工艺控制对双捻机断丝率的影响
双捻机设计原理

双捻机控制系统设计16技术资料Technology Libraries No Comments »钢帘线是用优质高碳钢制成的表面镀有黄铜且具有特殊用途的细规格钢丝股或绳,主要用于各种车辆轮胎和飞机轮胎及其他橡胶制品的骨架材料[1]。
钢帘线的生产主要包括拉丝和捻制两个工艺过程,双捻机将拉成的多股钢丝捻制成钢帘线绳。
双捻机根据放线工字轮位置分为两种基本类型,一种是放线工字轮在主机飞轮的里边,而收线工字轮在飞轮的外面,即“内放外收”型;另一种是放线工字轮在主机飞轮的外面,而收线工字轮在飞轮的里边即“外放内收型”[2]。
本文研究的是用于钢帘线生产的“内放外收”型双捻机控制系统设计。
1 双捻机工作原理双捻机的基本原理是机身旋转一周,捻出两个捻距的股或绳的钢丝绳。
其结构以及工作原理如图1所示。
图1中,收线工字轮位于旋转体的外部,7个放线工字轮(1个芯线轮和6个丝轮)分两面安装在飞轮内部的摇篮上。
钢丝和芯线从内部放线工字轮引出,通过若干过线导轮汇集到固定在摇篮上的过线轴B,再经过固定在飞轮轴右端的过线轮A后,到达固定在左端飞轮轴上的过线轮C,继而到达过捻器。
再经过若干导轮和相关检测装置到达收线工字轮。
在BA段和CD段分别实现了主捻和过捻,捻出了两个捻距[3]。
根据双捻机的工作原理分析,其生产工艺主要包括主捻、过捻和收排线三道工序。
其中,捻股部分由主电机驱动飞轮旋转体实现主捻和扭转伺服电机驱动过捻器实现过捻(即完成双稔);收线部分由电机驱动收线轮和排线电机控制排线;此外还有摇篮电机控制摇篮翻转;吸风、排风电机对机器内部进行冷却。
根据工艺要求,整个设备的运转速度能够根据需要进行调整,而且要求主捻电机、过捻电机和收线电机转速之间保持一定的比例,即各电机同步运转。
所以,双捻机控制系统的核心功能就是控制设备中各个电机根据工艺要求转速间始终保持一定比例的同步运行。
同时系统还要求具有运行控制、工艺参数设置、系统调试、成品长度计算、设备状态监测、故障报警处理等功能。
羊绒纱线的纺纱捻度与拉伸性能

羊绒纱线的纺纱捻度与拉伸性能羊绒纱线作为一种高档的纺织原料,具有柔软舒适、保暖性强等特点,广泛应用于高档羊绒面料的制作中。
在羊绒纱线的生产过程中,纺纱捻度和拉伸性能是两个非常重要的指标,直接影响着羊绒纱线的质量和性能。
纺纱捻度是指纱线中每英寸的捻数。
通过调节捻度的大小,可以控制纱线的结构和力学性能。
适当的捻度可以提高纺纱的均匀性和强度,使纱线更加紧密、结构更稳定。
过高或过低的捻度都会导致纱线出现问题。
如果捻度过高,纱线容易发生断裂,因为单根纤维之间的摩擦力过大,纤维之间的结构容易疏松。
而捻度过低,则容易导致纱线松散,纤维之间的结构较松散,纱线容易起毛或开裂。
此外,纺纱捻度还会影响纱线的柔软度和颗粒感。
通常情况下,捻度较高的纱线具有较强的柔软度和绒感,适合用于制作高档面料。
而捻度较低的纱线则更适合用于制作针织品和毛线等。
除了纺纱捻度,拉伸性能也是评估羊绒纱线质量的重要指标之一。
拉伸性能是指纱线在承受外力时能够延展的程度。
拉伸性能好的纱线具有更高的强度和延展性,不容易断裂和变形。
这对于制作高档面料非常重要,因为面料在使用过程中经常要承受外力的拉伸。
羊绒纱线的拉伸性能与原料的质量和纺纱工艺有着密切的关系。
纤维的粗细、长度、弹性等都会影响纱线的拉伸性能。
同时,纺纱过程中的加湿、调剂等工艺控制也会对拉伸性能产生影响。
正确控制拉伸性能可以使羊绒纱线更具有弹性、耐用性和舒适性。
在羊绒纺纱过程中,通过优化原料选择和纺纱工艺,可以有效地调控纺纱捻度和拉伸性能。
首先,在选择原料时,要考虑纤维的质量和特性,选择纤维长度均匀、弹性好的原料,以便制作出高质量的羊绒纱线。
其次,要根据羊绒纺纱的用途和要求,调整纺纱机的捻度和拉伸力,以获得所需的捻度和拉伸性能。
最后,在后处理过程中,要进行适当的水洗和整理,使纱线更加柔软舒适,并提高纱线的绒感和延展性。
总之,羊绒纱线的纺纱捻度和拉伸性能是影响其质量和性能的重要因素。
通过科学调控纺纱捻度和拉伸性能,可以制作出质量优良的羊绒纱线,为高档面料的制作提供有力支持。
捻接工艺参数优化与质量
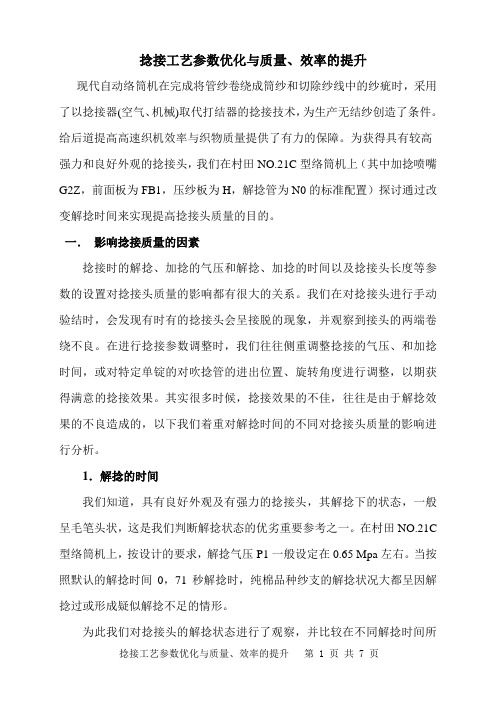
捻接工艺参数优化与质量、效率的提升现代自动络筒机在完成将管纱卷绕成筒纱和切除纱线中的纱疵时,采用了以捻接器(空气、机械)取代打结器的捻接技术,为生产无结纱创造了条件。
给后道提高高速织机效率与织物质量提供了有力的保障。
为获得具有较高强力和良好外观的捻接头,我们在村田NO.21C型络筒机上(其中加捻喷嘴G2Z,前面板为FB1,压纱板为H,解捻管为N0的标准配置)探讨通过改变解捻时间来实现提高捻接头质量的目的。
一.影响捻接质量的因素捻接时的解捻、加捻的气压和解捻、加捻的时间以及捻接头长度等参数的设置对捻接头质量的影响都有很大的关系。
我们在对捻接头进行手动验结时,会发现有时有的捻接头会呈接脱的现象,并观察到接头的两端卷绕不良。
在进行捻接参数调整时,我们往往侧重调整捻接的气压、和加捻时间,或对特定单锭的对吹捻管的进出位置、旋转角度进行调整,以期获得满意的捻接效果。
其实很多时候,捻接效果的不佳,往往是由于解捻效果的不良造成的,以下我们着重对解捻时间的不同对捻接头质量的影响进行分析。
1.解捻的时间我们知道,具有良好外观及有强力的捻接头,其解捻下的状态,一般呈毛笔头状,这是我们判断解捻状态的优劣重要参考之一。
