分离共沸混合物
共沸除水的原理再说明

共沸除水的原理再說明共沸除水是一种物理分离技术,通常用于从混合物中分离出水。
它基于液体的沸点是其蒸气与环境中压强相当的温度。
这种方法的原理涉及到液体和蒸汽的相互作用以及压力的影响。
1. 理解共沸除水在混合物中,如果我们希望从一个液体中分离出水,可以利用共沸除水的原理。
这种方法依赖于在一定压强下,液体和蒸汽达到平衡,达到共沸点。
共沸点是液体和该液体对应蒸气压的平衡温度。
2. 液体蒸发与沸腾当液体与固体或气体的界面接触时,它的分子将不断撞击界面,并以不同速度转化为蒸气。
这个过程被称为蒸发。
当液体接触到较高温度的表面时,分子的能量增加,导致更多的分子转化为气体。
这个过程称为沸腾。
3. 液体蒸汽与平衡液体中的分子以各种速度运动。
在开放容器中,快速的分子逃逸并形成蒸气,但慢速的分子会返回液体中。
当蒸汽和液体达到平衡时,称为饱和蒸气压。
这意味着在给定的温度和压力下,液体和蒸汽之间的分子转化达到平衡。
4. 共沸点在混合物中,液体和蒸汽之间的相互转化仍然存在。
如果混合物中的两种液体具有相似的蒸气压,在给定的温度和压力下,它们将具有相同的蒸汽-液体平衡。
这个温度称为共沸点。
在共沸点下,液体和蒸汽之间的分子转化达到平衡,从而实现了分离。
5. 共沸除水原理共沸除水利用了水的特性和其他液体的相似性。
在混合物中,当我们加热液体混合物时,水和另一种液体的蒸汽压趋于相等。
这意味着,在共沸点下,水和另一种液体的蒸汽-液体平衡将达到。
通过控制温度和压力,我们可以将水从混合物中去除。
6. 具体步骤共沸除水通常使用分馏设备来实现。
它包括一个加热器和一个冷凝器。
混合物被加热到共沸点,使液体转变为蒸汽。
蒸汽进入冷凝器,在冷却器中冷却并转变为液体形式。
由于水和另一种液体的蒸气-液体平衡相似,水将凝结为液体,而另一种液体则以蒸汽形式保持。
通过收集冷凝器中的液体,我们可以分离出水。
总结与回顾:共沸除水是一种物理分离技术,用于从混合物中分离出水。
共沸精馏分离生物醇-水混合物的模拟与优化
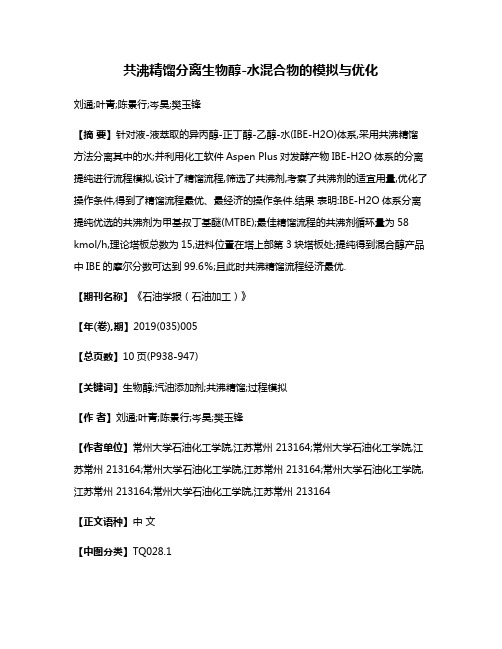
共沸精馏分离生物醇-水混合物的模拟与优化刘通;叶青;陈景行;岑昊;樊玉锋【摘要】针对液-液萃取的异丙醇-正丁醇-乙醇-水(IBE-H2O)体系,采用共沸精馏方法分离其中的水;并利用化工软件Aspen Plus对发酵产物IBE-H2O体系的分离提纯进行流程模拟,设计了精馏流程,筛选了共沸剂,考察了共沸剂的适宜用量,优化了操作条件,得到了精馏流程最优、最经济的操作条件.结果表明:IBE-H2O体系分离提纯优选的共沸剂为甲基叔丁基醚(MTBE);最佳精馏流程的共沸剂循环量为58 kmol/h,理论塔板总数为15,进料位置在塔上部第3块塔板处;提纯得到混合醇产品中IBE的摩尔分数可达到99.6%;且此时共沸精馏流程经济最优.【期刊名称】《石油学报(石油加工)》【年(卷),期】2019(035)005【总页数】10页(P938-947)【关键词】生物醇;汽油添加剂;共沸精馏;过程模拟【作者】刘通;叶青;陈景行;岑昊;樊玉锋【作者单位】常州大学石油化工学院,江苏常州 213164;常州大学石油化工学院,江苏常州 213164;常州大学石油化工学院,江苏常州 213164;常州大学石油化工学院,江苏常州 213164;常州大学石油化工学院,江苏常州 213164【正文语种】中文【中图分类】TQ028.1化石燃料的燃烧导致雾霾等诸多环境问题,可再生生物能源受到越来越多的关注[1]。
研究发现[2],生物丁醇是一种高辛烷值、高热值的替代燃料,其热值可与汽油媲美。
生物丁醇主要来自发酵产物,但生物丁醇在发酵液中的浓度低且与水形成共沸物[3],造成组分分离提纯困难,因此正丁醇的分离提纯一直是生物丁醇生产过程中的难题。
一般而言,发酵产物包含丙酮-正丁醇-乙醇(ABE)的混合物[4]。
丙酮作为生物燃料性能差,是一种非理想的发酵副产物;而异丙醇作为燃料具有更好的性能。
因此,人们在发酵过程中添加生物催化剂将丙酮还原为异丙醇[5-6],得到异丙醇-正丁醇-乙醇(IBE)的混合物。
离子液体分离乙酸乙酯-乙醇共沸体系研究进展

第50卷第4期辽 宁化工V〇1.50,No. 4 2021 年 4 月Liaoning Chemical Industry_________________________________A p ril,2021离子液体分离乙酸乙酯-乙醇共沸体系研究进展何鑫,张强,范雪萤,王丽达,李文秀(沈阳化工大学辽宁省化工分离技术重点实验室,辽宁沈阳丨10142)摘要:乙酸乙酯(E A)是一种用途广泛且需求量较大的精细化T产品=在乙酸乙酯的生产中存在大量乙酸乙酯与乙醇的混合物,乙酸乙酯与乙醇两者易形成共沸物,普通的精馏方法无法有效分离两种物质离子液体因其良好的物理、化学性质和对环境友好,结构可灵活调节,在化工萃取分离方面有良好的表现。
对离子液体分离乙酸乙酯混合物研究进展进行介绍,总结了单一离子液体、混合离子液体对共沸物系的分离效果,并对离子液体分离共沸物的机理进行研究关键词:共沸物分离;离子液体;萃取中图分类号:TQ028.3‘I文献标识码:A文章编号:1004-0935(2021 ) 04-0489-041简介1.1乙酸乙酯(E A)-乙醇纯净乙酸乙酯是用途最广的脂肪酸酯之一,具 有良好的溶解性是常用的工业溶剂和有机化工原 料,被大量用于工业产品的合成中;因其无毒的特 性也常被用于提取香料和药品。
E A的快干性,常 被添加在油漆和涂料中。
特殊的酯香味也会应用在 食品里。
随着我国实体经济的高速发展,E A成为 高消耗品,我国对E A的需求量几乎占到全世界需 求量的一半。
目前E A工业生产主要的方法有四种,分别是乙酸酯化法、乙酸/乙烯加成法、乙醛缩合法 和乙醇脱氢法。
世界各国工业发展和自然资源情况 不同选择生产工艺也不同,美国以直接酯化法为主,日本和欧洲则以乙醛缩合法为主。
从产能上看,国内外市场主要供应来自直接酯化法,大约占67.5%,我国当前主要也是采用该工艺。
在生产中为使价格 相对较高的乙酸达到最优转化率,常会加入过量的 乙醇,粗产品中主要是乙醇与E A的混合物。
共沸物分离的方法
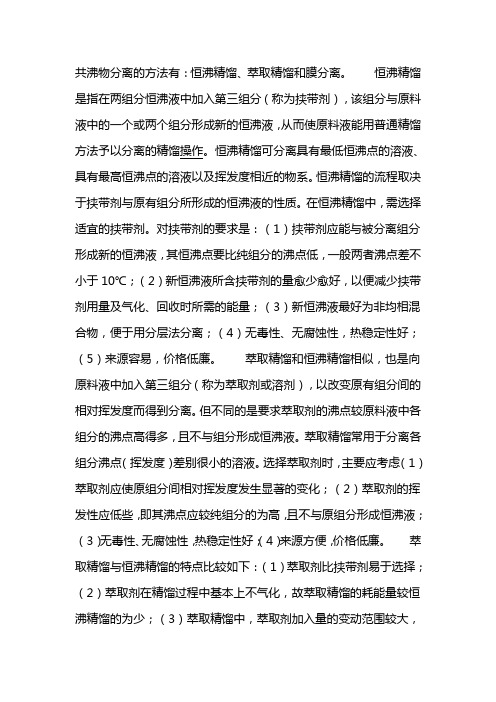
共沸物分离的方法有:恒沸精馏、萃取精馏和膜分离。
恒沸精馏是指在两组分恒沸液中加入第三组分(称为挟带剂),该组分与原料液中的一个或两个组分形成新的恒沸液,从而使原料液能用普通精馏方法予以分离的精馏操作。
恒沸精馏可分离具有最低恒沸点的溶液、具有最高恒沸点的溶液以及挥发度相近的物系。
恒沸精馏的流程取决于挟带剂与原有组分所形成的恒沸液的性质。
在恒沸精馏中,需选择适宜的挟带剂。
对挟带剂的要求是:(1)挟带剂应能与被分离组分形成新的恒沸液,其恒沸点要比纯组分的沸点低,一般两者沸点差不小于10℃;(2)新恒沸液所含挟带剂的量愈少愈好,以便减少挟带剂用量及气化、回收时所需的能量;(3)新恒沸液最好为非均相混合物,便于用分层法分离;(4)无毒性、无腐蚀性,热稳定性好;(5)来源容易,价格低廉。
萃取精馏和恒沸精馏相似,也是向原料液中加入第三组分(称为萃取剂或溶剂),以改变原有组分间的相对挥发度而得到分离。
但不同的是要求萃取剂的沸点较原料液中各组分的沸点高得多,且不与组分形成恒沸液。
萃取精馏常用于分离各组分沸点(挥发度)差别很小的溶液。
选择萃取剂时,主要应考虑(1)萃取剂应使原组分间相对挥发度发生显著的变化;(2)萃取剂的挥发性应低些,即其沸点应较纯组分的为高,且不与原组分形成恒沸液;(3)无毒性、无腐蚀性,热稳定性好;(4)来源方便,价格低廉。
萃取精馏与恒沸精馏的特点比较如下:(1)萃取剂比挟带剂易于选择;(2)萃取剂在精馏过程中基本上不气化,故萃取精馏的耗能量较恒沸精馏的为少;(3)萃取精馏中,萃取剂加入量的变动范围较大,而在恒沸精馏中,适宜的挟带剂量多为一定,故萃取精馏的操作较灵活,易控制;(4)萃取精馏不宜采用间歇操作,而恒沸精馏则可采用间歇操作方式;(5)恒沸精馏操作温度较萃取精馏的为低,故恒沸精馏较适用于分离热敏性溶液。
膜分离是根据生物膜对物质选择性通透的原理所设计的一种对包含不同组分的混合样品进行分离的方法。
共沸混合物

常见有机溶剂间的共沸混合物压力单位换算表注:毫米水柱是指4摄氏度状态的水柱高度,毫米汞柱是指0摄氏度状态的水柱高度。
实验室常用酸、碱的浓度试剂名称密度(20℃)g/ml 浓度mol/L 质量分数浓硫酸 1.84 18.0 0.960 浓盐酸 1.19 12.1 0.372 浓硝酸 1.42 15.9 0.704 磷酸 1.70 14.8 0.855 冰醋酸 1.05 17.45 0.998 浓氨水0.90 14.53 0.566 浓氢氧化钠 1.54 19.4 0.505一些溶剂与水形成的二元共沸物用于有机溶剂的中等强度的干燥剂有机化合物的鉴别在药品的生产、研究及检验等过程中,常常会遇到有机化合物的分离、提纯和鉴别等问题。
有机化合物的鉴别、分离和提纯是三个既有关联而又不相同的概念。
分离和提纯的目的都是由混合物得到纯净物,但要求不同,处理方法也不同。
分离是将混合物中的各个组分一一分开。
在分离过程中常常将混合物中的某一组分通过化学反应转变成新的化合物,分离后还要将其还原为原来的化合物。
提纯有两种情况,一是设法将杂质转化为所需的化合物,另一种情况是把杂质通过适当的化学反应转变为另外一种化合物将其分离(分离后的化合物不必再还原)。
鉴别是根据化合物的不同性质来确定其含有什么官能团,是哪种化合物。
如鉴别一组化合物,就是分别确定各是哪种化合物即可。
在做鉴别题时要注意,并不是化合物的所有化学性质都可以用于鉴别,必须具备一定的条件:(1)化学反应中有颜色变化(2)化学反应过程中伴随着明显的温度变化(放热或吸热)(3)反应产物有气体产生(4)反应产物有沉淀生成或反应过程中沉淀溶解、产物分层等。
本课程要求掌握的重点是化合物的鉴别,为了帮助大家学习和记忆,将各类有机化合物的鉴别方法进行归纳总结,并对典型例题进行解析。
一.各类化合物的鉴别方法1.烯烃、二烯、炔烃:(1)溴的四氯化碳溶液,红色腿去(2)高锰酸钾溶液,紫色腿去。
