3.6.3风机轴承寿命计算报告
轴承寿命计算小结

有限元分析方法
通过建立轴承的有限元模型,模 拟其在实际工况下的应力分布和 变形情况,进而预测其寿命。
05 轴承寿命计算的未来展望
新材料的应用
新材料如陶瓷、碳纤维等具有更高的 强度和耐热性,能够提高轴承的承载 能力和耐久性,从而延长轴承寿命。
新材料的引入可能会改变轴承的摩擦 、磨损和疲劳特性,需要进一步研究 其与轴承寿命的关系。
轴承寿命计算小结
目 录
• 引言 • 轴承寿命计算的基本理论 • 轴承寿命计算的实例分析 • 轴承寿命计算中的注意事项 • 轴承寿命计算的未来展望
01 引言
目的和背景
轴承是机械设备中的重要组成部分, 其寿命直接影响设备的运行效率和安 全性。因此,准确计算轴承寿命对于 设备维护和更新具有重要意义。
轴承失效可能导致设备损坏和生产事 故,准确计算轴承寿命有助于预防潜 在的安全风险,保障生产安全。
降低维护成本
合理安排轴承更换和维修计划,可以 减少不必要的维修和更换成本,为企 业节约开支。
02 轴承寿命计算的基本理论
轴承寿命的定义
轴承寿命是指在一定的工作条件下, 轴承从开始工作到失效的时间长度。
实例三:特殊工况下的轴承寿命计算
在高温环境下,轴承的材料性能和润滑剂的稳 定性会受到影响,导致轴承寿命降低。
在重载工况下,轴承的接触压力分布和材料应力状态 需要进行详细的分析和计算,以确保轴承的安全运行
。
在特殊工况下,如高温、低温、高速、重载等 ,轴承的寿命计算需要更加复杂和精确。
在高速旋转下,轴承的离心力和陀螺力矩对寿命 的影响不容忽视,需要进行相应的计算和分析。
VS
失效通常是指轴承的滚动体或内外圈 出现疲劳断裂、磨损或塑性变形等无 法修复的损伤。
风机轴承寿命预测算法研究

风机轴承寿命预测算法研究随着风机技术的不断进步,风机轴承作为关键部件之一也越来越受到重视。
对于风电场运营商来说,风机轴承的寿命是影响电站生产经济效益的重要因素之一。
因此,提高风机轴承的寿命是一个非常重要的研究方向。
随着信息技术的飞速发展和应用,利用数据采集和分析技术进行风机轴承寿命预测已成为当前研究的热点之一。
一、风机轴承寿命的重要性风机轴承是风力发电机的重要部件。
随着风电行业快速发展,风机轴承的工作状态要求不断提高,对于风电场运营商来说,风电机组的可靠性和经济性至关重要。
在风电机组运行过程中,轴承的损坏会严重影响风电机组的运行,并直接降低发电效率和电站经济效益。
因此,提高风机轴承的可靠性和寿命,对于提高风电机组的经济性和可靠性具有重要的意义。
二、风机轴承寿命预测算法的研究现状1. 基于统计模型的寿命预测算法基于统计模型的寿命预测算法,最基本的思路是通过对轴承寿命数据的统计分析,建立寿命模型,然后根据模型进行风机轴承寿命预测。
常见的统计模型包括最小二乘法回归分析、生存分析等。
这类算法不需要考虑轴承的具体工作环境和工况,仅仅基于统计数据进行预测,适用范围较窄。
2. 基于物理模型的寿命预测算法基于物理模型的寿命预测算法,是将轴承的工作环境和实际工况考虑进去,结合物理学和数学建立轴承寿命模型,进行寿命预测。
这类算法需要建立完整的轴承模型,将轴承的力学、热学、磨损等因素综合考虑进去,预测精度较高。
但是建模和参数标定等任务较为繁琐,对算法研究人员的专业素质和经验要求较高,应用范围较窄。
3. 基于深度学习的寿命预测算法基于深度学习的寿命预测算法,是近年来的研究热点之一。
深度学习的特点是通过大量数据的训练来建立模型,具有良好的自适应性和泛化能力。
该类算法适用于轴承寿命预测场景,可以通过大量轴承振动、温度等各种传感器数据的采集,训练出具有较高预测精度的模型。
三、风机轴承寿命预测的关键技术1. 数据采集数据采集是风机轴承寿命预测的关键技术之一。
轴承寿命计算范文

轴承寿命计算范文轴承寿命是指轴承在一定的工作条件下能够正常运转的时间长度。
轴承的寿命与负荷、转速、温度、润滑及清洗方法等因素有关。
正确地计算轴承寿命对于延长轴承使用寿命、提高设备可靠性和降低维护成本具有重要意义。
轴承寿命的计算通常采用L10寿命模型,即在连续运转的条件下,在统计学暗示(即90%清单)下,90%的轴承寿命的货币值L10达到或超过理想寿命。
轴承寿命的计算可以按照以下步骤进行:1.确认轴承负荷:根据设备的工作要求,确定轴承所承受的负荷。
负荷包括径向负荷和轴向负荷。
这可以通过工程计算或测量获得。
2. 确认转速:根据设备的工作要求,确定轴承的旋转速度。
转速的单位通常是rpm(每分钟转速)。
这也可以通过工程计算或测量获得。
3.确认润滑方式:根据设备的实际情况,选择适当的润滑方式。
轴承的润滑方式可以是油润滑或脂润滑。
润滑方式直接影响轴承的寿命。
4.确认清洗方法:轴承在安装之前需要进行清洗。
确定清洗方法可以很好地去除轴承表面的污垢和杂质,从而减少摩擦和磨损。
