锅炉受热面氧化皮预防措施
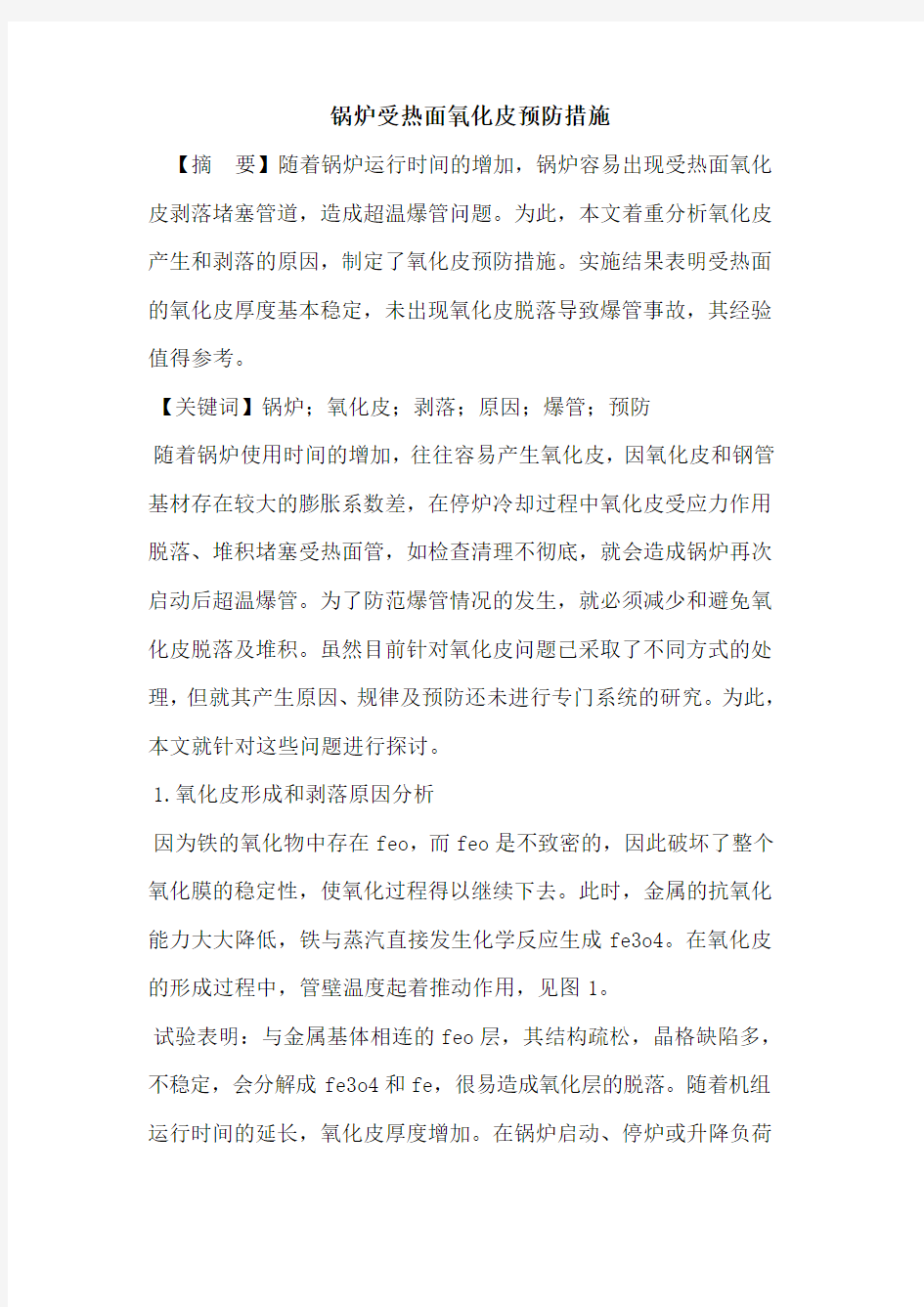
- 1、下载文档前请自行甄别文档内容的完整性,平台不提供额外的编辑、内容补充、找答案等附加服务。
- 2、"仅部分预览"的文档,不可在线预览部分如存在完整性等问题,可反馈申请退款(可完整预览的文档不适用该条件!)。
- 3、如文档侵犯您的权益,请联系客服反馈,我们会尽快为您处理(人工客服工作时间:9:00-18:30)。
锅炉受热面氧化皮预防措施
【摘要】随着锅炉运行时间的增加,锅炉容易出现受热面氧化皮剥落堵塞管道,造成超温爆管问题。为此,本文着重分析氧化皮产生和剥落的原因,制定了氧化皮预防措施。实施结果表明受热面的氧化皮厚度基本稳定,未出现氧化皮脱落导致爆管事故,其经验值得参考。
【关键词】锅炉;氧化皮;剥落;原因;爆管;预防
随着锅炉使用时间的增加,往往容易产生氧化皮,因氧化皮和钢管基材存在较大的膨胀系数差,在停炉冷却过程中氧化皮受应力作用脱落、堆积堵塞受热面管,如检查清理不彻底,就会造成锅炉再次启动后超温爆管。为了防范爆管情况的发生,就必须减少和避免氧化皮脱落及堆积。虽然目前针对氧化皮问题已采取了不同方式的处理,但就其产生原因、规律及预防还未进行专门系统的研究。为此,本文就针对这些问题进行探讨。
1.氧化皮形成和剥落原因分析
因为铁的氧化物中存在feo,而feo是不致密的,因此破坏了整个氧化膜的稳定性,使氧化过程得以继续下去。此时,金属的抗氧化能力大大降低,铁与蒸汽直接发生化学反应生成fe3o4。在氧化皮的形成过程中,管壁温度起着推动作用,见图1。
试验表明:与金属基体相连的feo层,其结构疏松,晶格缺陷多,不稳定,会分解成fe3o4和fe,很易造成氧化层的脱落。随着机组运行时间的延长,氧化皮厚度增加。在锅炉启动、停炉或升降负荷
过程中管子温度变化很大,由于母材和氧化膜的热膨胀能力不同,基体会对表面的氧化皮产生拉或压的作用,导致氧化膜开裂。钢材的热膨胀系数一般在(16~20)×10-6k-1,而氧化铁的热膨胀系数一般在9.1×10-6k-1。由于热膨胀系数的差异,多层氧化层达到一定厚度,加上温度发生剧烈或反复变化,氧化皮就很容易从金属本体剥离。具体如下:
(1)机组运行期间过热器管和再热器管表面氧化层会逐渐增厚。当管壁超温时过热器管和再热器管表面氧化层会迅速增厚,并由双层结构变成多层结构。
(2)不同材料的氧化层抗剥离能力有较大差别,因此材料的选用是否合理是氧化皮剥离的重要影响因素。
(3)机组在停机和启动时,以及负荷、温度和压力变化较大时产生较大的热应力。
(4)蒸汽管道汽侧氧化皮的生长与剥离与机组是否采用给水全挥发处理或给水加氧处理没有直接关联。
2.ot处理法基本原理和特点
传统给水avt处理是尽可能降低给水中溶解氧的质量浓度,并加入氨提高水、汽系统的ph值,同时加入联氨除去给水剩余的o2,使水、汽系统处于还原性条件下。在avt工况下,碳钢表面形成fe3o4保护膜,该氧化膜在高速流动的高温纯水中有较高的溶解度,因此碳钢制的高压加热器、给水管、省煤器以及疏水系统等容易发生流动加速腐蚀。给水、疏水中铁质量浓度一般较高,会带来锅炉受热
面结垢速率偏高、锅炉化学清洗周期缩短等问题。而给水高ph值的运行条件也明显缩短凝结水精处理混床的运行周期,精处理混床再生频繁,再生剂的消耗量、再生自用水量及废水排放量等大大提高。
3.氧化皮生成预防
3.1 氧化皮预防措施
3.1.1 启动阶段
启动阶段应注意:
(1)启动前严格按照规定进行系统冲洗,不盲目追求启动速度,各个阶段严控水质。
(2)控制点火后的温升速度在1.5k/min以下,短时最大不超过3k/min。对采用微油和等离子点火机组,必须控制启动速度,尽量保持给煤量在35t/h以下。
(3)启动过程中对管道进行吹管,排除杂物,保持较大的旁路开度,使有较大流量的蒸汽对管屏进行吹管。严控冲转参数,尽量减少氧化皮对汽轮机的影响。
(4)启动阶段严格控制减温水的投入。尽量通过燃烧控制启动温度和压力,不投入减温水;确实需要投入减温水时要控制减温水分级小量投入,保障减温器前、后温差在30k以下,防止温度剧减造成氧化皮脱落。
3.1.2 正常运行阶段
正常运行时应注意:
(1)保持屏式过热器、高温过热器和高温再热器沿程汽温恒定,避免汽温大幅波动使氧化皮脱落。
(2)金属管屏严禁超温运行,超温后如燃烧调整无效,必须降参数甚至降负荷运行,将壁温控制在允许极限温度以下。
