机制工艺答疑
机制工艺学习题
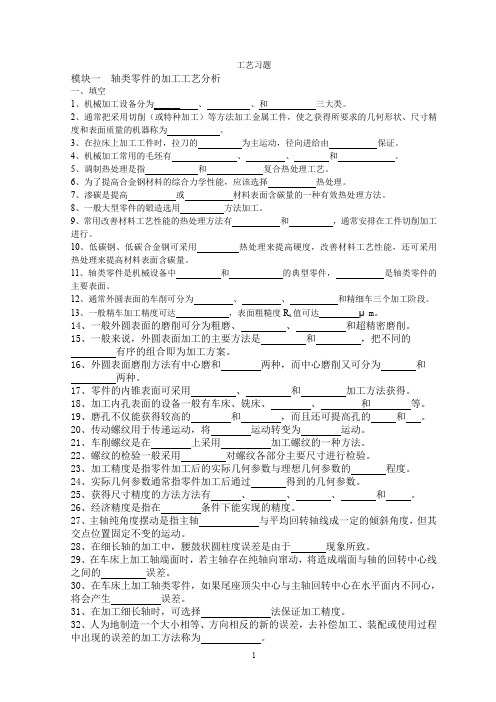
工艺习题模块一轴类零件的加工工艺分析一、填空1、机械加工设备分为______ 、、和三大类。
2、通常把采用切削(或特种加工)等方法加工金属工件,使之获得所要求的几何形状、尺寸精度和表面质量的机器称为。
3、在拉床上加工工件时,拉刀的为主运动,径向进给由保证。
4、机械加工常用的毛坯有、、和。
5、调制热处理是指和复合热处理工艺。
6、为了提高合金钢材料的综合力学性能,应该选择热处理。
7、渗碳是提高或材料表面含碳量的一种有效热处理方法。
8、一般大型零件的锻造选用方法加工。
9、常用改善材料工艺性能的热处理方法有和,通常安排在工件切削加工进行。
10、低碳钢、低碳合金钢可采用热处理来提高硬度,改善材料工艺性能,还可采用热处理来提高材料表面含碳量。
11、轴类零件是机械设备中和的典型零件,是轴类零件的主要表面。
12、通常外圆表面的车削可分为、、和精细车三个加工阶段。
13、一般精车加工精度可达,表面粗糙度R a值可达μm。
14、一般外圆表面的磨削可分为粗磨、、和超精密磨削。
15、一般来说,外圆表面加工的主要方法是和,把不同的有序的组合即为加工方案。
16、外圆表面磨削方法有中心磨和两种,而中心磨削又可分为和两种。
17、零件的内锥表面可采用、和加工方法获得。
18、加工内孔表面的设备一般有车床、铣床、、和等。
19、磨孔不仅能获得较高的和,而且还可提高孔的和。
20、传动螺纹用于传递运动,将运动转变为运动。
21、车削螺纹是在上采用加工螺纹的一种方法。
22、螺纹的检验一般采用对螺纹各部分主要尺寸进行检验。
23、加工精度是指零件加工后的实际几何参数与理想几何参数的程度。
24、实际几何参数通常指零件加工后通过得到的几何参数。
25、获得尺寸精度的方法方法有、、、和。
26、经济精度是指在条件下能实现的精度。
27、主轴纯角度摆动是指主轴与平均回转轴线成一定的倾斜角度,但其交点位置固定不变的运动。
28、在细长轴的加工中,腰鼓状圆柱度误差是由于现象所致。
机制工艺选择题

机制工艺选择题测试卷1.型砂抵抗外力破坏的能力称为()A.韧性;B.强度;C.硬度;D.塑性;2.在铸型中,主要起补缩作用的是()A.浇口杯;B.直浇道;C.冒口;D.内浇道;3.防止铸件产生裂纹的基本方法之一是()A.提高型砂质量;B.提高浇注温度;C.使铸件壁厚均匀;4.离心铸造适用于()的铸件。
A.形状复杂;B.大型;C.旋转体;5.当坯料的质量不好,加热不正确,锻造温度过低,锻件冷却不当时,产生的缺陷是()。
A.裂纹;B.折叠;C.夹层;D.错移;6.可锻造的金属材料有()。
A.碳素钢;B.可锻铸铁;C.灰铸铁;7.金属锻造加工的重要环节为()A.加热;B.预热;C.保温;D.冷却;8.水压机适用于生产锻件类型是()A.小型;B.中型;C.大型;9.自由锻冲孔时,为便于从坯料中取出冲子,应在冲孔位置加一些()。
A.煤粉;B.石英粉;C.木屑;D.石墨份;10.气割时要求金属材料的燃点()熔点。
A.低于;B.高于;C.等于;11.下列金属材料能满足气割要求的是()A.铸铁;B.铜;C.铝;D.低碳钢;12.金属燃烧后生成的氧化物的熔点应该()金属本身的熔点。
A.低于;B.高于;C.等于;13.会削弱焊件结构强度和减小结构承载能力的焊接缺陷是()。
A.气孔;B.咬边;C.裂纹;14.在正交平面上测量的角度有()。
A.刃倾角;B.主偏角;C.前角;15.消耗功率最多、作用在切削速度方向上的分力是()。
A.切削力;B.背向力;C.进给力;16.将工件上的被切削层转化成切屑所需的运动是()。
A.主运动;B.进给运动;C.旋转运动;17.对总切削力影响最大的是()。
A.工件材料;B.吃刀量;C.刀具角度;18.在切削加工中,主运动通常只有()。
A.一个;B.二个;C.三个;19.切削时,刀具上与工件加工表面相对应的面是()。
A.前面; B.主后面; C.副后面;20.在生产率相同条件下,为减小对加工的不利影响,应设法尽可能地减小()。
机制工艺简答题

2)可采用普通机床和单工序专用机床,工艺装备简单,调整方便, 操作工人易于掌握,生产准备工作量小,容易适应产品 更换。
3)工序数目多,相应的设备数量和工人数量多,生产场地面积大, 工艺路线长,使生产计划工作比较复杂。
