BH高碳势工艺介绍
几种可控气氛的产气原理碳势调节和安全事项
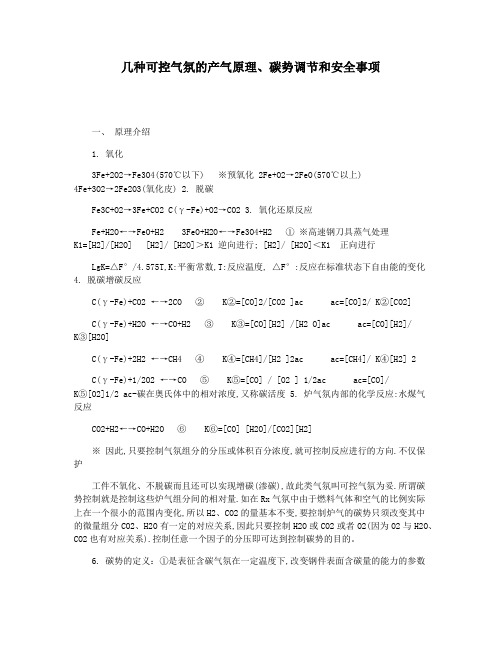
几种可控气氛的产气原理、碳势调节和安全事项一、原理介绍1. 氧化3Fe+2O2→Fe3O4(570℃以下) ※预氧化2Fe+O2→2FeO(570℃以上)4Fe+3O2→2Fe2O3(氧化皮) 2. 脱碳Fe3C+O2→3Fe+CO2 C(γ-Fe)+O2→CO2 3. 氧化还原反应Fe+H2O←→FeO+H2 3FeO+H2O←→Fe3O4+H2 ① ※高速钢刀具蒸气处理K1=[H2]/[H2O] [H2]/ [H2O]>K1 逆向进行; [H2]/ [H2O]<K1 正向进行LgK=△F°/4.575T,K:平衡常数,T:反应温度, △F°:反应在标准状态下自由能的变化4. 脱碳增碳反应C(γ-Fe)+CO2 ←→2CO ② K②=[CO]2/[CO2 ]ac ac=[CO]2/ K②[CO2]C(γ-F e)+H2O ←→CO+H2 ③ K③=[CO][H2] /[H2 O]ac ac=[CO][H2]/K③[H2O]C(γ-Fe)+2H2 ←→CH4 ④ K④=[CH4]/[H2 ]2ac ac=[CH4]/ K④[H2] 2C(γ-Fe)+1/2O2 ←→CO ⑤ K⑤=[CO] / [O2 ] 1/2ac ac=[CO]/K⑤[O2]1/2 ac-碳在奥氏体中的相对浓度,又称碳活度 5. 炉气氛内部的化学反应:水煤气反应CO2+H2←→CO+H2O ⑥ K⑥=[CO] [H2O]/[CO2][H2]※ 因此,只要控制气氛组分的分压或体积百分浓度,就可控制反应进行的方向.不仅保护工件不氧化、不脱碳而且还可以实现增碳(渗碳),故此类气氛叫可控气氛为妥.所谓碳势控制就是控制这些炉气组分间的相对量.如在Rx气氛中由于燃料气体和空气的比例实际上在一个很小的范围内变化,所以H2、CO2的量基本不变,要控制炉气的碳势只须改变其中的微量组分CO2、H2O有一定的对应关系,因此只要控制H2O或CO2或者O2(因为O2与H2O、CO2也有对应关系).控制任意一个因子的分压即可达到控制碳势的目的。
碳碳的制造工艺

碳碳的制造工艺概述碳碳复合材料是一种具有优异性能的高温结构材料,广泛应用于航空航天、汽车制造、核能工业等领域。
碳碳复合材料由碳纤维和炭化石墨矩阵组成,具有高温强度、耐腐蚀性和热震稳定性等特点。
本文将详细介绍碳碳的制造工艺。
1. 碳纤维制备1.1 原料选择制备碳纤维的原料通常为聚丙烯腈(PAN)纤维或石墨化沥青(Pitch)纤维。
PAN纤维具有较高的强度和模量,适用于制备高性能的碳纤维;Pitch纤维则具有较高的导电性和耐高温性能。
1.2 碳化过程1.2.1 预氧化PAN纤维在氧气氛中进行预氧化处理,将其转变为具有一定结晶度和稠度的物质,增加后续碳化过程中的产率和强度。
1.2.2 碳化经过预氧化的PAN纤维或Pitch纤维在高温下进行碳化处理,使其转变为高纯度的碳纤维。
碳化过程需要控制温度和气氛,以确保纤维的结构和性能。
1.3 纤维表面处理碳纤维表面通常存在一定的氧化物,需要进行表面处理以提高其与矩阵材料的结合性能。
常用的表面处理方法包括等离子体处理、化学处理和机械磨削等。
2. 炭化石墨矩阵制备2.1 矩阵原料选择炭化石墨矩阵通常采用煅烧型树脂(Resin)或者沥青(Pitch)作为原料。
树脂型矩阵具有较低的导电性和耐高温性能,适用于一些低温应用;而沥青型矩阵具有较高的导电性和耐高温性能,适用于高温应用。
2.2 矩阵浸渍将碳纤维预制件浸泡在树脂或沥青中,使其充分浸渍,形成浸渍体。
浸渍过程中需要控制浸渍时间和温度,以确保纤维和矩阵的结合质量。
2.3 热处理经过浸渍的碳纤维预制件在高温下进行热处理,使其转变为炭化石墨矩阵。
热处理过程需要控制升降温速率和保持时间,以确保矩阵的致密性和均匀性。
3. 碳碳复合材料制备3.1 预成型将经过碳化的碳纤维预制件与经过热处理的炭化石墨矩阵预制件放置在模具中,进行定型压制。
预成型过程中需要控制压力、温度和时间,以确保复合材料的密实性和尺寸精度。
3.2 热压缩经过预成型的复合材料在高温下进行热压缩处理,使其形成致密的结构。
高碳钢77BYL82B钢种工艺要点比对

控制标准:
Als
≤0.0025
0.22 0.72 0.01
0.01
铁水→混铁炉→2#转炉→2#LF炉→2#连铸水 符合科技处有关标准。铁水硅≥0.30%,硫≤ 0.050%,铁水温度≥1280℃,高炉护炉期间不生产 本钢种。
