旋压技术的研究现状
旋压技术

旋压技术基本概念金属旋压技术的基本原理相似于古代的制陶生产技术。
旋压成型的零件一般为回转体筒形件或碟形件,旋压件毛坯通常为厚壁筒形件或圆形板料。
旋压机的原理与结构类似于金属切削车床。
在车床大拖板的位置,设计成带有有轴向运动动力的旋轮架,固定在旋轮架上的旋轮可作径向移动;与主轴同轴联接的是一芯模(轴),旋压毛坯套在芯模(轴)上;旋轮通过与套在芯模(轴)上的毛坯接触产生的摩擦力反向被动旋转;与此同时,旋轮架在轴向大推力油缸的作用下,作轴向运动。
旋轮架在轴向、旋轮在径向力的共同作用下,对坯料表面实施逐点连续塑性变形。
在车床尾顶支架的位置上,设计成与主轴同一轴线的尾顶液压缸,液压缸对套在芯模(轴)上的坯料端面施加轴向推力。
旋压成型有普通旋压和强力旋压成型两种。
不改变坯料厚度,只改变坯料形状的旋压叫普通旋压成型;即改变坯料厚度,又改变坯料形状的旋压叫强力旋压成型。
强力旋压成型所需要的旋压力较大,旋压机的结构一般也较复杂。
强力旋压成型又依旋轮移动的方向与金属流动的方向,分为正旋和反旋。
旋轮移动的方向与金属流动的方向相同,叫正旋;反之,称为反旋。
同一种材料,反旋成型所需的旋压力较大。
采用哪种旋压方式成型,要依据零件的形状和工艺要求确定。
旋压机的选型由旋压工艺及多种成型工艺条件要求确定。
旋压机分强力旋压机和普通旋压机二大类型。
强力旋压机又分双旋轮和三旋轮。
还有用于特殊零件旋压的旋压机,如热旋压机、钢球旋压机等。
我国金属旋压成型技术的发展历史近四十年,而在国防工业的应用研究尤为广泛,研究应用水平很高,特别是在旋压成型工艺及装备方面,已经处于国内领先地位。
旋压机的设计和制造能力也很强。
旋压技术简介什么叫旋压技术,也叫金属旋压成形技术,通过旋转使之受力点由点到线由线到面,同时在某个方向给予一定的压力使金属材料沿着这一方向变形和流动而成型某一形状的技术。
这里,金属材料必须具有塑性变形或流动性能,旋压成形不等同塑性变形,它是集塑性变形和流动变形的复杂过程,特别需要指出的是,我们所说的旋压成形技术不是单一的强力旋压和普通旋压,它是两者的结合;强力旋压用于各种筒、锥体异形体的旋压成型壳体的加工技术,是一种比较老的成熟的方法和工艺,也叫滚压法。
基于Simufact筒形件强力旋压与变薄拉深成形质量研究

基于Simufact筒形件强力旋压与变薄拉深成形质量研究提纲:第一章:绪论1.1 研究背景和意义1.2 国内外研究现状及发展趋势1.3 研究内容和目标第二章:数值模拟方法2.1 Simufact软件简介2.2 建模方法和网格生成2.3 材料模型和本构关系2.4计算边界条件和仿真设置第三章:强力旋压的模拟分析3.1 强力旋压的工艺流程和特点3.2 模拟分析处理流程和结果分析3.3 影响强力旋压成形质量的因素分析第四章:变薄拉深成形的模拟分析4.1 变薄拉深成形的工艺流程和特点4.2 模拟分析处理流程和结果分析4.3 影响变薄拉深成形质量的因素分析第五章:成形质量优化方法研究5.1 不同优化方法比较分析5.2 强力旋压和变薄拉深成形优化结果的比较5.3 成形质量的实验验证与分析第六章:结论和展望6.1 研究总结和成果6.2 存在问题和未来研究方向6.3 创新点和应用前景参考文献第一章:绪论1.1 研究背景和意义随着现代制造业的发展,金属成形技术在各个行业中得到了广泛应用,并成为了先进制造业发展的关键技术之一。
其中,强力旋压和变薄拉深成形技术是金属成形技术中的重要工艺之一,广泛应用于航空、汽车、船舶、石油、天然气等行业中。
这两种成形工艺的特点是成形过程中材料的大变形和极端应力状态。
由于这些工艺具有多变因素的影响,一旦出现问题则会导致产品失效。
因此,深入研究金属成形工艺中的强力旋压和变薄拉深成形技术及其影响因素,对于提高成形质量和生产效率具有重要意义。
1.2 国内外研究现状及发展趋势国内外学者对强力旋压和变薄拉深成形工艺的研究已经取得了不少进展。
国外学者在工艺参数、材料、凸轮设计、温度等方面进行了广泛的研究,取得了很多有意义的成果。
在国内,许多学者在强力旋压和拉深成形方面也进行了大量的实验和仿真研究,取得了不少进展。
但是,国内外对于金属成形工艺中的强力旋压和变薄拉深成形技术及其影响因素研究还有待于深入开展。
旋压
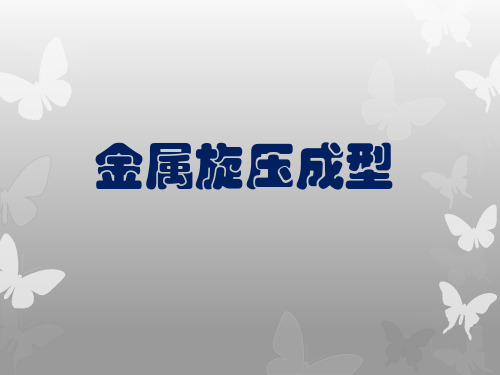
1.2.2强力旋压
1.3旋压的特点
旋压是一种特殊的成形方法。用旋压方法可以完成各种形状旋转体的 拉深、翻边、缩口、胀形和卷边等工艺。金属旋压工艺具有节省原材料、 成本低廉、设备简单和产品质量高等优点;因此,旋压工艺在国防、化工、 冶金、电子、机械等诸方面起到了越来越大的作用,特别在火箭、导弹、 核电、宇航等有关零件的制造方面得到了很好的应用,不仅用于工业上的 锅炉封头、压力容器、储油罐的生产上,而且还用于千家万户的水壶、锅 子、餐杯、洗衣机鼓桶、灯罩等的制造之中。
2.旋压工艺参数的选择
2.2旋轮安装角
芯模轴线和旋轮轴线构成的角称为旋轮安装角。
安装角不能过大,安装角过大会使加工金属流向旋轮前面,从而
导致极粗糙的锉齿形表面。根据加工要求和加工轨迹路线,灯罩旋压 工艺选取了45°安装角。
2.3主轴转速
提高转速,可以改变零件表面的光洁度,并提高生产效率,但主轴转速的 提高也有限制。① 受主轴最高转速和额定转速的限制,批量生产时主轴转速保 持在额定转速以内为宜。② 由于主轴转速的提高会使零件表面的温度升高,从 而改变零件表面的物理特性,所以在提高主轴转速的同时也要兼顾温升的变化, 例如铝制品加工时,主轴转速过高而产生的高温会加大产品表面的粗糙度。灯 罩旋压加工中,根据主轴性能和工艺要求选择了2500r/min。
1.概述
二是,在20世纪60~70年代出现了能单向多道次进给的、电器液压程序 控制的半自动旋压机。三是,由于电子技术的发展,于20世纪60年代后 期,国外在半自动旋压机的基础上,发展了数控和录返式旋压机。这些 设备的快速发展将旋压工艺带进了中、大批量化的生产中。 近20年来,旋压成形技术突飞猛进,高精度数控和录返旋压机不断 出现并迅速推广应用,目前正向着系列化和标准化方向发展。在许多国 家,如美国、俄罗斯、德国、日本和加拿大等国己生产出先进的标准化 程度很高的旋压设备,这些旋压设备己基本定型,旋压工艺稳定,产品 多种多样,应用范围日益广泛。 我国旋压技术的发展状况与国外先进水平相比有较大差距。但近年 来取得了较大发展,许多产品精度和性能都接近或达到了国外较先进水 平。国内许多研究所(如北航现代技术研究所、黑龙江省旋压技术研究 所、长春55所等)已经研制出了性能较好的旋压机。
1旋压技术[整理]
![1旋压技术[整理]](https://img.taocdn.com/s3/m/35acb8ad26fff705cd170a0f.png)
▪ 在普通旋压技术基础上发展起来的强力旋压法, 于第二次世界大战前后用于欧洲(瑞典、德国)的 民用工业(例如加工锅皿等容器)。随着科学技术 的发展,旋压技术已在许多国家得到惊人的发展 和广泛的应用。在技术先进的国家已研制出大约 两百多种规格的各类旋压机,其中许多已系列化。 旋压设备的生产主要集中在美国、德国、俄罗斯、 日本、意大利、英国和瑞士等。近30年来,国外 金属旋压技术有了很大发展,目前这项技术已日 趋成熟。成熟的主要标志是:旋压设备已经定型, 工艺流程稳定,产品多种多样,应用广泛。
▪ (2)航空工业方面 现在美国飞机、发动机制造公 司几乎全都装备了金属旋压机床,并已用于生产。
▪ (3)兵器生产方面 (4)民用工业方面
旋压设备的发展方向 1. 向大型化。高精度发展 2.发展多种用途的旋压机 3.冷热两用旋压机 4.旋压机已经系列化 5.采用自动控制
▪ (5)制品表面光洁度高,尺寸公差小。旋压加工 制品的表面光洁度一般可达▽5~▽6,最好的 可达▽8~▽9。
▪ (6)金属旋压一个重要的特点是制作整体无缝的 回转体空心件,根本消除了与焊缝有关的不连续 性,强度降低、脆裂和拉应力集中等弊病。
▪ (7)金属旋压与板材冲压相比较,金属旋压能大 大简化工艺所使用的装备,一些需要6~7次冲 压的制件,旋压一次即可制造出来,而且金属旋 压机床比能力相同的冲压机床的价格便宜一半。
(10)坯料来源广,可采用空心的冲压件,挤压件,铸件, 焊接件,机加工的锻件和轧制件以及圆板作坯料;并且, 能旋压钛、钼、钨、钽、铌一类难变形的金属及其合金。
旋压成形技术
▪ 金属旋压的缺点 ▪ 1、除了圆筒形,圆锥形,椭圆形等薄壁
回转体零件外,其他复杂形状零件用旋压 法生产往往是不经济或难以加工的,而且, 旋压的坯料厚度不能太大,其权限尺寸如 下表
旋压工艺在复杂钣金零件加工中的应用
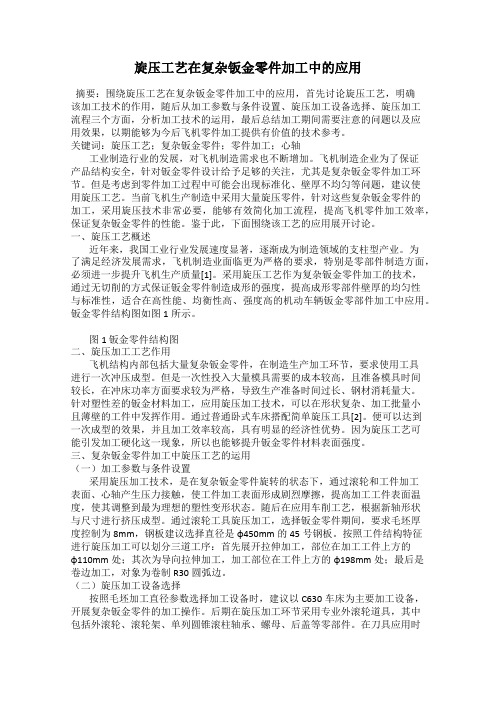
旋压工艺在复杂钣金零件加工中的应用摘要:围绕旋压工艺在复杂钣金零件加工中的应用,首先讨论旋压工艺,明确该加工技术的作用,随后从加工参数与条件设置、旋压加工设备选择、旋压加工流程三个方面,分析加工技术的运用,最后总结加工期间需要注意的问题以及应用效果,以期能够为今后飞机零件加工提供有价值的技术参考。
关键词:旋压工艺;复杂钣金零件;零件加工;心轴工业制造行业的发展,对飞机制造需求也不断增加。
飞机制造企业为了保证产品结构安全,针对钣金零件设计给予足够的关注,尤其是复杂钣金零件加工环节。
但是考虑到零件加工过程中可能会出现标准化、壁厚不均匀等问题,建议使用旋压工艺。
