半水煤气湿法脱硫和干法脱硫的脱硫状况
脱硫工艺技术对比

脱硫工艺技术对比脱硫工艺技术是指将燃煤电厂或锅炉排放的硫化物进行减排的技术方法。
目前常见的脱硫工艺技术包括湿法脱硫和干法脱硫两种。
下面将对这两种脱硫工艺技术进行对比。
湿法脱硫是一种利用化学反应将SO2转化为硫酸盐的方法。
这种技术主要包括石灰石石膏法、石灰浆喷雾吸收法和海水脱硫法等。
其中石灰石石膏法是最常用的湿法脱硫技术。
这种方法是将石灰石与SO2气体反应生成硫酸钙,然后再通过过滤的方式分离出硫酸盐。
湿法脱硫技术具有脱硫效率高、操作稳定等优点,但是其缺点是投资大、设备体积大、能耗高。
干法脱硫是一种通过化学吸附或物理吸附的方式将SO2气体去除的技术。
这种技术主要包括活性炭吸附法、电吸附法和干式法等。
其中活性炭吸附法是最常用的干法脱硫技术。
这种方法是将煤炭燃烧产生的SO2经过活性炭吸附,使其转化为硫酸盐。
干法脱硫技术具有投资小、装置简单等优点,但是其缺点是脱硫效率低、处理能力有限。
对比来看,湿法脱硫技术相较于干法脱硫技术在脱硫效率和稳定性上更有优势。
湿法脱硫技术通过化学反应将SO2转化为硫酸盐,脱硫效率可以达到90%以上,而干法脱硫技术的脱硫效率一般在70%左右。
此外,湿法脱硫技术操作相对稳定,适用范围广,可以适应不同燃煤电厂或锅炉的需求。
然而,湿法脱硫技术也存在一些问题。
首先是投资成本高,设备体积大,需要占用较多的空间。
其次是能耗高,需要大量的能源来进行操作。
另外,湿法脱硫技术还会产生大量的废水和废渣,对环境造成一定的污染。
干法脱硫技术相较于湿法脱硫技术在投资成本和能耗方面具有优势。
干法脱硫技术投资成本相对较低,适用于一些投资有限的企业。
同时,干法脱硫技术使用的能源相对较少,节省了能源成本。
然而,干法脱硫技术的脱硫效率相对较低,不能达到湿法脱硫技术的脱硫效果。
此外,干法脱硫技术对煤种的适应性较差,处理能力有限。
因此,在选择脱硫工艺技术时,需要综合考虑各种因素,选择最合适的技术方案。
综上所述,在湿法脱硫技术和干法脱硫技术之间进行对比,可以发现每种技术都有自己的优势和劣势。
干法、半干法与湿法脱硫技术的性能比较分析
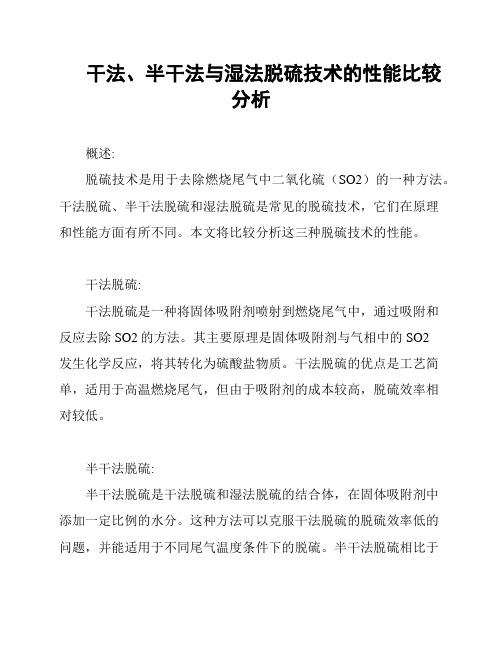
干法、半干法与湿法脱硫技术的性能比较分析概述:脱硫技术是用于去除燃烧尾气中二氧化硫(SO2)的一种方法。
干法脱硫、半干法脱硫和湿法脱硫是常见的脱硫技术,它们在原理和性能方面有所不同。
本文将比较分析这三种脱硫技术的性能。
干法脱硫:干法脱硫是一种将固体吸附剂喷射到燃烧尾气中,通过吸附和反应去除SO2的方法。
其主要原理是固体吸附剂与气相中的SO2发生化学反应,将其转化为硫酸盐物质。
干法脱硫的优点是工艺简单,适用于高温燃烧尾气,但由于吸附剂的成本较高,脱硫效率相对较低。
半干法脱硫:半干法脱硫是干法脱硫和湿法脱硫的结合体,在固体吸附剂中添加一定比例的水分。
这种方法可以克服干法脱硫的脱硫效率低的问题,并能适用于不同尾气温度条件下的脱硫。
半干法脱硫相比于干法脱硫的优点是脱硫效率提高,同时工艺相对简单,但仍存在着固体湿度的控制问题。
湿法脱硫:湿法脱硫是通过喷射液态吸收剂,将燃烧尾气中的SO2吸收起来,形成硫酸盐溶液的方法。
这种方法可以达到较高的脱硫效率,适用于不同的燃烧尾气温度和湿度条件。
湿法脱硫的优点是脱硫效果好,可以将SO2的排放量降至很低水平,但同时也存在着液态吸收剂的消耗和废液处理的问题。
比较分析:在脱硫效率方面,湿法脱硫优于干法脱硫和半干法脱硫。
湿法脱硫可以达到90%以上的脱硫效果,而干法脱硫和半干法脱硫则在70%左右。
然而,湿法脱硫的成本相对较高,液态吸收剂的消耗和废液处理需要较大的投入。
在工艺简单性方面,干法脱硫是最简单的方法,其次是半干法脱硫,湿法脱硫的工艺相对复杂。
干法脱硫适用于高温尾气处理,半干法脱硫适用于不同温度条件下的处理,湿法脱硫适用于不同温度和湿度条件下的处理。
结论:根据对干法脱硫、半干法脱硫和湿法脱硫的性能比较分析,可以得出以下结论:- 干法脱硫适用于高温燃烧尾气,工艺简单但脱硫效率相对较低。
- 半干法脱硫兼具干法脱硫和湿法脱硫的优点,脱硫效率较高且工艺相对简单。
- 湿法脱硫脱硫效率最高,但成本较高,液态吸收剂消耗和废液处理需要考虑。
半水煤气脱硫系统硫堵浅析
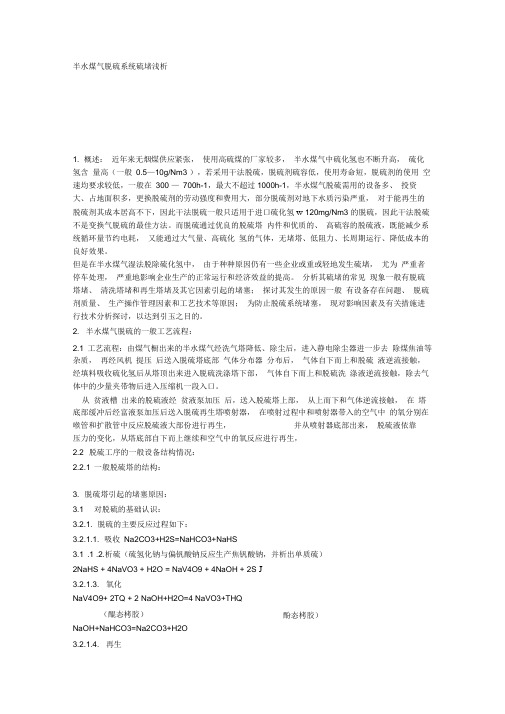
半水煤气脱硫系统硫堵浅析1. 概述:近年来无烟煤供应紧张,使用高硫煤的厂家较多,半水煤气中硫化氢也不断升高,硫化氢含量高(一般0.5—10g/Nm3 ),若采用干法脱硫,脱硫剂硫容低,使用寿命短,脱硫剂的使用空速均要求较低,一般在300 —700h-1,最大不超过1000h-1,半水煤气脱硫需用的设备多、投资大、占地面积多,更换脱硫剂的劳动强度和费用大,部分脱硫剂对地下水质污染严重,对于能再生的脱硫剂其成本居高不下,因此干法脱硫一般只适用于进口硫化氢w 120mg/Nm3 的脱硫,因此干法脱硫不是变换气脱硫的最佳方法。
而脱硫通过优良的脱硫塔内件和优质的、高硫容的脱硫液,既能减少系统循环量节约电耗,又能通过大气量、高硫化氢的气体,无堵塔、低阻力、长周期运行、降低成本的良好效果。
但是在半水煤气湿法脱除硫化氢中,由于种种原因仍有一些企业或重或轻地发生硫堵,尤为严重者停车处理,严重地影响企业生产的正常运行和经济效益的提高。
分析其硫堵的常见现象一般有脱硫塔堵、清洗塔堵和再生塔堵及其它因素引起的堵塞;探讨其发生的原因一般有设备存在问题、脱硫剂质量、生产操作管理因素和工艺技术等原因;为防止脱硫系统堵塞,现对影响因素及有关措施进行技术分析探讨,以达到引玉之目的。
