潜在失效模式及后果分析FMEA70页
潜在失效模式与后果分析(FMEA)

卡死等损坏现象。
4
FMEA过程顺序
系统有那功能,特征,需要条件?会有Leabharlann 些错误?发生错误会有多惨?
那些错误是什么造成的?
发生之频率? 有那些预防和检测?
检测方法能多好程度?
我们能做什么? -设计变更 -过程变更 -特殊控制 -改变标准程序或指南
DFMEA and PFMEA
潜在失效模式与后果分析
Failure Mode and Effect Analysis
讲授内容
一.FMEA基本概念 二.FMEA之演变 三.国际间采用FMEA之状况 四.设计FMEA表填写说明 五.制程FMEA表填写说明 六.FMEA结果之应用
2
FMEA的基本概念
1.对失效的产品进行分析,找出零组件之 失效模式,鉴定出它的失效原因,研究
2.设备失效
错误的原物料规格。
生产良率。
不适当的的设计寿命假设。 原物料材质不稳定。
润滑或加油能力不足。
磨损。
不适当的维护作业。
金属疲劳。
缺之环境保护。
装备欠流畅。
错误的算法。
腐蚀。
超过压力。
19
设计FMEA填写说明
(15)发生度
参考下列各要素,决定发生度等级值(1~10): 1.相似零件或子系统的过去服务历史数据和相关经验? 2.零件、上一阶零件或分系统是否滞销? 3.上一阶零件或分系统改变程度的大小? 4.零件与上一阶零件,基本上是否有差异? 5.零件是否为全新的产品? 6.零件使用条件是否改变? 7.作业环境是否改变? 8.是否运用工程分析去预估,应用此零件之发生度?
8
国际间采用FMEA之状况
潜在失效模式和后果分析FMEA
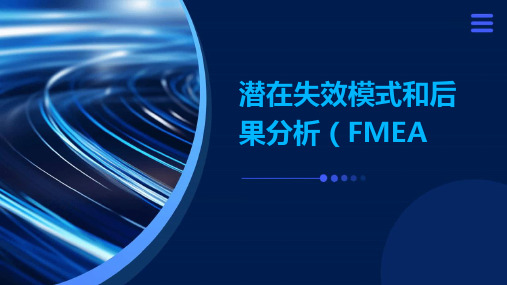
制定优先改进措施
01
根据RPN值评估结果,确定需要优先改进的潜在失效模式。
02
制定针对性的改进措施,包括设计优化、工艺改进、检验加强
等。
制定改进措施的实施计划和时间表,确保改进措施的有效执行
03 。
跟踪改进措施的实施情况
要点二
详细描述
在汽车行业中,FMEA被广泛应用于产品设计、生产和质 量控制过程中。例如,在发动机设计阶段,FMEA分析可 能识别出发动机气缸密封圈的潜在失效模式,如密封圈材 料疲劳或安装不当。这种失效可能导致发动机性能下降或 漏油,影响车辆的安全性和可靠性。通过FMEA分析,设 计团队可以采取措施优化密封圈材料和安装工艺,降低失 效风险。
服务流程改进
在服务流程中应用FMEA,有助于发 现和改进可能导致服务失败的潜在问
题。
生产过程控制
在生产过程中应用FMEA,有助于识 别和解决可能导致生产不合格品的潜 在问题。
维修和维护
在产品维修和维护过程中应用FMEA ,有助于预防和解决可能导致产品失 效的潜在问题。
02
CATALOGUE
FMEA分析过程
详细描述
潜在失效模式是指产品或过程中可能发生的故障或性能下降。通过分析历史数据、类似产品的失效模式以及专家 意见等途径,可以识别出潜在的失效模式。
确定失效影响
总结词
评估潜在失效模式对系统、产品或过程 的影响,有助于了解失效的严重程度。
VS
详细描述
失效影响是指潜在失效模式发生时,对系 统、产品或过程性能的影响程度。通过评 估失效影响,可以了解失效的严重程度, 为后续的风险评估提供依据。
潜在失效模式及后果分析(FMEA)—培训教材.

決定失效模式
確認效應 確認原因 確認目前控制 評價嚴重度 評價發生度 評價偵測度 三種 評價 完成 ? 否 是 收集數據 進行變更 確認改變 執行改變 收集數據 原因順序 影響要因 確認改變 是 知道如何 影響 遴選最重要 失效模式
嚴重度? 發生度? 偵測度? 否
更新文件 重訂優先順序
CAUSE
MODE
EFFECT
FMEA
潜在失效模式及后果分析
何謂过程 FMEA?
过程的潛在 FMEA 是一種分析技術,係由負責过程的工程師或小組使用,在 儘可能的範圍內用來確保所有潛在的失效模式及其原因/機制均已納入考量並 予以處理。过程潛在 FMEA旨在: • 鑑別过程的機能和要求 • 鑑別潛在的產品和过程有關的失效模式 • 評估失效對顧客的潛在影響 • 鑑別潛在的製造或組裝過程原因和鑑別过程變數 ( Variables ),並 且據以控制降低發生率或失效情況的偵測度。 • 鑑別过程變數,以著眼於过程控制 • 列出潛在失效模式之排序,並據以建立考慮採取預防/矯正措施 的優先順序 • 將製造或組裝過程的結果予以文件化。
偵 測 度
R P N
建議措施
責任與 目標 完成日期
措施結果
嚴 難 偵 R
採行措施 重 檢 測 P
度 度 度 N
效應為何?
