常规炼焦工艺与热回收炼焦工艺的比较
炼焦工艺流程解说
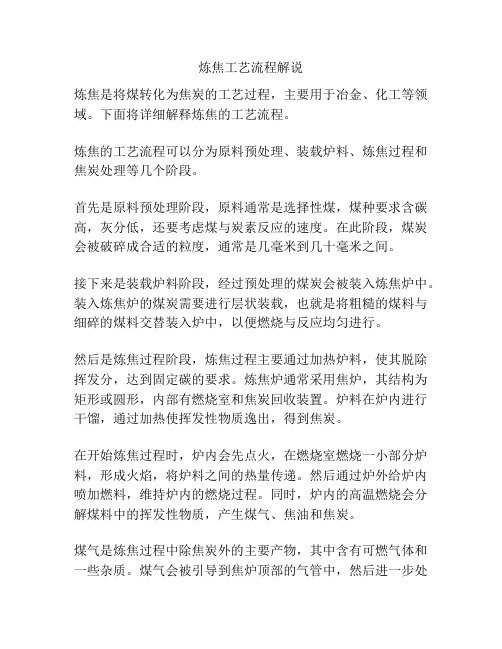
炼焦工艺流程解说炼焦是将煤转化为焦炭的工艺过程,主要用于冶金、化工等领域。
下面将详细解释炼焦的工艺流程。
炼焦的工艺流程可以分为原料预处理、装载炉料、炼焦过程和焦炭处理等几个阶段。
首先是原料预处理阶段,原料通常是选择性煤,煤种要求含碳高,灰分低,还要考虑煤与炭素反应的速度。
在此阶段,煤炭会被破碎成合适的粒度,通常是几毫米到几十毫米之间。
接下来是装载炉料阶段,经过预处理的煤炭会被装入炼焦炉中。
装入炼焦炉的煤炭需要进行层状装载,也就是将粗糙的煤料与细碎的煤料交替装入炉中,以便燃烧与反应均匀进行。
然后是炼焦过程阶段,炼焦过程主要通过加热炉料,使其脱除挥发分,达到固定碳的要求。
炼焦炉通常采用焦炉,其结构为矩形或圆形,内部有燃烧室和焦炭回收装置。
炉料在炉内进行干馏,通过加热使挥发性物质逸出,得到焦炭。
在开始炼焦过程时,炉内会先点火,在燃烧室燃烧一小部分炉料,形成火焰,将炉料之间的热量传递。
然后通过炉外给炉内喷加燃料,维持炉内的燃烧过程。
同时,炉内的高温燃烧会分解煤料中的挥发性物质,产生煤气、焦油和焦炭。
煤气是炼焦过程中除焦炭外的主要产物,其中含有可燃气体和一些杂质。
煤气会被引导到焦炉顶部的气管中,然后进一步处理,用于炼焦炉的燃烧或者作为其他化工生产的原料。
焦油是炼焦过程中除焦炭外的另一个主要产物,其中含有水、苯、酚等有机物质。
焦油会被冷凝成液体,然后通过分离和再加工,可以用于制取煤焦油、柴油等燃料,或作为化工原料。
焦炭是炼焦过程中得到的主要产品,也是电炉炼钢和冶金铸造中的重要原料。
焦炭会被释放出炉体,然后经过冷却、除尘等处理,得到成品焦炭。
最后是焦炭处理阶段,成品焦炭会被进行分类、包装等处理,以便于储存、运输和使用。
总的来说,炼焦工艺流程是将煤炭转化为焦炭的过程,主要包括原料预处理、装载炉料、炼焦过程和焦炭处理等几个阶段。
通过这些工艺步骤,可以有效地将煤炭转化为有用的能源和原材料,满足不同领域的需求。
一种炼焦化学产品的回收与精制工艺

一种炼焦化学产品的回收与精制工艺
炼焦是将煤炭等矿物质在高温下加热分解,得到焦炭和其他化学产品的过程。
在炼焦过程中,会产生大量的副产物,如焦油、氨水、苯、甲醇等。
这些副产物中含有许多有价值的化学物质,因此需要进行回收和精制。
以下是一种炼焦化学产品的回收与精制工艺:
1. 焦油回收:将炼焦炉中产生的焦油收集起来,经过蒸馏、萃取等工艺,分离出苯、甲醇、苯乙烯等有价值的化学品。
2. 氨水回收:将炼焦炉中产生的氨水收集起来,经过蒸馏、吸附等工艺,分离出氨、尿素等有价值的化学品。
3. 焦炭精制:将炼焦炉中产生的焦炭进行精制,去除其中的杂质和灰分,提高焦炭的质量和价值。
4. 炼焦煤气回收:将炼焦炉中产生的煤气收集起来,经过净化、脱硫等工艺,得到高纯度的煤气,可用于发电、加热等用途。
通过以上工艺,可以将炼焦过程中产生的副产物回收和精制,提高资源利用率和经济效益。
同时,也可以减少环境污染和资源浪费。
钢铁工艺流程废热利用分析
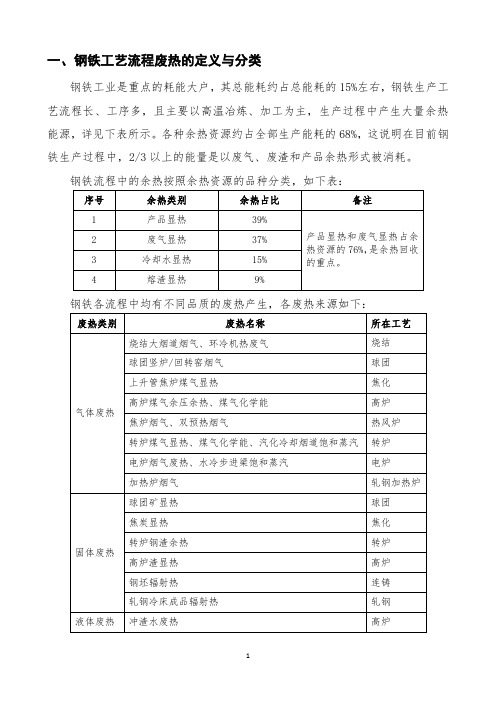
一、钢铁工艺流程废热的定义与分类钢铁工业是重点的耗能大户,其总能耗约占总能耗的15%左右,钢铁生产工艺流程长、工序多,且主要以高温冶炼、加工为主,生产过程中产生大量余热能源,详见下表所示。
各种余热资源约占全部生产能耗的68%,这说明在目前钢铁生产过程中,2/3以上的能量是以废气、废渣和产品余热形式被消耗。
钢铁流程中的余热按照余热资源的品种分类,如下表:钢铁各流程中均有不同品质的废热产生,各废热来源如下:二、钢铁工艺流程废热利用技术现状(一)常规废热利用方式钢铁流程的废热利用中,废热回收发电是经济性比较高的一种废热回收方式,因此钢铁行业的废热回收主要以废热回收发电方式为主,在余热发电技术的研发应用方面,与发达国家钢铁工业相比,我们钢铁行业的余热发电技术起步较晚。
目前,钢铁工业余热发电主要有以下几种方式,一是利用焦化、烧结工序烟气余热换热产生过热蒸汽发电;二是利用炼钢、轧钢工序烟气余热换热产生饱和蒸汽发电;第三种是煤气-蒸汽联合循环发电。
另外目前有人提出利用高炉的冲渣热水余热进行ORC发电,此技术目前尚在论证中,市场未有应用案例。
1、过热蒸汽发电(1)干熄焦余热发电炼焦生产中,高温红焦冷却有两种熄焦工艺:一种是传统的采用水熄灭炽热红焦的工艺,简称湿熄焦,另一种是采用循环惰性气体与红焦进行热交换冷却焦炭,简称干熄焦。
干熄焦余热发电技术是指利用与红焦热交换产生的高温烟气驱动汽轮发电机组进行发电,其主要工艺流程为:焦炉生产出来的约1000℃赤热焦炭运送入干熄炉,在冷却室内与循环风机鼓入的冷惰性气体进行热交换。
惰性气体吸收红焦的显热,温度上升至800℃左右,经余热锅炉生产中高压过热蒸汽,驱动汽轮发电机组发电,同时汽轮机还可产生低压蒸汽用于供热。
随着干熄焦技术所产生的社会和节能环保效益得到普遍认可,干熄焦余热发电技术也得到了国内钢铁企业越来越广泛的应用。
该项发电技术已十分成熟,目前的发展趋势集中在进一步提高余热的回收利用效率上,正逐步由传统的小型中压参数系统向系列化、大型化、高参数发展。
新型热回收焦炉-张 莹
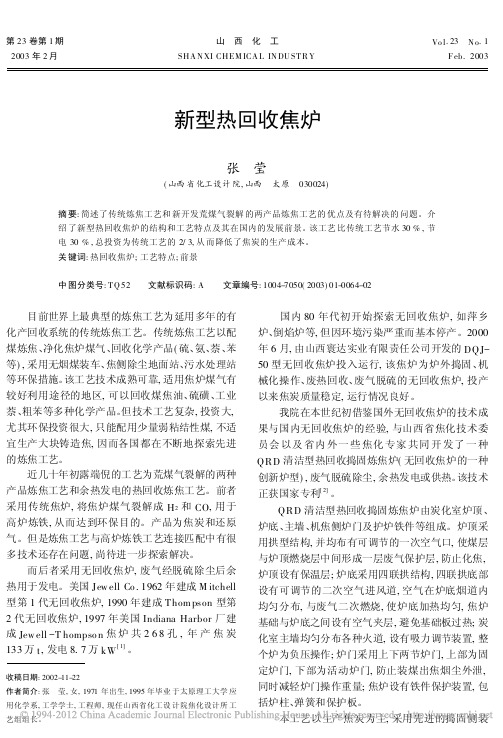
第23卷第1期山 西 化 工Vo l.23 N o.1 2003年2月SHA N XI CHEM ICA L IN DU ST R Y F eb.2003新型热回收焦炉张 莹(山西省化工设计院,山西 太原 030024)摘要:简述了传统炼焦工艺和新开发荒煤气裂解的两产品炼焦工艺的优点及有待解决的问题。
介绍了新型热回收焦炉的结构和工艺特点及其在国内的发展前景。
该工艺比传统工艺节水30%,节电30%,总投资为传统工艺的2/3,从而降低了焦炭的生产成本。
关键词:热回收焦炉;工艺特点;前景中图分类号:T Q52 文献标识码:A 文章编号:1004-7050(2003)01-0064-02 目前世界上最典型的炼焦工艺为延用多年的有化产回收系统的传统炼焦工艺。
传统炼焦工艺以配煤炼焦、净化焦炉煤气、回收化学产品(硫、氨、萘、苯等),采用无烟煤装车、焦侧除尘地面站、污水处理站等环保措施。
