产品工程DFM制作检验清单
如何制作DFM(两篇)

引言概述:在制造业中,DFM(Design for Manufacturing)是一个重要的概念。
它指的是在产品设计阶段就考虑到制造的可行性和效率,以最大程度地降低制造成本和缩短生产周期。
本文将详细介绍如何制作DFM,包括设计规范、材料选择、工艺流程和品质控制等方面的内容。
正文内容:1. 设计规范1.1.了解制造能力和限制:在开始设计前,应了解制造厂商的能力和限制,包括设备和技术。
这将有助于避免设计上的不可行之处。
1.2.简化设计:通过减少零部件数量和复杂性来简化设计,可以降低制造成本和提高生产效率。
1.3.尺寸与公差:在设计过程中,应合理设置尺寸和公差。
不合理的尺寸和公差可能导致制造困难和许多再加工工序。
1.4.设计可维修性:考虑到产品的维修和保养需求,设计应具有易于拆卸和更换零部件的特点,以降低维修成本和减少停机时间。
1.5.标准化和模块化设计:采用标准元件和模块化设计可以提高设计的可重复性和可扩展性,从而降低制造成本并加快产品交付速度。
2. 材料选择2.1.材料特性:根据产品的特性和使用要求,选择适合的材料。
例如,在高温环境下要求高强度和耐腐蚀性的产品可以选择不锈钢等材料。
2.2.供应链管理:选择可靠的供应商和合适的材料,同时对供应链进行管理,以确保材料的质量和及时交货。
2.3.可回收材料:考虑到环境保护的需求,优先选择可回收材料,以减少对自然资源的消耗。
3. 工艺流程3.1.制程规划:制定详细的工艺流程和制程规范,包括材料准备、加工工序、装配工序等,以确保生产过程的顺利进行。
3.2.自动化生产:使用自动化设备和流程以提高生产效率和降低人工成本。
例如,采用自动化装配线可以提高装配速度和产品质量。
3.3.质量控制:在每个制程工序中进行严格的质量控制,包括原材料检验、工序检验和成品检验。
这有助于提前发现和纠正制程中的问题,并确保产品质量符合要求。
4. 设备投资4.1.设备选择:根据生产需求和预期产量,选择适合的设备。
电子产品dfm报告

电子产品dfm报告1.引言1.1 概述概述:DFM(Design for Manufacturability,制造可行性设计)是一种在产品设计阶段就考虑到产品的制造过程的设计方法。
通过DFM,设计人员可以提前考虑到产品的制造过程中可能出现的问题,有效降低产品的制造成本、缩短产品的制造周期,同时提高产品的质量和可靠性。
本报告旨在深入探讨电子产品设计中DFM的重要性和实际应用案例,探讨DFM对电子产品设计的影响,并展望未来DFM的发展趋势。
通过对DFM的深入了解,可以帮助设计人员更好地理解和应用DFM方法,从而优化电子产品的设计与制造流程。
1.2 文章结构文章结构部分内容:本文将分为三个主要部分,分别是引言、正文和结论。
在引言部分,将对DFM报告进行概述和阐述文章的结构,同时明确本文的目的。
在正文部分,将分三个子部分来讨论DFM在电子产品设计中的重要性,包括什么是DFM、DFM的实际应用案例等。
最后,在结论部分,将总结DFM 对电子产品设计的影响,并展望未来DFM发展的趋势,最终给出结论。
通过这样的结构设计,将全面分析DFM在电子产品设计中的重要性和实际应用,为读者提供全面深入的了解和启发。
1.3 目的本报告旨在探讨DFM(Design for Manufacturing)在电子产品设计中的重要性以及其实际应用案例。
通过对DFM概念的深入剖析和对其在电子产品设计中的影响的研究,旨在为电子产品设计师和制造商提供更好的理解,并帮助他们在产品设计阶段就考虑到制造的可行性和成本效益性。
另外,通过展望未来DFM的发展趋势,也有助于行业内人士对DFM 的重要性有更清晰的认识,并为未来的产品设计和制造提供更好的指导和建议。
2.正文2.1 什么是DFMDFM是Design for Manufacturing的缩写,即为制造设计。
它是一种在产品设计阶段就考虑产品制造过程的方法和原则。
DFM的目标是通过在设计阶段考虑制造工艺及成本等因素,来优化产品的设计,提高产品制造的效率和质量,降低制造成本,缩短产品的上市时间。
SMT DFM(可制造性设计)检查表

文件编号:LCT-PC-All-QD一、产品基本信息□研发阶段□中试阶段□量产阶段二、SMT技术资料三、PCB制造工艺要求(一)PCB 设计3、PCB之工艺边:定位孔A、定位孔直径(∮=3~4mm);B、定位孔距离板角坐标:X=5mm,Y=5mm。
C、PCB四边均需要工艺边框,其中2个长边宽度应大于8mm以上,短边应大于3mm以上。
D、PCB板顶角成圆弧形。
□□□1、PCB之工艺边定位孔:Ph ilips FCM高速贴装机Carrier传动结构特殊要求。
2、见图示(一)。
4、PCB小板:夹具孔周边1mm内不允许有元器件,以免与夹具干涉。
□□□1、PCB小板夹具孔:通用要求。
2、见图示(一)。
5、PCB焊盘、通孔设计A、同一元件Pad形状、面积要相同;与材料管脚规格匹配。
B、焊盘相邻边间隙要求大于8Mil;若无法达到8Mil,则不能小于6Mil(且须在Gerber文件中指出其位置)。
C、PCB上通孔(via hole)需要密封。
