材料成形工艺原理9章
高分子材料成型加工(考试重点及部分习题答案)

高分子材料成型加工考试重点内容及部分习题答案第二章高分子材料学1、热固性塑料:未成型前受热软化,熔融可塑制成一定形状,在热或固化剂作用下,一次硬化成型。
受热不熔融,达到一定温度分解破坏,不能反复加工。
在溶剂中不溶。
化学结构是由线型分子变为体型结构。
举例:PF、UF、MF2、热塑性塑料:受热软化、熔融、塑制成一定形状,冷却后固化成型。
再次受热,仍可软化、熔融,反复多次加工。
在溶剂中可溶。
化学结构是线型高分子。
举例:PE聚乙烯,PP聚丙烯,PVC聚氯乙烯。
3、通用塑料:是指产量大、用途广、成型性好、价格便宜的塑料。
4、工程塑料:具有较好的力学性能,拉伸强度大于50MPa,冲击强度大于6kJ/m2,长期耐热温度超过100度的、刚性好、蠕变小、自润滑、电绝缘、耐腐蚀可作为结构材料。
举例:PA聚酰胺类、ABS、PET、PC5、缓冷:Tc=Tmax,结晶度提高,球晶大。
透明度不好,强度较大。
6、骤冷(淬火):Tc<Tg,大分子来不及重排,结晶少,易产生应力。
结晶度小,透明度好,韧性好。
定义:是指熔融状态或半熔融状态的结晶性聚合物,在该温度下保持一段时间后,快速冷却使其来不及结晶,以改善制品的冲击性能。
7、中速冷:Tc>=Tg,有利晶核生成和晶体长大,性能好。
透明度一般,结晶度一般,强度一般。
8、二次结晶:是指一次结晶后,在一些残留的非晶区和结晶不完整的部分区域内,继续结晶并逐步完善的过程。
9、后结晶:是指聚合物加工过程中一部分来不及结晶的区域,在成型后继续结晶的过程。
第三章添加剂1、添加剂的分类包括工艺性添加剂(如润滑剂)和功能性添加剂(除润滑剂之外的都是,如稳定剂、填充剂、增塑剂、交联剂)2、稳定剂:防止或延缓高分子材料的老化,使其保持原有使用性能的添加剂。
针对热、氧、光三个引起高分子材料老化的主要因素,可将稳定剂分为热稳定剂、抗氧剂(防老剂)、光稳定剂。
热稳定剂是一类能防止高分子材料在成型加工或使用过程中因受热而发生降解或交联的添加剂。
dt!_复合材料制备技术讲义(9)-拉挤成型实例
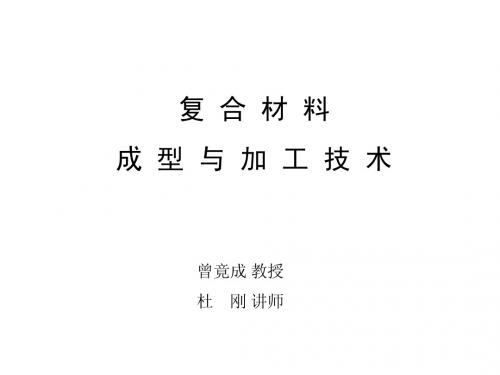
3.4模具尺寸的确定 模具尺寸的确定
目前国内模具长度一般设计为 左右。 目前国内模具长度一般设计为900mm左右。一般模具厚度为制品厚 模具长度一般设计为 左右 一般模具厚度为制品厚 度的2~ 倍 度的 ~3倍。
玻璃钢窗框型材大多是中空制品,一般芯模具的有效长度为模具长 玻璃钢窗框型材大多是中空制品,一般芯模具的有效长度为 芯模具的有效长度 度的2/3~ ,而在拉挤工艺过程中要考虑到芯棒固定及调整以及防止 芯棒固定及调整以及 度的 ~3/4,而在拉挤工艺过程中要考虑到芯棒固定及调整以及防止 偏心,此外芯棒还要考虑到配重的问题, 考虑到配重的问题 偏心,此外芯棒还要考虑到配重的问题, 对于模具长度为 左右的模具, 可设计为1200mm 对于模具长度为900mm左右的模具,芯棒的长度可设计为 模具长度为 左右的模具 芯棒的长度可设计为 左右。 左右。
浸渍区:
预成型区(preforming area) : (1)赋于概略形状,可以降低纤维束与固化模入口处的摩 擦与多余树脂。 (2)赋于纤维束、mat、或其它补强材适当的位置,以进 入固化模。
固化区:
拉挤模具 (die) :赋于工件的形状 加热装置: 电热板 电波加热 热油循环
辅助加热:在含浸纤维入模口之前先行预加热(微波加 热) 。 优点:树脂所需热传导的时间缩短,模具长度可以缩短,用 于大型工件。
建立拉挤模具温度传递模型,利用计算机辅助设计可以确定最佳的模 具温度分布及分析。 牵引速度:是平衡固化程度和生产速度的参数。在保证固化度的条件下 应尽可能提高牵引速度。 牵引力:是保证制品顺利出模的关键,牵引力的大小由制品与模具之间 的界面上的剪切应力确定。 温度参数、拉挤速度、牵引力在三个参数中,温度参数是由树脂系统的 特性确定的,是拉挤工艺中首要解决的因素。通过树脂固化体系的放热 曲线的峰值和有关条件,确定模具加热的各段温度值。拉挤速度确定的 原则是在给定的模内温度下的凝胶时间,保证制品在模具中部凝胶、固 化。牵引力与模具温度关系很大,并受拉挤速度的控制。脱模剂的影响 也是重要因素。
材料成型工艺基础(第三版) 第9章

图9-2 光固化成型过程
它使用的成型材料是对某特种光束敏感的树脂。其基本原 理为:在液槽内盛有液态的光敏树脂,激光束或紫外光光点在 液面上按计算机切片软件所得到的轮廓轨迹,对液态光敏树脂 进行扫描固化,形成连续的固化点,从而构成模样的一个薄截 面轮廓。一个层面扫描完成后,进行下一层扫描,新固化的层 黏结在前一层上,直至完成整个三维零件,如图9-2所示。
具体工作原理如图9-1所示,激光扫描器在计算机控制下按加 工零件各分解层面的形状对成型材料有选择性地扫描,从而形 成一层片,再进行下一层的扫描,新层黏结在前一层上,直至 整个零件制造完成。
图9-1 快速成型技术的工作原理 (a)三维模型;(b)二维截面;(c)激光扫描;(d)叠加三维制件
零件是点、线、面集合的空间实体,快速成型过程就是将 体-面-线离散与点-线-面叠加的过程。由于它把复杂的三维制 造转化为一系列二维制造的叠加,因而可以在不用模具和工具 的条件下生成几乎任意复杂的零部件,极大地提高了生产效率 和制造柔性。
当激光在模样几何形状所确定的区域内移动时,就能将粉末烧 结,从而生成模样的截面形状,并与下面已成型的部分黏结在 一起。每层烧结都是在先制成的那层顶部进行,一层截面烧结 完成以后,铺上新的一层材料粉末,选择性地烧结下层截面。 未烧结的粉末在制完模样后,可用刷子或压缩空气去除。
9.1.2 快速成型技术的分类及特点
快速成型工艺的种类很多,可按照材料的不同进行分类, 快速成型材料包括液态材料、离散颗粒和实体薄片。液态材料 的快速成型方法有液态树脂固化成型和熔融材料凝结成型,而 液态树脂固化又包括逐点固化和逐面固化;熔融材料凝结成型 又包括逐点凝结和逐面凝结。离散颗粒材料快速成型方法包括 激光熔融颗粒成型和黏结剂黏结颗粒成型两种方法。实体薄片 材料快速成型方法有薄片黏结堆积成型和采用光堆积成型两种。