(3)运行中加强壁温监视。
(4)主汽温尽量通过煤水比调整,控制减温水量恒定,分级小量投入,保障减温器前、后温差在50k以下,防止温度剧减造成氧化皮脱落。
(5)再热汽温采用烟气再循环和火焰中心控制,尽量避免投入减温水或减温水量大幅波动。
(6)加强受热面的热偏差监视和调整,进行超温及氧化皮变化情况实时统计、记录,有效进行锅炉寿命管理,实现“状态检修”。(7)采用锅炉给水加氧控制技术,促使锅炉受热面氧化皮沉积速率显著降低。
3.1.3 停炉阶段
停炉时应注意:
(1)降温速率控制在1.2k/min以下,不为节能而加快停机速度。(2)尽量控制较少的减温水投入,当确认不再需要减温水控制汽温时,尽快隔离减温水,防止阀门内漏,在停炉过程或者停炉后仍有冷水进入造成氧化皮剥落。
(3)正常停炉10h后才进行自然通风,自然通风6~8h后才进行强制通风,控制高温过热器烟温下降速度≤0.5k/min,二次风热
风温度与室温差≤85k才破坏炉底水封,主汽压到1mpa以下进行热炉放水。
(4)事故状态下采用滑参数停机,锅炉快冷时,主蒸汽的温降、压降必须严格控制,降低受热面的冷却速度,不能过分追求缩短停炉和冷却时间。
(5)停炉后,定期监测锅炉管内壁氧化层厚度。
3.2 氧化皮监测
采用金相显微镜测量:
(1)高温过热器(取其中a40排)氧化皮主要成分fe3o4、fe2o3及少量mfe2o4等,其中m为ni、cr等。氧化皮最大厚度约26μm,最薄处小于5μm。
(2)高温再热器(取其中a20排),氧化皮主要成分fe3o4,fe2o3少量mfe2o4等,其中m为ni、cr等。最大厚度约18μm,最薄处氧化皮厚度小于2μm。实践证明:预防措施是有效的。
3.3 给水加氧预控
给水加氧处理时,在合适的给水溶解氧质量浓度下,为了中和微量酸性物质,调整凝结水精处理出口加氨量,使给水和凝结水的ph
值维持在8.8~9.0,相应给水电导率为1.8~2.7μs/cm(加氨泵投自动情况下,除氧器入口给水电导率设定值为2.0μs/cm)。给水的ot处理向avt(o)处理切换的条件:
(1)机组正常停机前4~6h;
(2)当机组给水氢电导>0.15μs/cm,并有继续增大的趋势时,