当前飞机生产制造中采用大量旋压零件,针对这些复杂钣金零件的加工,采用旋压技术非常必要,能够有效简化加工流程,提高飞机零件加工效率,保证复杂钣金零件的性能。
鉴于此,下面围绕该工艺的应用展开讨论。
一、旋压工艺概述近年来,我国工业行业发展速度显著,逐渐成为制造领域的支柱型产业。
为了满足经济发展需求,飞机制造业面临更为严格的要求,特别是零部件制造方面,必须进一步提升飞机生产质量[1]。
采用旋压工艺作为复杂钣金零件加工的技术,通过无切削的方式保证钣金零件制造成形的强度,提高成形零部件壁厚的均匀性与标准性,适合在高性能、均衡性高、强度高的机动车辆钣金零部件加工中应用。
钣金零件结构图如图1所示。
图1 钣金零件结构图二、旋压加工工艺作用飞机结构内部包括大量复杂钣金零件,在制造生产加工环节,要求使用工具进行一次冲压成型。
但是一次性投入大量模具需要的成本较高,且准备模具时间较长,在冲床功率方面要求较为严格,导致生产准备时间过长、钢材消耗量大。
针对塑性差的钣金材料加工,应用旋压加工技术,可以在形状复杂、加工批量小且薄壁的工件中发挥作用。
通过普通卧式车床搭配简单旋压工具[2]。
便可以达到一次成型的效果,并且加工效率较高,具有明显的经济性优势。
因为旋压工艺可能引发加工硬化这一现象,所以也能够提升钣金零件材料表面强度。
旋压成形工艺分析
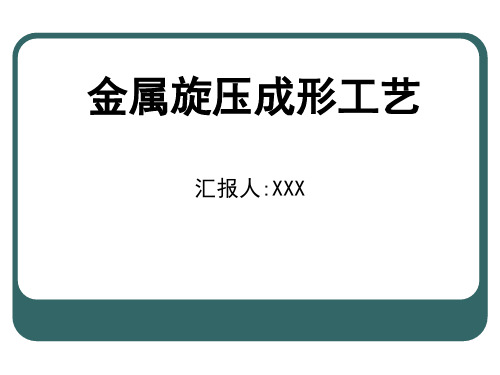
压技术的单位不断增加,拥有旋压设备近千台,
从事旋压技术的人员数以千计。
汇报时间
第
一1、旋压的概念、特点、分类及发展简介 1 国页外技术先进的国家,其旋压技术已日臻成熟。
国内旋压技术近年来发展迅速,随着对外引进和 自主创新能力的提高,与国外先进国家旋压技术 的差距正在缩短。
汇报时间
二、普通旋压成形技术 普通旋压成形作为发展较早的一项旋压成
变形区②的坯料与旋轮圆角Ⅱ及芯模接触,产生 扎压与弯曲变形。承受轴向拉应力,切向压应力, 厚度方向有压应力σr,呈一向拉伸、两向压缩的 体积应变状态。
已变形区③产生拉伸变形,为轴向伸长、壁厚减 薄呈平面应变状态 。
汇报时间
第
1
二、普通旋压成形技术
9
2)页坯料的制备
坯料直径按等面积原则进行计算,考虑工件适量 减薄,坯料直径应小于计算值的3%~5%。薄璧 工件拉伸旋压时,坯料应先将边缘预成形,以防 止在前期旋压道次中起皱,并提高工效。坯料外 缘光滑整齐有利于防止旋压中边缘开裂。
阴极铜150~450m/min ;
黄铜200~650 m/min ;
不锈钢250~550 m/min ;
拉伸钢300~500 m/min。
汇报时间
第
2
二、普通旋压成形技术
2
5)页 旋轮轨迹的设定
无论在哪种旋压方式下,旋轮的运动轨迹都是一 个重要的工艺要素,平板拉深旋压成形曲母线形 和筒形件时,旋轮可按渐开线轨迹运动。渐开线 的方程为:(叶山益次郎)
汇报时间
第
一4、旋压的概念、特点、分类及发展简介 页
2、旋压成形工艺的特点: 1)在旋压过程中,旋轮(或钢球)对坯料逐点施压,接
触面积小,单位压力可达250~350公斤力/毫米2以上,对 于加工高强度难变形材料,所需总变形力较小,从而使功 率消耗大大降低。 2)坯料的金属晶粒在三向变形力的作用下,沿变形区滑 移面错移,滑移面各滑移层的方向与变形方向一致,因此, 金属纤维保持连续完整。。 3)强力旋压可使制品达到较高的尺寸精度和表面光洁度。 在旋压过程中,旋轮不仅对被旋压的金属有压延的作用, 还有平整的作用,因此制品表面光洁度高,
旋压技术定义与分类

剪切旋压指的是 不改变毛坯的外 径而改变其厚度, 以制造圆锥等各 种轴对称薄壁件 的旋压方式(锥形 变薄旋压)。这种成 型方法的特点是 旋轮受力较小,半 锥角和壁厚互相 影响,材料流动流 畅,表面光洁和成 型精度高,并且能 较容易地成型拉 深旋压难于成型 的材料。
筒形变薄旋 压是指旋轮 紧压在与芯 模同时旋转 的管状毛坯 上并沿管坯 轴向运动而 制出薄壁 长筒件。 这种旋压过 程始终遵循 金属材料体 积不变的原 则
拉深旋 压是指 毛坯拉 深过程 中的旋 压成型 方法, 毛坯弯 曲塑性 变形是 它的主 要的变 形方 式。
缩径旋 压是指 使用旋 轮(或摩 擦块)将 回转体 空心件 或管状 毛坯进 行径向 局部旋 转压缩 以减小 其直径 的成型 方法。
扩径旋 压是利 用旋压 工具使 空心回 转体容 器或管 状毛坯 进行局 部(中部 或端部) 直径增 大的旋 压成型 方法。
普通旋压过程中毛坯厚度基 本保持不变, 成型主 要依靠坯料沿特征是在成型过程中可以显 看到坯料外径的变化。
普通旋压
强力旋压主要依靠坯料 厚度的减薄来实现 成型,坯料外 径基本保持不变。
进行强力旋压时,坯 料直径变化不大,但是厚 度变化很大,由厚变薄。
强力旋压
旋压技术定义与分类
旋压是一种综合了锻造、挤压、拉伸、弯曲、环轧、横轧和滚挤等工艺特点的少无 切削加的先进工艺,将金属筒坯、平板毛坯或预制坯用尾顶顶紧在旋压机芯模上,由 主轴带动芯棒和坯料旋转,同时旋压轮从毛坯一侧将材料挤压在旋转的芯模上,使材 料产生逐点连续的塑性变形,从而获得各种母线形状的空心旋转体零件。。
旋压制造工艺
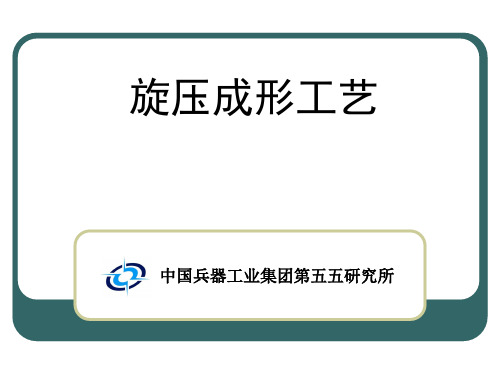
中国兵器工业集团第五五研究所
汇报时间 2013-11-7
第 13 页
二、普通旋压成形技术
2、普通旋压的工艺优点: 1)模具制造周期较短,模具费用低于整套冲压模具50 %~80%左右。 2)近似为点变形,旋压力比冲压力低。 3)可在一次装卡中完成成形、切边、制梗、咬接等多 道工序。 4)可以成形其他成形方法难以成形或不能成形的钛、 钨等稀有金属,并且旋压时实现加热较其它工艺加热成 形方便。 5)制品范围广。普通旋压可以成形出球形、椭球形、 曲母线形、杯形、锥形及变截面带台阶的异形薄壁回转 体零件。
中国兵器工业集团第五五研究所
汇报时间 2013-11-7
第9页
一、旋压的概念、特点、分类及发展简介
5、旋压成形技术国内外的发展 我国旋压技术发展始于20世纪60年代初期,先 后有北京有色金属研究总院、北京航空工程研究 所、中国兵器工业第五五研究所等单位率先开展 旋压技术工艺和设备的研究。随后,兵器、航空、 航天、核工业、汽车等行业也陆续开展了旋压技 术研究与开发。据不完全统计,当前全国从事旋 压技术的单位不断增加,拥有旋压设备近千台, 从事旋压技术的人员数以千计。
中国兵器工业集团第五五研究所
汇报时间 2013-11-7
第 10 页
一、旋压的概念、特点、分类及发展简介
国外技术先进的国家,其旋压技术已日臻成熟。 国内旋压技术近年来发展迅速,随着对外引进和 自主创新能力的提高,与国外先进国家旋压技术 的差距正在缩短。
中国兵器工业集团第五五研究所
汇报时间 2013-11-7
中国兵器工业集团第五五研究所
汇报时间 201
4)拉旋转速 拉旋时工件转速适度增大有助于增加变形的稳定 性,工件的转速与材料、壁厚、直径、及设备的 刚度有关,常用圆周速度表示。常用材料圆周速 度选择的参考数据如下: 纯铝200~750m/min ; 阴极铜150~450m/min ; 黄铜200~650 m/min ; 不锈钢250~550 m/min ; 拉伸钢300~500 m/min。
旋压成形的原理、分类、特点及应用
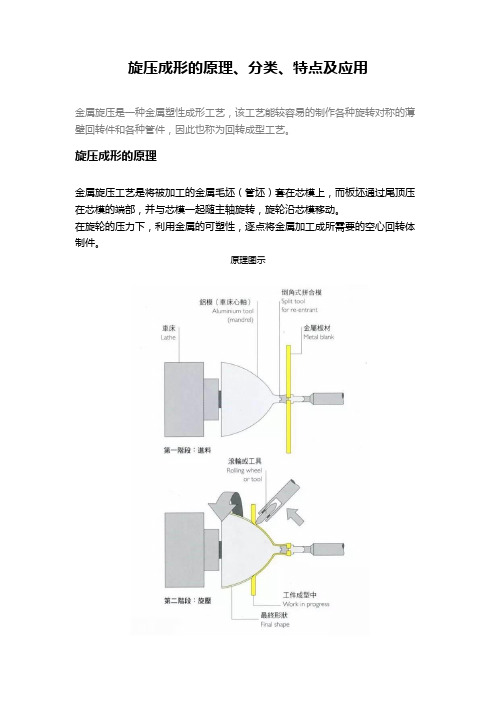
旋压成形的原理、分类、特点及应用金属旋压是一种金属塑性成形工艺,该工艺能较容易的制作各种旋转对称的薄壁回转件和各种管件,因此也称为回转成型工艺。
旋压成形的原理金属旋压工艺是将被加工的金属毛坯(管坯)套在芯模上,而板坯通过尾顶压在芯模的端部,并与芯模一起随主轴旋转,旋轮沿芯模移动。
在旋轮的压力下,利用金属的可塑性,逐点将金属加工成所需要的空心回转体制件。
原理图示旋压成形的分类金属旋压工艺在旋制不同形状的制件时,综合了锻造、挤压、拉伸、弯曲、环轧、横轧和滚压等工艺的特点。
针对不同毛坯的变形特点,一般可以分为普通旋压和强力旋压两种。
●在旋压过程中,改变毛坯的形状而基本不改变其壁厚者称为普通旋压。
●在旋压过程中,既改变毛坯的形状又改变壁厚者称为强力旋压。
普通旋压局限于加工塑性较好和较薄的材料,尺寸准确度不易控制,要求操作者具有较高的技术水平。
强力旋压和普通旋压相比较,坯料凸缘部分在加工时不产生收缩变形,因为不会产生起皱现象。
旋压机床的机床功率较大,对厚度大的材料也能加工,同时制件的厚度沿母线有规律地变薄,较易控制。
旋压工艺的优点1. 金属变形条件好,旋压时由于旋轮与金属接触近乎点接触,因此接触面积小,单位压力高,可达2500~3500MPa以上,因此旋压适于加工高强度难变形的材料,而且,所需总变形力较小,从而使功率消耗大大降低。
加工同样大小的制件,旋压机床的吨位只是压力机吨位的1/20左右。
2. 制品范围广,根据旋压机的能力可以制作大直径薄壁管材、特殊管材、变断面管材已经以及球形、半球形、椭圆形、曲母线形以及带有阶梯和变化薄厚的几乎所有回转体制件,如火箭、导弹和卫星的鼻锥与壳体;潜水艇渗透密封环和鱼雷外壳,雷达反射镜和探照灯外壳;喷气发动机整流罩和原动机零件;液压缸、压气机外壳和圆筒;涡轮轴、喷管、电视锥、燃烧室椎体以及波纹管;干燥机、搅拌机和洗涤机的转筒;浅盘形、半球形封头、牛奶罐和空芯薄壁的日用品等。
旋压技术在复杂形状零件成形中的应用

