8D——团队导向问题解决方法
8D又称团队导向问题解决方法

8D工作方法简介8D又称团队导向问题解决方法、8D问题求解法(8D Problem Solving)是福特公司处理问题的一种方法,亦适用于制程能力指数低於其应有值时有关问题的解决,它提供了一套符合逻辑的解决问题的方法,同时对於统计制程管制与实际的品质提升架起了一座桥梁。
8D工作方法是发现真正肇因的有效方法,并能够采取针对性措施消除真正肇因,执行永久性矫正措施。
8D 工作方法创造了能够帮助探索“允许问题逃逸的控制系统”,对逃逸点的研究有助于提高控制系统在问题再次出现时的监测能力,而预防机制的研究则有助于系统将问题控制在初级阶段。
8D工作方法要求建立一个体系,让整个团队共享信息,努力达成目标,是处理问题的一种方法,也适用于制程能力指数低于其应有值时有关问题的解决,对不合格产品问题的解决,面对顾客投诉、反复频发问题以及需要团队作业问题的解决。
[编辑]8D工作方法的起源二战期间,美国政府率先采用一种类似8D的流程——“军事标准1520”,又称之为“不合格品的修正行动及部署系统”。
1987年,福特汽车公司首次用书面记录下8D法,在其一份课程手册中这一方法被命名为“团队导向的问题解决法”(Team Oriented Problem Solving)。
当时,福特的动力系统部门正被一些经年累月、反复出现的生产问题搞得焦头烂额,因此其管理层提请福特集团提供指导课程,帮助解决难题。
[编辑]8D适用范围∙该方法适用于解决各类可能遇到的简单或复杂的问题;∙8D方法就是要建立一个体系,让整个团队共享信息,努力达成目标。
∙8D本身不提供成功解决问题的方法或途径,但它是解决问题的一个很有用的工具;∙亦适用于过程能力指数低于其应有值时有关问题的解决;∙面对顾客投诉及重大不良时,提供解决问题的方法。
∙8D法是美国福特公司解决产品质量问题的一种方法,曾在供应商中广泛推行,现已成为国际汽车行业(特别是汽车零部件产家)广泛采用来解决产品质量问题最好的、有效的方法。
8D (问题解决法)

何时
比较重大的制程品质问题
采用
8D
重复发生,一直没有解决的问题
第四部分
什么是8D. 为什么要推行8D. 什么时候采用8D. 8D工作方法.
8D改善案例分享.
8D工作方法
定义
D0
Define
建立小组
D1
Form the Team
D 2
问题描述 Describe the Problem
临时对策
D 3
Contain the Problem
原因分析 RCA
D4
确定可能原因
Identify the Root Cause
选择最可能原因
最有
NO
可能的原因
是否是根本
原因?
YES
确定根本原因
验证长期改善对策
D5
Formulate and Verify
Corrective Actions
改善并确定最终结果
D6
8D工作方法-D5验证长期对策
目的:在生产前测试方案,并对方案进行评审以确定所选的 校正措施能够解决客户问题,同时对其它过程不会有不良 影响。
关键要点: 重新审视小组成员资格;决策,选择最佳措施;重 新评估临时措施,如必要重新选择;验证;管理层承诺执行 永久纠正措施;控制计划
8D工作方法-D6确定最终结果
8D改善案例分享.
为什么要推行8D
● 提供问题有效解决的方法 ● 防止相同或类似问题的再发生。 ● 通过建立小组提高组织内部合作的技巧。 ● 提高顾客满意度,增强顾客的信心。
第三部分
什么是8D. 为什么要推行8D. 什么时候采用8D. 8D工作方法.
8D改善案例分享.
什么时候采用8D
IATF16949中的8D详解

8D详解8D 的原名叫做 8 Eight-Disciplines,其意思是指8个人人皆知解决问题的固定步骤。
也可以称之为TOPS(Team Oriented problem solving),即团队导向问题解决方法。
8D主要用于汽车及类似加工行业的问题解决方法。
原始是由Ford公司,全球化品质管制及改善的特殊必备方法,之后已成为QS9000/ISO TS16949、福特公司的特殊要求。
SQE在给供应商做8D报告的培训的时候,必须跟供应商讲清楚,作为供应商在撰写8D报告的时候,务必要保证下面的问题被清楚准确有理有据地回答:D2-问题是什么?D3~D6-问题如何解决?D7-将来该问题如何预防?然而作为SQE在审阅供应商的8D报告的时候,也务必保证以下的问题被如实回答:1、对零件的知识进行了充分的论证。
2、完全确定了根本原因并聚焦于该原因。
3、遗漏点已经被识别。
4、确定与根本相匹配的纠正措施。
5、纠正措施计划的验证已经被确定。
6、包括了实施纠正措施的时间计划。
7、有证据显示供方将把纠正措施纳入整个系统。
8D的实施过程可能用到的质量工具总结如下:可靠性;设计验证DV;产品和过程确认;潜在失效模式及后果分析FMEA;控制计划CP;PPAP文件;SPC;DOE;QC7大工具。
8D是解决问题的8条基本准则或称8个工作步骤,但在实际应用中却有9个步骤:D0:征兆紧急反应措施;D1:小组成立;D2:问题说明;D3:实施并验证临时措施;D4:确定并验证根本原因;D5:选择和验证永久纠正措施;D6:实施永久纠正措施;D7:预防再发生;D8:小组祝贺。
D0:征兆紧急反应措施目的:主要是为了看此类问题是否需要用8D来解决,如果问题太小,或是不适合用8D来解决的问题,例如价格,经费等等,这一步是针对问题发生时候的紧急反应。
关键要点:判断问题的类型、大小、范畴等等。
与D3不同,D0是针对问题发生的反应,而D3是针对产品或服务问题本身的暂时应对措施。
8D法则

