高炉低硅铁的冶炼实践
高炉炼铁技术创新实践及未来展望

千里之行,始于足下。
高炉炼铁技术创新实践及未来展望高炉炼铁技术是钢铁工业中非常重要的一个环节,对于钢铁产量和质量有着直接影响。
随着科技的不断发展和进步,高炉炼铁技术也在不断创新和实践。
本文将介绍高炉炼铁技术的创新实践及未来展望。
高炉炼铁技术主要包括焦炭冶炼、铁矿石还原和炉渣处理三个方面。
近年来,针对这几个环节进行了一系列的技术创新,以提高钢铁产量和质量,减少能源消耗和环境污染。
首先,在焦炭冶炼方面,高炉炼铁技术实践了煤炭气化技术,将煤炭转化为合成气或制备气,用来代替部分焦炭。
这样可以减少焦炭的消耗量,提高炉温和炉效,提高炼铁效果和节约能源。
其次,在铁矿石还原方面,高炉炼铁技术实践了混合还原技术,将不同种类的铁矿石混合使用,以提高还原效率和减少还原剂的消耗。
同时,还运用了制粒和球团矿技术,提高了炉料的密实度和还原性能,使得炼铁效果更好。
再次,在炉渣处理方面,高炉炼铁技术实践了炉渣处理技术,包括高炉渣套料、炉渣粉磨和炉渣稳定化等。
这些技术可以减少炉渣的生成和排放,降低对环境的污染,同时还能回收利用一部分有价值的元素。
未来,高炉炼铁技术仍将继续创新和发展。
一方面,可以进一步拓宽原料的来源,包括使用青海盐湖等资源,以降低对传统铁矿石的依赖程度。
另一方面,可以进一步提高炉渣的利用率,实现钢铁工业的循环经济。
此外,还可以用高效节能的加热方式替代传统的冶炼方法,以进一步降低能源消耗和环境污染。
第1页/共2页锲而不舍,金石可镂。
综上所述,高炉炼铁技术的创新实践为钢铁工业的发展提供了重要支撑。
未来,随着技术的不断进步和创新,高炉炼铁技术将更加高效、环保和可持续,为钢铁产量和质量的提高做出更大贡献。
同时,需要在技术创新的同时,加强对环境保护的重视,实现钢铁工业的可持续发展。
高炉低硅冶炼技术
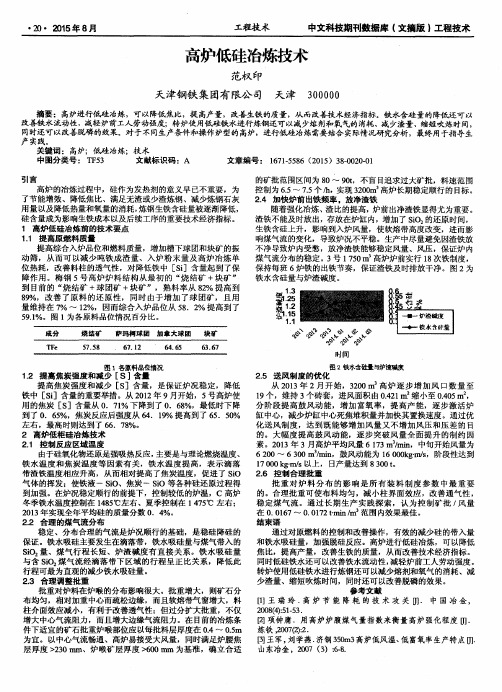
工程技术
中文科 技期 刊数 据库 ( 文摘 版 l 工程技术
高炉低硅冶炼技术
范 杈 印
天津钢铁 集 团有 限公 司 天津
3 0 0 0 0 0
摘要 :高炉进行低硅冶炼 ,可以降低 焦比,提 高产量 ,改善生铁 的质量 ,从而改善技术经济指标 。铁水含硅量 的降低还可 以 改善铁水 流动性 ,减轻炉前 工人 劳动 强度;转炉使用低硅 铁水进行 炼钢还可 以减少熔剂和氧气的消耗 、减 少渣量 、缩短 吹炼时间, 同时还可 以改善脱磷的效果。对 于不同生产条件和操作炉型的 高炉,进行循硅 冶炼需要结合 实际情况研 究分析 ,最终用于指导生 产 实践。 关键 词 :高炉;低硅冶炼;技术 中图分类号 :T F 5 3 文献标识码 :A 文章编号 : 1 6 7 1 . 5 5 8 6( 2 0 1 5 )3 8 . 0 0 2 0达 到 了 6 6 。7 8 %。
2 高炉低柜硅 冶炼技术
2 . 1 控 制 反 应 区 域 温 度 由于硅氧 化物 还原是强吸热反应 , 主要 是与理论燃烧温度 、 铁 水温 度和焦 炭温度 等 因素 有关 ,铁 水温度 提高 ,表 示滴 落 带渣铁温度相应升高 ,从而相对提高 了焦炭温度 ,促进 了 S i O
臻
I 十 铰 康 翕 许 鬣
时问
圈 l各原料 晶位情况
瞪 2铁琦 、 舍链量与炉渣碱度
2 . 5 送风制度的优化 1 . 2 提高焦炭 强度和减少 [ S]含量 提 高焦炭强度和 减少 [ s l含量 ,是 保证炉况 稳定 ,降低 从 2 0 1 3年 2月开 始,3 2 0 0 I I l 3 高 炉逐 步增 加 风 口数量 至 铁中 [ s i ]含量 的重要举措 。从 2 0 1 2年 9月开始,5号 高炉使 1 9 个 ,维持 3个砖套 ,进风面积 由0 . 4 2 1 缩小至 0 . 4 0 5 1 l l 2 , 用 的焦炭 [ S ]含量从 0 .7 1 % 下 降到 了 0 .6 8 %,最低 时下 降 分 阶段 提高鼓 风动 能,增加 富氧率 ,提 高产 能,逐步激 活炉 到了0 .6 5 %,焦炭反应后强度从 6 4 .1 9 % 提高到 了 6 5 .5 0 % 缸 中心 ,减少炉缸 中心死焦堆积量并加快其 置换速度 。通过优
[中学]高炉低硅冶炼生产实践
![[中学]高炉低硅冶炼生产实践](https://img.taocdn.com/s3/m/95bffd04312b3169a451a4c0.png)
[中学]高炉低硅冶炼生产实践高炉低硅冶炼生产实践黄少磊摘要从高炉低硅冶炼原理进行研究,,通过对生产指标的对比分析,改善焦炭质量、合理炉料结构、调整操作制度等措施,实现高炉低硅冶炼的生产实践。
关键词高炉低硅冶炼操作制度成本1 前言高炉冶炼过程中,铁水含硅量的控制是评价高炉冶炼技术水平和高炉铁水质量的重要指标。
高炉进行低硅冶炼,可以降低焦比,提高产量,改善生铁的质量,从而改善技术经济指标;铁水硅含量的降低还可以改善铁水流动性,减轻炉前工人劳动强度;转炉使用低硅铁水进行炼钢生产可以减少熔剂和氧气的消耗、减少渣量、缩短吹炼时间,同时还可以改善脱磷的效果。
可见,采用低硅冶炼会给炼铁和炼钢带来很好的经济效益,是企业实现低成本战略的有效途径。
对于不同生产条件和操作炉型的高炉,进行低硅冶炼需要结合实际情况研究分析,最33终用于指导生产实践。
二铁高炉有效容积480m,高炉设计年平均利用系数3.0 t,(m d),其采用PW串罐无钟炉顶、TRT炉顶煤气余压发电、高温顶燃式热风炉、大喷煤等一系列先进、成熟、可靠的炼铁技术与设备。
2 高炉进行低硅冶炼的机理分析在高炉冶炼过程中,高炉铁水中的硅主要来源于焦炭灰分、矿石脉石、煤粉中的二氧化硅,现在高炉炼铁者普遍认为焦炭灰分中的二氧化硅是高炉铁水硅的最主要的来源。
(1)在高炉冶炼过程中,硅(分子式为“Si”)主要是以SiO形式存在,可是SiO 是非常22稳定的化合物,分解压力很小,用CO还原SiO几乎是不可能的,只能用固体碳部分地还2[1]原SiO,且SiO还原的还原率仅为5,,10,。
