PPL-73B-002产品试产作业程序(A-2)
生产试产程序
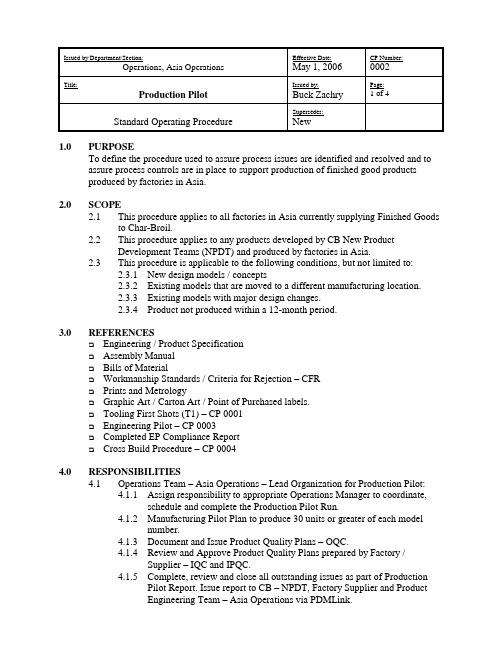
1.0PURPOSETo define the procedure used to assure process issues are identified and resolved and to assure process controls are in place to support production of finished good productsproduced by factories in Asia.2.0SCOPE2.1This procedure applies to all factories in Asia currently supplying Finished Goodsto Char-Broil.2.2This procedure applies to any products developed by CB New ProductDevelopment Teams (NPDT) and produced by factories in Asia.2.3This procedure is applicable to the following conditions, but not limited to:2.3.1New design models / concepts2.3.2Existing models that are moved to a different manufacturing location.2.3.3Existing models with major design changes.2.3.4Product not produced within a 12-month period.3.0REFERENCES❑Engineering / Product Specification❑Assembly Manual❑Bills of Material❑Workmanship Standards / Criteria for Rejection – CFR❑Prints and Metrology❑Graphic Art / Carton Art / Point of Purchased labels.❑Tooling First Shots (T1) – CP 0001❑Engineering Pilot – CP 0003❑Completed EP Compliance Report❑Cross Build Procedure – CP 00044.0RESPONSIBILITIES4.1Operations Team – Asia Operations – Lead Organization for Production Pilot:4.1.1Assign responsibility to appropriate Operations Manager to coordinate,schedule and complete the Production Pilot Run.4.1.2Manufacturing Pilot Plan to produce 30 units or greater of each modelnumber.4.1.3Document and Issue Product Quality Plans – OQC.4.1.4Review and Approve Product Quality Plans prepared by Factory /Supplier – IQC and IPQC.4.1.5Complete, review and close all outstanding issues as part of ProductionPilot Report. Issue report to CB – NPDT, Factory Supplier and ProductEngineering Team – Asia Operations via PDMLink.4.1.6Work with Factory and Product Engineers to identify and resolve allcritical relationship of processes to product.4.1.7Implement the Product Workmanship Standards and Criteria for productrejections. Obtain input from New Product Development Team as requiredfor clarification. Communicate these standards and criteria to the FactorySupplier.4.1.8Select and assemble product units in accordance with the productinstruction manual the planned quantity of production units to confirm fitand function and proper assembly capability.4.1.9Complete and Issue First Article report for specific Product being piloted.4.1.10First Article Report is authorization to the factory to produce product inaccordance with purchase order releases.4.1.11Confirm Warranty Parts – Release of Minimum Order Documentation isconducted and accurate.4.1.12Confirm successful completion of all certification and third party testing.4.2Product Engineering – Asia Operations4.2.1Assign Engineering Pilot responsibilities by Product EngineeringManager – Asia Operations.4.2.2To participate in internal review of model and provide comments toOperations Team – Asia