一.8D8D 的原名叫做8 Eight-Disciplines,意思是8 个人人皆知解决问题的固定步骤;也可以称为TOPS(Team Oriented problem solving)即团队导向问题解决方法。
Discipline 1. 成立改善小组(Form the TeamDiscipline 2. 描述问题(Describe the Problem)—5W1HDiscipline 3. 实施及确认暂时性的对策(Contain the Problem)--工具FMEA/DOEDiscipline 4. 原因分析及验证真因(Identify the Root Cause)—--4M1EDiscipline 5. 选定及确认长期改善行动效果(Formulate and Verify Corrective Actions) Discipline 6. 改善问题并确认最终效果(Correct the Problem and Confirm the Effects) Discipline 7. 预防再发生及标准化(Prevent the Problem)Discipline 8. 恭喜小组及规划未来方向,结案(Congratulate the Team)二.DOE(Design of Experiment,试验设计)D OE(Design of Experiment)试验设计,一种安排实验和分析实验数据的数理统计方法;试验设计主要对试验进行合理安排,以较小的试验规模(试验次数)、较短的试验周期和较低的试验成本,获得理想的试验结果以及得出科学的结论。
什么时候用到DOE要为原料选择最合理的配方时(原料及其含量);要对生产过程选择最合理的工艺参数时;要解决那些久经未决的“顽固”品质问题时;要缩短新产品之开发周期时;要提高现有产品的产量和质量时;要为新或现有生产设备或检测设备选择最合理的参数时等。
DOE的步骤第一步确定目标第二步剖析流程第三步筛选因素第四步快速接近第五步析因试验第六步回归试验第七步稳健设计三.5W3H分析法,又称“八何分析法”。
8D---团队导向问题解决方法

8D又称团队导向问题解决方法,是福特公司处理问题的一种方法,亦适用于制程能力指数低於其应有值时有关问题的解决,它提供了一套符合逻辑的解决问题的方法,同时对於统计制程管制与实际的产品质量提升架起了一座桥梁。
主要步骤包括:D1:小组成立D2:问题说明D3:实施并验证临时措施D4:确定并验证根本原因D5:选择和验证永久纠正措施D6:实施永久纠正措施D7:预防再发生D8:小组祝贺D1:小组成立目的: 成立一个小组,小组成员具备工艺/产品的知识,有配给的时间并授予了权限,同时应具有所要求的能解决问题和实施纠正措施的技术素质。
小组必须有一个指导和小组长。
关键要点: 成员资格,具备工艺、产品的知识目标分工程序小组建设D2:问题说明目的: 用量化的术语详细说明与该问题有关的内/外部顾客抱怨,如什么、地点、时间、程度、频率等。
“什么东西出了什么问题”方法:质量风险评定,FMEA分析关键要点: 收集和组织所有有关数据以说明问题问题说明是所描述问题的特别有用的数据的总结审核现有数据,识别问题、确定范围细分问题,将复杂问题细分为单个问题问题定义,找到和顾客所确认问题一致的说明,“什么东西出了什么问题”,而原因又未知风险等级D3:实施并验证临时措施目的: 保证在永久纠正措施实施前,将问题与内外部顾客隔离。
(原为唯一可选步骤,但发展至今都需采用)方法:FMEA、DOE、PPM 关键要点: 评价紧急响应措施找出和选择最佳“临时抑制措施”决策实施,并作好记录验证(DOE、PPM分析、控制图等)D4:确定并验证根本原因目的: 用统计工具列出可以用来解释问题起因的所有潜在原因,将问题说明中提到的造成偏差的一系列事件或环境或原因相互隔离测试并确定产生问题的根本原因。
方法:FMEA、PPM、DOE、控制图关键要点: 评估可能原因列表中的每一个原因原因可否使问题排除验证控制计划D5:选择并验证永久纠正措施目的: 在生产前测试方案,并对方案进行评审以确定所选的校正措施能够解决客户问题,同时对其它过程不会有不良影响。
8D准则