22 大量研究表明,高炉内硅(Si)还原主要是分两步完成的:第一步是焦炭灰分中的SiO,,12与碳(C)反应形成SiO蒸气;第二步是随着煤气上升的SiO蒸气被铁珠吸收或吸附在焦炭块上,被铁中[C]和焦炭的C还原成Si。
基本化学反应如下: SiO+C,SiO(g)+CO 2SiO+[C],[Si]+COSiO+C,[Si]+CO(2)在高炉冶炼过程中,硅(Si)被还原同时,还存在着[Si]被重新氧化成为(SiO)的耦合反2应,该反应发生在铁滴穿过渣层时和在炉缸贮存的渣铁界面上。
韶钢6号高炉降低生铁含硅的冶炼实践
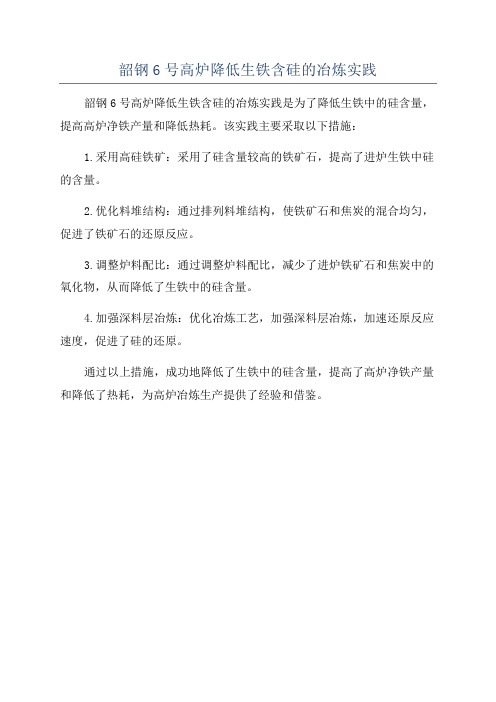
韶钢6号高炉降低生铁含硅的冶炼实践韶钢6号高炉降低生铁含硅的冶炼实践是为了降低生铁中的硅含量,提高高炉净铁产量和降低热耗。
该实践主要采取以下措施:
1.采用高硅铁矿:采用了硅含量较高的铁矿石,提高了进炉生铁中硅的含量。
2.优化料堆结构:通过排列料堆结构,使铁矿石和焦炭的混合均匀,促进了铁矿石的还原反应。
3.调整炉料配比:通过调整炉料配比,减少了进炉铁矿石和焦炭中的氧化物,从而降低了生铁中的硅含量。
4.加强深料层冶炼:优化冶炼工艺,加强深料层冶炼,加速还原反应速度,促进了硅的还原。
通过以上措施,成功地降低了生铁中的硅含量,提高了高炉净铁产量和降低了热耗,为高炉冶炼生产提供了经验和借鉴。
高炉低硅冶炼实践

高炉 冶炼 生产 中采用 的降硅 方式有 3种 : 是在 一 高炉 内抑制硅从 炉料 中还原 进入 生铁 ; 是从 风 口喷 二 入脱硅 剂进行 炉 内脱 硅 ; 三是 高 炉炉 外 铁水 脱 硅 , 包
括 炉前 脱硅 和铁水 罐 脱硅 。1 高炉 选 择抑 制 硅从 # 炉料 中还 原进入 生铁的方法进行 生铁 降硅 。
a d bl n owi n g i n 2 0 ng o a a n i 0 9. I m a e t e iio c tnti h t m ea e u e r d l fo 0.5 t d h sl n on e n o t lr d c d g a ual r m c y 3% t o
A b ta t Th o — slc n s etn e h q a a p e n # b a tf r a e ofTa g Ste fe e h u sr c : e l w iio m li g tc niue w s do t d i 1 l s u n c n e la rov r a l t
1
引 言
铁水 含硅量 是评 价高 炉生铁 质量 和高 炉冶炼 技
术 水平 的重要 指 标 之一 。1 高炉 自 2 0 # 0 9年 大修 开
钢铁 工业是 国 民经济 的支 柱 产业 , 发 展速 度 其
与程 度是衡 量一 个 国家工 业发展 水平 的重要 标 志之
一
炉后 就一 直尝 试实行 低硅 冶炼 。铁水 含硅 量 由开 炉 时的 0 5 %逐步 降低到 目前 的 0 3 % , 体过 程 如 .3 .8 具
口和缩小 风 口面积 , 均匀 了炉缸煤气 流 的初始 分 布 。
宝钢高炉低燃料比生产实践
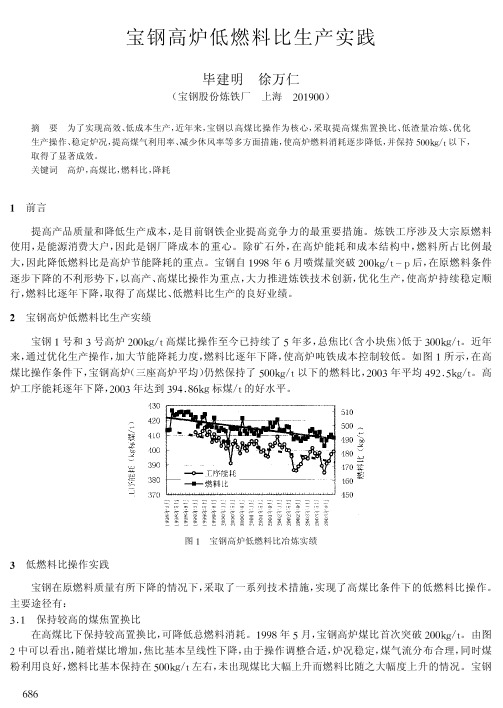
宝钢高炉低燃料比生产实践毕建明徐万仁(宝钢股份炼铁厂上海!"#$"")摘要为了实现高效、低成本生产,近年来,宝钢以高煤比操作为核心,采取提高煤焦置换比、低渣量冶炼、优化生产操作、稳定炉况,提高煤气利用率、减少休风率等多方面措施,使高炉燃料消耗逐步降低,并保持%""&’/(以下,取得了显著成效。
关键词高炉,高煤比,燃料比,降耗!前言提高产品质量和降低生产成本,是目前钢铁企业提高竞争力的最重要措施。
炼铁工序涉及大宗原燃料使用,是能源消费大户,因此是钢厂降成本的重心。
除矿石外,在高炉能耗和成本结构中,燃料所占比例最大,因此降低燃料比是高炉节能降耗的重点。
宝钢自#$$)年*月喷煤量突破!""&’/(+,后,在原燃料条件逐步下降的不利形势下,以高产、高煤比操作为重点,大力推进炼铁技术创新,优化生产,使高炉持续稳定顺行,燃料比逐年下降,取得了高煤比、低燃料比生产的良好业绩。
"宝钢高炉低燃料比生产实绩宝钢#号和-号高炉!""&’/(高煤比操作至今已持续了%年多,总焦比(含小块焦)低于-""&’/(。
近年来,通过优化生产操作,加大节能降耗力度,燃料比逐年下降,使高炉吨铁成本控制较低。
如图#所示,在高煤比操作条件下,宝钢高炉(三座高炉平均)仍然保持了%""&’/(以下的燃料比,!""-年平均.$!/%&’/(。
高炉工序能耗逐年下降,!""-年达到-$./)*&’标煤/(的好水平。
!号和"号高炉近年分别常年维持##$%&/’和#$(%&/’的较高煤比操作,而燃料比基本维持在)*(%&/’左右的水平。
与国外同行相比,欧洲某高炉#$$!年平均煤比#!!%&/’,焦比"!#%&/’,总燃料比(#"%&/’。
邯钢三炼钢低硅铁水冶炼探讨与实践
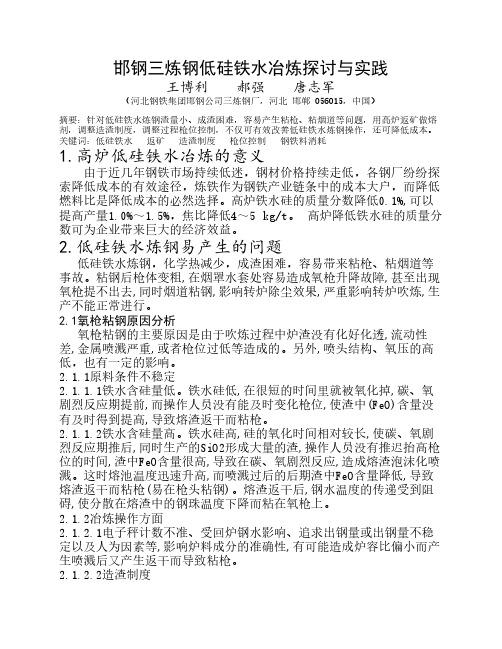
邯钢三炼钢低硅铁水冶炼探讨与实践王博利 郝强 唐志军(河北钢铁集团邯钢公司三炼钢厂,河北 邯郸 056015,中国)摘要:针对低硅铁水炼钢渣量小、成渣困难,容易产生粘枪、粘烟道等问题,用高炉返矿做熔剂,调整造渣制度,调整过程枪位控制,不仅可有效改善低硅铁水炼钢操作,还可降低成本。
关键词:低硅铁水 返矿 造渣制度 枪位控制 钢铁料消耗1.高炉低硅铁水冶炼的意义由于近几年钢铁市场持续低迷,钢材价格持续走低,各钢厂纷纷探索降低成本的有效途径,炼铁作为钢铁产业链条中的成本大户,而降低燃料比是降低成本的必然选择。
高炉铁水硅的质量分数降低0.1%,可以提高产量1.0%~1.5%,焦比降低4~5 kg/t。
高炉降低铁水硅的质量分数可为企业带来巨大的经济效益。