2. 半水煤气脱硫的一般工艺流程:2.1 工艺流程:由煤气橱出来的半水煤气经洗气塔降低、除尘后,进入静电除尘器进一步去除煤焦油等杂质,再经风机提压后送入脱硫塔底部气体分布器分布后,气体自下而上和脱硫液逆流接触,经填料吸收硫化氢后从塔顶出来进入脱硫洗涤塔下部,气体自下而上和脱硫洗涤液逆流接触,除去气体中的少量夹带物后进入压缩机一段入口。
从贫液槽出来的脱硫液经贫液泵加压后,送入脱硫塔上部,从上而下和气体逆流接触,在塔底部缓冲后经富液泵加压后送入脱硫再生塔喷射器,在喷射过程中和喷射器带入的空气中的氧分别在喉管和扩散管中反应脱硫液大部份进行再生,并从喷射器底部出来,脱硫液依靠压力的变化,从塔底部自下而上继续和空气中的氧反应进行再生,2.2 脱硫工序的一般设备结构情况:2.2.1 一般脱硫塔的结构:3. 脱硫塔引起的堵塞原因:3.1 对脱硫的基础认识:3.2.1. 脱硫的主要反应过程如下:3.2.1.1. 吸收Na2CO3+H2S=NaHCO3+NaHS3.1 .1 .2.析硫(硫氢化钠与偏钒酸钠反应生产焦钒酸钠,并析出单质硫)2NaHS + 4NaVO3 + H2O = NaV4O9 + 4NaOH + 2S J3.2.1.3. 氧化NaV4O9+ 2TQ + 2 NaOH+H2O=4 NaVO3+THQ(醌态栲胶)酚态栲胶)NaOH+NaHCO3=Na2CO3+H2O3.2.1.4. 再生2 THQ+1/2O2=2TQ+H2O3.1.1.5. 副反应2NaHS+2O2=NaS2O3 +H2O Na2CO3+CO2+H2O=2NaHCO3 Na2CO3+HCN=NaCHS2NaCN+5 O2=Na2SO4+CO2 f +S02 f + N2 f副反应消耗了Na2CO3,降低了溶液脱硫的能力,使溶液的活性下降,因此生产中应严格控制副反应。
湿法脱硫和干法脱硫的原理
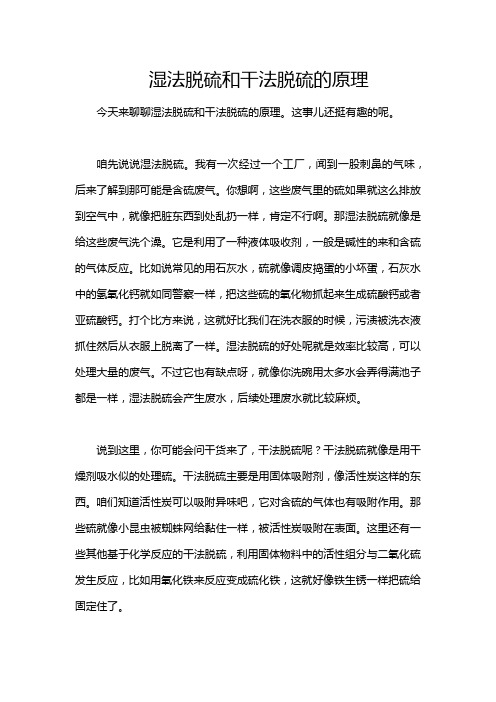
湿法脱硫和干法脱硫的原理今天来聊聊湿法脱硫和干法脱硫的原理。
这事儿还挺有趣的呢。
咱先说说湿法脱硫。
我有一次经过一个工厂,闻到一股刺鼻的气味,后来了解到那可能是含硫废气。
你想啊,这些废气里的硫如果就这么排放到空气中,就像把脏东西到处乱扔一样,肯定不行啊。
那湿法脱硫就像是给这些废气洗个澡。
它是利用了一种液体吸收剂,一般是碱性的来和含硫的气体反应。
比如说常见的用石灰水,硫就像调皮捣蛋的小坏蛋,石灰水中的氢氧化钙就如同警察一样,把这些硫的氧化物抓起来生成硫酸钙或者亚硫酸钙。
打个比方来说,这就好比我们在洗衣服的时候,污渍被洗衣液抓住然后从衣服上脱离了一样。
湿法脱硫的好处呢就是效率比较高,可以处理大量的废气。
不过它也有缺点呀,就像你洗碗用太多水会弄得满池子都是一样,湿法脱硫会产生废水,后续处理废水就比较麻烦。
说到这里,你可能会问干货来了,干法脱硫呢?干法脱硫就像是用干燥剂吸水似的处理硫。
干法脱硫主要是用固体吸附剂,像活性炭这样的东西。
咱们知道活性炭可以吸附异味吧,它对含硫的气体也有吸附作用。
那些硫就像小昆虫被蜘蛛网给黏住一样,被活性炭吸附在表面。
这里还有一些其他基于化学反应的干法脱硫,利用固体物料中的活性组分与二氧化硫发生反应,比如用氧化铁来反应变成硫化铁,这就好像铁生锈一样把硫给固定住了。
老实说,我一开始也不明白为啥不能都用一种方法脱硫,后来才知道不同的工业环境、要求等适用不同的脱硫方法。
比如说小型的、对废气处理量少的可能干法脱硫就够用了,又简单又不用考虑废水。
而大型的工厂,要处理大规模的含硫废气,湿法脱硫效率高就能发挥优势了。
进一步延伸思考呀,现在环保要求越来越严格,不管是湿法脱硫还是干法脱硫都在不断改进。
未来会不会有更完美的脱硫方法呢?比如说不用复杂的设备,也不会产生废水废渣的方法。
各位读者朋友你们有没有啥看法呀?欢迎大家一起讨论。
在实际应用的时候,干法脱硫对于低浓度的含硫气体比较合适,而且操作简单,维护成本也低;湿法脱硫适合高浓度、大规模的含硫气体处理,虽然设备复杂、维护成本高一些,但是效率很高。
干法脱硫与湿法脱硫优劣谈
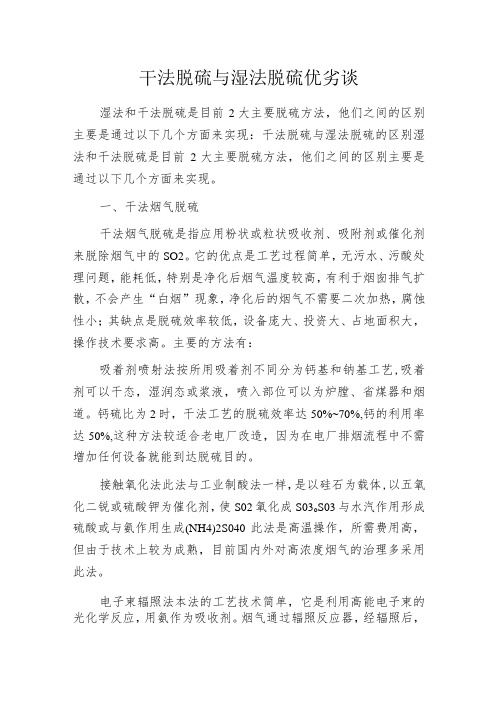
干法脱硫与湿法脱硫优劣谈湿法和干法脱硫是目前2大主要脱硫方法,他们之间的区别主要是通过以下几个方面来实现:干法脱硫与湿法脱硫的区别湿法和干法脱硫是目前2大主要脱硫方法,他们之间的区别主要是通过以下几个方面来实现。
一、干法烟气脱硫干法烟气脱硫是指应用粉状或粒状吸收剂、吸附剂或催化剂来脱除烟气中的SO2。
它的优点是工艺过程简单,无污水、污酸处理问题,能耗低,特别是净化后烟气温度较高,有利于烟囱排气扩散,不会产生“白烟”现象,净化后的烟气不需要二次加热,腐蚀性小;其缺点是脱硫效率较低,设备庞大、投资大、占地面积大,操作技术要求高。
主要的方法有:吸着剂喷射法按所用吸着剂不同分为钙基和钠基工艺,吸着剂可以干态,湿润态或浆液,喷入部位可以为炉膛、省煤器和烟道。
钙硫比为2时,干法工艺的脱硫效率达50%~70%,钙的利用率达50%,这种方法较适合老电厂改造,因为在电厂排烟流程中不需增加任何设备就能到达脱硫目的。
接触氧化法此法与工业制酸法一样,是以硅石为载体,以五氧化二锐或硫酸钾为催化剂,使S02氧化成S03o S03与水汽作用形成硫酸或与氨作用生成(NH4)2S040此法是高温操作,所需费用高,但由于技术上较为成熟,目前国内外对高浓度烟气的治理多采用此法。
电子束辐照法本法的工艺技术简单,它是利用高能电子束的光化学反应,用氨作为吸收剂。
烟气通过辐照反应器,经辐照后,分解产生了大量的氢氧基和氧原子,促进烟气中二氧化硫和氮氧化物形成硫酸和硝酸,继而与添加物氨反应生成硫酸锭、硝酸铁等混合物,作为农用肥料。
二、湿法烟气脱硫湿法烟气脱硫是指应用液体吸收剂(如水或碱性溶液等)洗涤烟气脱除烟气中的SO2。
