钻孔短刃长钻针的优势
钻头基础介绍

D
S
B D
Type N – 圆柱柄
螺旋角 γ = 20°-30° 圆弧后刀面 顶角 σ = 118° 标准钻头,主要用来加工拉伸强度不超 过1200 N/mm²合金或非合金钢, 灰铸铁, 球墨铸铁 以及 粉末金属
339
317
D
D
DZ DZ DZ
235 236 237
D D D
The Tool Company Art.-Nr. 245
有倒角
ρby Xu_Hanguang
ρby Xu_Hanguang
Type N : 标准槽型
退刀次数 : 8
d
The Tool Company
TYPE GT
Type GT
10 x d
3xd
Type GT: 宽大的排屑槽,适宜加工孔深为 3 x D 以上的孔
1xd
ρby Xu_Hanguang
退刀次数 : 2
d
The Tool Company
FN FN FN
618 619
FN FN
S S S S
The Tool Company
抛物钻) 麻花钻 GT100(抛物钻 抛物钻
刃带氮化处理
TIN coated
FireX coated
ρby Xu_Hanguang
d
The Tool Company
TYPE N
Type N
5xd
1,5 x d 1,5 x d 1,5 x d 1xd 1xd 1xd 1xd 0,5 x d
DIN 最大钻深 338 DZ DZ DZ 340 DZ DZ DZ 1869 Series 1 Series 2 Series 3 Series 1 Series 2 DZ DZ DZ DZ DZ
PCB钻孔异常知识
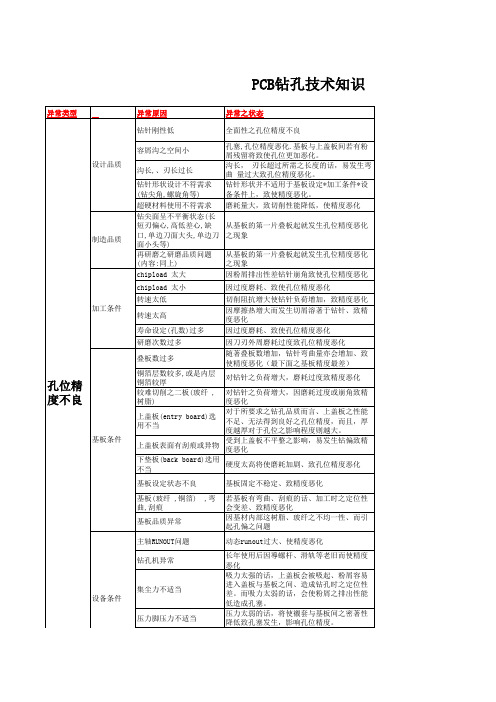
寿命设定(孔数)过多
随著孔数增加,磨耗加剧
chipload太小
与基板接触之时间拉长,使磨耗增加
转速太高
与基板接触之时间拉长,使磨耗增加
研磨次数过多
随著研磨次数增加,外周磨耗持续累积 ,所以 磨耗量大
铜箔层数较多,或是内层 铜箔较厚
对钻针之负荷增加,使摩耗加剧
较难切削之基板(玻纤,树 脂)
对钻针之负荷增加,造成磨耗或是崩角
转速太高
因磨擦然增大而发生切屑溶著于钻针,致断针 发生
钻尖面有附著物(铜等基 板构成材料附著,从基板 退出时粉屑附著)
在钻上盖板之过程中,因定位性差而发生弯 曲,导致断针
分段加工之条件不适当
分段次数及加工量与基板之设定不符,造成粉 屑排出差,发生断针
下垫板穿透量过多
因粉屑量增加,使粉屑排出性恶化,而发生断 针
上盖板表面有刮痕或异物
受到上盖板不平整之影响.易发生钻偏导致断 针
下垫板(backupboard)选 用不当
硬度太高使磨耗加剧,切削阻抗增加而断针
基板设定状态不良
基板固定不稳定,致精度恶化而导致断针
基板(玻纤 ,铜箔)凹凸, 弯曲,刮痕
基板品质异常
若基板有弯曲,刮痕的话,加工时之定位性会 变差,致精度恶化而发生断针 因基材内部之树脂,玻纤之不均一性,而引 起孔偏而发生断针之问题
钻针刚性底
易因弯曲量大而在沟底部处发生断针
容屑沟之空间小
瞬间扭力增加在沟长的中间附近断针
沟长, 刃长过长
沟长,刃长超过所需之长度的话,易发生弯曲 量过大致孔位精度恶化
超硬材料使用不符需求 抗折力低,因切削阻抗而断针.
