优良工艺介绍(前道)
晶圆制造前道量检测工艺分类、特征、价值分析
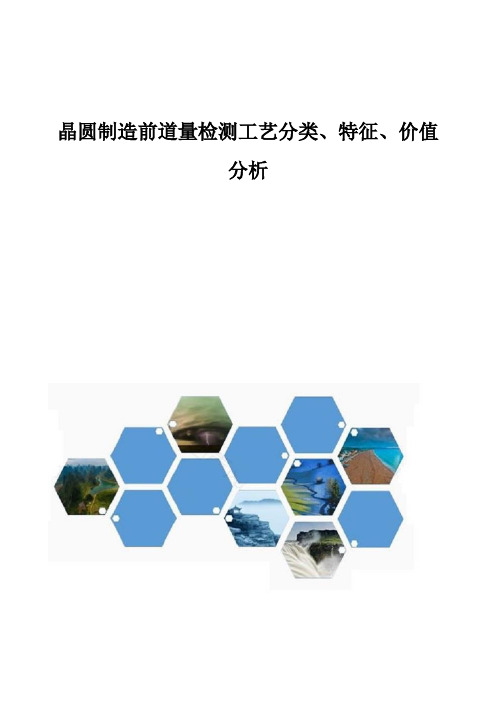
晶圆制造前道量检测工艺分类、特征、价值分析(一)前道量检测贯穿晶圆制造环节始终,是芯片生产线的“监督员”前道量检测使整条前道工艺产线的控制达到最佳化,同时也为追寻芯片生产中发现的问题提供了重要的追寻线索。
半导体芯片制造工艺步骤极多,各步骤之间可能会相互影响,因此很难根据最后出厂产品的检测结果准确分析出影响产品性能与合格率的具体原因。
而且如果不能在生产过程中及时检测到工艺缺陷,则此批次工艺中生产出来的大量不合格产品也会额外增加厂商的生产成本。
因此前道量检测贯穿芯片制造环节始终,对加工制造过程进行实时的监控,确保每一步加工后的产品均符合参数要求。
而且,产品小组可以通过分析前道量检测产生的检测数据及时发现问题根源,使之能够采取最有效的方式进行应对,从而制造出参数均匀、成品率高、可靠性强的芯片。
前道量检测根据测试目的可以细分为量测和检测。
量测主要是对芯片的薄膜厚度、关键尺寸、套准精度等制成尺寸和膜应力、掺杂浓度等材料性质进行测量,以确保其符合参数设计要求;而检测主要用于识别并定位产品表面存在的杂质颗粒沾污、机械划伤、晶圆图案缺陷等问题。
前道量检测分类及主要技术资料来源:公开资料前道量测、检测均会用到光学技术和电子束技术,但是两种技术在量测与检测下各具不同的特点。
光学量测通过分析光的反射、衍射光谱间接进行测量,其优点是速度快、分辨率高、非破坏性,但缺点是需借助其他技术进行辅助成像;电子束量测是根据电子扫描直接放大成像,其优点是可以直接成像进行测量,但缺点是速度慢、分辨率低,而且使用电子束进行成像量测操作时需要切割晶圆,(立鼎产业研究网)因此电子束量测具有破坏性。
光学检测是通过光信号对比发现晶圆上存在的缺陷,其优点是速度快,但缺点是无法呈现出缺陷的具体形貌;而电子束检测可以直接呈现缺陷的具体形貌,但是该方法在精度要求非常高的情况下会耗费大量的时间。
在实际的芯片制造过程中,光学技术与电子束技术常常被结合使用,比如检测环节一般先采用光学检测定位缺陷位置,再使用电子束检测对缺陷进行精确扫描成像,两种技术的结合使用可以提高量检测的效率,并降低对芯片的破坏性。
前道 生产工艺

工艺介绍(前道)第一节 分 选一、准备工作:1、穿工作服、鞋,戴手套(或指套)、工作帽;2、清理工作台面,保持台面整洁;3、准备流转盒、泡沫垫、流转单;4、将电池片从仓库内领出。
二、所需要的材料、设备和工具1、所需材料:1)电池片 2)指套 3)标准电池片2、设备:单片测试仪三、操作程序1、电性能测试:尽量使每个组件内各电池片功率在设计范围内1)校准标准片(方法见设备的使用和保养中的单片测试仪项)2)从包装箱内取出一包电池片,用刀片划开包装袋。
3)将外观良好的电池片拿到单片测试仪上进行电性能测试4)保存所测数据(Voc、Isc、Pm、Vm、Im、FF、η、Rs、Rsh)5)根据所测数据分档(理论上应以Isc为主要参数,由于设备存在不同误差,生产上以实测功率来分档)2、外观分选1)放若干个较厚的泡沫垫一一排列,以便分选电池片的颜色,右手轻轻拿起电池片边上中心部位距离眼睛约30cm处,在一定的光照度下检查每片电池片是否有色差、破片、裂纹、缺角、崩边、栅线印刷不良、正极鼓包等不良现象。
3)每72片为一个组件,每10片之间用泡末垫隔开,编写流转单,流转单上写明电池片生产厂家、电池片等级、型号规格、操作人员姓名等流入下一道工序。
四、质量要求1、电池片必须按技术要求及实测功率分档2、测试环境温度应控制在25℃左右3、测试仪在连续操作2小时后需重新用标准片校准4、确保电池片清洁无损伤5、外观颜色均匀一致6、电池片的外观缺陷根据检验规范要求五、注意事项1、严禁裸手接触电池片;2、作业时,电池片要轻取轻放;3、开机测试前应对标准片进行校准,测试不同规格电池片时要用不同规格的标准片进行校准;4、定时检查设备是否完好;5、测试时眼睛避免直视光源,以防伤害眼睛6、在电池片拆包前先要检查外包装有无破损现象,如有则拍照记录并上报,若无破损可拆包检查电池片。
7、每开一包要尽快用完,防止氧化。