Operations in support of Production Pilot Report.4.2.3Complete all required actions identified as open issues during theEngineering Pilot.4.2.4Confirm that all design issues are closed prior to production pilot run.4.3Factory/Supplier4.3.1To provide Product Engineering – Asia Operations with documentation(drawings) referencing completed tooling / process plan relating to themodel being reviewed.4.3.2To participate in internal review of model and provide comments toOperations Team – Asia Operations in support of Production Pilot Report.4.3.3Document and issue Product Quality Plans – IQC and IPQC.4.3.4For all off tool components complete metrology reports and provide Firstpiece Inspection (FPI) documentation to Product Engineering andOperations Team – Asia Operations. Note – This requirement should beachieved as part of the T1 process – Reference CP 0001.4.3.5To have available off tool parts and components needed to support thebuild of production pilot plan number of units.4.4Product Data System4.4.1To complete the product BOM’s and any revisions prior to the ProductionPilot Run.4.4.2To complete any revisions to product instruction manuals prior to theProduction Pilot Run.4.5NPD Team - Provide the following in support of MP.4.5.1Product Description Statement (PDS)4.5.2Product Specification Document (PSD)4.5.3Review and comments regarding Final Prototype Models4.5.4Complete Product Specifications and General Workmanship Standards.5.0Procedure5.1All parts for production pilot should be 100% manufactured off final tooling.5.2Review tooling to check repeatability of the parts.5.3Randomly select parts to assemble selected units per the Instruction Manual.5.4Check fit and function of the assembled units.5.5Compare ALL artwork to required standards, including, but not limited to thefollowing:5.5.1Graphic and carton art; POP; carton, rating and warning labels.5.5.2Instruction Manuals5.6Note any discrepancies between the Product Specification, BOM, InstructionManual and unit on PP Report.5.7Compare units to CFR / Workmanship Standards.5.8Perform functional test. (Use as consumer would)5.9Review final packaging and communicate any identified issues or concerns. Thisitem should be completed at EP.5.10Operations Team to work with Product Engineering Team – Asia Operations andsupplier factory to determine understanding of critical relationship of processesrequired to manufacture product.5.11If requested, send samples to US product development team.5.12Issue Production Pilot (PP) report to respective departments via PDMLink.5.13Process after Production Pilot and before First Production.5.13.1Supplier shall provide schedule for implementation of requiredimprovements as per the Production Pilot report.5.13.2Operations Team shall perform or arrange to have performed requiredproduct transit testing and provide test report / results to respectivedepartments via PDM Link.5.13.3If