它的优点是脱硫效率高,设备小、投资省、操作较容易、容易控制以及占地面积小;而缺点是易造成二次污染,存在废水后处理问题,能耗高,特别是洗涤后烟气的温度低,不利于烟囱排气的扩散,易产生“白烟”,需要二次加热,腐蚀严重等。
主要的方法有:石灰石-石膏法该工艺是利用石灰石/石灰石浆液洗涤烟道气,使之与S02反应,生成亚硫酸钙(CaSo3),经分离的亚硫酸钙可以抛弃,也可以通入空气强制氧化和参加一些添加剂,以石膏形式开展回收。
有图有真相,干法、半干法、湿法脱硫,太详细
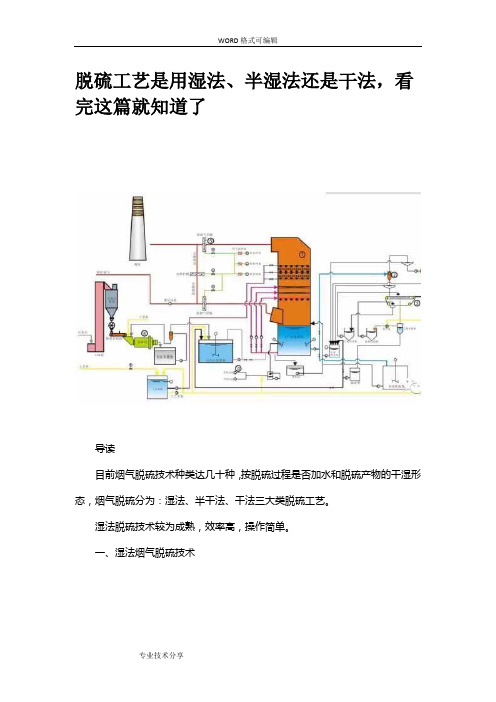
脱硫工艺是用湿法、半湿法还是干法,看完这篇就知道了导读目前烟气脱硫技术种类达几十种,按脱硫过程是否加水和脱硫产物的干湿形态,烟气脱硫分为:湿法、半干法、干法三大类脱硫工艺。
湿法脱硫技术较为成熟,效率高,操作简单。
一、湿法烟气脱硫技术优点:湿法烟气脱硫技术为气液反应,反应速度快,脱硫效率高,一般均高于90%,技术成熟,适用面广。
湿法脱硫技术比较成熟,生产运行安全可靠,在众多的脱硫技术中,始终占据主导地位,占脱硫总装机容量的80%以上。
缺点:生成物是液体或淤渣,较难处理,设备腐蚀性严重,洗涤后烟气需再热,能耗高,占地面积大,投资和运行费用高。
系统复杂、设备庞大、耗水量大、一次性投资高,一般适用于大型电厂。
分类:常用的湿法烟气脱硫技术有石灰石-石膏法、间接的石灰石-石膏法、柠檬吸收法等。
技术路线A、石灰石/石灰-石膏法原理:是利用石灰石或石灰浆液吸收烟气中的SO2,生成亚硫酸钙,经分离的亚硫酸钙(CaSO3)可以抛弃,也可以氧化为硫酸钙(CaSO4),以石膏形式回收。
是目前世界上技术最成熟、运行状况最稳定的脱硫工艺,脱硫效率达到90%以上。
目前传统的石灰石/石灰—石膏法烟气脱硫工艺在现在的中国市场应用是比较广泛的,其采用钙基脱硫剂吸收二氧化硫后生成的亚硫酸钙、硫酸钙,由于其溶解度较小,极易在脱硫塔内及管道内形成结垢、堵塞现象。
对比石灰石法脱硫技术,双碱法烟气脱硫技术则克服了石灰石—石灰法容易结垢的缺点。
B 、间接石灰石-石膏法:常见的间接石灰石-石膏法有:钠碱双碱法、碱性硫酸铝法和稀硫酸吸收法等。
原理:钠碱、碱性氧化铝(Al2O3·nH2O)或稀硫酸(H2SO4)吸收SO2,生成的吸收液与石灰石反应而得以再生,并生成石膏。
该法操作简单,二次污染少,无结垢和堵塞问题,脱硫效率高,但是生成的石膏产品质量较差。
C、柠檬吸收法:原理:柠檬酸(H3C6H5O7·H2O)溶液具有较好的缓冲性能,当SO2气体通过柠檬酸盐液体时,烟气中的SO2与水中H发生反应生成H2SO3络合物,SO2吸收率在99%以上。
半水煤气脱硫

成氨工艺有很大的危害, 常见的有: 对催化剂的危害; 对产品质量的危害; 对碳酸丙烯酯脱碳操作的危害; 对铜洗操作的危害;对金属腐蚀; 对人体的危害。
合成氨厂半水煤气中硫化物的种类较多。
其主要是硫化氢, 约占硫化物总量的90%。
另外还含有少量的有机硫化物, 主要是二硫化碳、羰基硫、硫醇等。
硫化氢分子式为H 2 S, 是无色气体, 有类似腐烂鸡蛋的恶臭味。
性剧毒, 易溶于水, 其水溶液呈酸性, 能与碱生成盐。
可用碱溶液来吸收它以除去气体中的硫化氢。
硫化氢有很强的还原能力, 易被氧化成硫磺和水, 这一性质被广泛的用于脱除硫化氢并副产硫磺的工艺上。
硫化氢还容易与金属、金属氧化物或金属的盐类生产金属硫化物。
由于在生产过程中的H2 S会对生产造成很大的危害, 同时硫化氢为有毒有害气体, 为了减少生产的损失、保护环境必须除掉H2 S 气体。
脱硫的方法很多, 可分为干法和湿法两大类, 其中湿式氧化法脱硫多用于半水煤气和变换气的一次脱硫, 而干法脱硫多用于变换气脱硫和碳化气的精脱硫。
干法脱硫具有流程短, 设备结构简单, 气体净化度高, 操作平稳的优点。
但此法经常采用固定层反应器, 需要定期更换脱硫剂, 不能连续。
由于受脱硫剂硫容量( 单位质量脱硫剂能脱除硫的最大含量) 的限制, 干法脱硫一般用于含硫量较低的情况。
湿式氧化法脱硫不仅具有吸收速度快,生产强度大等特点,而且具有脱硫过程连续,溶液易再生,副产硫磺等特点,因而被合成氨厂广泛采用;湿式氧化法脱硫的不足之处是不能有效脱除有机硫化物,没有干法脱硫净化度高。
脱硫技术在合成氨厂中常采用湿式氧化法脱硫, 目前中小型合成氨厂常用的湿式氧化脱硫法有: 氨水催化法、栲胶法、改良ADA法、PDS法、M SQ 法, KCA 法, 888法。
1.氨水催化法氨水催化法系采用8~ 25滴度的氨水, 其中加0. 2~ 0. 3 g /L对苯二酚作催化剂, 使溶解于液相的硫化氢氧化为元素硫; 本法有氨损失较大的缺点, 此外, 溶液的硫容量较低, 仅为0. 1~ 0. 15g /L。
合成氨厂半水煤气脱硫技术现状及展望
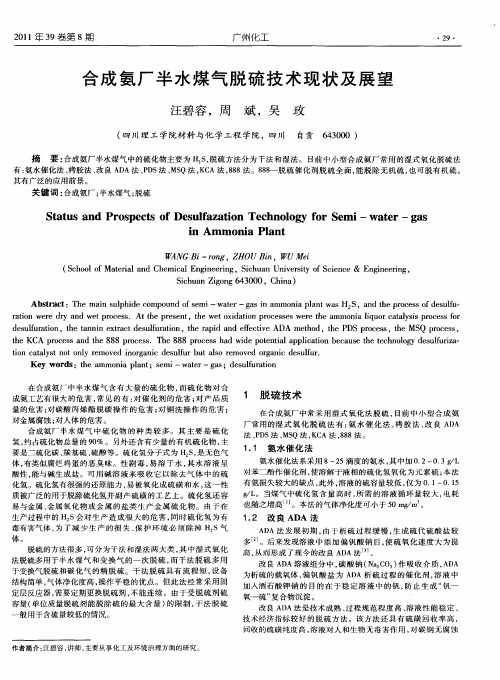
体, 有类似腐烂鸡 蛋 的恶臭 味。性剧 毒 , 易溶 于水 , 其水 溶 液呈 酸 性 , 与 碱 生 成 盐 。可 用 碱 溶 液 来 吸 收 它 以 除 去 气 体 中 的 硫 能 化氢。硫化氢有很强 的还原能力 , 易被 氧化成 硫磺和 水 , 这一性 质被广泛的用于脱除硫化氢并 副产硫磺 的工艺 上。硫化 氢还容 易 与 金 属 、 属 氧 化 物 或 金 属 的盐 类 生 产 金 属 硫 化 物 。 由 于 在 金 生 产 过 程 中 的 H S会 对 生 产 造 成 很 大 的 危 害 , 时 硫 化 氢 为 有 : 同 毒有 害气体 , 了减 少 生产 的 损失 、 护 环境 必 须 除掉 H S气 为 保
