热轧板凸度控制的探讨
热轧薄材板凸度控制
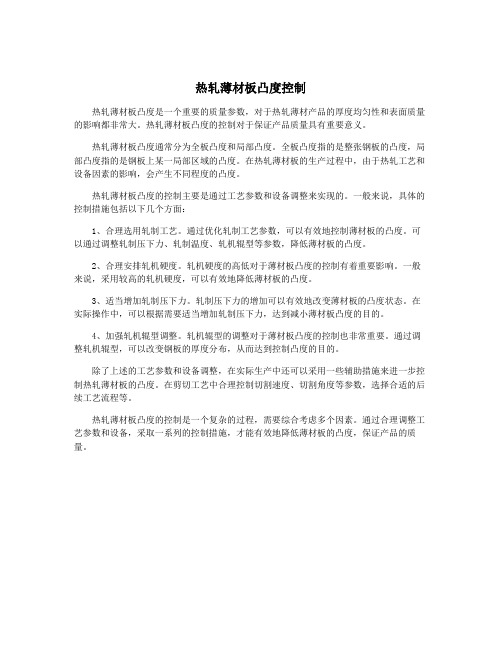
热轧薄材板凸度控制热轧薄材板凸度是一个重要的质量参数,对于热轧薄材产品的厚度均匀性和表面质量的影响都非常大。
热轧薄材板凸度的控制对于保证产品质量具有重要意义。
热轧薄材板凸度通常分为全板凸度和局部凸度。
全板凸度指的是整张钢板的凸度,局部凸度指的是钢板上某一局部区域的凸度。
在热轧薄材板的生产过程中,由于热轧工艺和设备因素的影响,会产生不同程度的凸度。
热轧薄材板凸度的控制主要是通过工艺参数和设备调整来实现的。
一般来说,具体的控制措施包括以下几个方面:1、合理选用轧制工艺。
通过优化轧制工艺参数,可以有效地控制薄材板的凸度。
可以通过调整轧制压下力、轧制温度、轧机辊型等参数,降低薄材板的凸度。
2、合理安排轧机硬度。
轧机硬度的高低对于薄材板凸度的控制有着重要影响。
一般来说,采用较高的轧机硬度,可以有效地降低薄材板的凸度。
3、适当增加轧制压下力。
轧制压下力的增加可以有效地改变薄材板的凸度状态。
在实际操作中,可以根据需要适当增加轧制压下力,达到减小薄材板凸度的目的。
4、加强轧机辊型调整。
轧机辊型的调整对于薄材板凸度的控制也非常重要。
通过调整轧机辊型,可以改变钢板的厚度分布,从而达到控制凸度的目的。
除了上述的工艺参数和设备调整,在实际生产中还可以采用一些辅助措施来进一步控制热轧薄材板的凸度。
在剪切工艺中合理控制切割速度、切割角度等参数,选择合适的后续工艺流程等。
热轧薄材板凸度的控制是一个复杂的过程,需要综合考虑多个因素。
通过合理调整工艺参数和设备,采取一系列的控制措施,才能有效地降低薄材板的凸度,保证产品的质量。
热轧薄材板凸度控制

热轧薄材板凸度控制热轧生产中,薄板的凸度控制是非常重要的一环。
由于热轧生产工艺复杂,薄板在生产过程中易发生弯曲、扭曲等凸度问题,会严重影响薄板的质量和生产效率。
因此,凸度的控制成为生产过程中必须注意的问题。
1. 凸度的含义及表现形式凸度(Crown)是指薄板断面沿箭头所示方向的弯曲曲率半径。
凸度又分为正凸度和负凸度,正凸度是指薄板从中央开始向两端逐步升高的情况,负凸度是指薄板从中央开始向两端逐步下降的情况。
薄板凸度的表现形式有以下几种:(1)中央凸起:指薄板在中央出现凸起的现象。
(2)端部下沉:指薄板两端出现向下凹陷的现象。
(3) S 形弯曲:指薄板出现 S 形弯曲的现象。
2. 凸度影响因素影响薄板凸度的因素非常多,主要有以下几点:(1)板形控制不当:板形控制不当会引起薄板内部张力分布不均,从而导致薄板出现弯曲和扭曲现象。
(2)薄板材料和尺寸:薄板的材料和尺寸对凸度的影响也很大。
例如,薄板的长度和宽度越大,凸度就越容易产生。
(3)温度控制:热轧生产过程中,高温时段的温度控制对薄板的凸度影响非常大。
3. 凸度控制方法为了控制薄板的凸度,可以采取以下方法:(1)优化板形控制:通过调整辊系的传动比,保证辊系的制动力均匀,优化板形控制,减少薄板内部张力分布不均,从而减少凸度的产生。
(2)采用适当的工艺措施:在热轧过程中,可以掌握好浇注和轧制技术,建立热轧生产记录,合理调整轧制工艺参数,减少薄板的凸度。
(3)加强温度控制:对于薄材的过渡卷,要严格控制加热炉温度,保证卷材的温度均匀,从而减少凸度的产生。
总之,控制凸度是热轧生产过程中非常重要的环节。
只有采取正确的控制手段,才能保证薄板的质量和生产效率。
热轧薄材板凸度控制

热轧薄材板凸度控制热轧薄材板凸度控制是钢铁生产过程中非常重要的一个环节。
凸度是指钢板在轧制过程中产生的弯曲程度,通过控制凸度可以确保薄材板的质量,提高产品的市场竞争力。
本文将详细介绍热轧薄材板凸度控制的原理、方法和常见问题。
一、凸度控制原理热轧薄材板在轧制过程中会受到各种因素的影响,如轧机调整、轧辊磨损、轧件温度和厚度等。
这些因素会影响到薄材板的形状,产生凸度。
凸度控制的目标就是通过调整这些因素,使薄材板的形状达到设计要求。
热轧薄材板凸度的控制原理可以简单地分为两个方面:1. 引起凸度的原因:轧辊形状、轧辊温度和轧制力的不均匀分布会导致薄材板产生凸度;2. 控制凸度的方法:通过调整轧制参数、轧辊形状、温度分布等,来控制薄材板的凸度。
二、凸度控制方法1. 调整轧制参数:热轧薄材板的轧制参数包括轧制速度、轧制力、轧辊间距等。
通过调整这些参数可以改变薄材板的形状,从而控制凸度。
增加轧制力可以使薄材板产生更大的弯曲程度,减小凸度;而减小轧制力可以减小凸度。
2. 控制轧辊形状:轧辊的形状对凸度有重要影响。
通过设计合理的轧辊形状,可以减小凸度。
常用的轧辊形状有带凸辊型、带凹辊型和摆式辊型等。
这些不同形状的轧辊可以产生不同的压力分布,从而实现凸度的控制。
3. 控制轧机温度:热轧薄材板的温度对凸度有很大影响。
通过控制轧机的温度,可以控制薄材板的冷却速度,从而影响凸度。
通常情况下,高温下凸度会减小,而低温下凸度会增大。
4. 轧后形状修正:有些情况下,调整轧制参数和轧辊形状等方法不能完全控制凸度,此时可以通过轧后形状修正来进行补偿。
常用的方法有轧后拉伸、轧后弯曲和轧后剪切等。
三、凸度控制常见问题及解决方法1. 出现凸度不符合要求的情况:可能是由于轧辊形状不合理、轧机参数设置错误或轧机温度控制不当等原因导致。
解决方法是重新设计合理的轧辊形状,调整轧机参数并正确控制轧机温度。
2. 出现凸度控制较难的情况:可能是由于轧材板厚度不均匀、轧机结构复杂或轧件材料柔软等原因导致。
热轧薄材板凸度控制
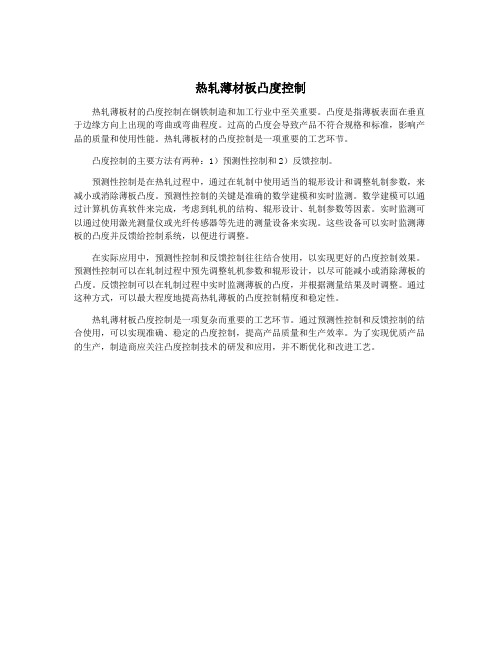
热轧薄材板凸度控制
热轧薄板材的凸度控制在钢铁制造和加工行业中至关重要。
凸度是指薄板表面在垂直于边缘方向上出现的弯曲或弯曲程度。
过高的凸度会导致产品不符合规格和标准,影响产品的质量和使用性能。
热轧薄板材的凸度控制是一项重要的工艺环节。
凸度控制的主要方法有两种:1)预测性控制和2)反馈控制。
