注塑机和模具的匹配关系
注塑成型—注塑模具(高分子成型课件)
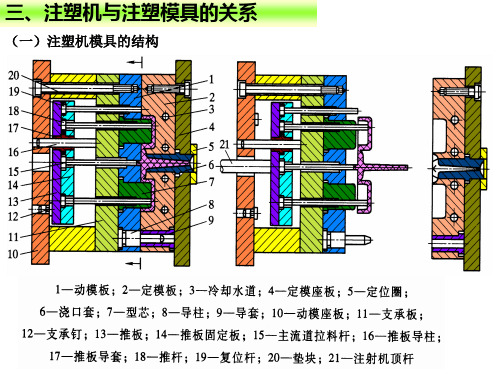
模具安装在注射机上必须使模具中心线与 料筒、喷嘴的中心线相重合,因此,注射机 定模板上设有一定位孔,要求模具的定位部 分也设计一个与主流道同心的凸台,即定位 圈(环),并要求定位圈(环),与注射机 定模板上的定位孔之间采用一定的配合。
三、注塑机与注塑模具的关系
(二)注塑机与注塑模关系
⑥注塑机顶出装置和模具推出装置的校核
a 中心顶杆机械顶出 b 两侧双顶杆机械顶出 c 中心顶杆液压顶出与两侧顶杆机械顶出联合作用 d 中心顶杆液压顶出与其他开模辅助油缸联合作用
螺钉、压板固定。模具重量较重的用螺钉固定;模具重量较轻用压板 固定。
三、注塑机与注塑模具的关系
(二)注塑机与注塑模关系
5 有关模具ቤተ መጻሕፍቲ ባይዱ装部分的尺寸校核
⑤开模行程的校核
开模行程也叫做合模行程,指模具开合过程中注塑机动模固定板的移动 距离,用符号s表示。 当模具厚度确定以后,开模行程的大小直接影响模具所能成型制品高度。 即s太小时,模具不能成型高度较大的制品,否则,成型后的制品无法从模 具脱出。因此,设计模具时必须校核它所需用的开模距离是否与注塑机的 开模行程相适应。 开模距离的校核分①注射机最大开模行程与模厚无关②注射机最大开模 行程与模厚有关③有侧向抽芯时的最大开模行程三种情况进行校核。
三、注塑机与注塑模具的关系
(一)注塑机模具的结构 5 侧向分型与抽芯机构
对于有侧孔或侧凹的塑件,在被顶出脱模 之前,必须先进行侧向抽芯或分开滑块, 方能顺利脱模。主要作用完成侧向活动型 芯抽出和复位。 其由斜导柱、侧型芯滑块、锁紧块(斜锲) 和侧型芯滑块的定位装置(挡块、滑块拉 杆、弹簧)等组成。
三、注塑机与注塑模具的关系
(一)注塑机模具的结构 3 导向机构
注射模结构与注塑机参数的关系

利用先进的技术手段,开发智能化模具与注塑机,实现参数的自适应调整和优化,提高生 产效率和降低能耗。
加强注射模与注塑机的绿色制造技术研究
随着环保意识的提高,加强注射模与注塑机的绿色制造技术研究,降低能耗和减少废弃物 排放,实现可持续发展。
THANKS FOR WATCHING
感谢您的观看
冷却
通过冷却水将塑料 件在模具中冷却至 硬化。
加料
将塑料加入注塑机 的加料斗中。
注射
通过注射装置将熔 融的塑料注入模具 中。
脱模
将冷却后的塑料件 从模具中脱出。
04 注射模结构与注塑机参数 的关系
注射模结构对注塑机参数的影响
1 2 3
模具尺寸
模具的尺寸决定了注塑机的最大和最小模具尺寸, 选择注塑机时应确保模具尺寸与机器的尺寸相匹 配。
注塑机的参数设置
01
02
03
注射量
注射量是注塑机的重要参 数,它决定了注塑机能够 生产出多大的塑料件。
注射压力
注射压力是注塑机在注射 塑料时所施加的压力,它 影响着塑料件的密度和强 度。
模具温度
模具温度是塑料件在模具 中冷却时的温度,它影响 着塑料件的冷却时间和质 量。
注塑机的操作流程
加热
通过加热器将塑料 加热至熔融状态。
顶出系统
用于将塑料制品从模具中顶出 的机构。
冷却系统
用于将塑料制品冷却定型,通 常由冷却水道和冷却元件组成
。
注射模的设计原则
满足塑料制品的形状、 尺寸和精度要求。
优化模具结构,降低 成本,提高生产效率。
确保模具强度高、寿 命长、易于加工和维 护。
注射模的分类
根据模具结构
模具与注射机的关系

模具与注射机的关系模具都必须安装在与其相适应的注射机上才能进行生产。
因此设计模具时,必须熟悉所选注射机的技术规范,并对相关参数进行校核,判断模具能否在所选注射机上使用。
1 注射机注射机是进行注塑加工的设备,也是应用最广的塑料成型设备。
1.1 .注射机的结构组成注射机通常由注射装置、锁(合)模装置、液压传动系统和电器控制系统等组成。
( 1)注射装置。
是注射机的主要部分,将颗粒状或粉状的固体塑料原料均匀塑化成熔融状态,并以适当的速度和压力将一定量的塑料熔体注射进模具型腔。
注射装置主要由塑化部件8 、料斗9 、注射和移动液压缸11 、计量装置和传动装置10 等组成。
其中塑化部件是主要部分,由螺杆(柱塞)、料筒、加热器和喷嘴组成。
( 2 )锁模装置。