33
使用"有/没有"工作单详细描述问题(继续) 何处: 在对象上哪个地方有了问题?对象上的其 它地方也可能有那个问题,但却没有? 从位置上讲,哪里第一次有了问题?其它 位置也可能有那个问题,但却没有?
34
使用" 没有 工作单详细描述问题(继续) 没有" 使用"有/没有"工作单详细描述问题(继续)
31
详细描述问题 详细描述问题是对问题描述进行详细补充, 目的在于阐明:什么问题,哪里发生,何时 发生,问题多大.也称为"有/没有"过程.
32
使用" 没有 没有" 使用"有/没有"工作单详细描述问题 何物: 什么对象有了问题?什么类似的对象也可 能有那个问题,但却没有? 有什么问题?什么类似的问题也可能发生 在那个对象,但却没有?
何时: 什么时候第一次探测到了问题?其它时间也可 能第一次探测到那个问题,但却没有? 在第一次后,什么时候又探测到了问题?第一 次后的其它时间也可能探测到那个问题,但却 没有? 制程中的什么时间有了问题?制程中的其它时 间也也可能有那个问题,但却没有? 制程中的什么班次有了问题?制程中的其它班 次也可能有那个问题,但却没有? 在产品周期的什么时间有了问题?在产品周期 的其它时间可能有那个问题,但却没有?
13
选择紧急反应行动
通常最合适的紧急反应行动由几个人就可 以确定的,比如, 以确定的,比如,团队保驾人和那些对产 生问题的系统有认知的人员. 生问题的系统有认知的人员. 有时,最合适的紧急反应行动是显而易见 有时, 比如,停止出货. 的,比如,停止出货.当紧急反应行动并 不明确时, 不明确时,可以采用头脑风暴法提出一些 备用方案,从中选择出最佳方案. 备用方案,从中选择出最佳方案.
团队导向问题解决方法 8D(核心要素)

达成目标 未达成目标
不稳定
短期型 失败型
稳定
理想型 稳定性
22
D7:预防再发生 标准化是把企业所累积的技术、经验,通过文件的方式进行规范。 1. 将现场必须要做到的条件可视化; 2.制作易懂、易记、易做的标准书(照片、图片、流程图) 3.进行教育培训 4.制定检查体系 5.进行标准重审和修正
23
人是不可靠的动物
✓ 努力避免失误
形式 标示型 警告型 自働化 防错型
作业员的作用 禁止事项、注意事项放大化
治工具与设备的作用
标示、分色清晰
出现误操作,蜂鸣或闪灯 警示
出现误操作,工件不能往 下送
设计为无法误操作的工治 具和设备
工件的作用 颜色管理 出现误操作,下一工序可 立刻判断 下一工序无法装配
团队导向问题解决方法 8D
撰写人:XXX 2019年08月07日
目录
01 8D简介
02 8D的逻辑核心点
2
3
公司请你的目的
4
没有问题,才是最大的问题
应有的姿态 差距
现状
=目标、基准、标准、要求
问题
大野耐一
5
8D是什么?
8D问题解决法(Eight Disciplines Problem Solving, 缩写:8D)也称为团队导向问题解决方法或8D report,是一个处理及解决问题的方法
6
异常处理逻辑步骤
紧急反应措施 小组成立 问题说明 实施并确认临时措施 确定并验证根本原因 选择并验证永久纠正措施 预防再发生 小组祝贺
D1 紧急反应措施
D8 小组祝贺
D7 预防再发生
D2 小组成立
D6 选择并验证 永久措施
8D(解决问题的8个步骤)

四、问题处理描述
3D: 暂时对策
为使外部或内部的客户都不受到该问题的 影响,制定并执行临时性的围堵措施,直到已 采取了永久性的改进。要确保围堵行动可收到 预期的效果。
四、问题处理描述
4D: 找根本原因及忽略点 就问题的描述和收集到的资料进行比较分 析,分析有何差异和改变,识别可能的原因, 测验每一个原因,以找出最可能的原因,予以 证实。
二、方法介绍
主要特点之三:肯定贡献
8D程序的第8D就是管理者要衷 心肯定团队及个人的贡献,予 以祝贺。这是使8D能持续开展 的保证。
三、问题处理图
四、问题处理描述
症状:是一个显示存在 一个或多个问题的可测 量的事件或结果。这个 事件的后果必须被一个 或多个(顾客经历症状 是问题的显示)
D0:问点紧急响应 1/状态的定义 2、紧急响应措施 3、量化症状
四、问题处理描述
5D: 选择最佳永久性纠正对策 针对已确认的根本原因制订永久性的纠正 措施,要确认该措施的执行不会造成其它任何 不良影响。
四、《8D》的问题处理描述
6D: 执行永久对策 执行永久性的纠正措施,并监视其长 期效果 。
四、《8D》的问题处理描述
7D:预防再发生 修正必要的系统,包括方针、 运作方式、 程序,以避免此问 题及类似问题的再次发生。必要 时,要提出针对体系本身改善的 建议。
目 录
一、目的 二、方法介绍 三、问题处理图 四、问题处理描述
一、目的
ቤተ መጻሕፍቲ ባይዱ
1、及时解决客户对公司的投诉; 2、公司各部门以此举一反三;
3、倡导企业的团队精神。
二、方法介绍
8D(Eight-Discipline)也可称为TOPS(Team Oriented Problem Solving) 即团队导向问题解 决对策。
8D是什么