2.低硅铁水炼钢易产生的问题低硅铁水炼钢,化学热减少,成渣困难,容易带来粘枪、粘烟道等事故。
粘钢后枪体变粗,在烟罩水套处容易造成氧枪升降故障,甚至出现氧枪提不出去,同时烟道粘钢,影响转炉除尘效果,严重影响转炉吹炼,生产不能正常进行。
2.1氧枪粘钢原因分析氧枪粘钢的主要原因是由于吹炼过程中炉渣没有化好化透,流动性差,金属喷溅严重,或者枪位过低等造成的。
另外,喷头结构、氧压的高低,也有一定的影响。
2.1.1原料条件不稳定2.1.1.1铁水含硅量低。
铁水硅低,在很短的时间里就被氧化掉,碳、氧剧烈反应期提前,而操作人员没有能及时变化枪位,使渣中(FeO)含量没有及时得到提高,导致熔渣返干而粘枪。
2.1.1.2铁水含硅量高。
铁水硅高,硅的氧化时间相对较长,使碳、氧剧烈反应期推后,同时生产的SiO2形成大量的渣,操作人员没有推迟抬高枪位的时间,渣中FeO含量很高,导致在碳、氧剧烈反应,造成熔渣泡沫化喷溅。
这时熔池温度迅速升高,而喷溅过后的后期渣中FeO含量降低,导致熔渣返干而粘枪(易在枪头粘钢)。
熔渣返干后,钢水温度的传递受到阻碍,使分散在熔渣中的钢珠温度下降而粘在氧枪上。
高炉炼铁工艺流程
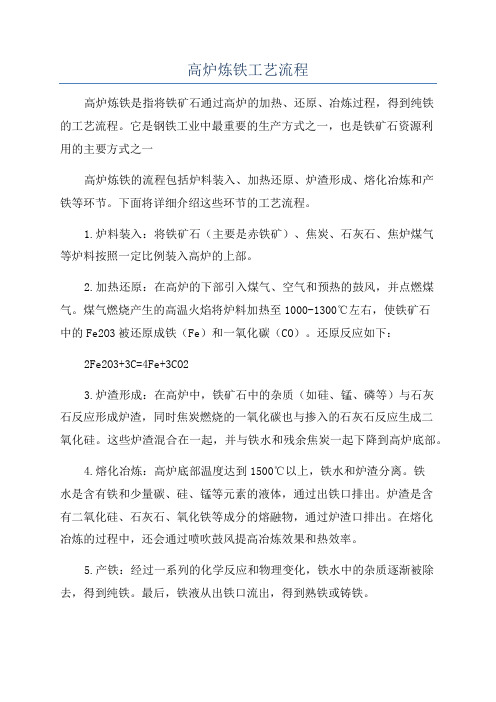
高炉炼铁工艺流程
高炉炼铁是指将铁矿石通过高炉的加热、还原、冶炼过程,得到纯铁
的工艺流程。
它是钢铁工业中最重要的生产方式之一,也是铁矿石资源利
用的主要方式之一
高炉炼铁的流程包括炉料装入、加热还原、炉渣形成、熔化冶炼和产
铁等环节。
下面将详细介绍这些环节的工艺流程。
1.炉料装入:将铁矿石(主要是赤铁矿)、焦炭、石灰石、焦炉煤气
等炉料按照一定比例装入高炉的上部。
2.加热还原:在高炉的下部引入煤气、空气和预热的鼓风,并点燃煤气。
煤气燃烧产生的高温火焰将炉料加热至1000-1300℃左右,使铁矿石
中的Fe2O3被还原成铁(Fe)和一氧化碳(CO)。
还原反应如下:2Fe2O3+3C=4Fe+3CO2
3.炉渣形成:在高炉中,铁矿石中的杂质(如硅、锰、磷等)与石灰
石反应形成炉渣,同时焦炭燃烧的一氧化碳也与掺入的石灰石反应生成二
氧化硅。
这些炉渣混合在一起,并与铁水和残余焦炭一起下降到高炉底部。
4.熔化冶炼:高炉底部温度达到1500℃以上,铁水和炉渣分离。
铁
水是含有铁和少量碳、硅、锰等元素的液体,通过出铁口排出。
炉渣是含
有二氧化硅、石灰石、氧化铁等成分的熔融物,通过炉渣口排出。
在熔化
冶炼的过程中,还会通过喷吹鼓风提高冶炼效果和热效率。
5.产铁:经过一系列的化学反应和物理变化,铁水中的杂质逐渐被除去,得到纯铁。
最后,铁液从出铁口流出,得到熟铁或铸铁。
降低高炉冶炼生铁含硅量的研究

降低高炉冶炼生铁含硅量的研究降硅是一项重大节能增产的措施应生铁含硅的降低和稳定,是高炉冶炼条件和技术水平的标志性指标,也是提高产量.减少料消耗,降低生铁成本的重要因素。
标签:生铁含硅量;炉温物理热;炉渣碱度;煤气流分布1 前言1#高炉是在原600m3高炉基础上扩容为900m3,1#高炉采用了比较先进的冷却壁镶砖的薄壁炉衬,炉顶安装了十字测温和雷达探尺等先进设备.于2016年3月6日投产。
开炉后由于原燃料等条件的限制,由于对薄壁炉衬炉型的经验不足等原因,炉况顺行度较差。
为了改善炉渣的流动性,炉渣二元碱度控制在1.10左右,为了保证生铁质量,生铁含硅量控制在0.45%,行业较高水平。
2017年1月份以后经过稳定煤比、高顶压、优化炉渣性能等指施,使生铁含硅量稳步下降,到2017年4月后稳定在0.3%以下,[s]控制在0.025%左右,到5月份以后含硅量进一步降低,高炉的主要技术经济指标也大幅提高。
2 降硅的理论依据和操作思路降硅是一重大节能增产的措施。
生铁含硅的降低和稳定,是高炉冶炼条件和技术水平的标志性指标,也是提高产量,减少燃料消耗,降低生铁成本的重要因素。
但降硅不能盲目降低,要有理论依据及生产实践。
降硅是一个逐步的过程,也是操作观念转变的过程.炼铁厂对高妒臊作者进行了为期一星期关于降硅万面专门培训,制定了各种应对措施和注意事项,同时适时对各项燥作参数进行调整,使高炉操作者从思想上对炉温概念有了重新的认识,了解了降硅的好处及一些低硅冶炼操作的理念.3 降硅措施3.1 原料管理1#高炉原料组成以高碱度烧结矿+低碱度烧结矿+酸性球团矿或配加部分高品位块矿。
炼铁厂从2017年1月份起狠抓原料质量,特别是在稳定烧结矿碱度,提高烧结矿强度,严格控制入炉料的筛分,降低返矿率方而做了大量工作。
3.2 合理煤气流分布冶炼低硅生铁时,最重要的是改善高炉冶炼条件,优化高炉操作管·保证煤气流分布合理且稳定,提高煤气热能和化学能的利用,以保证[Si]的稳定,降低炉凉的风险,保证高炉处于正常顺行的稳定状态,是降硅的重要手段。
低硅冶炼技术详解
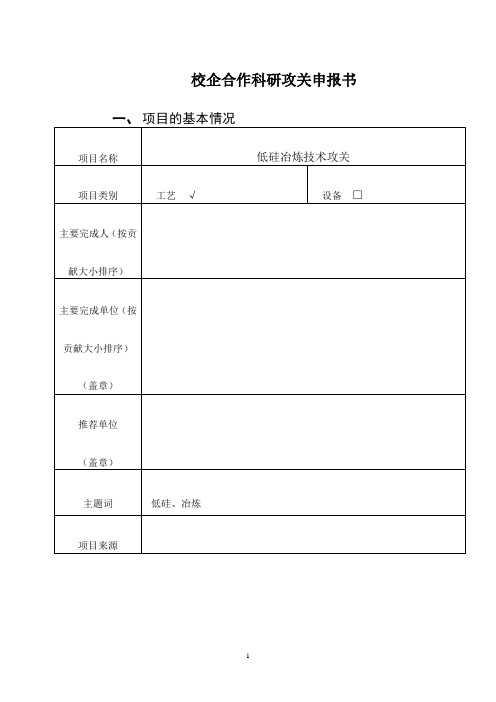
20世纪60年代以来高炉解剖研究的结果说明,在软熔带下沿形成的液态铁水含[Si]、[S]量即已开始增高,下降到风口水平面时[Si]、[S]含量达到最大值。而后,炉缸下部铁滴穿过渣层时,[Si]、[S]又转移入渣,最后降低至出炉成分。铁水的硅还原第一步是焦炭灰分中的SiO2或炉渣中的(SiO2)在风口带高温区还原生成SiO蒸汽,第二步是SiO气并随高温煤气上升,被由软熔带向下滴落的铁液吸收,并被[C]还原。通过以上高炉内的硅的还原机理,铁水中硅的含量主要受炉料中带入的SiO2以及风口高温区生成的SiO(g)气体反应的影响。根据Si在高炉内的行为,冶炼低硅生铁的必要条件是:(1)控制Si源,从精料上下功夫,努力降低焦炭灰分和含铁料中的SiO2量;(2)选择合适的的炉渣碱度以及降低渣中SiO2的活度;(3)选用有利于高温区下移的技术措施和操作制度使炉缸有稳定的充足热量,使铁水的物理热稳定在较高的水平;(4)精心操作,包括原燃料成分稳定,波动小,包括槽下称量准确等。