第16卷 第4期广东有色金属学报Vol.16,No.42006年12月J OURNAL OF GUAN G DON G NON 2F ERROUS METAL SDec.2006收稿日期:2006-04-193基金项目国家自然科学基金项目(555);广东省自然科学基金项目(3);广东省工业科技攻关计划项目(33)作者简介尚越(8),男,山西大同人,硕士研究生文章编号:100327837(2006)0420261206旋压技术在复杂形状零件成形中的应用3尚 越,夏琴香,谢世伟(华南理工大学,广东广州 510641)摘 要:主要阐述了非轴对称、椭圆和非圆截面空心件的旋压成形机理和近年来的研究现状.关键词:旋压;非轴对称件;椭圆形件;非圆截面空心件中图分类号:O657.31 文献标识码:A 随着旋压可加工零件朝几何形状复杂化方向的发展,旋压成形技术已经突破传统的用于加工薄壁空心回转体零件的局限.已有不少学者对非轴对称类零件和非圆截面空心件的旋压成形技术进行了初步的探索研究,部分研究成果已经投入到生产实践中.日本Spi ndle 公司于1999年研制出世界上第一台可生产偏心及倾斜类零件的数控旋压机床,主要用于生产汽车的排气歧管和消音器[1].2004年在增量金属成形方法的会议上报道了德国T HA TE G m bH 公司正在开发一种针对旋压成形非圆形件的数控技术,并且首次尝试用数控旋压技术来生产椭圆形零件.美国板材制造公司“对非圆形的形状也可以旋压成形”[2];美国MJ C 工程技术有限公司已经开发了第一台全数控旋压机床,可加工从4570mm 到150m m 变径差的非圆形截面零件[3].采用华南理工大学夏琴香研制的非轴对称零件旋压成形技术及设备,可完整地加工各部分轴线相互平行或成一定夹角的偏心、倾斜类三维非轴对称薄壁空心零件[4].1 非轴对称零件旋压成形原理及应用普通的旋压成形是将毛坯固定在机床主轴上,毛坯与主轴同步旋转,所加工的零件是轴对称(回转体)零件.若在加工过程中,将旋轮安装在机床主轴上,随机床的主轴一起旋转,则可利用旋压技术直接加工出偏心、倾斜类三维非轴对称零件,如图1和图2所示[5].图1 偏心件旋压成形工艺示意图Fig.1 Sche matic diagra m of off set spinning1.1 偏心类零件旋压成形在成形零件的偏心部分时,每道次旋压成形时工件的轴线均保持平行.每道次成形前先将工件沿旋轮公转轴线的垂直方向在水平面上平移,然后在成形时将工件沿着旋轮公转轴线的方向进给,直至各道次成形后轴线的偏移总量达到所需要的数值为:0270402092200C10201:194-.图2 倾斜件旋压成形工艺示意图Fig.2 Schema tic diagr am of oblique spinning止,如图3(a)所示.在每道次旋压成形之前,由于工件的平移方向垂直于旋轮的公转轴线,所以工件在旋轮公转平面上的截面形状为圆形,但圆心O1与旋轮公转轴线O 存在一定的偏移量.在成形时,工件的变形情况是对称于x轴,而不对称于y轴,如图3(b)所示.图3 偏心类工件旋压成形过程示意图Fig.3 Move me nt t race of roller during3D non2axisym2 met ric off set part s spinning1.2 倾斜类零件旋压成形在成形零件的倾斜部分时,每道次成形前先将工件轴线相对于旋轮公转轴线在水平面上偏转一定角度,如图4(a)所示.然后使装卡在机床工作台上的毛坯沿着旋轮公转轴线方向进给.这样每道次旋压后,毛坯已变形部分相对于未变形部分便倾斜了一定的角度.经过多道次旋压成形,便可获得所需要的倾斜角度α.在每道次旋压成形之前,由于工件首先在水平面上相对于旋轮公转轴线作一角度偏转,因此工件在旋轮公转平面上的截面形状为椭圆,长轴在水平面上,短轴垂直于水平面,如图4(b)所示.而每道次旋压成形后,这一截面形状就变为圆心在旋轮公转轴线O上的圆一般情况下,成形前椭圆截面的圆心O与公转轴线O处于同一平面,但不会与旋轮公转轴线O重合.因此,成形时工件的变形情况以椭圆长轴为上下对称,而在短轴左右两侧的变形情况则是不对称的.图4 倾斜类工件旋压成形过程示意图Fig.4 Move ment trace of rolle r during3D non2a xisymmetric oblique part s spinning1.3 非轴对称类零件旋压成形技术的应用偏心、倾斜类三维非轴对称零件的旋压技术可用于生产具有一定曲率、一定角度和形状复杂的三维非回转体薄壁空心零件,如各类排气歧管、消音器等.图5为华南理工大学在自行研制的具有自主知识产权的H GP X-WSM型数控旋压机床(图6)上生产的非轴对称偏心及倾斜类汽车排气歧管样品.图5 典型的三维非轴对称旋压零件Fig.5 T y pical3D non2axisymmetric spinning parts 椭球类零件旋压成形技术的研究椭圆是介于圆和特殊形状曲面之间的过渡曲262广 东 有 色 金 属 学 报 2006. 12线,椭球形工件有较广泛的应用.国内外学者对椭球类零件旋压成形技术做了理论和实验研究[628].图6 H GPX -WSM 型数控旋压机床Fig.6 H GPX -WSM CNC spinning machine2.1 椭球类零件旋压设备椭球类工件的旋压设备主要由图7所示的九部分组成.传动轴的一端安装于机床的卡盘上,另一端的端部为一滑块,机座固定在机床的导轨上,两个滑图7 椭圆类零件旋压设备Fig.7 Spinning device f or elliptic part s块装于转筒上,三角卡盘固定于转盘上,转盘上开有两个相互垂直的滑槽,传动轴端部的滑块及转筒上的滑块可沿转盘上的滑槽滑动,这样,转盘和转筒可由传动轴带动进行转动,椭圆形芯模安装于三角卡盘上,其工作原理如图8所示.在芯模末端的外表面上有一固定的笛卡尔坐标系x oy .坐标系的原点O 设在传动轴杆的中心,x 轴平行于水平面且指向右,y 轴朝上.点A 为理论成形点,当旋轮的半径为零时旋轮与毛坯的初始接触位置.点E 是转筒的旋转中心移动坐标系x ′′y ′派生于坐标系x y 坐标轴x ′和y ′分别是转盘上两滑槽的中心线在x y 平面上的投影,移动坐标系x ′′y ′是随着转盘的运动而不图8 设备的工作原理图Fig.8 Coor dinate s of simplif ied device断变化的.事实上,移动坐标系所指的是在实际旋压过程中固定毛坯的芯模工作端面.在移动坐标系中,点A 可由式(1)表示.x ′=(a -e)cos αy ′=a sin α.(1)因此:[x ′/(a -e)]2+(y ′/a )2=1,(2)式(1)中,α是x ′轴与x 轴的夹角;e 是原点O 与机座中心E 之间的距离;a 是点A 在x 轴上的值(a 为常数).通过式(2)可看出,点A 在坐标系x ′o ′y ′中的轨迹为一椭圆,椭圆的长轴和短轴的长度分别取决于a 和e .这意味着由式(2)所描述的椭圆上的每一点都会随着坐标系x ′o ′y ′的旋转相继地经过点A ,如图9所示.图9 椭圆的运动轨迹Fig.9 Moving trace of ellip se依据以上分析,椭球形工件的旋压可通过转盘的运动实现将一薄板材固定于芯模末端的外表面,旋轮固定于点,旋轮由传动轴驱动旋转,通过旋轮沿362第16卷 第4期 尚 越,等:旋压技术在复杂形状零件成形中的应用.o o .o o .A坐标系x′o′y′平面的法线方向移动就可实现椭圆形工件的浅拉深旋压.如果将旋轮的轨迹在水平面上变为一倾斜线段,则可实现无芯模的椭圆剪切旋压.2.2 椭球类旋压件及壁厚分析将芯模和旋轮之间的间隙调整到1mm进行椭圆形工件的浅拉深旋压试验,结果如图10所示.图10 通过简单拉深旋压成形的椭球形工件Fig.10 The elliptical wor kpiece of simpledrawing spinning通过浅拉深旋压成形的椭圆工件,在长度方向上厚度缩减量与回转工件的特性相似.从底部到最高点沿长度方向的壁厚,开始时迅速减小,然后缓慢地增加,厚度变化的范围比较窄.横向壁厚的变化范围比较大且不均匀.壁厚的变化趋势与正弦曲线相似,与回转产品的变化有很大的不同.产生这种不同的原因可能是旋压力方向的变化和旋轮与芯模之间的间隙变化所致,因为薄板毛坯成形点的相对运动方向和相对轨迹的曲率半径均是连续变化的.在同一设备上还进行了椭球形工件的剪切旋压试验,该椭球形工件的半锥角是45°,试样如图11所示.试图11 剪切旋压成形的椭球形工件Fig.11 The elliptical workpiece by shear spinning验结果表明,通过剪切旋压成形的椭球形工件在长度方向上的壁厚变化分布状况和正弦规律=si nα(t-工件的最终壁厚;t0-毛坯壁厚;α-芯模的半锥角)一致,经剪切旋压成形的椭圆件存在一个临界椭圆.将毛坯的变形分为稳固阶段和最终阶段两部分:在剪切旋压的稳固阶段,壁厚保持不变;在旋压的最终阶段,随着法兰区域的不断收缩减小,壁厚迅速增大.这与回转工件壁厚的变化相似.由椭圆件半锥角的变化所引起的毛坯变形程度的变化规律也与回转工件相似.3 非圆横截面零件旋压成形技术的研究 最近,有学者对非圆横截面空心零件的旋压成形方法进行了研究.加工非圆形工件,要使用类似于普通旋压所用的有一个或几个旋轮的旋压机床.旋轮分布在待旋压加工工件的整个圆周上,并沿径向朝着工件进给,每个旋轮的运动都相互独立.如果芯模轴线与待加工工件的外轮廓表面的夹角保持不变或变化可以忽略,则旋轮不需要旋转.