8D是什么8D方法由8个步骤和1个准备步骤组成,客观地确定、定义和解决问题并防止相似问题的再次发生。
8D方法应用流程:—1—D1组建问题解决团队8D原名就是叫团队导向问题解决步骤,8D小组需要由具备产品、制程及相关知识,能支配时间且拥有职权及技能的人士组成,必须指定一名8D团队组长。
不具备以上条件的8D是失败的8D,它没法在你需要资源解决问题时提供帮助。
若一个体系出现了异常,绝非单一部门职能失效,否则整个体系需要重新进行完善。
8D团队的角色构成:8D负责人:作为8D项目支持者的身份参与8D项目。
没有负责人的签字8D报告不能进行关闭审批。
8D组长:负责8D全过程的进行直至问题解决、8D项目关闭8D组员:在组长的协调下利用自身知识与技能参与8D问题的解决确定团队成员应注意的问题:团队人数:4~10人组长的选择:部门经理指定本部门人员或亲自担任组员的选择原则:与问题相关且具备相关的资源、能力D1的常见性错误:选择的8D团队成员对涉及问题没有相关知识或认识;只有一两个人实施8D过程。
—2—D2描述问题以客户的角度和观点详细描述其所感受到的问题现象,将所遭遇的问题,以量化的方式,明确出所涉及的人、事、时、地、为何、如何、多少。
如何进行问题描述?要找到问题的根源而不是表现症状的简单描述;要定义问题的边界(不要将问题范围扩大到不可控的范围之外)5W2H方法Who~谁发现的问题?When~什么时间发现的问题?Where~在何处发现的问题?What~有什么问题发生?Why~为何问题此时发生?How~问题如何发生?Howmany~问题发生的程度(多大?范围?比例?)D2的常见性错误:针对表象而不是针对真正的问题进行描述;对问题的根本原因做过早的假设。
—3—D3开发临时性控制措施定义、验证和执行临时控制行动,保证在永久纠正措施实施前,将问题与内外部客户隔离。
采用ICA作为暂时性的问题解决对策~隔离问题开发ICA:-保护问题可能的相关角色免受问题的影响~隔离问题-争取时间让8D团队找到问题的根本原因~在根本性解决措施出台之前防范问题的重复发生-ICA将执行到根本性解决措施(PCA) 采用为止—4—D4确定问题根本原因寻真因如求医问诊,误诊或诊断不全,后患无穷。
8D(团队导向问题解决对策)

名稱::8D(團隊導向問題解決對策)編號:版次:A一〃8D 概觀 這八項准則,或稱為8Ds,是福特汽車公司在問題原因不明時用于解決問題的方 法,它是一种在同一時間之內將三种不同事情一起處理的方法:1一個問題解決程序2一個標准3一份報告格式(利害關系分析報告表或CAR)做為一個問題解決程序,它是一种事件的程序且必須自問題開始顯著時即予遵行,當正 确地遵行時,它有助于能在時間之內完全地解決一項問題。
它是一項標准,是進行的一個規則,它反映解決一已知問題的主要利害關系處,在此強 調兩區域: A一個事實為基礎之偏差,在此,問題的解決,決策以及計划係由實質之事實數据 來驅動及偵測。
B問題的解決表示承諾問題之根源,并不只是遮蓋問題之徵候或其結果。
做為一個報告格式,8D用來作解決一問題時之溝通工具,本表格係用于福特汽車公 司之內或給報告至福特汽車公司。
什么時候您該寫一份8D呢?一個8D之填報在原因不明之情況就适宜,但如果一 利害關系僅用于決策或僅用于預防問題時就不适于填報。
因為8D是一种事情實個步驟僅當有适當的資訊時才予以完成,因此8D報告通常僅包括某些8D步驟, 因為要填報其他之步驟需要有更多的資訊才行,在這种報告的情況之下,8D提供之 至今進度以及完成其他各步驟之行動計划,8D報告是一种活生生的文件用以顯示 至今之進展及完成問題解決工作之一項計划。
在某些情況之下當題嚴得性大的時候,8D報告之格式即使在問題之擊因已知道時仍适當,這情況這例子可能是在每周之品質管制表上的一個問題之清單,然后8D報告變成為一管理工具用于審查鑒別及証明擊因之過程,并用于執行永久性改正措施及管理層利潤管理品質及安全管成本物名稱::8D(團隊導向問題解決對策)編號:版次:A 預防其再度發生。
本工作書本節係為提供一未來之參考用,當在本課程中完成時,有一份每一項8D之類別。
在本節之中,當完成時,它是用于擴大但不是用于更換,團隊導向問題解決書中所提供之每一個8D課程之更詳細的部份。
8d解决问题的方法

