拉丝工序培训
电线电缆-拉丝镀锡培训

拉絲鍍錫資料一﹑拉絲部份:1.拉絲機的工作原理1.1.利用銅的金屬塑性原理,配備相應的設備,在串列式模具上實現拉制。
1.2.利用銅的金屬再結晶原理,配備相應的退火設備,將拉制后已經硬化的銅線再行軟化,回復銅線原有的塑性。
2.拉絲機相應的組成部件﹕2.1.放線架﹕采用籠式放線,固定放置,以利于換軸時接線,實現連續生產。
2.2 拉線系統2.2.1 軋線機﹕利用相向回轉的凸輪組,將銅線軋細,以便穿模。
2.2.2 拉線箱﹕2.2.3 拉線模具﹕拉線模具為圓柱狀,側放于模具座中,模具由四個區域組成﹕2.2.3.1 入口區﹕導入銅線,並由此引入潤滑液。
2.2.3.2 工作區﹕銅線受拉力變形的區域。
2.2.3.3 定徑區﹕保持銅線尺寸的區域。
2.2.3.4 出口區﹕銅線應力釋放區域,即線徑回彈區域。
2.2.3.4 拉線單位﹕拉線箱內的模具按照走線方向及過線位置,將拉線模具按孔徑由大到小排列串列模具,每一個模具座內的模具與後面相鄰的牽引輪(塔輪)構成一個拉線單位,實現拉制過程。
2.3.潤滑系統﹕2.3.1.拉線潤滑液的作用﹕潤滑作用﹕減少銅線在模具工作區與模具接觸面的摩擦。
冷卻作用﹕帶走摩擦產生的熱量,降低模具與銅線的溫度。
清洗作用﹕沖洗掉銅線變形過程中掉下的銅屑。
3.退火系統3.1.退火箱3.1.1.上下電極輪﹕通過一定的電流,加熱繞過的銅線,進行退火.3.1.2.進、出水管﹕提供冷卻水,對熱銅線進行充分冷卻。
蒸汽噴出管﹕引入蒸汽,退火時對熱銅線進行保護,避免氧化。
3.1.3.空氣吹乾器﹕吹乾銅線上的水汽,避免水斑痕及氧化。
3.2.冷卻系統﹕3.2.1.冷卻液的作用﹕對已經退火的銅線進行充分冷卻。
3.2.2.冷卻液循環系統﹕拉線退火液儲存箱→進液管→噴嘴→退火箱內儲液→回流管→拉線退火液儲存箱。
4.儲線架﹕調節拉線與收線的平衡,即當收線速度小于拉線速度時,在儲線架上暫時性的儲備一定的銅線;即當收線速度大于于拉線速度時, 在儲線架上暫時性的補償一定的銅線,以避免因供應不及收線而導致的斷線;銅線的張力由加載的砝碼以及儲線輪上纏繞的圈數決定。
拉丝绞线 简单培训
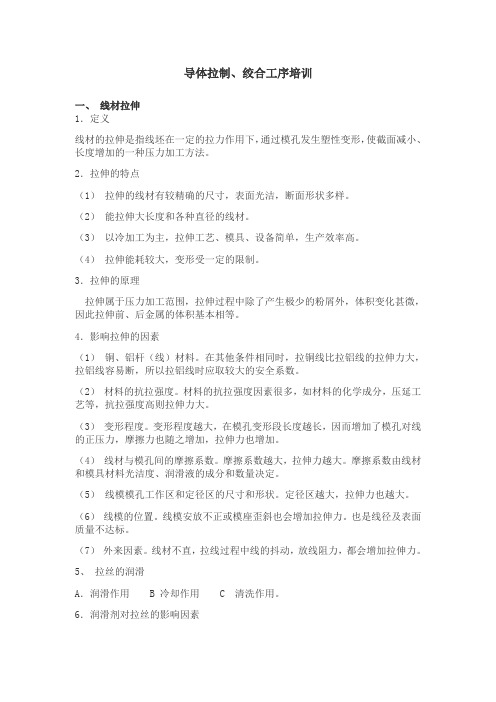
导体拉制、绞合工序培训一、线材拉伸1.定义线材的拉伸是指线坯在一定的拉力作用下,通过模孔发生塑性变形,使截面减小、长度增加的一种压力加工方法。
2.拉伸的特点(1)拉伸的线材有较精确的尺寸,表面光洁,断面形状多样。
(2)能拉伸大长度和各种直径的线材。
(3)以冷加工为主,拉伸工艺、模具、设备简单,生产效率高。
(4)拉伸能耗较大,变形受一定的限制。
3.拉伸的原理拉伸属于压力加工范围,拉伸过程中除了产生极少的粉屑外,体积变化甚微,因此拉伸前、后金属的体积基本相等。
4.影响拉伸的因素(1)铜、铝杆(线)材料。
在其他条件相同时,拉铜线比拉铝线的拉伸力大,拉铝线容易断,所以拉铝线时应取较大的安全系数。
(2)材料的抗拉强度。
材料的抗拉强度因素很多,如材料的化学成分,压延工艺等,抗拉强度高则拉伸力大。
(3)变形程度。
变形程度越大,在模孔变形段长度越长,因而增加了模孔对线的正压力,摩擦力也随之增加,拉伸力也增加。
(4)线材与模孔间的摩擦系数。
摩擦系数越大,拉伸力越大。
摩擦系数由线材和模具材料光洁度、润滑液的成分和数量决定。
(5)线模模孔工作区和定径区的尺寸和形状。
定径区越大,拉伸力也越大。
(6)线模的位置。
线模安放不正或模座歪斜也会增加拉伸力。
也是线径及表面质量不达标。
(7)外来因素。