required, supplier shall send graphic samples to NPD Team and ProductEngineering – Asia Operations for review.5.13.4NPD Team Quality Manager shall provide finalized WorkmanshipStandards and Criteria for Rejection (CFR) documentation.5.13.5NPD Team to finalize Product Specification.5.13.6Supplier to provide final factory quality plan.5.13.7Supplier to provide sample of unit with all required improvements fromproduction pilot and close all issues related to the factory as noted in theProduction Pilot Report.5.13.8Product Data Systems Team to complete BOM, instruction manuals andany revisions prior to Production Run.5.13.9Supplier to complete updated drawings prior to first production run.5.13.10Product Data Systems Team to release final drawings prior to firstproduction run.5.13.11Operations Team – Asia Operations to issue First Article and authorize theFactory Supplier to produce specific new model grill.。
产品试产程序

产品试产程序1、目的验证整机或其零配件质量性能,确保顺利量产。
2 、适用范围第一次生产的新产品或关键零配件在功能或配合上有所改变的老产品需例行试产。
试产的对象可以是产品的功能、配合或加工工艺等。
3、职责3.1技术部负责发出试产通知,并准备相关资料。
3.2 生产部负责根据试产通知准备物料并编进《生产计划》内。
3.3质检部负责试产过程及结果的检验。
3.4生产部负责按照技术要求组织生产。
并对以配合或加工工艺为试产对象的试产,进行试产确认。
3.5如程序有变更或者试产程序时实验室在试产前三天提供程序给生产部(书面签收)。
负责小批量试产后新产品的性能实验,实验完成时间依据测试要求及测试项目而定。
4、程序4.1当新产品、新零部件在开发或量产前,需要确认其功能或相互间的结构配合是否达到设计要求时,技术部负责发出试产通知单(注明试产目的、要求达到的效果),同时项目组应发放相关图纸、BOM表(时间与试产通知下发时间同行)、工艺文件、正式的现场作业指导书、工装夹具、爆炸图、成品检验标准(时间在试产前一周)等资料;负责主持整个试产过程,对试产报告或测试报告进行核实和确认。
4.2生产部在技术部BOM表准备好的前提下于1个工作日内下达物料清单给采购部,根据试产通知要求时间结合生产实际情况编制《生产计划表》通知相关人员试产时间;根据《试制-鉴定表-APQP》存储保管试产产品。
4.3质检部根据技术部提供的成品检验标准及相关参数编制成品检验作业指导书(必要时),并对试产过程、成品进行检验。
4.4生产部根据技术要求、《生产计划表》组织好生产,在试产成品的包装箱封条处粘贴试产内容,并在试产结束1个工作日内提出书面的《试制-鉴定表-APQP》给相关人员核签。
4.5 研发负责人根据生产及质检部意见于4个小时内做最终结果的判定,最终结果必须包含以下内容:A:试产OK,是否可正常销售;B:试产NG,明确需返工整改的项目,整改完成时间、整改责任人;C:是否需要贸易部跟进市场反馈,如需要,须提供《试产跟踪记录》。
新产品试产工艺流程

新产品试产工艺流程一.工艺准备:1 )2)BOM文件:、附件(产品)BOM等。
PCBA托工:(长、宽、厚、拼接方式等)PCB贴片图:提供单板尺寸、置PCBA(以生产配置表为准按工站编二.工艺内部评审:1)工艺文件评审:评审有无缺陷的地方。
需要改善的地方2) 首板样机内部评审:评审电路板及样机是否有设计隐患和不合理设计。
3) 工装夹具评审:评审工装夹具设计和审批周期及内部手续。
4) 了解PCBA外协加工情况,确认其对后续的组装及调试是否有影响。
如有需要则在试产准备会上通报,并商定出处理措施。
试产前工艺评审会要以邮件的形式发出会议记录。
三、试产准备会确认内容1、明确试产目标:2、确定试产性质试产性质包括:1) 客户要求/新机种2) 更换供应商3) 设计变更/工程试做4) 常规实验5) 工程实验6) 增加模具/工程试做7) 其他3、参考图纸、BOM表、工艺文件:工艺部在工艺文件完成后内部召开试产前工艺评审会整合信息在试产准备会上做通报。
4、物料齐套性确认---计划部通报物料齐套情况。
包括生产备料后的报缺及缺料到货日期等信息。
5、IQC来料检验情况:数据内容包括不良问题的问题点,判定结果,判定人。
(方便后期组装时对接受不良品的验证及影响产品装配情况的判定)。
6、工装、设备调配情况---生产部根据生产配置表评估满足情况。
7、人员调配情况---生产部根据生产配置表评估满足情况。
8、项目成员试产工作分工:工艺协同硬件提供调试、测试技术支持。
工艺协同结构提供装配技术支持。
9、试产计划:根据试产准备会时确认的时间做出试产计划,以邮件的形式发给各项目成员。
试产计划内容包括人员培训时间:生产部调配时间(正式试产前)试产开始时间:生产部按排期确定试产时间首件检验时间(QA估算):试产总时间(PE估算):试产总结会时间(PE估算):试产准备会要填写《签到表》,会后发出<<试产准备会会议纪要>>,相应的问题对未完成跟踪项确定计划完成时间和实际完成时间,对相应负责人跟踪完成进度。
新产品试产流程

1、负责相关文件的核对、发行、制的跟踪。为生产线提供技术上的支持,生产问题的统计及处理。
4、召开试产后会议,总结试产情况,讨论是否量产。
品保部:参与产品验证,参加相关会议,试产过程的中的质量检测等。
(5)、能处理的问题应及时处理。不能处理的及时反馈到相关部门,并对相关部门的处理情况进行跟进。
15、试产时生产部应及时统计产品工时、辅料数据,并在试产后的二个工作日内将工时、辅料数据发送至财务部。
16、工程部在各制程段试产结束后的两个工作日内发行SOP。(经由文件中心发行至相关单位)。
