生产现场9大浪费点检表-最终
生产现场浪费的原因分析表

பைடு நூலகம்序号
浪费项目
浪费形成的原因
改善对策
1
等待的浪费
(1)工作方法的不一
(2)长时间的机器换装
(3)人、机配合效果差
(4)缺乏合适的机器
2
搬运的浪费
(1)大批量加工
(2)生产作业缺乏全理的计划
(3)换装、换线、换模时间长
(4)工作场地组织差
(5)生产现场布局不合理
3
不良/修理的浪费
(4)换装、换线、换模时间长
(5)机器有效运行时间短,预防维护不够
(6)仅关注销售预测,而不是客户的需求
(1)操作工控制失误
(2)管理层的决策失误
(3)操作工及相关人员缺乏培训
(4)工装夹具不合格
(5)车间布置差造成不必要的搬运
4
动作的浪费
(1)设备、办公室及工厂布局不合理
(2)作业场所缺乏组织
(3)机器、人力产生的低效率
(4)工作方法不一致
(5)大批量生产
(6)员工未真正参与到过程中
5
过多处理的浪费
(1)没有过程控制的工艺变更
(2)新技术的利用不当
(3)由不适当级别的人做决定
(4)无效的政策和程序
6
库存的浪费
(1)工序能力欠缺
(2)供应商能力欠缺
(3)换装、换线、换模时间长
(4)部门(局部)优化
(5)预测系统、统计数据不准确的
7
过量生产的浪费
(1)生产现场缺乏沟通
(2)部门(局部)最优化
(3)在不适当的地方自动化
生产现场9大浪费点检表-最终

24 是否进行了岗位交叉培训(多技能培训)
25 换手是否必要?
一级目标 人,设备能力 人,机 料 人 人 应急制度 人 人 人
二级分类 操作 操作 供料及时 工作饱和度 工作合理性 产品安全控制 操作规范 工作饱和度 操作规范
多
1 员工是否对样品、产品的要求是否理解?(0.1的误差精度,0.01操作)
1 零件、工具等,是否可以尽量放置于近处?(搬运距离是否过长)
2 物品及工具等,是否整齐的放置?(例如电源线凌乱,是否有合适的BOX或架子,便于拿取)
3 物品及工具等,放置场所的位置与顺序恰当吗?(物品、工具无交叉,一个流方向)
4 物品箱是否整理过?(过脏、存有垃圾,造成操作工使用麻烦)
5 物品箱的大小适切否?(过大、太小)可否斜置或重迭?
8 现场半成品是否有准确的管理管控?
9 仓库台车、box 是否进行统计管理?没有过多,或者过少(现场堆积产品),或者浪费严重
10 各个部门、各个工序产能是否均衡?半成品是否过低或者过高?
1 生产速度是否过快或者过慢(计划是否遵守?人力、设备安排是否合理)
2 是否缺少拉动的管理系统,而造成各个部门生产不匹配,各自为政
17 非得使用手以外的身体部位,才能进行作业吗?
18 工具尽可能共通使用(标准化)?(或者配件标准化,例如丰田汽车通用汽车底盘)
19 二种以上的工具,可被归纳成一种吗?
20 装配、插下能够简单快速吗?
21 须要用力的手把、把柄等的握把与手接触面积可否加大?
22 能否使用自动化工具?(电动螺丝起子)
23 工作是否标准化(张三需要3个动作,王五需要六个动作,或者左手右手)
7
管理浪费之管理成本的浪费: ①计划编制无依据;②计划执行不严肃;③计划查核不认真;④计划处置完善不到位;⑤费用投入与收入不匹配
九大浪费

M u d a 一:制造过多的Muda制造过多的 M u d a,是生产线督导人员的心理作用造成的,他担心机器会出故障、不合格品会产生,以及员工会缺席,而被迫生产比需要数更多的产品,以策安全。
此种形式的 M u d a,是由于提早生产造成的,尤其是对昂贵的机器,为了有效地运用而生产超过需要的数量。
然而,在及时生产体系里,提早生产被视为比延后生产更不好。
生产过多产生巨大的浪费:提早耗用原材料、浪费人力及设施、增加了机器负荷、增加利息负担及额外的空间以储存多余的存货,及增加搬运和管理成本。
在所有的M u d a中,制造过多是最严重的 M u d a,它带给人们一个安心的错觉,掩盖了各种问题,以及隐藏了现场中可供改善的线索。
要把制造过多当做犯罪看待。
制造过多是起源于下列无效的观念及政策造成的:没有考虑到下一个流程或下一条生产线的正确生产速度,而只尽其所能,在本流程生产过多的产品。
让作业员有生产伸缩的充分空间。
让每一流程或生产线有提高自己的生产力的利益。
因为有不合格品而想提高直行率(直行率值指产品不用重修的比率)。
因为有多余的产能,所以容许机器生产多于所需之量。
因为引进了昂贵的机器设备—为折旧费的分摊,而提高稼动率,生产过多的产品。
M u d a 二:存货的Muda成品、半成品、零件及物料的存货,是不会产生任何附加价值的,反而增加了营运的成本;因为占用了空间,需要额外的机器及设施,例如:仓库、堆高机以及电脑自动搬运系统。
此处,仓库又需要额外的人员来操作及管理。
多余的库存品又积满灰尘,是没有附加价值的,其质量随着时间而腐化。
更糟的是,会因遭逢火灾或其他灾难而化为灰烬。
如果没有存货的 M u d a,就可以避免许多浪费。
存货是由生产过多所造成的。
如果说制造过多是罪恶的话,那么存货就要视为被击毙的个人。
不幸的是,我们都知道管理人员若没有“足够的库存”,夜晚就难以入眠。
存货有时被比作为隐藏问题的水库。
当库存的水位高涨时,管理者就感受不到问题的严重性,像质量的问题、机器故障、及员工缺勤,也因此而失去了改善的机会。
需消除的九大浪费

需消除的九大浪费
【说明】提出需消除的这九大浪费源自日本丰田提出的著名七大浪费,不同在于:后者限于生产车间与仓储系统里的动作与物料方面,重新提出的这九大浪费则尽量覆盖工厂全员、全过程、全方位,除了动作与物料方面,还将工具、流程、组织、信息、思考等方面需消除的浪费包括了,同时试图利用价值工程的原理消除浪费。
欢迎各位有识之士对此进一步提出完善、指正意见、建议。
1.不合适动作和无意义担忧、评判的浪费
2.闲置、等待与虚度的浪费
3.物的搬运与信息传递、沟通不畅的浪费
4.重复与多余的浪费
5.库存与停滞的浪费
6.改错、返工与制造新问题的浪费
7.过度加工与过于超值的浪费
8.不合适职责权分工和未采用合适工具、流程的浪费
9.没有合适思考、有效开发和充分利用创造力的浪费。
消除九大浪费

附件2:练习转圈观察
练习的目的是观察有哪些工作属于九种浪费 学习者站在一个事先确定了地点和范围大小的圆圈内,观察1-8小时,他只能在这个圆圈中移动。 在这段时间里,他能以360度的视角观察周围的操作过程,记录下来他看到的浪费现象。 他的任务是对所有的东西都要提出质疑。 随着观察的深入,他看到的越来越细。练习结束时,就能看得很深入的细节。 在这个过程中,先不要寻求问题的答案或解决的办法。
动作的浪费是指在生产过程中,员工所有拿取零件、工具、夹具和获取信息,机器或人为了抓
取零件及启动操作而进行的一切不创造价值的移动或动作。因此这些动作都要避免,或减少到最低
程度。
现象举例
措施举例
行走距离远 零件没有放在20-50cm的范围内 员工做了很多身体的动作 拎/扛/背着零件/工具/文件 人/设备的空行程 机器人的运行轨迹 在岗位上寻找零件或工具
• 目标:降至最低
消除浪费
浪费的定义
错误的做法
正确的做法
目的是:提高创造价值比例
消除浪费
意义和目的:
• 提高创造价值比例 • 降低成本 • 减少通过时间
意义和目的
消除浪费
步骤:
一、识别浪费
• 认识九种浪费 • 实际观察:现场观察或录像,反复观察
二、消除浪费
• 解决问题的技术 • 运用方法模块
步骤
如:螺钉拧紧,铆接,焊接,定位 焊,结合/接缝,用卡扣联接,把零 件用线夹/卡扣夹上,加工零件,设 计零件,必要的检查等 • 目标:提高这部分工作占的比例
隐含的浪费
▪ 不能带来增值的工作,但在一 定条件下必须做的工作 例如:零件运输,拿取工具, 放置零件,行走,工位器具的 搬运,准备零件,必要的检查 等
生产现场管理八大浪费

生产现场管理八大浪费生产现场管理八大浪费1、时间的浪费1)缺乏适当的计划,使人员在换规格时产生等待,或停工待料。
2)班组长未能彻底了解其所接受之命令与指示。
3)缺乏对全天工作内容的认识。
4)对班组长的命令或指示不清楚。
5)未能确实督导工具、材料、小装置等应放置于一定之处所。
6)不应加班的工作,造成加班。
7)未要求员工准时开始工作,松于监督。
8)拖延决策。
9)班组长本身不必要的请假与迟到或不守时。
10)迟交报告。
11)未检查每一工作是否供给合适的工具与装配。
12)放任员工故意逃避他们能作的工作。
13)需要的人员不足。
14 )保有太多冗员。
15)拙于填写报告及各种申请表格。
16)纵容员工养成聊天、擅离工作岗位、浪费时间之坏习惯。
17)疏于查问与改正员工临时旷职及请假的原因。
2、创意的浪费1)未能倾听员工的建议。
2)未能鼓励员工多提建议。
3)未充分向其它部门(如生技等)请教。
4)未考虑或指定适当人员处理所有有用的提案。
5)未能从会议中获取有益的意见。
6)在各种问题上不能广听部属的意见。
7) 不能广泛的研讯本身工作与业务之有关方法。
8)未询问新进人员过去之工作经验,以获取有益的意见。
3、材料与供应品的浪费?1)督导不良,造成材料的浪费。
a.对新人指导不够。
b.指派新工作时未充分指导。
c.蓝图或草图破损、难懂、看错、标准未及时更正、或自作主张。
d.机械故障或未调整好。
e.未对每一工序检查材料使用情形,(标准与差异分析)。
2)未让部属了解材料或供应品的价值。
3) 命令与指示不清。
4)纵容不良的物料搬运。
5)未注意部属的眼力与健康,造成不良品。
6)缺乏纪律,纵容粗心或不当的工作。
7) 容许部属用不适当的材料,如太好或太差。
8)未能追踪不良工作起自何人,以致不能纠正。
9)不能适才适用,特别是新人。
10)请领太多材料,多余却未办退料。
11)未请领正确的材料,用错材料。
12)未检查材料是否排列整齐,正确放置。
13)未能检查蒸气、水、气体、电和压缩空气等管路电线之裂开破损。
《降本增效——生产现场九大浪费精益解决方法》

降本增效——生产现场九大浪费精益解决方法课程背景:“减少一成浪费就等于增加一倍销售额”——大野耐一!具权威数据统计,在许多制造业企业中任何时刻都有85%的工人没有做增值工作:5%的人看不出来是在工作;25%的人正在等待着工作;30%的人正在为增加库存而工作;25%的人正在按照低效的标准或方法进行工作……在生产制造型企业,正确地减少不必要的浪费是降低生产成本、提升企业利润的关键!许多制造型企业的管理者,尤其是中基层管理者由于没有真正认识到在生产管理过程中哪些行为是在真正提升企业的效益、那些行为是给企业制造浪费,往往错误地在指挥下属努力给企业制造库存、浪费、增加成本而自己却一无所知。
《降本增效——生产现场九大浪费精益解决之道》课程,是宋曦老师根据15年制造业生产管理经验和6年生产管理咨询、培训经验以及对中国制造型企业的现状研究,专为制造企业精心打造的现场管理提升经典课程。
课程收益:●帮助企业挖掘平时没有认识到却又存在的种种浪费与损耗●帮助企业分析出现场巨大浪费与损耗的根本原因●帮助企业找出杜绝这些浪费与损耗最有效的根本对策●将生产九大浪费与精益生产结合讲解,系统讲解解决方案●彻底改变参加学习人员对生产过程浪费的认知与理解●帮助企业找到减少浪费、降低成本、增加千万效益的方法●帮助企业提升整体管理人员的管理意识与管理水平课程时间:2天,6小时/天课程对象:生产副总、部门经理、车间主任、班组长及其他与生产相关职员课程方式:课程讲授60%,视频与文字案例分析及互动研讨30%,实操练习10%第一讲:了解认知生产现场中的浪费1. 浪费的核心概念2. 浪费的识别过程方法1)精益价值流VSM分析图介绍2)三流分析:信息流、物料流、价值流3. 浪费的六大根源4. 浪费的解决目的1)降低成本2)增加效益视频案例&互动思考:《如此医院》片段分享5. 生产现场的九大浪费划分类别1)与物相关:生产过多、库存、搬运、加工2)与人相关:等待、不良品、动作、人工技能、管理第二讲:生产现场九大浪费之专项问题分析与改善手段九大浪费之一:生产过多浪费1. 生产过多的定义2. 生产过多原因与后果描述案例分析:某小家电企业生产过多图表分析3. 生产过多的浪费改善和消除1)提高人的操作技能2)技能必须“多能化”3)管理层教育与培训4)培养员工听从调动5)目视化标准化作业九大浪费之二:库存的浪费1. 库存的定义2. 库存浪费的原因分析与后果描述案例分析:某电机厂库房设置不合理带来的浪费分析案例分析:某小家电企业库存浪费分析3. 库存的浪费的改善和消除1)供应商的供货节拍化2)合理的领料退料机制3)尽量减少消除呆滞料4)产品品质提升与处理5)生产计划的合理安排九大浪费之三:搬运的浪费1. 搬运浪费的定义2. 搬运浪费的原因分析与后果描述3. 搬运的浪费改善和消除1)减少断点2)减少二次停顿3)合理设计路线4)合理安排生产计划5)改善搬运浪费的案例案例分析:某小家电企业断点合并与流水线合并案例分析九大浪费之四:加工的浪费1. 加工浪费的定义2. 加工浪费的原因分析与后果描述3. 加工的浪费改善和消除1)制定合理的产品工艺标准2)进行工序作业重组或合并3)改善工装夹具匹配合理性4)使用改造或增加生产设备课堂案例&互动思考:某上海纺织品企业减少加工浪费九大浪费之五:等待的浪费1. 等待浪费的定义2. 等待浪费的原因分析与后果描述3. 等待浪费改善和消除1)合理的给每位员工分配作业量2)提高设备的保障力,降低设备的损坏率3)物料的数量与品质得到保障4)根据生产与现场的实际情况改进布局5)管理人员提前工作与做准备案例分析:某上海纺织品企业减少等待浪费。
浪费检查表
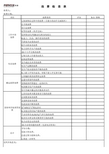
检查人:项目
浪费类型评估备注/事例
1.取放物品过程中的浪费(尽量小的动作完成取料)
2.寻找浪费
3.行走浪费
4.等待浪费(两手空闲)
5.伸背动作/弯腰动作/转身角度大
6.返工,次品,操作错误的浪费
7.重复不必要的动作
8.作业准备的浪费
9.只用单手生产的浪费
10.左右手交换的浪费
1.每天的工作量变动很大
2.传送带浪费
3.半成品及库存的浪费
4.生产过剩的浪费
5.生产线未能取的平衡的浪费
6.上游工序发生延误,导致下游工序无事可做
1.传输距离的浪费转运浪费
2.遗失零部件的浪费
3.物流的停留超过一定的时间
4.因搜寻而产生的浪费
5.可否减少搬运的次数或者动作
1.没有处理弃置设备而引致的浪费
2.闲置设备的浪费
3.故障设备的浪费
4.流水线中断的浪费
5.“切削空气"情况存在
6.未能达到目标产量的浪费
7.未有善用水/油/电/气所引致的浪费
8.没有合理安排及整理所引致的浪费
9.非必要会议的浪费
10.非必要问题的浪费(包括电话咨询)评估分数:
3.能立即改善;
2.通过努力能够改善;
1.需进一步研究
说明其他意见:总计浪 费 检 查 表
工作中的
浪费布局浪费搬运流程浪费设备和其他类型浪费。
生产现场浪费排查计划表

生产现场浪费排查计划表英文回答:Production Site Waste Reduction Plan.Objective:To identify and eliminate waste in production processes to improve efficiency and reduce costs.Scope:This plan applies to all production operations at the facility.Methodology:The following steps will be taken to identify and eliminate waste:1. Waste Identification:Conduct lean manufacturing assessments and process mapping to identify non-value-adding activities.Collect data on defects, rework, machine downtime, and inventory levels.Observe production processes and interview operators to identify bottlenecks and inefficiencies.2. Waste Analysis:Categorize waste into different types, such as overproduction, waiting, transportation, and inventory.Determine the root causes of waste and analyze their impact on production.3. Waste Reduction Strategies:Implement process improvements to eliminateunnecessary steps and reduce cycle times.Optimize production planning to avoid overproduction and minimize inventory levels.Improve maintenance schedules and reduce machine downtime.Train operators on lean principles and waste reduction techniques.4. Implementation:Develop and implement standard work procedures to ensure consistency and reduce errors.Provide regular feedback to operators on their progress and areas for improvement.Monitor key performance indicators (KPIs) to track progress and identify areas for further improvement.Timeline:The waste reduction plan will be implemented over a period of three years. The first six months will be dedicated to waste identification and analysis. The following six months will focus on developing and implementing waste reduction strategies. The final two years will be used to monitor progress, make adjustments, and sustain the improvements.Benefits:The implementation of this waste reduction plan is expected to result in the following benefits:Reduced production costs.Improved production efficiency.Reduced inventory levels.Increased quality and reduced defects.Enhanced customer satisfaction.Responsibility:The production manager is responsible for the implementation and maintenance of this waste reduction plan. All production employees are expected to activelyparticipate in the waste reduction efforts.Review and Revision:This plan will be reviewed and revised annually to incorporate lessons learned and ensure its continued effectiveness.中文回答:生产现场浪费排查计划表。
生产现场管理的151种浪费
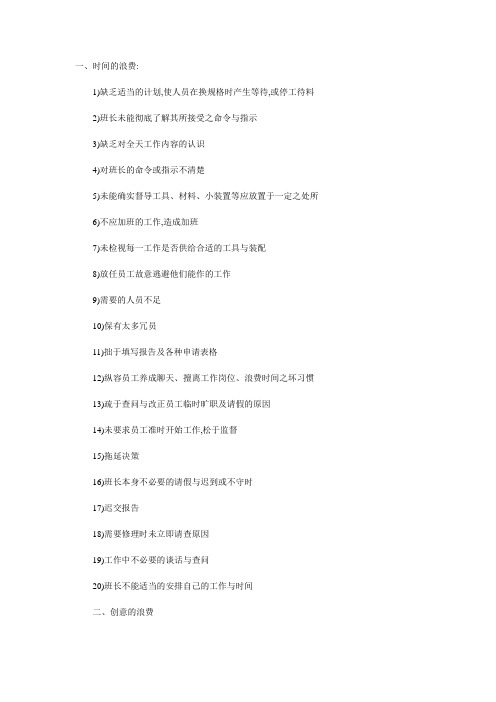
一、时间的浪费:1)缺乏适当的计划,使人员在换规格时产生等待,或停工待料2)班长未能彻底了解其所接受之命令与指示3)缺乏对全天工作内容的认识4)对班长的命令或指示不清楚5)未能确实督导工具、材料、小装置等应放置于一定之处所6)不应加班的工作,造成加班7)未检视每一工作是否供给合适的工具与装配8)放任员工故意逃避他们能作的工作9)需要的人员不足10)保有太多冗员11)拙于填写报告及各种申请表格12)纵容员工养成聊天、擅离工作岗位、浪费时间之坏习惯13)疏于查问与改正员工临时旷职及请假的原因14)未要求员工准时开始工作,松于监督15)拖延决策16)班长本身不必要的请假与迟到或不守时17)迟交报告18)需要修理时未立即请查原因19)工作中不必要的谈话与查问20)班长不能适当的安排自己的工作与时间二、创意的浪费1)未能倾听员工的建议2)未能鼓励员工多提建议3)在各种问题上不能广听部属的意见4)不能广泛的研讯本身工作与业务之有关方法5)未询问新进人员过去之工作经验,以获取有益的意见6)未充分向其它部门(如生技等)请教7)未考虑或指定适当人员处理所有有用的提案8)未能从会议中获取有益的意见9)管理机能不好三、材料与供应品的浪费1)督导不良,造成材料的浪费a.对新人指导不够b.指派新工作时未充分指导c.蓝图或草图破损、难懂、看错、标准未及时更正、或自作主张d.机械故障或未调整好e.未对每一工序检查材料使用情形,(标准与差异分析)2)未让部属了解材料或供应品的价值3)命令与指示不清4)纵容不良的物料搬运5)未注意部属的眼力与健康,造成不良品6)缺乏纪律,纵容粗心或不当的工作7)容许部属用不适当的材料,如太好或太差8)未能追踪不良工作起自何人,以致不能纠正9)不能适才适用,特别是新人10)请领太多材料,多余却未办退料11)未请领正确的材料,用错材料12)未检查材料是否排列整齐,正确放置13)未能检查蒸气、水、气体、电和压缩空气等管路电线之裂开破损14)纵容部属私事使用油、压缩空气、小工具、化学药品等15)让不良材料当良品流入制程16)缺乏有效系统防止材料外流、避免损失或被偷17)可再用的材料当废料处理18)纵容浪费或滥用以下供应品:扫把、文具、油布、灯泡、水管等19)产生不良未立即停止生产四、机器与设备的浪费1)缺乏工作计划,使所有可用的机器未获得充分且适合的利用2)疏于检查机器,使其保持良好状态及避免故障3)班长缺乏正确使用机器的知识,不了解各种机器的能力4)未定期检查—绳、皮带、链条、输送带、润滑系统等5)杀鸡用牛刀,小工作用大机械6)在保养、修理、油漆工作上缺乏与保养部门协调7)闲置机器未加保养,任受潮湿、脏物、灰尘、锈等侵蚀8)缺乏定期清洁,机器不洁9)所有转动零件未检查是否有适当的润滑10)应修理之处未立即办理11)机器没有适当的操作说明书12)缺乏良好纪律以避免机器设备的滥用13)纵容部属用「不当方法」修理机器14)领班不知机器与设备的最新型式15)未促使部属注意机器的价值与情况16)滥用小机器作笨重工作17)该报废的机器仍加以修理,比买新机花了更多的费用18)可修理的机器却报废19)没有效率管理之数据(机械效率)五、人力的浪费1)由于下列原因,无法控制有能力部属之人事变动a.未评估员工变动之直接与间接成本b.“管”得太多,聪明的领导却太少c.对纪律要求「太严」或「太松」d.能做到的「承诺」,却未遵守e.许下不能作到的「承诺」,如加薪或升迁f.无充分理由而解雇人,不应使用解雇作为一种处罚g.强留部属在他极端不喜欢的工作上h.对待部属不公正i.部属争吵时,偏袒一方j.对一个部属批语其它的部属(指桑骂槐)k.未能查出自愿离职部属之理由l.不能向部属正确说明公司的目标与政策m.在员工调薪上,班长未参与n.班长的权威不好2)不能使新进人员充分发挥其生产力a.没有以亲切、帮助的态度接纳新员工b.对新进人员没给予安全的工作指导c.未让新进人员了解全天的工作及其它内容d.没有选择够格的人配合工作e.对学习速度慢的人没有耐心f.未促使其它部属对新人表示友善、帮助的态度g.未尽可能的接近新人h.没有告知新人,工厂生活情况与规划,如安全、发薪日期、厕所、饮用水、浴室等i.未安排完整的训练计划3)未使部属尽其所能a.未指导部属如何做好工作b.未尽可能的说明工作,使其发生兴趣c.未对部属的进步与个人生活表示关心d.没有容纳部属错误的雅量e.未注意部属的力量与个性,适当的指派工作f.未研究部属个人的不同,以发挥他最大的潜力g.纵容部属派系存在或组成小圈圈h.评价一个人只重资格、种族、宗教、关系、地域等i.明知某人的心理或生理不适当,却未加调动j.生病的部属仍让他工作k.未给予需要的协助l.当可能且适当的时间,却未给予升迁m.未考虑影响薪资与工作条件的问题n.未训练一个侯补者4)欠缺对标准工时教导之概念5)欠人员效率管理之数据六、意外事故的浪费1)未认识到预防意外事故是工作的一部份2)未对全体部属彻底说明安全事务3)未给机器装上安全防护,并使确保有效4)纵容在工作场所滥用安全防护5)未在适当处所标上危险记号,并保持干凈与易读6)未彻底了解意外事故的间接成本7)物料放置不善8)不了解构成意外危险的成因9)未保存事故记录,并未加分析与应用10)未建立良好的安全范例11)没有定期与切实的检查安全12)未能持久地执行安全规则13)工作人员缺乏必要的安全装配:如手套、安全带、电焊护面等14)管理人员未认清其安全责任与事故责任15)不能激发与保持部属的安全意识以防止事故16)未与政府或保险公司之安全检查员配合七、缺乏合作的浪费1)未与a.其它管理人员或部门合作b.事务人员、工程师、业务员、人事等合作2)未确实了解公司政策并向部属解释3)不能聪明地处理谣言4)推诿责任给其它班长、部属或主管5)未适当地将部属的意见反应给主管6)纵容不满的员工煽动反抗公司的作法7)管理人员未能给予那些尚不普及的公司规章予以全力支持8)未能鼓舞部属间的友爱与合作的气氛9)管理人员在本部门内轻率地批评公司政策与私人10)在公司之教育活动上未与管理阶层诚心全力合作,包括学徒训练、公布栏、员工通讯、提案制度等八、空间的浪费整理整顿1)材料之不适排放与储存2)未充分注意材料在工厂中的途程计划3)机械与其它永久性设备之错误安置4)纵容部属丢置手工具、梯子、手推车等在过道上,不能保持走道清洁者5)废料未报废6)橱柜、油筒、材料供应处等放置于不便之处7)纵容不用的机器与设备占据重要的空间8)由于未及时修理楼板、屋顶等以致需要的空间未加利用9)照明不足,形成黑点,死角10)单位内布置不良,不能保持条理11)工作场所放不需要的物料,仓库与工场不分12)未重视事物整顿的重要13)未培养及督导物品用完要归、定位14)未彻底执行定期(每日、每周、每月)清理项目,以永久保持。
生产现场八大浪费分析改善对应表
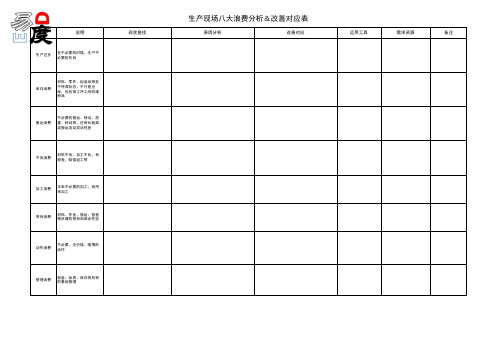
浪费说明现状查找原因分析改善对应运用工具需求资源备注
生产过多在不必要的时候,生产不必要的东西
库存浪费材料、零件、组装品等处于停滞状态,不只是仓库,也包括工序之间的堆积品
搬运浪费不必要的搬运、移动、放置、转动等,还有长距离或搬运流动灵活性差
不良浪费材料不良、加工不良,有检查,赔偿返工等
加工浪费本来不必要的加工,而用来加工
等待浪费材料、作业、搬运、检查等所谓的等待和闲余作业
动作浪费不必要、无价值、缓慢的动作
管理浪费检查、品质、库存等所有
的事后管理
生产现场八大浪费分析&改善对应表。
工厂中常见的八大浪费
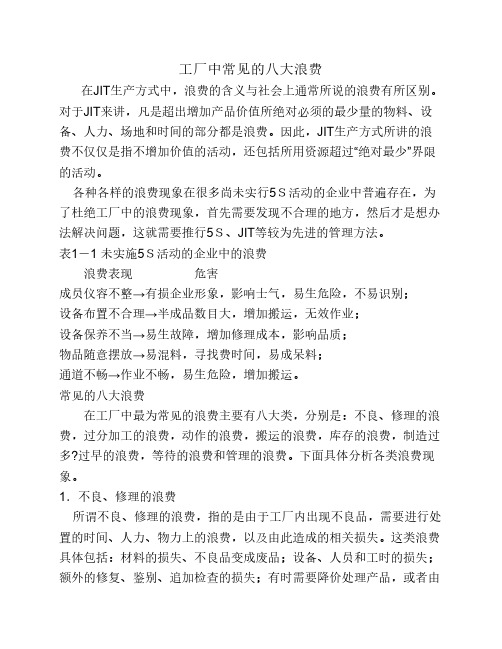
工厂中常见的八大浪费在JIT生产方式中,浪费的含义与社会上通常所说的浪费有所区别。
对于JIT来讲,凡是超出增加产品价值所绝对必须的最少量的物料、设备、人力、场地和时间的部分都是浪费。
因此,JIT生产方式所讲的浪费不仅仅是指不增加价值的活动,还包括所用资源超过“绝对最少”界限的活动。
各种各样的浪费现象在很多尚未实行5S活动的企业中普遍存在,为了杜绝工厂中的浪费现象,首先需要发现不合理的地方,然后才是想办法解决问题,这就需要推行5S、JIT等较为先进的管理方法。
表1-1 未实施5S活动的企业中的浪费浪费表现危害成员仪容不整→有损企业形象,影响士气,易生危险,不易识别;设备布置不合理→半成品数目大,增加搬运,无效作业;设备保养不当→易生故障,增加修理成本,影响品质;物品随意摆放→易混料,寻找费时间,易成呆料;通道不畅→作业不畅,易生危险,增加搬运。
常见的八大浪费在工厂中最为常见的浪费主要有八大类,分别是:不良、修理的浪费,过分加工的浪费,动作的浪费,搬运的浪费,库存的浪费,制造过多?过早的浪费,等待的浪费和管理的浪费。
下面具体分析各类浪费现象。
1.不良、修理的浪费所谓不良、修理的浪费,指的是由于工厂内出现不良品,需要进行处置的时间、人力、物力上的浪费,以及由此造成的相关损失。
这类浪费具体包括:材料的损失、不良品变成废品;设备、人员和工时的损失;额外的修复、鉴别、追加检查的损失;有时需要降价处理产品,或者由于耽误出货而导致工厂信誉的下降。
2.加工的浪费加工的浪费也叫过分加工的浪费,主要包含两层含义:第一是多余的加工和过分精确的加工,例如实际加工精度过高造成资源浪费;第二是需要多余的作业时间和辅助设备,还要增加生产用电、气压、油等能源的浪费,另外还增加了管理的工时。
3.动作的浪费动作的浪费现象在很多企业的生产线中都存在,常见的动作浪费主要有以下12种:两手空闲、单手空闲、作业动作突然停止、作业动作过大、左右手交换、步行过多、转身的角度太大,移动中变换“状态”、不明技巧、伸背动作、弯腰动作以及重复动作和不必要的动作等,这些动作的浪费造成了时间和体力上的不必要消耗。
成本控制培训_九大浪费(PPT46页)
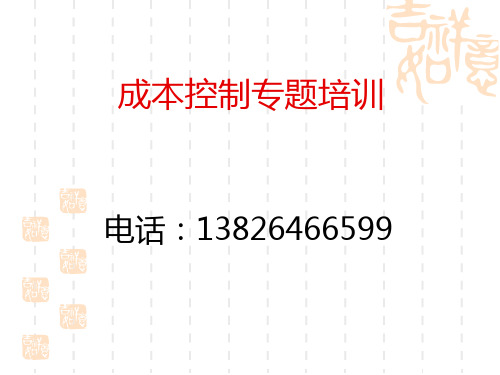
•生产线布置不当,物流混乱 •设备配置、保养不当 •生产计划安排不当 •工序间生产能力不平衡 •材料未及时到位 •管理控制点过多,忙于应付 •品质不良
对策:
•合理安排生产 •合理配置人员、均衡化生 产 •快速流动、确保衔接 •品质、欠料与异常的处理 •自动化及设备保养加强 •实施目视管理
•加注强进意料:控制
5.加工上的浪费
原因:
•加工、操作顺序检讨不足 •作业内容与工艺检讨不足 •模夹治具不良 •标准化不彻底 •材料问题,内部返工等
对策:
•技术设计合理化 •作业内容与顺序的修正 •夹治具改善及自动化 •标准作业的贯彻 •严格控制来料的品质 •生产过程员工献计献策、 改良工艺、合理化建议
注意:
•了解同行的技术发展 •公司各部门对于改善的共 同参与及持续不断的改善
成本控制专题培训
电话:13826466599
浪费乃万恶 之源!!!
动作改善、作业流程改善、物流改善、设 备模夹治具改善、品质改善、管理改善等
九大浪费
动作标准化、作业流程标准化、操作流程 标准化、包装运输标准化等
整理、整顿、清扫、清洁、素养、安全
成本管理看板
何谓浪费:
不产生任何价值或附加价值的动 作、方法、行为和计划等,均为 浪费!
用不同的评判标准去判断一个 动作、行为、方法或计划时,所得 到的浪费程度都会不同。
现场活动包括“有附加价值的”和“没有附加价值的” 活动,那些不产生附加价值的活动应坚决予以消除.
1.制造过多的浪费 2.等待的浪费 3.搬运的浪费 4.材料的浪费 5.加工的浪费 6.库存的浪费 7.动作的浪费 8.制作不良的浪费 9.时间的浪费
•未彻底使用完的浪费
现场浪费的检查表

6
是否适度引入了防呆方案
7
是否存在对人的潜在危险
备注:
工站名:
观察日期: 观察员:
1
桌椅对员工而言是否舒适
2
照明及温度是否合作
六动作浪费
3
是否可以增加工装夹具
4
是否存在动作等级五
5
是否可以降低动作等级
6
是否可以降低动作幅度
7
作业动作顺序是否有明确规定
1
员工作业与作业指导书是否一致
2
作业指导书是否反应了产品特性
七不良浪费
3
作业指导书是否是优化过的规定
4
工程师是否清楚当前稳态
5
是否及时对数据进行解析并预防
6
计划不当造成员工的等待
7
换品种生产导致等待时间超过10分钟
三搬运
1
零件、工具等,尽量放置于近处
浪费
2
机器与机器间的距离可以缩短吗
(产线)
3
能够缩短搬运距离吗
4
是否有不必要的周转
5
是否可运用传送带或重力(溜滑梯)
6
是否有逆流或孤岛式作业
7
人员走动是否过多
1
是否清晰产品的最终用途
2
是否有效管控产品的特性
类别
序
点检内容
现状
措施
1
是否按计划生产
2
是否有堆积现象
一过量生产
3
生产速度是否均匀
4
物料是否及时供应
5
是否及时自检等手段控制质量
6
生产批量是否合理
7
是否是产线中的瓶颈
பைடு நூலகம்
二等待
1
由于前工序供应不及导致等待
生产现场管理中常见的浪费现象

生产现场管理中常见的浪费现象第一篇:生产现场管理中常见的浪费现象生产现场管理中常见的浪费现象摘要:企业再起成长过程中,常常会经历各种不同的阶段和遇到不同层面的与多问题点。
对于企业来说,发展战略是成功的坚实基础,但是失败往往是解决不了自身出现的诸多问题,其中,生产现场浪费现象是让很多企业都头疼也是很关键的一个问题。
所以解决生产现场浪费问题显得尤为重要。
所有工作的开展都离不开具体的时间和空间,由此便构成了一个有一个具体的现场。
童声,所有的工作都离不开具体的成果和价值,当然,这就需要在特定的现场中完成特定的管理。
现场管理可使企业全面改善经营环境,提高整体经营素质。
它讲究在低成本高效率的前提下,开展企业全方位的环境整洁,目的是使自然环境美观化,作业环境合理化,内外经营环境全面优化,从而起到鼓舞士气,增强退队协调作战能力的作用,是企业由营销产品走向营销企业直至进行营销企业文化的境界,使各方面达到最优境界。
换言之,也就是企业通过各方面的现场管理最终达到一个整洁.秩序.美观.效率.成本.充满时期的整体工作范围。
如果不能对管理工作中的浪费形成共识,齐抓共管,是很难持续有效发展下去的,管理工作中的浪费一旦在某种程度上被消除,则可能会出现集合数级的放大效应,因此,我们要鼓起勇气,从消除点滴的管理做起,想着经营管理革新的目标一步一步坚定不移的走下去。
关键字:生产现场管理中常见的浪费现象,生产现场中浪费的影响解决方法企业常见的几个浪费现象 1.等待浪费等待并非加工过程,不能改变物料的形状、尺寸、性质和状态从而改变韧料的功能,所以等待不创造价值。
待工和待料是两种最常见的等待情形。
常见的等待现象有:物料供应或前工序能力不足造成待料,监视设备作业造成员工作业停顿,设备故障造成生产停滞,质量问题造成停工,型号切换造成生产停顿。
减少方法:1)生产资源的调合,减少人员等待。
2)调整作业线的平衡。
3)部门之间合作,更快。
造成等待的常见原因有:流水线能力不平衡,计划不合理,设备维护不到位,物料供应不及时等。
发现浪费检查表
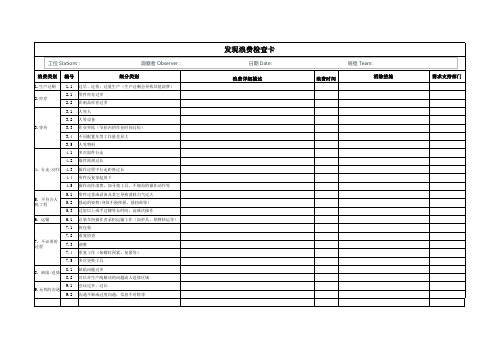
观察者 Observer:
浪费类别 编号
细分类别
1.生产过剩 1.1 过早、过快、过量生产(生产过剩会导致其他浪费)
2.库存
2.1 零件库存过多 2.2 在制品库存过多
3.1 人等人
3.2 人等设备
3.型工作量差异大
6. 运输
6.1 总装车间操作者承担运输工作(如护具、铭牌转运等)
7.1 拆包装
7. 不必要的 过程
7.2 重复检查 7.3 调整 7.4 重复工作(如螺钉预紧,复紧等)
7.5 多次更换工具
8.1 缺陷问题过多 8. 缺陷/返修
8.2 可以在生产线解决的问题流入返修区域
9.1 会议过多,过长 9.无效的沟通
3.5 人等物料
4.1 多次取件行走
4.2 取件距离过长
4. 行走/动作 4.3 操作过程中行走距离过长
4.4 零件反复拿起放下
4.5 操作动作浪费,如寻找工具、不规范的操作动作等
5. 不符合人 机工程
5.1 零件过重或设备及其它导致消耗力气过大 5.2 强迫的姿势(身体不能伸展、强扭曲等) 5.3 过肩以上或手过膝等长时间、高频次操作
9.2 沟通不够或过度沟通,信息不对称等
发现浪费检查卡
日期 Date: 浪费详细描述
浪费时间
班组 Team: 消除措施
需求支持部门
生产现场管理的151种浪费

一、时间的浪费:1) 缺乏适当的计划,使人员在换规格时产生等待,或停工待料2) 班长未能彻底了解其所接受之命令与指示3) 缺乏对全天工作内容的认识4) 对班长的命令或指示不清楚5) 未能确实督导工具、材料、小装置等应放置于一定之处所6) 不应加班的工作,造成加班7) 未检视每一工作是否供给合适的工具与装配8) 放任员工故意逃避他们能作的工作9) 需要的人员不足10) 保有太多冗员11) 拙于填写报告及各种申请表格12) 纵容员工养成聊天、擅离工作岗位、浪费时间之坏习惯13) 疏于查问与改正员工临时旷职及请假的原因14) 未要求员工按时开始工作,松于监督15) 拖延决策16) 班长本身不必要的请假与迟到或不守时17) 迟交报告18) 需要修理时未立即请查原因19) 工作中不必要的谈话与查问20) 班长不能适当的计划自己的工作与时间二、创意的浪费1) 未能倾听员工的建议2) 未能鼓励员工多提建议3) 在各种问题上不能广听部属的意见4) 不能广泛的研讯本身工作与业务之有关方法5) 未询问新进人员过去之工作经验,以获取有益的意见6) 未充分向其它部门(如生技等)请教7) 未考虑或指定适当人员处理所有有用的提案8) 未能从会议中获取有益的意见9) 管理机能不好三、材料与供应品的浪费1) 督导不良,造成材料的浪费a. 对新人指导不够b. 指派新工作时未充分指导c. 蓝图或草图破损、难懂、看错、标准未及时更正、或自作主张d. 机械故障或未调整好e. 未对每一工序检查材料使用情形,(标准与差异分析)2) 未让部属了解材料或供应品的价值3) 命令与指示不清4) 纵容不良的物料搬运5) 未注意部属的眼力与健康,造成不良品6) 缺乏纪律,纵容粗心或不当的工作7) 容许部属用不适当的材料,如太好或太差8) 未能追踪不良工作起自何人,以致不能纠正9) 不能适才适用,特别是新人10) 请领太多材料,多余却未办退料11) 未请领正确的材料,用错材料12) 未检查材料是否排列整齐,正确放置13) 未能检查蒸气、水、气体、电和压缩空气等管路电线之裂开破损14) 纵容部属私事使用油、压缩空气、小工具、化学药品等15) 让不良材料当良品流入制程16) 缺乏有效系统防止材料外流、避免损失或被偷17) 可再用的材料当废料处理18) 纵容浪费或滥用以下供应品:扫把、文具、油布、灯泡、水管等19) 产生不良未立即停止生产四、机器与设备的浪费1) 缺乏工作计划,使所有可用的机器未获得充分且适合的利用2) 疏于检查机器,使其保持良好状态及避免故障3) 班长缺乏正确使用机器的知识,不了解各种机器的能力4) 未定期检查—绳、皮带、链条、输送带、润滑系统等5) 杀鸡用牛刀,小工作用大机械6) 在保养、修理、油漆工作上缺乏与保养部门协调7) 闲置机器未加保养,任受潮湿、脏物、灰尘、锈等侵蚀8) 缺乏定期清洁,机器不洁9) 所有转动零件未检查是否有适当的润滑10) 应修理之处未立即办理11) 机器没有适当的操作说明书12) 缺乏良好纪律以避免机器设备的滥用13) 纵容部属用「不当方法」修理机器14) 领班不知机器与设备的最新型式15) 未促使部属注意机器的价值与情况16) 滥用小机器作笨重工作17) 该报废的机器仍加以修理,比买新机花了更多的费用18) 可修理的机器却报废19) 没有效率管理之数据(机械效率)五、人力的浪费1) 由于下列原因,无法控制有能力部属之人事变动a. 未评估员工变动之直接与间接成本b. “管”得太多,聪明的领导却太少c. 对纪律要求「太严」或「太松」d. 能做到的「承诺」,却未遵守e. 许下不能作到的「承诺」,如加薪或升迁f. 无充分理由而解雇人,不应使用解雇作为一种处罚g. 强留部属在他极端不喜欢的工作上h. 对待部属不公正i. 部属争吵时,偏袒一方j. 对一个部属批语其它的部属(指桑骂槐)k. 未能查出自愿离职部属之理由l. 不能向部属正确说明公司的目标与政策m. 在员工调薪上,班长未参与n. 班长的权威不好2) 不能使新进人员充分发挥其生产力a. 没有以亲切、帮助的态度接纳新员工b. 对新进人员没给予安全的工作指导c. 未让新进人员了解全天的工作及其它内容d. 没有选择够格的人配合工作e. 对学习速度慢的人没有耐心f. 未促使其它部属对新人表示友善、帮助的态度g. 未尽可能的接近新人h. 没有告知新人,工厂生活情况与规划,如安全、发薪日期、厕所、饮用水、浴室等i. 未计划完整的训练计划3) 未使部属尽其所能a. 未指导部属如何做好工作b. 未尽可能的说明工作,使其发生兴趣c. 未对部属的进步与个人生活表示关心d. 没有容纳部属错误的雅量e. 未注意部属的力量与个性,适当的指派工作f. 未研究部属个人的不同,以发挥他最大的潜力g. 纵容部属派系存在或组成小圈圈h. 评价一个人只重资格、种族、宗教、关系、地域等i. 明知某人的心理或生理不适当,却未加调动j. 生病的部属仍让他工作k. 未给予需要的协助l. 当可能且适当的时间,却未给予升迁m. 未考虑影响薪资与工作条件的问题n. 未训练一个侯补者4) 欠缺对标准工时教导之概念5) 欠人员效率管理之数据六、意外事故的浪费1) 未认识到预防意外事故是工作的一部份2) 未对全体部属彻底说明安全事务3) 未给机器装上安全防护,并使确保有效4) 纵容在工作场所滥用安全防护5) 未在适当处所标上危险记号,并保持干凈与易读6) 未彻底了解意外事故的间接成本7) 物料放置不善8) 不了解构成意外危险的成因9) 未保存事故记录,并未加分析与应用10) 未建立良好的安全范例11) 没有定期与切实的检查安全12) 未能持久地执行安全规则13) 工作人员缺乏必要的安全装配:如手套、安全带、电焊护面等14) 管理人员未认清其安全责任与事故责任15) 不能激发与保持部属的安全意识以防止事故16) 未与政府或保险公司之安全检查员配合七、缺乏合作的浪费1) 未与a. 其它管理人员或部门合作b. 事务人员、工程师、业务员、人事等合作2) 未确实了解公司政策并向部属解释3) 不能聪明地处理谣言4) 推诿责任给其它班长、部属或主管5) 未适当地将部属的意见反应给主管6) 纵容不满的员工煽动反抗公司的作法7) 管理人员未能给予那些尚不普及的公司规章予以全力支持8) 未能鼓舞部属间的友爱与合作的气氛9) 管理人员在本部门内轻率地批评公司政策与私人10) 在公司之教育活动上未与管理阶层诚心全力合作,包括学徒训练、公布栏、员工通讯、提案制度等八、空间的浪费整理整顿1) 材料之不适当排放与储存2) 未充分注意材料在工厂中的途程计划3) 机械与其它永久性设备之错误安置4) 纵容部属丢置手工具、梯子、手推车等在过道上,不能保持走道清洁者5) 废料未报废6) 橱柜、油筒、材料供应处等放置于不便之处7) 纵容不用的机器与设备占据重要的空间8) 由于未及时修理楼板、屋顶等以致需要的空间未加利用9) 照明不足,形成黑点,死角10) 单位内布置不良,不能保持条理11) 工作场所放不需要的物料,仓库与工场不分12) 未重视事物整顿的重要13) 未培养及督导物品用完要归、14) 未彻底执行定期(每日、每周、每月)清理项目,以永久保持随机读管理故事:《都是玩笑惹的祸》杂志《读者》上曾讲过这样一个故事:军犬黑子目光如电,精神饱满,威风凛凛,每逢甄别嫌疑犯时总能让做贼者先心虚起来。
生产现场管理的151种浪费

生产现场管理的151种浪费一、时间的浪费:1) 缺乏适当的计划,使人员在换规格时产生等待,或停工待料2) 班长未能彻底了解其所接受之命令与指示3) 缺乏对全天工作内容的认识4) 对班长的命令或指示不清楚5) 未能确实督导工具、材料、小装置等应放置于一定之处所6) 不应加班的工作,造成加班7) 未检视每一工作是否供给合适的工具与装配8) 放任员工故意逃避他们能作的工作9) 需要的人员不足10) 保有太多冗员11) 拙于填写报告及各种申请表格12) 纵容员工养成聊天、擅离工作岗位、浪费时间之坏习惯13) 疏于查问与改正员工临时旷职及请假的原因14) 未要求员工准时开始工作,松于监督15) 拖延决策16) 班长本身不必要的请假与迟到或不守时17) 迟交报告18) 需要修理时未立即请查原因19) 工作中不必要的谈话与查问20) 班长不能适当的安排自己的工作与时间二、创意的浪费1) 未能倾听员工的建议2) 未能鼓励员工多提建议3) 在各种问题上不能广听部属的意见4) 不能广泛的研讯本身工作与业务之有关方法5) 未询问新进人员过去之工作经验,以获取有益的意见6) 未充分向其它部门(如生技等)请教7) 未考虑或指定适当人员处理所有有用的提案8) 未能从会议中获取有益的意见9) 管理机能不好三、材料与供应品的浪费1) 督导不良,造成材料的浪费a. 对新人指导不够b. 指派新工作时未充分指导c. 蓝图或草图破损、难懂、看错、标准未及时更正、或自作主张d. 机械故障或未调整好e. 未对每一工序检查材料使用情形,(标准与差异分析)2) 未让部属了解材料或供应品的价值3) 命令与指示不清4) 纵容不良的物料搬运5) 未注意部属的眼力与健康,造成不良品6) 缺乏纪律,纵容粗心或不当的工作7) 容许部属用不适当的材料,如太好或太差8) 未能追踪不良工作起自何人,以致不能纠正9) 不能适才适用,特别是新人10) 请领太多材料,多余却未办退料11) 未请领正确的材料,用错材料12) 未检查材料是否排列整齐,正确放置13) 未能检查蒸气、水、气体、电和压缩空气等管路电线之裂开破损14) 纵容部属私事使用油、压缩空气、小工具、化学药品等15) 让不良材料当良品流入制程16) 缺乏有效系统防止材料外流、避免损失或被偷17) 可再用的材料当废料处理18) 纵容浪费或滥用以下供应品:扫把、文具、油布、灯泡、水管等19) 产生不良未立即停止生产四、机器与设备的浪费1) 缺乏工作计划,使所有可用的机器未获得充分且适合的利用2) 疏于检查机器,使其保持良好状态及避免故障3) 班长缺乏正确使用机器的知识,不了解各种机器的能力4) 未定期检查—绳、皮带、链条、输送带、润滑系统等5) 杀鸡用牛刀,小工作用大机械6) 在保养、修理、油漆工作上缺乏与保养部门协调7) 闲置机器未加保养,任受潮湿、脏物、灰尘、锈等侵蚀8) 缺乏定期清洁,机器不洁9) 所有转动零件未检查是否有适当的润滑10) 应修理之处未立即办理11) 机器没有适当的操作说明书12) 缺乏良好纪律以避免机器设备的滥用13) 纵容部属用「不当方法」修理机器14) 领班不知机器与设备的最新型式15) 未促使部属注意机器的价值与情况16) 滥用小机器作笨重工作17) 该报废的机器仍加以修理,比买新机花了更多的费用18) 可修理的机器却报废19) 没有效率管理之数据(机械效率)五、人力的浪费1) 由于下列原因,无法控制有能力部属之人事变动a. 未评估员工变动之直接与间接成本b. “管”得太多,聪明的领导却太少c. 对纪律要求「太严」或「太松」d. 能做到的「承诺」,却未遵守e. 许下不能作到的「承诺」,如加薪或升迁f. 无充分理由而解雇人,不应使用解雇作为一种处罚g. 强留部属在他极端不喜欢的工作上h. 对待部属不公正i. 部属争吵时,偏袒一方j. 对一个部属批语其它的部属(指桑骂槐)k. 未能查出自愿离职部属之理由l. 不能向部属正确说明公司的目标与政策m. 在员工调薪上,班长未参与n. 班长的权威不好2) 不能使新进人员充分发挥其生产力a. 没有以亲切、帮助的态度接纳新员工b. 对新进人员没给予安全的工作指导c. 未让新进人员了解全天的工作及其它内容d. 没有选择够格的人配合工作e. 对学习速度慢的人没有耐心f. 未促使其它部属对新人表示友善、帮助的态度g. 未尽可能的接近新人h. 没有告知新人,工厂生活情况与规划,如安全、发薪日期、厕所、饮用水、浴室等i. 未安排完整的训练计划3) 未使部属尽其所能a. 未指导部属如何做好工作b. 未尽可能的说明工作,使其发生兴趣c. 未对部属的进步与个人生活表示关心d. 没有容纳部属错误的雅量e. 未注意部属的力量与个性,适当的指派工作f. 未研究部属个人的不同,以发挥他最大的潜力g. 纵容部属派系存在或组成小圈圈h. 评价一个人只重资格、种族、宗教、关系、地域等i. 明知某人的心理或生理不适当,却未加调动j. 生病的部属仍让他工作k. 未给予需要的协助l. 当可能且适当的时间,却未给予升迁m. 未考虑影响薪资与工作条件的问题n. 未训练一个侯补者4) 欠缺对标准工时教导之概念5) 欠人员效率管理之数据六、意外事故的浪费1) 未认识到预防意外事故是工作的一部份2) 未对全体部属彻底说明安全事务3) 未给机器装上安全防护,并使确保有效4) 纵容在工作场所滥用安全防护5) 未在适当处所标上危险记号,并保持干凈与易读6) 未彻底了解意外事故的间接成本7) 物料放置不善8) 不了解构成意外危险的成因9) 未保存事故记录,并未加分析与应用10) 未建立良好的安全范例11) 没有定期与切实的检查安全12) 未能持久地执行安全规则13) 工作人员缺乏必要的安全装配:如手套、安全带、电焊护面等14) 管理人员未认清其安全责任与事故责任15) 不能激发与保持部属的安全意识以防止事故16) 未与政府或保险公司之安全检查员配合七、缺乏合作的浪费1) 未与a. 其它管理人员或部门合作b. 事务人员、工程师、业务员、人事等合作2) 未确实了解公司政策并向部属解释3) 不能聪明地处理谣言4) 推诿责任给其它班长、部属或主管5) 未适当地将部属的意见反应给主管6) 纵容不满的员工煽动反抗公司的作法7) 管理人员未能给予那些尚不普及的公司规章予以全力支持8) 未能鼓舞部属间的友爱与合作的气氛9) 管理人员在本部门内轻率地批评公司政策与私人10) 在公司之教育活动上未与管理阶层诚心全力合作,包括学徒训练、公布栏、员工通讯、提案制度等八、空间的浪费整理整顿1) 材料之不适当排放与储存2) 未充分注意材料在工厂中的途程计划3) 机械与其它永久性设备之错误安置4) 纵容部属丢置手工具、梯子、手推车等在过道上,不能保持走道清洁者5) 废料未报废6) 橱柜、油筒、材料供应处等放置于不便之处7) 纵容不用的机器与设备占据重要的空间8) 由于未及时修理楼板、屋顶等以致需要的空间未加利用9) 照明不足,形成黑点,死角10) 单位内布置不良,不能保持条理11) 工作场所放不需要的物料,仓库与工场不分12) 未重视事物整顿的重要13) 未培养及督导物品用完要归、定位14) 未彻底执行定期(每日、每周、每月)清理项目,以永久保持。
- 1、下载文档前请自行甄别文档内容的完整性,平台不提供额外的编辑、内容补充、找答案等附加服务。
- 2、"仅部分预览"的文档,不可在线预览部分如存在完整性等问题,可反馈申请退款(可完整预览的文档不适用该条件!)。
- 3、如文档侵犯您的权益,请联系客服反馈,我们会尽快为您处理(人工客服工作时间:9:00-18:30)。
浪費及改善細項
企业实际问题备注
生产现场九大浪费点检表
浪费分类 序号
16 17 18 1 2 3 4 不良品的浪费 5 6 7 8 9 1 2 3 4 5 6 7 8 9 10 11 12 动作 浪費 13 14
浪費及改善細項
包装是否恰当?(标示是否可以一面全部贴完,而不是翻来覆去的贴) 是否可不必透过人力使物品移动?(流水线移动,自动机械手、自动滑道) 使用的工具,是否能吊着使用呢?是否使用自动打包带?自动条码器等? 有没有容易混淆的标签、标注?(例如,作业员现场很容易拿错产品,因为标签,如颜色过近等) 容易操作错误的机械,是否装置自动停止之危险防止装置?(比方说自动螺丝钉,螺钉反方向就报警,停止) 容易发生作业错误之机械工具等,是否有预防策?(1 关键设备操作,是否培训 2 是否遵守 3 是否检查设备) 次品率是多少,是否有进行每天管理和持续改善(Time Check ) 工艺是否过于复杂,造成不浪率较高(工艺是否可以简化,作业手法是否过于陈旧,没有进步) 库存里是否隐藏了次品(1,现场良品不良品是否进行了混放,造成不良2.供应商不良率较高) 机器,工具,技术是否有问题(是否没有经过批量产,没有进行全面的检讨,4M1E就盲目生产) 标准化工作是否被遵守(1.未按照SOP标准流程产生不良的产生2.SOP 文件复杂,难懂,员工不理解) 次品是由准确的依据还是凭感觉来决定(1.检验标准是否培训 2 是否遵守,操作工及品质) 动作不能删除吗?不必要的额外动作? 供应商来料是否标准,是否有不合格造成,挑选 动作能合并吗? 能够缩短移动距离吗? 可否以双手或手脚同时动作? 是否操作区域是在其正面前135度视角操作 是否有弯腰的动作 是否有来回走动的动作 是否有转身的动作 是否靠蹲、仰头、不必要的摆动才能生产? 以双手动作是相反方向或是相对方向来进行呢? 由腕到手,或由手到指头,能够顺利达成工作? 重的东西或抗力大的东西是否使用机械化? 动作圆滑顺畅吗?是否有急促激烈的方向变更?(生产的动作没有交叉,也像一个流的方式进行)
多余加工浪费
3 4 5 1 2 3 4
库存浪费
5 6 7 8 9 10
生产现场九大浪费点检表
浪费分类 序号
1 2 3 过量生产浪费 4 5 6 7 8 1 2 3 管理浪费 4 5 6 7
浪費及改善細項
生产速度是否过快或者过慢(计划是否遵守?人力、设备安排是否合理) 是否缺少拉动的管理系统,而造成各个部门生产不匹配,各自为政 计划安排是否合理?没有过小的情况?(注塑、喷涂)而造成人力、物力、财力投入过大(临时生产、加班) 是否有库存排队等待加工(现场堆积半成品过多) 标准的设备产能、流水线的产能是否准确?(而造成过多生产) 是否存在“因不良过多,而生产过多,避免出货不够?” 生产进度的安排是基于生产实际需求还是依据人员主观意识? 伴随着生产不良的下降,BOM loss 率设置是否合理? 管理浪费之等待浪费。 ①等待上级的指示;②等待外部的回复;③等待下级的汇报;④等待生产现场的联系。 管理浪费之协调不利的浪费。 ①工作进程的协调不利;②领导指示的贯彻协调不利;③信息传递的协调不利;④ERP业务流程的协调不利。 管理浪费之闲置的浪费。 ①组织职能重叠;②人员配置臃肿浪费;③重复的信息传达;④企业设备、车辆的配置过剩。 管理浪费之无序的浪费。 ①职责不清造成的无序;②业务能力低下造成的无序;③有章不循造成的无序;④业务流程的无序。 管理浪费之失职的浪费。 ①做事不认真,敷衍 ②忽视团队能力,管理者尽己所能 ③自身监督、指导、沟通不利造成的问题 管理浪费之低效的浪费。 ①工作的低效率或者无效率;②错误的工作,是一种负效率,没有一次把事情做好就是最大的浪费。 管理浪费之管理成本的浪费: ①计划编制无依据;②计划执行不严肃;③计划查核不认真;④计划处置完善不到位;⑤费用投入与收入不匹配 丧失机会浪费: ①不良品过多或者送货不及时,导致订单损失,减少公司利润收益 ②QDC、人员利用率、生产效率没有最优化,造成订单增加机会减少(生产性改善活动增加) ③计划实施未完全遵守,没做到今日事今日毕,拖到明天,导致明天的利润减少,成本增加 资源浪费 ①人力浪费:未培训上岗,造成不良;未发挥人的主观能动,仅像机器使用;人员配置过剩;作业未标准化 ②设备浪费:设备过剩 ; 设备效率低下,综合设备效率低下;设备管理水平低下,稼动率低;设备采购维修费用 高 ③厂房使用率低、办公室过于奢华、电脑,水、电、气等浪费 工作方法浪费:①管理持续性与稳定性;②个人利益、部门利益优先忽视整体
企业实际问题备注
1
潜能浪费 2Βιβλιοθήκη 3企业实际问题备注
生产现场九大浪费点检表
动作 浪費
浪费分类
序号
15 16 17 18 19 20 21 22 23 24 25 1 2 有利用惯性动作吗? 有妨害动作的障碍物?或者作业台设置不合理 非得使用手以外的身体部位,才能进行作业吗?
浪費及改善細項
企业实际问题备注
工具尽可能共通使用(标准化)?(或者配件标准化,例如丰田汽车通用汽车底盘) 二种以上的工具,可被归纳成一种吗? 装配、插下能够简单快速吗? 须要用力的手把、把柄等的握把与手接触面积可否加大? 能否使用自动化工具?(电动螺丝起子) 工作是否标准化(张三需要3个动作,王五需要六个动作,或者左手右手) 是否进行了岗位交叉培训(多技能培训) 换手是否必要? 员工是否对样品、产品的要求是否理解?(0.1的误差精度,0.01操作) 检查基准是否简单明确,便于现场员工理解?(1员工看的懂吗?2 基准加严或者放宽了解吗?) 产品、工序是否理解其要求,而产生的动作浪费(内部件拼命加工,无意义) 工序设计是否不合理(例如无任何意义的海绵、螺丝、黏贴) 设备、模具、治具是否正常,不会造成额外动作(例如注塑毛边等) 库存周转率是否过低? 废品库存不良是多少?(库存不良品是否过大) 库存盘点差异率是否过大?(1%) 是否根据采购周期、生产周期进行备货?而不是大量的进行备品备货? 核心的备件是否做了备品?而不是缺少造成浪费? 安全库存设置是否合理?(而不是仓库面积的浪费,资金过多的占用,人员过多的保管) 仓库是否遵守先入先出?而不是造成产品过期造成产品浪费(例如油漆等) 现场半成品是否有准确的管理管控? 仓库台车、box 是否进行统计管理?没有过多,或者过少(现场堆积产品),或者浪费严重 各个部门、各个工序产能是否均衡?半成品是否过低或者过高?
生产现场九大浪费点检表
浪费分类 序号
1 2 3 4 5 等待的浪费 6 7 8 9 10 11 1 2 3 4 5 6 7 8 搬运的浪费 9 10 11 12 13 14 15 是否由于前面工序造成,下道工序的等待 是否由于检验检验时间过长造成,造成等待 是否由于供应商来料晚造成等待 机械自动加工,操作员只能在旁边等待(是否做到1人多台机器,或者人员空闲时间最小化) 计划安排不当,造成等待 产品是否突发批量不良,没有人快速处理,造成大量的浪费 操作是没有任何价值(例如没有标准化生产,检验造成动作增加,时间延长) 等待能否做其它事情,例如下一个产品准备或者增加其他的工作 是否遵循了标准化工作,例如有的员工30S、40S、35S秒操作,没有标准作业,造成NECK变化 工序之间是否有缓冲?数据是否正确 传递时间是否变化很大(gap 间隙,部门之间) 零件、工具等,是否可以尽量放置于近处?(搬运距离是否过长) 物品及工具等,是否整齐的放置?(例如电源线凌乱,是否有合适的BOX或架子,便于拿取) 物品及工具等,放置场所的位置与顺序恰当吗?(物品、工具无交叉,一个流方向) 物品箱是否整理过?(过脏、存有垃圾,造成操作工使用麻烦) 物品箱的大小适切否?(过大、太小)可否斜置或重迭? 机器与机器间的距离可以缩短吗? 机器保养检核表有确实执行吗? 能够缩短运搬距离吗? 可以利用输送带吗? 可以利用重力吗?(倾斜溜滑梯,倾斜的架子等) 一次运搬量可以增加否?(安全限制下) 较重物品是否利用台车等来搬运? 物品的流程曾作过整体检讨否?(是否最短最顺畅) 能否使用特殊进给匣装置?(螺丝振动排列) 是否有逆流或连续来回之工程存在?