有多不好?
功能, 特徵 或要求為何?
原因為何?
其發生 頻率為何?
改善風險程度 能夠做什麼? -- 設計變更 -- 过程變更 -- 特別控制 -- 標準, 程序書 或指引變更 -- 導入防呆措施 -- 加強設備保養 -- 加強參數控制 -- 加強工作技能
FMEA
潜在失效模式及后果分析
FMEA 作業說明(FMEA 團隊遴選及流程)
FMEA潜在的失效模式及后果分析
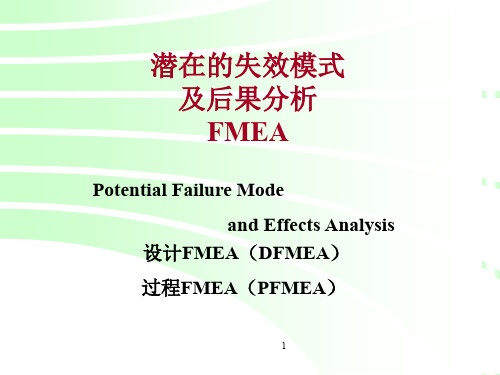
措施结果
项目 功能
潜在失 效模式
潜在失 效后果
严 重 度 S
级 别
潜在失 频 效起因/ 度
机理 O
现行设 计控制
预防
现行设 计控制
探测
探 测 度 D
R P N
建议措 施
责任及目 标完成日
期
采取的措 施
S
O
R DP
N
19
正表 DFMEA(设计)
项目/功能:
1、零部件、编号,修改状态 2、要满足设计意图的功能 3、工作环境
计、分析、试验、可 靠性、材料、质量、 服务、供方、以及高 一层和低一层总成、 系统、零部件设计人
• FMEA应成为促进不 同部门之间充分交换 意见的催化剂,从而 提高整个集体的工作 水平
• 可以邀请一位有 FMEA和团队工作推 进经验的推进员来协 助小组工作。
11
DFMEA是一份动态文件
• DFMEA要在一个设计概念最终 形成之时或之前开始
理效
的师是 一、负 种小责 分组设 析主计 技要的 术采工
用程
)Leabharlann 、9降低失效风险的方式
• 能客观评价设计,包括 功能要求及设计方案
• 为满足生产、装配、服 务和回收要求而评价初 步的设计
• 潜在失效对系统和车辆 运行产生影响在设计和 开发过程中得到考虑
• 为设计、开发、确认项 目的策划提供更多信息
4、其他方法
8
二、DFMEA简介
•
•
•
•
•
和维计体 文过过现 件程程了 化,中工
并正程 规常师 范的在 化思设
(
避 免 可 能 的 出 错
零 部 件 的 设 计 思 想
潜在失效模式及后果分析(FMEA)

设计 思想
过去 经验
担心 问题
顾客 反应
可能的失效模式
解决方案
群策群力智能发光
2. PFMEA拓展--关注的重点
PFMEA假定所设计的产品能够 满足设计要求,其潜在失效模 式可能会因设计弱点而包括在 过程FMEA中,它们的影响及避 免措施由设计FMEA来解决。因 设计缺陷所产生失效模式可包 含在过程FMEA中
其发生的 几率为何?
为有可能 被预防和 探测吗?
可以做什么? -设计变更 -过程变更 -特别的控制 -标准、程序或
指南的更改
探测它 的方法 有多好?