17、工程部应完成试产的后续工作,包括但不限于以下内容:
2、此流程经总经理批准后施行,修改亦同。
拟定:******* 日期: ****** 日期: ***** 日期:
(1)、根据试产情况,对该修改的文件进行修改、发行。
(2)、发行尚未发行的文件。
(3)、对试产中反映出来的问题进行跟进处理。
18、试产的后续工作完成后,工程应在一个工作日内召开试产后会议。
(1)、参加人员:开发部、工程部、车间、品保部、仓库。
(2)、内容:总结试产情况,检查各项工作的完成情况(该发行的文件是否已经全部发行,该在文件中心存档的是否已经存档,该修改的是否已经全部修改),讨论是否可以量产。
7、工程部收到开发部门的资料后,应在两个工作日内基本完成对相关资料的编写、审核、签发。主要包括:
(1)、元件清单审核、发行。(经由文件中心发行至采购、仓库、财务)。
(2)、结构清单审核、发行。(经由文件中心发行至采购、仓库、财务)。
(3)、说明书审核、发行。(审核后经文件中心将发行版发行至仓库,审核版存档)。
公司试产流程作业规范
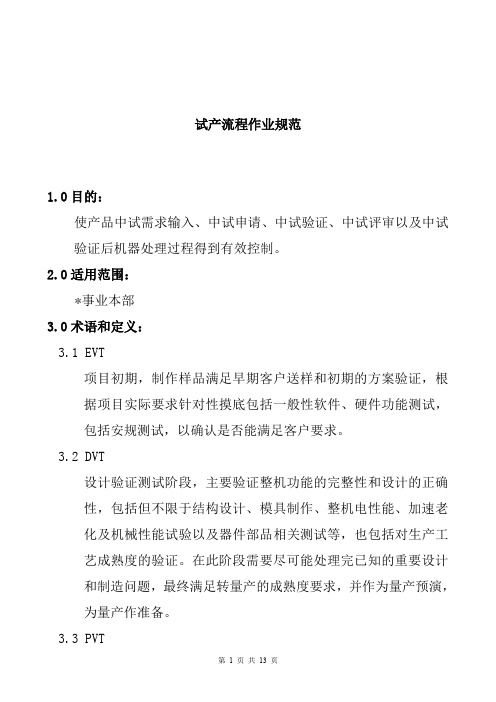
试产流程作业规范1.0目的:使产品中试需求输入、中试申请、中试验证、中试评审以及中试验证后机器处理过程得到有效控制。
2.0适用范围:*事业本部3.0术语和定义:3.1 EVT项目初期,制作样品满足早期客户送样和初期的方案验证,根据项目实际要求针对性摸底包括一般性软件、硬件功能测试,包括安规测试,以确认是否能满足客户要求。
3.2 DVT设计验证测试阶段,主要验证整机功能的完整性和设计的正确性,包括但不限于结构设计、模具制作、整机电性能、加速老化及机械性能试验以及器件部品相关测试等,也包括对生产工艺成熟度的验证。
在此阶段需要尽可能处理完已知的重要设计和制造问题,最终满足转量产的成熟度要求,并作为量产预演,为量产作准备。
3.3 PVT小批量生产验证测试阶段,主要验证DVT遗留问题、量产准备是否充分、以及各供应商批量生产的稳定性问题。
3.4中试包括EVT, DVT阶段,也可指业务需求样机的制作阶段。
3.5技术试验指产品开发导入时,对产品的功能、性能、安全规定以及可靠性作全面的测试验证过程。
试验条件一般包括:新产品开发、部件验证(如TP/液晶屏、电池、摄像头、主板元器件等)和软件升级或变更。
3.6试验评审指产品整个生产、测试、验证过程结束后,依据过程记录,对所中试的情况作综合的审核评价,一般情况下,评审结果有:试验通过、试验条件通过以及试验失败。
3.7 中试条件分类,A类、B类、C类产品定义3.7.1 A类产品定义:自研产品,硬件/核心软件、结构为新的设计,产品必须要中试,中试参考数量为50-100台;3.7.2 B类产品定义:3.7.2.1整机集成项目。
基于新的PCBA,新的外观结构,自主资源进行整机整合,按客户需求定制化。
产品必须要中试,中试参考数量为50-100台;3.7.2.2 A类项目的改型延伸项目:产品必须要中试,中试参考数量为20-50台;3.3.3 C类产品定义:在B类项目的基础上针对关键资源、客户需求进行延伸的项目或者经总经理办公会同意的对经营或客户及市场有重大意义的EMS项目。
新产品试产工艺流程

新产品试产工艺流程一.工艺准备:1 )2)工艺输出文件包括:BOM文件:电路板BOM等。
PCBA托工:PCB(长、宽、厚、拼接方式等)PCB贴片图:提供单板尺寸、置描述PCBA调试作业指导书:内容包括芯片程序烧录、电路板程序烧录、电气参数测试、功能测试。
组装作业指导书:内容包括工艺流程、生产配置表、各工站指导书(以生产配置表为准按工站编写的焊接、装配、验证、网络配置等内容)。
包装作业指导书:指导产品如何包装及验证。
老化作业指导书:指导老化过程重要有机芯老化、整机老化和老化记录。
设备操作指导书:设备安全操作规程。
二.工艺内部评审:1)工艺文件评审:评审有无缺陷的地方。
需要改善的地方2) 首板样机内部评审:评审电路板及样机是否有设计隐患和不合理设计。
3) 工装夹具评审:评审工装夹具设计和审批周期及内部手续。
4) 了解PCBA外协加工情况,确认其对后续的组装及调试是否有影响。
如有需要则在试产准备会上通报,并商定出处理措施。
试产前工艺评审会要以邮件的形式发出会议记录。
三、试产准备会确认内容1、明确试产目标:2、确定试产性质试产性质包括:1) 客户要求/新机种2) 更换供应商3) 设计变更/工程试做 4) 常规实验5) 工程实验6) 增加模具/工程试做7) 其他3、参考图纸、BOM表、工艺文件:工艺部在工艺文件完成后内部召开试产前工艺评审会整合信息在试产准备会上做通报。
4、物料齐套性确认---计划部通报物料齐套情况。
包括生产备料后的报缺及缺料到货日期等信息。
5、IQC来料检验情况:数据内容包括不良问题的问题点,判定结果,判定人。
(方便后期组装时对接受不良品的验证及影响产品装配情况的判定)。
6、工装、设备调配情况---生产部根据生产配置表评估满足情况。
7、人员调配情况---生产部根据生产配置表评估满足情况。
8、项目成员试产工作分工:工艺协同硬件提供调试、测试技术支持。
工艺协同结构提供装配技术支持。
9、试产计划:根据试产准备会时确认的时间做出试产计划,以邮件的形式发给各项目成员。
新产品试产工艺流程

新产品试产工艺流程一.工艺准备:、包装 、附件(产品) 等。
托工: 拼接图:发到印制板厂的印制板加工要求 长、宽、厚、拼接方式等钢网制作文件:外加工 所需单板制作钢网 贴片图:提供单板尺寸、置描述焊接作业指导书:外协托工电路板焊接加工要求。
检验文件:成品检验规程、出厂检验报告。
调试作业指导书:内容包括芯片程序烧录、电路板程序烧录、电气参数测试、功能测试。
组装作业指导书:内容包括工艺流程、生产配置表、各工站指导书 以生产配置表为准按工站编写的焊接、装配、验证、网络配置等内容 。
包装作业指导书:指导产品如何包装及验证。
老化作业指导书:指导老化过程重要有机芯老化、整机老化和老化记录。
设备操作指导书:设备安全操作规程。
二.工艺内部评审:)工艺文件评审:评审有无缺陷的地方。
需要改善的地方首板样机内部评审:评审电路板及样机是否有设计隐患和不合理设计。
工装夹具评审:评审工装夹具设计和审批周期及内部手续。
了解 外协加工情况,确认其对后续的组装及调试是否有影响。
如有需要则在试产准备会上通报,并商定出处理措施。
试产前工艺评审会要以邮件的形式发出会议记录。
三、 试产准备会确认内容、明确试产目标:、确定试产性质试产性质包括: 客户要求 新机种 更换供应商 设计变更 工程试做常规实验工程实验 增加模具 工程试做 其他、参考图纸、 表、工艺文件:工艺部在工艺文件完成后内部召开试产前工艺评审会整合信息在试产准备会上做通报。
、物料齐套性确认 计划部通报物料齐套情况。
包括生产备料后的报缺及缺料到货日期等信息。