若无法用完,则要进行密封保存第二节 单片焊接一.准备工作1、穿工作衣、鞋,戴指套(或手套),以防止裸手触摸电池片,手部的汗液将会影响电池片和EVA的交联强度;2、清洁工作台面,保持环境整洁;3、根据技术要求裁剪相应长度的互连条,将互连条以适当用量放入助焊剂盒浸泡 约3分钟;4、每次更换烙铁头和每天开始焊接前须检查恒温电烙铁的实际温度和标称温度是否相符,并作相应调整和记录,防止电烙铁温度变化影响焊接质量;5、新到的电池片必须试焊,每天正式焊接前也应试焊,检查焊接质量。
半导体前道制造工艺流程ppt

薄膜厚度的测量
总结词
薄膜厚度的测量是半导体前道制造工艺中非常重要的环节,对于产品的质量和稳 定性具有重要影响。
详细描述
薄膜厚度的测量一般采用光学测量方法,如椭圆偏振仪、干涉仪等。这些仪器利 用光的干涉原理来测量薄膜厚度,精度可达到纳米级别。在测量过程中,需要注 意薄膜的均匀性和稳定性,以避免对测量结果造成误差。
掺杂浓度的测量
总结词
掺杂浓度的测量是半导体前道制造工艺中的重要环节 ,对于产品的电学性能和质量具有重要影响。
详细描述
掺杂浓度的测量一般采用离子束分析(IBA)或二次离 子质谱(SIMS)等精密仪器。这些仪器通过分析薄膜 中的离子束或二次离子的数量和能量,来确定掺杂浓 度和分布情况。在测量过程中,需要注意仪器的精度 和稳定性,以避免对测量结果造成误差。
半导体前道制造工艺流程ppt
xx年xx月xx日
目 录
• 半导体前道制造工艺概述 • 半导体前道制造工艺流程 • 半导体前道制造工艺的设备 • 半导体前道制造工艺的检测与测量 • 半导体前道制造工艺的优化与发展趋势
01
半导体前道制造工艺概述
半导体前道制造工艺的定义
半导体前道制造工艺是指利用半导体材料和制程技术,将半 导体器件制作成集成电路的过程。
随着工艺节点缩小,技术难度和成本急剧 增加。
材料短缺
部分新型材料依赖进口,存在供应风险。
制造成本
工艺复杂度高,制造成本高。
良品率
工艺不稳定导致良品率低。
半导体前道制造工艺的未来发展
新工艺技术
研究和发展新的工艺技术,如新材 料、新结构、新器件等。
跨领域合作
加强与科研机构、高校的合作,推 动产学研一体化。
曝光设备
半导体封装制程与设备材料知识介绍

Plastic
2.54 mm (100miles) 1 direction
lead
16~24
S-DIP
Shrink Dual In-line
Package
Plastic 1.778 mm (70miles)
20 ~64
2024/10/16
Through Hole Mount
SK-DIP
Skinny Dual In-line
LS/GS5700
Tape & Reel BGA
Reel Tech MT TR3000
Socket
BGA/MLF Johnstech
Burn-In
BGA/MLF SSE
B1120M
2024/10/16
常用术语介绍
1. SOP-Standard Operation Procedure 2. FMEA- Failure Mode Effect Analysis 3. SPC- Statistical Process Control 4. DOE- Design Of Experiment 5. IQC/OQC-Incoming/Outing Quality
Detaping (Optional)
Wafer Mount
UV Cure (Optional)
Die Saw
Die Bond
Die Cure (Optional)
Plasma
Wire Bond
Molding Post Mold Cure Laser mark
Laser Cut Package Saw
Grind & Dicing (晶圓研磨及切割)
Die Attach (上片)
高速公路施工工艺流程图(全)资料

高速公路施工工艺流程图(全)资料高速公路是许多人出行的首选,而这些高速公路的建设离不开复杂的工艺流程。
下面将为大家介绍高速公路施工的工艺流程。
一、前期准备(筹备阶段)在高速公路建设之前,需要对建设区域进行勘察和设计,同时需要与相关部门商讨法规、手续等问题,并确定施工的经费和资源,然后才能进入到实际的施工工艺流程当中。
二、道路土方开挖道路土方开挖是高速公路施工中最重要的工序之一,也是最需要投入的资源和资金的阶段之一。
在这个阶段中,需要对土方进行开挖,同时进行起伏面培平、边沟开挖等工作。
三、路基处理路基处理是指在土方开挖后,进行地基填筑和打碎石料等工作,同时还要进行土石方差异处置,这些工作都是为了提高高速公路的稳定性和减缓道路小样系数差异的问题。