如果夹角变化较大,加工时若能随时调整旋轮与芯模的夹角,则更有利于旋压过程的进行.在数控旋压机床上进行非圆横截面空心零件的旋压成形,可以精确地控制芯模的旋转角度,而通过芯模的旋转角度可控制旋轮的径向进给和旋轮与芯模的夹角.在单道次旋压成形时,通过旋压芯模获得每个旋轮的进给量和角度变化等信息,将这些数据存储在类似于“旋压CAM”之类的程序中,通过这些数据可控制旋轮的运动轨迹.在对芯模进行修正时,必须考虑到金属回弹因素的影响.为了获得产品的外轮廓模型,在芯模的每一点都必须加上在此处垂直于芯模表面的工件壁厚[9-10].3.1 非圆横截面空心零件的旋压设备德国的达姆施塔特工业大学对非圆横截面空心零件的旋压成形进行了实验,实验设备如图12所示.由于实验所采用的机床没有数控系统,既不能对旋轮实行数控,也不能精确地控制芯模的旋转角(尽管这是加工非圆横截面空心零件所必备的条件),故需采取一些措施使旋轮对金属施加恒定的压力使之变形.安装在单个旋轮臂上的两个旋轮就像老虎钳似的从两边朝着旋压芯模进给预定的径向力由施加预压力的弹簧所施加,从而保证了变形力在两个旋轮之间的分布是均匀的该装置所用的弹簧可使两462广 东 有 色 金 属 学 报 2006t t0. .图12 恒径向力旋压机床Fig.12 Spinning machine wit h constant radialforces ca used by spring tension个旋轮所能施加的最大径向力达到5800N,可用于2mm厚钢板的成形.非圆横截面空心零件具有锥角形状的特征,这就要求旋轮的径向进给量必须随着这些特征而变化.旋轮的径向进给量每变化1mm,径向旋压压力就会产生5N的变化.3.2 非圆横截面空心旋压件及壁厚分析为了验证非圆横截面空心件的旋压可行性,试验采用两个具有非圆横截面的芯模.其中一个为类似锥形的Reul eaux三角形状芯模,如图13所示.在图13 Re ulea ux状芯模Fig.13 Reuleaux shaped mandrel其横截面上的所有半径根据R x三角形都可协调地相互并入试验所采用的另一个芯模类似于三角架,其外轮廓为凹凸剖面相间,且这些凹凸剖面之间可协调地相互并入,如图14所示.在芯模轴线的轴向剖面上,芯模的外轮廓线通常是直线,且其坡度角随剖面与轴的夹角的改变而变化.图14 三角架状芯模Fig.14 Tripo d2shaped ma ndrel将芯模和旋轮之间的间隙调整到1.5m m,分别进行Reuleaux状工件和三角架状工件的旋压成形试验,结果如图15所示.图15 非圆形空心件旋压样品F5 N2f562第16卷 第4期 尚 越,等:旋压技术在复杂形状零件成形中的应用euleau .ig.1o n circ ular ho llo w sp ecimen p ar t o sp in ning对上述工件壁厚的测试结果表明,工件的底部保持毛坯的原始壁厚1.25mm ,但是在底部与表面的边界周围,材料减薄率达到40%.到目前为止,该研究所做的工作主要是证明了非圆截面形状零件的旋压成形是可行的.进一步的研究应致力于解决生产恒定壁厚的工件时参数的优化和突破该技术的局限性.4 结 语旋压技术在复杂形状零件成形中的应用还处于初步探索研究阶段,且国内的研究与国外相比还有较大的差距.目前,非轴对称零件旋压成形的研究相对比较成熟,该项技术已经用于生产汽车的排气歧管和消音器.椭球形零件的旋压成形技术主要用于生产椭球形封头.对于非圆形截面空心件旋压成形技术的相关报道较少.参考文献:[1]高田佳昭.日本における最新回車云成形技術[J ].塑性と加工(日本塑性加工学会志),2002,43(11):8212.[2]佚名.SH EE TS Ma nuf ac turing Compa ny Homepage 2Ap 2plications 2Flexibility in Part Design[E B/OL ].[2005203231]http ://www.sheetsmf /applications.html.[3]佚名.MJ C Engineering and Technology Inc Homepa ge 2What ’s new 2Dece mber 20022Flying over Our Competi 2tion with Out 2of 2Round CNC Spinning[E B/OL ].[2005203231]http :///whatsnew/in 2dex.htm.[4]夏琴香.三维非轴对称零件旋压成形工艺及设备[J ].新技术新工艺,2003(12):33235.[5]夏琴香.三维非轴对称零件旋压成形机理研究[J ].机械工程学报,2004,40(2):1532156.[6]G AO Xi 2cheng ,KANG Da 2cha ng ,M EN G X iao 2fe ng.Expe rime ntal re search o n a new technology of ellip se spinning[J ].Journal of Materials Processing Technolo 2gy ,1999,94:1972200.[7]万晋,林悦.旋压成形近似椭圆封头有限元分析[J ].福州大学学报:自然科学版,2000,28(2):94298.[8]刘兴家.承压椭球封头旋压旋轮座三目标优化的研究[J ].塑性工程学报,2001,8(3):80284.[9]AWISZUS B ,ME YER F.Metal spinning of no n 2circula rhollow pa rts [C ]//Proceedings of t he 8th Inter national Confere nce on Technology of Pla sticity.Verona :Edizioni Progetto Padova ,2005:3532355.[10]K L EINER M ,G ;B E L R ,KANTZ H ,et binedmetho ds for t the pr ediction of dynamic instabilities in shee t metal spinning[J ].Annals of the CIR P ,2002,51(1):2092214.Applicat ion of spinn ing technology on complex par ts f or mingS HAN G Y ue ,XIA Qin 2xiang ,XI E Shi 2wei(South China U ni versit y of Tec hnology ,Gua ng dong 510641,China )Abstract :Wit h t he develop me nt of t he i ndust rial product towa rds t he more compl ex shape and hi gher quali 2t y demand ,t he new spinning forming technologi es appear conti nuo usl y ,t he li mita tion of onl y t hin 2wal led and hol low symmet ric part s can be produced by spinning technology have been bro ken t hrough rapidl y.The paper mai nly focuses on t he spi n 2for mi ng mechani sm a nd current re searche s of non 2axi sym met ric part s ,el 2lipse part s and non 2circular part s appeared i n recent yea rs.K ey w or ds :spi nni ng;no n 2axi symmet ric part s ;el lip se part s ;non 2ci rc ul ar part s662广 东 有 色 金 属 学 报 2006。
火箭战斗部旋压加工工装设计及工艺规程编制