炼 115±2吨,铁水:废钢按照105:10。废钢使用自产切割废 钢坯及轧废。补炉后前三炉不冶炼本钢种,新钢包前3炉不 冶炼本钢种,使用热炉冶炼本钢种,使用全镁碳衬钢包
2.1、工艺路线: 2.2、铁水、辅料 、合金 2.3、冶炼
符合科技处有关标准。铁水硅≥0.30%,硫≤ 2.2、铁水、辅料、 0.050%,铁水温度≥1280℃,高炉护炉期间不 合金 生产本钢种。 2.3、冶炼 115±2吨,铁水:废钢按照105:10。废钢使用自产切 2.3.1、装 割废钢坯及轧废。补炉后前三炉不冶炼本钢种,新钢 入量: 包前3炉不冶炼本钢种,使用热炉冶炼本钢种,使用全 镁碳衬钢包 2.3.2、供 工作氧压0.70-0.95Mpa,流量:17000-20000m3/h,供 氧: 氧强度按照2.9~3.1m3/(min.t)。
1640
1625
转炉炉长可综 合考虑钢包烘 控制范 目标温 控制范 烤情况,连铸 围 度 围 节奏情况、出 钢口情况进行 1620~ 1615~ 出钢温度调整 1630 。 1625 1620
连浇炉
开浇炉 目标 温度
第二炉
控制范 目标温 围 度 1635~ 1645
1640
1630
出钢时用电解锰和无铝硅铁进行钢水合金化,锰收得 2.3.7、出 率按90%考虑,硅收得率按85%考虑,硅、锰调整到成 钢合金化及 分下限。出钢开始即可加入石墨电极增碳剂,将碳调 增碳: 整至0.72% 2.38、转炉 出钢及合金 电解锰、无铝硅铁。出钢1/4开始加入,至3/4加完。 加入顺序: 成分 成份(转炉出 钢)目标 2.3.9、加 顶渣 C % 0.72 Si % 0.2 Mn % 0.7 P % ≤0.015
BH技术--热处理节能新技术的特点

一、在工艺温度降低40℃以上条件下(≥810℃)可保持工件在原工艺温度下的渗速不减。可减少变形,减少产品晶粒粗化倾向,使本质粗晶粒钢渗碳直接淬火后的马氏体级别得到一定控制,并显著延长设备及其耐热元件寿命。
二、在同样工艺温度下比常规渗碳或碳氮共渗渗速快20%以上,可显著减少工件在高温阶段的
三、BH技术可提高气氛中碳的活性,减少炭黑,显著缓解富化剂加空气直生式气氛渗碳中炭黑相对较多的难题,延长了氧探头寿命。
BH催渗技术是我国学者独立自主开发成功的一项具有国际领先水平的新技术。该技术的成功是热处理技术发展史上的一大突破,它将对我国未来热处理技术的发展产生深远影响,为我国热处理技术走向世界提供一个有利的平台。
BH技术--热处理节能新技术的特点
2011-08-26 11:03 近几年来,由于国外先进技术、先进设备的引进极大地推动了中国热处理技术的发展,使中国热处理技术向前迈进了一大步,缩短了与先进国家的差距。但中国的热处理行业目前的状况还远远落后于发达国家。
近几年来,由于国外先进技术、先进设备的引进极大地推动了中国热处理技术的发展,使中国热处理技术向前迈进了一大步,缩短了与先进国家的差距。但中国的热处理行业目前的状况还远远落后于发达国家。目前,国外的热处理设备大部分已采用燃气辐射管、全自动控制的热处理生产线。而国内仍处于一种设备陈旧、工艺保守、设备管理落后、装备笨重、能源利用率低等情况。与发达国家相比,在相同的能耗条件下,其产量是我国产量的5倍以上。由于我国的能源短缺,所以挖掘热处理设备节能的潜力是节省能耗的必要措施。
目前,有一项适用于在各种设备和气氛下进行低温快速渗碳或碳氮共渗的节能新技术――BH技术,使用该技术时只需利用催渗剂进行适当的工艺调整即可。BH的核心是通过在渗碳气氛中添加微量的催渗剂,使渗碳介质(丙烷、RX气、丙酮、煤油等)在气氛中产生部分正四价碳离子――正四价碳离子(φ0.15nm)体积只有碳离子(φ0.77nm)体积的1/135,因而活性高,在奥氏体中扩散阻力小、扩散速度快。
20Cr2Ni4A齿轮钢天然气渗碳工艺研究

540试验研究Vol.70 No.5 2021 20Cr2Ni4A齿轮钢天然气渗碳工艺研究刘国强1’2,王小海1’2,张鹏1’2,李军1’2,王卓1’2,班永华1’2,蔡红1,于庆峰1(1.内蒙古第一机械集团股份有限公司,内蒙古包头014030; 2.特种车辆及其传动系统智能制造国家重点实验室,内蒙古包头014030)摘要:为了解决常规渗碳过程中存在效率低、污染重、成本高的问题,采用净化后天然气作为富化介质对20C r2N i4A齿轮钢进行渗碳处理。
通过扫描电镜、能谱分析仪、显微硬度仪、碳硫分析仪、残余应力检测仪等手段对常规渗碳与天然气渗碳后的显微组织、渗层成分、硬度梯度、碳浓度梯度、残余应力分布梯度进行检测,并对两种渗碳工艺的生产效率进行对比,同时也对天然气渗碳后的常、低温冲击断口形貌进行了分析。