在村田NO.21C 型络筒机上,按设计的要求,解捻气压P1一般设定在0.65 Mpa左右。
当按照默认的解捻时间0,71秒解捻时,纯棉品种纱支的解捻状况大都呈因解捻过或形成疑似解捻不足的情形。
为此我们对捻接头的解捻状态进行了观察,并比较在不同解捻时间所产生的解捻的效果,以下是我们以纯棉27.8tex纱,在NO.21C型络筒机捻接器上,以不同的解捻时间所产生的不同的解捻效果照片。
解捻时间为0.71秒解捻时间为0.51秒解捻时间为0.40秒解捻时间为0.35秒根据比较分析,我们得出当解捻时间为0.40秒时,捻接头的解捻状态为最佳。
为了解不同解捻时间对捻接头的强力和外观所造成的影响,我们继续在村田NO.21C型络筒机做相关的试验。
影响纺粘法非织造材料性能的主要因素

影响纺粘法非织造材料性能的主要因素
1)纺丝牵伸工艺影响单丝细度和强力:相关实验表明,在相同挤出量条件下,长丝细度下降,其强力增加,断裂伸长减小。
随着纺丝速度的加快,纤维线密度减少,纺丝线上丝束的张力增大,致使成网长丝分子取向度随之增高。
2)喷丝孔吐出量Q对纤网的影响:纺丝成网工艺中纺丝速度相同时,若喷丝孔的吐丝量下降,则丝条在纺程上所受压力相对增加,这有利于长丝的取向、结晶和长丝细化。
3)喷丝孔的孔数和孔径:理论上讲纺丝成网喷丝板的孔径在0.2~0.80mm
范围内均可纺丝。
实际工程上选择孔径的依据是控制聚合物熔体出喷丝孔的剪切速率范围。
喷丝孔的排列和孔数对熔体细流的均匀冷却,良好凝固成形有很大关系。
圈形分布时喷丝板外圈的丝条能均匀冷却,但当孔数较多时,内圈的丝条往往不容易充分冷却。
矩形分布,其优点是可以改进内层丝条的冷却,但缺点是侧吹风迎风侧和背风侧丝条的冷却条件不一致。
4)冷却风条件:a.风速:冷却风速度过高,喷丝板温度过低,易产生断丝,但如果冷却风速过低,不能带走应排除的热量,丝条不能充分固化,拉伸时也易产生断丝现象;b.冷却吹风温度:温度10摄氏度以上,均匀分布;c.相对温度:比热容,静电;d.单体抽吸风。
SMS复合工艺的特点及常见的三种复合方式
特点:SMS复合非织造布同时具有纺粘材料和熔喷材料的优良性能。
薄型纺丝成网法非织造布具有良好的力学性能,但孔隙尺寸较大,抗渗透性较差。
而熔喷非织造材料具有超细纤维的纤网结构,其过滤和屏蔽性能很好,但抗拉强度较低。
复合而成的非织造布则弥补了彼此的不足,同时又保持了各自的优点。
纺丝断丝原因

1.原材料质量问题:原料质量不均匀,如短纤维、杂质含量高,会导致纤维间
断裂。
此外,原料物理机械性能不理想,如纤维断裂强度偏低,也会导致经丝抱合力差,在织造过程中经不起钢筘、综丝反复摩擦,导致经丝单纤起毛或断头。
2.环境因素:湿度过低、温度过高或过低等气候因素均可能影响纺纱质量。
环
境因素也会对纱线产生影响,比如温度、湿度、静电等。
如果环境湿度太大或者温度太高,纱线内部的水分太多,就容易导致纱线断丝。
3.设备问题:设备磨损、零部件松动、设备调整不当,都会导致纱线断丝。
此
外,设备的运行状态,如经丝的开口高度对经毛、断经也有很大的影响。
4.工艺问题:纺纱工艺流程设置不合理、扭度过大、捻度太高等,也可能导致
断丝问题。
5.储存和管理问题:纱线质量不佳也可能是由于纱线贮存不当导致的。
双捻机生产钢丝绳过程中断丝原因分析

SHU W e— o g,ZHANG u i n h L n,TANG in,D a -e g Ja AI Qio f n (ins at oe nGop C . L . J n y 14 3 h a J guF s nH ps ru o ,t , i g i 2 4 3 ,C i ) a e u d a n n
w trt n r rwig s e ie d a e . 5 mm,w r r w n p e s 8~ 1 s u e gh i 2 0 0 m ,tn i a e a k wi d a n t lw r i mtr0 1 e e i da igs ed i e 0 m/ ,c t ln t s3 0 ese l
me t t d p i ain a d n y t m d lc r g la i n u f r c d s l t n,t o t lte p fee to lt gS — n , o a o t t t d ig s se t a d e e t av n z g s l i a i o ui tr o o o i u c o o c n r h H o l cr p ai O o n l t n p e iey t su e s a y p o u t n,w i h d c e s s lyn r k n w r ae n r a e r d c in e ce c . ui rc s l o a s r t d rd c i o e o h c e r a e a ig b o e ie rt ,ic e s sp o u t f in y o i Ke wo d d u l w se ;srn i g te r o o e;ee t g la ii g H;t n i t n t y rs o b et itr ta dn ;se l e frr p wi lcr av n z ;p o n e sl sr gh e e
制丝工艺加工控制要素分析

制丝工艺加工控制要素分析制丝工艺是一种重要的化工加工过程,其加工控制要素的优劣直接影响产品的质量和产量。