D、Pad上via尽可能小,且必须全部密封。
E、零件间距不会造成放置时互相干涉。
F、BGA焊盘间面积要相等;焊盘上通孔(via hole)尽可能引至边缘或焊盘外。
□□□1、间隙太小,仅0.1mm。
2、间隙要大于8Mil(0.2mm)。
1、BGA焊盘面积不相同。
2、焊盘上通孔移至边缘或焊四、SMT制程控制要求4.1. 锡膏管控1、锡膏选择。
2、运输、存放。
3、生产使用管制。
4.2. 钢板及刮刀、治具管控4.3. 元件选择4.4. 材料Profile 参数设定1、 Profile 量测位置选取原则:大组件、BGA 、QFP 、屏蔽盖内等。
2、 Profile 参数:1) 有铅: 峰值温度为215℃~225℃;179℃~183℃回流时间60~90 S ;上升斜率<3℃/ S 。
2) 局部无铅:Peak 为225℃~230℃;220℃以上30~40S ;回流时间80~110S 。
dfm报告是什么意思
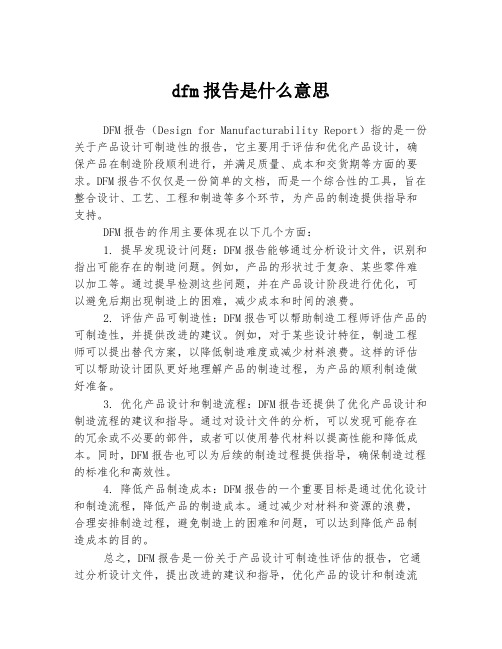
dfm报告是什么意思DFM报告(Design for Manufacturability Report)指的是一份关于产品设计可制造性的报告,它主要用于评估和优化产品设计,确保产品在制造阶段顺利进行,并满足质量、成本和交货期等方面的要求。
DFM报告不仅仅是一份简单的文档,而是一个综合性的工具,旨在整合设计、工艺、工程和制造等多个环节,为产品的制造提供指导和支持。
DFM报告的作用主要体现在以下几个方面:1. 提早发现设计问题:DFM报告能够通过分析设计文件,识别和指出可能存在的制造问题。
例如,产品的形状过于复杂、某些零件难以加工等。
通过提早检测这些问题,并在产品设计阶段进行优化,可以避免后期出现制造上的困难,减少成本和时间的浪费。
2. 评估产品可制造性:DFM报告可以帮助制造工程师评估产品的可制造性,并提供改进的建议。
例如,对于某些设计特征,制造工程师可以提出替代方案,以降低制造难度或减少材料浪费。
这样的评估可以帮助设计团队更好地理解产品的制造过程,为产品的顺利制造做好准备。
3. 优化产品设计和制造流程:DFM报告还提供了优化产品设计和制造流程的建议和指导。
通过对设计文件的分析,可以发现可能存在的冗余或不必要的部件,或者可以使用替代材料以提高性能和降低成本。
同时,DFM报告也可以为后续的制造过程提供指导,确保制造过程的标准化和高效性。
4. 降低产品制造成本:DFM报告的一个重要目标是通过优化设计和制造流程,降低产品的制造成本。
通过减少对材料和资源的浪费,合理安排制造过程,避免制造上的困难和问题,可以达到降低产品制造成本的目的。
总之,DFM报告是一份关于产品设计可制造性评估的报告,它通过分析设计文件,提出改进的建议和指导,优化产品的设计和制造流程,降低成本,并最终实现高质量、高效率的产品制造。
这份报告对于保证产品顺利制造,优化产品性能和降低成本都起到了关键的作用。
dfm分析报告步骤

dfm分析报告步骤引言:DFM(Design for Manufacturing,制造可行性设计)是一种通过在设计阶段考虑到产品制造过程中的各种约束和要求,以达到更好的产品制造质量、降低成本和提高生产效率的设计方法。
DFM分析报告是对设计方案进行DFM分析后所生成的一个报告,该报告旨在帮助设计师识别和解决产品制造过程中可能出现的问题,以改进设计方案。
本文将介绍DFM分析报告的步骤,以帮助读者更好地理解如何进行DFM分析并生成有效的报告。
一、收集设计和制造相关信息在进行DFM分析之前,我们首先需要收集设计和制造相关的信息。
这些信息包括设计方案、产品规格、产品材料、制造工艺等。
通过收集这些信息,我们可以全面了解设计和制造的要求和约束,为后续的分析提供准确的基础。
二、确定关键设计要素在进行DFM分析时,我们需要确定关键的设计要素。
这些设计要素可以是对产品性能和质量影响较大的因素,也可以是对制造过程中可能出现问题的因素。
通过确定关键设计要素,我们可以有针对性地进行分析和改进,以提高产品的制造可行性。
三、进行DFM分析在进行DFM分析时,我们需要综合考虑产品设计和制造的各个方面,以识别可能存在的问题。
例如,我们可以通过分析产品的材料选择、结构设计、尺寸要求、表面处理等方面,找出可能导致制造问题的因素,并提出相应的改进建议。
同时,我们还可以通过模拟和实验等方法验证提出的改进方案的有效性。
四、生成DFM分析报告在完成DFM分析后,我们需要将分析结果整理并生成DFM分析报告。
DFM分析报告应包括以下内容:1. 设计要求和制造约束:列出设计要求和制造约束,以便读者清楚了解设计和制造的要求和限制。
2. 分析结果:将进行DFM分析过程中所发现的问题和改进建议详细列出。
例如,如果发现某个设计要素可能导致制造问题,可以提出相应的修改意见,并说明修改后可能带来的好处。
3. 实施建议:根据分析结果,提出实施DFM改进的建议。
dfm报告

dfm报告【DFM报告:打造高效生产与卓越质量的关键】DFM (Design for Manufacturing,制造设计)是指在产品设计阶段,充分考虑到产品的制造性、工艺性和可靠性,以降低制造成本、缩短生产周期、提升产品质量的一系列技术与方法。