四、路基加固和压实当地基处理工作完成之后,需要对路基进行加固和压实,这有利于提高高速公路的承重能力和稳定性,保证道路在各种均布荷载和集中荷载作用下具有充分的稳定性。
五、基层路面施工基层路面施工是高速公路建设中的一个重要阶段,在这个阶段中,需要进行石料拌和、板层压实等工序,使路面表面平整、有足够的坚固度,并能够承受各种车辆行驶带来的荷载。
六、中间层路面施工中间层路面施工是为了保证高速公路在各种天气和气温下都能够具有良好的强度和平滑性。
这个阶段需要进行石料拌和、加硫铁等工序,同时还需要进行科学的温度控制工作。
七、面层路面施工面层路面施工是高速公路建设中的最后一个重要阶段,在这个阶段中需要进行石料拌和和面层压实等工序,使得道路表面光滑、易于行驶,同时还需要进行打标线等标记工作。
八、文明施工高速公路施工中,需要保证文明施工,避免对周围环境和群众造成过多的干扰和困扰。
在施工过程中,需要安装道路安全设施,同时也要保护现场环境和居民的利益。
以上是高速公路施工工艺流程的介绍,希望能够对大家有所帮助。
总的来说,高速公路的建设是一个较为复杂的过程,需要投入大量的资源、资金和人力,同时也需要高度讲究施工工艺和文明施工等方面。
焊接工艺介绍
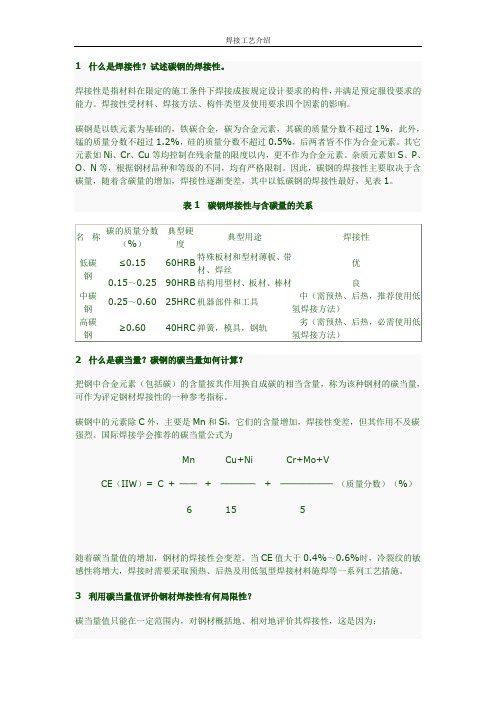
1 什么是焊接性?试述碳钢的焊接性。
焊接性是指材料在限定的施工条件下焊接成按规定设计要求的构件,并满足预定服役要求的能力。
焊接性受材料、焊接方法、构件类型及使用要求四个因素的影响。
碳钢是以铁元素为基础的,铁碳合金,碳为合金元素,其碳的质量分数不超过1%,此外,锰的质量分数不超过1.2%,硅的质量分数不超过0.5%,后两者皆不作为合金元素。
其它元素如Ni、Cr、Cu等均控制在残余量的限度以内,更不作为合金元素。
杂质元素如S、P、O、N等,根据钢材品种和等级的不同,均有严格限制。
因此,碳钢的焊接性主要取决于含碳量,随着含碳量的增加,焊接性逐渐变差,其中以低碳钢的焊接性最好,见表1。
表1 碳钢焊接性与含碳量的关系2 什么是碳当量?碳钢的碳当量如何计算?把钢中合金元素(包括碳)的含量按其作用换自成碳的相当含量,称为该种钢材的碳当量,可作为评定钢材焊接性的一种参考指标。
碳钢中的元素除C外,主要是Mn和Si,它们的含量增加,焊接性变差,但其作用不及碳强烈。
国际焊接学会推荐的碳当量公式为Mn Cu+Ni Cr+Mo+VCE(IIW)= C + ──+────+──────(质量分数)(%)6 15 5随着碳当量值的增加,钢材的焊接性会变差。
当CE值大于0.4%~0.6%时,冷裂纹的敏感性将增大,焊接时需要采取预热、后热及用低氢型焊接材料施焊等一系列工艺措施。
3 利用碳当量值评价钢材焊接性有何局限性?碳当量值只能在一定范围内,对钢材概括地、相对地评价其焊接性,这是因为:1)如果两种钢材的碳当量值相等,但是含碳量不等,含碳量较高的钢材在施焊过程中容易产生淬硬组织,其裂纹倾向显然比含碳量较低的钢材来得大,焊接性较差。
因此,当钢材的碳当量值相等时,不能看成焊接性就完全相同。
2)3)影响焊缝金属组织从而影响焊接性的因素,除了化学成分和冷却速度外,还有焊接循环中的最高加热温度和在高温停留时间等参数,在碳当量值计算公式中均没有表示出来。
半导体前道制造工艺流程

P+ N-epi P+ N-epi P+
N+-BL
N+-BL
P-SUB
涂胶—烘烤---掩膜(曝光)---显影---坚膜—蚀刻—清洗 —去膜--清洗—P+扩散(B)
第三次光刻—P型基区扩散孔
决定NPN管的基区扩散位置范围 SiO2
P
P
P+
P+ N-epi P+
N+-BL
N+-BL
P-SUB
去SiO2—氧化--涂胶—烘烤---掩膜(曝光)---显影---坚膜 —蚀刻—清洗—去膜—清洗—基区扩散(B)
• 5。光III---N管场区光刻,N管场区注入, 以提高场开启,减少闩锁效应及改善阱 的接触。
B+
光刻胶
P-
N-Si
CMOS集成电路工艺 --以P阱硅栅CMOS为例
• 6。光III---N管场区光刻,刻出N管场区 注入孔; N管场区注入。
P-
N-Si
CMOS集成电路工艺 --以P阱硅栅CMOS为例
第四次光刻—N+发射区扩散孔
• 集电极和N型电阻的接触孔,以及外延层的反偏孔。 • Al—N-Si 欧姆接触:ND≥1019cm-3,
P P+
N+-BL
N+
P+ NP-epi
