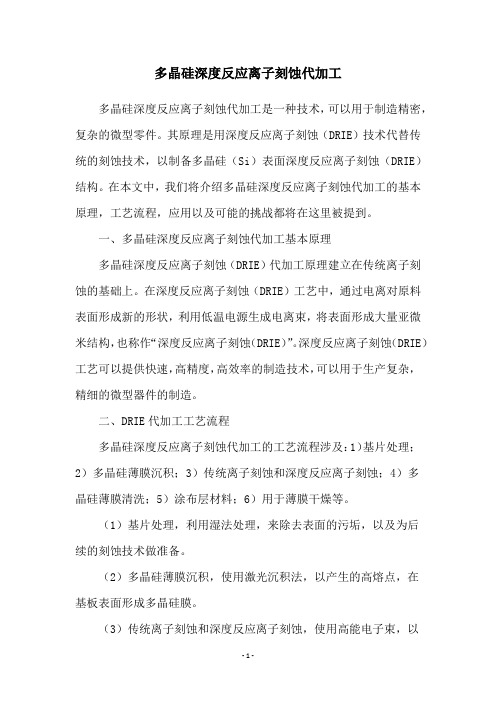
多晶硅深度反应离子刻蚀代加工多晶硅深度反应离子刻蚀代加工是一种技术,可以用于制造精密,复杂的微型零件。
其原理是用深度反应离子刻蚀(DRIE)技术代替传统的刻蚀技术,以制备多晶硅(Si)表面深度反应离子刻蚀(DRIE)结构。
在本文中,我们将介绍多晶硅深度反应离子刻蚀代加工的基本原理,工艺流程,应用以及可能的挑战都将在这里被提到。
一、多晶硅深度反应离子刻蚀代加工基本原理多晶硅深度反应离子刻蚀(DRIE)代加工原理建立在传统离子刻蚀的基础上。
在深度反应离子刻蚀(DRIE)工艺中,通过电离对原料表面形成新的形状,利用低温电源生成电离束,将表面形成大量亚微米结构,也称作“深度反应离子刻蚀(DRIE)”。
深度反应离子刻蚀(DRIE)工艺可以提供快速,高精度,高效率的制造技术,可以用于生产复杂,精细的微型器件的制造。
二、DRIE代加工工艺流程多晶硅深度反应离子刻蚀代加工的工艺流程涉及:1)基片处理;2)多晶硅薄膜沉积;3)传统离子刻蚀和深度反应离子刻蚀;4)多晶硅薄膜清洗;5)涂布层材料;6)用于薄膜干燥等。
(1)基片处理,利用湿法处理,来除去表面的污垢,以及为后续的刻蚀技术做准备。
(2)多晶硅薄膜沉积,使用激光沉积法,以产生的高熔点,在基板表面形成多晶硅膜。
(3)传统离子刻蚀和深度反应离子刻蚀,使用高能电子束,以改变基片表面的形状,也能形成多晶硅刻蚀槽和深度反应离子刻蚀(DRIE)结构。
(4)多晶硅薄膜清洗,使用化学清洗或光学清洗,在深度反应离子刻蚀(DRIE)前,将残留的氧化物和沉积物清除,以确保精度和切削效果。
(5)涂布层材料,使用厚膜沉积法或其他等离子体技术来涂布层材料,以增加多晶硅深度反应离子刻蚀(DRIE)特定材料的导电性、耐腐蚀性和热性能。
(6)用于薄膜干燥,避免湿度对深度反应离子刻蚀(DRIE)结构的影响,以保证精度和可靠性。
三、多晶硅深度反应离子刻蚀代加工应用多晶硅深度反应离子刻蚀(DRIE)代加工技术可以用于制造精密,复杂的微型零件,特别是那些拥有复杂的薄膜结构的微小零件。
金刚石线锯切割多晶硅片气相刻蚀制绒方法研究进展

金刚石线锯切割多晶硅片气相刻蚀制绒方法研究进展
气相刻蚀制绒是一种表面改性技术,通过在硅片的表面形成一层被氮
化物覆盖的细长晶须,从而实现提高硅片的质量和光电性能。
在金刚石线
锯切割多晶硅片后,使用气相刻蚀制绒方法可以去除切割剩余物,并在硅
片表面形成一层光滑、无缺陷的晶须层。
目前,关于金刚石线锯切割多晶硅片气相刻蚀制绒方法的研究主要集
中在以下几个方面。
首先,研究人员对气相刻蚀制绒参数进行了优化,以提高晶须层的质量。
例如,可以通过调节气相刻蚀的温度、气氛种类、气氛组成、气氛压
力等参数,来实现晶须层的合理生长。
研究发现,适当的温度和气氛组成
可以促进晶须层的生长,而氢气氛可以提高晶须层的平滑度和晶体质量。
其次,研究人员也尝试了不同的气相刻蚀制绒方法,以提高晶须层的
性能。
例如,可以使用微波等离子体刻蚀技术、电子束蒸发等技术,来实
现更加精确的刻蚀效果。
通过比较不同刻蚀方法的效果,可以选择最适合
多晶硅片制绒的方法。
此外,还有研究人员对切割过程中金刚石线锯的材料特性进行了改进。
例如,可以使用高纯度的金刚石线锯,以减少切割过程中对多晶硅片的损伤。
同时,也可以研发出更加高效、低损伤的金刚石线锯切割工艺。
总结起来,金刚石线锯切割多晶硅片气相刻蚀制绒方法是一种有效的
硅片表面改性技术,可以提高硅片的质量和光电性能。
该方法的研究进展
主要集中在优化刻蚀参数、改进刻蚀方法和提高金刚石线锯的材料特性等
方面。
未来,还需进一步深入研究,以推动该技术的应用和发展。
多晶硅栅极刻蚀过程中边缘刻蚀缺陷的研究及改善

多晶硅栅极刻蚀过程中边缘刻蚀缺陷的研究及改善作者:任昱聂钰节唐在峰来源:《科技资讯》2017年第25期DOI:10.16661/ki.1672-3791.2017.25.087摘要:刻蚀缺陷是半导体制程中最关键和最基本的问题,理想的等离子体刻蚀工艺过程中,刻蚀气体必须完全参与反应而形成气态生成物,最后由真空泵抽离反应室。
但实际上,多晶硅栅极等离子体刻蚀过程中,生成的反应聚合物(polymer)无法由真空泵抽离反应室而附着在刻蚀腔壁上,造成反应室的污染,有些甚至附着在晶圆表面而形成元器件的微粒子污染,造成产品良率下降甚至报废。
本文通过改变调整刻蚀工艺参数等方式,成功解决了多晶硅栅极刻蚀工艺制程中反应生成物转变为微粒子污染物这一问题,使得产品良率提升了3%,刻蚀反应腔体保养时数延长了一倍,晶圆报废率降低了0.03%。
关键词:多晶硅刻蚀干法刻蚀等离子体栅极刻蚀缺陷中图分类号:TN305.7 文献标识码:A 文章编号:1672-3791(2017)09(a)-0087-05随着微电子技术的发展,使器件的特征尺寸(Critical Dimension,简称CD)不断缩小,使得集成度不断提高,功耗降低,器件性能提高。
在微电子学中,特征尺寸通常指集成电路中半导体器件的最小尺寸,如MOSE管的栅极关键尺寸,特征尺寸是衡量集成电路设计和制造工艺水平的重要参数。
但是特征尺寸越小,栅极的尺寸容差要求就变得越来越严格,尤其是大尺寸的12寸晶圆硅片的应用,使得工艺控制变得更加苛刻。
例如按照刻蚀容差绝对值应控制在10%之内,对于45nm工艺节点,容差绝对值要小于5nm[1]。
在先进的多晶硅栅极工艺中,刻蚀腔之间CD偏差值匹配度已经小于1nm,而高的CD精度意味着工艺步骤的可重复性需要做到完美。
与此同时,由于堆叠结构越来越复杂,刻蚀过程中反应物和生成物也相应地增加,另外刻蚀反应腔体也要承担更多的工艺刻蚀内容,于是刻蚀反应腔体的匹配和工艺的可重复性,已经成为等离子体刻蚀中很大的挑战。
《湿法刻蚀多晶硅周边问题》范文
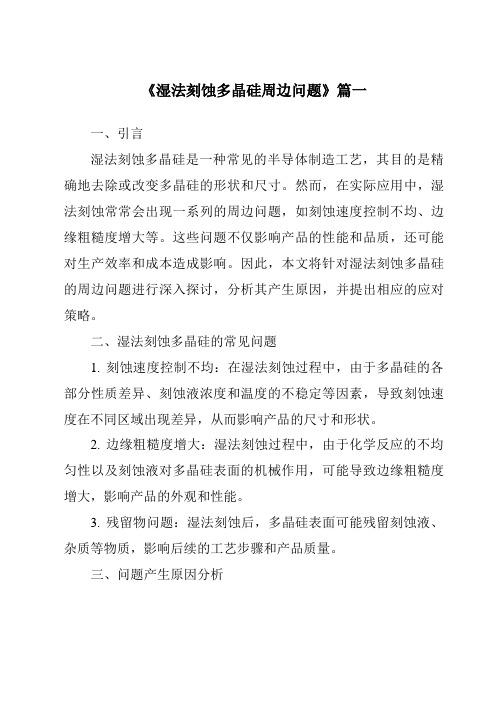
《湿法刻蚀多晶硅周边问题》篇一一、引言湿法刻蚀多晶硅是一种常见的半导体制造工艺,其目的是精确地去除或改变多晶硅的形状和尺寸。
然而,在实际应用中,湿法刻蚀常常会出现一系列的周边问题,如刻蚀速度控制不均、边缘粗糙度增大等。
这些问题不仅影响产品的性能和品质,还可能对生产效率和成本造成影响。
因此,本文将针对湿法刻蚀多晶硅的周边问题进行深入探讨,分析其产生原因,并提出相应的应对策略。
二、湿法刻蚀多晶硅的常见问题1. 刻蚀速度控制不均:在湿法刻蚀过程中,由于多晶硅的各部分性质差异、刻蚀液浓度和温度的不稳定等因素,导致刻蚀速度在不同区域出现差异,从而影响产品的尺寸和形状。
2. 边缘粗糙度增大:湿法刻蚀过程中,由于化学反应的不均匀性以及刻蚀液对多晶硅表面的机械作用,可能导致边缘粗糙度增大,影响产品的外观和性能。
3. 残留物问题:湿法刻蚀后,多晶硅表面可能残留刻蚀液、杂质等物质,影响后续的工艺步骤和产品质量。
三、问题产生原因分析1. 刻蚀液浓度和温度的影响:刻蚀液的浓度和温度是影响刻蚀速度的关键因素。
当浓度和温度不稳定时,会导致刻蚀速度在不同区域出现差异。
2. 多晶硅材料性质的不均:多晶硅的晶体结构、杂质含量等因素会影响其与刻蚀液的反应速度和程度,从而导致刻蚀速度的不均。
3. 工艺控制问题:包括设备的稳定性、操作人员的技能水平等都会对湿法刻蚀的效果产生影响。