DFM 报告是对产品设计进行评估和分析,以指导产品设计师制定出更好的产品设计方案。
本文将从DFM 的定义、重要性和关键要素等方面展开介绍,以及如何实施DFM 报告的步骤和效益。
DFM的定义及重要性DFM(Design for Manufacturing)是指在产品设计阶段,将制造过程的要素结合到产品结构中,以降低制造成本、提高质量并缩短生产周期的设计方法。
DFM 的最终目标是全面优化产品的制造性能,使其能够在现有生产设备和工艺条件下高效地生产出来。
DFM 在产品设计中的重要性不容忽视。
首先,通过在设计过程中考虑制造的可行性和工艺要求,可以降低产品的制造成本。
合理的设计方案,可以减少物料的浪费和加工工艺的复杂度,从而降低了产品的制造成本。
其次,DFM 还可以提高产品的质量。
通过合理的设计,可以减少产品在生产过程中出现的问题,提高产品的整体质量稳定性。
此外,DFM 还能缩短产品的生产周期,提高生产效率,使企业能够更快速地响应市场需求。
DFM 的关键要素在进行DFM 报告之前,必须了解DFM 的关键要素。
首先是构造设计,也就是产品的基本结构和形状。
构造设计直接关系到产品的制造过程和生产工艺,因此必须在设计阶段就进行合理的规划。
其次是材料选择,选择合适的材料可以降低制造成本、提高产品质量,并满足产品的性能需求。
再次是生产工艺,即确定产品的制造工艺和生产流程。
通过合理的生产工艺设计,可以提高生产效率并确保产品的质量稳定性。
最后是工装设计,工装是固定、辅助和保护产品在生产过程中的装置或工具。
合理的工装设计可以提高生产效率,减少误差和损坏。
DFM报告的步骤进行DFM 报告的过程需要经过以下步骤:首先是收集产品信息,包括产品的设计图纸、技术要求和工艺流程等。
DFM报告清单范文
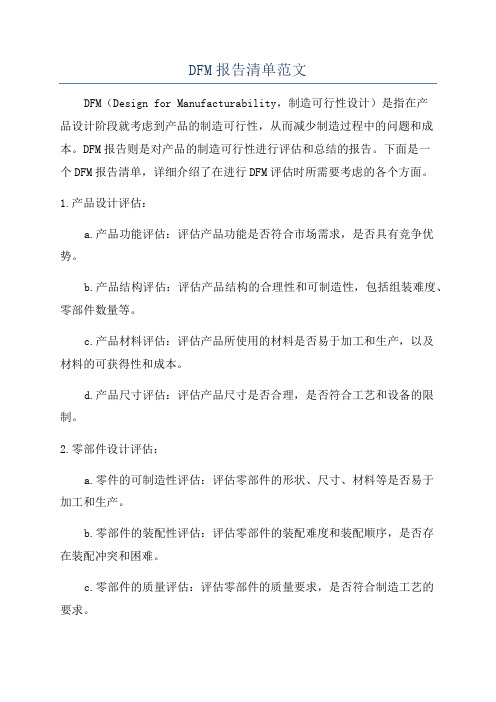
DFM报告清单范文DFM(Design for Manufacturability,制造可行性设计)是指在产品设计阶段就考虑到产品的制造可行性,从而减少制造过程中的问题和成本。
DFM报告则是对产品的制造可行性进行评估和总结的报告。
下面是一个DFM报告清单,详细介绍了在进行DFM评估时所需要考虑的各个方面。
1.产品设计评估:a.产品功能评估:评估产品功能是否符合市场需求,是否具有竞争优势。
b.产品结构评估:评估产品结构的合理性和可制造性,包括组装难度、零部件数量等。
c.产品材料评估:评估产品所使用的材料是否易于加工和生产,以及材料的可获得性和成本。
d.产品尺寸评估:评估产品尺寸是否合理,是否符合工艺和设备的限制。
2.零部件设计评估:a.零件的可制造性评估:评估零部件的形状、尺寸、材料等是否易于加工和生产。
b.零部件的装配性评估:评估零部件的装配难度和装配顺序,是否存在装配冲突和困难。
c.零部件的质量评估:评估零部件的质量要求,是否符合制造工艺的要求。
3.制造工艺评估:a.制造流程评估:评估产品的制造流程,包括加工、装配、测试等环节,是否合理和高效。
b.制造设备评估:评估所需的制造设备是否满足产品的制造需求,包括设备的性能和容量。
c.制造成本评估:评估产品的制造成本,包括材料成本、加工成本、人工成本等。
d.制造周期评估:评估产品的制造周期,是否满足市场的需求和竞争要求。
4.质量控制评估:a.质量标准评估:评估产品的质量标准和要求,包括尺寸、外观、功能等。
b.质量控制方案评估:评估产品的质量控制方案,包括检验、测试、保证和改进等环节。
c.不良品处理评估:评估产品不良品的处理方法和成本,以及减少不良品的措施和策略。
5.反馈和改进:a.制造问题反馈:总结和反馈制造过程中出现的问题,包括零部件加工难度、装配问题等。
b.设计改进建议:提出产品设计改进的建议和措施,以提高产品的制造可行性和质量控制。
c.制造成果总结:总结产品的制造成果和经验教训,以便后续产品的设计和制造过程参考。
产品dfm报告是什么意思

产品dfm报告是什么意思什么是DFMDFM是Design for Manufacturability(可制造性设计)的缩写,是一种将产品设计、工程和制造领域的原则和方法相结合的设计过程。
DFM的目标是通过优化产品的设计,使得产品在制造、装配和维护过程中更容易和更经济地生产。
DFM考虑了材料的选取、工艺的选择、零件的设计、装配的方案等诸多因素,以最大程度地提高制造效率、降低成本、增强产品质量。
什么是产品DFM报告产品DFM报告是对产品设计可制造性的评估和分析的文档,旨在为设计师、工程师和制造商提供指导和建议,帮助他们改进产品设计,以便更好地满足制造要求和标准。
产品DFM报告通常由专业的DFM团队或工程师编制,涵盖了产品设计、材料、工艺、质量和成本等方面的考虑。
产品DFM报告的内容产品DFM报告通常包括以下内容:1. 产品设计评估产品设计评估是产品DFM报告中的重要部分。
它涉及对产品设计图纸、样品或虚拟模型的分析,以评估其制造可行性和可优化性。
产品设计评估主要考虑以下因素:- 零件的形状和结构:评估零件的形状、尺寸和结构是否符合制造工艺的要求,是否能够在加工过程中保持稳定性和精度。