8d解决问题的方法摘要:1.问题背景和重要性2.8D解决问题的方法简介3.8D解决问题的步骤详解4.案例分析5.8D方法在各行业的应用6.提高8D方法效果的建议7.总结正文:一、问题背景和重要性在日常生活和工作中,我们总会遇到各种各样的问题。
解决问题的能力对于个人和团队的发展至关重要。
一个高效的问题解决方法可以帮助我们更好地应对挑战,提高工作效率,实现目标。
本文将介绍一个结构化的问题解决方法——8D解决问题法,并通过案例分析其应用,以提高大家对这一方法的认识和掌握。
二、8D解决问题的方法简介8D解决问题法(8 Disciplines Problem Solving Process)是一种团队导向的问题解决方法,适用于复杂、多因素的问题。
该方法以团队协作为基础,通过八个步骤有计划地分析问题、找出根本原因并制定解决方案。
这八个步骤分别是:1.组成团队2.确定问题3.制定计划4.收集数据5.分析数据6.确定根本原因7.制定解决方案8.实施并验证解决方案三、8D解决问题的步骤详解1.组成团队:一个跨职能的团队,包括涉及问题领域的专家和相关部门的代表。
团队成员应具备解决问题所需的技能和知识,人数一般在5-10人之间。
2.确定问题:明确问题的定义,描述问题的现象和影响,确保团队成员对问题有共识。
可以使用鱼骨图、流程图等工具辅助分析问题。
3.制定计划:确定解决问题的目标和期限,制定详细的工作计划,包括每个步骤的时间安排和资源分配。
4.收集数据:通过现场观察、访谈、问卷调查等方式收集与问题相关的数据。
数据应具有客观性、完整性和准确性,以便后续分析。
5.分析数据:对收集的数据进行整理和分析,找出数据的规律和趋势。
可以使用多种分析工具,如帕累托图、相关性分析等。
6.确定根本原因:根据数据分析结果,找出导致问题的根本原因。
可以使用因果图、头脑风暴等方法,充分挖掘问题的深层次原因。
7.制定解决方案:针对根本原因,制定具体的解决方案。
8D小组解决问题的方法

制造业生产部门经理/主管/专员
课程大纲
8D概述
●8D的目的
●8D报告必须回答问题●8D的处D0准备8D过程●实施紧急反应措施(ERA)
●症状和问题
●量化症状的工具:趋势图柏拉图
D0准备8D过程案例
D1确定团队
●为什么要确定团队
●确定团队成员时应考虑
●多功能复合资格
●头脑风暴过程
D1确定团队案例
●为什么要预防问题的再次发生
●预防再发生
●领导的责任
●标准化;
●防错法
D7防止问题再次发生案例
D8表彰小组和个人的贡献
●表扬小组和个人的贡献
8D报告填写提交
8D过程中常见的问题
b)此方式宜由公司各部门人员的共同投入,求得创造性及永久性的解决方案。
c)此方式可适用于任何问题,而且能促进相关目标的各部门间有效的沟通。
培训目的
了解问题解决的工具和技巧
掌握使用8D方法实施闭环纠正预防措施
使现场管理人员、生产制造人员、质量技术人员、工艺人员等掌握有效、系统的解决问题的方法和思路
能在最短的时间内消除不良,恢复生产,保证交付,降低成本,提高解决问题的效率
D2描述问题
●问题陈述
●如何进行问题描述
●5W2H的描述问题的方法
●“是/不是”表格
●5Why找出根本原因
●系统图
●过程流程图
●因果图(鱼骨头图)
D2描述问题案例
D3实施临时性遏制措施
●临时遏制措施ICA特点
●损失函数思维方式
●开发ICA的四个步骤
●临时对策需要考虑的问题
D3实施临时性遏制措施案例
D4确定和验证根本原因
课程名称
8D方法

成果? • 是否采用“头脑风暴”等方法收集纠正措施? • 是否获得了多项纠正措施方案并对其进行了筛选? • 是否需要召开决策评审会或者风险评估会? • 措施是否考虑了问题的时间? • 措施是否充分考虑条件? • 措施是否考虑问题的大小? • 纠正措施的实施是否涉及到顾客?是否与其进行了沟通? • 是否制定了工作进度时间表?
8D方法
目录
1 何谓8D 2 何时8D 3 如何8D 4 8D报告 5 8D实例学习
8D(8 Disciplines)又称团队导向问题解 决方法,意思是8个人人皆知解决问题的固定 步骤,是福特公司处理问题的一种方法。它提 供了一套符合逻辑的解决问题的方法,同时对 於统计制程管制与实际的品质提升架起了一座
8、小组祝贺:
• 目的:承认小组的集体努力,对小组工作进行 总结并祝贺 。
• 步骤:1、汇报工作成果(编写案例分析报告;有选择
的保留重要文档;流览小组工作,将心得形成文件;撰写PPT进 行汇报)
2、肯定与奖励(肯定小组对解决问题的集体力
量,及对解决问题作出的贡献;给予必要的物质、精神奖励)
注意:
撰写8D报告,并将所有重要文档归档保存。
端口破损数(卷) 频率(%) 累计频率(%)
A。产品堆放高度过高
12
52.17 52.17
B。包装方式不合理
4
17.39 69.56
C。操作粗心
2
8.69 78.25
D。库房湿度大
1
4.34 82.59
E。速度设定太快
1
质量工具-8D

