变速箱壳体消失模铸造工艺与缺陷防止
消失模铸造缺陷产生的原因及解决措施

消失模铸造缺陷产生的原因及解决措施一、消失模铸造缺陷的原因:1.模具设计不合理:模具的设计不合理是导致消失模铸造缺陷的主要原因之一、例如,模具的冷却系统设计不良或者模具结构不稳定,都会对铸件的形状和内部结构造成影响。
2.熔融金属冷却不均匀:熔融金属冷却不均匀也是导致消失模铸造缺陷的一个重要原因。
由于冷却速度不均匀,可能会导致铸件中出现热裂纹、气孔等缺陷。
3.模芯破损或散粘:消失模铸造过程中,如果模芯破损或散粘,会导致熔融金属进入模芯使其变形或者破裂。
4.硅溶胶合成不当:硅溶胶在消失模铸造中被用于形成陶瓷壳体,如果硅溶胶的合成过程不当,可能会导致模具的整体性能下降,从而产生各种缺陷。
5.炭化物形成不完全:在消失模铸造中,树脂炭化后形成的剩余炭化物对于确保铸件的完整性非常重要。
如果炭化物形成不完全,可能会导致铸件出现裂纹、气孔等缺陷。
二、消失模铸造缺陷的解决措施:1.设计合理的模具:在消失模铸造过程中,通过合理设计模具的冷却系统,可以提高铸件的冷却均匀性,减少缺陷的发生。
此外,模具的结构也应当稳定,以确保铸件形状和内部结构的准确性。
2.控制熔融金属温度和冷却速度:通过控制熔融金属的温度和冷却速度,可以减少热裂纹和气孔等缺陷的发生。
合理的工艺参数能够提高铸件的材质均匀性和密度。
3.检查模芯质量:在消失模铸造过程中,应该定期检查模芯的质量,以确保其完整性和稳定性。
如果发现模芯破损或者散粘,应及时更换或修复。
4.合理合成硅溶胶:在合成硅溶胶的过程中,应严格按照工艺要求进行操作。
确保硅溶胶的质量和性能,以避免模具整体性能下降。
5.控制炭化物的形成:合理控制炭化物的形成可以避免铸件的裂纹和气孔等缺陷的发生。
在树脂炭化的过程中,应注意控制炭化的温度和时间,确保炭化物的形成充分和均匀。
综上所述,消失模铸造缺陷的产生原因有模具设计不合理、熔融金属冷却不均匀、模芯破损或散粘、硅溶胶合成不当以及炭化物形成不完全等因素。
消失模铸造缺陷产生的原因及解决措施

一、浇注反喷、冒黑烟产生原因:1、浇杯潮湿2、白模密度大3、粘结用胶及表面修补太多4、涂料透气性不好5、砂箱内负压太低、砂箱网堵住6、模型没烘干解决措施:1、浇杯要烘烤(600。
保温1小时)并保持干燥2、降低白模密度(22-25g∕1)3、减少粘结用胶提高白模表面质量减少修补4、合理控制涂料厚度(小件1.2mm,浇道2.0mm,大件1.5-1.8mm,浇道2.5mm),提高涂料的透气性5、增加砂箱内的负压,不低于0∙045Mpa,更换砂箱网6、降低烘房湿度(20%以下),延长烘干时间二、砂孔产生的原因:1、浇包的砂2、浇杯没放好进砂3、浇道没组粘好进砂4、涂料薄或模型破裂进砂5、局部不紧实6、面砂太多随流进砂7、负压太低解决措施:1、修补好浇包2、浇杯下面封泥条后安放稳妥3、组粘好浇道后用快干涂料或泥条涂敷4、合理涂料的厚度损坏的模型不要装箱5、局部不易振实部位要预先填水玻璃砂6、面砂高度80mm左右,浇杯高度要高于面砂高度20mm以上7、负压低产生的塌箱进砂三、碳渣产生的原因:1、白模密度大2、粘结用胶太多及表面修补太多3、砂箱内负压低抽气率低4、浇注温度低5、涂料透气性差6、成分或球化孕育不当7、浇注速度没控制好8、白模气化后残渣多9、工艺不合理解决措施:1、降低白模密度2、提高白模表面质量减少修补量及粘结胶量3、增加砂箱内负压提高抽气率反喷会产生碳渣4、提高浇注温度,减少浇注过程温度损失5、合理化碳含量控制铸钢表面增碳6、合理涂料的透气性7、合理控制铸件成分及提高球化孕育效果8、合理浇注速度使其快速充型9、模型按要求烘干10、选用共聚料I1合理工艺尽量采取顶注方式,铸钢先烧后浇四、涂料产生的缺陷:1、涂料孔洞2、强度不够3、涂料不干4、涂料易返潮5、涂料透气性6、耐火度7、涂料厚度8、涂料变质解决措施:2、提高涂料1、局部不易振实部位及尖角部位涂料脱落造成的涂料孔(一般伴随有砂孔)的常温高温强度防止变形粘砂等缺陷3、确保涂料干燥4、涂料配制合理注意返潮5、合理涂料透气性6、耐火度高涂料不剥壳低了易粘砂7、根据铸件情况确定涂料厚度8、加防腐剂等措施防止变质五、粘砂产生的原因:1、涂料强度差不够2、涂料的骨料粉粗或者砂子粗引起机械粘砂粘涂料3、高温粘砂4、涂料厚度不够5、局部振实不好粘砂6、负压与温度与涂料的技术参数不对粘砂7、模型不干解决措施:1、合理涂料配方提高涂料强度2、合理选用骨料及型砂(批量换新砂时要注意)3、根据铸件壁厚情况选择合理的浇注温度,根据模型选择涂料厚度4、不易振实部位预填砂5、根据负压涂料厚度温度合理选择参数6、确保模型干燥六、渣孔产生的原因:1、炉渣2、拦渣不好3、炉辅料4、化学反应渣5、燃烧残渣6、随流产生的渣解决措施:1、出炉前炉内浇包内除渣2、浇注时茶壶包防渣或包咀硅酸铝纤维板拦渣3、用干净无锈蚀的原料4、球化孕育后要扒渣5、白模粘结修补尽量少6、浇包咀勤修,浇注工艺合理减少冲刷等七、塌箱产生的原因:1、负压太低2、浇注速度慢3、涂料厚度不够4、没有振实到位5、工艺设计不合理6、浇注温度解决措施:1、提高负压2、合理浇注速度3、增加涂料厚度4、不易振实部位预填砂,提高振实度5、合理设计浇注系统(避免大的水平面)6、根据铸件情况选择浇注温度八、铁豆、多肉、橘皮产生的原因:1、涂料产生气泡,露白产生铁豆2、朝下平面涂料剥离产生多肉3、局部振实不良产生粘砂多肉4、靠近模型的砂子中有杂物产生多肉5、浇温低薄壁件浇道附近橘皮解决措施:1、合理搅拌涂料,涂挂防止露白,露白的要补涂2、涂料朝下平面要注意涂料凸出剥离3、不易振实部位预填振实一定要紧实4、砂子除杂等5、薄壁件提高浇注温度。
消失模铸造缺陷及解决措施

