加工中心返参考点案例分析
数控加工中心双Mark回参考点

9 9 0 0 0—9 9 5 0 0+0= 一5 0 0。 6 0 6 0 0
即 [ 18 新值] = [18 旧值] + G 31) P83 P83 D N0 。
( ) 手 动 回零 ( 度 为 回零 低 速 [ 14 2 速 P25设 定 值 ] ,找到零点 后,置 P854 ( P ) = 。 ) 11# A Z 1
=
3 操作过程 ( 轴回零为例) . 以
( )确 认 P85 1=1 11 # 1 11# ,P 85 2=1 12 ,P81和 P82中的值是否正确 , 18 修改 P20 0 P83 0 ( 14 : , 1 = 如 8
果此处 P 8 3不 作 修改 ,执 行手 动 回零 ,找 到 参考 点 18 后 ,将 当前坐标显示值 D N 3 1加 到原来 的 P 83中 , G 0 18
数 控 加 工 中 心 双 Mak回 参 考 点 r
上海通用东岳动力总成有 限公 司 (6 0 6 郭 24 0 ) 兴
双 Mak回参考点 的方法定 义 :双 Mak法适用全 闭 r r
P 82 1( C ) 10 # D 4 :当使用带绝 对参考 标志的光栅 尺
环系 统 ,带 绝 对 参 考 标 志 的 光 栅 尺 。下 面 以 F N C A U 1M 6 B系统为例 ,说明双 Mak回参考点 的原理 。 r
“ E ”方 式 ,手 动 回参 考 点 ,光 栅 尺 测 量 Mak RF rl和
P83 18 :机床参考点到光栅尺理论原点的距离。
P 80 12 :指令倍乘 比。
z = 。
≮ l — I, 川l B E \
当C MR<1时 ,该 参数 的设 定值为 : ( / MR) + 1C
数控机床的回零及其常见故障分析[1]
![数控机床的回零及其常见故障分析[1]](https://img.taocdn.com/s3/m/bb6b1621bcd126fff7050be2.png)
数控机床参考点的回归及其常见故障诊断数控机床启动后通常需要进行返回参考点的操作,在这个过程中常会遇到各种问题,问题处理的正确与否在很大程度上会直接影响机床的使用及工件的加工精度。
一、为什么要返回参考点在数控机床上,各坐标轴的正方向是定义好的,因此只要机床原点一旦确定,机床坐标系也就确定了。
机床原点往往是由机床厂家在设计机床时就确定了,但这仅仅是机械意义上的,计算机数控系统还是不能识别,即数控系统并不知道以哪一点作为基准对机床工作台的位置进行跟踪、显示等。
为了让系统识别机床原点,以建立机床坐标系,就需要执行回参考点的操作。
如在CK0630型数控车床上,机床原点位于卡盘端面后20mm处,为让数控系统识别该点,需回零操作。
在CK0630型数控车床的操作面板上有一个回零按钮“ZERO”,当按下这个按钮时将会出现一个回零窗口菜单,显示操作步骤。
按照这个步骤,依此按下“X”按钮、“Z”按钮,则机床工作台将沿着X轴和Z轴的正方向快速运动,当工作台到达参考点的接近开关时,工作台减速停止。
回参考点的工作完成后,显示器即显示机床参考点在机床坐标系中的坐标值(X400,Z400),此时机床坐标系已经建立(如图1所示)。
目前,大多数数控机床均采用增量式位置检测装置来做位置环反馈元件,当机床在断电状态时NC系统会失去对机床坐标系值的记忆,因此每次机床重新通电之初,必须手动操作返回机床参考点一次,恢复记忆,以便进行自动加工。
对使用日本FUNAC系统的机床,除通电之初外,在机床工作过程中如出现断电、紧急停止或压下了机床行程限位开关时,也必须返回参考点。
机床返回参考点的方向、速度、参考点的坐标等均可由系统参数设定。
二、返回参考点的原理目前数控机床回参考点的方式有两种:使用脉冲编码器或光栅尺的栅格法和使用磁感应开关的磁开关法。
磁开关法由于存在定位漂移现象,因此较少使用。
大多数数控机床均采用栅格法回参考点。
栅格法根据检测元件计量方法的不同又可分为绝对栅格法和增量栅格法。
机床回参考点原理及故障处理.

在电机和丝杠上分别做一个记号, 拧紧联轴节 然后在运行该轴,观察其记号 更换位置编码器,并观察 偏差更换后,故障是否消 除 重新计算参考点计数器容量 特别是在0.1μ 的系统里, 更要按照说明书,仔细计 算 更换伺服控制扳或接口模 块
5
6
返回参考点异常,并在显示器屏幕上出现Alarm90 参考点返回时,位置偏差量未超过128时,位置误差量 可以在诊断画面里确认。 3/6/0系统诊断号为800~803 ; 16/18系统的诊断号为 300 a, 检查确认快进速度 b,检查确认快进速度的倍率选择信号(ROV1、ROV2) c,检查确认参考点减速信号(*DECX) d,检查确认外部减速信号±*EDCX e, 离参考点距离太近。 2、参考点返回时,位置偏差量超过128时。 a)位置反馈信号的1转信号没有输出。 b)位置编码器不良 c)位置编码器的供给电压偏低,一般不能低于4.8v
机床回参考点原理及故障处理 <使用挡块和限位开关>
通过接收安装在机床上的限位开关送出的信号(*DEC),检取 CNC 内部产生的电动机每转的栅格信号使伺服电动机Βιβλιοθήκη 止,将该位 置定为参考点。 ■动作概要
返回参考点时,出现偏差的故障分析与处理 (1)参考点位置偏差1个栅格
可能原因 项 目 如何检查 解决办法
(2)参考点返回位置是随机变化的
可能原因 项目 如何检查
1
干扰
a)检查位置编码器反馈信号线是否 屏蔽; b)检查位置编码器是否与电机动力 线分开
检查编码器供电电压不能低于 4.8V
屏敝位置编码器反馈信号 线; 分离位置编码器与电机动 力线
2 3 4
位置编码器的 供电电压太低 电机与机械的 联轴节松动 位置编码器不 良 回参考点计数 器容量设置错 误 伺服控制板或 伺服接口模块 不良
加工中心返参考点案例分析

加工中心返参考点案例分析【摘要】加工中心的参考点,作为机床和工件坐标系的原始参考点,一旦确定后,各工件坐标系随之建立。
机床参考点是机床坐标和工件坐标系的基础,如果机床参考点发生漂移,则加工零件的一致性不好,严重时可能废活,更甚者可能在交换工作台或换刀时发生撞车事故。
所以当机床参考点发生漂移时,一定要分析其原因,将故障排除。
【关键词】参考点;漂移;故障在日常设备维修过程中,经常可以遇到一些因为机床参考点发生漂移而导致的设备故障,现例举几例与参考点漂移有关的故障,供大家借鉴。