5.损失因素计算:确定各种损失因素,如因装配和拆卸等原因的损失经验因子a1,因负荷和粘度影响的损失经验因子a2,因清洗不良和润滑不良影响的损失经验因子a36.计算基本额定寿命:根据轴承的负荷、转速和润滑方式,计算基本额定寿命L10。
公式如下:基本额定寿命L10=(C/P)^p其中,C是基本动态负荷评定值(由厂家提供),P是等效动载荷,p是压力指数。
7. 计算修正额定寿命:根据具体的使用条件和影响因素,计算修正额定寿命Lna。
修正额定寿命Lna = a1 x a2 x a3 x L108. 根据使用环境和需求考虑其他因素:如轴承使用的温度、振动、磨损等特殊环境因素,可以通过对Lna进行修正或额外计算来得到更准确的轴承寿命。
总的来说,轴承寿命计算是一个复杂的过程,需要考虑多个因素。
正确的寿命计算可以帮助选择适当的轴承类型和尺寸,延长轴承的使用寿命,并提高设备的可靠性和运行效率。
(完整版)滚动轴承的寿命计算

滚动轴承的寿命计算一、基本额定寿命和基本额定动载荷1、基本额定寿命L10轴承寿命:单个滚动轴承中任一元件出现疲劳点蚀前运转的总转数或在一定转速下的工作小时数称轴承寿命。
由于材料、加工精度、热处理与装配质量不可能相同,同一批轴承在同样的工作条件下,各个轴承的寿命有很大的离散性,所以,用数理统计的办法来处理。
基本额定寿命L10——同一批轴承在相同工作条件下工作,其中90%的轴承在产生疲劳点蚀前所能运转的总转数(以106为单位)或一定转速下的工作时数。
(失效概率10%)。
2、基本额定动载荷C轴承的基本额定寿命L10=1(106转)时,轴承所能承受的载荷称基本额定动载荷C。
在基本额定动载荷作用下,轴承可以转106转而不发生点蚀失效的可靠度为90%。
基本额定动载荷 C(1)向心轴承的C是纯径向载荷;(2)推力轴承的C是纯轴向载荷;(3)角接触球轴承和圆锥滚子轴承的C是指引起套圈间产生相对径向位移时载荷的径向分量。
二、滚动轴承的当量动载荷P定义:将实际载荷转换为作用效果相当并与确定基本额定动载荷的载荷条件相一致的假想载荷,该假想载荷称为当量动载荷P,在当量动载荷P作用下的轴承寿命与实际联合载荷作用下的轴承寿命相同。
1.对只能承受径向载荷R的轴承(N、滚针轴承)P=F r2.对只能承受轴向载荷A的轴承(推力球(5)和推力滚子(8))P= F a3.同时受径向载荷R和轴向载荷A的轴承P=X F r+Y F aX——径向载荷系数,Y——轴向载荷系数,X、Y——见下表。
径向动载荷系数X和轴向动载荷系数表12-3考虑冲击、振动等动载荷的影响,使轴承寿命降低,引入载荷系数fp—见下表。
载荷系数fp表12-4三、滚动轴承的寿命计算公式图12-9 载荷与寿命的关系曲线载荷与寿命的关系曲线方程为:=常数(12-3)3 球轴承ε——寿命指数10/3——滚子轴承根据定义:P=C,轴承所能承受的载荷为基本额定功载荷时,∴∴(106r) (12-2)按小时计的轴承寿命:(h)(12-3)考虑当工作t>120℃时,因金属组织硬度和润滑条件等的变化,轴承的基本额定动载荷C有所下降,∴引入温度系数f t——下表——对C修正表 12-5(106r)(12-4)(h)(12-5)当P、n已知,预期寿命为L h′,则要求选取的轴承的额定动载荷C为N ——选轴承型号和尺寸!(12-6)不同的机械上要求的轴承寿命推荐使用期见下表。
轴承寿命的计算
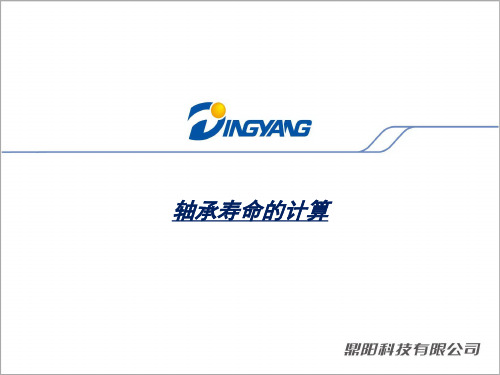
素也考虑其中 2.其中疲劳极限Pu是一个全新的概念,若承受的负 荷低于Pu 值,则轴承不会产生疲劳失效(损坏)
• 新寿命方法修改了调整的寿命等式以计算将理 论更进一步联系实际的新发现
调整的寿命公式中参数的选取:a1
• • • • • • • • a1 与可靠性相关的寿命调整系数. aSKF 与可靠性相关的寿命修正系数. 表现为以下相关方面: 轴承安装是否正确 轴承与相关零件选择的配合公差的选择是否合适 轴承在运行时的润滑状况 轴承在运行时的工作状态(外部的温升,振动,密封) 其他因素
ISO寿命等式
静态安全因素
L10 = 基本额定寿命,百万次旋转 C = 基本额定动态负荷,N P = 相应的动态轴承负荷,N p = 寿命公式的指数 当负荷 P = C时 L10 寿命将为 1百万次旋转
s0 = 静态安全因素 P0 = 相应的静态轴承负荷,N C0 = 基本额定静态负荷,N
当负荷 P0 = C0时 静态安全因素s0将为 1
正确认识额定动载荷C
额定动载荷仅是由轴承的若干基本 几 何尺寸计算而来 C ~ (la· cos)7/9· z3/4· Dw 29/27 与轴承实际制造质量和使用性能密切 相关的密切相关的很多因素, 并不能 通过C值反映: 材料质量 热处理工艺 内部结构设计 内部几何形状 制造精度 公差控制 表面硬度 滚动体与滚道的切合程度 内部摩擦
计算轴承寿命
L10h = 1,000,000 x (C/P)p 60 x n
Байду номын сангаас
L10h:工作小时 n:轴承工作转速
C:额定负荷. P:当量负荷.