下面将分析制丝工艺加工控制的要素,包括原料控制、设备控制、工艺参数控制和人员操作控制等方面。
首先,原料控制是制丝工艺加工的第一要素。
原料的质量好坏直接影响到制丝产品的质量和效率。
原料控制主要包括原料的选择、质量监测和存储等环节。
在原料选择方面,需要选择纯正的化纤原料,确保原料的质量符合要求。
在质量监测方面,要对原料的各项指标进行定期检测,确保原料的质量稳定。
在存储方面,要注意原料的存储环境和条件,避免原料受潮、受污染等,影响加工工艺的顺利进行。
其次,设备控制也是制丝工艺加工的重要要素。
设备的性能、品质直接影响了制丝工艺的加工效率和产品质量。
设备控制主要包括设备的选择、维护和保养等环节。
在设备选择方面,需要选择适合实际生产需要的设备,确保设备的品质和性能符合要求。
在设备维护和保养方面,要做好设备的定期维护和保养工作,确保设备的正常运转和使用寿命。
第三,工艺参数控制是制丝工艺加工的关键要素。
工艺参数的合理控制是确保产品质量和产量的关键。
工艺参数控制主要包括生产工艺流程、操作规程、加工温度、压力、速度等参数的控制。
在生产工艺流程方面,要根据实际生产情况合理安排工艺流程,确保每个环节的工艺参数符合设定要求。
在操作规程方面,要对工艺操作进行规范和标准化管理,确保每位操作人员按照标准操作流程进行加工。
在加工参数控制方面,要根据产品的要求和实际产量确定合理的加工温度、压力、速度等参数,确保产品的质量和产量都能满足要求。
最后,人员操作控制是制丝工艺加工的重要环节。
操作人员的技术水平和专业素养直接影响到产品的质量和产量。
人员操作控制主要包括人员的培训、管理和监督等环节。
在人员培训方面,要对操作人员进行专业技能培训,确保操作人员掌握加工工艺的操作技术和质量要求。
在管理和监督方面,要建立科学的管理机制和监督体系,对操作人员进行定期考核和监督,确保操作人员的操作行为合乎规范。
降低捻织厂捻线废丝率实践研究

1 捻 线 废 丝 率 现 状
统计 2 0 1 5年 捻 织 二 厂 生 产 过 程 中废 丝量 为 2 1 2 . 2 4
吨 ,根 据 当前 正 品 丝 与 废 丝 价 差 0 . 9 万 元 ,可 知 2 0 1 5 年 因 废丝减少 收入 2 1 2 . 2 4 x 0 . 9 万元= 1 9 1 万 元 。对 捻 织 二 厂 2 0 1 5
故障频发 ,同时受 到不规范管理和操作 因素 的影 响 ,捻织
现对捻织二厂生产 过程 中各工序废丝情况 进行统计 ,见表
1 所示 。 由表 1 可知 ,废 丝 主要 产生 在欠长 丝处理 工序和
初捻 工序 中 ,分别 占4 9 . 6 %和 3 5 . 5 % ,上 丝工 序所 占比重
最小 ,仅为 1 . 9 %。
了更直 观地 了解 生产各 工序 中产生废丝 量和工序 废丝率 ,
品尼 龙 丝 的价 位 比重最 高 ,当前 每 吨废 丝 价格 为 1 . 4 万 元 ,正 品丝价格 为 2 . 3 万元 ,因此 ,每节约 一吨废 丝可挽 回经济损 失 0 . 9 万元 ,且 吨布耗丝水 平也是 绩效考 核 的重 要 指标 。由于设备运 行年限较长 ,设备 更新 率较慢 ,设备
年 1 月至 1 2月 废 丝 率 进 行 统 计 , 1 月至 1 2月 分 别 为
1 _ 3 5 %、1 . 5 2 % 、1 - 4 9 %、l - 3 5 %、1 . 5 4 %、1 . 6 7 % 、1 . 5 7 %、
1 . 6 7 % 、1 . 4 7 % 、1 . 5 3 %、1 . 6 5 %、1 . 5 8 % ,- 平均 为 1 . 5 3 %,
经 验交流
DOI : 1 0 . 3 9 6 9 / j . i s s n . 1 0 0 9 - 9 4 9 2 . 2 0 1 7 . 0 8 . 0 6 1
高效工艺对成纱质量指标影响及对策
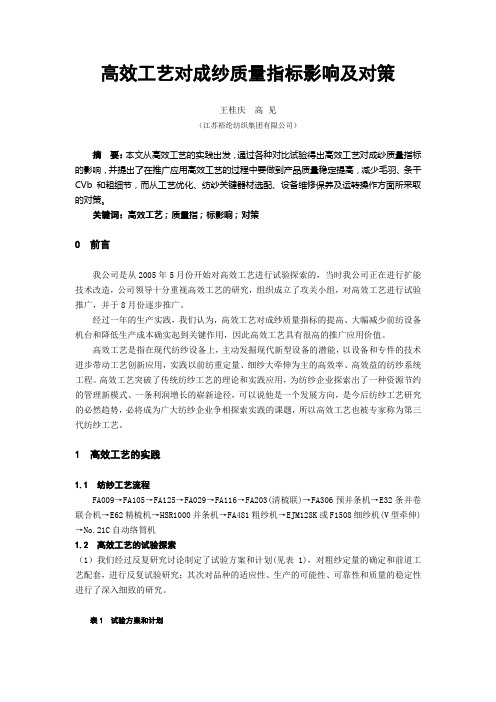
高效工艺对成纱质量指标影响及对策王桂庆高见(江苏裕纶纺织集团有限公司)摘要:本文从高效工艺的实践出发,通过各种对比试验得出高效工艺对成纱质量指标的影响,并提出了在推广应用高效工艺的过程中要做到产品质量稳定提高,减少毛羽、条干CVb和粗细节,而从工艺优化、纺纱关键器材选配、设备维修保养及运转操作方面所采取的对策。
关键词:高效工艺;质量指;标影响;对策0 前言我公司是从2005年5月份开始对高效工艺进行试验探索的,当时我公司正在进行扩能技术改造,公司领导十分重视高效工艺的研究,组织成立了攻关小组,对高效工艺进行试验推广,并于8月份逐步推广。
经过一年的生产实践,我们认为,高效工艺对成纱质量指标的提高、大幅减少前纺设备机台和降低生产成本确实起到关键作用,因此高效工艺具有很高的推广应用价值。
高效工艺是指在现代纺纱设备上,主动发掘现代新型设备的潜能,以设备和专件的技术进步带动工艺创新应用,实践以前纺重定量、细纱大牵伸为主的高效率、高效益的纺纱系统工程。
高效工艺突破了传统纺纱工艺的理论和实践应用,为纺纱企业探索出了一种资源节约的管理新模式、一条利润增长的崭新途径,可以说他是一个发展方向,是今后纺纱工艺研究的必然趋势,必将成为广大纺纱企业争相探索实践的课题,所以高效工艺也被专家称为第三代纺纱工艺。