结果表明:与常规渗碳相比,当渗碳层深为(丨.6±0.2)mm时,天然气渗碳可提升效率15%以上;可获得较为平缓的硬度梯度、碳浓度梯度分布和较高的渗层残余压应力。
低温冲击断口形貌具有韧窝少而浅、准解理形貌和二次裂纹多等特征,同时局部区域出现沿晶断裂。
天然气渗碳工艺可应用于高承载、长寿命重载齿轮的表面强化。
关键词:20C r2N i4A齿轮钢;天然气渗碳;显微组织;硬度梯度;残余应力梯度;冲击断口作者简介:刘国强(1980-),男,局级工程师,硕士,主要 从事金属材料表面强化与传动结构件抗疲劳制造研究工作。
电话:************,E-mail:nmyjlgql101@中图分类号:TGI56.8文献标识码:A文章编号:1001*4977(2021) 05-0540-07基金项目:包头市青年创新人才项目 (ZZ2019JT024 );内蒙古 自治区科技重大专项。
收稿日期:2021-02-0丨收到初稿,2021-02-21收到修订稿。
重载齿轮是大功率传动系统核心零部件,服役过程中有传递功率大、承载能力 高、耐冲击性能好等特点,被广泛应用于矿山、冶金、远洋运输、航空航天、重载 车辆等领域[W1。
BH产品说明
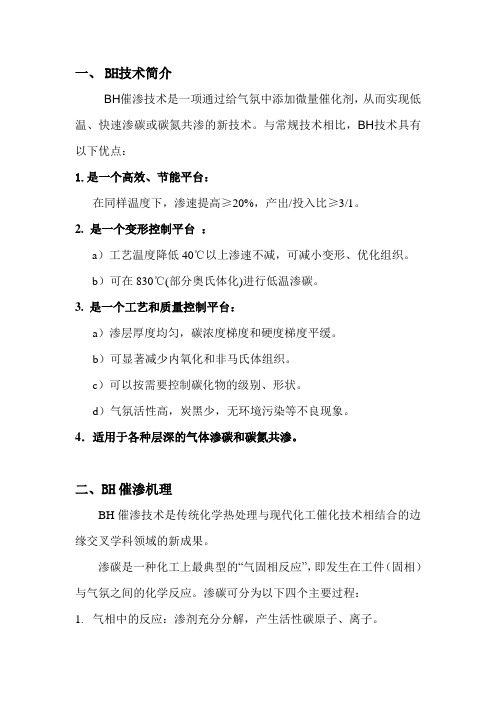
一、BH技术简介BH催渗技术是一项通过给气氛中添加微量催化剂,从而实现低温、快速渗碳或碳氮共渗的新技术。
与常规技术相比,BH技术具有以下优点:1.是一个高效、节能平台:在同样温度下,渗速提高≥20%,产出/投入比≥3/1。
2.是一个变形控制平台:a)工艺温度降低40℃以上渗速不减,可减小变形、优化组织。
b)可在830℃(部分奥氏体化)进行低温渗碳。
3. 是一个工艺和质量控制平台:a)渗层厚度均匀,碳浓度梯度和硬度梯度平缓。
b)可显著减少内氧化和非马氏体组织。
c)可以按需要控制碳化物的级别、形状。
d)气氛活性高,炭黑少,无环境污染等不良现象。
4.适用于各种层深的气体渗碳和碳氮共渗。
二、BH催渗机理BH催渗技术是传统化学热处理与现代化工催化技术相结合的边缘交叉学科领域的新成果。
渗碳是一种化工上最典型的“气固相反应”,即发生在工件(固相)与气氛之间的化学反应。
渗碳可分为以下四个主要过程:1.气相中的反应:渗剂充分分解,产生活性碳原子、离子。
2.活性碳原子、离子在气相(气氛)中的传递、扩散。
3.气固相表面渗碳反应:活性碳原子、离子与工件表面接触,在气固相界面发生反应,碳被工件表面吸收,并产生副产物CO和H2。
4.被吸收的碳原子、离子在工件内部扩散,此过程一般很慢。
在实际反应时,第1、2步的速度较快,第3步、第4步较慢,是影响渗速的瓶颈。
要提高渗速就必须解决第3步、第4步的问题。
BH催渗剂从以下4个方面影响着渗碳过程:1、对渗剂分解和碳原子活性的作用:渗剂(甲醇、丙酮、煤油、RX气体或天然气等)分解是渗碳的第一步,渗剂的充分分解和断链需要在较高的温度和催化剂下进行。
前苏联、欧美及早期在我国率先采用可控气氛技术的一汽、二汽等,为了保证渗剂的充分分解和生产工艺的稳定、可控,都采用了1050℃炉外造气的方法以保证气体成分,而且还要采用俗称“触媒”的分解催化剂。
但是不要忘了:炭黑一直是我们生产控制的一大难题,为了减少炭黑、为了控制的稳定,我们不得不采用较低的碳势生产,这样渗速就被人为地降低了。
炭素制品工艺技术

炭素制品工艺技术炭素制品是一种具有广泛应用的高性能材料,其制备技术的发展对于推动现代工业的发展起到了重要的推动作用。
炭素制品工艺技术主要包括炭化、焙烧、石墨化和石墨化等步骤,下面将分别介绍这些步骤的工艺特点以及应用。
首先是炭化过程。
炭化是将有机原料经过高温处理,使其脱去除碳以外的主要成分,形成具有高碳含量的炭素材料。
这种工艺技术主要适用于炭黑、焦炭和石墨的制备。
炭化过程中需要控制温度、时间和气氛等因素,以确保所制备的炭素材料具有所需的特性。
接下来是焙烧过程。
焙烧是将炭化后的材料在高温下进行热处理,以使其结构更加稳定。
焙烧过程主要通过提高温度和延长时间来实现。
焙烧的目的是提高材料的热稳定性和机械强度,同时减小材料的气孔,从而提高材料的密度和密封性。
石墨化是将经过焙烧的材料进行化学处理,从而使其获得更高的结晶度和石墨化程度。
石墨化过程主要通过在高温下进行氧化处理,使材料中的杂质得到去除,从而提高石墨材料的性能。
石墨化技术的主要应用是生产高纯度的天然石墨和人工石墨。
最后是石墨化过程。
石墨化是将经过焙烧和石墨化处理的材料进行加工,以使其形成具有特定形状和尺寸的产品。
石墨化工艺主要包括压制、加热和再压缩等步骤。