铸造缺陷及解决措施:1、砂眼(或白灰):是铸件的致命缺陷,重则报废。
要做到:①、浇口杯、直浇道、横浇道、内浇道与铸件封闭结合严密。
如不严密,在负压的作用下就会吸入砂子,所以装箱者一定要精心操作,把好各关口。
任何一个薄弱环节或疏忽都会造成此类缺陷。
②浇注系统多刷一遍涂料以增强其强度。
③涂料的强度、透气性、刚度、耐火度、暴热抗烈性也很重要,因为在运输、装填砂、震动时都会出现破坏、变形、开裂、脱落。
④震实时,开始幅度要小,待填满砂时再振幅大些。
⑤浇口杯无浮砂、尘土等杂物。
⑥浇注时,浇包嘴尽量靠近浇口杯,以免压力头过大。
⑦负压过大,使金属液流经开裂、裂纹处时,吸入干砂和杂物可能性加大,粘砂严重。
⑧过快的充型速度使冲刷力加大。
2、气孔:①浇注温度低,充型前沿金属液不能使泡沫充分分解汽化,未分解的残留物质来不及浮集到上面及冒口中,汽化分解生成的气体及残留物不能及时排出铸型而凝固在铸件中,另外,摸样分解不充分,液相残留物会堵塞涂料层,使热解气体排出受阻,腔内形成反压力,充型流动性下降,凝固快。
②涂料透气性差或负压不足,砂子透气性差,不能及时排除型腔内的气体及残留物,在充型压力下形成气孔。
③浇注速度慢,浇口杯未充满,暴露直浇道卷入空气,吸入杂质,形成携裹气孔和渣孔。
④浇杯容量小,金属液形成涡流,侵入空气生成气孔。
⑤浇口杯及浇注系统之间的连接处密封不好,尤其是直浇道和浇口杯。
在负压作用下很容易形成夹砂及气孔。
⑥型砂粒度太细,粉尘含量高,透气性差,负压管道内部堵塞,造成负压度失真,使型腔周围的负压值远低于指示负压,汽化物不能及时排出涂料层而形成气孔或皱皮。
⑦合理的浇注工艺和负压度。
消失模浇注工艺是以充满封闭直浇道为原则,不能忽快忽慢、紊流、断流,更不允许暴露直浇道。
浇注速度,尤其是在行车提升停顿瞬间力求平衡,不断流。
进入尾期慢慢收包,使渣、气、及汽化残留物有充分时间浮集到浇冒口中。
负压度过大,加剧金属液渗透粘砂,并造成附壁效应,不利于液相泡沫被涂层吸附,生成很多气孔。
消失模铸件易出现的缺陷及消除措施

消失模铸件易出现的缺陷及消除措施―攀枝花钢铁研究院试验中心陈建钢1、粘砂金属液渗入型砂中,形成金属与型砂的机械混合物,其中有两种情况:一种是金属液通过涂层开裂处渗入型砂中,形成铁包砂(即机械粘砂),此种缺陷一般可以清除掉;另一种情况是金属透过涂层渗入型砂中,形成难以清除的化学粘砂。
(一)产生的原因(1)在涂层开裂的情况下,由于型砂紧实度不够,型砂颗粒过大及真空度过高产生第一种粘砂情况;(2)在涂层过薄或局部未刷到的情况下,由于金属液温度较高,真空度较大时产生第二种粘砂。
(二)防止措施(1)提高涂层的厚度和耐火度。
(2)造型时紧实力不宜过大以免破坏涂层。
(3)选择合适的负压。
(4)选用较细的原砂。
(5)浇注温度不宜过高。
(6)选择合适的压力头。
2、气孔(一)气孔的分类(1)浇注时卷入空气形成的气孔。
(2)泡沫塑料模样分解产生的气孔。
(3)模样涂层不干引起的气孔。
(4)金属液脱氧不好引起的气孔。
(二)浇注时卷入空气形成的气孔消失模铸造浇注过程中如果直浇道不能充满就会卷入空气,这些气体若不能及时排出,就有产生气孔缺陷的可能。
防止卷入气体的措施:(1)采用封闭式的浇注系统。
(2)浇注时维持浇口盆内有一定的液体金属以保持直浇道处于充满状态。
(3)正确掌握浇注方法,采用慢—快—慢的浇注方法。
(三)泡沫塑料模样分解产生的气孔EPS和STMMA热解后产生大量的气体,如果充型平稳,金属与模样逐层置换,这些气体就会顺利通过液体前沿与模样间的气隙经铸型排出,特别在铸型处于负压状态下更有利气体排放,铸件不易产生气孔缺陷。
但是如果充型过程产生紊流或者顶注,侧注情况下、部分模样被金属液包围后进行分解产生的气体不能从金属液中排出时就会产生缺陷,这种气孔表面有炭黑存在。
防止措施:(1)改进浇注方案,使充型过程逐层置换,不产生紊流。
(2)提高浇注温度。
(3)在不发生紊流的情况下,适当提高真空度,如果发生紊流而产生气孔时,可适当降低真空度。
消失模工艺箱体件类铸件缺陷的防止措施
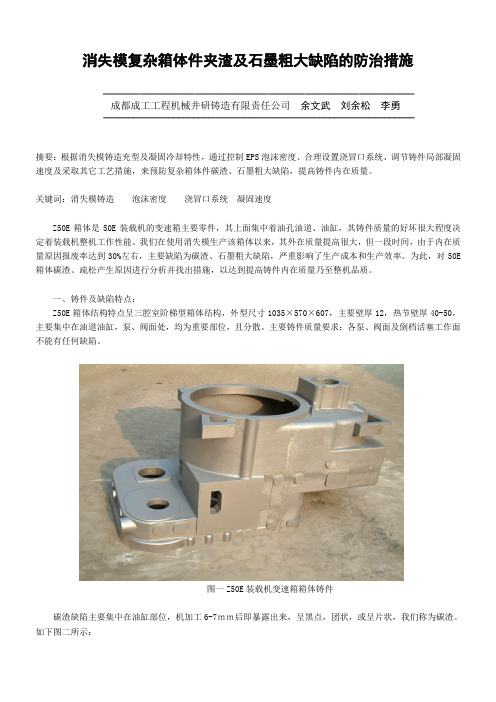
消失模复杂箱体件夹渣及石墨粗大缺陷的防治措施_________________成都成工工程机械井研铸造有限责任公司余文武刘余松李勇______________________________________________________________摘要:根据消失模铸造充型及凝固冷却特性,通过控制EPS泡沫密度、合理设置浇冒口系统、调节铸件局部凝固速度及采取其它工艺措施,来预防复杂箱体件碳渣、石墨粗大缺陷,提高铸件内在质量。
关键词:消失模铸造泡沫密度浇冒口系统凝固速度Z50E箱体是50E装载机的变速箱主要零件,其上面集中着油孔油道、油缸,其铸件质量的好坏很大程度决定着装载机整机工作性能。
我们在使用消失模生产该箱体以来,其外在质量提高很大,但一段时间,由于内在质量原因报废率达到30%左右,主要缺陷为碳渣、石墨粗大缺陷,严重影响了生产成本和生产效率。
为此,对50E 箱体碳渣、疏松产生原因进行分析并找出措施,以达到提高铸件内在质量乃至整机品质。
一、铸件及缺陷特点:Z50E箱体结构特点呈三腔室阶梯型箱体结构,外型尺寸1035×570×607,主要壁厚12,热节壁厚40-50,主要集中在油道油缸,泵、阀面处,均为重要部位,且分散。
主要铸件质量要求:各泵、阀面及倒档活塞工作面不能有任何缺陷。
图一Z50E装载机变速箱箱体铸件碳渣缺陷主要集中在油缸部位,机加工6-7mm后即暴露出来,呈黑点,团状,或呈片状,我们称为碳渣。
如下图二所示:图二 Z50E箱体铸件油缸(倒档活塞工作面)部位碳渣缺陷石墨粗大缺陷主要集中在油缸(倒档活塞工作面)及泵阀面处,主要表现为机加工时有成片灰黑色形似针孔或苍蝇脚,金相检验断面有粗大石墨片。
二、工艺分析及工艺措施消失模铸造较其它铸造工艺方法有着自身特性,金属液充型过程中,流动前沿界面上,发生着不同于其它铸造工艺方法的一系列的物理、化学反应,金属液与涂层、干砂、泡沫模样之间进行着热量传输,金属液前沿粘度增大,流动性降低,泡沫模样分解、气化过程中产生一定量的固态产物以碳黑形式存在,同时铸件凝固冷却速度较慢。
消失模铸件的缺陷与防治