注塑成型工艺第九章侧向分型与抽芯机构

材料:T10A、T8A及20钢 渗碳淬火,热处理硬度在 55HRC以上,表面粗糙度Ra 不大于0.8 μm
配合:斜销与其固定板采用H7/m6或H7/n6;与滑 块斜孔采用较松的间隙配合,如H11/d11,或留有0.5~ 1mm间隙,此间隙使滑块运动滞后于开模动作,且使分 型面处打开一缝隙,使塑件在活动型芯未抽出前获得松动, 然后再驱动滑块抽芯。
与β=0(即抽芯方向垂直开模方向)情况相比,斜销倾 角相同时,所需开模行程和斜销工作长度可以减小,而开 模力和斜销所受的弯曲力将增加,其效果相当于斜销倾角 为(α+β)时的情况。
由此可 见斜销的 倾角不能 过大,以 α+β≤15~ 20°为宜, 最大不能 超过25°。
③滑块抽拔方向朝定模方向倾斜β角时[图9—9(b)]
求斜销直径的另一种方法:采用查表法来确定。查 表前,首先要计算出抽芯力Fc,根据Fc和斜销倾角由表 9-l查出最大弯曲力,然后根据最大弯曲力、侧型芯中心 线与斜销固定底面的距离Hw(图9—8,Hw=Lcosα)以及斜 销的倾角由表9—2查得斜销的直径d。
4.斜销的长度
确定了斜销倾角α、有效工作长度L和直径d之后,可
H S cot (9-2)
斜销有效工作长度L与倾角α的关系为
L S
s in
(9-3)
上两式可见:倾角α增大,为完 成抽芯所需的开模行程及斜销有效 工作长度均可减小,有利于减小模 具的尺寸。
α对斜销受力情况的影响:
抽芯时滑块在斜销作用下沿导滑槽运动,忽略摩擦 阻力时,滑块将受到下述三个力的作用[图9—8 (a)],抽 芯阻力Fc、开模阻力Fk(即导滑槽施于滑块的力)以及斜 销作用于滑块的正压力F’。由此可得抽芯时斜销所受的 弯曲力F (与F’大小相等,方向相反)。
高分子材料成型加工考试重点及部分习题答案
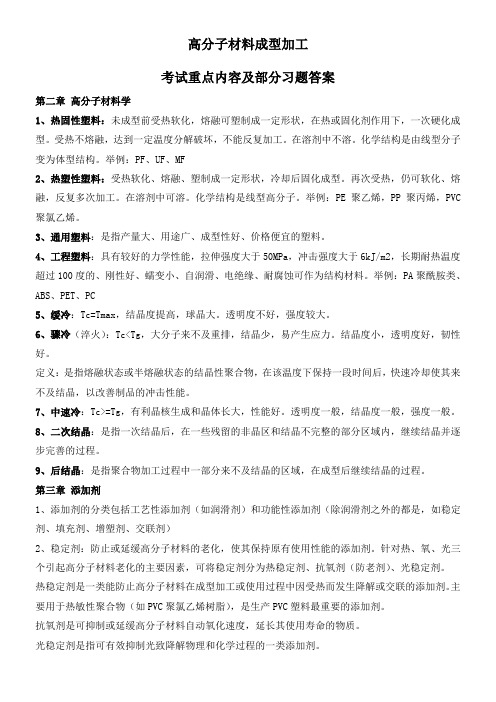
高分子材料成型加工考试重点内容及部分习题答案第二章高分子材料学1、热固性塑料:未成型前受热软化,熔融可塑制成一定形状,在热或固化剂作用下,一次硬化成型。
受热不熔融,达到一定温度分解破坏,不能反复加工。
在溶剂中不溶。
化学结构是由线型分子变为体型结构。
举例:PF、UF、MF2、热塑性塑料:受热软化、熔融、塑制成一定形状,冷却后固化成型。
再次受热,仍可软化、熔融,反复多次加工。
在溶剂中可溶。
化学结构是线型高分子。
举例:PE聚乙烯,PP聚丙烯,PVC 聚氯乙烯。
3、通用塑料:是指产量大、用途广、成型性好、价格便宜的塑料。
4、工程塑料:具有较好的力学性能,拉伸强度大于50MPa,冲击强度大于6kJ/m2,长期耐热温度超过100度的、刚性好、蠕变小、自润滑、电绝缘、耐腐蚀可作为结构材料。
举例:PA聚酰胺类、ABS、PET、PC5、缓冷:Tc=Tmax,结晶度提高,球晶大。
透明度不好,强度较大。
6、骤冷(淬火):Tc<Tg,大分子来不及重排,结晶少,易产生应力。
结晶度小,透明度好,韧性好。
定义:是指熔融状态或半熔融状态的结晶性聚合物,在该温度下保持一段时间后,快速冷却使其来不及结晶,以改善制品的冲击性能。
7、中速冷:Tc>=Tg,有利晶核生成和晶体长大,性能好。
透明度一般,结晶度一般,强度一般。
8、二次结晶:是指一次结晶后,在一些残留的非晶区和结晶不完整的部分区域内,继续结晶并逐步完善的过程。
9、后结晶:是指聚合物加工过程中一部分来不及结晶的区域,在成型后继续结晶的过程。
第三章添加剂1、添加剂的分类包括工艺性添加剂(如润滑剂)和功能性添加剂(除润滑剂之外的都是,如稳定剂、填充剂、增塑剂、交联剂)2、稳定剂:防止或延缓高分子材料的老化,使其保持原有使用性能的添加剂。
针对热、氧、光三个引起高分子材料老化的主要因素,可将稳定剂分为热稳定剂、抗氧剂(防老剂)、光稳定剂。
热稳定剂是一类能防止高分子材料在成型加工或使用过程中因受热而发生降解或交联的添加剂。
高分子材料成型加工(考试重点及部分习题答案)

高分子材料成型加工考试重点内容及部分习题答案第二章高分子材料学1、热固性塑料:未成型前受热软化,熔融可塑制成一定形状,在热或固化剂作用下,一次硬化成型。
受热不熔融,达到一定温度分解破坏,不能反复加工。
在溶剂中不溶。
化学结构是由线型分子变为体型结构。
举例:PF、UF、MF2、热塑性塑料:受热软化、熔融、塑制成一定形状,冷却后固化成型。
再次受热,仍可软化、熔融,反复多次加工。
在溶剂中可溶。
化学结构是线型高分子。
举例:PE聚乙烯,PP聚丙烯,PVC聚氯乙烯。
3、通用塑料:是指产量大、用途广、成型性好、价格便宜的塑料。
4、工程塑料:具有较好的力学性能,拉伸强度大于50MPa,冲击强度大于6kJ/m2,长期耐热温度超过100度的、刚性好、蠕变小、自润滑、电绝缘、耐腐蚀可作为结构材料。
举例:PA聚酰胺类、ABS、PET、PC5、缓冷:Tc=Tmax,结晶度提高,球晶大。
透明度不好,强度较大。
6、骤冷(淬火):Tc<Tg,大分子来不及重排,结晶少,易产生应力。
结晶度小,透明度好,韧性好。
定义:是指熔融状态或半熔融状态的结晶性聚合物,在该温度下保持一段时间后,快速冷却使其来不及结晶,以改善制品的冲击性能。
7、中速冷:Tc>=Tg,有利晶核生成和晶体长大,性能好。
透明度一般,结晶度一般,强度一般。
8、二次结晶:是指一次结晶后,在一些残留的非晶区和结晶不完整的部分区域内,继续结晶并逐步完善的过程。
9、后结晶:是指聚合物加工过程中一部分来不及结晶的区域,在成型后继续结晶的过程。
第三章添加剂1、添加剂的分类包括工艺性添加剂(如润滑剂)和功能性添加剂(除润滑剂之外的都是,如稳定剂、填充剂、增塑剂、交联剂)2、稳定剂:防止或延缓高分子材料的老化,使其保持原有使用性能的添加剂。
针对热、氧、光三个引起高分子材料老化的主要因素,可将稳定剂分为热稳定剂、抗氧剂(防老剂)、光稳定剂。
热稳定剂是一类能防止高分子材料在成型加工或使用过程中因受热而发生降解或交联的添加剂。
材料成型理论基础练习题上解读
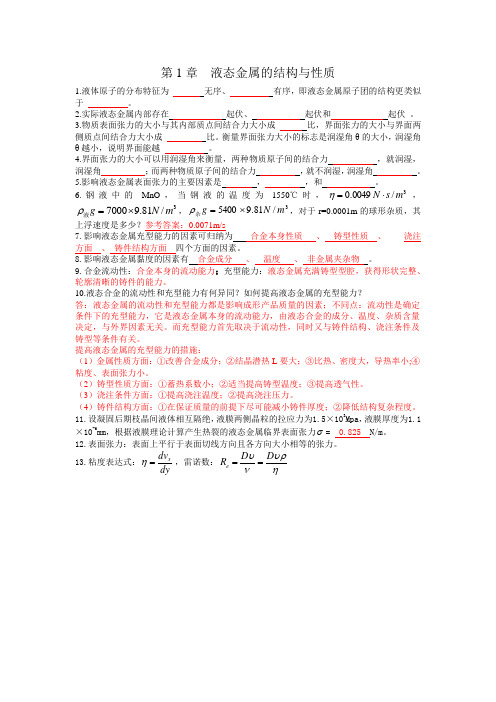