低硅冶炼经过一段时间的实施后,高炉取得了很好的经济效益,表2为高炉2011年1月~2011年12月铁水[Si]含量控制情况,由表可以看出高炉的[si]控制的比较好,高炉低硅冶炼取得了长足进步。低硅冶炼促进了高炉技术的进步,现入炉焦比已达到400kg/t以下,煤比150kg/t以上。高炉工艺人员正在通过一系列的努力,包括提高风温等一系列的措施,进一步将[Si]降至全国一流水平,以达到进一步降低生铁成本,增强企业市场竞争力的目的。
1.低硅冶炼前状况
天津钢管制铁有限公司1000m3高炉自2009年12月开炉后,一直稳定顺行,具备了低硅冶炼的条件。但综合来看,主要仍有2个方面的条件限制。
1.1原料条件
本厂烧结矿质量一直偏差,粉末入炉量偏高。直接导致高炉透气性差,风压较高,高炉顺行受到一定影响,时有小塌料、悬料现象。焦炭更换频繁,成分波动较大,质量不稳定,造成高炉炉温波动大,给降[Si]工作带来一定难度。
低硅铁水冶炼工艺实践_吴文东
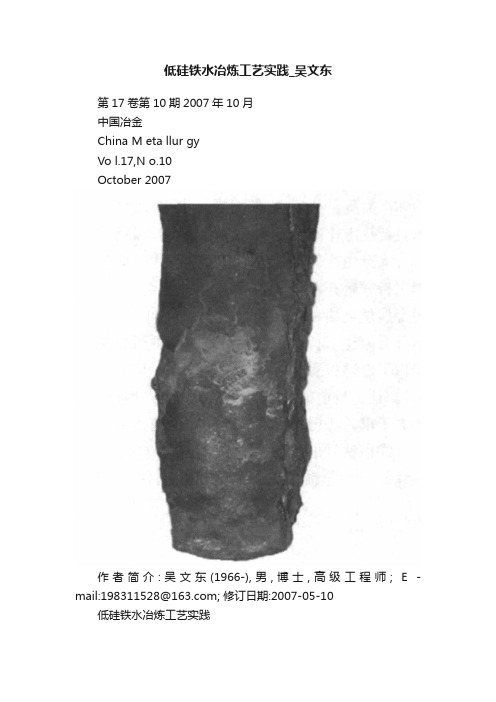
低硅铁水冶炼工艺实践_吴文东第17卷第10期2007年10月中国冶金China M eta llur gyVo l.17,N o.10October 2007作者简介:吴文东(1966-),男,博士,高级工程师; E -mail:*****************;修订日期:2007-05-10低硅铁水冶炼工艺实践吴文东, 彭波, 代宾, 张其欢, 肖建华(川威集团有限公司,四川威远642469)摘要:简介了川威炼钢厂低硅铁水冶炼工艺。
生产实践表明,采取加入一定的钢包余渣和留渣操作等技术措施,可有效解决低硅铁水冶炼成渣困难、热量少、易粘枪、不利于脱磷及炉况维护等难题。
关键词:低硅铁水;钢包余渣;留渣操作;工艺实践中图分类号:T F703 文献标识码:A 文章编号:1006-9356(2007)10-0014-02Practice of Steelmaking With Hot Metal Containing Low SiliconWU Wen -dong, PEN G Bo, DA I Bin, ZH A NG Q-i H uan, XIAO Jian -hua(Chuanw ei G ro up Co L td,Weiyuan 642469,Sichuan,China) Abstract:T he pro cess of steelmaking w ith ho t metal containing lo w silico n in Stee-l making Plant was int roduced.P roduct ion practice show s that so me pro blem o f slag for mation,shor t o f heat,slag adhesion o n ox y gen lance,less slag for dephospho rizatio n w ere so lved by adding sur plus slag and r emaining slag operation.Key words:hot metal co nt aining low silico n;sur plus slag o f ladle;remaining slag o per ation;pr actice 目前,川威集团炼铁厂由于加大了钒钛矿用量比例和采用富氧喷煤技术,使得铁水条件变差、碳和硅的质量分数较低、钒和钛的质量分数较高。
低硅生铁冶炼技术
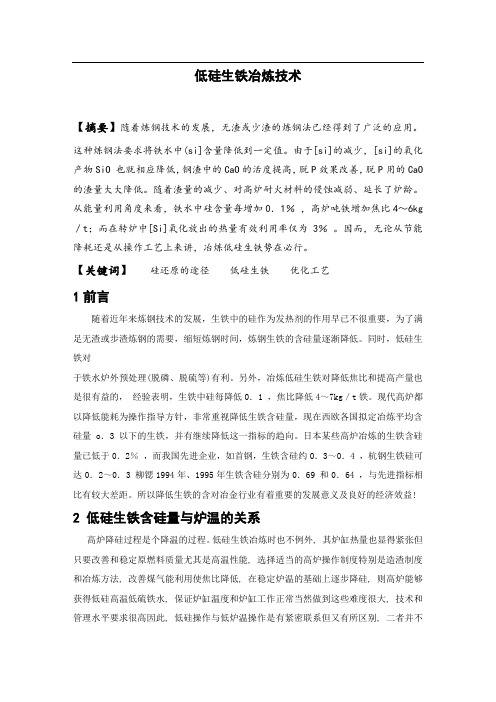
低硅生铁冶炼技术【摘要】随着炼钢技术的发展,无渣或少渣的炼钢法已经得到了广泛的应用。
这种炼钢法要求将铁水中(si]含量降低到一定值。
由于[si]的减少,[si]的氧化产物SiO 也就相应降低,钢渣中的CaO的活度提高,脱P效果改善,脱P用的CaO 的渣量大大降低。
随着渣量的减少、对高炉耐火材料的侵蚀减弱、延长了炉龄。
从能量利用角度来看,铁水中硅含量每增加0.1%,高炉吨铁增加焦比4~6kg /t;而在转炉中[Si]氧化放出的热量有效利用率仅为3%。
因而,无论从节能降耗还是从操作工艺上来讲,冶炼低硅生铁势在必行。
【关键词】硅还原的途径低硅生铁优化工艺1前言随着近年来炼钢技术的发展,生铁中的硅作为发热剂的作用早已不很重要,为了满足无渣或步渣炼钢的需要,缩短炼钢时间,炼钢生铁的含硅量逐渐降低。
同时,低硅生铁对于铁水炉外预处理(脱磷、脱硫等)有利。
另外,冶炼低硅生铁对降低焦比和提高产量也是很有益的,经验表明,生铁中硅每降低0.1 ,焦比降低4~7kg/t铁。
现代高炉都以降低能耗为操作指导方针,非常重视降低生铁含硅量,现在西欧各国拟定冶炼平均含硅量o.3 以下的生铁,并有继续降低这一指标的趋向。
日本某些高炉冶炼的生铁含硅量已低于0.2%,而我国先进企业,如首钢,生铁含硅约0.3~0.4 ,杭钢生铁硅可达0.2~0.3 柳锶1994年、1995年生铁含硅分别为0.69 和0.64 ,与先进指标相比有较大差距。
所以降低生铁的含对冶金行业有着重要的发展意义及良好的经济效益!2 低硅生铁含硅量与炉温的关系高炉降硅过程是个降温的过程。
低硅生铁冶炼时也不例外, 其炉缸热量也显得紧张但只要改善和稳定原燃料质量尤其是高温性能, 选择适当的高炉操作制度特别是造渣制度和冶炼方法, 改善煤气能利用使焦比降低, 在稳定炉温的基础上逐步降硅, 则高炉能够获得低硅高温低硫铁水, 保证炉缸温度和炉缸工作正常当然做到这些难度很大, 技术和管理水平要求很高因此, 低硅操作与低炉温操作是有紧密联系但又有所区别, 二者并不等同低硅生铁冶炼的成功关锭扰在于通过上述的技术措施能够使炉缸具有较好的和稳定的热状态,在降硅的同时能使铁水温度不致降低甚而有所提高。
高炉低硅铁冶炼技术应用
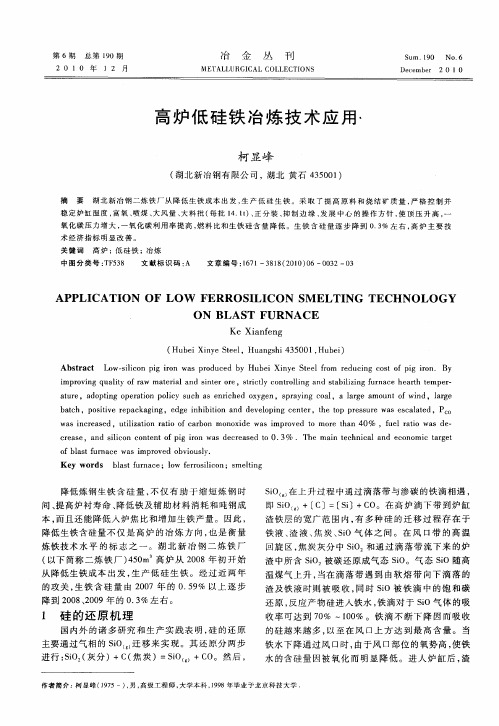