- 零件材料的选择:评估零件材料的可用性、成本和适用性,以及其对产品性能和质量的影响。
- 零件的装配方式:评估零件的装配方式和顺序,以确保装配过程的顺利进行和高效性。
2. 材料选择和工艺优化产品DFM报告还涉及材料选择和工艺优化的建议。
这部分主要考虑以下内容:- 材料的选择:根据产品的需求和制造要求,评估不同材料的可行性,并提出合适的材料选择建议。
- 工艺的选择:评估不同工艺的优劣,选择最适合产品要求和制造成本的工艺,并提供工艺优化的建议。
- 加工和装配方法:提供加工和装配方法的建议,以确保零件和组件能够在制造过程中顺利加工和装配。
3. 质量控制和测试方案产品DFM报告还包括质量控制和测试方案的建议。
这部分内容主要考虑以下方面:- 质量控制方法:提供质量控制方法和措施的建议,以确保产品在制造过程中达到预定质量标准。
DFM产品可制造性设计规范

文件制修订记录1.0目的为了让设计者更好的了解如何在材料,工艺和设备影响印刷电路设计,提供设计和布局的印刷电路组件的概念,给设计者一个基本的设计建议和NPI工程师一个基本指导。
2.0适用范围:适用于指导PCB产品的生产过程中所需的要求。
3.0术语:3.1 DFM:产品可制造性设计(Design for manufacturability)。
用来确定生产线的规划,使其设备满足公司产品、工艺和品质要求。
3.2 PCB:Printed Circuit Board印刷线路板;3.3 FPC:Flexible Printed Circuit 简称,柔性印刷线路板;3.4 layout: 布局设计。
4.0职责:4.1项目BU负责与客户沟通,向公司内部传达客户信息;4.2 NPI小组的PIE/ME负责制作DFM报告,NPI组长负责主导召开新产品评估会议和DFM报告的审核,工程部经理负责批准;4.3新产品导入小组(NPI)负责评估新产品的可制造性。
5.0程序:5.1项目BU负责在新合同评审时,在客户有要求或者NPI小组评估需要时召集公司NPI专家评审小组成员对新产品进行可制造性评审,由NPI PIE/ME负责根据会议的结果在两个工作日内完成“可制造性评估(DFM)报告”;5.2 NPI PIE/ME将制作完成的DFM报告提交给NPI主管审核,审核OK之后,提交工程部经理批准;5.3工程部经理批准后DFM报告NPI主管转发给项目经理提交给客户或直接提供客户对应的工程人员;5.4 PIE/ME确认DFM报告中客户的评价与改善方案,以便作出相应的对策。
6.0可制造性设计规范DFM 1、PCB/FPC layout1.1印制线路要点:虽然布置layout是运用的软件,但是要考虑线路的形状尽可能的简单以此缩减制作成本,直角形状的板子比其它不规则的形状的成本低且更容易处理。
设计内部的拐角必须考虑板子的外形,避免暴露在外面。
简易dfm报告模板

简易DFM报告模板DFM(Design for Manufacture)是一种对产品设计进行优化,使得产品在制造和组装过程中更加容易、高效、准确的技巧。
DFM 的报告通常被用来汇报产品的可制造性和可组装性,以及为制造和工艺人员提供指导。
为了方便不具备DFM报告经验的人士,我们提供一份简易的DFM报告模板,以帮助您快速编写一个完整的DFM报告。
DFM报告概述DFM 报告的主要目的是为了评估产品的可制造性和可组装性,以提高产品的质量和生产效率。
这个报告应该包括以下内容:•产品的各个组件•组件的制造和组装工艺•制造和组装过程的关键参数•工艺改进的建议和措施DFM报告内容1. 产品的各个组件在这个部分中,应该列出产品的所有组件,并且为每个组件提供一个简要的说明。
例如:组件说明壳体产品的外观外壳,由注塑成型制成电路板包含产品的所有电子元件和接口电路电池提供电源的不可拆卸电池按钮控制产品开关和音量等功能的按钮请注意,这个表格只需要列出最基础的组件,如果您的产品还包含其它复杂的组件,可以根据需要增加或删除。
2. 组件的制造和组装工艺在这个部分中,应该为每个组件提供制造和组装工艺的详细说明。
例如:电路板•制造工艺:采用印刷电路板(PCB)制造工艺•PCB 材料: FR4 板,1.6mm 厚度,2 oz 铜厚•元件安装工艺:采用表面贴装(SMT)技术,元件焊接采用回流焊接方法•焊接材料:使用高温铅自由钎焊材料壳体•制造工艺:采用注塑成型工艺•材料:采用 ABS 工程塑料•模具:采用冷却液循环的钢模具请注意,这个部分的描述应该足够详细,以便制造和工艺人员能够理解和操作。
3. 制造和组装过程的关键参数在这个部分中,应该列出组件制造和组装过程中的关键参数和质量控制点。
例如:电路板•PCB 的最小线宽/线距: 0.1mm•PCB 的最小孔径: 0.3mm•元件最小封装: 0603•最大元件尺寸: 25mm x 25mm•焊接温度曲线:最大温度 250℃,焊接时间不超过 10 秒壳体•壳体最大变形量: 0.3mm•壳体的裂纹和气泡缺陷不得超过 3 个•模具的使用次数不得超过 100,000 次请注意,这个部分中的参数和质量控制点应该根据产品的特性和制造工艺的实际情况进行调整。
DFM作业指导以及问题点checklist