、 来料检验情况:数据内容包括不良问题的问题点,判定结果,判定人。
(方便后期组装时对接受不良品的验证及影响产品装配情况的判定)。
、工装、设备调配情况 生产部根据生产配置表评估满足情况。
、人员调配情况 生产部根据生产配置表评估满足情况。
、项目成员试产工作分工:工艺协同硬件提供调试、测试技术支持。
工艺协同结构提供装配技术支持。
(完整版)新产品试产流程
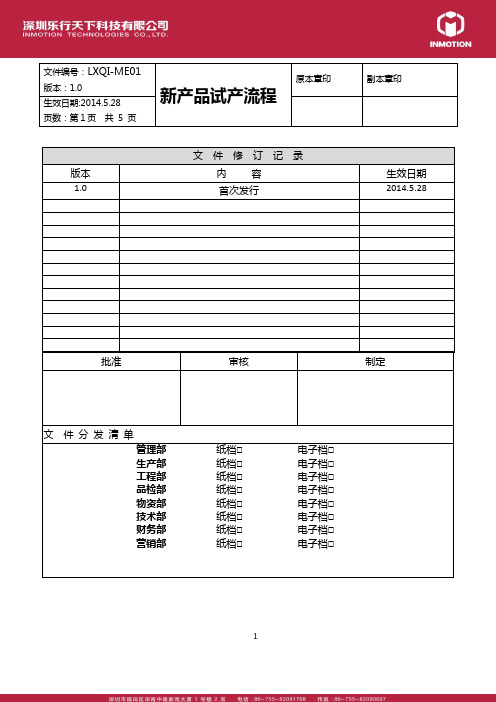
版本:1.0 新产品试产流程原本章印副本章印生效日期:2014.5.28页数:第1页共5 页文件修订记录版本内容生效日期1.0 首次发行2014.5.28批准审核制定文件分发清单管理部纸档□电子档□生产部纸档□电子档□工程部纸档□电子档□品检部纸档□电子档□物资部纸档□电子档□技术部纸档□电子档□财务部纸档□电子档□营销部纸档□电子档□版本:1.0 新产品试产流程原本章印副本章印生效日期:2014.5.28页数:第2页共5 页1目的本程序旨在建立对新产品试产过程的控制,以期达到新产品顺利进入批量生产阶段。
2范围本程序文件适合于INMOTION所有新产品的试产过程,其中包含包装以及量产后物料(塑胶、电子元件、五金、包装、软件等)的变更。
3定义无4权责4.1技术部负责新产品的设计开发工作,以及组织协调和统筹新产品的试作工作,负责解决试作中存在的问题并确保新产品顺利量产;4.2工程部负责对新产品的试产过程中产生的不良品及硬件、机械和工艺潜在问题的分析,并跟进其改善工作, 负责P/R制作并组织召开P/R后会议, 负责完成PFMEA及作业指示.负责对新产品的试作过程中排拉图的排列和作业时间计算以确定人力和效率,以及对作业动作进行优化。
4.3品质部负责对新产品试产生产过程的监控和品质保证,以及对试产过程作统计制程管制,同时对试产来料进行检验,以及对新产品进行可靠性验证。
4.4生产部负责新产品的试产的生产工作,提供试产的生产情况,结果统计等。
版本:1.0 新产品试产流程原本章印副本章印生效日期:2014.5.28页数:第3页共5 页5作业内容5.1 技术部召开新产品介绍会:标志一个新产品(新项目)正式启动,进入试产过程控制.5.2 技术部组织召开新产品介绍会:工程部了解新产品的功能、测试、结构、组装等方面情况,并将相类似产品易发生的问题点反馈技术部,要求其在设计开发阶段就考虑改善.在此阶段,需对新产品作生产可行性方面的风险评估(DFMEA), 技术部在此产品设计开发阶段就采取措施,降低或避免风险,以使新产品顺利进入试作过程.5.3 工程部确定此新产品的具体生产流程图、PFMEA及从生产工艺、品质、效率等方面考虑提出对设计开发的要求:如PCB板是作拼板还是作单板等,结构设计上怎样保证装配品质可靠等.5.4 工程部确定是否需要引进新工艺、新技术等,如需要则工程部须作好先期准备工作,着手引进消化吸收新工艺、新技术,并对生产人员、QC人员等作出培训,使相关人员尽快了解、熟悉新工艺、新技术,并将新工艺、新技术中的关键参数、工艺标准以及控制点等加入到相应制程控制文件、生产工艺标准中,以便对新工艺、新技术进行监控管理.5.5 工程部根据技术部文件准备样品制作所需的设备、仪器、治工具等,须在此阶段完成新产品的工程流程图和PFMEA,对即将开始的样品制作中可能发生的问题点及风险作出评估,并采取相应措施预防和降低这些高风险工站的风险指数,以使样品制作顺利进行.5.6 样品制作(QA1):PE、RD、QC等参与指导生产作业,针对来料、样品制作中存在问题点及不良品,PE进行汇总,完成样品制作<不良品分析报告>,提出改善对策及责任担当部门,要求其在下一次样品制作前将存在问题改善解决.5.7 PE须对自己的不良品分析报告作出跟进,针对各个问题点逐一跟进责任部门改善,如各问题点都已得到改善和解决,或者已采取有效对策来防止不良复发, 同时样品通过了QC 实验测试并达到可进行试产及客户要求的情况下,才可进入下一阶段,即:第二次样品制作(QA2),如果此阶段没有明显品质、工艺问题,则可直接进入量产阶段。
研发新产品报价打样试产流程图
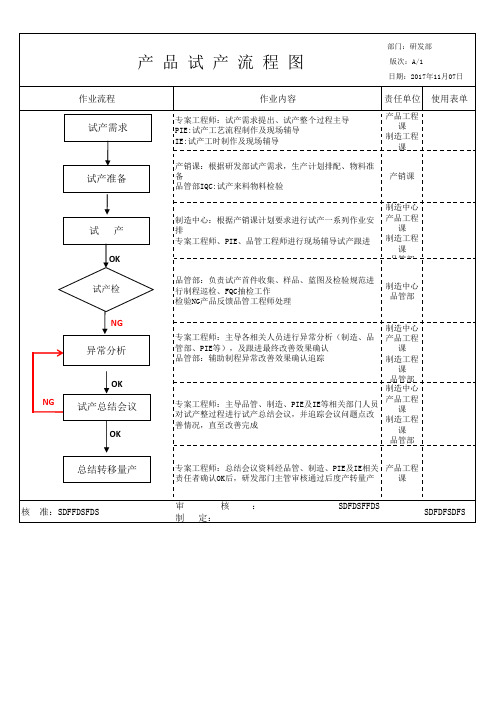
OK
制造中心
专案工程师:主导各相关人员进行异常分析(制造、品 产品工程
管部、PIE等),及跟进最终改善效果确认
课
品管部:辅助制程异常改善效果确认追踪
Байду номын сангаас制造工程
课
品管部
制造中心
专案工程师:主导品管、制造、PIE及IE等相关部门人员 对试产整过程进行试产总结会议,并追踪会议问题点改 善情况,直至改善完成
产品工程 课
制造工程 课
品管部
总结转移量产
专案工程师:总结会议资料经品管、制造、PIE及IE相关 产品工程
责任者确认OK后,研发部门主管审核通过后度产转量产
课
核 准:SDFFDSFDS
审
核:
制 定:
SDFDSFFDS
SDFDFSDFS
产销课
试产 OK
试产检
制造中心:根据产销课计划要求进行试产一系列作业安 排 专案工程师、PIE、品管工程师进行现场辅导试产跟进
制造中心 产品工程
课 制造工程
课 品管部
品管部:负责试产首件收集、样品、蓝图及检验规范进 行制程巡检、FQC抽检工作 检验NG产品反馈品管工程师处理
制造中心 品管部
NG 异常分析
产品试产流程图
部门:研发部 版次:A/1 日期:2017年11月07日
作业流程 试产需求
试产准备
作业内容
责任单位 使用表单
专案工程师:试产需求提出、试产整个过程主导 PIE:试产工艺流程制作及现场辅导 IE:试产工时制作及现场辅导
产品工程 课
制造工程 课
产销课:根据研发部试产需求,生产计划排配、物料准 备 品管部IQC:试产来料物料检验
试产作业流程[模板]
![试产作业流程[模板]](https://img.taocdn.com/s3/m/eb884f2a58f5f61fb6366655.png)
试产作业流程
1. 目的
规范注塑模具试产作业管理,确保注塑模具试产作业的顺利进行。
降低试产各方面的成本,提升试产效率,满足项目进度及客户的需求。
2. 概述
本文描述了注塑模具试产作业管理过程及各角色职责,包括各阶段对应角色所需输出及输入的文件及资料。
3. 术语
4. 角色与职责
5. 流程图
清晰版本见如下附件:
6.流程说明
7.裁剪指南
无
8.流程范围
9.流程绩效指标
10.支持文件
11.流程接口描述
1)对应的上层流程:
2)输入的流程接口描述:
3)输出的流程接口描述
12.记录的保存
13.补充说明
13.1模具在机台上维修确认时效权限:
模具异常需在机台上维修确认的,超过半小时的原则上下机处理。
特殊情况授予以下人员审批权限:试模PE1H内试模领班2H内试模课长3H内。
超过三小时必须经项目人员或工模人员最高主管与注塑工程人员最高主管确认批准。