四、应对策略1. 优化刻蚀液浓度和温度控制:通过精确控制刻蚀液的浓度和温度,保持其在整个刻蚀过程中的稳定性,从而确保刻蚀速度的均匀性。
2. 改进多晶硅材料的质量:提高多晶硅的纯度和晶体结构的均匀性,降低其与刻蚀液反应的不均匀性。
3. 加强工艺控制:提高设备的稳定性和操作人员的技能水平,确保工艺参数的准确性和一致性。
4. 引入先进的刻蚀技术:如干湿结合的刻蚀技术、激光辅助刻蚀技术等,这些技术可以更精确地控制刻蚀速度和形状,减少边缘粗糙度和残留物问题。
5. 定期维护和检查设备:定期对设备进行维护和检查,确保其正常运行和性能稳定,从而保证湿法刻蚀的效果。
多晶硅刻蚀工艺

多晶硅刻蚀工艺
多晶硅刻蚀是一种重要的半导体工艺步骤,它可以通过化学反应
将多晶硅转化为低电阻或高电阻硅材料。
该工艺通常使用非晶硅或其
他绝缘材料作为掩模,以控制刻蚀模式和形状。
多晶硅的刻蚀过程可以通过干法或湿法来实现。
在干法工艺中,
刻蚀介质通常是气体混合物,如氟化物和氯化物。
这种方法足够快速,对环境的污染较小,但需要高温和特殊的反应器。
在湿法工艺中,刻
蚀介质是强酸和强碱,例如氢氟酸和五氧化二磷。
这种方法刻蚀速度
较慢,但比较容易操作,成本也相对较低。
多晶硅的刻蚀必须控制好方向性和等深度,以获得高质量的硅材料。
此外,刻蚀过程中还需要注意反应的选择性,以免影响整个工艺
流程的稳定性和可靠性。
总之,多晶硅刻蚀工艺是制造半导体器件中的重要步骤,经过多
年的研究和改进已经变得更为成熟、可靠。
多晶干法刻蚀

多晶干法刻蚀是一种重要的半导体工艺步骤,主要应用于制造集成电路。
以下是关于多晶干法刻蚀的详细解释:
1. 刻蚀多晶硅时,必须确保掩膜上的尺寸准确地转移到多晶硅上。
2. 刻蚀后的轮廓也非常重要,例如,如果多晶硅刻蚀后栅极侧壁有倾斜,可能会屏蔽后续工艺中源极和
漏极的离子注入,导致杂质分布不均,同时沟道的长度会随栅极倾斜的程度而改变。
3. 对sio2的刻蚀选择比要足够高,这是因为需要去除阶梯残留,避免多晶硅电极间短路的发生。
同时,
多晶硅一般覆盖在很薄的栅极氧化层上,如果氧化层被完全刻蚀,则氧化层下的源极和漏极区域可能会被快速刻蚀。
4. 选择适当的刻蚀气体也是非常重要的。
CF4、SF6等F原子为主的等离子体是常用的刻蚀气体,但这类
气体也存在负载效应,即被刻蚀材料裸露在等离子体中面积较大的区域时刻蚀速率比在面积较小的区域时慢,导致局部刻蚀速率的不均匀。
5. 在干法刻蚀中,多晶硅相对于氮化硅和二氧化硅下层的选择性较差,因此需要非常精确地优化干蚀刻
配方和蚀刻时间的精细控制。
6. 另外,对于多晶硅的干法刻蚀,控制其过度刻蚀也非常重要。
这是因为过度刻蚀可能会导致多晶硅的
电阻不均匀。
总之,多晶干法刻蚀是一项复杂的工艺步骤,涉及精确的尺寸控制、化学选择性和物理特性考虑等多个方面。
多晶硅的生产工艺及研究

多晶硅的生产工艺及研究1.引言多晶硅是一种重要的半导体材料,广泛应用于太阳能电池、集成电路和微电子设备中。
它具有较高的电导率和热导率,因此在能源转换和电子器件方面具有巨大的应用潜力。
本文将介绍多晶硅的生产工艺及相关研究。
2.多晶硅的制备方法多晶硅的制备方法通常包括以下几个步骤:2.1原料制备:将硅砂经过粉碎、筛分和洗涤等处理,得到纯度较高的硅粉。
2.2单晶硅的生长:将硅粉在高温环境下进行还原反应,得到单晶硅块。
2.3多晶硅的制备:将单晶硅块经过熔化、晶化和切割等处理,得到多晶硅块。
2.4多晶硅片的制备:将多晶硅块经过切割、抛光和清洗等处理,得到多晶硅片。
3.多晶硅的电化学沉积法电化学沉积法是一种制备多晶硅的重要方法。
它利用电解质中的离子进行电极反应,沉积出多晶硅薄膜或纳米颗粒。
该方法具有简单、可控性强和成本低等优点,广泛应用于太阳能电池和微电子器件中。
4.多晶硅的激光熔化法激光熔化法是一种利用激光高能量密度对硅材料进行局部熔化和凝固的方法。
该方法可以获得高纯度、低缺陷的多晶硅薄膜,并具有较高的结晶度和电学性能。
该方法广泛应用于太阳能电池的制备中。
5.多晶硅的晶体生长技术多晶硅的晶体生长技术是一种通过控制晶界生长来提高多晶硅的结晶质量和电学性能的方法。
该技术包括定向凝固法、温度梯度法和溶液热法等。
这些方法通过调节温度梯度和晶体生长速度等参数,可以获得较大晶界能量和较高的晶界能垂直度,从而提高多晶硅的结晶质量和电学性能。
6.多晶硅的表面处理技术多晶硅的表面处理技术是一种通过改变表面形貌和化学性质来改善多晶硅的光吸收性能和光电转换效率的方法。
常用的表面处理技术包括湿法刻蚀、化学气相沉积和表面涂覆等。
这些技术可以形成纳米结构、提高表面反射率和降低表面缺陷密度,从而提高多晶硅的光吸收性能和光电转换效率。
7.多晶硅的尺寸效应研究多晶硅的尺寸效应研究是一种通过调控多晶硅的尺寸和形貌来改善其电学性能和光电转换效率的方法。
多晶硅刻蚀工艺

多晶硅刻蚀工艺
多晶硅刻蚀是一种基础的半导体加工工艺,用于制作太阳能电池、集成电路等器件。
该工艺主要利用化学反应来刻蚀多晶硅表面,以达到所需的形状和尺寸。
在该工艺中,通常会使用一种名为氢氟酸的强酸来刻蚀多晶硅表面,并且需要在特定的气氛中进行。
多晶硅刻蚀工艺可以根据所需的形状和尺寸进行优化,以获得最佳的结果。
通常,通过调整刻蚀时间、刻蚀速率、刻蚀深度等参数来实现优化。
此外,在多晶硅刻蚀过程中,还需要注意控制刻蚀剂的浓度、温度和搅拌速度等因素,以确保刻蚀均匀和稳定。
最终,通过多次刻蚀和清洗处理,可以得到所需的多晶硅结构和形状。
多晶硅刻蚀工艺在半导体制造行业中应用广泛,尤其是在太阳能电池制造中。
通过优化多晶硅刻蚀工艺,可以提高太阳能电池的转换效率,并降低制造成本。
- 1 -。
多晶硅纳米线的湿法刻蚀及光学性质研究

开发研究多晶硅纳米线的湿法刻蚀及光学性质研究刘波(江西新能源科技职业学院,江西新余338012)摘要:介绍了采用湿法刻蚀的方法来制备多晶硅纳米线,通过扫描电镜、反射率测试和XRD晶形分析等手段来对制备样岛的形貌和光学性质进行表征。
通过实验研究HF浓度、AgNOs浓度、H2O2浓度、反应时间对硅纳米线表面形貌和漫反射率的影响,从而得到刻蚀的最佳条件,制备出低反射率而又均匀的多晶硅纳米线材料。
关键词:湿法刻蚀;多晶硅;硅纳米线;反射率1硅材料及其物理特性1.1硅纳米线概念所谓纳米线,是一种在横向上被限制在100nm以下,纵向上没有限制的一维材料。
硅纳米线是一种新型的一维半导体纳米材料,线体直径一般在10nm左右,内晶核实单晶硅,外层有一层Si。
?包覆层。
硅纳米线可以通过紫外光电子刻蚀、反应性离子刻蚀、金属有机物化学气相沉积等方法制备得到。
在场效应晶体管、单电子探测器、双向电子泵、双重门电路、纳米线阵列方面都有硅纳米线的应用。
1.2硅纳米线特性1.2.1载流子浓度与迁移率载流子浓度和迁移率是半导体材料最基本的电学特性。
掺杂硅纳米线的电阻率很低,所以通过掺杂可提高硅纳米线的载流子浓度。
高载流子浓度对半导体能带有重要影响,从而对半导体光吸收边附近的吸收特性有若干重要的影响,最终导致带隙随载流子浓度变化。
1.2.2场发射特性场发射是利用肖特基效应,将指向导体表面的强电场(即所谓的提拉电场)作用于导体的表面,使其表面势垒降低、变窄,当势垒的宽度窄到可以与电子波长相比拟时,电子的隧道效应开始起作用,部分高能电子就可顺利穿透表面势垒进入真空。