消失模铸件的缺陷与防治铸件缺陷是导致铸件渗漏和报废的主要原因。
铸件缺陷主要有塌箱、抬箱、壁厚不均匀、变形、冷隔和浇不到、粘砂、气孔、缩孔和缩松、皱皮、珠粒状缺陷、节瘤等。
一、塌箱在浇注过程中铸型局部向下塌陷,金属液不能充满型腔,使铸件不能形成或局部缺肉称为塌箱。
(一)塌箱产生的原因(1)铸型顶部吃砂量过小,真空度不够,液体金属浮力使铸型顶部型砂溃散造成铸件成形不良。
(2)液体金属充型上升速度过慢或停流,使模样与金属前沿间隙过大,铸型内气压与砂型压力总和大于间隙内气压,造成铸型移动和坍塌使铸件成形不良。
(3)砂箱内的原始真空度定的太低,特别是深腔内由于模样壁的阻隔作用,其真空度更低。
(4)浇注过程中由于模样气化产生大量气体,排气过程中,真空度下降且造成砂子流动,损坏涂层使砂子进入型腔。
(5)砂温过高(大于70 C),把模样烫坏导致垮砂。
(二)主要防止措施(1)增加铸型顶部吃砂量及在铸型顶部放置压铁,防止液体金属浮力过大造成铸型上面溃散(2)采用合适的真空度(即浇注前真空度不低于-0.06MPa、浇注后真空度不低于-0.05MPa)及密封措施,以保证型砂的强度。
负压系统有足够大的排气能力。
(3)选用强度高透气好的涂料。
(4)选用较粗的原砂增加砂子的透气性。
(5)合理的设计浇注系统。
直浇道面积大于内浇道面积,直浇道不能与铸件距离太近,内浇道长度至少为25mm。
(6)选用低密度的泡沫塑料模(低于26kg/m3)和减少热熔胶的使用量,减少发气量。
(7)砂温不高于70C。
二、抬箱在浇注过程中铸型上表面向上移动,使铸件上部出现全部或局部多肉称为抬箱。
(一)抬箱产生的原因(1)砂箱内真空度偏低,型砂强度不够。
(2)浇注完后,真空度消失过早。
(3)铸件上面吃砂量太少,压力太小。
(二)主要防止措施(1)保证砂箱内有足够的真空度。
(2)浇注后,真空保持时间不少于3min。
(3)造型时,保证铸件上面的型砂高度大于200mm三、变形铸件几何形状与图样不符,诸如铸件弯曲弯曲变形、椭圆、壁厚不均等。
变速箱壳体消失模铸造工艺与缺陷防止

法在 实 际铸造 过程 中,有 效避 免 了上述 问题 ,且取 得 了 良
好 的效 果,要注 意 的是 ,竹 片数 量 的多少 一 定要按 照模 样
的具 体 情 况 而 定 。
3 . 2 碳缺陷 碳缺 陷主 要表 现在铸 铁 件顶面 和侧 面 ,以黑 色夹杂 缺 陷为判 断标 准 。碳 缺陷 产生 的原 因是金 属液 充型 速度 比热 解 产物 气化 及排 出速度 快 ,会 出现一层 与沥 青状 相似 的粘 稠 物质 覆盖 在金 属液 表面 。如果 前沿温 度低 ,后 续在金 属 液流动 作用 的推 动 下,粘稠 液就 会被推 到铸 件侧 面 ,最 终
因此在 挂涂 、埋 型等各 个环 节熔 体易 发生变 形 。针 对 于该 问题 ,可 以采 取 三种试 用解 决方 案:第 一种 就是在 经过 挂 涂烘 干处理 后 ,将 强 筋框架 安置 于模 样 的轮 廓外 部 ,框架 的尺 寸与模 样 的外部 轮廓 相符 合 ,采 用钢 筋焊接 而成 ;第
关键 词 :变速 箱壳体 消失模 铸造 形 变 碳 缺 陷 粘砂
消 失 模 铸 造 技 术 在 我 国普 遍 使 用 是 2 0世 纪 末 ,采 用 该 技术的企业越来越 多, 产 量也越来越大 。 为 了满 足 生 产 需 要 ,
要把 握好节奏 ,一快一 慢地对每件铸件进 行浇注 。
3 主 要 缺 陷 及 防止 方 法
将 会 减 小 。科 学 地 设 置 位 置 , 能 将 这 两 股 金 属 液 共 同集 聚 在 铸 件 的 端 部 , 为 了搜 集 铸 造 过 程 中产 生 的 废 渣 , 需 要 在
粘在 一起 ,在对 产 品进 行清 理时 , 比较 困难 ,因此 ,此种
方 法 并 不 理 想 。 第 二 种 方 法 由 于 在 浇 注 过 程 中 , 泡 沫 条 的 位 置 很 大 一 部 分 被 金 属 液 取 代 , 不 仅 增 加 了清 理 难 度 ,而 且 金 属 液 浪 费 较 为 严 重 , 甚 至 会 导 致 铸 件 失 败 ; 第 三 种 方
消失模工艺铸件气孔、渣孔缺陷,是怎么形成的?该如何防止?

消失模工艺铸件气孔、渣孔缺陷,是怎么形成的?该如何防止?本次疫情期间,罗通老师写了一篇关于铸件气孔、渣孔缺陷的文章,洲际铸造平台授权转载!许多消失模铸造厂在生产加工件时特别是碳钢不锈钢件,虽然抛丸后没有什么问题外观也比较理想,可是一加工就出现渣孔气孔,而产生的位置一般在产品的中上部及侧边和浇注系统的对面,夹渣是夹杂缺陷的铁液熔渣和模样残渣。
铸件上二者一般都呈黑色,大小不一,形状很不规则,有块状、片状、线条状等。
一般存在于铸件内部,多见于铸件上表面的皮下和拐角处。
那么泡沫模型气化分解生成大量的气体及残留物不能及时排出铸型,泡沫、涂料层填充干砂的干燥不良,在高温包围下,裂解出大量的氢气和氧气侵入铸件而形成气孔。
产生气孔渣孔的原因一般有以下几种:1,泡沫的水分干燥不透彻就去上涂料,涂料第一遍没干透就去上第二遍,在高温的液体浇注时产生的气孔,2,泡沫的密度过于太大使浇注时来不及气化而吐食泡沫产生的泡沫渣形成渣孔3,钢水脱氧不良、炉台、炉内、包内除渣不净,熔化铁水时,或多或少要产生熔渣,特别是炉料锈蚀严重或采用铁屑熔炼时,产生大量的金属熔渣。
在浇注时熔渣很容易随着铁水进入型腔,留在铸件内部,凝固后就形成黑色夹渣。
由于夹渣的密度比铁水小,一般要浮在铸件上面,铸件拐角处对熔渣有阻碍作用,熔渣上浮时易产生滞留,所以该部位也多见夹渣缺陷。
镇静时间过短,浇注过程中挡渣不力,浇注工艺不合理造成渣孔。
4,由于浇注系统设计不合理,大件小件混合搭配在一个砂型形成了纵横交错,钢水的充型速度大于泡沫气化退让及气体排出速度,造成充型前沿将气化残留物包夹在钢水中再次气化形成内壁烟黑色的分解气孔。
5,浇注温度低,充型前沿钢水不能使泡沫充分气化,未分解的残余物质来不及浮集到冒口而凝固在铸件中形成气孔。
5、内浇道开设位置不合理,充型时形成死角区,由于型腔内气体压力作用,使气化残留物积聚在死角处形成气孔,内浇道截面积过大,而且少使充型速度大于泡沫气化退让速度,吞食泡沫,在合金内部分解气化,而气体无法排出形成气孔。
消失模铸造缺陷有