1THM6363宁江加工中心交换工作台故障故障现象:在加工过程中,偶尔在交换工作台时发生故障,其报警内容为“工作台不在交换托盘上”。
此时,工作台已经被托盘托起,床身内的工作台由于不在托盘中心,已经倾斜,操作工通常会用手动方式,先将托盘落下,然后再重新将各轴返参考点,随后完成工作台交换。
由于故障不很频繁,操作工也就没有报修。
一次,操作工反映,早上开机加工零件时,感觉机床吃刀量变大,并有明显振动,随即按下了急停开关,发现零件位于圆周上的四个等分槽的尺寸已与图纸明显不符,于是将设备进行了报修。
故障分析:检查有关参数设置及信号电缆连接。
参数设置正常,光栅尺等线性测量元件及其接口电路未见明显故障。
先减小由参数设置的接近原点速度,重试回原点操作,原点不漂移。
由于该工件不是首件加工,排除了程序原因,据操作工反映,该工件前一天未加工完成,第二天继续加工时出现了故障。
联系到以前交换工作台时发生的故障,基本可以判断是参考点漂移造成的故障。
为了印证判断,连续开关机,返参考点并交换工作台,终于在一次实验中,又发生了床身内的工作台由于不在托盘中心而倾斜的故障,并且工作台距交换点相差了12mm,正好为一个螺距,也与报废工件的误差相吻合。
这就说明了参考点漂移而导致工作台交换点发生了变化。
该机床返参考点的过程是,在机床上安装一个感应块及感应开关,当感应块感应到感应开关时,伺服电机减速至接近参考点速度运行。
实验五 机床回参考点实验

一、实验目的实验五机床回参考点实验1、了解全功能数控机床回参考点功能与建立机床坐标系的概念。
2、掌握FANUC 0i D/0i mate D系列数控系统的回参功能调整。
二、实验设备1、RS-SY-0i D/0i mate D数控机床综合实验系统。
三、实验必备知识1、机床回参考点功能是全功能数控机床建立机床坐标系的必要手段,参考点可以设在机床坐标行程内的任意位置(一般由机床制造厂家设定)。
在数控机床上需要对刀具运动轨迹的数值进行准确控制,所以要对数控机床建立坐标系。
标准坐标系是右手直角笛卡尔坐标系。
右手直角笛卡尔坐标系规定了直角坐标X、Y、Z三者的关系及其正方向用右手定则判定,围绕X、Y、Z各轴的回转运动及其正方向+A、+B、+C分别用右螺旋法则判定。
数控车床坐标系的确定:Z轴坐标是由传递切削动力的主轴所确定,平行于主轴轴线,一般Z轴的正方向为远离主轴的方向。
X轴坐标是沿工件的径向且平行于横向导轨,一般X轴的正方向为远离工件旋转中心的方向。
加工中心坐标系的确定:Z轴坐标是由传递切削动力的主轴所确定,平行于主轴轴线,一般Z轴的正方向为远离工件的方向。
X轴坐标是水平的,一般平行于工件的装夹表面,X轴的正方向由右手直角笛卡尔坐标系判定。
Y轴坐标是由右手直角笛卡尔坐标系来判定。
2、机床回完参考点后,机床坐标系就已建立,参考点通常是坐标系中的某一点,该点不一定是坐标原点。
此时,各种补偿以及偏置生效,机床轴才能根据程序的命令走出正确的坐标值。
3、对于安装了绝对值编码器作位置反馈的机床,由于绝对值编码器具有记忆功能,无需每次开机都作回参考点操作。
而大多数的数控机床则使用增量值编码器作位置反馈,重新开机后的第一件事,便是作回参考点操作,建立坐标系,以避免因此而引起的撞刀现象。
4、机床回参考点操作,一般需有一定的硬件支持,除位置编码器以外,一般还须在坐标轴相应的位置上安装一硬件挡块与一行程开关,作为参考点减速开关。
加工中心回参考点的特殊故障及处理

2 F AGOE系统 立式 加工 中心 z轴 返 回参考 点故 障
另一 台 Z 52 式加工 中心是 原 北 京第 三 机 床 H 5立 1
是与上述元器件无直接关系的回参考点故障。
1 西门子 系统 卧式加工 中心 y轴返 回参 考点 厂 19 生产 。配 置 的是 西 班牙 F G R 8 2 MS数 9 3年 A O 0 5 故 障
否与 y 回参考点 故障有关?经过几 次修改 y轴漂 轴
移补偿参 数 (7 1最终 值调 整 为 l ) 22 0 。最 后 执 行 y轴 回参考 点 , 然 “ 未达 到 ” 示 灯 不 亮 了 , 考 点 也 果 轴 指 参 顺 利 完 成 了 , 次执 行 y轴 回参 考 点 证 实 故 障 解 决 。 多 ( 修改 y轴多项 增益 参数 20 也 可 以 ) 61
轴完成 回参考点标志始终未出现 。 首先怀疑减速开关位置与光栅尺零信号位置距离
太 近 。沿轴 向“+” “一” 动减速 开 关无 效 。其 次怀 、 移
疑 回参考点速度太快 , 将速度降低也不起作用。然后 更换光栅尺信号放大板和位置控制板 、 参考点补偿值
置 零 ( 疑参 考点 已找 到 , 怀 只是 补偿 值 没 作运 动 ) 不 均
回想在 安装 新 电动机 和伺服 驱动 时只设 置 了伺服 驱动 器参 数 , 有进 行数 控 系统 参数 的设置 。将 z轴 没 相关参 数核 对 , 多次 调 整 z轴 比例增 益 参 数 P 1 并 34、 P l 、36的设 置值 , 35 P l 也不 能解决 问题 ( 也许 没 有最 优 化) 。参考其 他 F G R数 控 系 统 类 似 机 床 的 系 统 参 AO 数 , 现其他 机 床 z轴定 位 带 参 数 P 1 [n—psin 发 38 I oio t
TH65100×100卧式加工中心回参考点故障分析

装置 的加工 中心机床 ,为 了 自动换刀 的需 要 , 除了设置第一参考点还设置 了第二参考点 。机 床参 考点是机床工件坐标系 的原始参照系 ,机 床参 考 点 确定 后 ,工 件坐 标 系 随之 建立 。 因此 , 数控机床 回参考点是数控技术的重要内容。
T 6 10×10卧式 加 工 中心 ,适 于复 杂 箱 H 50 0 体 多 工 作 面 的铣 、钻 、镗 、 铰 、攻 丝 、 二 维 、
三维 曲面等多种工 序加工 ,可在一次装夹 中完 成箱体孔系和平 面多工序精确加工 ,适合于箱
体孔 的调头 镗削加 工 。 机 床 采 用 F N C0— MA数 控 系 统 、数 字 A U i
第 3 卷
第 3期
清远职业技术学 院学报
Ju a o Qny a o t h i or l f igu n Pl e nc n yc
Vo .3 , No 1 .3
21 00年 6月
Jn. 00 u e 2 1
T 6 0 10 H 5 × 卧式加工中心回参考点故障分析 1 0 0
施 振 金 佘 小成 z
(. 1广东机电职业技术学 院机 电系 广东广州 50 1; 15 5
2 广东中远船务工程有 限公司 .