2实验讨论在这次试验中,我们通过改变HF浓度、AgNOs浓度、HQ?浓度、反应时间,来制备不同的硅纳米线样品。
每个实验只改变一个条件作为自变量,其他条件则完全相同,通过阶梯性改变自变量的值来得到不同的硅纳米线样品组。
使用紫外分光光度计测试样品组反射率,分析实验测试结果,得到自变量最佳条件。
超薄多晶硅的掺杂、钝化及光伏特性研究

第51卷第3期2022年3月人㊀工㊀晶㊀体㊀学㊀报JOURNAL OF SYNTHETIC CRYSTALS Vol.51㊀No.3March,2022超薄多晶硅的掺杂、钝化及光伏特性研究宋志成1,2,杨㊀露2,张春福1,刘大伟2,倪玉凤2,张㊀婷2,魏凯峰2(1.西安电子科技大学微电子学院,宽禁带半导体材料与器件教育部重点实验室,西安㊀710071;2.青海黄河上游水电开发有限责任公司西安太阳能电力分公司,西安㊀710000)摘要:本文对70nm 超薄多晶硅的掺杂工艺㊁钝化性能及光伏特性进行了研究㊂确定了70nm 超薄多晶硅的掺杂工艺,研究表明当离子注入剂量为3.2ˑ1015cm -3,在855ħ退火20min 时,70nm 超薄多晶硅的钝化性能可以达到与常规120nm 多晶硅相当的水平,且70nm 多晶硅的表面掺杂浓度达到5.6ˑ1020atoms /cm 3,远高于120nm 掺杂多晶硅的表面掺杂浓度(2.5ˑ1020atoms /cm 3)㊂基于70nm 超薄多晶硅厚度减薄和高表面浓度掺杂的特点,较低的寄生吸收和强场钝化效应使得在大尺寸(6英寸)直拉单晶硅片上加工的N 型TOPCon 太阳能电池的光电转换效率得到明显提升,主要电性能参数表现为:电流I sc 升高20mA,串联电阻R s 降低,填充因子FF 增加0.3%,光电转换效率升高0.13%㊂关键词:TOPCon 太阳能电池;多晶硅;掺杂;离子注入;钝化接触;寄生吸收;光电转换效率中图分类号:TM914.4㊀㊀文献标志码:A ㊀㊀文章编号:1000-985X (2022)03-0434-07Doping ,Passivation and Photovoltaic Properties of Ultra-Thin Poly-Silicon SONG Zhicheng 1,2,YANG Lu 2,ZHANG Chunfu 1,LIU Dawei 2,NI Yufeng 2,ZHANG Ting 2,WEI Kaifeng 2(1.Key Laboratory of Wide Bandgap Semiconductor Materials and Devices,Ministry of Education,School of Microelectronics,Xidian University,Xi an 710071,China;2.Xi an Solar Power Branch of Qinghai Huanghe Hydropower Development Co.,Ltd.,Xi an 710000,China)Abstract :The doping process,passivation and photovoltaic properties of 70nm ultra-thin poly-silicon were studied in this paper.The optimal doping process for 70nm ultra-thin poly-silicon was identified,the results show that when the ion implantation dose is 3.2ˑ1015cm -3and annealed at 855ħfor 20min,the passivation properties of 70nm ultra-thin poly-silicon is comparable to that of conventional 120nm poly-silicon,and the surface doping concentration value of 5.6ˑ1020atoms /cm 3for 70nm ultra-thin poly-silicon is achieved,which is much higher than that of 120nm doped poly-silicon (2.5ˑ1020atoms /cm 3).Based on the characteristic of reduced thickness and heavy doping for 70nm ultra-thin poly-silicon,the conversion efficiency of TOPCon solar cells processed on large area (6inch)Cz wafers significantly improves due to the low parasitic absorption and excellent filed passivation effect.The I sc is increased by 20mA and 0.3%improvement of FF ,leading to an absolute efficiency gain of 0.13%for the champion conversion efficiency,as well as low series resistance.Key words :TOPCon solar cell;poly-silicon;doping;ion implantation;passivation contact;parasitic absorption;photoelectric conversion efficiency㊀㊀㊀收稿日期:2021-12-16㊀㊀作者简介:宋志成(1985 ),男,湖北省人,硕士研究生㊂E-mail:songzhicheng@ ㊀㊀通信作者:杨㊀露㊂E-mail:yanglu2468@0㊀引㊀㊀言近年来,载流子选择性钝化接触的应用使晶硅太阳能电池的光电转换效率得到很大的提升[1-2]㊂据报道,德国Fraunhofer ISE 研究所开发的N 型背面全金属接触的隧穿氧化物钝化接触(tunnel oxide passivated contact,TOPCon)电池效率达到了25.8%的世界纪录[3-4],并且在P 型单晶氧化物多晶硅(Poly-Si)钝化接触叉指背接触(interdigital back contact,IBC)电池上实现高达26.1%的效率[5]㊂此外,由于TOPCon 电池与行业内现有产线的钝化发射结及背表面接触电池(passivated emitter and rear cell,PERC)具有高度的工艺和设㊀第3期宋志成等:超薄多晶硅的掺杂㊁钝化及光伏特性研究435㊀图1㊀TOPCon 电池结构图Fig.1㊀Structure of TOPCon solar cells 备兼容性,使其成为下一代晶硅电池技术升级的主要方向,TOPCon 电池的结构图如图1所示㊂TOPCon 