该工艺技术成熟可靠,适用焦炉煤气有较好利用途径的地区,可以回收煤焦油、硫磺、工业萘、粗苯等多种化学产品。
但技术工艺复杂,投资大,尤其环保投资很大,只能配用少量弱粘结性煤,不适宜生产大块铸造焦,因而各国都在不断地探索先进的炼焦工艺。
近几十年初露端倪的工艺为荒煤气裂解的两种产品炼焦工艺和余热发电的热回收炼焦工艺。
前者采用传统焦炉,将焦炉煤气裂解成H2和CO,用于高炉炼铁,从而达到环保目的。
产品为焦炭和还原气。
但是炼焦工艺与高炉炼铁工艺连接匹配中有很多技术还存在问题,尚待进一步探索解决。
而后者采用无回收焦炉,废气经脱硫除尘后余热用于发电。
美国Jew ell Co.1962年建成M itchell 型第1代无回收焦炉,1990年建成Thom pson型第2代无回收焦炉,1997年美国Indiana Harbor厂建成Jew ell-T hompso n焦炉共268孔,年产焦炭133万t,发电8.7万kW[1]。
收稿日期:2002-11-22作者简介:张 莹,女,1971年出生,1995年毕业于太原理工大学应用化学系,工学学士,工程师,现任山西省化工设计院焦化设计所工艺组组长。
炼焦原理及工艺流程
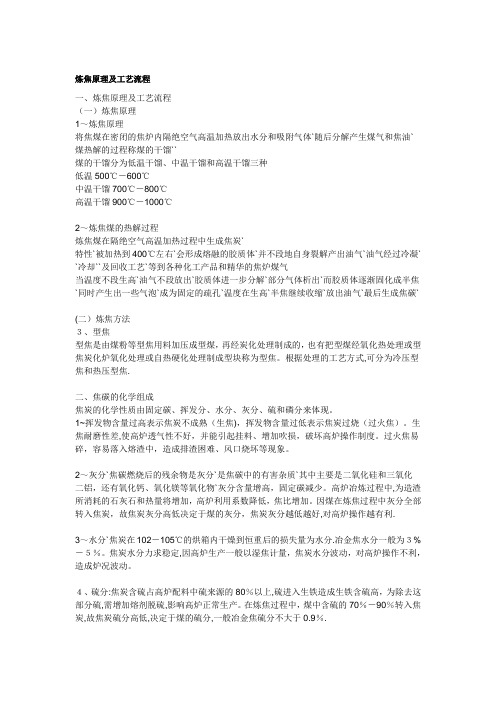
炼焦原理及工艺流程一、炼焦原理及工艺流程(一)炼焦原理1~炼焦原理将焦煤在密闭的焦炉内隔绝空气高温加热放出水分和吸附气体`随后分解产生煤气和焦油`煤热解的过程称煤的干馏``煤的干馏分为低温干馏、中温干馏和高温干馏三种低温500℃-600℃中温干馏700℃-800℃高温干馏900℃-1000℃2~炼焦煤的热解过程炼焦煤在隔绝空气高温加热过程中生成焦炭`特性`被加热到400℃左右`会形成熔融的胶质体`并不段地自身裂解产出油气`油气经过冷凝` `冷却``及回收工艺`等到各种化工产品和精华的焦炉煤气当温度不段生高`油气不段放出`胶质体进一步分解`部分气体析出`而胶质体逐渐固化成半焦`同时产生出一些气泡`成为固定的疏孔`温度在生高`半焦继续收缩`放出油气`最后生成焦碳`(二)炼焦方法3、型焦型焦是由煤粉等型焦用料加压成型煤,再经炭化处理制成的,也有把型煤经氧化热处理或型焦炭化炉氧化处理或自热硬化处理制成型块称为型焦。
根据处理的工艺方式,可分为冷压型焦和热压型焦.二、焦碳的化学组成焦炭的化学性质由固定碳、挥发分、水分、灰分、硫和磷分来体现。
1~挥发物含量过高表示焦炭不成熟(生焦),挥发物含量过低表示焦炭过烧(过火焦)。
生焦耐磨性差,使高炉透气性不好,并能引起挂料、增加吹损,破坏高炉操作制度。
过火焦易碎,容易落入熔渣中,造成排渣困难、风口烧坏等现象。
2~灰分`焦碳燃烧后的残余物是灰分`是焦碳中的有害杂质`其中主要是二氧化硅和三氧化二铝,还有氧化钙、氧化镁等氧化物`灰分含量增高,固定碳减少。
高炉冶炼过程中,为造渣所消耗的石灰石和热量将增加,高炉利用系数降低,焦比增加。
因煤在炼焦过程中灰分全部转入焦炭,故焦炭灰分高低决定于煤的灰分,焦炭灰分越低越好,对高炉操作越有利.3~水分`焦炭在102-105℃的烘箱内干燥到恒重后的损失量为水分.冶金焦水分一般为3%-5%。
焦炭水分力求稳定,因高炉生产一般以湿焦计量,焦炭水分波动,对高炉操作不利,造成炉况波动。
捣固炼焦与常规炼焦技术对比

捣固炼焦与常规炼焦技术对比摘要:目前,煤炭作为我国目前最重要的能源,在今后相当长的一段时期里,它仍是我国能源结构的重要组成部分。
经过焦化处理后的煤炭使用,可以改善煤的特性,适合于钢铁和其他工业。
为了提高焦化过程的效率,提高焦化产物的结构和品质。
以试验和分析的方式,着重比较了锻烧焦与传统焦化工艺条件下的焦炭结构与品质,并制定了具体的试验方案及产品的检测方法。
采用定量方法,对不同烧结密度对焦炭品质的影响进行了定量的分析。
关键词:捣固炼焦;常规炼焦;堆积密度;抗碎强;反应性所谓炼焦指的是将煤炭在隔绝空气的环境将其加热至1000℃左右,最终得到相应的高温焦炭、煤气以及其他化学产品等。但是,在实际的炼焦过程中可采用常规和捣固炼焦工艺。目前,我国针对捣固炼焦的研究尚浅,并不了解其与常规炼焦工艺之间关系,不明确捣固炼焦工艺是否能够改善焦炭质量且对应的改善幅度为多大。因此,本文重点对常规炼焦和捣固炼焦进行对比研究。1捣固炼焦技术概述所谓捣固炼焦指的是在炼焦之前,将焦煤采用捣固机捣固成略小于炭化室的煤饼后送入焦炉中。捣固炼焦的装煤量比传统焦炉的装煤量要高,捣固焦炉的装煤量最高为1.1吨/立方米,而传统焦炉的装煤量是0.7吨/立方米。
捣固炼焦技术的主要优点是它能从较低粘度、较不粘稠的焦煤中得到高质量的焦炭,也就是一定程度上增加了原煤的使用范围,从而降低了焦煤的炼焦成本。
2实验方案2.1实验方案设计本文首先比较了在不同的堆压密度条件下,根据捣固焦化过程得到的焦炭质量,并得到了锻烧过程中的最佳堆压密度;其次,以以上结果为依据,着重比较了捣固焦化与传统焦化技术的焦炭品质,并由此得出了捣固焦化与传统焦化技术在焦炭品质上的差异。
2.2实验方法实验方法包括有相关待实验煤样的制备和炼焦实验方法。
其中,针对煤样的制备包括有单种煤样的制备和生产配合煤的制备。
单种煤样的制备:选取当地某单种煤样分别通过3mm的方孔筛、颚式破碎机、10mm的圆孔筛等设备将煤样的粒度控制在10mm以下,保证细度大于90%;制备后混合均匀并测定其水分后密封备用。
常规炼焦工艺与热回收炼焦工艺的比较

世界金属导报/2011年/7月/5日/第010版原料炼铁常规炼焦工艺与热回收炼焦工艺的比较林立恒常规炼焦工艺和热回收炼焦工艺都能生产优质焦炭及达到能量平衡,同时可保证低生产成本。
为了选择更适合的炼焦工艺,美国哈奇公司对一些炼焦项目进行了可行性研究,并对常规炼焦工艺及热回收炼焦工艺进行了比较研究。
研究结果是炼焦工艺的选择必需就事论事,因为决定的因素很多,其中包括可用的土地及能源、钢厂总体布局、环境及设备投资等各个方面。
两种炼焦工艺的总能量平衡存在着很大差别,热回收炼焦工艺可以大量发电,而常规炼焦工艺能产出钢铁冶炼用的煤气。
1 炼焦工艺概述冶金焦生产工艺有三种类型:常规炼焦,热回收炼焦及蜂窝焦炼焦。
热回收炼焦工艺是蜂窝焦生产工艺的革新。
蜂窝焦生产工艺绝大多数已被淘汰。
下面重点比较常规炼焦工艺及热回收炼焦工艺。
炼焦选用的煤经过筛分破碎至3mm以下,根据煤的岩相组分混配在一起,用于生产优质焦炭。
在选煤中应选用成本低而炼焦效果高的煤。