第1章 液态金属的结构与性质1.液体原子的分布特征为 无序、 有序,即液态金属原子团的结构更类似于 。
2.实际液态金属内部存在 起伏、 起伏和 起伏 。
3.物质表面张力的大小与其内部质点间结合力大小成 比,界面张力的大小与界面两侧质点间结合力大小成 比。
衡量界面张力大小的标志是润湿角θ的大小,润湿角θ越小,说明界面能越 。
4.界面张力的大小可以用润湿角来衡量,两种物质原子间的结合力 ,就润湿,润湿角 ;而两种物质原子间的结合力 ,就不润湿,润湿角 。
5.影响液态金属表面张力的主要因素是 , ,和 。
6.钢液中的MnO ,当钢液的温度为1550℃时,3/0049.0m s N⋅=η,3/81.97000m N g ⨯=液ρ,3/81.95400m N g ⨯=杂ρ,对于r=0.0001m 的球形杂质,其上浮速度是多少?参考答案:0.0071m/s7.影响液态金属充型能力的因素可归纳为 合金本身性质 、 铸型性质 、 浇注方面 、 铸件结构方面 四个方面的因素。
8.影响液态金属黏度的因素有 合金成分 、 温度 、 非金属夹杂物 。
9.合金流动性:合金本身的流动能力;充型能力:液态金属充满铸型型腔,获得形状完整、轮廓清晰的铸件的能力。
10.液态合金的流动性和充型能力有何异同?如何提高液态金属的充型能力?答:液态金属的流动性和充型能力都是影响成形产品质量的因素;不同点:流动性是确定条件下的充型能力,它是液态金属本身的流动能力,由液态合金的成分、温度、杂质含量决定,与外界因素无关。
而充型能力首先取决于流动性,同时又与铸件结构、浇注条件及铸型等条件有关。
提高液态金属的充型能力的措施:(1)金属性质方面:①改善合金成分;②结晶潜热L 要大;③比热、密度大,导热率小;④粘度、表面张力小。
(2)铸型性质方面:①蓄热系数小;②适当提高铸型温度;③提高透气性。
(3)浇注条件方面:①提高浇注温度;②提高浇注压力。
(4)铸件结构方面:①在保证质量的前提下尽可能减小铸件厚度;②降低结构复杂程度。
材料成型原理

材料成型原理晶体形核与生长凝固是指物质由液体转变为固体的相变过程。
凝固包括液体向晶态固体转变,以及向非晶态固体转变两种过程方式。
4、2、1液固相变驱动力心相与谋相的体积,自由能之差ΔGv,即为相变驱动力。
第一,无论是液相还是固相,物质自由能随温度上升而下降。
第二,液相自由能随温度上升,而下降的速率比固相的大。
过冷度越大,凝固相变驱动力越大。
通常将过了,分为五种类型,动力学过冷,曲率过冷,压力过冷,热过冷,成份过冷。
由于曲率的影响,物质实际熔点比平衡熔点要低。
4、3凝固形核凝固理论将晶体形核分为均质形核和非均质形核。
均质形核是指形核前母相液体中无外来固相质点,而从液相自身发生形核的过程,所以也称自发形核。
一般来说凝固是从非均质形核开始的,即依靠外来质点或型壁界面提供的衬底进行形核过程,这种形核亦称为异质形核或非自发形核。
4、3、2非均质形核与均质形核的比较在金属熔体中,存在着大量高熔点的固相杂质微粒,可作为非均质形核的衬底。
形核率是指单位体积,单位时间形成的晶核数目。
4、3、3非均质形核的形核条件。
1基底与结晶相的晶格错配度的影响。
错配度越小,共格情况越好,界面张力就越小,越容易进行非均质形核。
2冷却速度的影响。
过冷度越大,能促使非均质型和外来质点的种类和数量越多,非均质形核能力越强。
3结晶相枝晶熔断和游离的作用。
4、4晶体生长1粗糙界面:固-液界面固相一侧的点阵位置有一半左右被固相原子所占据,形成坑坑洼洼,凹凸不平的界面结构。
粗糙界面也称非小晶面或非小平面。
2光滑界面,固液界面固相一侧的点阵位置几乎全部被固相原子所占满,只留下少数空位或台阶,从而形成整体上平整光滑的界面结构,光滑界面也称为小晶面或小平面。
界面结构类型的本质与判据:固液界面结构主要取决于物质的热力学性质,以及晶体生长时的晶面取向。
3界面结构类型的影响因素:①熔融熵越小,越容易成为粗糙界面。
粗糙还是光滑面主要取决于物质的热力学性质。
高分子材料成型工艺学2018-8教材版-PDF
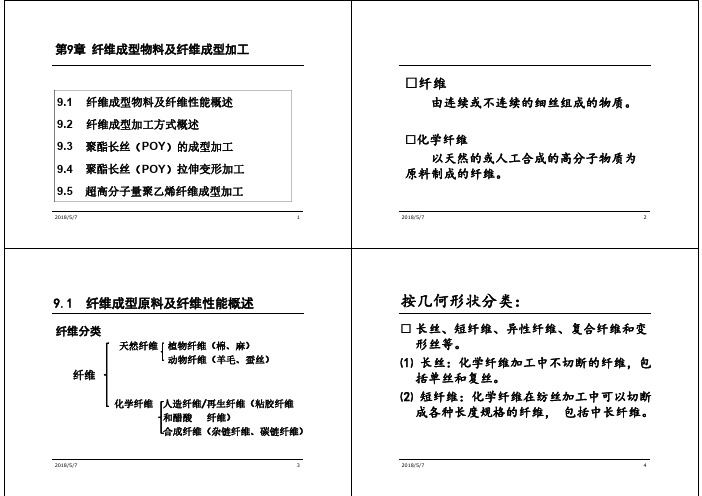
第9章纤维成型物料及纤维成型加工9.1纤维成型物料及纤维性能概述
腈纶
2018/5/7
第9章
9.2 纤维成型加工方法
9.2.2 熔融(熔体)纺丝
成纤高聚物首先要经加热形成聚合物熔体,再经螺
杆挤出机、纺丝组件等形成
纤维制品。
★聚酯、聚酰胺、聚丙烯等都采用熔融纺丝方法。
2018/5/729
熔点—熔点高低直接影响纺丝温度的高低,熔点波动
2018/5/737
熔融挤出-螺杆挤出机
预过滤金属丝网
纺丝挤出机流程
2018/5/7
9.3.4 高速纺丝(POY)工艺流程
1 加热管,
2 泵体,
3 轴承,
4 主动齿轴,
5 从动齿轮轴,
6 密封,
7 侧板
9.3.4 高速纺丝(POY)工艺流程
分配熔体
58并受卷绕牵引力作用,拉伸100-250倍。
62
第9章
9.3 聚酯长丝的成型加工
9.3.6 POY丝的质量评定
★冷拉伸应力—应变曲线
60%伸度时拉伸力的波动值:
可以表征纤维结构的均匀,波
动值应小于3%;
POY后拉伸倍数的选择:
选取POY伸长90%时的拉伸倍数为后拉伸倍数。
9.3 聚酯长丝的成型加工
81
86 9.4 聚酯长丝的拉伸变形加工
9.5.2 超高分子量聚乙烯纤维加工路线
十氢萘法进行高强高模聚乙烯纤维凝胶纺丝工艺示意图
矿物油法进行高强高模聚乙烯纤维凝胶纺丝工艺路线示意图
2018/5/7
☐熔喷无纺布
☐微纳米静电纺丝。
高分子材料成型加工原理

⾼分⼦材料成型加⼯原理第⼀章绪论1.按所属成型加⼯阶段划分,塑料成型加⼯可分为⼏种类型?分别说明其特点。
(1)⼀次成型技术⼀次成型技术,是指能将塑料原材料转变成有⼀定形状和尺⼨制品或半制品的各种⼯艺操作⽅法。
⽬前⽣产上⼴泛采⽤的挤塑、注塑、压延、压制、浇铸和涂覆等。
(2)⼆次成型技术⼆次成型技术,是指既能改变⼀次成型所得塑料半制品(如型材和坯件等)的形状和尺⼨,⼜不会使其整体性受到破坏的各种⼯艺操作⽅法。
⽬前⽣产上采⽤的只有双轴拉伸成型、中空吹塑成型和热成型等少数⼏种⼆次成型技术。