P+
N+-BL
P-SUB
SiO2
去SiO2—氧化--涂胶—烘烤---掩膜(曝光)---显影---坚膜 —蚀刻—清洗—去膜—清洗—扩散
二、晶圆针测制程
• 经过Wafer Fab之制程後,晶圆上即形成 一格格的小格 ,我们称之为晶方或是晶粒 (Die),在一般情形下,同一片晶圆上 皆制作相同的晶片,但是也有可能在同一 片晶圆 上制作不同规格的产品;这些晶圆 必须通过晶片允收测试,晶粒将会一一经 过针测(Probe)仪器以测试其电气特性, 而不合格的的晶粒将会被标上记号(Ink Dot),此程序即 称之为晶圆针测制程 (Wafer Probe)。然後晶圆将依晶粒 为单位分割成一粒粒独立的晶粒
介绍工艺流程举例

介绍工艺流程举例
《手工陶瓷制作工艺流程》
手工陶瓷制作是一门古老而精湛的工艺,其制作工艺流程需要经过多道复杂的工序。
下面就介绍一下手工陶瓷制作的工艺流程。
第一步:挑选原料
首先,需要挑选合适的陶土作为制作陶瓷的原料。
合适的陶土要求细腻、易于成型、可塑性好以及烧结后颜色均匀。
第二步:搅拌和制泥
将选好的陶土放入搅拌机中,加入适量的水,然后开始搅拌。
搅拌的目的是让陶土和水充分混合,形成柔软的陶泥。
第三步:成型
制作陶瓷的形状可以通过手工成型或者采用模具成型。
手工成型需要陶工经过长时间的练习和技巧,而采用模具成型则可以提高生产效率和产品质量。
第四步:干燥
成型完成后的陶瓷制品需要在通风干燥的环境下进行处理,目的是使陶瓷制品中的水分慢慢被蒸发掉,从而增加陶瓷制品的硬度和稳定性。
第五步:修整和涂釉
干燥后的陶瓷制品需要进行修整,包括去除表面的瑕疵和毛刺。
然后涂上适量的釉料,使其增加光泽和色彩,以及提高瓷器的耐磨性。
第六步:装瓷制品
经过修整和涂釉的陶瓷制品需要经过高温烧制,使其变得坚硬并具有一定的透明度。
第七步:包装和销售
经过烧制的陶瓷制品需要进行包装,然后投入市场销售。
以上就是手工陶瓷制作的工艺流程。
手工陶瓷制作需要耐心和技巧,每一个环节都需要经过精心的操作才能制作出精美的陶瓷制品。
热模锻工艺介绍 180813
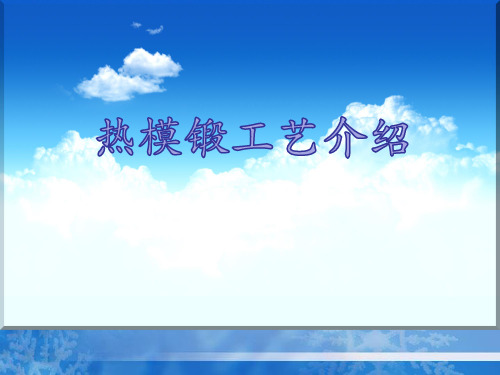
1)模锻锤: G=(3.5~6.3)KF(公斤) 2)热模锻压力机 P=(6.3~7.4)F(吨) 圆形锻件:P=8(1-0.001D)(1.1+20/D)2 FБbt 非圆形:P=8(1-0.001D)(1.1+20/D)2 (1+0.1 )FБbt 3)平锻机 P=5(1-0.001D)(D+10)2Бbt 4)螺旋压力机 P=KБbtF
热模锻压力机 (曲柄压力机)
和同样能力的模锻锤相比, 热模锻压力机的初次投资 大,但维护费用低,动力 消耗小。
和摩擦压力机模锻相比, 生产率较高,便于自动化。
热模锻压力机结构复杂, 制造条件要求高。
螺旋压力机种类:
摩擦螺旋压力机 电动螺旋压力机 离合器螺旋压力机 液压传动螺旋压力机
1、摩擦压力机靠飞轮积蓄 的能量工作,原则上可多次打击 干大活。实际有效打击次数不超 过3次。
键块分别紧固在锤头和下模座
的燕尾槽中。
•
燕尾使模块固定在锤头
(或砧座)上,使燕尾底面与
锤头(或砧座)底面紧密贴合。
•
楔铁使模块在左右方向定
位。键块使模块在前后方向定
位。
热模锻压力机与模锻锤相比,其 工作特性为: (1)静压成形,无震动和噪音; (2)机架和曲柄连杆机构的刚性 大,工作时弹性变形小; (3)滑块行程一定,每一模锻工 步只要一次行程完成; (4)导向精度和承受偏载的能力 强; (5)有上下顶件装置,便于锻件 脱模。
部分汽车件产品
转向系统 Steering System
制动系统 Braking System
传动系统 Drive System
➢ 转向系统 Components of Steering System
中国各地的非遗介绍

中国各地的非遗介绍中国各地的非物质文化遗产(简称非遗)是中华民族优秀传统文化的重要组成部分,具有丰富独特的地域特色和历史内涵。
下面将介绍一些中国各地的非遗,包括传统工艺、民间艺术、传统音乐等方面。
一、四川绣花——川绣川绣是中国四大名绣之一,以其细腻、精巧、色彩鲜艳而闻名于世。
川绣以蜀绣为代表,源远流长,历史悠久。
蜀绣绣工出色,绣品形象生动、栩栩如生,被誉为“一针一景”。
川绣的技艺独特,绣工需要具备高超的技艺和耐心,通过细腻的刺绣将花鸟鱼虫、山水人物等元素表现得栩栩如生。