SKF新的寿命计算方法
• 现已被ABMA/ISO接受
轴承的寿命计算
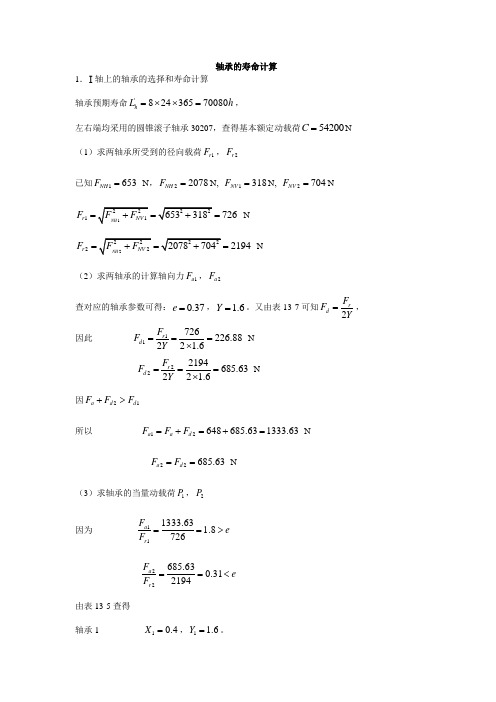
轴承的寿命计算1.I 轴上的轴承的选择和寿命计算轴承预期寿命'82436570080h L h =⨯⨯=,左右端均采用的圆锥滚子轴承30207,查得基本额定动载荷54200C =N(1)求两轴承所受到的径向载荷1r F ,2r F已知1653NH F = N ,22078NH F =N, 1318NV F =N, 2704NV F =N1726r F ===N 22194r F === N (2)求两轴承的计算轴向力1a F ,2a F查对应的轴承参数可得:0.37e =, 1.6Y =。
又由表13-7可知2r d F F Y =, 因此 11726226.8822 1.6r d F F Y ===⨯ N 222194685.6322 1.6r d F F Y ===⨯ N 因21a d d F F F +>所以 12648685.631333.63a a d F F F =+=+= N22685.63a d F F == N(3)求轴承的当量动载荷1P ,2P因为 111333.63 1.8726a r F e F ==>22685.630.312194a r F e F ==< 由表13-5查得轴承1 10.4X =,1 1.6Y =。
轴承2 21X =,20Y =因轴承运转中有轻微冲击载荷,按表13-6查得 1.0 1.2P f =-,取 1.1P f =。
则 11111() 1.1(0.4726 1.61333.63)2666.63P r a P f X F Y F =+=⨯⨯+⨯= N 22222() 1.1121942413.4P r a P f X F Y F =+=⨯⨯= N(4)验算轴承寿命因为12P P >,所以按轴承1的受力大小验算10663'110105420039373060609702666.63h h C L h L n P ε⎛⎫⎛⎫===> ⎪ ⎪⨯⎝⎭⎝⎭即所选轴承满足寿命要求。
轴承寿命的计算

念根据最新的滚动轴承疲劳寿命理论,一只设计优秀、材质卓越、制造精良而且安装正确的轴承,只要其承受的负荷足够轻松(不大于该轴承相应的某个持久性极限负荷值),则这个轴承的材料将永远不会产生疲劳损坏。因此,只要轴承的工作环境温度适宜而且变化幅度不大,绝对无固体尘埃、有害气体和水分侵入轴承,轴承的润滑充分而又恰到好处,润滑剂绝对纯正而无杂质,并且不会老化变质……,则这个轴承将会无限期地运转下去。这个理论的重大意义不仅在于它提供了一个比ISO寿命方程更为可靠的预测现代轴承寿命的工具,而且在于它展示了所有滚动轴承的疲劳寿命都有着可观的开发潜力,并展示了开发这种潜力的途径,因而对轴承产品的开发、质量管理和应用技术有着深远的影响。但是,轴承的无限只有在实验室的条件下才有可能“实现”,而这样的条件对于在一定工况下现场使用的轴承来说,既难办到也太昂贵。现场使用轴承,其工作负荷往往大于其相应的疲劳持久性极限负荷,在工作到一定的期限后,或晚或早总会由于本身材料达致电疲劳极限,产生疲劳剥落而无法继续使用。即使某些轴承的工作负荷低于其相应的持久性极限负荷,也会由于难以根绝的轴承污染问题而发生磨损失效。总之,现场使用中的轴承或多或少总不能充分具备上述实验室所具备的那些条件,而其中任一条件稍有不足,都会缩短轴承的可用期限,这就产生了轴承的寿命问题。一般地说,滚动轴承的寿命是指滚动轴承在实际的服务条件下(包括工作条件、环境条件和维护和保养条件等),能持续保持满足主动要求的工作性能和工作精度的特长服务期限。二、可计算的轴承寿命类别滚动轴承的失效形式多种多样,但其中多数失效形式迄今尚无可用的寿命计算方法,只有疲劳寿命、磨损寿命、润滑寿命和微动寿命可以通过计算的方法定量地加以评估。1、疲劳寿命在润滑充分而其他使用条件正常的情况下,滚动轴承常因疲劳剥落而失效,其期限疲劳寿命可以样本查得有关数据,按规定的公式和计算程序以一定的可靠性计算出来。2、磨损寿命机床主轴承取大直径以保证其高刚度,所配轴承的尺寸相应也大,在其远末达到疲劳极限之前,常因磨损而丧失要精度以致无法继续使用,对这类轴承必须用磨损寿命来徇其可能性的服务期限。实际上,现场使用的轴承大多因过度磨损而失效,所以也必须考虑磨损寿命问题。3、润滑寿命主要对于双面带密封的脂润滑轴承,一次填脂以后不再补充加脂,此时轴承有寿命便取决于滚脂的使用寿命。4、微动磨蚀寿命绞车、悬臂式起微型重机和齿轮变速箱以及汽车离合器等机构中的轴承,在其非运转状态下受到振动负荷所产生的微动磨蚀损伤。往往会发展成轴承失效的主导原因,对这类机构中的轴承,有时需要计算其微动磨蚀寿命。现将此四种寿命类别及其计算方法分别加以介绍。一、滚动轴承的疲劳寿命1、轴承疲劳寿命的基本概念一般意义的轴承疲劳寿命是指一定技术状态下(结构、工艺状态、配合、安装、游隙和润滑状态等)的滚动轴承,在主机的实际使用状态下运转,直至滚动表面发生疲劳而不能满足主机要求时的轴承内、外圈(轴、座圈)相对旋转次数的总值——总转数。当轴承转更大致恒定或为已知,疲劳寿命可用与总转数相应的运转总小时数来表示,此外,还应注意:1、影响轴承疲劳寿命的因素非常多,无法全部加以估计或通过标准试验条件而加以消除,这造成轴承实际疲劳寿命有很大的离散性,因此轴承疲劳寿命的表达参数为额定寿命L10,在ISO推荐标准R281中对L10的涵义明确规定如下:“数量上足够多的相同的一批轴承,其额定寿命L10用转数(或在转速不变时用小时数来表示,该批轴承中有90%在疲劳剥落发生前能达到或超过此转数(或小时数)”。迄今为止,世界各国都遵从上述规定。在美国等一些国家中,还用用中值寿命的概念。中值寿命LM是指一批相同轴承的中值寿命,即指其中50%的轴承在疲劳剥落前能够达到或超过总转数,或在一定转速下的工作不时数,中值寿命LM不是一批轴承寿命的算术平均值。一般中值寿命LM是额定寿命的5倍左右。2、额定寿命的概念只适用于数量足够的一批轴承,而不适用于个别轴承。