缩空气喷枪填料时,应适当提高压力和调整进料方
向。
1.1.2模样熔结不良.组合松散
产生原因:
( 1 )蒸汽的热量、温度不够。熟化时
间过长;( 2 )珠粒粒度太小,发泡或发泡剂含量太少;
( 3 )珠粒充型不均匀或未填满模型。
防止措施:
( 1 )控制预发泡粒子比重,控制熟
可实施三个方向振动(三维振动、上下左右前后振
动,如阀体、六通、复杂泵体等)。
( 3 )足够的弹性支撑能力震实台支撑力应大
于砂箱+型砂+台面的重量总和。如果震动台的举重
力(支撑力)小于工作时总重量之和。则影响造型或
根本无法成型甚至松散干砂。严重影响铸件质量。
震动台激振器要具有足够的激振力。使其达到
要求的振幅和振动加速度。
害白模(泡塑模样)状态。
( 1 )有效振动紧实干砂又不损害白模的造
型。采用高频低幅振动。频率3 08 0H Z ( 18 0 0~48 0 0
d mi n ),并根据不同白模布置在充型过程中调整频
率。振幅一般
0.5~
1.5m种
模式,垂直振动和两个方向的水平振动。也可以采用一个方向的振动(如平衬板垂直布置,磨球组串),也
作用:
( 1 )紧实干砂铸型,防止冲砂、铸型崩散及型壁
移动;( 2 )加快排气量和排气速度,降低界面气压加
快流股前沿推进速度,提高充型能力,有利于减少铸
件表面的碳黑缺陷;( 3 )抑制白模材料燃烧,促使其
气化;改善环境;( 4 )增加了流股的流动性,成形性,
( 4 )温度干砂温度应低于3 0~6 o℃。砂温太高
易使白模在造型震实过程中变形、扭曲、凹陷。
消失模铸造缺陷的影响因素及防止措施.

防止措施:(1及时加润滑油,保证模具工作表面光滑; (2修改模具结构,出模斜度,取模样工艺; (3延长模具冷却时间。
1.1.12飞边、毛刺
产生原因:模具在分型面处配合不严或操作时
收稿日期:2006-05-09
Abstract:A detailed description was made on the factors causing defects in EPC process production such as metal spraying, blow hole, too big dimension deviation, deformation, etc. The defect reasons were analyzed and relevant prevention measures were proposed. The principles were introduced for selecting dried sand system,
图4中等壁厚蠕墨铸铁件炉前三角试块
Fig.4Suggested wedge specimen for on-spot
control of vermicular iron castings with medium
thickness
75
A-A
40
A
V型缺口
A
180
!!!!!!!!!!!!!!!!!!!!!!!!!!!!!!!!!!!!!!!
(1.学林科技开发服务部铸造研究室,浙江
杭州
310012; 2.凯斯特化工有限公司,浙江
杭州311106; 3.
变速箱壳体消失模铸造工艺与缺陷防止
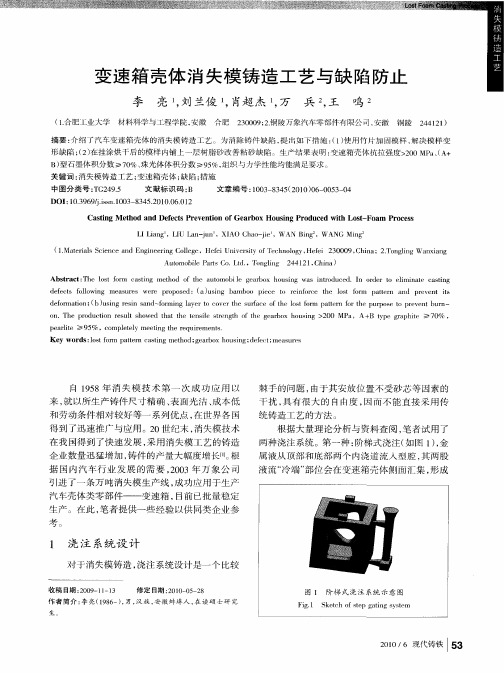
和 劳动条 件相 对 较好 等 一 系列 优点 , 在世 界各 国 得到 了迅 速推 广 与应用 。2 0世纪 末 , 消失 模技 术 在我 国得 到 了快 速发 展 , 用 消失模 工 艺 的铸 造 采 企 业 数量 迅猛 增加 , 件 的产量 大 幅度 增长 l 根 铸 l l 。 据 国 内 汽 车 行业 发 展 的 需 要 ,0 3年 万 象 公 司 20 引进 了一 条万 吨 消失模 生 产线 , 功 应用 于 生 产 成 汽 车壳 体类 零 部件 —— 变 速箱 , 目前 已批 量 稳定 生产 。在此 , 者提 供 一些 经 验 以供 同类 企 业参 笔
d fr t n ( u igr s a d fr n ae o c vrtes rae o els om atr 0 h up s o p’ e tb r — eomai ; b) sn ei s n ~omigly rt o e h ufc ft o t r p t n frte p roe t Iv n un o n h f e e
L in L U L n j n , I O C a -i , I a g , I a -H X A h o j WA ig, L e N B n WA G Mig N n
( . trasS in e a d E gn e i g C l g ,Hee i m’ t f e h o o y Hee 2 0 0 , h n ;2 T n l g W a xa g 1Mae i l c e c n n i e r ol e n e fiUn v s y o c n l g , f i 3 0 9 C i a . o g i n in i T n Auo b l ) t Co L d ,T n l g 2 4 2 , i a) tmo i I rs . t . o gi 4 1 1 Ch n e a n
消失模铸造制动盘夹杂缺陷的防止
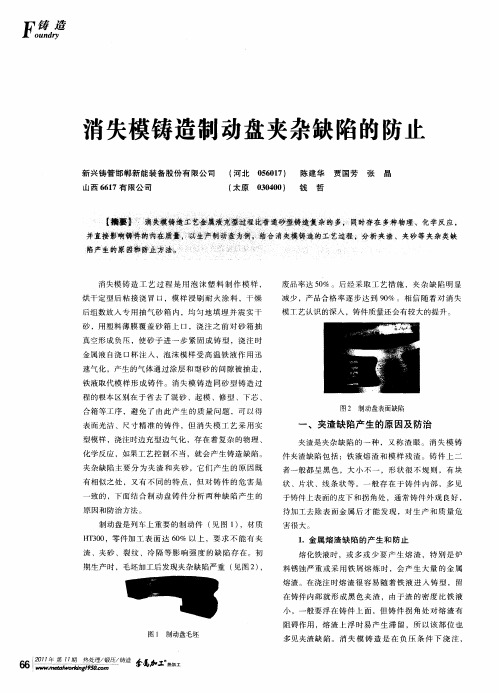
废 品率达 5 % 。后 经 采 取 工 艺措 施 ,夹 杂 缺 陷 明 显 0
2 模 样残渣缺陷的产生和防止 .
消 失模铸 造 在 浇 注 时 ,泡 沫 塑 料 模 样 与 高 温 铁
液发 生强 烈 的 物 理 化 学反 应 ,其 中 以泡 沫 模 样 剧 烈 的热 解气 化 为 主 ,产 生 的 气 体 被 真 空 泵 抽 走 。实 践
也证 明 ,任 何泡 沫塑 料热 解 反应 后 并 不能 全 部气 化 , 最终要 产 生 微量 的 固态 残 余 物 ,俗 称 残 渣 ,其 主 要
铁 液 温 度 提 高 ,有 利 于模
( ) 加强 扒 渣 和挡 渣 工 作 1
在 出 炉 前 ,铁 液 面
样 的充 分 气 化 分解 ,减少 残 渣 量 ,但 提 高 浇 注 温度 应 以防止铸 件粘砂 为前 提 。 ( )使 用 空心 浇 道 4 空 心 浇 道 有 利 于铁 液 的顺
观 区别在 于 :夹 砂 为 白色 颗粒 状 ,大 小 同 砂 粒 ,多 见于 铸件 浇 注位 置 的上 表 面皮 下 。 由于 夹砂 是 铁 液 流动 中冲破 型壁 带人 型砂 所 致 ,边 浇 注边 冲刷 带 人 , 因而铸 件 的其他 部位 往往 也 能 看到 夹 砂 。相 比之 下 ,
减少 ,产 品合 格率 逐 步 达 到 9 % 。相 信 随 着对 消 失 0 模T 艺认识 的深 入 ,铸件 质量 还会有 较大 的提 升 。
消失模薄壁复杂箱变形及夹渣缺陷防止措施