-非预期的功能
22
1. PFMEA简介
由“制造/装配工程师/小 组”采用的一种分析技术
以其最严密的形式总结了 开发一个过程时,工程师 /小组的设计思想
PFMEA
初始设计 设计完成 样件制造 设计/过程确认 制造开始
• PFMEA:开始于基本的操作方法讨论完成时, 完成时间早于制造计划制定和制造批准之前
10
实施FMEA的影响--范围和重点
• 新设计、新技术或新制程,这时的FMEA是完整的设计、 技术、或制程。
• 修改现有的设计或制程(假设其设计或制程FMEA已存 在)这时的FMEA的焦点在修改的设计、制程,以及由 于修改设计、制程而导致的相互作用。
1. PFMEA简介--作用
人
机
料
法
环
测
失效模式
一般是发生 在产品上
失效后果
一般是指对 下工程或最 终顾客的影响
1. PFMEA简介--作用
PFMEA是一种动态文件,主要体现在: 在可行性研究阶段之前或期间启动 在制造工装设计之前启动 考虑从个别的零部件到装配所有制造运作 包括工厂内所有影响制造和装配运作的过程,如材料
潜在失效模式及后果分析(FMEA)
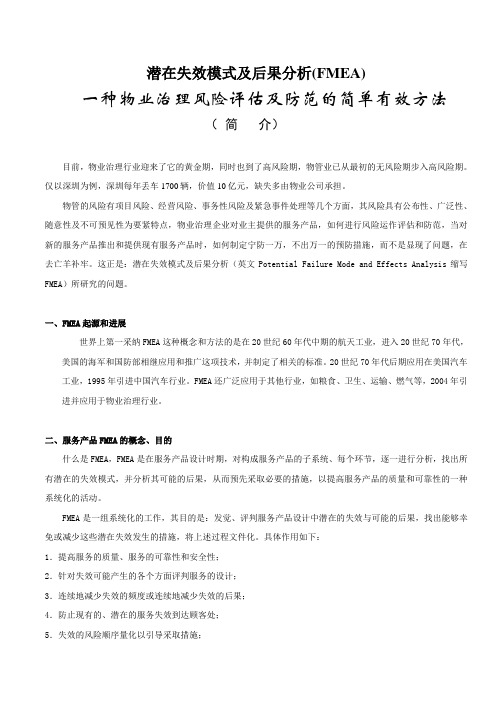
潜在失效模式及后果分析(FMEA)一种物业治理风险评估及防范的简单有效方法(简介)目前,物业治理行业迎来了它的黄金期,同时也到了高风险期,物管业已从最初的无风险期步入高风险期。
仅以深圳为例,深圳每年丢车1700辆,价值10亿元,缺失多由物业公司承担。
物管的风险有项目风险、经营风险、事务性风险及紧急事件处理等几个方面,其风险具有公布性、广泛性、随意性及不可预见性为要紧特点,物业治理企业对业主提供的服务产品,如何进行风险运作评估和防范,当对新的服务产品推出和提供现有服务产品时,如何制定宁防一万,不出万一的预防措施,而不是显现了问题,在去亡羊补牢。
这正是:潜在失效模式及后果分析(英文Potential Failure Mode and Effects Analysis缩写FMEA)所研究的问题。
一、F MEA起源和进展世界上第一采纳FMEA这种概念和方法的是在20世纪60年代中期的航天工业,进入20世纪70年代,美国的海军和国防部相继应用和推广这项技术,并制定了相关的标准。
20世纪70年代后期应用在美国汽车工业,1995年引进中国汽车行业。
FMEA还广泛应用于其他行业,如粮食、卫生、运输、燃气等,2004年引进并应用于物业治理行业。
二、服务产品FMEA的概念、目的什么是FMEA,FMEA是在服务产品设计时期,对构成服务产品的子系统、每个环节,逐一进行分析,找出所有潜在的失效模式,并分析其可能的后果,从而预先采取必要的措施,以提高服务产品的质量和可靠性的一种系统化的活动。
FMEA是一组系统化的工作,其目的是:发觉、评判服务产品设计中潜在的失效与可能的后果,找出能够幸免或减少这些潜在失效发生的措施,将上述过程文件化。
具体作用如下:1.提高服务的质量、服务的可靠性和安全性;2.针对失效可能产生的各个方面评判服务的设计;3.连续地减少失效的频度或连续地减少失效的后果;4.防止现有的、潜在的服务失效到达顾客处;5.失效的风险顺序量化以引导采取措施;6.优先使用行政的和工程的努力、时刻、人力资源和其他资源;7.运用团队原则和连续改进方法以获得好的服务产品;8.FMEA是补充设计时,必须做哪些情况才能使顾客中意;9.所有的FMEA都关注服务产品设计;10.应用于新的服务产品设计和现有未发生失效服务产品。
潜在失效模式及后果分析(FMEA)控制程序

潜在失效模式及后果分析(FMEA)控制程序潜在失效模式及后果分析(FMEA)控制程序1.目的通过分析、预测设计、过程中潜在的失效,研究失效的原因及其后果,并采取必要的预防措施,避免或减少这些潜在的失效,从而提高产品、过程的可靠性。
2.适用范围适用于公司设计FMEA、过程FMEA活动的控制。
3.职责3.1 产品研发部(R&D)负责组织成立DFMEA(设计FMEA)小组,负责DFMEA活动的管理。
3.2 生产技术部(PE)负责组织成立PFMEA(过程FMEA)小组,负责PFMEA活动的管理。