线材不直,拉线过程中线的抖动,放线阻力,都会增加拉伸力。
5、拉丝的润滑A.润滑作用 B 冷却作用 C 清洗作用。
6.润滑剂对拉丝的影响因素(1)浓度。
润滑剂的浓度大,提高了它的润滑作用,金属线材与模孔壁的摩擦系数小,相应的摩擦力也减小,拉伸力随之下降。
但是,浓度太大,润滑剂的粘度也随之上升,它的冲洗作用也减小,模孔的金属屑不易带走,造成线材表面质量差。
浓度太大,金属屑不会沉淀,悬浮在润滑剂中,反而影响润滑效果。
(2)温度。
润滑液的温度过高,失去了它的冷却作用,使金属线材及模具的温度升高,线材氧化变色、模具寿命减低,也影响油脂润滑膜的强度,润滑效果下降。
拉丝工艺理论知识培训

• 2.1 按 材 质 分 : 1. 硬 质 合 金 模 ; 2. 钻 石 模 ; 3. 聚晶模〔人造金刚石〕;4.钢模
• 2.2按孔型分: 圆模和型模
• 2.3按在拉线过程的作用分:成品模和过渡模
• 我们模模孔
模孔分四个区域:入口润滑区、 工作区〔压缩区〕、 定径区、出口区。
三、拉丝油
1、 拉丝液:
拉丝液在拉丝过程中起着润滑、冷却、清洗作用。拉丝液要控 制的主要性能参数有浓度,温度,PH值。
1.1、浓度:浓度太高,拉丝液清洗性能减弱,油脂消耗大,浓度太 低,润滑性能减弱,影响模具使用寿命和铜线外表质量,甚至造 成断线。现我司拉丝液浓度控制范围为大拉15-18%,中拉7-8%, 中小拉4-6%,小拉3-5%,微拉2-3%。
β
β
β 3
出口区 定径区
工作区 入口润滑区
各局部功能.
1). 入口区和润滑区
入口区一般带有圆弧,便于拉伸金 属进入工作区,而不致被模孔边 缘擦伤.润滑区是导入润滑剂, 使拉伸材料得到润滑.在拉线模 扩孔时,靠这局部来加大工作区 2). 工作区
工作区是金属拉伸塑性变形区,即 金属材料通过这个区,直径由大 变小.这个区的选择主要是高度 和锥角.
一、拉丝工艺工序流程图
8.000mm铜杆 2.600mm加工铜
检验①
合格
大拉机
退火线 过程线
检验②
不合格〔评审〕 规格线〔不退火〕
退货
让步接收
检验③
A+B类
C类
返拉
检验①
合格
不合格
评审 让步接收
退货
中拉机
规格线〔不退火〕
退火线 过程线
检验③
小拉机
拉丝工艺培训教材(共 50张PPT)

拉丝工艺
拉丝概述
原理: 指线坯通过模孔在一定拉力作用下,使线材发生塑性变形,使截面减小、 长度增加的一种压力加工方法,是一种冷变形。
特点
①拉伸的线材有较精确的尺寸,表面光洁,断面形状可以多样,可以拉圆线、扁 线、Z型线、梯形线等; ②能拉伸大长度和各种直径的线材;
③以冷压力加工为主,拉伸工艺、工具、设备简单,生产效率高,现在的设备 (仅对于铜拉)都具有了连拉连退功能,节约大量人力、物力。
1.4 拉丝油 1.4.1 拉丝油作用 ①润滑作用:避免模具与金属直接接触及粘结,降低摩擦系数减少摩 擦,使得金属沿 受力方向均匀变形,并增加金属的变形程度,延长模具的寿命. ②冷却作用:使用适当的润滑液,可以使由于金属变形产生的热量迅速传导,降低线 材与模孔的温度,防止线材温度过高发生氧化变色现象. ③清洗作用:金属在拉伸过程中,不断产生细微的金属粉尘,润滑液不断冲洗模孔,清 除金属粉末的作用. 1.4.2 拉丝油对拉丝的影响 ①浓度;润滑剂浓度增大,金属线材与模壁的摩擦系数减小,相应的摩擦力也减小,伸 力也就减小,反之,拉伸力增加.浓度大,润滑剂的粘度上升,冲洗模孔的作用减小, 拉伸中产生的屑不易被润滑剂冲洗带走,造成线材表面起槽等质量问题;浓度过 大,金属屑将悬浮在润滑剂中,不易沉淀,影响润滑效果以及拉伸后线材表面质 量.