优化发泡模具设计是整个工艺的关键环节之一
发泡模具工艺设计的好与坏,直接影响产品 质量。分块越多,成型发泡相对容易,白模 比重也可控制较轻,这就有利于减少铸件的 夹渣等缺陷,但尺寸精度相对难控制;分块 越少,尺寸相对较好控制,成型发泡就相对 较难,白模比重势必也较高,这就容易造成 铸件的夹渣等缺陷。
2、溢流冒口 气化模在浇注时不断产生溶渣,其随铁水上 流,流经死角容易形成夹渣状缺陷;因此应 在这些地方设计溢流冒口,使其收集残渣和 随浇注系统进入的散砂等。 3、工艺撑子 工艺撑子的设计是防止薄壁复杂箱体类铸件 变形的一个不可缺少的重要环节,其模样密 度及涂料室温强度要较高。
ZL50变矩器 壳体共设计 四个溢流冒 口,见图中4 和6,有效解 决了夹渣类 缺陷。
三、结论
1、适当增加受力部位壁厚、增加工艺补贴、 设计反变形量,能有效防止变形 。 2、发泡模具分块少便于保证铸件尺寸。 3、工艺设计时恰当设置溢流冒口、采用简单 的浇注系统,可有效防止夹渣缺陷。 4、涂料烘烤过程中恰当采用工装定位,能有 效防止涂料环节模样变形 。
谢
谢!
1.直浇道 2、5、8、 9、10工 艺撑子 3、7.溢 流冒口 6.溢流冒 口(共三 处)4.内 浇道 11. 内浇道 (兼工艺 撑子)
未防止变形工艺结构设计作如下调整:D处法兰外型尺 寸增加1mm,内型尺寸缩小1mm,使法兰由25mm增加 为27mm;E处窗口及附处增加壁厚1mm;C处圆弧加工 余量较其它处余量大1mm。
二、铸造工艺设计 1、浇注系统 2、溢流冒口 3、工艺撑子
4、涂料及烘烤工艺
一、铸件结构工艺性设计,发泡模具设计
在进行工艺结构设计的时候,重点考虑消失模铸 造工艺的特殊性,在不影响使用的前提下,适当 增加涂料、造型埋箱过程中受力部位壁厚、工艺 补贴及设计反变形量,有利于防止工艺过程中的 因变形而影响铸件尺寸。 同时还应考虑成型发泡的泡塑珠粒可填料性及造 型振实过程的干砂可填充性,防止因进料不足影 响强度以及因填砂不均匀而造成变形。
消失模铸造常见缺陷的分析与防止