通过这些加工步骤可以制备出石墨片、石墨乳液、石墨纤维和石墨复合材料等多种炭素制品。
炭素制品工艺技术的发展在很大程度上推动了现代材料科学的发展。
炭素制品具有很多优良的性能,如高强度、高导热性、高导电性、低摩擦系数和耐高温等特性,因此广泛应用于航空航天、电子、化工、能源和新能源等领域。
同时,炭素制品还具有很高的环保性能,不产生污染物和有害气体,符合可持续发展的要求。
总之,炭素制品工艺技术的发展为现代工业的发展提供了重要的支撑。
通过炭化、焙烧、石墨化和石墨化等工艺步骤,可以制备出具有高强度、高导热性、高导电性和耐高温等性能的炭素制品。
这些炭素制品在航空航天、电子、化工、能源和新能源等领域具有广泛应用前景。
高碳钢丝生产工艺
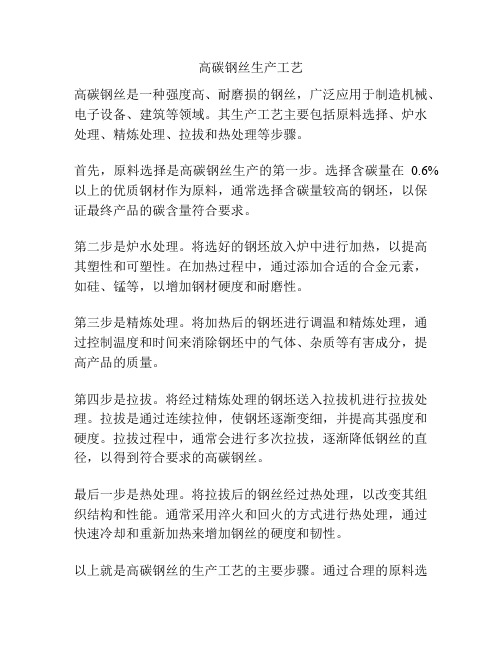
高碳钢丝生产工艺
高碳钢丝是一种强度高、耐磨损的钢丝,广泛应用于制造机械、电子设备、建筑等领域。
其生产工艺主要包括原料选择、炉水处理、精炼处理、拉拔和热处理等步骤。
首先,原料选择是高碳钢丝生产的第一步。
选择含碳量在0.6%以上的优质钢材作为原料,通常选择含碳量较高的钢坯,以保证最终产品的碳含量符合要求。
第二步是炉水处理。
将选好的钢坯放入炉中进行加热,以提高其塑性和可塑性。
在加热过程中,通过添加合适的合金元素,如硅、锰等,以增加钢材硬度和耐磨性。
第三步是精炼处理。
将加热后的钢坯进行调温和精炼处理,通过控制温度和时间来消除钢坯中的气体、杂质等有害成分,提高产品的质量。
第四步是拉拔。
将经过精炼处理的钢坯送入拉拔机进行拉拔处理。
拉拔是通过连续拉伸,使钢坯逐渐变细,并提高其强度和硬度。
拉拔过程中,通常会进行多次拉拔,逐渐降低钢丝的直径,以得到符合要求的高碳钢丝。
最后一步是热处理。
将拉拔后的钢丝经过热处理,以改变其组织结构和性能。
通常采用淬火和回火的方式进行热处理,通过快速冷却和重新加热来增加钢丝的硬度和韧性。
以上就是高碳钢丝的生产工艺的主要步骤。
通过合理的原料选
择、炉水处理、精炼处理、拉拔和热处理等步骤,可以得到优质的高碳钢丝产品。
这些产品具有高强度、耐磨损的特点,在各个领域都具有广泛的应用前景。
渗碳层非马氏体组织的控制方法

渗碳层非马氏体组织的控制方法展开全文普通气体渗碳过程中,非马氏体组织的产生是不可避免的,但是非马氏体组织的控制可以从渗碳(碳氮共渗)零件原材料、热处理工艺、渗碳介质及设备等方面进行综合考虑,从而最大限度减少非马氏体组织。
1. 渗碳零件原材料方面从钢材合金元素方面考虑,由于钢中的Si有大的氧化势系数,是决定钢内氧化深度的重要因素之一,因此应尽可能采用低的Si含量钢材,如采用优质渗碳钢(如DSG1钢,Si含量降至0.15%以下,而使内氧化现象及非马氏体大为减少);钢中的Mn是影响内氧化强度的重要因素,应适当控制Mn含量。
内氧化的程度一方面取决于渗碳气氛及渗碳条件;另一方面取决于渗碳材料中的合金元素。
许多资料研究表明,使用含Ni、Mo元素的渗碳钢可以大大减轻内氧化程度,原因是Ni、Mo的氧化倾向较小且能强烈增加钢的淬透性能。
因此,国外发达国家大多采用含Ni、Mo钢材制造渗碳零件(如齿轮)。
同20CrMnTi钢相比,采用美国8620H(相当于国内20CrNiMoH)、日本SCM822H(相当于国内22CrMoH)、德国17CrNiMo6(相当于国内17CrNiMo6H)等渗碳钢淬火,可减轻非马氏体组织的产生。
2. 热处理工艺方面非马氏体组织的产生在很大程度上又取决于气氛的氧势或碳势、渗碳介质中含水量、渗碳温度、加热和排气过程和渗碳时间等。
(1)采用氮—甲醇工艺减少非马氏体组织在可控气氛中,氮气是作为稀释气使用的,当气氛中加入一定量的氮气时,可以减少原料气的消耗,减少炭黑的形成。
试验表明,在渗碳气氛中通入氮气后,建立碳势的速度加快,碳势增高。
这是由于经氮气稀释后,炉气的分解率提高,CO和H2O含量降低,碳的活度增大,使反应加快,渗碳速度加快。
在氮基渗碳气氛中,不仅CO2和H2O可以减少,而且CO也可以适当降低。
由于CO2和H2O可同钢中的Cr、Mn、Si等元素发生氧化作用。
因此,氮基气氛渗碳可以降低钢件的内氧化程度。
碳势

碳势是气氛的热力学特性,它表示气氛的一种平衡能力。
气氛在热处理加热温度下,气氛的气相中提供的活性炭原子与钢表面奥氏体中的含碳量相平衡的能力。
影响钢脱碳的因素影响钢脱碳的因素有钢料的化学成分,加热温度,保温时间和煤气成分等。
1.钢料的化学成分对脱碳的影响钢料的化学成分对脱碳有很大影响。
钢中含碳量愈高脱碳倾向愈大W、Al、Si、Co等元素都使钢脱碳倾向增加;而 Cr、Mn等元素能阻止钢脱碳。