临时措施
消除问题及后果
长期措施
消除问题原因
可以治本 (不会再发)
四. 8D步骤—D4原因分析
用统计工具列出可以用来解释问题起因的所有潜在原因,再 分别针对每一可能原因予以测试,最终确定产生问题的根本 原因。 需要考虑的问题:
1.列可能 原因时要 周全。 2. 原因和结 果要有论证, 说得通。 3.原因一定是根本 原因,而非表面原 因。
对小组的效益进行沟通和文件化
8D知识介绍
一.什么是8D
8D 的原名叫做 8 Disciplines,又称团队导向问题解决方 法。是由福特公司始创,全球化品质管制及改善的必备方法,已 成为QS9001、ISO/TS16949、福特公司的特殊要求。凡是做福特 的零件,必需采用 8D 作为品质改善的工具,目前有些企业并非
福特的供应商或汽车业的合作伙伴,也很喜欢用这个方便而有效
问题初步了解(立项和准备工作)
鉴定是否有进行8D 的必要; 立项和确定主题; 收集资料。
此过程尽量获取内部 和外部的问题信息、 数据、进行初步的分 析和方案策划。
四. 8D步骤—D1建立小组
建立小组需要考虑的要素:
小组的领导: 小组的资源: 小组的成员: 谁来推动? 谁提供支持? 合作及分工?
选取最佳的的长期对策来解决根本原因。同时也选取 最佳的长期对策来控制根本原因的影响。
需要考虑的问题:
1. 一定是针对根本原 因来制定措施,一个 原因可能有几条措施。 2.对已经明确 的措施进行验 证。 3.措施 尽量具 体化。
四. 8D步骤—D6预防再发对策
需要考虑的问题:
1.确定并执行预 防再发对策,并 应注意持续实施 监控,以确定根 因已经消除。 2.待步入生产阶 段,应即监视纠 正措施之长期效 果,并于必要时 采行补救措施。 3.验证预 防再发对 策有效后, 可以停止 临时措施。
8D方法培训—团队导向问题解决方法