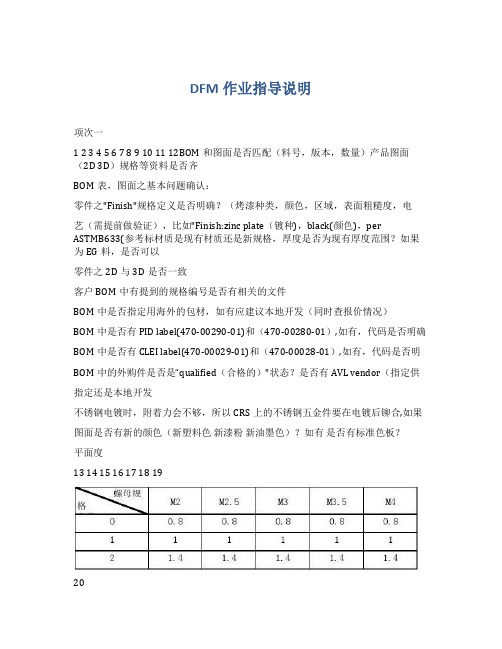
DFM作业指导说明项次一1 2 3 4 5 6 7 8 9 10 11 12BOM和图面是否匹配(料号,版本,数量)产品图面(2D 3D)规格等资料是否齐BOM表,图面之基本问题确认:零件之"Finish"规格定义是否明确?(烤漆种类,颜色,区域,表面粗糙度,电艺(需提前做验证),比如"Finish:zinc plate(镀种),black(颜色),per ASTMB633(参考标材质是现有材质还是新规格,厚度是否为现有厚度范围?如果为EG料,是否可以零件之2D与3D是否一致客户BOM中有提到的规格编号是否有相关的文件BOM中是否指定用海外的包材,如有应建议本地开发(同时查报价情况)BOM中是否有PID label(470-00290-01)和(470-00280-01),如有,代码是否明确BOM中是否有CLEI label(470-00029-01)和(470-00028-01),如有,代码是否明BOM中的外购件是否是“qualified(合格的)"状态?是否有AVL vendor(指定供指定还是本地开发不锈钢电镀时,附着力会不够,所以CRS上的不锈钢五金件要在电镀后铆合,如果图面是否有新的颜色(新塑料色新漆粉新油墨色)?如有是否有标准色板?平面度13 14 15 16 17 18 192021 22 23抽孔攻芽应确认底孔大小是否合适,抽孔高度是否足够3个芽距?通常依无屑攻芽针对自攻牙,必须清楚其是管控预冲孔,还是成型后尺寸,预冲孔必须要合适,对于烤漆件,必须确认清楚,图面相关的尺寸是否烤漆前尺寸还是烤漆后尺寸?螺母压入材料太浅或材料太薄均会导致松动,需检查板厚与螺母是否匹配?如S- 0.8厚的板上五金件规格是否明确,底孔规格是否与AVL供应商产品手册中的要求一致?烤漆件压铆五金件时,孔内不要溢漆,保证铆合强度要烤漆的上盖类产品后接缝要有0.5mm的间隙避免脱漆丝移印之Artwork(插图)规格是否明确,如内容,字体,大小,颜色,位置,定上)焊接需确认的问题点:a.品质要求(表面外观,打磨)焊接强度一般为母材的70是否可以做结构改善或者移动焊接位置);d.有无防水震动测试要求;e.需表面处理的产品,对在焊接位置加小凸包或凸点半剪凹坑来增加焊接强度及定位;g.缝焊时的对接间隙要求:对于可(因为实际由于加工误差自然会产生间隙)实际焊接时间隙要求为:对于氩焊(TIG焊)间隙于MIG焊间隙为10%t~1.0mm,对于激光焊间隙为0~10%T;h.激光焊一般是一点点焊,变形小强度有焊丝的铁件表面有丝印或移印要求,需要确认ARTWORK于铁件表面结构的匹配性,丝印工凸不平,在丝印区域附近不能有锋利棱角以免丝印时导致丝网破裂24 25 26 27 28 29 30 31 32 33 34 35 36 37图面每一条NOTES要求是否可以达到?Notes中信息与标题栏信息是否一致(材质零件之级面定义是否明确?尺寸标注是否齐全,功能性的配合尺寸是否有标注?零件(组件)之公差设定是否图面视图投影关系为第一还是第三视角?零件切边定义(毛边方向大小)是否清楚?冲孔毛刺方向如无特别指定,以装配毛边,当孔中要装配其他零件时考虑毛边对尺寸的影响,避免过小间隙的装配,可能的话让毛边图面引用什么标准?这些标准是否available(有效的)?零件是否能达到这些标准客户之要求与业界采用之标准(如工艺方面)不一致,且难以实现时需要提出。
可制造性设计(DFM)的实时质量检测
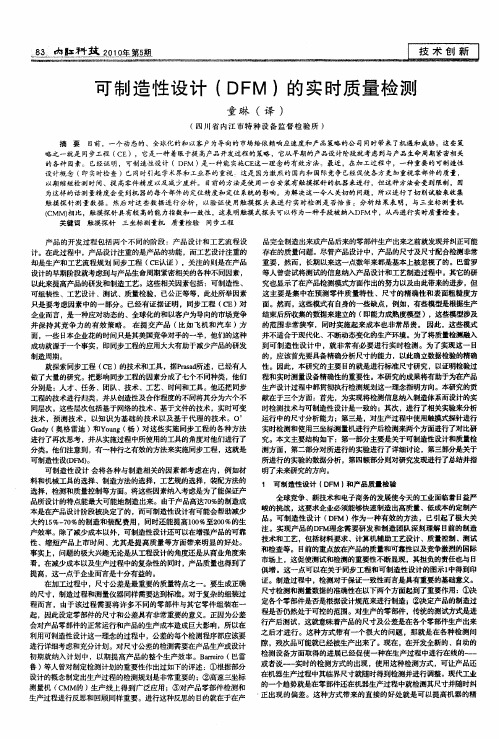
8 南 曩 署 2 1 年第5 3 工斗 0 o
技 术 创 新
可 制 造 性 设计 ( M )的实 时质 量检 测 DF
关键词ห้องสมุดไป่ตู้触摸 探 针 三 坐标 测 量 机 质 量检 验 同步 工 程
产品的开 发过程包 括两个 不同 的阶段 :产 品设计和 工艺流 程设 计。在此过程 中,产品设计注重的是产品 的功能 ,而工艺设计注重的
却是 生产 和工艺流程规 划 同步工 程 ( E C 认证 ),关注的则是在产 品 设计 的早期阶段就考虑到与产品生命周期紧密相关的各种不同因素 ,
品完全制造出来或产品后来的零部件生产出来之前就发现并纠正可能 存在的质量问题 。 管产品设计中 , 品的尺寸及尺寸配合检测非常 尽 产 重要 ,然而 ,长期以来这一点数年来 都是基 本上被 忽视了的。巴雷 罗 等人曾尝试将测试的信息纳入产 品设计和工 艺制造过程 中。其它的研
以此来提高产品的研发和制造工艺 。这些相关因素包括 :可制造性、 可组装性 、工艺设计 、测试 、质量检验 ,已公正等等 ,此处所 举因素 只是要 考虑 因素 中的一部 分。已经有 证据证明 ,同步工程 ( E) C 对 企业而言 ,是一种应对动态的 、全球化的和以客户为导向的市场竞争 并 保持 其竞 争力 的有效 策略 。 在 提交产 品 ( 比如 飞机和 汽车 ) 方 面 ,一些 日本企业花的时间只是其美国竞 争对手的一半 , 他们 的这种 成功就源于一个事实 ,即同步工程的应用大大有助于减少产 品的研发 制造周期。 就探索 同步工程 ( E)的技术和工 具,据Paa ̄述 ,已经有人 C rs d 做了大量的研究。把影响同步工程的因素分成了七个不 同种类 ,他们 分别是 :人才 、任务 、团队 、技术 、工艺、时间和工具 。他还把 同步 工程的技术进行归类 ,并从 创造性及 合作程 度的不 同将其分为六个不 同层次 。这些层次包 括基于 网络的技术 、基 于文件 的技术 ,实时可变