广东广州
502) 17 5
摘要 :数控机床 回参考 点的准确性 ,除 了影响机床 的稳定性 ,更重要 的还影响机床的加工精度及加工尺寸的稳定
性 。归纳了数控机床 回参考 点的故 障形 式及相 关对策 ,列举 了 T 6 10 0 H 50 ×10卧式加 工 中心 回参考 点的原理和故障分
合 的 点 。数 控 机 床 每 个 坐 标 轴 可 以设 置 一 个 参 考点 ,也可 以根据 需要 设 置 多个 参 考点 。例如 , 具有 自动刀具 交 换 ( T 或 自动拖 盘交 换 ( P ) A C) A C
加工中心编程-自动返回参考点G27、G28、G29

自动返回参考点G27、G28、G29(1)返回参考点校验指令G27格式:G27 X_Y_Z_;说明:1)该指令可以检验刀具是否能够定位到参考点上,指令中X、Y、Z分别代表参考点在工件坐标系中的坐标值,执行该指令后,如果刀具可以定位到参考点上,则相应轴的参考点指示灯就点亮。
在刀具补偿方式中使用该指令,刀具到达的位置将是加上补偿量的位置,此时刀具将不能到达参考点因而指示灯也不亮,因此执行该指令前,应先取消刀具补偿。
2)假如不要求每次执行程序时,都执行返回参考点的操作,应在该指令前加上“/ ”(程序跳),以便在不需要校验时,跳过该程序段。
(2)自动返回参考点指令G28格式:G28 X_Y_Z_;说明:1)该指令使刀具以点位方式经中间点快速返回到参考点,中间点的位置由该指令后面的X、Y、Z坐标值所决定,其坐标值可以用绝对值也可以用增量值,但这要取决于是G90方式还是G91方式。
省略了中间点的轴不移动;只有在命令里指派了中间点的轴执行其原点返回命令。
在执行原点返回命令时,每一个轴是独立执行的,这就像快速移动命令(G00)一样;通常刀具路径不是直线。
因此设置中间点,是为防止刀具返回参考点时与工件或夹具发生干涉。
2)为了安全,在执行该指令之前,应该清除刀具半径补偿和刀具长度补偿。
3)在G28程序段中不仅记忆移动指令坐标值,而且记忆了中间点的坐标值。
换句话说对于在使用G28的程序段中没有被指令的轴,以前G28中的坐标值就作为那个轴的中间点坐标值。
3)返回第2、3、4参考点G30格式:G30 P2 X_Y_Z_;返回第2参考点(P2可以省略)G30 P3 X_Y_Z_;返回第3参考点G30 P4 X_Y_Z_;返回第4参考点说明:1)格式中X、Y、Z为中间的位置,说明同G28。
2)在没有绝对位置检测器的系统中,只有在执行过自动返回参考点(G28)或手动返回参考点之后,方可使用返回第2、3、4参考点功能。
通常,当刀具自动交换(ATC)位置与第1参考点不同时,使用G30指令。
数控机床的回零及其常见故障分析[1]
![数控机床的回零及其常见故障分析[1]](https://img.taocdn.com/s3/m/bb6b1621bcd126fff7050be2.png)
数控机床参考点的回归及其常见故障诊断数控机床启动后通常需要进行返回参考点的操作,在这个过程中常会遇到各种问题,问题处理的正确与否在很大程度上会直接影响机床的使用及工件的加工精度。
一、为什么要返回参考点在数控机床上,各坐标轴的正方向是定义好的,因此只要机床原点一旦确定,机床坐标系也就确定了。
机床原点往往是由机床厂家在设计机床时就确定了,但这仅仅是机械意义上的,计算机数控系统还是不能识别,即数控系统并不知道以哪一点作为基准对机床工作台的位置进行跟踪、显示等。
为了让系统识别机床原点,以建立机床坐标系,就需要执行回参考点的操作。
如在CK0630型数控车床上,机床原点位于卡盘端面后20mm处,为让数控系统识别该点,需回零操作。
在CK0630型数控车床的操作面板上有一个回零按钮“ZERO”,当按下这个按钮时将会出现一个回零窗口菜单,显示操作步骤。
按照这个步骤,依此按下“X”按钮、“Z”按钮,则机床工作台将沿着X轴和Z轴的正方向快速运动,当工作台到达参考点的接近开关时,工作台减速停止。
回参考点的工作完成后,显示器即显示机床参考点在机床坐标系中的坐标值(X400,Z400),此时机床坐标系已经建立(如图1所示)。
目前,大多数数控机床均采用增量式位置检测装置来做位置环反馈元件,当机床在断电状态时NC系统会失去对机床坐标系值的记忆,因此每次机床重新通电之初,必须手动操作返回机床参考点一次,恢复记忆,以便进行自动加工。