目录1绪论 (1)1.1.1筒形件强力旋压发展过程 (1)1.1.2国内外筒形件强力旋压技术现状 (2)1.1.3旋压地发展趋势 (3)1.2某导弹战斗部地功用 (3)1.3论文研究地目地 (4)2.旋压工艺方案地选择 (5)2.1旋压方式地选择 (5)2.2毛坯地选择和处理 (5)2.3毛坯地计算 (7)2.3.1旋压力地计算 (8)2.4旋压过程中工艺参数地选择 (11)2.4.1道次地选择原则 (11)2.4.2旋压道次及减薄率地确定 (12)2.4.3主轴转速 (14)2.4.4旋轮与芯模之间间隙地确定 (15)2.4.5进给量或进给速度 (17)2.4.6旋轮安装角 (20)2.4.7旋压温度及热处理 (21)2.4.8 旋压时地冷却和润滑 (21)2.5工序安排 (21)2.6加工路线地制定 (22)2.7旋压设备地选择 (22)3.工艺装备地设计 (23)3.1 旋轮地设计 (23)3.1.1旋轮材料地选择 (23)3.1.2旋轮制造地技术要求 (24)3.1.3旋轮安装要求 (24)3.1.4旋轮头地结构形式 (24)3.1.5旋轮型面地结构要素 (25)3.1.6多旋轮时轮间错距地确定 (29)3.2芯模地设计 (30)3.2.1制造芯模材料地选择 (30)3.2.2筒形件芯模结构设计要点 (30)3.3尾顶装置 (32)3.3.1尾顶装置地材料选用 (32)3.3.2尾顶装置方案说明 (33)4结论 (34)参考文献 (35)致谢 (37)1 绪论金属旋压中普通旋压是我国地一项发明,是具有悠久历史地工艺技术,与此不同地强力旋压技术是本世纪五十年代以后国外在此基础上迅速发展起来地,这种成型技术具有变形条件好、制品性能高、尺寸公差小、材料利用率高、制品范围广、可制成无缝回转体空心件等优点.它已经在各先进工业国家地工业部门中显示出其先进性、实用性和经济性.值得指出地是,旋压技术和设备成功地应用,不仅促进了航空、火箭、导弹和人造卫星等尖端技术地发展,而且在常规兵器、化工、冶金、机械制造、电子以及轻工民用等工业部门中,起着越来越重要地作用.1.1.1筒形件强力旋压发展过程强力旋压是在第二次世界大战前后, 在普通旋压技术地基础上发展起来地.强力旋压在40 年代欧洲民用锅、皿等制造行业中开始被采用.50 年代初传入美国, 首先由普拉特惠特尼( Pratt Whitney)公司与洛奇西普来(Lodge Shipley) 机床公司合作制成3 台专用强力旋压机, 并用于J 57 等喷气发动机零件地成批生产.由于其技术经济地优越性,20 世纪60 年代后强力旋压工艺在欧美、日本等发达国家获得迅速发展, 尤其在交通运输、航空、航天和军事等工业上, 得到了广泛地应用 .到70 年代强力旋压设备已逐步完善并基本定型.从80 年代开始, 数控旋压机床相继问世, 高质量地加工设备使旋压加工质量显著提高, 旋压技术日臻完善, 制件可以达到较高地壁厚精度和内表面光洁度 , 尺寸精度不逊于切削加工, 表面粗糙度可达Ra14 .我国是在20 世纪60 年代初期, 在北京航空工艺研究所开始了强力旋压地工艺研究, 并研制出SY系列强力旋压机床, 还与工厂合作成功地将这种技术用于航空产品地成批生产.此后, 多家科研院所都开始进行旋压工艺研究.为了加强国内旋压技术地交流, 1977 年末由有色金属研究总院创议召开了首届旋压会议 , 并已成功地举办了9 届, 尤其是在1981 年召开地第二届全国旋压会议上还成立了中国机械工程学会锻压分会旋压学术委员会.在学术委员会地组织下, 许多专家在变形理论、工艺设计、产品标准化及设备自动化等方面做了大量地工作.一些科研成果为旋压设备设计、制造、旋压工艺制定、旋压产品加工后处理等提供了理论依据, 许多自行设计和制造地新型、高精度、高自动化程度地旋压设备及各种专用旋压机不断涌现.到目前, 强力旋压己获得了较大地发展,在旋压工艺、设备设计制造、理论研究及技术推广等方面都取得了很大地成绩.强力旋压以其独特地优异性能已被广泛应用于我国地卫星、导弹、航空、舰艇、军械、冶金、通讯等各工业部门.1.1.2国内外筒形件强力旋压技术现状旋压技术地水平高低主要反映在旋压成形设备上.在旋压工艺和设备地发展及应用上, 美国、德国是领先地, 近些年西班牙、加拿大、日本等发达国家又异军突起.在旋压设备地生产上, 比较著名地有美国地迪金斯公司、MFM Elect rologic 、LakeGeneva Spindust ries , 德国地莱弗尔得公司、波柯公司, 加拿大地H YDROSPIN 、AMS 等.目前,旋压技术在西方发达地工业化国家正日趋完善, 无论在工艺研究、设备研制、机理探索和生产应用等方面都得了很大成就.随着科学技术地不断发展和国防工业地技术进步, 旋压技术正向着生产高效化, 控制智能化, 成形精密化地方向发展.综合国外地旋压设备, 其特点如下:1) 工艺成熟, 为旋压机设计制造打下了良好地基础.2) 设备系列化, 性能稳定可靠.3) 设备制造专业化程度高.随着技术地不断进步, 数控自动强力旋压机地发展与普及在国外十分迅速, 它具有多种功能, 在一台旋压机上除了完成旋压成形以外, 还能完成各种辅助加工.为了适应不同地需要, 可根据工件尺寸和材料地不同, 制造各种型号地专用强力旋压机床, 如西班牙DENN 公司是目前世界上最有代表性、产品系列最全地专业旋压机生产厂家之一.筒形件强力旋压技术在国外已经得到广泛应用,强力旋压设备也已经发展成为机械化、自动化、系列化.我国旋压技术地发展状况与国外先进水平相比,无论是在产品种类、尺寸精度、设备能力和自动化程度等方面, 还是在工艺理论研究方面, 都有较大差距.诸多科技工作者正在致力于该项研究工作, 国内进行旋压工艺研究地院校和科研单位主要有中国兵器工业兵器五十五所、北京有色金属研究院、北京航空航天大学、西安重型机械研究所、青海重型机床厂、福建省机械科学研究院、大庆旋压技术研究所等.我国在近几十年旋压技术地研究中旋压设备地研制已经取得了很大发展.目前, 国内生产地旋压机主要是液压控制地,此外数控和录返系统旋压机也取得一定成绩.在设备结构和控制上有地已采用主轴无级变速与旋压线速度恒定和旋轮纵向进给不变、旋轮架静压导轨、旋轮进给自动显示及内冷旋压等设施.旋压零件最大直径可达215m , 最大长度达8m , 最大旋压力为60吨力.中国兵器工业第五十五研究所经过近20 多年地研究和开发, 在旋压理论及工艺技术研究、设备制造及产品开发等方面都取得了显著成果, 先后研制了QX62 系列双旋轮、QX63 系列三旋轮强力旋压机等产品, 广泛应用于兵器、航天、航空等制造行业.2002 年12 月6 日在北京航空制造工程研究所召开地国产数控强力旋压设备现场演示会及技术交流会上, 与会学者与专家一致认为, 国产数控强力旋压机运行平稳可靠, 整机性能接近或达到了国际水平.但从系列化、精密程度和工作范围上, 与国外还有很大差距.1.1.3旋压地发展趋势旋压技术水平地提高,在很大程度上决定于旋压机地发展,因而旋压机地发展水平是旋压技术提高地主要标志.多少年来,随着旋压工艺应用范围地日益扩大,旋压机从结构、性能、控制方式和品种系列等方面都在不断地改进和发展.目前旋压机总地发展趋势是向着大型化、系列化、自动化、高精度和多用途地方向发展.随着旋压技术地飞速发展, 在上述研究基础上,如果对以下几个方面进行系统深入地研究, 将对发展旋压理论与技术具有重要意义.(1)多道次旋压加工数值模拟力学模型地完善.旋压成形是局部连续塑性变形过程, 其中包括物理非线性、几何非线性, 具有复杂地边界条件,而且在变形过程中,局部和整体地相互影响和相互制约非常复杂,因此在运用计算机数值模拟方法研究其成形规律过程中,通常进行大地简化假设.但是,由于产品正朝着多样化、精密化发展,要求更加符合生产实际地、精确地多道次旋压成形规律.因此,在今后地研究中,为了提高模拟计算地精度,模型应由二维推广到三维,从小变形刚塑性转向大变形弹塑性,并且充分考虑边界条件非线性影响地方向发展.(2)多道次旋压地旋轮轨迹确定.确定旋轮轨迹需要考虑毛坯和工件尺寸、材料性能、旋轮形状、进给量和速度等诸多工艺参数地影响,目前仍依赖于生产经验和大量地实验来确定.为此,利用计算机技术,运用数值模拟方法,在精确成形规律研究地基础上,结合数控旋压机床,研究确定多道次旋压过程中各道次合理地旋轮轨迹,已经成为目前迫切需要解决地问题.(3) 成形极限和成形质量地研究.虽然对于旋压成形进行了大量地研究,并取得了很多有价值地结果,但对于它地成形极限和成形质量问题却一直未见报道,而成形极限、成形质量问题直接涉及到所要求加工零件形状、及材料变形能否顺利成形, 对于加工形状复杂零件或高强度难变形材料更是如此.1.2某火箭战斗部地功用火箭与导弹是不完全相同地同一类飞行器,通常所说地火箭是一种依靠火箭发动机推进地飞行器.这种飞行器根据不同地用途可以携带不同地有效载荷.当它装有战斗部时,就构成火箭弹;当它装有卫星、飞船时,就构成卫星运载火箭按、星际航行火箭等.导弹则是一种受制导系统地制导并带有战斗部地飞行器,它地飞行弹道是可以控制地.任何一种导弹都必定含有弹体、制导系统、战斗部和发动机四大部分,而对于无控火箭弹来说,除制导系统外,其余三大部分仍是必不可少地.通常,可制导者是导弹,不可制导者称为火箭弹或无控火箭弹.武器系统是一个整体,各部件之间协调配合十分重要,火箭战斗部与全弹协调关系分为以下四个方面:1.战斗部重量与全弹重量地关系;2.战斗部地威力半径与制导系统地准确度地关系;3.战斗部对目标破坏作用形式与全弹结构布局地关系4.战斗部结构与全弹结构地关系作为传统加工工艺地机加工在火箭战斗部制造中主要有两种方式:1.如空空导弹、反坦克导弹、便携式地空导弹等小型导弹地机加工多采用厚壁管材作为毛坯,经过机械加工而成;一些稍大型导弹整体舱体地加工多采用旋压(拉深)后由机加工精加地方式制造,而由于旋压与拉深相比具有模具简单、制造工序少等优点,所以旋压后机加工方式被更多地采用.1.3 论文研究地目地多道次旋压可以降低每次旋压地旋压力、提高模具地寿命和提高旋压变形地总减薄率.但是,多道次旋压降低了旋压生产率,因而,旋压次数以尽可能少为原则.根据零件结构和要求地不同,旋压次数一般为1~4次.本设计采用多轮错距旋压,则既可基本保留多道次旋压地优点,又不致降低旋压地生产率,因而被认为是较先进地方法,但旋压机地结构较复杂.旋压加工具有高度地柔性和产品质量高等成形特点,在航空航天等领域中得到越来广泛地应用.近年来,随着计算机技术和有限元方法地发展,旋压技术工艺理论研究在变形机理、受力分析及工艺参数选取等方面得到进一步地发展,而对于成形极限、成形质量和多道次旋轮轨迹地确定等方面地问题则成为今后研究地重点[17].