三乙胺、乙醇和水混合物分离工艺模拟与优化
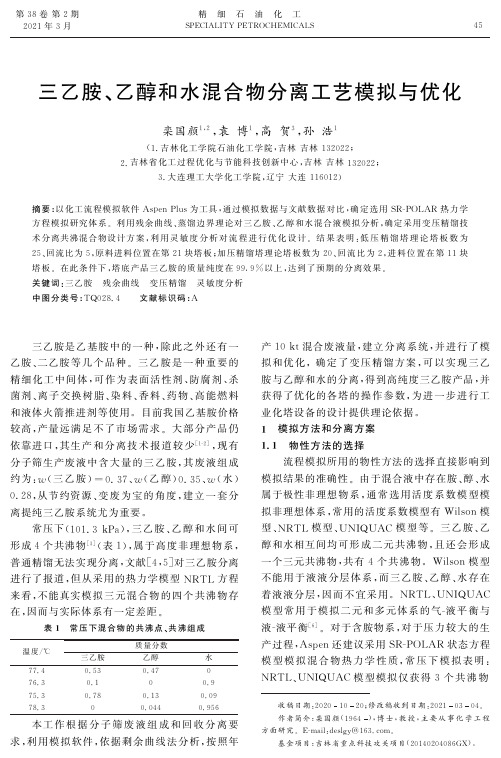
三乙胺㊁乙醇和水混合物分离工艺模拟与优化栾国颜1,2,袁博1,高贺3,孙浩1(1.吉林化工学院石油化工学院,吉林吉林132022;2.吉林省化工过程优化与节能科技创新中心,吉林吉林132022;3.大连理工大学化工学院,辽宁大连116012)摘要:以化工流程模拟软件A s p e nP l u s为工具,通过模拟数据与文献数据对比,确定选用S R-P O L A R热力学方程模拟研究体系㊂利用残余曲线㊁蒸馏边界理论对三乙胺㊁乙醇和水混合液模拟分析,确定采用变压精馏技术分离共沸混合物设计方案,利用灵敏度分析对流程进行优化设计㊂结果表明:低压精馏塔理论塔板数为25㊁回流比为5,原料进料位置在第21块塔板;加压精馏塔理论塔板数为20㊁回流比为2,进料位置在第11块塔板㊂在此条件下,塔底产品三乙胺的质量纯度在99.9%以上,达到了预期的分离效果㊂关键词:三乙胺残余曲线变压精馏灵敏度分析中图分类号:T Q028.4文献标识码:A三乙胺是乙基胺中的一种,除此之外还有一乙胺㊁二乙胺等几个品种㊂三乙胺是一种重要的精细化工中间体,可作为表面活性剂㊁防腐剂㊁杀菌剂㊁离子交换树脂㊁染料㊁香料㊁药物㊁高能燃料和液体火箭推进剂等使用㊂目前我国乙基胺价格较高,产量远满足不了市场需求㊂大部分产品仍依靠进口,其生产和分离技术报道较少[1-2],现有分子筛生产废液中含大量的三乙胺,其废液组成约为:w(三乙胺)=0.37㊁w(乙醇)0.35㊁w(水) 0.28,从节约资源㊁变废为宝的角度,建立一套分离提纯三乙胺系统尤为重要㊂常压下(101.3k P a),三乙胺㊁乙醇和水间可形成4个共沸物[3](表1),属于高度非理想物系,普通精馏无法实现分离,文献[4,5]对三乙胺分离进行了报道,但从采用的热力学模型N R T L方程来看,不能真实模拟三元混合物的四个共沸物存在,因而与实际体系有一定差距㊂表1常压下混合物的共沸点㊁共沸组成温度/ħ质量分数三乙胺乙醇水77.40.530.47076.30.100.975.30.780.130.0978.300.0440.956本工作根据分子筛废液组成和回收分离要求,利用模拟软件,依据剩余曲线法分析,按照年产10k t混合废液量,建立分离系统,并进行了模拟和优化,确定了变压精馏方案,可以实现三乙胺与乙醇和水的分离,得到高纯度三乙胺产品,并获得了优化的各塔的操作参数,为进一步进行工业化塔设备的设计提供理论依据㊂1模拟方法和分离方案1.1物性方法的选择流程模拟所用的物性方法的选择直接影响到模拟结果的准确性㊂由于混合液中存在胺㊁醇㊁水属于极性非理想物系,通常选用活度系数模型模拟非理想体系,常用的活度系数模型有W i l s o n模型㊁N R T L模型㊁U N I Q U A C模型等㊂三乙胺㊁乙醇和水相互间均可形成二元共沸物,且还会形成一个三元共沸物,共有4个共沸物㊂W i l s o n模型不能用于液液分层体系,而三乙胺㊁乙醇㊁水存在着液液分层,因而不宜采用㊂N R T L㊁U N I Q U A C 模型常用于模拟二元和多元体系的气-液平衡与液-液平衡[6]㊂对于含胺物系,对于压力较大的生产过程,A s p e n还建议采用S R-P O L A R状态方程模型模拟混合物热力学性质,常压下模拟表明: N R T L㊁U N I Q U A C模型模拟仅获得3个共沸物收稿日期:20201020;修改稿收到日期:20210304㊂作者简介:栾国颜(1964),博士,教授,主要从事化学工程方面研究㊂E-m a i l:d e s l g y@163.c o m㊂基金项目:吉林省重点科技攻关项目(20140204086G X)㊂54第38卷第2期2021年3月精细石油化工S P E C I A L I T YP E T R O C H E M I C A L S存在,与实际体系4个共沸物不一致;S R-P O-L A R状态方程模型模拟可以出现4个共沸物,通过不同物性方程模拟的温度和组成与文献值数据对比(表2)㊂为了比较各热力学模型计算结果的准确性,按照:计算总误差=ð共沸物个数1A B S(文献值-模拟值),分别计算N R T L㊁U N I Q U A C和S R-P O L A R 模型模拟值与计算值误差值后得到表2㊂表2常压下不同模型模拟共沸物沸点与组成物性方程共沸物个数种类沸点/ħ误差质量分数三乙胺乙醇水N R T L3 U N I Q U A C3 S R-P O L A R4三乙胺-水69.65-6.650.847400.1526三乙胺-乙醇78.26+0.860.18840.81160水-乙醇78.15-0.1500.04040.9596三乙胺-水70.55-5.70.851700.1483三乙胺-乙醇78.27+0.870.26320.73680水-乙醇78.16-0.1400.95830.0417三乙胺-水81.55+4.150.806200.1938三乙胺-水-乙醇76.25+0.950.45040.01870.5308三乙胺-乙醇76.29-1.110.45480.54520水-乙醇78.04-0.3600.9560.044表3常压下计算共沸点、共沸组成与文献值累积误差对比模型沸点差三乙胺计算差乙醇计算差水计算差总计算误差N R T L7.661.49480.68321.831211.6692 U N I Q U A C6.761.50340.53361.828610.6256 S R-P O L A R6.621.41240.15041.82410.0068由表3结果可知,S R-P O L A R模型计算结果累计误差最小㊂表4不同压力下S R-P O L A R模型计算值与文献值误差对比压力/P a与文献值比共沸点温差/K与文献值比相对误差分数/% 200003.441.12266603.151.00400001.220.38 101325-0.05-0.01 2100000.810.22 4000001.240.32从表4可以看出,采用S R-P O L A R模型模拟,除在低于常压下,沸点差误差较大外,在其他情况下,计算模拟值与文献值符合较好㊂因而可以采用此模型进行后续分离方案模拟研究㊂1.2分离方案的确定剩余曲线是间歇蒸馏过程釜内液相浓度随时间的变化轨迹㊂剩余曲线是有向线,由低沸点出发到高沸点终止,同一条剩余曲线上的不同点对应着不同的蒸馏时间,箭头所指方向既是时间延长的方向,又是温度升高的方向㊂将三元物系的三角形相图分成不同蒸馏区域的特殊剩余曲线称为精馏边界线,精馏边界常常把三元相图分割成几个不同的精馏区域,在不同区域进行精馏可以得到不同的产品㊂对分离物系三元相图中的剩余曲线分析研究,通过剩余曲线图可以判断分离趋势,成为共沸精馏过程研究的重要工具[6-8]㊂利用A s p e n模拟软件,采用S R-P O L A R模型,模拟常压下三乙胺㊁乙醇和水三元相图,获得剩余曲线和共沸物情况结果如图1所示㊂图1常压下,三乙胺㊁乙醇和水三元相图进料点m(三乙胺)/m(乙醇)/m(水)=0.37/0.35/0.28;塔顶产品点m(三乙胺)/m(乙醇)/m(水)=0.52/0.40/0.0864精细石油化工2021年3月从图1可知,进料点在精馏区域3内,按照精馏理论,塔底产品可以获得纯产品水,塔顶获得是沸点为76.25ħ的三乙胺㊁乙醇和水共沸物或一定组成的三乙胺和乙醇的混合物,如图1所标注的塔顶产品,无法获得高纯三乙胺㊂如果以此混合物作为进料,继续采用常压操作,按照图1所示的剩余曲线和精馏区域,可知获得的塔顶产品是沸点为76.25ħ的三乙胺㊁乙醇和水的共沸物,塔底产品81.78ħ的三乙胺水的共沸物,无法获得高纯三乙胺㊂为了解决精馏区域的限制,可以采用加入质量分离剂和改变操作压力的办法实现混合物跨越过原来精馏区域㊂但加入质量分离剂,势必要增加质量分离剂装置,一般不是首选分离方案,为此,考虑改变精馏操作压力来实现分离的目的㊂首先,采用降低分离操作压力,获得的三元相图如图2所示㊂从图2可知,随着操作压力的降低,塔顶获得的混合物产品组成不断变化,三乙胺含量逐渐增大㊂水和乙醇含量均下降㊂常压下的精馏区域1㊁2范围缩小,精馏区域3范围增大㊂图2塔压50k P a和20k P a下,三乙胺㊁乙醇和水三元相图其次,采用增加精馏操作压力,获得的三元相图如图3所示㊂从图3可以看到,加压到200k P a 后,3个精馏区域发生新的变化,精馏区域3减小,精馏区域1明显增大,常压操作时获得的塔顶产品点已经移入加压操作时精馏区域1内,当操作压力进一步加大到400k P a时,精馏区域1也进一步加大㊂按照前面的剩余曲线指向,在加压塔中,塔顶获得的是三乙胺㊁乙醇和水的共沸混合物,塔底可获得高纯三乙胺,如图3加压塔底产品点箭头所示㊂根据上面剩余曲线图和精馏区域,可以看出,如果采用如下分离方案:第一个精馏塔采用常压或减压操作,第二个精馏塔采用加压操作可以获得高纯度三乙胺产品,从而实现共沸物分离㊂图3塔压200k P a和400k P a下,三乙胺㊁乙醇和水三元相图2流程模拟及工艺参数优化与讨论分离回收三乙胺的工艺流程由变压精馏实现,三乙胺㊁乙醇和水分离工艺流程如图4所示㊂图4三乙胺㊁乙醇和水精馏流程三乙胺㊁乙醇和水混合液加入低压精馏塔中,精馏后塔底采出水㊁乙醇混合物,塔顶得到三乙胺㊁乙醇和少量水,进入加压塔后塔顶得到是三乙胺㊁乙醇和水,塔底采出高纯度的三乙胺㊂74第38卷第2期栾国颜,等.