也称为合模装置,主要作用是:实现模具可靠地开合,提供必要的行程;在注射和保压时,提供足够的锁模力;提供推出塑件的推出力和相应的行程。
锁模装置主要由定模固定板6 、动模固定板3 、拉杆5 、锁模液压缸1 、锁模机构2 、塑件推出机构4 和模具调整装置等组成。
常用的锁模装置有液压一机械式和全液压式。
( 3 )液压传动和电器控制系统。
该系统保证注射机按塑化、注射、固化成型各个工艺过程的预定要求(如温度、压力、速度、时间等)和动作程序准确有效地工作。
液压系统主要由各个液压油缸、管道、各类阀件和其他液压元件组成,电器控制系统主要由各种仪器和仪表组成。
1.2 .注射机的分类注射机发展很快,类型不断增加,分类方法各异。
最常见的是按注射机外形特征分类,即按注射装置和锁模装置的排列方式分类,可分为卧式注射机、立式注射机、角式注射机等。
( l )卧式注射机。
卧式注射机是使用最广泛的注射成型设备,它的注射螺杆或柱塞的轴线与锁模装置轴线在一条直线上(或相互平行),并且沿水平方向装设。
卧式注射机的优点是机器重心低,比较稳定,便于操作、维修和加料,塑件推出模具后可利用其自重自动落下,容易实现全自动操作等。
注塑机与模具关系

⑤ 安装螺孔尺寸
5.按合模装置的特征分类
机械式、液压式 、液压机械式
3.3.3
注射成型机规格及其表示
注射机型号标准表示法主要有: 注射量、锁模力、注射量与锁模力 同时表示 3 种。 1 注射量表示法
以注射机最大注射量(额定注射量)表示。国家标准采用 注射量 表 示法。卧式 注射机(国产),型号有:XS-Z30、XS-Z60、XS-ZY125、XSZY500 、XS-ZY1000等。
过小:不能充分发挥注射机的加工能力,料滞留在料筒中中时间 过长易降解。 过大:制品不能成型。
模具设计时:保证注射模内所需要的熔料总量在注射机允许的最
大注射量范围内。
3.3.4.1 注射机 注射装置 的技术参数及其校核:注射量 注射量的校核:
校核注射机的 额定注射量 是否满足所需成型的塑件所需要的实际 注射量(容积量或质量)(制件+浇注系统两部分)即:
• 3.3.1 注射成型机组成 • 3.3.2 注射成型机分类 • 3.3.3 注射成型机规格及其表示• 3.3.4 注射成型机来自术参数及其校核3.3.1
注射成型机组成
注射装置(系统) 合模装置(系统)(锁模装置) 液压传动及电器控制系统 辅助部分:机架„
3.3.1
(1)注射系统
注射成型机组成
3.3.4.1 注射机 注射装置 的技术参数及其校核
注射速率、注射速度和注射时间(以PS料)
注射速率:指公称注射量的熔料在注射时间内注射出去的 量(体积),即单位时间内所能达到的体积流速(见表)。 注射速度:指螺杆或柱塞的移动速度。 注射时间:指螺杆(或柱塞)射出一次公称注射量所需要 的时间。(注射量与注射时间的关系见表5-4/P248)
第四章 注塑机和注塑模具的关系

⑵成型制品精度较高。生产批量较大时,模具应当设有 温度控制系统。
⑶对制品成型的适应性很强。 ⑷成型周期短,生产效率最高,便于实现自动化操作, 因此便于大批量制品的生产。
第四章 注塑机和注塑模具的关系
本章重点: 掌握注塑机主要参数与模具结构之间的关系 注塑机的主要参数: 最大注射量、最大注射压力、最大锁模力、最大成型
面积、模具最大和最小厚度、最大开模行程、安装位置 尺寸、喷嘴球径和孔径、顶杆位置。
第四章 注塑机和注塑模具的关系
用注塑模来生产制品主要有以下特点: ⑴塑料的加热和塑化是在注塑机的高温料筒内完成的,
注塑机的主要参数:
最大注射量、最大注射压力、最大锁模力、最大成型面积、模具最大 和最小厚度、最大开模行程、安装位置尺寸、喷嘴球径和孔径、顶杆位置。
一、最大注射量的校核:
注塑机最大注射量的标定:通常用常温下注射机一次注射
聚苯乙烯PS (1.06g/cm³) 的最大容积量为注射机公称注射量。 -----体积(cm³)
一 、注塑机的种类及应用
㈠注塑机的种类及其应用: 按成型塑料性质:有热塑性塑料注塑机和热固性塑料注塑机。
按塑化方式:有柱塞式注塑机和螺杆式注塑机。
柱塞式注塑机一般在公称注射量60cm3 以下;
螺杆式注塑机,是目前产量最大,应用最广的类型。
按锁模机构驱动方式:有液压式和液压-机械联合式。 按操作方式:有全自动、半自动和手动式。 按结构形式:有立式、卧式和直角式