2.加热温度的影响随着加热温度的提高,脱碳层的深度不断增加。
一般低于1000℃时,钢表面的氧化皮阻碍碳的扩散,脱碳比氧化慢,但随着温度升高,一方面氧化皮形成速度增加;另一方面氧化皮下碳的扩散速度也加快,此时氧化皮失去保护能力,达到某一温度后脱碳反而比氧化快。
3.保温时间和加热次数的影响加热时间越长,加热火次愈多,脱碳层愈深,但脱碳层并不与时间成正比增加。
例如高速钢的脱碳层在1000℃加热0.5h,深度达0.4mm;加热4h达1.0mm;加热12h后达1.2mm。
4.炉内气氛对脱碳的影响在加热过程中,由于燃料成分,燃烧条件及温度不同,使燃烧产物中含有不同的气体,因而构成不同的炉内气氛,有氧化性的也有还原性的。
他们对钢的作用是不同的。
氧化性气氛引起钢的氧化与脱碳,其中脱碳能力最强的介质是H2O(汽),其次是CO2与O2,最后是H2;而有些气氛则使钢增碳,如 CO和 CH4。
炉内空气过剩系数α大小对脱碳也有重要的影响:当α过小时、燃烧产物中出现H2,在潮湿的氢气内的脱碳速度随着含水量的增加而增大。
因此,在煤气无氧化加热炉中加热,当炉气中含H2O较多时,也要引起脱碳;当α过大时,由于形成的氧化皮多,阻碍着碳的扩散,故可减小脱碳层的深度。
在中性介质中加热时,可使脱碳最少碳势与水势、电势一样,势差决定了物质流动的趋势。
碳势差决定了碳扩散的方向。
当自由扩散时,碳总是从碳势高的地方向碳势低的地方扩散。
钢铁材料、炉气、炉渣中碳势取决于的碳含量(浓度)和温度。
汽车后桥齿轮渗碳工艺

工艺进 行时间/ mi n |
3 0 2 4 8 1 4 4 1 6 5 6 0 2 0
温度F C 9 O 0
9 0 0 9 3 0 9 0 0 8 3 0 8 3 0 9 0 0
丙烷/ m3 . h O . 1 3 ~0 . 1 5
G
汽车后桥齿轮渗碳工艺
郑 州华威齿 轮有 限公司 ( 河南 4 5 2 3 7 0 ) 高永强
汽 车 零 件 的渗 碳 热 处 理 设 备 主要 有 密 封 箱式 多
钢 。 产 品 技 术 要 求 : 显 微 组 织 按 QC 2 6 2 —1 9 9 9 汽 车 渗 碳 齿 轮 金 相 检 验 标 准 进 行 评 定 ,其 中 M. A/ 1 ~5 级 和 K1 ~5 级 为 合 格 ;硬 化 层深 度 为 1 . 0
密封 箱 式 淬 火炉 ,型号 S HQF一2 / 2 。
变形 ,从而提 高产品的热处理质量 ,同时还能有效 地达到节能的 目的 ,降低产品的热处理成本 。
1 . 金杯 面包车后桥 从动弧齿锥齿 轮渗碳工艺
S Y6 4 8 0 系 列 金 杯 海 狮 面 包车 后 桥 从 动 弧 齿 锥 齿轮 如 图1 所示 。材料为2 0 Cr Ni Mo H ( 8 6 2 0 H)
丙烷追加
强渗 扩散
降温
3 0
l 8 6 1 2 6
1 2 4
9 3 0
9 3 0 8 8 0
8 3 0
0 . 1 3 ~0 . 1 5
O . 1 3 ~0 . 1 5 O . 1 3 ~O . 1 5
0 . 1 3渗碳 的主 要 消耗 就 是 介 质 和 电能 。如 果 在 渗 碳 时 采 用 催 渗工 艺 ,这样 不 仅 能 节 约时 间 ,减 小
聚异丁烯生产工艺
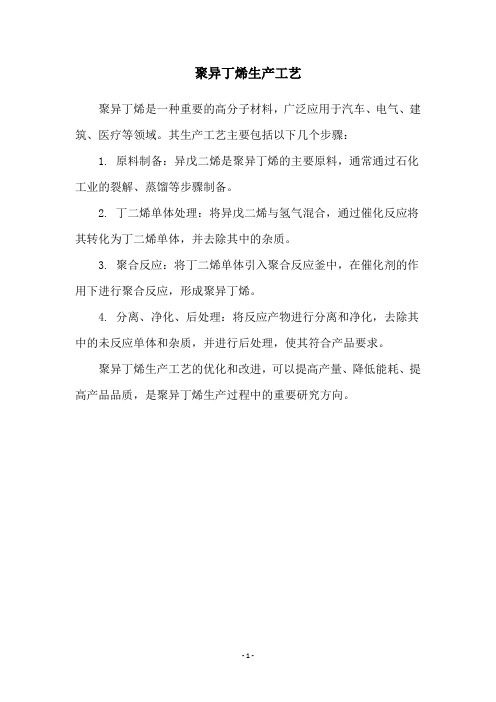
聚异丁烯生产工艺
聚异丁烯是一种重要的高分子材料,广泛应用于汽车、电气、建筑、医疗等领域。
其生产工艺主要包括以下几个步骤:
1. 原料制备:异戊二烯是聚异丁烯的主要原料,通常通过石化工业的裂解、蒸馏等步骤制备。
2. 丁二烯单体处理:将异戊二烯与氢气混合,通过催化反应将其转化为丁二烯单体,并去除其中的杂质。
3. 聚合反应:将丁二烯单体引入聚合反应釜中,在催化剂的作用下进行聚合反应,形成聚异丁烯。
4. 分离、净化、后处理:将反应产物进行分离和净化,去除其中的未反应单体和杂质,并进行后处理,使其符合产品要求。
聚异丁烯生产工艺的优化和改进,可以提高产量、降低能耗、提高产品品质,是聚异丁烯生产过程中的重要研究方向。
- 1 -。
推杆球座渗碳淬硬工艺

件推 杆球 座结构 如 图 1 所示 。技术 要求 :渗 碳 层 深度1 ~1 mm,硬度为5 ~5 HRC . 0 . 4 2 8 。其 工艺流 程 :下料 一冷挤压成形 一渗碳淬硬 ( 渗碳深度 1 . 0
~
1m . m,硬 度5 ~5H C)一机 加 工 一焊接 。 4 0 8R
所示 。为 了改变这种情况 ,我们改进装炉方式 ,采 用 人工排料 ,减少零件重 叠现 象 ,如 图5 所示 从
。 .