二、江苏剪纸——苏剪苏剪是江苏地区的传统剪纸工艺,有着悠久的历史和丰富的文化内涵。
苏剪以其独特的造型和精湛的剪纸技艺而闻名。
苏剪的主要特点是造型复杂多样,线条流畅,寓意深远。
苏剪常常用来装饰窗户、门框,寓意吉祥和美好。
三、广东陶瓷——粤瓷粤瓷是广东地区的传统陶瓷工艺,以其独特的烧制工艺和精美的装饰而著称。
粤瓷的特点是色彩鲜艳、造型精美、图案瑰丽,常常以花鸟、人物等为主题。
粤瓷的瓷器制作工艺复杂,需要经过多道工序,包括制泥、制胎、上釉、彩绘等,每一道工序都需要经验丰富的工匠来完成。
四、山西剪纸——晋剪晋剪是山西地区的传统剪纸工艺,有着悠久的历史和独特的风格。
晋剪的特点是造型简练、线条流畅、寓意深远。
晋剪常常用来装饰窗户、门框等,寓意吉祥和幸福。
晋剪的剪纸工艺独特,需要经验丰富的工匠手工剪刻出各种精美的图案。
五、云南布纹——云布云布是云南地区的传统纺织工艺,以其独特的布纹和精美的织布技艺而闻名。
云布的特点是色彩鲜艳、布纹独特,常常以花鸟、山水等为主题。
云布的制作过程复杂,需要经验丰富的工匠手工织造,将丝线编织成色彩艳丽的布料。
六、江西剪纸——赣剪赣剪是江西地区的传统剪纸工艺,具有悠久的历史和独特的风格。
赣剪的特点是造型简练、线条流畅、寓意深远。
赣剪常常用来装饰窗户、门框等,寓意吉祥和幸福。
赣剪的剪纸工艺需要经验丰富的工匠手工剪刻出各种精美的图案。
先进半导体器件前中后工艺流程

先进半导体器件前中后工艺流程
先进半导体器件的前、中、后工艺流程如下:
前工序(前道工艺):
1. 成膜淀积工艺:在晶圆上形成各种薄膜材料,包括导体、半导体和介质材料等。
这些薄膜材料由不同的元素和化合物组成,形成器件的关键结构。
2. 光刻工艺:在薄膜上形成图案并刻蚀,加工成确定形状。
光刻是半导体制造中的关键环节,通过光刻技术将设计好的电路图案转移到光敏材料上,然后进行刻蚀和剥离,形成电路图样。
3. 掺杂工艺:在半导体中掺入微量导电性杂质,以控制器件的电学性能,如导电类型、载流子浓度等。
掺杂工艺是实现半导体器件导电性能的关键步骤之一。
中工序(中道工艺):
1. 刻蚀工艺:将经过光刻和掺杂后的晶圆表面进行刻蚀,以形成各种半导体器件的结构和电路。
刻蚀工艺是实现器件微观结构的关键步骤之一。
2. 镀膜工艺:在器件表面镀上一层薄膜,以保护器件免受环境影响,提高器件的稳定性和可靠性。
镀膜工艺对于提高器件性能和延长使用寿命具有重要意义。
后工序(后道工艺):
1. 封装工艺:将制作好的芯片进行封装,以实现芯片与外部电路的连接和保护。
封装工艺是半导体制造中的重要环节,对于保证芯片的性能和可靠性具有重要意义。
2. 测试与可靠性验证:对封装好的芯片进行测试和可靠性验证,以确保其性能符合要求。
测试环节是保证芯片性能和可靠性的关键步骤之一。
以上是先进半导体器件的前、中、后工艺流程的简要介绍,每个环节都有其特定的作用和要求,只有严格控制每个环节的质量和工艺参数,才能制造出高性能、高可靠性的半导体器件。
喷水织机工艺流程

喷水织机织造工艺流程:前道工艺:定捻——络筒——整经-—穿结经经纱经过加捻,定捻,并捻之后,然后络筒,整经,然后穿综扒扣,开始上机织造.如果纱线的强力不够,或者容易起毛,需要通过浆纱工序给纱线上浆.定捻:经过加捻的纱线,特别是强捻后,纤维产生了扭应力,在纱线张力较小或自由状态下,纱线会发生退捻、扭曲。
为防止这种现象的产生,使后道加工顺利进行,必要时以定捻加工来稳定这些纱线的捻度。
络筒(又称络纱)是织前准备的第一道工序,它的任务是将来自纺部的管纱或绞纱在络筒机上加工成符合一定要求的筒子。
络筒工序的作用可以概括为以下两点:(1)将原纱(或长丝)做成容量圈套的筒子,提供给整经、卷纬、针织、无梭织机的供纬或漂染等工序.管纱容量上,大卷装的管纱也仅能容纳29。
2tex(20英支)的中特棉纱约2500m左右.若将管纱直接用于整经或织机上供纬等工序,都将因频繁换管而使停车时间过长,这样即不符合工艺上的要求,也不利于提高生产效率。
而筒子的卷装容量则大大增加,一般中特纱的筒子其绕长度可达10万米左右。
(2)清除纱线上的某些疵点、杂技、改善纱线品质.由纺厂运来的原纱一般有较多的外观疵点,在通过络筒机上的清纱装置时,可以清除其上的绒毛,尘屑及弱纱、粗结等杂质疵点,这样,既可改善织物的外观质量,又因剔除了纱线上的薄弱环节而提高了它们的平均强度,从而减少了纱线的后道工序中的断头.络筒质量直接影响到后工序。