对使用日本FUNAC系统的机床,除通电之初外,在机床工作过程中如出现断电、紧急停止或压下了机床行程限位开关时,也必须返回参考点。
机床返回参考点的方向、速度、参考点的坐标等均可由系统参数设定。
二、返回参考点的原理目前数控机床回参考点的方式有两种:使用脉冲编码器或光栅尺的栅格法和使用磁感应开关的磁开关法。
磁开关法由于存在定位漂移现象,因此较少使用。
大多数数控机床均采用栅格法回参考点。
栅格法根据检测元件计量方法的不同又可分为绝对栅格法和增量栅格法。
加工中心回参考点故障分析与排除
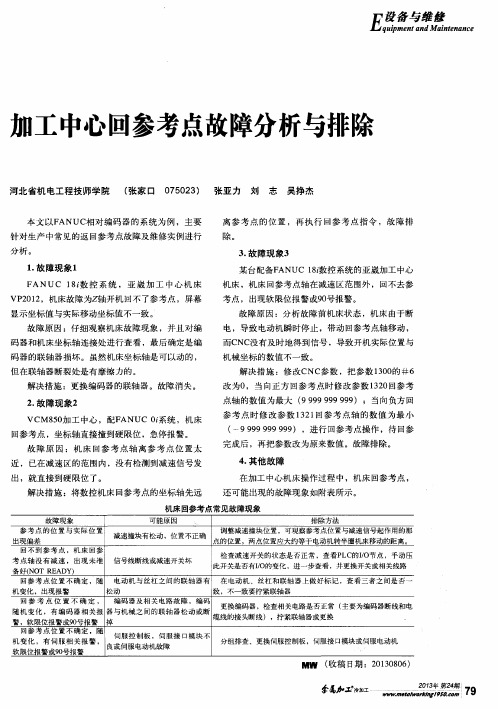
解决措施 :将数控机床 回参考点的坐标轴先远
机床回参考点常见故障现象
故障现象 可能原因 参 考 点的 位 置与 实际 位置 减速撞块有松动 位置不正确 出现偏差 回不 到参 考 点 ,机床 回参 考 点轴 没有 减 速 , 出现 未 准 信号线断线或减速开关坏 备好( N OT R E ADY)
码 器 和 机床 坐 标 轴 连 接处 进 行 查 看 ,最 后 确定 是 编
电,导致 电动机瞬时停止 ,带动 回参考点轴移动 ,
而C NC 没有 及 时地 得 到 信号 ,导 致开 机 实 际位 置 与 机 械坐 标 的 数 值不 一 致 。 解决 措 施 :修 改C NC 参 数 ,把 参 数 1 3 0 0 的 #6
, ,
,
软 限位报警或9 o 号报 警
Mi l l /( 收 稿 日期 :2 0 1 3 0 8 0 6 )
磊
冷 加 工
7 9
设 备 s 维 修
上 q u i p 工中心回参考点故障分析与排除
河北省 机 电工程技 师学院 ( 张家 口 0 7 5 0 2 3 ) 张亚 力 刘 志 吴挣 杰
本 文 以F ANUC  ̄ N 对 编 码 器 的 系 统 为 例 ,主 要
码器的联轴 器损坏。虽然机床坐标轴是可以动 的,
但 在 联 轴 器断 裂 处是 有 摩 擦 力 的 。
解决措施 :更换编码器的联轴器。故障消失。
改为0 ,当向正方 回参考 点时修改参数 1 3 2 0 回参考
点轴的数值为最大 ( 9 9 9 9 9 9 9 9 9 9 );当向负方 回
故 障 原 因 :分 析 故 障 前 机 床状 态 ,机 床 由于 断
数控机床回参考点过程分析、典型模式和故障分析
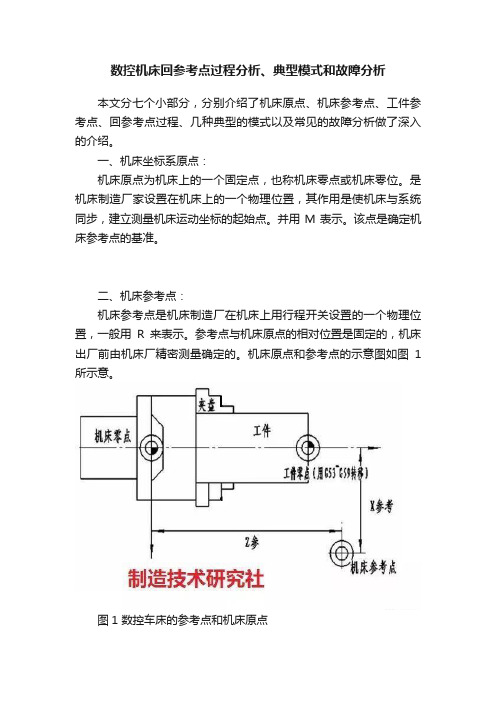
数控机床回参考点过程分析、典型模式和故障分析本文分七个小部分,分别介绍了机床原点、机床参考点、工件参考点、回参考点过程、几种典型的模式以及常见的故障分析做了深入的介绍。
一、机床坐标系原点:机床原点为机床上的一个固定点,也称机床零点或机床零位。
是机床制造厂家设置在机床上的一个物理位置,其作用是使机床与系统同步,建立测量机床运动坐标的起始点。
并用M表示。
该点是确定机床参考点的基准。
二、机床参考点:机床参考点是机床制造厂在机床上用行程开关设置的一个物理位置,一般用R来表示。
参考点与机床原点的相对位置是固定的,机床出厂前由机床厂精密测量确定的。
机床原点和参考点的示意图如图1所示意。
图1 数控车床的参考点和机床原点一般来说,机床坐标系原点或机床零点是通过机床参考点间接确定的。
机床参考点是机床上的一个固定点,其与机床零点间有一确定的相对位置,一般设置在刀具运动的X、Z正向最大极限位置。
展开剩余85%在机床每次通电之后,工作之前,必须进行回机床零点操作,使刀具运动到机床参考点,其位置由机械档块确定。
这样,通过机床回零操作,确定了机床零点,从而准确地建立机床坐标系,即相当于数控系统内部建立一个以机床零点为坐标原点的机床坐标系。
机床坐标系是机床固有的坐标系,一般情况下,机床坐标系在机床出厂前已经调整好,不允许用户随意变动。
对于铣床来说,有的机床参考点就是原点,有的参考点在最大行程位置。
而对于车床来说,参考点和原点不是同一点,这在图1中显示得十分明显。
三、工件坐标系原点:工件坐标系是用来确定工件几何形体上各要素的位置而设置的坐标系,工件原点的位置是人为设定的,它是由编程人员在编制程序时根据工件的特点选定的,所以也称编程原点。