例如有40套6204轴承按其使用条算得其额定寿命为1000h而不致发生疲劳破坏,其余的4套则可能不到1000h即出现疲劳失效的轴承,额定疲劳寿命的意义就代表这批轴承在正常发挥其材料潜力时可期望的寿命。因此在大多数情况下,用户在选择轴承时仍先作疲劳寿命计算,再根据实际失效类别进行校核,例如磨损寿命校核,取计算结果中的较小值为轴承计算寿命。二、轴承疲劳寿命的估计方法、轴承疲劳寿命的估计方法有计算方法和试验湛支两种。按规定公式和计算规则计算出来的轴承疲劳寿命作为计算疲劳寿命,所算出总转数值规定为内圈或轴圈转动(此时外圈或座圈为固定)时的总转数值。按照我国规定的标准试验方法(ZQ 12-94)滚动轴承疲劳寿命试验规程),在使用性能上能满足为一方法所规定各项要求的试验机,对一批轴承进行抽样疲劳寿命试验,从试验数据处理中得到的实际试验寿命,即为被试轴承所代表的该批轴承的疲劳试验寿命。滚动轴承疲劳寿命试验裨上是充分的润滑最大限度地抑制滚动轴承的磨损因素,采用强化的负荷与转速以突出轴承疲劳因素的一种强化的疲劳寿命试验方法。轴承疲劳寿命的计算法和疲劳寿命试验是相辅相成的,二者所得的结果有足够的对应性。事实上,如对每一个特定的使用场合,都抽取足够数量的轴承进行寿命试验,以验证所选轴承是否合适,这在经济上、时间上和劳动量上都是十分浩大的,所以轴承寿命的试验方法只是在十分必要或重要的情况下才使用,在绝大多数情况下,采用标准的寿命计算方法来估计轴承的使用寿命,有着足够程度的可依赖性。三、疲劳寿命的计算下述轴承疲劳寿命的计算方法是以国家标准GB6391-96《滚动轴承——-额定动负荷和额定寿命的计算方法》和国家标准ISO281/I-1997《滚动轴承——额定动负荷和额定寿命——第一部分:计算方法》为依据,此外,还介绍了瑞典SKF轴承公司新的轴承公司新的轴承疲劳寿命理论和疲劳寿命计算方法。1、疲劳寿命的基本计算公式滚动轴承疲劳寿命的基本计算公式有多种形式,以适应不同用途的需要,以下分别加以介绍。(1)基本额定寿命方程(用总转数表示)1、几个有关的基本概念,在介绍基本额定寿命方程之前,先介绍几个相关的基本概念即:单个轴承的疲劳寿命——单个轴承在其任一套圈(或垫圈)或滚动体的材料首次出现疲劳扩展之前,其中一个套圈(或垫圈)相对于另一套圈(或垫圈)转动的总转数。轴承寿命的可靠性——在同一条件下运转的一组在相同条件下运转的一组条件相同的轴承,可期望达到或超过某一规定寿命的百分率,对于单个轴承,其可靠性为该轴承能达到或超过某一规定寿命的概念。轴承的基本额定寿命——单个轴承或一组在相同条件下运转的技术条件相同的轴承,其可靠性达到90%时的寿命。3、基本额定寿命方程的计算式用总转数表示的轴承基本额定寿命方程的计算式为:L10=C/P式中L10——轴承的基本额定疲劳寿命(106r); C——对向心类轴承为径向当量动负荷(N),对推力类轴承为轴向当量动负荷(N);P——对向心类轴承为径向当量动负荷(N),对推力类轴承为轴向当量动负荷(N);ε——寿命指数,对球轴承ε=3,对滚动轴承ε=10/3。式5-1为我国国家标准和国际标准规定的滚动轴承基本额定寿命的标准计算式。轴承疲劳轴承寿命试验机的转数记录仪,可以准确地记录下轴承疲劳试验的总转数,得以方便与计算结果相对照。4、基本额定寿命方程的适用范围基本额定寿命方程5-1适用于具备以下技术条件的滚动轴承在额定疲劳寿命计算;轴承的外形尺寸选自由国家相应标准规定的轴承尺寸范围;轴承用优质淬硬钢材制造并且加工质量良好;轴承滚动接触表面的表面质量(包括几何形状精度和材质等)合乎常规标准。这些轴承必须安装正确,润滑充分,无外界杂质侵入而且不是在极端条件下运转。当不符合这些条件时,使用式5-1的计算结果便会发生偏差。为了抵消这样的偏差,就必须将按式5-1计算所得的结果乘上相应的修正系数。5、基本额定寿命方程的应用限制基本额定寿命方程5-1不适用例如有装填满的深沟球轴承,或在滚动体与套圈滚道之间的接触面积上有相当大缺口的其他种类轴承,因为这种缺口影响到接触区的承载能力。式5-1还不适用滚动体直接在轴或座孔表面上运转的场合,除非相应的轴或座孔完全按照滚动轴承承载元件的技术条件制造。当轴承在实际使用时其所承受的负荷为非正常分布(例如由于轴线不对中,外壳或轴有较大变形,滚动体的离心力作用或其他高速效应,以及向心轴承采用特别大的游隙或施加预负荷等情况造成),按式5-1计算其基本额定寿命时,就不能取得满意的结果。
轴承的寿命与计算
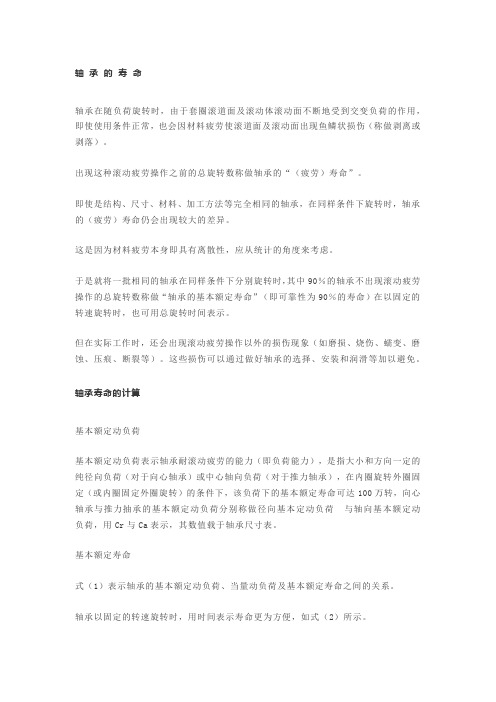
轴承的寿命轴承在随负荷旋转时,由于套圈滚道面及滚动体滚动面不断地受到交变负荷的作用,即使使用条件正常,也会因材料疲劳使滚道面及滚动面出现鱼鳞状损伤(称做剥离或剥落)。
出现这种滚动疲劳操作之前的总旋转数称做轴承的“(疲劳)寿命”。
即使是结构、尺寸、材料、加工方法等完全相同的轴承,在同样条件下旋转时,轴承的(疲劳)寿命仍会出现较大的差异。
这是因为材料疲劳本身即具有离散性,应从统计的角度来考虑。
于是就将一批相同的轴承在同样条件下分别旋转时,其中90%的轴承不出现滚动疲劳操作的总旋转数称做“轴承的基本额定寿命”(即可靠性为90%的寿命)在以固定的转速旋转时,也可用总旋转时间表示。
但在实际工作时,还会出现滚动疲劳操作以外的损伤现象(如磨损、烧伤、蠕变、磨蚀、压痕、断裂等)。
这些损伤可以通过做好轴承的选择、安装和润滑等加以避免。
轴承寿命的计算基本额定动负荷基本额定动负荷表示轴承耐滚动疲劳的能力(即负荷能力),是指大小和方向一定的纯径向负荷(对于向心轴承)或中心轴向负荷(对于推力轴承),在内圈旋转外圈固定(或内圈固定外圈旋转)的条件下,该负荷下的基本额定寿命可达100万转,向心轴承与推力抽承的基本额定动负荷分别称做径向基本定动负荷与轴向基本额定动负荷,用Cr与Ca表示,其数值载于轴承尺寸表。
基本额定寿命式(1)表示轴承的基本额定动负荷、当量动负荷及基本额定寿命之间的关系。
轴承以固定的转速旋转时,用时间表示寿命更为方便,如式(2)所示。