三乙胺㊁乙醇和水混合物分离工艺模拟与优化在整个工艺流程中精馏塔的工艺参数直接影响精馏塔塔顶产品三乙胺的纯度,并影响着整个塔的能量消耗,因此利用化工流程模拟软件A s-p e n P l u s中R a d F r a c模块和S e n s i t i v i t y模块[4],对精馏塔理论板数㊁原料进料位置㊁回流比进行优化,确定适宜的操作参数㊂低压塔和加压塔的工艺参数优化从操作方法和原理上无差异,以下以低压塔优化为例㊂2.1理论板数对分离效果的影响在精馏操作过程中,精馏塔塔板数的增加会使分离效果增强,但会使得设备费和操作费也增大,因此要综合整个工艺指标,平衡好理论塔板数和产品质量及产量的关系,以此采用严格塔计算模块分别对低压塔和加压塔进行计算,在回流比为2㊁40块板为进料板的条件下,在保证塔顶㊁塔底纯度不变的情况下,分析理论塔板数的变化对塔底再沸器能耗的影响如图5所示㊂图5理论塔板数对塔底再沸器能耗的影响图5中可以看出,随理论板数增加,塔底再沸器的能量消耗逐渐减少,特别在理论板为25块和26块时再沸器能量消耗几乎成直线上升㊂综合考虑增加理论板数会增加设备成本,所以选择25块为全塔理论板数㊂2.2原料进料位置对分离效果的影响低压塔理论塔板数为25块㊁回流比为5的情况下,模拟进料位置的变化对塔底再沸器能耗和塔底三乙胺含量的影响关系为图6所示㊂图6中可知,随着低压塔的进料位置从第2块塔板到第10块塔板,塔底热负荷下降较显著,从10块板后,减少趋缓,21块板后,塔底再沸器能耗不再下降,可以看到从21板进料,塔底三乙胺含量较低,超过25块板,三乙胺含量增加显著,会造成后续分离三乙胺回收率下降和分离难度加大,因此在第21块板进料时较合适㊂图6进料位置变化对塔底再沸器能耗和塔底流三乙胺组分含量的影响2.3回流比对分离效果的影响回流比的大小不仅控制着塔的分离效果,而且影响着塔底再沸器的蒸汽消耗,因此为了达到产品的品质要求,且使能量消耗达到最小,选择合适的回流比尤为重要[5]㊂在理论板数为25块㊁进料位置在第21块板的条件下,模拟回流比的变化对塔顶水㊁塔底三乙胺含量耗的影响如图7所示㊂图7回流比对塔顶水和塔底三乙胺含量的影响由图7可见,随着低压塔的回流比增加,塔顶的水量减少,塔底三乙胺的含量也随之减少,当回流比为5时,水的含量开始减少缓慢,但三乙胺含量自回流比为1之后,虽然下降较快,但数量级很小,已经满足废水排放纯度要求,回流比加大势必造成塔底再沸器的热负荷也随之增加,因而,易于选择操作回流比为5㊂2.4模拟优化结果采用A S P E N的灵敏度分析模块优化精馏塔理论塔板数㊁原料进料位置和回流比㊂模拟优化结果汇总如表5所示㊂此时三乙胺的总收率为60%,其余未被回收的三乙胺和乙醇水混合物从加压塔塔顶采出,循环至来料混合罐混合后进入低压塔进一步分离三乙胺产品,低压塔塔底为可排放废水㊂84精细石油化工2021年3月表5 模拟优化结果汇总塔塔压/k P a 理论板数进料位置回流比w (三乙胺)低压塔202521565.3加压塔2002011299.93 结 论以化工流程模拟软件A s p e nP l u s 为工具,对比不同热力学模型计算三乙胺㊁乙醇和水混合液热力学性质,发现S R -P O L A R 方程模拟出的组分共沸点数据与文献数据符合较好,此热力学模拟结果更接近实际值㊂以残余曲线㊁蒸馏边界理论为指导,在保证产品三乙胺产品纯度要求下,通过分析残余曲线,确定了变压分离技术方案,并利用软件对变压精馏流程进行了模拟与优化,确定了低压精馏塔㊁加压精馏塔优化操作相关参数㊂对于高度非理想难分离物系,采用该模拟分析方法是行之有效的,也为其他相关共沸物体系分离提供参考㊂参 考 文 献[1] 冯烈.乙基胺的生产和应用[J ].上海化工,1997,22(3):32-34.[2] 齐继成.我国乙基胺产销概况[J ].中国制药信息,1999,15(10):32-33.[3] 穆光照,陈敏为,欧阳仁耀,等.实用溶剂手册[M ].上海:上海科学技术出版社,1990.[4] 韦隆武,钱晔.乙基胺生产分离系统脱轻塔的设计[J ].杭州化工,2006(1):39-44.[5] 李群生,陈文.乙基胺分离系统各塔的设计和模拟计算[J ].北京化工大学学报:自然科学版,2010,37(1):23-27.[6] L u y b e n W L .D i s t i l l a t i o n d e s i g n a n d c o n t r o l u s i n g A s pe n T M s i m u l a t i o n [M ].S h a n g h a i :E a s t C h i n aU n i v e r s i t y of S c i e n c e a n dT e c h n o l og y P r e s s ,2015:102-107.[7] 刘家棋,李永红,陈洪仿.共沸精馏分区特性的研究[J ].化学工程,1991,19(4):6-11.[8] 黄旭,罗祎青,袁希钢.带共沸的乙醇/乙酸乙酯/2-丁酮三元物系变压精馏分离过程及其参数优化[J ].化工学报,2018,69(5):2089-2099.S I M U L A T I O NA N DO P T I M I Z A T I O NO FS E P A R A T I O NP R O C E S SF O RM I X T U R EO FT R I E T H Y L A M I N E ,E T H A N O LA N D W A T E RL u a nG u o ya n 1,2,Y u a nB o 1,2,G a oH e 3,S u nH a o 1(1.S c h o o l o f P e t r o c h e m i c a l a n dE n g n i e e r i n g ,J i l i n I n s t i t u t e o f Ch e m i c a l T e c h n o l o g y ,J i l i n 132022,J i l i n ,C h i n a ;2.J i l i nC h e m i c a lP r o c e s sO p t i m i z a t i o na n dE n e r g y -S a v i n g S c i e n c e a n dT e c h n o l o g y I n n o v a t i o n C e n t e r ,J i l i n 132022,J i l i n ,C h i n a ;3.S c h o o l o f C h e m i c a l a n dE n g i n e e r i n g ,D a l i a nU n i v e r s i t y o f T e c h n o l o g y ,D a l i a n 116012,L i a o n i n g ,C h i n a )A b s t r a c t :B a s e do nA s p e nP l u s ,a c h e m i c a l p r o c e s s s i m u l a t i o ns o f t w a r e ,S R -P O L A Rt h e r m o d yn a m i c e q u a t i o n i s s e l e c t e d f o r t h e s i m u l a t i o n p r o c e s s ,a n dP r e s s u r e -s w i n g d i s t i l l a t i o n i s a d o p t e d t h r o u ghr e -s i d u a l c u r v ea n dd i s t i l l a t i o nb o u n d a r y t os i m u l a t et h es e p a r a t i o n p r o c e s so f t h e m i x t u r eo f t r i e t h yl -a m i n e ,e t h a n o l a n dw a t e r .S e n s i t i v i t y a n a l y s i s i su s e d t oo pt i m i z e t h e p r o c e s s .T h e r e s u l t s s h o wt h a t t h e p u r i t y o f t r i e t h y l a m i n e (T E A )i s o v e r 99.9%u n d e r t h e s e p a r a t i o n s ys t e mo f a l o w p r e s s u r e t o w e r a n da h i g h p r e s s u r e t o w e r .T h e o r e t i c a l p l a t e s n m b e r o f t h e l o w -pr e s s u r e t o w e r i s 25,r e f l u x r a t i o i s 5,f e e d p l a t e i s 21,t h e o r e t i c a l p l a t e s n u m b e r o f h i g h p r e s s u r e t o w e r i s 20,r e f l u x r a t i o i s 2a n d f e e d p l a t e i s 11.K e y wo r d s :t r i e t h y l a m i n e ;r e s i d u a l c u r v e ;p r e s s u r e -s w i n g d i s t i l l a t i o n ;s e n s i t i v i t y a n a l y s i s 94第38卷第2期栾国颜,等.三乙胺㊁乙醇和水混合物分离工艺模拟与优化。
苯酚-水混合物的共沸精馏分离
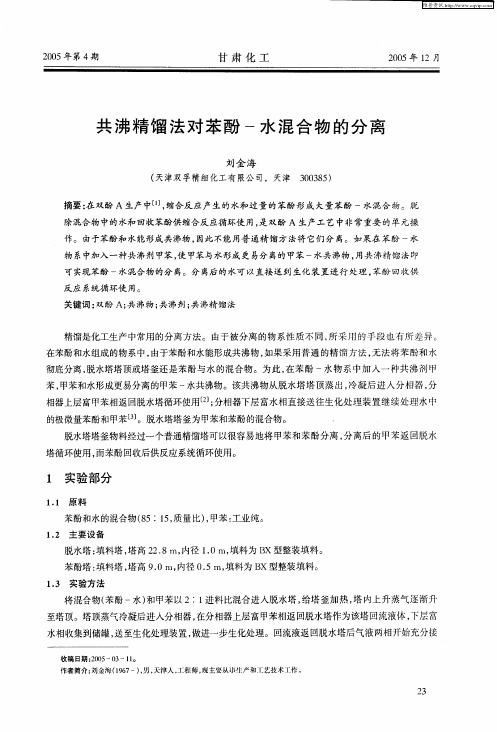
工艺技 术
甘 肃 化 工
20 年第 4 05 期
3 结 语
( ) 化裂 化干 气与 苯烃化 制 取 乙苯 工艺 技 术 , 1催 已基本 成熟 。工业 化 装 置 的工艺 技 术 、 料 乙苯 原
产品质量都已基本达到或接近设计要求 , 在苯乙烯产品用于普通材料时, 可满足后序产 品工艺的要求 ( 除不能满足食品级的要求外 ) 。采用稀乙烯工艺技术上是可行的。 () 2 稀乙烯工艺技术在经济上也是可行的。进一步优化装置 的工艺流程 , 加强装置的精细操作 ,
2 2 脱 水塔和 苯酚 塔双 塔流 程的选 择 .