因此,对络筒工序提出如下的要求:(1)筒子卷装容量要大,以提高后道工序的生产效率;筒子卷绕应坚固结实,以便于贮存和运输:(2)卷绕过程中应保持一定的纱线张力,以保证筒子成形良好;(3)要便于筒子在后道工序中的退绕,防止出现脱圈上缠断头;(4)筒子上纱线的结头要小而牢;(5)不损伤纱线原有的物理机械性能。
整经:将一定根数的经纱按规定的长度和宽度平行卷绕在经轴或织轴上的工艺过程。
经过整经的经纱供浆纱和穿经之用。
整经要求各根经纱张力相等,在经轴或织轴上分布均匀,色纱排列符合工艺规定。
棉纺织工艺并条工序

04
并条工序的常见问题与解决方案
梳棉过程中的纤维损伤问题
01
02
03
04
总结词:纤维损伤
详细描述:在梳棉过程中,由 于机械摩擦和高温作用,容易 导致纤维损伤,影响纱线品质
。
解决方案:采用新型梳棉机, 优化工艺参数,降低机械摩擦
和温度,减少纤维损伤。
预防措施:定期检查和维护梳 棉机,保持设备良好运转状态
效率和产品质量。
绿色环保生产
02
注重环保和可持续发展,推广绿色环保的生产模式,降低能耗
和排放,实现可持续发展。
资源循环利用
03
加强资源循环利用,降低生产成本,减少浪费,实现经济效益
和环境效益的双重提升。
THANKS
感谢观看
并条工序的主要设备与工具
01
02
03
04
并条机
并条工序的主要设备是并条机 ,它能够将多根棉条合并为一
道棉条。
罗拉
罗拉是并条机上的重要部件, 用于控制棉条的输出和张力。
皮辊
皮辊是并条机上的另一个重要 部件,用于控制棉条的滚动和
输送。
检测仪器
为了确保并条工序的质量和效 率,需要使用各种检测仪器对 棉条的质量进行检测和控制。
提高棉条的品质和均匀度。
并条工序通常在纺纱工艺的前道 工序中进行,为纺纱工序提供优
质的原料。
并条工序在棉纺织工艺中的位置和作用
并条工序是棉纺织工艺中的一道重要 工序,位于纺纱工艺的前道工序中。
并条工序的质量直接影响到后续纺纱 工序的质量和效率,因此并条工序的 操作和管理至关重要。
并条工序的作用是将多根棉条合并, 改善纤维的分布,提高棉条的品质和 均匀度,为纺纱工序提供优质的原料。
铸钢件生产工艺流程(精)

模型的生产管理;
有关模型的技术标准; 可以说模型影响着整个铸造厂(车间)的生产。
-3-
B.型砂 ※型砂直接影响着造型、制芯的生产操作,影响或者说决定生 产节奏和效率。
※型砂对铸件质量起着极大的影响,液体合金充型,在型砂中
流动、冷却、凝固、再冷却。在整个过程中有自身的、合金与 铸型的以及合金与空气的物理变化和化学反应。铸件的大多数 缺陷都与型砂直接或间接的有关,如粘砂、夹砂、气孔、裂纹、 折皱等等,还直接影响表面质量。 ※型砂直接影响劳动条件和环境。 ※型砂对生产成本的影响很大,有些砂种占成本的比例很大。
害元素、去除夹杂物、脱氧、除气调整化学成分,最后获得
合格的钢水。 (4)支持、配合的工作(工序) A.筑炉; B.备料(废钢、合金、增碳剂、脱氧剂、氧气、矿石、造渣材料 等); C.化学分析。 -7-
5.浇注
(1)任务 将钢水浇入铸型中。 (2)重要性 是直接形成铸件的一道工序。
(3)支持配合的工作:
10.入库前的抛丸:
(1)碳钢,中低合金钢铸件的最后一道工序,决定了铸件的外 观质量。
(2)对于不锈钢铸件,为最后一次钝化做准备,一定要将缺陷 彻底暴露。
11.防锈处理 (1)碳钢不锈钢铸件在表面质量合格并抛丸后应立即刷防锈油, 入库 (2)不锈钢铸件在表面质量合格抛丸后,酸洗钝化处理入库。 -15-
-12-
7.热处理:
通过热加工制度(加热、保温、冷却)改变铸件性能的加工方法 (1)任务 改变金相组织,消除应力,获得所需要的工艺性能(机加工)和使 用性能(机械性能和化学性能等) (2)重要性 铸件仅化学成分合格还不能满足用户的使用要求或工艺要求,还 需要通过热处理来使铸件满足这些要求,通过热处理可以: ※满足用户需要的机械性能;※满足用户需要的耐腐蚀性能; ※满足用户需要的工艺性能;※消除应力,稳定尺寸等。 (3)常见的热处理方法有:退火,正火,淬火,回火。 (4)设备:热处理炉,冷却水池。 -13-
半导体制造前道工艺

文档仅供参考,如有不当之处,请联系改正。
文档仅供参考,如有不当之处,请联系改正。
文档仅供参考,如有不当之处,请联系改正。
蚀刻