3.3 产品研发部、生产技术部、品管部、生产部、营销部、采购部等部门指定人员参加DFMEA小组、PFMEA小组。
必要时,由品管部邀请供应商、客户参加。
3.4 DFMEA小组负责制定《DFMEA潜在失效后果严重程度(S)评价标准》、《DFMEA潜在失效模式发生概率(O)评价标准》、《DFMEA潜在失效模式发现难度(D)评价标准》。
3.5 PFMEA小组负责制定《PFMEA潜在失效后果严重程度(S)评价标准》、《PFMEA潜在失效模式发生频度(O)评价标准》、《PFMEA潜在失效模式发现难度(D)评价标准》。
4.工作程序4.1 设计FMEA的开发实施4.1.1 DFMEA实施的时机4.1.1.1 按APQP的计划进行DFMEA。
4.1.1.2 在出现下列情况时,DFMEA小组应在产品零件图纸设计之前进行DFMEA活动:① 开发新产品/产品更改;② 产品应用的环境发生变化;③ 材料或零部件发生变化。
4.1.2 DFMEA实施前的准备工作① 产品研发部(R&D)牵头成立DFMEA(设计FMEA)小组,生产技术部、品管部、生产部、营销部、采购部等部门指定人员参加DFMEA小组,必要时,由品管部邀请供应商、客户参加。
② 在DFMEA活动实施前,DFMEA小组应制定出《DFMEA潜在失效后果严重程度(S)评价标准》、《DFMEA潜在失效模式发生概率(O)评价标准》、《DFMEA潜在失效模式发现难度(D)评价标准》。
潜在失效模式及后果分析(FMEA)
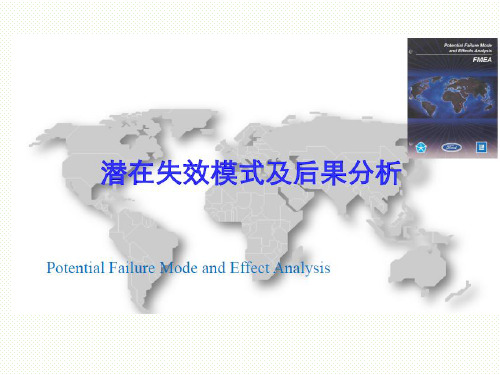
1. PFMEA简介--作用
人
机
料
法
环
测
失效模式
一般是发生 在产品上
失效后果
一般是指对 下工程或最 终顾客的影响
1. PFMEA简介--作用
范围包括公司内部和各阶层供应商产生的FMEA; 适用时,应阐明DFMEA和PFMEA; 通过将FMEA过程作为APQP过程的一个完整部分; 作为工程技术评审的一部分; 产品和过程设计定期的审核和批准的一部分。
实施FMEA的影响--跟踪和持续改进
• 为了确保FMEA所采取的预防措施是有效的,所以应对这些 行动进行追踪,对这方面的要求无论怎样强调都不过份,一个经
面对问题时FMEA应发挥的作用
可能会发生的问题 事先分析 了解原因
已做的事
要做的事
发生了什么事 什么原因
4
FMEA解决问题的逻辑思路
现行预计的产品/过程 可能产生的失效模式
分 析 对顾客或下工程的影响
哪些原因可能造成这个 失效模式
分 析
可采取的对策
是否消除
5
PFMEA实施的时间与时机
概念
• 事前花时间很好地进行综合的FMEA分析,能够容 易、低成本地对产品或过程进行修改,从而减轻 事后修改的危机
• 适当应用FMEA是一个相互作用的过程,永无止境
实施FMEA的影响--RPN分值
• 不适合将一个小组的FMEA分数和其它组的FMEA分数 进行比较,因为即使设计或过程是一样的,但由于 每个状况不一样所以打出来的分数也会不一样
其发生的 几率为何?
为有可能 被预防和 探测吗?
可以做什么? -设计变更 -过程变更 -特别的控制 -标准、程序或
指南的更改
潜在失效模式及后果分析(PFMEA)
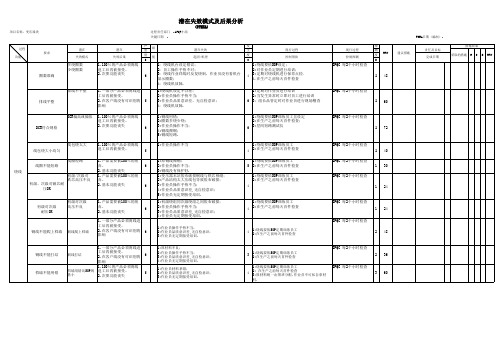
过程 要求 功能
潜在 失效模式
潜在 失效后果
潜在失效 起因/机理
现行过程 控制预防
现行过程 控制探测
焊锡不能虚焊,假焊, 焊锡虚焊,假焊,包 2.有外观项目上的问题,并 焊 包焊 且被绝大多数顾客( >75% )
察觉到 1.100%的产品在处理前,必 须在线返工。 2.有外观项目上的问题,并 焊锡不能太深 焊锡太深 且被绝大多数顾客( >75% ) 察觉到 一次焊锡 1.100%的产品在处理前,必 须在线返工。 焊锡焊满变压器引脚1圈 焊锡不能焊满变压 2.有外观项目上的问题,并 (360°) 器引脚1圈(360°) 且被绝大多数顾客( >75% ) 察觉到 1.100%的产品在处理前,必 须在线返工。 焊锡后PIN要光亮 焊锡后PIN不光亮 2.有外观项目上的问题,并 且被绝大多数顾客( >75% ) 察觉到 1.100%的产品在处理前,必 须在线返工。 