拉丝机名称 进线直径 mm 大 中 小 细 微 8 3 1.6 0.6 0.12 出线直径 mm 4-1.7 1.0-3.0 0.12-0.4 0.05-0.15 0.02-0.05 模具数量 13 9,13,14,10 22,24 4 20 塔轮直径 mm 400 280,250 240 150 70
(3*3-2.54*2.54)/(3*3)=28%
拉丝培训

(铜线)拉丝工艺技术培训一.拉丝工艺基础知识1.线材的拉伸原理是指线坯通过模孔在一定拉力作用下,发生塑性变形,使截面减少、长度增加的一种方法,拉伸过程中产生极少粉末,可忽略不计,因此可认为拉伸前后金属的体积不变。
表示拉伸过程金属变形量的基本参数:1.1 延伸系数(µ):金属拉伸后与拉伸前线材长度的比值。
1.2 减面率(δ):线材拉伸前后断面面积之差与拉伸前断面面积的比值。
延伸系数与减面率的关系:δ=1-1/µ2.滑动式连续多次拉伸特点:铜线拉伸方法属于滑动式连续多次拉伸,滑动式连续多次拉伸有两个特点:2.1 除最后一道外,其余各道鼓轮与线材之间存在滑动,由于滑动式连续拉丝机是鼓轮上的线材与鼓轮之间的滑动摩擦力来牵引线材运动,所以增加了功率消耗,还会造成鼓轮表面磨损,形成沟槽,使线材在鼓轮上的轴向移动发生困难,造成压线,甚至断线,同时影响线材表面质量,但由于滑动,能自动调节张力,不致中间断线或留有余线。
要想使线材与鼓轮之间产生滑动,必须使线材拉伸后的长度与拉伸前的长度之比大于后面和前面的鼓轮线速度之比。
2.2 除第一道外,其余各道次都存在反拉力。
绕线圈数的多少对下一道的反拉力影响很大,绕线圈数越少,下一道的反拉力越大,绕线圈数越多,下一道的反拉力越小,当绕线较多时,滑动对张力变化的反应迟钝,同时线材在鼓轮上轴向移动困难,容易压线,所以拉丝时要合理确定鼓轮上的绕线圈数。
3.影响拉伸力的因素3.1 金属材材料的种类:拉伸不同的金属所需的拉伸力不一样,如拉铜线比拉铝线拉伸力大,拉铝线时容易断。
3.2 变形程度:变形程度越大,拉伸力越大。
3.3 线材与模孔之间的摩擦系数:摩擦系数越大,拉伸力越大。
3.4 模孔工作区和定径区的尺寸和形状:工作区角度太大或太小,都会增加拉伸力,定径区越长,拉伸力越大。
3.5 模具位置:模具摆放不正或模座不正都会增加拉伸力,而且影响线材表面质量。
3.6 反拉力:反拉力增大,则拉伸力增大。
拉丝厂操作规程培训计划

拉丝厂操作规程培训计划一、培训目的及意义拉丝是一种常见的加工工艺,用于加工金属材料,使其表面更加光滑、均匀。
拉丝工艺在金属制品生产中有着广泛的应用,因此对拉丝工艺的操作规程进行培训,可以提高拉丝产品的质量和生产效率,确保生产过程安全可靠。
二、培训对象本培训计划面向拉丝工艺操作人员、维护人员和管理人员。
三、培训内容1. 拉丝工艺的基本原理2. 拉丝机的结构和工作原理3. 拉丝模具的选择和维护4. 拉丝工艺中的安全生产知识5. 拉丝工艺中的常见问题及处理方法6. 拉丝产品的质量检验方法和标准四、培训方式1. 理论讲解2. 实地操作3. 观摩学习五、培训时间安排本次培训计划共分为三个阶段,每个阶段为5天。
第一阶段:拉丝工艺的基本原理和设备的介绍时间:2022年10月10日-14日第二阶段:拉丝机的操作和模具的使用时间:2022年10月17日-21日第三阶段:拉丝工艺中的安全生产知识和质量检验方法时间:2022年10月24日-28日六、培训评估每个阶段结束后,将进行培训效果评估,并根据评估结果对培训内容进行调整和完善。
七、培训考核培训结束后将进行考核,通过考核的学员将获得培训合格证书。
八、培训师资本次培训将邀请具有丰富实践经验和理论知识的拉丝工艺专家担任讲师,确保培训内容丰富、权威。
九、培训设施本次培训将在公司内部专门设置拉丝培训中心,配备先进的拉丝设备和模具,为学员提供良好的实训环境。
十、培训费用本次培训的费用由公司承担,学员无需承担任何费用。
十一、培训后续培训结束后,公司将对拉丝工艺的操作规程进行修订,制定更加完善的工艺流程和安全生产规范,确保拉丝产品的质量和生产效率。
十二、培训效果分析培训结束后,将对学员的实际操作能力进行考核,对培训效果进行分析和总结,为今后的培训提供参考和改进的方向。
以上为拉丝厂操作规程培训计划,希望本次培训能够提高学员的拉丝工艺操作能力,确保产品质量和生产效率,促进公司的可持续发展。
拉丝工艺理论知识 PPT

此种断线的断面呈孔洞状,其放大图片其孔洞表面非常平滑,无凸起 或开裂的现象。
气泡断线的形成原因是铸成时氢气控制不当,冷却不良产生缩孔
所致,若孔洞较小则在后续的热加工过程中也许会闭合,若孔洞较 大则无法闭合,于是造成气泡断线。
• B、 夹杂物断线(主要是铜才原因所致)
夹杂物断线是断线中较为常见的一种,从外形看可以分为两类,一类 是夹杂物存在的断线,另一类是夹杂物丢失的断线。
2.1 按 材 质 分 : 1. 硬 质 合 金 模 ; 2. 钻 石 模 ; 3. 聚晶模(人造金刚石);4.钢模 • 2.2按孔型分: 圆模和型模 • 2.3按在拉线过程的作用分:成品模和过渡模 我们公司现在使用的模具只有钻石模和聚晶模两种.