• 一般所指蚀刻也称光化学蚀刻,指经过曝 光制版、显影后,将要蚀刻区域旳保护膜 清除,在蚀刻时接触化学溶液,到达溶解 腐蚀旳作用,形成凹凸或者镂空成型旳效 果。(选择性刻蚀转移光刻胶上旳IC设计 图形到晶圆表面)
• 硅片清洗烘干(用于降低污染物,降低缺陷,使光刻 胶更轻易粘附。)
• 涂底 • 旋转涂胶*(利用离心力) • 软烘(清除圆片表面旳潮气,增长粘附性) • 边沿光刻胶旳清除 • 对准* • 曝光*(接触、接近、投影、步进) • 后烘(平衡驻波效应,提升辨别率。) • 显影* • 硬烘(提升刻蚀和注入旳抵抗力,提升粘附性)
• 氧化:使硅片表面形成氧化膜。主 要措施有热氧化法及气相成长法。 (绝缘、保护等作用)
• 化学气相沉积:反应物质在气态条 件下发生化学反应,生成固态物质 沉积在加热旳固态基体表面,进而 制得固体材料旳工艺技术。
文档仅供参考,如有不当之处,请联系改正。
光刻加工
• 光刻是一种利用类似于照片洗印旳原 理经过曝光和选择性化学腐蚀将掩膜 版上旳集成电路印制到硅片上旳精密 表面加工技术。
文档仅供参考,如有不当之处,请联系改正。
晶圆处理工序
• 本工序主要是经过清洗、氧化、 化学气相沉积、涂膜、曝光、显 影、蚀刻、离子植入、金属溅镀 等反复环节在晶圆上制作电路及 电子元件,最终在晶圆上完毕数 层电路及元件加工与制作。
文档仅供参考,如有不当之处,请联系改正。
• 清洗:用特殊旳清洗机和不同旳清 洗剂进行多道清洗。用于降低污染 物。
文档仅供参考,如有不当之处,请联系改正。
几种常见金属表面处理工艺
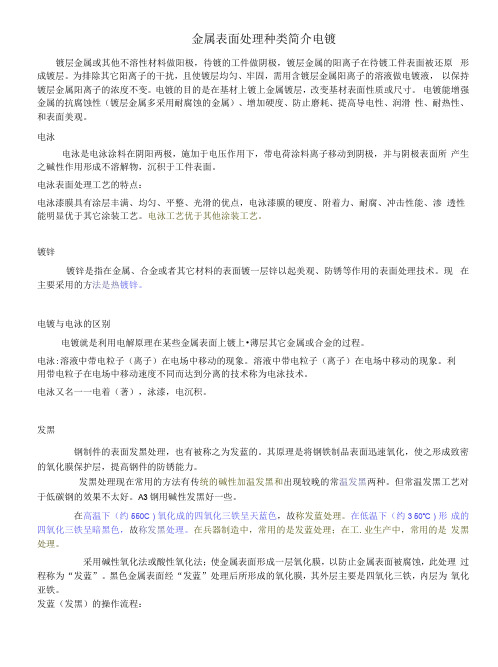
金属表面处理种类简介电镀镀层金属或其他不溶性材料做阳极,待镀的工件做阴极,镀层金属的阳离子在待镀工件表面被还原形成镀层。
为排除其它阳离子的干扰,且使镀层均匀、牢固,需用含镀层金属阳离子的溶液做电镀液,以保持镀层金属阳离子的浓度不变。
电镀的目的是在基材上镀上金属镀层,改变基材表面性质或尺寸。
电镀能增强金属的抗腐蚀性(镀层金属多采用耐腐蚀的金属)、增加硬度、防止磨耗、提高导电性、润滑性、耐热性、和表面美观。
电泳电泳是电泳涂料在阴阳两极,施加于电压作用下,带电荷涂料离子移动到阴极,并与阴极表面所产生之碱性作用形成不溶解物,沉积于工件表面。
电泳表面处理工艺的特点:电泳漆膜具有涂层丰满、均匀、平整、光滑的优点,电泳漆膜的硬度、附着力、耐腐、冲击性能、渗透性能明显优于其它涂装工艺。
电泳工艺优于其他涂装工艺。
镀锌镀锌是指在金属、合金或者其它材料的表面镀一层锌以起美观、防锈等作用的表面处理技术。
现在主要采用的方法是热镀锌。
电镀与电泳的区别电镀就是利用电解原理在某些金属表面上镀上•薄层其它金属或合金的过程。
电泳:溶液中带电粒子(离子)在电场中移动的现象。
溶液中带电粒子(离子)在电场中移动的现象。
利用带电粒子在电场中移动速度不同而达到分离的技术称为电泳技术。
电泳又名一一电着(著),泳漆,电沉积。
发黑钢制件的表面发黑处理,也有被称之为发蓝的。
其原理是将钢铁制品表面迅速氧化,使之形成致密的氧化膜保护层,提高钢件的防锈能力。
发黑处理现在常用的方法有传统的碱性加温发黑和出现较晚的常温发黑两种。
但常温发黑工艺对于低碳钢的效果不太好。
A3钢用碱性发黑好一些。
在高温下(约550C)氧化成的四氧化三铁呈天蓝色,故称发蓝处理。
在低温下(约3 50℃)形成的四氧化三铁呈暗黑色,故称发黑处理。
在兵器制造中,常用的是发蓝处理;在工.业生产中,常用的是发黑处理。
采用碱性氧化法或酸性氧化法;使金属表面形成一层氧化膜,以防止金属表面被腐蚀,此处理过程称为“发蓝”。
- 1、下载文档前请自行甄别文档内容的完整性,平台不提供额外的编辑、内容补充、找答案等附加服务。
- 2、"仅部分预览"的文档,不可在线预览部分如存在完整性等问题,可反馈申请退款(可完整预览的文档不适用该条件!)。
- 3、如文档侵犯您的权益,请联系客服反馈,我们会尽快为您处理(人工客服工作时间:9:00-18:30)。
四、叠层
重点质量要求:
⑴叠层布局符合设计要求; ⑵玻璃、背板、EVA的绒面朝向电池片; ⑶电池串正负极摆放正确,汇流条平直光亮; ⑷叠层时互连条和汇流条焊接时每个点都要加锡避免引起虚 焊,焊接到位、牢固,电池片完好; ⑸叠层过程中,保持内部无杂质、污物、手印、涂锡带残余等 ⑹叠层剪汇流条互连条时注意斜口钳不要碰到电池片以免电池 片破片 ⑺ EVA、背板要满盖玻璃,超出边界5mm以上;