胶布用错比SOP规 2.有外观项目上的问题,并 胶布不能用错 格小 且被绝大多数顾客( >75% ) 察觉到 1.100%的产品在处理前,必 须在线返工。 胶布用错比SOP规 磁芯背胶 2.有外观项目上的问题,并 胶布不能用错 格大 且被绝大多数顾客( >75% ) 察觉到 1.100%的产品在处理前,必 须在线返工。 2.有外观项目上的问题,并 胶布歪斜 胶布不能歪斜 且被绝大多数顾客( >75% ) 察觉到 1.100%的产品在处理前,必 须在线返工。 2.有外观项目上的问题,并 点黑胶面积太大 且被绝大多数顾客( >75% ) 察觉到 点黑胶正确 1.100%的产品在处理前,必 须在线返工。 点黑胶 2.有外观项目上的问题,并 点黑胶面积太小 且被绝大多数顾客( >75% ) 察觉到 1.100%的产品在处理前,必 须在线返工。 2.有外观项目上的问题,并 黑胶需要烘干 黑胶不能烘干 且被绝大多数顾客( >75% ) 察觉到
FMEA潜在失效模式及后果分析

2.改变弹簧几何尺寸
8
HIC
1.回火温度超差
2.回火时间超差
3
见上
质保部打硬度2只/班
4
96
8
HIC
1.回火炉设备故障
2.温度计失效
2
-设备预防性维修
-温度计采用PLC控制、温控报警装置
-定期对温度计标定、报警装置标定
-温度计寿命管理
-记录纸100%数据记录
-操作工检查1次/2h
-每周重新配置
检查PH值2次/班
5
90
加作业指导书关于表调液的调整方法
生产科
6
3
5
90
9-4磷化
精密度、厚度未符合要求
弹簧涂层易剥落防锈防腐性能降低
6
温度、时间、喷头压力、总酸度、游离酸度、促进剂比例失调
4
-检测中心对磷化液进行来料检查
-.操作者点检1次/2h
-检查磷化膜外观1次/2h
-检测SEA/重量2次/月
1.操作工定期抽检一班1次/2h
2.质保定期抽检1次/4h
3
72
专用量具
6
4
2
40
2
冷卷成形
-达到指定几何尺寸:
表面平滑
2-3.旋向错误
影响弹簧影响弹簧装配
6
方向绕反
2
同上
最后线菏载测试误差验证
1
12
总圈数
2-4.自由长度
力超差
影响整车舒适性
7
HIC
1.顶杆节距推出误差
2.设备精度误差
3
-首件样品确认程序
-设备PM计划
-.操作者1次/2h
-.QC 2次/4h
潜在失效模式与后果分析(FMEA)
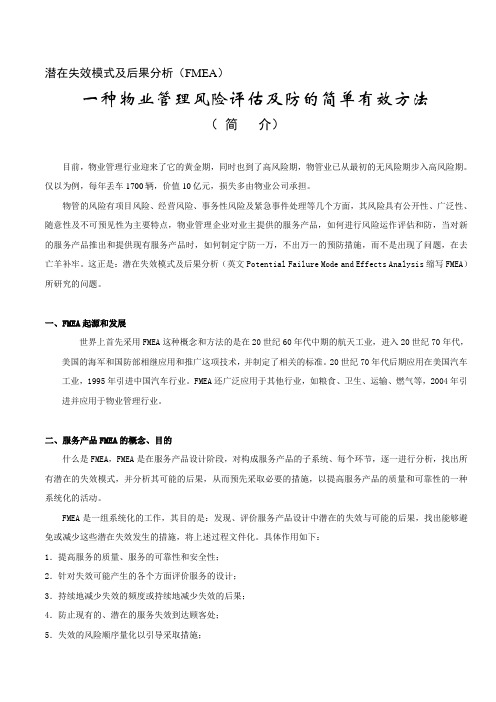
潜在失效模式及后果分析(FMEA)一种物业管理风险评估及防的简单有效方法(简介)目前,物业管理行业迎来了它的黄金期,同时也到了高风险期,物管业已从最初的无风险期步入高风险期。
仅以为例,每年丢车1700辆,价值10亿元,损失多由物业公司承担。
物管的风险有项目风险、经营风险、事务性风险及紧急事件处理等几个方面,其风险具有公开性、广泛性、随意性及不可预见性为主要特点,物业管理企业对业主提供的服务产品,如何进行风险运作评估和防,当对新的服务产品推出和提供现有服务产品时,如何制定宁防一万,不出万一的预防措施,而不是出现了问题,在去亡羊补牢。
这正是:潜在失效模式及后果分析(英文Potential Failure Mode and Effects Analysis缩写FMEA)所研究的问题。
一、F MEA起源和发展世界上首先采用FMEA这种概念和方法的是在20世纪60年代中期的航天工业,进入20世纪70年代,美国的海军和国防部相继应用和推广这项技术,并制定了相关的标准。
20世纪70年代后期应用在美国汽车工业,1995年引进中国汽车行业。
FMEA还广泛应用于其他行业,如粮食、卫生、运输、燃气等,2004年引进并应用于物业管理行业。
二、服务产品FMEA的概念、目的什么是FMEA,FMEA是在服务产品设计阶段,对构成服务产品的子系统、每个环节,逐一进行分析,找出所有潜在的失效模式,并分析其可能的后果,从而预先采取必要的措施,以提高服务产品的质量和可靠性的一种系统化的活动。
FMEA是一组系统化的工作,其目的是:发现、评价服务产品设计中潜在的失效与可能的后果,找出能够避免或减少这些潜在失效发生的措施,将上述过程文件化。