钻针面呈不平衡状态(长
短刃偏心,高低差偏心,缺 孔位精度恶化导致断针
长螺旋钻机的施工应用特点
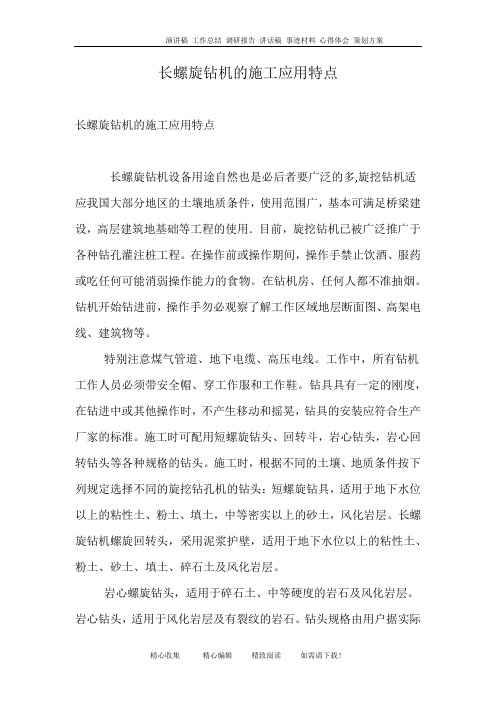
长螺旋钻机的施工应用特点长螺旋钻机的施工应用特点长螺旋钻机设备用途自然也是必后者要广泛的多,旋挖钻机适应我国大部分地区的土壤地质条件,使用范围广,基本可满足桥梁建设,高层建筑地基础等工程的使用.目前,旋挖钻机已被广泛推广于各种钻孔灌注桩工程。
在操作前或操作期间,操作手禁止饮酒、服药或吃任何可能消弱操作能力的食物。
在钻机房、任何人都不准抽烟。
钻机开始钻进前,操作手勿必观察了解工作区域地层断面图、高架电线、建筑物等。
特别注意煤气管道、地下电缆、高压电线。
工作中,所有钻机工作人员必须带安全帽、穿工作服和工作鞋。
钻具具有一定的刚度,在钻进中或其他操作时,不产生移动和摇晃,钻具的安装应符合生产厂家的标准。
施工时可配用短螺旋钻头、回转斗,岩心钻头,岩心回转钻头等各种规格的钻头。
施工时,根据不同的土壤、地质条件按下列规定选择不同的旋挖钻孔机的钻头:短螺旋钻具,适用于地下水位以上的粘性土、粉土、填土,中等密实以上的砂土,风化岩层。
长螺旋钻机螺旋回转头,采用泥浆护壁,适用于地下水位以上的粘性土、粉土、砂土、填土、碎石土及风化岩层。
岩心螺旋钻头,适用于碎石土、中等硬度的岩石及风化岩层。
岩心钻头,适用于风化岩层及有裂纹的岩石。
钻头规格由用户据实际工程的情况选购选配。
根据结构的差别,旋挖钻机施工过程中,可根据地质状况的差异选择不同斗底形式的钻头。
单底板土层钻斗适用于粘土层及干孔条件下的施工。
双层底的旋挖钻斗主要适用于流沙层作业,砂土、胶结较差粒径较小的卵石层,湿孔钻进条件下使用双层底旋挖钻斗也可有利于孔底的清孔施工。
施工实践已证明在复杂地层中,双层底钻斗钻进效率及孔底清洁度明显优于单层底钻斗。
旋挖钻机配合不同钻具,适用于干式(短螺旋)或湿式(回转斗)及岩层(岩心钻)的成孔作业。
旋挖钻机还可配挂长螺旋钻、地下连续墙抓斗、振动桩锤等,实现多功能特点,其施工效率高,是市政建设、铁路、公路桥梁、地下连续墙、水利、防渗护坡等理想的基础施工设备。
钻头钻刃在麻花钻的重要性直接影响孔加工效果
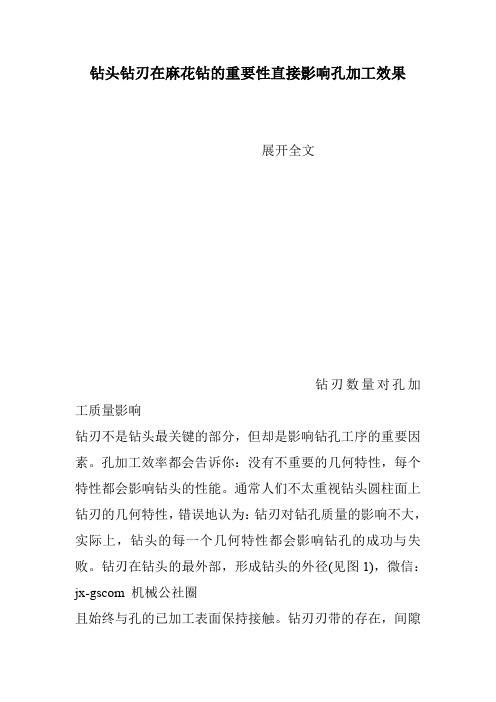
钻头钻刃在麻花钻的重要性直接影响孔加工效果展开全文钻刃数量对孔加工质量影响钻刃不是钻头最关键的部分,但却是影响钻孔工序的重要因素。
孔加工效率都会告诉你:没有不重要的几何特性,每个特性都会影响钻头的性能。
通常人们不太重视钻头圆柱面上钻刃的几何特性,错误地认为:钻刃对钻孔质量的影响不大,实际上,钻头的每一个几何特性都会影响钻孔的成功与失败。
钻刃在钻头的最外部,形成钻头的外径(见图1),微信:jx-gscom 机械公社圈且始终与孔的已加工表面保持接触。
钻刃刃带的存在,间隙形成了,这有助于控制摩擦和由摩擦产生的热量,此外,间隙还可使冷却液流入钻头刃口,进一步减少热量的产生。
钻刃刃带还有利于钻削稳定、图1 刃带形成了钻头的外径。
由刃带生成的间隙可使冷却液流入钻头刃增加钻头的强度及防止钻头粘连。
除了这些主要作用,刃带的尺寸、表面光洁度和数量还会影响钻孔的质量和加工时间。
刃带尺寸对孔加工质量的影响钻刃刃带高度不同时,会形成较大的跳动,导致加工孔的尺寸大。
钻刃刃带太宽,由此产生的较大摩擦也会导致加工孔的尺寸大;刃带太窄,钻头将不稳定,加工时容易引起摆动。
上述两种情况都会降低钻头的寿命。
如果刃带的宽度相差太大,钻削时,径向力不平衡,这时,由于刀具固有的“惰性”,钻削将顺着阻力小的方向即径向力小、刃带窄的方向进行。
钻刃刃带几何尺寸的变化对钻孔也会有影响。
刃带的锥度太大或从钻尖到柄部刃带的宽度变化太大,钻削中的压力和接触面积将发生变化,使钻头受切削力和摩擦力不均匀,导致钻削不稳定,加工孔成喇叭口或椭圆。