我 们认 为 , “ 表面预氧化+ 人工排放 ”可 以解
决一些渗层的均匀性 问题 ,提高一点渗速 ,但即使
延长工艺时间也不能满足技术要求。 ( )渗碳后重新加热淬盐水试验 将正常工艺 2 随意堆放 的零件 、正 常工艺人工排放的零件和延长
推杆球座渗碳淬硬工艺
一
汽解放公 司无锡柴 油机 厂 ( 江苏 2 4 2 ) 马静芬 冯雅 明 1 0 6
我厂2 钢推杆球座 ,一直选用爱协林 多用箱式 0 炉直接渗碳淬硬 ,但渗碳淬硬后往往深度偏浅 ,硬 度合格。即使延长工艺时间,返工率也较高 ,箱式 多用炉生产成本较高。
( )问题分析 针对推杆球座 (0 )返工率 3 2钢
.
1h 2
( )改 变装炉方式 2
原 装炉方式 是随意堆放
由表 1 可知 :人 工排料 比随意堆放渗碳 层深 度 深 ,预氧化温度提高 ̄ 4 o U 8 ℃,深度提高不明显 ,
采 取这 两 个措 施 都 不 能达 到 技 术要 求 。
的 ,零 件与零 件之 间有重叠 现象 ,不 利于 气体流 动 ,影 响渗碳速度和造成渗碳 层深浅不一 ,如 图4
中高碳钢成分及轧制工艺
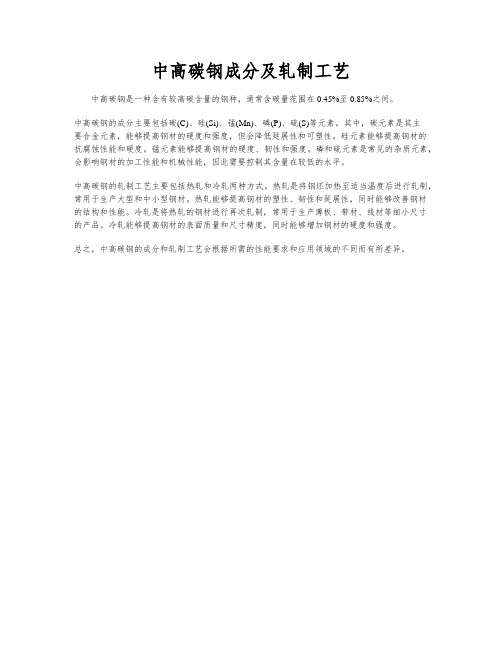
中高碳钢成分及轧制工艺
中高碳钢是一种含有较高碳含量的钢种,通常含碳量范围在0.45%至0.85%之间。
中高碳钢的成分主要包括碳(C)、硅(Si)、锰(Mn)、磷(P)、硫(S)等元素。
其中,碳元素是其主
要合金元素,能够提高钢材的硬度和强度,但会降低延展性和可塑性。
硅元素能够提高钢材的抗腐蚀性能和硬度。
锰元素能够提高钢材的硬度、韧性和强度。
磷和硫元素是常见的杂质元素,会影响钢材的加工性能和机械性能,因此需要控制其含量在较低的水平。
中高碳钢的轧制工艺主要包括热轧和冷轧两种方式。
热轧是将钢坯加热至适当温度后进行轧制,常用于生产大型和中小型钢材。
热轧能够提高钢材的塑性、韧性和延展性,同时能够改善钢材的结构和性能。
冷轧是将热轧的钢材进行再次轧制,常用于生产薄板、带材、线材等细小尺寸的产品。
冷轧能够提高钢材的表面质量和尺寸精度,同时能够增加钢材的硬度和强度。
总之,中高碳钢的成分和轧制工艺会根据所需的性能要求和应用领域的不同而有所差异。
碳五工艺流程
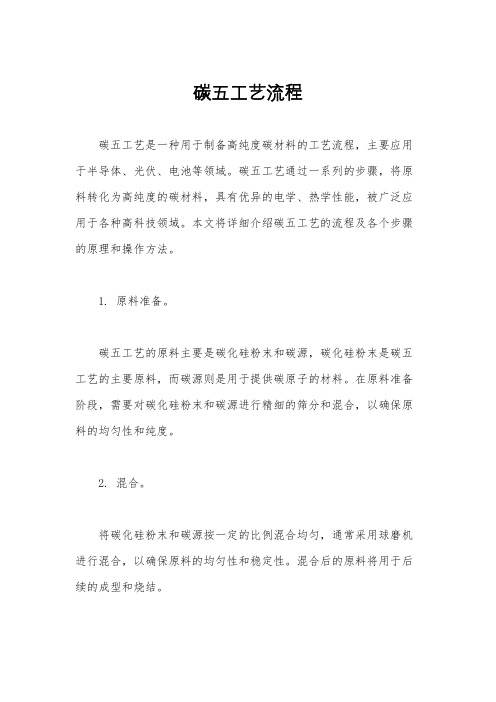
碳五工艺流程
碳五工艺是一种用于制备高纯度碳材料的工艺流程,主要应用于半导体、光伏、电池等领域。
碳五工艺通过一系列的步骤,将原料转化为高纯度的碳材料,具有优异的电学、热学性能,被广泛应用于各种高科技领域。
本文将详细介绍碳五工艺的流程及各个步骤的原理和操作方法。
1. 原料准备。
碳五工艺的原料主要是碳化硅粉末和碳源,碳化硅粉末是碳五工艺的主要原料,而碳源则是用于提供碳原子的材料。
在原料准备阶段,需要对碳化硅粉末和碳源进行精细的筛分和混合,以确保原料的均匀性和纯度。
2. 混合。
将碳化硅粉末和碳源按一定的比例混合均匀,通常采用球磨机进行混合,以确保原料的均匀性和稳定性。
混合后的原料将用于后续的成型和烧结。
3. 成型。
将混合后的原料进行成型,通常采用压制成型的方法,将原料压制成坯状。
成型后的坯状原料将用于后续的烧结工艺。
4. 烧结。
烧结是碳五工艺的关键步骤,通过高温烧结,使原料中的碳源与碳化硅粉末发生反应,生成高纯度的碳材料。
烧结过程需要严格控制温度、气氛和时间,以确保碳材料的纯度和稳定性。
5. 后处理。
经过烧结后,还需要对碳材料进行后处理,包括表面处理、尺寸加工等工艺,以满足不同应用领域的要求。
后处理工艺需要根据具体的应用需求进行设计和优化。