直角式注塑机:
如图所示,其注射装置轴线与锁模机构轴线相互正交垂直。 优点:结构简单,便于自制,适于一模仅成型一件,
几种常见样式的双色注塑机与模具结构的匹配性概述

几种常见样式的双色注塑机与模具结构的匹配性概述摘要:本文概要介绍了四种卧式双色注塑机结构样式与模具构造特征的匹配性,以及它们的差异性、优缺点等内容,方便注塑成型行业人员了解双色塑料制品成型生产的相关应用特性。
关键词:双色,注塑机,模具,直角式,平行式,背负式0 前言双色塑料制品在人们的日常生活中、工业生产中有着广泛的应用,例如双色的牙刷柄、笔筒、玩具壳,有着舒适的软硬触感和绚丽的颜色感观,增加人们生活幸福感和满足感;例如汽配件中的门柱塑壳使用硬质塑料满足机械强度,搭配使用软质材料提供密封性能,可实现特定的结构性或密封性;在特定条件下使用廉价塑料作局部填充,减少优质材料的用量,可降低生产成本;双色或多色制品一体成型,减少后处理工艺(如喷漆上色、连接组装),节省人工、节能环保、减少污染,提高生产效率,降低生产复杂程度。
所谓双色塑料制品,是注塑成型行业的一种俗称,不仅指代两种不同的颜色,也可以是两种不同的塑胶材质,或同种材质不同颜色。
相应地,所谓双色注塑机,可以统述为具有成型两种或两种以上材料或颜色制品的注塑机。
1 几种常见样式的卧式双色注塑机与模具构造特征的匹配性自双色模具诞生之初,双色注塑机的结构形式就是为了与之配套而作适应性设计,以满足双色制品的生产,下面概要介绍几种常见的结构样式。
1.1平行式如上图所示的两副模具,左右并行安装于注塑机模板的中心两侧,一副为第一色半成品模具,另一副为第二色成品,两副模具的唧嘴中心要分别与注塑机的两射嘴中心対正安装。
按照双色模具设计的第一原则“动模相同,定模不同”,通常两副动模的构造包括模仁或模腔是完全相同的。
一色模中成型的是仅有一色材料的半成品,通常不做顶出脱模,二色模中成型的才是包含一色和二色材料的完成品,开模后顶出脱模,塑料件取出清空模腔,以供下一生产周期连续注射成型。
这种两副模具平行安装的结构,适合选用宽模板的平行射台双色机。
平行安装的两副分体的模具,也可以设计制作为一个整体式的,或者是两副模架分体,而模具底板一体制作连为一个整体,如下图所示,但要注意模具的一色和二色唧嘴中心距要与平行双色机的两射嘴中心距保持一致。
注塑机与模具的匹配关系
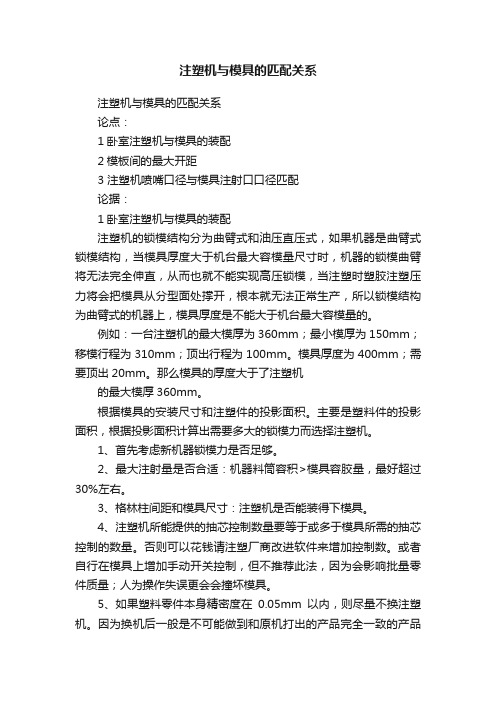
注塑机与模具的匹配关系注塑机与模具的匹配关系论点:1卧室注塑机与模具的装配2模板间的最大开距3 注塑机喷嘴口径与模具注射口口径匹配论据:1卧室注塑机与模具的装配注塑机的锁模结构分为曲臂式和油压直压式,如果机器是曲臂式锁模结构,当模具厚度大于机台最大容模量尺寸时,机器的锁模曲臂将无法完全伸直,从而也就不能实现高压锁模,当注塑时塑胶注塑压力将会把模具从分型面处撑开,根本就无法正常生产,所以锁模结构为曲臂式的机器上,模具厚度是不能大于机台最大容模量的。
例如:一台注塑机的最大模厚为360mm;最小模厚为150mm;移模行程为310mm;顶出行程为100mm。
模具厚度为400mm;需要顶出20mm。
那么模具的厚度大于了注塑机的最大模厚360mm。
根据模具的安装尺寸和注塑件的投影面积。
主要是塑料件的投影面积,根据投影面积计算出需要多大的锁模力而选择注塑机。
1、首先考虑新机器锁模力是否足够。
2、最大注射量是否合适:机器料筒容积>模具容胶量,最好超过30%左右。
3、格林柱间距和模具尺寸:注塑机是否能装得下模具。
4、注塑机所能提供的抽芯控制数量要等于或多于模具所需的抽芯控制的数量。
否则可以花钱请注塑厂商改进软件来增加控制数。
或者自行在模具上增加手动开关控制,但不推荐此法,因为会影响批量零件质量;人为操作失误更会会撞坏模具。
5、如果塑料零件本身精密度在0.05mm以内,则尽量不换注塑机。
因为换机后一般是不可能做到和原机打出的产品完全一致的产品(调整工艺不可能全部解决问题),这时往往需要修配模具尺寸。
6、外观要求高的透明零件所使用的注塑机不能使用其它有色原料;且需要无尘环境;相应的原料干燥等辅助设备也有较高要求。
7、产品稳定性要求高的零件不要将注塑机换成稳定性更差的。
一般来说,新的、电动的机器优于老的、液压的。