所有异常工时同步转嫁需求责任部门。
13.2 试产订单每套模具调机损耗用料标准:
180T 调机损耗5KG /套模具280T调机损耗10KG /套模具
350T调机损耗15KG /套模具双色机调机损耗10KG /套模具
调机损耗用料随试产订单同步下达。
13.3 试产订单损耗结案条件
试产工单损耗按照10%下达,同时500PCS以内的工单按照实际生产数量结案。
500PCS以上的工单按照完成计划数量的80%自动设置结案。
对于试产过程中的模具维修,由项目工程师按实际情况用补料单适当补料完成试产任务。
14.文件拟制/修订记录。
产品试装工作流程
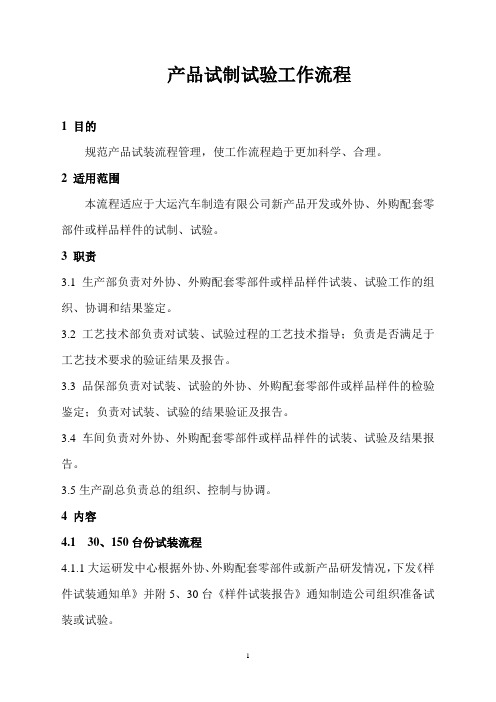
产品试制试验工作流程1 目的规范产品试装流程管理,使工作流程趋于更加科学、合理。
2 适用范围本流程适应于大运汽车制造有限公司新产品开发或外协、外购配套零部件或样品样件的试制、试验。
3 职责3.1 生产部负责对外协、外购配套零部件或样品样件试装、试验工作的组织、协调和结果鉴定。
3.2 工艺技术部负责对试装、试验过程的工艺技术指导;负责是否满足于工艺技术要求的验证结果及报告。
3.3 品保部负责对试装、试验的外协、外购配套零部件或样品样件的检验鉴定;负责对试装、试验的结果验证及报告。
3.4车间负责对外协、外购配套零部件或样品样件的试装、试验及结果报告。
3.5生产副总负责总的组织、控制与协调。
4 内容4.1 30、150台份试装流程4.1.1大运研发中心根据外协、外购配套零部件或新产品研发情况,下发《样件试装通知单》并附5、30台《样件试装报告》通知制造公司组织准备试装或试验。
4.1.2生产部根据研发中心通知,下发《工作联络单》通知并组织工艺技术部、品保部、车间对经检验合格的配套零部件或样品样件在规定的时间和地点进行试装、试验工作。
4.1.3 品保部外检人员要对外协、外购配套零部件或样品样件,按技术要求进行检查验证,查验供应商是否有自检合格报告、材质试验报告、金相分析报告,对涉及3C认证的强制性检查产品或环保项要有国家有关部门出具的型式试验报告书。
否则不提供《试装零部件检验报告》。
4.1.4经检验员检验合格的试装、试验样品样件,且有相关合格报告书的给予入库,并做好标识,分类存放;经检验员检验不合格的试装、试验零部件不予入库,并做好标识,由技术中心负责退回原生产单位。
4.1.5 工艺技术部按生产部下发的《工作联络单》,组织相关的工程技术人员,准时到达规定地点参加试装、试验并记录车身VIN码号。
4.1.6车间按生产部下发的《工作联络单》,组织安排相关人员对试装、试验的零部件,按工艺要求或技术标准进行试装、试验并进行标识。
新产品试产作业流程(参考模板)
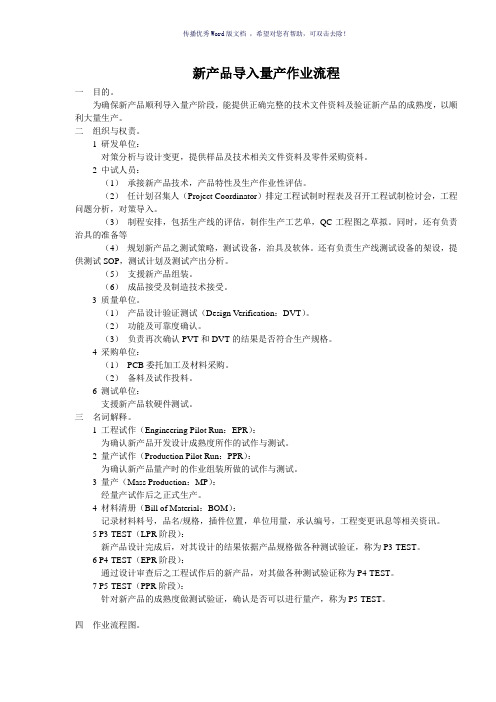
新产品导入量产作业流程一目的。
为确保新产品顺利导入量产阶段,能提供正确完整的技术文件资料及验证新产品的成熟度,以顺利大量生产。
二组织与权责。
1 研发单位:对策分析与设计变更,提供样品及技术相关文件资料及零件采购资料。
2 中试人员:(1)承接新产品技术,产品特性及生产作业性评估。
(2)任计划召集人(Project Coordinator)排定工程试制时程表及召开工程试制检讨会,工程问题分析,对策导入。
(3)制程安排,包括生产线的评估,制作生产工艺单,QC工程图之草拟。
同时,还有负责治具的准备等(4)规划新产品之测试策略,测试设备,治具及软体。
还有负责生产线测试设备的架设,提供测试SOP,测试计划及测试产出分析。
(5)支援新产品组装。
(6)成品接受及制造技术接受。
3 质量单位。
(1)产品设计验证测试(Design Verification:DVT)。
(2)功能及可靠度确认。
(3)负责再次确认PVT和DVT的结果是否符合生产规格。
4 采购单位:(1)PCB委托加工及材料采购。
(2)备料及试作投料。
6 测试单位:支援新产品软硬件测试。
三名词解释。
1 工程试作(Engineering Pilot Run:EPR):为确认新产品开发设计成熟度所作的试作与测试。
2 量产试作(Production Pilot Run:PPR):为确认新产品量产时的作业组装所做的试作与测试。
3 量产(Mass Production:MP):经量产试作后之正式生产。
4 材料清册(Bill of Material:BOM):记录材料料号,品名/规格,插件位置,单位用量,承认编号,工程变更讯息等相关资讯。
5 P3-TEST(LPR阶段):新产品设计完成后,对其设计的结果依据产品规格做各种测试验证,称为P3-TEST。
6 P4-TEST(EPR阶段):通过设计审查后之工程试作后的新产品,对其做各种测试验证称为P4-TEST。
7 P5-TEST(PPR阶段):针对新产品的成熟度做测试验证,确认是否可以进行量产,称为P5-TEST。
OPPO手机产品试产流程作业指导书

更改记录1 目的规范新机型试产的流程,明确试产过程中各职能块的工作职责及相互的协作关系,保证试产过程能有序和高效地进行,达到试产的目的。
2 范围适用于公司自主研发及合作开发(ODM)的新产品试产的全过程。
3 权责3.1 研发部:项目经理:负责对整个项目工作进度、试产时间进行总协调和确认;负责每周一次呈报《项目时间进度表》,按《新品资源检查表》提供试产资源;负责在试产前发布《试产申请单》,对试产过程的整体资源进行协调;组织项目成员在试产前两天召开试产产前沟通会,试产结束后2-3个工作日内召开试产总结沟通会;若试产计划变更或调整须及时通知相关人员。
并负责试产问题的跟踪落实工作。
研发项目组成员:项目成员如结构工程师、硬件工程师、软件工程师等根据各试产阶段的需求,负责提供如白油图、钢网文件、原理图、2D/3D图等生产技术工艺文件;试产当天负责到现场协助项目PE进行技术指导或确认;负责提供试产故障机分析、异常分析等必要的技术支持工作。
3.2 PMC部:PMC负责人:根据新机型的品质问题及工程准备情况确定具体试产日期,并在试产前两天发出新品试产时间安排以提醒相关人员;根据试产申请单合理安排试产计划,若试产计划变更需及时调整并通知相关人员;负责试产物料的跟进,确保试产所需的物料提前齐套;负责物料接收、备料、发料;负责在试产生产结束后统计公布尾料信息,并按试产总结会的物料处理方案对尾料及时进行处理。
3.3 工程部:项目PE:负责新品试产从准备工作、SMT、总装到试产总结等一系列试产全过程的主导。
依据《试产申请单》及时将试产要求通知到各生产相关人员,整体协调并提前确保试产各方面资源的提供到位。
负责跟踪落实外协SMT的试产准备情况,跟踪发现SMT试产问题并推动研发改善,完成SMT部分的试产总结报告。
负责在总装线试产前确认(临时)SOP、测试方案、工装治具、测试软硬件等,并组织生产成员参加产前准备沟通会。