dfm报告

dfm报告DFM(Design for Manufacturing)报告,即制造设计报告,是一份制造工程师对产品设计提供反馈、建议和优化方案的报告。
DFM报告的主要目的是提高产品制造效率、延长产品寿命、降低制造成本、提升产品的质量和可靠性。
本文将详细介绍DFM报告的意义、内容、流程和实施步骤。
一、DFM报告的意义1.提高产品的制造效率:通过DFM报告,制造工程师可以对产品设计进行评估,确定是否存在制造难度大、制造成本高、制造周期长等问题,从而及早发现和解决这些问题,提高产品的制造效率。
2.延长产品的寿命:DFM报告还可以评估产品的设计可靠性和寿命,及早发现设计缺陷和制造难点,减少产品故障率,延长产品的寿命,提高产品使用价值和客户满意度。
3.降低制造成本:通过DFM报告,制造工程师可以提出优化方案和改进建议,减少废品率、提高制造效率和生产线利用率,降低产品的制造成本。
4.提升产品的质量和可靠性:DFM报告可以从制造工程师的角度评估产品的设计合理性和可制造性,提出合理的改进建议和制造流程优化方案,从而提升产品的质量和可靠性。
二、DFM报告的内容1.产品的重点制造特性:制造工程师应该首先确定产品的重点制造特性,包括产品的材料、制造工艺、尺寸、形状、结构、工艺容限、装配要求等。
2.制造工艺评估:制造工程师需要评估产品的制造工艺,包括生产线的流程、工具和设备的选择、模具及夹具的制作、工艺标准的制定等。
3.制造成本估算:制造工程师需要对产品的制造成本进行估算,包括人力、材料、设备、能源等各方面的成本,并提供降低成本的建议和方案。
4.产品的可靠性评估:制造工程师需要对产品的可靠性进行评估,包括产品的寿命、可靠性要求、环境要求等,提供改进建议和方案。
5.产品的优化和改进:DFM报告还应该提供产品优化和改进的建议和方案,包括加工方式、加工方法、材料选择、工艺流程等。
6.可制造性评估:DFM报告还需要对产品的可制造性进行评估,确定产品的生产性、维修性、可靠性等指标,并提出措施和建议。
塑料dfm报告模板

塑料DFM报告模板摘要本文档介绍了塑料制品设计的DFM(Design for Manufacturing)报告模板,包括DFM报告的必要性、报告格式和内容要素等,旨在帮助塑料制品设计者更好地进行DFM设计。
DFM报告的必要性DFM设计是指在产品设计之初,考虑到产品的制造过程,即设计师将产品的制造过程视为设计的一部分。
DFM设计可以提高产品的制造效率、降低制造成本、缩短周期和提高产品质量等方面的优势。
而DFM报告是对产品进行DFM设计的结果进行记录和总结,能够提供给制造工程师和相关制造部门,帮助他们了解产品设计的考虑,以便更好地进行制造过程的安排和管理。
因此,DFM报告对于一个产品的制造过程是非常重要的,可以提高产品的制造效率、降低制造成本、缩短周期和提高产品质量等方面的优势。
报告格式DFM报告的格式通常分为四大部分,分别是背景信息、主要内容、阶段总结和结论。
背景信息这部分主要是对设计任务的背景、目标、约束条件等的描述,包括项目名称、设计任务说明、产品描述、所用软件工具、设计人员、项目时间表等等。
主要内容主要内容部分是DFM报告的核心部分,包括对设计的材料选择、CAD设计、几何形状、加工特征、尺寸公差、表面质量、成型方式、注塑模具设计、成型工艺参数等进行了分析和评估,力求将DFM设计中的问题都找到并列出来。
阶段总结这一部分主要介绍了在分析和评估过程中发现的问题,同时还总结了设计过程中的经验和教训。
结论最后一部分是结论,对DFM报告进行总结与归纳,提出建议,以便更好地进行产品制造。
建议可分为技术方面和管理方面。
内容要素DFM报告的内容大体上包括下面几个方面的要素:•材料属性:包括熔融温度、塑料成型特性等•加工工艺:包括成型方式、成型周期等•尺寸公差:涉及到规格、形状和位置公差等•表面质量:包括表面平整度、注塑机的压力等•模具设计:需考虑到模具的设计与制造时所遇到的问题•生产计划:包括生产过程中的计划安排等结论通过本文对塑料DFM报告模板进行总结归纳,我们可以发现,DFM报告对产品的制造过程是相当重要的,可以帮助制造工程师和相关制造部门更好地进行制造过程的安排和管理。
dfm加工与制造工程师手册
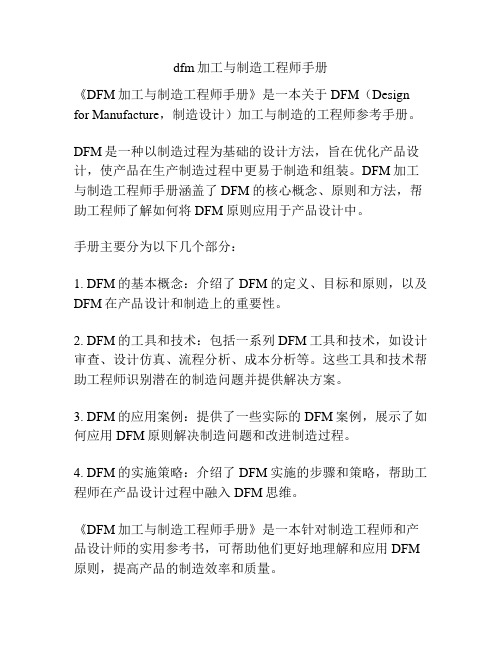
dfm加工与制造工程师手册
《DFM加工与制造工程师手册》是一本关于DFM(Design for Manufacture,制造设计)加工与制造的工程师参考手册。
DFM是一种以制造过程为基础的设计方法,旨在优化产品设计,使产品在生产制造过程中更易于制造和组装。
DFM加工与制造工程师手册涵盖了DFM的核心概念、原则和方法,帮助工程师了解如何将DFM原则应用于产品设计中。
手册主要分为以下几个部分:
1. DFM的基本概念:介绍了DFM的定义、目标和原则,以及DFM在产品设计和制造上的重要性。
2. DFM的工具和技术:包括一系列DFM工具和技术,如设计审查、设计仿真、流程分析、成本分析等。
这些工具和技术帮助工程师识别潜在的制造问题并提供解决方案。
3. DFM的应用案例:提供了一些实际的DFM案例,展示了如何应用DFM原则解决制造问题和改进制造过程。
4. DFM的实施策略:介绍了DFM实施的步骤和策略,帮助工程师在产品设计过程中融入DFM思维。
《DFM加工与制造工程师手册》是一本针对制造工程师和产品设计师的实用参考书,可帮助他们更好地理解和应用DFM 原则,提高产品的制造效率和质量。
dfm加工与制造工程师手册
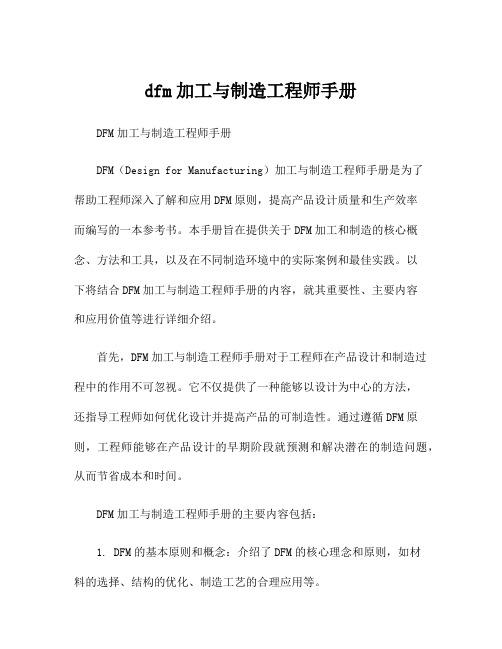
dfm加工与制造工程师手册DFM加工与制造工程师手册DFM(Design for Manufacturing)加工与制造工程师手册是为了帮助工程师深入了解和应用DFM原则,提高产品设计质量和生产效率而编写的一本参考书。
本手册旨在提供关于DFM加工和制造的核心概念、方法和工具,以及在不同制造环境中的实际案例和最佳实践。
以下将结合DFM加工与制造工程师手册的内容,就其重要性、主要内容和应用价值等进行详细介绍。
首先,DFM加工与制造工程师手册对于工程师在产品设计和制造过程中的作用不可忽视。
它不仅提供了一种能够以设计为中心的方法,还指导工程师如何优化设计并提高产品的可制造性。
通过遵循DFM原则,工程师能够在产品设计的早期阶段就预测和解决潜在的制造问题,从而节省成本和时间。
DFM加工与制造工程师手册的主要内容包括:1. DFM的基本原则和概念:介绍了DFM的核心理念和原则,如材料的选择、结构的优化、制造工艺的合理应用等。
2. DFM的应用方法和工具:介绍了一系列可以帮助工程师实施DFM的方法和工具,如故障模式与影响分析(FMEA)、制造可行性分析(MFA)、实际生产情况模拟等。
3.实际案例和最佳实践:分析了一些真实的制造案例,讲述了工程师如何应用DFM原则解决问题,并总结了一些经验和教训。
4. DFM加工与制造的未来发展趋势:展望了DFM加工与制造领域的发展方向,包括自动化和数字化制造等。
DFM加工与制造工程师手册的应用价值主要体现在以下几个方面:1.提高产品质量:通过合理的设计和制造流程,可以预防和减少产品的制造缺陷和质量问题,提高产品的可靠性和稳定性。
2.缩短产品开发周期:通过在产品设计的早期阶段解决潜在的制造问题,可以减少后期的改动和调整,从而缩短产品的开发周期。
3.降低生产成本:通过优化设计和制造流程,可以减少生产过程中的浪费和成本,提高生产效率和利润率。
4.提高制造竞争力:通过实施DFM原则,可以增强企业在市场上的竞争力,提高产品的市场份额和盈利能力。
DFM报告清单
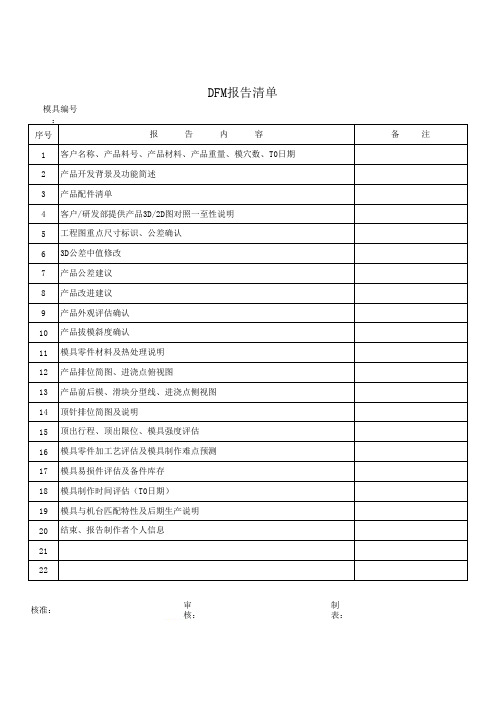
序号1
2
3
4
5
6
7
8
9
10
11
12
13
14
15
16
17
18
19
20
21
22核准:审核:制表:顶针排位简图及说明DFM报告清单
产品前后模、滑块分型线、进浇点侧视图产品公差建议顶出行程、顶出限位、模具强度评估模具零件加工艺评估及模具制作难点预测产品排位简图、进浇点俯视图模具易损件评估及备件库存产品配件清单模具与机台匹配特性及后期生产说明结束、报告制作者个人信息3D公差中值修改工程图重点尺寸标识、公差确认产品外观评估确认 模具编号 :客户名称、产品料号、产品材料、产品重量、模穴数、T0日期产品开发背景及功能简述客户/研发部提供产品3D/2D图对照一至性说明模具零件材料及热处理说明产品拔模斜度确认模具制作时间评估(T0日期)备 注
报 告 内 容产品改进建议。
dfm评审流程
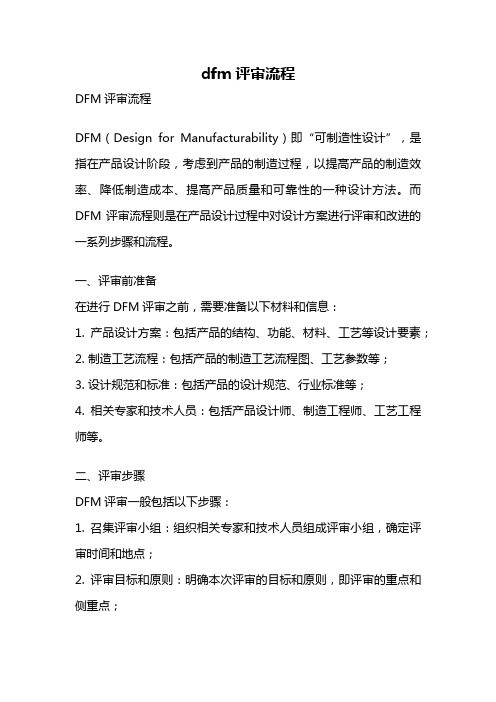
dfm评审流程DFM评审流程DFM(Design for Manufacturability)即“可制造性设计”,是指在产品设计阶段,考虑到产品的制造过程,以提高产品的制造效率、降低制造成本、提高产品质量和可靠性的一种设计方法。
而DFM评审流程则是在产品设计过程中对设计方案进行评审和改进的一系列步骤和流程。
一、评审前准备在进行DFM评审之前,需要准备以下材料和信息:1. 产品设计方案:包括产品的结构、功能、材料、工艺等设计要素;2. 制造工艺流程:包括产品的制造工艺流程图、工艺参数等;3. 设计规范和标准:包括产品的设计规范、行业标准等;4. 相关专家和技术人员:包括产品设计师、制造工程师、工艺工程师等。
二、评审步骤DFM评审一般包括以下步骤:1. 召集评审小组:组织相关专家和技术人员组成评审小组,确定评审时间和地点;2. 评审目标和原则:明确本次评审的目标和原则,即评审的重点和侧重点;3. 进行评审:评审小组根据产品设计方案、制造工艺流程、设计规范和标准等材料,对产品的可制造性进行评审,提出评审意见和改进建议;4. 记录评审结果:评审小组将评审意见和改进建议记录下来,包括问题描述、改进方案等;5. 提出改进方案:评审小组根据评审结果,提出具体的改进方案和措施,包括设计方案的修改、工艺流程的调整等;6. 汇总评审报告:评审小组将评审结果和改进方案汇总成评审报告,包括问题清单、改进计划等;7. 分发评审报告:将评审报告分发给相关的设计师、工程师等,让他们了解评审结果和改进方案;8. 实施改进措施:相关人员根据评审报告中的改进方案,进行相应的修改和调整;9. 进行再评审:在修改和调整完成后,再次进行评审,以确认改进措施的有效性;10. 完成评审报告:根据最终的评审结果,完成最终的评审报告,包括改进措施的实施情况和效果等。