预测性控制是在热轧过程中,通过在轧制中使用适当的辊形设计和调整轧制参数,来减小或消除薄板凸度。
预测性控制的关键是准确的数学建模和实时监测。
数学建模可以通过计算机仿真软件来完成,考虑到轧机的结构、辊形设计、轧制参数等因素。
实时监测可以通过使用激光测量仪或光纤传感器等先进的测量设备来实现。
这些设备可以实时监测薄板的凸度并反馈给控制系统,以便进行调整。
在实际应用中,预测性控制和反馈控制往往结合使用,以实现更好的凸度控制效果。
预测性控制可以在轧制过程中预先调整轧机参数和辊形设计,以尽可能减小或消除薄板的凸度。
反馈控制可以在轧制过程中实时监测薄板的凸度,并根据测量结果及时调整。
通过这种方式,可以最大程度地提高热轧薄板的凸度控制精度和稳定性。
热轧薄材板凸度控制是一项复杂而重要的工艺环节。
通过预测性控制和反馈控制的结合使用,可以实现准确、稳定的凸度控制,提高产品质量和生产效率。
为了实现优质产品的生产,制造商应关注凸度控制技术的研发和应用,并不断优化和改进工艺。
热轧板凸度控制研究

ti u in a d b ln e f r ec n r li i ih n l,a d t e p ro so h n e wo k—r l a d b c — r t n a a c o c o t o n f s i g mi b o n l n h e i d fc a g r ol n a k u o l r e e r h d f rt e d fe e tr q i t n o lt o v x t n h tr l d p o u t p r l we e r s a c e o h i r n e u s i fpa e c n e iy i o o l r d c .Th o — f io e ec n
维普资讯
第 2 3卷 第 2期 20 0 2年 6月
钢 铁
钒
钛
Vo . 3. . 1 2 NO 2
I RON TEE VANADI S L UM TANI M TI U
J n 0 u e2 02
热 轧 板 凸 度 控 制 研 究
楔 形 等缺 陷 的 出现 , 且 能 够 保 证 带 钢 平 直 度 。 因 而
2 热 轧 带钢 板 凸度 的影 响 因素
对 于热 轧成 品 而言 , 板 凸度 的 影 响因 素 有 : 其 轧 辊热 凸度 和 磨损 、 辊辊 形 配置 、 轧 负 荷 分 配 、 轧 精 弯
此 , 热轧 生 产 中 , 凸 度控 制 对确 保产 品实 物 质量 在 板 是极 其 重 要的 。
统 等影 响板 凸度 的各 类 因板 凸度 的 有效 控 制 。
板 凸度 又 称带 钢 横 向 厚 差 , 指板 带材 沿 宽度 方 向 是 的 厚度 差 ; 直 度 是指 板 带材 横 向 各 部 位是 否产 生 平 波 浪和 瓢 曲 。有 效 控制 带钢 板 凸度 不但 可 以防 止如
热轧薄材板凸度控制
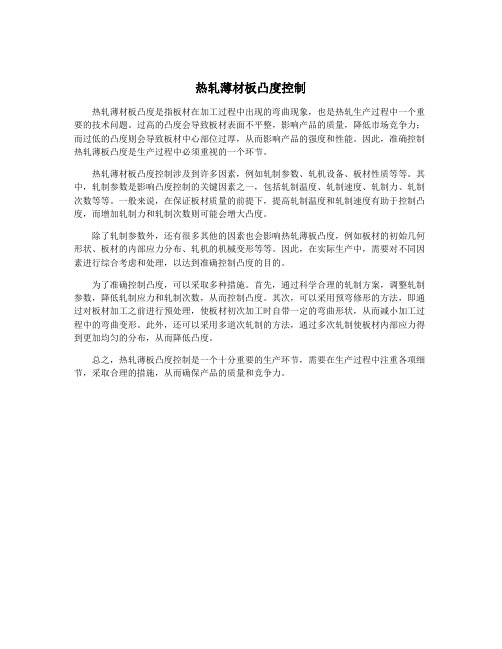
热轧薄材板凸度控制
热轧薄材板凸度是指板材在加工过程中出现的弯曲现象,也是热轧生产过程中一个重要的技术问题。
过高的凸度会导致板材表面不平整,影响产品的质量,降低市场竞争力;而过低的凸度则会导致板材中心部位过厚,从而影响产品的强度和性能。
因此,准确控制热轧薄板凸度是生产过程中必须重视的一个环节。
热轧薄材板凸度控制涉及到许多因素,例如轧制参数、轧机设备、板材性质等等。
其中,轧制参数是影响凸度控制的关键因素之一,包括轧制温度、轧制速度、轧制力、轧制次数等等。
一般来说,在保证板材质量的前提下,提高轧制温度和轧制速度有助于控制凸度,而增加轧制力和轧制次数则可能会增大凸度。
除了轧制参数外,还有很多其他的因素也会影响热轧薄板凸度,例如板材的初始几何形状、板材的内部应力分布、轧机的机械变形等等。
因此,在实际生产中,需要对不同因素进行综合考虑和处理,以达到准确控制凸度的目的。
为了准确控制凸度,可以采取多种措施。
首先,通过科学合理的轧制方案,调整轧制参数,降低轧制应力和轧制次数,从而控制凸度。
其次,可以采用预弯修形的方法,即通过对板材加工之前进行预处理,使板材初次加工时自带一定的弯曲形状,从而减小加工过程中的弯曲变形。
此外,还可以采用多道次轧制的方法,通过多次轧制使板材内部应力得到更加均匀的分布,从而降低凸度。
总之,热轧薄板凸度控制是一个十分重要的生产环节,需要在生产过程中注重各项细节,采取合理的措施,从而确保产品的质量和竞争力。
热轧薄材板凸度控制

热轧薄材板凸度控制随着现代工业的发展,热轧薄材板在工业生产中扮演着重要的角色。
热轧薄材板广泛应用于汽车制造、船舶建造、压力容器、航空航天等领域。
在生产过程中,热轧薄材板的凸度控制问题一直是制造商面临的难题。
凸度不仅影响了产品的质量,还会给生产带来额外的成本和麻烦。
研究和控制热轧薄材板凸度,对提高产品质量和生产效率具有非常重要的意义。
一、热轧薄材板凸度的形成原因热轧薄材板的凸度是指板材在加热、轧制和冷却过程中产生的一种弯曲形变。
其形成主要有以下几个原因:1.材料特性:热轧薄材板在轧制过程中,会受到温度和应力的影响,导致板材内部结构发生变化,从而产生弯曲形变。
2.轧机操作:轧机的工作状态和轧辊调整不当,会导致板材受到不均匀的挤压,从而形成凸度。
3.冷却过程:板材在冷却过程中,由于温度变化不均匀,会导致板材内部产生不同程度的收缩,进而产生凸度。
热轧薄材板的凸度一旦超出允许范围,就会对产品的质量造成严重影响。
凸度过大会导致板材塑性变形不均匀,严重影响板材的表面质量和力学性能,从而降低产品的使用价值。
如果凸度严重,还会增加生产成本,影响生产效率,降低企业的竞争力。
控制热轧薄材板凸度是非常重要的。
1.材料选择:选择合适的原材料是控制热轧薄材板凸度的第一步。
优质的原材料具有较好的塑性和韧性,能够在轧制过程中减小内部应力,并且易于形变,从而降低凸度的产生。
2.轧机调整:合理的轧机调整是控制热轧薄材板凸度的关键。
轧机的工作状态和轧辊的调整对板材形变有着直接的影响。