间、 提高 炉衬寿命 、 降低 铁及辅 助材料 消耗 和吨钢成
本, 而且 还能降低 入炉焦 比和增 加生 铁产 量。 因此 , 降低生铁 含硅量 不仅 是 高 炉 的冶 炼 方 向 , 是衡 量 也 炼铁 技术 水 平 的 标 志 之 一 。湖 北 新 冶 钢 二 炼 铁 厂 ( 以下简称 二 炼铁 厂 ) 5 m 4 0 高 炉从 2 0 0 8年初 开 始 从 降低生 铁成本 出发 , 产低 硅 生铁 。 经过 近两 年 生 的攻 关 , 铁含 硅 量 由 2 0 生 0 7年 的 0 5 % 以上 逐 步 .9 降到 2 0 、0 9年 的 0 3 左右 。 0820 .%
K e r b a tf n c y wo ds l s ur a e;l w f r o ii o o e r s l n;s l n c me t g i
降低 炼钢生 铁含 硅 量 , 不仅 有 助 于 缩短 炼 钢 时
SO 在上 升过 程 中通过 滴落带 与渗碳 的铁 滴相遇 , i 即 SO +[ ]=[ i C 。在 高炉 滴下 带 到炉 缸 i C s]+ O 渣 铁层 的宽广 范 围 内, 多种 硅 的迁 移 过 程存 在 于 有 铁 液 、 液 、 炭 、i 渣 焦 SO气 体 之 间 。在 风 口带 的高 温 回旋 区 , 炭 灰分 中 SO 焦 i 和通 过 滴 落带 流下来 的炉 渣 中所含 SO 被碳还原 成气态 SO i, i 。气态 SO随高 i
低硅冶炼

以促使铁水降硅反应的进行,因而有利于降 低铁水含硅量。 硅在高炉内的氧化反应: 2(CaO)+【Si】+2 【S】=(SiO2)+2(CaS) 2(MnO)+ 【Si】=(SiO2)+2 【Mn】 2(FeO)+ 【Si】=(SiO2)+2 【Fe】 (TiO2)+ 【Si】=(SiO2)+2【Ti】 (O2) (风) + 【Si】=(SiO2)
2、控制反应温度及反应时间
强吸热,高温有利于还原;反应区温度 (主要是理论燃烧温度、铁水温度和焦炭 温度)对铁水含硅量影响极大,铁水温度 提高,表示滴下带渣铁温度相应升高,从 而相对提高了焦炭温度,使铁液-SiO、焦炭 -SiO等各种硅还原过程得到加强。另外,焦 炭温度升高,风口理论燃烧温度相应提高, 促进了SiO气体的挥发。因此降低反应区温 度有利于抑制硅还原的发生,减少SiO气体 的挥发,从而减少硅的吸收。
高炉低硅冶炼
张武动 2013年3月
高炉低硅冶炼的意义
1、高炉低硅冶炼可以提升料速,
大大增加产量。 2、由于炉温降低可降低焦炭消耗, 优化指标,降低生产成本。 3、有利于炼钢造渣。
对高炉内硅还原机理的认识
大量吸热。还原1kg硅的吸热是还原1kg铁的 8倍;硅的还原在高温区; 问题:在高温区的什么位置? 在炉腰上部开始还原;炉腰中部迅速升 高,风口上部可以达到铁水含硅量的3-4倍; 风口区以下迅速下降。
生铁中硅的来源及降硅机理
来源:主要是来源于焦炭灰分和矿石脉石中的 SiO2 。 研究和实践表明硅的还原时逐级进行的: (SiO2)+C(s)→SiO(g)+ CO(g) (1) SiO(g) + [C] →[Si] + CO(g) (2)
高炉低硅冶炼之实践
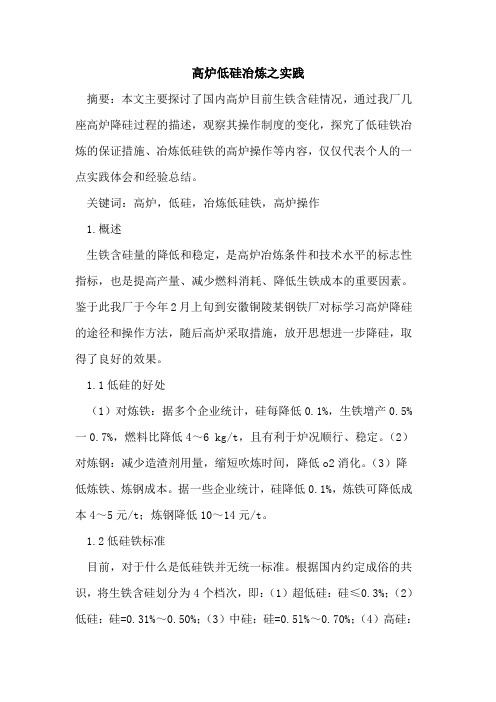
高炉低硅冶炼之实践摘要:本文主要探讨了国内高炉目前生铁含硅情况,通过我厂几座高炉降硅过程的描述,观察其操作制度的变化,探究了低硅铁冶炼的保证措施、冶炼低硅铁的高炉操作等内容,仅仅代表个人的一点实践体会和经验总结。
关键词:高炉,低硅,冶炼低硅铁,高炉操作1.概述生铁含硅量的降低和稳定,是高炉冶炼条件和技术水平的标志性指标,也是提高产量、减少燃料消耗、降低生铁成本的重要因素。
鉴于此我厂于今年2月上旬到安徽铜陵某钢铁厂对标学习高炉降硅的途径和操作方法,随后高炉采取措施,放开思想进一步降硅,取得了良好的效果。
1.1低硅的好处(1)对炼铁:据多个企业统计,硅每降低0.1%,生铁增产0.5%一0.7%,燃料比降低4~6 kg/t,且有利于炉况顺行、稳定。
(2)对炼钢:减少造渣剂用量,缩短吹炼时间,降低o2消化。
(3)降低炼铁、炼钢成本。
据一些企业统计,硅降低0.1%,炼铁可降低成本4~5元/t;炼钢降低10~14元/t。
1.2低硅铁标准目前,对于什么是低硅铁并无统一标准。
根据国内约定成俗的共识,将生铁含硅划分为4个档次,即:(1)超低硅:硅≤0.3%;(2)低硅:硅=0.31%~0.50%;(3)中硅:硅=0.5l%~0.70%;(4)高硅:硅≥0.71%。
1.3国内高炉目前生铁含硅情况目前,不同企业中相近炉容的硅差距也较大,低的在0.4%以下,高的在0.8%以上。
在300~1 000m3高炉中,宣钢1号(300m3)0.39%,新兴铸管3号(360)硅0.33%,青岛4号(500 m3)硅0.38%,鄂钢2号(620 m3)[silo.38%,莱钢(750m3)硅0.38%,因此<1000 m3高炉降硅的空间是比较大的。
2.我厂六座高炉的降硅实践下面通过我厂几座高炉降硅过程的描述,观察其操作制度的变化。
降低生铁硅含量,见表1:表1过程中采取的措施有:(1)高炉风口长度平均增长了20-30mm、风速从140m/s提高到160~170 m/s,用以“吹透”中心,保持炉缸整体活跃。
济钢高炉低硅低成本冶炼实践
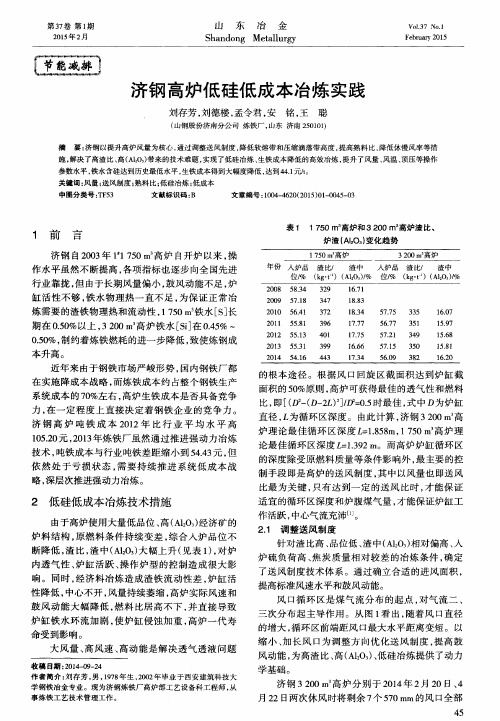
1 前
言
年份
表1 1 7 5 0 m。 高炉和 3 2 0 0 m。 高炉 渣 比 、
1 8 . 3 4 1 7. 7 7
1 7. 7 5
5 7 . 7 5 5 6 . 7 7
5 7 . 2 1
3 3 5 3 51
3 49
1 6. 0 7 1 5. 9 7
1 5. 68
2 01 3 5 5 . 31
2 01 4 5 4 . 1 6
由于高炉 使用 大 量低 品位 、 高( A 1 : 0 ) 经 济矿 的