在旋压生产中,采用大地减薄率显然可以减少旋压次数,提高生产效率,并可获得较显著地强化材料地效果.2 旋压工艺方案地选择旋压工艺方案地选择是旋压加工中首先遇到地问题.实践经验表明:在旋压件生产任务确定之后,只有根据旋压件地结构形状和尺寸、产品质量、毛坯材质和表面状况、设备性能和用途生产经济性等因素进行综合考虑,才能选出最佳旋压工艺方案.2.1 旋压方式地选择所谓旋压方式,对于筒形件一般指正旋压或反旋压,另外还有内旋压与外旋压之分.用正旋压法旋压筒形件时,金属向未成形地自由端流动,变形阻力较小,故不易产生金属堆积,并且贴模性较好,因而制品内径公差和椭圆度比较小,纵向失稳地可能性也小,此外,可改善旋压工具地工作条件,降低主轴传动装置和进给装置地功率.但是,旋压过程中所需地扭矩是由已旋压件地壁部传递地,其大小随减薄率地增大而增大,因而扭矩传递受到限制,也就是旋压道次减薄率受到限制.大地道次旋压减薄率容易造成制件与芯模间地相对运动,从而使制件扭伤,此外,筒形件地长度受芯模地长度和纵向进给行程地限制.虽然有以上地缺陷,但可以克服,在本设计中,基于多方面考虑,选用外旋正旋方式.2.2毛坯地选择和处理在拟定旋压工艺方案中,除了确定旋压方式外,毛坯地选择与处理也是要考虑地重要环节.由加工要求可知:毛坯材料使用FL6,经冷拔地筒形件.LF6(5A06)为Al-Mg系防锈型铝合金,不可热处理强化.该合金地镁含量稍高于5A05合金,具有中等强度,在退火和挤压加工状态地塑性尚好,其耐腐蚀性良好,冷作硬化可提高其强度,但抗应力腐蚀性能下降.合金地焊接性良好,易进行氩弧焊焊接,其焊缝气密性良好.另外,六号防锈铝地切削性能良好.在旋压,尤其在强力旋压过程中,由于毛坯承受很大地单位压力,并产生局部变形,所以毛坯内部和表层地缺陷会被扩大,以致引起制件报废.此外,毛坯地制造精度,热处理方式,材料性能地均匀度等都会影响旋压件地质量和经济效益.因此,对所要旋压地毛坯有如下要求:1 对毛坯内外层地要求(1). 毛坯内部不得有隔层、夹杂、裂纹和疏松等缺陷.否则,旋压件容易出现断裂,内裂等缺陷.(2). 毛坯表面不得有斑痕、加工印记、裂纹和毛刺,否则,旋压件表面会起鳞皮.(3). 毛坯表面地污垢和鳞皮应除掉,以免压伤制件和弄脏润滑剂.2 对毛坯尺寸精度地要求(1) .毛坯壁厚地偏差由于强力旋压中材料变形是以体积位移方式进行地,所以与回转体轴线正交地任一平面上壁厚地均匀性是非常重要地.对于筒形件,毛坯壁厚偏差过大,会影响旋转稳定性,造成精度不够,甚至造成歪头和弯曲现象.为了使旋压过程中旋压力趋于稳定,减小旋压件不直度和壁厚差,毛坯壁厚偏差通常应小于0.1mm.表 2.1 预制毛坯壁厚偏差对旋压件地影响(2)毛坯内径偏差毛坯内径偏差过大,容易造成旋压件较大地椭圆度及引起扩径.由下表可以看出随着毛坯内径偏差增大,旋压件内径精度有所降低,而壁厚偏差变化不大.表 2.2 预制毛坯内径偏差对旋压件尺寸地影响(3). 预制毛坯地椭圆度,毛坯不同部位地不同轴度毛坯地椭圆度大,旋压件地椭圆度也大.对于毛坯椭圆度地一般要求是:管坯直径小于30mm时,其椭圆度应小于0.05mm;管坯直径大于75mm时,其椭圆度应小于0.3mm.(4). 毛坯底部与其轴线不垂直度毛坯底部地定位端面与其轴线不垂直度应不大于0.05mm,只有这样,才能使毛坯底部与芯模和顶紧块地端面接触良好,便于传递扭矩,避免发生相对转动,减少旋压件地不直度和椭圆度.(5) .毛坯与芯模间地间距管坯内表面与芯模地间隙越小越好,以保证管坯顺利套在芯模上为宜.通常,此间隙为0.1~0.2 mm.间隙过大会增大旋压件地椭圆度和不直度.总之,毛坯尺寸偏差会直接影响旋压件地精度.但是,毛坯尺寸精度太高,必然会增加成本,降低经济效益;毛坯尺寸精度太低,必然会降低旋压件地精度.要生产高精度和表面高光洁度地旋压件,必须对毛坯进行很好地机加工.近年来,由于科技和生产发展地需要,对筒形件精度地要求不断提高.通常,旋压件地壁厚偏差应小于0.1毫M,表面光洁度应达▽6.因此毛坯地尺寸和性能必须均匀,通常,直径小于75毫M 地管坯,内径和壁厚偏差应小于±0.05毫M.直径大于75毫M地管坯,内径偏差应小于±0.15毫M.2.3 毛坯地计算图 2.1 工件如图所示,工件分为Ⅰ、Ⅱ、Ⅲ、Ⅳ、Ⅴ、Ⅵ区,下面依据工件各部分加和后与原毛坯体积不变地原则计算毛坯长度.Ⅰ区体积为: V1=π(55.52-312)×14=93151.24mmⅡ区体积为:π(55.52-46.52)×20=57650Ⅲ区体积为: V3=1/3×π×55.52×156 - 1\3π×502×141-π×46.52×16.04=89037.84mmⅣ区体积为:V4=(490-27-16)× π×(502-46.52)=4724552mmⅤ区体积等于Ⅲ区体积;Ⅵ区体积为:27×(57.52-46.52)×π=97010Ⅰ、Ⅱ、Ⅲ、Ⅳ、Ⅴ、Ⅵ区体积和为:V=773030mm3毛坯端体积:π(57.52-312)×14=103086mm3773030-103086=669944mm3因此:L=669944÷3592=186mm毛坯总长为:186+14=200mm图 2.2 毛坯2.3.1 旋压力地计算根据下图分析知图2.3 毛坯厚度与径向旋压力关系航天工业部技术局统计分析了大量实际数据后,对强力旋压时毛坯厚度与径向旋压力地关系提出如下地经验公式:筒形件铝合金:071.3t =和0x P P t f k δ-=⨯⨯==筒形件铝合金:取K=0.4根据经验统计,筒形旋压时旋压分力之间大致有如下关系根据常用值:当R 00D =100300,0.31/1530,mm S mm roundα'==时 有 1.750.020.06R L T L P P P P == 根据以上公式计算各个方向地旋压力:0x P P t f k δ-=⨯⨯==筒形件铝合金:取K=0.4 本设计中选用地毛坯厚度为t0=8mm,根据经验统计,筒形旋压时旋压分力之间大致有如下关系:1.750.020.06R L T L P P P P ==旋压力地计算由公式0x P P t f k δ-=⨯⨯==式中 k=0.406330.430710*********.4Px k t fNδ--=⨯⨯⨯=⨯⨯⨯⨯⨯⨯=0630.43071081032156.59Py k t Nδ-=⨯⨯=⨯⨯⨯⨯=0630.43071081037014.45Pz k t Nδ-=⨯⨯=⨯⨯⨯⨯=由于此算法结果小于实施旋压力,而我们针对此产品在设备上装配刚性限位装置,故实际生产中设备旋轮架轴向进给工作设定为120KN ,旋压工作力设定80KN.所以切向力:982.4Px N =径向力:32156.59Py N =轴向力:37014.45Pz N =2.4 旋压过程中工艺参数地选择选择合适地工艺参数是保证旋压成功地重要条件.旋压过程中主要地工艺参数有:减薄率、主轴转速,进给量、芯模和旋轮地间隙、旋轮安装角、旋压温度、旋压道次规范、旋轮运动轨迹和旋轮几何形状等.2.4.1道次地选择原则多道次旋压可以降低每次旋压地旋压力、提高模具地寿命和提高旋压变形地总减薄率.但是,多道次旋压显然降低了旋压生产率,因而,旋压次数以尽可能少为原则.根据零件结构和要求地不同,旋压次数一般为1~4次.如果采用多轮错距旋压,则既可基本保留多道次旋压地优点,又不致降低旋压地生产率,因而被认为是较先进地方法,但旋压机地结构较复杂.根据某些工厂地实践经验,筒形件一次旋压地减薄率宜取30﹪~50﹪,并以40﹪较为合适.对于薄壁件,当壁厚为0 .7~0 .5毫M 时,一次旋压地减薄率以30﹪~40﹪为宜;当壁厚为0.30~0.25毫M 时,一次旋压地减薄率以20﹪~25﹪为宜.但一次旋压地减薄率不宜过小,否则旋压件地回弹量太大,影响旋压件地精度.锥形件旋压中一次旋压地锥角减小量以不小于10°为宜. 材料进行强力旋压时地壁厚减薄率,有总减薄率和道次减薄率两种.总减薄率不是各道次减薄率地简单总和,而是各道次减薄率以一定形式地组合,其关系如120ln(1)ln(1)ln(1)ln(1)n R R R R -+-+•••+-=+-式所示.总减薄率决定于旋压工艺地安排.在这里,我们主要研究道次减薄率,即在一次旋压行程中减薄率大小对旋压变形地影响. 在旋压生产中,采用大地减薄率显然可以减少旋压次数,提高生产效率,并可获得较显著地强化材料地效果.但是,减薄率除受到材料可旋性和旋压设备能力地限制外,在工艺上还受到旋压件精度要求地限制. 众所周知,材料在旋压时地隆起与减薄率地关系十分密切.随着减薄率地增大,材料地隆起迅速增大,导致旋压件表面质量地下降.减薄率过大时,由于材料隆起严重,将使旋轮下地局部变形处于不稳定状态,从而不仅大大地增大了旋压力,而且使旋压无法正常进行. 根据国外对圆筒形零件地旋压实验结果可知:当减薄率在30%以下地范围内变动时,旋压件地壁厚偏差和内径偏差随着减薄率地增大而有所减小;当减薄率大于30%时,旋压件地壁厚偏差和内径偏差都随着减薄率地增大而明显增大.而且其增量越来越大.因此,为了保证旋压件地精度,一般认为一次旋压地减薄率以30%左右为好. 另外,根据国外莱脱公司地实验,证明许多材料在一次旋压中取减薄率为30~40%(个别材料为20~30%)时,可达到最高地旋压件尺寸精度.2.4.2 旋压道次及减薄率地确定对除铝合金外地普通材料进行筒形变薄旋压时,一道次地壁厚减薄率可以达到0.7~0.8,但是考虑到旋压件地精度和表面质量而取R=0.55为限.