() 1 在脱水塔分离苯酚 一水 一甲苯混合物操作 中, 虽然 甲
苯和水很容易从塔顶蒸出, 但塔釜如果直接生产苯酚 , 不易保证苯 酚中不 含甲苯 , 因此在设计时允许
脱 水塔塔 釜含一 定 量 甲苯 [ 。塔 釜分 析结果 见 表 2 5 ] 。
[ ] 陈洪钫 . 6 基本有 机化工分离工程 . 北京 : 化学 工业出版社 。9 118 10 18 .7 - 8 .
3 6
作。由于苯酚和水能形成共沸物 , 因此不能用普通精馏方法将它们分 离。如果在苯酚 一水 物系中加入一种共沸剂甲苯, 甲苯与水形成更易分离的甲苯 一水共沸物 , 使 用共沸精馏法即
可 实现苯 酚 一水混合 物 的分 离。分 离后 的 水可 以直接 送 到 生化 装 置 进行 处理 , 酚 回 收供 苯
表 2 塔 釜 分 析 结 果
() 2 脱水塔塔釜苯酚 一甲苯混合物经过一个普通精馏塔 ( 苯酚塔 ) 精馏后 , 塔釜生产出完全不含
甲苯 的苯酚 , 顶轻 组分 甲苯 的一部 分 经苯酚 塔 回流 , 塔 一部 分返 回脱水塔 循 环使 用 。 ()采用 双塔 流程 既可 以保 证 回收苯 酚 的质 量 , 3 又能使 脱 水塔容 易操 作 。
多组分共沸混合物精馏工艺流程的研究

多组分共沸混合物精馏工艺流程的研究1、萃取精馏的原理在基本有机化工生产中,经常会遇到组分的相对挥发度比较接近,组分之间也存在形成共沸物的可能性。
若采用普通精馏的方法进行分离,将很困难,或者不可能。
对于这类物系,可以采用特殊精馏方法,向被分离物系中加入第三种组分,改变被分离组分的活度系数,增加组分之间的相对挥发度,达到分离的目的。
如果加入的溶剂与原系统中的一些轻组分形成最低共沸物,溶剂与轻组分将以共沸物形式从塔顶蒸出,塔底得到重组分,这种操作称为共沸精馏;如果加入的溶剂不与原系统中的任一组分形成共沸物,其沸点又较任一组分的沸点高,溶剂与重组分将随釜液离开精馏塔,塔顶得到轻组分,这种操作称为萃取精馏。
2、溶剂甄选原理由于萃取精馏混合物多为强非理想性的系统,所以工业生产中选择适宜溶剂时主要应考虑以下几点:(1)选择性:溶剂的加人必须使待拆分组分的相对溶解度提高明显,即为建议溶剂具备较低的选择性,以提升溶剂的利用率;2)溶解性:要求溶剂与原有组分间有较大的相互溶解度,以防止液体在塔内产生分层现象,但具有高选择性的溶剂往往伴有不互溶性或较低的溶解性,因此需要通过权衡选取合适的溶剂,使其既具有较好的选择性,又具有较高的溶解性;(3)沸点:溶剂的沸点应当低于原进料混合物的沸点,以避免构成溶剂与组分的共沸物。
但也无法过低,以防止导致溶剂回收塔釜梅过低。
目前提炼减压蒸馏溶剂甄选的方法存有实验法、数据库查阅法、经验值方法、计算机辅助分子设计法用实验法甄选溶剂就是目前应用领域最广泛的方法,可以获得较好的结果,但是实验花费很大,实验周期较长。
实验法存有轻易法、沸点仪法、色谱法、气论调等。
实际应用领域过程中往往须要几种方法融合采用,以延长吻合目标溶剂的时间。
溶剂甄选的通常过程为:经验分析、理论指导与计算机辅助设计、实验检验等。
若文献资料和数据不全系列,则只有实行最基本的实验方法,或者实行极具应用领域前景的计算机优化方法以谋求最佳溶剂。
异丙醇和水的混合物常用的分离方法
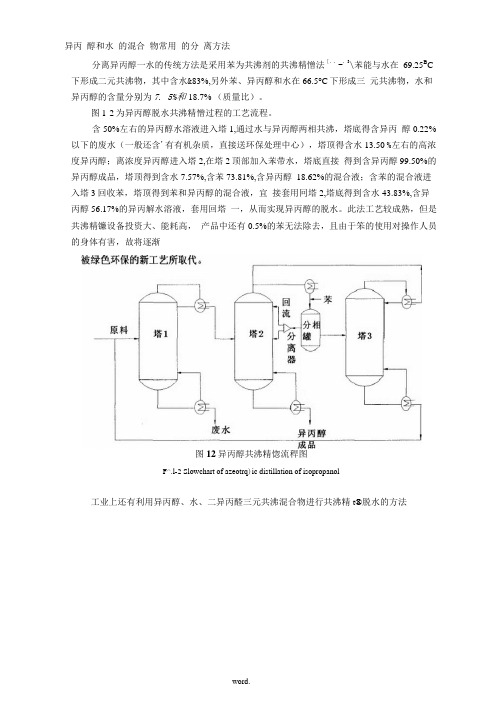
异丙醇和水的混合物常用的分离方法分离异丙醇一水的传统方法是采用苯为共沸剂的共沸精憎法[,,-,3\苯能与水在69.25B C 下形成二元共沸物,其中含水&83%,另外苯、异丙醇和水在66.5°C下形成三元共沸物,水和异丙醇的含量分别为7. 5%和18.7% (质量比)。
图1-2为异丙醇脱水共沸精憎过程的工艺流程。
含50%左右的异丙醇水溶液进入塔1,通过水与异丙醇两相共沸,塔底得含异丙醇0.22%以下的废水(一般还含'有有机杂质,直接送环保处理中心),塔顶得含水13.50 %左右的高浓度异丙醇;离浓度异丙醇进入塔2,在塔2顶部加入苯带水,塔底直接得到含异丙醇99.50%的异丙醇成品,塔顶得到含水7.57%,含苯73.81%,含异丙醇18.62%的混合液;含苯的混合液进入塔3回收苯,塔顶得到苯和异丙醇的混合液,宜接套用冋塔2,塔底得到含水43.83%,含异丙醇56.17%的异丙解水溶液,套用回塔一,从而实现异丙醇的脱水。
此法工艺较成熟,但是共沸精镰设备投资大、能耗高,产品中还有0.5%的苯无法除去,且由于笨的使用对操作人员的身体有害,故将逐渐图12异丙醇共沸精惚流稈图F^.l-2 Slowchart of azeotrq)ic distillation of isopropanol工业上还有利用异丙醇、水、二异丙醛三元共沸混合物进行共沸精t®脱水的方法,10\二异丙醛虽然無性较苯低,但易与空气形成过氧化物,有爆炸的危险,且带水壘比苯少,总体效果也不理想。
1.3.2吸附蒸tg工艺吸附分离技术^是20世纪60年代以后得到迅速发展的新分离技术,对于相对挥发度接近1・0的难分离物系,吸附技术在许多方面明显优于常规蒸蚀技术。
吸附蒸馅是将吸附和蒸懈相复合的分离过程,具有吸附过程分离因数高、蒸馆过程连续的优点, 适用于有共沸点物系的分离。
文献:⑷采用吸附蒸馆技术分离异丙醇-水混合物,该工艺流程如图卜3所示。
萃取精馏分离丙酮-正庚烷的模拟与优化
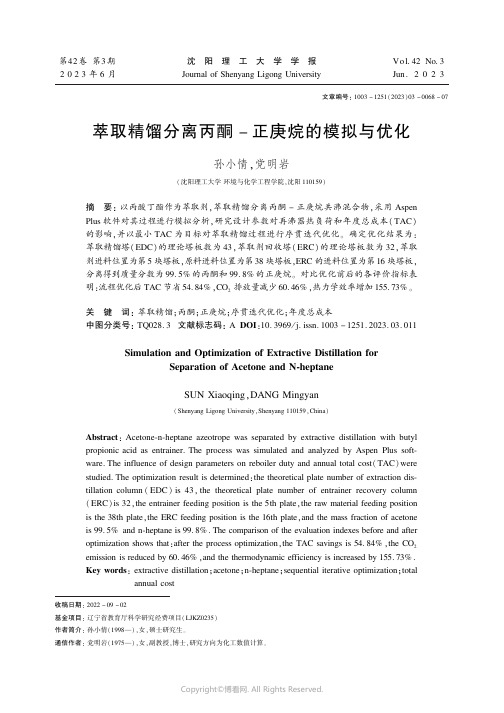
第42卷第3期2023年6月沈㊀阳㊀理㊀工㊀大㊀学㊀学㊀报JournalofShenyangLigongUniversityVol 42No 3Jun 2023收稿日期:2022-09-02基金项目:辽宁省教育厅科学研究经费项目(LJKZ0235)作者简介:孙小情(1998 )ꎬ女ꎬ硕士研究生ꎮ通信作者:党明岩(1975 )ꎬ女ꎬ副教授ꎬ博士ꎬ研究方向为化工数值计算ꎮ文章编号:1003-1251(2023)03-0068-07萃取精馏分离丙酮-正庚烷的模拟与优化孙小情ꎬ党明岩(沈阳理工大学环境与化学工程学院ꎬ沈阳110159)摘㊀要:以丙酸丁酯作为萃取剂ꎬ萃取精馏分离丙酮-正庚烷共沸混合物ꎬ采用AspenPlus软件对其过程进行模拟分析ꎬ研究设计参数对再沸器热负荷和年度总成本(TAC)的影响ꎬ并以最小TAC为目标对萃取精馏过程进行序贯迭代优化ꎮ确定优化结果为:萃取精馏塔(EDC)的理论塔板数为43ꎬ萃取剂回收塔(ERC)的理论塔板数为32ꎬ萃取剂进料位置为第5块塔板ꎬ原料进料位置为第38块塔板ꎬERC的进料位置为第16块塔板ꎬ分离得到质量分数为99.5%的丙酮和99.8%的正庚烷ꎮ对比优化前后的各评价指标表明:流程优化后TAC节省54.84%ꎬCO2排放量减少60.46%ꎬ热力学效率增加155.73%ꎮ关㊀键㊀词:萃取精馏ꎻ丙酮ꎻ正庚烷ꎻ序贯迭代优化ꎻ年度总成本中图分类号:TQ028.3文献标志码:ADOI:10.3969/j.issn.1003-1251.2023.03.011SimulationandOptimizationofExtractiveDistillationforSeparationofAcetoneandN ̄heptaneSUNXiaoqingꎬDANGMingyan(ShenyangLigongUniversityꎬShenyang110159ꎬChina)Abstract:Acetone ̄n ̄heptaneazeotropewasseparatedbyextractivedistillationwithbutylpropionicacidasentrainer.TheprocesswassimulatedandanalyzedbyAspenPlussoft ̄ware.Theinfluenceofdesignparametersonreboilerdutyandannualtotalcost(TAC)werestudied.Theoptimizationresultisdetermined:thetheoreticalplatenumberofextractiondis ̄tillationcolumn(EDC)is43ꎬthetheoreticalplatenumberofentrainerrecoverycolumn(ERC)is32ꎬtheentrainerfeedingpositionisthe5thplateꎬtherawmaterialfeedingpositionisthe38thplateꎬtheERCfeedingpositionisthe16thplateꎬandthemassfractionofacetoneis99.5%andn ̄heptaneis99.8%.Thecomparisonoftheevaluationindexesbeforeandafteroptimizationshowsthat:aftertheprocessoptimizationꎬtheTACsavingsis54.84%ꎬtheCO2emissionisreducedby60.46%ꎬandthethermodynamicefficiencyisincreasedby155.73%.Keywords:extractivedistillationꎻacetoneꎻn ̄heptaneꎻsequentialiterativeoptimizationꎻtotalannualcost㊀㊀丙酮和正庚烷是化学工业中十分重要的有机溶剂ꎬ也是有机合成的基本化学品[1-2]ꎬ丙酮-正庚烷混合物存在于许多生产过程中ꎮ丙酮(沸点329.28K)和正庚烷(沸点371.55K)在常压下会形成共沸物ꎬ其共沸温度为328.96Kꎬ共沸组成(质量分数)为87.82%丙酮和12.18%正庚烷ꎬ采用一般精馏方法分离得到高纯度丙酮和正庚烷非常困难ꎮ用于分离共沸物的常见方法有共沸精馏[3]㊁萃取精馏[4-5]和变压精馏[6-7]等ꎮ由于实验过程耗时较长ꎬ且成本较高ꎬ故一般在工艺设计时采用流程模拟软件对化工过程进行模拟优化ꎬ以确定适宜的操作条件或较优的设计参数ꎮWang等[8]采用AspenPlus软件模拟正庚烷-异丁醇共沸物的稳态萃取精馏过程ꎬ采用序贯迭代方法对其进行优化ꎬ并对最佳萃取精馏过程进行动态控制分析ꎮYuan等[9]利用AspenPlus模拟了丙酮-四氢呋喃㊁正己烷-四氢呋喃㊁正己烷-乙酸乙酯和乙酸乙酯-乙醇等二元共沸混合物的萃取精馏分离过程ꎬ并通过实验证明了该技术分离共沸混合物的可行性ꎮQi等[5]通过萃取精馏㊁共沸精馏及变压精馏三种特殊精馏方法分离乙腈-水共沸物ꎬ并以年度总成本(TotalAnnualCostꎬTAC)为目标函数ꎬ采用AspenPlus流程模拟软件对分离过程进行序贯迭代优化ꎬ确定了最优的设计参数ꎮ安永胜等[10]采用AspenPlus对甲醇-丁酮萃取精馏过程进行序贯迭代优化ꎬ确定了最佳的工艺流程及适宜的工艺参数ꎮ本文以丙酸丁酯为萃取剂ꎬ利用AspenPlus流程模拟软件对丙酮-正庚烷共沸物系的萃取精馏分离过程进行稳态模拟ꎮ以TAC为目标函数ꎬ对流程的各设计参数进行序贯迭代优化ꎬ并针对优化前后的流程进行TAC㊁CO2排放量和热力学效率三个指标的对比分析ꎮ1㊀稳态模型的建立1.1㊀萃取剂的选择萃取精馏是通过向原料中加入第三组分(称为萃取剂或溶剂)ꎬ改变原有组分间相对挥发度而实现分离的操作ꎮ萃取剂的选择原则主要有:与原溶液中的溶剂互不相溶ꎻ对溶质的溶解度远大于原溶剂ꎻ不易挥发ꎮ文献[11]采用丙酸丁酯作为萃取剂ꎬ通过萃取精馏实验分离丙酮-正庚烷二元共沸混合物ꎬ取得了较好的分离效果ꎮ丙酮-正庚烷-丙酸丁酯的三元剩余曲线如图1所示ꎬ图中A㊁B㊁S分别代表丙酮㊁正庚烷㊁丙酸丁酯ꎬwA㊁wB㊁wS分别表示丙酮㊁正庚烷㊁丙酸丁酯的质量分数ꎮ图1㊀常压下丙酮-正庚烷-丙酸丁酯的三元剩余曲线图㊀㊀由图1可见ꎬ等挥发性曲线在代表丙酮-正庚烷二元混合物的直线上汇于一点ꎬ即共沸点ꎬ该点为不稳定节点ꎬ而代表纯丙酮㊁正庚烷和丙酸丁酯的各顶点为稳定节点ꎬ说明丙酮-正庚烷的共沸物与纯丙酮㊁正庚烷㊁丙酸丁酯不能同时得到ꎮ此外ꎬ图1中不存在精馏边界线ꎬ说明丙酸丁酯能够分离丙酮-正庚烷共沸混合物ꎮ丙酸丁酯沸点为418.08Kꎬ远高于丙酮和正庚烷的沸点ꎬ其挥发度小ꎬ同时具有较低的蒸汽压㊁良好的混合能力㊁高电阻和气味较轻等优点ꎬ被认为是绿色环保的溶剂ꎮ故本文选择丙酸丁酯作为萃取剂ꎮ1.2㊀分离要求原料流量为100kmol/hꎬ其中丙酮和正庚烷的含量(物质的量分数)均为50%ꎬ产品纯度(质量分数)要求为99.5%以上ꎮ为保证产品的回收率ꎬ两种产品馏出物的流量均设置为50kmol/hꎮ1.3㊀物性方法的选择为使模拟结果准确可靠ꎬ需要选择适宜的描述汽液平衡状态的热力学方法ꎮ文献[12]的研究表明ꎬUNIQUAC物性方法可以很好地预测丙酮-正庚烷-丙酸丁酯体系的汽液平衡关系ꎬ故96第3期㊀㊀㊀孙小情等:萃取精馏分离丙酮-正庚烷的模拟与优化本文采用UNIQUAC物性方法ꎮ表1列出了由AspenPlus物性数据库给出的UNIQUAC模型二元交互作用参数ꎮ表1㊀UNIQUAC模型二元交互作用参数组分i丙酮丙酮正庚烷组分j正庚烷丙酸丁酯丙酸丁酯aij012.554723.4640aji0-7.9191-7.0087bij/K39.0511-1645.91-2713.31bji/K-280.3772390.132498.761.4㊀流程搭建搭建丙酮-正庚烷萃取精馏流程如图2所示ꎮ萃取精馏流程由一个萃取精馏塔(ExtractiveDistillationColumnꎬEDC)和一个萃取剂回收塔(EntrainerRecoveryColumnꎬERC)组成ꎮ丙酸丁酯由EDC塔上部进入ꎬ原料由EDC塔中下部进入ꎬEDC塔顶得到符合产品纯度要求的丙酮ꎬ含有丙酸丁酯和正庚烷的混合物由EDC塔底馏出后进入ERC塔ꎻERC塔顶馏出符合纯度要求的正庚烷产物ꎬ丙酸丁酯在ERC塔塔底回收后循环使用ꎬ与补充的丙酸丁酯混合后进入EDC塔顶部ꎮ图中F1代表EDC塔进料ꎻxA和xB表示原料中丙酮和正庚烷的物质的量分数ꎻD1和D2分别代表EDC和ERC的塔顶出料ꎬ即两种产品的馏出液ꎮ图2㊀萃取精馏流程图2㊀设计参数的优化设计参数的优化是通过调整各精馏塔的理论塔板数㊁进料位置㊁萃取剂的流量等方式降低再沸器热负荷及整个流程的TACꎬ优化过程中通过调整回流比保证目标产物丙酮和正庚烷的收率及纯度要求ꎮ2.1㊀优化方法以最小TAC为目标ꎬ通过序贯迭代方法对萃取精馏的相关参数进行优化ꎮTAC主要包括操作费用和设备投资费用[13]ꎮ设备投资费用计算公式如表2所示[14]ꎬ表中D为精馏塔塔径ꎬmꎻL为精馏塔塔高ꎬmꎻA为换热器的换热面积ꎬm2ꎮ操作费用计算所需数据如表3所示ꎮ设备回收期设定为3年ꎬTAC即为每年的操作费用与折算的设备投资费用之和ꎮ表2㊀设备投资费用计算公式设备名称设备投资费用/美元精馏塔17640ˑD1.066ˑL0.802换热器7296ˑA0.65表3㊀操作费用计算所需数据项目数值冷却水单价/(美元 GJ-1)[15]0.354中压蒸汽(457.15K)单价/(美元 GJ-1)[15]8.220低压蒸汽(433.15K)单价/(美元 GJ-1)[15]7.780电费单价/(美元 kW-1 h-1)[16]0.084㊀㊀图3为萃取精馏序贯迭代优化程序ꎮ图中p1和p2分别为EDC和ERC的操作压力ꎻS1为丙酸丁酯的进料流量ꎬkmol/hꎻN1为EDC理论塔板数ꎻN2为ERC理论塔板数ꎻNF1为原料进料位置ꎻNS为萃取剂进料位置ꎻNF2为ERC的进料位置ꎻRR1和RR2分别为EDC和ERC的操作回流比ꎻQreb1和Qreb2分别为EDC和ERC的再沸器热负荷ꎮ本文中p1和p2均设置为1atmꎮ稳态模拟优化的初始参数设置为:N1=35ꎬN2=29ꎬNS=5ꎬNF1=33ꎬNF2=22ꎮ2.2㊀优化过程分析2.2.1㊀萃取剂流量增大萃取剂的用量虽然能够提高产品的纯度ꎬ但同时增加了EDC塔底再沸器的热负荷ꎮ在不同的萃取剂流量下ꎬ通过改变NS㊁NF1和N1ꎬ考察Qreb1和TAC的变化ꎬ以最小TAC为目标ꎬ确定各流量下最优的NS㊁NF1和N1ꎮ模拟得到TAC及Qreb1随S1的变化如图4所示ꎮ07沈㊀阳㊀理㊀工㊀大㊀学㊀学㊀报㊀㊀第42卷图3㊀萃取精馏序贯迭代优化程序图4㊀TAC及Qreb1与S1的关系㊀㊀由图4可见ꎬ随着S1的增加ꎬ进入再沸器的物料流量也随之增加ꎬQreb1提高ꎬTAC增加ꎮ模拟中发现ꎬ当S1为40kmol/h时ꎬ在给定操作条件下丙酮-正庚烷萃取精馏无法达到分离要求ꎬ当S1为50kmol/h时ꎬ可分离得到符合要求的丙酮和正庚烷产品ꎬ且TAC值最小ꎬ故确定萃取剂的最佳流量为50kmol/hꎮ2.2.2㊀EDC设计参数选择S1为50kmol/hꎬ对EDC的理论板数㊁进料位置等进行优化ꎮ给定不同的N1ꎬ通过调整NS和NF1ꎬ确定满足最小TAC的最优设计参数ꎮ模拟得到TAC和Qreb1随N1的变化如图5(a)所示ꎮ由图5(a)可见ꎬ随着N1的增加ꎬQreb1降低ꎬ操作费用下降ꎬ但同时N1增加会引起设备投资费用的提高ꎬ故TAC随着N1的增加呈先降低后升高的趋势ꎮ当N1较小时ꎬ操作费用的降低远大于设备投资费用的增加ꎬTAC明显减小ꎬ当N1为43时ꎬTAC的值最小ꎬ故EDC的最优理论塔板数为43ꎮ在N1为43时ꎬ模拟得到Qreb1随NS的变化如图5(b)所示ꎮ由图5(b)可见ꎬ随着NS的增加ꎬQreb1先减小后增大ꎬ当NS为5时ꎬQreb1的值最小ꎮ在N1为43㊁NS为5时ꎬ模拟得到Qreb1随NF1的变化如图5(c)所示ꎮ由图5(c)可见ꎬ随着NF1的增加ꎬQreb1先减小后增大ꎬ当NF1为38时ꎬQreb1值最小ꎬ为1433.79kWꎮ故萃取剂的最佳进料位置为第5块塔板ꎬ原料的最佳进料位置为第38块塔板ꎮ17第3期㊀㊀㊀孙小情等:萃取精馏分离丙酮-正庚烷的模拟与优化图5㊀EDC设计参数优化结果2.2.3㊀ERC设计参数保持2.2.1和2.2.2中的最优设计参数ꎬ给定不同的N2ꎬ通过调整NF2ꎬ确定满足最小TAC的最优设计参数ꎮ模拟得到TAC和Qreb2随N2的变化如图6(a)所示ꎮ由图6(a)可见ꎬ随着N2的增加ꎬQreb2减小ꎬTAC先减小后稍有增加ꎮ虽然N2增加会引起设备投资费用提高ꎬ但当操作费用的降低图6㊀ERC设计参数优化结果远大于设备投资费用的增加时ꎬTAC显著降低ꎬ当N2为32时ꎬTAC的值最小ꎬ故EDC的最优理论塔板数为32ꎮ在N2为32时ꎬ模拟得到Qreb2随NF2的变化如图6(b)所示ꎮ由图6(b)可见ꎬ随着NF2的增加ꎬQreb2先减小后增加ꎬ当NF2为16时ꎬQreb2的值最小ꎬ为900.65kWꎮ故ERC的最佳进料位置为第16块塔板ꎮ2.3㊀优化结果以最小TAC为优化目标ꎬ通过序贯迭代优化程序得到以丙酸丁酯为萃取剂分离丙酮-正庚烷共沸物的最优流程如图7所示ꎮ在最优设计参数下可分离得到质量分数为99.5%的丙酮和99.8%的正庚烷ꎬ同时回收丙酸丁酯的纯度也达到了99.99%ꎮ图7㊀萃取精馏优化流程图3㊀优化前后对比3.1㊀优化参数的对比表4为萃取精馏流程优化前后的主要设计参数比较ꎮ由表4可以看出ꎬ与未优化的萃取精馏相比ꎬ优化后萃取剂的流量下降ꎬ理论塔板数增多ꎬ通过操作费用的大幅降低抵消设备投资费用的提高ꎬ达到TAC最小的目标ꎮ表4㊀萃取精馏流程优化前后的参数对比流程S1/(kmol