炉 料 结构 , 原 燃 料条 件 持 续 变差 , 综 合 入 炉 品位 不 断 降低 , 渣比, 渣中( A 1 : 0 ) 大 幅上 升 ( 见表 1 ) , 对 炉
作 活跃 , 中心气流 充沛n ] 。
2 . 1 调整送 风制度
针对 渣 比高 、 品位 低 、 渣中( A l 。 O , ) 相对 偏 高 、 入
( 山钢股份济南分公司 炼铁厂 , 山东 济南 2 5 0 1 0 1 )
摘
要: 济钢 以提升高炉风量 为核 心 , 通过调整送 风制度 , 降低 软熔 带和压缩滴落 带高度 , 提 高熟料 比 , 降低休慢风 率等措
施, 解决 了高渣 比、 高( A 1 0 , ) 带来 的技术难题 , 实 现了低硅冶炼 、 生铁成本降低 的高 效冶炼 , 提升 了风量 、 风温 、 顶压 等操作 参数水平 , 铁水含硅达到历史最低水平 , 生铁成本 得到大幅度降低 , 达到 4 4 . 1 元/ t 。
宣钢8号高炉低硅冶炼操作实践
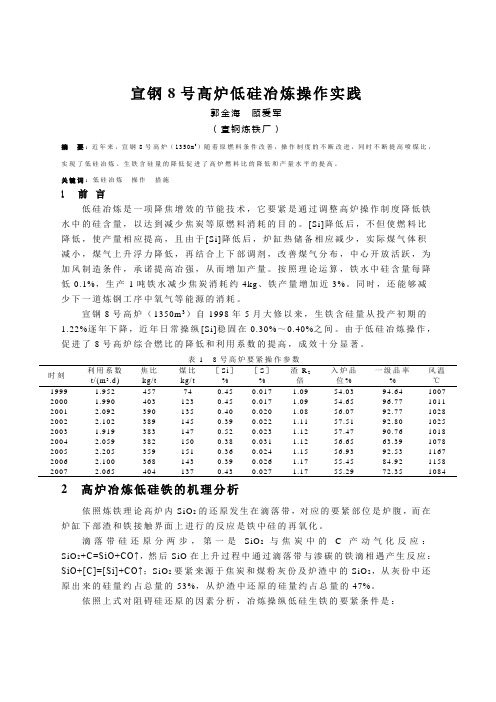
宣钢8号高炉低硅冶炼操作实践郭金海顾爱军(宣钢炼铁厂)摘要:近年来,宣钢8号高炉(1350m3)随着原燃料条件改善,操作制度的不断改进,同时不断提高喷煤比,实现了低硅冶炼。
生铁含硅量的降低促进了高炉燃料比的降低和产量水平的提高。
关键词:低硅冶炼操作措施1 前言低硅冶炼是一项降焦增效的节能技术,它要紧是通过调整高炉操作制度降低铁水中的硅含量,以达到减少焦炭等原燃料消耗的目的。
[Si]降低后,不但使燃料比降低,使产量相应提高,且由于[Si]降低后,炉缸热储备相应减少,实际煤气体积减小,煤气上升浮力降低,再结合上下部调剂,改善煤气分布,中心开放活跃,为加风制造条件,承诺提高冶强,从而增加产量。
按照理论运算,铁水中硅含量每降低0.1%,生产1吨铁水减少焦炭消耗约4kg、铁产量增加近3%。
同时,还能够减少下一道炼钢工序中氧气等能源的消耗。
宣钢8号高炉(1350m3)自1998年5月大修以来,生铁含硅量从投产初期的1.22%逐年下降,近年日常操纵[Si]稳固在0.30%~0.40%之间。
由于低硅冶炼操作,促进了8号高炉综合燃比的降低和利用系数的提高,成效十分显著。
表18号高炉要紧操作参数时刻利用系数t/(m3.d)焦比kg/t煤比kg/t[Si]%[S]%渣R2倍入炉品位%一级品率%风温℃1999 1.952 457 74 0.45 0.017 1.09 54.03 94.64 1007 2000 1.990 403 123 0.45 0.017 1.09 54.65 96.77 1011 2001 2.092 390 135 0.40 0.020 1.08 56.07 92.77 1028 2002 2.102 389 145 0.39 0.022 1.11 57.51 92.80 1025 2003 1.919 383 147 0.52 0.023 1.12 57.47 90.76 1018 2004 2.059 382 150 0.38 0.031 1.12 56.65 63.39 1078 2005 2.205 359 151 0.36 0.024 1.15 56.93 92.53 1167 2006 2.100 368 143 0.39 0.026 1.17 55.45 84.92 1158 2007 2.065 404 137 0.43 0.027 1.17 55.29 72.35 1084 2高炉冶炼低硅铁的机理分析依照炼铁理论高炉内SiO2的还原发生在滴落带,对应的要紧部位是炉腹,而在炉缸下部渣和铁接触界面上进行的反应是铁中硅的再氧化。
高炉冶炼低硅生铁技术的探讨
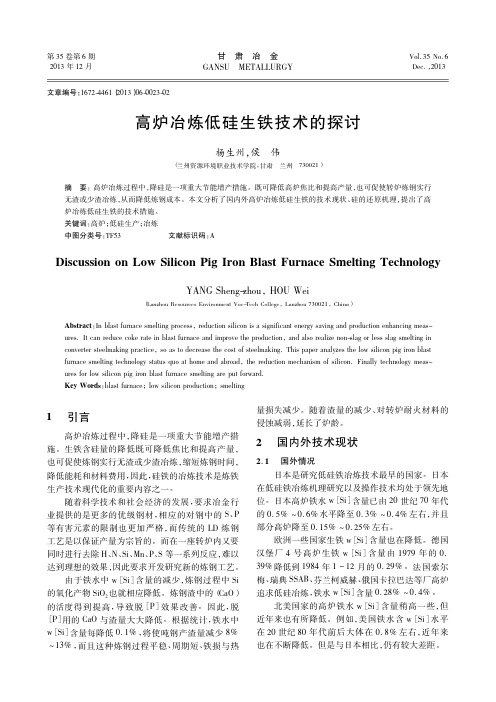
第35卷第6期2013年12月甘肃冶金GANSU METALLURGYVol.35No.6Dec.,2013文章编号:1672-4461(2013)06-0023-02高炉冶炼低硅生铁技术的探讨杨生州,侯伟(兰州资源环境职业技术学院,甘肃兰州730021)摘要:高炉冶炼过程中,降硅是一项重大节能增产措施。
既可降低高炉焦比和提高产量,也可促使转炉炼钢实行无渣或少渣冶炼,从而降低炼钢成本。
本文分析了国内外高炉冶炼低硅生铁的技术现状、硅的还原机理,提出了高炉冶炼低硅生铁的技术措施。
关键词:高炉;低硅生产;冶炼中图分类号:TF53文献标识码:ADiscussion on Low Silicon Pig Iron Blast Furnace Smelting TechnologyYANG Sheng-zhou,HOU Wei(LanzhouResources Environment Voc-Tech College,Lanzhou730021,China)Abstract:In blast furnace smelting process,reduction silicon is a significant energy saving and production enhancing meas-ures.It can reduce coke rate in blast furnace and improve the production,and also realize non-slag or less slag smelting in converter steelmaking practice,so as to decrease the cost of steelmaking.This paper analyzes the low silicon pig iron blast furnace smelting technology status quo at home and abroad,the reduction mechanism of silicon.Finally technology meas-ures for low silicon pig iron blast furnace smelting are put forward.Key Words:blast furnace;low silicon production;smelting1引言高炉冶炼过程中,降硅是一项重大节能增产措施。