(3)⼆次加⼯技术这是⼀类在保持⼀次成型或⼆次成型产物硬固状态不变的条件下,为改变其形状、尺⼨和表观性质所进⾏的各种⼯艺操作⽅法。
也称作“后加⼯技术”。
⼤致可分为机械加⼯、连接加⼯和修饰加⼯三类⽅法。
2.成型⼯⼚对⽣产设备的布置有⼏种类型?(1)过程集中制⽣产设备集中;宜于品种多、产量⼩、变化快的制品;衔接⽣产⼯序时所需的运输设备多、费时、费⼯、不易连续化。
(2)产品集中制⼀种产品⽣产过程配套;宜于单⼀、量⼤、永久性强的制品、连续性强;物料运输⽅便,易实现机械化和⾃动化,成本降低。
3.塑料制品都应⽤到那些⽅⾯?(1)农牧、渔业(2)包装(3)交通运输(4)电⽓⼯业(5)化学⼯业(6)仪表⼯业(7)建筑⼯业(8)航空⼯业(9)国防与尖端⼯业(10)家具(11)体育⽤品和⽇⽤百货4.如何⽣产出⼀种新制品?(1)熟悉该种制品在物理、机械、热、电及化学性能等⽅⾯所应具备的指标;(2)根据要求,选定合适的塑料,从⽽决定成型⽅法;(3)成本估算;(4)试制并确定⽣产⼯艺规程、不断完善。
第⼆章塑料成型的理论基础1.什么是聚合物的结晶和取向?它们有何不同?研究结晶和取向对⾼分⼦材料加⼯有何实际意义?2.请说出晶态与⾮晶态聚合物的熔融加⼯温度范围,并讨论两者作为材料的耐热性好坏。
晶态聚合物:Tm——Td;⾮晶态聚合物:Tf——Td。
对于作为塑料使⽤的⾼聚物来说,在不结晶或结晶度低时最⾼使⽤温度是Tg,当结晶度达到40%以上时,晶区互相连接,形成贯穿整个材料的连接相,因此在Tg以上仍不会软化,其最⾼使⽤温度可提⾼到结晶熔点。
材料成型基本原理习题答案答案
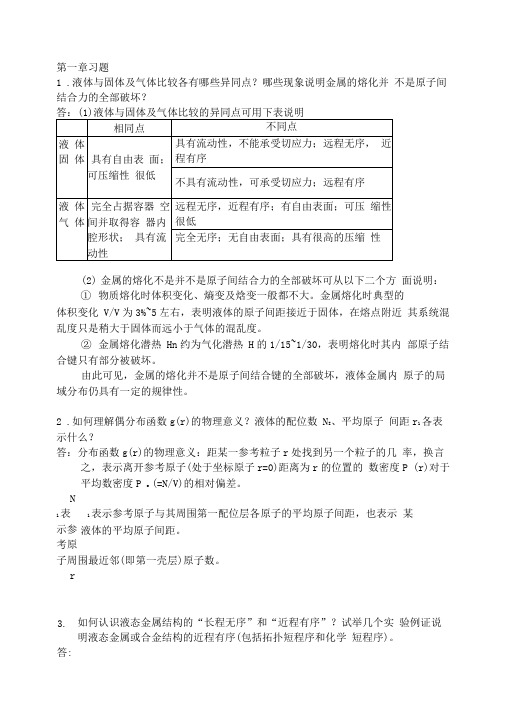
第一章习题1 .液体与固体及气体比较各有哪些异同点?哪些现象说明金属的熔化并 不是原子间结合力的全部破坏?答:(1)液体与固体及气体比较的异同点可用下表说明(2) 金属的熔化不是并不是原子间结合力的全部破坏可从以下二个方 面说明: ① 物质熔化时体积变化、熵变及焓变一般都不大。
金属熔化时典型的体积变化 V/V 为3%~5左右,表明液体的原子间距接近于固体,在熔点附近 其系统混乱度只是稍大于固体而远小于气体的混乱度。
② 金属熔化潜热 Hn 约为气化潜热 H 的1/15~1/30,表明熔化时其内 部原子结合键只有部分被破坏。
由此可见,金属的熔化并不是原子间结合键的全部破坏,液体金属内 原子的局域分布仍具有一定的规律性。
2 .如何理解偶分布函数g(r)的物理意义?液体的配位数 N I 、平均原子 间距r 1各表示什么?答:分布函数g(r)的物理意义:距某一参考粒子r 处找到另一个粒子的几 率,换言之,表示离开参考原子(处于坐标原子r=0)距离为r 的位置的 数密度P (r)对于平均数密度P o (=N/V)的相对偏差。
N1表示参考原子周围最近邻(即第一壳层)原子数。
r如何认识液态金属结构的“长程无序”和“近程有序”?试举几个实 验例证说明液态金属或合金结构的近程有序(包括拓扑短程序和化学 短程序)。
1表示参考原子与其周围第一配位层各原子的平均原子间距,也表示 某液体的平均原子间距。
3. 答:(1 )长程无序是指液体的原子分布相对于周期有序的晶态固体是不规则的,液体结构宏观上不具备平移、对称性。
近程有序是指相对于完全无序的气体,液体中存在着许多不停“游荡” 着的局域有序的原子集团(2)说明液态金属或合金结构的近程有序的实验例证① 偶分布函数的特征对于气体,由于其粒子(分子或原子)的统计分布的均匀性,其偶分布函数 g(r) 在任何位置均相等,呈一条直线 g(r)=1 。
晶态固体因原子以特定方式周期排列,其 g(r) 以相应的规律呈分立的若干尖锐峰。
塑料模具选修课件:第9章 推出机构设计

第九章推出机构设计§9.1 推出结构的结构组成与分类§9.2 推出力的计算§9.3 简单推出机构§9.4 二次推出机构§9.5 定、动模双向顺序推出机构§9.6 浇注系统凝料的推出机构§9.7 带螺纹塑件的脱模–使塑件及其浇注系统凝料从模具(凸模或凹模)中脱出的机构,又称为脱模机构。
–动作方向与开启模的运动方向一致的,通常由安装在注射机上的顶杆或液压缸来完成。
–推出机构设计的合理性与可靠性直接影响到塑件的质量,因此也是注射模设计的一个重要环节。
1. 推出机构的组成(典型结构)§9.1 推出结构的结构组成与分类–推出部件:Ø推杆、拉料杆、推杆固定板、推出板–推出导向部件:Ø推杆导柱、推杆导套–复位部件:Ø复位杆–其他:Ø支承钉推杆固定板垫板支承钉推出板拉料杆推杆导柱推杆导套推杆复位杆a)合模b)塑件及系统凝料推出2. 推出机构的分类–按驱动方式分:Ø机动推出机构Ø液压推出机构Ø气动推出机构Ø手动推出机构–按推出元件的类别分:Ø推杆推出机构Ø推管推出机构Ø推板推出机构–按模具结构特征分:Ø简单推出机构Ø二级推出机构Ø定模推出机构Ø浇注系统自动切断推出机构Ø带螺纹塑件的推出机构3. 推出机构的设计要求①尽量使塑件留于动模一侧Ø塑件留于动模,推出机构简单,否则要设计定模推出机构。
②保证塑件在推出过程中不变形不损坏③推出位置尽量选在塑件内侧,保证塑件外观良好④合模时应使推出机构正确复位⑤工作可靠、运动灵活、制造和更换容易顶针压下时留下的痕迹(顶白/Visible ejector marks )由于顶出导致的强烈变形(Deformation during demolding)在下部凹陷区由于强行脱模而导致的变形§9.2 推出力(脱模力)的计算–脱模力:将塑件从型芯上脱出时所需克服的阻力–包括:Ø成型收缩的包紧力及脱模时的摩擦力Ø不带通孔的壳体类塑件的大气压力Ø机构运动的摩擦力Ø塑件对模具的粘附力l开始脱模时瞬间所要克服的阻力,称为初始脱模力,以后脱模所需的力称为相继脱模力,后者比前者小l所以计算脱模力的时候,总是计算初始脱模力。
合工大版材料成型原理课后习题参考答案(重要习题加整理)

第二章 凝固温度场P498. 对于低碳钢薄板,采用钨极氩弧焊较容易实现单面焊双面成形(背面均匀焊透)。
采用同样焊接规范去焊同样厚度的不锈钢板或铝板会出现什么后果?为什么?解:采用同样焊接规范去焊同样厚度的不锈钢板可能会出现烧穿,这是因为不锈钢材料的导热性能比低碳钢差,电弧热无法及时散开的缘故;相反,采用同样焊接规范去焊同样厚度的铝板可能会出现焊不透,这是因为铝材的导热能力优于低碳钢的缘故。