单件小批生产,应尽量选择通用夹具。 大批量生产,应选择生产率和自动化程度高的专用夹具。 多品种中、小批生产可选用可调夹具或组合夹具。 2) 刀具的选择原则 一般应选用标准刀具,必要时可选择各种高生产率的复合刀具 及其它 一些专用刀具。刀具的类型、规格及精度应与工件的加工要求 相适应。 3) 量具的选择原则 单件、小批生产应选择通用量具。选量具的量程和精度要与工 件的尺寸 和精度相适应。 大批量生产应尽量选择效率高的专用量具。 35.简述影响加工精度的因素有哪些? 答题时间5分 难易程度2 标准答案 1) 工艺系统的几何误差包括加工方法的原理误差、机床的几何
主轴经向跳动在车外圆时,该误差将以1:1的关系转化 为加工误差。当其跳动频率与主轴转速一致时,将使加 工后的圆柱与基准圆柱面产生同轴度误差,横截面产生 圆度误差。 37.简述车床导轨的直线误差敏感方向及在车外圆时产生何种加工误 差? 答题时间5分 难易程度3 标准答案 误差敏感方向为机床导轨的水平面。 导轨水平面内的直线度误差使车刀在被加工外圆的法线 方向产生位移(∆y),造成外圆面的径向尺寸误差。当 车削长外圆时,则产生圆柱度误差。 38.简述减小工艺系统受力变形的主要措施及常用方法(或举例)。 答题时间8分 难易程度2 标准答案 (1) 提高接触刚度。常用方法是改善机床部件主要零件接 触面的配合质量。(例如对机床导轨及装配基面进行 刮研;提高顶尖锥体同主轴和尾座套筒锥孔的接触质 量,多次修研加工精密零件用的中心孔等)。 提高接触刚度的另一措施是在接触面间预加载荷。(例如对 角接触轴承的预紧)。 (2) 提高工件、部件刚度。常用方法是减小支承间的长 度。(例如设置辅助支承、安装跟刀架或中心架。) (3) 采用合理的装夹方法。(例如在装夹薄壁套筒类零件 时,用加大三爪夹盘的接触面积或用开口垫套等)。 39.简答提高加工精度的工艺措施。各举一例说明。 答题时间8分 难易程度3
《机制工艺》期中试卷
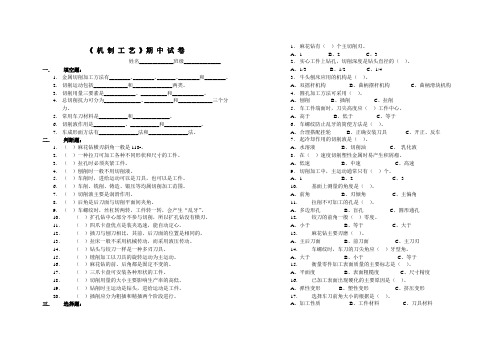
《机制工艺》期中试卷姓名_____________班级______________ 一.填空题:1.金属切削加工方法有________、________、_______、________和________。
2.切削运动包括_____________和_______________两类。
3.切削用量三要素是____________、__________和____________。
4.总切削抗力可分为______________、___________和_____________三个分力。
5.常用车刀材料是___________和______________。
6.切削液作用是____________、___________和______________。
7.车成形面方法有_______________法和_______________法。
二.判断题:1.()麻花钻横刃斜角一般是118o。
2.()一种拉刀可加工各种不同形状和尺寸的工件。
3.()拉孔时必须夹紧工件。
4.()刨削时一般不用切削液。
5.()车削时,进给运动可以是刀具,也可以是工件。
6.()车削、铣削、铸造、锻压等均属切削加工范围。
7.()切削液主要是润滑作用。
8.()后角是后刀面与切削平面间夹角。
9.()车螺纹时,丝杠转两转,工件转一转,会产生“乱牙”。
10.()扩孔钻中心部分不参与切削,所以扩孔钻没有横刃。
11.()四爪卡盘优点是装夹迅速,能自动定心。
12.()插刀与刨刀相比,其前、后刀面的位置是相同的。
13.()拉床一般不采用机械传动,而采用液压传动。
14.()钻头与铰刀一样是一种多刃刀具。
15.()镗削加工以刀具的旋转运动为主运动。
16.()麻花钻的前、后角都是固定不变的。
17.()三爪卡盘可安装各种形状的工件。
18.()切削用量的大小主要影响生产率的高低。
19.()钻削时主运动是钻头,进给运动是工件。
20.()插削应分为粗插和精插两个阶段进行。
机制工艺习题

1-1 铸造基础一、填空题1、铸造所得到的金属工件或毛坯称为。
2、按生产方法不同,铸造可分为和两大类。
3、铸造组织,晶粒,铸件的力学性能特别是冲击韧度,铸件质量不。
4、铸件被广泛应用于机械零件的制造。
二、判断题1、将熔融金属浇注、压射或吸入铸型型腔中,待其凝固后而得到一定形状和性能铸件的方法称为铸造。
2、铸件内部易产生缩孔、缩松、气孔等缺陷,会导致铸件的力学性能特别是冲击韧度低,铸造质量不够稳定。
3、铸件的力学性能特别是冲击韧度低,但铸件质量很稳定。