高炉低硅冶炼知识
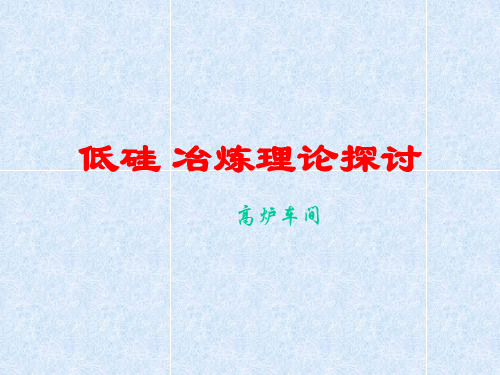
以上是高炉内硅的还原与氧化等的主 要反应式,如果以风口中心线(面) 为界,从以上反应特点可知,风口中 心线(面)以上为硅的还原区(吸硅、 增硅),风口中心线(面)以下为硅 的氧化区(脱硅、减硅)。以离子式 可以表达为: Si4++4e=Si(风口中心线以上)
Si-4e=Si4+(风口中心线以下)
4.4一些冶炼低硅铁的高炉炉渣与[Si]含量 的回归方程
日本解剖了12座大小高炉,从软熔带液相以下, [Si]一直是增加的,在风口处达到最大,这与上述反 应式传统的炼铁理论截然不同. 日本Байду номын сангаас先提出高炉内Si迁移的新理论,确认在炉 腹和炉缸,SiO气相的生成对Si迁移起着重要的作用。 Si的还原过程反应为:
SiO2(焦炭灰分中或炉渣中)+C(S)=SiO(R)+CO(g)
三、最佳硅含量的选择
• 铁水含硅不一定越低越好,要综合考虑 冶炼效果。特别是在炉况不正常、原料 条件大幅度波动或炉役后期,很难做到 维持铁水含[Si]不波动,同时考虑到原料 准备等诸方面付出的代价和操作人员精 神紧张程度,倒不如采取低硅冶炼与炉 外处理相结合更为合理。
我国精料水平近年来虽然有大幅度提高, 但原料条件差,炉容不大,顶压也较低,热 损失大,铁水温度也比日本低,要实现生铁 含硅量在0.25%左右困难太大,而且硅含量 在0.25%左右时经济效益也不一定就好。 就我国目前情况而言,铁水含[Si]普遍 偏高,就现阶段来看,铁水含[Si]可能在 0.3~0.4%左右为宜。
(7)日本水岛高炉(2500m3级)冶炼[Si]=0.18%时(2#高炉) [Si]%=1.913-1.309((CaO+MgO)/(SiO2+AI2O3))-0.50 (FeO)%-0.529[Mn]%
- 1、下载文档前请自行甄别文档内容的完整性,平台不提供额外的编辑、内容补充、找答案等附加服务。
- 2、"仅部分预览"的文档,不可在线预览部分如存在完整性等问题,可反馈申请退款(可完整预览的文档不适用该条件!)。
- 3、如文档侵犯您的权益,请联系客服反馈,我们会尽快为您处理(人工客服工作时间:9:00-18:30)。
第5期2000年9月湖 南 冶 金HUNAN M ETALLU R GYN o 15Sep t 12000收稿日期: 2000—06—12高炉低硅铁的冶炼实践尹 坚(湘潭钢铁集团有限公司,湖南 湘潭 411101)摘 要:分析了高炉冶炼中硅的还原机理,根据分析结果明确了低硅冶炼应具备的条件。
湘钢1#高炉在低硅冶炼的攻关实践中,按低硅冶炼应具备的条件采取了相应的技术措施与管理措施,取得了良好的经济效益。
关键词:高炉;低硅铁冶炼;技术措施;管理措施中图分类号:T F 631 文献标识码:A 文章编号:1005—6084(2000)05—0022—03PRACTI CE OF S M EL TING LOW -SI LL I CONIRON ON B LAST FURNACEY I N J ian(X iang tan I ron &S teel G roup L i m ited Co m p any ,X iang tan 411101,Ch ina )ABSTRACT :Sillicon reducing p rinci p le on b last fu rnace s m elting w asanalyzed .Conditi on s of s m elting low -Sillicon iron w ere po in ted ou t .A cco rding to the conditi on s ,co rresponding techno logy m easu res and m anagem en t m easu rs w ere app lied ,better econom ic effect w as gained .KEY WORD S :b last fu rnace ;s m elting low -Sillicon iron ;techno logym easu res ;m anagem en t m easu res1 前 言降低生铁含硅量不仅高炉能降低焦比,提高产量,而且炼钢也可减少造渣量,缩短炼钢冶炼时间,因此低硅铁的冶炼技术是炼铁生产技术现代化的重要内容之一,也是现代炼钢工艺的必然要求。
目前先进高炉的生铁含硅量控制在012%~013%。
湘钢1#高炉自1996年投产后的两年中,由于受设备、原料、工艺操作技术的影响,高炉炉况不稳,焦比极高,生铁含硅量高达01834%。
1999年以来,随着原料条件的稳定,设备管理水平的提高,操作技术的进步,1#高炉开展了降低生铁含硅量的攻关,生铁含硅量明显降低,尤其是近半年来生铁中硅含量达到了0140%左右的水平。
2 冶炼低硅生铁的必备条件211 硅的还原机理国内外的高炉解剖证明,硅从炉腹中部第5期尹 坚: 高炉低硅铁的冶炼实践 23明显增加,到炉腹下部超过了成品生铁中硅含量,而进入渣层后硅又逐渐降低。
因此高炉内硅的还原反应主要发生在1500℃以上的高温区,即主要发生在滴落带,硅进入铁水中的反应过程为:Si O2在高温下(>1500℃)被碳还原,先生成Si O气体,Si O2+C= Si O+CO;Si O再被[C]还原生成[Si]而进入生铁,Si O+[C]=[Si]+CO。
由此可以看出,从软熔带顶部开始至风口区,[Si]量逐步增加。