通过以上流程,碳五工艺可以制备出高纯度、高稳定性的碳材料,广泛应用于半导体、光伏、电池等领域。
碳五工艺的工艺流程复杂,需要严格控制各个步骤的工艺参数,以确保产品的质量和性能。
随着高科技产业的发展,碳五工艺将会有更广阔的应用前景。
异丁烯制高活性聚异丁烯工艺设计.doc
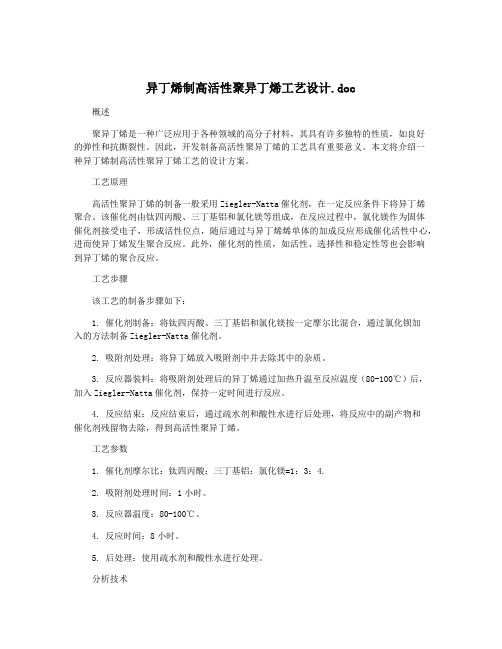
异丁烯制高活性聚异丁烯工艺设计.doc概述聚异丁烯是一种广泛应用于各种领域的高分子材料,其具有许多独特的性质,如良好的弹性和抗撕裂性。
因此,开发制备高活性聚异丁烯的工艺具有重要意义。
本文将介绍一种异丁烯制高活性聚异丁烯工艺的设计方案。
工艺原理高活性聚异丁烯的制备一般采用Ziegler-Natta催化剂,在一定反应条件下将异丁烯聚合。
该催化剂由钛四丙酸、三丁基铝和氯化镁等组成,在反应过程中,氯化镁作为固体催化剂接受电子,形成活性位点,随后通过与异丁烯烯单体的加成反应形成催化活性中心,进而使异丁烯发生聚合反应。
此外,催化剂的性质,如活性、选择性和稳定性等也会影响到异丁烯的聚合反应。
工艺步骤该工艺的制备步骤如下:1. 催化剂制备:将钛四丙酸、三丁基铝和氯化镁按一定摩尔比混合,通过氯化钡加入的方法制备Ziegler-Natta催化剂。
2. 吸附剂处理:将异丁烯放入吸附剂中并去除其中的杂质。
3. 反应器装料:将吸附剂处理后的异丁烯通过加热升温至反应温度(80-100℃)后,加入Ziegler-Natta催化剂,保持一定时间进行反应。
4. 反应结束:反应结束后,通过疏水剂和酸性水进行后处理,将反应中的副产物和催化剂残留物去除,得到高活性聚异丁烯。
工艺参数1. 催化剂摩尔比:钛四丙酸:三丁基铝:氯化镁=1:3:4.2. 吸附剂处理时间:1小时。
3. 反应器温度:80-100℃。
4. 反应时间:8小时。
5. 后处理:使用疏水剂和酸性水进行处理。
分析技术为了评价所制得的高活性聚异丁烯的性能,可以使用以下分析技术:1. 热重分析(TGA):可用于分析高活性聚异丁烯的热稳定性和失重率。
2. 红外光谱(FTIR):可用于分析高活性聚异丁烯的化学结构和官能团。
总结本文介绍了异丁烯制高活性聚异丁烯的工艺设计方案。
在该工艺中,采用Ziegler-Natta催化剂进行反应,通过对反应条件的控制可以制备出高活性聚异丁烯。
该工艺不仅具有成本低,易操作等优点,在制备高活性聚异丁烯方面也有着广泛的应用价值。
高质量高效率的热处理新技术——BH渗碳催渗技术

高质量高效率的热处理新技术——BH渗碳催渗技术
安峻岐
【期刊名称】《现代零部件》
【年(卷),期】2006()1
【总页数】3页(P65-67)
【关键词】技术;催渗;渗碳;热处理;高效率;质量;工业应用;碳氮共渗;工艺温度【作者】安峻岐
【作者单位】西安北恒热处理工程公司
【正文语种】中文
【中图分类】TG156.82;TG156.81
【相关文献】
1.BH催渗技术对渗碳螺旋伞齿轮组织和性能的影响 [J], 刘汾;彭竹琴;张太超
2.运用BH催渗技术解决齿轮渗碳变形 [J], 刘琼
3.BH催渗剂在齿轮轴渗碳中的应用 [J], 李家新;付云峰
4.运用BH催渗技术解决ZJ30钻机链条传动箱齿轮渗碳变形 [J], 刘琼
5.BH-2催渗剂在微机控制下的井式渗碳炉的应用 [J], 胡明发;张荣久
因版权原因,仅展示原文概要,查看原文内容请购买。
甲醇渗碳工艺
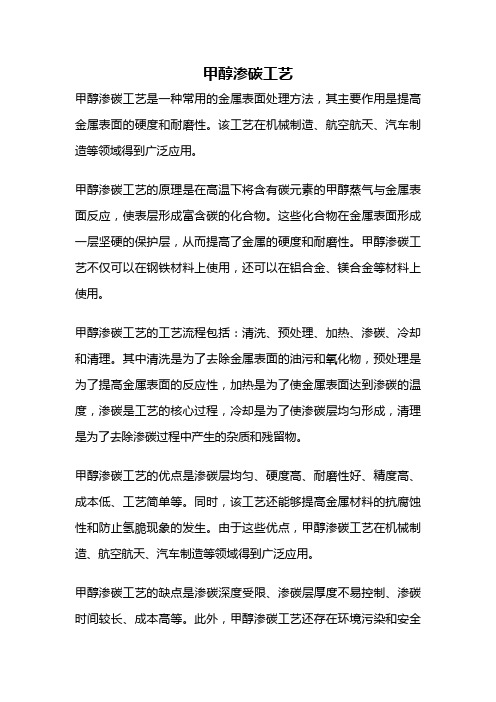
甲醇渗碳工艺
甲醇渗碳工艺是一种常用的金属表面处理方法,其主要作用是提高金属表面的硬度和耐磨性。
该工艺在机械制造、航空航天、汽车制造等领域得到广泛应用。