操作人员需要熟练掌握轧机的操作技巧,根据板材的材料和规格,合理调整轧机的工作参数,以减小凸度的产生。
3.冷却控制:冷却过程对热轧薄材板凸度也有着重要的影响。
要合理控制板材的冷却速度和温度分布,避免板材内部产生不均匀的收缩,减小凸度的产生。
通过以上几个方面的控制,可以有效减小热轧薄材板的凸度,提高产品的质量和生产效率。
具体的操作和控制还需要根据不同的板材材料和规格来进行调整,生产厂家可以根据实际情况进行合理的控制。
热轧薄材板凸度控制

热轧薄材板凸度控制一、热轧薄板的概念及特点热轧薄板是由钢厂在高温下经过轧制而成的一种金属板材,其厚度通常在3mm以下。
热轧薄板主要用于汽车制造、航空航天、建筑等领域,具有重量轻、强度高、成形性好等特点,因此在工业生产中得到了广泛应用。
热轧薄板的生产过程涉及多道工序,其中凸度控制是其中一个重要的环节。
凸度指的是板材在平整状态下的中间高于两端的高度差,也可以理解为板材在平整状态下的弯曲程度。
由于热轧薄板的产品特点和生产过程,其板材凸度控制显得尤为重要。
二、热轧薄板凸度控制的重要性1.质量标准要求热轧薄板产品通常需要符合一定的质量标准,包括凸度方面的要求。
凸度超标会影响产品的平整度和外观质量,不符合客户的使用要求。
2.生产成本控制凸度超标的板材通常需要进行后续的纠正处理,如预弯、修矫等,会增加生产成本。
而且凸度超标的板材在搬运、储存、运输等环节更容易造成损伤,增加了生产环节中的损耗和报废率。
3.产品应用要求热轧薄板作为汽车、航空航天等领域的零部件,对平整度和凸度要求非常高。
凸度超标可能导致该产品在后续的加工和装配中无法满足要求,影响产品的使用性能和安全性。
由此可见,热轧薄板的凸度控制对产品的质量、成本和应用性能都具有非常重要的意义。
三、热轧薄板凸度的影响因素1.原材料的影响原材料的宽度、厚度、材质等因素会直接影响到热轧薄板的凸度。
一般来说,原材料的质量越好,热轧薄板的凸度控制越容易。
2.轧制过程的影响轧制过程中的温度、压力、速度等参数的控制会直接影响到热轧薄板的凸度。
特别是在板坯的预弯、精轧等环节,对板材凸度的影响尤为显著。
3.设备和工艺的影响热轧薄板生产线的设备和工艺水平也会影响到板材的凸度。
如果设备的运转稳定性和精度不够,或者工艺参数的控制不到位,都会导致板材凸度的波动。
1.优化轧制工艺2.加强设备维护保证热轧薄板生产线设备的运转稳定性和精度,减少因设备原因导致的板材凸度超标问题。
3.严格原材料管理对原材料的尺寸、质量等进行严格把控,减少原材料因素对板材凸度的影响。
热轧板凸度控制的探讨

热轧板凸度控制的探讨陈 勇(新疆钢铁研究所)摘 要: 阐述了凸度与平直度的关系及凸度控制的策略,指出对板凸度影响的各种因素,并探讨控制各因素影响的措施。
关键词: 热轧板;凸度;平直度;控制1 前言板形是衡量板带产品质量重要的指标之一,板形包括板凸度、平直度和边部形状等。
目前热轧产品主要分为供冷轧原料和商品板卷,这两类产品对板凸度要求存在一定差别,为了便于带钢咬入,保证冷轧穿带过程稳定,一般冷轧料需要80~90μm的板凸度,而商品板卷的用户出于节约材料、降低成本的考虑,一般要求板凸度越小越好。
热轧精轧机组板形控制有两个目标:一是保证成品机架的出口带钢具有理想的凸度;二是保证带钢的平直度。
结合八钢热轧1750mm的工装情况阐述凸度与平直度的关系,介绍板凸度的控制方法,对轧辊热膨胀、轧辊磨损、轧制力、弯辊力等对板凸度的影响进行分析。
2 八钢热轧项目的主要设备及技术参数八钢1750mm热轧机组设计采用传统的半连续轧机,一期主要设备:步进式加热炉两座,粗轧+立辊轧机一架,热卷箱,6机架精轧,层流冷却,两个具有AJC功能的卷曲机,在F6后有宽度仪、厚度仪、凸度仪、平直度仪等检测仪器。
表1 轧机部分的主要技术参数名 称技术参数立辊轧机(E M)附着式上部驱动具有AWC和S CC功能四辊粗轧机(R M)四辊可逆式双传动F1~F6精轧机(F M)四辊全液压不可逆轧机AGC控制精轧工作辊弯辊系统(WRB) F1~F4 1500k N/侧正弯辊力: F5~F6 1100k N/侧精轧工作辊窜辊系统(WRS)移动行程: ±125mm3 板凸度与平直度关系3.1 凸度和相对凸度的表示方法带钢板凸度用C40指标表示,计算公式如下:板凸度:δi=[H i m-(H io+H id)/2]×1000(1)相对凸度:δi X=2δi/(H i0+H id)(2) 式中,δi 为第i机架出口板凸度;Hi m为第i机架出口带钢中部厚度;Hio为第i机架出口带钢操作侧距带钢边部40mm处厚度;Hid为第i机架出口带钢传动侧距带钢边部40mm处厚度;δiX为第i机架出口板相对凸度(%)。
热轧薄材板凸度控制
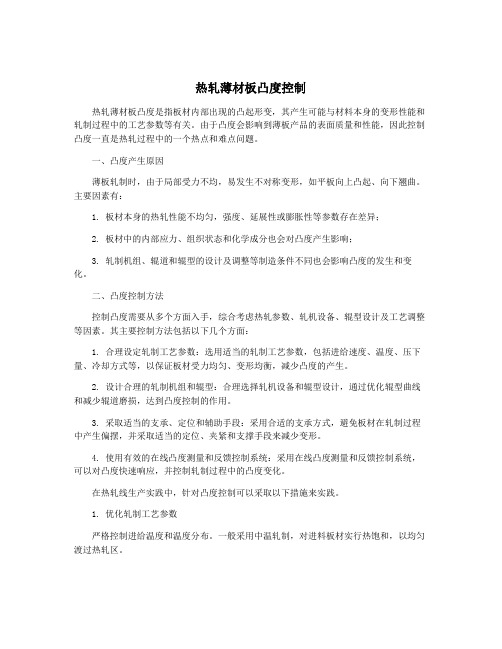
热轧薄材板凸度控制热轧薄材板凸度是指板材内部出现的凸起形变,其产生可能与材料本身的变形性能和轧制过程中的工艺参数等有关。
由于凸度会影响到薄板产品的表面质量和性能,因此控制凸度一直是热轧过程中的一个热点和难点问题。
一、凸度产生原因薄板轧制时,由于局部受力不均,易发生不对称变形,如平板向上凸起、向下翘曲。
主要因素有:1. 板材本身的热轧性能不均匀,强度、延展性或膨胀性等参数存在差异;2. 板材中的内部应力、组织状态和化学成分也会对凸度产生影响;3. 轧制机组、辊道和辊型的设计及调整等制造条件不同也会影响凸度的发生和变化。
二、凸度控制方法控制凸度需要从多个方面入手,综合考虑热轧参数、轧机设备、辊型设计及工艺调整等因素。
其主要控制方法包括以下几个方面:1. 合理设定轧制工艺参数:选用适当的轧制工艺参数,包括进给速度、温度、压下量、冷却方式等,以保证板材受力均匀、变形均衡,减少凸度的产生。
2. 设计合理的轧制机组和辊型:合理选择轧机设备和辊型设计,通过优化辊型曲线和减少辊道磨损,达到凸度控制的作用。
3. 采取适当的支承、定位和辅助手段:采用合适的支承方式,避免板材在轧制过程中产生偏摆,并采取适当的定位、夹紧和支撑手段来减少变形。