h-1)NSNF1N1NF2N2优化前80533352229优化后505384316323.2㊀评价指标的对比对于一个工艺过程ꎬ除要考虑其经济指标外ꎬ也要考虑其环境效益ꎮ本文采用CO2排放量评27沈㊀阳㊀理㊀工㊀大㊀学㊀学㊀报㊀㊀第42卷估萃取精馏过程的环境效益ꎬCO2主要源于加热炉和气体涡轮机等ꎬ这些公用工程装置用来提供蒸汽和动力等ꎬ耗能较大ꎬ是炼化行业节能减排的重点单元[17-18]ꎮ此外ꎬ为评价萃取精馏系统有效能利用情况ꎬ对比优化前后两个过程的能源经济性ꎬ引入热力学效率指标ꎮCO2排放量计算式为[19]GCO2=QfuelNHVæèçöø÷ˑwC100æèçöø÷ˑα(1)式中:GCO2为CO2排放量ꎬkg/hꎻQfuel为燃料燃烧热ꎬkWꎻNHV为净热值ꎬkJ/kgꎻwC为燃料中碳元素的质量分数ꎬ%ꎻα为CO2与C的相对分子质量比ꎮQfuel的计算式为Qfuel=Qprocλprocˑ(hproc-419)ˑTFTB-T0TFTB-Tstack(2)式中:Qproc为再沸器热负荷ꎬkWꎻλproc为蒸汽潜热ꎬkJ/kgꎻhproc为蒸汽的焓ꎬkJ/kgꎻTFTB和Tstack分别为锅炉火焰温度和烟囱温度ꎬKꎻT0为环境温度ꎬKꎮ热力学效率计算式为[20]η=WminEx(3)式中:η为热力学效率ꎻWmin为最小分离功ꎬkWꎻEx为有效能ꎬkWꎮWmin和Ex的计算参见文献[20]ꎮ计算所需各数值均引自文献[19-20]ꎮ流程优化前后的各指标如表5所示ꎮ由于优化后再沸器和冷凝器负荷均显著下降ꎬ使得CO2排放量明显降低ꎬ同时热力学效率显著升高ꎮ对比优化前的流程ꎬ优化后的萃取精馏流程TAC节省54.84%ꎬCO2排放量减少约60.46%ꎬ热力学效率增加155.73%ꎮ表5㊀优化前后各指标对比参数优化前优化后塔费用/103美元782.05537.63再沸器费用/103美元346.76180.82冷凝器费用/103美元303.71153.93冷却器费用/103美元48.3135.59设备投资费用/103美元1480.83907.97蒸汽费用/(103美元 a-1)1349.77534.52冷却水费用/(103美元 a-1)56.8520.95操作费用/(103美元 a-1)1406.62555.47TAC(回收期3年)/(103美元 a-1)1900.23858.13CO2排放量/(kg h-1)1419.68561.37热力学效率/%2.536.474㊀结论以丙酸丁酯为萃取剂ꎬ萃取精馏分离丙酮-正庚烷共沸物ꎬ使用AspenPlus流程模拟软件建立分离过程的稳态模型ꎬ以最小TAC为目标ꎬ采用序贯迭代方法对设计参数进行优化ꎮ1)确定优化参数为:EDC的理论塔板数为43ꎬERC的理论塔板数为32ꎻ萃取剂进料位置为第5块塔板ꎬ原料进料位置为第38块塔板ꎬERC的进料位置为第16块塔板ꎮ分离得到质量分数为99.5%的丙酮和99.8%的正庚烷ꎮ2)通过TAC㊁CO2排放量和热力学效率三个指标对优化前后流程进行对比ꎬ结果显示ꎬ萃取精馏流程优化后的TAC节省54.84%ꎬCO2排放量减少约60.46%ꎬ热力学效率增加155.73%ꎮ参考文献:[1]BERJEJꎬSCHEDEMANNAꎬGMEHLINGJ.Liquiddensitiesofacetoneandn ̄heptaneandexcessvolumesofthebinarysysteminawidetemperatureandpres ̄surerange[J].FluidPhaseEquilibriaꎬ2011ꎬ300(1/2):110-115.[2]DRUECKHAMMERDGꎬGAOSQꎬLIANGXFꎬetal.Acetone ̄heptaneasasolventsystemforcombiningchromatographyonsilicagelwithsolventrecycling[J].ACSSustainableChemistry&Engineeringꎬ2012ꎬ1(1):87-90.[3]郑世富ꎬ黄佩佩ꎬ邹亮.Aspen模拟乙醇-水体系的共沸精馏[J].浙江化工ꎬ2021ꎬ52(4):30-32.[4]ZHAOLꎬLYUXYꎬWANGWCꎬetal.Comparisonofheterogeneousazeotropicdistillationandextractivedistillationmethodsforternaryazeotropeethanol/tolu ̄ene/waterseparation[J].Computers&ChemicalEngi ̄neeringꎬ2017ꎬ100:27-37.[5]QIJꎬLIYFꎬXUEJXꎬetal.Comparisonofheteroge ̄neousazeotropicdistillationandenergy ̄savingextrac ̄tivedistillationforseparatingtheacetonitrile ̄watermixtures[J].SeparationandPurificationTechnologyꎬ2020ꎬ238:116487.[6]GUANGCꎬSHIXJꎬZHANGZSꎬetal.Comparisonofheterogeneousazeotropicandpressure ̄swingdistil ̄37第3期㊀㊀㊀孙小情等:萃取精馏分离丙酮-正庚烷的模拟与优化lationsforseparatingthediisopropylether/isopropanol/watermixtures[J].ChemicalEngineeringResearchandDesignꎬ2019ꎬ143:249-260.[7]孔鹏ꎬ高瑞昶.变压精馏分离甲醇-丙酮的工艺模拟及优化[J].化工进展ꎬ2013ꎬ32(11):2583-2587. [8]WANGYLꎬLIANGSSꎬBUGLꎬetal.Effectofsol ̄ventflowratesoncontrollabilityofextractivedistil ̄lationforseparatingbinaryazeotropicmixture[J].In ̄dustrial&EngineeringChemistryResearchꎬ2015ꎬ54(51):12908-12919.[9]YUANSFꎬZOUCCꎬYINHꎬetal.Studyonthesep ̄arationofbinaryazeotropicmixturesbycontinuousex ̄tractivedistillation[J].ChemicalEngineeringResearchandDesignꎬ2015ꎬ93:113-119.[10]安永胜ꎬ谢小强ꎬ胡南ꎬ等.甲醇-丁酮共沸物萃取精馏的模拟与优化[J].北京化工大学学报(自然科学版)ꎬ2021ꎬ48(5):11-16.[11]ZHANGTꎬLIAꎬXUXꎬetal.Separationofazeotropicmixture(acetone+n ̄heptane)byextractivedistillationwithintermediateandheavyboilingentrainers:vapour ̄liquidequilibriummeasurementsandcorrelation[J].TheJournalofChemicalThermodynamicsꎬ2021ꎬ152:106284.[12]MAHSAKꎬMAJIDAS.Thedesignandoptimizationofextractivedistillationforseparatingtheacetone/n ̄heptanebinaryazeotropemixture[J].ACSOmegaꎬ2021ꎬ6(34):22447-22453.[13]LUYBENWL.Comparisonofextractivedistillationandpressure ̄swingdistillationforacetone/chloroformseparation[J].Computers&ChemicalEngineeringꎬ2013ꎬ50:1-7.[14]LUYBENWL.Comparisonofextractivedistillationandpressure ̄swingdistillationforacetone ̄methanolseparation[J].Industrial&EngineeringChemistryRe ̄searchꎬ2008ꎬ47(8):2696-2707.[15]ZHANGYRꎬWUTWꎬCHIENIL.Energy ̄efficientheterogeneousazeotropicdistillationcouplingwithpressureswingdistillationfortheseparationofIPA/DIPE/watermixture[J].JournaloftheTaiwanInstitu ̄teofChemicalEngineersꎬ2022ꎬ130:103843. [16]WANGCꎬZHUANGYꎬLIULLꎬetal.Heatpumpas ̄sistedextractivedistillationsequenceswithintermedi ̄ate ̄boilingentrainer[J].AppliedThermalEngineer ̄ingꎬ2021ꎬ186:116511.[17]YOUXQꎬRODRIGUEZ ̄DONISIꎬGERBAUDV.ReducingprocesscostandCO2emissionsforextrac ̄tivedistillationbydouble ̄effectheatintegrationandmechanicalheatpump[J].AppliedEnergyꎬ2016ꎬ166:128-140.[18]GADALLAMꎬOLUJIC'ŽꎬDERIJKEAꎬetal.Reduc ̄ingCO2emissionsofinternallyheat ̄integrateddistil ̄lationcolumnsforseparationofcloseboilingmixtures[J].Energyꎬ2006ꎬ31(13):2409-2417.[19]DIPRETOROAꎬCIRANNAFꎬFEDELIMꎬetal.Afeasiblepath ̄basedapproachfordividingwallcolumndesignprocedure[J].Computers&ChemicalEngi ̄neeringꎬ2021ꎬ149:107309.[20]LIUYLꎬZHAIJꎬLILMꎬetal.Heatpumpassistedreactiveandazeotropicdistillationsindividingwallcolumns[J].ChemicalEngineeringandProcessing:ProcessIntensificationꎬ2015ꎬ95:289-301.(责任编辑:李继龙ꎬ宋颖韬)47沈㊀阳㊀理㊀工㊀大㊀学㊀学㊀报㊀㊀第42卷。