三、评审要点和注意事项在进行DFM评审时,需要注意以下要点和事项:1. 重点关注制造工艺:评审过程中,重点关注产品的制造工艺,包括工艺流程、工艺参数、工艺设备等,以确保产品的制造可行性和效率;2. 关注设计规范和标准:评审过程中,要遵循相关的设计规范和标准,以确保产品的设计符合行业要求和标准;3. 充分沟通和合作:评审过程中,评审小组成员之间需要充分沟通和合作,共同解决问题,提出改进建议;4. 综合考虑多个因素:评审过程中,需要综合考虑多个因素,如制造成本、生产效率、产品质量等,以找到最合理的设计方案;5. 审慎处理评审意见:评审过程中,评审小组提出的评审意见需要审慎处理,根据实际情况进行判断和决策;6. 及时跟进和反馈:评审过程中,需要及时跟进改进措施的实施情况,并及时反馈评审结果和效果。
DFM工程师岗位职责
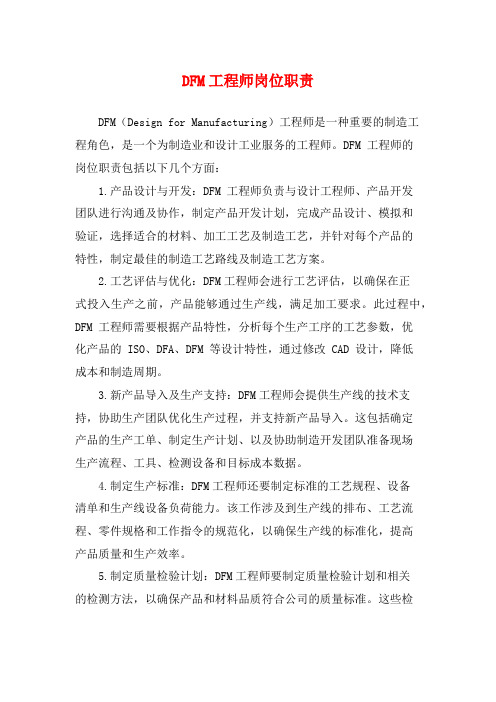
DFM工程师岗位职责DFM(Design for Manufacturing)工程师是一种重要的制造工程角色,是一个为制造业和设计工业服务的工程师。
DFM 工程师的岗位职责包括以下几个方面:1.产品设计与开发:DFM 工程师负责与设计工程师、产品开发团队进行沟通及协作,制定产品开发计划,完成产品设计、模拟和验证,选择适合的材料、加工工艺及制造工艺,并针对每个产品的特性,制定最佳的制造工艺路线及制造工艺方案。
2.工艺评估与优化:DFM工程师会进行工艺评估,以确保在正式投入生产之前,产品能够通过生产线,满足加工要求。
此过程中,DFM 工程师需要根据产品特性,分析每个生产工序的工艺参数,优化产品的 ISO、DFA、DFM 等设计特性,通过修改 CAD 设计,降低成本和制造周期。
3.新产品导入及生产支持:DFM工程师会提供生产线的技术支持,协助生产团队优化生产过程,并支持新产品导入。
这包括确定产品的生产工单、制定生产计划、以及协助制造开发团队准备现场生产流程、工具、检测设备和目标成本数据。
4.制定生产标准:DFM工程师还要制定标准的工艺规程、设备清单和生产线设备负荷能力。
该工作涉及到生产线的排布、工艺流程、零件规格和工作指令的规范化,以确保生产线的标准化,提高产品质量和生产效率。
5.制定质量检验计划:DFM工程师要制定质量检验计划和相关的检测方法,以确保产品和材料品质符合公司的质量标准。
这些检验计划设计、开发和实施,还需监控现场生产的质量情况,及时调整和改进。
综上所述,DFM工程师的主要职责是协调产品设计团队和制造技术团队,确保产品设计能够在最短的时间内、最小的成本和资源投入下,通过生产线,生产出高质量的产品。
同时,DFM工程师需要了解市场需求和技术趋势,与客户和供应商进行沟通和协作,以提高公司的市场竞争力。
- 1、下载文档前请自行甄别文档内容的完整性,平台不提供额外的编辑、内容补充、找答案等附加服务。
- 2、"仅部分预览"的文档,不可在线预览部分如存在完整性等问题,可反馈申请退款(可完整预览的文档不适用该条件!)。
- 3、如文档侵犯您的权益,请联系客服反馈,我们会尽快为您处理(人工客服工作时间:9:00-18:30)。
项目号:OK NG 1
产品材质可制造性评估2
产品未注公差/特殊公差评估3
产品标注基准可制造性评估4
产品标注尺寸/特殊特性尺寸可制造性评估5盲孔/通孔/螺牙孔/异形孔尺寸公差与可制造性评估
6客户特殊指定技术标准可制造性评估
7产品组装辅料零件可制造性评估
8产品表面处理标准与性耐/功能可测试性评估
9产品外观要求以及指定面粗糙度可制造性评估10产品刻字位置以及字体要求评估
11参照3D确认2D 图面以及版本一致性
123D零件重量/面积计算
13零件压铸生产可行性评估
143D零件图与2D 图面以及版本一致性
15零件壁厚均匀性评估
16零件拔模斜度评估
17零件结构CNC机加工可行性评估
18零件深腔体/薄弱肋片/深孔位/异形结构生产可行性评估19产品工艺流程实际生产可行性评估
20各工序使用夹具/设备工装/检具需求评估
21各工序生产风险工序评估
22各工序段问题汇总并形成DFM
23客户回复DFM信息反馈给各责任部门
1模具压铸机台评估
2模具分模示意图以及浇口评估
3模具顶针排位图评估
4模具冷却系统评估
5产品特殊特性尺寸输入评审
6产品机加工余量模具尺寸评估
7模具镶针、镶件、滑块制作可行性评估
8
铸件图/模具设计图评审权责部门序号
检验项目D FM可行性判定
3D零件图2D图面苏州市永创金属科技有限公司
产品工程DFM检验清单(check list)
客户:料号:类型评审会议产品工程部模具设计模具设计部
计
检验人员:审核:
D。