德国机强过日本机。
8、确定换机后,将模具浇口套上的曲面和浇口直径与注塑机上射嘴的曲面和内径匹配2模板间的最大开距3注塑机喷嘴口径与模具注射口口径匹配:有两点要注意1.模具R>喷嘴R2.模具浇口套孔径>喷嘴孔径如下图所示:模具模具与喷嘴。
模具与注射机的关系
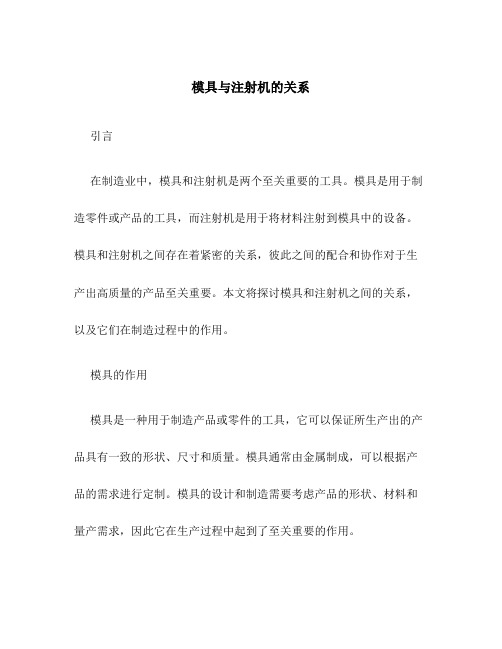
模具与注射机的关系引言在制造业中,模具和注射机是两个至关重要的工具。
模具是用于制造零件或产品的工具,而注射机是用于将材料注射到模具中的设备。
模具和注射机之间存在着紧密的关系,彼此之间的配合和协作对于生产出高质量的产品至关重要。
本文将探讨模具和注射机之间的关系,以及它们在制造过程中的作用。
模具的作用模具是一种用于制造产品或零件的工具,它可以保证所生产出的产品具有一致的形状、尺寸和质量。
模具通常由金属制成,可以根据产品的需求进行定制。
模具的设计和制造需要考虑产品的形状、材料和量产需求,因此它在生产过程中起到了至关重要的作用。
模具的设计模具的设计是模具制造的首要步骤。
在设计模具时,需要考虑产品的形状、尺寸、材料以及生产量等因素。
模具应具备易于安装和拆卸的特点,以便于在生产过程中进行模具的更换和维修。
模具的设计还需要考虑产品的生产周期和成本,以确保生产过程的高效性和经济性。
模具的制造模具的制造是根据设计要求将模具加工成形的过程。
制造模具需要使用专业的加工设备和工艺,例如数控机床、电火花机等。
模具的制造过程包括模具的铣削、钻孔、铣床等加工工艺,以及模具的热处理等工序。
制造完成后,模具需要进行质量检验和调试,以确保模具符合产品的设计要求。
注射机是将材料注射到模具中的设备,它承担着将原材料转化为成品的重要任务。
注射机通过对原材料进行加热和压力控制,将材料注射到模具中,并在一定时间内冷却固化。
注射机在生产过程中发挥了重要的作用,对产品的质量和产量有着直接的影响。
注射机的工作原理注射机通过加热器将塑料颗粒加热至熔化状态,然后将熔化的塑料注入到模具中。
注射机通过螺杆将塑料颗粒推入注射筒,然后通过压力将熔化的塑料注入到模具的腔体中。
注射机在注射过程中需要控制加热温度、塑料的注射速度和注射压力等参数,以确保产品的质量和生产效率。
根据注射机的工作方式和结构特点,可以将注射机分为垂直注射机和水平注射机。
垂直注射机将注射筒和模具安装在同一轴线上,适用于对注射过程中的空气和气泡要求比较高的产品制造。
注塑模与注塑机分析
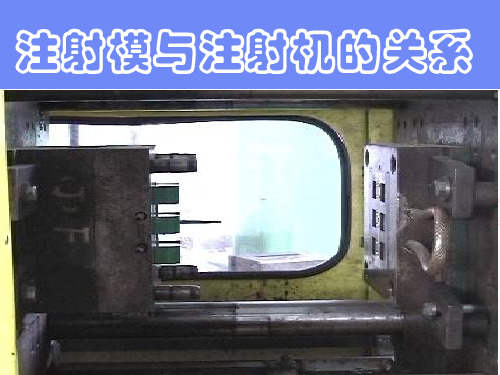
双分型面注射模(为了保证开模后既能取出制品又能取 出流道内的凝料,需要在开模距离中另定模座板与 此同时间板之间的分开距离a,a的大小应该保证可 以方便地取出流道内的凝料,因此 Smax≥H1+H2+a+(5~10)mm
斜导柱侧向分型与抽芯注射模具
带有活动镶件的注射模
齿轮齿条侧向抽芯注射模具
热流道注射模具 气辅模具 倒装模
注射成型设备
任何注射模只有安装在注射机 上才能使用,所以两者在注射成型 生产中是一个不可分割的整体。
注射机的基本组成 注射机的分类 规格及主要技术参数 有关工艺参数的效核
注射机的基本组成
螺杆式:(用于卧式)
柱塞式注射机示意图
型腔
喷嘴
鱼雷
进料漏斗
活塞
模具
加热器
从漏斗落下的塑料同时计量,在计量最后时,活塞往前推进, 材料通过加热缸内面与鱼雷构成的较小通路,在此充分加热成为熔融塑料, 再从喷嘴注塑到模穴中。
这种装置可塑化能力不佳,已较少使用。
螺杆式注射机示意图
喷嘴 型腔
进料漏斗
驱动马达
Hmin<H<Hmax
式中:H---模具厚度(mm);
Hmin---注射机充许的最小模厚,即 动、定模之间的最小开距( mm);
( mm);
Hmax---注射机充许的最大模厚
如果太厚—无法安装;假若太小,需增加垫板。
模具的长度和宽度
要与注射机拉杆间距相适应, 使模具安装时可以穿过拉杆空间 在动、定模固定板固定。
螺杆 (注塞) 直径 /mm
20, 25
最大注 注射 最大注 射量 压力 射面积 /cm3(g) /Mpa /cm3
第二节 模具与注射机的关系