另外,对于铁路车辆或汽车等用行走距离(KM)表示寿命较多,如式(3)所示。
这里:L10:基本额定寿命,106转L10h:基本额定寿命,hL10s:基本额定寿命,kmP:当量动负荷,N{Kgf}厖......参照后面C:基本额定动负荷,N{Kgf}n:转速,rpmp:寿命指数球轴承..........p=3滚子轴承.......p=10/3D:车轮或轮胎直径,mm因此,作为轴承的使用条件,设当量动负荷为P,转速为n,则满足设计寿命所需要的轴承基本额定动负荷C可由式(4)计算,从轴承尺寸表中选出满足C值的轴承,即可确定轴承的尺寸。
轴承寿命计算

mm
承载中心与轴承B间距L2(附录1) L2
mm
轴承A承载负荷
F5
N
轴承B承载负荷
F6
N
30000 29509.5 27547.5 25585.5
27324
143 180 34393 7070
30000 29509.5 27547.5 25585.5 27314
143 180 34381 7067
1
计算公式: F1=F-M*0.1*9.81/Y F2=F-M*0.5*9.81/Y F3=F-M*0.9*9.81/Y F4=[(F1P*15%)+(F2P*55%)+(F3P*30%)]1/P F5=F4*L2/L1 F6=abs(F5-F4)
3、轴承寿命系数计算:
轴承 型号 转速 额定动负荷 径向负荷 可靠度系数
设计计算书
轴承寿命计算
编制: 校对: 批准: 日期:
一、计算目的:
通过轴承的承载负荷计算和轴承的寿命需求计算校核轴承寿命是否满足要求。
二、参考资料:
《机械设计手册》第3卷,P20-77至P20-86、《SKF轴承样品选型手册》
三、计算过程:
1、轴承寿命需求计算:
输入参数
载重 速度 曳引轮直径 绕绳比 使用寿命(年) 每年运行次数 平均每次运行距离(m) 输出结果:
轴承B(SKF) 6217 167 83300 7,067 0.62
3 163,320 101,259 1637.6 1015.3 127.3
7.97
计算公式: n=[60*V/(π*D/1000)]*Y Q1=[1000000/(60*n)]*(C/R)P Q2=a1*Q1 Q3=(C/R)P Q4=a1*Q3 Q5=Q*X*Z/1000000 α=Q4/Q5
轴承寿命计算公式程序

轴承寿命计算公式程序在工程领域中,轴承是一种常见的机械零件,用于支撑和减少旋转摩擦。
轴承的寿命是指在一定条件下,轴承能够正常运转的时间,通常以小时或者圈数来表示。
轴承的寿命对于机械设备的性能和可靠性具有重要的影响。
因此,准确地计算轴承的寿命对于工程设计和维护具有重要意义。
轴承的寿命计算公式是根据轴承的负荷、转速、润滑方式等因素来确定的。
一般来说,轴承的寿命可以通过以下公式来计算:L = (C/P)^p。
其中,L为轴承的寿命(小时),C为基本额定动载荷(N),P为等效动载荷(N),p为指数。
在实际应用中,轴承的寿命计算还需要考虑到轴承的使用环境、润滑方式、轴承材料等因素。
因此,轴承的寿命计算公式程序需要考虑到这些因素的影响。
首先,基本额定动载荷(C)是指在轴承额定寿命(106次转动)内,轴承能够承受的最大动载荷。
它是由轴承制造商根据轴承的材料、几何形状等因素确定的。
基本额定动载荷是轴承寿命计算的重要参数,它直接影响到轴承的寿命。
其次,等效动载荷(P)是指在实际工作条件下,轴承承受的动载荷。
由于轴承在实际工作中可能同时承受径向载荷和轴向载荷,因此需要将这两种载荷转换为等效动载荷。
等效动载荷的计算需要考虑到轴承的载荷分布、工作条件等因素。
最后,指数(p)是根据轴承的类型、润滑方式等因素确定的。
不同类型的轴承具有不同的指数,它反映了轴承在不同工作条件下的寿命特性。
综上所述,轴承的寿命计算公式程序需要考虑到轴承的基本额定动载荷、等效动载荷和指数等因素。
通过合理地计算轴承的寿命,可以帮助工程师们选择合适的轴承类型和规格,从而提高机械设备的性能和可靠性。
除了轴承的寿命计算公式程序,轴承的寿命还受到许多其他因素的影响。
例如,轴承的润滑方式对于轴承的寿命具有重要影响。
合适的润滑方式可以减少轴承的摩擦和磨损,延长轴承的寿命。
此外,轴承的安装和维护也会影响轴承的寿命。
正确的安装和定期的维护可以减少轴承的故障率,延长轴承的使用寿命。
轴承寿命计算
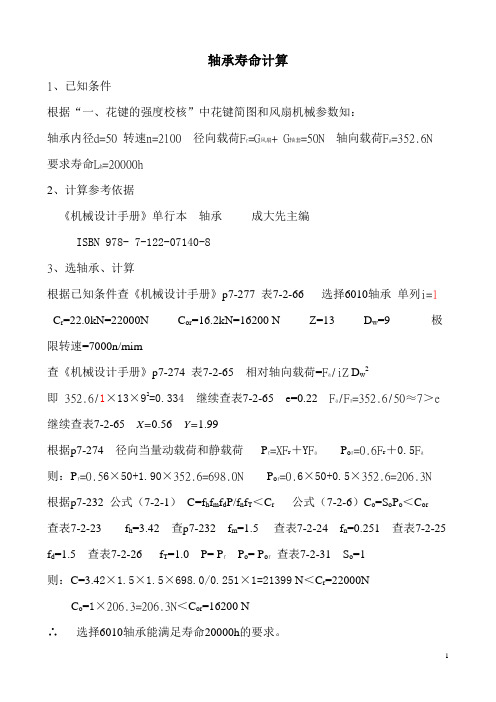
轴承寿命计算
1、已知条件
根据“一、花键的强度校核”中花键简图和风扇机械参数知:
轴承内径d=50转速n=2100径向载荷Fr=G风扇+G轴套=50N轴向载荷Fa=352.6N
要求寿命Lh=20000h
2、计算参考依据
《机械设计手册》单行本轴承成大先主编
ISBN 978- 7-122-07140-8
3、选轴承、计算
继续查表7-2-65X=0.56Y=1.99
根据p7-274径向当量动载荷和静载荷Pr=XFr+YFaPor=0.6Fr+0.5Fa
则:Pr=0.56×50+1.90×352.6=698.0NPor=0.6×50+0.5×352.6=206.3N
根据p7-232公式(7-2-1)C=fhfmfdP/fnfT<Cr公式(7-2-6)Co=SoPo<Cor
根据已知条件查《机械设计手册》p7-277表7-2-66选择6010轴承单列i=1
Cr=22.0kN=22000N Cor=16.2kN=16200N Z=13 Dw=9极限转速=7000n/mim
查《机械设计手册》p7-274表7-2-65相对轴向载荷=Fa/iZDw2
即352.6/1×13×92=0.334继续查表7-2-65e=0.22Fa/Fr=352.6/50≈7>e
查表7-2-23fh=3.42查p7-232 fm=1.5查表7-2-24 fn=0.251查表7-2-25 fd=1.5查表7-2-26 fT=1.0 P=PrPo=Por/0.251×1=21399N<Cr=22000N
Co=1×206.3=206.3N<Cor=16200N
轴承寿命的计算.