电池较高的效率优势主要来源电池背面的钝化接触结构,该钝化接触结构由一层超薄的隧穿氧化层二氧化硅和掺杂多晶硅层组成,不仅具有优异的钝化性能和良好的接触性能,而且可以将金属接触与硅基体分离开,从而显著降低金属接触区域的复合,可以极大提升太阳能电池的转换效率㊂产业化多晶硅钝化接触太阳能电池设计中的一个关键因素是多晶硅层的厚度㊂多晶硅层,通常是高浓度掺杂[6-7],厚度为100~300nm [8-9],由于多晶硅寄生吸收的影响,会导致太阳能电池的短路电流(J sc )有显著的降低[10-11]㊂新加坡SERIS 研究所开发的双面monoPoly 6英寸大面积太阳能电池获得了23.4%[12-13]的转换效率,同时天合光能研发的大面积钝化接触太阳能电池的转换效率进一步提升至24.58%[14]㊂但至今为止,关于多晶硅的大部分工作都应用于太阳能电池的背面,并且使用了较厚的多晶硅层(至少大于70nm)[13-15]㊂而光学模拟结果表明多晶硅层厚度应该尽可能地减少[16-17]㊂但是,在不影响界面化学钝化的前提下,超薄多晶硅层的精准掺杂仍然是一项具有挑战性和关键的任务㊂同时,基于离子注入技术对小于100nm 厚度的多晶硅进行磷掺杂,并将其应用于产业化电池中的研究甚少㊂本文不仅对70nm 超薄多晶硅的掺杂特性㊁钝化性能进行了研究,并将磷掺杂超薄多晶硅应用于产业化6英寸(1英寸=2.54cm)大面积钝化接触电池中,所制备的钝化接触电池的电流和光电转换效率得到了明显提升㊂1㊀实㊀㊀验本实验采用158.75mm ˑ158.75mm 规格的N 型Cz 硅片,电阻率范围为0.3~2.1Ω㊃cm,少子寿命ȡ500μs㊂隧穿氧化层的生长和本征多晶硅的沉积由Tempress 公司生产的5管式量产设备完成,采用低压化学气相沉积(low pressure chemical vapor deposition,LPCVD)法生长隧穿氧化层和本征多晶硅㊂此设备可一次性直接完成隧穿氧化层的生长和多晶硅的沉积,且在低压下完成生长工艺,具有成膜致密㊁整舟均匀性好㊁产量大㊁生长速度快㊁工艺成熟等优点㊂采用凯世通ipv-3000机台实现不同离子注入剂量的掺杂㊂实验过程使用到的测试仪器有:电化学电容-电压(electrochemical capacitance-voltage profiler,ECV)测试仪测试样品表面掺杂浓度和掺杂结深,WCT-120Sinton 模块测试对称结构的钝化性能,SENTECH 800激光椭偏仪测试多晶硅的沉积厚度,IV 测试仪测试电池的电性能参数㊂钝化性能监控结构的制备过程:双面制绒后的硅片经过双面刻蚀,再沉积隧穿氧化层和本征多晶硅,然后经过离子注入㊁退火和双面镀膜工艺完成钝化结构的制作,最后经过烧结炉高温烧结完成制作,其结构如图2所示㊂表征钝化性能的参数有隐开路电压i V oc ㊁J 0和寿命,当测试结构钝化性能越好时,i V oc 值越高,寿命越高,J 0值越低㊂图2㊀Poly-Si(N +)钝化性能测试结构Fig.2㊀Poly-Si(N +)passivation performance test structure TOPCon 电池的制备工艺流程如图3所示,首先将原始硅片经过碱制绒形成金字塔陷光结构,再将制绒后的硅片在850~1000ħ进行低压硼扩散,完成前表面发射结掺杂工艺㊂然后进行刻蚀工艺去除硼扩散过程中硅片侧面形成的横向PN 结和正面的硼硅玻璃,并对非扩散面进行抛光处理㊂采用LPCVD 在硅片背面沉积1.5nm 的二氧化硅层和本征多晶硅层㊂通过离子注入磷和高温热处理实现多晶硅层的重掺杂和非晶相到多晶相的转变㊂再通过优化的清洗技术去除正面绕镀的多晶硅层,并在正面沉积钝化叠层薄膜,起到钝化和减少反射的作用㊂最后在电池正反面印刷金属电极收集光生载流子㊂436㊀研究论文人工晶体学报㊀㊀㊀㊀㊀㊀第51卷图3㊀TOPCon电池的制备工艺流程Fig.3㊀Preparation process of TOPCon solar cell2㊀结果与讨论2.1㊀120nm Poly-Si(N+)掺杂曲线与钝化性能常规120nm厚度的多晶硅匹配的离子注入剂量为2.6ˑ1015cm-3,退火条件为875ħ热处理20min,其掺杂曲线和钝化性能如图4所示㊂从图中可看出,120nm掺杂多晶硅的表面掺杂浓度为2.5ˑ1020atoms/cm3,掺杂结深为0.35μm,此时钝化性能达到最优,隐开路电压i V oc为736mV,J0为2fA/cm2㊂图4㊀120nm Poly-Si(N+)上(a)掺杂分布与(b)钝化性能测试Fig.4㊀Doping concentration distribution(a)and passivation performance(b)of120nm Poly-Si(N+)2.2㊀70nm薄Poly-Si的掺杂工艺优化与钝化性能多晶硅沉积的反应气体为高纯硅烷(SiH4),采用炉口和炉尾两个进气口的设计,在高温环境下热分解形成多晶硅薄膜沉积在硅片表面,反应式如下所示:SiH4ʏңSiˌ+2H2ʏ(1)当沉积温度㊁反应压力和气体流量一定时,沉积时间对多晶硅生长厚度有重要影响㊂基于前期实验数据,在沉积时间分别为1300s㊁1700s㊁2100s的工艺条件下可制备厚度90nm㊁120nm和150nm的多晶硅薄膜㊂采用片内测试5点求平均值的方式获得实验数据,并绘制沉积时间与薄膜厚度的散点图,线性拟合得出图5(a)㊂图5㊀(a)多晶硅厚度与沉积时间线性拟合曲线;(b)沉积时间1050s时多晶硅厚度的实际测试值Fig.5㊀(a)Liner fitting curve of poly-silicon thickness and deposition time;(b)value of poly-silicon thickness underdeposition time of1050s㊀第3期宋志成等:超薄多晶硅的掺杂㊁钝化及光伏特性研究437㊀从图5(a)可以看出,沉积时间与多晶硅厚度基本呈线性关系,且对时间变化敏感㊂当沉积时间为2100s时,多晶硅测试厚度为150nm,当沉积时间为1700s时,多晶硅测试厚度为120nm,因此可以通过该曲线预测沉积特定厚度的多晶硅所需要的沉积时间㊂从图中延长线上可以预测,当沉积时间小于1400s 时,可以沉积100nm以下的多晶硅,而当设定沉积时间为1050s时,可生长70nm的本征多晶硅㊂图5(b)为沉积时间1050s时多晶硅厚度的实际测试值,其中取炉口㊁炉中和炉尾三个位置各一片,每片测试5个点,共15个测试点,可以看出实际测试的多晶硅厚度为(70ʃ2)nm,与图5(a)拟合曲线预测的数值基本一致㊂图6为120nm和70nm厚度多晶硅的监控片外观图,可以看出不同厚度的多晶硅对应不同的颜色,可直接从监控片外观进行辨别,这对电池生产过程中多晶硅膜层厚度的监控具有重要指导意义㊂图6㊀沉积120nm和70nm厚度多晶硅的监控片外观图Fig.6㊀Appearance of monitoring wafers deposited with thicknesses of120nm and70nm deposited poly-silicon 