4. 使用有效的在线凸度测量和反馈控制系统:采用在线凸度测量和反馈控制系统,可以对凸度快速响应,并控制轧制过程中的凸度变化。
在热轧线生产实践中,针对凸度控制可以采取以下措施来实践。
1. 优化轧制工艺参数严格控制进给温度和温度分布。
一般采用中温轧制,对进料板材实行热饱和,以均匀渡过热轧区。
优化轧制方案,降低轧制压下量。
对于厚度较薄的轧制板,保证轧制压下量不宜过大,以减轻板材变形度。
2. 优化辊型设计采用合理的辊型参数,如合理张开力、辊压和中间凸度等,可以有效控制板材的变形和凸度。
针对一些式样普遍的轧机,比如四辊轧机和三辊轧机,研究其参数和使用条件,了解其特点和局限性,以优化辊型设计,减少板材变形和凸度。
热轧钢产品的测厚仪与凸度控制

热轧钢产品的测厚仪与凸度控制【关键词】热轧钢;质量控制;测厚仪;凸度控制随着现代化建设进程的加快,钢产品的用途广泛,从国防、交通建设到精密仪器制造,对钢产品的材料强度和产品规格要求日趋提高。
由于钢板轧制与定尺长度的增加、厚度同板差的减小、厚度公差范围的缩小、异形板轧制及钢板平直度控制的需要,对厚度自动控制和凸度控制越来越重视,已成为现代化中厚板轧机必不可少的重要手段。
一.热轧钢产品的精度检测以热轧钢为例,许多热轧中厚板车间都有相应的在线测厚装置,如产品厚度仅仅依靠人工定时检测不能做到及时测量就谈不上厚度控制,产品厚度尺寸波动极大,更不能检测产品凸度,使客户得不到凸度较小且恒定的热轧成品。
据了解一方面缘于射线测厚有一定危险,现场不愿使用,另一方面价格昂贵且装置防护系统比较复杂。
曾经有人认为800mm以上宽带才安装凸度检测,实际上现场500mm宽带已经有3点式测量,直接获知板凸度,这可为中宽带钢凸度控制提供参考,对稳定产品质量具有重要意义。
热轧除了有激光测厚测宽仪还有γ测厚仪,它是应用射线穿透被测材料时,γ射线的强度的变化与材料的厚度相关的特性,从而测定材料的厚度,是一种非接触式的动态计量仪器。
它以PLC和工业计算机为核心,采集计算数据并输出目标偏差值给轧机厚度控制系统,达到要求的轧制厚度。
为轧钢生产带来方便。
目前激光测厚精度还不如射线测厚,通常使用的有γ测厚仪,它是利用γ射线穿透特性的放射性厚度计,但钢板横截面上的相对厚度还是可以比较。
二、热轧钢的厚度高精度控制随着现代工程和机械等精度的高度要求,对热轧钢产品也提出了较高的要求,主要体现在厚度和凸度的精密控制。
除了要求热轧钢机床的精准,还对钢产品的检测提出了严格的要求。
电动压下高出6倍,精度也大大高于电动压下螺丝。
在带钢精轧机成品架安装液压缸,可以实现PM-AGC快速辊縫调整。
如果与成品前架压力传感器配合,可以实现压力测厚计的前馈控制。
1.无活套微张力轧制活套支撑器用来反映机架间张力水平,但在厚坯轧制时耗能很高,在成品机架又反应不够快,限制了板厚精度的进一步提高。
热轧薄材板凸度控制
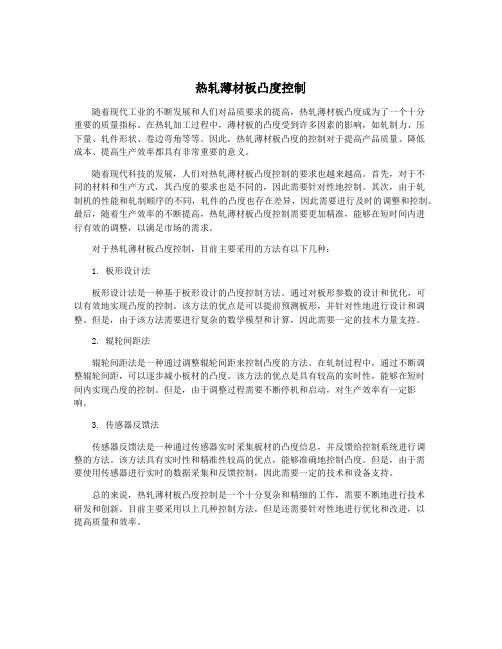
热轧薄材板凸度控制随着现代工业的不断发展和人们对品质要求的提高,热轧薄材板凸度成为了一个十分重要的质量指标。
在热轧加工过程中,薄材板的凸度受到许多因素的影响,如轧制力、压下量、轧件形状、卷边弯角等等。
因此,热轧薄材板凸度的控制对于提高产品质量、降低成本、提高生产效率都具有非常重要的意义。
随着现代科技的发展,人们对热轧薄材板凸度控制的要求也越来越高。
首先,对于不同的材料和生产方式,其凸度的要求也是不同的,因此需要针对性地控制。
其次,由于轧制机的性能和轧制顺序的不同,轧件的凸度也存在差异,因此需要进行及时的调整和控制。
最后,随着生产效率的不断提高,热轧薄材板凸度控制需要更加精准,能够在短时间内进行有效的调整,以满足市场的需求。
对于热轧薄材板凸度控制,目前主要采用的方法有以下几种:1. 板形设计法板形设计法是一种基于板形设计的凸度控制方法。
通过对板形参数的设计和优化,可以有效地实现凸度的控制。
该方法的优点是可以提前预测板形,并针对性地进行设计和调整。
但是,由于该方法需要进行复杂的数学模型和计算,因此需要一定的技术力量支持。
2. 辊轮间距法辊轮间距法是一种通过调整辊轮间距来控制凸度的方法。
在轧制过程中,通过不断调整辊轮间距,可以逐步减小板材的凸度。
该方法的优点是具有较高的实时性,能够在短时间内实现凸度的控制。
但是,由于调整过程需要不断停机和启动,对生产效率有一定影响。
3. 传感器反馈法传感器反馈法是一种通过传感器实时采集板材的凸度信息,并反馈给控制系统进行调整的方法。
该方法具有实时性和精准性较高的优点,能够准确地控制凸度。
但是,由于需要使用传感器进行实时的数据采集和反馈控制,因此需要一定的技术和设备支持。
总的来说,热轧薄材板凸度控制是一个十分复杂和精细的工作,需要不断地进行技术研发和创新。
目前主要采用以上几种控制方法,但是还需要针对性地进行优化和改进,以提高质量和效率。
热轧薄材板凸度控制
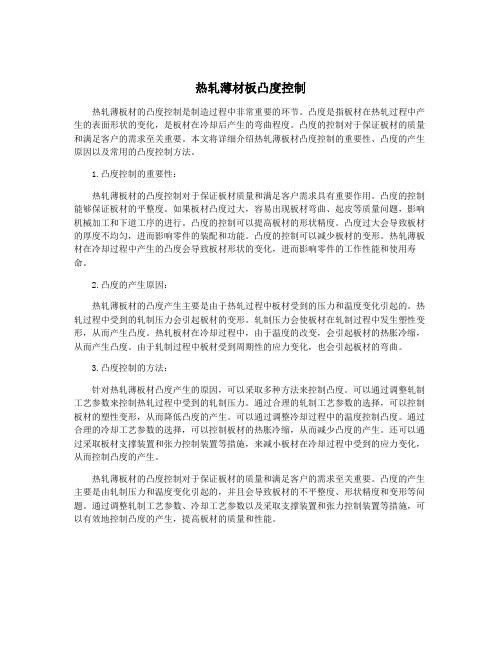
热轧薄材板凸度控制热轧薄板材的凸度控制是制造过程中非常重要的环节。
凸度是指板材在热轧过程中产生的表面形状的变化,是板材在冷却后产生的弯曲程度。
凸度的控制对于保证板材的质量和满足客户的需求至关重要。
本文将详细介绍热轧薄板材凸度控制的重要性、凸度的产生原因以及常用的凸度控制方法。
1.凸度控制的重要性:热轧薄板材的凸度控制对于保证板材质量和满足客户需求具有重要作用。
凸度的控制能够保证板材的平整度。
如果板材凸度过大,容易出现板材弯曲、起皮等质量问题,影响机械加工和下道工序的进行。
凸度的控制可以提高板材的形状精度。
凸度过大会导致板材的厚度不均匀,进而影响零件的装配和功能。
凸度的控制可以减少板材的变形。
热轧薄板材在冷却过程中产生的凸度会导致板材形状的变化,进而影响零件的工作性能和使用寿命。
2.凸度的产生原因:热轧薄板材的凸度产生主要是由于热轧过程中板材受到的压力和温度变化引起的。
热轧过程中受到的轧制压力会引起板材的变形。
轧制压力会使板材在轧制过程中发生塑性变形,从而产生凸度。