8D过程概述(续)
D7 防止问题再次发生。修改必需的系统包括政策、程序等来防止同一或相似问题的再发生。如果需要对系统改进提出建议,并将学到的技术教训形成文件。D8 表彰小组和个人的贡献完成小组的经验。真诚地表彰小组和个人的贡献。
13
问题发生顾客投诉;发生质量事故;生产不良率骤然升高控制图出现异常;σ变化很大; …….
过程介绍- D1 成立8D小组
33
建立一个团队,团队成员具备相关产品的知识,有解决问题需要的时间和授予的权限,具有所要求的解决问题和实施纠正措施的技术素质,团队必须有一个指定的带头人(公司明确团队队长由副总担任);团队成员由保护与问题密切相关的技术人员或管理人员、相关的质量工程师组成;质量部负责招集和组织团队的活动。
请假人数太多
为什么会发生异常 ?
设定改善目标并形成解决方案
如何改善异常 ?如何控制发生异常的原因 ?
处置:问题发生立即采取公布人员出勤状况的措施
分析原因WHY
治标:解决问题的手段 強化请假制度控制,并跟踪
治本:避免问题再发生加強员工向心力的方法
8D 的本质: 问题解决程序
6
8D课程的目标
完成本课程后,参加本课程的人员能够:描述8D过程的每一个步骤。作为8D成员有效地参加到工作中去。8D帮助提高顾客满意度的目标。8D帮助公司解决重复发生的问题,最终达到在卓越的产品和顾客满意度方面居于行业领先。
相关的QC工具
行动计划
团队宪章
Gantt Chart (Pilot)
……
时间管理
过程介绍- D1 成立8D团队
34
过程介绍- D2 描述问题
为什么要描述问题:要想成为一个有效的问题解决者,必须在采取行动前知道尽可能多的关于问题的描述。D2 阶段以在手边的问题为中心避免低效率:尽可能准确地定义问题作为问题描述的数据库驱动余下的8D过程在D2阶段的任何不清楚和不准确都会导致小组得到错误的原因和采取错误的纠正行动
8D问题改善手法
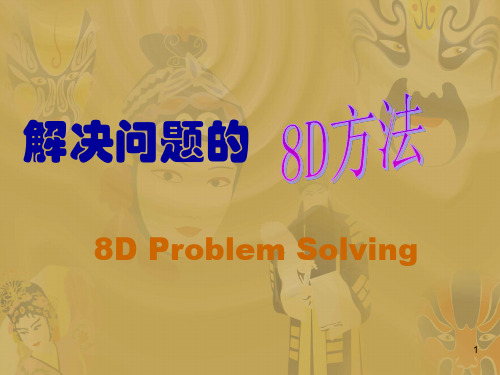
针对选定的纠正措施
修正衡量指标以及 对现行的质量控制 模式进行工程变更
利用三十天的数据 (如SPC或推移图)
来进行确认
建立纠正措施 执行计划
审核改版的 设计FMEA
识别设计或生产过程 中的主要、安全、
关键特性
经过推移图和初次的 测量来停止临时措施
审核改版的 过程FMEA
开发或修正控制计划 以及过程窗体以监控
为一根本原因
列出所有可能的原因 收集适当的资料信息
根据资料显示 确定根本原因
智联培训30
root cause
root cause就是只要解决它就可以解
决失效模式。
使用方法:Why, Why, Why, Why, Why 丰田员工提出“5个为什么”。要找 出问题的根本原因,必须至少依次提 出5个“为什么?”这就象一层层剥洋 葱一样。
造成ALT-5检测器包装工作进度延误,
要求派人处理。
智联培训48
1.成立小组
按问题涉及范围确定小组成员: 责属单位: 生管课、销售课、库管课、品保课 责属人员: 王文新、李小朋、庄子清、张春明
智联培训49
2.描述问题
何时:1999年11月4日; 何人:浙江精密机械厂; 何地:浙江精密机械厂—包装车间; 何事:包装ALT-5检测器时,使用20μMHT
智联培训20
D2:描述问题
目的:
用量化的术语详细说明与该问题有 关的内/外部顾客问题,确认该问题 的人、事、时、地、为何、如何及 多少(5W2H)和程度、频率等。
“什么东西出了什么问题”
方法:
质量风险评定,FMEA分析
智联培训21
关键要点:
收集和组织所有有关数据以说明问题 问题说明是所描述问题的特别有用的数据 的总结 审核现有数据,识别问题、确定范围 细分问题,将复杂问题细分为单个问题 问题定义,找到和顾客所确认问题一致的 说明,“什么东西出了什么问题”,而原 因又未知 风险等级
8D又称团队导向问题解决方法

8D又称团队导向问题解决方法、8D问题求解法(8D Problem Solving)是福特公司处理问题的一种方法,亦适用于制程能力指数低於其应有值时有关问题的解决,它提供了一套符合逻辑的解决问题的方法,同时对於统计制程管制与实际的品质提升架起了一座桥梁。
8D最早是美国福特公司使用的经典质量问题分析手法。
二战期间,美国政府率先采用一种类似8D的流程——“军事标准1520”,又称之为“不合格品的修正行动及部署系统”。
1987年,福特汽车公司首次用书面记录下8D法,在其一份课程手册中这一方法被命名为“团队导向的问题解决法”(Team Oriented Problem Solving)。
当时,福特的动力系统部门正被一些经年累月、反复出现的生产问题搞得焦头烂额,因此其管理层提请福特集团提供指导课程,帮助解决难题。
8D(8 Disciplines)问题解决8步法8D的原名叫做8 Disciplines,意思是8个人人皆知解决问题的固定步骤。
原始是由Ford公司,全球化品质管制及改善的特殊必备方法,之后已成为QS9000/ISO TS16949、福特公司的特殊要求。
凡是做FORD的零件,必须采用8D 作为品质改善的工具,目前有些企业并非 FORD 的供应商或汽车业的合作伙伴,也很喜欢用这个方便而有效的方法解决品质问题,成为一个固定而有共识的标准化问题解决步骤。
Discipline 1. 成立改善小组(Form the Team):由议题之相关人员组成,通常是跨功能性的,说明团队成员间的彼此分工方式或担任的责任与角色。
Discipline 2. 描述问题(Describe the Problem):将问题尽可能量化而清楚地表达,并能解决中长期的问题而不是只有眼前的问题。
Discipline 3. 实施及确认暂时性的对策(Contain the Problem):对于解决 D2 之立即而短期行动,避免问题扩大或持续恶化,包含清库存、缩短PM时间、加派人力等。
解决问题的方法8D手法