此处研究离子注入剂量和退火温度对70nm多晶硅掺杂和钝化性能的影响㊂当离子注入设备稳定运行时,主要通过控制离子注入剂量来调整掺杂浓度,而改变离子注入剂量本质上就是改变离子注入机反应腔体内传输皮带的运行速度㊂当基于产线现有设备进行工艺,多晶硅厚度的减薄会对离子注入剂量要求较高,导致传输带的运行速度太慢,这将不利于设备的稳定运行,产生粘片或卡片的情况㊂故本文同时对70nm薄多晶硅的隧穿氧化层生长工艺进行了优化㊂2.2.1㊀离子注入剂量的影响图7为不同离子注入剂量下多晶硅磷掺杂分布和钝化性能的曲线,样品1至样品3采用的离子注入剂量分别为2.4ˑ1015/cm3㊁2.8ˑ1015/cm3和3.2ˑ1015/cm3㊂其中3.2ˑ1015/cm3为离子注入机台所能实现的最高注入剂量,得到的掺杂曲线如图7(a)所示㊂图7㊀不同条件下Poly-Si(N+)的掺杂分布与钝化性能Fig.7㊀Doping concentration distribution and passivation performance of poly-Si(N+)in different conditions 从图中可以看出,离子注入剂量的增加对多晶硅的掺杂分布和钝化性能影响较小㊂在相同的退火条件下,随离子注入剂量增加,表面掺杂浓度有微弱升高,即当离子注入剂量由2.4ˑ1015cm-3升高到3.2ˑ1015cm-3时,表面掺杂浓度由5.44ˑ1020atoms/cm3升高至6.49ˑ1020atoms/cm3㊂而钝化性能随离子注入剂量的升高呈现先微弱升高后不变的趋势,其中2.4ˑ1015cm-3注入剂量的隐开路电压均值为735mV,2.8ˑ1015cm-3和3.2ˑ1015cm-3注入剂量的隐开路电压均值为737mV㊂此时磷掺杂多晶硅与硅基底形成了良好的隧穿438㊀研究论文人工晶体学报㊀㊀㊀㊀㊀㊀第51卷效应㊂当离子注入剂量为2.8ˑ1015cm-3和3.2ˑ1015cm-3时,隐开路电压均值保持在737mV,表明磷掺杂多晶硅的钝化性能已达到最优,故制作电池确定离子注入的最佳剂量㊂电池电性能测试结果如表1所示㊂从表1可以看出,随离子注入剂量升高,电池的开路电压升高,电流升高,串联电阻R s降低,填充因子FF升高,电池的光电转换效率升高㊂当离子注入剂量为3.2ˑ1015cm-3时,电池开路电压最高为689mV,接触性能好,光电转换效率最高㊂同时,在同一退火条件下,低离子注入剂量对应的多晶硅层表面激活的磷原子较少,影响电池的接触性能,导致串联电阻R s升高,填充因子FF降低㊂而对于较高的离子注入剂量,掺杂多晶硅层的场钝化效果提升较明显,且表面激活的磷原子多,电池的表面钝化和接触性能均得到较大改善,使电池的转换效率得到提高㊂表1㊀基于不同离子注入剂量掺杂的TOPCon电池的I-V参数Table1㊀I-V parameters of TOPCon solar cells doped with different ion implantation doses Group V oc/V I sc/A R s FF/%E ta/%2.4ˑ10150.68510.390.002080.0622.612.8ˑ10150.68610.400.001980.5322.803.2ˑ10150.68910.420.001780.7823.01 2.2.2㊀退火时间的影响固定隧穿氧化层生长温度和多晶硅的沉积时间,采用相同的离子注入剂量3.2ˑ1015cm-3,相同的退火温度855ħ,研究退火时间对磷掺杂特性的影响,退火时间分别为15min㊁20min㊁25min㊂图8㊀不同退火时间下Poly-Si(N+)的掺杂分布和钝化性能Fig.8㊀Doping concentration distribution and passivation performance of Poly-Si(N+)annealing for different time 图8为不同退火时间的磷掺杂多晶硅掺杂曲线和钝化性能测试结果,由图中可以看出,当氧化层厚度和退火温度一定时,随退火时间延长,掺杂结深增加,即当退火时间从15min增加至20min和25min时,掺杂结深由0.2μm增加至0.25μm和0.3μm㊂表面浓度稍有下降,但均保持在5.2ˑ1020atoms/cm3以上,而隐开路电压均值i V oc呈现先升高后降低的现象,在退火时间为20min时达到最高值736mV,钝化性能达到最优㊂综合以上得出70nm多晶硅的最优掺杂条件为:离子注入剂量3.2ˑ1015/cm3,在855ħ退火20min时,其钝化性能可与120nm poly-Si(N+)的钝化性能相媲美,此时70nm掺杂多晶硅的表面掺杂浓度为5.6ˑ1020atoms/cm3,高于120nm掺杂多晶硅的表面掺杂浓度(2.7ˑ1020atoms/cm3),而高表面浓度更有利于电池的金属接触特性㊂2.3㊀基于70nm Poly-Si(N+)电池的电性能研究基于以上最优实验结果,制备70nm掺杂多晶硅的TOPCon电池,实验同时制作120nm掺杂多晶硅的TOPCon电池作为对比组,图9为不同厚度多晶硅的掺杂曲线,电池电性能测试结果如表2所示㊂㊀第3期宋志成等:超薄多晶硅的掺杂㊁钝化及光伏特性研究439㊀图9㊀不同厚度多晶硅的掺杂曲线Fig.9㊀Doping concentration distribution of Poly-Si(N+)with different thickness表2㊀基于不同厚度多晶硅的TOPCon电池的I-V参数Table2㊀I-V results of TOPCon solar cells featuring with different thickness of poly-silicon Group V oc/V I sc/A R s FF/%E ta/%70nm Poly-Si0.69110.470.002081.3023.34 120nm Poly-Si0.69110.450.002381.0023.21从图9可知70nm超薄多晶硅的表面掺杂浓度远高于120nm多晶硅的表面掺杂浓度,且70nm超薄Poly-Si电池效率具有明显的优势(见表2)㊂主要参数表现在电流I sc升高20mA,串联电阻R s降低,填充因子FF增加0.3%㊂其中电流升高是因为背面多晶硅减薄后寄生吸收减小,降低了背面多晶硅吸光的损失,而串联电阻降低和填充因子升高是因为70nm多晶硅表面掺杂浓度升高导致电池接触变好,因此70nm超薄Poly-Si电池效率得到明显提升㊂3㊀结㊀㊀论通过调整隧穿氧化层生长工艺和多晶硅沉积时间,制备了70nm超薄的本征多晶硅,并对离子注入剂量和退火时间进行了优化,确定了70nm超薄多晶硅的最优掺杂工艺㊂研究表明对于70nm超薄多晶硅,离子注入剂量的增加对多晶硅的掺杂分布和钝化性能影响较小,而退火时间对掺杂结深影响较大,这是因为工艺优化后的隧穿氧化层能够阻挡大量的磷原子进入基体硅,此时退火时间对掺杂结深的影响占主导作用㊂工艺优化后,70nm超薄多晶硅的钝化性能达到最优,与120nm Poly-Si(N+)的钝化水平相当,隐开路电压i V oc 平均值可达到736mV,且此时70nm超薄多晶硅的表面掺杂浓度是常规120nm的约2倍,达到5.6ˑ1020atoms/cm3㊂基于70nm多晶硅的高表面浓度掺杂和厚度减薄的特点,对应TOPCon电池的电流I sc 升高㊁串联电阻R s降低,填充因子FF升高,电池的光电转换效率得到明显提升㊂参考文献[1]㊀NANDAKUMAR N,RODRIGUEZ J,KLUGE T,et al.21.6%monoPoly TM cells with in situ interfacial oxide and poly-Si layers deposited byinline PECVD[C]//2018IEEE7th World Conference on Photovoltaic Energy Conversion(WCPEC).June10-15,2018,Waikoloa,HI,USA.IEEE,2018:2048-2051.