在试产当天及时发现问题,收集试产相关信息数据;试产结束后及时整合试产问题点完成生产方面的试产总结报告;制定新品周报,推动跟踪试产问题的改善与落实;同时将试产中的工艺问题编入工程文件中,以进一步提高工程整体水平。
新产品试产工艺流程

新产品试产工艺流程新产品试产工艺流程详细说明一.工艺准备:1 ) 参考图纸:工艺部统计该试产项目参考图纸及相关信息。
2) 工艺输出文件:确定工艺输出文件是否都已下发。
工艺输出文件包括:BOM文件:电路板BOM、裸机BOM、包装BOM、附件(产品)BOM等。
PCBA托工: PCB拼接图:发到印制板厂的印制板加工要求(长、宽、厚、拼接方式等)钢网制作文件:外加工SMT所需单板制作钢网PCB贴片图:提供单板尺寸、置描述PCBA焊接作业指导书:外协托工电路板焊接加工要求。
检验文件:成品检验规程、出厂检验报告。
调试作业指导书:内容包括芯片程序烧录、电路板程序烧录、电气参数测试、功能测试。
组装作业指导书:内容包括工艺流程、生产配置表、各工站指导书(以生产配置表为准按工站编写的焊接、装配、验证、网络配置等内容)。
包装作业指导书:指导产品如何包装及验证。
老化作业指导书:指导老化过程重要有机芯老化、整机老化和老化记录。
设备操作指导书:设备安全操作规程。
二.工艺内部评审:1)工艺文件评审:评审有无缺陷的地方。
需要改善的地方2) 首板样机内部评审:评审电路板及样机是否有设计隐患和不合理设计。
3) 工装夹具评审:评审工装夹具设计和审批周期及内部手续。
4) 了解PCBA外协加工情况,确认其对后续的组装及调试是否有影响。
如有需要则在试产准备会上通报,并商定出处理措施。
试产前工艺评审会要以邮件的形式发出会议记录。
三、试产准备会确认内容1、明确试产目标:2、确定试产性质试产性质包括:1) 客户要求/新机种 2) 更换供应商 3) 设计变更/工程试做 4) 常规实验5) 工程实验 6) 增加模具/工程试做 7) 其他3、参考图纸、BOM表、工艺文件:工艺部在工艺文件完成后内部召开试产前工艺评审会整合信息在试产准备会上做通报。
4、物料齐套性确认---计划部通报物料齐套情况。
包括生产备料后的报缺及缺料到货日期等信息。
5、IQC来料检验情况:数据内容包括不良问题的问题点,判定结果,判定人。
产品试产工艺流程

新产品试产工艺流程详细说明一.工艺准备:1 ) 参考图纸:工艺部统计该试产项目参考图纸及相关信息。
2) 工艺输出文件:确定工艺输出文件是否都已下发。
工艺输出文件包括:BOM文件:电路板BOM、裸机BOM、包装BOM、附件(产品)BOM等。
PCBA托工:PCB拼接图:发到印制板厂的印制板加工要求(长、宽、厚、拼接方式等)钢网制作文件:外加工SMT所需单板制作钢网PCB贴片图:提供单板尺寸、置描述PCBA焊接作业指导书:外协托工电路板焊接加工要求。
检验文件:成品检验规程、出厂检验报告。
调试作业指导书:内容包括芯片程序烧录、电路板程序烧录、电气参数测试、功能测试。
组装作业指导书:内容包括工艺流程、生产配置表、各工站指导书(以生产配置表为准按工站编写的焊接、装配、验证、网络配置等内容)。
包装作业指导书:指导产品如何包装及验证。
老化作业指导书:指导老化过程重要有机芯老化、整机老化和老化记录。
设备操作指导书:设备安全操作规程。
二.工艺内部评审:1)工艺文件评审:评审有无缺陷的地方。
需要改善的地方2) 首板样机内部评审:评审电路板及样机是否有设计隐患和不合理设计。
3) 工装夹具评审:评审工装夹具设计和审批周期及内部手续。
4) 了解PCBA外协加工情况,确认其对后续的组装及调试是否有影响。
如有需要则在试产准备会上通报,并商定出处理措施。
试产前工艺评审会要以邮件的形式发出会议记录。
三、试产准备会确认内容1、明确试产目标:2、确定试产性质试产性质包括:1) 客户要求/新机种2) 更换供应商3) 设计变更/工程试做4) 常规实验5) 工程实验6) 增加模具/工程试做7) 其他3、参考图纸、BOM表、工艺文件:工艺部在工艺文件完成后内部召开试产前工艺评审会整合信息在试产准备会上做通报。
4、物料齐套性确认---计划部通报物料齐套情况。
包括生产备料后的报缺及缺料到货日期等信息。
5、IQC来料检验情况:数据内容包括不良问题的问题点,判定结果,判定人。
新产品试产工艺流程

新产品试产工艺流程一.工艺准备:1 )2)BOM BOM、附件(产品)BOM 等。
PCBA(长、宽、厚、拼接方式等)SMT所需单板制作钢网PCB PCBA气参数测试、功能测试。
书(化记录。
设备操作指导书:设备安全操作规程。
二.工艺内部评审:1)工艺文件评审:评审有无缺陷的地方。
需要改善的地方2) 首板样机内部评审:评审电路板及样机是否有设计隐患和不合理设计。
3) 工装夹具评审:评审工装夹具设计和审批周期及内部手续。
4) 了解PCBA外协加工情况,确认其对后续的组装及调试是否有影响。
如有需要则在试产准备会上通报,并商定出处理措施。
试产前工艺评审会要以邮件的形式发出会议记录。
三、试产准备会确认内容1、明确试产目标:2、确定试产性质试产性质包括:1) 客户要求/新机种 2) 更换供应商 3) 设计变更/工程试做 4) 常规实验5) 工程实验 6) 增加模具/工程试做 7) 其他3、参考图纸、BOM表、工艺文件:工艺部在工艺文件完成后内部召开试产前工艺评审会整合信息在试产准备会上做通报。
4、物料齐套性确认---计划部通报物料齐套情况。
包括生产备料后的报缺及缺料到货日期等信息。
5、IQC来料检验情况:数据内容包括不良问题的问题点,判定结果,判定人。
(方便后期组装时对接受不良品的验证及影响产品装配情况的判定)。
6、工装、设备调配情况---生产部根据生产配置表评估满足情况。
7、人员调配情况---生产部根据生产配置表评估满足情况。
8、项目成员试产工作分工:工艺协同硬件提供调试、测试技术支持。
工艺协同结构提供装配技术支持。
9、试产计划:根据试产准备会时确认的时间做出试产计划,以邮件的形式发给各项目成员。
试产计划内容包括人员培训时间:生产部调配时间(正式试产前)试产开始时间:生产部按排期确定试产时间首件检验时间(QA估算):试产总时间 (PE估算):试产总结会时间(PE估算):试产准备会要填写《签到表》,会后发出<<试产准备会会议纪要>>,相应的问题对未完成跟踪项确定计划完成时间和实际完成时间,对相应负责人跟踪完成进度。
新产品试产工艺准备程序(DOC 15页)
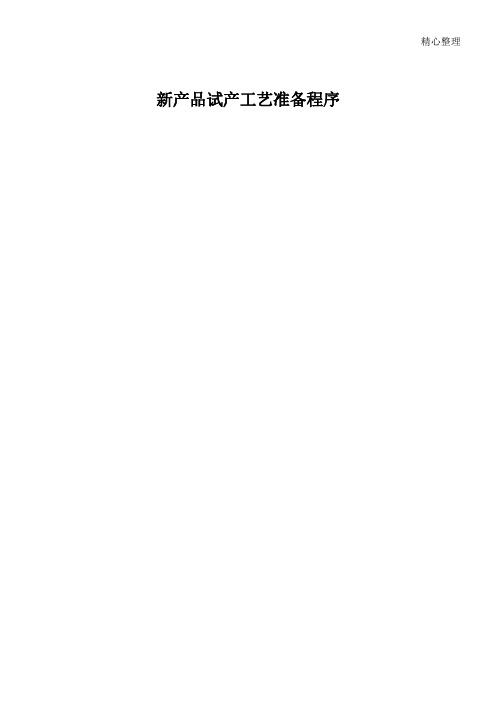
成员
职责分工
完成期限
输出结果
REV:01
版次
文件编号
制订日期
页次
7
保存年限
xx电子有限公司
工艺评审记录
评审内容:□工艺参数
□产品流程
□操作规格
□检验标准
□工艺、夹具图纸
评审意见(是否通过评审?有何问题?)