2、电性能分选
主要指标及质量要求:
⑴电池片必须按技术要求及实测功率分档; ⑵测试环境温度应控制在25±2℃; ⑶测试仪在连续操作2小时后需重新用标准片校准。
二、单片焊接
焊接工艺:
焊接手势:见录像 焊接的正确手势,焊接时电烙铁的移动速度。 涂锡带侧视图: 焊接后截面图:
▲2
二、单片焊接
重点提示:
▲1
一、分选
2、电池片的电性能分选
目的: 尽量使每个组件内电池片的功率在一定范围内。 主要项目: 功率分档、电流分档
2、电性能分选
使用工具及注意事项: 使用工具:单片测试仪、标准电池片 注意事项: ⑴严禁裸手接触电池片; ⑵作业时,电池片要轻取轻放; ⑶开机测试前应拿标准片对单片测试仪进行校准,测试 不同规格电池片时要用不同规格的标准片进行校准; ⑷定时检查设备是否完好; ⑸测试时眼睛避免直视光源,以防伤害眼睛。
主要质量指标:
⑴负极焊接表面仍然保持光亮; ⑵电池片表面清洁,单片完整,无破裂现象; ⑶互连条要均匀、平直地焊在背电极内,每一单串电池片的底 边在同一直线上,错位<0.5mm。
四、叠层
叠层工艺步骤:见录像 重点提示:
a.电池串的拿放方式; b.引出汇流条的焊接及引出方式; c.互连条与汇流条的焊接及防止位移的方式。
第六章
优良工艺介绍
一、分选
1、电池片的物理性能分选
目的: 减少同一个组件内电池片的色差及使组件无裂纹 破片等不良现象,从而使组件外观美观,性能优 越。 主要项目: 色差、破片、裂纹、缺角、崩边、栅线印刷不良、 正极鼓包等不良现象.
1、物理性能分选
使用工具及注意事项:
使用工具:指套、流转盒、泡沫垫、流转单 注意事项:
⑷汇流条和电池片的间距整齐一致; ⑸不允许条形码不正或者褶皱; ⑹左右两串电池片的边沿到玻璃边缘距离一致; ⑺各串电池片的间距之差小于0.5 mm。
重点质量要求: ⑴无脱焊、虚焊、过焊、侧焊,保证良好的电性能; ⑵焊接表面光亮,无锡珠和毛刺; ⑶焊接好后电池片的弯曲度应小。
三、串联焊接
常用的本工序自检方法:
⑴用相对较薄的物体(如薄纸片等)嵌入涂锡带与电池片之 间,检查有无脱焊。检验方法如图: ⑵串联好后,将电池串翻面,负极向上,检查负极是否光亮。 检验方法如图: ▲4
a. 对于不同厂家的电池片,不同厂家的涂锡带要调整 工艺; b. 加热板、电烙铁要正确使用; c. 电烙铁应每隔一定时间测一次温度; d. 选择合适的助焊剂,涂锡带在助焊剂中的浸泡时间 应合适、涂锡带的干湿度要合适。
二、单片焊接
重点质量要求 ⑴无脱焊、虚焊、过焊、侧焊,保证良好的电性能; ⑵焊接表面光亮,无锡珠和毛刺; ⑶焊接好后电池片的弯曲度应小; ⑷焊接长度最低要求:
▲3
二、单片焊接
主要质量指标:
⑴电池片表面清洁,单片完整; ⑵具有一定的机械强度,沿45°方向轻拉互连条不脱 落; ⑶当把已焊上的互连条拆下时主栅线上应留下均匀的 银锡合金; ⑷互连条要均匀、平直地焊在主栅线内。
三、串联焊接
焊接工艺:见录像 重点提示:
a.加热模板、电烙铁需正确使用; b.使用不同的电池片需合理调整电烙铁的温度; c.合理的使用助焊剂。
连续焊接>2/3主删线长, 断点焊接累计> 1/2主删线长。
二、单片焊接
常用的本工序的自检方法:
1、将电池片侧放,检查涂锡带与电池片主栅线 结合是否良好。检验方法如图: 2、用相对较薄的物体(如薄纸片等)嵌入涂锡 带与电池片之间,检查有无脱焊。检验方法如图: 3、沿45度方向轻提互连条,检查有无脱焊。检验 方法如图:
四、叠层
本工序中电流电压简易测试的重要性:
四ห้องสมุดไป่ตู้叠层
常用的本工序自检方法: ⑴汇流条是否光亮平整、汇流条是否剪齐,检验方法
如图:
⑵检查组件内有无异物及残留物,检验方法如图: ⑶检查组件各个电池片的间距 ,检验方法如图:
▲5
四、叠层
主要质量指标:
⑴玻璃无破损破裂无明显的气泡和划痕; ⑵背板干净整洁无划伤、褶皱、划痕; ⑶不允许有焊带和汇流条未剪及位置差异;
⑴严禁裸手接触电池片; ⑵作业时,电池片要轻取轻放; ⑶在电池片拆包前先要检查外包装有无破损现象,如 有则拍照记录并上报,若无破损可拆包检查电池片; ⑷每开一包要尽快用完,防止氧化。若无法用完,则 要进行密封保存。
1、物理性能分选
主要指标及质量要求: ⑴ 确保电池片清洁无损伤; ⑵ 颜色均匀一致; ⑶ 电池片的外观缺陷根据检验规范要求。