具体作用如下:1.提高服务的质量、服务的可靠性和安全性;2.针对失效可能产生的各个方面评价服务的设计;3.持续地减少失效的频度或持续地减少失效的后果;4.防止现有的、潜在的服务失效到达顾客处;5.失效的风险顺序量化以引导采取措施;6.优先使用行政的和工程的努力、时间、人力资源和其他资源;7.运用团队原则和持续改进方法以获得好的服务产品;8.FMEA是补充设计时,必须做哪些事情才能使顾客满意;9.所有的FMEA都关注服务产品设计;10.应用于新的服务产品设计和现有未发生失效服务产品。
潜在失效模式及后果分析(FMEA)
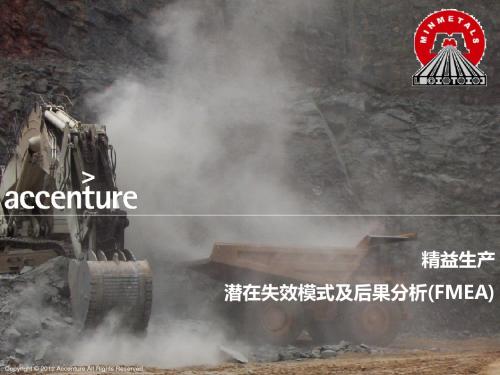
11
FMEA的第四步:严重度
后果 影响到人 员或不符 合政府的 法规 评定准则:后果的严重度 潜在失效模式在无警告的情形下影响到人身或不符合政府的法规 严重度 10
潜在失效模式在有警告的情形下影响到人身或不符合政府的法规
9
对设备 的影响
丧失设备主要功能(不能运行)
部分功能下降,设备效率降低(车辆能运行,但效率下降) 影响生产的正常进行(生产不能进行,影响时间大于1天) 对生产有部分的影响(生产能够进行,但生产效率下降) 无可辨别的后果。
17
频度 10 9 8 7 6 5 4 3 2 1
低:相对很少发生的失效
极低:失效不太可能发生
Copyright © 2012 Accenture All Rights Reserved.
FMEA的第七步:探测度
探测性 几乎 不可能 准则 绝对肯定不可能 探测 控制方法可能探 测不出来 控制有很少的机 会能探测出 控制有很少的机 会能探测出 检查类别 A B C X 探测方法的推荐范围 不能探测或没有检查 只能通过间接或随机检查来实 现控制 只通过目测检查来实现控制 只通过双重目测检查来实现控 制 探测 度 10
精益生产 潜在失效模式及后果分析(FMEA)
Copyright © 2012 Accenture All Rights Reserved.
什么是潜在失效模式及后果分析(FMEA) 在产品生产过程阶段,对构成产品的子系统、 零件,对构成过程的各个工序逐一进行分析, 找出所有潜在的失效模式,并分析其可能的后 果,从而预先采取必要的措施,以提高产品的 质量和可靠性的一种系统化的活动
Copyright © 2012 Accenture All Rights Reserved.
潜在失效模式及后果分析FMEA

9
很高
车辆/系统无法运行(丧失基本功能)。
8
高
车辆/系统能运行,但性能下降。顾客很不满意。
7
中等
车辆/系统能运行,但舒适性/方便性方面失效。顾客不满意。
典型的失效模式可以是,但不限于下列情况:
破碎 粘结
滑动(无法保持全扭力)
变形 氧化
无法支撑(构造的)
松动 断裂
支撑不足(构造的)
泄露 无法传递扭力 粗糙的接合
脱离过快 信号不适当 间歇信号 无信号
EMC/RFI 漂移
注:应该用“物理的”、专业性的术语来描述潜在失效模式,而不同于顾客所 见的
现象。
11)潜在失效后果 潜在失效的后果就是失效模式对功能的影响,就如顾客感受 的一样。
典型的失效后果可能是,但不限于:
噪音
外观不良
粗糙
不适的异味
运行不良
不稳定
无法运作
运行减损
间歇运行 发热 泄露 定期的不符合
12)严重度(S)
严重度是对一个已假定失效模式的最严重影响的评价等级。 严重度是在单独FMEA范围内的一个比较级别。要减少失效 严重度级别数值,只能通过设计变更来实现。严重度应该 使用下一张的指南来评价:
FMEA Potential Failure Mode and Effects Analysis
潜在失效模式及后果分析
什么是FMEA
FMEA可以描述为一组系统化的活动,其目 的是:
发现和评价产品/过程中潜在的失效及其失 效后果;
找到能够避免或减少这些潜在失效发生的 措施;
将上述整个过程文件化。
轻 突然爆破的严重度,“安全带”可以减轻车辆撞击的
严 重度。
推荐的DFMEA严重度评价准则
FMEA潜在失效模式及后果分析