第二节模具与注射机的关系注射模必须安装在与其相适应的注射机上才能进行生产,因而在设计模具时,必须熟悉所选用注射机的技术参数,如注射机的最大注射量、最大注射压力、最大锁模力、最大成型面积、模具最大厚度和最小厚度、开模最大行程、拉杆间距、安装模板的螺孔(或T形槽)位置和尺寸、定位孔尺寸、喷嘴球面半径,等等。
以便设计的模具与所选注射机相适应。
一、国产注射机台模部分的基本参数注射机合模部分的基本参数包括模板尺小、拉杆间距、模板间最大开距、动模板的行程、模具最大厚度和最小厚度等,这些参数规定了注射机所安装模具的尺寸范围;图5—9至图5—12所示为几种国产注射机合模部分的基本参数,供模具设计时参考。
其它类型注射机可查阅有关产品样本和有关设计资料。
二、注射机有关工艺参数的校核1.最大注射量的校核注射机最大注射量和制品的质(重)量或体积有直接关系,两者必须相适应,不然会影响制品的产量和质量。
若最大注射量小于制品的质(重)量,就会造成制品的形状不完整或内部组织硫松,制品强度下降等缺陷;而注射量过大,注射机利用率降低,浪费电能,而且可能导致塑料分解。
因此,为了保证正常的注射成型,注射机的最大注射量应稍大于制品的质(重)量或体积(包括流通凝料)。
通常注射机的实际注射量最好在注射机的最大注射量 的80%以内。
当注射机最大注射量以最大注射容积标定时,按下式校核:流V VV KV ni i+=≥∑=10 (5-1)0V ——注射机最大注射容积(3cm );V ——制品的总体积(包括制品、流通凝料在内) (3cm )i V ——一个制品的体积(3cm ); 流V ——流道凝料的体积(3cm );n ——型腔数:K ——注射机最大注射星的利用系数,取K =0.8因塑料的体积与压缩比有关,所以所需塑料体积为:V K 压料=V (5-2)式中 压K ——压缩比,压K 可查表5—1;料V ——塑料的体积(3cm )。
把注射机的最大注射容积换算为最大注射质(重)量时,其值为00V m ρ'= (5-3)式中 ρ'——在料简温度和压力下熔融塑料的密度;ρρC ='ρ——塑料在常温下的密度,单位为g/3cm ,见表5—1;C——在料简温度下塑料体积膨胀的校正系数(未考虑压力的影响),对结晶型塑料,C≈0.85,对非结晶配料,C≈0.93。
检查模具与设备匹配方法

模具与注塑机设备匹配检查具体步骤
模具安装到注塑机上方法分成两种: 第一种采用自动换模辅助设备,模具从上下格林柱的垂直空间里水平进入注塑机。模具处于注塑状态天 地侧尺寸必须小于设备上下格林柱的垂直内间距,同时模具的最大、最小模厚满足设备要求。 第二种模具从设备天侧吊入注塑机。 1,模具宽度小于设备立柱水平内间距,模具直接从天侧吊入注塑机,检查模具厚度是否符合最大、最小 模厚和其它装夹问题; 2,模具宽度大于设备立柱水平内间距,模具长度小于设备立柱垂直内间距,模具旋转90度后进入注塑 机,再旋转90度后到固定位置,检查模具厚度必须小于设备立柱水平内间距,模具对角线长度必须小于设备 最大开模间距; 3,模具宽度大于设备立柱水平内间距,模具长度大于设备立柱垂直内间距,检查模具厚度必须小于设备 立柱水平内间距。将模具长度方向超出设备立柱垂直内间距的部分减材料处理,要求减材料后的对角线长度 小于设备立柱水平内间距,模具对角线长度必须小于设备最大开模间距
注塑机介绍
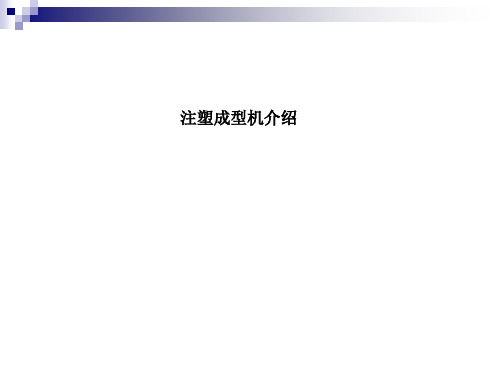
目录
一.注塑成型机与模具的关系 二.注塑成型机有关工艺参数的校核 1.型腔数量的决定;
2.注塑压力的校核
3.锁模力的校核 4.模具与注塑机装模部位相关尺寸的校核 5.开模行程与塑件推出距离的校核 三:注塑成型机的分类 1.卧式注塑机 2.立式注塑机 3.角式注塑机 四:注塑成型机辅助设备的介绍 1.模温机2.干燥机3.上料机4.冷水机5. 机械手
(4).模具闭合厚度
Hmax≥Hm≥Hmin
(5).安装螺孔尺寸 模具重量较轻用压板固定 模具重量较重的用螺钉固定
5.开模行程与塑件推出距离的校核 注塑机的开模行程是有限制的,取出制件所需要的开模距离必须小于注塑机 的最大开模距离。 (1).注塑机的最大开模行程(s)与模具厚度(Hm)无关
单分型面模具:S>=H1+H2+(5~10)mm 双分型面模具:S>=H1+H2+a+(5~10)mm
6.最大开模行程;
7.模板安装模具的螺钉孔(或T形槽)的位置和尺寸; 8.注塑机喷嘴孔直径和喷嘴球头半径值.