t e KCA r c s n he8 o e s h p o e sa d t 88 pr c s .Th 8 r c s a d oe ta p lc to e a s h e h o o y d s lu ia e 8 8 p o e s h d wie p t n ila p i ai n b c u e t e tc n lg e u f rz — to aay tn to l e v d i o g ni e u f r b tas e v d o g ni e u f r in c t ls o ny r mo e n r a c d s lu u lo r mo e r a c d s lu .
半水煤气脱硫

置:主页> 大气治理技术> ?正文水煤气,水煤气,半水煤气系统脱硫综合分析2011-11-21 15:55湖南环保网-湖南第一环保门户网站,绿色,低碳点击: 302 次天然气,焦炉气,煤气,石油裂解气等气体中都含有一定数量的硫化氢和有机硫化物(主要有羰基硫,二硫化碳,硫醇,硫醚等),原料气中的硫化物能导致甲醇,合成氨生产中催化剂中毒,增加液态溶剂的黏度,腐蚀,堵塞设备和管道,影响产品质量。
燃烧物和工业装置排放的气体进入大气,造成环境污染,危害人体健康。
笔者主要针对合成氨,甲醇工业原料气中的硫化氢脱除工艺进行简单介绍。
1 小型氮肥企业脱硫工艺状况1.1 工艺条件的选择气体中硫化物的脱除方法主要有吸收,吸附,膜渗透,化学转化,凝缩等,根据原料气的种类,处理量大小和硫化物的种类,含量,可选用不同的脱除方法和工艺条件。
一般在1套系统中采用2种以上脱硫方法。
国内大型氮肥企业采取的脱硫工艺一般为低温甲醇洗,小型氮肥企业一般采取碱性溶液加催化剂吸收以及吸附或膜渗透等方法。
碱性溶液加催化剂吸收方法工艺路线基本相同,区别在于不同企业根据自身情况而选用不同的脱硫催化剂。
1.2 水煤气,半水煤气脱硫湿法脱硫一般的工艺路线水煤气,半水煤气由气柜经洗气塔,静电除焦器,罗茨风机和降温塔后,进入脱硫塔,在脱硫塔填料层中与脱硫液逆流接触,气体中的无机硫和部分有机硫被溶液吸收后,进入分离器和清洗冷却器,冷却分离后的气体经静电除焦器进入气体压缩机。
脱硫泵从贫液槽抽取"贫液"进入塔内,吸收后的"富液"进入富液槽经泵加压后送入再生槽,经喷射器吸收空气氧化再生后,单质硫以泡沫的形式从再生槽中浮选出来,"富液"转化为"贫液""贫液"经液位调节器进入贫液槽,循环使用。
1.3 变换气脱硫变换气脱硫工序的工艺和设备基本与半水煤气脱硫相同,各企业根据自身的情况选择不同的操作压力.一般的工艺路线为:来自变换或其他工段的气体进入脱硫塔,在脱硫塔填料层中与脱硫液逆流接触,气体中的H2S被溶液吸收后,进入分离器,分离后的气体进入后续工段.脱硫泵从贫液槽抽取"贫液"进入塔内,吸收后的"富液"进入再生槽,在催化剂的作用下经喷射器吸收空气氧化再生后,单质硫以泡沫的形式从再生槽中浮选出来,"富液"转化为"贫液""贫液"经液位调节器进入贫液槽,循环使用,由于干法脱硫剂存在饱和硫容,故干法脱硫虽然在水煤气,半水煤气系统无泵的动力消耗,但企业一般并不采用。
干法、半干法和湿法脱硫技术的综合比较

干法、半干法和湿法脱硫技术的综合比较干法、半干法与湿法脱硫技术的综合比较摘要:大气SO污染状况日益严重,治理技术亟待解决,其中烟气脱硫技术是目前世界上唯一大规模商业化应用的脱硫方式。
比较成熟的烟气脱硫技术主要有湿法、干法、半干法烟气脱硫技术。
本文主要综述了脱除烟气中SO的一些主要技术,包括干法、半干法、湿法烟气脱硫的原理、反应系统、技术比较以及它们的优缺点,其中湿法烟气脱硫应用最为广泛,干法、半干法烟气脱硫技术也有了较多的应用。
关键字:烟气脱硫,湿法,干法,半干法1引言煤炭在我国的能源结构占主导地位的状况已持续了几十年,近年来随着石油天然气和水能开发量的增加,煤炭在能源结构中的比例有所减少,但其主导地位仍未改变,其消费量占一次能源总消费量的70流右,这种局面在今后相当长时间不会改变,目前燃煤SQ排放量占SO总排放量的90%U上,我国超过美国成为世界SQ 排放第一大国。
烟气中的SQ是大气污染的主要成份,也是形成酸雨的主要物质。
酸雨不仅严重腐蚀建筑物和公共设施,而且毁坏大面积的森林和农作物。
如何经济有效地控制燃煤中SO的排放是我国乃至世界能源和环保领域亟待解决的关键性问题。
从世界上烟气脱硫技术的发展来看主要经历了以下3个阶段:a) 20世纪70年代,以石灰石湿法为代表第一代烟气脱硫。
b) 20世纪80年代,以干法、半干法为代表的第二代烟气脱硫。
主要有喷雾干燥法、炉喷钙加炉后增湿活化(LIFAC)、烟气循环流化床(CFB)、循环半干法脱硫工艺(NID)等。
这些脱硫技术基本上都采用钙基吸收剂,如石灰或消石灰等。
随着对工艺的不断改良和发展,设备可靠性提高,系统可用率达到97%脱硫率一般为70%-95%适合燃用中低硫煤的中小型锅炉。
c) 20世纪90年代,以湿法、半干法和干法脱硫工艺同步发展的第三代烟气脱硫。
2.1湿法脱硫技术湿法烟气脱硫(WFGD技术是使用液体碱性吸收剂洗涤烟气以除去二氧化硫。
该技术的特点是整个脱硫系统位于燃煤锅炉的除尘系统之后、烟囱之前,脱硫过程在溶液中进行,脱硫剂和脱硫生成物均为湿态,其脱硫过程的反应温度低于露点,反应速度快,脱硫效率咼,技术比较成熟,生产运行安全可靠,因此在众多的脱硫技术中,始终占据主导地位。
燃煤电厂各种干法、半干法、湿法脱硫技术及优缺点汇总
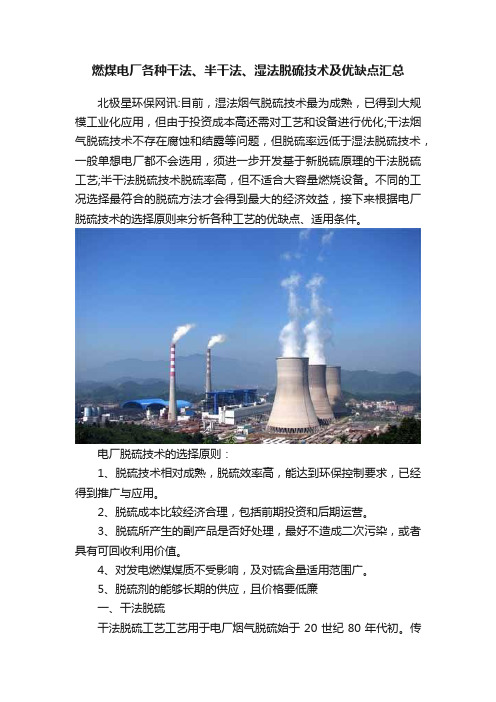
燃煤电厂各种干法、半干法、湿法脱硫技术及优缺点汇总北极星环保网讯:目前,湿法烟气脱硫技术最为成熟,已得到大规模工业化应用,但由于投资成本高还需对工艺和设备进行优化;干法烟气脱硫技术不存在腐蚀和结露等问题,但脱硫率远低于湿法脱硫技术,一般单想电厂都不会选用,须进一步开发基于新脱硫原理的干法脱硫工艺;半干法脱硫技术脱硫率高,但不适合大容量燃烧设备。