消失模铸造常见缺陷的分析与防止2010-07-23 18:35:56| 分类:默认分类| 标签:|字号大中小订阅1.铸铁件表面皱皮(积碳)铸件表面有厚薄不同的皱皮,有波纹状、滴瘤状、冷隔状、渣状或夹气夹杂状等。
波纹状较浅,其余皱皮则较厚、较深。
其表面常呈轻质发亮的碳薄片(光亮碳膜),深凹沟陷处充满烟黑、碳黑等。
皱皮的厚度为0.1一1.0mm,甚至超过10mm,导致铸件报废。
这种缺陷往往在铁液最后流到的部位或液流的“冷端”部位。
大件出现在上部;15-20mm现在侧面或铸件的死角部位,这与浇注系统(顶注、底注、侧注、阶梯注)有关。
当1350-1420℃的铁液注人型内时,EPS或STMMA料模急剧分解,在模样与铁液间成气隙,料模热解形成一次气相、液相和固液气相主要由CO,CO2,H2,CH4,和分子量较小的乙烯及其衍生物组成;液相由苯、甲苯、乙烯和璃态聚苯乙烯等液态烃基组成;固相主要是由聚苯乙烯热解形成的光亮碳和焦油状残留物组成,因固相中的光亮碳与气相、液相形成熔胶粘着液相也会以一定速度分解形成二次气相和固液态中的二聚物、三聚物及存在再聚合物,这当中往往会出现一种粘稠的沥青状液体,这种液分解物残留在涂层内侧,一部分被涂层吸收分在铸件与涂层之间形成薄膜,这层薄膜在还原(CO)气氛下形成了细片状或皮屑状、波纹状的结晶残碳即光亮碳,此种密度较低(疏松)的光碳与铁液的润湿性很差,因此在此铸件表面形成碳沉积(皱皮)。
A.影响因素(1)泡塑模样:模料EPS比EPMMA,STMMA更容易形成皱皮,因为EPS含碳量比后二者高,其中EPS 含碳92% , STMMA(苯乙烯—甲基丙烯酸甲脂共聚树脂)含碳69.6% , EPMMA(可发性聚甲基丙烯酸甲脂)含碳60.0%;此外,模样密度越高体积越大,分解后液相产物越多,越容易产生皱皮。
(2)铸件材料成分的影响:含碳低的铸铁件(合金铸铁),模型分解产物中的碳可以部份溶解其中,不易产生皱皮;含碳高的铸铁(球铁)最易形成皱皮缺陷。
消失模铸件易出现的缺陷及消除措施
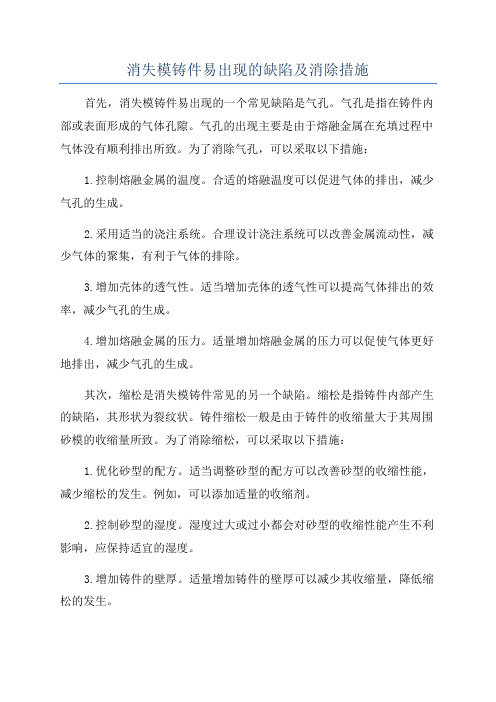
消失模铸件易出现的缺陷及消除措施首先,消失模铸件易出现的一个常见缺陷是气孔。
气孔是指在铸件内部或表面形成的气体孔隙。
气孔的出现主要是由于熔融金属在充填过程中气体没有顺利排出所致。
为了消除气孔,可以采取以下措施:1.控制熔融金属的温度。
合适的熔融温度可以促进气体的排出,减少气孔的生成。
2.采用适当的浇注系统。
合理设计浇注系统可以改善金属流动性,减少气体的聚集,有利于气体的排除。
3.增加壳体的透气性。
适当增加壳体的透气性可以提高气体排出的效率,减少气孔的生成。
4.增加熔融金属的压力。
适量增加熔融金属的压力可以促使气体更好地排出,减少气孔的生成。
其次,缩松是消失模铸件常见的另一个缺陷。
缩松是指铸件内部产生的缺陷,其形状为裂纹状。
铸件缩松一般是由于铸件的收缩量大于其周围砂模的收缩量所致。
为了消除缩松,可以采取以下措施:1.优化砂型的配方。
适当调整砂型的配方可以改善砂型的收缩性能,减少缩松的发生。
例如,可以添加适量的收缩剂。
2.控制砂型的湿度。
湿度过大或过小都会对砂型的收缩性能产生不利影响,应保持适宜的湿度。
3.增加铸件的壁厚。
适量增加铸件的壁厚可以减少其收缩量,降低缩松的发生。
4.增加充填缓慢度。
适当降低熔融金属的充填速度可以减少金属流动过快造成的收缩不均,减少缩松的发生。
此外,消失模铸件还可能出现其他缺陷,如未充填、冷隔离、裂纹等。
为了消除这些缺陷,可以采取以下措施:1.控制熔融金属的温度。
适当降低熔融金属的温度可以减少未充填和冷隔离的发生。
2.增加砂型的强度。
优化砂型的配方、增加砂型的固化时间和温度,以及采用合适的固化剂等措施可以提高砂型的强度,减少裂纹的发生。
3.控制熔融金属的充填速度。
适当降低金属的充填速度可以减少未充填和冷隔离的发生。
4.增加浇注口的大小。
适当增加浇注口的大小可以改善金属的流动性,减少未充填和冷隔离的发生。
综上所述,消失模铸件易出现的缺陷包括气孔、缩松、未充填、冷隔离等。
针对这些缺陷,可以采取相应的措施来消除,如控制熔融金属的温度和压力、优化砂型的配方和固化条件、增加浇注口的大小等。
变速箱、后桥壳体消失模铸造工艺研究
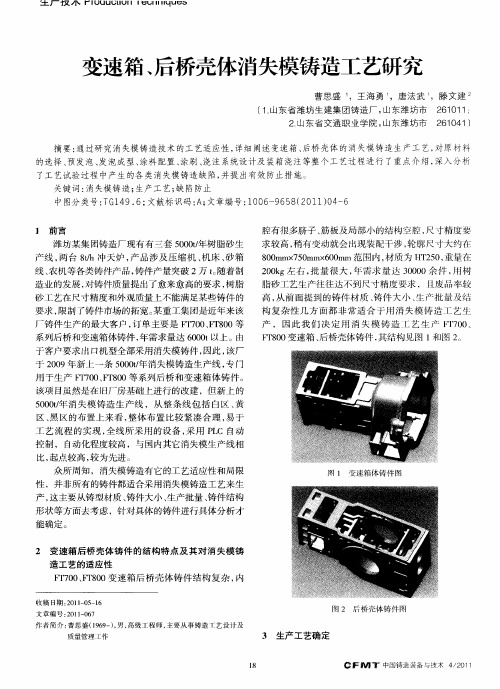
用 于生产 F 70 F' 0等系列后桥和变速箱体铸件 。 T 0 、I0 8
该 项 目虽 然是在 旧厂房基 础上 进行 的 改建 ,但新 上 的 5 0 年 消 失 模 铸 造 生 产 线 ,从 整 条 线包 括 白 区 、 0 ̄/ 黄
区、 黑区的布置上来看 , 整体布置 比较紧凑合理 , 易于 工 艺 流程 的实 现 , 线 所 采 用 的 设备 , 用 P C 自动 全 采 L
2 11 ; 6 0 1
2 14 ) 6 0 1
摘要: 通过研究消失模铸造技术的工艺适应性, 详细阐述变速箱、 后桥 壳体的消失模铸造生产工艺, 对原材料
的选择 、 预发 泡 、 发泡 成 型 、 涂料 配 置 、 刷 、 涂 浇注 系统设 计及 装 箱浇注 等整 个 工 艺过程 进行 了重 点介 绍 , 深入 分析 了工 艺试验 过程 中产 生的各 类消 失模铸 造缺 陷, 并提 出有 效 防止措 施 。
311 模 样材 料 ..
模 样材 料主要 有两种 ,即聚苯 乙烯 ( xedb E pn al e pl t ee , o s r )简称 E S yy n P 和聚 甲基丙烯酸 甲酯( P M ) E M A
和共 聚料 (T S MMA) 类 。前 者价 格 比较低 , 型 加 工 两 成
Pr d c inT c nq e o u t e h iu s生 严 技 术 o
31 原 材料 的 选择 .
数: 铸件加工余量底侧面取 5 m, a r 顶面取 6 m, m 模具收
缩 率包 括泡 沫模 样 的收缩 和 铸件 的 收缩 ,长 度方 向取 1 % , 度 方 向取 05 高度 方 向取 1 %。另外 , 具 . 宽 6 .%, . 0 模
消失模铸造薄壁复杂箱体类铸件变形及夹渣缺陷的防止措施

消失模薄壁复杂箱体类铸件变形及夹渣缺陷的解决措施一、铸件结构工艺性设计,发泡模具设计箱体类铸件塑料模样在加工制作、挂涂料、搬运、造型、振实、抽真空过程中,容易变形,因此要求铸件结构应尽可能紧凑、刚性好。
在进行工艺结构设计的时候,除考虑传统性铸造结构要求外,最重要一点就是重点考虑消失模铸造工艺的特殊性,在不影响使用的前提下,适当增加涂料、造型埋箱过程中受力部位壁厚、工艺补贴及设计反变形量,有利于防止工艺过程中的因变形而影响铸件尺寸。
同时铸件结构设计还应考虑成型发泡的泡塑珠粒可填料性及造型振实过程的干砂可填充性,防止因进料不足影响强度以及因填砂不均匀而造成变形。
ZL50变矩器壳体(见图三、四)结构工艺性设计时由于D面法兰、E面窗口、C处圆法兰,造型埋箱时以经常容易变形,所以结构设计作如下调整:D处法兰外型尺寸增加1mm,内型尺寸缩小1mm,使法兰由25mm增加为27mm;E处窗口及附处增加壁厚1mm;C处圆弧加工余量较其它处余量大1mm。
图一 图二ZL50E 箱体原发泡模具设计方案(部分) ZL50E 箱体现发泡模具设计方案(部分)发泡模具工艺设计的好与坏,直接影响产品质量。
分块越多,成型发泡相对容易,白模比重也可控制较轻,这就有利于减少铸件的夹渣等缺陷,但尺寸精度相对难控制;分块越少,尺寸相对较好控制,成型发泡就相对较难,白模比重势必也较高,这就容易造成铸件的夹渣等缺陷。
因此,优化发泡模具设计是整个工艺的关键环节之一。
我们刚试制ZL50E 箱体时,整套模具设计成18块,组合较复杂,经常因尺寸偏差造成铸件报废,见图一,外形由四大块组成。
所以,我们后来将整套模具设计成8块,见图二,外形减少为三大块,取消了部分组合工装,生产效率提高了,表面质量因也少一道分模面而提高了,更重要的是尺寸能很好控制,曾经几个月生产无一件ZL50E箱体铸件因尺寸原因而报废。
为了保证ZL50变矩器壳体铸件尺寸,发泡模具设计成两大块,见图三A、B两部分,两块模样采用圆形止口定位,分块少,组合效率高,尺寸能得到有效保证。
变速箱壳体消失模铸造工艺与缺陷防止