热轧板材在冷却过程中,由于温度的改变,会引起板材的热胀冷缩,从而产生凸度。
由于轧制过程中板材受到周期性的应力变化,也会引起板材的弯曲。
3.凸度控制的方法:针对热轧薄板材凸度产生的原因,可以采取多种方法来控制凸度。
可以通过调整轧制工艺参数来控制热轧过程中受到的轧制压力。
通过合理的轧制工艺参数的选择,可以控制板材的塑性变形,从而降低凸度的产生。
可以通过调整冷却过程中的温度控制凸度。
通过合理的冷却工艺参数的选择,可以控制板材的热胀冷缩,从而减少凸度的产生。
还可以通过采取板材支撑装置和张力控制装置等措施,来减小板材在冷却过程中受到的应力变化,从而控制凸度的产生。
热轧薄板材的凸度控制对于保证板材的质量和满足客户的需求至关重要。
凸度的产生主要是由轧制压力和温度变化引起的,并且会导致板材的不平整度、形状精度和变形等问题。
通过调整轧制工艺参数、冷却工艺参数以及采取支撑装置和张力控制装置等措施,可以有效地控制凸度的产生,提高板材的质量和性能。
热轧薄材板凸度控制

热轧薄材板凸度控制热轧薄材板凸度控制是一项关键的加工过程,是确保制造出符合要求的板材的重要环节。
凸度是指板材在垂直于其表面的平面上,由于材料内部的应力分布不均匀而产生的曲率。
对于一些特殊的应用,板材的凸度控制要求非常严格,因此需要采取相应的控制措施。
热轧薄材板凸度的产生主要有三个方面的原因:材料原有的应力、加工过程中的应力和板材的形状设计。
材料原有的应力指的是在材料的加工前就存在的应力,这些应力来源于材料的生产和贮存过程中的各种因素。
在热轧过程中,由于板材在高温下受到了较大的变形,所以会产生一些应力,这些应力可能会导致板材产生凸度。
板材的形状设计也会对其凸度产生影响,如果板材的设计不合理,很容易导致板材产生凸度。
为了控制热轧薄材板的凸度,可以采取以下措施:1. 选用适当的材料:在热轧薄材板加工过程中,选择合适的材料对于凸度控制非常重要。
一些材料具有较低的热膨胀系数和较高的抗应力松弛能力,这些特性能够降低板材的应力分布差异,减少凸度的产生。
2. 控制热轧参数:热轧过程中的一些参数对于凸度控制也有重要的影响。
热轧温度、轧制力度、轧制速度等都是需要合理控制的参数。
合理控制这些参数可以调整板材的形变和应力分布,从而减小凸度的产生。
3. 优化板材的形状设计:板材的形状设计对于凸度的控制也非常重要。
合理的形状设计可以减小板材加工过程中的形变和应力分布差异,从而降低板材的凸度。
4. 加工过程中的应力释放:在热轧过程中,应力释放是非常重要的一步。
通过对板材进行退火等处理,可以释放材料内部的应力,减小凸度的产生。
热轧薄材板凸度的控制是一项复杂的工程,需要综合考虑材料、工艺和设计等因素。
只有找到合适的方法,并加以合理的控制,才能更好地控制板材的凸度,制造出高质量的产品。
热轧薄材板凸度控制

热轧薄材板凸度控制热轧薄材板是一种广泛应用于各种行业的材料,在生产过程中,由于各种原因,可能会出现凸度问题。
凸度是指材料在轧制过程中弯曲形成的形状不平整现象。
控制热轧薄材板的凸度对于保证产品质量和提高生产效率具有重要意义。
本文将从凸度的原因分析和控制方法两个方面进行探讨。
一、凸度的原因分析1. 板材材质问题热轧薄材板的材质是影响凸度的一个重要因素。
不同材质的板材具有不同的塑性变形特性,某些材质在轧制过程中容易产生弯曲变形,从而引起凸度问题。
2. 过大的轧制压力热轧薄材板的凸度问题还与轧制过程中施加的压力有关。
如果轧制压力过大,容易使材料发生过度塑性变形,从而导致严重的弯曲形变。
3. 不合理的轧制工艺参数轧制工艺参数的选择也会对凸度产生影响。
过大的轧制温度和过大的轧制速度等因素都会使凸度加剧。
4. 不均匀的冷却热轧薄材板在轧制之后要进行冷却,如果冷却不均匀,也会导致板材不平整,产生凸度。
二、凸度的控制方法1. 合理选择材质在生产中选择适合的材质也是减少凸度的重要方法。
根据产品的要求和各种材质的特性,选择合适的材质以减少凸度的产生。
2. 控制轧制压力合理选择轧制压力,避免过大的压力产生。
通过控制轧制力度,减少弯曲形变,降低凸度的产生。
3. 调整轧制工艺参数通过合理选择轧制温度、轧制速度、轧制道次等参数来减小板材的凸度。
降低轧制温度和速度,合理调整轧制道次,能有效控制凸度的产生。
4. 均匀冷却在轧制之后要进行均匀的冷却,避免冷却不均匀引起的凸度问题。
可以采用喷淋冷却、风冷等方法来保证板材的均匀冷却,从而降低凸度的产生。
5. 增加工艺监控引入先进的自动化设备和监控系统,对热轧薄材板的生产过程进行实时监控和控制,及时发现和纠正产生凸度的问题,提高生产效率。
热轧薄材板的凸度控制是生产过程中需要重视的一个问题。
通过分析凸度的产生原因,并采取相应的控制措施,可以有效降低凸度的出现,并提高产品的质量和生产效率。
热轧薄材板凸度控制

热轧薄材板凸度控制热轧薄材板的凸度是指钢板在经过轧制过程后的形变程度,是评估钢板质量的重要指标之一。
凸度的大小直接影响到钢板的平整度和形状稳定性,因此凸度控制是热轧薄材板生产过程中的一项重要工作。
热轧薄材板的凸度控制既涉及到轧机设备的优化,也需要依靠有效的工艺措施。
下面将从轧机设备和工艺措施两个方面来介绍热轧薄材板的凸度控制方法。
首先是轧机设备方面。
一般来说,凸度控制主要通过轧机辊位的组合和凸度控制系统的调整来实现。
辊位的组合是凸度控制的关键之一。
辊位的选择要根据钢板的厚度、宽度和材质等参数来进行合理搭配。
通常会采用对称辊位组合,即在辊位的两侧设置相同直径的辊子,这样可以使钢板在轧制过程中得到均匀的变形,减小凸度产生的可能性。
合理选择辊位的排列顺序和角度也是凸度控制的关键之一。
凸度控制系统的调整是另一个重要环节。
辊位的线速度差、辊位的侧压力等参数的调整都会影响到钢板的凸度。
一般来说,通过减小辊位的线速度差和增加辊位的侧压力可以有效降低凸度。
还可以通过调整辊位的温度、注润滑液的压力和温度等参数来控制凸度。
首先是在轧制过程中进行有效的冷却措施。
钢板在经过轧制后会处于高温状态,如果不能及时冷却,会导致钢板的变形加剧,进而产生凸度。