3、拉丝模模孔
模孔分四个区域:入口润滑区、 工作区(压缩区)、 定径区、出口区。
三、拉丝过程中一些常见问题分析
• 拉丝过程中铜线断线原因分析与判断 • 一、 目的
了解和熟悉《铜线断线原因与分析》有助于拉丝车 间在生产过程中对铜线断线的原因作出合理客观的分 析和判断。
• 二、 断线种类及其论述 • A、 中央爆裂
中央爆裂:断线处从铜线的中心部位断裂,一端为 尖锥,一端为尖锐的孔洞。中央爆裂的孔洞最容易被 误认为气泡断线,将中央爆裂的孔洞洞壁放大可以发 现,材料本身因受外力的影响而呈现凹凸状的撕裂现 象。
• 1.1、浓度:浓度太高,拉丝液清洗性能减弱,油脂消耗大,浓度 太低,润滑性能减弱,影响模具使用寿命和铜线表面质量,甚至 造成断线。现我司拉丝液浓度控制范围为大拉15-18%,中拉7-8%, 中小拉4-6%,小拉3-5%,微拉2-3%。
• 1.2、温度:温度太低,拉丝液粘度较大,塔轮容易绞线,清洗性 能变弱,也不能很好地发挥润滑性能,温度太高,拉丝液润滑性 能变差,冷却效果不佳,铜线出线温度高,影响模具的使用寿命 和产品质量,现我司拉丝液温度控制范围30-45℃。
铜线拉丝车间的培训计划

铜线拉丝车间的培训计划一、培训背景铜线拉丝车间是一个重要的生产车间,主要负责生产铜线材和铜制品。
由于铜材料本身的特性,以及拉丝工艺的复杂性,对操作工人的技能要求较高。
因此,为了提高生产效率,保证产品质量,提升员工技能水平,铜线拉丝车间需要定期进行培训。
本培训计划旨在为车间员工提供全面的技能培训,帮助他们学习和掌握铜线拉丝的相关知识和技能。
二、培训目标1.了解铜线拉丝车间的生产流程和工艺要求。
2.掌握铜线拉丝设备的操作方法和维护保养技巧。
3.学习拉丝工艺的基本原理和操作规程。
4.提高员工的安全意识,确保生产过程中的安全生产。
5.提升员工的团队协作能力和问题解决能力。
三、培训内容1.铜线拉丝车间生产流程和工艺要求。
2.铜线拉丝设备的操作方法和维护保养技巧。
3.拉丝工艺的基本原理和操作规程。
4.安全生产知识和操作规范。
5.团队协作和问题解决能力培训。
四、培训方式1.理论培训:通过讲解、演示和视频学习等形式进行。
2.实践培训:通过实际操作设备,模拟生产场景进行培训。
3.案例分析:结合实际案例,讨论问题并提出解决方案。
4.学习小组:设立学习小组进行讨论和交流,提升团队协作能力。
五、培训时间和地点1.培训时间:预计为期1个月,每周安排2次培训课程。
2.培训地点:铜线拉丝车间内设专门的培训区域。
六、培训计划第一周:1.了解铜线拉丝车间的生产流程和工艺要求。
2.学习铜线拉丝设备的操作方法和维护保养技巧。
第二周:1.学习拉丝工艺的基本原理和操作规程。
2.进行实际操作设备,模拟生产场景进行培训。
第三周:1.学习安全生产知识和操作规范。
2.共同分析讨论实际案例,提出解决方案。
第四周:1.学习团队协作和问题解决能力培训。
2.组织学习小组进行讨论和交流,提升团队协作能力。
七、培训考核1.理论考核:通过闭卷考试进行。
2.实践考核:通过实际操作设备,模拟生产场景进行考核。
3.综合考核:考核内容包括理论知识、操作技能和安全意识等。
拉丝工安全培训

# 拉丝工安全培训1. 简介拉丝工是一项常见的金属加工工艺,用于将金属材料拉成细长的丝状。
然而,由于潜在的安全风险,进行拉丝工作时需要掌握一系列安全知识和技能。
本文档旨在为拉丝工提供一份全面的安全培训指南,以确保他们在工作中的安全。
2. 安全意识在进行拉丝工之前,拉丝工必须具备充分的安全意识。
以下是一些可帮助拉丝工提高安全意识的要点:•理解工作环境中的潜在危险和风险。
•知晓相应的安全规定和程序。
•识别并采取适当的措施来降低安全风险。
3. 个人防护装备为了保护自身免受拉丝工作中的伤害,拉丝工必须正确佩戴个人防护装备。
以下是一些必备的个人防护装备:•安全帽:用于保护头部免受物体的撞击。
•护目镜:用于防止眼睛受到飞溅物和金属碎片的伤害。
•隔热手套:用于防止手部热风和烫伤。
•耳塞或耳罩:用于减少噪音对听力造成的损害。
•工作服和防护鞋:用于防止身体和脚部受到损伤。
4. 机械设备安全在拉丝工作中,机械设备的安全性和正常运行至关重要。
拉丝工必须了解和遵守以下机械设备安全指南:•定期检查和维护机械设备,确保其在安全和良好的工作状态。
•确保机械设备的紧固螺母和螺栓处于正确位置,以避免意外松动。
•在启动机械设备之前,确保周围没有人员并保持安全距离。