1 高效工艺的实践1.1 纺纱工艺流程FA009→FA105→FA125→FA029→FA116→FA203(清梳联)→FA306预并条机→E32条并卷联合机→E62精梳机→HSR1000并条机→FA481粗纱机→EJM128K或F1508细纱机(V型牵伸)→No.21C自动络筒机1.2 高效工艺的试验探索(1)我们经过反复研究讨论制定了试验方案和计划(见表1),对粗纱定量的确定和前道工艺配套,进行反复试验研究;其次对品种的适应性、生产的可能性、可靠性和质量的稳定性进行了深入细致的研究。
表1 试验方案和计划(2)进行专题试验并整理试验数据和分析。
造成纱线断头的原因分析

造成纱线断头的原因分析从现状来看,造成纱线断头的因素较多,每天平均纱线断头率在20%以上。
对造成纱线断头的主要因素,我们进行了以下分析:(1)由于原料中的棉结、杂质、短绒较多而影响了纱线的强力和条干,导致纱线断头较多。
特别是短纤维浮游动程大,变速点分散,牵伸机构在牵伸过程中不能有效控制其运动,从而易恶化条干,并且原料中短绒含量越多,则条干越差,纱线上的弱环就多;短绒还会使纤维间的抱合长度短,纱线强力低,从而导致纱线断头较多。
短绒还易导致成纱中粗节、细节和棉结增多,产生较多的飞花。
短绒含量多的原因:一是配棉时原料中含有较多的短绒特别是长度较短(12 mm以下)的短绒。
二是在清梳工序经过开松、打击和分梳过程产生了较多的短绒,落棉数量不足。
(2)由于机械状态不良而导致纱线断头较多,特别是细纱机牵伸元件的选用和工艺配置对成纱条干均匀度影响较大。
例如,胶圈和上下销的性能规格、胶辊弹性及表面处理方法、胶辊直径等影响对纤维握持的稳定性;胶圈张力、胶圈钳口隔距的大小既影响前区摩擦力界的分布,也影响胶圈运动的稳定性,进而影响对纤维运动的控制。
歪锭子、跳筒管、钢领起浮等会造成纱线张力波动。
能否正确使用集合器对纱线断头也有一定影响。
钢丝圈型号、号数的选用以及更换方法,钢领表面处理方法、处理周期等都影响纱线断头。
(3)由于各工序挡车工操作不当、清洁工作不及时或清洁效果差而导致纱线断头较多。
例如,棉卷正卷率控制差、梳棉机开关车轻条子拿掉的长度不足、条子和粗纱接头不良、擗条子、并条机断头自停失灵、粗纱喂人时意外牵伸大、挡车工清洁不及时导致纤维三绕和挂花、集合器横动不良和挂花、细纱挡车工接头合格率低、接头或清洁碰断纱线等。
(4)工艺配置不合理而影响纱条条子,导致纱线断头较多。
粗纱捻系数、粗纱定量与细纱机后区牵伸工艺配置不合理等都会恶化条干均匀度,进而增加纱线断头的机率。
(5)空气调节及生产管理中存在的问题。
原料进入清花车间前未能充分吸湿或放湿,不能达到工艺要求的吸湿平衡回潮率,使得纤维偏干或偏湿。
400型双捻机的技术分析
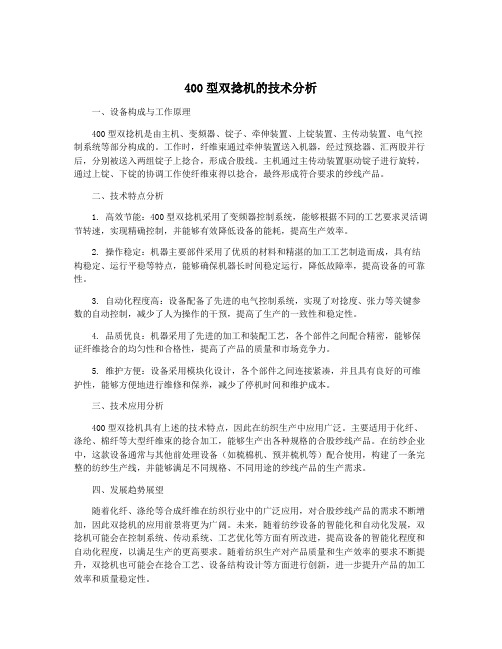
400型双捻机的技术分析一、设备构成与工作原理400型双捻机是由主机、变频器、锭子、牵伸装置、上锭装置、主传动装置、电气控制系统等部分构成的。
工作时,纤维束通过牵伸装置送入机器,经过预捻器、汇两股并行后,分别被送入两组锭子上捻合,形成合股线。
主机通过主传动装置驱动锭子进行旋转,通过上锭、下锭的协调工作使纤维束得以捻合,最终形成符合要求的纱线产品。
二、技术特点分析1. 高效节能:400型双捻机采用了变频器控制系统,能够根据不同的工艺要求灵活调节转速,实现精确控制,并能够有效降低设备的能耗,提高生产效率。
2. 操作稳定:机器主要部件采用了优质的材料和精湛的加工工艺制造而成,具有结构稳定、运行平稳等特点,能够确保机器长时间稳定运行,降低故障率,提高设备的可靠性。
3. 自动化程度高:设备配备了先进的电气控制系统,实现了对捻度、张力等关键参数的自动控制,减少了人为操作的干预,提高了生产的一致性和稳定性。
4. 品质优良:机器采用了先进的加工和装配工艺,各个部件之间配合精密,能够保证纤维捻合的均匀性和合格性,提高了产品的质量和市场竞争力。
5. 维护方便:设备采用模块化设计,各个部件之间连接紧凑,并且具有良好的可维护性,能够方便地进行维修和保养,减少了停机时间和维护成本。
三、技术应用分析400型双捻机具有上述的技术特点,因此在纺织生产中应用广泛。
主要适用于化纤、涤纶、棉纤等大型纤维束的捻合加工,能够生产出各种规格的合股纱线产品。
在纺纱企业中,这款设备通常与其他前处理设备(如梳棉机、预并梳机等)配合使用,构建了一条完整的纺纱生产线,并能够满足不同规格、不同用途的纱线产品的生产需求。
四、发展趋势展望随着化纤、涤纶等合成纤维在纺织行业中的广泛应用,对合股纱线产品的需求不断增加,因此双捻机的应用前景将更为广阔。
未来,随着纺纱设备的智能化和自动化发展,双捻机可能会在控制系统、传动系统、工艺优化等方面有所改进,提高设备的智能化程度和自动化程度,以满足生产的更高要求。
400型双捻机的技术分析
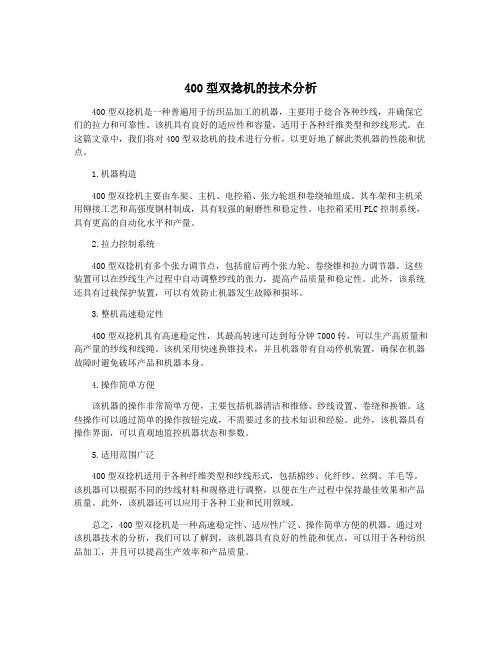
400型双捻机的技术分析400型双捻机是一种普遍用于纺织品加工的机器,主要用于捻合各种纱线,并确保它们的拉力和可靠性。
该机具有良好的适应性和容量,适用于各种纤维类型和纱线形式。
在这篇文章中,我们将对400型双捻机的技术进行分析,以更好地了解此类机器的性能和优点。
1.机器构造400型双捻机主要由车架、主机、电控箱、张力轮组和卷绕轴组成。
其车架和主机采用铆接工艺和高强度钢材制成,具有较强的耐磨性和稳定性。
电控箱采用PLC控制系统,具有更高的自动化水平和产量。