不同的工况选择最符合的脱硫方法才会得到最大的经济效益,接下来根据电厂脱硫技术的选择原则来分析各种工艺的优缺点、适用条件。
电厂脱硫技术的选择原则:1、脱硫技术相对成熟,脱硫效率高,能达到环保控制要求,已经得到推广与应用。
2、脱硫成本比较经济合理,包括前期投资和后期运营。
3、脱硫所产生的副产品是否好处理,最好不造成二次污染,或者具有可回收利用价值。
4、对发电燃煤煤质不受影响,及对硫含量适用范围广。
5、脱硫剂的能够长期的供应,且价格要低廉一、干法脱硫干法脱硫工艺工艺用于电厂烟气脱硫始于20世纪80年代初。
传统的干法脱硫工艺主要有干法喷钙脱硫工艺、荷电干法吸收剂喷射脱硫法、电子束照射法、吸附法等。
传统的干法脱硫技术有工艺简单投资少,设备简占地面积小且不存在腐蚀和结露,副产品是固态无二次污染等优点,在缺水地区优势明显。
但是脱硫效率很低,一般脱硫效率只能达到70%左右,难以满足排放要求。
干法喷钙脱硫工艺工艺介绍磨细的石灰石粉通过气力方式喷人锅炉炉膛中温度为900~1250℃的区域在炉内发生的化学反应包括石灰石的分解和煅烧,SO2和SO3与生成的CaO之间的反应。
颗粒状的反应产物与飞灰的混合物被烟气流带人活化塔中;剩余的CaO与水反应,在活化塔内生成Ca(OH)2,而Ca(OH)2很快与SO2反应生成CaSO3,其中部分CaSO3被氧化成CaSO4;脱硫产物呈干粉状,大部分与飞灰一起被电除尘器收集下来,其余的从活化塔底部分离出来从电除尘器和活化塔底部收集到的部分飞灰通过再循环返回活化塔中。
浅谈半干法脱硫技术问题及脱硫效率

浅谈半干法脱硫技术问题及脱硫效率半干法脱硫技术是一种常用的烟气脱硫方法,其原理是在烟气中加入一定量的水蒸气,使烟气中的二氧化硫与水蒸气反应生成硫酸气体,然后通过沉降或过滤的方式去除硫酸气体,从而达到脱硫的目的。
半干法脱硫技术相比于湿法脱硫技术具有一定的优势。
由于半干法脱硫中烟气所含水分较少,所以在氧化反应中,氧化剂与反应物接触面积较大,反应速度较快,脱硫效率较高。
半干法脱硫中使用的吸收剂可以循环利用,降低了运行成本。
半干法脱硫设备体积相对较小,占地面积较少,适用于空间有限的场所。
半干法脱硫技术也存在一些问题。
半干法脱硫设备需要消耗一定的水蒸气,因此在水资源紧张的地区可能面临供水问题。
半干法脱硫技术对烟气的温度和湿度有一定的要求,过低或过高的温湿度会影响脱硫效果。
由于半干法脱硫设备中含有一定量的水分,可能会导致设备的腐蚀问题。
半干法脱硫技术对所用的吸收剂要求较高,吸收剂的合理选择和循环利用的技术也是亟待解决的问题。
在提高半干法脱硫效率方面,可以采取以下措施。
通过优化设备结构和提高设备的操作稳定性,减小烟气与吸收剂的接触时间,提高反应效率。
研究合理的吸收剂配比和添加剂,增加脱硫效果。
可以采取多级脱硫的方式,提高脱硫效率。
适当提高烟气温度和水蒸气的含量,也能提高脱硫效率。
半干法脱硫技术是一种常用的烟气脱硫方法,具有脱硫效率高、设备体积小等优势。
但在实际应用中还存在一些问题,如水资源供应、设备腐蚀和吸收剂选择等。
通过改进设备结构、提高设备操作稳定性、优化吸收剂配比和添加剂、采用多级脱硫等措施,可以提高半干法脱硫的效率。
浅谈湿法脱硫技术问题及脱硫效率

浅谈湿法脱硫技术问题及脱硫效率摘要:随着我国家国民经济的持续发展,对工业生产的需求和生活在电力上的人们日益增加。
但同时电厂所提供的生产力是会对环境产生影响的,为了尽可能的达到国家制定的安全标准,严格控制了过程中生成的二氧化硫。
基于此,讨论和分析湿脱硫技术和脱硫效率的问题。
关键词:湿法脱硫;技术问题;脱硫效率引言:脱硫是工业生产中防治大气污染的重要技术措施之一。
一般指燃料燃烧前从燃料中脱硫的过程和燃烧气体排放前脱硫的过程。
脱硫有很多选择。
总的来说,脱硫技术的选择原则主要有:脱硫技术比较成熟,脱硫效率高,能满足环保控制要求,并已得到推广应用;脱硫成本相对便宜且合理,包括初期投资和后续运行;无论副产品是否易于处理,最好不要造成二次污染或具有可回收价值;不影响发电用燃煤质量,硫含量应用范围广;脱硫剂可长期供货,价格低廉。
目前最常用的方法只有三种,即干法脱硫、湿法脱硫和半干半湿法脱硫。
其余的原因是成本高、技术要求高、使用频率低。
一般来说,三类硫排放控制工艺是:在燃烧前向其他化学原料中添加物质以改变其性质,减少污染;燃烧中选择封闭式鼓风炉,对这些污染气体进行均匀回收;燃烧后经过专业处理,达到国家统一脱硫标准。
工艺的种类很多,化学法有石膏法和磷铵肥法,用得比较多,化学法有喷雾干燥法。
湿法脱硫技术在我国燃煤发电项目中应用广泛。
下面就湿法脱硫和脱硫效率的技术问题进行分析探讨。
一、燃煤电厂脱硫废水的来源及特点在燃煤电厂中,烟气污染物主要包括二氧化硫、硫化物、氯化物、氟化物、重金属离子和烟尘等。
为防止硫污染,必须对含硫烟气进行脱硫处理。
根据工艺特点,目前烟气脱硫技术有湿法、半干法和干法三种,大部分燃煤电厂采用石灰石-石膏湿法脱硫工艺。
为避免污染物在厂内堆积,湿法脱硫工艺为避免系统内污染物富集,须排放一部分废水以维持系统内污染物浓度,这部分废水主要含有大量悬浮物、过饱和的亚硫酸盐、硫酸盐以及重金属等污染物。
二、湿法脱硫技术出现问题原因1结垢、堵塞等问题分析在湿法脱硫技术中,使用的主要材料是石灰石或石膏。
湿法脱硫和干法脱硫的区别
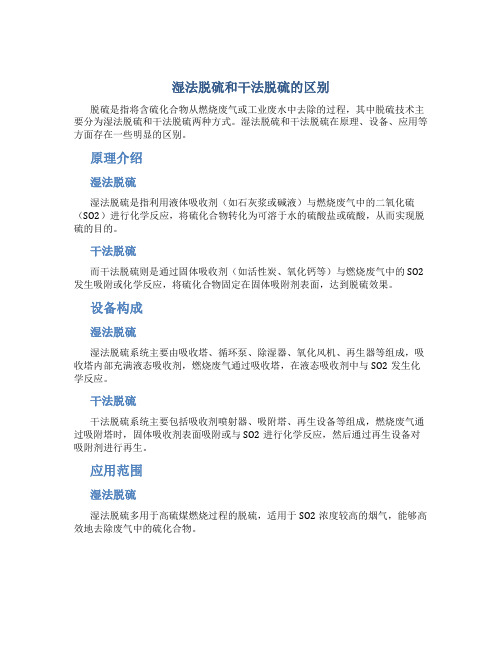
湿法脱硫和干法脱硫的区别
脱硫是指将含硫化合物从燃烧废气或工业废水中去除的过程,其中脱硫技术主要分为湿法脱硫和干法脱硫两种方式。
湿法脱硫和干法脱硫在原理、设备、应用等方面存在一些明显的区别。
原理介绍
湿法脱硫
湿法脱硫是指利用液体吸收剂(如石灰浆或碱液)与燃烧废气中的二氧化硫(SO2)进行化学反应,将硫化合物转化为可溶于水的硫酸盐或硫酸,从而实现脱硫的目的。