混配好的煤料装入焦炉里,大约1100℃或更高的温度下使煤料分解干馏变成焦炭。
一个炼焦周期结束后,从炉内推出热焦,使之落入熄焦车里,以便送往熄焦塔,在塔内使焦炭冷却及稳定。
用水熄焦称为湿熄焦,也可用氮气熄焦,这种气体熄焦称为干熄焦。
熄焦后的成品焦供高炉使用。
常规炼焦是因炼焦当中将释放出的各种挥发性物质收集起来精炼成化学副产品而得名。
常规炼焦是在碳化室内,在无氧气氛中进行。
碳化室内保持正压,以防外部空气窜入,挥发性物质被燃烧。
现代焦炉高度通常为4-8m。
对于双联火道常规炼焦炉,保证整个炉组温度高而分布均匀至关重要。
1.1 常规炼焦工艺常规炼焦时主要污染物排放源生成于推焦过程。
推焦时炉门打开,红焦直接暴露在大气中。
焦炉碳化室高度越高,焦炉生产的焦炭就越多,因而能以较少的装煤及推焦次数以及较少的污染物排放量生产出更多的焦炭。
常规炼焦中放出来的各种挥发性物质进入总集气管,然后送到副产品回收装置。
炼焦工艺
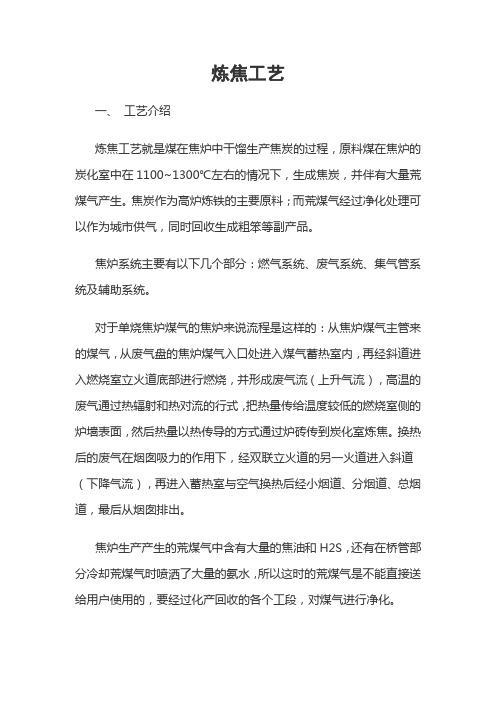
炼焦工艺一、工艺介绍炼焦工艺就是煤在焦炉中干馏生产焦炭的过程,原料煤在焦炉的炭化室中在1100~1300℃左右的情况下,生成焦炭,并伴有大量荒煤气产生。
焦炭作为高炉炼铁的主要原料;而荒煤气经过净化处理可以作为城市供气,同时回收生成粗笨等副产品。
焦炉系统主要有以下几个部分:燃气系统、废气系统、集气管系统及辅助系统。
对于单烧焦炉煤气的焦炉来说流程是这样的:从焦炉煤气主管来的煤气,从废气盘的焦炉煤气入口处进入煤气蓄热室内,再经斜道进入燃烧室立火道底部进行燃烧,并形成废气流(上升气流),高温的废气通过热辐射和热对流的行式,把热量传给温度较低的燃烧室侧的炉墙表面,然后热量以热传导的方式通过炉砖传到炭化室炼焦。
换热后的废气在烟囱吸力的作用下,经双联立火道的另一火道进入斜道(下降气流),再进入蓄热室与空气换热后经小烟道、分烟道、总烟道,最后从烟囱排出。
焦炉生产产生的荒煤气中含有大量的焦油和H2S,还有在桥管部分冷却荒煤气时喷洒了大量的氨水,所以这时的荒煤气是不能直接送给用户使用的,要经过化产回收的各个工段,对煤气进行净化。
1、冷凝部分:荒煤气中含有大量的焦油,首先要经过初冷器冷凝回收大部分的焦油,产生的冷凝液循环冷凝回流量要调节。
2、电捕部分:电捕焦油器对从初冷器出来的煤气进一步去除含有的少量焦油,这里面电部绝缘箱的温度要控制在一定的范围内,超过范围要联锁,停鼓风机,电捕后煤器含氧量如果过高的话也要联锁停鼓风机。
3、槽区部分:初冷器冷凝产生的焦油,电捕焦油器捕到的焦油都汇集到槽区部分。
4、鼓风机:经过冷凝、电捕后煤气中大部分的焦油已经被去除了,进入鼓风机的环节,鼓风机在整个煤气净化过程中起着非常重要的作用,是煤气流动的动力所在,不同的厂家的鼓风机略有不同,但这里的联锁控制很复杂,比如: 鼓风机轴承温度联锁,盘车电机的联锁等。
5、硫部分的主要工艺设备是预冷塔和脱硫塔,通过和氨水的反应除掉煤气中含有的硫,主要流程及控制如下:6、从脱硫出来的煤气中含有大量的氨,主要是因为在脱硫过程中用到了氨水,所以下一步就要去除这的氨,这里的主要设备是饱和器和蒸氨塔,饱和器加入大量的浓硫酸,和氨反应生成硫酸氨晶体,蒸氨塔则是通过蒸汽加热的方式使氨气挥发出来,这里需要控制的是蒸氨塔顶的温度,是通过进蒸氨塔的蒸汽量调节的。
炼焦工业现状和炼焦工艺的发展
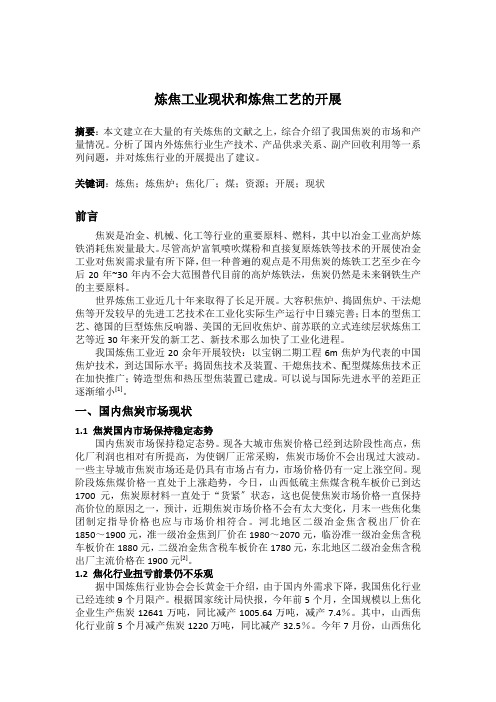
炼焦工业现状和炼焦工艺的开展摘要:本文建立在大量的有关炼焦的文献之上,综合介绍了我国焦炭的市场和产量情况。
分析了国内外炼焦行业生产技术、产品供求关系、副产回收利用等一系列问题,并对炼焦行业的开展提出了建议。
关键词:炼焦;炼焦炉;焦化厂;煤;资源;开展;现状前言焦炭是冶金、机械、化工等行业的重要原料、燃料,其中以冶金工业高炉炼铁消耗焦炭量最大。
尽管高炉富氧喷吹煤粉和直接复原炼铁等技术的开展使冶金工业对焦炭需求量有所下降,但一种普遍的观点是不用焦炭的炼铁工艺至少在今后20年~30年内不会大范围替代目前的高炉炼铁法,焦炭仍然是未来钢铁生产的主要原料。
世界炼焦工业近几十年来取得了长足开展。
大容积焦炉、捣固焦炉、干法熄焦等开发较早的先进工艺技术在工业化实际生产运行中日臻完善;日本的型焦工艺、德国的巨型炼焦反响器、美国的无回收焦炉、前苏联的立式连续层状炼焦工艺等近30年来开发的新工艺、新技术那么加快了工业化进程。
我国炼焦工业近20余年开展较快:以宝钢二期工程6m焦炉为代表的中国焦炉技术,到达国际水平;捣固焦技术及装置、干熄焦技术、配型煤炼焦技术正在加快推广;铸造型焦和热压型焦装置已建成。
可以说与国际先进水平的差距正逐渐缩小[1]。
一、国内焦炭市场现状1.1 焦炭国内市场保持稳定态势国内焦炭市场保持稳定态势。
现各大城市焦炭价格已经到达阶段性高点,焦化厂利润也相对有所提高,为使钢厂正常采购,焦炭市场价不会出现过大波动。
一些主导城市焦炭市场还是仍具有市场占有力,市场价格仍有一定上涨空间。
现阶段炼焦煤价格一直处于上涨趋势,今日,山西低硫主焦煤含税车板价已到达1700元,焦炭原材料一直处于“货紧〞状态,这也促使焦炭市场价格一直保持高价位的原因之一,预计,近期焦炭市场价格不会有太大变化,月末一些焦化集团制定指导价格也应与市场价相符合。
河北地区二级冶金焦含税出厂价在1850~1900元,准一级冶金焦到厂价在1980~2070元,临汾准一级冶金焦含税车板价在1880元,二级冶金焦含税车板价在1780元,东北地区二级冶金焦含税出厂主流价格在1900元[2]。
浅谈热回收焦炉的应用前景

浅谈热回收焦炉的应用前景王蓉【摘要】热回收焦炉是我国近年来新开发的炼焦炉型,该技术的应用与实施,从根本上扩大了炼焦资源,实现了产品的清洁型生产,减少了废热废气的排放量,响应了国家节能减排、清洁生产的方针政策.本文介绍了热回收焦炉的工艺技术、生产过程中存在的一些问题及热回收焦炉的发展前景.【期刊名称】《山西焦煤科技》【年(卷),期】2011(000)0z1【总页数】3页(P59-61)【关键词】热回收焦炉;应用;前景【作者】王蓉【作者单位】山西西山煤气化有限责任公司,山西古交030200【正文语种】中文【中图分类】TQ522.15随着我国钢铁企业的发展和高炉大型化,对焦炭需求量和质量的要求也随之提高,但是优质炼焦煤资源却日趋匮乏。