2.拉力控制系统400型双捻机有多个张力调节点,包括前后两个张力轮、卷绕锥和拉力调节器。
这些装置可以在纱线生产过程中自动调整纱线的张力,提高产品质量和稳定性。
此外,该系统还具有过载保护装置,可以有效防止机器发生故障和损坏。
3.整机高速稳定性400型双捻机具有高速稳定性,其最高转速可达到每分钟7000转,可以生产高质量和高产量的纱线和线绳。
该机采用快速换锥技术,并且机器带有自动停机装置,确保在机器故障时避免破坏产品和机器本身。
4.操作简单方便该机器的操作非常简单方便,主要包括机器清洁和维修、纱线设置、卷绕和换锥。
这些操作可以通过简单的操作按钮完成,不需要过多的技术知识和经验。
此外,该机器具有操作界面,可以直观地监控机器状态和参数。
5.适用范围广泛400型双捻机适用于各种纤维类型和纱线形式,包括棉纱、化纤纱、丝绸、羊毛等。
该机器可以根据不同的纱线材料和规格进行调整,以便在生产过程中保持最佳效果和产品质量。
此外,该机器还可以应用于各种工业和民用领域。
总之,400型双捻机是一种高速稳定性、适应性广泛、操作简单方便的机器。
通过对该机器技术的分析,我们可以了解到,该机器具有良好的性能和优点,可以用于各种纺织品加工,并且可以提高生产效率和产品质量。
纺织厂后纺车间攻关捻接合格率措施

纺织厂后纺车间攻关捻接合格率措施纺织厂后纺车间是整个纺织生产过程中非常重要的一个环节,直接影响着产品的质量和生产效率。
捻接是指在纺纱过程中将多股纱线合并成一股纱线的工序,合格率是衡量捻接工艺是否良好的重要指标。
本文将针对纺织厂后纺车间捻接合格率不达标的问题,提出相应的解决措施。
首先,要加强工艺流程和操作规范的培训和管理。
纺织厂后纺车间的操作人员需要进行全面的培训,了解捻接工艺的各个环节和要求,掌握操作规范。
同时,建立完善的管理制度,对操作人员进行监督和考核,确保每个环节都得到正确执行。
只有具备严谨的工艺流程和规范的操作,才能提高捻接合格率。
其次,要采用先进的捻接设备和技术。
现代纺织行业发展迅速,不断涌现出新的捻接设备和技术,例如自动捻接机器人、智能化捻接设备等。
这些设备和技术的应用可以提高捻接工艺的稳定性和一致性,降低合格率的波动性。
纺织厂后纺车间应积极引进先进设备和技术,不断提升捻接合格率。
第三,要加强质量监控和质量检验。
纺织厂后纺车间应建立完善的质量监控体系,对捻接工艺的各个环节进行实时监测,及时发现问题并采取措施解决。
同时,要加强质量检验,对捻接后的产品进行严格抽检,确保产品的质量符合标准要求。
第四,要重视员工的技能培训和团队建设。
员工是纺织厂后纺车间的核心力量,他们的技能水平和团队精神直接关系到捻接合格率的提高。
纺织厂后纺车间应加强员工的技能培训,提升他们的专业素质和工作能力。
同时,要倡导团队合作精神,建立和谐的工作氛围,激发员工的工作积极性和创造力。
第五,要加强与供应商的合作和沟通。
纺织厂后纺车间的捻接工艺需要依赖原材料供应商提供优质的原材料。
因此,纺织厂后纺车间应与供应商建立良好的合作关系,密切沟通,共同解决问题。
通过与供应商的合作,可以有针对性地解决原材料质量不稳定等问题,提高捻接合格率。
总之,纺织厂后纺车间捻接合格率是一个复杂的问题,需要从多个方面综合施策。
通过加强工艺流程和操作规范的培训和管理,采用先进的捻接设备和技术,加强质量监控和质量检验,重视员工的技能培训和团队建设,加强与供应商的合作和沟通等措施,可以提高捻接合格率,确保纺织产品的质量和生产效益的提升。
并捻工艺对亚麻与维纶并捻纱拉伸性能的影响
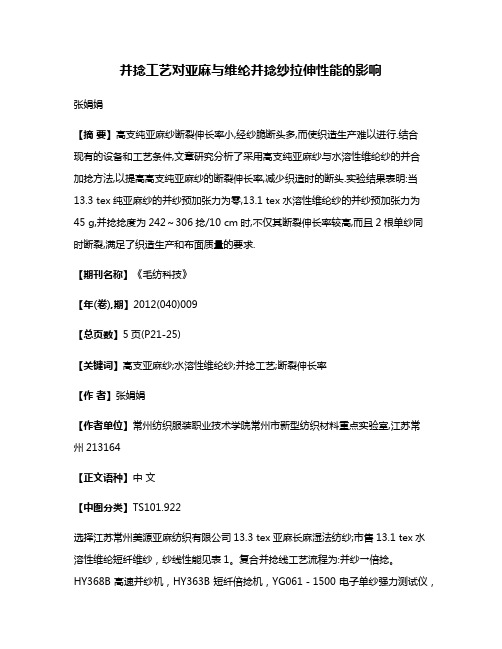
并捻工艺对亚麻与维纶并捻纱拉伸性能的影响张娟娟【摘要】高支纯亚麻纱断裂伸长率小,经纱脆断头多,而使织造生产难以进行.结合现有的设备和工艺条件,文章研究分析了采用高支纯亚麻纱与水溶性维纶纱的并合加捻方法,以提高高支纯亚麻纱的断裂伸长率,减少织造时的断头.实验结果表明:当13.3 tex纯亚麻纱的并纱预加张力为零,13.1 tex水溶性维纶纱的并纱预加张力为45 g,并捻捻度为242~306捻/10 cm时,不仅其断裂伸长率较高,而且2根单纱同时断裂,满足了织造生产和布面质量的要求.【期刊名称】《毛纺科技》【年(卷),期】2012(040)009【总页数】5页(P21-25)【关键词】高支亚麻纱;水溶性维纶纱;并捻工艺;断裂伸长率【作者】张娟娟【作者单位】常州纺织服装职业技术学院常州市新型纺织材料重点实验室,江苏常州213164【正文语种】中文【中图分类】TS101.922选择江苏常州美源亚麻纺织有限公司13.3 tex亚麻长麻湿法纺纱;市售13.1 tex水溶性维纶短纤维纱,纱线性能见表1。
复合并捻线工艺流程为:并纱→倍捻。
HY368B高速并纱机,HY363B短纤倍捻机,YG061-1500电子单纱强力测试仪,Nikon-D5000照相机。
并纱速度为500m/min;倍捻转速为4 500 r/min。
亚麻纱强力测试参照GB/T 3916—1997《纺织品卷装纱单根纱线断裂强力和断裂伸长率的测定》,采用北京华昊电子有限公司的YG029K单纱强力仪测试拉伸性能,拉伸速度500 mm/min,预加张力0.5 cN,夹头隔距500 mm,每种不同并捻工艺的纱线测试10次,取其平均值。
并纱张力值用附加张力垫圈的质量(g)表示。