二:注塑成型机有关工艺参数的校核
1.型腔数量的决定 当塑件设计完成之后就进入了模具设计,首先必须考虑采用单型腔还是多型腔 模,并决定数量的多少。考虑的因素主要有:现有注塑机的规格、所要求的塑件质量、 塑件成本及交货期,起决定作用的因素很多,它既有技术方面的因素,也有生产 管理方面的因素。 型腔数量可以从以下几个方面进行计算: (1).由交货期计算型腔数:当某产品采用一副模具生产时可按下式确定型腔数。 n=(1.05*N*tc)/(3600*th(to-tm)) 式中1.05—故障系数(以5%计) N—一副模具定货量(件) tc—成型周期(s) to—从定货到交货时间(月)
注塑机与模具的关系
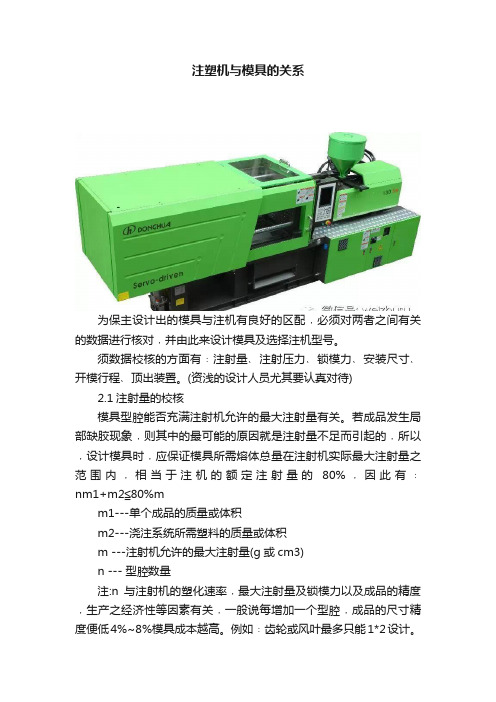
注塑机与模具的关系为保主设计出的模具与注机有良好的区配﹐必须对两者之间有关的数据进行核对﹐并由此来设计模具及选择注机型号。
须数据校核的方面有﹕注射量﹑注射压力﹑锁模力﹑安装尺寸﹑开模行程﹑顶出装置。
(资浅的设计人员尤其要认真对待)2.1注射量的校核模具型腔能否充满注射机允许的最大注射量有关。
若成品发生局部缺胶现象﹐则其中的最可能的原因就是注射量不足而引起的﹐所以﹐设计模具时﹐应保证模具所需熔体总量在注射机实际最大注射量之范围内﹐相当于注机的额定注射量的80%﹐因此有﹕nm1+m2≦80%mm1---单个成品的质量或体积m2---浇注系统所需塑料的质量或体积m ---注射机允许的最大注射量(g或cm3)n --- 型腔数量注:n与注射机的塑化速率﹐最大注射量及锁模力以及成品的精度﹐生产之经济性等因素有关﹐一般说每增加一个型腔﹐成品的尺寸精度便低4%~8%模具成本越高。
例如﹕齿轮或风叶最多只能1*2设计。
2.2注射压力校核﹕这是为了核定注机的最大注射压力能否满足该塑件成型的需要﹐成品所需注射压力是由注机类型﹐喷嘴形式﹐塑料流动性﹐浇注系统和型腔的流动阴力等因素决定的﹐注射压力不足会真接形成短射现象。
一般讲来﹐注射压力是否满中成品所需可以通过调机人员的有机控制﹐不可将其调至过大﹐以防浇口处或模具强度不足处被压受损或模具不能分模2.3锁模力的校核﹕注射成型时﹐塑件在模具分模面上的投影面积是影响锁模力的主要因素﹐并且锁模力的大小与投影面成正比﹐若注塑机所能提供的锁模力不及则会使模具分模面闭合不紧﹐靠﹑插破不充分﹐从而直接形成毛边或溢料现象。
注塑机的吨位型号是由锁模力决定的﹐而快速计算注塑机锁模力所需吨位的公式为﹕F1=(n A1+A2) PA1---成品的最大投影面积﹐总长*总宽单位:cm2A2---浇注系统之投影面积单位﹕cm2P --- 压强系数(高压﹕0.75吨/cm2 普压﹕0.5吨/cm2)F1---树脂压力单位﹕吨F1≦80% F F---注塑机的锁模力2.4安装尺寸的校核﹕为保证模具能顺利安装﹐对其安装尺寸的校核十分重要﹐这个环节﹐往往设计人员因过分依赖计算机作业而经常疏忽的问题﹐结果造成模具无法按时试模2.4.1喷嘴尺寸﹕喷嘴的孔径dn与注道衬套之孔径dp之间﹐还有喷嘴的凸球面半径Rn与衬套面半径Rp之间﹐必须分别满足以下关系。
注塑机和模具的匹配关系
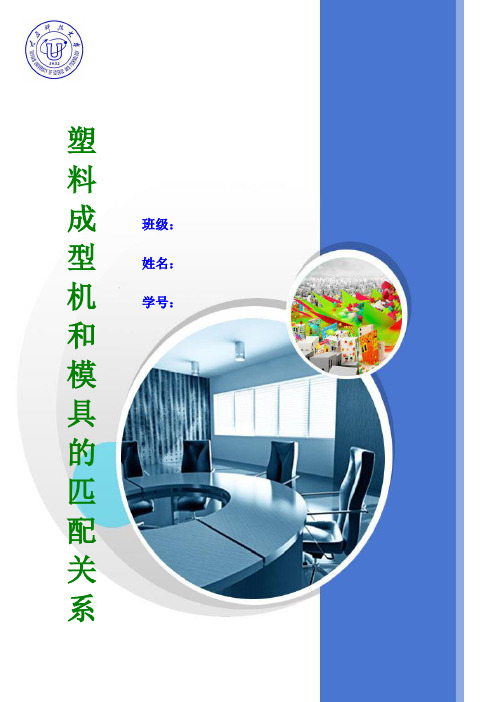
塑
料
成班级:
型姓名:
机学号:
和
模
具
的
匹
配
关
系
前言:
塑料注射成型机是将热塑性塑料或热固性塑料利用塑料成型模具制成塑料制件的主要成型设备。注射成型能一次成型出形状复杂、尺寸精确和带有嵌件的塑料制品,生产效率高、易于实现自动化。