工件坐标系原点和机床原点是有偏移的,所有的编程都是以工件原点作为原点的,在通过G53,G59来指定偏移。
四、机床回参考点过程:机床回参考点过程在往期文章(《端午节,回家就向数控机床回参考点一样,不需要理由,只需要团聚》)中已经详细说明了,这里再简单回顾一下:1)设置回参考点工作方式;2)选择返回参考点的轴并操作该轴返回参考点,该轴以G00快速向参考点运动;3)当随滑板一起运动的撞块压下参考点开关触头,使其内断(ON)转通(OFF)状态后,机床滑板会减速并按参数设定的速度继续移动。
数控机床回参考点的故障分析与排除过程

摘要:本文针对数控机床回参考点故障的常见类型,通过分析回参考点的方式以及回参考点故障的排除方法,并以实例分析排除故障,使大家了解数控机床回参考点的故障分析及排除方法。
关键词:数控机床回参考点故障排除0引言数控机床回参考点就是我们常说的机床回零点。
数控机床的参考点是机床厂家设定的(一般是接近机床各坐标轴的正极限位置)通常是不能改变的,通过机床正确回参考点,CNC系统才能确定机床的原点位置。
数控机床的原点是数控生产厂家设定在机床上的一个固定点,作为机床调整的基准点。
回参考点的操作是数控机床重要的功能环节之一,但由于操作频繁,在这个过程中常会遇到各种问题,若回参考点出现故障,将无法进行程序加工,回参考点的位置不准确,将影响到加工精度,甚至出现撞车事故。
因此,掌握回参考点常见故障的分析及诊断方法是非常必要的。
1返回参考点的方式数控机床回参考点时根据检测元件的不同分绝对脉冲编码器方式和增量脉冲编码器方式两种,使用绝对脉冲编码器作为反馈元件的系统,由于系统断电后位置检测装置靠电池来维持坐标值实际位置的记忆,所以在机床安装调试后的正常使用过程中,只要绝对脉冲编码器的后备电池有效,机床开机不必再进行回参考点操作。
而使用增量脉冲编码器的系统,由于系统断电后,工件坐标系的坐标值就失去记忆,所以机床每次开机后都必须先进行回参考点操作,通过参考点来确定机床的坐标原点,建立正确的机床坐标系。
另外机床在按下急停开关后以及机床出现故障并修复后都需要进行一次返回参考点的操作。
回参考点方式一般有如下五种:1.1轴向预定点方向快速运动,挡块压下零点开关后减速向前继续运动,因栅格法是采用脉冲编码器或光栅尺发出的栅格信号来确定脉冲参考点的,所以当轴部挡块压下零点开关后,系统开始查询脉冲编码器或光栅尺发出的基准信号,当该信号出现时,便控制回参考点坐标轴制动停止。
此时所处位置便是数控机床坐标系的参考点。
1.2轴向预定点方向快速运动,挡块压下零点开关后减速向前继续运动,直到挡块脱离零点开关后,系统开始查询脉冲编码器或光栅尺发出的基准信号,当该信号出现时,便控制回参考点坐标轴制动停止,便以确定参考点位置。
数控机床回参考点故障分析与排除

开关 ,触点状态 由断转为通后 ,数控 系统等到感 应开关 信
20 年l 月 l中国 08 1 设备工程
5 7
乡 翟
考点返回完成信号 ,参考点灯亮。
速度
. .
g
壤 g 。
现 “O E D N T R A Y”状态 ,回参考 点失 败。这种故 障一般 有
四种情 况 。
I将方式开关拨 到 “ . 回参 考点 ”挡 ,选择 返 回参 考点
所 以不会产 生栅格信号 ,通常利用 磁感应开关 回参考 点定
位 。如某 数控 车床 用 磁 开关法 返 回参 考 点 的原 理 和过 程
( ) 图2 。图中,快进速度 、慢进速度 、加减速 时间 、偏 移量
的轴 ,按下该轴正向点动按钮 ,该轴快速向参 考点移动 。
检 P 信 .L 上 上 上 上 上 上_— 测c 号 - 上 上 上 上 上 | z ÷上 L
栅格 信 山 土 _JL -
图 1 增量栅格法 回参考点原理 开环系统没 有位 移检 测反馈装 置脉 冲编码器或光栅尺 ,
偏移量 等参数分别 由数 控系统设定 。机床返 回参考点 的操 作步骤如下 。
弹 |
口寤#
≈#一
矗s
}崩| 帮 曩
*球 # l0 拜
辨 ∞ # 0 一 簪
文章编 号 :17— 7 1 (0 8 1- 07 0 6 10 1 20 ) 10 5— 3
数控机床 回参 考点故 障分析与排除
宋建武 ,杨
( 张家 口职业技术学 院,河北
丽
张家 口 050) 70 0
2 当与工作 台一起运 动的减速挡 块压下减 速开关 触点 .