1.4.1 并纱张力由表1可知,13.3 tex亚麻纱和13.1 tex水溶性维纶纱的断裂伸长率有较大差异,如果在并线时对上述2种纱线采用相同的预加张力(即等长混并)时,由于复合纱线在拉伸时其不同组分之间存在断裂不同时性[1—2],则会使混并线在拉伸时,当伸长达到断裂伸长率较小的亚麻纱的断裂伸长时,亚麻纱中的纤维开始迅速断裂,而维纶纱还在被继续拉伸,这将达不到提高亚麻纱断裂伸长率的目的,同时还将影响织机的正常生产和布面质量。
络筒机工艺参数的设定对万米剪切数、运转效率的影响

络筒机工艺参数的设定对万米剪切数、运转效率的影响邵作敬(山东德源纱厂有限公司)我公司使用的自动络筒机是意大利SA VIO公司生产的OIRON “M”型络筒机,每台络筒机由64锭构成,使用的捻接器是TWINSPLICER机械式捻接器,电清是LOEPFE公司的TK830型电清。
结合多年来的工作实践,得出要想降低机配件的消耗,提高设备运转效率,除了络筒机有良好的工作状态和具有较强责任心的挡车工外,合理的工艺参数的设定,能降低万米剪切数,保证了产品质量和前后生产平衡,为企业赢得更多利润。
1 我厂生产的紧密纺JC32SK和JC60S筒纱主要参数的设定注:其中Nep为棉节,DS为短粗节直径,LS为短粗节长度,DL 为长粗节直径,LL为长粗节长度,-D为短粗节直径,-L为短粗节长度。
络纱速度的高低对筒纱的毛羽和条干影响极大,毛羽和条干基本上是随着络纱速度的提高而逐步恶化,应根据不同的纱线支数和对质量的不同要求,来选择不同的络纱速度。
压力的大与小直接影响筒纱的松紧度,压力太大筒纱紧,压力太小筒纱松,都不利于后道工序的退绕,在保障成型良好的情况下,压力应偏小掌握。
电清参数,尤其是短粗节直径DS、短粗节长度LS,其设定尤为重要,因为管纱90%纱疵是短粗节,也可以说80-90%的纱疵是A类和B类纱疵,短粗节设定的严紧与宽松,就决定了络筒机万米剪切数的高低,络筒机的运转效率会随着万米剪切的升高而降低。
2 紧密纺JC32SK和JC60S筒纱在表1下的7个班次的生产记录:表2 JC32SK生产记录表3.JC60S生产记录由表2、3可看出品种JC32SK和JC60S七个班次产量、万米剪切数和单锭效率变化波动不大,单锭效率和万米剪切数成反比例,单锭效率随着万米剪切数的升高而降低,纺JC32SK 1台络筒机对应9台细纱机,纺JC60S 1台络筒机对应10台细纱机,我公司细纱机的配置是DTM129细纱机528台(456锭/台),OIRON “M”型络筒机60台,理论上1台络筒机要对应9台细纱机,实际生产情况基本跟理论一致,保持了细纱与络筒生产平衡。
双捻机原理
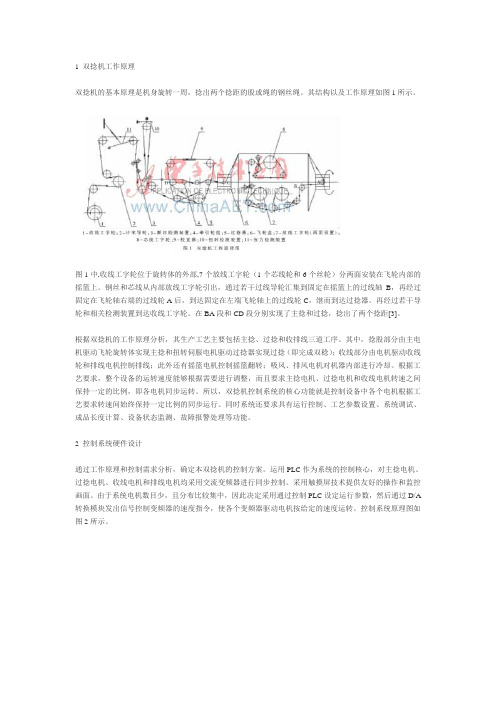
1 双捻机工作原理双捻机的基本原理是机身旋转一周,捻出两个捻距的股或绳的钢丝绳。
其结构以及工作原理如图1所示。
图1中,收线工字轮位于旋转体的外部,7个放线工字轮(1个芯线轮和6个丝轮)分两面安装在飞轮内部的摇篮上。
钢丝和芯线从内部放线工字轮引出,通过若干过线导轮汇集到固定在摇篮上的过线轴B,再经过固定在飞轮轴右端的过线轮A后,到达固定在左端飞轮轴上的过线轮C,继而到达过捻器。
再经过若干导轮和相关检测装置到达收线工字轮。
在BA段和CD段分别实现了主捻和过捻,捻出了两个捻距[3]。
根据双捻机的工作原理分析,其生产工艺主要包括主捻、过捻和收排线三道工序。
其中,捻股部分由主电机驱动飞轮旋转体实现主捻和扭转伺服电机驱动过捻器实现过捻(即完成双稔);收线部分由电机驱动收线轮和排线电机控制排线;此外还有摇篮电机控制摇篮翻转;吸风、排风电机对机器内部进行冷却。
根据工艺要求,整个设备的运转速度能够根据需要进行调整,而且要求主捻电机、过捻电机和收线电机转速之间保持一定的比例,即各电机同步运转。
所以,双捻机控制系统的核心功能就是控制设备中各个电机根据工艺要求转速间始终保持一定比例的同步运行。
同时系统还要求具有运行控制、工艺参数设置、系统调试、成品长度计算、设备状态监测、故障报警处理等功能。
2 控制系统硬件设计通过工作原理和控制需求分析,确定本双捻机的控制方案。
运用PLC作为系统的控制核心,对主捻电机、过捻电机、收线电机和排线电机均采用交流变频器进行同步控制。
采用触摸屏技术提供友好的操作和监控画面。
由于系统电机数目少,且分布比较集中,因此决定采用通过控制PLC设定运行参数,然后通过D/A 转换模块发出信号控制变频器的速度指令,使各个变频器驱动电机按给定的速度运转。
控制系统原理图如图2所示。
控制系统主要包括主捻控制、过捻控制、收线控制和排线控制等子系统。
2.1 主捻控制主捻电机M1根据负荷选用Y160M-4 11 KW型电机,变频器1选择台达VFD185B43A 18.5 KW型变频器,主电机速度检测选用台达ES3-0CCN6942型编码器。
400型双捻机的技术分析
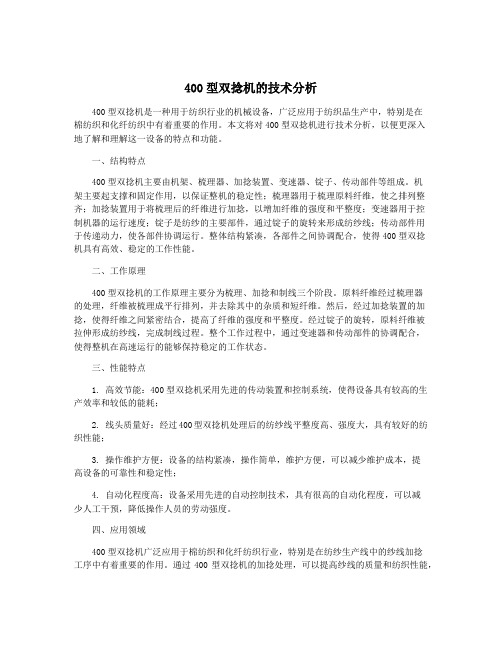
400型双捻机的技术分析400型双捻机是一种用于纺织行业的机械设备,广泛应用于纺织品生产中,特别是在棉纺织和化纤纺织中有着重要的作用。
本文将对400型双捻机进行技术分析,以便更深入地了解和理解这一设备的特点和功能。
一、结构特点400型双捻机主要由机架、梳理器、加捻装置、变速器、锭子、传动部件等组成。
机架主要起支撑和固定作用,以保证整机的稳定性;梳理器用于梳理原料纤维,使之排列整齐;加捻装置用于将梳理后的纤维进行加捻,以增加纤维的强度和平整度;变速器用于控制机器的运行速度;锭子是纺纱的主要部件,通过锭子的旋转来形成纺纱线;传动部件用于传递动力,使各部件协调运行。