•使用正确的速度和压力来拉丝,以避免意外破裂或绷紧。
5. 紧急事故应急措施尽管进行了足够的安全预防,但任何时候都有可能发生紧急情况。
拉丝工需要了解并掌握以下应急措施:•火灾事故:学习使用灭火器并了解适当的灭火方法。
•人员伤害:立即寻求医疗协助并报告任何伤害事件。
•机械故障:立即关闭机械设备并报告维修部门。
6. 安全培训和检查为了确保拉丝工的持续安全,定期的安全培训和检查非常重要。
以下是一些相关措施:•定期举办拉丝工安全培训课程,以加强他们的安全意识和知识。
•组织安全检查,定期检查个人防护装备和机械设备的完整性和功能。
•积极参与和反馈,拉丝工可以提出改进建议和意见,以促进工作环境的安全和健康。
拉丝工序培训
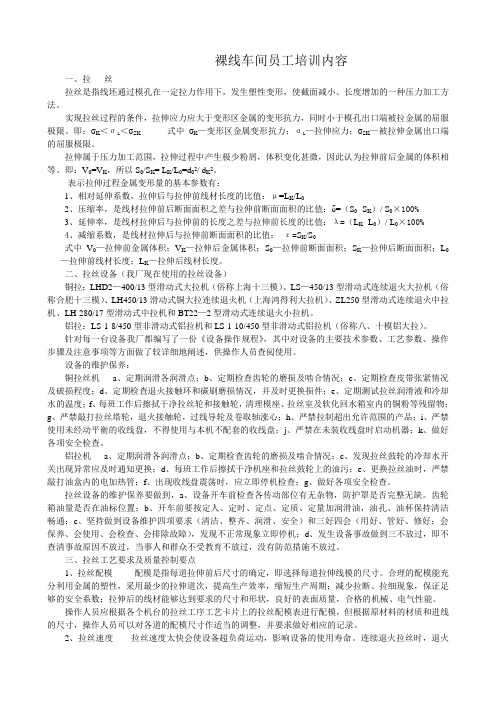
裸线车间员工培训内容一、拉丝拉丝是指线坯通过模孔在一定拉力作用下,发生塑性变形,使截面减小、长度增加的一种压力加工方法。
实现拉丝过程的条件,拉伸应力应大于变形区金属的变形抗力,同时小于模孔出口端被拉金属的屈服极限。
即:σK<σL<σSK式中σK—变形区金属变形抗力;σL—拉伸应力;σSK—被拉伸金属出口端的屈服极限。
拉伸属于压力加工范围,拉伸过程中产生极少粉屑,体积变化甚微,因此认为拉伸前后金属的体积相等。
即:V0=V K,所以S0/S K= L K/L0=d02/ d K2。
表示拉伸过程金属变形量的基本参数有:1、相对延伸系数,拉伸后与拉伸前线材长度的比值:μ=L K/L02、压缩率,是线材拉伸前后断面面积之差与拉伸前断面面积的比值:δ=(S0- S K)/ S0×100%3、延伸率,是线材拉伸后与拉伸前的长度之差与拉伸前长度的比值:λ=(L K- L0)/ L0×100%4、减缩系数,是线材拉伸后与拉伸前断面面积的比值:ε=S K/S0式中V0—拉伸前金属体积;V K—拉伸后金属体积;S0—拉伸前断面面积;S K—拉伸后断面面积;L0—拉伸前线材长度;L K—拉伸后线材长度。
二、拉丝设备(我厂现在使用的拉丝设备)铜拉:LHD2—400/13型滑动式大拉机(俗称上海十三模)、LS—450/13型滑动式连续退火大拉机(俗称合肥十三模)、LH450/13滑动式铜大拉连续退火机(上海鸿得利大拉机)、ZL250型滑动式连续退火中拉机、LH-280/17型滑动式中拉机和BT22—2型滑动式连续退火小拉机。
铝拉:LS-1-8/450型非滑动式铝拉机和LS-1-10/450型非滑动式铝拉机(俗称八、十模铝大拉)。
针对每一台设备我厂都编写了一份《设备操作规程》,其中对设备的主要技术参数、工艺参数、操作步骤及注意事项等方面做了较详细地阐述,供操作人员查阅使用。
设备的维护保养:铜拉丝机a、定期润滑各润滑点;b、定期检查齿轮的磨损及啮合情况;c、定期检查皮带张紧情况及破损程度;d、定期检查退火接触环和碳刷磨损情况,并及时更换损件;e、定期测试拉丝润滑液和冷却水的温度;f、每班工作后擦拭干净拉丝轮和接触轮,清理模座、拉丝室及软化回水箱室内的铜粉等残留物;g、严禁敲打拉丝塔轮,退火接触轮,过线导轮及卷取轴涨心;h、严禁拉制超出允许范围的产品;i、严禁使用未经动平衡的收线盘,不得使用与本机不配套的收线盘;j、严禁在未装收线盘时启动机器;k、做好各项安全检查。
拉丝培训

• 1、 有一根试样,其长度200mm,经拉伸试验 拉断后,长度变为290mm,试求其延伸率。 • 2、 有一根试样,其直径为Φ2.0mm,当受拉 力为1256N时,试样断裂,试求其抗拉强度。 • 3、 用Φ8.0mm铜杆拉制成Φ2.65mm铜线, 计算其延伸系数和压缩率。 • • 4、 试计算在20℃时,与电阻率 0.01748Ω·mm2/m相应的导电率。
拉丝工序问题汇总
• 1、拉线的定义是什么? • 答:在一定拉力作用下,使线坯通过模空后,截面积减少,长度增 加的过程 • 2、 实现线材拉制的必要条件是什么? • 答:拉伸应力大于或等于金属的变形抗力,小于金属的屈服极限。 • 3、相对延伸率的定义是什么? • 答:是线材拉伸后与拉伸前的长度之差与拉伸前长度的比值. • 4.千分尺的保养方法是什么? • 答:(1)使用时须注意爱护,,经长保持清洁,,小心轻放。. • (2)千分尺不用时,,应将测量面擦净,两测量面不应接触。. • (3)量尺失准后应及时送交计量室检修。. • (4)要长期保存时,应擦上油,装在盒里。 • 5.退火氧化线产生的主要原因是什么?