[2]㊀CHEN Y,CHEN D,ALTERMATT P P,et al.25%large area industrial silicon solar cell[C].Learning From History and Future Perspective.in:36th EUPVSEC,Marseille,France,Proc.36th EUPVSEC,2019.[3]㊀GREEN M A,KEITH E,YOSHIHIRO H,et al.Solar cell efficiency tables(version49)[J].Progress in Photovoltaics,2017,25(1):3-13.[4]㊀RICHTER A,BENICK J,FELDMANN F,et al.N-type Si solar cells with passivating electron contact:identifying sources for efficiencylimitations by wafer thickness and resistivity variation[J].Solar Energy Materials and Solar Cells,2017,173:96-105.[5]㊀HAASE F,HOLLEMANN C,SCHÄFER S,et ser contact openings for local poly-Si-metal contacts enabling26.1%-efficient POLO-IBCsolar cells[J].Solar Energy Materials and Solar Cells,2018,186:184-193.[6]㊀PADHAMNATH P,WONG J,NAGARAJAN B,et al.Metal contact recombination in monoPoly TM solar cells with screen-printed&fire-throughcontacts[J].Solar Energy Materials and Solar Cells,2019,192:109-116.440㊀研究论文人工晶体学报㊀㊀㊀㊀㊀㊀第51卷[7]㊀WU Y,STODOLNY M K,GEERLIGS L J,et al.In-situ doping and local overcompensation of high performance LPCVD polysilicon passivatedcontacts as approach to industrial IBC cells[J].Energy Procedia,2016,92:427-433.[8]㊀FELDMANN F,FELLMETH T,STEINHAUSER B,et rge area TOPCon cells realized by a PECVD tube process[C]//36th EuropeanPhotovoltaic Solar Energy Conference and Exhibition.2019.[9]㊀DUTTAGUPTA S,NANDAKUMAR N,PADHAMNATH P,et al.mono Poly TM cells:large-area crystalline silicon solar cells with fire-throughscreen printed contact to doped polysilicon surfaces[J].Solar Energy Materials and Solar Cells,2018,187:76-81.[10]㊀LIMODIO G,YANG G,GE H,et al.Front and rear contact Si solar cells combining high and low thermal budget Si passivating contacts[J].Solar Energy Materials and Solar Cells,2019,194:28-35.[11]㊀REITER S,KOPER N,REINEKE-KOCH R,et al.Parasitic absorption in polycrystalline Si-layers for carrier-selective front junctions[J].Energy Procedia,2016,92:199-204.[12]㊀DUTTAGUPTA S,NANKAKUMAR N,RODRIGUEZ J W,et al.monoPoly TM Technology platform for enabling passivated-contacts in PERC/Tproduction lines[C].The SNEC Scientific Conference,2019.[13]㊀NANDAKUMAR N,RODRIGUEZ J,KLUGE T,et al.Approaching23%with large-area monoPoly cells using screen-printed and fired rearpassivating contacts fabricated by inline PECVD[J].Progress in Photovoltaics:Research and Applications,2018:pip.3097. [14]㊀CHEN D M,CHEN Y F,WANG Z G,et al.24.58%total area efficiency of screen-printed,large area industrial silicon solar cells with thetunnel oxide passivated contacts(i-TOPCon)design[J].Solar Energy Materials and Solar Cells,2020,206:110258.[15]㊀CHEN Y F,CHEN D M,LIU C F,et al.Mass production of industrial tunnel oxide passivated contacts(i-TOPCon)silicon solar cells withaverage efficiency over23%and modules over345W[J].Progress in Photovoltaics:Research and Applications,2019,27(10):827-834.[16]㊀LING Z P,XIN Z,WANG P Q,et al.Double-sided passivated contacts for solar cell applications:an industrially viable approach toward24%efficient large area silicon solar cells[M]//Silicon Materials:IntechOpen,2019:.[17]㊀RÖMER U,PEIBST R,OHRDES T,et al.Recombination behavior and contact resistance of n+and p+poly-crystalline Si/mono-crystalline Sijunctions[J].Solar Energy Materials and Solar Cells,2014,131:85-91.。