变速箱壳体消失模铸造工艺与缺陷防止
李亮;刘兰俊;肖超杰;万兵;王鸣
【期刊名称】《现代铸铁》
【年(卷),期】2010(030)006
【摘要】介绍了汽车变速箱壳体的消失模铸造工艺.为消除铸件缺陷,提出如下措施:(1)使用竹片加固模样,解决模样变形缺陷;(2)在挂涂烘干后的模样内铺上一层树脂砂改善粘砂缺陷.生产结果表明:变速箱壳体抗拉强度>200 MPa、(A+B)型石墨体积分数≥70%、珠光体体积分数≥95%,组织与力学性能均能满足要求.
【总页数】4页(P53-56)
【作者】李亮;刘兰俊;肖超杰;万兵;王鸣
【作者单位】合肥工业大学,材料科学与工程学院,安徽,合肥,230009;合肥工业大学,材料科学与工程学院,安徽,合肥,230009;合肥工业大学,材料科学与工程学院,安徽,合肥,230009;铜陵万象汽车零部件有限公司,安徽,铜陵,244121;铜陵万象汽车零部件有限公司,安徽,铜陵,244121
【正文语种】中文
【中图分类】TG249.5
【相关文献】
1.传动箱体消失模铸造工艺中的缺陷问题 [J], 张家骏;赵清祯;郭洪钢;谭建波
2.变速箱壳体消失模铸造工艺与缺陷防止 [J], 刘腊勤
3.灰铸铁薄壁类变速箱壳体消失模铸造工艺的优化 [J], 扈广麒;杨争光;朱文文
4.消失模铸造工艺技术讲座(六)——第六讲常见铸造缺陷及防止方法 [J], 李传栻
5.消失模铸造工艺技术讲座(一)——第一讲怎样认识消失模铸造工艺 [J], 李传栻因版权原因,仅展示原文概要,查看原文内容请购买。
消失模铸造浇注注意事项及塌箱防治方案

消失模铸造浇注注意事项及塌箱防治方案一、消失模铸造浇注注意事项进行消失模铸造有一定的规范和要求,造型工艺中要注意以下方面:消失模铸造使用的一般是硅砂,要求其二氧化硅量在85%~90%以上。
从透气性和耐火度方面考虑,铸钢、铸铁件一般选用粒径0.850~0.300mm的硅砂。
先在砂箱底布上一层厚度约100mm的干砂,然后将刷有涂料的EPS模及浇冒口放置在砂箱中央,边填砂边震实,直到干砂离砂箱顶面50mm左右时停止加砂,在干砂上面覆盖塑料薄膜,然后将浇口杯置于直浇口顶端,并在薄膜上撤上一层散砂,以防止浇注时铁水溅落,烧穿薄膜导致漏气塌箱。
浇注在消失模铸造工艺中,整个工艺流程包括七个环节,每个环节对于消失模铸件质量都具有很大的影响作用,当然浇注过程也是整个消失模铸造工艺流程中至关重要的一环,掌握浇注工艺注意事项,严格把控浇注工艺中的每个细节是生产高质量消失模铸件的关键。
消失模铸造的浇注过程是钢液充型,同时泡塑模具汽化消失的过程。
整个过程中需要注意的是:(1)浇道自始至终要冲满钢液,如若不满,由于涂料层强度有限,很容易发生型砂塌陷以及进气现象,造成铸件缺陷。
(2)浇筑钢液时一定要把握住,保证做到稳、准、快。
瞬时充满浇口杯,并做到快速不断流,吨钢液在大约一分钟左右。
如果同箱铸件的钢液断流会吸进空气,有可能引起塌砂现象或者铸件增多气孔的问题,导致铸件报废。
(3)消失模铸造采用负压封闭式,而且必须是在浇口杯以下封闭。
钢液进入模塑模具,其开始液化燃烧,并气化消失,钢液前端短距离形成暂时的空腔,所以设计钢液充型的速度和泡塑模型消失的速度大致相同。
为防止钢液高温辐射熔化同箱其它模型,浇道适当离铸件模型远一点。
立浇道的位置选择整箱铸件最低位置。
浇注时注意调节和控制负压真空度在一定范围内,浇注完毕后保持在一定负压状态下一段时间,负压停止、钢液冷凝后出箱。
防止返喷消失模铸造是铸造工艺中的一种,在铸造工艺中会存在种种铸造缺陷,从而导致铸造件的缺陷,消失模铸造也不例外。
变速箱壳体消失模铸造工艺与缺陷防止