为了减少主焦煤的用量,多用弱黏结性煤、无黏结性煤,随后研究开发了配型煤炼焦、捣固炼焦、预热煤炼焦及调湿煤技术等。
目前,常见的是捣固炼焦,因为在相同配煤比的情况下,捣固炼焦所产的焦炭质量较好。
因此,为了扩大炼焦用煤,特别是对高挥发分煤和弱黏结性煤贮量多的区域,采用捣固炼焦更为有利。
但是随着国民经济建设的大力发展,我国政府对焦化工业产业结构调整和环境保护工作越来越重视。
投入大量的人力和财力,进行多次土焦改造和大力发展大机焦建设。
焦炭工业必须加大技术创新力度,淘汰落后的简易小机焦,加强资源综合利用,加大环境保护力度,提高炼焦技术水平。
清洁型热回收焦炉就是在这种产业结构调整的要求下,应用发展起来的。
山西西山煤气化公司焦化二厂采用的就是QRD-2000清洁型热回收捣固焦炉。
该焦炉由山西省化工设计院设计,是在总结国外无回收焦炉技术以及我国成熟的焦炉生产经验的基础上改进创新的清洁型焦炉。
在该公司投入使用之前,山西兴高能源股份有限公司、晋城沁泽焦化有限公司等企业已应用QRD-2000清洁型热回收捣固焦炉生产焦炭,操作环境好,机械化程度较高。
1 热回收焦炉概述热回收焦炉是指炼焦煤在炼焦过程中产生焦炭,其化学产品、焦炉煤气和一些有害的物质在炼焦炉内部合理地充分燃烧,回收高温废气的热量用来发电或其他用途的一种焦炉。
炼焦工艺技术有哪些优点
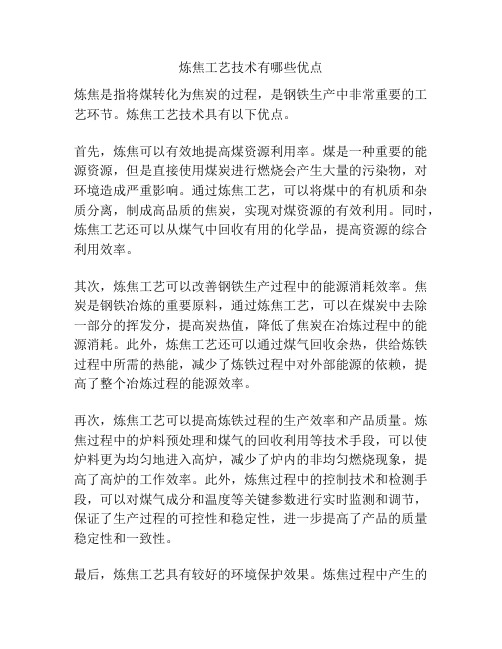
炼焦工艺技术有哪些优点炼焦是指将煤转化为焦炭的过程,是钢铁生产中非常重要的工艺环节。
炼焦工艺技术具有以下优点。
首先,炼焦可以有效地提高煤资源利用率。
煤是一种重要的能源资源,但是直接使用煤炭进行燃烧会产生大量的污染物,对环境造成严重影响。
通过炼焦工艺,可以将煤中的有机质和杂质分离,制成高品质的焦炭,实现对煤资源的有效利用。
同时,炼焦工艺还可以从煤气中回收有用的化学品,提高资源的综合利用效率。
其次,炼焦工艺可以改善钢铁生产过程中的能源消耗效率。
焦炭是钢铁冶炼的重要原料,通过炼焦工艺,可以在煤炭中去除一部分的挥发分,提高炭热值,降低了焦炭在冶炼过程中的能源消耗。
此外,炼焦工艺还可以通过煤气回收余热,供给炼铁过程中所需的热能,减少了炼铁过程中对外部能源的依赖,提高了整个冶炼过程的能源效率。
再次,炼焦工艺可以提高炼铁过程的生产效率和产品质量。
炼焦过程中的炉料预处理和煤气的回收利用等技术手段,可以使炉料更为均匀地进入高炉,减少了炉内的非均匀燃烧现象,提高了高炉的工作效率。
此外,炼焦过程中的控制技术和检测手段,可以对煤气成分和温度等关键参数进行实时监测和调节,保证了生产过程的可控性和稳定性,进一步提高了产品的质量稳定性和一致性。
最后,炼焦工艺具有较好的环境保护效果。
炼焦过程中产生的大量煤气中含有大量的有害气体和烟尘颗粒物等污染物,对环境造成了严重影响。
但通过采用先进的废气处理技术,可以将煤气中的污染物有效去除,减少了对环境的污染。
同时,炼焦过程中回收利用的煤气还可以用作燃料或再开发利用,减少了对外部环境的压力。
总之,炼焦工艺技术具有提高煤资源利用率、改善能源消耗效率、提高生产效率和产品质量、保护环境等多方面的优点。
随着技术的不断创新和发展,炼焦工艺将会更加高效、环保和可持续。
炼焦与化产回收

炼焦与化产回收名词解释⾼炉炼焦的焦⽐:指每炼⼀顿⽣铁焦炭的消耗量,⽤公⽄/吨⽣铁表⽰.M25(M40):当焦炭承受冲击⼒时,焦炭沿结构的裂纹或缺陷处碎成⼩块,焦炭抵抗此种破坏的能⼒称焦炭的抗碎性或抗碎强度。
⽤M25(M40)表⽰。
M10:当焦炭表⾯承受的切向摩擦⼒超过⽓孔壁的强度时,会产⽣表⾯薄层分离现象形成碎屑或粉末,焦炭抵抗此种破坏的能⼒称耐磨性或耐磨强度,⽤M10值表⽰。
备煤的细度:是指配合煤中<3 mm粒级占全部配合煤的质量百分率。
炼焦速度:炭化室平均宽度与结焦时间的⽐值.成层结焦:各层处于结焦过程的不同阶段,在炉墙附近先结成焦炭⽽后逐层向炭化室中⼼推移——成层结焦。
⾥⾏⽓:炭化室内⼲煤层热解⽣成的⽓态产物和塑性层内所产⽣的⽓态产物中的⼀部分只能向上或从塑性层内侧流往炉顶空间——⾥⾏⽓。
外形⽓:塑性层内的所产⽣的⽓态产物中的⼤部分及半焦层内产⽣的⽓态产物则穿过⾼温焦炭层缝隙,沿焦饼与炭化室墙之间的缝隙向上流⼊炉顶空间——外⾏⽓。
炼焦最终温度:炭化室中⼼⾯上炉料温度始终最低,因此结焦末期炭化室中⼼⾯温度(焦饼中⼼温度)可以作为焦饼成熟程度的标志,称为炼焦最终温度。
焦炉的机侧和焦侧:整座焦炉靠推焦车⼀侧称为机侧,另⼀侧称为焦侧。
炭化室的锥度:为顺利推焦,炭化室的⽔平呈梯形,焦侧宽度 > 机侧,两侧宽度之差称锥度荒煤⽓:炼焦煤于炼焦炉内在隔绝空⽓⾼温加热条件下,煤质发⽣⼀系列变化,裂解⽣成挥发性产物净焦炉煤⽓:经回收化学产品和净化后的煤⽓轻苯和重苯:粗苯⼯段⽣产的粗苯,经两苯塔分馏为轻苯和重苯循环氨⽔:氨⽔由澄清槽上部满流⾄氨⽔中间槽,再⽤循环氨⽔泵送回焦炉集⽓管以冷却荒煤⽓,这部分氨⽔称为循环氨⽔.剩余氨⽔:在氨⽔循环系统中,由于加⼊配煤⽔分和炼焦时产⽣的化合⽔,使氨⽔量增多⽽形成所谓的剩余氨⽔。
重质焦油:在⽤循环氨⽔于集⽓管内喷洒荒煤⽓时,约60%的焦油冷凝下来,这种集⽓管焦油是重质焦油.轻质焦油:煤⽓在初冷器中冷却,冷凝下来的焦油为轻质焦油.混合焦油:轻质焦油和重质焦油的混合物.饱和器母液:饱和器中被硫酸铵和硫酸氢铵所饱和的硫酸溶液.饱和器母液酸度:溶液中酸式盐和中式盐的⽐例取决于母液中游离硫酸的浓度,这种浓度以质量百分数表⽰,称之为酸度。
清洁型热回收捣固炼焦技术、工作原理、特点、护炉设备及其应用

文件编号:__________版号:________生效日期:________编制人:________日期:_________审核人:________日期:_________批准人:________日期:_________受控印章:_______分发号:________目录第一篇、CHS67-2021清洁型热回收捣固炼焦技术与应用 (3)一、引言: (3)二、清洁型热回收捣固炼焦技术在国内外发展情况: (3)三、清洁型热回收捣固炼焦技术的原理及其特点: (4)(一)清洁型热回收捣固炼焦技术的原理: (4)(二)清洁型热回收捣固炼焦技术的特点: (5)四、清洁型热回收捣固炼焦技术的应用情况: (6)五、结论与展望: (6)(一)结论: (6)(二)展望: (7)第二篇、清洁型热回收捣固焦炉的工作原理及其特点 (7)一、清洁型热回收捣固焦炉工作原理: (7)二、特点: (7)三、发展方向: (9)第三篇、清洁型热回收捣固焦炉的护炉设备 (10)一、炉柱: (10)二、保护板: (10)三、炉门架: (11)四、横拉条: (11)五、纵拉条: (12)六、弹簧: (12)第一篇、CHS67-2021清洁型热回收捣固炼焦技术与应用一、引言:1、炼焦是指炼焦煤在隔绝空气条件下加热到1000℃左右,通过热分解和结焦产生焦炭、焦炉煤气和其他炼焦化学产品的工艺过程。