在轧制过程中需要对钢板进行有效的冷却,可以采用喷水冷却、冷却辊等措施。
其次是合理控制轧制参数。
轧制参数包括轧制速度、轧制力等。
通过合理调整这些参数,可以降低钢板的变形程度,从而减小凸度的产生。
最后是适当增加轧制次数。
在质量要求较高的情况下,可以适当增加轧制次数,使钢板得到更加均匀的变形,从而降低凸度。
热轧薄材板的凸度控制是一个复杂的工艺过程,需要通过轧机设备的优化和合理的工艺措施来共同实现。
只有在轧制过程中严格控制凸度,才能保证热轧薄材板的质量,并满足不同领域的应用需求。
热轧薄材板凸度控制

热轧薄材板凸度控制
热轧薄材板的凸度控制是制定热轧工艺参数和采取相应措施,以减小热轧薄材板在轧
制过程中产生的凸度偏差,使得轧制后的薄材板具有优良的平整性。
热轧薄材板的凸度主要有正凸度和负凸度两种情况。
正凸度指薄材板的中心部位高于
两侧的情况,负凸度则相反,中心低于两侧。
凸度的产生主要是由于热轧过程中的热变形
和内部应力的释放造成的。
在热轧过程中控制凸度是非常重要的。
在热轧薄材板的凸度控制过程中,有以下几个关键环节需要注意:
1. 热轧温度控制:适当控制热轧温度可以减小凸度的产生。
由于薄材板的热变形比
较大,所以在热轧过程中温度的变化会引起凸度的变化。
合理的热轧温度有助于减小凸度
的产生,提高薄材板的平整性。
2. 轧机辊型控制:辊型的选择和调整对于减小凸度也起到了重要的作用。
辊型的设
计应符合轧机产生的应力和变形规律,能够尽量减小薄材板的凸度。
在热轧过程中,及时
调整辊型的参数,也能够有效减小凸度的产生。
3. 轧制过程参数控制:热轧薄材板凸度的产生与轧制过程中的轧制力、轧制速度、
轧制间隙等参数有关。
合理控制这些参数,可以减小凸度的产生。
一般来说,增大轧制力,适当加大轧制速度,减小轧制间隙,都能够减小薄材板的凸度。
4. 回火工艺控制:轧制后的薄材板需要进行回火处理,以消除内部应力,进一步减
小凸度。
回火工艺的控制包括回火温度、回火时间和冷却速率等。
合理的回火工艺有助于
提高薄材板的平整性。
热轧板带凸度影响因素的敏感性分析

· 282 ·区域治理综合信息热轧板带凸度影响因素的敏感性分析程斌河钢集团邯钢邯宝热轧厂,河北 邯郸 056003摘要:本文通过基于支持向量机方法,针对热轧工艺生产过程中的板带凸度进行影响因素敏感性分析。
采用支持向量机建立工艺参数与板带凸度的关系模型,获得影响板带凸度的关键因素,敏感性分析方法可以准确定位关键因素,为实现热轧过程中的生产控制提供指导。
关键词:热轧板带;凸度;敏感因素板带凸度是描述板带横截面形状的主要指标之一,一方面反映了板带在生产过程中的横向板厚差,另一方面直接影响板带的板形状态和辊形调控目标,对生产过程的稳定和产品质量的控制有决定性作用。
一、影响热轧板带凸度的因素随着对热轧带材性能的需求不断增加,改进轧制控制模型以提高控制精度的需求变得越来越迫切。
随着传感技术,控制技术和数据库技术的发展,现代生产企业已经产生了大量的实际生产数据,并利用数据分析方法获取生产经验,改变传统的手工经验,了解生产过程。
为了更好地理解控制变量,测量变量和其他因素对轧制过程中钢带性能的影响,钢带的凸度由负荷辊缝的形状和影响钢筋形状的所有因素决定。
负载辊缝会影响板的形状。
这些影响因素可归因于两个方面:内部因素(金属性质)和外部因素(轧制条件)。
金属本身的物理性质(例如硬化性能和抗变形性)直接影响轧制力,因此与带材的冠部密切相关。
金属的几何特征,特别是带材的纵横比,以及入口带的凸度是影响带材冠部的另一个重要因素;轧制条件的影响更加复杂,轧辊的顶部直接构成初始轧辊间隙形状。
轧制过程中轧制压力分布的变化对轧辊变形和轧辊间隙有很大影响。
本文主要介绍以下影响因素。
1板凸度作为板形横向典型指标的板凸度和纵向典型指标的板平直度之间的关系密切 ,板平直度的控制最终还要归结到板凸度的控制上 ,如何控制好板凸度是解决板形控制问题的关键为获得良好板形要求带钢横向有均一的延伸,带钢的轧前与轧后断面各处尺寸比例恒定 ,即良好板形条件为带材轧前比例凸度必须等于轧后比例凸度。
热轧薄材板凸度控制

热轧薄材板凸度控制热轧薄材板的凸度控制是针对热轧过程中产生的板材凸度问题进行的一项重要工作。
薄材板的凸度是指板材在热轧过程中在板材宽度方向上的弯曲程度,通常以凸度值表示。
凸度控制的目的是保持最小的凸度,使得板材成品平整度高、尺寸稳定。
控制热轧薄材板的凸度需要从两个方面进行,一方面是要掌握好热轧过程中的工艺参数,另一方面是对轧机设备的性能进行合理的设计和改进。
首先是控制好热轧过程中的工艺参数。
热轧工艺参数的选择对薄材板的凸度影响非常大。
首先是控制好轧制力和回火温度。
热轧过程中的轧制力过大或过小都会导致板材的凸度过大,因此要根据板材的性质和要求选择合适的轧制力;回火温度也会影响板材的凸度,回火温度过高会导致板材回火脆性增加,凸度也会增大。
其次是控制好的板坯温度和轧制温度。
板坯温度过高或过低都会导致板材的凸度过大,因此要根据板材的性质和要求选择合适的板坯温度;轧制温度的选择也很重要,过高的轧制温度会导致板材的塑性变差,凸度也会增大。
选择合适的轧矫方法也是控制板材凸度的关键,不同的轧矫方法对凸度的控制效果也不同。
其次是对轧机设备的性能进行合理的设计和改进。
轧机设备的性能对热轧薄材板的凸度控制有着很大影响。
首先是轧机的结构设计,合理的轧机结构设计可以减小板材的凸度。
采用弯辊、双辊和辊圈倾轧等技术可以有效减小板材的凸度。
其次是对轧机辊的材料和制造工艺进行优化。
轧机辊是热轧过程中与板材直接接触并施加力的部件,轧机辊的材料和制造工艺的优化可以有效地减小板材的凸度。
采用高硬度的轧机辊可以减小板材的凸度。
热轧薄材板凸度控制是一项复杂而重要的工作。
要控制好板材的凸度,需要从工艺参数的控制和轧机设备的设计和改进两个方面进行。
只有在工艺参数和设备性能都经过合理的设计和优化的情况下,才能够实现对热轧薄材板凸度的有效控制。
热轧板凸度控制研究

! 26 !