王林慧 1 ,张宝庆 2,袁东洲 3 ,裴虎平 4,王国平 3
(1.山西晋城市春晨兴汇实业公司,山西 晋城 048012;2.郑州机械研究所,河南 郑州 450052;3.晋城市金珂铸业制 造有限公司,山西 晋城 048012;4.晋城市鑫金铸造有限公司,山西 晋城 048012)
33碳缺陷碳缺陷是消失模铸造特有的铸造缺陷该项缺陷约占整个铸件缺陷的50在消失模铸铁件中表现尤为特殊成为制约消失模技术发展的瓶颈技术消失模铸造铸铁件的碳黑缺陷是最常见的一种碳缺陷表现为在铸铁件侧面或顶面有时在内剖面上出现黑色的夹杂缺陷
Lost Foam Casting Process 消 失 模 铸 造 工 艺
消失模铸造铸铁件的碳黑缺陷是最常见的 一种碳缺陷,表现为在铸铁件侧面或顶面(有时 在内剖面上)出现黑色的夹杂缺陷[4]。当金属液的
配置。在排除人为错误操作的基础上,确保每个 工位都要严格按照工艺流程卡既定参数操作,是 稳定产品合格率的关键。万象公司生产的变速箱 壳体牌号为 HT200,其性能和组织为:抗拉强度> 200 MPa、(A+B) 型石墨体积分数≥70%(见图 6)、珠光体体积分数≥95%(见图 7),均能满足购 货方的要求。
关键词:消失模铸造;夹砂、夹渣缺陷;对策
中图分类号:TG249.5;TG250.6
文献标识码:B
文章编号:1003-8345(2010)06-0056-03
DOI:10.3969/j.issn.1003-8345.2010.06.013
Sand Inclusion and Slag Inclusion Formation Reasons and Countermeasures of Lost foam Castings
- 1、下载文档前请自行甄别文档内容的完整性,平台不提供额外的编辑、内容补充、找答案等附加服务。
- 2、"仅部分预览"的文档,不可在线预览部分如存在完整性等问题,可反馈申请退款(可完整预览的文档不适用该条件!)。
- 3、如文档侵犯您的权益,请联系客服反馈,我们会尽快为您处理(人工客服工作时间:9:00-18:30)。
[3]解明国.消失模铸铁件碳缺陷的分析与研究[D].合肥:合肥工 业大学,2004:7-8.
2010 / 6 现代铸铁 55
消 Lost Foam Casting Process 失 模 铸 造 工 艺
Abstract:The lost form casting method of the automobi le gearbox housing was introduced. In order to eliminate casting defects following measures were proposed:(a)using bamboo piece to reinforce the lost form pattern and prevent its deformation;(b)using resin sand-forming layer to cover the surface of the lost form pattern for the purpose to prevent burnon. The production result showed that the tensile strength of the gearbox housing >200 MPa,A +B type graphite ≥70% , pearlite ≥95%,completely meeting the requirements. Key words:lost form pattern casting method;gearbox housing;defect;measures
消失模铸件夹砂和夹渣缺陷的成因及对策
王林慧 1 ,张宝庆 2,袁东洲 3 ,裴虎平 4,王国平 3
(1.山西晋城市春晨兴汇实业公司,山西 晋城 048012;2.郑州机械研究所,河南 郑州 450052;3.晋城市金珂铸业制 造有限公司,山西 晋城 048012;4.晋城市鑫金铸造有限公司,山西 晋城 048012)
涂料本身强度不足造成粘砂;⑦人为操作不当造 尽量降低 w(C)量。
成粘砂,等。
⑤型砂的透气性:用 25~30AFS、透气性为
根据大量的理论分析,并结合万象公司生产 13.5~16.5 cm2/Pa·min 的硅砂,砂温≤45 ℃,含水
铸件的实际情况,采用了如下措施:在挂涂烘干后 量≤3%。
的模样内铺上一层特配的自硬树脂砂 (命名为Ⅰ
形缺陷;(2)在挂涂烘干后的模样内铺上一层树脂砂改善粘砂缺陷。生产结果表明:变速箱壳体抗拉强度>200 MPa、(A+
B)型石墨体积分数≥70%、珠光体体积分数≥95%,组织与力学性能均能满足要求。
关键词:消失模铸造工艺;变速箱壳体;缺陷;措施
中图分类号:TG249.5
文献标识码:B
文章编号:1003-8345(2010)06-0053-04
自 1958 年消失模技术第一次成功应用以 来,就以所生产铸件尺寸精确、表面光洁、成本低 和劳动条件相对较好等一系列优点,在世界各国 得到了迅速推广与应用。20 世纪末,消失模技术 在我国得到了快速发展,采用消失模工艺的铸造 企业数量迅猛增加,铸件的产量大幅度增长[1]。根 据国内汽车行业发展的需要,2003 年万象公司 引进了一条万吨消失模生产线,成功应用于生产 汽车壳体类零部件— ——变速箱,目前已批量稳定 生产。在此,笔者提供一些经验以供同类企业参 考。
充型速度超过热解产物的气化和排出速度时,在
参考文献
金属液的表面就会聚集一层未热解或热解不充 分的沥青状粘稠液态[5]。此时若金属液前沿温度 较低,后续金属液的流动会将粘稠液推向铸件的 侧面,最终使得铸件侧面形成细片状或皮屑状碳 缺陷。
[1]梁光泽.我国实型(消失模)铸造的应用与发展[J].特种铸造及 有色金属,2003,(2):54-55.
收稿日期:2009-11-13
修定日期:2010-05-28
作者简介:李亮(1986-),男,汉族,安徽蚌埠人,在读硕士研究
生。
2010 / 6 现代铸铁 53
消 Lost Foam Casting Process
失
模
铸
造
工
图 2、图 3 所示冷隔类皱皮缺陷。
艺
在相同条件下,合理的直浇道长度以及适宜
⑥真空度:负压控制在-55~-40 KPa。
型),在铸件拐角、死角处铺厚些。模样做过此种处
理后所浇出的铸件粘砂缺陷有很大改观,在工人 4 结束语
不违规操作的情况下,粘砂缺陷基本可以杜绝。
一个合格铸件的生产,需要每道工序的合理
3.3 碳缺陷 碳缺陷是消失模铸造特有的铸造缺陷,该项
缺陷约占整个铸件缺陷的 50%,在消失模铸铁件 中表现尤为特殊,成为制约消失模技术发展的 “瓶颈”技术[3]。
消失模铸造铸铁件的碳黑缺陷是最常见的 一种碳缺陷,表现为在铸铁件侧面或顶面(有时 在内剖面上)出现黑色的夹杂缺陷[4]。当金属液的
Hale Waihona Puke 配置。在排除人为错误操作的基础上,确保每个 工位都要严格按照工艺流程卡既定参数操作,是 稳定产品合格率的关键。万象公司生产的变速箱 壳体牌号为 HT200,其性能和组织为:抗拉强度> 200 MPa、(A+B) 型石墨体积分数≥70%(见图 6)、珠光体体积分数≥95%(见图 7),均能满足购 货方的要求。
有应用,每件所用竹片数目根据模样情况而定。 塑料,并对其进行处理,如可向泡沫塑料中加入
3.2 粘砂
适量促进气化和组织燃烧裂解的苯醌、甲基紫、
粘砂是金属液渗出涂层与干砂形成的机械 三氯化硼等添加剂。
混合物。多出现在铸件的热节、局部结构复杂的
②浇注温度与速度:相比于砂型铸造,消失
拐角、死角处。消失模工艺生产变速箱壳体产生 模铸造铸铁件时温度需提高 30~80 ℃,在确保金
振实台振实。用 3 t 中频炉熔炼,原材料主要为生 铁、硅铁、锰铁、废钢以及回炉料;金属液在 1 520 ℃左右出炉,用 0.5 t 浇包,金属液浇注温度控制
在 1 420~1 480 ℃,为防止反喷现象的发生,对每 一件都采用慢—快—慢的节奏浇注。
3 常见缺陷及解决方法
3.1 模样变形 采用 EPS401 为原料,熟化成型制成密度为
54 现代铸铁 2010 / 6
接到模样强度相对较低部位的两端。 方案一没有取得很好的成效,部分铸件与加
Lost Foam Casting Process 消
失
模
铸
造
影响碳缺陷的因素及对策[6]:
工
艺 ① 模 样 材 料 :不 同 的 模 样 材 料 ,w(C)量 不
强筋粘在了一起,造成产品清理困难。方案二中, 同。可发性聚苯乙烯 EPS 的 w(C)量为 92%,聚
采用两个内浇道与采用单个浇道相比,既使单个 铸件的浇注时间缩短,也起到了分流的作用,这
的内浇道位置会使产品的合格率大幅提升。因 样就降低了金属液对壳体底面涂料的冲刷力。其
而,万象公司通过长时间的生产实践,生产变速 位置的合理设置可使两股金属液流汇集于铸件
箱壳体的浇注系统采用了第二种浇注方式— —— 端部,另外在此端部设置冒口用于集渣。
DOI:10.3969/j.issn.1003-8345.2010.06.012
Casting Method and Defects Prevention of Gearbox Housing Produced with Lost-Foam Process
LI Liang1,LIU Lan-jun1,XIAO Chao-jie1,WAN Bing2,WANG Ming2
1 浇注系统设计
对于消失模铸造,浇注系统设计是一个比较
棘手的问题,由于其安放位置不受砂芯等因素的 干扰,具有很大的自由度,因而不能直接采用传 统铸造工艺的方法。
根据大量理论分析与资料查阅,笔者试用了 两种浇注系统。第一种:阶梯式浇注(如图 1),金 属液从顶部和底部两个内浇道流入型腔,其两股 液流“冷端”部位会在变速箱壳体侧面汇集,形成
气量增大、强度低,金属液流出涂层而粘砂;④负
③内浇道位置要合理,根据实际情况,万象公
压度过低、内浇口引入位置不当,也会使铸件粘 司对变速箱壳体采用底注式,顶部端面设置冒口。
砂;⑤金属液的浇注温度过高或铸件局部结构热
④原材料的化学成分:根据每炉的实际情
量不易散出而降低涂料的耐火度,造成粘砂[2];⑥ 况,在保证铸件性能与经济性的基础上,配料时
Lost Foam Casting Process 消 失 模 铸 造 工 艺
变速箱壳体消失模铸造工艺与缺陷防止
李 亮 1,刘兰俊 1,肖超杰 1,万 兵 2,王 鸣 2
(1.合肥工业大学 材料科学与工程学院,安徽 合肥 230009;2.铜陵万象汽车零部件有限公司,安徽 铜陵 244121)
摘要:介绍了汽车变速箱壳体的消失模铸造工艺。为消除铸件缺陷,提出如下措施:(1)使用竹片加固模样,解决模样变
WANG Lin-hui1,ZHANG Bao-qing2,YUAN Dong-zhou3,PEI Hu-ping4,WANG Guo-ping3
底注式(如图 4)。
图 4 中两个内浇道与铸件的内部底面相连, 2 其它工艺参数设计
采用目数为 200~270、w(Si)量≥(96±1)%的 Si 砂粉。涂料使用桂林 5 号铸粉,按 1:10的比例 加水搅拌;手工挂涂,需两层,挂涂完放入50±5
℃ 烘 房 烘 15 ~20 h。 雨 淋 式 加 砂 埋 型 ,采 用 1 200 mm×1 000 mm×900 mm 规格砂箱,一箱多 件。使用振幅 0.5~1.0 mm、频率 40~80 Hz 的三维
(1.Materials Science and Engineering College,Hefei University of Technology,Hefei 230009,China;2.Tongling Wanxiang Automobile Parts Co. Ltd.,Tongling 244121,China)