数控机床回参考点故障分析与诊断

数控机床回参考点故障分析与诊断一、概述数控机床一般都采用增量式旋转编码器或增量式光栅尺作为位置反馈元件,在机床断电后就失去了对各坐标位置的记忆,因而在每次开机后都必须首先让各坐标轴回到机床的一个固定点上,这一固定点就是机床坐标系的原点或零点,也称机床参考点。
使机床回到这一固定点的操作称回参考点或回零操作。
数控机床返回参考点的方式,因数控系统类型和机床生产厂家而异,就大多数而言,常用的返回参考点方式有两种,即栅格方式和磁性开关方式。
采用栅格方式时,可通过移动栅格(可由系统参数设定)来调整参考点位置。
该方法的特点是机床如果接近原点的速度小于某一固定值,则数控机床总是停止于同一点,也就是说,在进行回原点操作后,机床原点的保持性好。
采用磁性开关方式时,可通过移动接近开关来调整其参考点位置。
该方法的特点是软件及硬件简单,但原点位置随着伺服电机速度的变化而成比例地漂移,即原点不确定。
因此,目前大部分机床采用栅格方式。
现仅以栅格方式返回参考点的情况为例进行分析。
二、回参考点的方式增量式检测装置的数控机床一般有四种回参考点方式。
1.方式一回参考点前,先用手动方式以速度:快速将轴移到参考点附近,然后启动回参考点操作,轴便以速度。
:慢速向参考点移动。
碰到参考点开关后,数控系统即开始寻找位置检测装置上的零标志。
当到达零标志时,发出与零标志脉冲相对应的栅格信号,轴速度即在此信号作用下制动到零,然后再前移参考点偏移量而停止,所停位置即为参考点。
偏移量的大小通过测量由参数设定。
2.方式二回参考点时,轴先以速度v1向参考点快速移动,碰到参考开关后,在减速信号的控制下,减速道速度v2并继续前移,脱开挡块后,再找零标志。
当轴到达测量系统零标志发出栅格信号时,速度即制动到零,然后再以v2速度前移参考点偏移量而停止于参考点。
3.方式三回参考点时,轴先以速度v1快速向参考点移动,碰到参考点开关后速度制动到零,然后反向以速度v2慢速移动,到达测量系统零标志产生栅格信号时,速度制动到零,再前移参考点偏移量而停止于参考点。
数控机床回参考点故障案例(增量式)
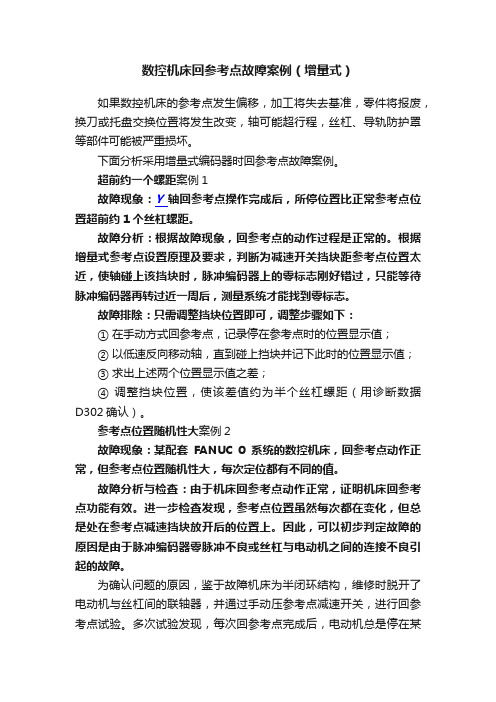
数控机床回参考点故障案例(增量式)如果数控机床的参考点发生偏移,加工将失去基准,零件将报废,换刀或托盘交换位置将发生改变,轴可能超行程,丝杠、导轨防护罩等部件可能被严重损坏。
下面分析采用增量式编码器时回参考点故障案例。
超前约一个螺距案例1故障现象:Y轴回参考点操作完成后,所停位置比正常参考点位置超前约1个丝杠螺距。
故障分析:根据故障现象,回参考点的动作过程是正常的。
根据增量式参考点设置原理及要求,判断为减速开关挡块距参考点位置太近,使轴碰上该挡块时,脉冲编码器上的零标志刚好错过,只能等待脉冲编码器再转过近一周后,测量系统才能找到零标志。
故障排除:只需调整挡块位置即可,调整步骤如下:①在手动方式回参考点,记录停在参考点时的位置显示值;② 以低速反向移动轴,直到碰上挡块并记下此时的位置显示值;③ 求出上述两个位置显示值之差;④ 调整挡块位置,使该差值约为半个丝杠螺距(用诊断数据D302确认)。
参考点位置随机性大案例2故障现象:某配套FANUC 0系统的数控机床,回参考点动作正常,但参考点位置随机性大,每次定位都有不同的值。
故障分析与检查:由于机床回参考点动作正常,证明机床回参考点功能有效。
进一步检查发现,参考点位置虽然每次都在变化,但总是处在参考点减速挡块放开后的位置上。
因此,可以初步判定故障的原因是由于脉冲编码器零脉冲不良或丝杠与电动机之间的连接不良引起的故障。
为确认问题的原因,鉴于故障机床为半闭环结构,维修时脱开了电动机与丝杠间的联轴器,并通过手动压参考点减速开关,进行回参考点试验。
多次试验发现,每次回参考点完成后,电动机总是停在某一固定的角度上。
这说明,编码器零脉冲无故障,问题的原因应在电动机与丝杠的机械连接上。
故障排除:仔细检查发现,原来是丝杠与联轴器间的弹性胀套配合间隙过大,导致连接松动。
修整胀套,重新安装后机床恢复正常。
参考点位置随机性大案例3故障现象:一台数控铣床Y轴能进行返回参考点操作,能找到参考点,但是每次返回参考点所停的位置不固定。
数控机床回参考点的故障分析与排除

数控机床回参考点的故障分析与排除1概述数控机床回参考点时根据检测元件的不同分绝对脉冲编码器方式和增量脉冲编码器方式两种,使用绝对脉冲编码器作为反馈元件的系统,在机床安装调试后,正常使用过程中,只要绝对脉冲编码器的后备电池有效,此后的每次开机,都不必再进行回参考点操作。
而使用增量脉冲编码器的系统中,机床每次开机后都必须首先进行回参考点操作,以确定机床的坐标原点,寻找参考点主要与零点开关、编码器或光栅尺的零点脉冲有关,一般有两种方式。
1)轴向预定点方向快速运动,挡块压下零点开关后减速向前继续运动,直到挡块脱离零点开关后,数控系统开始寻找零点,当接收到第一个零点脉冲时,便以确定参考点位置。
配FANUC系统和北京KND系统的机床目前一般采用此种回零方式。
2)轴快速按预定方向运动,挡块压向零点开关后,反向减速运动,当又脱离零点开关时,轴再改变方向,向参考点方向移动,当挡块再次压下零点开关时,数控系统开始寻找零点,当接收到第一个零点脉冲,便以确定参考点位置。
配SIEMENS、美国AB系统及华中系统的机床一般采用这种回零方式。
采用何种方式或如何运动,系统都是通过PLC的程序编制和数控系统的机床参数设定决定的,轴的运动速度也是在机床参数中设定的,数控机床回参考点的过程是PLC系统与数控系统配合完成的,由数控系统给出回零命令,然后轴按预定方向运动,压向零点开关(或脱离零点开关)后,PLC向数控系统发出减速信号,数控系统按预定方向减速运动,由测量系统接收零点脉冲,收到第一个脉冲后,设计坐标值。
所有的轴都找到参考点后,回参考点的过程结束。
数控机床回不了参考点的故障常见一般有以下几种情况:一是零点开关出现问题;二是编码器出现问题;三是系统测量板出现问题;四是零点开关与硬(软)限位置太近;五是系统参数丢失等等。