FMEA (F ailure M ode and E ffects A nalyses )——潜在失效模式及后果分析------预防问题发生的有效工具初次接触FMEA ,感到比较陌生,以前仅仅在质量专业资格考试的教材中看到过简短的介绍,对它并没有过多的了解。
接到FMEA 培训的任务,让我有了深入了解它的机会,接下来,让我们共同揭开它神秘的面纱。
首先,我们来了解一下,什么是FMEA ?FMEA 是在产品设计阶段和过程设计阶段,对构成产品的子系统、零件,对构成过程的各个工序逐一进行分析,找出所有潜在的失效模式,并分析其可能的后果,从而预先采取必要的措施,以提高产品的质量和可靠性的一种系统化的活动,并将全部过程形成文件。
FMEA 是一种工具,是对确定设计或过程必须做哪些事情才能使顾客满意这一过程的补充;它是一种事前行为,可以帮助我们一次就把事情做对,通过运用FMEA ,就可以实现将内部的产品制造装配过程的问题纠正及外部客户投诉产生的纠正成本降到最低。
FMEA 具备以下几方面的特点:1. 失效还未产生,可能发生、但不是一定要发生;2.在设计或过程开发阶段前开始;3.需要由各种有经验和专业知识的人组成小组合作;4.FMEA 分析的文件记录为专用表格,作为动态文件使用,按照过程/产品/服务寿命周期期间要求随时更改;4.其核心以预防为主,对潜在失效模式的风险和后果进行评定;5.指导贯穿整个过程、产品和服务周期;FMEA 有哪些类型?1.SFMEA ——系统FMEA ;2.DFMEA ——产品FMEA (设计FMEA );3.PFMEA ——过程FMEA (制造/装配FMEA );4.AFMEA ——应用FMEA ;5.SFMEA ——服务FMEA ;6.PFMEA ——采购FMEA 。
从这些分类我们可以看出FMEA 应用于产品的设计初期、采购、生产过程、服务等过程,其应用范围之广,堪称强大。
介绍一下FMEA 的发展历史,世界上首次采用FMEA 这种概念与方法的是在20世纪60年代中期美国的航天工业。
- 1、下载文档前请自行甄别文档内容的完整性,平台不提供额外的编辑、内容补充、找答案等附加服务。
- 2、"仅部分预览"的文档,不可在线预览部分如存在完整性等问题,可反馈申请退款(可完整预览的文档不适用该条件!)。
- 3、如文档侵犯您的权益,请联系客服反馈,我们会尽快为您处理(人工客服工作时间:9:00-18:30)。
❖ 设计评审
❖ 样伯试验
❖ 确认试验
24
5如何做DFMEA?
❖ 17)探测度(D) 探测度是与设计控制中所 列的最佳探测控制相关联的定级数。探测度 是一个在某一FMEA范围内的相对级别。为 了获得一个较低的定级,通常计划的设计控 制(如确认和/或验证活动)必须予以改进。
❖
表面精加工规范不当
❖
行程规范不当
❖
规定的磨擦材料不当
❖
过热
❖
规定的公差不当
❖
典型的失效机理包括但不限于:
❖
屈服
化学氧化
❖
疲劳
电移
❖
材料不稳定性 蠕变
❖
磨损
腐蚀
19
5如何做DFMEA?
❖ 15)频度(O)
频度的指某一特定
的起因/机理在设计寿命内出现的可能性。描
述出现的可能性的级别数具有相对意义,而
2
❖ ①最终5用、户F:M使E用A产中品的的人四员类或组顾织客。
❖ ②OEM组装厂。 ❖ ③供应链制造:下游顾客(外部)或下一工序
操作者(内部)。 ❖ ④政府法规机构:制定并监督安全与环境法规
符合性的政府机构或其代理机构。这些要求和 规范可能影响到产品和过程。
3
7认识潜在失效影响(后果)
❖ 指顾客可感知的失效模式的影响,可以将其描述为 顾客可能的察觉或感受。
❖ 车型设计或更高一级装配过程设计的工程师/ 设计组
❖ 以及在生产过程中负责生产、装配和售后服 8
5如何做DFMEA?
❖ 仅供参考在城市内行驶等)的潜在失效模式应予以考虑。
❖ 典型的失效模式可包括,但不限于:
❖
裂纹
变形
❖
松动
泄漏
❖
粘结
氧化
❖
断裂
不传输扭矩
❖
打滑(不能承受全部扭矩) 无支撑(结构
的)
5如何做DFMEA?
❖ 典型的失效后果可能是但不限于以下情况:
❖ 噪音
粗糙
❖ 工作不正常
不起作用
❖ 外观不良
异味
❖ 不稳定
工作减弱
❖ 运行间歇
热衰变
❖ 泄漏
不符合法规
13
5如何做DFMEA?