1.最大注射量
注射机的最大注射量是指注射机螺杆或柱塞以最大注射行程对空注射时,一次所能达到的塑料注射量。设计注射模时,塑件加浇注系统凝料所用的塑料量,不应超过最大注射量。对于正常的批量生产,应满足:
Mr≤0.8Mmax (式中Mr是成型塑件说要求的注射量)
2.最大注射压力
每种塑料都有适于成型的压力范围,具体塑件所需成型压力范围不仅与塑料品种有关,也与塑件形状、壁厚及浇注系统断面积大小和长度有关。设计模具时,所要求的成型压力应在注射机所允许的最大注射压力范围内。
每副模具只有安装在与其相匹配的注射机上才能进行正常的生产,因此模具设计与所选用的注射机型号关系十分密切。
各种型号的注塑机安装模具部位的形状和尺寸各不相同。设计模具时应校核的主要项目有:喷嘴尺寸、定位圈尺寸、最大模厚、最小模厚、模板的平面尺寸和模具安装用螺钉孔位置尺寸等。
一:塑料注射机的选择
从模具没计角度出发,注射机的技术规范有:
3.锁模力
每一台注射机,都有一个额定的锁模力,所设计的模具在注射充模时,分型面张开的总力不能超过这一额定锁模力,可用如下关系式表示:
A·P型≤F
模具与注射机的关系
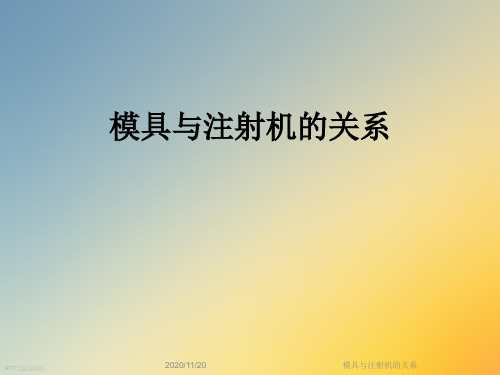
模具与注射机的关系
(6)注射机的选择与较核
主流道衬套(浇口套)与注射机相关的尺寸(如图所示)
PPT文档演模板
模具与注射机的关系
(6)注射机的选择与较核的校核
主流道衬套(浇口套)与注射机相关的尺寸:
• 如补充图所示:① 喷嘴 孔尺寸
d = d1 + 0.5 ~ 1mm ② 凹坑半径 R = R1 +1~2 mm
阶梯制件 图 5-66
• 对脱模斜度较大或内表面为阶梯状的制件,有时无须顶出型芯的 全部高度,即可取出制件,如图5-67所示。
• 故脱模距H1需视具体情况而定,以制件能顺利取出为度。
PPT文档演模板
模具与注射机的关系
(4)模具厚度和开模行程的校核
① 注射机开模行程与模厚无关时的校核 • ②② 注射机开模行程与模厚有关时的校核:
须小于注射机的最大开模距离。开模距离可分成下面两类情况校 核。
PPT文档演模板
模具与注射机的关系
(4) 模具厚度和开模行程的校核
• 2)开模行程(s) • 注塑机的开模行程是有限制的,取出制件所需要的开模距
离必须小于注塑机的最大开模距离。
•核定条件:S模具 < S机max
• 开模距离可分成两类情况校核: • 注射机最大开模行程与模厚无关时的校核
• 注射机最大开模行程与模厚有关时的校核
PPT文档演模板
模具与注射机的关系
① 注塑机最大开模行程与模厚无关时的校核
• 如图所示
PPT文档演模板
模具与注射机的关系
•① 注塑机最大开模行程与模厚无关时的校核
单分型面 图5-64
• S≥S=H1 + H2 +5~10 (mm)
- 1、下载文档前请自行甄别文档内容的完整性,平台不提供额外的编辑、内容补充、找答案等附加服务。
- 2、"仅部分预览"的文档,不可在线预览部分如存在完整性等问题,可反馈申请退款(可完整预览的文档不适用该条件!)。
- 3、如文档侵犯您的权益,请联系客服反馈,我们会尽快为您处理(人工客服工作时间:9:00-18:30)。
3.注射机的选择与较核
定位圈(环)作用:保证主流道中心线与喷嘴中心线重合
定位圈与注射机相关尺寸:定位圈外径和定位圈喷嘴孔尺寸:d=d1+0.5~1mm
A·P型≤F
式中A为塑件加注系统在分型面上的投影面积(mm2),P是型腔内塑料熔体的单位面积压力(MPa),F是注射机额定锁模力.