碳酸二甲酯_甲醇二元共沸物的分离方法2

碳酸二甲酯-甲醇二元共沸物的分离方法李光兴,熊国玺(华中科技大学化学系,湖北武汉430074)摘 要:论述了分离碳酸二甲酯-甲醇二元共沸物的各种方法,重点介绍了萃取精馏法,并对萃取剂的选择作了较为详细的报道。
关键词:萃取精馏;碳酸二甲酯;甲醇;共沸物;分离方法中图分类号:TQ225152 TQ028 文献标识码:A 文章编号:1004-0404(2000)05-0004-031 前言碳酸二甲酯(dimethyl carbonate,简称DMC)是近十年来国内外化工界广泛关注的一种新型绿色化工产品[15],可利用它来进行羰基化、羰基甲氧基化和甲基化反应,用以取代传统中广泛使用的剧毒性光气、氯甲酸甲酯以及硫酸二甲酯[610]。
我们在获得甲醇液相氧化羰基化法合成DMC150t/a工业实验成功的基础上[1113],正在对合成工艺作进一步的研究。
各种合成方法得到的粗产品均为DMC-MeOH共沸混合物[14],普通的分离方法难以达到分离产品的要求,而DMC的分离直接影响着整个工厂的经济效益,因此对DMC-MeOH共沸物分离方法的研究尤为重要。
2 DMC-MeOH二元共沸体系在甲醇液相氧化羰基化法合成DMC工艺中,反应体系包括气相(O2、CO和少量副产物CO2)、液相(DMC、MeOH和H2O)和固相。
气相除一部分循环到反应体系中进行反应外,其余可以放空,固相可通过离心或过滤法与液相分开,分离出来的催化剂(固相)经处理后加入到反应体系中继续使用。
从反应器流出的粗产品为DMC、MeOH、H2O三元混合物,经脱水塔处理后变为DMC-MeOH二元共沸物。
在酯交换法生产工艺中,从反应器常压蒸馏出的粗产品也为DMC-MeOH二元共沸物,常压下共沸温度为64℃,ω(DMC)为30%,ω(MeOH)为70%[15,16]。
3 DMC-MeOH共沸物的分离方法[17]311 低温结晶法低温结晶法[18]是利用DMC的凝固点(4℃)比甲醇的凝固点(-9718℃)高的特点,选择适宜的温度使DMC凝固结晶,分离结晶后再蒸馏获得DMC,DMC 的回收率可达95%96%。
共沸混合物
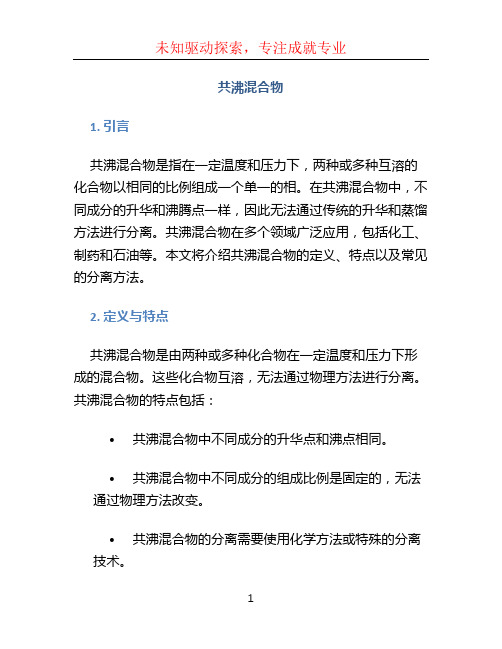
共沸混合物1. 引言共沸混合物是指在一定温度和压力下,两种或多种互溶的化合物以相同的比例组成一个单一的相。
在共沸混合物中,不同成分的升华和沸腾点一样,因此无法通过传统的升华和蒸馏方法进行分离。
共沸混合物在多个领域广泛应用,包括化工、制药和石油等。
本文将介绍共沸混合物的定义、特点以及常见的分离方法。
2. 定义与特点共沸混合物是由两种或多种化合物在一定温度和压力下形成的混合物。
这些化合物互溶,无法通过物理方法进行分离。
共沸混合物的特点包括:•共沸混合物中不同成分的升华点和沸点相同。
•共沸混合物中不同成分的组成比例是固定的,无法通过物理方法改变。
•共沸混合物的分离需要使用化学方法或特殊的分离技术。
3. 常见的分离方法3.1 蒸馏法蒸馏法是一种常见的分离共沸混合物的方法。
蒸馏法基于不同成分的沸点差异,通过控制温度和压力的变化,使其中一个成分先沸腾,然后将其收集。
这样可以将共沸混合物中的成分分离出来。
但是,对于沸点相同的共沸混合物,蒸馏法无法进行有效分离。
3.2 结晶法结晶法是另一种常见的分离共沸混合物的方法。
通过控制温度和溶解度的变化,可以使其中一个成分结晶形成固态,然后将其收集。
结晶法可以对沸点相同的共沸混合物进行有效分离。
3.3 萃取法萃取法是利用溶剂的选择性溶解性质来分离共沸混合物的方法。
通过将共沸混合物与适当的溶剂接触,使其中一个成分被溶解在溶剂中,而另一个成分则不能溶解。
然后可以通过分离溶剂和溶剂中溶解的成分,实现共沸混合物的分离。
3.4 晶体衍射法晶体衍射法是一种通过测量共沸混合物的晶体结构来确定其分子组成的方法。
通过X射线衍射或电子衍射技术,可以得到共沸混合物的晶体结构信息,进而确定其成分的比例。
4. 应用案例共沸混合物在化工、制药和石油等领域有着广泛的应用。
以下是一些共沸混合物的应用案例:•石油炼制中的分离和提纯,如汽油的分离和净化。
•制药中的药物提纯和分离,如药物的制剂和副产物的分离。
有机实验思考题答案
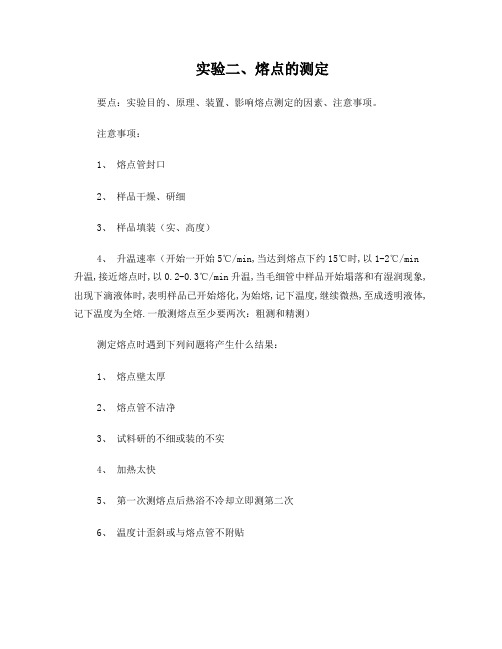
实验二、熔点的测定要点:实验目的、原理、装置、影响熔点测定的因素、注意事项。
注意事项:1、熔点管封口2、样品干燥、研细3、样品填装(实、高度)4、升温速率(开始一开始5℃/min,当达到熔点下约15℃时,以1-2℃/min 升温,接近熔点时,以0.2-0.3℃/min升温,当毛细管中样品开始塌落和有湿润现象,出现下滴液体时,表明样品已开始熔化,为始熔,记下温度,继续微热,至成透明液体,记下温度为全熔.一般测熔点至少要两次:粗测和精测)测定熔点时遇到下列问题将产生什么结果:1、熔点壁太厚2、熔点管不洁净3、试料研的不细或装的不实4、加热太快5、第一次测熔点后热浴不冷却立即测第二次6、温度计歪斜或与熔点管不附贴7、测A、B两种样品的熔点相同,将它们研细并以等量混合(1)测得混合物的熔点有下降现象且熔程增宽;(2)混合物的熔点与原子A、B物质的熔点相同。
试分析以上情况合说明什么1、熔点壁厚,影响传热,测得的初熔温度偏高2、熔点管不洁净,相当于样品中掺入杂质,导致测得的熔点偏低3、这样试料颗粒间空隙较大,其空隙间为空气所占据,而空气的导热系数较小,结果导致测得的熔距加大,测得熔点数值偏高。
4、加热太快,则热浴体温度大于热量转移到待测体中的转移能力,而导致测得熔点偏高,熔距加大。
5、连续测几次熔点时,第一次完成后需将热浴冷却原熔点温度的二分之一以下,才可测第二次,不冷却马上测第二次导致测得熔点偏高。
6、熔点测定的缺点就是温度分布不均匀,若温度计歪斜或熔点管与温度计不附贴,这样所测得的数值会产生不同程度偏差。
7、(1)A、B为两种不同的物质,一种物质在此充当另一种物质的杂质,故混合物的熔点降低,熔程增宽。
(2)降少数情况(如形成固熔体)外,一般可认为这两种是同一种物质。
实验三、蒸馏及沸点的测定实验目的、原理、仪器安装(从左到右,从下到上,竖直横平,水银球的位置,冷凝管)、注意事项1、温度计水银球位置2、冷凝管循环水下进上出,让管充满水3、蒸馏瓶中液体的量4、升温速率(先水火加热,使爱热均匀,再调大,当有液体滴出时,控制馏出液的速率1~2滴/秒。
变压精馏分离共沸物流程图
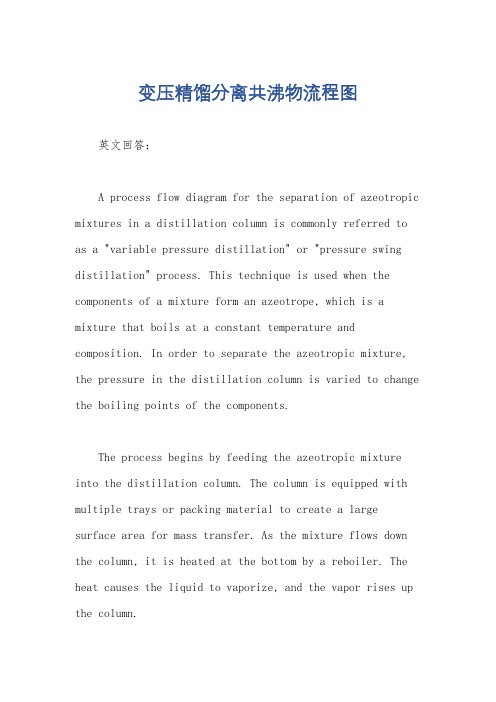
变压精馏分离共沸物流程图英文回答:A process flow diagram for the separation of azeotropic mixtures in a distillation column is commonly referred to as a "variable pressure distillation" or "pressure swing distillation" process. This technique is used when the components of a mixture form an azeotrope, which is a mixture that boils at a constant temperature and composition. In order to separate the azeotropic mixture, the pressure in the distillation column is varied to change the boiling points of the components.The process begins by feeding the azeotropic mixture into the distillation column. The column is equipped with multiple trays or packing material to create a large surface area for mass transfer. As the mixture flows down the column, it is heated at the bottom by a reboiler. The heat causes the liquid to vaporize, and the vapor rises up the column.As the vapor rises, it encounters cooler conditions near the top of the column. This causes the vapor to condense, and the liquid collects on the trays or packing material. The condensed liquid is referred to as the "reflux," and it flows back down the column. The reflux helps to provide additional separation between the components of the azeotropic mixture.In order to achieve separation, the pressure in the