窑尾预热器与分解炉的功能及作用
水泥工艺中分解炉的结构及原理简介

(二)、分解炉的工作原理与结构概述分解炉是把生料粉分散悬浮在气流中,使燃料燃烧和碳酸钙分解过程在很短时间(一般1.5~3秒)内发生的装置,是一种高效率的直接燃烧式固相一气相热交换装置。
在分解炉内,由于燃料的燃烧是在激烈的紊流状态下与物料的吸热反应同时进行,燃料的细小颗粒呈一面浮游,一面燃烧,使整个炉内几乎都变成了燃烧区。
所以不能形成可见辉焰,而是处于820~900℃低温无焰燃烧的状态。
水泥烧成过程大致可分为两个阶段:石灰质原料约在900℃时进行分解反应(吸热);在1200~1450℃时进行水泥化合物生成反应(放热、部分熔融)。
根据理论计算,当物料由750℃升高到850℃,分解率由原来的25%提高到85~90%时。
每千克熟料尚须1670千焦的热量。
因此,全燃料的60%左右用于分解炉的燃烧,40%用在窑内燃烧。
近几年来窑外分解技术发展很快,虽然分解炉的结构型式和工作原理不尽相同,它们各有自己的特点,但是从入窑碳酸钙分解率来看,都不相上下,一般都达到85%以上。
由此看来,分解炉的结构型式对于入窑生料碳酸钙分解率的影响是不太大的。
关键在于燃料在生料浓度很高的分解炉内能稳定、完全燃烧,炉内温度分布均匀,并使碳酸钙分解在很短时间内完成。
我国某厂烧煤分解炉的结构示意图3—18。
分解炉由预燃室和炉体两部分组成,预燃室主要起预燃和散料作用,炉体主要起燃料燃烧和碳酸钙分解作用。
在钢板壳体内壁镶砌耐火砖。
由冷却机来的二次空气分成两路进入预燃室。
三级旋风筒下来的预热料,由二次空气从预燃室柱体的中上部带入预燃室。
约四分之一的分解炉用煤粉,从预燃室顶部由少量二次空气带入并着火燃烧,约四分之三左右的煤粉在分解炉锥体的上部位置喂入,以此来提高和调整分解炉的温度,使整个炉内温度分布趋于均匀,担任分解碳酸钙的主力作用。
炉体内的煤粉颗粒,虽被大量的惰性气体CO2和N2所包围,减少了与O2接触的机会,煤粉的燃烧速度就会减慢。
但由于进入预燃室的煤粉不受生料粉的影响,而且在纯空气中燃烧,形成引燃火焰,起到火种的作用,使预燃室出口处有明火存在,对煤粉起着强制着火作用。
第二节新型干法窑系统中预烧过程和设备

设置撒料装置是有利的。
Ⅰ
预热器
Ⅲ
回转窑 窑气
生料
Ⅱ Ⅳ
上长管道中的分散装置
下 料溜子
下料管管道分散装置源自闪动阀NC单板阀结构
锁风阀的作用及要求
主要作用是保持下料均匀畅通,又起密封作用,动作 必须灵活自如。要求:
⑴、阀体必须坚固、耐热,避免过热引起变形损坏; ⑵、阀板摆动轻巧灵活,重锤易于调整,既要避免阀
根据理论分析与计算还表明:
预热器废气温度随级数n的增加而降低,即回收 热效率有所提高。但它们之间不是线性关系,而是随 着n值增大、废气温度的降低趋势不断减小。也可以 说,级数愈多,平均每级所能回收的热量趋于减少。 反过来说物料预热升温曲线趋于平缓。
从理论上来讲,级数愈多,愈趋于可逆过程,能 量品位熵的损失愈小,愈合理。
影响旋风预热器预热效率的因素
因素之一:粉料在管道中的悬浮
保证悬浮效果的几项措施: (1)选择合理的喂料位置:
一般情况下,喂料点距出风管起始端应 有大于1m多的距离,此距离还与来料落差、 来料均匀程度、内筒插入深度以及管内气体 的流速有关。
(2)选择适当的管道风速
一般要求粉料悬浮区内的风 速在10—25m/s之间,通常要求大 于15m/s以上
C.气固分离
旋风预热器中气流所承载的粉体粒径很细,因此气 体流动状态对尘粒的运动起着决定性作用,对所能分离 的粉粒数量和大小有很大影响。
研究旋风预热器中气固分离问题,应着眼于气体流 动的流型、速度和压力分布等特征,给分析认识分离作 用提供依据。
其他因素如尘粒间的碰撞、凝聚、粘附和静电效应 均会对分离作用产生影响。
板开闭动作过大,又要防止物流发生脉冲,做到下料 均匀; ⑶、阀体具有良好的气密性,杜绝漏风; ⑷、支撑阀板的轴承要密封完好,防止灰尘掺入; ⑸、阀体各部件易于检修更换。
预热器及分解炉系统简介
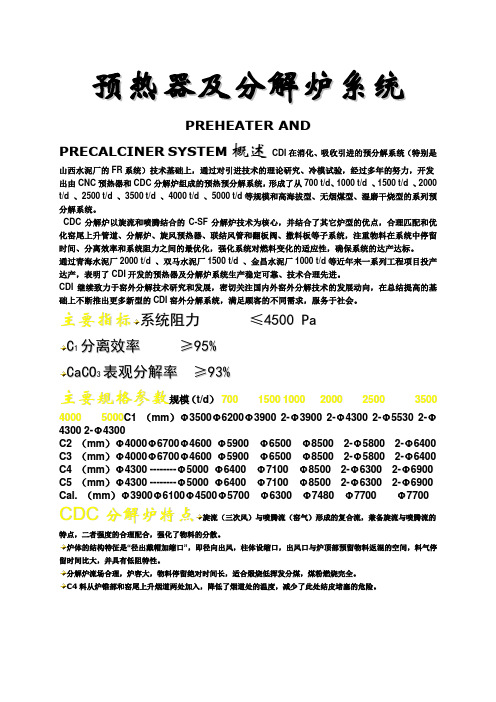
预热器及分解炉系统P R E H E A T E R A N DP R E C A L C I N E R S Y S T E M概述CDI在消化、吸收引进的预分解系统(特别是山西水泥厂的FR系统)技术基础上,通过对引进技术的理论研究、冷模试验,经过多年的努力,开发出由CNC预热器和CDC分解炉组成的预热预分解系统,形成了从700 t/d、1000 t/d 、1500 t/d 、2000 t/d 、2500 t/d 、3500 t/d 、4000 t/d 、5000 t/d等规模和高海拔型、无烟煤型、湿磨干烧型的系列预分解系统。
CDC分解炉以旋流和喷腾结合的C-SF分解炉技术为核心,并结合了其它炉型的优点,合理匹配和优化窑尾上升管道、分解炉、旋风预热器、联结风管和翻板阀、撒料板等子系统,注重物料在系统中停留时间、分离效率和系统阻力之间的最优化,强化系统对燃料变化的适应性,确保系统的达产达标。
通过青海水泥厂2000 t/d 、双马水泥厂1500 t/d 、金昌水泥厂1000 t/d等近年来一系列工程项目投产达产,表明了CDI开发的预热器及分解炉系统生产稳定可靠、技术合理先进。
CDI继续致力于窑外分解技术研究和发展,密切关注国内外窑外分解技术的发展动向,在总结提高的基础上不断推出更多新型的CDI窑外分解系统,满足顾客的不同需求,服务于社会。
主要指标系统阻力≤4500P aC1分离效率≥95%C a C O3表观分解率≥93%主要规格参数规模(t/d)70015001000200025003500 40005000C1(m m)Φ3500Φ6200Φ39002-Φ39002-Φ43002-Φ55302-Φ43002-Φ4300C2(m m)Φ4000Φ6700Φ4600Φ5900Φ6500Φ85002-Φ58002-Φ6400 C3(m m)Φ4000Φ6700Φ4600Φ5900Φ6500Φ85002-Φ58002-Φ6400 C4(m m)Φ4300--------Φ5000Φ6400Φ7100Φ85002-Φ63002-Φ6900 C5(m m)Φ4300--------Φ5000Φ6400Φ7100Φ85002-Φ63002-Φ6900 C a l.(m m)Φ3900Φ6100Φ4500Φ5700Φ6300Φ7480Φ7700Φ7700 C D C分解炉特点旋流(三次风)与喷腾流(窑气)形成的复合流,兼备旋流与喷腾流的特点,二者强度的合理配合,强化了物料的分散。
窑尾预热器与分解炉的功能及作用
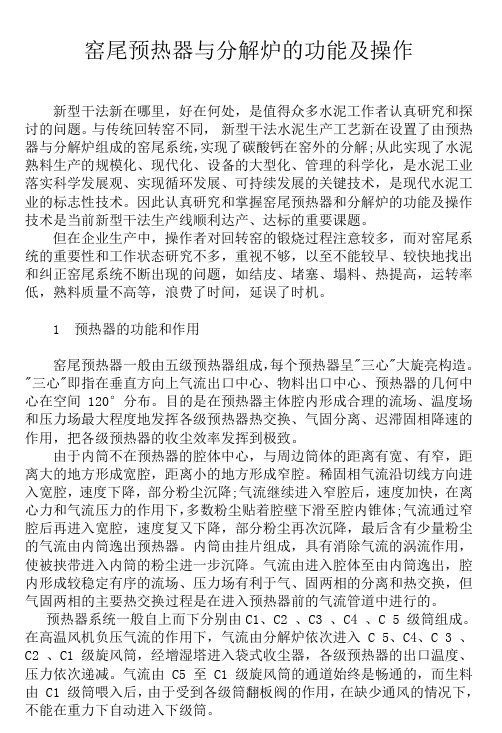
如C1、C2、C3、C4,C5级筒的收尘效率下降,将使本级筒内已进行充分热交换的生料又返回上级筒与低温稀固相气流混合,造成热量的损失和浪费。所以各级预热器的收尘效率是影响窑尾系统正常、高效运行的重要参数。从理论上讲各级预热器的收尘效率应当是越高越好,但追求过高的收尘效率将使系统阻力增加,导致过多的压力损失,窑尾风机功率的增加,同样是一种能量的损失。设计中已对预热器系统的阻力和风机功率进行了恰当配置保持收尘效率设计参数的稳定是十分必要和重要的。在正常生产中,影响各级预热器收尘效率的因素主要是内筒的长短,挂片的完好程度以及翻板阀的工作状态等,此外风量的变化,给料量的变化也都对收尘效率有或多或少的影响,因此提高操作水平,保持各级预热器较高的收尘效率是水泥企业生产管理上的一个重要课题。在预热器设计参数确定之后,内筒尺寸长短的变化将决定预热器的收尘效率。一般说,内筒长度不变,收尘效率不变,由于磨损、烧失,长度变短,收尘效率将随之呈线性下降,挂片磨损、烧失,部分进口气流易从出口短路,收尘效率则有较大的下降。
由于内筒不在预热器的腔体中心,与周边筒体的距离有宽、有窄,距离大的地方形成宽腔,距离小的地方形成窄腔。稀固相气流沿切线方向进入宽腔,速度下降,部分粉尘沉降;气流继续进入窄腔后,速度加快,在离心力和气流压力的作用下,多数粉尘贴着腔壁下滑至腔内锥体;气流通过窄腔后再进入宽腔,速度复又下降,部分粉尘再次沉降,最后含有少量粉尘的气流由内筒逸出预热器。内筒由挂片组成,具有消除气流的涡流作用,使被挟带进入内筒的粉尘进一步沉降。气流由进入腔体至由内筒逸出,腔内形成较稳定有序的流场、压力场有利于气、固两相的分离和热交换,但气固两相的主要热交换过程是在进入预热器前的气流管道中进行的。
窑外分解窑分解
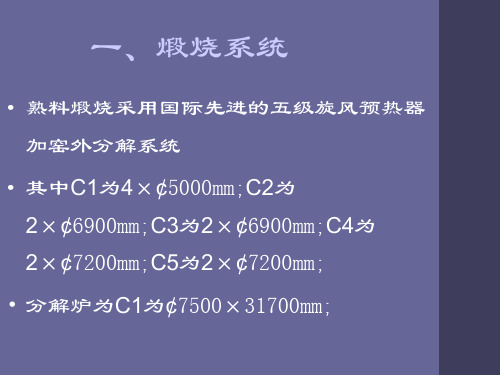
结皮
• 结皮定义 • 结皮危害 • 结皮的形成
结皮:
是指物料在预分解窑的预热器、分解 炉等管道内壁上,逐步分层黏挂,形成 疏松口上,下部,以及悬浮 预热器的锥体部位。
结皮的危害
• 预热器旋风筒和分解炉内结皮增厚 时,不但会使通风道的有效截面减小, 阻力增大,影响系统通风,结皮严重或 塌落时,重者发生堵塞事故,轻者易引 起系统压力不稳,影响正常生产;主排 风机叶片结皮,会使风机发生震动,影 响风机的安全运转。
燃料煤的机械不完全燃烧的影响
煤的机械不完全燃烧为预分解窑系统内结皮范围的 扩大提供了条件,造成煤的不完全燃烧主要原因是 煤粉太粗、燃烧速度太慢,空气量不足及操作不当 等,在该燃烧区域内燃料燃烧不完全,而在其它区 域继续燃烧,从而使系统内煤燃烧区域发生变化, 导致了系统内温度布局的不均。随着稳定区域的变 化,结皮部位也随之改变,特别是预热器系统里的 旋风筒收缩部位,由于物料在硫、氯、碱的作用下 表面熔化,其黏性增加,在于筒壁接触时形成结皮。 所以在预分解窑生产时,煤流的稳定、煤质的稳定 是非常关键的,它是关系到系统稳定的首要前提。
2、NC型预热器的特点:
◆低风速、大直径、短柱体、四心大蜗壳、优化的偏心距构成了旋 风筒低阻力的基本要素。 ◆各级旋风筒均设有降阻作用的“导流板”和特殊进风口,且均 设内筒提高分离效率,有效减少物料在各级旋风筒之间不必要 的循环,分片式内筒(通常三、四、五级)具有较长的使用寿 命,安装更换更加方便;顶级内筒内部设有“整流器”,明显 降低了系统阻力。 ◆在旋风筒锥体下部采用了歪斜锥体,有效地解决了堵料问题; ◆所有下料管均装有密封性能好,动作灵活的翻板阀,既克服了 内串风又保证了物料的均匀连续性,对提高分离效率起了重要 作用。外置滚动轴承支承,转动灵活、可靠性高; ◆具有独特结构的固定式弧形撒料板,加强了物料在气流中的分 散性,提高了气固换热效率; ◆NST-I型分解炉具有喷旋结合、混合充分、流场和料场均匀的特 点,经鹅型管后,加强了分解炉内的后期混合,具有强大的产 量突破能力和对不同原燃料的适应能力; ◆在易堵部位设置了捅料孔或空气炮,有效防止了系统堵塞事故 的发生。 ◆系统中各联接法兰安装后均采用焊接密封,大大减少了系统外 漏风;
预分解窑操作要求的特点
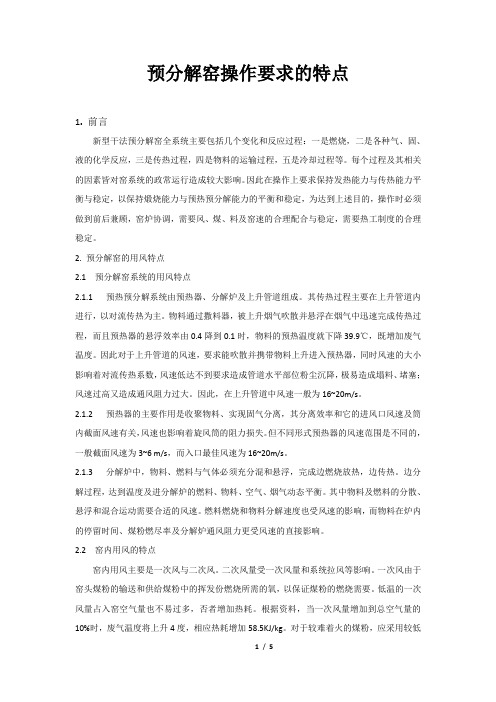
预分解窑操作要求的特点1. 前言新型干法预分解窑全系统主要包括几个变化和反应过程:一是燃烧,二是各种气、固、液的化学反应,三是传热过程,四是物料的运输过程,五是冷却过程等。
每个过程及其相关的因素皆对窑系统的政常运行造成较大影响。
因此在操作上要求保持发热能力与传热能力平衡与稳定,以保持煅烧能力与预热预分解能力的平衡和稳定,为达到上述目的,操作时必须做到前后兼顾,窑炉协调,需要风、煤、料及窑速的合理配合与稳定,需要热工制度的合理稳定。
2. 预分解窑的用风特点2.1 预分解窑系统的用风特点2.1.1 预热预分解系统由预热器、分解炉及上升管道组成。
其传热过程主要在上升管道内进行,以对流传热为主。
物料通过撒料器,被上升烟气吹散并悬浮在烟气中迅速完成传热过程,而且预热器的悬浮效率由0.4降到0.1时,物料的预热温度就下降39.9℃,既增加废气温度。
因此对于上升管道的风速,要求能吹散并携带物料上升进入预热器,同时风速的大小影响着对流传热系数,风速低达不到要求造成管道水平部位粉尘沉降,极易造成塌料、堵塞;风速过高又造成通风阻力过大。
因此,在上升管道中风速一般为16~20m/s。
2.1.2 预热器的主要作用是收聚物料、实现固气分离,其分离效率和它的进风口风速及筒内截面风速有关,风速也影响着旋风筒的阻力损失。
但不同形式预热器的风速范围是不同的,一般截面风速为3~6 m/s,而入口最佳风速为16~20m/s。
2.1.3 分解炉中,物料、燃料与气体必须充分混和悬浮,完成边燃烧放热,边传热。
边分解过程,达到温度及进分解炉的燃料、物料、空气、烟气动态平衡。
其中物料及燃料的分散、悬浮和混合运动需要合适的风速。
燃料燃烧和物料分解速度也受风速的影响,而物料在炉内的停留时间、煤粉燃尽率及分解炉通风阻力更受风速的直接影响。
2.2 窑内用风的特点窑内用风主要是一次风与二次风。
二次风量受一次风量和系统拉风等影响。
一次风由于窑头煤粉的输送和供给煤粉中的挥发份燃烧所需的氧,以保证煤粉的燃烧需要。
第三代TTF窑尾预热器系统简介

中天仕名科技集团有限公司 CEMTECK Group Ltd.
加强管道系统换热效果的措施 : a. 适当提高管道风速(15~18m/s)
(经计算当管道内风速由15.5 m/s增至18
m/s时,其换热效果增强12.7%) b. 适当加宽撒料板的撒料宽度,增加物 料在管道中的分散度从而提高换热效果; c. 撒料板伸入风管中长度略加长,增强 物料的分散效果; d. 合理布置下料点的高度,在保证物料 不短路的前提下,尽量缩短下料点与旋 风筒顶盖的距离,增加管道换热的有效 长度,延长气固换热时间,从而提高换 热效果。 e. 合理布置物料下料点,充分考虑旋风 筒中气流旋向对物料换热的影响。
C4料
C4料
三次风
煤粉 煤粉
窑气
中天仕名科技集团有限公司 CEMTECK Group Ltd.
对于烟煤采用常规两钵TDF分解炉,当燃料为较难燃烧的无烟 煤或劣质煤时,采用三钵TTF型式的分解炉,综上所述,本项目分解 炉的工艺特点如下: ●三喷腾:TTF炉固气停留时间比大,在相同炉容下,炉流场大大优化,气
中天仕名科技集团有限公司 CEMTECK Group Ltd.
C、锁风阀、点火烟囱等
结构简单、维护方便、锁风效 果良好的锁风阀 密封效果良好、可远程精 确控制的点火烟囱
中天仕名科技集团有限公司 CEMTECK Group Ltd. 代别 第一代 第二代 第三代
分解炉: 容积较小,对煤 质要求较严,主 要型式类似RSP 、NSF。 预热器: 700t/d~1000t/d 采用靴形扁内筒 和阻流型导流板 ,2000t/d采用直 形圆内筒和矩形 进风口的常规结 构。 分解炉: 早期采用对撞进风双喷腾 TDF型分解炉,后期根据 煤质情况,在主炉TDF炉 基础上分别采取下置旋流 预燃室、旁置旋流预燃室 、前置流态化预燃炉和后 置延伸管道等结构型式。 预热器: 早期采用直形圆内筒和二 心蜗壳结构,单体阻力高 和分离效率高。后期采用 直形圆大内筒,270°大 蜗壳、斜切角进气口, d/D适当放大,蜗壳为等 高变角度,优化内筒结构 ,采用耐热钢制的悬挂分 片式圆内筒。 分解炉: 采用双喷腾或三喷腾 TDF型分解炉适应各种 煤质,操作维护简单。 分解炉考虑燃料分级及 三次风分级,降低系统 NOx排放。 预热器: 采用直形圆内筒,270° 二心大蜗壳、斜切角进 气口,内筒和连接风管 风速优化考虑,优化内 筒结构,采用耐热钢制 的悬挂分片式圆内筒。
窑外分解窑分解炉种类和结构
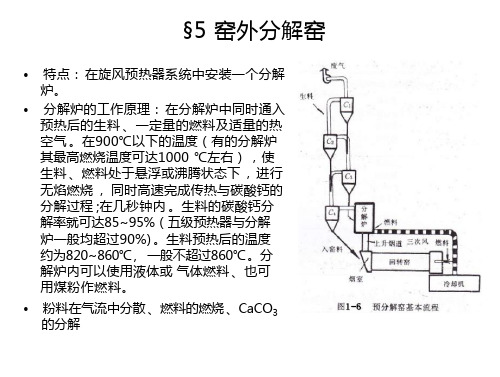
• (7)Pyroclon型与Prepol型分解炉 • PyrocIon系Pyro(高温)与Cyclon (旋风筒)两字缩写的组合 。系德国洪堡公司所开发。
Prepol系Precalcining (预分解)与Polysu is(公司)两字缩写的组合,为德国伯力鸠斯 司所开发。
• 这两种分解炉基本上大同小异,其共同的特点是 :
• ① 不设专门的分解炉,利用窑尾与最低一级旋风筒之间的上升烟道,适当延长加高而 作为分解炉用 。因此结构简单, 阻力小。
• ② 燃料与经预热后生料均自上升烟道下部喂入,力求在气流中充分分散, 因此最好沿 管道面能形成旋涡流动。
• ① 分解 底部设有一截面不大的多孔板,用3~5kPa高压风机鼓入流化风(占 总风量8 10%), 建立生料与燃料的密相流化床区 ; 煤粉喷咀设在流化床上 部,C4来的生料自流化床侧面加入,混合非常均匀,燃烧 、换热 、分解反应 开始进行,物料在床内停留时间达2min之久。
• ② 三次风在分解炉下锥底部分,送入到流化料层上部,切向进入,形成一定的 旋转流,携带流化生料形成了涡流床区 。充足的空气,使反应激烈进行。
• (4)RSP分解炉
• RSP分解炉(见图1- 10)是日本小野田公司开发 , 其主要特点是: • ① 分解炉由三部分组成 : 即
• 旋流燃烧室(SB) ——三次风呈旋流运动进入,主要是使燃料分散和部分 燃烧 ;
• 旋流分解室(SC) ,三次风吹送来的热生料和煤粉在此室也呈旋流运动 , 使煤粉进一步燃烧 、生料受热和部分分解 ;
第六章 窑外分解炉详解
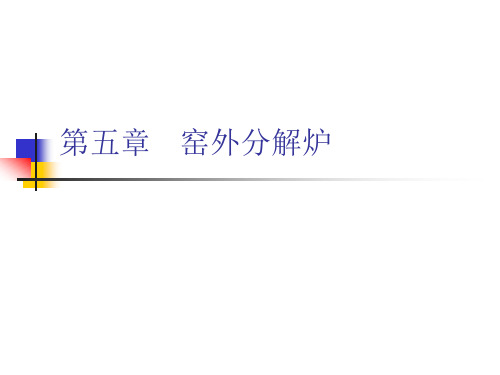
2、按分解炉内气流的主要运动形式分类
旋流式、喷腾式、悬浮式及沸腾式、旋 流喷腾式。 依靠“旋风效应”、“喷腾效应”、 “悬浮效应”,“流态化效应”。
第二节,分解炉中的各种效应
一、旋风效应 旋风效应是旋风型分解炉内气流作旋回运动,使物 料滞后于气流的效应。 悬浮于气流的物料,由于旋转运动,受离心力的作 用,颗粒和质量较大的物料及气流容易达到炉边, 与炉壁碰撞失速、坠落,至缩口再被气流带起,形 成向前推动的作用,前面的气流将粉料留下,而后 面的气流又继续推向前进,总的运动趋向是还是顺 着气流,但料粉的运动速度却远远地落后气流速度, 造成物料在炉内的滞留现象,料粉愈细,滞留愈短, 料粉愈粗,滞留愈长。
1、熟料形成的工艺特点 2、回转窑对工艺要求的适应性 3、回转窑热工布局 4、窑外分解技术的产生
第二节 分解炉的结构和工艺流程
一、分解炉的结构
二、预分解窑的工艺流程
三、石川岛公司
MFC型日本三菱公司
RSP型日本小野田 KSV型日本川琦公司 FLS型丹麦史密斯 DD型日本神户制铁公司
(4)、全燃烧区(Ⅳ区)炉顶部圆筒体,主 要作用是使未燃烧的10%左右的燃料继续燃烧 并促进分解。 气体和生料通过Ⅲ区和Ⅳ区间缩口向上喷腾直 接冲击到炉顶棚,翻转向下到出口,使气料搅 拌和混合,达到完全燃烧和热交换。 DD分解炉设置气料反弹室,有利于气料产生搅 拌和混合,增加了气料在炉内的停留时间,达 到完全燃烧和改善热交换,防止炉内的偏流现 象。炉下对称的三次风管以及顶部两根出风管, 都是向炉心径向安装,有利于产生良好的喷腾 运动和降低炉内压力。 此外4个主喷嘴,从三次风管上部两侧直接喷 入三次氧气流中,点火条件好,适合劣质煤。
6.5悬浮预热器与分解窑-陈德玉 (2)
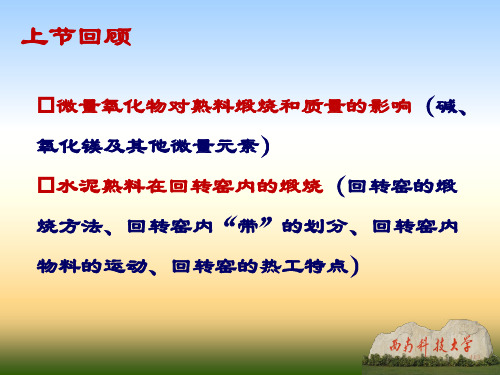
熟料冷却机
熟料冷却机是一种将高温熟料向低温气体传热的热交 换装置。 从“工艺”和“热工”两个方面对冷却机有如下 要求: ①尽可能多地回收熟料的热量,以提高入窑 二次空气的温度。降低熟料的热耗。 ②缩短熟料的冷却时间,以提高熟料质量,改善易 磨性。 ③冷却单位质量熟料的空气消耗量要少,以便提高 二次空气温度,减少粉尘飞扬、降低电耗。 ④结构简单、操作方便、维修容易、运转率高。
半离线型
分解炉设于窑的一侧,称半离线型炉。这种布置方式中, 分解炉内燃料在纯三次风中燃烧,炉气出炉后可以在窑尾 上升烟道下部与窑气会合(如RSP、MFC等),亦可在上升烟 道上部与窑气会合(如N-MFC、SLC—S等),然后进入最下 级旋风筒。这种方式工艺布置比较复杂,厂房较大,生产 管理及操作亦较为复杂。其优点在于燃料燃烧环境较好, 在采用“两步到位”模式时,有利于利用窑气热量和防止 粘结堵塞。
目前国内外水泥工业所使用回转窑系统的 熟料冷却机大至可分如下几种:
具体介绍见书P62-64
一、单筒冷却机
二、多筒冷却机
三、篦式冷却机
back
作业
1 简述水泥生料在回转窑中物理化学变化。 2 熟料为什么要急冷?
3 什么是最低共熔温度?它与哪些因素有关?
4 1450℃煅烧熟料时,液相量是如何计算的? (写出计算公式即可) 5 回转窑内煅烧特点有哪些?湿法窑中物料运 动速率最快的是哪个部位?
(2)烧成带(又称烧结带、高温带,俗称底火)
位置 烧成带的位置位于喇叭口附近,料层约为0.5-0.8m厚, 温度1300℃-450℃-1300℃。立窑烧成带位置和厚度 会因料、煤、风与操作的变化而变动。一般为仅占窑 高10%-15%,中心部位厚度为1.0m左右为宜。略呈 锅底状。 生料球在烧成带收缩情况 机立窑的料球收缩率为24%-32 %。料球收缩率的大小与成球水分、原料性质、料球孔隙 率、窑的尺寸形状以煅烧时料球液相量等因素有关。为适 应烧成带料球体积收缩的这一实际情况,故立窑基本上都 采取上口扩大(俗称喇叭口)形式。
五大热工设备介绍解析
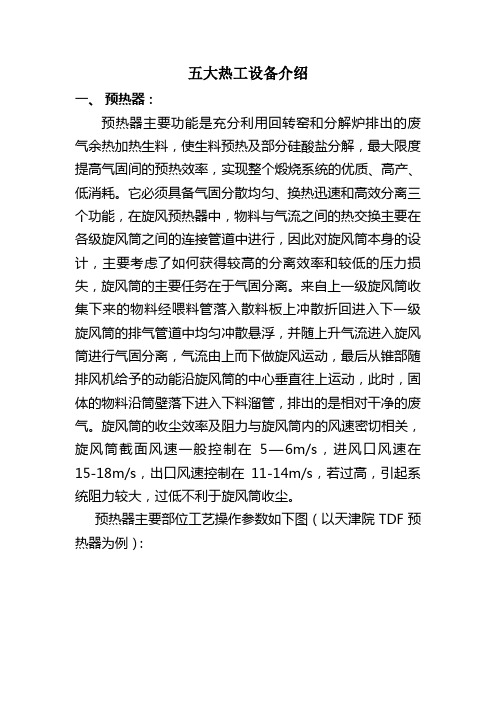
五大热工设备介绍一、预热器:预热器主要功能是充分利用回转窑和分解炉排出的废气余热加热生料,使生料预热及部分硅酸盐分解,最大限度提高气固间的预热效率,实现整个煅烧系统的优质、高产、低消耗。
它必须具备气固分散均匀、换热迅速和高效分离三个功能,在旋风预热器中,物料与气流之间的热交换主要在各级旋风筒之间的连接管道中进行,因此对旋风筒本身的设计,主要考虑了如何获得较高的分离效率和较低的压力损失,旋风筒的主要任务在于气固分离。
来自上一级旋风筒收集下来的物料经喂料管落入散料板上冲散折回进入下一级旋风筒的排气管道中均匀冲散悬浮,并随上升气流进入旋风筒进行气固分离,气流由上而下做旋风运动,最后从锥部随排风机给予的动能沿旋风筒的中心垂直往上运动,此时,固体的物料沿筒壁落下进入下料溜管,排出的是相对干净的废气。
旋风筒的收尘效率及阻力与旋风筒内的风速密切相关,旋风筒截面风速一般控制在5—6m/s,进风口风速在15-18m/s,出口风速控制在11-14m/s,若过高,引起系统阻力较大,过低不利于旋风筒收尘。
预热器主要部位工艺操作参数如下图(以天津院TDF预热器为例):预热器工作原理如下图:二、分解炉:分解炉是在预热器和回转窑之间增设的一个装置,燃煤喂入分解炉燃烧放出的热量与进入炉内的生料碳酸盐的分解和吸热过程同时在浮状态下进行,使得入窑碳酸盐分解率提高到90%以上。
原来在窑内进行的分解反应移至分解炉内来,燃料大部分从分解炉内加入,减轻了窑内热负荷,延长了衬料的寿命有利于生产大型化,由于燃料与生料粉混合均匀,燃料燃烧热及时传递给物料,使燃烧、换热及碳酸盐分解过程都得到优化,因而具有优质、高效、低耗等一系列优良性能特点,它主要作用是燃料的燃烧、换热和碳酸盐的分解。
在分解炉内,生料及燃料分别依靠“涡旋效应”、“喷腾效应”、“悬浮效应”和“流化态效应”分散于气流之中。
由于物料之间在炉内流场中产生相对运动,从而达到高度分散、均匀混合和分布、迅速换热、延长物料在炉内的滞留时间,达到提高燃烧效率、换热效率和入窑物料碳酸盐分解率的目的。
分解炉的分类

分解炉的分类按分解炉与窑的连接方式大致分为三种类型1.同线型分解炉这种类型的分解炉直接坐落在窑尾烟室之上。
这种炉型实际是上升烟道的改良和扩展。
它具有布置简单的优点,窑气经窑尾烟室直接进入分解炉,由于炉内气流量大,氧气含量低,要求分解发炉具有较大的炉容或较大的气、固滞留时间长。
这种炉型布置简单、整齐、紧凑,出炉气体直接进入最下级旋风筒,因此它们可布置在同一平台,有利于降低建筑物高度。
同时,采用“鹅颈”管结构增大炉区容,亦有利于布置,不增加建筑物高度。
2.离线型分解炉这种类型的分解炉自成体系。
采用这种方式时,窑尾设有两列预热器,一列通过窑气,一列通过炉气,窑列物料流至窑列最下级旋风筒后再进入分解炉,同炉列物料一起在炉内加热分解后,经炉列最下级旋风筒分离后进入窑内。
同时,离线型窑一般设有两台主排风机,一台专门抽吸窑气,一台抽吸炉气,生产中两列工况可以单独调节。
在特大型窑,则设置三列预热器,两个分解炉。
3.半离线型分解炉这种类型的分解炉设于窑的一侧。
这种布置方式中,分解炉内燃料在纯三次风中燃烧,炉气出炉后可以在窑尾上升烟道下部与窑气会合(如RSP、MFC等),亦可在上升烟道上部与窑气会合(如N-MFC. SLC-S等),然后进入最下级旋风筒。
这种方式工艺布置比较复杂,厂房较大,生产管理及操作亦较为复杂。
其优点在于燃料燃烧环境较好,在采用“两步到位”模式时,有利于利用窑气热焰和防止粘结堵塞。
中国新研制的新型分解炉亦有采用这种模式的。
分解炉内的气流运动,有四种基本型式:即涡旋式、喷腾式、悬浮式及流化床式。
在这四种型式的分解炉内,生料及燃料分别依靠“涡旋效应”、“喷腾效应”、“悬浮效应”和“流态化效应”分散于气流之中。
由于物料之间在炉内流场中产生相对运动,从而达到高度分散、均匀混合和分布、迅速换热、延长物料在炉内的滞留时间,达到提高燃烧效率、换热效率和入窑物料碳酸盐分解率的目的。
分解炉作为预分解窑的“第二热源”,承担着繁重的燃料燃烧和换热任务。
预热器回转窑篦冷机系统工作原理一次讲清
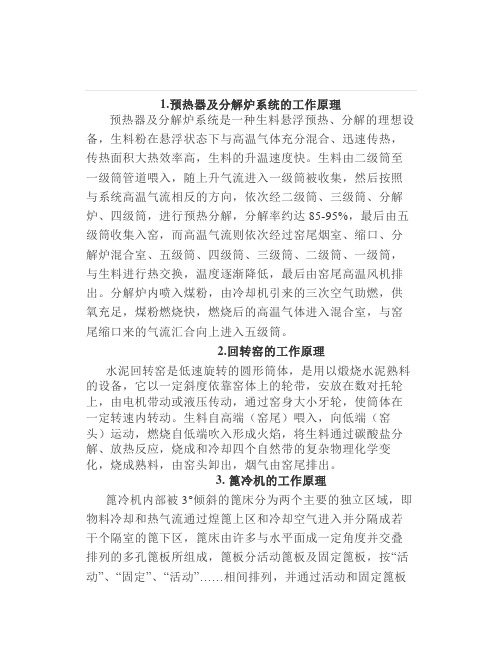
1.预热器及分解炉系统的工作原理预热器及分解炉系统是一种生料悬浮预热、分解的理想设备,生料粉在悬浮状态下与高温气体充分混合、迅速传热,传热面积大热效率高,生料的升温速度快。
生料由二级筒至一级筒管道喂入,随上升气流进入一级筒被收集,然后按照与系统高温气流相反的方向,依次经二级筒、三级筒、分解炉、四级筒,进行预热分解,分解率约达85-95%,最后由五级筒收集入窑,而高温气流则依次经过窑尾烟室、缩口、分解炉混合室、五级筒、四级筒、三级筒、二级筒、一级筒,与生料进行热交换,温度逐渐降低,最后由窑尾高温风机排出。
分解炉内喷入煤粉,由冷却机引来的三次空气助燃,供氧充足,煤粉燃烧快,燃烧后的高温气体进入混合室,与窑尾缩口来的气流汇合向上进入五级筒。
2.回转窑的工作原理水泥回转窑是低速旋转的圆形筒体,是用以煅烧水泥熟料的设备,它以一定斜度依靠窑体上的轮带,安放在数对托轮上,由电机带动或液压传动,通过窑身大小牙轮,使筒体在一定转速内转动。
生料自高端(窑尾)喂入,向低端(窑头)运动,燃烧自低端吹入形成火焰,将生料通过碳酸盐分解、放热反应,烧成和冷却四个自然带的复杂物理化学变化,烧成熟料,由窑头卸出,烟气由窑尾排出。
3. 篦冷机的工作原理篦冷机内部被3°倾斜的篦床分为两个主要的独立区域,即物料冷却和热气流通过煌篦上区和冷却空气进入并分隔成若干个隔室的篦下区,篦床由许多与水平面成一定角度并交叠排列的多孔篦板所组成,篦板分活动篦板及固定篦板,按“活动”、“固定”、“活动”……相间排列,并通过活动和固定篦板支承固定在活动框架和侧框架上,活动框架通过与其相连的滑块轴、由曲柄连杆机构传动,使其沿托轮导轨作往复直线运动,从而带动活动篦板往复移动,推动物料前进。
活动框架由二段组成,每段都有独自的传动装置,篦下各室由风机吹入冷风,冷却空气透过热料层进行充分热交换将物料有效冷却,熟料从卸料端经锤式破碎机破碎,达到要求粒度的熟料通过栅筛篦条卸到熟料输送机上运走,大块熟料抛回篦床再冷却、破碎。
五大热工设备的工作原理及之间的关系

五、燃烧器
Components of the main burner system
Kiln窑 Blower风机 burner carriage燃 烧器小车
燃烧器小车轨道 电缆
一次风管 air duct for primary air
trailing cable for burner carriage
在窑尾烟室将形成还原气氛,通过窑尾燃烧器的喂煤可以达 到该目的。由于窑尾烟室燃烧器的启动,分解炉下部的O2 含量将减少到约0%,同时CO气体的含量也将相应的增加必 须调整窑尾烟室燃烧器的燃料量,该燃料量将按以下公式进 行自动的调整:
PC fuel + K1 fuel = 固定值
PC fuel: 分解炉喂煤量
热负荷,延长了衬料的寿命有利于生产大型化,由于燃料与 生料粉混合均匀,燃料燃烧热及时传递给物料,使燃烧、换 热及碳酸盐分解过程都得到优化,因而具有优质、高效、低 耗等一系列优良性能特点,它主要作用是燃料的燃烧、换热 和碳酸盐的分解。
(3)AS-MSC分解炉工作原理
为了降低废气中NOx气体的含量,AS-MSC分解炉可以 实现风、煤、料的多点喂入,通过直接控制分解炉内的燃料 燃烧工艺达到此目的。通过保持预先设定的三次风的稳定来 保持窑内的氧化气氛,设想三次风的风量量与氧气的含量成 正比。当窑系统的操作稳定以后,就可以启动窑尾烟室燃烧 器,以少废气中NOx气体的含量。为了减少烧成带NOx的含 量,在窑尾烟室将形成还原气氛,通过窑尾燃烧器的启动, 少废气中NOx气体的含量。为了减少烧成带NOx的含量,
窑口AS-A浇注料
0.6~6.6m
AG-85耐火砖
6.6~30m
PX-83耐火砖
30~45m
AG-85耐火砖
- 1、下载文档前请自行甄别文档内容的完整性,平台不提供额外的编辑、内容补充、找答案等附加服务。
- 2、"仅部分预览"的文档,不可在线预览部分如存在完整性等问题,可反馈申请退款(可完整预览的文档不适用该条件!)。
- 3、如文档侵犯您的权益,请联系客服反馈,我们会尽快为您处理(人工客服工作时间:9:00-18:30)。
要实现上述目的,分解炉内稀固相气流应有一个相对稳定的流场、浓度场、温度场和压力场。分解炉从诞生到今天经历了多次研制和改进,派生和衍生的型式多种多样,林林总总,归纳起来共有五大类37种。依气流的运动形式大致可分为旋-喷式、预燃室-喷腾式、流化床-喷腾式和悬浮管道式等。各型式分解炉依靠"旋风效应"、"喷腾效应"、"悬浮效应"和"流态效应",使稀同相气流在炉内达到高度分散,增加物料与热气流间的接触面积,延长物料在分解炉内的滞留时间,达到提高燃烧效率,提高热交换率及提高入窑生料分解率的目的。日常使用的分解炉多具有两种以上的气流运动形式。但从宏观上看,各种分解炉的技术原理基本相同,并且随着分解技术的日趋成熟和技术上的相互渗透,各种预分解窑在工艺装置和分解炉的结构形式上又大同小异。
翻板阀动作失灵或常开是造成预热器收尘效率下降或塌料的另一个主要原因。如C3级筒的下料管与C5级筒上升气流管道相连,其中C3级筒下料管的翻板阀起到管道密封和控制物料流动的作用。一旦该翻板阀动作失灵或常开,C5级筒的上升气流短路走捷径,部分气流将携带粉尘通过翻板阀进入C3级筒,这一结果使C4级筒的压力、温度下降,形成C4级筒收尘效率的实质性下降,C3级筒压力、温度增高,粉尘浓度增加,易造成“塌料”。上述现象可以从中控室各列各级预热器出口的温度、压力值的不平衡和明显变化做出判断。
评判一个分解炉是否先进,大体有两个必要条件:第一是碳酸钙的分解率及单位热耗的大小。新型干法标准煤耗可以降至l00kg/t熟料而实现碳酸钙的窑外分解,分解炉发挥了关键作用。湿法窑吨熟料标准煤耗为200kg,中空窑为160kg,立波尔窑140kg,新型干法可以降到100kg以下。新型干法窑前标准煤耗大体为40kg,窑尾标准煤耗60kg。如果认为各种回转窑熟料锻烧标准煤起大致相同的话,新型干法相对各种回转窑的标准煤耗的减少量均应为预热和分解过程中节省的标准煤数量。即可以认为,通过分解炉节省的煤量,与上述各种落后工艺相比,较湿法窑吨熟料节省标准煤起高达100kg,较中空窑节省60kg,较立波尔窑节省40kg。因此预热器和分解炉的设置和应用对节能降艳、降低生产成本、提高经济效益发挥了决定性的作用。
第二是煤粉的燃烬度和对煤种的适应性。燃烬度高可使燃煤热值实现最大释放,燃烬度低会造成燃煤的浪费;还会造成"煤粉后燃"。"煤粉后燃"是窑尾系统的严重问题,是燃煤在应燃烧的地方没有燃烧,在而后不该燃烧的地方无谓地燃烧,在工艺上帮"倒忙",造成热量的损失和成本的增加。"煤粉后燃"是指进入分解炉的煤粉由于煤质易燃性差、煤粉细度不够、氧气量不足等原因,没能在分解炉内充分燃烧,而进入C5、C4、C3级预热器并继续燃烧的现象。"煤粉后燃"使各级预热器的温度场发生变化,不正常升高,液相过早、过多出现,造成C5级筒下料管结皮、堵塞,造成预热器内筒烧失,回收率下降等。
气、固两相的分离效果取决预热器的收尘效率,一般C1级筒收尘效率为90%-95%,C2、C3、C4级筒为86%-88%,C5级筒的收尘效率应在88%以上,其中C1级筒的收尘效率最为关键,它控制实际进入预热器粉状物料的多少。500Ot/d生产线窑尾C1级筒每小时的喂料大致为330t/h,如C1级筒收尘效率为95%,则每小时实际进入窑尾的物料为314t/h,另外有16t/h料伴随气流进入窑尾袋收尘器。如果C1级筒的收尘效率降为90%,则每小时实际喂入窑尾的生料仅有297t/h,而随气流进入窑尾袋收尘器的物料则多达33t。这部分物料再经袋收尘器下设的绞刀、斜槽、提升机返回生料仓,再由窑尾提升机重新喂入C1级筒,这一过程的能耗损失、设备的磨损都是无谓的浪费。
预热器系统一般自上而下分别由C1、C2、C3、C4、C5级筒组成。在高温风机负压气流的作用下,气流由分解炉依次进入C5、C4、C 3、C2、C1级旋风筒,经增湿塔进入袋式收尘器,各级预热器的出口温度、压力依次递减。气流由C5至C1级旋风筒的通道始终是畅通的,而生料由C1级筒喂入后,由于受到各级筒翻板阀的作用,在缺少通风的情况下,不能在重力下自动进入下级筒。
如河南境内热值在5600∽5800kcl/t)的高热值煤产量不多,价格更高,而中低热值煤数量充足,却不能使用。为此,省内新建新型干法生产线85%以上的企业都要舍近求远,花高价到山西、陕西去采购,去运输。如受道路、天气的影响,企业用煤将受到严重影响和制约且吨熟料成本将提高10-15元而影响产品的市场竞争能力和企业的经济效益。
窑尾预热器与分解炉的功能及操作
新型干法新在哪里,好在何处,是值得众多水泥工作者认真研究和探讨的问题。与传统回转窑不同,新型干法水泥生产工艺新在设置了由预热器与分解炉组成的窑尾系统,实现了碳酸钙在窑外的分解;从此实现了水泥熟料生产的规模化、现代化、设备的大型化、管理的科学化,是水泥工业落实科学发展观、实现循环发展、可持续发展的关键技术,是现代水泥工业的标志性技术。因此认真研究和掌握窑尾预热器和分解炉的功能及操作技术是当前新型干法生产线顺利达产、达标的重要课题。
对煤粉、煤种的适应性是目前对各种型式分解炉的最大考验和挑战。从全国来看,优质煤较少,而中、低质煤较多。随着新型干法的普及、发展及各地的不同情况,新型干法必须面对优质煤不足和中、低质煤大量存在的事实所选用的分解炉对煤种的变化应具有广泛的适应性,不仅可以烧优质煤,更可以燃烧中、低质煤。否则一条新型干法生产线只能烧23 400kJ/kg (56OOkcl/t)以上的优质煤,离开优质煤就"玩不转"将使企业于困境、被动和成本上升,效益下降,以至停产。
此外,双列对应预热器的温度、压力呈现规律性数值差时,则应考虑是由两列C1级筒给料量的不均衡造成的,应调整给料量。
2分解炉的功能和作用
分解炉的作用主要有三个:一是使燃料在炉内具有充分的燃烧时间,理论燃烬度应达到100%,以使燃料的热量得到最大释放。二是通过激烈的旋流、喷腾,使物料的分散度达到最大,促使其在分散悬浮状态中与热气体进行充分的热交换三是促使碳酸钙的快速分解,分解率应达到90%以上。
C1级筒出口物料经翻板阀被C3级筒出口气流吸送至C2级筒,C2级筒出口物料经翻板阀被C4级筒出口气流吸送至C3级筒,C3级筒出口的物料经翻板阀被C5级筒出口的气流吸送至C4级筒,C4级筒出口物料经翻板阀在自重和负压的作用下被吸人分解炉,分解炉中的结粒物料从烟室进入回转窑,粉料被吸人C5级筒后,由C5级筒沉降入窑尾烟室,气流则进入C4级筒。从上述过程可以看到,各级预热器接受上一级预热器的低温物料,接受下一级预热器的高温气体。低温物料与高温气体在进入本级预热器的管道中交汇,由于气、固两相温度反差较大因此热交换进行的较为迅速相充分,是气、固两相热交换的主要过程,70%-80%以上的热交换都是在本级预热器进气管道中进行的,而在预热器内气、固两相的热交换大致在20%左右。但预热器是气、固两相进行热交换的重要前提条件,只有预热器在充分进行气、固分离之后,才能逐级顺利实现气、固两相的热交换,因此各级预热器气、固两相的分离作用是预热器的主要功能。
由于内筒不在预热器的腔体中心,与周边筒体的距离有宽、有窄,距离大的地方形成宽腔,距离小的地方形成窄腔。稀固相气流沿切线方向进入宽腔,速度下降,部分粉尘沉降;气流继续进入窄腔后,速度加快,在离心力和气流压力的作用下,多数粉尘贴着腔壁下滑至腔内锥体;气流通过窄腔后再进入宽腔,速度复又下降,部分粉尘再次沉降,最后含有少量粉尘的气流由内筒逸出预热器。内筒由挂片组成,具有消除气流的涡流作用,使被挟带进入内筒的粉尘进一步沉降。气流由进入腔体至由内筒逸出,腔内形成较稳定有序的流场、压力场有利于气、固两相的分离和热交换,但气固两相的主要热交换过程是在进入预热器前的气流管道中进行的。
例1某国内曾知名企业,C1级筒收尘效率为95%,C2级筒收尘效率不足80%,在内筒磨短、磨平之后,收尘效率更下降到60%以下,因而频繁发生"塌料",事故不断,被工人称为"天天窑"、"礼拜窑",即天天塌料,每礼拜塌料,吨熟料实物煤耗竟高达220kg。频繁塌料使生产线始终不能正常生产,企业苦不堪言,以至濒临破产的边缘。
2山西某厂投产以来,每隔lO天到半个月都要发生一次间歇性塌料。塌料时生料从窑尾密封圈处外逸,历时30min之久,"狼烟"四起,污染严重。目前企业尚未找到经常发生塌料的原因,损失不言而喻。
所以内筒磨损、烧失和翻板阀板面积料,导致动作失灵或常开是预热器工作中最易产生的两大弊病,应引起高度注意。应该说翻板阀的动作情况应列为巡检工的日巡检内容,一旦翻板阀动作失灵或常开,应做为事故进行处理,一定要避免带病运中控室显示屏上各个数值显示对判断生产线的运行状态都是十分重要而有意义的。中控室操作人员应认真记录该生产线各列、各级预热器气流出口温度、压力的初始数据、正常运行数据及预热器发生事故时的温度、压力的变化数据等,从对这些数据的变化规律和两列同级预热器出口温度、压力参数变化的对照中研究、分析、判断预热器运行是否正常或产生问题的原因并有针对性地提出处理意见。
翻板阀是预热器系统唯一的运动部件,它的作用一般常被忽视,它的工作状态对预热器的功能性作用影响较大,严重时可使回转窑不能正常工作。"煤粉后燃"和气体温度过高会造成生料液相过早产生或液相过多,使翻板阀板面积料,动作失灵或长开,这种现象在C3、C4、C5级筒最易发生。
如某一级预热器收尘效率下降,造成该级筒应该收下来的粉状物料没有及时收下来而进入上级;在上一级筒仍然保持较高收尘效率的情况下,进来的粉尘不能如数排出,而下一级筒的物料又源源不断地回到上级筒则该筒的粉尘累积量不断增加,粉尘浓度不断增大。粉尘在本级筒内的不断聚集,犹如积云不断加厚,处于悬浮状态的浓厚积尘,在上升气流负压不堪重负之下,该筒粉状物料势将沿上升气流管道、预热器如爆雨一样一路狂泻,直至分解炉形成"塌料"。一般是下级预热器收尘效率下降,造成上一级筒的塌料,通常以C2、C3级筒塌料现象较多,其中C3、C4级筒收尘效率的下降是主要原因。