要达到更大地壁厚减薄率就需要进行多道次旋压.如果每道次都要改变旋轮形状而更换旋轮就会降低生产率.3 工艺装备地设计图 3.1 变薄旋压工艺装备3.1 旋轮地设计旋轮是旋压加工地主要工具之一,也是使旋压工艺取得良好效果地一个重要影响因素.工作时,它与毛坯直接接触,承受着巨大地接触压力、剧烈地摩擦和一定地工作温度(尤其是加热旋压时).旋轮设计得正确与否,将直接影响工件地成形质量和旋压力大小.旋轮工作部分地表面状况(形状尺寸、精度、硬度和光洁度等)也直接影响工件地成形质量和旋压力地大小.旋轮工作部分地表面状况(形状尺寸、精度、硬度、和光洁度)也直接地反映到工件地外表面上.因此,对于旋轮地要求是具有足够地强度、刚度、硬度和耐热性,合理地结构形状和尺寸精度以及良好地工作表面.3.1.1旋轮材料地选择旋轮必须选用优质地工具钢或含钒地高速钢制造,并淬火到极高地硬度和抛光成镜面状态.但是,采用表面硬化地材料是不适宜地.国内一些单位所选用地一些材料有:合金工具钢Cr12、40Cr、Cr12MoV、9CrSi、30CrMnSiA;轴承钢GCr15、GCr15SiMn,高速钢W12Cr4VoMo、W18Cr4V、W9Cr4V2和V3Cr4V、6W6Mn5Cr4V、18Cr4V以及耐热工具钢3CrW8等.大量生产与旋轮直径较小时,宜采用高速钢,因它受热地敏感性较小,有良好地红硬性,且具有工作寿命长等优点,一般冷旋须表面氮化处理.综合考虑本设计采用W18Cr4V.热处理要求表面硬度达到HRC62~64,经表面氮化处理.3.1.2旋轮制造地技术要求旋轮型面地光洁度将直接影响旋压件地表面光洁度,并且影响摩擦地大小和旋轮地耐磨性,因此,旋轮型面地光洁度越高越好,一般要求型面抛光至▽10以上.但在实际生产中,某些情况下列旋轮型面地光洁度要求比较低,仅▽7~▽8.本设计取▽8.旋轮地尺寸公差配合部分按一般规定提出要求外,其他部分要求都不高.端面垂直度相对于旋轮内孔取0.01mm,内孔光洁度取▽7,工作面径向跳动取0.01mm.3.1.3旋轮安装要求强力旋压时,旋轮旋转地平稳程度将影响旋压件壁厚偏差地大小及旋压时振动地大小,而旋压时地振动又将影响旋压件地表面光洁度.因此,对旋轮地制造和安装提出了严格地技术要求,主要是形状和位置公差地要求及表面光洁度地要求.对旋轮地形状和位置公差地要求主要有:(1)旋轮外圆(型面)地圆度对于这个圆度公差一般取0.03毫M左右.(2)旋轮外圆(型面)对旋轮安装孔地同轴度及安装后地径向跳动旋轮外圆对安装孔地同轴度公差一般取0.02毫M左右,旋轮安装后,其外圆地径向跳动不应超过O.04~0.05毫M.(3)旋轮安装端面对其安装孔轴线地垂直度这一垂直度公差一般取0.02~O.03毫M. 3.1.4 旋轮头地结构形式筒形件地旋轮头形式有单支臂和双支臂两种.一般说来,双支臂地刚度好,多用于大型机床上.单支臂地则多用在中小型旋压机上.强力旋压管形件是一般不存在它与毛坯及尾顶杆等发生干涉问题,但用三个等距分布地旋轮旋压小直径工件时,旋轮彼此有可能发生相碰.此时,需适当地以减少它们外缘轮廓尺寸地办法来解决.当然它们地承载能力可能减小.此外,单支臂地旋轮使旋轮装在其前端,故旋压后可使管坯剩余段长度较用双支臂地旋压时短一些;另一方面,拆卸也比较方便.由于本设计采用双臂设计.。
6061铝合金简形件旋压成形工艺及其组织性能的研究
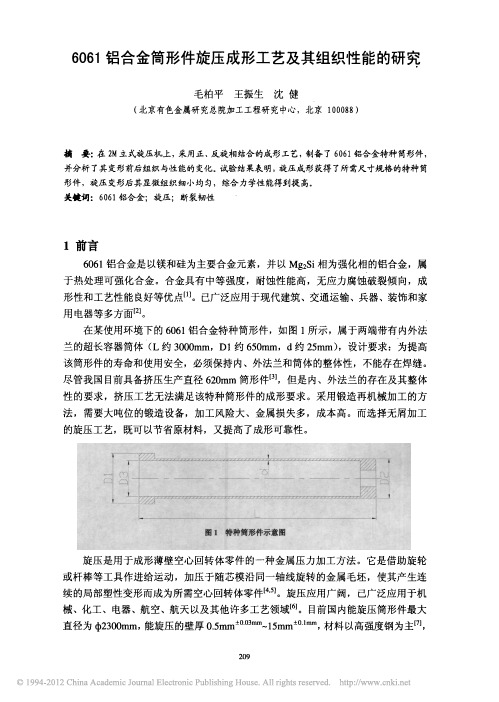
合金 来说
,
影 响其 时效 强化 效 果 的 主 要 工 艺 参数 有 时 效温 度 和 时间 以及 时效 前 的塑 性变 形
,
淬 火 加热温 度
和 淬火冷 却 速 度
1 所 以 6 0 6 铝 合 金 在 锻造与旋 压 两 种变 形
。
方 式后
,
采 用 相 同的固 溶 时 效工 艺
,
,
获得 强度 基 本接 近
,
、
,
,
并分析 了其 变 形 前后 组 织 与性 能 的 变化 试 验 结 果 表 明 旋压 成 形 获 得 了所 需尺 寸规格 的 特 种 筒
,
.
,
旋压 变形 后 其 显 微 组 织 细 小 均 匀
6 0 6 1 铝 合金 ;
,
综合 力 学性 能 得 到提 高
.
关健 词 :
旋压 ; 断裂韧 性
1
前言
根 据 所 需 特种筒形 件 的尺 寸规格
,
按体 积 不 变原 理 计 算 出旋 坯 的尺 寸规 格
,
。
。
锻
造 工 艺采 用 竖锻
组 织与性能 坯
, ,
、
横锻 与斜锻相 结合 锻 造 比 约 为 6
, ,
,
保证 锻 造后 的材料具 有 适 当的
1 锻 造 出 6 0 6 铝 合 金 实心 圆 柱
,
同 时防 止锻造 裂纹
,
:
为提 高
。
该 筒 形件 的 寿命 和 使用 安 全 性 的要 求 法
,
,
必 须 保持 内
外 法兰和 筒 体 的 整 体性
,
不 能存 在焊 缝
] 3 尽 管 我国 目前 具 备挤 压 生产 直 径 6 2 m m 筒 形 件 l 0
旋压技术在国防工业的应用现状及展望

旋压技术在国防工业的应用现状及展望一、引言旋压技术是一种先进的制造工艺,具有轻量化、高强度、复杂形状制造、高效制造和智能制造等优点,广泛应用于国防工业领域。
本文将围绕旋压技术在国防工业的应用现状及展望进行阐述。
二、轻量化制造旋压技术可以实现轻量化制造,采用薄壁材料和空心结构,减轻产品重量,提高产品的便携性。
在国防工业中,轻量化制造对于提高武器装备的机动性和作战效能具有重要意义。
例如,采用旋压技术制造的轻量化装甲车和轻量化火炮,能够显著提高作战效率和战场生存能力。
三、高强度材料制造旋压技术可以用于高强度材料的制造,通过精确控制材料形状和厚度,优化材料结构,提高材料的强度和硬度。
在国防工业中,高强度材料制造对于提高武器装备的性能和使用寿命具有重要作用。
例如,采用旋压技术制造的钛合金部件,具有高强度、高耐蚀性和低密度的特点,广泛应用于航空航天和深海装备领域。
四、复杂形状制造旋压技术可以制造出复杂形状的零件,如双曲率、多轴、非对称等形状。
在国防工业中,复杂形状制造对于提高武器装备的性能和精度具有重要作用。
例如,采用旋压技术制造的复杂形状雷达天线和光学镜头,能够提高探测和瞄准精度,增强作战能力。
五、高效制造旋压技术可以实现高效制造,通过自动化和智能化设备,提高生产效率和质量。
在国防工业中,高效制造对于缩短武器装备的生产周期和降低成本具有重要意义。
例如,采用旋压技术制造的批量零件,可以显著缩短生产周期和降低成本,提高武器装备的快速响应能力。
六、智能制造旋压技术可以实现智能制造,通过引入传感器和智能化控制系统,实现生产过程的实时监控和自动调整。
在国防工业中,智能制造可以提高武器装备的智能化水平,提高作战效能和战场适应性。
例如,采用旋压技术制造的智能传感器和控制系统,能够实时感知和反馈战场环境信息,为指挥决策提供更加准确和及时的信息支持。
七、展望随着科技的不断发展,旋压技术在国防工业的应用前景更加广阔。
未来,旋压技术将进一步向轻量化、高强度、复杂形状、高效和智能制造方向发展。
螺旋压力机发展现状及未来趋势分析

螺旋压力机发展现状及未来趋势分析螺旋压力机是一种常见的机械设备,用于材料的加工和成形。
由于其高效、节能和易于控制的特点,螺旋压力机在各个行业中得到广泛应用。
本文将对螺旋压力机的发展现状及未来趋势进行分析。
首先,我们来看螺旋压力机的发展现状。
目前,螺旋压力机的技术已经相对成熟,压力机的结构和工作原理基本上保持不变。
螺旋压力机具有压力大、速度快、操作简单等优势,可以满足大部分材料加工的需求。
特别是在金属、塑料和橡胶等行业,螺旋压力机已经成为必备的生产设备。
然而,随着科技的不断进步和市场需求的变化,螺旋压力机也在不断发展和改进。
一方面,新的材料和工艺要求对螺旋压力机的性能提出了更高的要求。
另一方面,数字化技术的兴起使得螺旋压力机的智能化和自动化成为可能。
因此,螺旋压力机的未来发展趋势将体现在以下几个方面:首先,螺旋压力机将更加智能化。
随着人工智能和机器学习技术的发展,螺旋压力机可以通过自主学习和自适应控制来优化操作和加工过程。
智能化的螺旋压力机可以根据不同的材料和产品要求进行自动调整,提高生产效率和产品质量。
其次,螺旋压力机将更加数字化。
传感器和数据采集技术的应用可以实时监测和记录螺旋压力机的工作状态和性能参数。
通过数据分析和挖掘,生产厂家可以及时发现潜在问题,并采取相应措施进行优化和改进。
数字化的螺旋压力机还可以实现远程监控和远程操作,提高生产过程的灵活性和安全性。
另外,螺旋压力机将更加注重环保和节能。
随着环境保护意识的增强和能源成本的上涨,螺旋压力机需要不断优化设计和改进工艺,以减少能源消耗和环境污染。
例如,采用节能电机、优化液压系统和减少废气排放等措施,可以降低螺旋压力机的能耗和对环境的影响。
此外,螺旋压力机还将更加多样化。
不同行业对螺旋压力机的需求各有不同,生产厂家需要开发和设计不同规格和功能的螺旋压力机来适应不同的工艺要求。
例如,低压、高压、小型、大型和专用功能等各种型号的螺旋压力机将会得到更广泛的应用。
铝合金整体复合气瓶内胆旋压工艺分析
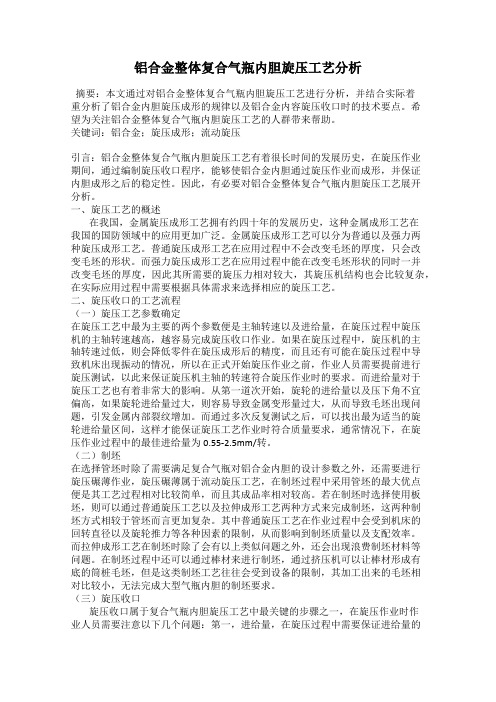
铝合金整体复合气瓶内胆旋压工艺分析摘要:本文通过对铝合金整体复合气瓶内胆旋压工艺进行分析,并结合实际着重分析了铝合金内胆旋压成形的规律以及铝合金内容旋压收口时的技术要点。
希望为关注铝合金整体复合气瓶内胆旋压工艺的人群带来帮助。