column is varied. This can be done by adjusting the pressure of the condenser or by using a pressure swing system. By changing the pressure, the boiling points of the components are altered, allowing for selective vaporization and condensation. The component with the lower boiling point will vaporize more readily at lower pressures, while the component with the higher boiling point will condense more readily at higher pressures.The vapor that is collected at the top of the column is referred to as the "overhead product." This product is enriched in the component with the lower boiling point.Conversely, the liquid that collects at the bottom of the column is referred to as the "bottoms product," and it is enriched in the component with the higher boiling point.The overhead product and the bottoms product can thenbe further processed or purified as desired. For example,the overhead product may be condensed and collected as a liquid, while the bottoms product may be further distilledto separate any remaining impurities.中文回答:变压精馏分离共沸物的流程图通常被称为“变压精馏”或“压力摇摆精馏”流程。
甲苯萃取精馏分离甲醇与碳酸二甲酯共沸物

收稿日期:2005204223;作者简介:张立庆(19622),男,教授,电邮lqzhang @hzcnc 1com ;基金来源:浙江省教育厅重点科研计划项目(编号20030836),浙江省自然科学基金项目(编号Y 404082),浙江省高校中青年学科带头人资助项目。
甲苯萃取精馏分离甲醇与碳酸二甲酯共沸物1张立庆,钟毓菁,王松岳,赵立明(浙江科技学院生物与化学工程学系,杭州 310012)摘要:根据萃取精馏原理,采用正交试验设计,运用计算机对实验数据进行最优化处理,确定了萃取精馏分离甲醇与碳酸二甲酯二元共沸物的最佳工艺条件:以甲苯为萃取剂,单圈为填料,回流比为5:1,滴加速率为5:1,萃取剂配比为2:1,以上述工艺条件,进行DMC 2甲醇分离,所得的碳酸二甲酯纯度为99199%。
关键词:碳酸二甲酯;甲醇;共沸物;萃取精馏中图分类号:TQ 02811 文献标识码:B 文章编号:100129219(2005)042512030 前言碳酸二甲酯(DMC ),是近几年来国内外化工界广泛关注的一种重要的新型绿色化工产品,DMC 的开发研究正日益受到人们的重视。
合成DMC 主要有4种方法,其中气相甲醇氧化羰基化法,因其原料易得,工艺简单,反应物和产物的毒性与腐蚀性均较小,是目前非常有发展潜力的DMC 合成方法。
但由于使用了过量的甲醇,在合成过程中形成了DMC 与甲醇的共沸物(其组成质量比为30∶70),而给分离造成了一定的困难。
如何高效、经济地分离得到DMC ,一直受到人们广泛地重视。
本文根据萃取精馏原理,采用正交试验设计,运用计算机对实验数据进行最优化处理,确定了萃取精馏分离甲醇与DMC 二元共沸物的最佳工艺条件。
1 实验部分111 实验方案的选择采用甲醇氧化羰基化法合成DMC 时,由于甲醇和DMC 形成共沸物,通过普通蒸馏不能分离提纯产品,为此,通常都采用两步分离,第一步为初馏阶段,在填料塔内蒸馏获得(CH 3OH 2DMC )共沸物,并将其副产物分离除去,CH 3OH 2DMC 共沸物的质量组成为70%CH 3OH 和30%DMC ,共沸温度为63℃;第二步为精制阶段,采用有效的分离方法获得DMC 。
化工分离过程(第13讲)(3.3.2共沸精馏)

(3-70)
式(3-70)即为塔Ⅰ精馏段的操作线,它与对角线的 交点是:x=xw2,斜率是L1/V1。
讨论:
(3-70)式是一条直线; (3-70)式代表塔Ⅰ内各板相遇物流之间关系; (3-70)式代表塔顶层板气相与回流液之间关系。
17
3.3.2.4 二元非均相共沸物的精馏
0.0138V最小 0.01L最小 0.9999W2 0.01(V最小 W2 ) 0.9999W2 0.01V最小 0.9899W2
故
V最小
0.9899W2 260W2 260 0.0038
24
(注:0.0138是与进料组成xF=0.01成平衡的汽相组成)
3.3.2.4 二元非均相共沸物的精馏
汽化潜热:乙醇为39020KJ/kmol,水为41532KJ/kmol
3
3.3.2.3 分离共沸物的双压精馏过程
乙醇水溶液共沸物与压力的关系表
系统压力,MPa 共沸组成,乙醇% 0.0093 100 0.0200 0.0533 96.2 91.4 共沸温度,℃ 27.79 42.00 62.80
0.1013 0.1933
Fzi W1 xW1,i W2 xW2 ,i
1.00 0.00001W1 0.9999W2
W1 W2 100
解得: W1 = 99.0, W2 = 1.0
22
3.3.2.4 二元非均相共沸物的精馏
确定Ⅰ塔的操作线: a 、精馏段操作线 由第n板与n+1板之间到Ⅱ塔一起作物 料衡算,得:
Vn Ln 1 W2
Vyn Lxn 1 0.9999W2
b 、提馏段操作线为: (A)
共沸物的分离方法
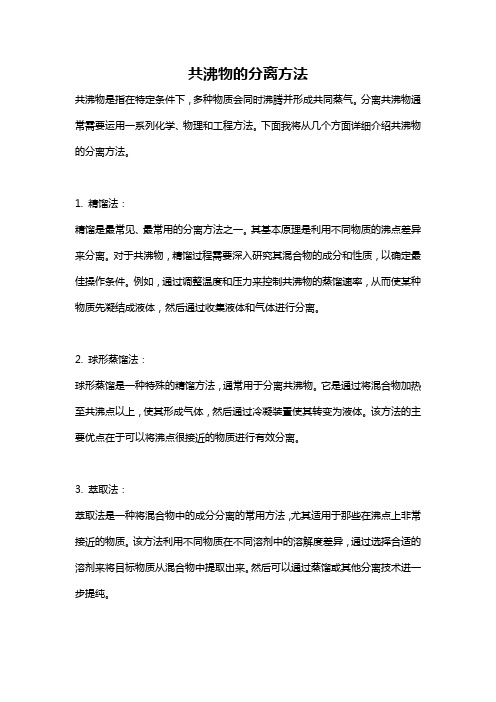
共沸物的分离方法共沸物是指在特定条件下,多种物质会同时沸腾并形成共同蒸气。
分离共沸物通常需要运用一系列化学、物理和工程方法。
下面我将从几个方面详细介绍共沸物的分离方法。
1. 精馏法:精馏是最常见、最常用的分离方法之一。
其基本原理是利用不同物质的沸点差异来分离。
对于共沸物,精馏过程需要深入研究其混合物的成分和性质,以确定最佳操作条件。
例如,通过调整温度和压力来控制共沸物的蒸馏速率,从而使某种物质先凝结成液体,然后通过收集液体和气体进行分离。
2. 球形蒸馏法:球形蒸馏是一种特殊的精馏方法,通常用于分离共沸物。
它是通过将混合物加热至共沸点以上,使其形成气体,然后通过冷凝装置使其转变为液体。
该方法的主要优点在于可以将沸点很接近的物质进行有效分离。
3. 萃取法:萃取法是一种将混合物中的成分分离的常用方法,尤其适用于那些在沸点上非常接近的物质。
该方法利用不同物质在不同溶剂中的溶解度差异,通过选择合适的溶剂来将目标物质从混合物中提取出来。
然后可以通过蒸馏或其他分离技术进一步提纯。
4. 溶剂转移法:溶剂转移法是一种利用混合物中各成分在不同溶剂中的溶解度差异将其分离的方法。
该方法通常用于具有很接近沸点的溶剂和共沸物的分离。
首先,在混合物中加入一个合适的溶剂,使其溶解相应的目标物质,然后通过蒸发或其他方法从溶液中分离出目标物质。
5. 晶体化学法:晶体化学法是一种通过溶解共沸物混合物,并通过晶体的结构特点来筛选出目标物质的方法。
该方法通常需要对混合物的组分和晶体特性进行详细研究和分析。
根据目标物质的晶体结构和溶解度等因素,通过适当的溶剂和溶液浓度来选择合适的条件,从混合物中分离出目标物质的晶体。
以上只是共沸物分离的一些常用方法,实际情况还需综合考虑共沸物的具体性质和需求。
在真实的实际应用中,有时需要结合使用多种方法来实现共沸物的高效分离。
此外,一些高级技术,如高效液相色谱、气相色谱和超临界流体萃取等,也可以在特定情况下用于分离共沸物。
- 1、下载文档前请自行甄别文档内容的完整性,平台不提供额外的编辑、内容补充、找答案等附加服务。
- 2、"仅部分预览"的文档,不可在线预览部分如存在完整性等问题,可反馈申请退款(可完整预览的文档不适用该条件!)。
- 3、如文档侵犯您的权益,请联系客服反馈,我们会尽快为您处理(人工客服工作时间:9:00-18:30)。
矿产资源开发利用方案编写内容要求及审查大纲
矿产资源开发利用方案编写内容要求及《矿产资源开发利用方案》审查大纲一、概述
㈠矿区位置、隶属关系和企业性质。
如为改扩建矿山, 应说明矿山现状、
特点及存在的主要问题。
㈡编制依据
(1简述项目前期工作进展情况及与有关方面对项目的意向性协议情况。
(2 列出开发利用方案编制所依据的主要基础性资料的名称。
如经储量管理部门认定的矿区地质勘探报告、选矿试验报告、加工利用试验报告、工程地质初评资料、矿区水文资料和供水资料等。
对改、扩建矿山应有生产实际资料, 如矿山总平面现状图、矿床开拓系统图、采场现状图和主要采选设备清单等。
二、矿产品需求现状和预测
㈠该矿产在国内需求情况和市场供应情况
1、矿产品现状及加工利用趋向。
2、国内近、远期的需求量及主要销向预测。
㈡产品价格分析
1、国内矿产品价格现状。
2、矿产品价格稳定性及变化趋势。
三、矿产资源概况
㈠矿区总体概况
1、矿区总体规划情况。
2、矿区矿产资源概况。
3、该设计与矿区总体开发的关系。
㈡该设计项目的资源概况
1、矿床地质及构造特征。
2、矿床开采技术条件及水文地质条件。