2、冶金焦炭含碳量高,气孔率高,强度大,是高炉炼铁的重要燃料和还原剂,也是整个高炉料柱的支撑剂和疏松剂。
3、炼焦副产的焦炉煤气发热值高,是平炉和加热炉的优良气体燃料,在钢铁联合企业中是重要的能源组分。
4、炼焦化学产品是重要的化工原料。
因此炼焦生产是现代钢铁工业的一个重要环节。
二、清洁型热回收捣固炼焦技术在国内外发展情况:1、热回收炼焦技术主要分为冷装冷出热回收炼焦技术和热装热出热回收炼焦技术。
两者的根本区别主要在于焦炉炉体结构、装煤出焦方式、余热利用率以及配套机械自动化等方面。
炼焦工艺流程

炼焦工艺流程
《炼焦工艺流程》
炼焦工艺是将煤炭加热至高温并在缺氧条件下进行干馏,从而产生焦炭和副产品的过程。
这一工艺起源于19世纪,如今已
成为炼焦煤和焦化气的重要生产方式。
在炼焦工艺中,煤炭被加热至高温,使其挥发性物质从煤体中释放出来并凝结为焦炭,而低挥发性物质则保留在焦炭中。
炼焦工艺的流程大致分为破碎、混配、煤气化、焦炭生产和副产品回收几个步骤。
首先,原料煤炭需要经过破碎和混配,以确保炉内反应的均匀性。
接下来,原料煤炭会被送入气化炉,经过高温干馏产生焦炭和煤气。
其中,产生的煤气还可以用于热能回收或其他化工生产。
最后,焦炭会被送入冷却车间进行冷却和分选,产生出不同规格的焦炭产品。
与此同时,炼焦工艺也会产生一些副产品,如焦油、煤气、苯、酚和氨等。
这些副产品可以再利用,如焦油可以作为沥青和石油添加剂,而煤气则可用于城市煤气、发电和加热。
这些副产品的回收能够有效减少生产成本、提高资源利用率,也有利于环境保护。
总的来说,炼焦工艺流程是一个复杂而高效的生产过程,既可以生产焦炭等重要工业原料,又可以回收和利用各种副产品,具有重要的经济价值和环保意义。
随着技术的不断进步,炼焦工艺也在不断完善和创新,将为煤炭资源的利用和化工产业的发展带来更多可能。
国标 焦化行业准入条件2014修订版

焦化行业准入条件(2014年修订)为促进焦化行业结构调整和转型升级,引导和规范焦化企业投资和生产经营,依据国家有关法律法规、产业政策和标准规范,按照“总量控制、科学规划、合理布局、节约能(资)源、保护环境、技术进步、创新转型”的原则,制定本准入条件。
一、总则本准入条件适用于新(改、扩)建焦化企业,包括炼焦、焦炉煤气制甲醇、煤焦油加工、苯精制生产企业。
(一)炼焦包含常规焦炉、热回收焦炉、半焦(兰炭)炭化炉三种生产工艺。
1.常规焦炉是指炭化室、燃烧室分设,炼焦煤隔绝空气间接加热干馏成焦炭和焦炉煤气,并设有煤气净化、化学产品回收的生产装置。
装煤方式分顶装和捣固侧装。
2.热回收焦炉是指焦炉炭化室微负压操作,机械化捣固、装煤、出焦,回收利用炼焦燃烧尾气余热的焦炭生产装置。
焦炉结构形式分立式和卧式。
3.半焦(兰炭)炭化炉(以下称“半焦炉”)是指将原料煤中低温干馏成半焦(兰炭)和焦炉煤气,并设有煤气净化、化学产品回收的生产装置。
加热方式分内热式和外热式。
(二)焦炉煤气制甲醇是指以焦炉煤气为主要原料生产甲醇的装置。
(三)煤焦油加工是指以常规焦炉生产的高温煤焦油或半焦炉生产的中低温煤焦油为原料,采用蒸馏方法生产酚、萘、洗油、蒽、煤焦油沥青等化工产品的装置。
(四)苯精制是指以炼焦煤化工产品粗苯或轻苯为原料生产苯、甲苯、二甲苯等产品的装置。
二、生产布局(一)新(改、扩)建焦化项目必须符合国家和省(区、市)主体功能区规划、区域规划、行业发展规划、城市建设发展规划、城市环境总体规划、土地利用规划、节能减排规划、环境保护和污染防治规划等规划的要求。
(二)炼焦项目建设应根据当地资源、能源状况,以及环境容量、市场需求情况,落实新增产能与淘汰产能等量或减量置换方案。
(三)新(改、扩)建焦化企业必须在依法设立、环境保护基础设施齐全并经规划环评的产业园区内布设。
在城市规划区边界外2公里(现有城市居民供气项目和钢铁生产企业厂区内配套项目除外)以内,生态环境承载力较弱的近岸海域岸线(大型钢铁生产企业厂区内配套项目除外)、主要河流两岸、高速公路两旁和其他严防污染的食品、药品等企业周边1公里以内,依法设立的自然保护区、风景名胜区、文化遗产保护区、世界文化自然遗产和森林公园、地质公园、湿地公园等保护地以及饮用水水源保护区内,不得建设焦化企业。
炼焦工艺学介绍
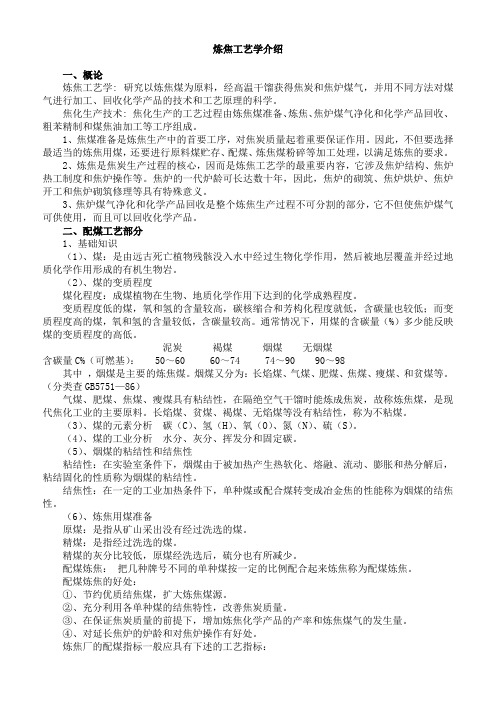
炼焦工艺学介绍一、概论炼焦工艺学: 研究以炼焦煤为原料,经高温干馏获得焦炭和焦炉煤气,并用不同方法对煤气进行加工、回收化学产品的技术和工艺原理的科学。
焦化生产技术: 焦化生产的工艺过程由炼焦煤准备、炼焦、焦炉煤气净化和化学产品回收、粗苯精制和煤焦油加工等工序组成。
1、焦煤准备是炼焦生产中的首要工序,对焦炭质量起着重要保证作用。
因此,不但要选择最适当的炼焦用煤,还要进行原料煤贮存、配煤、炼焦煤粉碎等加工处理,以满足炼焦的要求。
2、炼焦是焦炭生产过程的核心,因而是炼焦工艺学的最重要内容,它涉及焦炉结构、焦炉热工制度和焦炉操作等。
焦炉的一代炉龄可长达数十年,因此,焦炉的砌筑、焦炉烘炉、焦炉开工和焦炉砌筑修理等具有特殊意义。
3、焦炉煤气净化和化学产品回收是整个炼焦生产过程不可分割的部分,它不但使焦炉煤气可供使用,而且可以回收化学产品。
二、配煤工艺部分1、基础知识(1)、煤:是由远古死亡植物残骸没入水中经过生物化学作用,然后被地层覆盖并经过地质化学作用形成的有机生物岩。
(2)、煤的变质程度煤化程度:成煤植物在生物、地质化学作用下达到的化学成熟程度。
变质程度低的煤,氧和氢的含量较高,碳核缩合和芳构化程度就低,含碳量也较低;而变质程度高的煤,氧和氢的含量较低,含碳量较高。
通常情况下,用煤的含碳量(%)多少能反映煤的变质程度的高低。