干法脱硫
而干法脱硫则是通过固体吸收剂(如活性炭、氧化钙等)与燃烧废气中的SO2发生吸附或化学反应,将硫化合物固定在固体吸附剂表面,达到脱硫效果。
设备构成
湿法脱硫
湿法脱硫系统主要由吸收塔、循环泵、除湿器、氧化风机、再生器等组成,吸收塔内部充满液态吸收剂,燃烧废气通过吸收塔,在液态吸收剂中与SO2发生化学反应。
干法脱硫
干法脱硫系统主要包括吸收剂喷射器、吸附塔、再生设备等组成,燃烧废气通过吸附塔时,固体吸收剂表面吸附或与SO2进行化学反应,然后通过再生设备对吸附剂进行再生。
应用范围
湿法脱硫
湿法脱硫多用于高硫煤燃烧过程的脱硫,适用于SO2浓度较高的烟气,能够高效地去除废气中的硫化合物。
干法脱硫
干法脱硫适用于低SO2浓度的烟气处理,且对废气处理后的废水产生较少,能够实现资源的回收再利用。
结论
总的来说,湿法脱硫方式适用于高SO2浓度、对产生废水处理能力要求较高的场合,而干法脱硫则更加适用于低SO2浓度、对废水处理要求不高的场合。
在实际应用中,选择合适的脱硫技术将更好地保护环境、减少污染物排放。
半水煤气脱硫技术知识分享
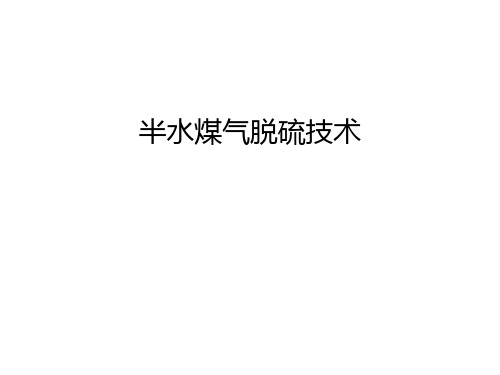
3) 废液处理流程较长,能耗高,致使装置投资费用较高。
PDS
PDS 工艺主要应用于煤气、焦炉气、合成 氨厂、半水煤气、炼厂气等,一般是与
ADA 法和栲胶法配合使用。只需要在原脱 硫液中加微量的 PDS 即可,消耗费用较
低。
PDS法脱硫的原理及工艺流程 来自粗苯的温度为30~35℃的煤气依次进入2台串联的脱硫塔底部,与塔顶
也较复杂,设备投资较大。
经济效益
栲胶法根据碱源不同分为碱性 栲胶(以橡椀栲胶和偏钒酸钠 为催化剂)脱硫和
氨法栲胶(以氨代替碱)脱硫。 栲胶法适用于焦炉气脱硫,焦 炉气与半水煤气的区
别在于其含萘及煤焦油、HCN 较多,而 C02 较少。因此,只 要前工序(静电除尘除
焦、脱萘等)正常,使用栲胶法 是可行的。栲胶法和改良的 ADA 法工艺流程完全相
离心后的硫膏外运,离心液经过低位槽返回脱硫系统,工艺流程见图1。
PDS碱法脱硫包括气体进入液体的扩散过 程,也包括化学反应过程。影响扩散的因 素有温度、液气比、传质面积、脱硫液浓 度等;影响化学反应的因素包括脱硫液组 成、温度、化学反应种类、反应进行程度 等。
该工艺优点
: 1) 适用范同广,能够脱除高含量硫; 2) 脱硫脱氰效率高,H2S 脱除率可达 96%以上,HCN 脱除率可达 95%以上。
Na2SO4≥40g/L 时,设备开始腐蚀,Na2SO4≥80g/L 时设备腐蚀相当严重。
ADA
我公司甲醇系统改良ADA法脱硫流程: 一、气体8 n) F, C) @. I0 _& Z 中变气脱硫塔底部,与塔顶进入的Na2CO3溶液逆向接触,脱除H2S,使出塔 气体中H2S含量<10PPm,COS含量<5PPm,再分别进入脱硫塔后分离器 分离夹带溶液,气体温度约50℃,压力2.4 MPa(G)送至脱碳工序。" v2 Y6 ~) u+ y9 w+ Y 二、溶液 脱硫塔底部排出的含硫富液进入氧化再生塔底部,来自空气压缩机J0502约 0.5Mpa(G)的压缩空气分别经U型管液封进入氧化再生塔底部空气分配器, 在塔内充分鼓泡混合、反应,使硫化物氧化,析出元素硫。形成的硫泡沫由 塔顶部溢流至硫泡沫槽F0201。经氧化再生后的贫液,由再生塔中上部扩大部 分自流到脱硫溶液循环槽,贫液再经脱硫泵J0203a,b升压后送入脱硫塔,继 续吸收中变气中的硫化物,并循环使用。硫泡沫槽内的硫泡沫液,经硫泡沫 泵J0201a,b送至转鼓真空过滤机L0201,过滤出单质硫,该硫膏液经下料斗流 到熔硫釜ⅠF0203,沉积到釜内的硫量不断增多,当釜内硫膏充满度达80%时, 进行间歇熔硫操作,利用0.4MPa(G)蒸汽通入熔硫釜夹套加热釜内硫膏, 使釜底部硫层的温度在120~130℃保持4h,硫变成熔融状态,易于流动的液 体硫,顺利地从釜内放出,到硫铸模内自然冷却成型。 Na2CO3 53g/l ADA 2g/l NaVO3 2g/l3 C" j/ S7 K- @. `0 L* ] PH值 8.0-8.5 总碱度(N)0.5-0.6
干法、半干法与湿法脱硫技术的综合比较
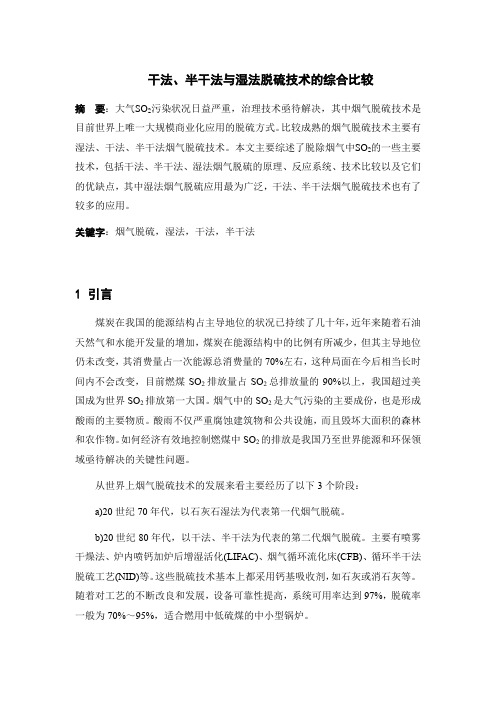
干法、半干法与湿法脱硫技术的综合比较摘要:大气SO2污染状况日益严重,治理技术亟待解决,其中烟气脱硫技术是目前世界上唯一大规模商业化应用的脱硫方式。
比较成熟的烟气脱硫技术主要有湿法、干法、半干法烟气脱硫技术。
本文主要综述了脱除烟气中SO2的一些主要技术,包括干法、半干法、湿法烟气脱硫的原理、反应系统、技术比较以及它们的优缺点,其中湿法烟气脱硫应用最为广泛,干法、半干法烟气脱硫技术也有了较多的应用。
关键字:烟气脱硫,湿法,干法,半干法1 引言煤炭在我国的能源结构占主导地位的状况已持续了几十年,近年来随着石油天然气和水能开发量的增加,煤炭在能源结构中的比例有所减少,但其主导地位仍未改变,其消费量占一次能源总消费量的70%左右,这种局面在今后相当长时间内不会改变,目前燃煤SO2排放量占SO2总排放量的90%以上,我国超过美国成为世界SO2排放第一大国。
烟气中的SO2是大气污染的主要成份,也是形成酸雨的主要物质。
酸雨不仅严重腐蚀建筑物和公共设施,而且毁坏大面积的森林和农作物。
如何经济有效地控制燃煤中SO2的排放是我国乃至世界能源和环保领域亟待解决的关键性问题。
从世界上烟气脱硫技术的发展来看主要经历了以下3个阶段:a)20世纪70年代,以石灰石湿法为代表第一代烟气脱硫。
b)20世纪80年代,以干法、半干法为代表的第二代烟气脱硫。
主要有喷雾干燥法、炉内喷钙加炉后增湿活化(LIFAC)、烟气循环流化床(CFB)、循环半干法脱硫工艺(NID)等。