多晶硅刻蚀oes光谱

多晶硅刻蚀oes光谱
多晶硅刻蚀是一种用于制作半导体器件的工艺,其中,OES(Optical Emission Spectroscopy,光学发射光谱)被广泛用于监测刻蚀过程中的化学反应。
在多晶硅刻蚀过程中,通常使用的刻蚀剂是氢氟酸(HF)和硝酸(HNO3)的混合物。
当这种混合液与多晶硅表面接触时,会产生化学反应,硅与氢氟酸和硝酸反应生成二氧化硅(SiO2)和其他气体(如硅烷(SiH4)和水(H2O))。
OES技术可以用来监测这些化学反应,因为每种气体在燃烧时都会产生特定的光谱线。
通过测量和分析这些光谱线,可以得到关于刻蚀过程中反应速率和产物组成的详细信息,从而帮助控制刻蚀过程,保证刻蚀品质。
总的来说,多晶硅刻蚀中的OES光谱技术,是一种重要的在线监测手段,可以帮助实现高效、精准的半导体器件生产。
多晶硅离子刻蚀代加工

多晶硅离子刻蚀代加工多晶硅离子刻蚀代加工技术是一种新型的加工技术,它可以为各种硅结构制品提供高质量的加工服务。
这种技术利用离子束来实现硅片和多晶硅的加工,它可以获得清晰的图形结构和精细的外形。
本文介绍了多晶硅离子刻蚀代加工技术的基本原理,原理应用,步骤和正确加工过程的细节。
一、多晶硅离子刻蚀代加工技术的基本原理多晶硅离子刻蚀代加工技术是一种由硅片和多晶硅结构制品加工而成的新型技术,它是一种基于离子束来实现硅片和多晶硅的加工。
离子束的方向受抛射的电路的控制,可把一定量的离子束射向硅片或多晶硅上,可以实现硅片和多晶硅的刻蚀,代替传统的加工技术。
离子刻蚀代加工技术利用负电荷离子来实现加工,其可以把微米尺度的规整图形结构和精细的外形完美成型。
离子束的准确控制,可以把多晶硅表面的裂纹减少,可以把硅片的表面细节处理得更精细。
二、多晶硅离子刻蚀代加工技术的应用原理多晶硅离子刻蚀代加工技术具有良好的加工精度、快速加工和高质量加工等优势,因此被广泛用于各种硅结构制品的加工。
多晶硅离子刻蚀代加工技术可以用于多晶硅集成电路(IC)材料上,可以清除掉多晶硅表面的污垢,避免影响IC的性能。
它还可以用于多晶硅光学结构上,可以提高多晶硅的光学性能,使多晶硅的表面更加光滑。
多晶硅离子刻蚀代加工技术还可以用于硅片制品上,可以实现硅片外形的精细加工,提高硅片表面质量。
离子刻蚀代加工技术可以在硅片表面形成规整的图形结构,可以改善硅片的抗氧化性能。
三、多晶硅离子刻蚀代加工技术的加工过程多晶硅离子刻蚀代加工技术的整个加工过程包括准备工作、离子刻蚀代加工、喷涂表面处理、聚焦和图形微调这几个步骤。
(1)准备工作:在多晶硅离子刻蚀代加工之前,要做好准备工作,包括加载和清理仪器,以及对硅片和多晶硅的表面处理。
(2)离子刻蚀代加工:离子刻蚀代加工是完成加工的关键步骤,要控制抛射的离子束的方向,来实现精确刻蚀。
离子刻蚀代加工不仅可以达到高精度,还可以把多晶硅表面的裂纹减少,从而提高多晶硅的质量。
多晶硅刻蚀工艺的研究

多晶硅刻蚀工艺的研究
多晶硅刻蚀工艺是一种用于制备微电子器件的工艺。
多晶硅是一种多晶性的硅材料,具有良好的导电性和机械性能,被广泛应用于电子器件中。
多晶硅刻蚀工艺主要包括湿刻蚀和干刻蚀两种方法。
湿刻蚀是利用湿化学溶液对多晶硅进行腐蚀,常用的溶液有氢氟酸、酸性过氧化氢等。
干刻蚀则是利用气体放电或离子轰击等方式将多晶硅表面物质转化为气体或离子,从而实现刻蚀作用,常用的气体有氧气、氟化氢等。
多晶硅刻蚀工艺的研究主要涉及以下几个方面:
1. 刻蚀过程的理论研究:研究多晶硅刻蚀过程的机理,包括湿刻蚀和干刻蚀过程中的化学反应和物理机制。
2. 工艺参数的优化:通过对刻蚀工艺参数的改变,如溶液浓度、温度、刻蚀时间、气体流量等的优化,可以得到更好的刻蚀效果。
3. 刻蚀剂的开发:研究和设计新型的刻蚀剂,提高刻蚀效率和选择性,减少副作用。
4. 刻蚀模型的建立和仿真:通过建立刻蚀模型,进行仿真分析,可以预测刻蚀过程中的表面形貌和质量,并指导实际工艺。
5. 刻蚀工艺的应用研究:将多晶硅刻蚀工艺应用于实际的微电子器件制备中,如太阳能电池、集成电路等,研究工艺对器件性能的影响。
综上所述,多晶硅刻蚀工艺研究涉及多个方面,包括理论研究、工艺参数优化、刻蚀剂开发、刻蚀模型建立和仿真分析以及应用研究等,这些研究对于提高多晶硅器件的制备工艺和性能具有重要意义。
等离子体刻蚀多晶硅
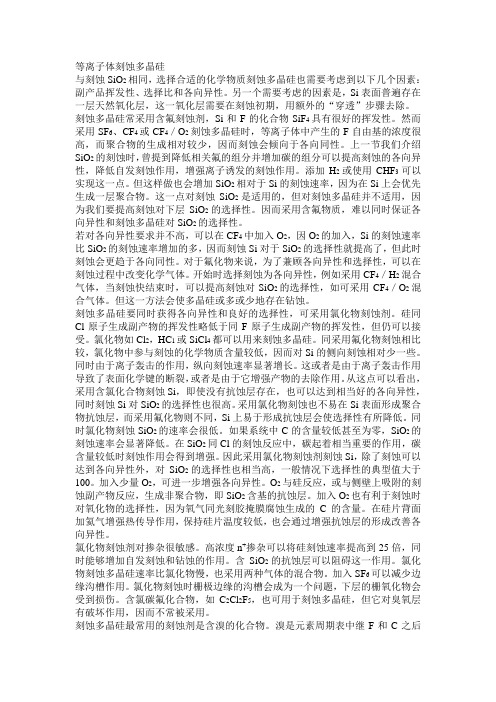
等离子体刻蚀多晶硅与刻蚀SiO2相同,选择合适的化学物质刻蚀多晶硅也需要考虑到以下几个因素:副产品挥发性、选择比和各向异性。
另一个需要考虑的因素是,Si表面普遍存在一层天然氧化层,这一氧化层需要在刻蚀初期,用额外的“穿透”步骤去除。
刻蚀多晶硅常采用含氟刻蚀剂,Si和F的化合物SiF4具有很好的挥发性。
然而采用SF6、CF4或CF4/O2刻蚀多晶硅时,等离子体中产生的F自由基的浓度很高,而聚合物的生成相对较少,因而刻蚀会倾向于各向同性。
上一节我们介绍SiO2的刻蚀时,曾提到降低相关氟的组分并增加碳的组分可以提高刻蚀的各向异性,降低自发刻蚀作用,增强离子诱发的刻蚀作用。
添加H2或使用CHF3可以实现这一点。
但这样做也会增加SiO2相对于Si的刻蚀速率,因为在Si上会优先生成一层聚合物。
这一点对刻蚀SiO2是适用的,但对刻蚀多晶硅并不适用,因为我们要提高刻蚀对下层SiO2的选择性。
因而采用含氟物质,难以同时保证各向异性和刻蚀多晶硅对SiO2的选择性。
若对各向异性要求并不高,可以在CF4中加入O2,因O2的加入,Si的刻蚀速率比SiO2的刻蚀速率增加的多,因而刻蚀Si对于SiO2的选择性就提高了,但此时刻蚀会更趋于各向同性。
对于氟化物来说,为了兼顾各向异性和选择性,可以在刻蚀过程中改变化学气体。
开始时选择刻蚀为各向异性,例如采用CF4/H2混合气体,当刻蚀快结束时,可以提高刻蚀对SiO2的选择性,如可采用CF4/O2混合气体。
但这一方法会使多晶硅或多或少地存在钻蚀。
刻蚀多晶硅要同时获得各向异性和良好的选择性,可采用氯化物刻蚀剂。
硅同Cl原子生成副产物的挥发性略低于同F原子生成副产物的挥发性,但仍可以接受。
氯化物如Cl2,HC1或SiCl4都可以用来刻蚀多晶硅。
同采用氟化物刻蚀相比较,氯化物中参与刻蚀的化学物质含量较低,因而对Si的侧向刻蚀相对少一些。
同时由于离子轰击的作用,纵向刻蚀速率显著增长。
这或者是由于离子轰击作用导致了表面化学键的断裂,或者是由于它增强产物的去除作用。