计算轴承寿命
L10h = 1,000,000 x (C/P)p 60 x n
L10h:工作小时 n:轴承工作转速
C:额定负荷. P:当量负荷.
SKF新的寿命计算方法
• 现已被ABMA/ISO接受
Lna = a1·aSKF (C/P)p
• 新寿命方法陈述了两个基本概念
1.将疲劳负荷极限和其他几项与润滑及污染有关的因
当负荷 P0 = C0时 静态安全因素s0将为 1
正确认识额定动载荷C
额定动载荷仅是由轴承的若干基本 几 何尺寸计算而来 C ~ (la· cos)7/9· z3/4· Dw 29/27 与轴承实际制造质量和使用性能密切 相关的密切相关的很多因素, 并不能 通过C值反映: 材料质量 热处理工艺 内部结构设计 内部几何形状 制造精度 公差控制 表面硬度 滚动体与滚道的切合程度 内部摩擦
谢 谢 大 家!
其中疲劳极限pu是一个全新的概念若承受的负荷低于pu值则轴承不会产生疲劳失效损坏新寿命方法修改了调整的寿命等式以计算将理论更进一步联系实际的新发现skf与可靠性相关的寿命修正系数
轴承寿命的计算
测算轴承寿命真空吸尘器的寿命可为1000小时
典型工业应用的寿命约为40,000小时,或4-5年 左右 较昂贵的机器一般设计的使用寿命较长 –造纸机轴承设计的使用寿命为10-20万小时 (10-20年)
素也考虑其中 2.其中疲劳极限Pu是一个全新的概念,若承受的负 荷低于Pu 值,则轴承不会产生疲劳失效(损坏)
• 新寿命方法修改了调整的寿命等式以计算将理 论更进一步联系实际的新发现
调整的寿命公式中参数的选取:a1
• • • • • • • • a1 与可靠性相关的寿命调整系数. aSKF 与可靠性相关的寿命修正系数. 表现为以下相关方面: 轴承安装是否正确 轴承与相关零件选择的配合公差的选择是否合适 轴承在运行时的润滑状况 轴承在运行时的工作状态(外部的温升,振动,密封) 其他因素
轴承寿命及推力计算

轴承使用寿命计算通用轴承寿命计算:ε⎪⎭⎫ ⎝⎛=P C n L h 6010610 (1) h L 10——基本额定寿命(h )C ——基本额定动载荷(N )P ——当量动载荷(N )N ——转速(r/min ,这里值暂取30)ε——寿命指数(球轴承取3,滚子轴承取10/3)其中当量载荷: P=X*Fr + Y*Fa (2)P 为当量动载荷Fr 轴承所受的径向载荷(N)Fa 轴承所受的轴向载荷(N)X 径向动载荷系数Y 轴向动载荷系数对悬臂轴承进行受力分析:上轴承6013-2Z 受到全部悬臂的重力以及径向力,下轴承6012-2Z 仅受到水平径向力。
根据力矩平衡,可以得出:对于6013-2Z :Fa = (∑Gi*Li)/h = 6620NFr = ∑Gi =1190N对于6012-2Z ::Fa = (∑Gi*Li)/h = 6620NFr = 0N(一)、轴承型号:GB/T 296 6013-2Z ,深沟球轴承,两侧间隙密封。
基本尺寸:基本额定静载荷:Cor = 24.8KN基本额定动载荷:Cr = 32KN查询工具书数值,带入公式计算,由Fa/Fr<e ,并根据Fa/Cor ,可以得到X 、Y 的值分别为1、0。
算出当量动载荷,带入公式: P=X*Fr + Y*Fa =0*1190+1*6620=6620Nε⎪⎭⎫ ⎝⎛=P C n L h6010610=361066203200030*6010⎪⎭⎫ ⎝⎛=h L ≈62748h(二)轴承型号:GB/T 296 6012-2Z ,深沟球轴承,两侧间隙密封。
图同上。
基本额定静载荷:Cor = 24.2KN基本额定动载荷:Cr = 31.5KN查询工具书数值,带入公式计算,由Fa/Fr>e ,并根据Fa/Cor ,可以得到X 、Y 的值分别为1、0。
算出当量动载荷,带入公式: P=X*Fr + Y*Fa =0*0+1*6620=6620Nε⎪⎭⎫ ⎝⎛=P C n L h 6010610=361066203150030*6010⎪⎭⎫ ⎝⎛=h L ≈59852h 摩擦力矩的计算:M ≈μ(d/2)F ,深沟球轴承μ值(0.0015~0.003)6013-2Z : M1=0.003*0.035*6620=0.6951NM6012-2Z : M2=0.003*0.03*6620 =0.5958NMM=M1+M2=0.6951+0.5958=1.2909NM在2400mm ,和500mm 处,推动转臂所需的力为:0.54N 、2.6N机械手受力分析一、自重夹取若四爪平衡受力,则重力有四爪平均分配。
轴承寿命的计算

轴承寿命的计算1、 基本额定动负荷基本额定动负荷表示轴承耐滚动疲劳的能力 (即负荷能力),是指大小和方向一定的纯径向负荷(对于向心轴承)或中心轴向负荷(对于推力轴承),在内圈旋 转外圈固定(或内圈固定外圈旋转) 的条件下,该负荷 下的基本额定寿命可达 100万转。
向心轴承与推力轴 承的基本额定动负荷分别称做径向基本额定动负荷与 轴向基本额定动负荷,用 Cr 与Ca 表示,其数值录入 轴承尺寸表。
2、 基本额定寿命式1表示轴承的基本额定动负荷, 当量动负荷及基本额定寿命之间的关系。
轴承以固定的转速时,用时间表示寿命更为方便,一卩(皿需【粹为1Ml “金耐盟⑴"和毎虞乘謐①“朝示谱汁於Lio: L TP :耳 M :动ftff. Ndtgf} t;舉水fig 宦动血荷・! < 的連、rpinP :"命他 球轴* ............... P=3険• f■轴承………P = 10/3U :书皑或轮強伍丫包mm因此,作为轴承的使用条件,设当量动负荷为 P ,转速为n ,则满足设计寿命所需要的轴承基本额定动 负荷c 可由式4计算。