二:模具的设计
各种型号的注塑机安装模具部位的形状和尺寸各不相同。设计模具时应校核的主要项目有:喷嘴尺寸、定位圈尺寸、最大模厚、最小模厚、模板的平面尺寸和模具安装用螺钉孔位置尺寸等。
1.
2.模具与注射机安装部分相关尺寸的校核
①设计模具的长、宽总体尺寸时要与注射机模板尺寸和拉杆间距相适应,保证模具能穿过拉杆间的距离装卡到模板上。
②模具的主流道中心线应保证与料筒、喷嘴的中心线相重合,模具上的定位环或定位圈尺寸要与注射机定模板上的定位孔尺寸一致且采用较松的间隙配合,注射机喷嘴的球面半径应与相接触的模具主流道始端的球面半径相吻合。
凹坑半径: R=R1+1~2mm
喷嘴与模具的正确匹配关系如下图
② 注射机开模行程与模厚有关时的校核:
单分型面:S≥H m+H1+H2+5~10; 双分型面:S≥H m+H1+H2+a+5~10
③ 有侧分型抽心时开模行程的校核
当H c﹥H 1+H 2 时:
S﹥ H c + 5~10
当H c≤H 1+H 2 时:
按完成抽芯所需开距小于开模行程
2. 顶出装置的校核
三:模具与注射机的匹配校核
① 注塑机最大开模行程与模厚无关时的校核:
核定条件:S模具 < S机max
单分型面和双分型面
S≥S=H1+H2+5~10(mm) S≥H1+H2+a+5~10(mm)
H1 —脱模距离 a—定模板与浇口板的距离
H2—制品加浇注系统高度
S—注射机的允许开模行程
阶梯制件
对脱模斜度较大或内表面为阶梯状的制件,有时无须顶出型芯的全部高度,即可取出制件,如图所示。此时脱模距H1需视具体情况而定,以制件能顺利取出为度。
1.模具厚度和开模行程的校核
(1)模具厚度(H m)
模具厚度设计必须满足:H min ≤H m ≤ H max
式中H min、H max分别是注射机允许安装的最小和最大模厚(mm).
(2).开模行程(s)
各种注射机的开模行程是有限制的,取出制件所需的开模距离必须小于注射机的最大开模距离。
(3).开模距离分注射机最大开模行程与模厚无关和有关时两类情况进行校核
塑
料
成班级:
型姓名:
机学号:
和
模
具
的
匹
配
关
系
前言:
塑料注射成型机是将热塑性塑料或热固性塑料利用塑料成型模具制成塑料制件的主要成型设备。注射成型能一次成型出形状复杂、尺寸精确和带有嵌件的塑料制品,生产效率高、易于实现自动化。
每副模具只有安装在与其相匹配的注射机上才能进行正常的生产,因此模具设计与所选用的注射机型号关系十分密切。
各种型号的注塑机安装模具部位的形状和尺寸各不相同。设计模具时应校核的主要项目有:喷嘴尺寸、定位圈尺寸、最大模厚、最小模厚、模板的平面尺寸和模具安装用螺钉孔位置尺寸等。
一:塑料注射机的选择
从模具没计角度出发,注射机的技术规范有:
1.最大注射量
注射机的最大注射量是指注射机螺杆或柱塞以最大注射行程对空注射时,一次所能达到的塑料注射量。设计注射模时,塑件加浇注系统凝料所用的塑料量,不应超过最大注射量。对于正常的批量生产,应满足:
Mr≤0.8Mmax (式中Mr是成型塑件说要求的注射量)
2.最大注射压力
每种塑料都有适于成型的压力范围,具体塑件所需成型压力范围不仅与塑料品种有关,也与塑件形状、壁厚及浇注系统断面积大小和长度有关。设计模具时,所要求的成型压力应在注射机所允许的最大注射压力范围内。
3.锁模力
每一台注射机,都有一个额定的锁模力,所设计的模具在注射充模时,分型面张开的总力不能超过这一额定锁模力,可用如下关系式表示: