铝合金低压铸造数字化车间设计
铝合金线材生产工艺及车间设计
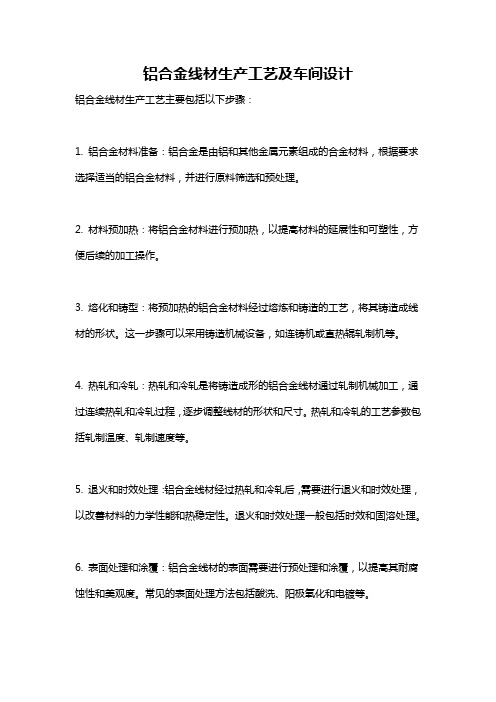
铝合金线材生产工艺及车间设计铝合金线材生产工艺主要包括以下步骤:1. 铝合金材料准备:铝合金是由铝和其他金属元素组成的合金材料,根据要求选择适当的铝合金材料,并进行原料筛选和预处理。
2. 材料预加热:将铝合金材料进行预加热,以提高材料的延展性和可塑性,方便后续的加工操作。
3. 熔化和铸型:将预加热的铝合金材料经过熔炼和铸造的工艺,将其铸造成线材的形状。
这一步骤可以采用铸造机械设备,如连铸机或直热辊轧制机等。
4. 热轧和冷轧:热轧和冷轧是将铸造成形的铝合金线材通过轧制机械加工,通过连续热轧和冷轧过程,逐步调整线材的形状和尺寸。
热轧和冷轧的工艺参数包括轧制温度、轧制速度等。
5. 退火和时效处理:铝合金线材经过热轧和冷轧后,需要进行退火和时效处理,以改善材料的力学性能和热稳定性。
退火和时效处理一般包括时效和固溶处理。
6. 表面处理和涂覆:铝合金线材的表面需要进行预处理和涂覆,以提高其耐腐蚀性和美观度。
常见的表面处理方法包括酸洗、阳极氧化和电镀等。
铝合金线材的车间设计需要考虑以下几个方面:1. 生产线布局:根据生产工艺流程,合理规划生产线的布局。
生产线之间应有足够的空间,以便设备的安装和维护。
同时,要确保生产线之间的物料和人员的流动线路畅通无阻。
2. 设备选择和摆放:根据生产工艺的要求,选择适当的设备。
设备摆放应合理,以便操作人员能够方便地进行操作和维护,同时要考虑安全和环保要求。
3. 设备安全:在生产车间中,应设置必要的安全设施,如防护网、防护栏等,以保障操作人员的安全。
此外,还需要设置紧急停机装置和灭火设备等应急设施。
4. 工艺参数控制:根据生产工艺的要求,合理设置工艺参数控制系统,以确保生产过程的稳定性和产品质量的一致性。
5. 环境管理:在车间设计中,还需要考虑环境管理,包括噪音控制、粉尘控制、废水处理等方面的工作。
总结起来,铝合金线材的生产工艺包括材料准备、熔化和铸型、热轧和冷轧、退火和时效处理、表面处理和涂覆等步骤。
《2024年低压铸造铝合金轮毂的数值模拟与工艺优化》范文

《低压铸造铝合金轮毂的数值模拟与工艺优化》篇一一、引言低压铸造技术是铝合金轮毂制造过程中广泛应用的一种铸造工艺。
它结合了计算机技术和精密铸造设备,为制造业提供了更加精确、高效率的制造方式。
通过数值模拟与工艺优化的研究,我们不仅可以对生产流程进行仿真分析,还可以优化工艺参数,提高产品质量和降低生产成本。
本文将就低压铸造铝合金轮毂的数值模拟与工艺优化进行详细探讨。
二、低压铸造铝合金轮毂的数值模拟1. 模型建立在数值模拟过程中,首先需要建立铝合金轮毂的几何模型。
通过CAD软件进行建模,并导入到有限元分析软件中。
在模型中,需要考虑到轮毂的几何形状、尺寸、材料属性等因素。
2. 材料属性设定设定材料属性是数值模拟的重要环节。
根据铝合金的材料性能,设定好材料的密度、导热系数、热膨胀系数等物理参数。
这些参数将直接影响数值模拟的结果。
3. 数值模拟过程在设定好模型和材料属性后,进行数值模拟过程。
这个过程包括填充、凝固和收缩等阶段。
通过模拟填充过程,可以观察到金属液在模具中的流动情况;通过模拟凝固和收缩过程,可以预测产品的质量和可能出现的缺陷。
三、工艺优化1. 填充速度优化在低压铸造过程中,填充速度对产品的质量和性能具有重要影响。
通过数值模拟,可以分析不同填充速度下金属液的流动情况,找到最佳的填充速度,从而提高产品的质量。
2. 温度制度优化温度制度是低压铸造过程中的重要参数之一。
通过优化温度制度,可以控制金属液的凝固过程,减少产品缺陷的产生。
通过数值模拟,可以分析不同温度制度下产品的质量和性能,从而找到最佳的温度制度。
3. 模具设计优化模具设计对产品的质量和性能具有重要影响。
通过优化模具的设计,可以提高产品的质量和降低生产成本。
在模具设计中,需要考虑到模具的材质、结构、冷却系统等因素。
通过数值模拟,可以分析不同模具设计对产品的影响,从而找到最佳的设计方案。
四、结论通过数值模拟与工艺优化的研究,我们可以对低压铸造铝合金轮毂的生产过程进行仿真分析,优化工艺参数,提高产品质量和降低生产成本。
数字化设计优化方案指导铸造工艺设备升级改造
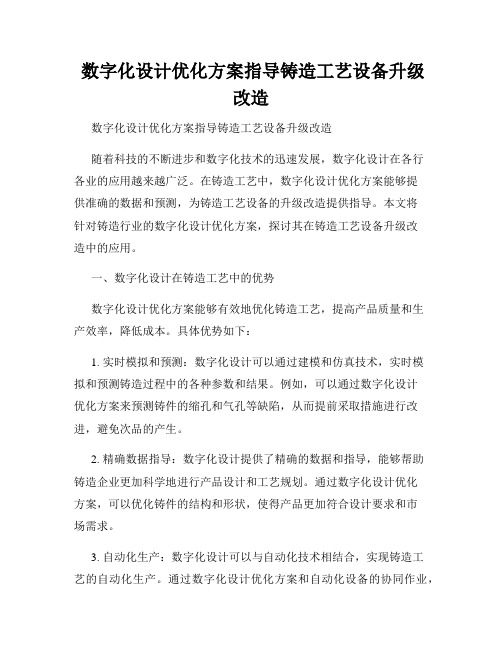
数字化设计优化方案指导铸造工艺设备升级改造数字化设计优化方案指导铸造工艺设备升级改造随着科技的不断进步和数字化技术的迅速发展,数字化设计在各行各业的应用越来越广泛。
在铸造工艺中,数字化设计优化方案能够提供准确的数据和预测,为铸造工艺设备的升级改造提供指导。
本文将针对铸造行业的数字化设计优化方案,探讨其在铸造工艺设备升级改造中的应用。
一、数字化设计在铸造工艺中的优势数字化设计优化方案能够有效地优化铸造工艺,提高产品质量和生产效率,降低成本。
具体优势如下:1. 实时模拟和预测:数字化设计可以通过建模和仿真技术,实时模拟和预测铸造过程中的各种参数和结果。
例如,可以通过数字化设计优化方案来预测铸件的缩孔和气孔等缺陷,从而提前采取措施进行改进,避免次品的产生。
2. 精确数据指导:数字化设计提供了精确的数据和指导,能够帮助铸造企业更加科学地进行产品设计和工艺规划。
通过数字化设计优化方案,可以优化铸件的结构和形状,使得产品更加符合设计要求和市场需求。
3. 自动化生产:数字化设计可以与自动化技术相结合,实现铸造工艺的自动化生产。
通过数字化设计优化方案和自动化设备的协同作业,可以提高生产效率,减少人为操作的不确定性,提高产品的稳定性和一致性。
二、数字化设计优化方案在铸造工艺设备升级改造中的应用数字化设计优化方案的应用不仅限于铸造工艺的设计和改进,还可以在铸造工艺设备的升级改造中发挥重要作用。
具体应用包括以下几个方面:1. 设备选型优化:通过数字化设计优化方案可以模拟和预测不同设备参数对铸造工艺的影响,例如浇注速度、温度控制等。
在设备升级改造中,可以基于数字化设计优化方案的结果选择最适合的设备类型和配置,从而提高生产效率和产品质量。
2. 工艺参数优化:数字化设计优化方案可以帮助改善铸造工艺中的关键参数,如浇注温度、模具温度、冷却时间等。
通过数字化设计优化方案的模拟和优化结果,可以找到最佳的工艺参数组合,提高产品的物理性能和表面质量。
《低压铸造铝合金轮毂的数值模拟与工艺优化》范文

《低压铸造铝合金轮毂的数值模拟与工艺优化》篇一一、引言随着汽车工业的飞速发展,铝合金轮毂以其轻量化、耐腐蚀等特性逐渐成为汽车制造中不可或缺的一部分。
低压铸造工艺因其生产效率高、铸件性能优良等特点在铝合金轮毂生产中得到了广泛应用。
然而,在实际生产过程中,仍需面对一系列复杂的技术挑战。
因此,本文以低压铸造铝合金轮毂为研究对象,采用数值模拟与工艺优化的方法,对生产过程进行深入分析,以提高生产效率和铸件质量。
二、低压铸造铝合金轮毂的数值模拟1. 建模与参数设定在数值模拟过程中,首先需要根据实际生产条件建立铝合金轮毂的物理模型。
模型应包括模具、金属液、压力等关键因素。
设定合理的参数,如模具温度、金属液温度、铸造压力等,是保证模拟结果准确性的关键。
2. 数值模拟过程通过有限元法对低压铸造过程进行数值模拟,包括金属液的充填过程、凝固过程以及收缩过程等。
通过模拟,可以观察到金属液在模具中的流动情况,以及铸件在凝固过程中的温度变化和应力分布。
3. 结果分析根据数值模拟结果,可以得出以下结论:(1)金属液的充填速度和压力对铸件的质量有显著影响。
过快的充填速度可能导致铸件出现气孔、夹杂等缺陷。
(2)模具温度对铸件的凝固过程有重要影响。
模具温度过高或过低都可能导致铸件产生变形或裂纹。
(3)合理的铸造压力有助于提高铸件的致密度和机械性能。
三、工艺优化1. 优化模具设计根据数值模拟结果,优化模具设计是提高铸件质量的关键。
具体措施包括:合理设计模具的进料口和排气口,以保证金属液的充填速度和排气效果;优化模具的结构,以减小铸件在凝固过程中的热应力和机械应力。
2. 控制铸造参数控制铸造参数是保证生产效率和铸件质量的重要措施。
具体包括:合理设置金属液温度和模具温度,以保证金属液的充填性能和铸件的凝固性能;控制铸造压力,以保证金属液的充填密实度和铸件的致密度。
3. 引入先进技术引入先进的低压铸造技术和设备,如真空辅助铸造、电磁搅拌等,有助于进一步提高铸件的质量和生产效率。
铸造车间低压配电系统及车间变电所的设计4

电气工程基础课程设计题目:铸造车间低压配电系统及车间变电所的设计学生姓名:学生学号:指导教师:学院:专业班级:本设计是对铸造车间的低压配电系统及车间变电所供电系统的设计。
本文首先进行了负荷计算,根据功率因数的要求在低压母线侧进行无功补偿,进而确定对主变器容量、台数,从经济和可靠性出发确定主接线方案。
其次,通过短路电流计算出最大运行方式和最小运行方式下的短路电流,确定导线型号及各种电气设备。
最后根据本厂对继电保护要求,确定相关的保护方案和二次回路方案。
本设计采用需用系数法进行负荷计算,无功功率补偿采用低压侧电容并联补偿方法,这种方法能补偿低压侧以前的无功功率、经济效益比较好。
根据铸造车间用电特点和需求,主接线方案采用了高压侧无母线、低压侧单母线分段的主接线方案。
根据干式变压器与油浸变压器在经济和安装条件对比,选择两台SC9-500/10系列干式变压器。
在仔细研究各负荷的实际数据,并严格按照国家规定,依照以上设计步骤设计本供电系统设计方案,以到达提高生产效益的目的。
一、设计任务及要求 (5)二、负荷计算和无功功率补偿 (7)2.1 负荷计算 (7)2.1.1 确定计算负荷的方法 (7)2.1.2 需要系数法 (7)2.1.3 负荷确定 (9)2.2 无功功率补偿 (9)2.2.1 无功功率补偿概念和基本原理 (9)2.2.2 无功补偿提高功率因数的意义 (10)2.3 无功补偿容量计算 (11)2.3.1 无功功率补偿方式选择 (11)2.3.2 无功补偿容量的确定 (11)2.3.3 补偿容量计算 (12)三、变电所位置和型式选择 (13)四、变电所主变压器台数和容量、类型的选择 (14)4.1 变压器容量、台数的确定 (14)4.2 主变压器型式的选择原则 (15)4.3 主变压器的确定 (16)五、变电所主接线方案的设计 (18)六、短路电流的计算 (19)6.1 短路计算的目的 (19)6.2 短路的类型 (19)6.3 短路电流计算的方法步骤 (21)6.4 短路电流计算 (21)七、变电所一次设备的选择与校验 (23)7.1 一次设备的选择 (23)7.1.1 概述 (23)7.1.2 一次设备的选择原则 (24)7.1.3 按短路情况校验电器的稳定性 (24)7.2 一次设备选择与校验 (26)八、变电所进出线的选择与校验 (31)8.1 高压进线选择 (31)8.2 低压出线选择 (33)九、变电所二次回路方案的选择及继电保护的整定 (34)9.1 概述 (34)9.2 继电保护 (34)9.2.1 继电保护的要求 (34)9.2.2 过电流保护 (34)9.2.3 电流速断保护 (35)9.3 变压器保护 (35)9.3.1 概述 (35)9.3.2 车间变电所的各分厂变压器保护 (36)9.3.3 降压变电所变压器保护 (36)9.4 继电保护的选择与整定 (37)9.4.1 继电保护的种类 (37)9.4.2 反时限过电流保护 (37)十、防雷保护和接地装置的设计 (39)10.1 概述 (39)10.2 防雷与接地 (40)10.2.1 防雷装置 (40)10.2.2 架空线路的防雷保护 (40)10.2.3 车间变电所的防雷保护和接地装置的设计 (41)10.2.4 电力系统的接地 (41)10.2.5 配电所公共接地装置的设计 (41)十一、设计心得 (44)十二、附录 (45)12.1 变电所主结线图 (45)12.2 防雷保护图 (46)一、设计任务及要求(一)任务:根据以下所给条件,合理选用高低压变、配电设备及供电系统运行方式。
数字化智能化铸造车间建设与实施方案
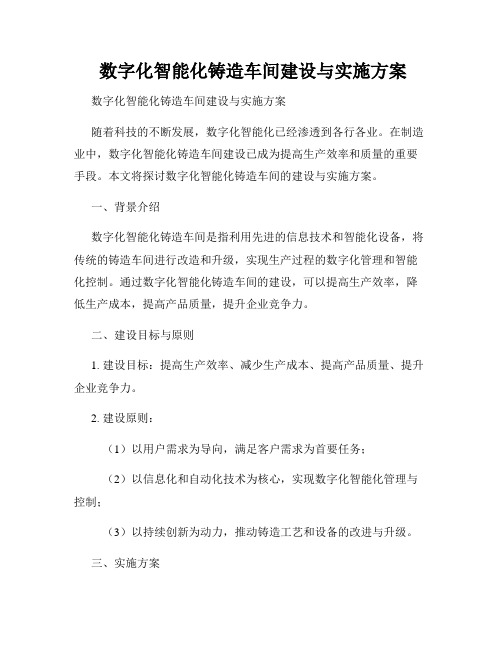
数字化智能化铸造车间建设与实施方案数字化智能化铸造车间建设与实施方案随着科技的不断发展,数字化智能化已经渗透到各行各业。
在制造业中,数字化智能化铸造车间建设已成为提高生产效率和质量的重要手段。
本文将探讨数字化智能化铸造车间的建设与实施方案。
一、背景介绍数字化智能化铸造车间是指利用先进的信息技术和智能化设备,将传统的铸造车间进行改造和升级,实现生产过程的数字化管理和智能化控制。
通过数字化智能化铸造车间的建设,可以提高生产效率,降低生产成本,提高产品质量,提升企业竞争力。
二、建设目标与原则1. 建设目标:提高生产效率、减少生产成本、提高产品质量、提升企业竞争力。
2. 建设原则:(1)以用户需求为导向,满足客户需求为首要任务;(2)以信息化和自动化技术为核心,实现数字化智能化管理与控制;(3)以持续创新为动力,推动铸造工艺和设备的改进与升级。
三、实施方案1. 设备更新与改造数字化智能化铸造车间的建设首先要对现有设备进行更新和改造。
采购先进的数字化智能化设备,如数字化铸造模具、智能化铸造机器人等,来替代传统的手工操作,提高生产效率和产品质量。
同时,引入智能化设备与生产线进行连接,实现数据采集、传输和分析,为智能化管理提供支持。
2. 数据采集与分析建设数字化智能化铸造车间需要对生产过程中的各个环节进行数据采集。
通过传感器、监控设备等,实时获取熔炉温度、压力、振动等数据。
同时,采用数据分析技术,进行数据挖掘和处理,提取有价值的信息,为生产决策提供依据。
3. 智能化管理与控制基于采集与分析的数据,数字化智能化铸造车间将实现精细化管理与智能化控制。
通过建立智能化生产管理系统,实现对整个生产过程的实时监控和调度。
同时,借助人工智能和大数据技术,对生产过程进行优化和预测,以提高生产效率和产品质量。
4. 员工培训与技能提升数字化智能化铸造车间的建设需要员工具备相应的技术与知识。
因此,企业应加强员工培训,提高员工的数字化技能和智能化操作能力。
铝合金缸盖低压铸造模具及工艺系统设计
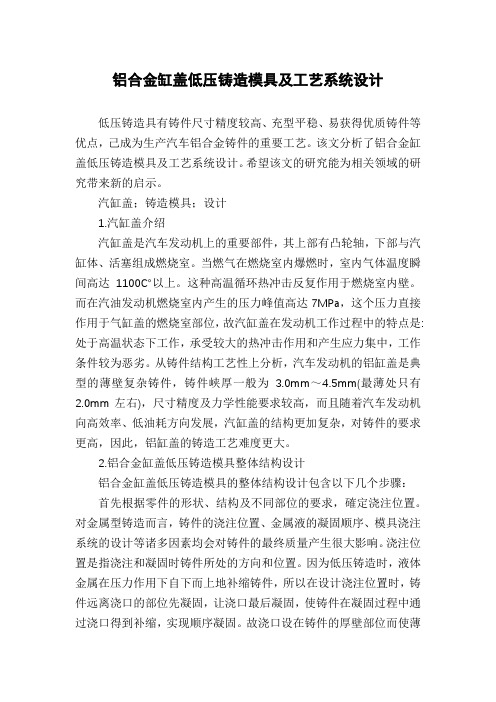
铝合金缸盖低压铸造模具及工艺系统设计低压铸造具有铸件尺寸精度较高、充型平稳、易获得优质铸件等优点,己成为生产汽车铝合金铸件的重要工艺。
该文分析了铝合金缸盖低压铸造模具及工艺系统设计。
希望该文的研究能为相关领域的研究带来新的启示。
汽缸盖;铸造模具;设计1.汽缸盖介绍汽缸盖是汽车发动机上的重要部件,其上部有凸轮轴,下部与汽缸体、活塞组成燃烧室。
当燃气在燃烧室内爆燃时,室内气体温度瞬间高达1100℃以上。
这种高温循环热冲击反复作用于燃烧室内壁。
而在汽油发动机燃烧室内产生的压力峰值高达7MPa,这个压力直接作用于气缸盖的燃烧室部位,故汽缸盖在发动机工作过程中的特点是:处于高温状态下工作,承受较大的热冲击作用和产生应力集中,工作条件较为恶劣。
从铸件结构工艺性上分析,汽车发动机的铝缸盖是典型的薄壁复杂铸件,铸件峡厚一般为 3.0mm~4.5mm(最薄处只有2.0mm左右),尺寸精度及力学性能要求较高,而且随着汽车发动机向高效率、低油耗方向发展,汽缸盖的结构更加复杂,对铸件的要求更高,因此,铝缸盖的铸造工艺难度更大。
2.铝合金缸盖低压铸造模具整体结构设计铝合金缸盖低压铸造模具的整体结构设计包含以下几个步骤:首先根据零件的形状、结构及不同部位的要求,確定浇注位置。
对金属型铸造而言,铸件的浇注位置、金属液的凝固顺序、模具浇注系统的设计等诸多因素均会对铸件的最终质量产生很大影响。
浇注位置是指浇注和凝固时铸件所处的方向和位置。
因为低压铸造时,液体金属在压力作用下自下而上地补缩铸件,所以在设计浇注位置时,铸件远离浇口的部位先凝固,让浇口最后凝固,使铸件在凝固过程中通过浇口得到补缩,实现顺序凝固。
故浇口设在铸件的厚壁部位而使薄壁部位远离浇1∶3。
确定各模块的成形方式。
当铸件的浇注位置确定以后,对金属型铸造而言,还须确定各部分的成形方法,也就是说,铸件的外形及内腔是由何种方式成形的。
对金属型铸造而言,国内外普遍采用的成形方式一般为金属模、砂芯、活块及冷铁。
铝合金铸件数字化转型案列

铝合金铸件数字化转型案列英文回答:Aluminum alloy casting digital transformation case study.In recent years, the aluminum alloy casting industryhas been undergoing a digital transformation to improve efficiency, reduce costs, and enhance product quality. One successful case study of this digital transformation is the implementation of 3D printing technology in the production process of aluminum alloy castings.3D printing, also known as additive manufacturing, has revolutionized the way aluminum alloy castings are produced. By using 3D printing technology, manufacturers are able to create complex and intricate designs with a high level of precision. This has led to a significant improvement in the quality of aluminum alloy castings, as well as a reductionin production time and material waste.Furthermore, the digitalization of the production process has allowed for better monitoring and control of the manufacturing parameters, leading to a more consistent and reliable product. This has not only improved theoverall quality of the aluminum alloy castings but has also increased customer satisfaction.In addition to the production process, digital transformation has also impacted other areas of the aluminum alloy casting industry, such as supply chain management, inventory control, and customer relationship management. By implementing digital tools and technologies, manufacturers are able to streamline their operations, reduce lead times, and enhance communication with customers and suppliers.Overall, the digital transformation of the aluminum alloy casting industry has brought about significant improvements in efficiency, cost reduction, and product quality. As technology continues to advance, it is expected that further innovations will continue to drive theindustry forward.中文回答:铝合金铸件数字化转型案例。
压铸车间优化设计报告范文

压铸车间优化设计报告范文1. 引言压铸是一种重要的金属成形工艺,在许多行业中都有广泛应用。
压铸车间作为进行压铸生产的关键环节,其优化设计对于提高生产效率、降低生产成本和提升产品质量具有重要意义。
本报告旨在分析现有压铸车间存在的问题,并提出相应的优化设计方案。
2. 现状分析2.1 设备配置目前压铸车间共设有10台压铸机,在不同生产线上进行生产。
然而,由于部分设备老化和技术参数滞后,导致生产效率较低;同时,设备之间的协同配合也存在一定的问题,影响了整体生产效率。
2.2 压铸工艺现有压铸车间的工艺流程较为简单,未能充分利用先进的工艺技术。
对于不同的产品型号,生产工艺并没有进行详细的分析和优化,导致浪费资源和降低产品质量。
2.3 环境安全压铸车间存在部分设备安全保护措施不完善的问题,增加了工人操作的风险。
此外,车间内的通风系统效果较差,容易导致有毒气体残留,对工人的健康构成威胁。
3. 优化设计方案为了提高压铸车间的生产效率、降低生产成本和提升产品质量,以下是本报告提出的优化设计方案。
3.1 设备升级与更新针对现有压铸机老化和技术参数滞后的问题,建议逐步进行设备升级与更新。
选择品质可靠、效率高的新型压铸机,以提高生产效率;同时,应考虑设备的数字化、智能化,以提高设备之间的协同配合。
3.2 工艺优化与自动化针对现有工艺的问题,建议进行工艺优化和自动化改造。
通过详细的工艺分析和测试,优化每一道工序的参数设置,以降低废品率和提高产品质量。
对于适合自动化流程的工序,引入机器人和自动化设备,提高生产效率和生产一致性。
3.3 环境安全改善为了确保车间内工人的安全和健康,建议加强环境安全改善措施。
针对设备的安全保护,应进行全面的安全检修和设备保护措施的加固。
对于通风系统,应进行改善和优化,以保证车间内空气质量的合格。
4. 实施计划为了顺利进行优化设计,并确保其效果的可持续,以下是本报告提出的实施计划。
4.1 设备升级与更新计划根据压铸车间的生产规模和资金预算,制定设备升级与更新计划。
再生铝合金铸造工艺技术的数字化制造与智能工厂
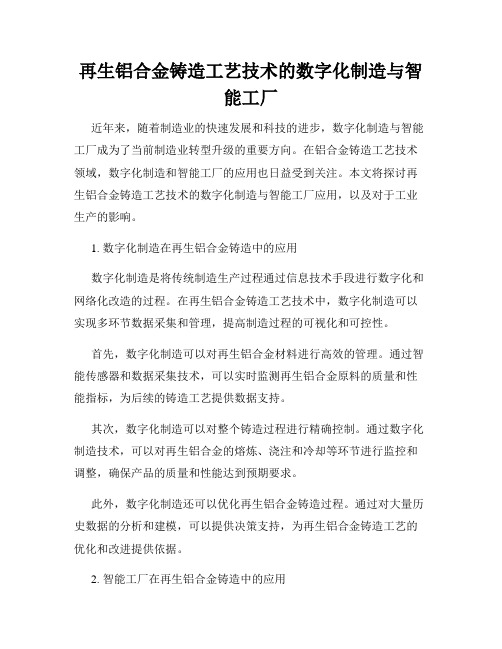
再生铝合金铸造工艺技术的数字化制造与智能工厂近年来,随着制造业的快速发展和科技的进步,数字化制造与智能工厂成为了当前制造业转型升级的重要方向。
在铝合金铸造工艺技术领域,数字化制造和智能工厂的应用也日益受到关注。
本文将探讨再生铝合金铸造工艺技术的数字化制造与智能工厂应用,以及对于工业生产的影响。
1. 数字化制造在再生铝合金铸造中的应用数字化制造是将传统制造生产过程通过信息技术手段进行数字化和网络化改造的过程。
在再生铝合金铸造工艺技术中,数字化制造可以实现多环节数据采集和管理,提高制造过程的可视化和可控性。
首先,数字化制造可以对再生铝合金材料进行高效的管理。
通过智能传感器和数据采集技术,可以实时监测再生铝合金原料的质量和性能指标,为后续的铸造工艺提供数据支持。
其次,数字化制造可以对整个铸造过程进行精确控制。
通过数字化制造技术,可以对再生铝合金的熔炼、浇注和冷却等环节进行监控和调整,确保产品的质量和性能达到预期要求。
此外,数字化制造还可以优化再生铝合金铸造过程。
通过对大量历史数据的分析和建模,可以提供决策支持,为再生铝合金铸造工艺的优化和改进提供依据。
2. 智能工厂在再生铝合金铸造中的应用智能工厂是通过各种信息技术手段实现生产自动化和智能化的工厂模式。
在再生铝合金铸造中,智能工厂的应用可以提高生产效率、产品质量和资源利用率。
首先,智能工厂可以实现再生铝合金铸造的自动化生产。
通过机器人和自动化设备的应用,可以实现再生铝合金材料的自动搬运、熔炼、浇注和冷却等工序,降低人力成本,提高生产效率。
其次,智能工厂可以实现再生铝合金铸造过程的实时监控和预警。
通过传感器和监测设备的安装,可以对再生铝合金铸造过程中的温度、压力、流速等关键参数进行实时监测,并及时发出预警,提高生产安全性和产品质量。
此外,智能工厂还可以实现再生铝合金铸造的资源优化利用。
通过智能化的调度和优化算法,可以对再生铝合金材料、能源和设备进行协调和优化配置,最大程度地提高资源利用效率,降低生产成本。
铝熔铸智能化建设方案

铝熔铸智能化建设方案铝熔铸智能化建设方案是指通过引入智能化技术和设备,提高铝熔铸生产过程的效率、质量和安全性。
以下是一个铝熔铸智能化建设方案的概述:1. 自动化控制系统:引入先进的自动化控制系统,对铝熔铸生产过程进行实时监控和控制。
通过传感器和监测设备,实时监测铝液温度、压力、流速等参数,并自动调节熔炉温度、调整冷却系统等,以确保铝熔铸过程的稳定性和一致性。
2. 智能化设备:引入智能化设备,如智能感应加热炉、智能液铝注入设备等,提高铝熔铸生产过程的效率和精度。
智能感应加热炉可以根据铝液的温度需求全自动控制加热功率,提高炉的加热效率和熔化速度;智能液铝注入设备可以根据注入要求和模具特性进行智能控制,提高注入精度和产品质量。
3. 数据采集和分析系统:建立铝熔铸生产过程的数据采集和分析系统,对生产数据进行实时监测、整理和分析。
通过分析数据,可以找出生产过程中存在的问题和优化空间,并及时采取措施进行改进。
这可以帮助提高生产效率、降低能源消耗,并减少废品率。
4. 物联网应用:引入物联网技术,实现铝熔铸设备和系统之间的互联互通。
通过将设备连接到云平台,可以实现设备的远程监控和控制,同时可以实现设备之间的互联互通,提高生产协同效率。
例如,可以通过远程监控熔炉温度和液铝注入情况,及时发现并解决潜在问题。
5. 人机协同:在智能化的铝熔铸生产过程中,人机协同也非常重要。
通过培训和教育,提高操作员的智能化设备操作能力和生产过程管理能力,以及对数据采集和分析应用的理解和使用。
同时,智能化设备和系统也应提供友好的用户界面,使操作员能够更轻松地掌握和操作设备。
以上是一个铝熔铸智能化建设方案的概述,当然还有许多其他的细节和技术可以进一步优化和细化。
铝熔铸智能化建设的目标是提高生产效率、降低能源消耗、提高产品质量和安全性,以及实现可持续发展。
数字化设计优化铸造结构件实现轻量化设计
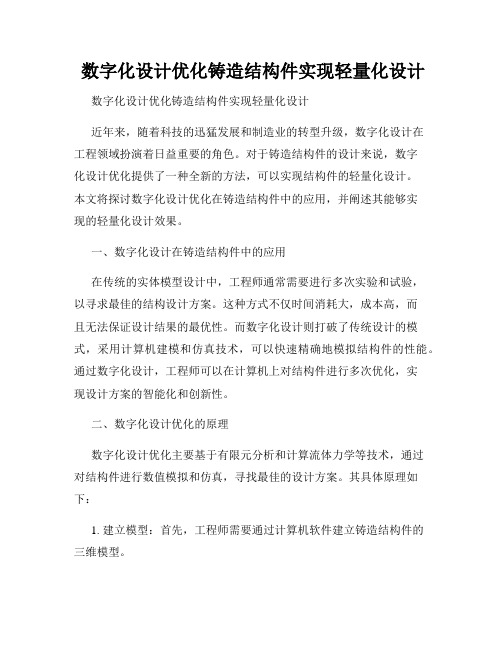
数字化设计优化铸造结构件实现轻量化设计数字化设计优化铸造结构件实现轻量化设计近年来,随着科技的迅猛发展和制造业的转型升级,数字化设计在工程领域扮演着日益重要的角色。
对于铸造结构件的设计来说,数字化设计优化提供了一种全新的方法,可以实现结构件的轻量化设计。
本文将探讨数字化设计优化在铸造结构件中的应用,并阐述其能够实现的轻量化设计效果。
一、数字化设计在铸造结构件中的应用在传统的实体模型设计中,工程师通常需要进行多次实验和试验,以寻求最佳的结构设计方案。
这种方式不仅时间消耗大,成本高,而且无法保证设计结果的最优性。
而数字化设计则打破了传统设计的模式,采用计算机建模和仿真技术,可以快速精确地模拟结构件的性能。
通过数字化设计,工程师可以在计算机上对结构件进行多次优化,实现设计方案的智能化和创新性。
二、数字化设计优化的原理数字化设计优化主要基于有限元分析和计算流体力学等技术,通过对结构件进行数值模拟和仿真,寻找最佳的设计方案。
其具体原理如下:1. 建立模型:首先,工程师需要通过计算机软件建立铸造结构件的三维模型。
2. 材料特性:然后,工程师需要输入材料的特性参数,如材料的强度、刚度等。
这些参数对于结构件的性能影响至关重要。
3. 载荷模拟:接下来,工程师可以通过载荷模拟对结构件进行仿真。
通过施加不同的力、温度、压力等载荷条件,可以模拟结构件在不同工况下的受力情况。
4. 优化算法:在数字化设计优化中,工程师可以使用不同的优化算法,如遗传算法、粒子群算法等,对结构件进行优化。
通过不断迭代计算,找到最佳的结构形状和参数。
5. 评估设计方案:最后,工程师需要对优化的设计方案进行评估和比较。
通过比较不同方案的性能指标,如重量、强度、刚度等,选择最优的设计方案。
三、数字化设计优化实现铸造结构件的轻量化设计数字化设计优化在铸造结构件的设计中,能够实现轻量化的目标。
具体体现在以下几个方面:1. 材料优化:数字化设计优化可以根据不同的载荷条件和工作环境,优化材料的使用。
压铸车间这么布置,生产效率直接提高10倍!(共9页)

压铸车间这么布置(bùzhì),生产效率直接提高10倍!一、压铸车间(chējiān)在工厂总平面布置中的位置一个完整的压铸生产企业要正常运作应有生产车间、辅助(fǔzhù)车间、动力设施、仓库及运输、行政管理及后勤等。
而一个产品厂则还有机加工车间、装配车间和其他车间。
压铸车间在工厂总平面布置中的位置应考虑以下几点:1、压铸车间属热加工车间,产生烟气较多,从环境保护考虑,应将压铸车间布置在夏季主导风向的下风区,并在离工厂入口较远地方;也不应与锻压、砂型铸造车间靠一起。
2、考虑铸件的运输方便,尽可能靠近机械加工车间。
3、根据本厂生产规模、技术水平和发展可能性,宜留有发展余地。
4、创造良好工作环境,应充分利用自然通风和自然采光,避免西晒,厂房的纵向天窗轴线应与夏季风主导风向成60-90°角,以便排出烟气和有害气体。
5、根据防火要求,压铸车间与邻近建筑物之间应有一定距离,在车间周围应有消防车行驶道路。
6、镁合金压铸车间应是独立单层建筑,车间地面应高于其他地面。
二、压铸车间的布置1、平面布置原则1)车间的平面布置首先要考虑物料(炉料、金属液、铸件及浇注系统等)流程通畅、紧凑,避免来回(láihuí)输送。
2)在充分利用车间(chējiān)面积的同时应考虑压铸机维修,压铸型装拆、维护和存放场地。
3)主要生产工部(压铸、熔化(rónghuà))应布置在具有良好采光和通风地方。
4)办公室的位置应保证工作人员出入方便,并有较良好的工作环境。
生活间应避免通过车间再到生活间。
2、压铸工部的布置1)压铸机的布置应根据规模大小分别集中布置,对于自动化程度高的压铸车间,宜按机组布置,便于生产管理。
2)根据厂房条件和压铸机的大小不同可采用单列布置和双列(多列)布置。
压铸机可垂直车间墙面,也可平行车间墙面布置,无论采用那种布置方法,压铸机最突出部分到墙面距离不应小于1米,车间内人行道不应小于1.5米,电瓶车的运输通道不应少于3米。
铝合金压铸车间的工艺布局探讨
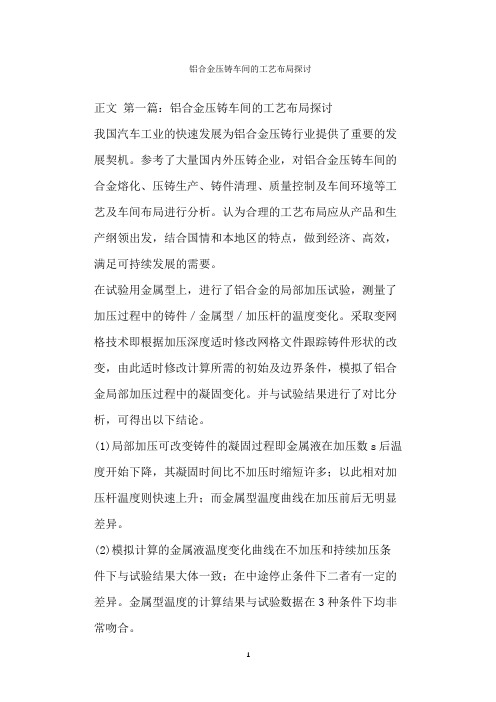
铝合金压铸车间的工艺布局探讨正文第一篇:铝合金压铸车间的工艺布局探讨我国汽车工业的快速发展为铝合金压铸行业提供了重要的发展契机。
参考了大量国内外压铸企业,对铝合金压铸车间的合金熔化、压铸生产、铸件清理、质量控制及车间环境等工艺及车间布局进行分析。
认为合理的工艺布局应从产品和生产纲领出发,结合国情和本地区的特点,做到经济、高效,满足可持续发展的需要。
在试验用金属型上,进行了铝合金的局部加压试验,测量了加压过程中的铸件/金属型/加压杆的温度变化。
采取变网格技术即根据加压深度适时修改网格文件跟踪铸件形状的改变,由此适时修改计算所需的初始及边界条件,模拟了铝合金局部加压过程中的凝固变化。
并与试验结果进行了对比分析,可得出以下结论。
(1)局部加压可改变铸件的凝固过程即金属液在加压数s后温度开始下降,其凝固时间比不加压时缩短许多;以此相对加压杆温度则快速上升;而金属型温度曲线在加压前后无明显差异。
(2)模拟计算的金属液温度变化曲线在不加压和持续加压条件下与试验结果大体一致;在中途停止条件下二者有一定的差异。
金属型温度的计算结果与试验数据在3种条件下均非常吻合。
(3)计算的加压杆温度上升梯度大于试验测量的温度梯度,二者有相当的差异,主要原因是变网格技术不能完全反应局部加压引起铸件形状的改变。
第二篇:压铸车间压铸车间车间现场管理制度1.目的:规范员工对生产现场的整理,实现均衡、安全、文明生产、提高业务素质,提高经济效益、达到优质、高效、低耗具有重要意义2.范围:公司生产车间3.内容3.1 质量管理3.1.1 各车间应严格执行《程序文件》的规定,履行自己的职责、协调工作。
3.1.2 对关键过程按《程序文件》的规定严格控制,对出现的异常情况,要查明原因,及时排除,使质量始终处于稳定的受控状态。
3.1.3 认真执行“三检”制度(自检、互检、巡检),操作人员对自己生产的产品要做到自检,检查合格后,方能转入下工序,下工序对上工序的产品进行检查,不合格产品有权拒绝接收。
压铸车间工程方案
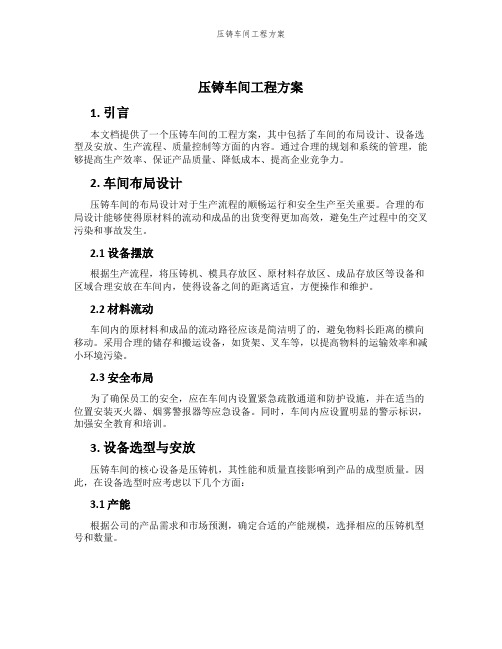
压铸车间工程方案1. 引言本文档提供了一个压铸车间的工程方案,其中包括了车间的布局设计、设备选型及安放、生产流程、质量控制等方面的内容。
通过合理的规划和系统的管理,能够提高生产效率、保证产品质量、降低成本、提高企业竞争力。
2. 车间布局设计压铸车间的布局设计对于生产流程的顺畅运行和安全生产至关重要。
合理的布局设计能够使得原材料的流动和成品的出货变得更加高效,避免生产过程中的交叉污染和事故发生。
2.1 设备摆放根据生产流程,将压铸机、模具存放区、原材料存放区、成品存放区等设备和区域合理安放在车间内,使得设备之间的距离适宜,方便操作和维护。
2.2 材料流动车间内的原材料和成品的流动路径应该是简洁明了的,避免物料长距离的横向移动。
采用合理的储存和搬运设备,如货架、叉车等,以提高物料的运输效率和减小环境污染。
2.3 安全布局为了确保员工的安全,应在车间内设置紧急疏散通道和防护设施,并在适当的位置安装灭火器、烟雾警报器等应急设备。
同时,车间内应设置明显的警示标识,加强安全教育和培训。
3. 设备选型与安放压铸车间的核心设备是压铸机,其性能和质量直接影响到产品的成型质量。
因此,在设备选型时应考虑以下几个方面:3.1 产能根据公司的产品需求和市场预测,确定合适的产能规模,选择相应的压铸机型号和数量。
3.2 稳定性和可靠性优先选择质量好、性能稳定、维修率低的压铸机,以确保生产过程的连续性和稳定性。
3.3 自动化程度考虑到人工成本的增加和操作的安全性,可以选择具有较高自动化程度的压铸机,提高生产效率和稳定性。
3.4 安放位置根据车间布局设计,将压铸机等配套设备和设施放置在合适的位置,方便操作和维护。
4. 生产流程良好的生产流程能够提高生产效率和产品质量,并有效避免生产过程中的事故和质量问题。
4.1 原材料准备对于压铸车间来说,原材料的准备是关键的一步。
确保原材料的供应充足、质量可靠,有规范的检验流程,以确保产品的质量稳定。
铝合金熔铸车间设计方案

铝合金熔铸车间设计方案铝熔铸是铝加工厂的第一道生产工序。
设计的主要内容为:工艺流程选择、设备选择和车间布置。
工艺流程选择铝熔铸生产包括配料、熔炼、铸造、均热、机械加工和检验等工序。
大型熔铸车间还有残屑及熔渣处理、中间合金制备、熔剂制备等关心工序。
配料熔炼铝及铝合金的炉料有:(1)铝电解厂运来的电解铝液或重熔铝锭以及镁、锌等;(2)铝一锰、铝一硅等中间合金;(3)铝加工厂各车间返回的废料、边角残料和碎屑;(4)外购的废旧铝及铝合金制品等。
生产时,依据原料供给状况和合金的化学成分,确定各种炉料的用量。
熔炼将配好的炉料加热熔化,调整熔体化学成分和温度,进展净化处理,以降低气体和夹杂物在熔体中的含量。
净化处理有炉内和炉外在线两种方法。
前者是在炉内除气,这种方法可能使熔体受到二次污染。
后者是将除气和除渣在配置于生产线中的特地装置内进展。
其中,以过滤除渣为主的有承受玻璃丝布、刚玉微孔陶瓷管和陶瓷泡沫过滤器等方法;除气除渣兼有的有 FILD 法(Fumeless In Line Degassing 法,英国铝业公司研制)、Alcoa 法(美国铝业公司研制)、SNIF 法(Spinning Nozzle Inert Flotation 法,美国联合碳化物公司研制)、MINT 法(Melt In Line Treatment System 法,美国联合铝业公司研制)等。
这些装置具有净化效果好、公害小、生产过程连续等优点。
铸造常用的铸造方法有立式半连续铸造、固定模水平连续铸造、活动模连续铸造和水冷模铸造四种。
(1)立式半连续铸造法。
能生产多种合金成分和多种规格的扁锭、空心圆锭、实心圆锭,并适于多模铸造,应用最广。
依据结晶成形方法,又可以分为使用一般水冷结晶器的铸造法、在水冷结晶器上部设有绝热保温帽的热顶铸造法和不用水冷结晶器,而用电磁力来保持铸锭断面外形,然后直接水冷成形的电磁铸造法等三种。
其中结晶器铸造法设备简洁,但铸锭内部组织和外表光滑度都不如后两种好。
- 1、下载文档前请自行甄别文档内容的完整性,平台不提供额外的编辑、内容补充、找答案等附加服务。
- 2、"仅部分预览"的文档,不可在线预览部分如存在完整性等问题,可反馈申请退款(可完整预览的文档不适用该条件!)。
- 3、如文档侵犯您的权益,请联系客服反馈,我们会尽快为您处理(人工客服工作时间:9:00-18:30)。
建筑与结构设计.4rchiiectural and Structural Design 铝合金低压铸造数字化车间设计Digital Workshop Design for Aluminum Alloy Low Pressure Casting李祖权(中机第一设计研究院有限公司,合肥230601)LI Zu-quan(First Design&Research Institute MI China Co.Ltd.,Hefei230601,China)【摘要】低压铸造工艺已用于生产汽车发动机铝合金缸体缸盖:论文对国家智能制造装备发展专项《年产45万件汽车发动机铝合金缸盖缸体低压铸造数字化车间》实施的任务、车间总体布局、主要工艺方案及相关节能、环保措施进行分析总结,以供相似项目设计参考。
[Abstract]Low pressure casting technology has been adopted in producing aluminum alloy cylinder and cylinder head of the automobile engine.The paper analyses and concludes the implementation task,workshop general layout,main technological scheme,relevant energy-savings and environmental actions for the national intelligent manufacturing equipment development project of**An annual output of 450,000pieces of automotive engine aluminum alloy cylinder head cylinder body low-pressure casting digital workshop",the purpose is to provide a reference to similar project designing.【关键词】铝合金;低压铸造;数字化车间;工艺设计[Keywords]aluminum alloy;lowpressure casting;digital workshop;technological design【中图分类号】TH181【文献标志码】A【文章编号】1007-9467(2019)02-0009-03[DOI]10.13616/ki.gcjsysj.2019.02.0011引言铸造是制造业的基础,对传统铸造车间进行数字化、智能化、绿色化升级建设和改造,是实现中国制造向中国创造发展的需要。
低压铸造是最早的反重力铸造技术,20世纪40年代开始用于工业生产。
如今,已用于生产铝合金、镁合金件的生产,如汽车工业的汽车轮毂、内燃发动机的气缸体、气缸盖、活塞、导弹外壳、叶轮、导风轮等形状复杂、质量要求高的铸件。
目前,我国汽车产业持续发展,作为汽车核心部件的发动机,已从依赖国外成熟生产线批量生产逐步发展到设计和制造具有自主知识产权的高性能发动机。
约占50%左右国内市场份额的国产品牌汽车自主创新的巨大需求对发动机关键部件一盖和缸体提出了轻量化、性能提升、成本更低等一系列更高的要求。
因此,必须对缸盖缸体低压铸造生产线进行柔性化、智能彳匕和绿色化升级,以满足发动机行业对铸件的要【作者简介】李祖权(1965~),男,安徽霍邱人,研究员,从事工程设计及技术质量管理研究。
求,并进一步提升我国低压铸造装备行业技术水平。
铝合金低压铸造数字化车间工艺设计是国家智能制造装备发展专项《年产45万件汽车发动机铝合金缸盖缸体低压铸造数字化车间》的一项重要内容,本文对相关的工艺设计进行分析总结,以供类似项目设计参考。
2车间任务本车间为国家智能制造装备发展专项《年产45万件汽车发动机铝合金缸盖缸体低压铸造数字化车间》项目的实施车间。
主要承担汽车发动机缸盖、缸体铝合金铸件的批量生产。
代表产品的外形尺寸:汽缸盖:50mmx350mmx250mm,汽缸体:450mmx250minx300mm:年生产铸件详见表10表1低压铸造数字化车间年生产铸件表序号铸件名称平均单件铸件质量/kg总件数/万件总质量/t 1汽缸盖182545002汽缸体252050003总计4595009工程建设与设计(Jonftruetion&Design For P roject3车间总体布局铝合金低压铸造数字化车间主要熔炼工部,制芯工部、成型热处理一体化工部、清整工部、半精加工工部、终检六个工部组成。