从轴承表选岀满足c 值的轴承, 即可确定轴承的尺寸。
机械要求的轴承必需寿命请参 考表4。
3、根据温度进行的基本额定动负荷的修正与轴承的 尺寸稳定处理轴承在高温下使用时,材料组织会发生变化、硬度降低,基本额定动负荷将比常温下使用时减小。
材 料组织一旦发生变化,即使温度恢复到常温也不会复原。
因此,在高温下使用时,必须将轴承尺寸表的基本额定动负荷乘以表1的温度系数进行修正。
表i 温度系数轴承长时间在120摄氏度以上的工作温度下使用时,由于经一般热处理的轴承尺寸变化大,必须进行 尺寸稳定处理。
尺寸稳定处理与使用温度范围如表2所示。
但经尺寸稳定处理的轴承硬度降低,有时基本额定动负荷 会减小。
Li«h"5onh/然幽稠定弁命・10’转 从衣额足胖話、h E 本檢定齐命,km如式2所示。
风电轴承寿命分析与案例

风电轴承寿命分析与案例摘要通过对轴承寿命理论演变过程进行梳理及影响轴承修正寿命的工况系数、可靠性系数、润滑工况、滚动体和滚道修型及可变的载荷-寿命指数等进行推理,得出轴承的修正参考寿命。
并利用BEARINX Easy对现有轴承进行分析,计算不同工况下的理论寿命。
关键词工况系数修正寿命 BEARINX Easy背景随着风力发电机设备的大型化,其对使用的轴承也提出了越来越高的要求,风电轴承使用环境恶劣,维修成本高,因此,轴承的可靠性及寿命对保证风力发电机组的安全稳定运行至关重要。
寿命理论的发展史备注:Lnm-修正的额定寿命(100-n%可靠),百万转。
1.P寿命理论模型轴承受力模型轴承的寿命计算轴承的基本额定寿命L10L10=(C/P)PP=X·Fr+Y·Fa(当量动载荷,由工况载荷计算得出,本文不展开叙述)C:轴承的额定动载荷(为设计值,由轴承厂家提供)向心球轴承:向心滚子轴承:轴承的修正寿命L10mL10m =a1.aISO.L10L10m:修正的额定寿命L10:基本额定寿命a1:可靠性系数aISO:工况系数基于Tallian寿命理论轴承的工况系数aISOaISO =f[(eC·Cu)/P,К]eC:污染系数Cu :疲劳极限载荷,轴承样本或图纸上给出P :当量动载荷,由工况载荷计算得出К :润滑剂粘度比,К=v/v1轴承的修正参考寿命LhmrLhmr =f(prH,Cu,k,ec)轴承寿命计算需考虑了实际接触应力和内部应力分布、轴承的倾斜(不对中)、轴承的工作游隙、滚动体和滚道修型以及可变寿命指数、润滑工况、滚动体和滚道修型及可变的载荷-寿命指数等,对因数进行修正,最终得出一个接近实际运行寿命的值。
aiso:工况系数qci,k:内圈的额定寿命q:外圈的额定寿命co,k基于BEARINX-online Easy EMachine对现有电机轴承(轴承详细信息这里不体现)倾斜、真实应力、载荷分布及疲劳进行分析:= 186178 hLh10r刚度矩阵轴承计算寿命:L= 260004 hh10r= 72 %L_rel总结是否考虑润滑脂添加剂对轴承的计算寿命具有很大的影响,而且在实际应用中很难判断并确保添加剂的应用效果!因此不推荐使用Lhmr作为主轴承计算寿命的评判标准。
轴承寿命的计算

轴承寿命的计算1、基本额定动负荷基本额定动负荷表示轴承耐滚动疲劳的能力(即负荷能力),是指大小和方向一定的纯径向负荷(对于向心轴承)或中心轴向负荷(对于推力轴承),在内圈旋转外圈固定(或内圈固定外圈旋转)的条件下,该负荷下的基本额定寿命可达100万转。
向心轴承与推力轴承的基本额定动负荷分别称做径向基本额定动负荷与轴向基本额定动负荷,用Cr与Ca表示,其数值录入轴承尺寸表。
2、基本额定寿命式1表示轴承的基本额定动负荷,当量动负荷及基本额定寿命之间的关系。
轴承以固定的转速时,用时间表示寿命更为方便,如式2所示。
另外,对于铁路车辆或汽车等用行车距离(km)表示寿命较多,如式3所示。
因此,作为轴承的使用条件,设当量动负荷为P,转速为n,则满足设计寿命所需要的轴承基本额定动负荷c可由式4计算。
从轴承表选出满足c值的轴承,即可确定轴承的尺寸。
机械要求的轴承必需寿命请参考表4。
3、根据温度进行的基本额定动负荷的修正与轴承的尺寸稳定处理轴承在高温下使用时,材料组织会发生变化、硬度降低,基本额定动负荷将比常温下使用时减小。
材料组织一旦发生变化,即使温度恢复到常温也不会复原。
因此,在高温下使用时,必须将轴承尺寸表的基本额定动负荷乘以表1的温度系数进行修正。
表1温度系数轴承工作温度°C125125175200250温度系数(fT)110.950.900.75轴承长时间在120摄氏度以上的工作温度下使用时,由于经一般热处理的轴承尺寸变化大,必须进行尺寸稳定处理。
尺寸稳定处理与使用温度范围如表2所示。
但经尺寸稳定处理的轴承硬度降低,有时基本额定动负荷会减小。
表2尺寸稳定处理尺寸稳定处理代号使用温度范围S0 S1 S2超过100摄氏度到150摄氏度超过150摄氏度到200摄氏度超过200摄氏度到250摄氏度4、修正额定寿命式1表示的是可靠性90%的基本额定寿命(L10),根据用途的不同,有时也需要可靠性高于90%的高可靠性寿命。
轴承的寿命计算
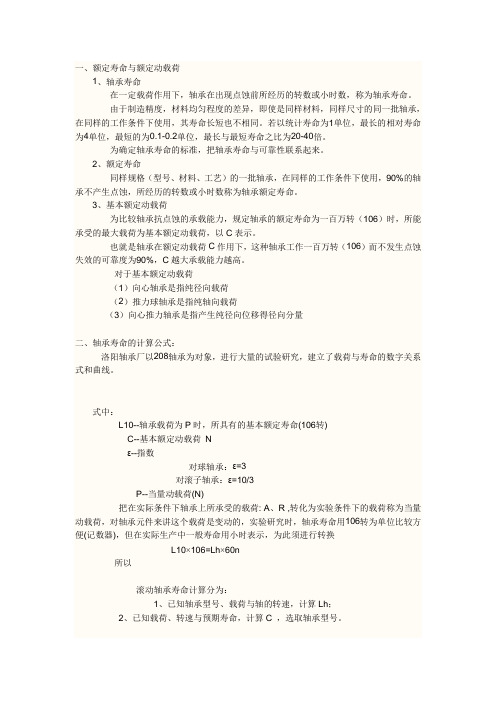
一、额定寿命与额定动载荷1、轴承寿命在一定载荷作用下,轴承在出现点蚀前所经历的转数或小时数,称为轴承寿命。
由于制造精度,材料均匀程度的差异,即使是同样材料,同样尺寸的同一批轴承,在同样的工作条件下使用,其寿命长短也不相同。
若以统计寿命为1单位,最长的相对寿命为4单位,最短的为0.1-0.2单位,最长与最短寿命之比为20-40倍。