❖ 12)严重度 严重度是一给定失效模式最严 重的影响后果的级别。
❖ 严重度是单一的FMEA范围内的相对定级结 果。严重度数值的降低只有通过改变设计才 能够实现。严重度应以表2化为导则进行估算:
5如何做DFMEA?
❖ 两种类型的设计控制:
❖ 预防:防止失效的起因/机理或失效模式出 现,或者降低 其出现的几率。
❖ 标杆分析研究
❖ 失效安全设计
❖ 设计和材料标准(内部和外部)
❖ 文件– 从相似设计中学到的最佳实践、经验
教训等的防错
23
❖ 两种类型的设计控制:
❖ 探测:在项目投产之前,通过分析方法或物 理方法,探测出失效的起因/机理或者失效模 式。
❖ 设计FMEA由4负谁责来设计做的F工M程师E编A制?,项目小组参
与分析。 ❖ 过程FMEA由负责制造的工程师编制,项目小组参
与分析。 ❖ 系统FMEA由项目总负责发起,系统FMEA 小组按
任务分配完成工作。
1
❖ ①成立小4组、FMEA的通用流程
❖ ②确定FMEA的关键日期(在项目计划中确定) ❖ ③收集类似产品已有的失效数量及比例 ❖ ④进行FMEA分析 ❖ ⑤采取措施 ❖ ⑥记录 ❖ ⑦在产品或过程更改前重新启动FMEA
17
5如何做DFMEA?
❖ 14)失效的潜在起因/机理 所谓失效的潜在 起因是指设计薄弱部分的迹象,其结果就是 失效模式。
18
5如何做DFMEA?
❖ 典型的失效起因可包括但不限于:
❖
❖
规定的材料不正确
❖
设计寿命设想不足
❖
应力过大
❖
润滑能力不足
❖
维护说明书不充分
❖
算法不正确
❖
维护说明书不当
❖
软件规范不当
❖
支撑不足(结构的)
刚性啮合
❖
脱离太快
信号不足
❖
信号间断
无信号
❖
EMC/RFI
漂移Βιβλιοθήκη 95如何做DFMEA?
❖ 注:潜在失效模式应以规范化或技术术语来 描述,不必与顾客察觉的现象相同。
10
5如何做DFMEA?
❖ 11)潜在失效的后果 潜在失效的后果定义 为顾客感受到的失效模式对功能的影响。
11
5如何做DFMEA?
14
5如何做DFMEA?
❖ 注:有时,高的严重度定级可以通过修改设 计、使之补偿或减轻失效的严重度结果来予 以减小。例如,“瘪胎”可以减轻突然爆胎 的严重度,“安全带”可以减轻车辆碰撞的 严重程度。
15
严重度DFMEA
16
5如何做DFMEA?
❖ 13)级别 本栏目可用于对那些可能需要附加的 设计或过程控制的部件、子系统或系统的产 品特殊性的分级(如关键、主要、重要、重 点)。
4
8认识失效起因
❖ 描述失效是因何发生的,它应被描述为可以纠正、 控制的事情。
❖ 在描述失效原因时应尽可能的详细,一个失效模式 可能有多个失效原因,应对每个原因独立分析。
5
❖ 从三个方面来评9估风,险最终评看估的结果是风险顺序
数RPN: ❖ 严重度S--指评估失效对顾客的影响等级。 ❖ 发生频度O--指一个失效原因可能的发生频率。 ❖ 探测度D—评估产品和过程控制对失效原因或
失效模式的探测能力。 ❖ RPN=严重度S×发生频度O ×探测度D
6
10特殊特性的识别
❖ 特殊特性 special characteristic ❖ 可能影响产品的安全性或法规符合性、配合、
功能、性能或其后续过程的产品特性或制造 过程参数。
7
5如何做DFMEA?
❖ 5.1DFMEA中顾客的定义
❖ 最終使用者
不是绝对的数值。通过设计变更或设计过程
变更(如设计检查表、设计评审、设计导则)
来预防或控制失效模式的起因/机理是可能影
响频度数降低的唯一的途径。(见表3。)
20
频度DFMEA
21
5如何做DFMEA?
❖ 16)现行设计控制
❖ 列出已经完成或承诺要完成的预防措施、设 计确认/验证或其它活动,并且这些活动将确 保设计对于所考虑的失效模式和/或起因/机理 是足够的。现行控制是指已被或正在被同样 或类似的设计所采用的那些措施(如设计评 审,失效与安全设计(减压阀),数学研究, 台架/试验室试验,可行性评审,样件试验, 道路试验,车队试验)。小组应一直致力于 22
❖ 要根据顾客可能发现或经历的情况来描述失 效的后果,要记住顾客既可能是内部的顾客 也可能是最终用户。如果失效模式可能影响 安全性右对法规的符合性,要清楚地予以说 明。
❖ 失效的后果应按照所分析的具体的系统、 子系统和系统之间存在着一种系统层次上的 关系。例如,一个零件可能会断裂,这样会 引起总成的振动、从而导致一个系统间歇性 12