泥炭褐煤烟煤无烟煤含碳量C%(可燃基): 50~60 60~74 74~90 90~98其中,烟煤是主要的炼焦煤。
烟煤又分为:长焰煤、气煤、肥煤、焦煤、瘦煤、和贫煤等。
(分类查GB5751—86)气煤、肥煤、焦煤、瘦煤具有粘结性,在隔绝空气干馏时能炼成焦炭,故称炼焦煤,是现代焦化工业的主要原料。
长焰煤、贫煤、褐煤、无焰煤等没有粘结性,称为不粘煤。
(3)、煤的元素分析碳(C)、氢(H)、氧(O)、氮(N)、硫(S)。
(4)、煤的工业分析水分、灰分、挥发分和固定碳。
(5)、烟煤的粘结性和结焦性粘结性:在实验室条件下,烟煤由于被加热产生热软化、熔融、流动、膨胀和热分解后,粘结固化的性质称为烟煤的粘结性。
焦化厂工艺介绍
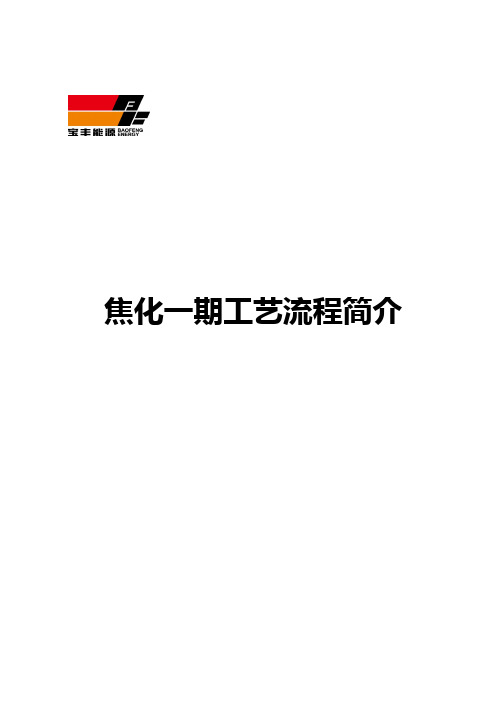
焦化一期工艺流程简介焦化厂一期年产200万吨焦化项目介绍一、2012年焦化厂产品生产计划及产率二、焦化厂产品质量指标三、焦化厂主要工艺流程介绍:焦化厂由6个车间组成,包括4个生产车间:备煤车间、炼焦车间、化产车间(煤气净化车间)、污水处理车间,两个辅助车间:储运车间、机修车间。
1、备煤工艺备煤工艺为先配煤后粉碎工艺;该工艺是将原料煤按一定比例配合后再进行粉碎的工艺。
外购的炼焦精煤由汽车运来后自卸于受煤坑,经受煤坑下叶轮给煤机将精煤给入煤1带式输送机,再经煤2带式输送机将煤送入堆取料机,把煤堆入精煤储场。
自洗煤厂的炼焦精煤由皮带通廊送来,由煤3带式输送机将煤送入堆取料机,把煤堆入精煤储场。
两种来煤方式均可不落煤场直接经煤4带式输送机把煤送往配煤仓。
煤场采用不同每种轮流上煤。
上煤时,由堆取料机取煤,经堆取料机主皮带、煤4带式输送机,转运至可逆带式输送机。
由可逆带式输送机将煤送入可逆配仓带式输送机,卸入配煤仓。
煤仓后设计为双系列。
配煤仓下设电子自动配料秤,将各种煤按相应的配合比例配送到仓下的备1带式输送机,除铁后,送入可逆反击锤式破碎机,煤被破碎至<3mm 占82%以上后,经备2、备3、备4、备5带式输送机,送入1#煤塔内;另一系列配送至仓下的备6带式输送机,除铁后,送入可逆反击锤式破碎机,煤被破碎至<3mm占82%以上后,经备7、备8、备9、备10、带式输送机,送入2#煤塔内,供焦炉使用。
宝丰能源焦化厂工艺流程框图2、炼焦工艺焦化厂炼焦设计公称能力为200万吨干全焦/年,焦炉炭化室全高5.5m,炭化室平均宽490mm的XY5549C型双联火道、废气循环、下喷、单热式、上升管与集气管置于焦侧、侧装捣固煤饼焦炉,炉组规模4×55孔。
炼焦生产采用高温炼焦工艺,高温炼焦是煤在隔绝空气条件下加热至1000±50℃时,发生一系列物理变化和化学反应,并得到焦炭、焦油和荒煤气的复杂过程,也称为煤的热解或干馏。
炼焦工艺资料

炼焦工艺的循环经济 与发展战略
• 炼焦工艺的循环经济与发展战略主要包括发展绿色炼焦、延伸产 业链、实现协同发展等
• 发展绿色炼焦:采用环保技术,降低污染物排放,实现绿色炼 焦工艺
• 延伸产业链:加强副产品利用,提高资源利用率,实现产业链 延伸
• 实现协同发展:加强上下游产业的合作,实现产业链优化升级, 提高整体竞争力
原料预处理方法的优缺点
• 优点:提高煤炭的利用率,降低能耗,提高焦炭质量 • 缺点:增加投资成本,操作复杂,技术要求较高
04
炼焦工艺的生产过程及影响因素
炼焦工艺的生产过程 概述
• 炼焦工艺的生产过程主要包括煤的预处理、焦炉加热、炼焦、熄 焦、煤气回收等
• 煤的预处理:将煤炭破碎、筛分、混合,提高煤炭的利用率 • 焦炉加热:将预处理后的煤炭在焦炉中加热,使其转化为焦炭 • 炼焦:在焦炉中高温炼焦,使煤炭转化为焦炭 • 熄焦:将炼焦后的焦炭冷却熄焦,便于运输和储存 • 煤气回收:回收炼焦过程中产生的煤气,提高资源利用率
炼焦工艺的未来趋势
• 炼焦工艺将继续向环保化、低碳化方向发展,减少环境污染 • 炼焦工艺将实现智能化、自动化生产,提高生产效率 • 炼焦工艺将加强与上下游产业的协同发展,实现产业链优化升级
02
炼焦工艺的分类及特点
常规炼焦工艺的分类及特点
常规炼焦工艺主要分为湿法炼焦和干法炼焦
• 湿法炼焦:将原料煤与液体介质混合,在高温条件下加热炼焦 • 干法炼焦:将原料煤直接加热炼焦,不需要液体介质
07
炼焦工艺的发展趋势与创新
炼焦工艺的发展趋势
• 炼焦工艺的发展趋势主要包括环保化、低碳化、智能化、自动化 等
• 环保化:采用环保技术,降低污染物排放,实现绿色炼焦工艺 • 低碳化:优化生产过程,降低能耗,减少碳排放 • 智能化:采用智能化技术,提高生产效率,降低人工成本 • 自动化:采用自动化设备,提高生产效率,降低人工成本
炼焦工艺流程总结

炼焦工艺流程总结
《炼焦工艺流程总结》
炼焦是将煤炭或木材等有机物质在高温下进行干馏,使其生成焦炭和各种有机气体的过程。
炼焦工艺流程是一个复杂的工程系统,需要经过多个步骤才能完成。
下面将对炼焦工艺流程进行总结。
首先是原料的准备。
在炼焦工艺中,主要原料是煤炭。
在进行炼焦之前,需要对煤炭进行破碎、除尘等处理,以确保煤炭的均匀性和质量。
接下来是煤气的预热。
在炼焦炉内,煤炭经过高温炼制后会产生大量煤气。
为了提高煤气的热值和减少热损失,需要对煤气进行预热处理。
然后是炼焦炉的炼制。
炼焦炉是炼焦工艺中最重要的设备,通过加热煤炭使其产生焦炭和煤气。
在炼焦炉内,煤炭经历干馏、软化、膨胀和热解等过程,最终生成焦炭和煤气。
接着是焦炭的冷却和收集。
炼焦后的焦炭需要进行冷却,以降低温度并减少煤气的损失。
同时,焦炭需要经过除尘、湿降尘等处理,以提高其质量。
最后是副产品的处理。
在炼焦工艺中,除了焦炭和煤气外,还会产生焦油、阿姆蒂尔和废水等副产品。
这些副产品需要经过处理和回收利用,以减少对环境的污染。
总的来说,炼焦工艺流程是一个复杂而又精密的过程,需要各种设备和技术的配合。
只有经过严格的控制和管理,才能保证炼焦工艺的正常运行和生产出优质的焦炭和副产品。
焦化厂现代炼焦技术问题的若干研究
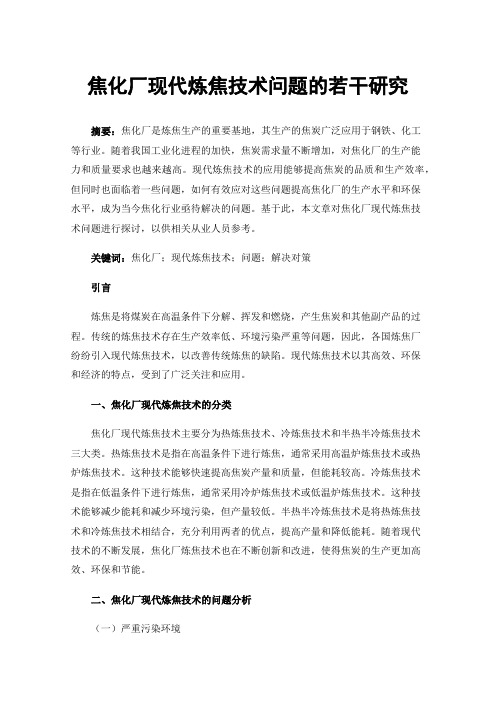
焦化厂现代炼焦技术问题的若干研究摘要:焦化厂是炼焦生产的重要基地,其生产的焦炭广泛应用于钢铁、化工等行业。
随着我国工业化进程的加快,焦炭需求量不断增加,对焦化厂的生产能力和质量要求也越来越高。
现代炼焦技术的应用能够提高焦炭的品质和生产效率,但同时也面临着一些问题,如何有效应对这些问题提高焦化厂的生产水平和环保水平,成为当今焦化行业亟待解决的问题。