在此区域,焦炭燃烧,温度高,原料中的Si O2活度大,与碳的接触条件好,被还原成大量的Si O气体,滴落带含有饱和碳的铁由Si O气体吸收被还原成[Si]进入生铁。
从风口区到铁口区段[Si]量逐步减少,降硅原因有两个:一是由于鼓风中的氧将[Si]氧化,二是渣中M nO、FeO等与[Si]发生偶合反应,将铁水中的[Si]氧化。
212 冶炼低硅生铁的必备条件根据上述分析,冶炼低硅生铁的主要条件是:(1)采用成分稳定,还原性好且熔化温度高的原料,这样可以扩大块状带区,减少高温区域热量消耗,使软熔带下移,缩短硅的还原路程,同时可使铁水保持较高温度而获得低硅铁水。
(2)采用合理的操作制度,要求炉内煤气流分布合理而且稳定。
(3)在喷吹量大时采用高风温,使高温区下移以减少硅的还原,同时在低硅条件下可获得较高的渣铁物理热,对降低含硅量有利。
(4)降低焦比、降低焦炭中灰分的含量有利于低硅铁的冶炼。
(5)维持较高的炉渣碱度,使炉渣内活度降低,不仅抑制Si O2的还原,而且有利于生铁中[Si]再氧化进入炉渣。
(6)设备完好,运行稳定。
3 生产实践在低硅冶炼攻关的实践中,1#高炉生铁含硅量及主要指标的变化见表1。
从表1可以看出,1#高炉的[Si]逐步降低,各项技术指标改善,取得明显成效。
近年来进行低硅冶炼攻关中所采取的技术与管理措施主要有以下几个方面。
表1 1#高炉生铁含硅量及主要技术指标年[Si] %风温 ℃CO2 %入炉焦比 kg・t-1喷煤比 kg・t-1渣铁比 kg・t-1利用系数 t・m-3・d-1 199601834 9329196603619452401921 199701699 992141805636618949211230 1998016841054151085637518247311424 1999015101049151924909013942511948 20003014701062151564739519641421080 3为2000年1~5月。
311 抓好高炉精料工作加强原料管理,抓好大宗原燃料的进厂质量,改善烧结矿的质量,提高熟料比。
对高炉烧结筛进行了改造,将其改为外传动高振幅双层电动筛,筛片由“人”字型改为梳式,提高筛分效率。
1999年开始对入炉生矿过筛,原料入炉粉末降至5%以下,为高炉降低焦比和冶炼低硅铁创造了有利条件。
焦炭质量不断提高,近年来焦炭灰分含量达到12%以下,焦炭硫约0156%,M25> 8811%的稳定率与M10<810%的稳定率达到了98%以上。
1#高炉烧结矿与焦炭改善情况见表2。
312 强化煤气的合理分布,稳定炉况冶炼低硅生铁时,最重要的是提高煤气的热能和化学能的利用,为得到合理的煤气24 湖 南 冶 金第5期表2 烧结矿与焦炭质量的改善情况年烧 结 矿T Fe稳定率 %R稳定率 %转鼓%焦 炭灰分%硫分%M25M1019977911673189661651214401718913713 19988213076100661951218101658819717 19998919882159671261211201588818718 200039116882186691291119301558819719 3为2000年1~5月。
流分布,主要措施有:(1)采用大矿批正分装,同时进行多环布料,促使高炉炉料分布均匀,有利于煤气流的稳定。
1#高炉矿批从原来18t 批扩大到31t 批,炉况稳定性增加,高炉坐料次数从原来的每月20多次降到0~1次 月。
(2)在送风制度上实现了全风量、全风口喷吹等措施,提高风速与鼓风动能。
使煤气在炉缸的初始分布合理,炉缸截面温度分布均匀;炉缸工作活跃,这对控制硅的还原和保证炉渣具有良好的脱硫性能提供了有利条件。
313 低焦比操作1#高炉自1999年以来,逐步实现了高风温、多风口均匀大喷吹。
风温从1000℃提高到1100℃,喷煤量从70kg t铁提高到110kg t铁,高炉煤气利用率也由14%提高至1615%左右,入炉焦比由520kg t铁降低到440kg t铁,入炉焦比的降低,有效地降低了Si O2带入量,同时减少了硅的还原。
314 采用高碱度、高氧化镁的造渣制度1#高炉在低硅铁的冶炼过程中,注重控制好炉渣碱度,碱度控制由原来的1115提高至1118~1120,同时保证渣中的M gO在9%~11%。
适当提高炉渣碱度及保证M gO含量,可提高炉渣的熔化温度,增加炉缸热量的储备,改善炉渣流动性,提高了炉渣的脱硫能力,又可缩短熔滴带的厚度,铁水温度相对提高,这样在较高的焦炭负荷条件下,也能促使低硅生铁冶炼顺利进行。
315 控制炉缸温度,稳定炉温在低硅生铁的冶炼过程中,炉缸温度的高低关系到炉温的稳定,1999年下半年以来,1#高炉的含硅量按013%~014%来操作,并努力防止炉温过低,保炉况的顺行,一级品率也逐步提高。
采取的具体措施有:(1)稳定风量与料批。
小时料批均匀,班与班之间的料批差控制在±1~2批。
(2)稳定风温与综合负荷。
一次降风温不能超过50℃,综合负荷在±011以上的调整不超过2h。
(3)加强原料入炉的电子秤的管理,执行定期校秤制度,防止原料称量变化引起炉温大起大落。
(4)加强三班操作统一。
搞好三班衔接的综合判断炉况,勤观察,勤分析,勤调剂,坚持早动、小动、小幅调剂。
316 加强管理,保证炉况稳定(1)强化出渣出铁的作业管理,提高出铁正点率,减少炉缸内的贮铁贮渣量,避免渣铁贮量过多而使风压过高、料速变慢而炉温升高。
铁次从10次提高至12次,正点率从30%提高至80%。
(2)加强设备管理,保证设备的稳定率与完好率,防止设备故障造成非计划休风而引起热量补充不足,休风率由原来的9%下降至215%。
(3)对主沟、渣铁沟、砂口、铁罐等系统的耐火材料的侵蚀加强跟踪管理,特别是对主沟的修补已做到不影响铁次。
4 结 语湘钢1#高炉进行低硅冶炼攻关后,月平均[Si]已由018%降至014%,产量增加,焦比下降,目前的入炉焦比已降至442kg t,利用系数已提高至2121t (m3・d)的水平,取得了良好的经济效益。