9. 对于板状对接单面焊焊缝,当焊接规范一定时,经常在起弧部位附近存在一定长度的未焊透,分析其产生原因并提出相应工艺解决方案。
解:(1)产生原因:在焊接起始端,准稳态的温度场尚未形成,周围焊件的温度较低,电弧热不足以将焊件熔透,因此会出现一定长度的未焊透。
(2)解决办法:焊接起始段时焊接速度慢一些,对焊件进行充分预热,或焊接电流加大一些,待焊件熔透后再恢复到正常焊接规范。
生产中还常在焊件起始端固定一个引弧板,在引弧板上引燃电弧并进行过渡段焊接,之后再转移到焊件上正常焊接。
第四章 单相及多相合金的结晶 P909.何为成分过冷判据?成分过冷的大小受哪些因素的影响? 答: “成分过冷”判据为:R G L <NLD RLL L e K K D C m δ-+-0011当“液相只有有限扩散”时,δN =∞,0C C L =,代入上式后得R G L<000)1(K K D C m L L -( 其中: G L — 液相中温度梯度 R — 晶体生长速度 m L — 液相线斜率 C 0 — 原始成分浓度 D L — 液相中溶质扩散系数 K 0 — 平衡分配系数K )成分过冷的大小主要受下列因素的影响:1)液相中温度梯度G L , G L 越小,越有利于成分过冷 2)晶体生长速度R , R 越大,越有利于成分过冷 3)液相线斜率m L ,m L 越大,越有利于成分过冷 4)原始成分浓度C 0, C 0越高,越有利于成分过冷 5)液相中溶质扩散系数D L, D L 越底,越有利于成分过冷6)平衡分配系数K 0 ,K 0<1时,K 0 越 小,越有利于成分过冷;K 0>1时,K 0越大,越有利于成分过冷。
材料成型原理
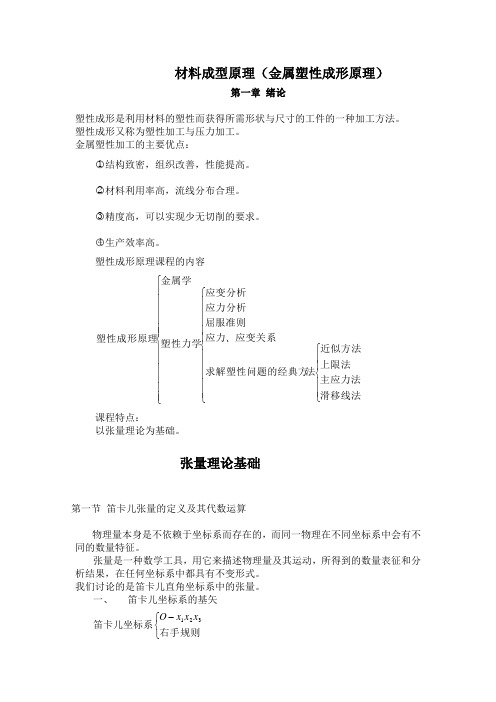
材料成型原理(金属塑性成形原理)第一章 绪论塑性成形是利用材料的塑性而获得所需形状与尺寸的工件的一种加工方法。
塑性成形又称为塑性加工与压力加工。
金属塑性加工的主要优点:○1结构致密,组织改善,性能提高。
○2材料利用率高,流线分布合理。
○3精度高,可以实现少无切削的要求。
○4生产效率高。
塑性成形原理课程的内容⎪⎪⎪⎪⎪⎪⎩⎪⎪⎪⎪⎪⎪⎨⎧⎪⎪⎪⎪⎪⎩⎪⎪⎪⎪⎪⎨⎧⎪⎪⎩⎪⎪⎨⎧滑移线法主应力法上限法近似方法法求解塑性问题的经典方应变关系应力屈服准则应力分析应变分析塑性力学金属学塑性成形原理、课程特点:以张量理论为基础。
张量理论基础第一节 笛卡儿张量的定义及其代数运算物理量本身是不依赖于坐标系而存在的,而同一物理在不同坐标系中会有不同的数量特征。
张量是一种数学工具,用它来描述物理量及其运动,所得到的数量表征和分析结果,在任何坐标系中都具有不变形式。
我们讨论的是笛卡儿直角坐标系中的张量。
一、 笛卡儿坐标系的基矢笛卡儿坐标系⎩⎨⎧-右手规则321x x x O设e k (k=1、2、3)沿Ox k 轴的单位矢量,称为基矢量或基矢。
定义基矢的点积或标量积:⎩⎨⎧≠==∙lk lk e e kl k .0.11δ kl δ为Kronecker 克氏符号。
定义基矢的叉积或矢量积为:k ijk j i e e e =∈⨯ ijk ∈为置换符号。
⎪⎩⎪⎨⎧-=∈,其它的奇数排列、、为、、,的偶数排列、、为、、,032113211k j i k j i ijk指标ijk 的原始排列顺序为1、2、3,如果将排列中的任意一对相邻指标互换,则称为指标的一次置换。
例如1 2 3给一次置换就成为1 3 2或2 1 3。
如果再互换一对指标,就称为二次置换。
依次类推可以定义指标排列的几次置换。
当几次为奇数时,称为奇置换。
而几为偶数时,称为偶置换。
二、 求和约定任一矢量 i i e e e e μμμμμ=++=332211 ij ij i j ij ij υμυμ=∑∑==3131在三维的欧矢空间内,如果某一指标在同一项中重复出现,就表示要对这个指标从1到3求和。
安工大材料成型专业课金属学第5-9章复习题(重修)
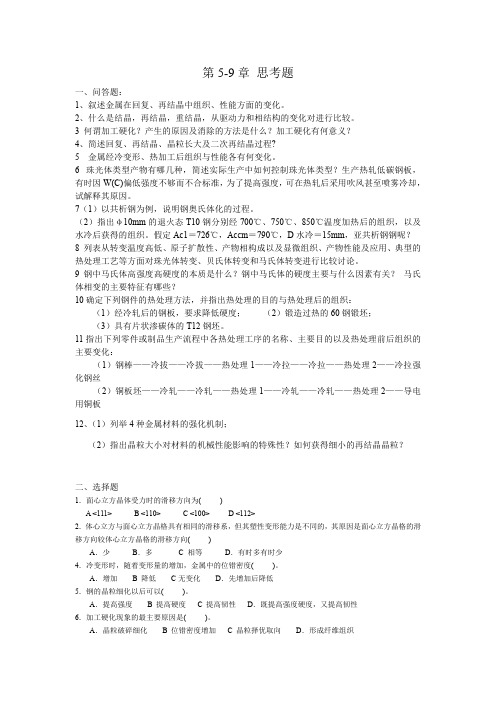
第5-9章思考题一、问答题:1、叙述金属在回复、再结晶中组织、性能方面的变化。
2、什么是结晶,再结晶,重结晶,从驱动力和相结构的变化对进行比较。
3何谓加工硬化?产生的原因及消除的方法是什么?加工硬化有何意义?4、简述回复、再结晶、晶粒长大及二次再结晶过程?5金属经冷变形、热加工后组织与性能各有何变化。
6珠光体类型产物有哪几种,简述实际生产中如何控制珠光体类型?生产热轧低碳钢板,有时因W(C)偏低强度不够而不合标准,为了提高强度,可在热轧后采用吹风甚至喷雾冷却,试解释其原因。
7(1)以共析钢为例,说明钢奥氏体化的过程。
(2)指出φ10mm的退火态T10钢分别经700℃、750℃、850℃温度加热后的组织,以及水冷后获得的组织。
假定Ac1=726℃,Accm=790℃,D水冷=15mm,亚共析钢钢呢?8列表从转变温度高低、原子扩散性、产物相构成以及显微组织、产物性能及应用、典型的热处理工艺等方面对珠光体转变、贝氏体转变和马氏体转变进行比较讨论。
9钢中马氏体高强度高硬度的本质是什么?钢中马氏体的硬度主要与什么因素有关?马氏体相变的主要特征有哪些?10确定下列钢件的热处理方法,并指出热处理的目的与热处理后的组织:(1)经冷轧后的钢板,要求降低硬度;(2)锻造过热的60钢锻坯;(3)具有片状渗碳体的T12钢坯。
11指出下列零件或制品生产流程中各热处理工序的名称、主要目的以及热处理前后组织的主要变化:(1)钢棒——冷拔——冷拔——热处理1——冷拉——冷拉——热处理2——冷拉强化钢丝(2)铜板坯——冷轧——冷轧——热处理1——冷轧——冷轧——热处理2——导电用铜板12、(1)列举4种金属材料的强化机制;(2)指出晶粒大小对材料的机械性能影响的特殊性?如何获得细小的再结晶晶粒?二、选择题1.面心立方晶体受力时的滑移方向为()A<111>B<110>C<100>D<112>2.体心立方与面心立方晶格具有相同的滑移系,但其塑性变形能力是不同的,其原因是面心立方晶格的滑移方向较体心立方晶格的滑移方向()A.少B.多C相等D.有时多有时少4.冷变形时,随着变形量的增加,金属中的位错密度()。