另外,车间另配有模具库、炉料库以及数字化控制室等。
本着物流顺畅、便于车间生产组织及环境卫生保护的原则,各操作区既紧密联系又相互独立。
车间主厂房长度为160m,跨度为30m,最大起吊质量为20t/5t。
详见车间平面布置简图(见图1)2卅料图1车间平面布置简图4主要工艺方案图2是铝合金缸盖缸体低压铸造数字化车间的主要工艺流程,主要包括制芯、熔炼、成型、热处理、清整粗加工、检测检验、半精加工等工序。
图2铝合金缸盖缸体低压铸造数字化车间的主要工艺流程图4.1制芯工部根据工艺分析,采用壳芯、热芯盒及冷芯3种制芯工艺。
为提高缸盖和缸体内部型腔的质量,缸盖的进气道、排气道采用壳芯工艺制芯.水套及其它辅助型芯等采用热芯工艺制芯,并且考虑到节能、环保、扩散性和铸件光洁度因素,缸盖和缸体的油道芯和内外冒口芯采用冷芯工艺制芯。
采用6台热芯机、2套冷芯机、2套AGV成套设备和1条覆膜砂再生线。
车间中心实验室检测覆膜砂原材料砂粒度、强度、发气量等关键参数。
制芯设备数控系统与车间数字化总控室进行网络连接,低压铸造数字化智能集成平台在线监测设备的吹砂压力、模具温度等参数,并上传存储参数信息。
采用料车固定RFID记录信息,做到砂芯与料车及作业者的对应,针对作业环境不同,分别设置了固定式和手持式RFID读写设备。
经过修配芯由AGV按照成型热处理一体化工部需求配送运输至相应的工位待用,废芯砂经再生后回用,实现铸造绿色化。
4.2熔炼工部车间采用2台1.5讪集中熔化炉,实现铝合金母液批量、连续熔化,电子配料系统自动®料。
熔化炉采用热泵式节能型天然气燃烧器热回收装置,在空炉烟气温度高时废热得到回收利用,利于铝锭预热,节能5%~10%甚至以上。
炉内安装燃烧控制系统,能够控制铝液的温度和燃烧器的燃烧过程,同时低压铸造数字化智能集成平台监测炉内熔解温度、时间、天然气压力等工艺参数。
车间配4台ALMT-800型液压可倾式圮竭炉用于辅助熔炼及精炼。
铝合金母液间歇放入液压可倾式圮竭炉中,加入回炉料进行熔炼及合金成分调整,铝液经精炼除气检测合格后,转倒到转运包中,利用智能行车转运至成型热处理工部低压铸造机的保温炉中储存。
在液压可倾式九埸炉上方采用回转式吸尘罩将冶炼烟尘抽出室外集中处理,达标排放。
配有1台直读光谱分析仪、2台密度测量仪、1台在线测氢系统,铝液试样送至炉前化验室,进行铝液化学成分和密度的快速在线检测,集成平台智能分析原材料的烧损,实时反馈和调整配料比。
4.3成型与热处理一体化工部车间采用节能型铸造成型热处理一体彳匕工艺进行缸盖缸体铸造成型和热处理,主要由两组节能型成型热处理一体化智能单元完成缸盖缸体铸造成型、震砂、热处理、切割浇冒口和激光打码等工序。
每组智能单元生产节拍小于90s,由4台铝合金智能低压铸造机、7台机器人、2台回转式固溶热处理炉、1台震砂机、1台回转式时效热处理炉、1套电磁导航AGV.1台切割机、1台半导体激光打码机及辅助装备组成。
缸套放置、砂芯下芯及铸件抓取全部由机器人完成,生产效率高。
铸件成型经震砂处理后,由机器人送到节能型回转式固溶10热处理炉中进行固溶处理,充分利用铸件成型后的余热,节能效果显著。
低压铸造机配有智能加压控制系统、模温监控系统,智能加压控制系统可以监控保温炉铝液温度、炉气温度、压力参数、充型位置等工艺参数;模温监控系统实时监测模具温度,及时反馈并调整工艺参数,实现铸件的顺序凝固;保温炉进行连续除气,配置在线测氢仪,实时监测铝液的含氢量,实时自动调整惰性气体流量,保证铝液质量。
热处理方面采用无料筐方式处理,应用机器人将铸件放置于回转式固溶热处理炉,在热状态下入炉,能够缩短升温和固溶时间,节省耗能30%以上,大大缩短了装料时间,降低了作业人员的劳动强度。
回转式固溶热处理炉及时效热处理炉具备了连续式铝合金热处理炉的各项性能特点,采用人机对话界面,可显示设备运行状态、各部位异常警报和处理方式。
时效热处理后的工件由机械手装箱,AGV运送到清整工部进行清整粗加工处理。
4.4清整工部该工部由6台清整机器人、8台清整加工机、2台密封检测设备、1套AGV成套设备、1台超声波清洗机等组成。
由数控加工机床完成铸件粗加工,机械手抓取铸件去除飞边毛刺。
采用全自动干式定量气密性检测设备进行气密性在线检测,分别采用试漏仪用于缸体油道、水套、曲轴腔(进排气道)的泄漏检验,采用液压形式对工件进行压封堵漏,通过对缸体缸盖水道油道和腔体充预定压力的压缩空气,采用F620差压空气泄漏仪分时完成对水套、油道与腔体的检测过程,检测压力自动调整为设置压力,通过被测工件内腔的压力变化值来判断工件是否泄漏。
试漏结束后对试漏合格工件打上合格标记。
经过密封测试后,如果有渗漏并且可以修整的铸件放置到专用料框中存放,集中进行浸渗处理。
浸渗处理是将树脂真空加热后注入到产品的微孑谜行修整处理,处理完成后再进行气密性测试,测试合格转运至半精机加工区。
应用在线检测系统可以对有泄漏产品已完成工序的过程参数统计分析,实时反馈到集成平台,自动调整相关工艺参数的设定值,实时控制后续铸件的铸造过程。
4.5半精加工工部按客户要求进行半精加工。
本车间采用8台加工中心,其中每4台组成自动生产单元,由机器人进行工件的装夹和转建筑与结构设计Architectural and Slructurnl Design 运。
由AGV进行物料运送。
机加工设备采用DNC系统完成设备的联网、加工状态的监控、NC加工数据的传输、工时计算等,并在智能集成平台的集中监控下进行。
4.6终检工部产品的最终检验,包括关键尺寸、金相组织、机械性能检测。
完成半精机加工的铸件,经抽样转运至中心实验室进行检测,中心实验室配有三坐标测量仪、拉力机、硬度计、光谱仪、快速金相分析仪和X光机等检测设备,采用样品编码识别标记检验结果,并在线传输检验结果到数字化集成平台。
检验完成的对应批次铸件经扫描一维ID码后,即由数字化集成平台自动生成整个铸造过程工艺参数的二维成品码,并进行二维码激光雕刻。