基于此,本文章对焦化厂现代炼焦技术问题进行探讨,以供相关从业人员参考。
关键词:焦化厂;现代炼焦技术;问题;解决对策引言炼焦是将煤炭在高温条件下分解、挥发和燃烧,产生焦炭和其他副产品的过程。
传统的炼焦技术存在生产效率低、环境污染严重等问题,因此,各国炼焦厂纷纷引入现代炼焦技术,以改善传统炼焦的缺陷。
现代炼焦技术以其高效、环保和经济的特点,受到了广泛关注和应用。
一、焦化厂现代炼焦技术的分类焦化厂现代炼焦技术主要分为热炼焦技术、冷炼焦技术和半热半冷炼焦技术三大类。
热炼焦技术是指在高温条件下进行炼焦,通常采用高温炉炼焦技术或热炉炼焦技术。
这种技术能够快速提高焦炭产量和质量,但能耗较高。
冷炼焦技术是指在低温条件下进行炼焦,通常采用冷炉炼焦技术或低温炉炼焦技术。
这种技术能够减少能耗和减少环境污染,但产量较低。
半热半冷炼焦技术是将热炼焦技术和冷炼焦技术相结合,充分利用两者的优点,提高产量和降低能耗。
随着现代技术的不断发展,焦化厂炼焦技术也在不断创新和改进,使得焦炭的生产更加高效、环保和节能。
二、焦化厂现代炼焦技术的问题分析(一)严重污染环境传统炼焦工艺在焦化过程中会产生大量的废气、废水和废渣,导致严重的环境污染问题。
在传统炼焦工艺中,煤炭在高温下分解释放出大量有害气体,如二氧化硫、氮氧化物等,这些气体会对大気造成污染,影响空气质量和人们的健康。
炼焦过程中产生的废水含有高浓度的悬浮固体和有机物质,如果未经处理直接排放会对水体造成污染,影响水生态系统的平衡。
焦炭生产也会产生大量废渣,包括煤焦油、焦油、煤渣等,如果处理不当会导致土壤污染和资源浪费。
- 1、下载文档前请自行甄别文档内容的完整性,平台不提供额外的编辑、内容补充、找答案等附加服务。
- 2、"仅部分预览"的文档,不可在线预览部分如存在完整性等问题,可反馈申请退款(可完整预览的文档不适用该条件!)。
- 3、如文档侵犯您的权益,请联系客服反馈,我们会尽快为您处理(人工客服工作时间:9:00-18:30)。
世界金属导报/2011年/7月/5日/第010版原料炼铁常规炼焦工艺与热回收炼焦工艺的比较林立恒常规炼焦工艺和热回收炼焦工艺都能生产优质焦炭及达到能量平衡,同时可保证低生产成本。
为了选择更适合的炼焦工艺,美国哈奇公司对一些炼焦项目进行了可行性研究,并对常规炼焦工艺及热回收炼焦工艺进行了比较研究。
研究结果是炼焦工艺的选择必需就事论事,因为决定的因素很多,其中包括可用的土地及能源、钢厂总体布局、环境及设备投资等各个方面。
两种炼焦工艺的总能量平衡存在着很大差别,热回收炼焦工艺可以大量发电,而常规炼焦工艺能产出钢铁冶炼用的煤气。
1 炼焦工艺概述冶金焦生产工艺有三种类型:常规炼焦,热回收炼焦及蜂窝焦炼焦。
热回收炼焦工艺是蜂窝焦生产工艺的革新。
蜂窝焦生产工艺绝大多数已被淘汰。
下面重点比较常规炼焦工艺及热回收炼焦工艺。
炼焦选用的煤经过筛分破碎至3mm以下,根据煤的岩相组分混配在一起,用于生产优质焦炭。
在选煤中应选用成本低而炼焦效果高的煤。
混配好的煤料装入焦炉里,大约1100℃或更高的温度下使煤料分解干馏变成焦炭。
一个炼焦周期结束后,从炉内推出热焦,使之落入熄焦车里,以便送往熄焦塔,在塔内使焦炭冷却及稳定。
用水熄焦称为湿熄焦,也可用氮气熄焦,这种气体熄焦称为干熄焦。
熄焦后的成品焦供高炉使用。
常规炼焦是因炼焦当中将释放出的各种挥发性物质收集起来精炼成化学副产品而得名。
常规炼焦是在碳化室内,在无氧气氛中进行。
碳化室内保持正压,以防外部空气窜入,挥发性物质被燃烧。
现代焦炉高度通常为4-8m。
对于双联火道常规炼焦炉,保证整个炉组温度高而分布均匀至关重要。
1.1 常规炼焦工艺常规炼焦时主要污染物排放源生成于推焦过程。
推焦时炉门打开,红焦直接暴露在大气中。
焦炉碳化室高度越高,焦炉生产的焦炭就越多,因而能以较少的装煤及推焦次数以及较少的污染物排放量生产出更多的焦炭。
常规炼焦中放出来的各种挥发性物质进入总集气管,然后送到副产品回收装置。
荒煤气经喷洒液及初冷器,焦油冷凝。
接着静电沉淀器脱除尚存的焦油。
根据市场需求,对煤气作更深层次的处理,生产出另外一些副产品,包括萘、硫酸铵及硫等。
被称为焦炉煤气的净煤气贮存在煤气柜中,予以升压,供全厂用作加热燃料及还原气体。
1.2 热回收炼焦工艺在热回收炼焦工艺中,各种挥发性物质都在焦炉内完全燃尽,以便保证炼焦所需热量。
热回收炼焦采用卧式焦炉。
炉门留有空气入口,用于引进一次燃烧空气,使挥发性物质在碳化室内发生局部燃烧。
二次燃烧空气从炉底烟道引入。
炉底烟道呈蛇形走势,位于煤气之下。
这种烟道布置型式及气流控制模式能保证煤层顶部及底部煤料达到均衡结焦。
由于炉内的温度极高,所以各种有害碳氢化合物及副产品都在碳化室内全部燃尽。
高温气体通过废气通道送至热回收蒸汽发生器,生产高压蒸汽,供加热及发电用。
冷却后的废气送入脱硫装置进行脱硫,然后排入大气。
2 案例研究根据钢厂布局及原燃料来源的不同,提供两种情景进行比较研究。
情景研究的内容包括:◆推导全厂总能量平衡;◆确定每种工艺的基建费用;◆推算每种工艺的生产成本;◆通过流动资金分析确定哪一种工艺在项目20年使用期限内投资回报最多;◆根据能耗强度以及SO2和其它有害物排放量计算每种工艺的环境影响。
2.1 情景1选择哈奇公司为南非偏远地区拟建一座新炼铁厂而作的炼焦厂作为情景1进行比较研究。
这家综合工厂包括烧结厂、球团厂、炼焦厂、高炉及发电厂,炼焦厂每年为高炉提供冶金焦(25-80mm)及小块焦(15-25mm)共计83万t,小于15mm的碎焦用作烧结厂及球团厂的固体燃料。
生产的生铁及铁矿石球团外销。
为了进行比较研究,重点分析常规炼焦工艺及热回收炼焦工艺的全厂能量平衡。
这样就可计算每种炼焦工艺的能量需求及评价其它各种设备之间的相互配合效果。
为进行分析比较,特做以下假设:◆此生铁冶炼厂能生产其所需的全部电力,不必从厂外电网购买电力;◆高炉及常规焦炉所产生的煤气不用于生铁冶炼而是用于生产蒸汽及发电;◆该厂卖给当地电网的多余电力,可获得额外收入;◆当需要为高炉提供高热值燃料时,使用的是重质燃料油,如果不能用副产煤气达到能量平衡,也是用燃料油来平衡电力缺口;◆厂区无天然气可用。
此研究中考虑三种燃料来源:①高炉煤气它来自本厂高炉,煤气成分大致为:20%CO,20%CO2,5%H2及55%N2。