材料成型原理各章重点

第一章重点总结第一节了解即可,没有出过题。
第二节1.纯金属的液态结构(11页第三段)2.实际金属的液态结构(11页第四段第五行,从“因此,实际液态金属-----”到段末)3.名词解释温度起伏,结构起伏,能量起伏(11页三、四段中)4.13页第一段“X射线衍射-----”第三节5.影响液态金属粘度的因素(14页)(1)化学成分,难熔化合物的液体粘度较高,熔点低的共晶成分合金粘度低(2)温度,液体金属的粘度随温度的升高而降低。
(3)非金属夹杂物,非金属夹杂物使液态金属粘度增加6.粘度在材料成形过程中的意义1)对液态金属净化的影响(2)对液态合金流动阻力的影响(3)对凝固过程中对流的影响7.名词解释,表面张力(15页最下面一句“总之,一小部分---”)8.表面张力产生的原因,(16页第一段)9.影响表面张力的因素(见2005年A卷二大题1小题)第四节10.流变铸造及特点(21页第一段“即使固相体积分数达到---”至最后,及21页最后一段,22页第一段)11.半固态金属表观粘度的影响因素(21页2 3 4段)第二章重点总结1铸造概念(22页第一段第一句)第一节2.液态金属充型能力和流动性有何本质区别(见2006年A卷第2题)3.两种金属停止流动机理(1)纯金属和窄结晶温度范围合金的停止流动机理(22页最后一段)(2)款结晶温度范围合金停止流动机理(23页第二三段)4.影响充型能力的因素及促进措施(1)金属性质方面的因素1.合金成分2.结晶潜热3.金属比热容4液态金属粘度5表面张力(2)铸型性质方面的因素1铸型蓄热系数,蓄热系数越大,铸型的激冷能力就越强2.铸造温度(3)浇注条件方面因素1.浇注温度2充型压头3浇注系统结构(4)铸件结构方面因素1折算厚度2铸件复杂程度(每点后最好总结一句话)第二节5.金属凝固过程中的流动(第二节1、2段)第三节6.了解存在三种传热;对流传热,传导传热,辐射传热即可第四节7.了解存在三种计算凝固时间的方法1理论计算法2平方根定律3折算厚度法即可第三章重点第一节1为什么过冷是液态合金结晶的驱动力(见2006年A卷第1题)2. 何为热力学能障和动力学能障?凝固过程中是如何克服这两个能障的?(见2005年D卷第3题)第二节 3.形核条件(40页第一段)4.名词解释,匀质形核,非匀质形核(41页最上部)5,2007年B卷第1题6.记住公式3-17 7.2006年A卷第3题第三节8.晶体宏观长大方式晶体宏观长大方式取决于界面前方液体中的温度分布,即温度梯度(1)平面方式长大固-液界面前方液体中的温宿梯度大于0,液相温度高于界面温度,称为正温度梯度分布。
材料成型工艺基础习题解答

第一章金属材料与热处理1、常用的力学性能有哪些?各性能的常用指标是什么?答:刚度:弹性模量E强度:屈服强度和抗拉强度塑性:断后伸长率和断面收缩率硬度:冲击韧性:疲劳强度:2、4、金属结晶过程中采用哪些措施可以使其晶粒细化?为什么?答:过冷细化:采用提高金属的冷却速度,增大过冷度细化晶粒。
变质处理:在生产中有意向液态金属中加入多种难溶质点(变质剂),促使其非自发形核,以提高形核率,抑制晶核长大速度,从而细化晶粒。
7、9、什么是热处理?钢热处理的目的是什么?答:热处理:将金属材料或合金在固态范围内采用适当的方法进行加热、保温和冷却,以改变其组织,从而获得所需要性能的一种工艺。
热处理的目的:强化金属材料,充分发挥钢材的潜力,提高或改善工件的使用性能和加工工艺性,并且可以提高加工质量、延长工件和刀具使用寿命,节约材料,降低成本。
第二章铸造成型技术2、合金的铸造性能是指哪些性能,铸造性能不良,可能会引起哪些铸造缺陷?答:合金的铸造性能指:合金的充型能力、合金的收缩、合金的吸气性;充型能力差的合金产生浇不到、冷隔、形状不完整等缺陷,使力学性能降低,甚至报废。
合金的收缩合金的吸气性是合金在熔炼和浇注时吸入气体的能力,气体在冷凝的过程中不能逸出,冷凝则在铸件内形成气孔缺陷,气孔的存在破坏了金属的连续性,减少了承载的有效面积,并在气孔附近引起应力集中,降低了铸件的力学性能。
6、什么是铸件的冷裂纹和热裂纹?防止裂纹的主要措施有哪些?答:热裂是在凝固末期,金属处于固相线附近的高温下形成的。
在金属凝固末期,固体的骨架已经形成,但树枝状晶体间仍残留少量液体,如果金属此时收缩,就可能将液膜拉裂,形成裂纹。
冷裂是在较低温度下形成的,此时金属处于弹性状态,当铸造应力超过合金的强度极限时产生冷裂纹。
防止措施:热裂——合理调整合金成分,合理设计铸件结构,采用同时凝固原则并改善型砂的退让性。
冷裂——对钢材材料合理控制含磷量,并在浇注后不要过早落砂。
复合材料的成型工艺

第一节 复合材料简述
2.复合材料的特点
(1)比强度和比刚度高 (2)抗疲劳性好 (3)高温性能好 (4)减振性能好 (5)断裂安全性高 (6)可设计性好
第一节 复合材料简述
二、复合材料用原料
1.增强材料
3)基体能够很好地保护纤维表面,不产生表面 损伤、不产生裂纹。
第一节 复合材料简述
(2)增强材料是承载的主要部分,因而纤维必须具 有很高的强度和刚度。
(3)增强材料与基体有好的结合强度。 (4)在复合材料中纤维必须具有适当的含量、直径
和分布。 (5) 纤维和基体应有相近的热膨胀系数。
第一节 复合材料简述
2. 井喷沉积法(Spray Co-Deposition)
井喷沉积法是运用特殊的喷嘴,将液态金属 基体通过惰性气体气流的作用后雾化成细小的 液态金属流,将增强相颗粒加入到雾化的金属 流中,与金属液滴混合在一起并沉积在衬底上 ,凝固形成金属基复合材料的方法。
图9-5所示是采用井喷沉积法生产陶瓷颗粒 增强金属基复合材料的示意图。
复合材料的一种成型方法,如图9-6所示。 热压成型时,先将粉料与蜡或有机高分子粘结剂混合、加热,利用蜡类材料热熔冷固的特点,把粉料与熔化的蜡料等粘合剂迅速搅合
成具有流动性的料浆,然后将混合料加压注入模具,冷却凝固后成型,即可得致密的、较硬实的坯体。
二、喷射成型工艺(Spray Moulding) (2)液态法 液态法是指基体处于熔融状态下制造金属基复合材料的方法。