刃带表面质量对孔加工质量的影响如果钻头的刃带没有经过很好的的磨削,并形成圆柱面的刃带,用户就要修磨刃带,否则,钻孔时就会擦伤、拉伤或刮伤孔壁造成较差的表面光洁度。
刃带的数量对加工孔的表面光洁度、直线度、圆度均有影响。
螺旋槽和刃带越多,即接触点越多,孔加工就越稳定。
普通双槽钻头有两个对称分布的接触点或支撑点,这种结构的刀具不稳定,加工时易产生摆动,(见图2)。
深孔钻枪钻钻孔具有的优点

深孔钻枪钻钻孔具有的优点
1.在小深孔加工范畴,它几乎是唯一的最有效的刀具,长径比越大,优越性越显著。
2.生产效率高,由于转速高,所以进给量在30~180mm/min以上,而且连续进给,不需要中途退刀排屑。
3.较稳定的孔径尺寸,及孔径变化范围较小,一般可稳定地获得H9级精度的孔,在条件较好时,也可达到H8级精度
4.被加工孔表面粗糙度较高,标准钢材可达Ra1.6~0.8以下,有色金属可达Ra0.4~0.05,铸铁Ra0.8以下。
5.高的形位公差,孔圆度<0.005mm,轴线平行度<0.2mm/1000mm (要根据孔径和材料的硬度确定)
6.适应范围广,被加工材料硬度大HRC45,仍可加工。
7.刀具耐用度高,加工钢材为4~15m/刃磨一次,铸铁约为100m/刃磨一次,铝约为380m/刃磨一次。
刀头一般允许重磨10-20次,其寿命是相当可观的。
8.孔钻通后,孔口无飞边、毛刺。
钻井使用钻头分类及特点

刮刀钻头分类
1、刮刀钻头
有双翼、三翼、四翼之分(也出现过多达 十几翼的刮刀钻头,如LX10),最常用的是三翼 刮刀钻头。翼片底部有阶梯形和无阶梯形的两 种,其刃部镶焊有硬质合金或金刚石。
刮刀钻头结构
刮刀钻头由钻头体、刮刀片和喷嘴等几部 分组成。
钻头体一般采用中碳钢材料加工而成,下 端焊接刮刀刀翼,上端车有丝扣和钻柱连接。
四刀翼PDC钻头
五刀翼PDC钻头
六刀翼PDC钻头 26
5、金刚石钻头按用途分类
5.2 定向PDC钻头:(定向钻头在头 型长度和保径尺寸上比常规钻头要 短),部分定向钻头在定向工作时 受力较大的切削部位设计了减震托。 基于切削深度控制技术为基础的减 少反扭矩、稳定工具面设计是影响 定向钻头使用效果关键。
2、牙轮钻头 2.2、牙轮钻头的工作原理
牙轮钻头除了对井底岩石产生 冲击、压碎作用外,还对井底岩石 产生剪切作用。牙轮在井底滚动的 同时还产生牙齿对井底的滑动,牙 齿的滑动对井底岩石形成剪切作用 ,象刮刀钻头那样刮削井底。
3、金刚石钻头
金刚石钻头:以金刚石为工作刃,最初只用于极硬地层和研磨性大的 地层,近几年随着金刚石钻头技术的发展,其使用范围不断扩大。由于 金刚石钻头能在低钻压高转速的情况下取得高钻速和高进尺,所以在许 多钻井作业中,能取得牙轮钻头无法比拟的技术-经济优势。
(1)碰撞:刃前岩石破碎后,岩石对刀片的扭转阻力 减小,刀片向前推进,碰撞刃前岩石;
(2)压碎及小剪切:刀片在扭转力作用下压碎前方的 岩石, 使其产生小剪切破碎;
(3)扭转力增大,刀片继续挤压前方岩石,当扭转力 增大 到极限值时,岩石沿剪切面产生大剪切破碎,然后扭 转力突然减小。
碰撞、压碎及小剪切、大剪切这三个过程反复进行,形 成刮刀钻头破碎塑脆性岩石的全过程。
不同形状钻头的切削特征
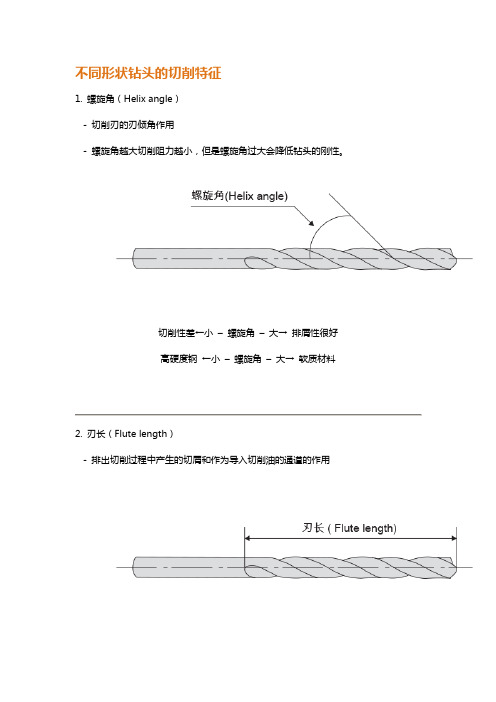
不同形状钻头的切削特征
1. 螺旋角(Helix angle)
- 切削刃的刃倾角作用
- 螺旋角越大切削阻力越小,但是螺旋角过大会降低钻头的刚性。
切削性差←小–螺旋角–大→排屑性很好
高硬度钢←小–螺旋角–大→软质材料
2. 刃长(Flute length)
- 排出切削过程中产生的切屑和作为导入切削油的通道的作用
排屑性能低←小–刃长–大→刚性差
3. 钻顶角(Point angle)
- 影响到切削性能,由工件决定角度
扭矩增加←小–钻顶角–大→扭矩减小
毛刺增多←小–钻顶角–大→毛刺减小
软质材料←小–钻顶角–大→高硬度钢
4. 钻边宽度(Margin width)
- 钻头外径与工件内径接触的部分,起到防止弯曲和引导作用。
- 主要由钻头的大小决定。
切削阻力减少←小–钻边宽度–大→切削阻力增加
引导性不够←小–钻边宽度–大→引导性良好
5. 钻腹厚度(Web)
- 形成钻头的轴心部,赋有刚性。
- 钻腹厚度较大时为降低阻力需做修磨。
切削阻力减小←小–钻腹厚度–大→切削阻力增加
刚性减小←小–钻腹厚度–大→刚性增加
排屑性良好←小–钻腹厚度–大→排屑性降低
软质材料←小–钻腹厚度–大→ 高硬度钢。
钻孔知识
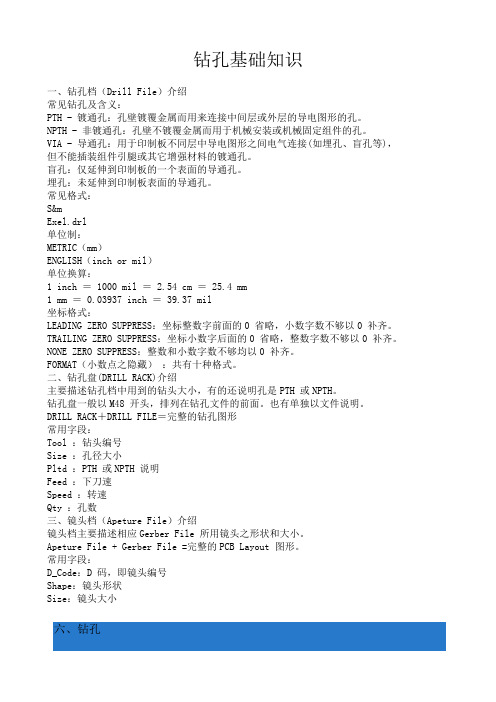
钻孔基础知识一、钻孔档(Drill File)介绍常见钻孔及含义:PTH - 镀通孔:孔壁镀覆金属而用来连接中间层或外层的导电图形的孔。
NPTH - 非镀通孔:孔壁不镀覆金属而用于机械安装或机械固定组件的孔。
VIA - 导通孔:用于印制板不同层中导电图形之间电气连接(如埋孔、盲孔等),但不能插装组件引腿或其它增强材料的镀通孔。
盲孔:仅延伸到印制板的一个表面的导通孔。
埋孔:未延伸到印制板表面的导通孔。
常见格式:S&mExel.drl单位制:METRIC(mm)ENGLISH(inch or mil)单位换算:1 inch = 1000 mil = 2.54 cm = 25.4 mm1 mm = 0.03937 inch = 39.37 mil坐标格式:LEADING ZERO SUPPRESS:坐标整数字前面的0 省略,小数字数不够以0 补齐。
TRAILING ZERO SUPPRESS:坐标小数字后面的0 省略,整数字数不够以0 补齐。
NONE ZERO SUPPRESS:整数和小数字数不够均以0 补齐。
FORMAT(小数点之隐藏):共有十种格式。
二、钻孔盘(DRILL RACK)介绍主要描述钻孔档中用到的钻头大小,有的还说明孔是PTH 或NPTH。
钻孔盘一般以M48 开头,排列在钻孔文件的前面。
也有单独以文件说明。
DRILL RACK+DRILL FILE=完整的钻孔图形常用字段:Tool :钻头编号Size :孔径大小Pltd :PTH 或NPTH 说明Feed :下刀速Speed :转速Qty :孔数三、镜头档(Apeture File)介绍镜头档主要描述相应Gerber File 所用镜头之形状和大小。
Apeture File + Gerber File =完整的PCB Layout 图形。
常用字段:D_Code:D 码,即镜头编号Shape:镜头形状Size:镜头大小六、钻孔6.1 制程目的单面或双面板的制作都是在下料之后直接进行非导通孔或导通孔的钻孔,多层板则是在完成压板之后才去钻孔。
常用的内孔加工方法与特点解析

常用的内孔加工方法与特点解析Company Document number:WTUT-WT88Y-W8BBGB-BWYTT-19998一、钻孔在模具零件上用钻头主要有两种方式:一种是钻头回转,零件固定不回转,如在普通台式钻床、摇臂钻、镗床上钻孔;另外一种方式零件回转而钻头不回转,如在车床上钻孔,这两种不同的钻孔方式所产生的误差不一样,在钻床或镗床上钻孔,由于钻头回转,使刚性不强的钻头易引偏,被加工孔的中心线偏移,但孔径不会发生变化。
钻头的直径一般不超过75mm,若钻孔大于30mm以上,通过采用两次钻销,即先用直径较小的钻头(被要求加工孔径尺寸的~倍)先钻孔,再用孔径合适的钻头进行第二次钻孔直到加工到所要求的直径。
以减小进给力。
钻头钻孔的加工精度,一般可以达到IT11~IT13级,表面粗糙度Ra为~。
二、扩孔用扩孔钻扩大零件孔径的加工方法,既可以作为精加工(铰孔、镗孔)前的预加工,也可以作为要求不高的孔径最终加工。
孔径的加工精度,一般可以达到IT10~IT13级,表面粗糙度Ra为~。
三、铰孔是用铰刀对未淬火孔进行精加工的一种孔径的加工方法。
铰孔的加工精度,一般可以达到IT6~IT10级,表面粗糙度Ra为~。
在模具制造加工中,一般用手工铰孔,其优点是切削速度慢,不易升温和产生积屑瘤,切削时无振动,容易控制刀具中心位置,因此当孔的精度要求很高时,主要用手工铰孔,或机床粗铰再用手工精铰。
在铰孔时应主要以下几点:a. 合理选择铰孔销孔余量及切削和规范;b. 铰孔刃口平整,能提高刃磨质量;c. 铰销钢材时,要用乳化液作为切削液。
四、车孔在车床上车孔,主要特征是零件随主轴回转,而刀具做进给运动,其加工后的孔轴心线与零件的回转轴线同轴。
孔的圆度主要取决于机床主轴的回转精度,孔的纵向几何形状误差主要取决于刀具的进给方向。
这种车孔方式适用于加工外圆表面与孔要求有同轴度的零件。
五、镗孔在镗床上镗孔,主要靠刀具回转,而零件做进给运动。
玉石打孔针测评
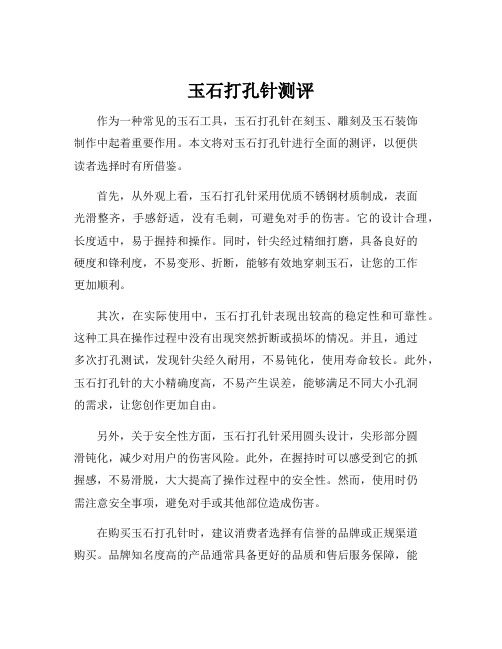
玉石打孔针测评作为一种常见的玉石工具,玉石打孔针在刻玉、雕刻及玉石装饰制作中起着重要作用。
本文将对玉石打孔针进行全面的测评,以便供读者选择时有所借鉴。
首先,从外观上看,玉石打孔针采用优质不锈钢材质制成,表面光滑整齐,手感舒适,没有毛刺,可避免对手的伤害。
它的设计合理,长度适中,易于握持和操作。
同时,针尖经过精细打磨,具备良好的硬度和锋利度,不易变形、折断,能够有效地穿刺玉石,让您的工作更加顺利。
其次,在实际使用中,玉石打孔针表现出较高的稳定性和可靠性。
这种工具在操作过程中没有出现突然折断或损坏的情况。
并且,通过多次打孔测试,发现针尖经久耐用,不易钝化,使用寿命较长。
此外,玉石打孔针的大小精确度高,不易产生误差,能够满足不同大小孔洞的需求,让您创作更加自由。
另外,关于安全性方面,玉石打孔针采用圆头设计,尖形部分圆滑钝化,减少对用户的伤害风险。
此外,在握持时可以感受到它的抓握感,不易滑脱,大大提高了操作过程中的安全性。
然而,使用时仍需注意安全事项,避免对手或其他部位造成伤害。
在购买玉石打孔针时,建议消费者选择有信誉的品牌或正规渠道购买。
品牌知名度高的产品通常具备更好的品质和售后服务保障,能够提供更好的购物体验。
此外,在使用玉石打孔针前,最好先了解相关的使用技巧和注意事项,提高使用效果。
总结而言,玉石打孔针是一种值得信赖的工具,它具备良好的外观、稳定性和安全性。
无论是刻玉、雕刻还是玉石装饰制作,都可以选用玉石打孔针来完成作品。
希望本文的测评能为选择适合的玉石打孔针提供一些指导,并帮助读者在玉石工艺创作中取得更好的效果。
空心钻头的选择原理

空心钻头的选择原理
空心钻头是一种常用于钻取混凝土、砖墙等硬质建筑材料的工具,选择适合的空心钻头需要考虑以下因素:
1. 钻头尺寸:根据需要钻取的孔径大小选择相应尺寸的钻头,一般情况下,直径较小的钻头可以更容易地控制钻孔位置和深度,但钻孔速度会较慢,直径较大的钻头则相反。
2. 钻头长度:钻头长度应根据需求钻取的深度来选择,如果钻头长度过短,无法钻到深度,会导致钻孔不完整;如果钻头长度过长,则会增加钻孔难度及不稳定性。
3. 钻头材质:不同材质的钻头适用于不同的工作场合,例如钻取混凝土时,可选择刀头经过淬炼的高速钢、钨钢合金或金刚石等材质的钻头,而钻取瓷砖、大理石等时,选择镀钛合金或碳化钨材质的钻头效果更好。
4. 钻头形状:空心钻头的形状有不同的类型,如扁平形、圆柱形、圆球形等,针对不同的孔型需求进行选择。
5. 钻孔深度:根据不同的钻孔深度选择合适的钻头,如果钻孔深度比较浅,可选择短型空心钻;如果钻孔深度较深,则需要选择针对深孔加强设计的钻头。
钻孔短刃长钻针的优势

*小结:在刃长变短的前提下,用同一参数加工同 一板材,切片分析钉头、孔粗等品质均符合要求,孔 位CPK有明显提升. 建议:试用刃长为7的钻针.
2010-04-14
12.结 论
我司选用刃长为7.0与刃长为10.0两款钻针进 行对比测试,测试证明刃长变短,并不影响钻 孔品质,且能够满足客户需求。 鉴于我司在ST0.85*7.0产品方面: ① 原料成本降低了26.8%; ② 生产成本降低了??; ③ 生产效率提高了25%; 本着双赢的原则,我司0.85价格将优惠:
2010-04-14
09.钻针制造成本差异
刃长
对比 项目
刃长10.0
刃长7.0
两者差异
单支加 工时间
钻针生 产效率
50S
40S
刃长7.0的比刃长10.0加工时 间节省10S
班产=(12小时-3) *60*60/50=720支
班产=(12小时-2) *60*60/40=900支
刃长7.0钻针的日均产量比刃 长10.0钻针的日均产量高出
对比项目刃长100刃长70两者差异工时间50s40s刃长70的比刃长100加工时间节省10s产效率班产12小时3606050720支班产12小时2606040900支刃长70钻针的日均产量比刃长100钻针的日均产量高出25孔位cpk19893211刃长70孔位明显好于刃长1002010041410
菁茂科技(姜堰)有限公司
2010-04-14
05.孔位CPK
0.85*10孔位 CPK-1.989
0.85*7孔位 CPK-3.211
2010-04-14
*说明:刃长为7的孔位CPK比10的孔位CPK高1.222。
06.孔粗、钉头
*小结:两款钻针的钉头、孔粗均在范围之内(钉头≤2.0 、孔粗≤1.0mil)
钻针与钻孔技术0531

钻针与钻孔技术一、钻针的种类钻针的种类大致分为MD型、ST型、UC型、SX型、ID型,所谓MD型它是极小径,无刃带式也就是沟背部没有内缩腹地,没有间隙部位在钻孔的过程中沟背部整个面会与孔壁磨擦接触。
早期MD型的钻针是从0.3mm以下尺寸全部为MD型,原因是早期的造针技术及设备比较没有那么好,再则早期也没有钻那么小的孔径,即使有质量也没有那么讲究,因而早期0.3mm以下的钻针好比是当样品,通常只有看的份。
往后科技发展迅速基板的要求轻薄短小,线路的密度更密,孔环变小,钻孔的孔径也随着缩小,小径化逐年缩小,它不再只是试钻样板而以,而是一种大量产化,同时也是开始要求起孔内壁质量、孔位精度等等。
为了因应这种高质量的需求,所以目前的MD型钻针是从0.15mm 以下,0.15~0.25mm都改为ST型钻针及UC型钻针TYPE。
UC型讲求的是孔内壁质量及钉头。
1、MD型钻针通常分为118度及130度,螺旋角度有26度及30度,钻径从0.05~0.25mm,刃长从1.5mm~4mm。
二阶段式的钻头把柄无刃带MD型钻针在钻孔时磨擦阻力较大,smear较易产生,孔壁较粗。
2、ST型的钻针为目前一般最常用的钻头,适用于含有纸材的线路板及环氧纸苯酚醛、BT、FR-4、CEM-3、聚亚酰胺板、复线板铁氟龙、软板及多层线路板等等。
目前市面上贩卖最普遍的ST型钻头型号是ST30,所谓ST30是表示它的螺旋角30度,适用于注重高效率,另外尚有一些如ST35及ST40它是属于高螺旋注重是高排屑性,例如纸基材系基板,它的Tg温度较低不适合高转速钻孔或是迭板厚度较厚需要排屑性较强,则可考虑使用ST35、ST40。
ST型是采Back Taper后倾锥形之尾颈部直径要比钻尖角处直径小10~25um 以减少磨擦。
沟背部位有凸出一条刃带, 从刃带处到尾颈部刃带的宽度越大与基板的孔接触面便会越大,会产生磨擦热,这便是造成smear的原因,如果刃带宽度太小(窄),对刃带的磨损会快速损耗产生针径不足或逆锥现象,而这也是smear产生的原因,尤其是钻孔数如果增加的话,钻头形成逆锥孔小会特别快。
长螺旋钻机在施工上的优势体现

桩机长螺旋钻机
当前人工操纵送钻的长螺旋钻机钻进主要是依据动力头电机的电流:当动力头电 机电流达到额定电流的90%时停止放钻,待动力头钻进一段时间,电流下降一定 值后,再次放钻,这样重复间断下放,最终成孔到指定深度。
而正弘研究的自动送钻控制是依据动力头输出功率的状态调速送钻,即速度变化基本是连 续的,不会出现大的阶跃性波动。由于长时间的人工调速控制不便,而在深度变化不大的 情况下人工调速可以在一定程度上和自动送钻类似。
因此,不管从效率还是其他的影响方面来讲,模拟自动送钻都比人工送钻具有更大的优势,如果能真正 实现自动送钻,将会带来更大的优势。
经过试验表明,在钻进相同深度的情况下,模拟送钻比传统人工送钻的时间要短。平均约快6.6s,按一根桩20m计算,每 成一根桩可以节约时间4.4分钟。
另外,传统人工送钻过程中,很多次电流都阶跃性的跳到额定电流的90%以上,且每送一次钻,桩架都产生比较大的振动。
模拟自动送钻的电流在钻进0.5m的过程中变化比较平稳,波动小,且桩架几乎没有振动。
所以本实验在深度变化不大的钻进过程中采用人为调速送钻来模拟自动送钻。
传统长螺旋钻机人工送钻时将绞车放绳速度调到最大,一次性放钻使动力头电流达到额定 电流的90%,待其电流下降到额定电流的80%再次控制液压绞车下放动力头,如此反复循环。
人工调速模拟自动送钻采取调节下放速度到使动力头电流稳定在额定电流的85%左右。
钻针,铣刀介绍

銑刀加工示意
名稱
前角(Rake angle)
圖示
應用
銑刀的加工方式為正角切削, 且分為單齒數與雙齒數,所 切削的振動方式也不同 單齒數振動較佳 雙齒數會有共振的狀況
S-轉速 F-移動速 進刀量 R-退刀速 I-下刀速 N-距離 板材 板材厚度 疊板數 EM-蓋板 BM-墊板 P-穿透度 TIR-偏擺 成型機 量測辨法
Number of hits PWB
PWD Thickness [mm] Layer count
Stack heights [pcs] Entry board [mm] Backup board [mm] Depth into backer [mm] Spindle run out [μm] Drilling machine
鑽頭各部名稱與功能2
名稱
鑿角(Chisel angle)
圖示
應用
負角切削,影嚮銅箔的纏留影嚮缺角 一般角度:145 ˚、磨損與缺角並重
鑽尖角鑽孔過程圖示
鑽頭各部名稱與功能3
名稱
心厚(Web Thickness)
圖示
逃隙直徑(Relief Dia.)
應用
心厚大小影嚮鑽孔的孔位與孔品質和缺角 心厚大剛性強,孔位佳,但孔壁差,缺角佳 心厚小剛性弱、孔位差,但孔品質佳,缺角大 心厚大小也會影嚮鑽針的外徑磨損
減少與孔壁的接觸,過長使得 鑽孔熱多,過短鑽頭磨損較大
鑽頭各部名稱與功能5
名稱
後端直徑(UC Dia.)
頸部長(Step length )
圖示
應用
UC鑽徑大會使得鑽頭逃熱不佳 UC徑小會使得鑽針剛性不足易斷針
鑽頭應力分散,可以減少斷針率
鑽柄前導角(Chamfer)
螺旋面钻尖的性能分析
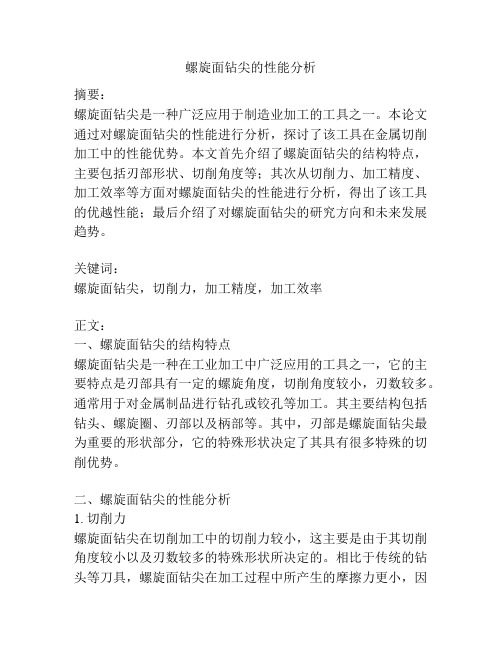
螺旋面钻尖的性能分析摘要:螺旋面钻尖是一种广泛应用于制造业加工的工具之一。
本论文通过对螺旋面钻尖的性能进行分析,探讨了该工具在金属切削加工中的性能优势。
本文首先介绍了螺旋面钻尖的结构特点,主要包括刃部形状、切削角度等;其次从切削力、加工精度、加工效率等方面对螺旋面钻尖的性能进行分析,得出了该工具的优越性能;最后介绍了对螺旋面钻尖的研究方向和未来发展趋势。
关键词:螺旋面钻尖,切削力,加工精度,加工效率正文:一、螺旋面钻尖的结构特点螺旋面钻尖是一种在工业加工中广泛应用的工具之一,它的主要特点是刃部具有一定的螺旋角度,切削角度较小,刃数较多。
通常用于对金属制品进行钻孔或铰孔等加工。
其主要结构包括钻头、螺旋圈、刃部以及柄部等。
其中,刃部是螺旋面钻尖最为重要的形状部分,它的特殊形状决定了其具有很多特殊的切削优势。
二、螺旋面钻尖的性能分析1. 切削力螺旋面钻尖在切削加工中的切削力较小,这主要是由于其切削角度较小以及刃数较多的特殊形状所决定的。
相比于传统的钻头等刀具,螺旋面钻尖在加工过程中所产生的摩擦力更小,因此在加工质量和工具耐用性上都有着显著的提升。
2. 加工精度螺旋面钻尖在加工过程中拥有更高的加工精度,其主要原因是在切削过程中产生的刷屑排出更加容易,不会形成刷屑的垂直振动。
另外,螺旋面钻尖具有较小的切削角度,因此成孔精度也得到了提高。
3. 加工效率相比于传统工具,螺旋面钻尖在加工过程中具有更高的加工效率。
其主要原因是由于刃部的特殊结构,拉切的刃数较多,加工时产生的热量更为均匀分散,因此在所需切削深度相同时,螺旋面钻尖能够更快速的完成加工过程。
三、螺旋面钻尖的未来发展趋势虽然螺旋面钻尖已经成为了当前金属切削加工领域中广泛使用的工具之一,但是其还有很多需要发展完善的方向。
例如,螺旋面钻尖的刃部结构、材质以及涂层等方面,都有待于进一步研究和优化。
可以预期的是,随着科技的进步和加工技术的不断提高,螺旋面钻尖在未来的发展中将会有着更加广泛的应用领域。
钻孔及其工艺特点

钻孔及其工艺特点
用钻头在工件实体部位加工孔称为钻孔。
钻孔属粗加工,可达到的尺寸公差等级为IT1 3~IT11,表面粗糙度值为Ra50~12.5μm。
由于麻花钻长度较长,钻芯直径小而刚性差,又有横刃的影响,故钻孔有以下工艺特点:
1.钻头容易偏斜。
由于横刃的影响定心不准,切入时钻头容易引偏;且钻头的刚性和导向作用较差,切削时钻头容易弯曲。
在钻床上钻孔时,如图7-2a所示,容易引起孔的轴线偏移和不直,但孔径无显著变化;在车床上钻孔时,如图7-2b 所示,容易引起孔径的变化,但孔的轴线仍然是直的。
因此,在钻孔前应先加工端面,并用钻头或中心钻预钻一个锥坑,如图7-3所示,以便钻头定心。
钻小孔和深孔时,为了避免孔的轴线偏移和不直,应尽可能采用工件回转方式进行钻孔。
2.孔径容易扩大。
钻削时钻头两切削刃径向力不等将引起孔径扩大;卧式车床钻孔时的切入引偏也是孔径扩大的重要原因;此外钻头的径向跳动等也是造成孔径扩大的原因。
3.孔的表面质量较差。
钻削切屑较宽,在孔内被迫卷为螺旋状,流出时与孔壁发生摩擦而刮伤已加工表面。
4.钻削时轴向力大。
这主要是由钻头的横刃引起的。
试验表明,钻孔时50%的轴向力和15%的扭矩是由横刃产生的。
因此,当钻孔直径d﹥30mm时,一般分两次进行钻削。
第一次钻出(0.5~0.7)d,第二次钻到所需的孔径。
由于横刃第二次不参加切削,故可采用较大的进给量,使孔的表面质量和生产率均得到提高。
- 1、下载文档前请自行甄别文档内容的完整性,平台不提供额外的编辑、内容补充、找答案等附加服务。
- 2、"仅部分预览"的文档,不可在线预览部分如存在完整性等问题,可反馈申请退款(可完整预览的文档不适用该条件!)。
- 3、如文档侵犯您的权益,请联系客服反馈,我们会尽快为您处理(人工客服工作时间:9:00-18:30)。
2010-04-14
05.孔位CPK
0.85*10孔位 CPK-1.989
0.85*7孔位 CPK-3.211
2010-04-14
*说明:刃长为7的孔位CPK比10的孔位CPK高1.222。
06.孔粗、钉头
*小结:两款钻针的钉头、孔粗均在范围之内(钉头≤2.0 、孔粗≤1.0mil)
2010-04-14
2010-04-14
09.钻针制造成本差异
刃长
对比 项目
刃长10.0
刃长7.0
两者差异
单支加 工时间
钻针生 产效率
50S
40S
刃长7.0的比刃长10.0加工时 间节省10S
班产=(12小时-3) *60*60/50=720支
班产=(12小时-2) *60*60/40=900支
刃长7.0钻针的日均产量比刃 长10.0钻针的日均产量高出
*小结:在刃长变短的前提下,用同一参数加工同 一板材,切片分析钉头、孔粗等品质均符合要求,孔 位CPK有明显提升. 建议:试用刃长为7的钻针.
2010-04-14
12.结 论
我司选用刃长为7.0与刃长为10.0两款钻针进 行对比测试,测试证明刃长变短,并不影响钻 孔品质,且能够满足客户需求。 鉴于我司在ST0.85*7.0产品方面: ① 原料成本降低了26.8%; ② 生产成本降低了??; ③ 生产效率提高了25%; 本着双赢的原则,我司0.85价格将优惠:
0.05~0.1
=9~18次
小结:刃长为7的钻针,以上假设条件下使用,研 磨次数至少可满足客户使用>8次。
2010-04-14
11. 小结
测试结果:
1.孔位:刃长7.0的钻针(3.211)好于刃长10.0的钻针 (1.989);
2.孔粗、钉头:两款钻针的孔粗、钉头值均在客户 要求范围之内; 3.推算钻针研磨次数至少可满足客户使用>8次。
07.两款钻针实物对比
7
10
0.85x7
0.85x10
2010-04-14
08.原料性价比
规格 碳化钨总长 (mm) 切断长度 (mm) 切断数量 (支) 价格差异 (RMB/支)
0.85*10(原)
237 237
15.5 11.7
14 19
0.41 0.30
0.85*7(现)
说明:刃长为7的比10的原料价格降低了26.8%
菁茂科技(姜堰)有限公司
GINAL TECHNOLOGY(JIANGYAN) CO., LTD.
刃长10.0与7.0 对比测试
2010-04-14
目 录
01.两款钻针参数对比 02.测试目的 03.钻孔参数 04.叠板、机台 05.孔位CPK 06.孔粗、钉头切片 07.两款钻针实物对比 08.钻针原料性价比 09.钻针制造成本差异 10.推算使用研次 11.小结 12.结论
2010-04-14
谢谢!
2010-04-14
25%
孔位CPK
1.989
3.211
刃长7.0孔位明显 好于刃长10.0
2010-04-14
10.推算使用研次
使用ST0.85 刃长7的钻针加工,推算使用研次
假设钻孔条件: 1.刃长——7.0mm 2.叠板——1.6mm*3片/叠, 3.铝片——0.2mm; 4.下钻深度——0.3mm; 5.排屑空间——0.8mm; 6.研磨量——0.05~0.1mm/次。 使用研次=刃长-(铝片+PCB板厚*叠片数+下钻深度+排屑空间) 每次研磨量 =7-(0.2+1.6*3+0.3+0.8)
2010-04-14
01.两种刃长钻针参数对比
*两款钻针除刃长不同 外,其余参数皆一样.
2010-04-14
02. 测试目的
对比测试刃长10.0和刃长7.0 对钻孔的影响
刃长:原——10.0、现——7.0Βιβλιοθήκη 1.孔位精度2.孔粗
3.钉头
2010-04-14
03.钻孔参数
2010-04-14
04.机台、叠板