下面以本人在工作中遇到的几个实例介绍维修的过程。
2维修实例例1)XH714加工中心开机回参考点,X轴向回参考的相反方向移动。
教学案例1机床不能正常返回参考点

教学案例1机床不能正常返回参考点参考点(Reference point)——是数控厂家通过在伺服轴上建立一个相对稳定不变的物理位置作为参考点,又称电气栅格。
所谓返回参考点,严格意义上是回到电气栅格零点。
(数控机床分为机械坐标零点、工件坐标零点、电气栅格零点——参考点。
我们加工时所使用的工件坐标零点(G54~G59),是在参考点的基础上进行一定量的偏置而生成的(通过参数)。
所以当参考点一致性出现问题时,工件零点的一致性也丧失,加工精度更无从保证。
目前建立参考点的方式主要分为两种:(1)增量方式(reference position with dogs)也称为有档块回零,在每次开电后,需要手动返回参考点,当“机械档块”碰到减速开关后减速,并寻找零位脉冲,建立零点。
一旦关断电源,零点丢失。
(2)绝对坐标方式(absolute-position detector)每次开电后不需要回零操作,零点一旦建立,通过后备电池将绝对位置信息保存在特定的SRAM区中,断电后位置信息也不丢失,这种形式被称为绝对零点。
不能正常返回参考点(增量方式)故障表现形式为:情况1:手动回零时不减速,并伴随超程报警情况2:手动回零有减速动作,但减速后轴运动不停止直至90# 报警——伺服轴找不到零点情况3:手动回零方式下根本没有轴移动那么我们从分析整个返回参考点的工作过程和工作原理入手。
原理及过程过程分析:1)回参考点方式有效(ZRN)(MD1/MD4)——对应PMC地址G43.7=1,G43.0=1/G43.2=1。
2)轴选择(+/-Jx)有效——对应PMC地址G100~G102=1。
3)减速开关读入信号(*DECx)——对应PMC地址X9.0~X9.3或G196.0~3=101。
4)电气格被读入,找到参考点。
增量式回零过程:图13-1 回参考点过程这里需要详细说明的是“电气栅格”。
FANUC 数控系统除了与一般数控系统一样,在返回参考点时需要寻找真正的物理栅格——编码器的一转信号(如图13-1所示),或光栅尺的栅格信号(如图13-2所示)。
分析fanuc数控系统返回参考点功能

分析FANUC数控系统返回参考点功能一.概述:现今汽车行业的机加工母机都使用数控机床。
我公司动力总成厂(SGMPT)的机加工机床也不例外的使用数控机床,且使用当今国际上最先进的数控系统。
我厂使用的数控系统有I)FANUC;2)INDRAMAT;3)1ANDIS;4) 等产品。
其中使用最多的是FANUC系统,97%以上的数控机床使用FANUC系统。
我厂使用FANUC系统控制的设备有:1)卧式加工中心;2)立式加工中心;2)立式车床;4)滚齿机;5)布磨机;6)高频淬火机;7)抛光机;8)上下料机械手(GANTRY)9)各种专机等。
使用FANUC数控系统的种类有:I)FS-160CM;2)FS-18BT;3)FS-PMD;4)FS-PMH;5)FS-PMb6)FS-15M0在我们对设备的使用和维修过程中,遇到较多的是返I可参考点(通常所说的“回零”)问题。
返回参考点的作用是修改数控系统(CNC)的软件记忆位置与设备的机械位置相一致(类似标定);所以数控机床在运行前必须进行返I口I参考点。
在调试时,要初次设置参考点;在使用时,加工超差有时需要调整参考点;在维修时,系统,伺服或光栅故障,或者更换丝杠后,需找回原参考点。
F ANUCCNC提供的返I川参考点方法有多种;根据各种设备的特点和应用场合等个性问题,设置各种设备的参考点方法不相同;同种设备的生产厂商不同,其返回参考点的方法也不相同;而各个厂商根据自己的思路,设计的返回参考点操作过程各不相同。
所以我们在现场操作过程中,感觉纷繁复杂,不着边际,且经常出错,造成设备或刀具受损。
所以我们急需分析清楚FANUCCNC各种方法返I可参考点功能的原理,从理论上找出其共性;以便在以后的操作中有理论依据,避免出错!下面针对我厂所使用的FANUCCNC各种返回参考点方法进行理论分析。
而我厂使用最多的FAUNCCNC是FS-160CM,FS-18BT,FS-PMD;且这三种CNC的参数和PMC接口体系是一致的;在分析过程使用FS-160CM参数和PMC接口信号。
- 1、下载文档前请自行甄别文档内容的完整性,平台不提供额外的编辑、内容补充、找答案等附加服务。
- 2、"仅部分预览"的文档,不可在线预览部分如存在完整性等问题,可反馈申请退款(可完整预览的文档不适用该条件!)。
- 3、如文档侵犯您的权益,请联系客服反馈,我们会尽快为您处理(人工客服工作时间:9:00-18:30)。
加工中心返参考点案例分析
【摘要】加工中心的参考点,作为机床和工件坐标系的原始参考点,一旦确定后,各工件坐标系随之建立。
机床参考点是机床坐标和工件坐标系的基础,如果机床参考点发生漂移,则加工零件的一致性不好,严重时可能废活,更甚者可能在交换工作台或换刀时发生撞车事故。
所以当机床参考点发生漂移时,一定要分析其原因,将故障排除。
【关键词】参考点;漂移;故障
在日常设备维修过程中,经常可以遇到一些因为机床参考点发生漂移而导致的设备故障,现例举几例与参考点漂移有关的故障,供大家借鉴。
1THM6363宁江加工中心交换工作台故障
故障现象:在加工过程中,偶尔在交换工作台时发生故障,其报警内容为“工作台不在交换托盘上”。
此时,工作台已经被托盘托起,床身内的工作台由于不在托盘中心,已经倾斜,操作工通常会用手动方式,先将托盘落下,然后再重新将各轴返参考点,随后完成工作台交换。
由于故障不很频繁,操作工也就没有报修。
一次,操作工反映,早上开机加工零件时,感觉机床吃刀量变大,并有明显振动,随即按下了急停开关,发现零件位于圆周上的四个等分槽的尺寸已与图纸明显不符,于是将设备进行了报修。
故障分析:检查有关参数设置及信号电缆连接。