4、由于铸造易产生缺陷,性能不高,因此多用于制造承受应力不大的工件。
5、铁液包、钢液包和灼热件起重作业影响范围内不得设置休息室、更衣室和人行通道,不得存放危险物品,地面应保持干燥。
6、液态金属、高温材料运输设备要设置耐热温、防喷溅设施,不得在有易燃、易爆物质的区域停留,离开厂区的应当发出警报信号。
7、铸件可以直接着地,工具分类装入工具箱中,化学品需放入专用箱内并盖好。
三、选择题1、下列不属于特种铸造的是【】A、压力铸造B、金属型铸造C、砂型铸造D、熔模铸造2、关于铸造,下列说法错误的是【】A、铸造可以生产出形状复杂,特别是具有复杂外腔的工作毛坯B、产品的适应性广,工艺灵活性大,工业上常用的金属材料均可用来进行铸造,铸件的质量可由几克到几百吨C、原材料大都来源广泛,价格低廉,并可直接利用废旧软件,故铸件成本较低D、铸造组织疏松,晶粒粗大,内部易产生缩孔、缩松、气孔等缺陷四,简答题铸造有哪些特点?五,应用题1,铸造加工的安全文明生产有哪些要求?1-2 砂型铸造一,填空题1、用来形成铸型的工艺装备称为模样,按其使用特点可分为模样和模样两大类。
2、砂型铸造中采用的是模样。
3、用来制造型芯的工艺装备称为。
4、在砂型铸造中,型(芯)砂的基本原材料是和型砂。
5、砂型铸造件的外形取决于型砂的,造型方法有造型和造型两种。
6、紧砂的方法常用的有法、法,法等。
7、整模造型的挖砂造型的模样都是的,但整模造型铸件的分型面为,挖砂造型铸件的分型面为。
复习思考题二 零件成形工艺(机制11)

复习二 零件成形工艺 第一篇 铸造一、基本概念充型能力、收缩、缩孔和缩松、热应力、机械应力、定向凝固(顺序凝固)、同时凝固、浇不足、冷隔、砂型铸造、浇注位置、分型面、机械加工余量、拔模斜度、特种铸造、金属型铸造、压力铸造、离心铸造、熔模铸造、结构斜度。
二、基本知识点1、液态合金的充型能力对铸件质量的影响2、影响液态金属充型能力的因素3、合金的收缩阶段及其对铸件质量的影响4、造型方法的种类、特点及应用5、浇注位置的选择(以保证铸件质量为主):6、分型面的选择(以简化造型工艺为主)7、常用特种铸造的种类、特点及应用8、铸造工艺对铸件结构的要求(主要考虑简化工艺,涉及铸件的外形和内腔的设计) 9、合金铸造性能对铸件结构的要求三、复习思考题1、零件、铸件和模样三者在形状、尺寸上有何不同?2、什么是铸件的结构斜度?它与起模斜度有何不同?图示铸件的结构是否合理?应如何改正?3、 分析图示的两种铸件结构,说明其合理性。
4、分析图示的四种铸件应采用何种手工造题2图 分型面型芯型芯题3图型方法?并确定它们的分型面和浇注位置。
第三篇 压力加工一、基本概念滑移、加工硬化、再结晶、冷变形、热变形、纤维组织、锻造性(可锻性)、敷料(余块)、分模面、冲裁、落料、冲孔、拉深、拉深系数、翻边、翻边系数二、基本知识点1、单晶体的塑性变形形式及特点2、多晶体塑性变形形式及特点:3、冷、热变形对金属组织和性能的影响:4、金属锻造性的衡量指标及影响锻造性的因素:4、常用锻造方法的种类、特点及应用:5、绘制锻件图时应考虑的因素6、模膛的种类及作用7、板料冲压的基本工序(定 义、应注意的问题) 8、轧制、挤压和拉拔的定 义、种类及作用9、压力加工件的设计原则三、复习思考题1、用模锻方法锻出图1中带孔的锻件,请指出合理的分模面,并说明其余分模面不合理的理由。
2、图2为2mm 厚的Q235-A 钢板冲压件,试说明冲制过程。
3、图3所示锻件结构是否适合于自由锻造的工艺要求?试修改不合适的部位。
机制工艺作业习题

机械加工工艺规程设计作业题:l-10 根据六点定位原理分析图1–92各图的定位方案并判断各定位元件分别限制了哪些自由度?1-18 图1-96所示小轴系大量生产,毛坯为热轧棒料,经过粗车、精车、淬火、粗磨、精磨后达到图纸要求。
现给出各工序的加工余量及工序尺寸公差如表1-27。
毛坯的尺寸公差为±1.5mm。
试计算各工序尺寸,标注工序尺寸公差,计算精磨工序的最大余量和最小余量。
1-20在图1-97所示工件中,315.03025.02025.005.01,20,60,70L L mm L mm L mm+--===不便直接测量,试重新给出测量尺寸,并标注该测量尺寸的公差。
l-21 某齿轮零件,其轴向设计尺寸如图1-99所示,试根据下述工艺方案标注各工序尺寸的公差:1.车端面l 和端面4;2.以端面l 为轴向定位基准车端面3;直接测量端面4和端面3之间的距离;3.以端面4为轴向定位基准车端面2,直接测量端画l 和端面2之间的距离(提示:属公差分配问题)。
1-23 图1-100所示小轴的部分工艺过程为:车外圆至φ30.5-0.1mm ,铣键槽深度为H +TH,热处理,磨外圆至mm 036.0015.030++φ。
设磨后外圆与车后外圆的同度公差为φ0.05mm,求保证键槽深度为4+0.2mm 的铣槽深度H +TH 。
讨论题:1-5某机床厂年产CA6140车床2000台,已知机床主轴的备品率为14%,机械加工[废品率为4%,试计算机床主轴的年生产纲领并说明属于何种生产类型,工艺过程有何特点?若一年工作日为282天,试计算每月(按26天计算)的生产批量。
1-6 试分析图1-90所示零件有哪些结构工艺性问题并提出正确的改进意见。
l-9 在图l-91中,注有加工符号的表面为待加工表面,试分别确定应限制的自由度。
l-12 图1-93为车床主箱体的一个视图,图中Ⅰ孔为主轴孔,是重要孔,加工时希望加工余量均匀。
试选择加工主轴孔的粗、精基准。
机制工艺学

填空题1.制造系统由物质流、能量流和信息流组成,物质流是本质,能量流是动力,信息流是控制。
2.人类的制造技术可分为三个阶段,手工业生产阶段,大工业生产阶段和虚拟现实工业生产阶段。
3.从材料成形机理来分类,加工工艺分为去除加工、结合加工和变形加工。
4.制造的范畴从过去的设计、加工和装配发展为产品的全生命周期,包括需求分析、设计、制造、运输、使用和报废等。
5.机械加工工艺过程由若干个工序组成,机械加工的每一个工序又可细分为安装、工位、工步和走刀。
6.工件在机床或夹具中的装夹主要有夹具中装夹、直接找正装夹、划线找正装夹三种方法。
7.工件以内孔定位常用的定位元件有刚性心轴和定位销两种。
8.加工主轴零件时为了确保支承轴颈和内锥孔的同轴度要求,通常采用互为基准原则来选择定位基面。
9.为减少误差复映,通常采用的方法有:提高毛坯制造精度、提高工艺系统刚度、多次加工。
10.机床夹具最基本的组成部分是定位元件、夹紧装置和夹具体。
11.机床主轴的回转误差分为轴向跳动、径向跳动、角度摆动。
12.生产中最常用的正确的定位方式有完全定位和不完全定位两种。
13.选择精基准应遵循以下四个原则,分别是重合基准、统一基准、自为基准、互为基准。
14.确定零件加工工艺方案的一般原则包括质量第一、效益优先、效率争先。
15.工艺基准分为定位基准、工序基准、测量基准和装配基准。
16.由于毛坯存在形状误差,工件加工后调整法加工表面的形状误差与毛坯相似,其比值ε=∆工/∆毛小于1,这一现象称为误差复映。
17.锥度心轴限制四个自由度,小锥度心轴限制五个自由度。
18.对那些精度要求很高的零件,其加工阶段可以划分为:粗加工阶段,半精加工阶段,精加工阶段,光整加工阶段。
19.拉孔,推孔,珩磨孔,铰孔,浮动镗刀块镗孔等都是自为基准加工的典型例子。
20.尺寸链的特征是关联性和封闭性。
21.为了改善切削性能而进行的热处理工序如退火、正火、调质等,应安排在切削加工之前。
机制工艺学复习题
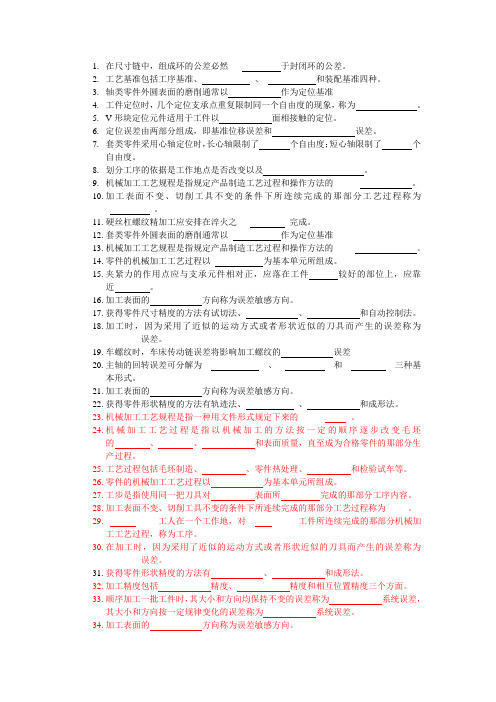
1.在尺寸链中,组成环的公差必然___ _于封闭环的公差。
2.工艺基准包括工序基准、、和装配基准四种。
3.轴类零件外圆表面的磨削通常以作为定位基准4.工件定位时,几个定位支承点重复限制同一个自由度的现象,称为。
5.V形块定位元件适用于工件以面相接触的定位。
6.定位误差由两部分组成,即基准位移误差和误差。
7.套类零件采用心轴定位时,长心轴限制了个自由度;短心轴限制了个自由度。
8.划分工序的依据是工作地点是否改变以及。
9.机械加工工艺规程是指规定产品制造工艺过程和操作方法的_______ 。
10.加工表面不变、切削工具不变的条件下所连续完成的那部分工艺过程称为___ 。
11.硬丝杠螺纹精加工应安排在淬火之____ ____完成。
12.套类零件外圆表面的磨削通常以作为定位基准13.机械加工工艺规程是指规定产品制造工艺过程和操作方法的_______ 。
14.零件的机械加工工艺过程以为基本单元所组成。
15.夹紧力的作用点应与支承元件相对正,应落在工件较好的部位上,应靠近。
16.加工表面的方向称为误差敏感方向。
17.获得零件尺寸精度的方法有试切法、、和自动控制法。
18.加工时,因为采用了近似的运动方式或者形状近似的刀具而产生的误差称为________误差。
19.车螺纹时,车床传动链误差将影响加工螺纹的误差20.主轴的回转误差可分解为___ ___、___ ___和___ ____三种基本形式。
21.加工表面的方向称为误差敏感方向。
22.获得零件形状精度的方法有轨迹法、、和成形法。
23.机械加工工艺规程是指一种用文件形式规定下来的_______ _。
24.机械加工工艺过程是指以机械加工的方法按一定的顺序逐步改变毛坯的、、和表面质量,直至成为合格零件的那部分生产过程。
25.工艺过程包括毛坯制造、、零件热处理、和检验试车等。
26.零件的机械加工工艺过程以为基本单元所组成。
27.工步是指使用同一把刀具对表面所完成的那部分工序内容。
机制工艺学判断题
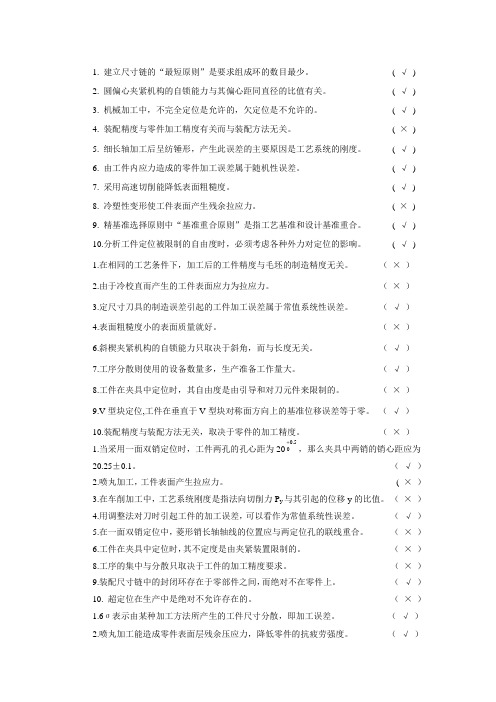
1. 建立尺寸链的“最短原则”是要求组成环的数目最少。
( √)2. 圆偏心夹紧机构的自锁能力与其偏心距同直径的比值有关。
( √)3. 机械加工中,不完全定位是允许的,欠定位是不允许的。
( √)4. 装配精度与零件加工精度有关而与装配方法无关。
( ×)5. 细长轴加工后呈纺锤形,产生此误差的主要原因是工艺系统的刚度。
( √)6. 由工件内应力造成的零件加工误差属于随机性误差。
( √)7. 采用高速切削能降低表面粗糙度。
( √)8. 冷塑性变形使工件表面产生残余拉应力。
( ×)9. 精基准选择原则中“基准重合原则”是指工艺基准和设计基准重合。
( √)10.分析工件定位被限制的自由度时,必须考虑各种外力对定位的影响。
( √)1.在相同的工艺条件下,加工后的工件精度与毛坯的制造精度无关。
(×)2.由于冷校直而产生的工件表面应力为拉应力。
(×)3.定尺寸刀具的制造误差引起的工件加工误差属于常值系统性误差。
(√)4.表面粗糙度小的表面质量就好。
(×)6.斜楔夹紧机构的自锁能力只取决于斜角,而与长度无关。
(√)7.工序分散则使用的设备数量多,生产准备工作量大。
(√)8.工件在夹具中定位时,其自由度是由引导和对刀元件来限制的。
(×)9.V型块定位,工件在垂直于V型块对称面方向上的基准位移误差等于零。
(√)10.装配精度与装配方法无关,取决于零件的加工精度。
(×)1.当采用一面双销定位时,工件两孔的孔心距为20005.,那么夹具中两销的销心距应为20.25±0.1。
(√)2.喷丸加工,工件表面产生拉应力。
( ×)3.在车削加工中,工艺系统刚度是指法向切削力P y与其引起的位移y的比值。
(×)4.用调整法对刀时引起工件的加工误差,可以看作为常值系统性误差。
(√)5.在一面双销定位中,菱形销长轴轴线的位置应与两定位孔的联线重合。
机制工艺问答题集

机制工艺问答题集1、什么是浇注系统?它有哪几部分组成?它们各起什么作用?答:浇注系统是为填充型腔和冒口而开设于铸型中的一系列通道。
组成:浇口杯、直浇道、横浇道、内浇道。
作用:浇口杯——缓和熔融金属对铸型的冲击,并使熔渣、杂质上浮,起挡渣作用。
直浇道——调节熔融金属流入型腔的速度和压力。
直浇道越高,流速越快,压力越大,熔融金属越容易充满型腔的狭薄部分。
横浇道——分配熔融金属流入内浇道,也起挡渣作用。
内浇道——控制熔融金属的流动速度和方向。
2、试述铸件常见缺陷及其产生的原因答:(1)气孔:造型材料水分过多或含有大量的发气物质,砂型、型心的透气性差,浇注速度过快。
(2)缩孔:铸件在凝固过程中收缩得不到足够熔融金属的补充,即由于补缩不良造成。
(3)砂眼:型砂强度不够或紧实度不够,以及浇注速度太快。
(4)粘砂:型砂耐火性差或浇注温度过高。
(5)裂纹:铸件壁厚相差大,浇注系统开设不当、砂型与型心退让性差。
3、铸造有哪些优点?答:(1)可获得复杂外形及内腔的铸件。
(2)铸件尺寸与质量不受限制。
(3)可铸造任何金属和合金铸件。
(4)成本低廉。
(5)铸件形状、尺寸与零件很接近。
4、特种铸造有哪些?分别有何特点?用于什么场合?答:(1)金属型铸造:金属型可多次使用,铸件形状精确,尺寸精度高,表面粗糙度小力学性能好,生产率高,制造成本高。
主要用于非铁合金铸件的大批量生产,铸件不宜过大,形状不能太复杂,壁不能太薄。
(2)压力铸造:铸件质量高于砂型或金属型铸造,生产率高。
用于铸造形状复杂的薄壁铸件。
(3)离心铸造:不需浇注系统,设备投资少,效率高。
主要用于铸造空心回转体和双层金属衬套、轴瓦。
(4)熔模铸造:可铸造形状很复杂的铸件,精度高,表面粗糙度值小,适应性广,但生产工艺复杂,周期长,成本高。
铸件质量不能太大。
主要用于铸造各种形状复杂的精密小型零件的毛坯,如汽轮机和航空发动机的叶片等。
5、试述砂型铸造的工艺过程答:造型——造心——烘干(用于干砂型铸造)——合型——浇注——落砂——清理及检验6、锻造前加热的目的是什么?如何确定坯料的加热速度?答:金属加热目的是为了提高其塑性,降低变形抗力,并使内部组织均匀。
机制技术习题解答工艺尺寸链计算

Σ δ Li=δ L6=0.2
δ L3=0.2,即:δ L3=Σ δ Li=0.2 ⑷、结果:计算正确, L6δ L6= 10
0 +0.2
工艺尺寸链计算
习题十一 工序尺寸链计算
解:定位方案比较: 定位方案1:工序尺寸为 L4δ L4=40+0.05+0.05 定位方案2:工序尺寸为 L δ L5=20 0
-0.1
10
+0.2
0
工艺尺寸链计算
习题十一 工序尺寸链计算
解:以工件孔内端面B定位时,其工序尺寸为L6。 ⑴、建立尺寸链
L3 L6
L1 L2 A L3
B
①、确定封闭环:L3
②、查找组成环:L6
L6
③、画尺寸链图:尺寸链如图所示。
④、确定封闭环:增环:L6
⑵、计算:计算结果为:L6δ L6= L3δ L3=10 ⑶、验算:
显然无法保证加工要求。
⑷、结果:不能满足加工要求。 减环L1 封闭环L3
-60
10
-(-0.05) -(0.05)
工艺尺寸链计算
习题十一 工序尺寸链计算
解:以工件右端面定位时,其工序尺寸为L5。 ⑴、建立尺寸链
L1 L2 A L3
B
①、确定封闭环:L3
②、查找组成环:L2、L5
L2 L3 L5
L5
机械制造技术
工艺尺寸链计算
工艺尺寸链计算
习题十一 工序尺寸链计算
L1 L2 A
图示为一套筒零件,现在铣床上 采用调整法加工A面,要求保证尺 寸 为 L3=100+0.2mm, 已 知 : L1=60±0.05,L2=300+0.1mm,试求 分别以工件左端面定位、以工件 右端面定位及以工件孔内端面B定 位的工序尺寸及偏差,并比较那 种定位方案为好。
机械加工工艺规程设计(机制工艺)

机械加工工艺规程设计帮助生产标准化、精细化,有助于生产成本控制和生产效率的提 高。
3 机械加工工艺规程设计的步骤和因素
机械加工工艺规程设计需要根据加工特点和要求,合理的选定设备,工艺流程和参数, 并对整个加工过程进行跟踪和优化。
机制工艺的重要性
精度和效率
机制工艺可以很好的控制工 件的精度,提高整个生产线 的效率。
成本控制
机制工艺可以有效地减少人 工错误,最大限度的降低生 产成本。
提高产能
机制工艺可以通过自动化和 改进工具、设备,提高整个 生产线的工作效率,实现高 质量和高产能的要求。
机械加工工艺制工艺)
本次分享将介绍机制工艺的定义,重要性以及机械加工工艺规程设计的重要 步骤和关键因素。
机制工艺的定义
概述
机制工艺是指将工件固定在加工设备上,利用切削、钻孔、钻攻、并且不断切削等方法来进 行形状加工,精度加工和物理性能加工的加工方法。
案例
机制加工工艺适用于汽车、航空航天、模具、纺织、机械等行业,可生产高精度、高质量的 零件和模具。
5
加工工艺验证和调整
对加工工艺进行实际生产过程验证,发现问题及时调整,并对结果进行评估, 确保生产工艺稳定和一致性。
机械加工工艺规程设计的关键因素
设备选型
根据工件的要求和生产效率,采用适当的 设备以达到加工目的。
合理的工艺参数设置
加工质量取决于工艺参数的选取和调整, 所以需要在实践中不断调整,以达到最佳 的加工质量效果。
通过机械加工工艺规程设计,使生产标准化,降低生产成本,提高生产效率。
2 质量控制
机械加工工艺规程设计可以有效地控制加工工艺的每一个环节,从而保证生产出的产品 质量稳定,满足标准化生产要求。
- 1、下载文档前请自行甄别文档内容的完整性,平台不提供额外的编辑、内容补充、找答案等附加服务。
- 2、"仅部分预览"的文档,不可在线预览部分如存在完整性等问题,可反馈申请退款(可完整预览的文档不适用该条件!)。
- 3、如文档侵犯您的权益,请联系客服反馈,我们会尽快为您处理(人工客服工作时间:9:00-18:30)。
26
5.5.2.4 本工序加工时装夹误差(Δεb)的影响
此误差除包括定位和夹紧误差外,还包括夹具本身的制造
误差,其大小为三者的向量和。它将直接影响被加工表面与刀
具的相对位置,因此有可能因余量不足而造成废品,所以必须 给予余量补偿。
空间偏差与装夹误差在空间是有不同方向的,二者对加工
余量的影响应该是向量和。 图5.13 类零件加工余量影响的示意图。 为上述各种因素对车削轴
12
根据零件的生产纲领确定零件的生产类型
零件的生产纲领可按下式计算:
N零= N· n(1+ a )· (1十β )
式中 N零——零件的生产纲领(件/年); N——产品的生产纲领(台/年); n—— 每 台 产 品 中 包 含 该 零 件 的 数 量 ( 件 / 台);
a——该零件备件的百分率;
β——该零件废品的百分率。
16
大量生产
产品数量很大,大多数工作地点经常重复地进行
某一个零件的某一道工序的加工。
例如,汽车、拖拉机、轴承等的制造通常都是以大量生 产的方式进行。
17
各种生产类型的工艺过程的特点可归纳成表
18
确定毛坯的种类
与零件的结构形状、尺寸大小、材料的机械性能和零件的生 产类型及毛坯车间的具体生产条件有关。
主要用于单件小批生产,靠经验确定加工 余量,因此不够准确。为保证不出废品,余量 往往偏大。
31
5.7 工序尺寸的确定
零件图上的尺寸、公差是毛坯经过加工之后最终达到的尺寸。 在加工过程中,各工序所达到的尺寸称工序尺寸,也就是在工序 图上所标注的尺寸。
5· 7· l 用计算法确定工序尺寸
工序尺寸的计算可分为四种
3
工艺过程的组成
工艺过程是由一个或若干个依次排列的工序所组成。毛坯顺次 通过这些工序就变成了成品或半成品。
工序
一个(或一组)工人,在一个固定的工作地点(一台机床或一 个钳工台),对一个(或同时对几个)工件所连续完成的那部 分工艺过程,称为工序。它是工艺过程的基本单元,又是生产 计划和成本核算的基本单元。
生产过程的实质是由原材料(或半成品)变为产品的过程。因 此一个工厂的生产过程,又可按车间分成若干个车间的生产过 程。 工艺过程
零件的机械加工工艺过程(工艺路线或工艺流程): 用机械加工的方法,直接改变原材料或毛坯的形状、尺寸和性能 等,使之变为合格零件。
将零件装配成部件或产品的过程,称为装配工艺过程。
7
安
装
工件在加工前,在机床或夹具中相对刀具应有一个正确的位 置并给予固定,这个过程称为装夹,一次装夹所完成的那部 分加工过程称为安装。安装是工序的一部分。 每一个工序可能有一次安装,也可能有几次安装。如表5.l 中第一工序,若对一个工件的两端连续进行车端面、钻中 心孔,就需要两次安装(分别对两端进行加工),每次安 装有两个工步(车端面和钻中心孔)。
20
加工余量的确定
加工余量的概念
为了保证零件图上某平面的精度和粗糙度值,需要 从其毛坯表面切去全部多余的金属层,这一金属层的总 厚度称为该表面的加工总余量。每一工序所切除的金属 层厚度称为工序余量。可见某表面的加工总余量与该表 面工序余量之间的关系为:
Z总 Z1 Z 2 Z i Z n
非对称表面(单边,如平面)的基本余量为:
Zb ta (Ra ta ) (ρ a △ ε b)
29
5.5.3.2 查表法
工厂中广泛应用这种方法,表格是以工 厂的生产实践和试验研究所积累的数据为
基础,并结合具体加工情况加以修正后制
定的,如《金属机械加工工艺人员手册》。
30
5.5.3.3 经验法
33
5.8 时间定额及经济分析
5.8.1 时间定额
时间定额是在一定的生产规模、生产技术和生产组织的条
件下,为完成某一工件的某一工序所需要的时间,称为工序单
件时间或工序单件时间定额。它是计算产品成本和企业经济核 算的依据,也是新建或扩建工厂(或车间)时决定所需设备和
人员的依据。
工序单件时间的组成,可表示如下: t单=t基十t辅十t服十t休
4
阶梯轴
若生产批量比较小则其加工工艺过程可由六个工序组成, 如下表所示。棒料毛坯依次通过这六个工序就变成阶梯轴的产 品零件。
5
阶梯轴加工工艺过程
工序号 1 2 工序内容 车端面,钻中心孔 车外圆、车槽、倒角 车床 车床 设 备
3 4
5 6
铣键槽、去毛刺 粗磨外圆
热处理 精磨外圆
铣床 磨床
高频淬火机 磨床
这种用正确分 布的六个支承点来 限制工件的六个自 由度,使工件在夹 具中得到正确位置 的规律,称为六点 定位原理。
图6.4 工件的六点定位
36
6.2工件的定位
• 6.2.1六点定位原理 一个自由的物体,它对三个相互垂直的坐标系来说,有六个活动可能性, 其中三种是移动,三种是转动。习惯上把这种活动的可能性称为自由度, 因此空间任一自由物体共有六个自由度。如图6.2所示,物体的六个自由 度分别为:
34
5.8.2 工艺过程的经济分析
5.8.2.1 生产成本的组成
5.8.2.2 工艺过程经济方案的选择
35
六点定位原理
若使物体在某个方向有确定的位置,就必须限制该方向的 自由度,所以要使工件在空间处于相对固定的位置,就必 须对六个自由度加以限制。限制的方法就是用相当于六个 支承点的定位元件与工件的定位基准面接触,如图6.4所 X Y 示:在底面 XOY内的三个支承点限制了 , , 三个自由 X Y Z 度;在侧面YOZ内的两个支承点限制了 , 两个自由度; 在端面XOY内的一个支承点限制了 一个自由度。
机械加工/加工工艺/中级
机械制造工艺基础答疑
常州精棱铸锻有限公司 人力资源部
机械制造工艺的基础知识
-基本概念
生产过程 工艺过程 机械加工工艺过程
2
机械制造工艺的基础知识
生产过程 生产过程包括: 产品设计、生产准备、原材料的运输和保管、毛坯制造、机械加 工、热处理、装配和调工 步
工步是工序的组成单位。在被加工的表面、切削用 量(指切削速度、背吃刀量和进给量)、切削刀具 均保持不变的情况下所完成的那部分工序,称工步。 当其中有一个因素变化时,则为另一个工步。 当同时对一个零件的几个表面进行加工时,则为复 合工步。
10
走
刀
被加工的某一表面,由于余量较大或其它原因,
在同一工序中,安装次数应尽量少,既可以提高生产效率,又 可以减少由于多次安装带来的加工误差。
8
工 位
为减少工序中的装夹次数,常采用回转工作台或回转夹具,使 工件在一次安装中,可先后在机床上占有不同的位置进行连续 加工,每一个位置所完成的那部分工序,称一个工位。
采用多工位加工,可以提高生产率和保证被加工
在切削用量不变的条件下,用同一把刀具对它进行多
次加工,每加工一次,称一次走刀。
11
生产类型对工艺过程的影响
生产类型对工艺过程有着重要影响。 当生产类型不同时,生产组织和生产管理、车间的机床 布置、毛坯的制造方法、采用的工艺装备(刀、夹、量具)、 加工方法以及工人的熟练程度等都有很大的不同,因此在制订 工艺路线之前必须明确该产品的生产类型。
27
图5.13 影响加工余量的因素
28
5.5.3 确定加工余量的方法
5.5.3.1 计算法
根据上面所述各种因素对加工余量的影响,并由图5.13可得出 下面的计算公式。 对称表面(双边,如孔或轴)的基本余量为:
或
Ta Z b ( Ra ta ) (ρ a △ε b ) 2
2Zb Tκ 2(Ra ta ) 2(ρ a △ ε b)
状可以很复杂,尺寸精度高,但机械性能差。
19
毛坯的选择
在大批、大量生产中,常采用精度和生产率较高的毛坯 制造方法,如金属型铸造、精密铸造、模锻、冷冲压、 粉末冶金等,使毛坯的形状更接近于零件的形状。因此 可大量减少切削加工的劳动量,甚至可不需要进行切削
加工,从而提高了材料的利用率,降低了机械加工的成 本。 在单件小批生产中,一般采用木模手工砂型铸造和 自由锻造,因此毛坯的精度低,成本高、废品率高、 切削加工劳动量大。
15
成批生产
一年中分批地制造相同的产品,制造过程有一定的重 复性。 例如,机床制造就是比较典型的成批生产。每批制造 的相同产品的数量称为批量。根据批量的大小,成批生产 又可分为:
小批生产---其工艺过程的工艺特点和单件小批生产相似; 大批生产---其工艺过程的特点和大量生产相似; 中批生产---其工艺过程的特点则介于单件小批生产和大批 大量生产之间。
式中n——加工该表面的工序(或工步)数目。 工件加工余量的大小,将直接影响工件的加工质量、生产率 和经济性。例如加工余量太小时,不易去掉上道工序所遗留 下来的表面缺陷及表面的相互位置误差而造成废品;加工余 量太大时,会造成加工工时和材料的浪费,甚至因余量太大 而引起很大的切削热和切削力,使工件产生变形,影响加工 质量。 21
(1)经过几道工序加工所形成的表面的工序尺寸计算
(2)工序基准与设计基准不重合而弓l起的工序尺寸计算 (3)从尚需继续加工表面标注的工序尺寸计算 (4)对某表面进行加工,要同时保证多个设计尺寸的工序尺 寸计算
32
5.7.2 用图表法综合确定工序尺寸
在加工过程中,当同一个方向上的尺寸较多而又需要多
次转换定位基准,或者当设计基准与其它基准不重合而需要 进行尺寸换算时,确定相应的各工序尺寸、公差和余量的工 作就显得很杂乱、很麻烦。如果采用图表法来解决这类问题, 就比较方便、明了、有次序。 关干图表的制作和应用的例子,请读者自行参阅有关资 料。
铸件
包括铸钢、铸铁、有色金属及合金的铸件等。铸件 毛坯的形状可以相当复杂,尺寸可以相当大,且吸振性 能较好,但铸件的机械性能较低,一般壳体零件的毛坯 多用铸件。 机械性能较好,有较高的强度和冲击韧性,但毛坯 的形状不宜复杂,如轴类和齿轮类零件的毛坯常用锻 件。