钢铁钒钛
2002 年第 23 卷
图 4 支承辊下机后的典型辊 形
剥落的情况 , 减小了 F 4~ F6 支承辊的轧制量, 调整 支承辊换辊方式 : 在两次换 F1~ F 3 支承辊 中间加 一到两次换 F4~ F6 支承辊, 以减小 F 4~ F6 支承辊 磨损后对带钢板凸度的影响。 支承辊辊形配置优化 后, 从开卷取样的数据来看, 板凸度得到了进一步的 控制 。 4. 2 精轧工作辊辊形配置对带钢板凸度的影响 在精轧支承辊辊形配置优化后, 必须对工作辊 辊形进行合理的配置 , 才能保证板凸度的良好控制 , 在确定各机架工作辊辊型大小时 , 主要考虑的影响 因素有 : 精轧机支承辊在各使用时期内的磨损形状 及磨损程度; 不同机架精轧机工作辊的热凸度分布 ; 辊型磨削应方便生产现场的管理。 根据支承辊的磨 损程度, 可把其使用周期分为前期 、 中期 、 末期 , 支承 辊不同时期内, 工作辊辊形采用相应的配置。
1
引言
板形是衡量板带产品质量最重要的指标之一 ,
衡量板形好坏通常的两个指标是板凸度和平直度 。 板凸度又称带钢横向厚差, 是指板带材沿宽度方向 的厚度差; 平直度是指板带材横向各部位是否产生 波浪和瓢曲。有效控制带钢板凸度不但可以防止如 楔形等缺陷的出现, 而且能够保证带钢平直度 。 因 此, 在热轧生产中, 板凸度控制对确保产品实物质量 是极其重要的。 攀钢热轧板厂自 1992 年投产以来 , 由于原设计 未考虑板形控制手段, 故板凸度控制精度和稳定性 难以得到保证。 为进一步提高产量和质量, 热轧板 厂随后进行了两次 大规模的技术 改造。 一期 改造 中, 在精轧 F1~ F 6 机架安装了最基础的板 形控制
- 1、下载文档前请自行甄别文档内容的完整性,平台不提供额外的编辑、内容补充、找答案等附加服务。
- 2、"仅部分预览"的文档,不可在线预览部分如存在完整性等问题,可反馈申请退款(可完整预览的文档不适用该条件!)。
- 3、如文档侵犯您的权益,请联系客服反馈,我们会尽快为您处理(人工客服工作时间:9:00-18:30)。
热轧板凸度控制的探讨陈 勇(新疆钢铁研究所)摘 要: 阐述了凸度与平直度的关系及凸度控制的策略,指出对板凸度影响的各种因素,并探讨控制各因素影响的措施。
关键词: 热轧板;凸度;平直度;控制1 前言板形是衡量板带产品质量重要的指标之一,板形包括板凸度、平直度和边部形状等。
目前热轧产品主要分为供冷轧原料和商品板卷,这两类产品对板凸度要求存在一定差别,为了便于带钢咬入,保证冷轧穿带过程稳定,一般冷轧料需要80~90μm的板凸度,而商品板卷的用户出于节约材料、降低成本的考虑,一般要求板凸度越小越好。
热轧精轧机组板形控制有两个目标:一是保证成品机架的出口带钢具有理想的凸度;二是保证带钢的平直度。
结合八钢热轧1750mm的工装情况阐述凸度与平直度的关系,介绍板凸度的控制方法,对轧辊热膨胀、轧辊磨损、轧制力、弯辊力等对板凸度的影响进行分析。
2 八钢热轧项目的主要设备及技术参数八钢1750mm热轧机组设计采用传统的半连续轧机,一期主要设备:步进式加热炉两座,粗轧+立辊轧机一架,热卷箱,6机架精轧,层流冷却,两个具有AJC功能的卷曲机,在F6后有宽度仪、厚度仪、凸度仪、平直度仪等检测仪器。
表1 轧机部分的主要技术参数名 称技术参数立辊轧机(E M)附着式上部驱动具有AWC和S CC功能四辊粗轧机(R M)四辊可逆式双传动F1~F6精轧机(F M)四辊全液压不可逆轧机AGC控制精轧工作辊弯辊系统(WRB) F1~F4 1500k N/侧正弯辊力: F5~F6 1100k N/侧精轧工作辊窜辊系统(WRS)移动行程: ±125mm3 板凸度与平直度关系3.1 凸度和相对凸度的表示方法带钢板凸度用C40指标表示,计算公式如下:板凸度:δi=[H i m-(H io+H id)/2]×1000(1)相对凸度:δi X=2δi/(H i0+H id)(2) 式中,δi 为第i机架出口板凸度;Hi m为第i机架出口带钢中部厚度;Hio为第i机架出口带钢操作侧距带钢边部40mm处厚度;Hid为第i机架出口带钢传动侧距带钢边部40mm处厚度;δiX为第i机架出口板相对凸度(%)。
第i机架间的相对凸度用δih i表示,δi表示该道次的板凸度,hi表示该道次的平均厚度(Hio+H id)。
3.2 保持良好平直度的条件凸度是单道次的控制行为,即通过单机架的控制可实现需要的板凸度,但这样会导致平直度指标的超差,产生边浪或中浪等,而平直度的控制是在多机架的控制行为,只有控制多机架的相对凸度变化量在一定的范围内才能既保证所需要的凸度,又能保证板的平直度良好。
板带精轧的前几道次,由于轧件的宽厚比未达 联系人:陈勇,男,36岁,本科,轧钢高级工程师,乌鲁木齐(830022)新疆钢铁研究所9到一定值时,轧件存在一定的宽展,此时道次间的相对凸度波动的允许范围较大,当宽厚比达到一定值时,轧件不存在横向流动,即无宽展,此时道次间的相对凸度变化值必须在一个小范围内波动,否则将产生浪形。
对机架间相对凸度变化量的允许范围,Shohet 等人提出如下曲线:上部曲线是产生边浪的临界线,下部曲线是产生中浪的临界线。
曲线的公式:-40(h b )1.86<△CR <80(h b)1.86 (3) △CR =δi +1h i +1-δih i式中,△CR 为相对凸度变化量;δi +1,δi 为i +1、i 机架出口带钢凸度;h i +1,h i 为i +1、i 机架出口带钢厚度(mm )。
图1 Shohet 的△CR 允许变化的范围曲线4 热轧板凸度控制的策略精轧机组分为凸度调节,平直度保持及平直度控制三个区段。
目前的热连轧精轧机组有7机架和6机架两种。
对7机架机组一般F 1~F 3为凸度调节区段,F 4~F 6为平直度保持区段,F 7为平直度控制区段,对6机架机组一般F 1~F 2为凸度调节区段,F 3~F 5为平直度保持区段,F 6为平直度控制区段,两种的控制原理相同。