为确定轴承寿命的标准,把轴承寿命与可靠性联系起来。
2、额定寿命同样规格(型号、材料、工艺)的一批轴承,在同样的工作条件下使用,90%的轴承不产生点蚀,所经历的转数或小时数称为轴承额定寿命。
3、基本额定动载荷为比较轴承抗点蚀的承载能力,规定轴承的额定寿命为一百万转(106)时,所能承受的最大载荷为基本额定动载荷,以C表示。
也就是轴承在额定动载荷C作用下,这种轴承工作一百万转(106)而不发生点蚀失效的可靠度为90%,C越大承载能力越高。
对于基本额定动载荷(1)向心轴承是指纯径向载荷(2)推力球轴承是指纯轴向载荷(3)向心推力轴承是指产生纯径向位移得径向分量二、轴承寿命的计算公式:洛阳轴承厂以208轴承为对象,进行大量的试验研究,建立了载荷与寿命的数字关系式和曲线。
式中:L10--轴承载荷为P时,所具有的基本额定寿命(106转)C--基本额定动载荷Nε--指数对球轴承:ε=3对滚子轴承:ε=10/3P--当量动载荷(N)把在实际条件下轴承上所承受的载荷: A、R ,转化为实验条件下的载荷称为当量动载荷,对轴承元件来讲这个载荷是变动的,实验研究时,轴承寿命用106转为单位比较方便(记数器),但在实际生产中一般寿命用小时表示,为此须进行转换L10×106=Lh×60n所以滚动轴承寿命计算分为:1、已知轴承型号、载荷与轴的转速,计算Lh;2、已知载荷、转速与预期寿命,计算C ,选取轴承型号。
通常取机器的中修或大修界限为轴承的设计寿命,一般取Lh'=5000,对于高温下工作的轴承应引入温度系数ftCt=ftCt ≤120 125 150 200 300ft 1 0.95 0.90 0.80 0.60上两式变为:对于向心轴承对于推力轴承三、当量动载荷P的计算在实际生产中轴承的工作条件是多种多样的,为此,要把实际工作条件下的载荷折算为假想寿命相同的实验载荷--当量载荷。
轴承寿命计算-PPT精选文档
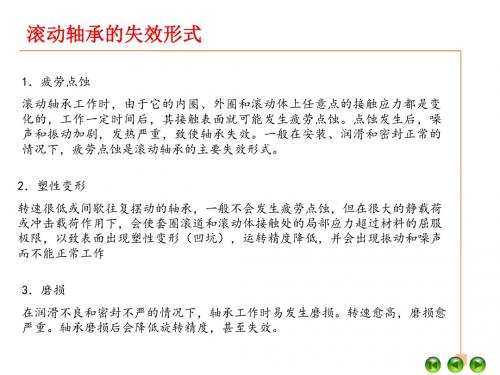
s0 = 静态安全因素 P0 = 相应的静态轴承负荷,N C0 = 基本额定静态负荷,N 当负荷 P0 = C0时 静态安全因素s0将为 1
5
轴承负荷能力
球轴承
圆柱滚子 轴承
球面滚子 轴承
在极重的负 荷下, C/P < 4, 请咨询专业工 程师
6
滚动轴承寿命计算的基本公式
7
滚动轴承的当量载荷
滚动轴承的当量动载荷
滚动轴承可能同时承受径向和轴向复合载荷,为了计算轴承 寿命时能和基本额定动载荷在相同条件下比较,需要将此复合载 荷下的实际工作载荷转化为径向当量动载荷(当量动载荷),其 计算式为
P = XFR + YFA
FR — 名义径向载荷; FA — 名义轴向载荷; X、Y — 径向动载荷系数和轴向动载荷系数,可查轴承样本。
d mm 25
D
r/min 15 000 12 000 11 000 12 000 10 000 9 000 10 000 9 000 8 500 9 500 8 500 7 500 9 000 7 500 6 700 18 000 15 000 14 000 15 000 13 000 11 000 13 000 11 000 10 000 12 000 10 000 9 000 11 000 9 000 8 000
1
轴承疲劳故障
2
轴承寿命的计算准则
对一般工作条件下的回转滚动轴承——经常发生点蚀, 主要进行寿命计算,必要时进行静强度校核; 对于不转动、摆动或转速低(n≦10 r/min)的轴承,要 求控制塑性变形,只需进行静强度计算;
对于高速轴承——由于发热而造成的粘着磨损、烧伤常常 是突出的矛盾,除进行寿命计算外,还需校验极限转速。
- 1、下载文档前请自行甄别文档内容的完整性,平台不提供额外的编辑、内容补充、找答案等附加服务。
- 2、"仅部分预览"的文档,不可在线预览部分如存在完整性等问题,可反馈申请退款(可完整预览的文档不适用该条件!)。
- 3、如文档侵犯您的权益,请联系客服反馈,我们会尽快为您处理(人工客服工作时间:9:00-18:30)。
海南昌江核电工程
JD-L11-2x12.5E风机
轴承寿命计算报告
设备编号:9DVN004~006ZV 设备型号:JD-L11-2x12.5E 设备名称:正常排风机
浙江金盾风机风冷设备有限公司
2009年9月10日
海南昌江核电工程
JD-L11-2x12.5E风机
轴承寿命计算报告
设备编号:9DVN004~006ZV
设备型号:JD-L11-2x12.5E
设备名称:正常排风机
批准:
审核:
校对:
编制:
JD-L11-2x12.5E风机轴承寿命计算
已知条件如下:
G1
f带拉力
带拉力:f1= 28563×P/(D×n)≈30000×250/(0.4×1280)= 14648N 带轮重加带拉力:f = 1260 + 14648 =15908N
叶轮重加不平衡力:G = M2×[(n/2135)2×g]= 6370N
悬臂轴重:G1 = 23×9.8 = 225N
两轴承间轴重:G2 = 226×9.8 = 2215N
= 0得
由∑M
A
R B×1.75-0.855×(6370+2215)+(225+15908) ×0.31 = 0
R B= 1337N
R A×1.75-0.855×(6370+2215)-(225+15908) ×2.06 = 0
R A = 23185N
风机运行时有轻微振动,取f p =1.1
则轴承A的载荷P A = 1.1×23185 = 25503N
轴承寿命L A = 106×(C/P A)3/60n = 467737h
结论:轴承寿命远远大于100000小时,满足技术规格书的要求。