由于惰性气体百分率很高,所以此煤气热值较低,约为3.5MJ/Nm3。
高炉煤气用于自身热风炉加热,如有可能,将剩余高炉煤气外销给其它厂家。
高炉煤气热值偏低,因而不适合用于烧结厂及球团厂。
在电厂,必需使用燃油来弥补高炉煤气的这种不足。
②焦炉煤气它是常规炼焦过程中产生的主要副产品。
焦炉煤气的主要成分为:50%H2,25%CO,20%CH4,5%CO2。
焦炉煤气热值极高达18MJ/Nm3,因而可用于钢厂各种加热作业,其中包括焦炉自身的加热。
③燃油燃油是在其它煤气完全耗尽或需用高热值燃料及无焦炉煤气可用时的补充燃料。
燃油热值为40MJ/kg。
但其硫分相当高,燃烧时会排放SO2。
生产成本是根据全厂物料及能量平衡以及中国设备供货商所提供的技术资料计算的。
计算所用各项单价是由买方提供或用一地区可比价确定的。
常规炼焦及热回收炼焦的基建投资是根据中国设备供货商的报价、哈奇计算的工程费及间接费计算的。
对每种工艺进行了简明财务分析,用20年期的净现值说明了分析结果,其中折现因数为10%。
为计算营业收入采用产品的售价:生铁为300美元/t,铁矿石球团为115美元/t。
项目工期定为三年。
环境影响是根据哈奇的4QA“可持续发展”方法计算的。
用此方法可从量及质两方面加权计算不同环境因素作出评价。
各种环境因素包括:①能耗强度是衡量净能量利用率的计算因素;②二氧化硫排放量是按照燃烧的燃油量计算出的SO2量。
由于安装了脱硫装置,热回收炼焦工艺发电厂排放的SO2及常规炼焦工艺焦炉煤气燃烧产生的SO2极少。
③从质上对萘及其它芳香烃等其它污染物作了说明。
④外销电力是指可出售给当地电网的那部分电力。
常规炼焦工艺使用煤气的生产环节有烧结厂,球团厂,炼焦厂及高炉铁厂。
发电厂需要生产足够的电力满足全厂的需求及生产高炉鼓风机所需的蒸汽。
在这种情况下不向当地电网出售电力。
热回收炼焦工艺与常规炼焦工艺的根本区别是将热回收焦炉产生的废热气流送至热回收蒸汽发生器生产高压蒸汽。
因为热回收焦炉是靠自身加热,所以全部剩余高炉煤气都用在发电厂上。
值得一提的是烧结厂、球团厂及发电厂所需的燃油总用量要比常规炼焦工艺少约40万GJ/a。
但热回收炼焦工艺有大量剩余电力卖给当地电网。
上述两种炼焦工艺的最大差别在于热回收炼焦炉所产生的废气中的显热被回收利用。
这是常规炼焦工艺无法做到的。
因为常规炼焦工艺必需将煤气冷却下来才能析出焦油和萘等;其产生的焦炉煤气虽然热值很高,但显热尚无法很好地回收利用。
全炼铁厂的基建投资预算列于表1。
表1中将炼焦厂基建投资分小项列出,以说明两种炼焦工艺的差别。
热回收炼焦厂基建投资费用较高,原因是这项费用中包括了废热发电厂及烟气脱硫设施。
该电厂管网含为高炉风机提供蒸汽及发电的煤气/燃油联合发电机组管路。
当两座电厂并网时将会从根本上降低热回收炼焦厂基建费,但此项目现尚未作进一步研究。
两种工艺生产成本的比较如表2所列。
其中主要差别是副产品出售、电力出售及燃油费。
操作及维护用工方面,热回收炼焦工艺用工较少,主要是因为它没有生产副产品所需的化工设施。
以项目20年使用期限内的流动资金为主要考核内容对两种炼焦工艺作了评价,详见表3。
表3表明在20年使用期限内(包括3年施工及试运行期)热回收炼焦工艺的净现值(NPV)及内部利润率(IRR)均高于常规炼焦工艺。
因此,热回收炼焦工艺虽然基建费较高,但由于使用费用较低,故20年使用期限中的投资利润高。
为确定哪些参数对项目NPV的影响大,进行了企业敏感性分析,着重对比了对基建费及电价变化的敏感性,结果表明,在任何情况下热回收炼焦工艺都不受这两项费用变化的影响,因而其NPV最高。
在环境影响方面,用哈奇的4QA方法进行了环境对比。
结果是,在情景1条件下,热回收炼焦工艺对环境危害小,环境成本低。
情景1表明热回收炼焦工艺优越,因为该工艺在无天然气及不能由当地电网供电条件下,自已发电可以明显降低生产成本,而且整个使用年限中投资回报较高。
2.2 情景2选择一家在新场地建厂的钢厂做比较研究,该厂也建在南非,但是位于发达地区。
这家综合工厂包含烧结厂、炼焦厂、高炉铁厂、氧气转炉钢厂、薄板坯连铸厂、热轧带钢厂及发电厂。
此情景认定可从当地电网获得电力且有天然气资源。
炼焦厂每年需生产41万t高炉用焦炭及烧结厂用固体燃料的碎焦(小于15mm),该厂年产带卷100万t。
研究方法与情景1相同,情景2的假设条件如下:◆高炉及常规焦炉发生的副产品煤气不用于钢铁生产,而是用于生产蒸汽及发电;◆生产的剩余电力外售给当地电网,可获得额外收入;◆全厂区甚至周边形成的电力需求均由当地电网保证供给;◆当高炉需要高热值燃料作补充时,使用天然气补充。
与情景1相同,这里所用的生产成本及基建投资数据也是以中国设备供货商提供的两种炼焦技术资料为基础。
工程费用及间接费用是由哈奇计算的。
常规炼焦工艺的发电厂只使用废气,但全厂需要从当地电网购买大量电力,不需要使用天然气。
热回收炼焦工艺用天然气作烧结厂、氧气转炉、高炉及轧钢均热炉的高热值燃料。
两种炼焦工艺的主要区别是:热回收炼焦工艺无需从当地电网输入电力,而需大量使用天然气。
相反,常规炼焦工艺无需使用天然气,而需从外部购买电力。
两种工艺的基建费用明细列于表4,表4表明热回收炼焦工艺的基建费用较高,其原因是热回收炼焦工艺的发电厂规模较大。
表5为两种工艺生产成本对比,两种工艺的主要差别是:一个需购入电力,另一个需购入天然气。
比较结果表明,两种工艺优劣相差无几,企业对电力及天然气价格的敏感性会成为影响全厂的头等重要因素。
表6为情景2下两种工艺的财务分析结果。
情景2表明常规炼焦基建投资较低且无需额外补充燃料。
所以常规炼焦工艺比热回收炼焦具有明显的经济优势。
分析表明,在电价及天然气价格方面隐藏着巨大的立项风险。
3 结语常规炼焦工艺及热回收炼焦工艺都能够生产出满足高炉要求的高质量焦炭。
客户选择何种类型炼焦厂,应当根据投资回报以及炼焦厂在整个钢厂中所起作用和外部能源可靠利用条件来决定。
在情景1的情况下,由于缺少当地电网可供的电力,并且不需要发电用的高价燃油,所以宜选用热回收炼焦工艺。
在情景2的条件下,如果电力及天然气都能以低价购入,则常规炼焦工艺是优先选择的工艺。
企业敏感性分析表明,一旦电价及天然气上涨则也不适宜选择常规炼焦工艺。
从环境角度来看,热回收炼焦工艺优于常规炼焦,因为前者环境危害很小。