• • • • • • • • • • • • • • •
1、 根据鼓轮的速度与线材速度相比,拉线机有几种? 答:1. 鼓轮速度大于线材速度的为滑动式拉线机; 2. 鼓轮速度等于线材速度的为非滑动式拉线机。 2、 拉线模工作区锥角大小对拉伸力有何影响力。 答:1. 当锥角过大时,模型作用于金属的水平分力也增大,并 使润滑剂从模孔中挤出,恶 化润滑条件,使拉伸力增加。 2. 当锥角过小时,坯料与模塑的接触面增大,使摩擦力增 大,从而导致拉伸力增大。 3、 线材拉伸有何特点? 答:1. 拉伸的线材有较精确的尺寸,表面光洁,断面形状可以 多样; 2. 能拉伸大长度和各种直径的线材; 3. 以冷压力加工为主的拉伸工艺、工具、设备简单,生产 效率高; 4. 拉伸能耗较大,变形体受一定限制。 4、 异型线拉伸工艺何特点? 答:1. 工艺复杂,一般用拉、轧、挤等工艺; 2. 道次加工率不能太大,因拉伸过程中制品四周变形不均 匀,容易造成表面质量不佳; 3. 拉伸速度不能过大,因局部变形量大的部位容易裂开。
拉丝基础知识培训资料

⑧反拉力增大的因素:放线张力过大,上一道离开绞轮的 张力增大等会增加下一道的反拉力。反拉力增加时,拉伸 力也随之增加
三.拉线设备
种 类 单模 拉线机 多模 拉线机 名 称 卧式单模拉线机 立式单模拉线机 滑动式连续拉线机 非滑动式连续拉线机 特 点 拉线鼓轮卧式放置 拉线鼓轮垂直放置 线材与鼓轮之间滑 动,鼓轮呈塔形 连续.线材与鼓轮之 间无滑动
电源相连,当退火线在这些滚轮上接触通过时,导线就有电 流通过,导线接触于本身的电阻将电能转变为热能加热,实 现了退火 本设备退火示意图如下:
M2 K2正电极 M3
吹干器
M1
K3负电极 K1负电极 M4
1.退火装置主要由机身.退火轮.蒸汽保护室.冷却室.吹干器. 润滑系统.磁刷冷却以及一组转动皮带组成. 2. 整个退火加热区为二段,第一段为预热区长度为12米,第 二段为退火区长度为2米,在退火区,铜线被加热到500550℃,直流电源经过三只导轮接触轮通到铜线上,其中第 一导轮K1与第三导轮K3相联变为一组通的负电极,第二导 轮通的是正电极. 退火电压:V=√UL 8.47 U-退火速度m/s L-退火段长度 2m, 3.在退火中,K1-M1-M2-M3为预热段,K2-K3为退火段,此区 域铜线被密闭于蒸汽保护槽内,目的就是保护铜线在加热 高温中不被氧化.蒸汽最大用量20Kg/h,压力0.2Mpa,蒸汽 流量球阀手动调节,不要太大,铜线不氧化即可. 被加温的铜线经过K3退火轮时,有一密闭于冷却室迅速冷 却,在经过水平 冷却槽到达M4转向轮,到这里面铜线其本
冷却,铜线温度稍高于常温,冷却室中的冷却液0.5%-1%的 皂化乳液,0.2Mpa,用量为208L/min,冷却室必须完全充满 乳液,避免铜线在冷却过程中氧化变色,在K3退火轮密闭壳 体上设有冷却水位观察窗,通过调节,流量进水阀与排水挡 板的位置,使冷却水位处于观察窗的中线. 被冷却后的铜线经过M4轮进入第一吹干器,把铜线上的 初始水份吹去,调节吹干器出风口间隙大小为最佳,然后进 入第二吹干器,把残余的水份吹干.
拉丝新员工培训基本知识

表面有严重的斑点,氧 化变色,毛刺,影响上 漆使用,不影响后续拉
丝使用。
外
陷可
观
以弥 补。
铁轴 标识
目测 目测
全检
铁轴内不应有生锈,油污及水渍,变形等现象,轴底圆周边 预留线头槽内应有足够的线段。
每轴铜线上的标识纸应填写工整,内容完整(日期,规格, 工号,机台,产地,退火与否等内容)。
直径偏差
首检
十二、千分尺的使用
2. 中拉 2.1 2.500,2.600(加工铜)mm退火软线→0.60、0.80,1.000mm 退火软线供小拉机及上漆车间过程线。 2.2 2.500,2.600(加工铜)mm退火软线→规格线直接供上漆车间 涂漆。
3. 小拉 3.1 0.600,0.800,1.000,1.200mm退火软线→规格线,直接供上 漆车间涂漆。 3.2 0.800,1.000mm退火软线→0.140,0.170,0.210,0.250, 0.310,0.340mm微拉母料供微拉车间拉双零线,其中0.250mm线还 可供小拉机拉0.08mm以上双零线。
铜
加工铜
东莞
南韩
常州金
华新 DHX A04 铜
大宇 DY A05 铜
源铜
JY A06
江铜
华艺 HY A07 台一 TY A08
铜
铜
3、 设备运行状况检查
1. 设备发出异常响声,应立即停机,上报车间管理人员,决不 能带病运行。
2. 检查张力系统,张力复位后,张力加与张力减是否亮灯。 3. 检查各进线导轮塔轮和张力轮,三沟导轮,排线导轮包括猪
(3)清洁度。润滑剂应保持洁净,如在润滑剂中混入酸类物质,会 造成润滑剂分层,失去润滑效果,不利于拉伸。含碱量增加,拉伸后的 金属线材表面残留的润滑剂对金属线材有腐蚀的危害,影响使用寿命。 润滑剂中杂质增加,会影响润滑系统的畅通,造成润滑剂供应量不足, 影响润滑冷却效果。为了增强拉丝液油脂的稳定性,防止油脂分层及产 生细菌,我司对酸碱性也进行了控制,PH值一般控制在7.5-9.0之间.