整体结构紧凑,各部件之间协调配合,使得400型双捻机具有高效、稳定的工作性能。
二、工作原理400型双捻机的工作原理主要分为梳理、加捻和制线三个阶段。
原料纤维经过梳理器的处理,纤维被梳理成平行排列,并去除其中的杂质和短纤维。
然后,经过加捻装置的加捻,使得纤维之间紧密结合,提高了纤维的强度和平整度。
经过锭子的旋转,原料纤维被拉伸形成纺纱线,完成制线过程。
整个工作过程中,通过变速器和传动部件的协调配合,使得整机在高速运行的能够保持稳定的工作状态。
三、性能特点1. 高效节能:400型双捻机采用先进的传动装置和控制系统,使得设备具有较高的生产效率和较低的能耗;2. 线头质量好:经过400型双捻机处理后的纺纱线平整度高、强度大,具有较好的纺织性能;3. 操作维护方便:设备的结构紧凑,操作简单,维护方便,可以减少维护成本,提高设备的可靠性和稳定性;4. 自动化程度高:设备采用先进的自动控制技术,具有很高的自动化程度,可以减少人工干预,降低操作人员的劳动强度。
四、应用领域400型双捻机广泛应用于棉纺织和化纤纺织行业,特别是在纺纱生产线中的纱线加捻工序中有着重要的作用。
通过400型双捻机的加捻处理,可以提高纱线的质量和纺织性能,使得最终的成品纺织品具有更好的品质和市场竞争力。
EP 帆布生产过程中的强力损失分析

EP 帆布生产过程中的强力损失分析李桂英(平顶山神马化纤织造有限责任公司,河南平顶山 467000) 摘要:分析EP 帆布生产过程中造成纤维强力性能损失的原因,并提出改进措施。
捻丝工序中控制捻丝速度为3160r ・min -1、尼龙钩质量为750mg 、筒管采用包铁皮的塑料管,可以将捻线的断裂强力保持率由78.4%提高到96.7%,断裂伸长率由8.5%提高到13.4%。
纬线生产设置两个储纬器,可提高帆布纬向强力及生产效率。
关键词:EP 帆布;强力损失;捻丝速度;筒管;尼龙钩 中图分类号:TQ336.2;TQ342+.1/.2 文献标识码:B 文章编号:10002890X (2006)0520304203作者简介:李桂英(19652),女,河南柘城县人,平顶山神马化纤织造有限责任公司工程师,学士,主要从事帆布产品开发工作。
帆布作为织物芯输送带的骨架材料,几乎承受了输送带的全部负荷。
用聚酯浸胶帆布作骨架材料的输送带具有强力高、耐腐蚀、使用寿命长和粘合力高等优点。
在国外,EP 帆布已经是织物芯输送带的主要骨架材料。
我国EP 帆布的用量也逐渐增长。
EP 帆布生产的原材料为聚酯和锦纶66工业丝。
工业长丝在加捻、整经和织造过程中受到外力作用,物理性能会发生变化,尤其是强力性能变化很大。
本文分析EP 帆布生产过程中造成强力损失的原因,并提出改进措施。
1 EP 帆布生产工艺流程EP 帆布生产工艺流程如图1所示。
图1 EP 帆布生产工艺流程示意2 加捻过程强力损失分析从帆布生产工艺流程可以看出,经线的加工有捻丝、整经、织造和浸胶4道工序。
EP 帆布经线使用的原丝是聚酯工业丝,由于聚酯工业丝模量高、柔性差,因此捻丝、整经和织造过程对其物理性能,尤其是强力性能影响很大,极易造成强力损失和断裂伸长率下降。
原丝加捻的目的是增大长丝的捻度,使丝线中的纤维抱合成束,提高织造加工性能。
加捻过程中捻丝速度、尼龙钩和筒管质量等都对丝线性能有影响。
- 1、下载文档前请自行甄别文档内容的完整性,平台不提供额外的编辑、内容补充、找答案等附加服务。
- 2、"仅部分预览"的文档,不可在线预览部分如存在完整性等问题,可反馈申请退款(可完整预览的文档不适用该条件!)。
- 3、如文档侵犯您的权益,请联系客服反馈,我们会尽快为您处理(人工客服工作时间:9:00-18:30)。
双捻机生产钢丝绳过程中断丝原因分析
采用双捻机进行捻股生产,具有速度快、生产效率高、占用空间少、股子捻制质量好等特点,广泛应用于钢丝绳捻制生产;然而,双捻机生产对于制绳钢丝性能的稳定性要求极高。
因此,制绳钢丝质量的稳定性,对钢丝绳的性能、双捻机捻制生产的效率,以及钢丝绳的综合成材率,都有着很大的影响。
特别是对于生产车台需求多,钢丝绳的定尺长度要求较长,产量相对较低的细规格钢丝绳(钢丝绳直径1.5mm以下),其影响更为明显[1]。
制绳钢丝质量稳定性,直接影响到双捻机生产的效率。
然而,制绳钢丝质量的稳定,取决于各个生产加工环节。
因此,严格控制好制绳钢丝每个生产环节,确保双捻机生产正常进行,提高钢丝绳的生产效率和综合成材率[2,3]。
近期双捻机生产情况不稳定,双捻机断丝率出现较大的波动(如图1所示),明显低于标准值,严重影响钢丝绳的生产效率和综合成材率。
因此,必须找到导致双捻机断丝率出现波动的原因,制定出合理的预防性措施,确保生产控制过程的稳定有效,才能满足双捻机捻制生产的顺利进行。
图1 1³3-0.30mm双捻机生产情况
1制绳钢丝生产环节
1.1热处理生产
钢丝的热处理,就是把钢丝加热到一定的温度,并保温一定的时问,然后用选定的速度和方法使之冷却,最后得到所需要的显微组织和性能的一种生产工艺。
钢丝经过拉拔后,内部组织变长、变细,甚至受到一定程度的破坏,产生冷加工硬化现象。
为了恢复钢丝的塑性,以便下一步继续拉拔,需要对拉拔后的钢丝进行热处理生产[4]。
为了得到细规格制绳钢丝(0.10-0.20mm),选取进线为0.7mm的半成品钢丝,进行热处理生产。
热处理工艺参数,见表1所示。