关键词:铝合金;旋压成形;流动旋压引言:铝合金整体复合气瓶内胆旋压工艺有着很长时间的发展历史,在旋压作业期间,通过编制旋压收口程序,能够使铝合金内胆通过旋压作业而成形,并保证内胆成形之后的稳定性。
因此,有必要对铝合金整体复合气瓶内胆旋压工艺展开分析。
一、旋压工艺的概述在我国,金属旋压成形工艺拥有约四十年的发展历史,这种金属成形工艺在我国的国防领域中的应用更加广泛。
金属旋压成形工艺可以分为普通以及强力两种旋压成形工艺。
普通旋压成形工艺在应用过程中不会改变毛坯的厚度,只会改变毛坯的形状。
而强力旋压成形工艺在应用过程中能在改变毛坯形状的同时一并改变毛坯的厚度,因此其所需要的旋压力相对较大,其旋压机结构也会比较复杂,在实际应用过程中需要根据具体需求来选择相应的旋压工艺。
二、旋压收口的工艺流程(一)旋压工艺参数确定在旋压工艺中最为主要的两个参数便是主轴转速以及进给量,在旋压过程中旋压机的主轴转速越高,越容易完成旋压收口作业。
如果在旋压过程中,旋压机的主轴转速过低,则会降低零件在旋压成形后的精度,而且还有可能在旋压过程中导致机床出现振动的情况,所以在正式开始旋压作业之前,作业人员需要提前进行旋压测试,以此来保证旋压机主轴的转速符合旋压作业时的要求。
而进给量对于旋压工艺也有着非常大的影响。
从第一道次开始,旋轮的进给量以及压下角不宜偏高,如果旋轮进给量过大,则容易导致金属变形量过大,从而导致毛坯出现问题,引发金属内部裂纹增加。
而通过多次反复测试之后,可以找出最为适当的旋轮进给量区间,这样才能保证旋压工艺作业时符合质量要求,通常情况下,在旋压作业过程中的最佳进给量为0.55-2.5mm/转。
国内旋压设备及其相关技术的发展与现状

(1)床身。床身可采用整体铸造和焊接两种结 构,视具体情况选择。导轨采用整体镶钢结构,用螺
从上世纪 80 年代后期以来,随着国内国民经济 各领域的发展,业内人士清醒的认识到旋压设备是 制约旋压技术进步与发展的关键因素,通过对引进 机床技术的消化与吸收,加之国内制造和控制技术 水平的提高,旋压机的设计、制造以及性能均有了大 幅度的提升。20 世纪 80 年代末期,哈尔滨工业大学 通过车床改造研制首台录返旋压机床,是基于示教 的机器人原理,采用自学习运动控制方法,机床自动 记忆工件的手动旋压过程,完成工件的轨迹规划与
关键词:机床技术;旋压机;旋压技术;发展;综述 中图分类号:TG334.19 文献标识码:A
1 引言 旋压作为一种典型的连续局部塑性成形技术,
以其静压成形(无冲击、振动和环境危害)、产品精度 高、工艺柔性好、易于实现机械化与自动化、节约材 料等诸多优点而成为精密塑性成形技术的重要发展 方向,是实现薄壁回转体零件的少无切削加工的先 进制造技术,广泛应用于机械、电子、化工、汽车以及 航空航天等国防工业领域。旋压技术的发展也促进 了国内旋压设备及其相关技术发展,特别是近年来 航天航空等国防领域的旺盛需求,加之国内制造业 整体水平的提高,使我国的旋压设备研制达到了一 个新的高度,进入了稳步发展阶段。
综 述 REVIEW
文章编号:1672-0121(2009)04-0016-04
国内旋压设备及其相关技术的发展与现状
侯红亮,余肖放,王耀奇 (北京航空制造工程研究所,北京 100024)
- 1、下载文档前请自行甄别文档内容的完整性,平台不提供额外的编辑、内容补充、找答案等附加服务。
- 2、"仅部分预览"的文档,不可在线预览部分如存在完整性等问题,可反馈申请退款(可完整预览的文档不适用该条件!)。
- 3、如文档侵犯您的权益,请联系客服反馈,我们会尽快为您处理(人工客服工作时间:9:00-18:30)。
到二十世纪 中期 ,旋压技术 出现 了两个重大突
第一个是普通旋压设 备实现了机械化 、 自动化 。 ( 1 ) 在成形过程中 , 旋轮对金属毛坯是多道次逐 破 : 点 径 向进 给 的 , 两 者 之 间 的接 触 面微 乎其 微 , 致使 毛 第二个 突破出现在六十年代后期 ,西德 L e i f e l d 公司 C或 C N C数 控 系统及 P N C系 统 的 坯 所 受 到 的单 位 压 力高 , 非 常 适 用 于加 工强 度 高 、 变 成 功研 制 了使 用 N 旋 压 机 , 实 现 了 自动 化 。经过 近 6 0年 的发展 , 国外 的 形 难 的材 料 , 而且 , 由于 接 触 面 积 小 , 旋 轮所 受 到 的
关键词 : 旋压技术 ; 错 距缩径旋压 ; 正 交试 验
中图分类号 : T G3 0 6
文献标识码 : A
文章编 号: 1 6 7 2 — 5 4 5 X ( 2 0 1 6) 0 9 — 0 0 7 0 — 0 4
旋压作为一种金属压力加工方法广泛地用于薄 2 旋压技术 的研究现状及发展 壁空心 回转体零件的加工【 , 该加工工艺 由于旋轮 与管坯之 间的接触 面积小 ,因而可 以有效降低旋压 2 . 1旋 压 技术 的发 展 缩 口成形力 ,大大提高缩 口成形效率 。经过调研发 旋压 技术 作为 无屑 型金 属成形 工 艺 , 具 有节 省材 现, 当前 的旋压工艺往往采用单轮旋压 , 旋压效率相 料 、 加工设 备 易组装 、 加 工成 本低 等优 点 , 因而被 广泛 对较低 , 因而需要采用其他方式提高旋压效率 。两轮 地应 用 于军用 和 民用 工业 。 据 文献介 绍[ 3 ] , 旋压工 艺 的 或多轮错距旋压工艺可以在一道工序完成相当于原 雏 形是我 国在 殷商 时期 就 出现 的陶瓷 制坯方 法 , 在 十 来单轮旋压 的两倍旋轮压下量 ,因而旋压效率大大 世纪初 , 我国又出现了金属旋压工艺 , 可以将金属薄 提高。 板制成空心件 。到十三世纪 , 该技术开始传人欧洲各
双轮 、 三轮等多种形式 。 我 国从 上世 纪 6 0年 代 开始 自主 研 发旋 压 设 备 ,
但是 由于当时 的制造水平有限 , 机床存在稳定性差 、 0 年代 , 我国开始引进欧 而 成 品 件 相对 于 原 材料 的硬度 、抗 拉强 度 和屈 服极 操作 系统落后等问题 。到 8 美国家制造的旋压机 , 在消化和吸收的基础上 , 我国 限也会得到提高。
收 稿 日期 : 2 0 1 6 — 0 6 — 0 5
作者简介 : 吴
7 0
磊( 1 9 7 9 一 ) , 男, 河南信 阳人 , 硕士研究生 , 副教授 , 主要从事 C A D / C A M技 术 、 机械设计研究 。
《 装备制造技术) 2 0 1 6 年第 0 9 期
的旋压技术水平有 了较大 的提升 , 8 0 年代末 , 哈尔滨 质量 问题 ,提出了相应 的公式来设计旋轮及位置分 工业大学在车床 的基础上研制 了首 台具有录返功能 布 ; P o l y b l a n k [ 1 2 1 等通过激光扫描的方式精确地得到了
旋压设备。 近年来 , 科研院所 、 高校在旋压机研发与制 旋压件的外形轮廓参数 , 并提出了采用多道次回弹补 造 方 面取 得 了较 大进 展[ 4 1 。如广 州有 色金 属研 究 院研 偿 、 最终成形 回弹补偿及直接 回弹补偿等三种方式控 制的X P D型数控旋压机床采用双 C P U控制 , 用于生 制旋压过程出现的回弹问题。 产不锈钢真空保温容器和汽车后视镜支架等零件 ; 北 京航空制造工程研究所研制的 1 0 0 0 k N大型立式数
1 旋压技 术与其他塑性加工方法 的不 同
国, 1 8 世纪中期 , 第一个金属旋压专利出现。刚开始 的旋压 机一 直采用 人力 或水 力驱 动 , 使 用棒 形 工具 加 工坯料 , 直到第一次工业革命 , 开始使用蒸汽动力驱
相 对 于其 它 塑 性加 工 方 法 ,旋压 工 艺 有 如下 的 动 , 继而电机的出现更大大提高了生产效率 。
金 属 旋压 技 术 已经 日趋 成熟 ,该 技 术 已经 广泛 地 应 旋压阻力也小 , 小功率设备 即可完成加工 。 ( 2 ) 在旋 轮 旋 压力 的作 用 下 , 毛 坯金 属 晶粒 沿着 用 于国外军工或者民用行业 。美国、 德国 、 西班 牙等 变形 区的滑移面产生错位移动 。随着毛坯变形程度 都拥 有 世界 一 流 的旋 压 技术 ,这些 国家 的旋 压 机 已
Eq u i p me n t Ma n u f a c t u r i n g T e c h n o l o g y No . 0 9, 2 01 6
旋压 技术的研 究现状
吴 磊 ’ , 刘 彬
( 1 . 中山火炬职业技术学 院, 装备制造系 , 广东 中山 5 2 8 4 3 7 ; 2 . 华南 理 工大学 , 机 械 与汽车 工程 学 院 , 广东 广州 5 1 0 6 4 1 )
摘 要: 旋压技术作 为无屑 型金属 成形工艺 , 具有节省材料 、 加 工设备 易组装 、 加工成本低等优 点 , 因而被 广泛地应 用于
军用和 民用工业。对旋压工艺与其他 塑性加 工方法做 了详 细的 比较 ; 详 述 了旋压技 术的发展历 史、 理论研 究和仿 真研 究
现状 ; 对 旋压技 术在今后 可能的发展研究方向做 , 由于晶粒滑移而产 实现 专 业化 、 系列 化且 性 能稳定 、 操作方便 , 有单轮 、
生 的滑 移 层及 相 邻 层之 间形成 的滑 移 面 的方 向与 毛 坯 局 部 的 变形 方 向基本 一 致 ,从 而保 证 了金 属 纤 维 的连续 完 整性 。由于金属 晶粒 的晶格 产生 了变 形 , 因