- 1、下载文档前请自行甄别文档内容的完整性,平台不提供额外的编辑、内容补充、找答案等附加服务。
- 2、"仅部分预览"的文档,不可在线预览部分如存在完整性等问题,可反馈申请退款(可完整预览的文档不适用该条件!)。
- 3、如文档侵犯您的权益,请联系客服反馈,我们会尽快为您处理(人工客服工作时间:9:00-18:30)。
裸线车间员工培训内容一、拉丝拉丝是指线坯通过模孔在一定拉力作用下,发生塑性变形,使截面减小、长度增加的一种压力加工方法。
实现拉丝过程的条件,拉伸应力应大于变形区金属的变形抗力,同时小于模孔出口端被拉金属的屈服极限。
即:σK<σL<σSK式中σK—变形区金属变形抗力;σL—拉伸应力;σSK—被拉伸金属出口端的屈服极限。
拉伸属于压力加工范围,拉伸过程中产生极少粉屑,体积变化甚微,因此认为拉伸前后金属的体积相等。
即:V0=V K,所以S0/S K= L K/L0=d02/ d K2。
表示拉伸过程金属变形量的基本参数有:1、相对延伸系数,拉伸后与拉伸前线材长度的比值:μ=L K/L02、压缩率,是线材拉伸前后断面面积之差与拉伸前断面面积的比值:δ=(S0- S K)/ S0×100%3、延伸率,是线材拉伸后与拉伸前的长度之差与拉伸前长度的比值:λ=(L K- L0)/ L0×100%4、减缩系数,是线材拉伸后与拉伸前断面面积的比值:ε=S K/S0式中V0—拉伸前金属体积;V K—拉伸后金属体积;S0—拉伸前断面面积;S K—拉伸后断面面积;L0—拉伸前线材长度;L K—拉伸后线材长度。
二、拉丝设备(我厂现在使用的拉丝设备)铜拉:LHD2—400/13型滑动式大拉机(俗称上海十三模)、LS—450/13型滑动式连续退火大拉机(俗称合肥十三模)、LH450/13滑动式铜大拉连续退火机(上海鸿得利大拉机)、ZL250型滑动式连续退火中拉机、LH-280/17型滑动式中拉机和BT22—2型滑动式连续退火小拉机。
铝拉:LS-1-8/450型非滑动式铝拉机和LS-1-10/450型非滑动式铝拉机(俗称八、十模铝大拉)。
针对每一台设备我厂都编写了一份《设备操作规程》,其中对设备的主要技术参数、工艺参数、操作步骤及注意事项等方面做了较详细地阐述,供操作人员查阅使用。
设备的维护保养:铜拉丝机a、定期润滑各润滑点;b、定期检查齿轮的磨损及啮合情况;c、定期检查皮带张紧情况及破损程度;d、定期检查退火接触环和碳刷磨损情况,并及时更换损件;e、定期测试拉丝润滑液和冷却水的温度;f、每班工作后擦拭干净拉丝轮和接触轮,清理模座、拉丝室及软化回水箱室内的铜粉等残留物;g、严禁敲打拉丝塔轮,退火接触轮,过线导轮及卷取轴涨心;h、严禁拉制超出允许范围的产品;i、严禁使用未经动平衡的收线盘,不得使用与本机不配套的收线盘;j、严禁在未装收线盘时启动机器;k、做好各项安全检查。
铝拉机a、定期润滑各润滑点;b、定期检查齿轮的磨损及啮合情况;c、发现拉丝鼓轮的冷却水开关出现异常应及时通知更换;d、每班工作后擦拭干净机座和拉丝鼓轮上的油污;e、更换拉丝油时,严禁敲打油盒内的电加热管;f、出现收线盘震荡时,应立即停机检查;g、做好各项安全检查。
拉丝设备的维护保养要做到,a、设备开车前检查各传动部位有无杂物,防护罩是否完整无缺。
齿轮箱油量是否在油标位置;b、开车前要按定人、定时、定点、定质、定量加润滑油,油孔、油杯保持清洁畅通;c、坚持做到设备维护四项要求(清洁、整齐、润滑、安全)和三好四会(用好、管好、修好;会保养、会使用、会检查、会排除故障),发现不正常现象立即停机;d、发生设备事故做到三不放过,即不查清事故原因不放过,当事人和群众不受教育不放过,没有防范措施不放过。
三、拉丝工艺要求及质量控制要点1、拉丝配模配模是指每道拉伸前后尺寸的确定,即选择每道拉伸线模的尺寸。
合理的配模能充分利用金属的塑性,采用最少的拉伸道次,提高生产效率,缩短生产周期;减少拉断、拉细现象,保证足够的安全系数;拉伸后的线材能够达到要求的尺寸和形状,良好的表面质量,合格的机械、电气性能。
操作人员应根据各个机台的拉丝工序工艺卡片上的拉丝配模表进行配模,但根据原材料的材质和进线的尺寸,操作人员可以对各道的配模尺寸作适当的调整,并要求做好相应的记录。
2、拉丝速度拉丝速度太快会使设备超负荷运动,影响设备的使用寿命。
连续退火拉丝时,退火电压与拉丝速度有关,拉丝速度太快会使单线的退火达不到要求的效果。
拉丝速度太快也会降低拉丝润滑液和冷却水对单线的冷却程度,可能引起单线表面氧化变色。
当然,拉丝速度过慢使生产效率降低,造成资源浪费。
操作人员应根据各个机台的拉丝工序工艺卡片上规定的拉丝速度值进行操作设定,但在设备运行能力允许的情况下,冬天生产时的拉丝速度可比夏天稍高。
3、拉丝润滑与冷却铜拉丝润滑剂,在拉丝过程中起到润滑、冷却和清洗作用。
要求成膜性好,能有效地粘附在加工金属的表面;能承受高压,热稳定性好;没有腐蚀性;冷却效果好;加工之后易除去;没有刺激性气味,对人体无害。
注意:润滑液必须每天使用,循环;定期测定润滑液的三度(温度、酸碱度和百分比浓度),温度控制在30~40℃为宜,酸碱度PH值在7.5~8.5之间,百分比浓度根据拉丝机的型号(大拉、中拉、小拉和细拉)而定;保持润滑液的清洁,定期清理设备和池内沉积的铜泥;为了不破坏所用润滑液的平衡体系,不要将不同厂家生产的润滑剂混合使用;任何一种润滑液不可长期使用,必须定期(6~12个月)更换。