★准确的找出根本原因是本步的关键★
评审所有的过程,考虑 所有的变异来源 分析最有可能的根本原 因
采用适当的统计方法对 资料进行分析
应用鱼骨图来了解所有 的可能原因
决定需要什么样的资料 来识别可能的原因为根 本原因
根据资料显示确定根本 原因
列出所有可能的原因
收集适当的资料信息
实际模拟与数据图表的 方式验证根本原因
功解决问题的方法或途径,但它是解决问题的
一个有利于找出根本 原因
强调精确地陈述问题, 并使用合理的思考与统 计工具来详细的描述问 题
管理者要衷心肯定团队 及个人的贡献,予以祝 贺
解决问题的每个步骤的 集合,因而可从其中找 到经提炼的基本信息
8D 的目标
8D的流程--D3:验证和实施临时措施
运用目前已知的信息以及问 题的陈述来采取临时防制措 施 选择、可疑的不良区域 事先验证、成本、是时间 执行
在每一个过程点停止缺失的 产生
确认产品的缺陷以及客户 的不满意已经不存在
确认临时措施采取后是否完 全有效(效果)
执行后的确认
8D的流程--D4:确定根本原因及验证
8D 手 法
解决问题的方法
目录
何谓8D
8D的主要特点
何时使用8D
8D 的目标
8D的流程
案例说明
何谓8D
1、8D 是8 个人人皆知解决问题的固定步骤, 又称团队导向问题解决方法。 2、该方法适用于解决各类可能遇到的简单或 复杂的问题。 3、8D方法就是要建立一个体系,让整个团队 共享信息,努力达成目标。8D本身不提供成
否
识別可能原因
选择最有可能 的原因 最有可能的原因 是否是根本原因
是
D5:选定及验证纠正措施
- 1、下载文档前请自行甄别文档内容的完整性,平台不提供额外的编辑、内容补充、找答案等附加服务。
- 2、"仅部分预览"的文档,不可在线预览部分如存在完整性等问题,可反馈申请退款(可完整预览的文档不适用该条件!)。
- 3、如文档侵犯您的权益,请联系客服反馈,我们会尽快为您处理(人工客服工作时间:9:00-18:30)。
8D又称团队导向问题解决方法,是福特公司处理问题的一种方法,亦适用于制程能力指数低於其应有值时有关问题的解决,它提供了一套符合逻辑的解决问题的方法,同时对於统计制
程管制与实际的产品质量提升架起了一座桥梁。
主要步骤包括:
D1:小组成立
D2:问题说明
D3:实施并验证临时措施
D4:确定并验证根本原因
D5:选择和验证永久纠正措施
D6:实施永久纠正措施
D7:预防再发生
D8:小组祝贺
D1:小组成立目的: 成立一个小组,小组成员具备工艺/产品的知识,有配给的时间并授予了权限,同时应具有所要求的能解决问题和实施纠正措施的技术素质。
小组必须有一个指导和小组长。
关键要点: 成员资格,具备工艺、产品的知识目标分工程序小组建设
D2:问题说明目的: 用量化的术语详细说明与该问题有关的内/外部顾客抱怨,如什么、地点、时间、程度、频率等。
“什么东西出了什么问题” 方法:质量风险评定,FMEA分析关键要点: 收集和组织所有有关数据以说明问题问题说明是所描述问题的特别有用的数据的总结
审核现有数据,识别问题、确定范围细分问题,将复杂问题细分为单个问题问题定义,找到和顾客所确认问题一致的说明,“什么东西出了什么问题”,而原因又未知风险等级
D3:实施并验证临时措施目的: 保证在永久纠正措施实施前,将问题与内外部顾客隔离。
(原为唯一可选步骤,但发展至今都需采用)方法:FMEA、DOE、PPM 关键要点: 评价紧急响应措施找出和选择最佳“临时抑制措施” 决策实施,并作好记录验证(DOE、PPM分析、控制图等)
D4:确定并验证根本原因目的: 用统计工具列出可以用来解释问题起因的所有潜在原因,将问题说明中提到的造成偏差的一系列事件或环境或原因相互隔离测试并确定产生问题的根本原因。
方法:FMEA、PPM、DOE、控制图关键要点: 评估可能原因列表中的每一个原因原因可否使问题排除验证控制计划
D5:选择并验证永久纠正措施目的: 在生产前测试方案,并对方案进行评审以确定所选的校正措施能够解决客户问题,同时对其它过程不会有不良影响。
方法:FMEA 关键要点: 重新审视小组成员资格决策,选择最佳措施重新评估临时措施,如必要重新选择验证管理层承诺执行永久纠正措施控制计划
D6:实施永久纠正措施目的: 制定一个实施永久措施的计划,确定过程控制方法并纳入文件,以确保根本原因的消除。
在生产中应用该措施时应监督其长期效果。
方法:防错、统计控制关键要点: 重新审视小组成员执行永久纠正措施,废除临时措施利用故障的可测量性确认故障已经排除控制计划、工艺文件修改
D7:预防再发生目的: 修改现有的管理系统、操作系统、工作惯例、设计与规程以防止这一问题与所有类似问题重复发生。
关键要点: 选择预防措施验证有效性决策组织、人员、设备、环境、材料、文件重新确定
D8:小组祝贺目的: 承认小组的集体努力,对小组工作进行总结并祝贺。
关键要点: 有选择的保留重要文档流览小组工作,将心得形成文件了解小组对解决问题的集体力量,及对解决问题作出的贡献必要的物质、精神奖励。