- 1、下载文档前请自行甄别文档内容的完整性,平台不提供额外的编辑、内容补充、找答案等附加服务。
- 2、"仅部分预览"的文档,不可在线预览部分如存在完整性等问题,可反馈申请退款(可完整预览的文档不适用该条件!)。
- 3、如文档侵犯您的权益,请联系客服反馈,我们会尽快为您处理(人工客服工作时间:9:00-18:30)。
多晶硅刻蚀特性的研究
随着硅珊MOS器件的出现,多晶硅渐渐成为先进器件材料的主力军。
文章主要对多晶硅刻蚀的特性进行研究,希望能够给相关人士一定的借鉴。
标签:多晶硅;刻蚀;研究
1 硅和多晶硅刻蚀的介绍
硅栅(Poly Gate)的干法刻蚀:
随着晶体管尺寸的不断缩小对硅栅的刻蚀就越具有挑战性。
因为受到光刻线宽的限制,为达到最后的CD线宽要求往往需要先对光阻进行缩小处理,然后进一步往下刻蚀。
BARC打开后,再以光阻为阻挡层将TEOS打开。
接着把剩余的光阻去除,再以TEOS作为阻挡层对硅栅进性刻蚀。
为了保护栅极氧化层不被损伤,通常要把硅栅的刻蚀分成几个步骤:主刻蚀、着陆刻蚀和过刻蚀。
主刻蚀通常有比较高的刻蚀率但对氧化硅的选择比较小。
通过主刻蚀可基本决定硅栅的剖面轮廓和关键尺寸。
着陆刻蚀通常对栅极氧化层有比较高的选择比以确保栅极氧化层不被损伤。
一旦触及到栅极氧化层后就必须转成对氧化硅选择比更高的过刻蚀步骤以确保把残余的硅清除干净而不损伤到栅极氧化层。
Cl2,HBr,HCl是硅栅刻蚀的主要气体,Cl2和硅反应生成挥发性的SiCl4而HBr和硅反应生成的SiBr4同样具有挥发性。
为了避免伤及栅极氧化层,任何带F基的气体如CF4,SF6,NF3都不能在过刻蚀的步骤中使用。
2 硅和多晶硅刻蚀的结构
我们介绍一个Logic刻蚀的程式,刻蚀多晶硅的结构包括PR,SION,Poly,Oxide。
多晶硅的线宽要求非常小。
如图1所示。
在MOS器件中,掺杂的LPCVD多晶硅是用做栅极的导电材料。
掺杂多晶硅线宽决定了有源器件的栅长,并会影响晶体管的性能。
因此,CD控制是很关键的。
多晶硅栅的刻蚀工艺必须对下层栅氧化层有高的选择比并具有非常好的均匀性和可重复性。
同时也要求高度的各向异性,因为多晶硅栅在源/漏的注入过程中起阻挡层的作用。
倾斜的侧壁会引起多晶硅栅结构下面部分的掺杂。
刻蚀多晶硅(硅)通常是一个三步工艺过程。
这使得在不同的刻蚀步骤中能对各向异性刻蚀和选择比进行优化。
这三个步骤是:
(1)第一步是预刻蚀,用于去除自然氧化层、硬的掩蔽层(如SiON)和表面污染物来获得均匀的刻蚀(这减少了刻蚀中作为微掩蔽层的污染物带来的表面缺陷)。
(2)接下来的是刻至终点的主刻蚀。
这一步用来刻蚀掉大部分的多晶硅膜,并不损伤栅氧化层和获得理想的各向异性的侧壁剖面。
(3)最后一步是过刻蚀,用于去除刻蚀残留物和剩余多晶硅,并保证对栅氧化层的高选择比。
这一步应避免在多晶硅周围的栅氧化层形成微槽。
3 硅和多晶硅刻蚀的实验
在MOS器件中,刻蚀多晶硅(硅)的第一步工艺过程(去除自然氧化层、硬的掩蔽层SiON)中,会出现刻蚀中作为微掩蔽层的污染物带来的表面缺陷。
致使多晶硅相连导电,造成器件不能工作,结果导致低的良品率。
我们需要在这预刻蚀的步骤中能对程序进行优化。
图2所示缺陷类型分析图。
3.1 扫描电镜和能谱分析
利用SEM环境扫描电子显微镜对原料的形貌进行观察及元素组成进行分析。
扫描电子分析结果见图3以及扫描电镜及能谱分析结果见图4所示:
图3 缺陷示意图
图4 扫描电镜及能谱分析结果
由图3缺陷示意图可知,晶片缺陷在硅片的边上,形成一堆的形状。
从图4扫描电镜及能谱分析结果表现为SiON已经刻蚀完毕,只剩下多晶硅没有被刻蚀。
3.2 刻蚀工艺所使用的仪器及型号
本章实验所用的仪器及型号是日本生产的TEL- Unity IIe型号
图5 仪器设备
3.3 刻蚀工艺的分析和优化
从机台本身的工艺参数去验证晶片缺陷的来源。
用一片单晶硅首先去测试晶片缺陷的数量,然后把它放进机器的腔室,用产品的程序只是通气体和压力运行,最后再去测试晶片缺陷的数量,用这次的数量减去上次的数量,得到的是机台的缺陷测试结果:
图6 晶片激光作用样品的电子电镜高分辨像
图6晶片激光作用样品的电子电镜高分辨像所示,测试结果和产品缺陷图是一致的,并且从EDX分析出有C,F,O的成分。
刻蚀残留物是刻蚀以后留在硅片表面不想要的材料。
它常常覆盖在腔体内壁
或被刻蚀图形的底部。
它的产生有多种原因,例如被刻蚀膜层中的污染物、选择了不合适的化学刻蚀剂、腔体中的污染物、膜层中不均匀的杂质分布。
刻蚀以后的残留物有不同的名称,包括长细线条、掩蔽物、冠状物和栅条。
长细线条是一些没有完全去除干净的细小的被刻蚀材料残留物,具有电活性,能在图形之间形成不希望的短路。
聚合物的形成有时是有意的,是为了在刻蚀图形的侧壁上的形成抗腐蚀膜从而防止横向刻蚀,这样做能形成高的各向异性图形,因为聚合物能阻挡对侧壁的刻蚀,增强刻蚀的方向性,从而实现对图形关键尺寸的良好控制。
这些聚合物是在刻蚀过程中由光刻胶中的碳转化而来并与刻蚀气体和刻蚀生成物结合在一起而形成的。
这些侧壁聚合物很复杂,包括刻蚀剂和反应的生成物。
聚合物链有很强的难以氧化和去除的碳氟键。
然而,这些聚合物又必须在刻蚀完成以后去除,否则器件的成品率和可靠性都会受到影响。
这些侧壁的清洗常常需要在等离子体清洗工艺中使用特殊的化学气体,或者有可能用强溶剂进行湿法清洗后再用去离子水进行清洗。
聚合物链有很强的难以氧化和去除的碳氟键,聚合物淀积在工艺腔中的内部部件,也被聚合物覆盖。
如图7所示,形成CFx的聚合物淀积在工艺腔中,这是对于CF4/CO/Ar/CH2F2气体反应形成的聚合物。
但对于刻蚀掩蔽层SiON的程序采用的是CF4/CHF4/O2气体,它产生的聚合物带有CxHFx,不容易覆盖在工艺腔体中,并且容易毁坏工艺腔体中的覆盖层,使聚合物从工艺腔体中落在晶片表面,形成晶体缺陷。
聚合物形成原理如图8。
图8 聚合物形成原理
3.4 试验结果与讨论
聚合物淀积的一个不希望的副作用是工艺腔中的内部部件也被聚合物覆盖。
刻蚀工艺腔需要定期的清洗来去除聚合物或替换掉不能清洗的部件。
所以我们研究改变工艺参数来减低聚合物淀积到晶片表面。
通常,标准的工艺顺序是首先晶片吸附,再衬底表面上提供能量比较高的离子,然后当工艺完成后,晶片进行去电荷。
这样的工艺顺序容易使工艺腔体中和其他部件上的聚合物在晶片吸附和去电荷的过程中掉在晶片上。
如图9标准的工艺过程顺序。
图9 标准的工艺过程顺序
根据图10改进的工艺过程顺序,通过优化的反应程序,在工艺吸附电荷和释放电荷的步骤一直给衬底表面上提供能量比较高的离子作用,使刻蚀工艺腔形成聚合物,从而减低聚合物淀积到晶片表面。
图11 所示为优化后的反应程序。
3.5 本章小结
3.5.1 对于刻蚀多晶硅(硅)的第一步工艺过程(去除自然氧化层、硬的掩蔽层SiON)中,会出现刻蚀中作为微掩蔽层的污染物带来的表面缺陷。
图10 改进的工艺过程顺序
图11 优化后的反应程序
3.5.2 通过机台参数的测试,发现机台端测试的结果与产品反应出来的缺陷是同样的,SEM和EDX实验结果均表明,造成缺陷的原因是由于腔体中有聚合体的残留。
3.5.3 刻蚀工艺腔需要定期的清洗来去除聚合物或替换掉不能清洗的部件,可以使残留物减低。
优化实验研究结果还表明,在同样腔体环境中,如果采用优化程序可以延长刻蚀工艺腔需要定期清洗的时间。