铜拉冷却液,对连续退火后的铜线进行冷却,一般是0.5%的皂化水。
拉丝过程中要求从冷却室出口处流出的冷却液的温度控制在60℃以下,如发现温度偏高时,可降低拉丝速度或加大冷却水量。
我厂对拉丝冷却液进行了循环冷凝处理,可保证温度在控制范围内。
铝拉丝润滑油,一般使用过热汽缸油,夏天用52号,冬天用38号。
为了保证拉制的铝单线表面质量(主要是油污),要求每班开机时必须将出线模和前一模座内的润滑液换到其它模内,该两只应加新的润滑液并充分搅拌才能开机,冬天还需将油盒内的加热器开启,将润滑油的温度升至约65℃时才能开机。
根据铝单线表面质量情况,也可用机油+汽缸油+猪油按一定比例调配使用。
铝拉冷却水,该冷却水作用在拉丝鼓轮内壁上对缠绕在鼓轮上的铝线进行冷却。
当发现出线模的铝丝表面将有槽时要及时开冷却水,丝表面不光亮时应及时关闭冷却水。
4、拉丝的质量控制要点对线坯要认真检查,线坯必须符合标准要求;配模必须符合规范,与所用的拉丝机相适应。
模具符合规定要求;润滑剂必须定期检测,浓度与所拉制的规格相适应;拉丝鼓轮上的缠绕圈数要按照规定;拉制产品的偏差值控制在标准规定的范围内。
四、不合格品产生的原因及解决的办法作参考。
五、文明生产与现场5S管理即使拥有世界上最先进的生产工艺或设备,如不对其进行有效地管理,工作场地一片混乱,工件乱堆乱放,其结果只能是生产效率低下,员工越干越没劲,这样的企业我们认为它只会生产问题和制造麻烦,对人类社会没有任何积极的意义。
5S来自日文SEIRI(整理)、SEITON(整顿)、SEISO(清扫)、EIKETSU(清洁)、SHITSUKE(修养)发音的第一个字母“S”,所以统称为“5S”。
5S活动不仅能够改善生产环境,还能提高生产效率、产品品质、员工士气,是其他管理活动有效展开的基石之一。
(一)、5S现场管理的内容5S现场管理包括整理、整顿、清扫、清洁、修养五方面的内容,具体包括:1、整理整理就是将必需物品与非必需品区分开,必须品摆在指定位置挂牌明示,实行目标管理,不要的东西则坚决处理掉,在岗位上不要放置必需以外的物品。
这些被处理掉的东西可能包括原辅材料、半成品和成品、设备仪器、工模夹具、管理文件、表册单据等。
其要点如下:①对每件物品都要看看是必要的吗?非这样放置不可吗?②要区分对待马上要用的、暂时不用的、长期不用的;③即便是必需品,也要适量;将必需品的数量要降低到最低程度;④在哪儿都可有可无的物品,不管是谁买的,有多昂贵,也应坚决处理掉,决不手软!⑤非必需品是指在这个地方不需要的东西在别的地方或许有用,并不是“完全无用”的意思,应寻找它合适的位置。
⑥当场地不够时,不要先考虑增加场所,要整理现有的场地,你会发现竟然还很宽绰。
2、整顿①除必需物品放在能够立即取到的位置外,一切乱堆乱放、暂时不需放置而又无特别说明的东西,均应受到现场管理干部(小组长、车间主任等)的责任追究。
这种整顿对每个部门都同样重要,它其实也是研究提高效率方面的科学,它研究怎样才可以立即取得物品,以及如何能立即放回原位。
任意存放物品并不会让你的工作速度加快,反而使你的寻找时间加倍,你必须思考分析怎样拿取物品更快,并让大家都能理解这套系统,遵照执行。
这样:②将寻找的时间减少为零;③有异常(如丢失、损坏)能马上发现;④其他人员也能明白要求和做法,即其它人员也能迅速找到物品并能放回原处;⑤不同的人去做,结果是一样的(已经标准化)。
3、清扫就是将工作场所、环境、仪器设备、材料、工具等上的灰尘、污垢、碎屑、泥砂等脏东西清扫擦拭干净,创造一个一尘不染的环境。
①最好能分配每个人应负责清洁的区域。
分配区域时必须绝对清楚地划清界限,不能留下没有人负责的区城(即死角)。
②对自己的责任区域都不肯去认真完成的员工,不要让他担当更重要的工作。
③到处都干净整洁,客户感动,员工心情舒畅。
④在整洁明亮的环境里,任何异常,包括一颗螺丝掉在地上都可马上发现。
⑤设备异常在保养中就能发现和得到解决,不会在使用中“罢工”。
4、清洁清洁就是在“整理”、“整顿”、“清扫”之后的日常维持活动,即形成制度和习惯。
每位员工随时检讨和确认自己的工作区域内有无不良现象,如有,则立即改正。
在每天下班前几分钟(视情况而定)实行全员参加的清洁作业,使整个环境随时都维持良好状态。
实施了就不能半途而废,否则又回到原来的混乱状态。
①领导的言传身教、制度监督非常重要;②一时养成的坏习惯,要花十倍的时间去改正。
5、修养修养就是培养全体员工良好的工作习惯、组织纪律和敬业精神。
每一位员工都应该自觉养成遵守规章制度、工作纪律的习惯,努力创造一个具有良好氛围的工作场所。
如果绝大多数员工能够将以上要求付诸实践的话,个别员工就会抛弃坏的习惯,转向好的方面发展。
①学习、理解并努力遵守规章制度,使它成为每个人应具备了一种修养;②领导者的热情帮助与被领导者的努力自律是非常重要的;③需要人们有更高的合作奉献精神和职业道德;④互相信任,管理公开化、透明化;⑤勇于自我检讨反省,为他人着想,为他人服务。
⑥近年来,随着人们对这一活动的不断深入认识,有人又添加了“坚持、习惯”等两项内容,分别称为6S或7S活动。
(二)、5S现场管理的重要作用5S现场管理对企业的重要意义可从以下几个方面来认识。
(1)工作场所干净而整洁。
员工的工作热情提高了,忠实的顾客也越来越多了,企业的知名度不断很高,很多人慕名而来参观学习,结果扩大了企业的声誉和销路;(2)员工能够具有很强的品质意识。
按要求生产,按规定使用,尽早发现质量隐患,生产出优质的产品。