成品机架用于平直度的反馈控制,当控制调节量过大,会造成偏离目标凸度,此时应将成品前机架也纳入平直度的反馈控制中,生产薄规格的的最佳凸度调节在F 2,尤其对6机架的精轧机组,厚规格的的最佳凸度调节在F 3,这样在保证目标凸度的同时也保证了平直度的要求,具体控制策略见图2(以7机架为例)。
各机架凸度理想条件应满足公式(4)和(5)。
(1)F 1~F 3为凸度调节段,使F 3的出口带钢的凸度满足公式(4):δ3=δ7×h 3h 7 (4)式中,δ7为成品目标凸度;h 3为F 3出口厚度;h 7为成品出口厚度;(2)F 4~F 6则严格保持相对凸度恒定,既各架相对凸度满足公式(5):δ3h 3=δ4h 4=δ5h 5=δ6h 6=δ7h 7 (5)实际生产中在F 3~F 6间不可能绝对保持公式(5)的要求,存在一定的偏差是不可避免的,但偏差的幅度应满足公式(3)的限制条件,否则将破坏钢带的平直度。
图2 临界曲线5 热轧生产中对凸度影响因素的分析轧出带钢的断面形状(凸度)就是有载辊缝形状,对有载辊缝形状的控制就是对凸度的控制,影响有载辊缝形状的因素很多,主要有轧制力造成的辊系变形、弯辊力的影响、原始辊形、轧辊的热膨胀、轧辊的磨损等,后两种影响称为辊缝的漂移。
八钢精轧具有弯窜辊功能,弯辊能改变有载辊缝形状,正确使用能消除部分轧辊因受到轧制力的作用而产生的挠度,起到调节凸度的功能,而窜辊功能对调节凸度基本不起直接作用,但能通过减轻轧辊的局部磨损,改变磨损辊形,达到控制凸度的效果,尤其在减轻钢带边缘的局部磨损上作用明显,增加同宽轧制量。
有载辊缝形状可用方程(6)表示:δ=P K p +F K F+E ∑(W R +W m +W Y )+E 0δ (6)式中,δ为辊缝中部与板边缘处之差;P 为轧制力;F 为弯辊力;K P 为轧机横向刚度;K F 为轧辊横向刚度;W R 为热辊型;W m 为磨损辊型;W Y 为原始辊型;δ为入口带钢凸度。
可以看出轧辊热凸度和磨损、原始辊形配置、轧制力变化、弯辊力变化等对凸度均有一定影响。
15.1 工作辊热凸度对板凸度的影响带钢轧制过程中,支撑辊和工作辊均会产生热膨胀,主要的热膨胀来自工作辊,工作辊受到轧制变形功转换的热量、摩擦热、高温轧件热传导的作用,使表面温度升高;同时,受轧辊冷却水、空气冷却的影响,轧辊表面温度下降。
由于轧辊中部受边部的热影响而使中部的热传导较边部慢,同时轧件中部较边部的温度高而导致的轧件向轧辊不同部位热传导的差异造成工作辊的中部温度高于边部温度,必然导致工作辊中部热膨胀大于边部,产生热凸度,其直接影响到有载辊缝的形状,造成轧件凸度的变化。
机架越接近成品,轧制力的分配越小,同时轧件的温度越来越低,热传导能力下降,造成工作辊的热凸度在精轧的各机架间是不完全相同的,通常呈现热凸度逐渐减少的趋势。
因此如何合理控制运用热凸度是生产中需注意的问题。
热凸度的产生,在生产中能被合理运用,对控制板凸度是有益的,当支撑辊或工作辊的使用中后期,热凸度能弥补因轧辊磨损而造成的凹型,这在完全使用正弯辊能力仍无法控制凸度的情况下不失为一个补救,对于新换辊的情况就相反,热凸度可能会在弯辊力完全卸载(保留必要的平衡力),此时应在工作辊的冷却装置上考虑一组调节集管,专门控制工作辊的中部温度,减少轧辊的热凸度。
5.2 精轧辊辊形配置对带钢板凸度的影响随着轧钢的进行,在轧件和工作辊、工作辊和支撑辊之间均存在不同程度的磨损,精轧支撑辊的磨损一般呈现凹型状,各机架支撑辊的磨损程度也不尽相同,对凸度的影响程度也不相同,并随着轧制吨位的增加各机架磨损趋于严重,即使增加正弯辊力也不能消除磨损量对有载辊缝造成的影响,其结果是在F1~F6各机架的相对凸度难以保持一致,尤其在换精轧支撑辊的后期,即使正弯辊力使用到额定极限仍不能控制凸度,同时出现钢带的边浪。
通行的解决办法是在新支撑辊上机前考虑一定的辊型凸度以弥补其后续的磨损,或在支撑辊的换辊周期内随着轧制量的增加考虑工作辊的辊型凸度来弥补支撑辊的部分磨损量,在使用前者方案时应考虑辊型凸度不能取太大,否则在换辊初期将使有载辊缝呈凹型,不仅易产生中浪并且使轧制不稳定,引起轧件横窜容易造成断带事故,在采用后方案的时候,应在充分了解F1~F6在不同轧制量时的支撑辊的磨损状况后适,当在工作辊上弥补,宁小勿大,并应考虑工作辊的储备量,减少原始辊型的种类。
5.3 轧制力和弯辊力对带钢板凸度的影响从有载辊缝方程可以看出;轧制力的变化对凸度是有着重要影响,随着轧制力的增大和减小,辊系变形的程度也随之改变,造成凸度的变化,即使精轧机架的能耗负荷分配不变,由于钢温、轧辊直径、轧制线速度、机架间的张力、前机架的来料凸度、弯辊力设置等因素的变化造成轧制力的波动能使有载辊缝形状发生改变,同时AGC的投入对轧制力也造成一定的影响变化,若对各机架的能耗重新进行分配,则精轧各机架的轧制力将有一个比较明显的变化,而导致凸度的变化,正是利用这一点,在生产中操作人员经常为保证板型良好而对精轧机架的负荷分配进行小幅度调整。
近二十多年来在板带轧机上发展的工作辊弯辊装置(WRB)被成功运用于热轧机,八钢热轧1750mm机组具有该功能,该装置能在轧机负荷情况下,对工作辊施以一定的弯辊力以改变有载辊缝形状来实现所需要的轧件凸度,在轧钢过程中的调节比较方便,收效明显、及时,是控制凸度的一个重要手段。
轧钢中的凸度设定模型首先计算限制条件的板凸度范围,然后计算实现目标平直度的各机架目标板凸度,综合考虑计算轧制力、辊磨损、辊热膨胀、原始辊型等对有载辊缝的影响,确定各机架的弯辊力,以达到目标的板凸度并保持板的平直度良好。
7 结束语八钢1750mm热轧机组的建成可为目前已投产的1422mm冷轧机组提供原料,为市场提供优质的热轧卷板,将极大地扩展八钢的产品结构。
热轧机组如何在较短的时间内顺产,板型控制是关键因素,也是产品能进入市场的前提。
板型控制的核心是板凸度的控制,轧辊磨损、轧辊热膨胀、轧制力、弯辊力等因素对板凸度的影响规律和程度还需在生产中结合原始辊型、轧制计划的安排、不同机架的轧机刚度等诸多因素做大量细致复杂的工作,需要综合考虑各因素的影响,不断优化轧辊磨损、轧辊热膨胀、轧制力、轧件温降等数学模型,提高模型计算的精确度,为得到良好的板型打下基础。
11。