下压制成型。
树脂基复合材料(resin matrix composites-RMC)、金属基复合材料(metallic matrix composites -MMC)、陶瓷基复合材料(ceramic matrix
《材料成型理论基础》课程大纲
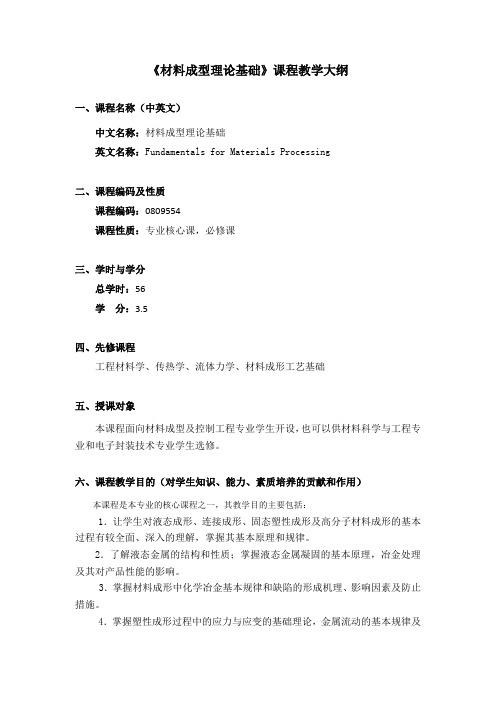
《材料成型理论基础》课程教学大纲一、课程名称(中英文)中文名称:材料成型理论基础英文名称:Fundamentals for Materials Processing二、课程编码及性质课程编码:0809554课程性质:专业核心课,必修课三、学时与学分总学时:56学分:3.5四、先修课程工程材料学、传热学、流体力学、材料成形工艺基础五、授课对象本课程面向材料成型及控制工程专业学生开设,也可以供材料科学与工程专业和电子封装技术专业学生选修。
六、课程教学目的(对学生知识、能力、素质培养的贡献和作用)本课程是本专业的核心课程之一,其教学目的主要包括:1.让学生对液态成形、连接成形、固态塑性成形及高分子材料成形的基本过程有较全面、深入的理解,掌握其基本原理和规律。
2.了解液态金属的结构和性质;掌握液态金属凝固的基本原理,冶金处理及其对产品性能的影响。
3.掌握材料成形中化学冶金基本规律和缺陷的形成机理、影响因素及防止措施。
4.掌握塑性成形过程中的应力与应变的基础理论,金属流动的基本规律及其应用。
5.了解高分子材料的组织转变及流动、成形的基本规律。
表1 课程目标对毕业要求的支撑关系七、教学重点与难点:教学重点:1)本课程以材料成形工艺的理论基础为主线,根据成形加工过程中材料所处或经历的状态,分为液态凝固成形、固态塑性成形、连接成形、塑料注射成形等几类,学习材料在成形过程中的组织结构、性能、形状随外在条件的不同而变化的规律性知识。
2)本课程着重利用前期所学的物理、化学等基础理论,以及传热学、流体力学等专业基础理论知识,学习液态成形、塑性成形、连接成形等基本材料成形技术的内在规律和物理本质,包括共性原理,同时也要注重个性规律性认识。
3)课程将重点或详细介绍三种主要材料成形方法中的主要基础理论和专门知识,阐述这些现象的本质,揭示变化的规律。
而对次要成形方法的基本原理或发展状况等只作简要介绍或自学。
4)重点学习的章节内容包括:第4章“单相合金与多相合金的凝固”(6学时)、第5章“铸件凝固组织的形成与控制”(6学时)、第7章“焊缝及其热影响区的组织和性能”(6学时)、第8章“成形过程的冶金反应原理”(6学时)、第11章“应力与应变理论”(4学时)、第12章“屈服准则”(6学时)。
- 1、下载文档前请自行甄别文档内容的完整性,平台不提供额外的编辑、内容补充、找答案等附加服务。
- 2、"仅部分预览"的文档,不可在线预览部分如存在完整性等问题,可反馈申请退款(可完整预览的文档不适用该条件!)。
- 3、如文档侵犯您的权益,请联系客服反馈,我们会尽快为您处理(人工客服工作时间:9:00-18:30)。
图9-1b为杆I和杆Ⅱ的冷却曲线。开始冷却时,
两杆具有相同的温度tL,最后又冷却到同一温度
t0。由于杆I较厚,冷却前期杆Ⅱ的冷却速度大于 杆I,而后期必然是杆I的冷却速度比杆Ⅱ快。在 整个冷却过程中,两杆的温差变化如图9-1c所示。
近期的研究工作表明,合金的温度低于液相 线以后,其变形由弹性变形、塑性变形和粘弹 性变形组成,且以弹性变形为主。这样,铸件 在冷凝过程中,收缩一旦受阻,就产生应力。
B. 按应力存在的时间分:
(1)临时应力(temporary stress):产生应力 的原因消失,应力便消失。 (2)残余应力(residual stress):产生应力的
原因消除后,仍然存在的应力。
3、应力的危害:
铸造应力和铸件的变形对铸件质量的危害
很大。铸造应力是铸件在生产、存放、加工以
及使用过程中产生变形和裂纹的主要原因,它 降低铸件的使用性能。 例如,当机件工作应力的方向与残余应力 的方向相同时,应力叠加,可能超出合金的强 度极限,发生断裂。
因此在其它条件相同时,合金钢具有较大的残余
应力。
相变对残余应力的影响表现在以下两个方面:
a) 相变引起比容的变化,
b) 相变热效应改变铸件各部分的温度分布。
2、铸型性质方面
铸型蓄热系数越大,铸件的冷却速度越大,铸
件内外的温差就越大,产生的应力则越大。金属
型比砂型容易在铸件中引起更大的残余应力。
3、浇注条件
2、自然时效(natural ageing)
将具有残余应力的铸件放置在露天场地,经数
月至半年以上,应力慢慢自然消失,称此消除应力 方法为自然时效。 铸件中存在残余应力,必然使晶格发生畸变, 畸变晶格上的原子势能较高,极不稳定。长期经受
不断变化的温度作用,原子有足够时间和条件发生
能量交换,原子的能量趋于均衡,晶格畸变得以恢 复,铸件发生变形,应力消除。
这种方法虽然费用低,但最大缺点是时间太长,
效率低,近代生产很少采用。
3、共振时效(resonance ageing)
共振时效的原理是:调整振动频率,使铸件 在具有共振频率的激振力作用下,获得相当大的 振动能量。 在共振过程中,交变应力与残余应力叠加,
铸件局部屈服,产生塑性变形,使铸件中的残余
应力逐步松弛、消失。同时也使处在畸变晶格上 的原子获得较大能量,使晶格畸变恢复,应力消 失。
3、浇注条件
(1)内浇口和冒口的位置应有利铸件各部分温 度的均匀分布,内浇口布置要同时考虑温度分 布均匀和阻力最小的要求。
(2)铸件在铸型内要有足够的冷却时间,尤其
是采用水爆清砂时,不能打箱过早,水爆温度
不能过高。但对一些形状复杂的铸件,为了减
小铸型和型芯的阻力,又不能打箱过迟。
4、改进铸件结构
提高浇注温度,相当于提高铸型的温度,延 缓了铸件的冷却速度,使铸件各部分温度趋于 均匀,因而可以减小残余应力。
4、铸件结构
铸件壁厚差越大,冷却时厚薄壁温差就越大, 引起的热应力则越大。
四、减小应力的途径
减小铸造应力的主要途径是针对铸件的结构
特点在制定铸造工艺时,尽可能地减小铸件在冷
却过程中各部分的温差,提高铸型和型芯的退让 性,减小机械阻碍。可采用以下具体措施:
2、分类: A. 按应力形成的原因分:
(1) 热应力(thermal stress):
铸件各部分厚薄不同, 在凝固和凝固后的 冷却过程中,冷却速度不同,造成同一时刻各 部分收缩量不一致,铸件各部分彼此制约,产 生的应力。
(2) 相变应力(phase transformation stress): 固态发生相变的合金,由于铸件各部分冷却 条件不同,它们到达相变温度的时刻不同,且相 变的程度也不同而产生的应力。 (3)机械阻碍应力(mechanism hindered stress): 铸件收缩受到铸型、型芯、箱挡和芯骨等机 械阻碍所产生的应力。
第二阶段(τ1~τ2):
tⅡ<ty ,tⅠ<ty。
此时杆I温度也已降 到ty 以下,开始线收缩,
在τ1时两杆具有相同长
度。在以后的冷却过程 中,两杆的温差沿图9-
1c中ab变化,到τ2时两
杆温差最大,为Δtmax。
从τ1到τ2,两自由线收缩量的差为:
式中:
α——线收缩系数,
L——杆长。
即杆Ⅱ要比杆I多收缩α(Δtmax- ΔtH) L。但两杆彼此相连,始终具有相同 长度,故杆Ⅱ被拉长,杆I被压缩。
1、合金方面
在零件能满足工作条件的前提下,选择弹性 模量和收缩系数小的合金材料。
2、铸型方面
(1) 使铸件在冷却过程中温度分布均匀:
(a) 可在铸件厚实部分放置冷铁,或采用蓄
热系数大的型砂;
(b) 可对铸件特别厚大部分进行强制冷却,
即在铸件冷却过程中,向事先埋没在铸型内的
冷却器吹入压缩空气或水气混合物,加快厚大
中的实际条件而定。重量大的铸件处理时间要长 一些。
共振时效具有显著的优越性:时间短,费 用低,功率小,一马力的振动器可处理50t以上 铸件,省能源,无污染,机构轻便,易操作,
铸件表面不产生氧化皮 ,不损害铸件尺寸精
度.该方法对箱、框类铸件效果尤为显著,但 对盘类 和 厚大铸件效果较差 ,有待进一步完 善.
E/(107N.m-2)
19600
16600
(2) 铸件的残余应力与合金的自由线收缩系数 成正比。图9—2是几种材料从0—600℃的线膨胀
曲线。当其它条件相同时,奥氏体不锈钢由于α 值大,其残余应力比铁素体不锈钢的要大50%。
(3) 合金的导热系数直接影响铸件厚薄两部分
的温差值。合金钢比碳钢具有较低的导热性能,
有残余应力的铸件,放置日久或经机械加
工后会变形,使机件失去精度。产生变形的铸 件可能因加工余量不足而报废,为此需要加大 加工余量。 在大批量流水生产时,变形的铸件在机械 加工时往往因放不进夹具而报废。此外,挠曲 变形还降低铸件的尺寸精度,尤其对精度要求 较高的铸件,防止产生变形尤为重要。
二、金属凝固和冷却过程中产生的应力
瞬时应力的发展过程可分四个阶段加以说明, 如图9-1d所示。合金线收缩开始温度为ty 第一阶段(τ0~τ1): tⅡ<ty , tⅠ>ty 。 杆 Ⅱ 开 始 线收缩,而杆I仍处于凝 固初期,枝晶骨架尚未形 成。显然,此时铸件的变 形由杆Ⅱ确定,杆Ⅱ带动 杆I一起收缩。到η1时,两 杆具有同一长度,温差为 ΔtH,铸件不产生应力。
部位的冷却速度。
(c) 可在铸件冷却过程中,将铸件厚壁部位 的砂层减薄。 (d) 预热铸型可减小铸件各部分的温差。在 熔模铸造中,为了减小铸造应力和裂纹等缺陷, 型壳在浇注前被预热到600~900℃。
(2)提高铸型和型芯的退让性: 减小砂型的紧实度,或在型砂中加入适量 的木屑、焦炭等,采用壳型或树脂砂型,效 果尤为显著。 采用细面砂和涂料,可以减小铸型表面的 摩擦力。
第二节
热
裂(Hot Tearing)
一、热裂特征和分类
热裂是铸件生产中最常见的铸造缺陷之一。 热裂的外观特征如图9—4所示,裂纹表面呈氧 化色(铸钢件裂纹表面近似黑色,铝合金呈暗灰 色),不光滑,可以看到树枝晶(图9—5)。
裂纹是沿晶界产生和发展的(图9—6),外
形曲折。
热裂分为外裂和内裂。在铸件表面可以看到 的裂纹称为外裂,其表面宽,内部窄,有时贯穿 铸件整个断面。 外裂常产生在铸件的拐角处、截面厚度有突 变或局部冷凝慢且在凝固时承受拉应力的地方。 大部分外裂用肉眼就能观察到,细小的外裂 需用磁力探伤或其它方法才能发现;内裂需用x 射线,γ射线或超声波探伤检查。
内裂产生在铸件内部最后凝固的部位,也常 出现在缩孔附近或缩孔尾部(图9—7)。
以应力框为例(图9-1),讨论瞬时应力的发展过
程。 在不考虑机械阻碍时,该合金铸件中的瞬时
应力就是热应力。
应力框由杆I,杆Ⅱ以及横梁Ⅲ组成。为便于讨
论,作如下假设:
1) 金属液充满铸型后,立即停止流动,杆I和 杆Ⅱ从同一温度tL开始冷却,最后冷却到室温 t0。 2) 合金线 收缩 开始 温度 为 ty , 材 料的 收缩 系数α不随温度变化。 3) 铸件不产生挠曲变形。 4) 铸 件 收 缩 不 受 铸 型 阻 碍 。 5) 横梁Ⅲ是刚性体。
材料成形工艺原理
材料成形系
高文理
第九章 铸造应力
第一节 铸造应力 第二节 热裂 第三节 冷裂
第九章 铸造应力Casting Stress
第一节 铸造应力
一、铸造应力的定义、分类和危害
1、定义: 铸造应力(casting stress):金属在凝固和冷却 过程中体积变化受到外界或其本身的制约,变形 受阻,而产生的应力。
态,在此温度下保温一定时间,使应力消失,再
缓慢冷却到室温。
确定热处理规范应注意的是,在铸件升温和 冷却过程中力求其各处温度均匀,以免温差过 大产生附加应力,造成铸件变形或冷裂。 为此,铸件升温,冷却速度不宜过快,但从 生产实际出发,为了提高生产效率,加热和冷 却速度均不应过小,保温时间不易过长,要根
(1) 金属的弹性模量越大,铸件中的残余应力就
越大。例如,铸钢、白口铁和球铁的残余应力比灰 口铸铁的大,原因之一是与金属的弹性模量有关 (表9—1)。
表9-1 一些铸造合金的弹性模量 材料 钢 白口铸铁 球墨铸铁 1350018200 灰铸铁 735010800 铜合金 1100013200 铝合金 65008300
据具体情况制定既有较高生产效率,又不产生
较大附加热应力的最佳热处理规范。
在确定某合金铸件的热处理规范时,可用同
种合金铸成许多尺寸相同的环形试样,环上开有
同样尺寸的缺口,并在缺口处楔入楔形铁,使环
处于应力状态(图9—3),然后将试样放入加热炉