参数设置正常,光栅尺等线性测量元件及其接口电路未见明显故障。
先减小由参数设置的接近原点速度,重试回原点操作,原点不漂移。
由于该工件不是首件加工,排除了程序原因,据操作工反映,该工件前一天未加工完成,第二天继续加工时出现了故障。
联系到以前交换工作台时发生的故障,基本可以判断是参考点漂移造成的故障。
为了印证判断,连续开关机,返参考点并交换工作台,终于在一次实验中,又发生了床身内的工作台由于不在托盘中心而倾斜的故障,并且工作台距交换点相差了12mm,正好为一个螺距,也与报废工件的误差相吻合。
这就说明了参考点漂移而导致工作台交换点发生了变化。
该机床返参考点的过程是,在机床上安装一个感应块及感应开关,当感应块感应到感应开关时,伺服电机减速至接近参考点速度运行。
当感应块离开感应开关后,数控系统检测到的第一个栅点或电机一转即为参考点。
这种返参考点的特点是如果接近原点速度小于某一固定值,则伺服电机总是停止于同一点,也就是说,在进行回参考点操作后,机床参考点的保持性好。
处理过程:当一个减速信号由硬件输出后,数字伺服软件识别这个信号需要一定时间。
因此当减速撞块离原点太近时,软件有时捕捉不到原点信号,导致原点漂移。
由于该运动轴返参考点时有减速过程,并能够完成整个过程,故感应开关没有问题,检查感应块时,发现感应块松动,导致参考点发生偏移,偏移量正好为一个螺距。
紧固好感应块后,设备故障排除,再也没有出现类似故障。
2HS500日立精机加工中心换刀故障
故障现象:该设备采用FANUC18i控制系统,先是出现电池报警,复位后继续运行,在加工过程中执行换刀程序时,机械手抓刀时,主轴位置误差过大,机械手被卡死。
故障分析:设备返参考点按照检测元件测量方式的不同,分为绝对脉冲编码器方式归零和增量脉冲编码器方式归零。
在使用绝对脉冲编码器作为测量反馈元件的系统中,机床调试时第一次开机后,通过参数设置配合机床回零操作调整到合适的参考点后,只要绝对脉冲编码器的电池有效,此后每次开机,不必进行回参考点操作。
如果原点发生漂移,首先检查并重新设置与机床回原点有关的检测绝对位置有有关参数,重新再试一次回原点操作。
若原点仍漂移,检查机械相对位置是否有变化。
如果没有漂移,只是位置显示有偏差,则检查工件坐标偏置是否有效,若机械位置偏移,则绝对脉冲编码器故障。
该设备采用绝对脉冲编码器方式归零,由于电池电压过低,参考点位置丢失,换刀点位置随之改变,所以导致换刀故障。
如果参考点漂移量不大,机床换刀及交换工作台时都影响不大,但工件的一致性不好,加工质量会受到影响。
处理过程:更换电池,重新设置参考点。
在手动模式下,将各轴摇到换刀点,执行单步换刀指令,调整该轴到合适位置,然后通过1815号参数设置参考点。
参考点位置已经发生细微变化,在加工过程中需要注意。
当加工中心回参考点出现故障时,先检查原点感应块是否松动,感应开关固定是否牢固或是损坏。
若无问题,应进一步确定漂移量;检查减速撞块的长度;检查回原点起始位置、减速开关位置与原点位置的关系;检查回原点的模式;是否开机后的第一次回原点,是否采用绝对脉冲编码器;检查回原点快速进给速度的参数设置、接近原点速度的参数设置及快速进给时间常数的参数设置是否合适;确认系统是全闭环还是半闭环;检查与参考点相关的参数设置是否适当等。
如果减小接近原点速度参数设置后,重试原点复归,若原点仍漂移,可减小快速进给速度或快速进给时间常数的参数设置,重回原点。
若减小快进时间常数或快速进给速度的设置,重新回原点,原点仍有漂移,应检查参考计数器设置的值是否有效,修正参数设置。
若只是在开机后第一次回原点时原点漂移,则为零标志信号受干扰,应确保电缆屏蔽线接地良好,,不要使检测反馈元件的通信电缆线与强电线缆靠得太近。
数控设备远离焊接设备及电加工设备,防止干扰信号对设备造成影响。
如果通过上述步骤检查仍不能排除故障,应检查编码器电源电压是否太低;编码器是否损坏;伺服电机与进给轴联轴器是否松动;;有关伺服轴驱动器是否正常等。
加工中心回参考点故障需要警惕参考点漂移,此类故障一般不会报警,对加工精度有一定的影响,而无法回参考点会有报警,可通过排除故障解决问题,不会对工件产生影响。
(上接第303页)
为根据我国高铁运用现状,合理安排轮对探伤方法和探伤周期,提高我国轮对检修效率和列车安全运行系数,两个方面需要考虑:(1)对运行几十年的失效轮对数据积累,分析导致失效的原因,由此指导选用合适的探伤方法和探伤周期,同时指导设计改进,提高我国高铁轮对新制和检修水平;(2)对各种无损检测方法在应用中发现的问题及时进行完善,必要时采用多种方法和其它新技术验证高速动车轮对的完好性,保证我国高速动车的安全运行。
参考文献:
[1]中华人民共和国铁道部运装客车[2009]493号,铁路客车轮轴探伤工艺规程(试行)[Z].
[2]周贤全.改善新干线车辆车轴常规检测[J].国外铁道车辆.2001(04).
[3]BerndROCKSTROH,WolfgangKAPPES,etal.UltrasonicandEddy-CurrentInspectionofRailWheelsandWheelSetAxles.17thWorl dConferenceonNondestructiveTesting,2008,Shanghai.
[4]ErnestoGARC?AARES,JoséLuisGARC?AALONSO,etal.AutomaticIn-serviceTrainAxleInspectionSystems.ECNDT(2006).
[5]中华人民共和国铁道部运装客车[2008]694号,CRH系列动车组空心车轴超声波探伤工艺规程(试行)[Z].
[6]胡晓军.法国TGV高速列车轮对制造与检修[J].国外铁道车辆.1992(01).
[7]中华人民共和国铁道部运装客车[2011]428号,CRH系列动车组车轮超声波探伤工艺规程(试行)[Z].
[8]彭朝勇,王黎,高晓蓉.我国高速动车组车轮超声波探伤技术[J].高速铁路.2011(11).。