这些脱硫技术基本上都采用钙基吸收剂,如石灰或消石灰等。
随着对工艺的不断改良和发展,设备可靠性提高,系统可用率达到97%,脱硫率一般为70%~95%,适合燃用中低硫煤的中小型锅炉。
c)20世纪90年代,以湿法、半干法和干法脱硫工艺同步发展的第三代烟气脱硫。
2.1 湿法脱硫技术湿法烟气脱硫(WFGD)技术是使用液体碱性吸收剂洗涤烟气以除去二氧化硫。
该技术的特点是整个脱硫系统位于燃煤锅炉的除尘系统之后、烟囱之前,脱硫过程在溶液中进行,脱硫剂和脱硫生成物均为湿态,其脱硫过程的反应温度低于露点,反应速度快,脱硫效率高,技术比较成熟,生产运行安全可靠,因此在众多的脱硫技术中,始终占据主导地位。
有图有真相_干法、半干法、湿法脱硫_太详细

脱硫工艺是用湿法、半湿法还是干法,看完这篇就知道了导读目前烟气脱硫技术种类达几十种,按脱硫过程是否加水和脱硫产物的干湿形态,烟气脱硫分为:湿法、半干法、干法三大类脱硫工艺。
湿法脱硫技术较为成熟,效率高,操作简单。
一、湿法烟气脱硫技术优点:湿法烟气脱硫技术为气液反应,反应速度快,脱硫效率高,一般均高于90%,技术成熟,适用面广。
湿法脱硫技术比较成熟,生产运行安全可靠,在众多的脱硫技术中,始终占据主导地位,占脱硫总装机容量的80%以上。
缺点:生成物是液体或淤渣,较难处理,设备腐蚀性严重,洗涤后烟气需再热,能耗高,占地面积大,投资和运行费用高。
系统复杂、设备庞大、耗水量大、一次性投资高,一般适用于大型电厂。
分类:常用的湿法烟气脱硫技术有石灰石-石膏法、间接的石灰石-石膏法、柠檬吸收法等。
技术路线A、石灰石/石灰-石膏法原理:是利用石灰石或石灰浆液吸收烟气中的SO2,生成亚硫酸钙,经分离的亚硫酸钙(CaSO3)可以抛弃,也可以氧化为硫酸钙(CaSO4),以石膏形式回收。
是目前世界上技术最成熟、运行状况最稳定的脱硫工艺,脱硫效率达到90%以上。
目前传统的石灰石/石灰—石膏法烟气脱硫工艺在现在的中国市场应用是比较广泛的,其采用钙基脱硫剂吸收二氧化硫后生成的亚硫酸钙、硫酸钙,由于其溶解度较小,极易在脱硫塔内及管道内形成结垢、堵塞现象。
对比石灰石法脱硫技术,双碱法烟气脱硫技术则克服了石灰石—石灰法容易结垢的缺点。
B 、间接石灰石-石膏法:常见的间接石灰石-石膏法有:钠碱双碱法、碱性硫酸铝法和稀硫酸吸收法等。
原理:钠碱、碱性氧化铝(Al2O3·nH2O)或稀硫酸(H2SO4)吸收SO2,生成的吸收液与石灰石反应而得以再生,并生成石膏。
该法操作简单,二次污染少,无结垢和堵塞问题,脱硫效率高,但是生成的石膏产品质量较差。
C、柠檬吸收法:原理:柠檬酸(H3C6H5O7·H2O)溶液具有较好的缓冲性能,当SO2气体通过柠檬酸盐液体时,烟气中的SO2与水中H发生反应生成H2SO3络合物,SO2吸收率在99%以上。
- 1、下载文档前请自行甄别文档内容的完整性,平台不提供额外的编辑、内容补充、找答案等附加服务。
- 2、"仅部分预览"的文档,不可在线预览部分如存在完整性等问题,可反馈申请退款(可完整预览的文档不适用该条件!)。
- 3、如文档侵犯您的权益,请联系客服反馈,我们会尽快为您处理(人工客服工作时间:9:00-18:30)。
半水煤气湿法脱硫和干法脱硫的脱硫状况
一、湿法脱硫的现状:
净化作业区湿法脱硫是两套脱硫装置,原设计是年产20万吨焦炉气生产合成氨所配套的湿法脱硫,设计脱硫数据是250mg/ m3脱除到10mg/ m3,由于焦炉气供量不足,另上一套年产10万吨半水煤气生产合成氨的配套装置。
下面对1-6月份湿法脱硫岗位主要指标统计:
1、湿法脱硫岗位进出口半水煤气H2S和有机硫统计:
从目前的生产状况来看,湿法脱硫整体运行较好。
目前主要存在的主要问题是;一、原设计富液槽过小,导致溶液留时间过短,再生不好,悬浮硫有所增加。
二、硫回收硫泡沫过滤不好,高温残液增加,使系统复盐有所上升,但未影响湿法脱硫的正常运行。
从湿法脱硫进出口的硫化氢的分析来看,脱出无机硫的效率在99.8%,脱出有机硫的效率为67.1%,因此从总体来说,湿法脱硫的脱硫效率是走在行业前列的,并未影响到干法脱硫。
二、半水煤气干法脱硫的现状
(1)、原设计焦炉气干法系统流程图:
从原设计流程来看,氧化锌主要起精脱硫把关,保护转化、低变触媒的作用。
按原设计满负荷生产氧化锌最少可用1-2年。
由于焦炉气气量不足,公司决定上半水煤气系统,原设计流程有所改动,改动如下:
目前焦炉气干法系统流程图:
目前半水煤气系统流程图:
三、在使用第二槽过程中,我们对氧化锌进行分析数据跟踪,统计如下:
1#氧化锌槽进口H2S和有机硫统计:
1#氧化锌更换时间为2014年1月26日,1月28日投入系统运行,6月15日,因出口总硫达到7.08mg/NM3时,为保证精脱氧化锌的安全运行,将1#氧化锌槽切出。
在运行过程中发生2次氧含量超标导致氧化锌温度超标,(最高温度为590℃),共脱出半水煤气量为:49519829NM3,其中1#氧化锌进口总硫平均为9.2mg/m3(其中有机硫为8.29mg/m3),1#氧化锌装填触媒为30吨,根据厂家提供氧化锌硫容(无机硫为20%--25%,有机硫为2%--3%),1#氧化锌槽可吸无机硫为:30×0.2=6(T),有机硫为:30×0.02=0.6(T);
根据目前实际使用情况,1#氧化锌槽吸无机硫为:50.73kg,吸有机硫为:380.25kg;
四、1#、2#氧化锌在使用过程中出现的问题;
1、1#、2#氧化锌自2013年8月24日投运,2014年1月6日出口总硫超标,最高达到,于1月13日停车,计划对1#、2#氧化锌脱硫剂进行更换。
2、氧化锌运行时因2次氧含量超标出现热点温度超标,之后下层5点温度持续在500℃左右,但出口温度正常;