甲醇渗碳工艺的原理是在高温下将含有碳元素的甲醇蒸气与金属表面反应,使表层形成富含碳的化合物。
这些化合物在金属表面形成一层坚硬的保护层,从而提高了金属的硬度和耐磨性。
甲醇渗碳工艺不仅可以在钢铁材料上使用,还可以在铝合金、镁合金等材料上使用。
甲醇渗碳工艺的工艺流程包括:清洗、预处理、加热、渗碳、冷却和清理。
其中清洗是为了去除金属表面的油污和氧化物,预处理是为了提高金属表面的反应性,加热是为了使金属表面达到渗碳的温度,渗碳是工艺的核心过程,冷却是为了使渗碳层均匀形成,清理是为了去除渗碳过程中产生的杂质和残留物。
甲醇渗碳工艺的优点是渗碳层均匀、硬度高、耐磨性好、精度高、成本低、工艺简单等。
同时,该工艺还能够提高金属材料的抗腐蚀性和防止氢脆现象的发生。
由于这些优点,甲醇渗碳工艺在机械制造、航空航天、汽车制造等领域得到广泛应用。
甲醇渗碳工艺的缺点是渗碳深度受限、渗碳层厚度不易控制、渗碳时间较长、成本高等。
此外,甲醇渗碳工艺还存在环境污染和安全
隐患等问题。
因此,需要在工艺过程中加强环保和安全管理,减少污染和事故的发生。
甲醇渗碳工艺是一种常用的金属表面处理方法,其优点是渗碳层均匀、硬度高、耐磨性好、精度高、成本低、工艺简单等,但也存在一些缺点和问题。
在实际应用中,需要根据具体情况选择合适的工艺参数和管理措施,以确保工艺效果和安全环保。
- 1、下载文档前请自行甄别文档内容的完整性,平台不提供额外的编辑、内容补充、找答案等附加服务。
- 2、"仅部分预览"的文档,不可在线预览部分如存在完整性等问题,可反馈申请退款(可完整预览的文档不适用该条件!)。
- 3、如文档侵犯您的权益,请联系客服反馈,我们会尽快为您处理(人工客服工作时间:9:00-18:30)。
以领先科技强民族筋骨
BH 催渗技术
BH催渗技术是一项通过催化剂和配套工艺,实现低温、快速渗碳的新技术。
与常规渗碳技术相比,BH技术具有以下优点:
1.是一个高效、节能平台——在同样温度下提高渗速15%以上,投资收益率超过300%。
2.是一个变形控制平台——在温度降低40℃以上条件下渗速不减,可在820℃渗碳。
3.是一个工艺和质量控制平台:
1)可细化组织、显著减少内氧化和非马。
碳浓度梯度平缓。
2)气氛活性高、炭黑少、渗层均匀,无环境污染等不良现象。
自1997年以来BH技术已先后被法士特、株洲齿轮、洛阳轴承、瓦房店轴承、上海汽车等百余家企业率先采用;BH-2技术还是《中国热处理行业十五期间重点推广的节能和热处理质量控制技术》,其核心技术被列为《中华人民共和国国家机密级技术》,部分辅助技术获美、日、韩、欧盟、俄罗斯专利。
自1993年第1代BH技术进入生产以来,每5-8年我们都能研发一代新技术,目前第5代技术已经开始推广。
第6、7代技术3小时渗1.5~1.8mm、渗速成倍提高;相关的稳定、可靠性研究,预计还需要持续数年。
BH技术的主要突破点是通过催化剂,成功的突破了碳势对炭黑和碳化物的影响:
1)温度高:材料和变形难以控制;
2)碳势高:碳化物和炭黑难以控制;
温度和碳势是渗碳的主推动力:国内外很多人都尝试过高温、高碳势,但都因为以上问题难以突破,而告终;采用BH技术后:
1.催渗剂的催化功能可促使正四价碳离子的产生,平缓碳浓度梯度。
2.催渗剂的催化功能还可促使渗剂充分分解,抑制和减少了炭黑的形成(在同样温度和碳势
+0.2-0.3%条件下产生的炭黑仅和原工艺相当——详见《BH技术说明书》)。
碳黑和碳化物问题的解决,解决了长期困扰人们的技术难题(故采用BH催渗剂时我们应当采用高碳势工艺,这样才能充分发挥BH的技术优势),时任《国际热处理与表面工程联合会》主席Toten博士欣然题词:“BH技术是热处理技术发展史上的一项重大突破”(详见彩色宣传册)。
1。