Operator Configuration Guide for VIP Aircraft - Water and Waste
计算机科学部WiFi基础IMSI捕获器介绍说明书

Automatic WiFi Authentication
• Port Based Network Access Control [IEEE 802.1X]
• Uses Extensible Authentication Protocol (EAP) [RFC3748] over LAN
Department of Computer Science
WiFi-Based IMSI Catcher
Piers O’Hanlon
Ravishankar Borgaonkar
BlackHat, London, 3rd November 2016
Overview
• What is an IMSI?
• Apple included ‘conservative peer’ support due to our work
• Deployed in many countries – adoption growing
EAP-SIM/AKA Identities
• Three basic identity types for authentication
• ‘Auto Connect’ Encrypted WiFi access points
• WiFi key is negotiated without user intervention
• Based on credentials in the USIM/UICC (‘SIM Card’)
• Controlled by operator provided configuration
• One of a few like WiFi/Bluetooth/NFC Hardware address (e.g.
Automated External Defibrillator Trainer2 Operator

Show current scenario selection (press once) Start scenario (press again)
CPR Metronome set up to beep or not beep
(Real CPR Help® during CPR interval)
MAINTENANCE
1.
Keep Trainer2 and Remote Controller clean, undamaged,
and free of excessive wear.
2.
Verify that there are no cracks or loose parts in Trainer2 and
TROUBLESHOOlem / display:
Trainer2 does not respond
(green light in status window
is not lit) when On/Off
button is pushed
On
Off
Remote Controller does not respond (scenario selection is not lit) when view/enter button is pushed
© ZOLL Medical Corporation 2007 TRAINING USE ONLY - NOT FOR CLINICAL USE
REF 9650-XXXX-XX Rev. A
CONTROLS / INDICATORS Handheld Remote Controller:
Scenario Set-up Controls:
AirLink MP70高性能车载路由器说明书

Sierra Wireless EMBEDDED MODULES HL SERIES AirLink MP70 DatasheetAirLink® MP70 High Performance Vehicle RouterVehicle Grade, LTE-Advanced, Gigabit Wi-Fi The AirLink® MP70 is a high performance, LTE-Advanced vehicle router developed specifically for mission critical applications in public safety, transit and field services. Offering high power, long range Gigabit Wi-Fi and Gigabit Ethernet, and up to 300 Mbps downlink speeds over LTE-Advanced, the AirLink MP70 unites the fleet with the enterprise network and enables multiple field applications to work simultaneously, further and faster from the vehicle than ever before. The MP70 supports advanced remote visibility and instant insight into the vehicle area network (VAN), field applications and assets, and the mobile workforce. Purpose built for the vehicle, the MP70 delivers superior reliability and uninterrupted operation in harsh mobile environments.Secure, managed LTE networking for mission critical applicationsE-TicketingRecognitionVehicle Routers and Gateways Secure, Intelligent Communications Network ManagementHIGH PERFORMANCE VEHICLE AREA NETWORK (VAN)With dual-band Gigabit Wi-Fi and Gigabit Ethernet, the AirLink MP70 enables a complete portfolio of broadband mission critical applications to work simultaneously, further and faster from the vehicle than ever before.Built for first responders and field personnel, the MP70 offers up to 300 Mbps downlink speeds over LTE-Advanced, and up to 1.3 Gbps over 802.11ac Wi-Fi (with 3x3 MIMO) and Gigabit 4-port Ethernet. The AirLink MP70 can host up to 128 simultaneous Wi-Fi clients, and concurrently connect multiple mission critical applications in and around the vehicle including laptops, DVRs and tablets, in addition to providing live video streaming, and rapid and secure access to remote databases, such as record management systems.The AirLink MP70 supports 21 LTE frequency bands, enabling superior coverage on LTE networks worldwide. With automatic configuration of the radio based on the SIM, the AirLink MP70 has two product variants—one for LTE networks in North America, Europe, Middle East and Africa, and another variant to support all major LTE networks in Asia Pacific.Outside of the US, the AirLink MP70 offers dual-SIM functionality to enable automatic failover between SIMs, providing superior connectivity and cost optimization when roaming.CONNECTED VEHICLE AWARENESSThe AirLink MP70 increases efficiency, streamlines operations and reduces costsby supporting advanced remote visibility and instant insight into the vehicle area network (VAN), field applications and assets, and the workforce.Offering built-in vehicle-ready I/O, with the capacity to support AirLink Vehicle Telemetry, the MP70 enables remote monitoring of auxiliary devices such as light bars, sirens and gun racks, and can collect OBD-II vehicle telemetry data for engine diagnostics and performance data to monitor vehicle health.The MP70 offers an integrated mobile events engine to monitor hundreds of router, network, and connected vehicle parameters in real time, and create custom alerts, event triggers and reports. Reports and alerts are synchronized with third party server platforms or AirLink network management software to enable centralized and remote management of critical events.Utilizing next generation GNSS location technology that supports 48 satellites from 4 different satellite constellations (GPS, GLONASS, Galileo, Beidou), the MP70 provides fast, reliable and precise vehicle location, even in the most challenging environments. The MP70 contains an Inertial Navigation System1 that allows it to track without satellites, using dead reckoning algorithms integrated with the GNSS. The Inertial Navigation System continues to provide positioning information when the GNSS is unable to acquire satellites. This enables tracking through urban canyons, tunnels and underground parking.Location information can be streamed from the GNSS locally over the serial portto connected in-vehicle driver navigation and dispatch systems, and remotely over NMEA, TAIP, RAP and XORA protocols for integration with 3rd party applications.1activated in an upcoming software releasePURPOSE BUILT FOR VEHICLESThe MP70 provides superior reliability and continuous operation in harsh environments. It will survive extreme transient surges, and maintain continuous power during 5V brownouts and spikes from -600 VDC to 200 VDC.The AirLink MP70 safeguards vehicle operation by using built-in battery charge protection to monitor ignition state and battery voltage and, with a class leading power supply which meets and exceeds the requirements for E-Mark, ISO 7637-2 and SAEJ1455, the MP70 requires no additional power conditioning. Developed with industrial grade components, the AirLink MP70 has a customized die cast aluminum housing to manage the thermal output from its high performance LTE-Advanced and Wi-Fi radios. The MP70 is designed to meet IP64 for resistance to dust and water ingress, and is tested to meet and exceed the MIL-STD-810G specifications for shock, vibration, temperature and humidity. SECURE, INTELLIGENT COMMUNICATIONS The AirLink MP70 provides consolidated data security for all field applications and mobile assets in the vehicle area network (VAN). Offering up to 5 concurrent VPN sessions, the AirLink MP70 enables secure communications to multiple back-end systems, and provides remote authentication management to allow the implementation of enterprise-grade systems to control access to devices in the field. Secure signing and authentication of software images offers end-to-end protection of the software upgrade process, protecting the MP70 against unwanted malware. NETWORK MANAGEMENT Network Management solutions for the MP70 allow over-the-air registration, configuration and software updates for all AirLink gateways and routers, and can be deployed either as a hosted cloud-based service, or as a licensed software platform in the enterprise data center. Both options provide a centralized and remote view of an entire vehicle fleet and enable simplified management, control and monitoring of connected MP70s, field applications and mobile assets. AirLink Management Service (ALMS) is a secure, centralized cloud-based service that remotely monitors and manages signal strength, network technology and location. ALMS provides dashboards with up-to-date views of an entire deployment, and custom alerts to monitor and report critical events, to increase efficiency and prevent downtime.oMM Management System (oMM) is a licensed, unified software platform which can be deployed in the enterprise data center, and provides a consolidated network view of an entire fleet, using a virtual dashboard to monitor, report, manage, and troubleshoot all mobile resources as required.DASHBOARDSOFTWARE UPGRADES/UPDATESMONITOR CONNECTIVITYSECURITY CONFIGURATION2 activated in an upcoming software releaseNorth America and EMEA Model (Sierra Wireless MC7455) Carrier Approvals: Verizon, AT&T, T-Mobile USA Other major carriers pending Supported Frequency BandsLTE: 2100(B1), 1900(B2), 1800(B3), AWS(B4), 850(B5), 2600(B7), 900(B8), 700(B12), 700(B13), 800(B20), 1900(B25), 850(B26), 700(B29), TDD B41WCDMA: 2100(B1), 1900(B2), 1800(B3), AWS(B4), 850(B5), 900(B8)Industry Approvals: FCC, IC, PTCRB, R&TTE, GCF, CEAutomatic Network Operator Switching based upon SIM Dual SIM Functionality (2FF SIM)APAC Model (Sierra Wireless MC7430) Supported Frequency BandsLTE: 2100(B1), 1800(B3), 850(B5), 2600(B7),900(B8), 850(B18), 850(B19), 1500(B21), 700(B28), TDD Bands 38, 39, 40, 41WCDMA: 2100(B1), 850(B5), 800(B6), 900(B8), 1700(B9), 850(B19), TD-SCDMA B39 Industry Approvals: RCMAutomatic Network Operator Switching based upon SIM Dual SIM Functionality (2FF SIM)USB 2.0 Micro-B Connector6 SMA antenna connectors (cellular, diversity, GNSS, 3x3 Wi-Fi) Active GNSS antenna supportWPA2 EnterpriseHigh output power 21 dBm (per chan) 3x3 MIMO (Reverse Polarity SMA Connectors) Simultaneous AP/Client Mode (2.4 GHz) WiFi as WAN Mode1 Digital Open Collector Output > sinking 500 mA 3 Analog Inputs: 0.5-36 VDCConfigurable Pull-ups for dry contact input VLANHost Interface Watchdog PPPHost Port Routing NEMO/DMNR VRRPReliable Static RouteSplit TunnelDead Peer Detection (DPD)Remote Authentication (LDAP, RADIUS, TACACS+) DMZInbound and Outbound Port filtering Inbound and Outbound Trusted IP MAC Address Filtering PCI compatibleReports: NMEA 0183 V3.0, TAIP, RAP, XORA Multiple Redundant Servers Reliable Store and ForwardRouter staging over the air and local Ethernet connection Over-the-air software and radio module firmware updates Device Configuration Templates Configurable monitoring and alertingRemote provisioning and airtime activation (where Event Types: Digital Input, Network Parameters, Data Usage, Timer, Power, Device Temperature and VoltageReport Types: RAP, SMS, Email, SNMP Trap, TCP (Binary, XML, CSV)Event Actions: Drive Relay OutputSMS CommandsBuilt-in protection against voltage transients including 5 VDC engine cranking and +200 VDC load dump Humidity: 90% RH @ 60°CMilitary Spec MIL-STD-810G conformance to shock, vibration, thermal shock, and humidity IP64 rated ingress protectionISO7637-2, SAE J1455 (Shock, Vibration, Electrical) Environmental: RoHS2, REACH, WEEE1-day Accelerated Hardware Replacement available through In the box: DC Power Cable and Quick Start Guide----About Sierra Wireless Sierra Wireless is building the Internet of Things with intelligent wireless solutions that empower organizations to innovate in the connected world. We offer the industry’s most comprehensive portfolio of 2G, 3G, and 4G embedded modules and gateways, seamlessly integrated with our secure cloud and connectivity services. OEMs and enterprises worldwide trust our innovative solutions to get their connected products and services to market faster. Sierra Wireless has more than 950 employees globally and operates R&D centers in North America, Europe, and Asia. For more information, visit .。
AADvance Configuration Guide(配置手册)
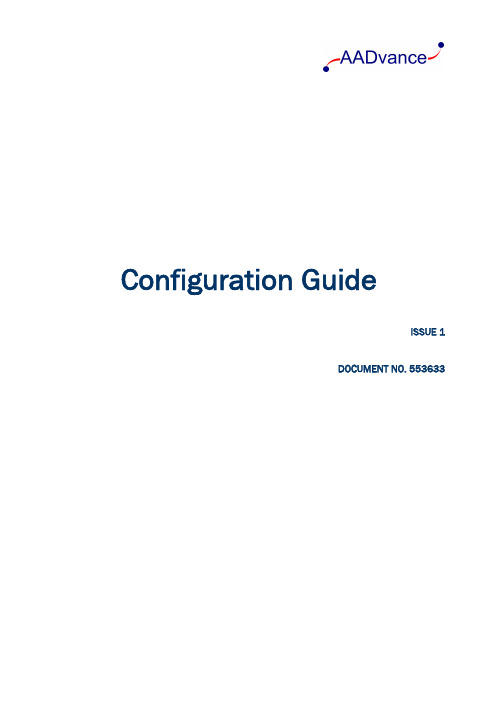
Document no. 553633 Issue 1: February 2009
iii
Configuration Guide
WARNING
ELECTRICAL ARCS AND EXPLOSION RISK
Do not remove wiring, modules or communications cabling while circuit is live unless area is known to be non hazardous.
Failure to follow these instructions may result in personal injury.
CAUTION
Caution notices call attention to methods and procedures which must be followed to avoid damage to the equipment.
SAFETY Note
This symbol calls attention to items which must be considered and implemented when designing and building a safety system using the AADvance range of products.
If you connect or disconnect wiring, modules or communications cabling while power is applied, an electrical arc can occur. This could cause an explosion in hazardous location installations. Be sure that power is removed or the area is nonhazardous before proceeding.
数字有线电视网络手动搜台指南说明书
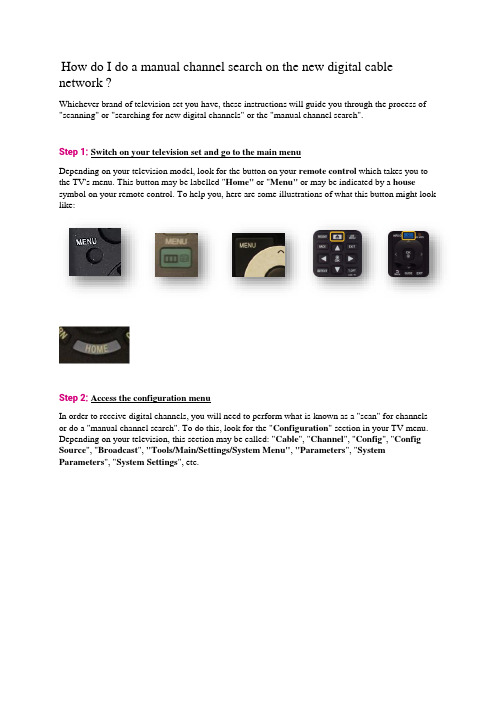
How do I do a manual channel search on the new digital cable network ?Whichever brand of television set you have, these instructions will guide you through the process of "scanning" or "searching for new digital channels" or the "manual channel search".Step 1:Switch on your television set and go to the main menuDepending on your television model, look for the button on your remote control which takes you to the TV's menu. This button may be labelled "Home" or"Menu" or may be indicated by a house symbol on your remote control. To help you, here are some illustrations of what this button might look like:Step 2:Access the configuration menuIn order to receive digital channels, you will need to perform what is known as a "scan" for channels or do a "manual channel search". To do this, look for the "Configuration" section in your TV menu. Depending on your television, this section may be called: "Cable", "Channel", "Config", "Config Source", "Broadcast", "Tools/Main/Settings/System Menu", "Parameters", "System Parameters", "System Settings", etc.Here are some illustrations to help you (the following illustrations have been taken from a "Samsung" television". However, the steps remain the same for all brands of television):Step 3:Select the installation optionThen select"Channels","Index", "Installation", "Installation Programme", "Install channels", "Parameters", "System Parameters", "Channel Search", "Digital Settings", "Rescan" "Scan", etc.Step 4:Select the option to search for digital channelsTo carry out a "scan" or perform a "manual channel search", you need to look for the manual channel search option amongst the available settings. If this option is not available, carry out an automatic channel searchThe channel search function may have different names, such as: "Search Assistant", "Auto Installation", "Automatic/Operator Scan", "Auto System Configuration", "Clear Channels", "Aerial/Cable/Service Installation", "Auto Digital Store", "Channel Settings", "Reinstall/Search All Channels", "Automatic Digital Channel Search", "Automatic Digital Cable Network Search", "Manual DVB-C Search", "Factory/Manual Digital Settings", "Reinitialise Channels/TV", "Reinstall everything", "Reset to startup settings", "Cable synchronisation", etc.Please note! Do not choose updateSome television models will ask you if you want to perform a scan for digital or analogue channels. Here you want to search for digital channels.The television might ask you if you want to search for channels via the aerial or via the cable network. In all cases, you want to search via the cable network.Step 5:Enter your password if the television requests itIt's possible that the television will ask you to enter a password during this process. If you know your password, enter it now. If you don't know the password, try: "0000", "1111", "1234", "8888", "9999".If your equipment warns you that all your previous channels will be deleted, this is normal.Step 6:Set the channel search settingsWhen you have found the right section, you should be on a configuration page with some settings which can be modified. Here are some general indications of what you might be asked:Reference table:Step 7:Start a channel searchOnce you have entered these settings, you can start a search by pressing "Start Scan", "Start ATP", "Start", or "Search",Wait until the process is complete. This can take several minutes.Step 8:Exit the installation menuPress "Back", "Confirm", "Exit", "Menu" or "Complete" to exit the installation menu.Step 9:Check that the scan has returned the correct channelsYou will now be asked to go to Channel 99. You should see the following screen:If you see this screen, you have completed the scan and now have access to cable television.。
易于管理的 Wi-Fi 来宾网络 快速生成安全的来宾通行证说明书

NetworkingSimplified Wi-fi GueSt AcceSS mAnAGementGuest pass generation made simple and secure in under 60 seconds.Ruckus Guest Networking radically simplifies the setup and management of wireless LAN (WLAN) access for guests, contractors and other temporary WLAN users.Guest networking is an essential capability required forenterprises, healthcare organizations, schools, hotels and local “hotzones” such as airports, restaurants and other venues that want to provide Internet connectivity to a myriad of guests while controlling access times, privileges and bandwidth consumption. An integrated capability within every Ruckus ZoneDirector™ Smart WLAN controller, Ruckus Guest Networking is a highly intuitive, browser-based facility that lets any guest-facing staff generate a unique Wi-Fi guest pass in less than 60 seconds with no configuration changes required on any client device.Since the guest WLAN uses the same enterprise infrastructure that carries internal traffic, Ruckus Guest Networking segregates guest traffic from corporate traffic while providing IT administra-tors controls for limiting bandwidth and the amount of connection time that guests can access the network.Guest Pass authentication enables enterprises and hotzone providers to generate time-limited access passes in hour, day, and week increments allowing more granularity between different types of guests.Highly flexible, unique pass keys can be dynamically generated by the ZoneDirector for a single guest or in batch for a large group of guests, where each key is bound to a specific clientfeAtuReS/BenefitSSimple, browser-based guest pass generationIn less than a minute, any guest-facing staff can generate single or multiple guest passes from a centrally-hosted URL through an intuitive, point-and-click, menu-driven interface, freeing IT administrators from this tasktime-limited guest accessAdministrators can simply and easily limit the time of guest passes forcing them to expire in hours, days or weeks from when the pass is created or from when the user first logs inflexibleOperators can create a guest pass on demand, orgenerate multiple passes by uploading a list of guests — if they want to be able to identify the guest pass users by their names (for monitoring or auditing purposes in a hotel). Pass keys can be random, system-generated values, or they can be defined by the operator as an easy-to-remember phrase.customizableAdministrators can customize the Guest Pass Portal with their company logo, terms of use and login instructionsAutomatic guest redirectionAfter agreeing to terms and conditions, users can be au-tomatically redirected to a custom Web page or directed to the requested URLRestricted subnet accessGuest pass users can be automatically blocked from accessing pre-defined subnets, leaving enterprise users unaffected by guest usageBandwidth thresholds per SSidAdministrators can limit capacity for a given guest network (SSID) as well as bandwidth per user within a given guest networkAcceSS mAnAGementportals are customizable with the organization’s logo and welcome text can be customized into any language. Print a single guest pass or print all of them. (see Figure 3: Step 2a and Step 2b).MAC address upon successful authentication. A single pass key can also be shared among many users. Keys can be randomly generated values, or the operator can specify an easy to remember phrase. Unlike other solutions, no additional appliances are needed.enterprise and Guest SecurityGuest WLANs can be created without requiring special con-figuration of authentication and encryption settings on client devices to minimize guest connectivity problems (see Figure 1).The Guest WLAN provides authentication services while the wireless client isolation option prevents clients on the same WLAN from communicating with each other (see Figure 2). Guests can be automatically blocked from accessing any or all of the subnets connected through the ZoneDirector and its managed access points (APs).When APs are on subnets different from the ZoneDirector, the administrator can block guest users from accessing these subnets by adding access restrictions for them.Additionally, IT administrators can limit the bandwidth for the guest WLAN to ensure sufficient performance for employee applications. The guest is placed on the guest virtual LAN and all its traffic is sent directly to the Internet, or bypassing the ZoneDirector, thereby preventing a bottleneck in the network.Guest Account creationSimple-to-use menus guide front desk staff and other guest-facing personnel through the process of creating single or multiple guest passes. For a single guest pass enter the guest user name, specify the time period (days, hours, or weeks), WLAN, optional remarks, and use the ZoneDirector randomly generated key or change it to a customized key between one and 16 ASCII characters (see Figure 3; Step 1a). Or choose multiple guest passes and specify the time period, WLAN, and the number of guest passes or upload a file with guest pass user names, remarks, and customized keys (see Figure 3; Step 1b).For example, contractors can receive extended access to the network, while a visitor can get access only for the day. This minimizes inconvenience for the guest while maximizing enterprise security.The guess pass printout is a printable HTML page that contains all the login information needed for the guest to use the WLAN and connection instructions for Windows. Ruckus Guest PassFigure 1: A single Web-based screen that lets administrators point-and-click through a variety of optionsFigure 2: IT administrator enables guest WLANRuckus Wireless, Inc. 350 West Java DriveSunnyvale, CA 94089 USAAcceSS mAnAGementThe Ruckus ZoneDirector provides comprehensive guest management for monitoring, tracking, and removing guestaccounts. The IT administrator can receive a list of all generated guest passes, and a log tracks when guests joined and left the guest WLAN. The ZoneDirector shows all authorized and unauthorized guests.When a guest has a problem connecting to the WLAN, theadministrator can easily see if that user has successfully entered the guest pass. The IT administrator can deal with threats by removing any guest pass and blocking any client device attempting to connect to the WLAN APs. A historical log of all blocked clients is maintained over time for the IT administrator.Guest pass portalWhen guests on a pre-defined guest SSID open a browser to connect to the Internet, they are redirected to captive portal page hosted on the Ruckus ZoneDirector, requesting login credentials (see Figure 3: Step 3). Ruckus Guest Pass portals are customizable with the organization’s logo and welcome text.Once a valid pass key is entered, a terms of use agreement page (optional) is sent to the guest for acceptance. Uponacceptance, guests can be redirected to a specific URL or sent to the originally requested Web site.Guest WlAn managementIT administers the guest pass generation rights to employees and selection of authentication servers to validate their login to the ZoneDirector.Copyright © 2012, Ruckus Wireless, Inc. All rights reserved. Ruckus Wireless and Ruckus Wireless design areregistered in the U.S. Patent and Trademark Office. Ruckus Wireless, the Ruckus Wireless logo, BeamFlex, ZoneFlex, MediaFlex, MetroFlex, FlexMaster, ZoneDirector, SpeedFlex, SmartCast, and Dynamic PSK are trademarks of Ruckus Wireless, Inc. in the United States and other countries. All other trademarks mentioned in this document or websiteFigure 3: Simplified setup of guest portalStep 2a: Single Guest Access Generated Step 1b: Multiple Guest Pass CreationStep 1a: Single Guest Pass CreationF o r m o r e i n f o r m a t i o n , p l e a s e c a l l 877.449.0458, o r e m a i l u s a t S a l e s @C o r p o r a t e A r mo r .c o m .。
千兆光猫用户手册说明书
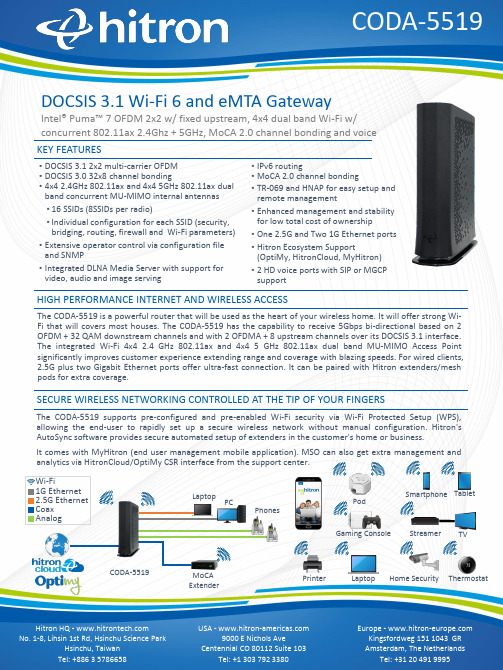
The CODA-5519is a powerful router that will be used as the heart of your wireless home.It will offer strong Wi-Fi that will covers most houses.The CODA-5519has the capability to receive 5Gbps bi-directional based on 2OFDM +32QAM downstream channels and with 2OFDMA +8upstream channels over its DOCSIS 3.1interface.The integrated Wi-Fi 4x42.4GHz 802.11ax and 4x45GHz 802.11ax dual band MU-MIMO Access Point significantly improves customer experience extending range and coverage with blazing speeds.For wired clients,2.5G plus two Gigabit Ethernet ports offer ultra-fast connection.It can be paired with Hitron extenders/mesh pods for extra coverage.•DOCSIS 3.1 2x2 multi-carrier OFDM •DOCSIS 3.0 32x8 channel bonding•4x4 2.4GHz 802.11ax and 4x4 5GHz 802.11ax dual band concurrent MU-MIMO internal antennas •16 SSIDs (8SSIDs per radio)•Individual configuration for each SSID (security, bridging, routing, firewall and Wi-Fi parameters)•Extensive operator control via configuration file and SNMP•Integrated DLNA Media Server with support for video, audio and image servingDOCSIS 3.1 Wi-Fi 6 and eMTA GatewayIntel® Puma™ 7 OFDM 2x2 w / fixed upstream, 4x4 dual band Wi-Fi w/ concurrent 802.11ax 2.4Ghz + 5GHz, MoCA 2.0 channel bonding and voice HIGH PERFORMANCE INTERNET AND WIRELESS ACCESSThe CODA-5519supports pre-configured and pre-enabled Wi-Fi security via Wi-Fi Protected Setup (WPS),allowing the end-user to rapidly set up a secure wireless network without manual configuration.Hitron's AutoSync software provides secure automated setup of extenders in the customer's home or business.It comes with MyHitron (end user management mobile application).MSO can also get extra management and analytics via HitronCloud/OptiMy CSR interface from the support center.SECURE WIRELESS NETWORKING CONTROLLED AT THE TIP OF YOUR FINGERSKEY FEATURES•IPv6 routing•MoCA 2.0 channel bonding•TR-069 and HNAP for easy setup and remote management•Enhanced management and stability for low total cost of ownership•One 2.5G and Two 1G Ethernet ports •Hitron Ecosystem Support (OptiMy, HitronCloud, MyHitron)•2 HD voice ports with SIP or MGCP supportTVStreamer Smartphone TabletThermostatHome Security LaptopCODA-5519Printer PCMoCA ExtenderPhonesWi-Fi1G Ethernet Analog2.5G Ethernet Coax PodLaptop Gaming ConsoleConnectivity•RF F-Type 75Ωfemale connector•2x RJ-45 Ethernet port 10/100/1000Mbps•1x RJ-45 Ethernet port 10/100/1000/2500Mbps•USB 3.0 type A connector with host interface•2x RJ-11 HD voice ports•EBBU jackManagement•Protocol support: TR-069, TFTP, SSHv2, SNMP v2C, v3•Web-based GUI control, configuration and management •Power-on self diagnostic•Hitron proprietary MIBs for extended support onDOCSIS, router management, Wi-Fi managementand MoCA management•app support•and back end supportReception-Demodulation•DOCSIS 3.1/3.0/2.0•DOCSIS 3.1 demodulation: Multi-carrier OFDM 16 to 4096QAM •DOCSIS 3.1 data rate: Up to 5Gps with 2 OFDM 192MHz downstream channels +32 QAM•DOCSIS 3.0 demodulation: 64QAM, 256QAM•DOCSIS 3.0 data rate: Up to 1.2Gbps with 32 bonded downstream channels•Frequency (edge-to-edge): 108-1218MHz and 258-1218 •Channel Bandwidth: 6MHz•Signal level: -15dBmV to 15dBmVTransmitter-Modulation•DOCSIS 3.1/3.0/2.0•DOCSIS 3.1 modulation: Multi-carrier OFDMA BPSK to 4096QAM •DOCSIS 3.1 data rate: Up to 700Mbps with OFDMA 96MHz upstream channels•DOCSIS 3.0 modulation: QPSK, 8QAM, 16QAM, 32QAM, 64QAM, and 128QAM (SCDMA only)•DOCSIS 3.0 data rate: Up to 320Mbps with 8 bonded upstream channels•Frequency: Fixed 5-85MHz•Upstream transmit signal level: +11 to 65dBmVMoCA 2.0 Reception / Transmitter-Modulation •Demodulation/ Modulation: BPSK, QPSK, 8QAM, 16QAM,32QAM, 64QAM, 128QAM, 256QAM, 512QAM, 1024QAM •PHY data rate: 700Mbps (baseline Mode) / 1400Mbps (bonding channel)•Throughput: 400+Mbps (baseline mode) / 500+Mbps (turbo mode, point to point) / 800Mbps (bonding channel)•Frequency (center frequencies): 1400-1625MHz•Channel bandwidth: 100MHz (baseline mode) / 225MHz (bonding channel)Voice•Protocol support: SIP or MGCP•2x 8kHz each HD voice•Audio codecs: G.711 (a-law and mu-law), G.722 (HD codec), G.723.1, G.726, G.728, and G.729Routing Support•Protocol support: IGMP v3 for IPTV service capability•MAC address filtering (IPv4/IPv6)•IP source/destination address filtering (IPv4/IPv6)•DHCP, TFTP and ToD clients (IPv4/IPv6)•DHCP server supports RFC 1541 (IPv4)•DHCPv6 obtains prefix from DHCPv6 server through prefix delegation•Firewall with stateful inspection (IPv4/IPv6)•Hacker intrusion prevention and detection•Application content filtering (IPv4/IPv6)•Complete NAT software implemented as per RFC 1631 with port and address mapping (IPv4)•DSLite support for IPv4 in-home support with IPv6 MSO backbone •6RD support for quick IPv6 deployment over IPv4 backbone •RIPv2 for static IP supportWireless•802.11a/b/g/n/ac/ax•4T4R 2.4GHz 11ax and 4T4R 5GHz 11ax dual band concurrent MU-MIMO with 1Gbps+4.8Gbps PHY rate•20/40/80/160MHz channel bandwidth•Up to 8 SSIDs for each frequency•Security: WPA-PSK/WPA2-PSK (TKIP/AES), WPA3, WAPI •QoS: WMM/WMM-PS•WPS (Wi-Fi Protected Setup) PBC, PIN•Airtime Fairness (ATF), Band Steering (BS)•Dynamic Frequency Selection (DFS)•Wi-Fi output power range: Max permitted by FCC/IC Electrical•Input power: 12VDC, 4A•Power adaptor: 100-240VAC, 50/60Hz•Power consumption: 4.92 (power saving), 22W (typ.), 38W (Max)•Support power outage for 24 hours on Hitron external battery •Surge protection: RF input sustains at least 4KVEthernet RJ-45 sustains at least 4KV Mechanical•Factory default reset button•WPS button•Dimensions: 74.3mm (W) x 251.5mm (H) x 230.8mm (D)•Weight: Weight: 1850 ±10gEnvironmental•Operating temperature: 0°C (32°F) ~ 40°C (104°F)•Operating humidity: 10% ~ 90% (Non-condensing)•Storage temperature: -40°C (-40°F) ~ 60°C (140°F) Compliance Certificates•RoHS compliant•FCC, IC, ULSPECIFICATIONS。
配置说明书

Step 28. Select Latch Type SubmenuPress d to display flashing DSBL / ENBL .If flashing DSBL is displayed, press a , if ENBL is displayed, press b until DSBL is displayed, then press d to store and go to the next menu item.Step 29. Select the Above Type of Active Submenu Press d . If flashing ABoV Above is displayed, press a ,otherwise press b until ABoV is displayed. Press d to store and advance to next menu item.Step 30. Select the Deadband Value Submenu Press d . The display will show 020.0, otherwisepress b or c.Press d to store and advance to next menu item.Step 31. Enter the Alarm 2 MenuThe display will show ALR2the top menu for Alarm 2.Repeat steps from 29 and 30 to set for Alarm 2 the same conditions as for Alarm 1.Step 32. Configuration of Display Color Selection Press a until the COLR Display Color Selection Menu appears on the Display. Configure COLR as N.CLR / GRN (green), 1.CLR / RED (red), 2.CLR / AMBR (amber). Please refer to the operator’s manual if needed.Step 33. Run a TestPress a until reset the controller and return to RUN Mode to display 075.0(Ambient Temperature). Now you are ready to observe temperature as it rises 10°F higher than displayed. Touch the tip of the Thermocouple to raise the temperature above the Alarm 2 value 082.0, and AL2 will turn on, and Display Color will change from Green toAmber. Continue touching the tip to raise the temperature above the Alarm 1 value 087.0and Display Color will change from Amber to Red.Step 10. Enter to the Thermocouple Input Submenu Press d to store Thermocouple Input. The display will stop flashing and show the top menu for Thermocouple types. If you press a controller will step to next menu item (Skip to Step 14).Step 11. Enter to the Thermocouple Type Input Submenu Press d to display flashing, previously selected Thermocouple type.Step 12. Scroll through available selection of TC types Press b to sequence thru flashing Thermocouple types,(select k -for type "K" CHROMEGA ®/ALOMEGA ®)J K T E N DIN J R S B C - TC types J k t E N dN J R S b C - DisplayStep 13. Store TC typeAfter you have selected the Thermocouple type press d to store your selection, the instrument automatically advances to the next menu item.Step 14. Enter to Reading Configuration MenuThe display shows RDG Reading Configuration, which is the top menu for 4 submenus: Decimal Point, Degree Units,Filter Constant and Input/Reading Submenus.Step 15. Enter to Decimal Point Submenu Press d to show DEC Decimal Point.Step 16. Display the Decimal Point positionPress d again to display the flashing Decimal Point position.Step 17. Select the Decimal Point position Press b to select FFF.F Decimal Point position.Step 18. Store selected Decimal Point positionBy pressing d momentarily the Decimal Point position will be stored and the instrument will go to the next menu item.Step 19. Enter to Temperature Unit Submenu Display shows TEMP Temperature Unit.Step 20. Display available Temperature Units Press d to display the flashing Degree °F or °C .Step 21. Scroll through Temperature Units selection Press b to select °F Degree.Step 22. Store the Temperature UnitPress d to display momentarily that the Degree Unit has been stored and the instrument will go automatically to the next menu item.Step 23. Enter the Filter Constant Submenu Display shows FLTR Filter Constant Submenu.Step 24. Display the Filter Constant Value Submenu Press d to display the flashing, previously selected Filter Constant.Step 25. Scroll through available Filter Constants Press b to sequence thru Filter Constants 0001, 0002,0004, 0008, 0016, 0032, 0064and 0128.Step 26. Store the Filter ConstantPress d momentarily to store 0004Filter Constant and the instrument will automatically go to the next menu item.Step 27. Enter Alarm 1 MenuPress a until the ALR1Alarm 1 Menu appears on the Display. In the following steps we are going to DisableLatch, Active Above, Deadband 020.0, and above Setpoint 1Value will activate Alarm 1.MQS3846/N/0905SPECIFICATIONAccuracy:+0.5°C temp;0.03% rdg. process typical Resolution:1°/0.1°; 10 µV process Temperature Stability:0.04°C/°C RTD;0.05°C/°C TC @ 25°C (77°F); 50 ppm/°C process Display:4-digits, 9-segments LED,10.2 mm (0.40") with red, green and amber programmable colors Input Types:Thermocouple, RTD, Analog Voltage and Current TC:(ITS90)J, K, T, E, R, S, B, C, N, L RTD:(ITS68)100/500/1000 ohm Pt sensor 2-wire, 3-wire, or 4-wire;0.00385 or 0.00392 curve Voltage:0 to 100 mV, 0 to 1 V, 0 to 10 Vdc Current:0 to 20 mA (4 to 20 mA)Output 1†:Relay 250 Vac @ 3 A Resistive Load,SSR, Pulse, Analog Voltage and Current Output 2†:Relay 250 Vac @ 3 A Resistive Load,SSR, Pulse †Only for AlarmsOptions:Communication RS-232 / RS-485 or 10BaseT or Excitation:24 Vdc @ 25 mAExc. not available for Low Power OptionLine Voltage/Power:90 - 240 Vac ±10%,50 - 400 Hz*,or 110-375 Vdc, 4W for i16; 5W for i16D* No CE compliance above 60 HzLow Voltage Power Option:12 - 36 Vdc, 3 W** for i16;20 - 36 Vdc, 4 W** for i16D;**Units can be powered safely with 24 Vac but No Certification for CE/UL are claimed.Dimensions:48 H x 48 W x 127 D mm (1.89 x 1.89 x 5")Weight:159 g (0.35 lb)Approvals:CE per EN 61010-1:2001NEWPORT is constantly pursuing certification of its products to the European New Approach Directives.NEWPORT will add the CE mark to every appropriate device upon certification.The information contained in this document is believed to be correct, but NEWPORT Electronics, Inc.accepts no liability for any errors it contains, and reserves the right to alter specifications without notice.TRADEMARK NOTICE:,NEWPORT , NEWPORT , ,andthe “Meter Bezel Design”are Trademarks of NEWPORT ELECTRONICS, INC.This Quick Start Reference provides informationon setting up your instrument for basic operation.The latest complete Communication and OperationalManual as well as free Software and ActiveX Controlsare available at /i or on theCD-ROM enclosed with your shipment.SAFETY CONSIDERATIONThe instrument is a panel mount device protected in accordance with EN61010-1:2001. Remember that the unit has no power-on switch. Building installation should include a switch or circuit-breaker that must be compliant to IEC 947-1 and 947-3.SAFETY:•Do not exceed voltage rating on the label located onthe top of the instrument housing.•Always disconnect power before changing signal andpower connections.•Do not use this instrument on a work bench withoutits case for safety reason.•Do not operate this instrument in flammable orexplosive atmospheres.•Do not expose this instrument to rain or moisture. EMC:•Whenever EMC is an issue, always use shielded cables.•Never run signal and power wires in the same conduit.•Use signal wire connections with twisted-pair cables.•Install Ferrite Bead(s) on signal wire close to theinstrument if EMC problems persist.Panel Mounting Instruction:ing the dimensions from the panel cutout diagramshown above, cut an opening in the panel.2.Insert the unit into the opening from the front of the panel,so the gasket seals between the bezel and the front of the panel.3.Slide the retainer over the rear of the case and tightenagainst the backside of the mounting panel.。
远程SIM配置用户手册说明书

RemoteSIM Configurations User ManualMarch2023Introduction3 Requirements3 Scenario1:SIM Injector in LAN of Cellular Router4 Setup topology4 Configuring the SIM Injector/SIM Injector Mini4 Configuring the Cellular Router5 Scenario2:SIM Injector in WAN of main Router and multiple Cellular Routers8 Setup topology8 Additional configurations for Cellular Routers8 Configuration requirements for the main Router10 Scenario3:SIM Injector in LAN of main Router and multiple Cellular Routers11 Setup topology11 Main Router configuration12 Scenario4:SIM Injector in LAN of main Router and Dome with Starlink13 Setup topology13 Configuring the MAX HD2router14 Configuring the SIM Injector15 Configuring the HD1Dome Pro16 Scenario5:SIM Injector/SIM Injector Mini in a remote location18 Setup topology18 Cellular Router configuration18 How to check if a Peplink Cellular Router supports RemoteSIM20 Monitor the status of the RemoteSIM20 Appendix A:Declaration21IntroductionPeplink has developed a unique technology called RemoteSIM,which allows SIM cards to remotely link to a cellular router.This can be done via cloud or within the same physical network.There are a few key scenarios to fit certain applications.The purpose of this manual is to provide an introduction on where to start and how to set up for the most common scenarios and uses.Requirements-Cellular router that supports RemoteSIM technology.-SIM Injector.-SIM card.Notes:-Always check for the latest Firmware version for both the cellular router and the SIM Injector.You can also check for the latest Firmware version on the device’s WEBconfiguration page.-A list of products that support RemoteSIM can be found on the SIM Injector WEB page.Please check under the section Supported models.SIM Injector reset and login detailsHow to reset a SIM Injector:-Hold the reset button for5-10seconds.Once the LED status light turns RED,the reset button can be released.SIM Injector will reboot and start with the factory default settings. The default WEB login settings:-User:admin-Password:admin-IP address:the device only has a DHCP client and no fallback IP address..Therefore,it is advised to check every time what IP address is assigned to the SIM Injector.Notes:-The SIM Injector can be monitored via InControl2.Configuration is not supported.Scenario1:SIM Injector in LAN of Cellular RouterSetup topologyThis is the most basic scenario in which the SIM Injector/SIM Injector Mini(hereinafter referred to as SIM Injector)is connected directly to the cellular router’s LAN port via an ethernet cable. This allows for the cellular router to be positioned for the best possible signal.Meanwhile,the SIM cards can be conveniently located in other locations such as the office,passenger area,or the bridge of a ship.The SIM Injector allows for easily swapping SIM cards without needing to access a cellular router.IMPORTANT:Cellular WAN will not fallback to the local SIM if it is configured to use the SIM Injector.Configuring the SIM Injector/SIM Injector Mini1.Connect the SIM Injector to the LAN port of the cellular router.2.Insert SIM cards into the SIM Injector.The SIM cards will be automatically detected. IMPORTANT:SIM cards inserted into SIM Injector must not have a PIN code.Note1:The SIM Injector gets its IP address via DHCP and doesn't have a static IP address.To find it’s address,please check the DHCP lease on the cellular router.Configuring the Cellular RouterStep1.Enable the SIM Injector communication protocol.1a.If you are using a Balance cellular router,go to the Network tab(top navigation bar).1b.If you are using a MAX cellular router,go to the Advanced tab(top navigation bar).2.Under Misc.settings(left navigation bar)find Remote SIM Management.3.In Remote SIM Management,click on the edit icon next to Remote SIM is Disabled.4.Check the Auto LAN discovery checkbox and click Save and Apply Changes.5.Click Save and then Apply Changes.Step2.Enable RemoteSIM for the selected Cellular interface.1.Go to Network(top navigation bar),then WAN(left navigation bar)and click Details for a selected cellular WAN.This will open the WAN Connection Settings page.2.Scroll down to Cellular settings.3.In the SIM Card section,select Use Remote SIM Only.4.Enter configuration settings in the Remote SIM Settings section.Click on Scan nearby remote SIM server to show the serial number(s)of the connected SIM Injector(s).Available configuration options for cellular interface are shown below:A.Defining SIM Injector(s)-Format:<S/N>-Example1:1111-2222-3333-Example2:1111-2222-33334444-5555-6666B.Defining SIM Injector(s)SIM slot(s):-Format:<S/N:slot number>-Example1:1111-2222-3333:7,5(the Cellular Interface will use SIM in slot7,then5)-Example2:1111-2222-3333:1,21111-2222-3333:3,4(the cellular Interface will use SIM in slot1,then in2from the first SIM Injector,and then it will use3and4from the second SIM Injector).Note:It is recommended to use different SIM slots for each cellular interface.5.Click Save and Apply Changes.Step3.(Optional)Custom SIM cards settings.1a.For a Balance router,go to the Network(Top tab).1b.For a MAX router,go to the Advanced(Top tab).2.Under Misc.settings(Left-side tab)find Remote SIM Management.3.Click on the Add Remote SIM button,fill in all the required info and click Save.This section allows defining custom requirements for a SIM card located in a certain SIM slot: -Enable/Disable roaming(by default roaming is disabled).-Add Custom mobile operator settings(APN,user name,password).4.Repeat configuration for all SIM cards which need custom settings.5.Click Apply Changes to take effect.Scenario2:SIM Injector in WAN of main Router and multiple Cellular RoutersSetup topologyIn this scenario,each HD Dome creates a WAN connection to the main router.A single SIM Injector is used to provide SIM cards for each HD Dome.The HD Dome can be replaced with any Peplink cellular router supporting RemoteSIM technology.This scenario requires the completion of the configuration steps shown in Scenario1in addition to the configuration steps explained below.Additional configurations for Cellular RoutersStep1.Disable the DHCP server.-HD Dome1should act as a DHCP server.-HD Dome2should be configured to have a static IP address with DHCP disabled.-Both routers should be in the same subnet(e.g.192.168.50.1and192.168.50.2).1.Go to Network(Top tab),then Network Settings(Left-side tab),and click on Untagged LAN.This will open up the LAN settings page.2.Change the IP address to192.168.50.2.3.In the DHCP Server section,uncheck the checkbox to disable DHCP Server.4.Click Save and Apply Changes.Step2.Ethernet port configurationThe Ethernet port must be set to ACCESS mode for each HD Dome.To do this,dummy VLANs need to be created first.1.Go to Network(Top tab),then Network Settings(Left-side tab),and click on New LAN.This will open the settings page to create a dummy VLAN.2.The image below shows the values that need to be changed to create a new VLAN:Note:set different IP addresses for each HD dome(e.g.192.168.10.1and192.168.10.2).3.Click Save and Apply Changes.4.Go to Network(Top tab),then Port Settings(Left-side tab).5.Set the Port Type to Access and set VLAN to Untagged LAN(see picture below).6.Click Save and Apply Changes.Configuration requirements for the main RouterRequirements for the main router are:-Configure WAN1as a DHCP client.-WAN1will automatically get the Gateway IP address from HD Dome1.-Configure WAN2as a Static IP and set it to192.168.50.12.-Configure WAN2Gateway to192.168.50.2.Same as the HD Dome2’s IP address.Scenario3:SIM Injector in LAN of main Router and multiple Cellular RoutersSetup topologyIn this scenario,SIMs are provided to the HD Domes via the main router.In this example,the Remote SIM Proxy functionality needs to be enabled on the main router.Notes:-HD Dome can be replaced with any other cellular router that supports RemoteSIM.-It is recommended to use Peplink Balance series or X series routers as the main router.This scenario requires the completion of the configuration steps for the cellular router and the SIM Injector as in Scenario1.The configuration for the main router is explained below.Main Router configurationIMPORTANT:Main router LAN side and Cellular Routers must be configured using different subnets,e.g.192.168.50.1/24and192.168.100.1/24.Note:please make sure the Peplink router is running Firmware8.1.0or above.1.Open the main router WEB interface and change:From<IP address>/cgi-bin/MANGA/index.cgi to<IP address>/cgi-bin/MANGA/support.cgi.This will open the support.cgi page.2.Scroll down to find Remote SIM Proxy and click on[click to configure]that is located next to it.3.Check the Enable checkbox.4.Click on Save.5.Go back to the index.cgi page and click on Apply Changes.Scenario4:SIM Injector in LAN of main Router and Dome with StarlinkSetup topologyEquipment used:-HD1Dome Pro(MAX-HD1-DOM-PRO-5GD),FW version8.2.1-MAX HD2(MAX-HD2-LTEA-W-T),FW version8.2.1-SIM Injector Mini(SIM-MINI-8-1E),FW version1.1.120Configuring the MAX HD2routerIMPORTANT:Main router LAN side and Cellular Routers must be configured using different subnets,e.g.192.168.50.1/24and192.168.100.1/24.Step1.Change router subnet to192.168.100.1/24.1.Go to Network tab,then click on LAN network2.Change IP addresses to the new subnet:3.Click on Save.4.Go back to the index.cgi page and click on Apply Changes.Step2.Enable the Remote SIM Proxy1.Open the main router WEB interface and change:From192.168.100.1/cgi-bin/MANGA/index.cgi to192.168.100.1/cgi-bin/MANGA/support.cgi 2.Scroll down to find Remote SIM Proxy and click on[click to configure]that is located next to it.3.Check the Enable checkbox.4.Click on Save.5.Go back to the index.cgi page and click on Apply Changes.Configuring the SIM InjectorThere is no need to configure a SIM Injector mini.Once the HD2router configuration is finished you power on SIM Injector mini.IMPORTANT:in case SIM Injector Mini was connected to HD2before its configuration,then need to power off and then power on SIM Injector Mini.Configuring the HD1Dome ProStep1.Enable the SIM Injector communication protocol.1.By default the HD1Dome Pro IP address is192.168.50.1.Open WEB based configuration interface and then go to Advanced tab(top navigation bar).2.Under Misc.settings(left navigation bar)find Remote SIM Management.3.In Remote SIM Management,click on the edit icon next to Remote SIM is Disabled.4.Check the Auto LAN discovery checkbox and click Save and Apply Changes.5.Click Save and then Apply Changes and reboot the HD1Dome Pro.Step2.Enable RemoteSIM for the selected Cellular interface.1.Go to Network(top navigation bar),then WAN(left navigation bar)and click Details for a selected cellular WAN.This will open the WAN Connection Settings page.2.Scroll down to Cellular settings.3.In the SIM Card section,select Use Remote SIM Only.4.Click Scan nearby remote SIM server.The system must find the SIM Injector Mini serial number as shown below.5.Click Update RemoteSIM Settings.6.Click Save and Apply Changes.Step3.(Optional)Custom SIM cards settings.1.For a MAX router,go to the Advanced(Top tab).2.Under Misc.settings(Left-side tab)find Remote SIM Management.3.Click on the Add Remote SIM button,fill in all the required info and click Save.This section allows defining custom requirements for a SIM card located in a certain SIM slot: -Enable/Disable roaming(by default roaming is disabled).-Add Custom mobile operator settings(APN,user name,password).4.Repeat configuration for all SIM cards which need custom settings.5.Click Apply Changes to take effect.Scenario5:SIM Injector/SIM Injector Mini in a remote locationSetup topologyRequirements for installing a SIM Injector/SIM Injector Mini(hereinafter referred to as SIM Injector)in a remote location:●Cellular router communicates with the SIM Injector via UDP port50000.Therefore thisport must be reachable via public IP over the Internet.●The one way latency between the cellular router and the SIM Injector should be up to250ms.A higher latency may lead to instability issues.●The cellular router must have Internet connection to connect to the SIM Injector.It canbe another Internet connection via Ethernet or Fiber if possible,or a secondary cellular interface with a local SIM(Ignite SIM).●Due to its high latency,it is not recommended to use satellite WAN for connecting to aSIM Injector in remote locations.SIM Injector configuration is the same as in Scenario1.Cellular Router configurationStep1.Enable the SIM Injector communication protocol.1a.For a Balance cellular router,go to the Network(Top tab).1b.For a MAX cellular router,go to the Advanced(Top tab).2.Under Misc.settings(Left-side tab),find Remote SIM Management.3.In Remote SIM Management,click on the edit icon next to Remote SIM is Disabled.4.Enter the public IP of the SIM Injector and click Save and Apply Changes.Notes:-Do NOT check Auto LAN Discovery.-Adding a SIM Injector serial number to the Remote SIM Host field is a mistake! Step2.RemoteSIM and custom SIM card settings configurations are the same as in Scenario1.How to check if a Peplink Cellular Router supports RemoteSIM1.Go to Network(Top tab),then WAN(Left-side tab),and click Details on any cellular WAN. This will open the WAN Connection Settings page.2.Scroll down to Cellular settings.If you can see the Remote SIM Settings section,then the cellular router supports RemoteSIM.Monitor the status of the RemoteSIM1.Go to Network(Top tab),then WAN(Left-side tab),and click Details on the cellular WAN which was configured to use RemoteSIM.2.Check the WAN Connection Status section.Within the cell WAN details,there is a section for Remote SIM(SIM card IMSI,SIM Injector serial number and SIM slot).Appendix A:DeclarationFCC Requirements for Operation in the United StatesFederal Communications Commission(FCC)Compliance Notice:For SIM InjectorFederal Communication Commission Interference StatementAny changes or modifications not expressly approved by the party responsible for compliance could void your authority to operate the equipment.This equipment has been tested and found to comply with the limits for a Class B digital device, pursuant to part15of the FCC Rules.These limits are designed to provide reasonable protection against harmful interference in a residential installation.This equipment generates, uses and can radiate radio frequency energy and,if not installed and used in accordance with the instructions,may cause harmful interference to radio communications.However,there is no guarantee that interference will not occur in a particular installation.If this equipment does cause harmful interference to radio or television reception,which can be determined by turning the equipment off and on,the user is encouraged to try to correct the interference by one or more of the following measures:—Reorient or relocate the receiving antenna.—Increase the separation between the equipment and receiver.—Connect the equipment into an outlet on a circuit different from that to which the receiver is connected.—Consult the dealer or an experienced radio/TV technician for help.This device complies with Part15of the FCC Rules.Operation is subject to the following two conditions:(1)this device may not cause harmful interference and(2)this device must accept any interference received,including interference that may cause undesired operation.Industry Canada StatementThis product meets the applicable Innovation,Science and Economic Development Canada technical specifications.Le présent produit est conforme aux spécifications techniques applicables d'Innovation, Sciences et Développementéconomique Canada.This device contains licence-exempt transmitter(s)/receiver(s)that comply with Innovation, Science and Economic Development Canada’s licence-exempt RSS(s).Operation is subject to the following two conditions:(1)This device may not cause interference.(2)This device must accept any interference,including interference that may cause undesired operation of the device.Le present appareil est conforme aux CNR d'Industrie Canada applicables aux appareils radio ex-empts de licence.L'exploitation est autorisee aux deux conditions suivantes:(1)l’appareil ne doit pas produire de brouillage,et(2)l’utilisateur de l’appareil doit accepter tout brouillage radioelectrique subi,meme si le brouillage est susceptible d’enFCC Requirements for Operation in the United StatesFederal Communications Commission(FCC)Compliance Notice:For SIM Injector MiniFederal Communication Commission Interference StatementAny changes or modifications not expressly approved by the party responsible for compliance could void your authority to operate the equipment.This equipment has been tested and found to comply with the limits for a Class B digital device, pursuant to part15of the FCC Rules.These limits are designed to provide reasonable protection against harmful interference when the equipment is operated in a commercial environment.This equipment generates,uses,and can radiate radio frequency energy and,if not installed and used in accordance with the instruction manual,it may cause harmful interference to radio communications.Operation of this equipment in a residential area is likely to cause harmful interference,in which case the user will be required to correct the interference at his own expense.This device complies with Part15of the FCC Rules.Operation is subject to the following two conditions:(1)this device may not cause harmful interference and(2)this device must accept any interference received,including interference that may cause undesired operation.Industry Canada StatementThis product meets the applicable Innovation,Science and Economic Development Canada technical specifications.Le présent produit est conforme aux spécifications techniques applicables d'Innovation, Sciences et Développementéconomique Canada.This device contains licence-exempt transmitter(s)/receiver(s)that comply with Innovation, Science and Economic Development Canada’s licence-exempt RSS(s).Operation is subject to the following two conditions:(1)This device may not cause interference.(2)This device must accept any interference,including interference that may cause undesired operation of the device.Le present appareil est conforme aux CNR d'Industrie Canada applicables aux appareils radio ex-empts de licence.L'exploitation est autorisee aux deux conditions suivantes:(1)l’appareil ne doit pas produire de brouillage,et(2)l’utilisateur de l’appareil doit accepter tout brouillage radioelectrique subi,meme si le brouillage est susceptible d’enCE Statement for Pepwave Routers(SIM Injector Mini)contact as:https:///UK Statement for Pepwave Routers(SIM Injector Mini)。
阿特拉斯·科普柯 STwrench A 万能扳手说明书

AInterchangeable end fittings with patented recognition technology for PSET selection. Full traceability of various applications.BOptional advanced electronic gyroscope for precise angle measurement.CLow clearance compact head to get better accessibility and stability of operation.DBright LED headlight in front of the smartHEAD to illuminate dark spaces.EThe communication interfaces are USB or Wi-Fi thanks to the radio module. It is also possible to have communication with Power Focus via Wi-Fi or Bluetooth. Barcode module can be added to improve traceability and automatically startthe tests.FEasy-to-read display that can beread at angles of up to 180°.GFour signal lights forimproved operator feedback visible at 360°. Three special LED signals guide the operator for accurate tightening and measuring control.HErgonomic vibrating handle to ensure precise use.FeaturesABD FGHE C147.5 - 1 344 m m30 - 1 000 N m UNLIKE ANY OTHERCritical fastening duties are among themost essential tightening operations within industry today. So whether you are in thebusiness of assembling cars or trucks, tractors or harvesters, trains or planes, you need to be in control when it comes to production and quality assurance.That is where the Atlas Copco STwrench comes in. The STwrench provides a whole new approach to manual assembly applications. Naturally, it provides the accuracy, durability and ergonomics that are the hallmarks of the Atlas Copco product range. But the construction of the tool itself is entirely different.This is far from your standard transduce r i zed hand-held nutrunner. Unlike any other Atlas Copco tool, you can build the STwrench to meet your exact requirements. Due to its truly modular design, you have the freedom to create a tool that suitsThe STwrench implements a patented residual torque/angle measurement algorithm to measure the torque left on the joints by the tools inproduction. The STwrench residual torque/angle algorithm makes the residual torque check operator independent.Furthermore, as the residual point is detected in realyour applications perfectly. So you get outstanding Atlas Copco performance, but with greater flexibility than ever before.Use the STwrench for production to get full traceability of the entire tightening oper a tion including torque control, angle control and yield control. Or build your wrench to just tighten your joint with high torque accuracy.Use the STWrench for quality control to checkresidual torque, to perform joint analysis, including joint behaviour and stiffness, to set the correcttightening parameters for production and to test the reproducibility of joint stiffness on the benches.Build your own STwrench and create theultimate wrench for your specific requirements.Residual Torque/Angle Algorithmtime, buzzer, LEDs and vibration alert the operator to stop, avoiding overtorqueing.BUILD TO FITDeciding on the degree of control andconnectivity is the next step in creating your STwrench system. Establish what is right for you. Critical fastening duties are demanding, Atlas Copco believes in keeping both control and connectivity simple.Be in control. The STwrench controller puts you in charge. Menus, parameters and alarms are more manageable, with easy-to-use, text based software. Simply use the five navigation buttons for anytightening activity. Built-in LED signals immediately alert you to deviations from the preset program.Decrease downtime. Get fast access to the programmed data you need with Atlas Copco’spatented Rapid Backup Unit (RBU). The RBU transfers critical data to the hardware unit and serves as back-up for programming and configuration. If you need to change hardware, just connect the RBU on to the new hardware, switch on the unit and you are ready. All programming and network config u rations are transferred in seconds.Accessorize. Add the right accessories to yourSTwrench controller. Choose the wireless module to support wireless transmission of critical data. Add the barcode reader to easily scan barcode labels on assembly components for ease of traceability. Or select the correct PSet or Job. Manage up to four levels of barcodes for better error proofing.Get connected. It’s easy to connect your STwrench to the control systems you have in place. Standard fieldbus I/O, TCP/IP or Ethernet connectivity lets you decide between wired or wireless communications. Communications with ToolsNet, Torque Supervisor and Power Focus are easy with the wide variety of formats.Program and customize. Use ToolsTalk BLM to program the STwrench. You can export the latest 5000 results into an excel file or save the latest 10 traces. View and zoom the tightening trace for accurate analysis.STwrench RBU Production(8059 0930 91)STwrench Battery(8059 0930 86)smartHEAD A400 – 400 Nm(8059 0930 60)Reversible ratchet 14 x 18 – 3/4 in(4620 0082 00)THE SMARTHEADThe SmartHEAD really lives up to itsname. The smartHEAD has a built-in memorychip to store calibration values that areautomatically recognized by the STwrenchcontroller. They come in 21 different versionsfrom 15 Nm up to 1000 Nm, with or withoutangle reading. The smartHEAD is fast toexchange, this makes STwrench easy toupgrade and Service.The transducer and the gyroscope are locatedin the front part of the smartHEAD to be lessdependent from bending effects, a coefficientis stored after calibration to compensate anyremaining bending effect. The smartHEADhas a patented mechanism to recognize theend fitting tool connected, this allows toautomatically start the associated program.Choose your smartHEAD fitting yourapplication, connect it and you are ready to go.IRC Modules. Two different IRC moduleswith two different wireless technologies.No extra software isneeded. Simply plug in the new module to activatecommunication to the Power Focus, QATnode or different systems on the internet.QATnode P. The QATnode P makes it possible to print out a ticket result on a STAR DP8340 that is a 40 column serial printer. The layout of the ticket is fully configurable via TT BLM.OPTIONS AND ACCESSORIESQA TnodeThree different models ofQATnodes provide customized solutions to meet individual customer needs. The STwrench Modules can be connected to the QATnodes with WiFi via access point in real time – or via IrDa when not mounted on the cradle.With this module, theSTwrench is able to handle four different bar codes that activate or control the process. It also enables traceability. Simply plug in the module to activate the function.The battery charger fullyrecharges a STwrench battery in just four hours. The charger can be mounted horizontally on a wall, the battery screws into the charger.The lithium ion battery provides 16 hours of working time. If wireless communication is used, the working time is 10 hours.Connect the STwrench to the Power Focus using a standard Tensor SL cable. The STwrench cable box supplies power to the wrench and handles the communication between the wrench and the Power Focus.Battery charger Battery Cable boxBar code modulePower Focus 4000 is the control system for the STwrench. The Power Focus 4000 is available in one model with two versions, PF 4000 Compact and PF 4000 Graph. Power Focus 4000 or Focus 4000 is used in combination with the STwrench for line integration via digital I/O or fieldBus. This makes it possible to use Atlas CopcoQuality Integration Fastening (QIF) accessories, such as stack light, operator panel, mini display and other Atlas Copco standard QIF components.QATnode I/O. Inaddition to the QATnode P functionality, there are also 6 digital inputs and 5 digital outputs. Each of these are fully configurable and make it possible to enable or disable the wrench, select a PSet or JOB, as well as send out an OK or NOK.QATnode ing QATnode T function-ality, the STwrench can also send data to the ToolsNet server.• Lightweight and ergonomic all purpose manual torque wrench.• Tailored to your exact requirements.• Modular and cost-effective – only invest in what you need.• Easy to integrate, use, service and upgrade.• Joint analysis and quality control.• Quick and easy residual torque checks during production when traceability and error proofing are required.• Joint analysis when advanced functionality such as trace export,• Difficult access or limited space applications.• For immediate temporary backup on the line and assembly of special production.• Repair stations that need greater flexibility and a wider torque range.WHY YOU SHOULD INVESTThere are many reasons to invest in the STwrench. It could be the ergonomic lightweight design. Maybe you feel that its modularity guarantees that you’ll get just the right tool for your job – at the right cost. Maybe The agility and accessibility is what is appealing to you. Any way, this tool will easily find its place in your applications and have them run fast, easy and correct.Product Benefits:Benefits in quality assurance:Benefits in production:• Reliable, always up-to-date programming strategies and backup.• Smart accessories for error proofing and traceability, including wireless module, barcode reader, and Power Focus or Focus Interface Module.zoom and yield point detection are required.• Accurate residual torque checks communication using a reliablepaperless interface to the quality system.• Accurate and afford a ble tube-nut tightening.• When you need the same error proofing, traceability and quality as an electric tool.For all types of applications*End fitting has to be ordered separately, please see Industrial Power Tools Catalogue 9837 3000 01*Dimension Z is 50.5 mm when the STwrench battery short HD is installed (and Dimension K decreases by 45.5 mm). **Dimension J is the standard arm (measured at the center of the end-fitting tool); these data are used to calculate the torque correction coefficient when anextension is used. This dimension is calculated for the standard Atlas Copco end-fitting tools; if a different end-fitting tool is used, this measure must be recalculated.Refer to the “Appendix A – Calculating Torque and Angle Correction Coefficients” for further details. ***For STwrench Heavy Duty, both the feature “IRDA Port” and “Shock Indicator” arenot available.Functionality overviewTypeAB H L g Ordering No. mm mm mm mm Open end 9 x 12722517.5404620 0001 00822517.5394620 0002 00926 5.517.5384620 0003 001026 5.517.5424620 0004 001126 5.517.5414620 0005 001230717.5434620 0006 001330717.5484620 0007 001435817.5524620 0008 001535817.5514620 0009 0016388.517.5584620 0010 0017388.517.5604620 0011 001842920714620 0012 001942920744620 0013 00Open end 4 x 1813307251284620 0049 0014358251294620 0050 0015358251324620 0051 0016389251404620 0052 0017389251364620 0053 00184210251474620 0054 00194210251474620 0055 00215011251714620 0056 00225011251654620 0057 00245312251674620 0058 00276013302194620 0059 00306614302454620 0060 0032661432.52464620 0061 0034661432.52394620 0062 00B ALLHStandard end fitting tools with TAGTypeHexB H W L gOrdering No.mm mm mm mm mm Flared end 9 x 121022127.117.5574620 0028 001122.5128.617.5554620 0029 001223.512917.5594620 0030 001325.2121017.5554620 0031 001427131117.5604620 0032 001630131317.5654620 0033 001731.5131417.5654620 0034 0018331514.817.5744620 0035 001934.51515.819804620 0036 002137.51516.219884620 0037 002239151719924620 0038 002442151819754620 0039 00TypeAH L gOrdering No.mm mm mm mm Blank end 9 x12for making up specials 8 x 1414.58304620 0048 00Blank end 14 x1811 x 2521.521984620 0084 00Blank end 21 x2613 x 3030132204620 0085 00ALHBLWLHStandard end fitting tools with TAGTypeHexB H L g Ordering No. mm mm mm mm Ring end 9 x 12713817.5374620 0014 00814.2817.5404620 0015 001017.2917.5444620 0016 001118.5917.5414620 0017 0012201217.5494620 0018 001321.51217.5564620 0019 0014231217.5524620 0020 001524.21217.5524620 0021 001625.71317.5544620 0022 001727.21317.5594620 0023 001828.51317.5564620 0024 001930.31317.5654620 0025 0021331517.5714620 0026 002234.51517.5744620 0027 00Ring end 14 x 181321.511251274620 0063 00142311251234620 0064 001524.211251284620 0065 001625.712251334620 0066 001727.212251354620 0067 001828.512251344620 0068 001930.512251384620 0069 00213315251444620 0070 002234.515251454620 0071 002437.515251534620 0072 002741.517251624620 0073 00304519251824620 0074 003247.519251814620 0075 003450.519282104620 0076 00365319282034620 0077 00415920302404620 0078 00BLHTypeHexB H L gOrdering No.in mm mm mm Reversible ratchet 9 x 121/42214.517.5624620 0043 003/8332417.51364620 0044 001/23328.317.51474620 0045 00Reversible ratchet 14 x 181/24326.2253024620 0081 00*3/45030.7254674620 0082 00Reversible ratchet 21 x 263/4693062.513504620 0086 00BLHThe TAG placed on the ratchet defines the Pset. NOTE: Since several sockets could be used, it is recom -mended to hold the socket in such a way that it is not possible to remove it (e.g. using a pin).* The maximum torque which can be applied with 4620 0081 00 is 300 Nm.Standard end fitting tools without TAGTypeAB H L g Ordering No. mm mm mm mm Open end 9 x 12722517.5408059 0975 ********.5398059 0975 01926 5.517.5388059 0975 021026 5.517.5428059 0975 031126 5.517.5418059 0975 041230717.5438059 0975 051330717.5488059 0975 061435817.5528059 0975 071535817.5518059 0975 *******.517.5588059 0975 *******.517.5608059 0975 101842920718059 0975 111942920748059 0975 12Open end 14 x 1813307251288059 0976 0014358251298059 0976 0115358251328059 0976 0216389251408059 0976 0317389251368059 0976 04184210251478059 0976 05194210251478059 0976 06215011251718059 0976 07225011251658059 0976 08245312251678059 0976 09276013302198059 0976 10306614302458059 0976 1132661432.52468059 0976 1234661432.52398059 0976 13B ALHTypeHexB H W L gOrdering No.mm mm mm mm mm Flared end 9 x 121022127.117.5578059 0975 271122.5128.617.5558059 0975 281223.512917.5598059 0975 291325.2121017.5558059 0975 301427131117.5608059 0975 311630131317.5658059 0975 321731.5131417.5658059 0975 3318331514.817.5748059 0975 341934.51515.819808059 0975 352137.51516.219888059 0975 362239151719928059 0975 372442151819758059 0975 38B L WH TypeHexB H L g Ordering No. in mm mm mm Reversible ratchet 9 x 121/42214.517.5628059 0975 423/8332417.51368059 0975 431/23328.317.51478059 0975 44Reversible ratchet 14 x 181/24326.2 253028059 0976 32*3/45030.7254678059 0976 33Reversible ratchet 21 x 263/4693062.513508059 0976 38B LHStandard end fitting tools without TAGTypeHexB H L g Ordering No. mm mm mm mm Ring end 9 x 12713817.5378059 0975 13814.2817.5408059 0975 141017.2917.5448059 0975 151118.5917.5418059 0975 1612201217.5498059 0975 171321.51217.5568059 0975 1814231217.5528059 0975 191524.21217.5528059 0975 201625.71317.5548059 0975 211727.21317.5598059 0975 221828.51317.5568059 0975 231930.31317.5658059 0975 2421331517.5718059 0975 252234.51517.5748059 0975 26Ring end 14 x 181321.511 251278059 0976 14142311251238059 0976 151524.211251288059 0976 161625.712251338059 0976 171727.212251358059 0976 181828.512251348059 0976 191930.512251388059 0976 20213315251448059 0976 212234.515251458059 0976 222437.515251538059 0976 232741.517251628059 0976 24304519251828059 0976 253247.519251818059 0976 263450.519282108059 0976 27365319282038059 0976 28415920302408059 0976 29B L H TypeHex B H L g Ordering No. in mm mm mm Bits holder 9 x 121/4141017.5508059 0975 455/161612.517.5478059 0975 46Bits holder 14 x 185/161612.5251128059 0976 34BLHTypeHex B H L g Ordering No. in mm mm mm Fixed square 9 x 121/4221417.5718059 0975 393/8221417.5768059 0975 401/2221417.5828059 0975 41Fixed square 14 x 181/23018252038059 0976 303/44025253968059 0976 31BLHTypeA H L gOrdering No.mm mm mm mm Blank end 9 x 12for making up specials 8 x 1414.58308059 0975 47Blank end 14 x 1811 x 2521.521988059 0976 35Blank end 21 x 2613 x 3030132208059 0976 36ALHL* The maximum torque which can be applied with 8059 0976 32 is 300 Nm.ECO DESIGN STwrenchAtlas Copco BLMVia Guglielmo Pepe, 11 Paderno Dugnano (MI) - Italy 9 8 3 3 1 9 0 9 0 1 2 0 1 5 : 1–E N ©A t l a s C o p c o B L M , M i l a n , I t a l y . P r o d u c t i o n : A t l a s C o p c o B L M . 2 0 2 0。
自动传输设备操作手册说明书

1 M anual operation (unloaded) provided for all product configurations; manual operation (under load)available for select catalog configurations.2 Feature/rating available for select catalog configurations.Unmatched performance, safety and serviceabilityProven performance and reliability•Automatic bypass switch provides operational redundancy and quickly restores power to criticalloads when the ATS has been isolated for test or removed for service•Automatic, non-automatic and manual A operation modes provide multiple methods of transferring the load between power sources•UL 1008 listed short-circuit and short-time B withstand closing current ratingsmaximize system reliability •Tethered remote controlallows an operator to initiate a non-automatic transfer outside the arc flash boundaryEnhanced safety•Unique three-door,compartmentalized design provides steel barriers protecting workers from energized components •All doors open/closeindependently eliminating unnecessary exposure to adjacent compartments •Integral safety interlocks automatically open the main contacts prior to the ATS or automatic bypass switch being isolated for test or removed for service•Rear shutters B automatically close to isolate bus stabs when the ATS or automatic bypass switch is being racked outEaton has enhanced its comprehensive portfolio of UL T 1008 and CSA 178 listed bypass isolation ATSsolutions with power contactor type designs specifically engineered for applications between 100 and 3000 A.Our bypass isolation ATSs are not only simple to operate, but also available in a broad selection of configurations and features to meet a wide variety of application requirements.When coupled with our extensive custom engineering capabilities, Eaton’s innovative three-door bypass isolation ATS design, robust compartmentalized construction, and redundant automatic operation set the standard for concurrent serviceability, worker safety, and optimizing critical system uptime.Improved serviceability•Innovative three-door design eliminates the need to schedule shutdowns for routine test, inspection or maintenance•Maintenance isolationswitch (MIS) permits service personnel to electricallyisolate control compartment elements and minimize shock hazard prior to beginning work —without disruption to critical loads•Control compartment door and adjoining electrical panel slide forward from the enclosure to provide easy access to wiring and components•Dual drawout design allows the ATS or automatic bypass switch to be disconnected from the electrical bus and isolated in cell for regular testing as prescribed by code (NFPA T 70, 99, 110)•Testing of isolated switch can be performed while ATS or automatic bypass switch is in automatic or non-automatic mode of operationSimplified installation and integration•Field-configurable terminals allow cable ingress at top/bottom for power source and load connections•Internal floor-mount anchors minimize footprint andfacilitate efficient integration into an equipment lineup •Seismic certified to OSHPD,CBC, IBC and UBC•Front and rear access availableFeatures and benefitsBypass isolationContactor type, 100–3000 AOpen/closed transitionDesign featuresDual automatic technologyEaton’s unique design includes an automatic bypass switch and an ATS within a single assembly to provide redundant automatic operation and uninterrupted power to critical loads.Optimize reliability and maximize uptimeThe automatic bypass switch and ATS can be racked out and isolated in cell for regular testing to ensure the entire bypass isolation transfer switch is maintained in proper operating condition.Facilitate scheduled maintenance The automatic bypass switch or ATS can be withdrawn for visual inspection andcompletely removed for bench testing without impacting automatic operation.Enhance worker safetyThe upper and lower doors can be operated independently, maintaining electrical isolation of the energized compartment.T esting… it’s as easy as 1-2-3 A three-step operator interface helps simplify testing procedures of the automatic bypass switch or ATS when racked out to the isolated position.Safe and serviceableEngineered for safety, athree-door compartmentalized construction coupled with an MIS allow personnel to perform maintenance on the bypass isolation transfer switch while energized.To mitigate shock hazard, the MIS can be placed in the maintenance position prior to opening the door, electrically isolating elements of the control compartment from system and control voltage.Once isolated, the control compartment door can beopened and adjoining electrical panel slid forward, allowing a technician to safely inspect, troubleshoot and replace electrical components.Upon completion, the door is closed and MIS returned to the normal operation position.Multiple operation modes Local operation is possible in the following modes:•Automatic •Non-automatic •Manual AIn Automatic mode, the transfer switch is self-acting, and atransfer is automatically initiated by the intelligent controller logic.In Non-Automatic mode, a transfer is initiated by theoperator using a door-mounted selector switch or an optional tethered remote control.In Manual mode, a transfer is initiated by the operator using controls mounted directly on the automatic bypass switch or ATS.Alternatively, a transfer can be initiated remotely via an HMi remote annunciator controller or network communication.Automatic bypass switch With the upper door open, operators can draw out the automatic bypass switch for inspection or maintenance.With the upper door closed, operators can rack out, isolate and test the automatic bypass switch in cell.Automatic transfer switch With the lower door open,operators can draw out the ATS for inspection or maintenance. With the lower door closed, operators can rack out, isolate and test the ATS in cell.Control compartment door and adjoining electrical panel slide forward.MIS provides ability to electrically isolate control compartment elements prior to start of maintenance.Safe, easy and spacious access to wiring and components.Electrical load remains connected to power during maintenance procedures.Featuring simplified testing procedures for the ATS and automatic bypass switchT ethered remote control for non-automatic operationA Manual operation (unloaded) provided for all product configurations;manual operation (under load) available for select catalog configurations.2EATON Bypass isolation automatic transfer switches (ATS)Product selectionCatalog numbering systemTechnical specificationsA Check with your local Eaton sales representative for NEMA 12 and NEMA 4X enclosure specifications. NEMA 3R stainless steel available upon request.B Dimensions in inches (mm) and weight in lb (kg). Data is approximate, subject to change, and representative of a typical product configuration.Please reference product outline drawing(s) for latest information. Custom-engineered enclosure options available upon request.A Standard mechanical lugs are UL listed, solderless screw-type Cu/Al. Number of conductors and size range shown is per pole and representative of typical product configuration.B Two-hole compression lug or bus connect provisions available upon request. Please contact your local Eaton sales representative for more details.C Only applies to wye system configuration with solid neutral. For four-pole (switched neutral) configurations, the number and size of conductors supported will mimic the Normal,Emergency and Load terminal information shown.ote: N Some catalog number combinations may not be available. For additional information, please contact your local Eaton sales representative.3EATON Bypass isolation automatic transfer switches (ATS)UL 1008 listed withstand closing current ratingsATC-900—intelligent controlEaton’s ATC-900 controller brings ease of use, adaptability, supervisory and programming capabilities to mission-criticalapplications. The 4.3-inch color TFT display provides simple arrow keys for quick screen navigation and easy viewing of event logs as well as recorded time-stamped events. Field configuration of programmable I/O allows user adaptability to special requirements.1Time duration is 0.13 sec. maximum.4EATON Bypass isolation automatic transfer switches (ATS)Eaton is a registered trademark.All other trademarks are property of their respective owners.Eaton5050 Mainway Burlington, Ontario L7L 5Z1 CanadaEatonCanada.ca© 2020 EatonAll Rights Reserved Printed in CanadaPublication No. PA140014EN October 2021HMi remote annunciator controllerEvolving arc flash regulations and requirements for personal protective equipment are driving more and more end users toward the use of remote monitoring and control devices. Eaton’s HMi remote annunciator controller offers a simple and cost-effective means of managing up to eight ATSs via serial or ethernet communication.In many cases, standard products can be custom-order engineered to meet unique application needs. For additional information, please contact your local Eaton sales representative.Custom-order engineeringRemote annunciator controllerT /bypassATSFollow us on social media to get the latest product and support information.。
7950 XRS 路由器配置指南说明书

Getting StartedIn This ChapterThis chapter provides process flow information to configure routing entities, virtual routers, IP andMAC filters, and Cflowd.Alcatel-Lucent 7750 SR-Series Router Configuration Pro-cessTable 2 lists the tasks necessary to configure logical IP routing interfaces, virtual routers, IP andMAC-based filtering, and Cflowd.This guide is presented in an overall logical configuration flow. Each section describes a softwarearea and provides CLI syntax and command usage to configure parameters for a functional area. Table 2: Configuration Processincluding router interfaces andaddresses, router IDs, autonomoussystems, and confederations.VRRP VRRP on page 305Protocol configura-tionIP and MAC filters Filter Policies on page 409Cflowd Cflowd on page 563Standards and Protocol Support on page 599 Reference List of IEEE, IETF, and otherproprietary entities.Getting StartedNote: In SR OS 12.0.R4 any function that displays an IPv6 address or prefix changes to reflectrules described in RFC 5952, A Recommendation for IPv6 Address Text Representation.Specifically, hexadecimal letters in IPv6 addresses are now represented in lowercase, and thecorrect compression of all leading zeros is displayed. This changes visible display outputcompared to previous SR OS releases. Previous SR OS behavior can cause issues with operatorscripts that use standard IPv6 address expressions and with libraries that have standard IPv6parsing as per RFC 5952 rules. See the section on IPv6 Addresses in this guide for moreinformation.。
空客缩略语

3D Three Dimensional (Lat, Long, Alt)4D Four Dimensional (Lat, Long, Alt, Time)A AmpereA AlternateA AmberA AreaA AirA-D Airbus DeutschlandA-E Airbus EspanaA-F Airbus FranceA-UK Airbus UKAA Arithmetical AverageAA Airworthiness AuthoritiesAAAH Airbus Approved Abbreviations HandbookAAC Airline Administrative CommunicationsAADC Analog Air Data ComputerAAL Above Aerodrome LevelAAMG Airbus Application Management GroupAAP Additional Attendant PanelAAP Aft Attendant PanelABBR AbbreviationABCD Airbus Collective Data DictionaryABCU Alternate Braking Control UnitABD Airbus DirectivesABM AbeamABM APU Build-up ManualABN AbnormalABNORM AbnormalABRN AirborneABS Autobrake SystemABS VAL Absolute ValueABSORB AbsorberABV AboveAC Airplane Characteristics for Airport PlanningAC Alternating CurrentAC Advisory CircularACARS Aircraft Communication Addressing and Reporting System ACAS Airborne Collision Avoidance SystemACC Area Control CentreACC Active Clearance ControlACCEL Acceleration/AccelerateACCESS AccessoryACCLRM AccelerometerACCU AccumulatorACD Airworthiness Certification DossierACD Airframe Certification DocumentACDB Aircraft Component Data BaseACE Altimeter Control EquipmentACE Airbus Concurrent EngineeringACFT AircraftACFU Aircraft Check Follow UpACIA Asynchronous Communications Interface Adaptor ACJ Advisory Circular-JointACK AcknowledgeACM Aircraft Conversion ManualACM Abbreviated Component Maintenance ManualACMB Aircraft Configuration Management BoardACMM Abbreviated Component Maintenance ManualACMM Aircraft Configuration Meta ModelACMP Airframe Condition Monitoring ProcedureACMR Aircraft Configuration Management RulesACMS Aircraft Condition Monitoring SystemACN Aircraft Classification NumberACOB Automatic Call Out BoxACOC Air Cooled Oil CoolerACP Altimeter Check PointACP Area Call PanelACP Audio Control PanelACQ AcquireACQN AcquisitionACRT Additional Cross Reference TableACS AccessACS Alternating Current SupplyACT Additional Center TankACT ActiveACT ActivityACTD ActuatedACTG ActuatingACTIV ActiveACTN ActionACTR ActuatorACTVT ActivateACU Antenna Coupler UnitACVR Alternating Current Voltage RatioAD AerodromeAD Airplane DatumAD Airworthiness DirectiveADAM Airbus Spares Distribution and Materials System ADAU Auxiliary Data Acquisition UnitADB Area Distribution BoxADC Air Data ComputerADC Airbus Delivery CentreADCL Airworthiness Directives Compliance ListADCN Avionics Data Communication NetworkADCOMS Advanced Configuration Management SystemADD Addition, AdditionalADD Aircraft Description Data BaseADD Aircraft Design DeclarationADD BY Added ByADF Automatic Direction FinderADG Air Driven GeneratorADI Attitude Director IndicatorADIRS Air Data/Inertial Reference SystemADIRU Air Data/Inertial Reference UnitADJ AdjustADJMT AdjustmentADM Air Data ModuleADO Airbus Documentation OfficeADPM Aircraft Deactivation Procedures ManualADPTN AdaptationADPTR AdapterADR Advisory RouteADR Air Data ReferenceADRES Aircraft Documentation Retrieval SystemADRS AddressADS Automatic Dependent SurveillanceADS Air Data SystemADU Align Display UnitADV AdvisoryAEB Airline Engineering BulletinAECMA The European Association of Aerospace Industries AEEC Airlines Electronic Engineering CommitteeAERO Aviation Routine Weather ReportAES Aircraft Earth StationAEVC Avionics Equipment Ventilation ComputerAEX Access AuthorizedAF DME Arc to Fixed WaypointAF All FreighterAF Audio FrequencyAFB Antifriction BearingAFC Automatic Frequency ControlAFCS Automatic Flight Control SystemAFDX Avionics Full Duplex Switched EthernetAFECU Automatic Fire Extinguishing Control UnitAFIS Airbus In-Flight Information ServicesAFL Auto FlushAFMC Auxiliary Fuel Management ComputerAFN ATS Facilities NotificationAFR AirframeAFS Automatic Flight SystemAFTN Aeronautical Fixed Telecommunication NetworkAFU Artificial Feel UnitAGB Accessory GearboxAGB Angle GearboxAGC Automatic Gain ControlAGE Aircraft Ground EquipmentAGG Airbus General GuideAGL Above Ground LevelAGMT AugmentAGW Actual Gross WeightAH Ampere HourAHP Anti-Hijacking PanelAHRS Attitude and Heading Reference SystemAHRU Attitude and Heading Reference UnitAI Anti-IcingAIB Airbus IndustrieAIBU Advanced Integrated Ballast UnitAIC Access Illustration CardsAIC Airbus Integrated CompanyAICC Aviation Industry CBT CommitteeAID Aircraft Installation DelayAIDA Airbus Industrie Drawing AccessAIDS Aircraft Integrated Data SystemAIG Accident InvestigationAIL AileronAIM Aircraft Integrated MaintenanceAIM-FANS Airbus Interoperable Modular-Future Air Navigation Sys AIMS Airbus Industrie Material SpecificationAIMS Airbus Inventory Management SystemAIM/CRM Airbus Integrated Management/Cockpit Resource Management AINA Airbus North AmericaAINS Aircraft Information Network SystemAIP Attendant Indication PanelAIP Aeronautical Information PublicationAIPS Airbus Process SpecificationAIQI Airbus Industrie Quality InstructionAIR Aircraft Inspection ReportAIRCOND Air ConditioningAIS Audio Integrated SystemAIS Aeronautical Information ServiceAISI American Iron and Steel InstituteAITM Airbus Test MethodAL AirlineALERFA Alert PhaseALF Aft Looking ForwardALHP Airframe Life-History ProgramALIGN AlignmentALPHA Angle-of-AttackALPHANUM AlphanumericalALS Approach Light SystemALSCU Auxiliary Level Sensing Control UnitALT AltitudeALT ACQ Altitude AcquireALT TO Alternate ToALTM AltimeterALTN Alternate, AlternativeALTU Annunciator Light Test UnitALU Arithmetic and Logic UnitAM Amplitude ModulationAM Airbus Means and Methods DocumentAMB AmbientAMC Acceptable Means of ComplianceAMJ Advisory Material-JointAMM Aircraft Maintenance ManualAMM AmmeterAMP AmpereAMP AmperageAMPL AmplifierAMS Aircraft Modification StatusAMS Aerospace Material SpecificationAMS Aeronautical Material SpecificationsAMTOSS Aircraft Maintenance Task Oriented Support System AMU Audio Management UnitAN Air NavigationANCE AnnounceAND Aircraft Nose DownANI Analog InputANLG AnalogicANN AnnunciatorANN LT Annunciator LightANNCE AnnounceANNCMT AnnouncementANO Analog OutputANPT Aeronautical National Taper Pipe ThreadsANSI American National Standards InstituteANSU Aircraft Network Server UnitANT AntennaANU Aircraft Nose UpAO Access OpeningAOA Angle-Of-AttackAOAS Angle of Attack SensorAOC Airline Operational ControlAOC Air Operator's CertificateAOD Audio on DemandAOG Aircraft On GroundAOHX Air/Oil Heat ExchangerAOLS Airbus On-Line ServicesAOM Aircraft Operating ManualAOT All Operator TelexAP Airbus ProcedureAP AutopilotAP Airborne PrinterAPASHE Aircraft Publication Automated Shipping Expedite APC Area Positive ControlAPI Application Programming InterfaceAPLC Aircraft Power Line ConditionerAPM ARINC Processing ModuleAPM Airport Planning ManualAPM Aircraft Performance Monitoring ProgramAPP Approach Control-Approach Control OfficeAPP AppearanceAPPR ApproachAPPROX ApproximatelyAPPU Asymmetry Position Pick Off UnitAPQ Airline Pre-QualificationAPS Aircraft Prepared for ServiceAPS Auxiliary Power SupplyAPU Auxiliary Power UnitAPU AFE APU Automatic Fire Extinguishing Control UnitAP/FD Autopilot/Flight DirectorAQP Advanced Qualification ProgramAR As RequiredARG Arresting Gear or HookARINC Aeronautical Radio IncorporatedARM Airworthiness Review MeetingARM Aircraft Recovery ManualARMD ArmedARMG ArmingARMT ArmamentARN Aircraft Registration NumberARND AroundARO After Receipt OrderARP Aerospace Recommended PracticeARP Aerodrome Reference Point - Airport Reference Point ARPT AirportARR Arrival, ArrivingART Active Repair TimeARTCC Air Route Traffic Control CentreARTCLD ArticulatedARTF ArtificialARU Audio Reproducer UnitAS AirspeedAS AirscoopASA All Speed AileronASAP As soon as possibleASCII American Standard Code for Information Interchange ASCO Airbus Service Company Inc.ASD Accelerate Stop DistanceASDC Airline Service Data CollectionASE Airborne Support EquipmentASE Airbus Supplied EquipmentASF Amperes per Square FootASG Airbus Security GroupASI Airspeed IndicatorASIC Application Specific Integrated CircuitsASM American Society for MetalsASM Aircraft Schematics ManualASN Aerospatiale Norme (Standard)ASP Audio Selector PanelASPSU Autonomous Standby Power Supply UnitASR Airport Surveillance RadarASSY AssemblyASYM Asymmetric(al)AT AutothrottleAT AutothrustATA Air Transport Association of AmericaATA Actual Time of ArrivalATAM Airbus Takeoff Analysis ModuleATB ATA 100 BreakdownATC Air Traffic ControlATCA Air Traffic Control BoardATCDB Aircraft Technical Characteristics Data Base ATCH Attach(ment)ATCI Air Traffic Control and InformationATCK AttackATCRB Air Traffic Control Radar BeaconATCSS Air Traffic Control Data Link Signalling System ATD Aircraft Technical DefinitionATD Actual Time of DepartureATE Automatic Test EquipmentATEC Automatic Test Equipment ComplexATI Air Transport IndicatorATIMS Air Traffic and Information Management System ATLAS Abbreviated Test Language for Avionics Systems ATLAS Abbreviated Test Language for All SystemsATM Aircraft Transportability ManualATM Air Traffic ManagementATM Available Ton-MileATMG Airbus Technical Management GroupATMS Advanced Text Management SystemATN Aeronautical Telecommunications NetworkATO Authorization to OfferATR Austin Trumbull RadioATRCCS Automatic Turbine Rotor Clearance Control System ATS Air Traffic ServiceATS Airbus Technical SpecificationATS Autothrottle SystemATS Autothrust SystemATSU Air Traffic Service UnitATT AttitudeATT Attitude ReferenceATTEN AttenuationATTND AttendantATZ Aerodrome Traffic ZoneAUD AudioAUDSWTGSYS A udio Switching SystemAUDSWTGUNIT Audio Switching UnitAUTH AuthorizeAUTO AutomaticAUTOCAL AutocalibrationAUTOLAND Automatic LandingAUW All-Up WeightAUX AuxiliaryAVAIL AvailableAVG AverageAVIONICS Aviation ElectronicsAVNCS AvionicsAVRS Audio/Video Recording SystemAWB Air WaybillAWG Audible Warning GeneratorAWG American Wire GageAWL Aircraft Wiring ListAWLS All Weather Landing SystemAWM Aircraft Wiring ManualAWS American Welding SocietyAWY AirwayAX Access AuthorizedAX Longitudinal AccelerationAY Lateral AccelerationAZ Vertical AccelerationAZ AzimuthAZFW Actual Zero Fuel WeightA/BRK AutobrakeA/C AircraftA/COLL Anti-CollisionA/D Analog/DigitalA/D Analog to Digital Converter (conversion)A/DC Analog-to-Digital ConverterA/F Auto FlightA/G Air to GroundA.ICE Anti-ice, Anti-icingA/L AirlineA/N AlphanumericA/N SIZE Alpha Numeric SizeA/R Audio ReproducerA/S Auto StabilizationA/S AirspeedA/SKID Anti-SkidA/STAB Auto StabilizerA/T Adjustment/TestA/THR AutothrustA.T.I.S Airbus Technical Information SystemA/XFMR AutotransformerB BlueBAABI Basic Approved ATA Breakdown IndexBAF BaffleBAFO Best and Final OfferBAL Basic Assembly Languagebar10?kPaBARC Barometric Altitude Rate ComputerBARO BarometricBAT Battery (Electrical)BBRG Ball BearingBC Baggage Container TrainBCD Binary Coded DecimalBCDS BITE Centralized Data SystemBCL Battery Charge LimiterBCMS Brake Control and Monitoring SystemBCN BeaconBCRC Bulk Crew Rest CompartmentBCRU Battery Charge and Rectifier UnitBCU Brake Control UnitBCWP Budgeted Cost of Work PerformedBCWS Budgeted Cost of Work ScheduledBDLI Bundesverband der Deutschen Luft-und Raumfahrt Industrie BEA Bureau d'Enqu阾e AccidentBEL CRK BellcrankBER Beyond Economical RepairBETW BetweenBEV BevelBEW Basic Empty WeightBFD Bi-Folding DoorBFDAS Basic Flight Data Acquisition SystemBFE Buyer Furnished Equipment BFEMS BFE Management SystemBFO Beat Frequency Oscillator BFR BufferBG Build Group (Assembly Group) BGC Build Group ComponentBGM Boarding MusicBGS Build Group Stack-UpBH Block HoursBHD BulkheadBIST Built-in Self TestBITE Built-in Test EquipmentBIU BITE Interface UnitBK BlackBK UP Back UpBL BleedBLC Basic Lines CatalogBLES Brake Life Extension System BLG Body Landing GearBLK BlockBLK BlackBLKT BlanketBLOW BlowerBLST BallastBLT BoltBLV Bleed ValveBLW BelowBM BeamBMC Bleed Monitoring Computer BMS Bulletin M閠閛 Sp閏ialBND BondedBNDG BondingBNDRY BoundaryBNR BinaryBNR Binary WordsBO Body OdourBO Blocking OscillatorBOH Brake-Off WeightBOT BottomBOT Begin of TapeBP Bottom PlugBR BrownBRC BraceBRD BraidBRDG BridgeBRG BearingBRK BrakeBRKNG BrakingBRKR BreakerBRKS BrakesBRKT BracketBRT Bright, BrightnessBSCU Braking/Steering Control UnitBSHG BushingBSU Beam Steering UnitBT Bus TieBTC Bus Tie ContactorBTL BottleBTMU Brake Temperature Monitoring UnitBTN ButtonBTR Bus Tie RelayBTU British Thermal UnitBU Battery UnitBUS BusbarBYDU Back-Up Yaw Damper UnitBYP BypassB/B Back-BeamB/D Bottom of DescentC Celsius, CentigradeC CyanC CloseC Clearc Equal MarginC Cold (Electric Point)C ComparatorC ConvertibleC-MOS Complementary Metal Oxyde SemiconductorC of A Certificate of AirworthinessCA Cable AssemblyCA CableCAA Civil Aviation AuthorityCAATS Computer Assisted Aircraft Trouble ShootingCAB CabinCAB PRESSCabin PressurizationCAD Computer Aided DesignCADETS Computer Assisted Documentation Education Tutorial System CAG Circulation A閞ienne G閚閞aleCAGE Commercial and Government EntityCAGE Commercial and Government EntityCAI Combustion Area InspectionCAL Calibration, CalibratedCALC Cargo Acceptance and Load ControlCAM Computer Aided ManufacturingCAM Cabin Assignment ModuleCAN CanopyCANC CancelCANTIL CantileverCAO Cargo Aircraft OnlyCAOA Corrected Angle Of AttackCAOM Cabin Attendant Operating ManualCAP CapacitorCAPLTY CapabilityCAPT CaptainCAR Civil Aviation RequirementsCAR CargoCARE Continuing Airframe - Health Review and Evaluation CARE Common Airbus Requirements EngineeringCARP CarpetCAS Computed Air SpeedCAS Collision Avoidance SystemCAS Calibrated Air SpeedCAS Calculated Air SpeedCAT Clear Air TurbulenceCAT CategoryCATCH Complex Anomaly Tracking and SearchCAUT CautionCAUT LT Caution LightCBAL CounterbalanceCBIT Continuous BITECBMS Circuit Breaker Monitoring SystemCBMU Circuit Breaker Monitoring UnitCBO Cycles between OverhaulCBORE CounterboreCBR California Bearing RatioCBS Cost Breakdown StructureCBSV Cycles Between Scheduled VisitsCC Current ComparatorCCC Crash Crew ChartCCC Component Change CardCCCP Compressor Cavity Control PressureCCG Cabin Configuration GuideCCITT Consultative Committee International Telegraphy & Teleph CCOM Cabin Crew Operating ManualCCQ Cross Crew QualificationCCR Credit Card ReaderCCR Customer Change RegisterCCRC Cabin Crew Rest CompartmentCCRM Cabin Crew Rest ModuleCCS Cabin Communications SystemCCW Counter ClockwiseCD Count DragCD Cold DrawnCD Control DisplayCD-ROM Compact Disc - Read Only MemoryCD-WD Component Data Working DocumentCDDS Component Documentation Data SystemCDE Consumption Data Exchange CardCDIM Component Data Instruction ManualCDL Configuration Deviation ListCDP Compressor Discharge PressureCDS Cold Drawn SteelCDS Component Documentation StatusCDS Control and Display SystemCDU Control and Display UnitCDU Center Drive UnitCE Central EntityCECAM Centralized Cabin MonitoringCED Cooling Effect DetectorCEET Cabin Emergency Evacuation TrainerCEL Component Evolution ListCELLI Ceiling Emergency LED LightCEO Chief Executive OfficerCEPT Council of European Posts and Telegraphs CEV Clutch Electro ValveCF Course to a Fixed WaypointCFDIU Centralized Fault Display Interface Unit CFDS Centralized Fault Display SystemCFE Customer Furnished EquipmentCFH Cubic Feet per HourCFM Cubic Feet per MinuteCFM Cable Fabrication ManualCFMI CFM InternationalCFR Code of Federal RegulationsCFRP Carbon Fiber Reinforced PlasticCFS Cold Finished SteelCFS Cabin File ServerCG Center of GravityCGCS Center of Gravity Control SystemCGM Computer Graphics MetafileCH Centre HatrackCH CharacterCH ChargeCHAM ChamferCHAN ChannelCHAS ChassisCHG ChangeCHK CheckCHM ChimeCHMBR ChamberCHRG ChargeCHRO ChronometerCI Course to an InterceptCI Conversion InstructionCI Configuration ItemCi CurieCI Cast ironCICS Customer Information Control SystemCICS/VS Customer Information Control System/Virtual Storage CIDS Cabin Intercommunication Data SystemCIM Continuous Image MicrofilmCIN Change Identification NumberCINS Cabin Information Network SystemCIT Compressor Inlet TemperatureCIU Camera Interface UnitCK CheckCKD CheckedCKPT CockpitCKT CircuitCL ClutchCL Center LineCL ClipCL Check ListCL ClimbCLB ClimbCLCTR CollectorCLD ClosedCLDB Component Location Data BankCLG CeilingCLG Centerline Landing GearCLK ClockCLM Component Location ManualCLN ClinometerCLNG CeilingCLOG CloggingCLP ClampCLPR ClapperCLR ClearCLR ALT Clearance AltitudeCLRD ClearedCLS Cargo Loading System ManualCLS Cargo Loading SystemCLSD ClosedCLSG ClosingCLTM Component Location Training ManualCLV ClevisCM Conversion ManualCM Crew MemberCM Call MaintenanceCM CentimetersCM Collective ModificationCMC Central Maintenance ComputerCMD CommandCMEU Cabin Passenger Management Memory Expansion Unit CMFLR Cam FollowerCMI Computer Managed InstructionCML Consumable Material ListCMM Component Maintenance ManualCMM Calibration Memory ModuleCMMM Component Maintenance Manual ManufacturerCMP Customer Maintenance ProgramCMPLRY ComplementaryCMPNT ComponentCMPS CPLRCompass CouplerCMPTG ComputingCMPTR ComputerCMRLR Cam RollerCMS Code Mati鑢e Soci閠?CMS Cabin Management SystemCMS Central Maintenance SystemCMS Component Maintenance SheetCNA Common Nozzle AssemblyCNCT ConnectCNCTD ConnectedCNCTN ConnectionCNCTR ConnectorCNCTRC ConcentricCNCV ConcaveCND ConduitCNSU Cabin Network Server UnitCNTNR ContainerCNTOR ContactorCNTR CounterCNTRTR ConcentratorCO Cut-OffCO CompanyCO RTE Company RouteCOAX CoaxialCOC Customer Originated ChangeCOHO Coherent OscillatorCOL ColumnCOM CommunicationCOM CommonCombL Combustible LiquidCOMDL Coding ModuleCOML CommercialCOMP CompensatorCOMP CompassCOMPSN CompensationCOMPT CompartmentCOMPT TEMP C ompartment TemperatureCOMPTR ComparatorCOMTN CommutationCOND Conditioned, ConditioningCONDTN ConditionCONDTR ConditionerCONFIG ConfigurationCONT Continue, ContinuousCONT ContourCONT ControllerCONV ConverterCOO Chief Operating OfficerCOOL Cooling, CoolerCOORD CoordinateCOPI CopilotCORA Customer Order AdministrationCORCTD CorrectedCORR CorrectCORR CorrugateCORR CorrugationCor.M Corrosive MaterialCOS CosineCOT CotterCOTS Commercial Off-The-ShelfCOUNT CounterCOV CoverCOWL CowlingCP Clock PulseCPC Cabin Pressure ControllerCPCS Cabin Pressure Control SystemCPCU Cabin Pressure Control UnitCPDLC Controller-Pilot DataLink Communications CPIOM Core Processing Input/Output ModuleCPL CoupleCPLD CoupledCPLG CouplingCPLR CouplerCPMS Cabin and Passenger Management System CPMU Cabin Passenger Management UnitCPRSR CompressorCPT CompartmentCPT CaptureCPU Central Processing UnitCR CruiseCR Cold RolledCRC Camera Ready CopyCRC Cyclic Redundancy CheckCRC Crew Rest CompartmentCRC Continuous Repetitive Chime CRE Corrosion-ResistantCRES Corrosion-Resistant SteelCRG CargoCRI Certification Review ItemCRK CrankCRL CollarCRR Component Reliability Report CRS CourseCRS Cold Rolled SteelCRSN CorrosionCRT Cathode Ray TubeCRU Card Reader UnitCRZ CruiseCS CentistokesCS Cabin Cleaners StepsCS Call SwitchCS Center SparCSD Constant Speed DriveCSE Course Set ErrorCSF/L Continuous Safe Flight/Landing CSI Cycles Since InstallationCSK CountersinkCSKH Countersunk HeadCSL ConsoleCSM Computer Software ManualCSM/G Constant Speed Motor/Generator CSN Catalog Sequence NumberCSS Cockpit System SimulatorCSTG CastingCSTR ConstraintCSU Command Sensor UnitCSV Cycles Since Last Shop Visit CT Current TransformerCT Center TapeCTA Control AreaCTF Central Test FacilitiesCTF.P Central Test Facility Response CTF.Q Central Test Facility QuestionsCTK Capacity Tonne KilometreCTK Center TankCTL ControlCTL CentralCTR CenterCTR Control ZoneCTR ContourCTRD CenteredCTSK CountersunkCTU Cabin Telecommunications UnitCTWT Counterweightcu CubicCU Control UnitCUDU Current Unbalance Detection UnitCUR CurrentCVL Configuration Variation ListCVR Cockpit Voice RecorderCVT Center Vent TubeCVU Crypto Voice UnitCW ClockwiseCWG Cockpit Working GroupCWLU Cabin Wireless LAN UnitCWS Control Wheel SteeringCWY ClearwayCY CycleCY Calendar Year - Current YearCYL CylinderC/B Circuit BreakerC/L Check ListC/M Command/MonitorC/M Crew MemberC/O Change OverC/S Call SignC/SSR Cost/Schedule Status ReportDA Drift AngleDABS Discrete Address Beacon SystemDAC Drawing Aperture CardDAC Digital to Analog ConverterDADC Digital Air Data ComputerDADS Digital Air Data SystemDAF Damping Augmentation FunctionDAMP DampingdaN Load (DecaNewton)DAR Digital AIDS RecorderDAS/STC Designated Alteration Station/Supplemental Type Certific DB DecibelDB Data BasedB DecibelDBBS Data Base Bulletin ServiceDBC Data Bus CommunicationDBD Data Basis for DesignDBLR DoublerdB(A)A-Weighted DecibelDC Direct CurrentDCD DecodeDCD Double Channel DuplexDCD Data Control and DisplayDCDR DecoderDCDU Datalink Control and Display UnitDCP Display Control PanelDCS Designated Certification SpecialistDCS Double Channel SimplexDCS Direct Current SupplyDCU Direction Control UnitDCV Directional Control ValveDCVR Direct Current Voltage RatioDDA Digital Differential AccumulationDDCU Dedicated Display and Control UnitDDI Design Drawing InstructionDDI Documentary Data InsertDDM Difference in Depth of ModulationDDM Digital Data ModuleDDP Declaration of Design and PerformanceDDRMI Digital Distance and Radio Magnetic IndicatorDDTS Digital Data Technology StandardsDDV Direct Drive ValveDEC DeclinationDECEL DecelerateDECR DecreaseDEDP Data Entry and Display PanelDEF DefinitionDEFDARS Digital Expandable Flt Data Acquisition & Recording Sys DEFL DeflectDEG DegreeDEL Delay MessageDEL DeleteDEL BY Deleted byDELTA P Differential PressureDEM Digital Electronic ModuleDEMOD DemodulatorDEP Data Entry PanelDEPLD DeployedDEPRESS DepressurizationDEPT DepartmentDES DescentDES Digital Equipment SimulatorDEST DestinationDET Detection, DetectorDETNG DeterminingDEU Decoder/Encoder UnitDEV DeviationDEVN DeviationDEW Delivery Empty WeightDEX Access DemandedDF Direction FinderDFA Delayed Flaps ApproachDFDAMU Digital Flight Data Acquisition and Management Unit DFDAU Digital Flight Data Acquisition UnitDFDR Digital Flight Data RecorderDFDRS Digital Flight Data Recording SystemDFIDU Dual Function Interactive Display UnitDFT DriftDG Directional GyroDGAC Direction Generale de l'Aviation CivileDGI Digital InputDGO Digital OutputDGTL DigitalDH Decision HeightDI DeicingDI Data InputDIA DiameterDIAPH DiaphragmDIFF DifferentialDIM DimmingDIM DimensionDIM Direction Input ModuleDIPLXR DiplexerDIR Direct, Direction, DirectorDIR Direction, Direct, DirectorDIR TO Direct toDIS-IN Discrete InputDISC Disconnect, DisconnectedDISCH Discharge, DischargedDISCTN DisconnectionDISRMD DisarmedDIST DistanceDISTR Distribute, Distribution, DistributorDITCH DitchingDITS Digital Information Transfer SystemDIU Digital Interface UnitDLC Direct Lift ControlDLK Data LinkDLOAD Data LoadingDLRB Data Loading Routing BoxDLS Data Loading SelectorDLY DelayDMA Direct Memory AccessDMC Direct Maintenance CostDMC Display Management ComputerDMC Design Modification Committee DMDLTR DemodulatorDME Distance Measuring EquipmentDMP Display Management ProcessorDMPR DamperDMU Data Management UnitDN DownDNI Drawing Numerical IndexDNLK DownlockDO Data OutputDO Design OfficeDOA Design Organisation ApprovalDOC Direct Operating CostDOC.DATA Documentary DataDOLLI Dome LED LightDOM Design Organisation ManualDOW Dry Operating WeightDP Data ProcessingDP Differential ProtectionDPCU Digital Passenger Control UnitDPDT Double Pole/Double ThrowDPI Differential Pressure IndicatorDPM Design Progress MeetingDR Dead ReckoningDR DoorDRIP Design Response Intended for Playback DRM Duct Repair ManualDRMI Distance Radio Magnetic Indicator DRVG DrivingDRVN DrivenDRVR DriverDS DownstreamDSAPP DisappearanceDSCRM DiscriminatorDSCRT DiscreteDSCS Doors and Escape Slides Control System DSDL Dedicated Serial Data LinkDSENGD DisengagedDSI Discrete InputDSO Discrete OutputDSPL DisplayDSTRK Desired TrackDSUG Drawing Set User GuideDTD Document Type DefinitionDTG Distance to GoDTMF Dual Tone Multiple FrequencyDTMS Damage Tolerance Monitoring SystemDTMU Damage Tolerance Monitoring UnitDU Display UnitDUM DummyDVD Digital Versatile DiskDWG DrawingDX Access DemandedDYNMTC DynamometricD/A Digital to AnalogD/D Engine Out Drift Down PointD/LNA Diplexer/Low Noise AmplifierD/O Description and OperationE EastEADI Electronic Attitude Director IndicatorEADS European Aeronautic Defence and Space Company EAROM Electrically Alterable Read Only MemoryEAS Equivalent AirspeedEAT Expected Approach TimeEBCU Emergency Brake Control UnitEBHA Electrical Backup Hydraulic ActuatorEBS Engine Build SpecificationEBU Engine Build-up UnitEC Engine ControlECAM Electronic Centralized Aircraft Monitoring ECB Electronic Control BoxECDB Equipment Central Data BankECM Engine Condition MonitoringECM Engineering Coordination MemoECMS Electrical Contactor Management SystemECMU Electrical Contactor Management UnitECN Engineering Change NoteECON EconomyECON EconomicECP Ecam Control PanelECS Electronic Cooling SystemECS Environmental Control SystemECSB Embedded Computer System BusECU Electronic Control UnitECUCV Electronic Control Unit Cooling ValveED Edge Distance。
Cardax_门禁系统使用说明
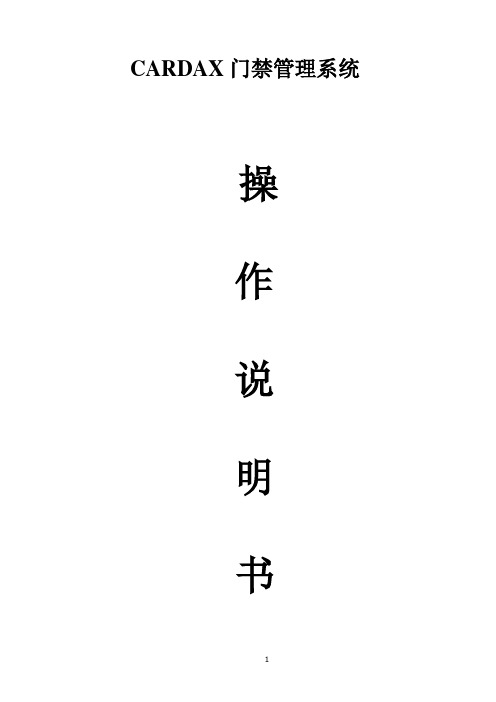
CARDAX门禁管理系统操作说明书目录概述 (1)系统功能技术 (1)系统功能及菜单 (5)备份与还原 (6)创建操作人权限组 (8)创建卡片类型 (10)访问控制技术 (12)访问群体 (22)区域与门 (27)系统维护 (28)1-1概述门禁管理系统是指根据大楼在不同时间对进出人员权限的设置,通过门禁管理软件下达指令给出入口现场的硬件设备,控制人员进出的综合出入口管理系统。
具体到实际情况,通过对工作人员以及外来人员进出权限的设置,以达到既能保障人员在管制区域合理流动的自由,又能维护管制区域内设备安全的目的。
设置出入口管理系统后,每当人员要进出受管制的区域时,必须先在该区域门旁的读卡器上刷一下卡,经现场控制器判断合法后开启电锁,门才能被打开。
每道门边的读卡器均通过现场控制器和系统集中控制器受到管理计算机的控制。
每一张卡根据系统设置,只能在规定时间内打开规定范围的门,采用这种管理方式既防止了钥匙管理的混乱现象,且人员不可能随便复制,极大地增强了安全。
如发生卡片丢失或人员调动的情况,只需在管理计算机上撤消该卡的进出权限即可。
由于门常处于闭锁状态,可以防止外来人员随意进入,如有人强制破门或进出后没有关门,门锁装置(门磁)将发出报警信号,管理计算机马上显示报警的门号,并及时通知相关管理人员进行处理。
由于人员的全部资料都存贮在管理计算机的数据库中,进出权限可通过管理软件事先设定,而且每一笔事件记录(包括合法与非法记录)均实时上传至管理计算机,这样门禁系统就可以实现完全的出入口电子控制,所以管理人员在控制中心即可方便的对管制区域进行监测和控制。
1-2系统功能技术1-31)系统总体结构系统采用三层体系架构:管理级,网络级与现场级。
所有控制设备都要安装在弱电间,既便于施工和将来的维护保养,又增加了系统的安全性。
管理级既系统管理平台及在此平台之上的各类应用模块,由服务器、各种应用工作站组成,通过以太网实现信息的交换。
3516BMPD操作说明
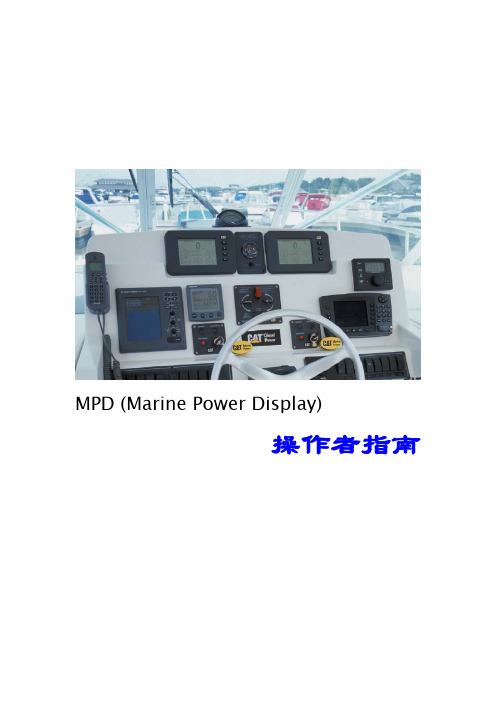
船桥、左舷、右舷、船塔、发动机室、后舱、驾驶桥楼、前舱 显示单位
英制、公制 航速单位
KNOTS、MPH、KPH
鲜俊林
第4页
nic.xian@
Marine Power Display操作者指南
C AT E R P I L L A R M A R I N E P O W E R D I S P L AY Operator’s Guide
SAE J1708 数据链路(有限参数)
鲜俊林
第2页
nic.xian@
Marine Power Display操作者指南
C AT E R P I L L A R M A R I N E P O W E R D I S P L AY Operator’s Guide
MARINE POWER DISPLAY CONFIGURATION AND OPERATION The Marine Power Display can accommodate up to three users with five screens for each. Three users can set up the Power Display screens to their preferences. The buttons have multiple functions dependent on which screen is displayed. The button primary functions for the gauge screens are:
综保使用说明书
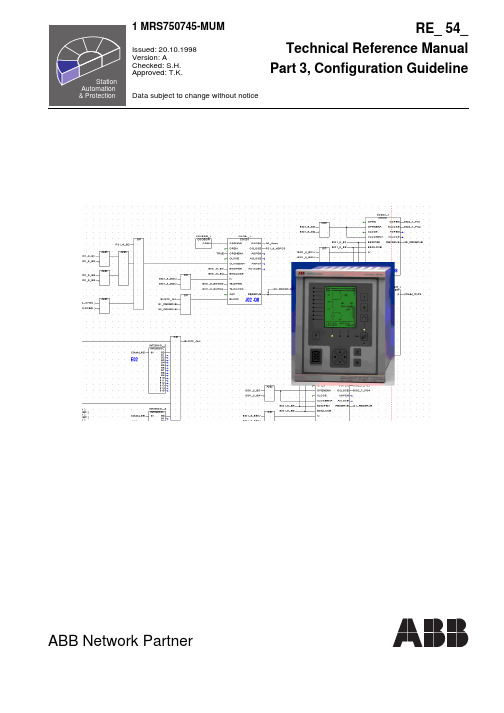
ABB Network PartnerRelay Configuration Tool (4)Specification for RE_ 54_ Configurations (5)Editing the RE_ 54_ Relay Terminal Configurations (6)Getting started (6)Libraries (6)Logical POUs (7)Program Organisation Unit (POU) (7)Physical hardware (9)Configuration (10)Resource (11)Hardware version (11)Analogue channels (11)Binary inputs (16)Measurements (17)Condition monitoring (18)Tasks (19)Programs and tasks (19)Task interval (19)Global variables (20)Declaring variables (21)Variables declared as global (25)Compiling the project (28)Main Configuration Rules for RE_ 54_ (29)General (29)Binary inputs (29)Explicit feedback (30)Measurement function blocks (31)Warnings (31)Execution order (32)F-key (33)APPENDIX A (35)APPENDIX B............................................................................................ 37-50 APPENDIX C............................................................................................ 51-65About this manualThis guideline describes in general the procedures for configuring the REF 54_ feeder terminals or REM 543 machine terminals correctly with the Relay Configuration Tool. Furthermore, chapter 4 provides some practical tips as well as recommendations and restrictions for doing the configuration.Please note that the examples and dialogue pictures of the Relay Configuration Tool in this manual refer to REF 54_ feeder terminals.1.Relay Configuration ToolThe Relay Configuration Tool, which is a standard programming system for RED500devices, is used for configuring the protection, control, condition monitoring, measure-ment and logic functions of the feeder terminal. The tool is based on the IEC 1131-3standard, which defines the programming language for relay terminals, and includes thefull range of IEC features. The PLC logics are programmed with Boolean functions,timers, counters, comparators and flip-flops. The programming language described inthis manual is a function block diagram (FBD) language.2.Specification for RE_ 54_ ConfigurationsPrior to starting the configuration of a relay terminal, the Specification for Relay Con-figuration is to be filled out. The specification can be found as appendix B for REF 54_and appendix C for REM 543 in the end of this manual.The purpose of the specification is to provide the technical information required for theproper configuration of the relay terminals.3.Editing the RE_ 54_ Relay Terminal Configurations 3.1.Getting startedStart up the tool by double clicking the icon. After adding a new object as an empty con-figuration to the CAP505 environment (refer to the CAP505 Operator’s Manual, 1MRS750838-RUM), the program opens an empty project template (see figure below) with atoolbar at the top. The next step is to build the project tree structure by inserting librar-ies, program organisation units (POUs) and target specific items to the project tree.The project tree editor is a window in which the whole project is represented as a tree.The project tree is illustrated with several icons. Most of the icons represent a file of theproject and different looking icons represent different types of files. The tree alwayscontains 4 subtrees: Libraries, Data Types, Logical POUs and Physical Hardware.Fig. 3.1-1. The project tree with its four subtrees.The project tree is the main tool for editing the project structure. Editing the projectstructure means inserting POUs or worksheets to the project structure or deleting exist-ing ones. The editors for editing the data of the code bodies and the variable declarationcan be called by double clicking the corresponding object icons.If you intend to edit an old project, note that saving the changes made with the “save as”project unchanged, the project has to be saved with a new name before making anychanges.3.1.1.LibrariesBefore editing any worksheets of POUs, the whole project tree structure must be build.The function block library (protection, control, measurement, condition monitoring andstandard functions) needed in the relay configuration is to be inserted to the “Libraries”subtree.Before inserting the library to the project, all worksheets are to be closed; otherwise theI/O description of function blocks will be confused. The programs, function blocks (e.g.NOC3Low, the low set stage of non-directional three-phase overcurrent protection) andfunctions of the library can be reused in the new project, which is edited.The library, e.g. REFLIB01 for REF54_ (see the figure below), includes all availablefunction blocks. Therefore, attention is to be paid to which function blocks can be usedin a specific configuration. For example, if the protection library PR116005(1MRS116005) has been ordered, the auto-reclose function block AR5Func cannot beinserted to the project since AR5Func is not included in that library.Fig. 3.1.1.-1. Libraries for REF54_ and REM 543.3.1.2.Logical POUsIn the project tree editor and in the library editor, the “Logical POUs” subtree representsa directory for all POUs related to the project. The maximum of 20 POUs can beinserted to the subtree. The figure below shows a “Logical POUs” subtree with 6 POUs;“Measure”, “Prot_Me” and “Co_CM_A” represent FBD (Function Block Diagram)programs, and “Horizon”, “CONDIS” and “SWG” are FBD function blocks.Fig. 3.1.2.-1. “Logical POUs” subtree with 6 POUs.3.1.3.Program Organisation Unit (POU)Each Program Organisation Unit, a POU, consists of several worksheets: a POUdescription worksheet for comments, a variable worksheet for variable declarations anda code body worksheet for the relay configuration. The name of each worksheet is indi-cated beside the corresponding icon and the *-symbol after the name of a worksheetindicates that the worksheet has not been compiled yet.Fig. 3.1.3.-1. Program organisation unit with three worksheets.The description worksheet (e.g. ProtectT) illustrated below is for describing the POU or the configuration element. The worksheet is named by adding a ’T’ to the name of the POU.Fig. 3.1.3.-2. Description worksheet.The variable worksheet (e.g. ProtectV) is for the variable declaration. The worksheet is named by adding a ’V’ to the name of the POU.Fig. 3.1.3.-3. Variable declaration worksheet.A code body worksheet (e.g. Protect, Measure) is for a code body declaration in theform of an FBD, a Function Block Diagram. All configurations for relays of the RED500 platform are made in the graphical FBD language. A code body programmed in theFBD language is composed of functions and function blocks that are connected to eachother using variables or lines. An output of a function block can be connected to the out-put of another function block only via an OR gate (refer to section 4.1.)Fig. 3.1.3.-4. Code body declaration in FBD language.Even though the tool permits adding several graphical worksheets under one POU, onlyone worksheet is recommended to be used per POU. If more space is needed for a con-figuration, the worksheet size can be increased or, if more I/O points are required, thefunctionality can be divided to several POUs. Note that one POU has altogether 511 I/Opoints available for function blocks. For example, the function block NOC3High in thefigure above includes 15 I/O points, which means that there are still 496 I/O pointsavailable.3.1.4.Physical hardwareIn the project tree editor, the physical hardware is represented as a subtree (see below)after the hardware of the relay terminal, i.e. Configuration, Resource and Tasks, hasbeen defined.Fig. 3.1.4.-1. Example of a subtree for the physical hardware.The configuration elements available in the “Physical Hardware” subtree may differfrom configuration to configuration. Each terminal of the RED 500 platform can beconfigured separately.3.1.4.1.ConfigurationThe name and target of the configuration are first defined in the dialogue Properties/Configuration.Fig. 3.1.4.1.-1. Defining the configuration type.3.1.4.2.ResourceThe configuration “Conf” above is for the REF 543 resource (the selected processortype), which is defined in the dialogue Properties/Resource. The resource must also begiven a name.Fig. 3.1.4.2.-1. Defining the processor type.Hardware versionAfter selecting the processor type, click “Settings...” in the dialogue Properties/Resource (see figure above) to define the correct hardware version.Note! After selecting the correct hardware version (Relay Variant; see figure below), donot click OK but wait until the next dialogue opens and select “Analog Channels” (seefigure 3.1.4.2.-3.).Fig. 3.1.4.2.-2. Defining the hardware version.Analogue channelsIn the dialogue Settings/Analog Channels, click each channel in turn to select the meas-uring device and signal type for the channels used and select “Not in use” for otherchannels.Furthermore, the technical data and measurements for the selected channels are to becompleted correctly before the configuration is used in a real application.Fig. 3.1.4.2.-3. Defining the analogue channels.Technical dataFig. 3.1.4.2.-4. Defining the rated values for the selected channel.MeasurementsFor information about the special measurements required for each function block, refer to the Technical Descriptions of Functions (CD-ROM 1MRS 750889-MCD).Phase currents and voltagesIf the signal type selected for an analogue channel is to be shown in the MIMIC view via the MMIDATA_ function block (MIMIC dynamic data point), the true RMS mode must be selected in the “Special Measurements” dialogue. Moreover, in case the Inrush3 function block (3-phase transformer inrush and motor start-up current detector) is to be used, the 2nd harmonic restraint must be selected for the analogue channels (IL1, IL2, IL3) used.Fig. 3.1.4.2.-5. Selecting the required special measurement modes for phase current measurement.Neutral currentWhen e.g. the DEF2_ function block (directional earth-fault protection) is going to be used, intermittent earth-fault protection must be selected for the channel via which the current Io is measured. Unless intermittent earth-fault protection has been chosen, the following configuration error indication will appear on the display of the relay terminal ( # denotes the number of the analogue channel in question):System: SUPERVCh # errorFig. 3.1.4.2.-6. Selecting the required special measurement modes for neutral current measurement.FrequencyWhen, for example, any of the function blocks MEFR_ (system frequency measure-ment), SCVCSt_ or Freq1St_ is in use, frequency measurement must be selected for the channel via which the voltage is measured for frequency measurement (for example: Channel 10, Voltage Transformer 4, Signal type U3 / Measurements button in the “Con-figuration of REF543” dialogue).Fig. 3.1.4.2.-7. Selecting the required special measurement modes for frequency meas-urement.Virtual channelsIn case no measuring devices are applied for measuring residual voltage (Uo) and neu-tral current (Io), the virtual channels 11 and 12 must be used.Fig. 3.1.4.2.-8. Using virtual channels 11 and 12 in case no measuring devices are applied for measuring Io and Uo.In case of the virtual channel 12, voltage measuring devices must be associated with phase voltages.Fig. 3.1.4.2.-9. Associating voltage measuring devices with phase voltages.After a compiled configuration is downloaded to a relay and the relay is started (storing and resetting are done), it will internally check whether the analogue channels are cor-rectly configured regarding the analogue inputs of function blocks. If the connectedchannels have been configured incorretly, the ERR output signal of the specific function block goes active and the event E48 is sent. Furthermore, either the event E13 or E5 is sent depending on the function block in question.Binary inputsThe filter time is set for each binary input of the relay terminal via the resource settings dialogue “Binary Inputs”. Inversion of the inputs can also be set. For further informa-tion refer to the Technical Reference Manual of REF 54_ or REM 543.Fig. 3.1.4.2.-10. Defining the binary inputs.MeasurementsWhen the MEPE7 function block (power and energy measurement) is used, the measur-ing mode must be selected via the resource settings dialogue “Measurements”.Fig. 3.1.4.2.-11. Selecting the measuring mode for power and energy measurement.Condition monitoringValues for the circuit-breaker wear function blocks CMBWEAR 1 and 2 can be set via the resource settings dialogue “Condition Monitoring”.Fig. 3.1.4.2.-12. Setting the values for circuit-breaker wear.3.1.4.3.TasksPrograms and tasksPrograms are associated with tasks via the dialogues Properties/Task and Properties/Program. Cyclic tasks are activated within a specific time interval and the program isexecuted periodically.The two dialogues below illustrate the association of a program type (Prot_Me) with atask (Task1) (see also figure 3.1.4.-1. in section “Physical hardware”).Fig. 3.1.4.3.-1. Naming a cyclic task.Fig. 3.1.4.3.-2. Associating the selected task with the desired program type.Task intervalGenerally, the operation accuracy is increased when the task speed is increased, but atthe same time, the load of the microprocessors is increased as well. Although the taskspeed can be freely chosen with the tool, it is necessary to determine a maximum taskexecution interval for each function block; otherwise the operation accuracy and operatetimes for protection functions cannot be guaranteed. The maximum task executioninterval is based on test results and has also been used in the type testing of the functionblocks. The recommended task execution interval quaranteed by the manufactirer canbe found in section Technical Data in the technical description of each function block.According to the standard, the Relay Configuration Tool includes the possibility ofdefining the tasks on two different levels:1) each POU (= program organisation unit) can be tied to a separate task2) a separate function block inside a POU can be tied to any taskHowever, the alternative 2) is not yet supported in the RED environment, which meansthat if a separate function block inside a POU is given a separate task definition, it willbe ignored when transferred to the relay. This means that when the function blocks arebeing placed in different POUs, not only the category of the function (protection, con-trol, etc.) but also the maximum task execution interval should be considered since allfunction blocks inside a POU will run at the same speed.For further information about the microprocessor loads and task execution intervals offunction blocks refer to the manual “Technical Descriptions of Functions, Introduction”(CD-ROM: Technical Descriptions of Functions, 1MRS750889-MCD).The task execution interval for each task is defined via the dialogue Properties/Task(click “Settings...”). For example, the task execution interval for Task1 in figure belowis defined as 10 ms, which means that the program Prot_Me is run 100 times per onesecond.Fig. 3.1.4.3.-3. Setting the task execution interval for a program.3.2.Global variablesThe physical contacts of RE_ 54_ are defined in the “Global Variables” worksheet.Declarations for the physical contacts are automatically defined when the correct hard-ware version of RE_ 54_ is selected. Declarations for the analogue channels are createdafter the analogue channel settings defined in the resource settings dialogue have beenapproved.Fig. 3.2-1. Global Variables worksheet.3.3.Declaring variablesAt its beginning, each programmable controller POU type declaration is to contain atleast one declaration part that specifies the types of the variables used in the organisa-tion unit. The declaration part shall have the textual form of one of the keywordsV AR_INPUT, VAR_OUTPUT, V AR and V AR_EXTERNAL followed by one or moredeclarations separated by semicolons and terminated by the keyword END_V AR. Allthe comments you write must be edited in parentheses and asterisks.(**********************************)(*Variable declaration*)(*of REF 541*)(**********************************)Caution is required regarding comments and variable declarations. The following codeexample will be compiled successfully but because of the non-closed comment theEND_VAR - V AR_EXTERNAL couple will be excluded and thus the channel numbersbecome local variables of the POU and they get the initial value zero.V AR (*AUTOINSERT*)NOC3Low_1:NOC3Low; (* Erroneous nonclosed comment *END_VARV AR_EXTERNALU12:SINT;(* Measuring channel 8 *)U23:SINT;(* Measuring channel 9 *)U31:SINT;(* Measuring channel 10 *)END_VARThree examples of creating the textual declaration for different kinds of graphical pro-grams are given below.EXAMPLE 1.•POU type:FBD program •Function block type declaration: VARINPUT1:BOOL :=FALSEINPUT2:BOOL :=FALSEINPUT3:BOOL :=FALSEOUTPUT:BOOL :=FALSE END_VARFig. 3.3-1. Function block image.EXAMPLE 2.•POU type:NOC3Low, manufacturer dependent function block •Function block type declaration:V AR_INPUTIL1:SINT :=0;(* Analogue channel *)IL2:SINT :=0;(* Analogue channel *)IL3:SINT :=0;(* Analogue channel *)BS1:BOOL :=FALSE;(* Blocking signal *)BS2:BOOL :=FALSE;(* Blocking signal *)TRIGG:BOOL :=FALSE;(* Triggering *)GROUP:BOOL :=FALSE;(* Grp1/Grp2 select *)DOUBLE:BOOL :=FALSE;(* Doubling signal *)BSREG:BOOL :=FALSE;(* Blocking registering *)RESET:BOOL :=FALSE;(* Reset signal *)END_VARV AR_OUTPUTSTART:BOOL :=FALSE; (* Start signal *)TRIP:BOOL :=FALSE; (* Trip signal *)CBFP:BOOL :=FALSE; (* CBFP signal *)ERR:BOOL :=FALSE; (* Error signal *)END_VARFig. 3.3-2. Function block image of NOC3Low.EXAMPLE 3.•POU type:Configurer dependent FBD function block CONDIS •Function block type declaration:Fig. 3.3-3. Type declaration of the configurer made function block CONDIS.Fig. 3.3-4. Use of the configurer made function block CONDIS.Fig. 3.3-5. Contents of the CONDIS function block.In the example 3 above, part of the configuration has been separated to a configurermade function block called CONDIS. Such function blocks may not be given namesalready belonging to library functions blocks or IEC standard function blocks. Thefunction block CONDIS has been used like any other function block in the graphicalprogram. The order of inputs of a function block that has been inserted to a worksheetmay not be changed. It must also be remembered that a function block with an instancenamed by the configurer can only be inserted to the project once.3.4.Variables declared as globalThe range of validity of the declarations included in the declaration part shall be“local”to the POU in which the declaration part is contained. One exception to this rule are var-iables that have been declared to be “global”. Such variables are only accessible to aPOU via a V AR_EXTERNAL declaration. The type of a variable declared in aV AR_EXTERNAL block shall agree with the type declared in the V AR_GLOBALblock of the associated program, configuration or resource.Fig. 3.4-1. Local and global variables.The figure above illustrates the ways how values of variables can be communicated among software elements. Variable values within a program can be communicated directly by connecting the output of one program element to the input of another or via local variables such as the variable y illustrated in the upper left corner of the figure above. In the same configuration, variable values can be communicated between pro-grams via global variables such as the variable x illustrated in “Configuration C” in the figure above. In such a case, make sure that the global variable is only written from one location in the project. The global variable can still be read from several locations. Do not use binary inputs or outputs for data transfer between tasks.Despite the fact that according to the IEC standard 1131-3 all local variables that have no initial value are initially FALSE (0), the initial values for all local variables have to be given in the variable worksheet of the logical POU. This is because somewhere in the configuration, especially in the beginning of running the configuration i.e. when the relay is started up, the variable can be used before the initial value has been created for the variable. The initial values for global variables are given in the global variable worksheet (see CASE 1 below).CASE 1. Variables declarationV ARIABLE WORKSHEET of logical POU*********************************************************************V ARTRIPPING:BOOL:= FALSE;BLOCK:BOOL:= TRUE;TMP1:BOOL:= FALSE;END_VARV AR_EXTERNALPS1_4_HSPO1 :BOOL; (* Double pole high speed power output *)(* 4.1/10,11,12,13 *)PS1_4_HSPO2 :BOOL; (* Double pole high speed power output *)(* X4.1/15,16,17,18 *)PS1_4_HSPO3 :BOOL; (* Double pole high speed power output *)(* X4.1/6,7,8,9 *)END_VARV AR_EXTERNALTCS1_ALARM:BOOL;END_VAR********************************************************************* GLOBAL V ARIABLE WORKSHEET*********************************************************************V AR_GLOBALPS1_4_HSPO1AT %QX 1.1.2 :BOOL := FALSE;(* Double pole high speed power output X4.1/10,11,12,13 *) PS1_4_HSPO2AT %QX 1.2.2 :BOOL := FALSE;(* Double pole high speed power output X4.1/15,16,17,18 *) PS1_4_HSPO3AT %QX 1.3.2 :BOOL := FALSE;(* Double pole high speed power output X4.1/6,7,8,9 *) END_VARV AR_GLOBALTCS1_ALARM:BOOL:= FALSE;END_VAR*********************************************************************piling the projectThe “Build Project” mode in the “Make” menu is used to compile the whole project forthe first time after editing, which means compiling all POUs, global variables, resourcesetc., whereas the “Make” mode can be used to compile the worksheets that have beenedited. The changed worksheets are marked with an asterisk in the project tree editor.“Make” is the standard mode for compiling and should normally be used when you havefinished editing.In the Relay ConfigurationTool you can view the execution order of the different func-tions or function blocks in your worksheet. The execution order corresponds to theintermediate PLC code created while compiling. Note that the execution order can onlybe seen if you have already compiled the worksheet using the menu item “CompleteWorksheet” in the submenu “Make”.By editing the mwt.ini file, one can affect the execution order. The line below can beadded to section [MAKE]:SH_EXECUTION_ORDER_TOP_BOTTOMSets the order of execution of functions and function blocks in graphical editor0Sets the execution order from left to right1Sets the execution order from top to bottomThe default value is …0“. The execution order can only be changed when compiling aworksheet again.4.Main Configuration Rules for RE_ 54_4.1.General Make sure that all analogue signals are connected and all necessary inputs and outputs are wired. Note that the outputs of function blocks may not be connected together. There are also many other FBD programming rules to follow. One of the most typical rules is not to use the “wired-OR” connection. All signals that are connected to the same output signal (both output relays and horizontal communication outputs) must be connected via an OR-gate (see figure below).Fig. 4.1-1. Use of an explicit Boolean OR gate (on the right).4.2.Binary inputs Do not write binary inputs - like BIO2_7_BI2.Fig. 4.2-1. Writing global binary inputs is not allowed.Binary inputs can be read from several locations.I>I>>TRIP TRIP PS1_4_HSPO1PS1_4_HSPO1I>I>>TRIP TRIP PS1_4_HSPO1"wired-OR" structure is not allowed an explicit Boolean "OR" block is required instead ORFig. 4.2-2. Correct way of using global binary inputs.4.3.Explicit feedbackAn explicit feedback loop may not be used. In case the tool gives a warning about thefeedback loop after compiling, the loop must be broken up by connecting the input ofthe function block and the output of another function block separately to the auxiliaryvariable.Fig. 4.3-1. Explicit feedback loop is not allowed.Fig. 4.3-2. Explicit feedback via the auxiliary variable FEEDBACK.4.4.Measurement function blocksAll the measurement inputs of the function blocks must be connected. In case e.g. thethree-phase current measurement function block MECU3A is implemented by twophases of currents, one of the currents available must be connected to the remainingthird input of MECU3A. Unless something is connected to the third current input, thefunction block will attempt to use the sensor channel 1 instead of the empty channel,and if no measurements have been defined for channel 1, a supervision error will result.4.5.WarningsIn case of the indication “Warning: Instance ‘xx’ is never used” in connection with Array compilation, remove the corresponding instances of the function block from the varia-bles worksheet of the POU. The tool will not give a separate warning for unused varia-bles, which is why they need to be removed manually. When a global variable is addedto a sheet as a copy-paste -function, the global radio button has to be chosen (see figurebelow); otherwise the variable becomes a local variable of the POU, which is due to theauto-insert feature of the tool (global variable = V AR_EXTERNAL, local variable =V AR).Fig. 4.5-1. Copying a global variable to a worksheet of a POU.4.6.Execution orderCheck the execution order after the compilation. The connection of simple variables toeach other generates a code, the execution order of which in relation to the callingsequence of POUs cannot be seen by means of the Layout Execution Order function.Fig. 4.6-1. The INTERLOCKING variable is updated (TMP1) during the task executioncycle (see the execution order 1,2,3).In addition, the execution order may be illogical or even incorrect considering the func-tionality.Fig. 4.6-2. The explicit feedback (TMP1) delays the updating of the INTERLOCKINGvariable by one task execution cycle.If the MOVE function is used instead of direct connection, the execution order can beutilised in concluding whether the result is desirable.4.7.F-keyThe freely programmable F-key is declared as VAR_GLOBAL in the global variableworksheet as follows:F001V021:BOOL:=0;(* Free configuration point (F-key) *)The F-key parameter can be added to the configuration logic as an external variable(V AR_EXTERNAL). Similar parameters that can be inserted to a relay logic are listedbelow:F001V011:BOOL:=0;(*(W) Resetting of operation indications*)F001V012:BOOL:=0;(*(W) Resetting of operation indications & latched output signals*)F001V013:BOOL:=0;(*(*(W) Resetting of operation indications, latched output signals & wave-form memory*)*)F001V020:BOOL:=0;(*(W) Resetting of accumulated energy measurement*) F001V021:BOOL:=0;(’(R, W) Free configuration point (F-key)*)F002V004:BOOL:=0;(*(*(R, W) Control: Interlocking bypass mode for all control objects (Enables all)*)*)F002V005:USINT:=0;(*(W) Control: Recent control position*) F002V006:BOOL:=0;(*(W) Control: Virtual LON input poll status*)F900V251:BOOL:=0;(*(*(W) Control: Execute all command for selected objects (inside module)*)*)F900V252:BOOL:=0;(*(W) Control: Cancel all command for selected objects (inside module)*)F000V251:BOOL:=0;(*(*(W) Control: Execute all command for selected objects (inside module)*)*)F000V252:BOOL:=0;(*(W) Control: Cancel all command for selected objects (inside module)*)。
MODEM Mobile Connection设备使用说明说明书

FAQ & AnswersIf you meet problems in service, please refer to the following answers for guidance. Ifthe problems persist, please contact your supplier via the contact detail in your operator user guide.Problem DescriptionPossible Causes Problem Solving The system cannot run the installation program automaticallyThe system configuration is having difficulty with the auto-run software. The device will appear as a virtual disc in ‘My Computer’ on the PC’s start menu. Click on the icon and start the autorun.exe. If you have previously installed a version of the program, please uninstall it first.After installation, the system doesn't install the driver program properly.The system configuration is having difficulty with the auto-run software. Please install the driver program manually. The driver program can be found in the installation folder; C:\Program Files\MODEM Mobile Connection\driversAfter the device is plugged in, the UI program doesn't run automatically.The system configuration is incorrect. Please open the UI program manually. You can find it in the Start menu: ¨C:\Program menu or an alias icon on the desktop.1. You are in the place where there is no GSM/ GPRS/EDGE/WCDMA /HSDPA(HSUPA) network coverage. Such places include underground parking garages, tunnels, and someremote rural areas.1.Change the location to find a coverage.2. The device is not properly connected.2. Close the device safely as usual,pull out the device and reinsert the device again.3. The SIM/USIM card isn't inserted properly.3. Remove and reinsert the SIM/USIM card correctly.After restarting the computer, there is no signalindicated.4. The MODEM device is positioned in such a way as that adversely affects the devices signal reception.4. Adjust the angle/position of the MODEM device or its proximity to other electronic devices.When the Device is being installed, the computer cannot find it.1. The installation programs of the MODEM device have not been installed properly. 1. Run the installation program first then connect the device. Now install the drivers as normal in Windows.2. The device is not connected properly. 2. Restart the computer, or reconnect the device.3. The SIM/USIM card is not inserted properly.3. Reinsert the SIM/USIM cardcorrectly.1. The SMS center number is incorrect.1. Your device is preconfigured so itis unlikely that it will need changing. However if it is missing or incorrect contact your operator.Sent Message failure.2. The network is busy or you are in an area with no signal.2. Try later or move to an area with a stronger signal.1. You are in the place where there is no GSM/ GPRS/ EDGE/ WCDMA/ HSDPA(HSUPA) network coverage. 1. Move to an area with good signal.2. The network is busy.2. Try later.3. The APN in the user configuration file is incorrect.3. Check the APN in the userconfiguration file in the "Network settings".4. The device data is corrupted.4. Local network access or the target server maybe experiencing problems. Retry data request.Data connection failed.5. The network type has been selected manually, but is incorrect.5. Reselect the network type according to the type of the SIM/USIM card.1. After connection, you are unable to open web pages.1. Check that the APN in the configuration files is correct.2. IE browser is causing problems.2. Upgrade to the new version or reinstall the IE browser.3. Your operating system maybe infected by a virus. Worm Blaster for xample can affect upload and downloaded data flow, resulting in an inability to access a website.e 3. Use the professional anti-virussoftware to check and remove the virus. Connected to the Internet, but it cannot open any website page.4. You have connected to an APN which cannot connect to the Internet.4. This happens when you are changing any preset operator value in the setting section. Check the entry and enter the correct APN from your operator.。
Code Reader 2600 Configuration Guide

Code Reader™ 2600 Configuration GuideModem Settings (for use with the Charging Station with an Embedded CodeXML® Modem or the external CodeXML® M3 Modem when paired with a CR2600)Modem ID and Firmware Version....................................................................................................................................................................................5 (A2) USB Keyboard Communication Mode - Default ..............................................................................................................................................................5 (A3) USB HID POS (Terminal 1D 131)....................................................................................................................................................................................5 (A4) RS232 Communication Mode (Applicable for the CodeXML® M3 Modem Only) ...........................................................................................................5 (B1) RS232 9600 Baud Rate (applicable for the CodeXML® M3 Modem Only).....................................................................................................................5 (B2) RS232 19200 Baud Rate (applicable for the CodeXML® M3 Modem Only)...................................................................................................................5 (B3) RS232 38400 Baud Rate (applicable for the CodeXML® M3 Modem Only)...................................................................................................................5 (B4) RS232 57600 Baud Rate (applicable for the CodeXML® M3 Modem Only)..................................................................................................................5 (C1) RS232 115200 Baud Rate - Default (applicable for the CodeXML® M3 Modem Only) .................................................................................................5 (C2) US English Keyboard Mapping - Leading 0 ...................................................................................................................................................................5 (C3) Keyboard Control Characters for Non Printable ASCII ..................................................................................................................................................5 (C4) USB Keyboard Mode No Leading 0 - Default.................................................................................................................................................................5 (D1) Universal Keyboard Mapping .........................................................................................................................................................................................5 (D2) French Keyboard............................................................................................................................................................................................................5 (D3) German Keyboard ..........................................................................................................................................................................................................5 (D4) Japanese Keyboard.........................................................................................................................................................................................................5 (E1) Enable Preemptive Mode ................................................................................................................................................................................................5 (E1) Disable Preemptive Mode - Default.................................................................................................................................................................................5 (E3) Enable Reader Paging - Default......................................................................................................................................................................................5 (E4) Disable Reader Paging................................................................................................................................................................................................... 5 (F1)CR2600 Reader SettingsReader ID and Firmware Version ....................................................................................................................................................................................5 (F2)Reset, Clear and Save Reader SettingsReset Reader to RF Factory Defaults ............................................................................................................................................................................6 (A1) Clear All Stored Data and Images and Reboot .............................................................................................................................................................6 (A2) Clear all JavaScript Rules..............................................................................................................................................................................................6 (A3) Save All Reader Settings...............................................................................................................................................................................................6 (A4)Reader Text SettingsReader Text Commands On ...........................................................................................................................................................................................6 (B1) Reader Text Commands Off - Default ...........................................................................................................................................................................6 (B2)Communication SettingUSB Downloader Mode...................................................................................................................................................................................................6 (B3)Batch Mode SettingsUSB Keyboard Mode (Batch Mode Only)........................................................................................................................................................................6 (B4) USB Virtual COM - 1 Way Mode (Batch Mode Only) .....................................................................................................................................................6 (C1)Batch Mode Enable - Send and Log...............................................................................................................................................................................6 (C2) Batch Mode Disable - Default.........................................................................................................................................................................................6 (C3) Batch Mode Enable - Log Only.......................................................................................................................................................................................6 (C4)Enable Alternative Operating System (Windows CE/MAC/Linux) - Batch Mode Only ...................................................................................................6 (D2) Disable Alternative Operating System - Batch Mode Only - Default...............................................................................................................................6 (D3)USB Speed - High Speed (Batch Mode only) - Default..................................................................................................................................................6 (D4) USB Speed - Full Speed (Batch Mode only) ..................................................................................................................................................................6 (E1)Image SettingsRead Both Wide and High Density Field - Default...........................................................................................................................................................6 (E2)Read Wide Field Only......................................................................................................................................................................................................6 (E3) Read High Density Field Only .........................................................................................................................................................................................6 (E4)Targeting SettingsTargeting On - Default .....................................................................................................................................................................................................6 (F1) Targeting Off....................................................................................................................................................................................................................6 (F2)Continuous Trigger Optimization and SettingsContinuous Scan On .......................................................................................................................................................................................................6 (F3) Continuous Scan Off - Default.........................................................................................................................................................................................6 (F4)Scan DelayDuplicate Scan Disabled - Default..................................................................................................................................................................................7 (A1)1 sec Duplicate Scan Delay............................................................................................................................................................................................7 (A2)2 sec Duplicate Scan Delay............................................................................................................................................................................................7 (A3)3 sec Duplicate Scan Delay............................................................................................................................................................................................7 (A3) 5 sec Duplicate Scan Delay............................................................................................................................................................................................7 (B1) 10 sec Duplicate Scan Delay..........................................................................................................................................................................................7 (B2) 30 sec Duplicate Scan Delay..........................................................................................................................................................................................7 (B3) 1 hour Duplicate Scan Delay..........................................................................................................................................................................................7 (B4) 1 day Duplicate Scan Delay ...........................................................................................................................................................................................7 (C1)Prefix/Suffix SettingsPrefix - AIM IDs On........................................................................................................................................................................................................ 7 (D1) Prefix - AIM IDs Off - Default............................................................................................................................................................. .............................7 (D2) Prefix - Comma...............................................................................................................................................................................................................7 (D3) Prefix - Space.................................................................................................................................................................................................................7 (D4) Prefix - Tab (USB Keyboard Mode ONLY)......................................................................................................................................................................7 (E1) Prefix - Erase/None - Default..........................................................................................................................................................................................7 (E2) Suffix - Comma...............................................................................................................................................................................................................7 (E3) Suffix - Space .................................................................................................................................................................................................................7 (E4) Suffix - Enter (USB Keyboard Mode ONLY)...................................................................................................................................................................7 (F1) Suffix - Tab (USB Keyboard Mode ONLY)......................................................................................................................................................................7 (F2) Suffix - Erase/None - Default..........................................................................................................................................................................................7 (F3) Erase All Prefix & Suffix Data - Default...........................................................................................................................................................................7 (F4)Feedback SettingsBeep Volume 0%............................................................................................................................................................................................................8 (A1) Beep Volume 33%..........................................................................................................................................................................................................8 (A2) Beep Volume 67%..........................................................................................................................................................................................................8 (A3) Beep Volume 100% - Default .........................................................................................................................................................................................8 (A4) Beep On Vibrate On - Default.........................................................................................................................................................................................8 (B1) Beep Off Vibrate On .......................................................................................................................................................................................................8 (B2) Beep On Vibrate Off .......................................................................................................................................................................................................8 (B3) Beep Off Vibrate Off .......................................................................................................................................................................................................8 (B4)Bluetooth SettingsBluetooth Radio Out of Range Beep - On ..................................................................................................................................................................... 8 (C1) Bluetooth Radio Out of Range Vibrate - On ...................................................................................................................................................................8 (C2) Bluetooth Radio Out of Range Beep and Vibrate - On.................................................................................................................................................. 8 (C3) Bluetooth Radio Out of Range Beep and Vibrate - Off - Default ................................................................................................................................... 8 (C4) Bluetooth Radio Disconnect (Reconnect via QuickConnect Code)................................................................................................................................8 (D1)Remote Management SettingsRemote Management Enable.........................................................................................................................................................................................8 (D2) Remote Management Disable - Default .........................................................................................................................................................................8 (D3)Table of ContentsCell PhoneEnable Cell Phone Reading Enhancement....................................................................................................................................................................8 (E1) Disable Cell Phone Reading Enhancement - Default.....................................................................................................................................................8 (E2)SymbologiesAztec On - Default ...........................................................................................................................................................................................................8 (F1) Aztec Off..........................................................................................................................................................................................................................8 (F2) Aztec Inverse On.............................................................................................................................................................................................................8 (F3) Aztec Inverse & Normal...................................................................................................................................................................................................8 (F4) Codabar On - Default ......................................................................................................................................................................................................9 (A1) Codabar Off.....................................................................................................................................................................................................................9 (A2) Code 32 On .....................................................................................................................................................................................................................9 (A3) Code 32 Off - Default.......................................................................................................................................................................................................9 (A4) Code 39 On - Default.......................................................................................................................................................................................................9 (B1) Code 39 Off .....................................................................................................................................................................................................................9 (B2) Code 39 Enable Checksum.............................................................................................................................................................................................9 (B3) Code 39 Disable Checksum - Default ............................................................................................................................................................................ 9 (B4) Code 39 Enable Checksum and Strip ............................................................................................................................................................................9 (C1) Code 39 Extended Full ASCII On.................................................................................................................................................................................. 9 (C2) Code 39 Extended Full ASCII Off - Default ................................................................................................................................................................... 9 (C3) Code 93 On - Default......................................................................................................................................................................................................9 (C4) Code 93 Off ....................................................................................................................................................................................................................9 (D1) Code 128 On - Default ...................................................................................................................................................................................................9 (D2) Code 128 Off ..................................................................................................................................................................................................................9 (D3) Data Matrix (defaulted on and can not be disabled)Data Matrix Rectangle (defaulted on and can not be disabled)Data Matrix Inverse On....................................................................................................................................................................................................9 (E1) Data Matrix Inverse Off - Default.....................................................................................................................................................................................9 (E2) GS1 Limited DataBar On.................................................................................................................................................................................................9 (E3) GS1 DataBar 14/ Truncated 14 On .................................................................................................................................................................................9 (E4) GS1 DataBar Stacked On ...............................................................................................................................................................................................9 (F1) GS1 DataBar Expanded On ............................................................................................................................................................................................9 (F2) All GS1 DataBar On - Default..........................................................................................................................................................................................9 (F3) All GS1 DataBar Off ........................................................................................................................................................................................................9 (F4) Int 2 of 5 On - Default ................................................................................................................................................................................................... 10 (A1) Int 2 of 5 Off.................................................................................................................................................................................................................. 10 (A2) Int 2 of 5 with Control Character Stripped .....................................................................................................................................................................10 (A3) Int 2 of 5 Enable Checksum ..........................................................................................................................................................................................10 (A4) Int 2 of 5 Disable Checksum..........................................................................................................................................................................................10 (B1) MSI Plessey On - Default ..............................................................................................................................................................................................10 (B2) MSI Plessey Off.............................................................................................................................................................................................................10 (B3) PDF417 On - Default....................................................................................................................................................................................................10 (C1) PDF417 Off...................................................................................................................................................................................................................10 (C2) Plessey On ...................................................................................................................................................................................................................10 (C3) Plessey Off - Default.....................................................................................................................................................................................................10 (C4) QR Code On - Default ..................................................................................................................................................................................................10 (D1) QR Code Off.................................................................................................................................................................................................................10 (D2) QR Code Inverse and Standard On .............................................................................................................................................................................10 (D3) QR Code Inverse On....................................................................................................................................................................................................10 (D4) Straight 2 of 5 On ..........................................................................................................................................................................................................10 (E1) Straight 2 of 5 Off - Default............................................................................................................................................................................................10 (E2) UPC On - Default...........................................................................................................................................................................................................10 (E3) UPC Off .........................................................................................................................................................................................................................10 (E4) UPC Expansion Enable.................................................................................................................................................................................................10 (F1) UPC Expansion Disable - Default..................................................................................................................................................................................10 (F2) UPC Supplemental On ..................................................................................................................................................................................................10 (F3) UPC Supplemental Off - Default....................................................................................................................................................................................10 (F4)。
FAX-30 Operator’s Guide

FACSIMILE RECEIVER FAX-30Operator’s GuideThe purpose of this Operator's Guide is to provide basic operating procedures for this equipment. For more detailed information see the Operator's Manual.<For NavNet>Key Name Functions 1Trackball Chooses menu items. 2ALARM Displays alarm message. 3CLEAR Clears data.4MENUOpens FAX-30 menu;returns to standby.5ENTER knob Push: Registers setting. Rotate: Selects menuitems and options. Mayalso be used to enter alphanumeric data.6Alphanumeric keys Enter alphanumeric data.7POWER/BRILLLong press: Turns power off.Momentary press: Turnsthe power on; opens the display for adjustment of brilliance.8DISPDisplays the modeselection window.9Soft keysExecute the appropriatefunction.Accessing the FAX Mode1. Press the DISP key to show the displayselection window.EXT VIDEO WXFAX2. Rotate the ENTER knob to choose theWX FAX icon. 3. Push the ENTER knob to show the faxstand-by display.Automatic FAX Receiving1. At the standby display, press the WXFAX soft key. Thumbnails of receivedimages are shown.JMH JUN/05 03:46 JMH JUN/05 04:29 JMH JUN/05 05:212. Press the RCV WX FAX soft key.3. Press the CH SETUP soft key.4. Press the ZONE soft key to display theZONE window.5. Rotate the ENTER knob to choose zonedesired and press the ENTER soft key.6. Press the STATION soft key to show theSTATION option.7. Rotate the ENTER knob to choosedesired station and press the ENTERsoft key.8. Press the CHANNEL soft key to showthe CHANNEL options.9. Rotate the ENTER knob to choosechannel desired and press the ENTERsoft key.10. If necessary you may fine tune thefrequency, press the FREQ soft key.Then enter appropriate frequency.11. Press the RETURN soft key severaltimes to return to the stand-by display.The FAX-30 will receive the next scheduled broadcast from the station selected.Displaying Navtex Message1. At the standby display, press theNAVTEX soft key.2. Rotate the ENTER knob to choose themessage to display.3. Press the SELECT MSG soft key orpush the ENTER knob.4. Press the RETURN soft key severaltimes to return to the stand-by display.2<For PC>Accessing the FAX-30 Top Display1. Start up the browser software.2. Type in the FAX-30’s URLhttp://172.31.8.1 and then press theENTER key. The facsimile receiver topdisplay appears. (For one-touch accessto the FAX-30 make a bookmark.)3. Click WX FAX for facsimile or NAVTEXfor navtex to show the correspondingstandby display, which is where youbegin all facsimile (or navtex)operations.Facsimile standby display○1: Top menu○2: Click to return to top display.○3: Facsimile image thumbnails appear when received.○4: Facsimile image dataNavtex standby display○1: Top menu○2: click to return to top display.○3: Navtex message display area○4: Navtex message data○5: Navtex message listLogging out1. At the facsimile or navtex menu display,click “<Top” to return to the facsimilereceiver top display.2. Click LOGOUT to logout the PC fromFAX-30.Automatic FAX Receiving1. At the facsimile stand-by display, clickTIMER SETUP followed by PROGRAMLIST to show the timer schedule.2. Click the LIST column you want to set.For example, click the center column ofNo. 1. The following timer programmenu appears.33. Click the arrow button on ZONE andchoose desired zone.4. Click the arrow button on STATION andchoose desired station.5. Click the arrow button on CHANNEL andchoose desired channel or AUTO.6. Click the arrow button on IOC andchoose desired IOC or AUTO.7. Click the arrow button on SPEED andchoose desired speed or AUTO.8. Key in the start and end time.9. Click ON below FREQUENCY.10. Click OK.11. Click “<back” or Back button severaltimes to return to the top menu.12. Repeat steps 1-13 to set other timerschedule.13. At the facsimile stand-by display, clickTIMER SETUP.14. Click PROGRAM LIST.15. Click START.16. Click OK.17. Click “<back” or Back button to return tothe top menu.Displaying Navtex MessagesAt the navtex standby display, click themessage number at the top of the display.Navtex message dataIA55:Station ID (I), Category (A),Message No. (55)06/05:Date received03:57:Time received518kHz:FrequencyError rateOSE-62600-A4。
SINUMERIK Operate 4.5 SP6 HF3 for PCU 50.5 升级指南说明书

SINUMERIK 840D sl2016-06-13Upgrade InstructionsSINUMERIK Operate 4.5 SP6 HF3 for PCU 50.5_________________________________________________________________________________________ SINUMERIK Operate 04.05.06.03 (internal version 04.05.06.03.003) for PCU 50.5_________________________________________________________________________________________ A PCU 50.5 with pre-installed PCU base software WinXP from V1.3 or a PCU 50.5 with pre-installed PCU base software Win7 V1.0 is required in order to install this software::- PCU 50.5-C/XP 6FC5210-0DF52-2AA0 with PCU base software from V1.3- PCU 50.5-P/XP 6FC5210-0DF53-2AA0 with PCU base software from V1.3- PCU 50.5-C/W7 6FC5210-0DF52-3AA0 with PCU base software from V1.0- PCU 50.5-P/W7 6FC5210-0DF53-3AA0 with PCU base software from V1.0The Commissioning Guide for SINUMERIK Operate Operate 4.5 SP2, PCU base software V1.3 or Win7 V1.0, the Operator Components Manual and the Operating Manual SINUMERIK Operate 4.5 SP2 apply. Furthermore, the supplementary conditions published for CNC Software 4.5 SP6 HF3 must be taken into account.Before using SINUMERIK Integrate for Production (SIP), please read the notes provided in the Annex "SINUMERIK_Integrate_liesmich_Operate_4.5.6.pdf".SINUMERIK Operate comprises all texts in German, English, French, Italian, Spanish and “Chinese simplified“. In general, the help for setting and machine data is only provided in German and English. The V2.7.1 additional languages for SINUMERIK Operate can be used.SINUMERIK Operate 4.5 SP6 HF3 has only been released for operating∙an 840D sl NCU7x0 with CNC Software 4.5 SP6 HF3 or for a∙SIMATIC-CPU 317 / 319 in combination with HMI Pro sl.To do this, the PCU 50 must be integrated in the plant / system network. By default, the SINUMERIK Operate is connected to the NCU address 192.168.214.1. The NCU address can be set in the "NCU connection" screen under Commissioning / HMI.Note for laboratory operation: When connecting the PCU 50 to the X130 of the NCU, the simulation cannot be executed.The SINUMERIK Operate for PCU 50 does not include any technological cycles or measuring and ISO cycles. These are available on the CF card of the NCU and are automatically installed during the NCU startup – see also the relevant information provided in the Upgrade Instructions for the CNC Software 4.5 SP6.User texts must always be downloaded into the system in the UTF-8 format.SINUMERIK Operate for PCU 50 does not have general access to the CF card of the NCU. This means that option "user memory on CF card of the NCU" cannot be used.The "Local drive" in SINUMERIK Operate for PCU 50 WinXP is located on the hard disk underF:\hmisl\user\sinumerik\data, for PCU 50 Win7 underC:\ProgramData\siemens\MotionControl\user\sinumerik\data and is always available without option.STEP7 5.5 for SINUMERIK PCU 50 can also be integrated for SINUMERIK Operate. The desktop function "Step7 authorization" is used for this purpose.Important note for operation on PCU 50.5 Windows 7:Before deactivating the power supply of the PCU 50.5, shut down the system via the Operate softkey EXIT resp. Windows shutdown, analogously to a PC with Windows 7. You can use a UPS to protect the system against unexpected power cuts.The EXIT softkey can be made accessible to all operators by setting the display MD 9110 = 7.© Siemens AG 2016DF MC R&D 5Page 1 of 5InstallationImportant: If a version <= 4.5 SP3 of SINUMERIK Operate for PCU 50 has already been installed, it must first be uninstalled under Control Panel / Add or Remove Programs or Programs and Features.SINUMERIK Operate for PCU 50 is installed by calling the file Setup_HMIsl_......exe from the Windows desktop of the PCU 50. To do this, establish either a network connection to a PC using the DVD supplied or copy the software from the DVD supplied to a USB data medium that can then be directly connected to the PCU 50.3. The installation directory is permanently specified as F:\hmisl resp. C:\Program Files (x86).The installation version is requested during the installation:∙Operation on a SINUMERIK NCU (default)∙Operation on a SIMATIC-CPU 317 / 319∙Integration of .NET-Framework for OEM applicationsThe following settings are required in /oem/.../Systemconfiguration.ini:[miscellaneous]DoNotHandleSvcAdapter="ReadAD"For multiple EXEs: DoNotHandleSvcAdapter="ReadAD, SetAccessLevel"The EXEs which use the SVC adapter must be entered here, so execute GetObj()/releaseObj.If Operate crashes, .dmp files are stored in addition to the crash logs and allow a better analysis.The following information has to be entered into the file /card/user/sinumerik/hmi/cfg/slguiconfig.ini or /card/oem/sinumerik/hmi/cfg/slguiconfig.ini in order to solve the issue 288130 or 298506: [Keyboard]IgnoreSoftkeyRepeatings = false====================================================================Compatibility====================================================================SINUMERIK Operate 4.5 SP6 HF3 can be combined with 840D sl NCU 7x0.3 CNC SW 4.5 SP6 HF3.∙The help system is based on the documentation for the CNC SW 4.5 SP2.∙The NC alarm texts are based on the CNC SW 4.5 SP2.∙STEP7 for SINUMERIK PCU 50 from V5.5 can be integrated in SINUMERIK Operate 4.5 SPx where it can run.∙OEM applications which are based on the SINUMERIK Operate Programming Package 4.5 can run when using generally released interfaces.∙The available additional languages V4.5.2 for SINUMERIK Operate can be used.====================================================================Notes====================================================================System:∙If, in conjunction with STEP7 on PCU 50 WinXP, no communication is established between the HMI and the NCU, please check the settings made under Control Panel / Set PG/PC Interface. In addition to S7ONLINE, an Access PointSINUMERIK_CP (SINUMERIK 7xx) -> TCP/IP -> VIA Rhine III Fast Eth. ..<Board 2>must be included. If necessary, configure this Access Point as indicated.∙Editor: The key combination Shift+Insert must be used to edit cycle calls directly in the DIN code. At present, this is not provided on all SINUMERIK OPs. Remedy: Use an external PC keyboard.∙To operate the simulation, the NC-MD $MC_FRAME_ACS_SET must be set to 1.∙To operate a PCU50 with an external monitor, you can set the screen size of the Operate in the file … \user\sinumerik\hmi\cfg\slrs.ini with the entry[Global]Resolution = ; permissible values: 640x480, 800x600, 1024x768, 1280x1024∙As standard, in the Machine area, the "Retract" softkey is no longer available. It can be reactivated by creating the slmaconfig.xml in /oem/sinumerik/hmi/cfg file with the following content:<?xml version="1.0" encoding="UTF-8" standalone="yes" ?><CONFIGURATION><Settings><ShowRetractSoftkey type="bool" value="true" /></Settings></CONFIGURATION>∙Subsequently enter Autostart of Operate for a (another) user on PCU 50.5-Win7:On the desktop, start menu "All Programs", select Startup. Right-click on "Open". An Explorer is thenopened. In the right-hand window of Explorer, right click on "New" create " Shortcut".Then using "Browse ...", enter the "C:\Program Files(x86)\Siemens\MotionControl \siemens\sinumerik\hmi\ autostart\slstartup.exe" file.∙The “AppSight-Blackbox” is available in Operate (resource to analyze the causes of application crashes) and is active as standard. It can be deactivated using an entry in the run_hmi.ini file:[AppSight]; enabled could be set to true or false. Default: trueenabled=trueThe log file generated by AppSight-Blackbox in the case of a fault is called:…/user/sinumerik/hmi/log/hmi/blackbox_run_hmi.aslIt is written to when exiting Operate. It may be necessary to explicitly exit processes that are running.Together with the HMI crash or, this log file must be sent to the SINUMERIK hotline.∙When writing to a NodeID of the PLC via OPC-UA (e.g. "/Random/Plc/DB123.DBB0“), the valu e must not be transferred as a variant/string or string. This results in a false value being written. The value first has to be converted to a proper data type, e.g. Variant/Int32 or Int32.∙When simultaneously recording the same part programs several times in succession, the Alarm 17010 may be output.∙When executing part programs from network drives respectively editing files on network drives, the user must provide for a stable, interference-free network connection to the network drives.。
- 1、下载文档前请自行甄别文档内容的完整性,平台不提供额外的编辑、内容补充、找答案等附加服务。
- 2、"仅部分预览"的文档,不可在线预览部分如存在完整性等问题,可反馈申请退款(可完整预览的文档不适用该条件!)。
- 3、如文档侵犯您的权益,请联系客服反馈,我们会尽快为您处理(人工客服工作时间:9:00-18:30)。
ACJ Water/waste 3838 Water/wasteACJObjectivefaucets etc.Basic aircraft stalled.DescriptionEPAC selection mode IndividualWater/waste 38 ACJIntentionally left blank38 Water/wasteACJObjectiveflight and on the ground. Basic aircraftnormal flight conditions. Description•••ACJ Information systems 4646 Information systems ACJ 46.21.000 - Air Traffic Services Unit (ATSU) alternate equipmentObjectiveTo select an ATSU hardware and software configuration,capable of the following options (to be selected sepa-rately):- activation of high speed VHF datalink transmission(VDL mode 2)- activation of high speed software dataloading (compli-ant with AEEC 615A standard).Basic aircraftThe aircraft is equipped with an ATSU not capable ofhigh speed VHF datalink transmission (VDL mode 2) orhigh speed software dataloading.DescriptionIn order to activate the required ATSU functions it is nec-essary to have the adequate ATSU hardware and soft-ware platform. This option proposes the different ATSUconfigurations.EPAC selection modeIndividualInformation systems 46ACJ46 Information systemsACJ46.21.106 - Airbus standard Airline Operational Communication (AOC) softwarealternate equipmentObjectiveTo provide alternate supplier for Airbus standard defini-tion of Airline Operational Communication (AOC) soft-ware in the Air Traffic Service Unit (ATSU).Basic aircraftThe aircraft is equipped with a software diskette provid-ing Airbus standard definition of Airline Operational Communication (AOC) in the Air Traffic Service Unit (AT-SU).DescriptionThe baseline diskette providing Airbus standard defini-tion of Airline Operational Communication (AOC) in the Air Traffic Services Unit (ATSU) is provided by an alter-nate supplier.NoteNote 1: Use of the ATSU requires installation of airline ground system and contract with Datalink Service Pro-viders.Note 2: Customization of the AOC software Customization of the AOC function is the responsibility of the airline and its selected supplier. It should not require airworthiness re-certification of the ATSU. Particular at-tention should be given to compatibility of the custom-ized AOC software with the ATSU aircraft interface (core) software.Note 3: Customization of the ATSUIn order to use the ATSU, it must be configured with air-line specific information. Providing this information is supplied by the operator during the delivery process, Air-bus can handle the customization of the ATSU during aircraft delivery under direct responsibility of the airline (configuration of ACARS router and VHF scan mask). In addition, Airbus can install the customized AOC soft-ware.Should problem occur during the customization process or if the operator does not provide customization infor-mation in due time, the aircraft will be delivered with de-fault ATSU configuration: default router and scan mask configuration, selected standard AOC software. Information to be provided during the delivery process:Information systems 46 ACJ46.21.106 - Airbus standard Airline Operational Communication (AOC) softwarealternate equipment (Continued)•Airline Identification: 2 characters and 3 characterscode•List and regional applicability of Datalink Service Pro-viders contracted by the airline for VHF 3 Scan Mask(e.g. SITA Europe, SITA Pacific, Arinc, Avicom, AirCanada)•Customized AOC software diskettes.EPAC selection modeIndividual46 Information systemsACJInformation systems 46 ACJIntentionally left blank46 Information systemsACJObjectiveBasic aircraftmode A are installed. Description•2/AOA function •capable.Notecertification.Information systems 46 ACJIntentionally left blank46 Information systemsACJObjectiveBasic aircraftA429 bus. Descriptionthe avionics bay). Note••Information systems 46 ACJIntentionally left blank46 Information systemsACJObjectivetenance purposes.Basic aircraftNoneDescriptionhind the first officer seat.•••NoteIncompatible with:•ties in cockpit••third occupant DME •cockpit wall.ACJ Auxiliary Power Unit (APU) 4949 Auxiliary Power Unit (APU)ACJ 49.00.111 - Auxiliary Power Unit (APU) alternate equipmentObjectiveTo provide alternate APU.Basic aircraftThe APU is installed in the tailcone of the aircraft and theassociated Electronic Control Box (ECB) in the pressur-ized bulk cargo compartment, No. 5.DescriptionThe basic APU and ECB are replaced by alternateequipment, designed to be compatible with all aircraftsystem interfaces (drop-in installation).It is fully interchangeable with the basic equipment.EPAC selection modeIndividualAuxiliary Power Unit (APU) 49ACJ49 Auxiliary Power Unit (APU)ACJ51.00.115 - Fuselage and wings extended corrosion preventionObjectiveTo have an extended corrosion protection on fuselage and wings.Basic aircraftThe following areas are treated with Type III Corrosion Inhibitor (CI) & Water Repellent Fluid (WRF) as per AIMS 09-08-003:Fuselage•from frames C01 to C12, between stringers P32 LH and P32 RH•from frames C12 to C21, between stringers P19 LH and P19 RH•from frames C21 to C35, between stringers P32 LH and P32 RH•from frames C35 to C47.5, between stringers P23 LH and P23 RH•from frames C47.5 to C60, between stringers P36 LH and P36 RH•from frames C60 to C77, between stringers P23 LH and P23 RH•floorgrid (cross beam only) and tail cone, between stringers P13 LH and P13 RH.Doors•emergency exits •hatches•cargo holds doors•bulk compartment door.Vertical stabilizer•rear spar including servo-control.Horizontal stabilizer•rear spar including servo-control.Wings•MLG bay on areas of underwing and overwing panel (wing strut wells)•aft face of false rear spar•aft face of rear spar inboard of gear rib 5•aft faces of shroud box.DescriptionCorrosion prevention Type III is enlarged on fuselage, floor grid and wings.The following additional areas are protected:Fuselage•lower shell from frames C01 to C12, between string-ers P23 and P32 on LH and RH sides51.00.115 - Fuselage and wings extended corrosion prevention (Continued)•lower shell from frames C21 to C35, between string-ers P23 and P32 on LH and RH sides•lower shell from frames C47.5 to C60, betweenstringers P23 and P36 on LH and RH sides•the whole pressure bulk head, longitudinal beamsand seat rails between frames C36 and C70•floor panel connection sheets in the area sections 13to 18.Wings•all along forward face of front spar•all along aft face of rear spar•forward face of false rear spar•wing root joint and build door•pylon enclosure external top and bottom surfaces(forward face of front spar, aft face of D-nose subspar and adjacent leading edge ribs)•internal surfaces of the dry bay wing.EPAC selection modeIndividualIntentionally left blank51.22.300 - Alternate paint system on standard areas (fuselage, vertical stabilizersand nacelles)ObjectiveTo provide alternate paint systems for basic paintscheme on fuselage, vertical stabilizer and nacelles.Basic aircraftThe basic paint scheme on fuselage, vertical stabilizerand nacelles is:•primer•top coat.DescriptionThe fuselage, vertical stabilizer and nacelle are paintedusing paint according to the customers choice.EPAC selection modeIndividualorative adhesive film. Basic aircraftspray process. Descriptionfollowing criteria:••EPAC selection modeIndividualACJ Stabilizers 5555 StabilizersACJObjectiverepair at an early stage. Basic aircraftDescriptionals.NoteEPAC selection mode IndividualStabilizers 55ACJ55 Stabilizers ACJIntentionally left blankACJ Windows 5656 Windows ACJ 56.10.102 - Cockpit windows alternate equipmentObjectiveTo provide alternate equipment for cockpit windows.Basic aircraft• 2 front windshields made of glass (all fixed)• 4 lateral windows made of acrylic (2 sliding and2fixed).DescriptionThis modification consists in replacing the two front wind-shields and/or four lateral windows by windows from analternate manufacturer.EPAC selection modeIndividualWindows 56ACJ56 WindowsACJWindows 56ACJ56 Windows ACJIntentionally left blankACJ Engines 7272 Engines ACJ 72.01.119 - Engines selectionObjectiveTo allow basic engines selection by the customer.Basic aircraftThe following engines are installed:•CFM INTERNATIONAL (CFMI): CFM56-5B7/P at 27000 lbf nominal thrust,Or•INTERNATIONAL AERO ENGINES (IAE): V2527M-A5 at 26 500 lbf nominal thrust.Description•installation of CFMI or IAE engines•modification or pin programming of the associatedequipment: DMC, ELAC, FAC, FDIMU, FMGC, FWC.EPAC selection modeIndividualEngines 72ACJ72 Engines ACJACJ Oil 7979 Oil ACJ 79.00.101 - Engine, engine accessories and Auxiliary Power Unit (APU) alternatelubricating oilObjectiveTo provide alternate engine/APU lubricating oil.Basic aircraftOil MOBIL JET II is used.DescriptionChange lubricating oil type in the following equipment:•engine•engine starter•IDG•APU.Instruction labels on the oil system shall also be re-placed.EPAC selection modeIndividualOil 79ACJ79 OilACJOil 79 ACJIntentionally left blank79 Oil ACJ。