3、打开检查后发现1#氧化锌槽内衬局部脱落并有约10mm 的裂纹,2#氧化锌槽内衬整体脱落,耐火球表面有一层黑灰(疑似积碳);
分析原因:1、根据目前氧化锌的使用状况,依照厂家提供的数据,氧化锌在350℃,脱除无机硫的硫熔为20%—25%,在370℃的时候硫熔在28%左右,而氧化锌脱除有机硫的硫熔在2%—3%,氧化锌脱除有机硫的能力仅为无机硫的1/10。
另外氧化锌虽然对CS2、COS有一定的转化脱除功能,但对二甲基硫醚没有脱除功能,从我们的分析数据来看,我们残留的有机硫大多数为二甲基硫醚,二甲基硫醚含量在10g/l。
氧化锌对硫醚、噻吩没有脱除功能,在长期使用过程中硫醚、噻吩慢慢吸附在氧化锌表面,使氧化锌孔隙率降低,脱硫能力下降,从我们使用完的氧化锌可以看出,中间部分氧化锌还没有被利用,造成氧化锌使用寿命降低。
2、氧化锌运行时出现5、6点出现热点温度,分析发生析碳和燃烧反应,方程式如下;
(1)、析碳反应
2CO C + CO2 △H ° 298 = - 172 . 50 k J / mol (1)
CO + H2 C + H2O △H °298 = - 131 . 47 k J / mol (2)
CH4 C + 2 H2 △H °298 = 76 . 20 k J / mol (3)从热力学看,式(1)、(2)析碳的可能性随温度升高而减小,随压力增大而增大;式(3)析碳的可能性则随温度的升高而增大,随压力的增大而减小。
由于半水煤气近似干气,故式(1)逆反应除碳的可能性不大。
又因半水煤气中CH4量较少,故在一般情况下,式(3)析碳可忽略,当发生剧烈的放热反应时可能出现。
T305脱硫槽在入口温度270℃左右、1.9MPa的干半水煤气条件下,已发生了析碳反应,析碳反应在床层下部进行。
(2)、燃烧反应
当半水煤气中O2含量严重超标时,可能发生C、H2、CO与O2的燃烧反应。
C+O2CO2 △H ° 298 = - 393 . 80 k J / mol (4)
2H2+O22H2O △H ° 298 = - 242 k J / mol (5)
2CO + O22CO2 △H °298 = - 283 . 20 k J / mol (6)
石墨、H2、CO在空气中的最低着火温度分别为:427℃、572℃和609℃。
通常,即使O2含量超标,T305脱硫槽也达不到最低着火点而导致后工序中变炉超温。
故可以认为,T305脱硫槽入口温度控制较高时 ,首先产生了析碳反应,由于空速较小(198h-1)及壁流效应,生成的碳在槽内四周积存;一旦O2含量严重超标 ,碳被氧化生成的热量比气流带走的热量多,热量积累的结果使得碳达到了起燃温度;碳层越厚,O2 含量越高,则燃烧反应速度越快;
温度达到H2、CO等的燃点后,H2、CO 等也参与了燃烧反应。
使用过程中出现的超温现象,氧化锌5、6点温度超标,但是出口温度和进口温度几乎一样,打开槽发现在触媒层栅板和热电偶套管表面有析碳现象,氧化锌颗粒中间没有穿透,且出现氧化锌槽内衬大面积脱落等现象。
(3)、氧化锌不是触媒,它只是一种转化性的脱硫剂,而且在我们使用过程中发生析碳反应(在370℃的时候)造成氧化锌飞温。
氧含量每升高0.1%,温度将升高35℃--40℃,从目前氧化锌的生产状况来看,氧化锌不适合半水煤气干法脱硫,只有通过改变脱硫剂或者改变流程来实现硫的脱除。
其次,根据原始设计,氧化锌在焦炉气流程中做精脱功能,只能脱微量的无机硫才能保证它的使用周期。
五、改变目前这种现状的方案
方案一:
利用目前焦炉气流程,对半水煤气进行加氢实验,1)观察半水煤气能不能通过镍钼将目前的有机硫转化,2)镍钼加氢温度能不能控制住,3)如果能够过半水煤气量,就将目前的1#氧化锌改装为镍钼转化催化剂,镍钼加氢脱硫催化剂的作用与钴钼加氢脱硫催化剂相同,也是使有机硫氢解,转变成易于脱除的硫化氢,以便进一步除去,从而达到净化烃类原料的目的。
方案二:T305氧化锌脱硫剂在流程中的工序设置不当
首先,以氧化锌为脱硫剂的流程中,氧化锌脱硫槽通常用于
CO≦3.0%,水/气比(1-1.5)﹕1,温度为200-260℃的低变催化剂之前;其次,对含复杂有机硫的天然气、焦炉气、油田气、炼厂气及轻油 ,通常先将各种有机硫化物经铁钼或钴钼加氢转化催化剂转化为H2 S ,再用氧化锌精脱除,操作温度一般在350~400℃。
因此,原料不同、原料组成不同,则氧化锌催化剂在流程中的位置就不应相同。
T305脱硫槽置于中变炉前含CO30%~35%、H236%~39%的干半水煤气脱硫气氛中,这在同行中既无先例也不妥当。
可以认为流程工序设计不合理。
设想与建议
(1)综合上述,严格控制T305脱硫槽入口温度220~230 ℃, 最高不大于250℃,无论是析碳反应、燃烧反应,还是甲烷化反应,都可受到抑制。
(2)在T305脱硫槽入口管道焊接蒸汽管道备用,当析碳和超温时可用其压制。
据介绍,水/气比为1∶1和200℃下,仍有20%的穿透硫容。
因而,必要时加入水蒸汽不会造成大的影响。
(3)为避免燃烧反应和硫容下降 ,应严格控制半水煤气中 O2 含量不大于0.5%。
(4)当T305脱硫槽热点温度大于350℃时,进气减量,大于400℃时,切断气源。
方案三:
将现有半水煤气滤油器的活性炭改变为高效活性炭脱硫剂,进一步降低有机硫,再进一步将1#氧化锌槽改装镍钼转化催化剂,
这样就可以将有机硫转化后用2#氧化锌将无机硫脱除。
方案四:水解法脱除有机硫
水解法脱除有机硫由于操作温度为中低温,可避免强放热的甲烷化副反应发生,是目前国内外脱除煤气中有机硫十分活跃的研究领域。
但水解催化剂的活性随温度的升高和煤气中氧含量的增大而急剧下降,且对COS、CS2水解效果好,对煤气中的噻吩、硫醚、硫醇基本不起作用,这是水解法脱除有机硫的致命缺陷。
丰盛公司净化作业区
2014年7月15日。