热处理生产工艺流程:放线→热处理加热炉→铅浴炉→盐酸酸洗→水洗→烘干→收线。
注:热处理加热设备为天然气明火加热炉,炉子分为4段;
1.2电镀锌生产
电镀锌生产工艺流程:放线→酸洗→水冲洗→电镀锌→水洗→烘干→收线。
电镀锌生产工艺参数,见表2所示。
表2 电镀锌生产工艺参数
1.3水箱车拉丝生产
水箱车拉丝生产工艺参数,见表3所示。
表3 水箱车拉丝生产工艺
1.4制绳钢丝性能
制绳钢丝性能,见表4所示。
2原因分析
2.1断口分析
制绳钢丝0.15mm其性能指标中,扭转指标存在较大波动,出现低值——180次(按生产控制标准:0.15mm双捻机用制绳钢丝,其扭转值≥200)。
同时,收集双捻机断丝断口,对断口进行扫描电镜(SEM)分析,断口形貌如图2、图3所示。
钢丝断口处白亮斑点内存在裂纹源和扩展区;在扩展区,微观断口形貌为脆性解理形貌,并与基体断裂区形成鲜明的轮廓[5]。
上述观察分析结果表明:该断口具有氢脆断裂的形貌特征。
因此,双捻机断丝率偏高,是由于制绳钢丝存在氢脆现象。
唯一能够产生氢脆的生产环节,就是钢丝电镀锌生产环节。
由此可推断:电镀锌生产环节,出现了生产异常情况。
图2 0.15mm制绳丝断口形貌(SEM)图3 0.15mm制绳丝断口形貌(SEM)
2.2氢脆过程分析
根据电化学原理,电镀溶液中,由于水分子的离解,或多或少地存在一定数量的氢离子。
在钢丝电镀锌酸性环境中,在阴极析出锌原子的同时,溶液中电离出的氢离子,形成氢气的过程分为如下几步:
1)H3O+离子从溶液中转移到阴极钢丝表面附近;
2)H3O+离子在阴极上脱水还原,生成的氢原子吸附在钢丝表面,如下反应:
H3O++e→H吸+H2O
3)两个吸附的氢原子结合成氢分子,如下反应:
H吸+ H吸→H2
在阴极还原后,一部分形成氢气逸出,一部分以原子氢的形式渗入钢丝基体及镀锌层中;氢在金属内使晶格扭曲,产生很大的内应力,致使金属的机械性能大幅度降低,析氢不仅对镀层性能产生不利影响,如产生针孔、麻点、气泡等缺陷,而且会渗透至钢丝基体中,使钢丝基体和镀层的韧性大幅度降低,导致再加工所得的制绳钢丝,在进行双捻机捻制生产过程中,出现脆断[6,7]。
氢脆现象是细规格制绳钢丝最严重的质量隐患之一,严重影响制绳钢丝的使用性能。
2.3 电镀锌溶液分析
通过对制绳钢丝生产工序进行分析,钢丝氢脆的生产环节发生在钢丝电镀锌过程。
通过对电镀锌溶液的浓度、pH值等指标进行跟踪,发现电镀溶液的pH值出现异常波动,其变化范围明显超出了工艺规定要求(见表2),如图5所示。
图4 电镀锌溶液pH 值变化曲线
电镀锌生产过程中,定时添加H 2SO 4溶液,补充电镀过程所消耗的H +离子。
在每次添加过程中,由于高浓度的
H 2SO 4直接倒入电镀池,造成在一段较长的时间内,电镀溶液的pH 值急剧降低(即H +离子浓度增大)。
在一定时间内,酸性越强,则钢丝电镀过程越容易发生氢脆现象[8,9]。
3改进措施
3.1电镀溶液滴定添加方案
为了消除因添加H 2SO 4溶液,造成电镀锌溶液pH 值急剧降低,H +离子浓度增大,钢丝在强酸性环境下进行电镀锌发生氢脆,影响电镀锌钢丝质量。
决定采用溶液滴定添加系统,自动添加H 2SO 4溶液,如图5所示。
图5 电镀锌硫酸滴定添加系统
3.2改进后效果
通过采用H 2SO 4滴定添加系统,实现了H 2SO 4添加溶液的均匀配置。
配置好的溶液按照一定滴定速度,均匀地进行补充添加。
这样就确保了,电镀锌溶液的pH 值始终保持在2—3.5范围内,避免了pH 值大幅度的波动,消除了因H 2SO 4溶液添加后,电镀锌溶液pH 值急剧降低,H +离子浓度增大,
导致氢脆现象的产生[10]。
双捻机捻制生产过程中,断丝率得到明显降低和稳定,如图6所示。
图6 采用滴定添加系统后,1³3-0.30mm双捻机断丝情况
4 结语
综上所述,通过对制绳丝生产过程、双捻机断丝原因进行分析,确定了电镀锌钢丝氢脆现象是引起双捻机断丝率大幅度波动的主要原因;同时,改进电镀锌生产设备,设计并采用滴定添加系统,进行电镀锌H2SO4溶液的添加,精确控制电镀锌溶液的pH值,使其稳定的保持在工艺规定的范围内,减少氢脆现象的发生,确保电镀锌生产过程的稳定,为双捻机生产提供质量稳定的细规格制绳钢丝。
参考文献
[1] 杨程,梁益龙,黄忠渠.钢丝绳中股在生产时“起泡”问题的分析[J]. 贵州工业大学学报:自然科学版,2006(1):73-77.
[2] 黄忠渠.用双捻机生产普通钢丝绳探析[J].金属制品,2010(2):10-13.
[3] 韩铁继. 对双捻机捻制过程的分析[J].金属制品,1996(A00):34-40.
[4] 王利明,杨恒,刘礼华,等.中碳钢丝拉拔断裂原因分析及改进措施[J].金属制品,2010(4):8-11.
[5] 文斯雄.电镀锌弹性零件断裂的原因分析[J].腐蚀与防护,2000(1):34-35.
[6] 董朝阳.零件电镀后裂纹分析[J].电镀与精装,2009(4):21-22.
[7] 汤智慧,张晓云,陆峰,蔡健平,宇波.镀层结构与氢脆关系研究[J].材料工程,2006(10):37-42.
[8] 黄平,陈端杰.电镀过程中的析氢及氢脆控制研究[J].长安科技,2002(1):29-31.
[9] 李金桂.电镀氢脆故障及应对措施[J].材料保护,2006(8):51-53.
[10] 任培东.电镀锌钢丝的生产[J].酒钢科技,2000(1):40-42.
(刘红芳,张伦)。