评审结论(问题的解决措施或批准该工艺的决定)
工程经理:
年月日
参加评审人员签名
REV:01
7.5新产品的工艺确认
7.5.1工艺试验(小批试产)结束後,各相关部门和车间,应准备试产情况的报告
资料,工程经理召集开发小组成员,参与工艺试验的有关人员,对试产阶段的
情况进行总结和分析,作出是否确认试产用文件的结论。
7.5.2被确认的新品工艺开发文件,盖“受控文件”章,按「文件与资料管制作业
程序」发放。
4.1.2全新产品:须采用新工艺、新设备才能生产的产品。
4.2设计和开发:在公司暂未进行产品设计和开发,本程序定义之设计和开发由总公司
或客户提供。
5.人员资格要求
参与新开发的人员,须对产品、材料、工艺、设备有一定了解,具备独立完成指定
开发任务并与开发小组其他成员沟通的能力。
6.职责和许可权
6.1总经理或业务部经理提出新产品开发要求。
REV:01
版次
文件编号
制订日期
页次
9
保存年限
主旨:
内容说明:(功能、特质、用途、价位、有无侵权行为**,或以附件说明)
核准: 承办:
各单位评估回覆意见:(栏位不足,以附件说明)
核准: 承办:
相关单位
□品保部□工程部□业务部□制造部□财务部
- 1、下载文档前请自行甄别文档内容的完整性,平台不提供额外的编辑、内容补充、找答案等附加服务。
- 2、"仅部分预览"的文档,不可在线预览部分如存在完整性等问题,可反馈申请退款(可完整预览的文档不适用该条件!)。
- 3、如文档侵犯您的权益,请联系客服反馈,我们会尽快为您处理(人工客服工作时间:9:00-18:30)。
修订记录:日期/ 修订记录:日期/版本
2002-6-24 A 版;2003-10-8 A-1;2004-10-5 B 版: 2005-5-17 A 版;2005-9-2 A-1 ; 2005-9-20 A-2 修订内容: 1、修订 4.6.4.2 条款:正式投入量产前,工程部需制 作好公司标准包装图片(1W、2W、1N、2N、吸塑包装和 非白盒/硬盒之 PSE 包装等)放于“柏力 PC100 上工程课 之包装图片”里供使用部门参考;并应确保每款新产品 均有公司标准包装图片。
觀
标 题 产品试产作业程序 工程部 编 号 PPL-73BPPL-73B-002 2005-9-20 2005版本 页次 A-2 3/4 管理归口 制订日期
企划部文控中心依《文件控制程序》规定将已转换之文件进行建档、分发等受控 作业。 4.6.4 产品量产通知: 4.6.4.1 工程部、设计部在受控文件全部发行后,若为新产品,工程部以董事总经理 签批的 《产品转产通知书更管理程序》 规定并以 《产品型号停产/复产指示书》 的形式通知相关部门。 4.6.4.2 正式投入量产前,工程部需制作好公司标准包装图片(1W、2W、1N、2N、吸塑 包装和非白盒/硬盒之 PSE 包装等)放于“柏力 PC100 上工程课之包装图片”里 供使用部门参考;并应确保每款新产品均有公司标准包装图片。 4.7 试产产品量产: 依据《制程管制程序》进行作业; 5.参考文件 参考文件: 5.参考文件: 5.1 设计和开发控制程序 5.3 文件控制程序 6.记录 6.记录 6.1 产品试产记录 6.3 产品转产通知书 附件: 7.附件: 7.1 附件一:试产文件转换作业流程图 7.2 附件二:产品试产作业流程图
批准
确认
审核
拟定
觀
标 题 产品试产作业程序 工程部 编 号 PPL-73BPPL-73B-002 2005-5-17 2005版本 页次 A 2/4 管理归口 制订日期
4.2.4 试产前,新产品开发负责人应核查试产所需图纸、文件、物料、夹、治具等是 否齐备。 4.3 产品试产: 4.3.1 试产时,工程课人员应随线监控试产状况,并将试产过程中出现的问题记录在 《产品试产记录》上; 4.3.2 针对试产过程中出现的问题应进行分析,制定改善措施。解决不了的问题应及 时报告新产品开发负责人及工程部经理,以便研究解决。 4.4 产品检验: 4.4.1 当试产产品做出来后,电子课负责组织人员对新产品的外形尺寸、功能、可靠 性及安全性能等逐一进行测试,并记录于《电池规格》及《原装/试产电池功能 测试记录》中; 4.4.2 核对总结测试时应引用或包含验收准则; 4.4.3 如测试不合格,则工程部、设计部应根据具体情况进行修改或重新试产; 4.4.4 如测试合格,则转交相关单位对试产产品进行评审、确认。 4.5 产品确认: 4.5.1 验证新产品评审合格时,工程部将样品转交营业部,如客户需求时将提供相关 资料及文件供参考,并由营业部送至客户处进行确认,如客户无特殊要求时, 也可直接由工程部仿真客户使用条件进行确认,并将确认意见呈交董事总经理 最终确认;如为旧产品发生重大工程变更而经试产并评审合格时,则直接由工 程部仿真客户使用条件进行确认,并将确认意见呈董事总经理最终确认; 4.5.2 需要时工程部需将样品与相关文件及资料通过品质会议进行评审(必要时可由 品保部再次测试) ; 4.5.3 如董事总经理确认样品不合符规格,则工程部、设计部应制定改善措施,对图 纸、工艺标准、夹、治具、模具等需要修改的地方作适当的修改; 4.5.4 修改后,董事总经理如认为有必要重新试产,应再次试产及送样确认; 4.5.5 如客户或董事总经理确认样品合符规格,则工程部、设计部将确定正式工程图 纸等相关文件与资料进行转换工作。 4.6 文件转换: 4.6.1 确认报告转交: 工程课将确认合格的文件转交给相关部门; 4.6.2 试产文件转换: 工程部负责将试产产品确认后的 BOM 及时输入 K3 系统,并将 BOM、图纸、产品 规格等其它相关文件与资料依《文件控制程序》规定转换成受控文件; 4.6.3 受控文件发行:
5.2 工程变更管理程序
6.2 原装/试产电池功能测试记录 6.4 产品型号停产/复产指示书
附件一:试产文件转换作业流程图 流程图 確認報告轉交 权责单位 工程課
試産文件轉換
工程部 設計部
受控文件發行
企划部
産品量産通知
工程部
觀
标 题 产品试产作业程序 产品试产作业程序 工程部
附件二:产品试产作业流程图 流程图 設計驗證 變更確認 权责单位 工程部 設計部 工程部 設計部 工程部 設計部 工程部 設計部
觀
标 题 产品试产作业程序 工程部 编 号 PPL-73BPPL-73B-002 2005-9-20 2005版本 页次 A-2 1/4 管理归口 制订日期
1.目的: 1.目的: 目的 使产品的试产过程规范化,以符合客户的最终要求,制造出优质产品。 2.范围 范围: 2.范围: 凡本公司开发之新产品和发生重大工程变更之旧产品的试产均属之。 3.权责: 3.权责: 权责 3.1 董事总经理:负责试产产品之确认; 3.2 工程部: 3.2.1 归口管理本程序; 3.2.2 负责制作试产产品之技术资料及试产通过后产品之受控资料; 3.2.3 负责 BOM、公司标准包装图片的制作及试产产品安全性能之测试; 3.2.4 负责试产过程中出现的问题加以分析、解决。 3.2.5 负责试产产品所需物料之申购。 3.3 设计部: 3.3.1 负责编制产品图纸等技术资料,及其受控转换; 3.3.2 负责对试产过程中出现的产品结构问题分析、解决。 3.4 营业部:负责送样给客户确认。 3.5 采购部:负责试产产品所需物料之采购。 4.作业内容: 4.作业内容: 作业内容 4.1 设计输出/变更确认: 新产品设计输出或旧产品发生重大工程变更并经确认后,依《设计和开发控制程序》 或《工程变更管理程序》即进入试产准备阶段。 4.2 试产准备: 4.2.1 工程部各课将要试产产品的图纸、公司标准包装图片、新材料的规格、BOM、检 验标准等相关资料备齐并转交给工程课; 4.2.2 试产所需夹具、治具、检具、装配模具,由工程部负责制作或备齐后转交给制 造一部;总务部负责保证各使用设备的性能完好; 4.2.3 新材料由采购部依据工程部提供的规格要求负责采购,并由工程部负责对新材 料是否符合规格要求进行检验;
品質會議 董事總經理 客戶
编
号
PPL-73BPPL-73B-002 2005-5-17 2005-
版本 页次
A 4/4
管理归口
制订日期
試産準備
試産 NG
産品檢驗 OK
NG
産品確認 OK 文件轉換 OK 量産
工程部 設計部 生産部門