后端盖零件成形工序CAE分析及冲压模设计
轴承端盖冲压工艺分析及冲压模具设计

轴承端盖冲压工艺分析及冲压模具设计Summary:轴承端盖冲压工艺追求零件工艺参数计算的精准与设备选择的正确,它设计模具结构对零件伸拉过程中可能产生的拉裂现象进行分析,并提出相应技术解决措施。
本文中就分析了轴承端盖冲压工艺与冲压模具的设计技术要点,对主要零件的设计与与标准件选用、冲压设备的选择与校核进行了深度剖析。
Keys:轴承端盖;冲压工艺;冲压模具设计;标准件选用、冲压设备校核轴承端盖属于手扶拖拉机就中的重要零部件,它在装配后会直接外露表面,且对零件提出了诸多技术要求,例如表面划伤划痕要在0.15mm以内,且不允许出现任何拉裂、起皱、缺料等等缺陷问题。
一般来说轴承端盖的生产批量较大,每年产量超过10000件,所以针对它的冲压工艺与冲压模具设计必须做到技术娴熟、精细到位。
1.轴承端盖工件的基本工艺设计分析图1轴承端盖工件的基本结构示意CAD图如图1为待加工的轴承端盖工件,它的零件制作材料选择了硬度较高的08F钢,针对生产要求追求小批量,它的材料厚度一般设置为1.5mm左右,采用工件CAD图配合优质碳素结构钢进行制作,这其中所采用到的08F钢中含碳质量大约为0.07%~0.20%(低碳钢)。
轴承端盖的抗剪切强度一般控制在220~320MPa之间,它的屈服点也能达到180MPa左右,整体看来材料的焊接性与塑性表现相当好,适合冲裁施工。
从零件外形看来,其对零件的冲压制造需要围绕3步工序完成,它分别包括了落料、拉深与切边,结合3种方案展开级进模加工。
在具体施工中,要基于每道工序展开1套模具配合3套模具施工,有效提升生产效率,保证工件精度到位,最大限度节约搬运半成品时间与财力投入。
在施工过程中要保证模具制作到位,有效降低制造成本,提高生产效率,全面优化工件精度,最后提出最适合开展的轴承端盖冲压模具设计施工方案如下[1]:落料→拉深→切边→复合生产2.轴承端盖工件的重要工艺设计分析轴承端盖工件的重要工艺设计围绕多方面技术要点展开,下文简单谈3点。
端盖冲压工艺与模具设计综述

端盖冲压工艺与模具设计综述引言端盖是一种常见的机械设备零件,广泛应用于汽车、摩托车、工程机械等领域。
而端盖的成型过程中,冲压工艺和模具设计起着至关重要的作用。
本文将对端盖冲压工艺和模具设计进行综述,以帮助读者更全面地了解并掌握相关知识。
一、端盖冲压工艺概述1.1 端盖冲压工艺的定义冲压工艺是一种利用模具对金属材料进行变形、分离和加工的方法,通过冲击或压力使材料产生塑性变形,从而得到所需形状的工件。
端盖冲压工艺即指在冲压工艺中,针对端盖的加工特点进行的工艺处理。
1.2 端盖冲压工艺的优势端盖冲压工艺具有以下优势:•高效率:冲压工艺可以实现连续生产,提高生产效率;•高精度:冲压工艺可以获得高度精确的工件尺寸和形状;•节约材料:冲压工艺可以最大限度地利用材料,减少废料产生;•适应性强:冲压工艺适用于多种材料和复杂形状的加工。
二、端盖模具设计概述2.1 端盖模具设计的意义模具是冲压工艺中的关键设备,直接影响到冲压工艺的质量和效率。
端盖模具设计是为实现端盖冲压工艺提供必要的技术支持,保证工艺能够正常进行。
2.2 端盖模具设计的基本要求端盖模具设计需要满足以下基本要求:•合理性:模具设计应考虑到冲压工艺的特点,采取合理的设计方案,以确保工艺能够稳定、高效地进行;•易制造性:模具设计应考虑到模具的制造和维修难度,尽量采用标准化部件和加工工艺,以降低制造成本;•高可靠性:模具设计应确保模具在长期使用过程中具有较高的可靠性和寿命,减少故障和损坏的可能性。
2.3 端盖模具设计的关键技术端盖模具设计涉及到许多关键技术,包括但不限于以下几个方面:•模具结构设计:确定模具的整体结构,包括顶模、底模、导向机构等;•模具材料选择:选择适合冲压工艺的模具材料,考虑到材料的强度、硬度和耐磨性等;•模具零件设计:设计各个模具零件的形状和尺寸,包括模腔、模板、导向柱等;•模具热处理:对关键部件进行适当的热处理,提高模具的硬度和耐磨性;•模具装配和调试:对完成的模具进行装配和调试,确保模具的正常工作。
浅谈覆盖件的冲压成型CAE分析技术
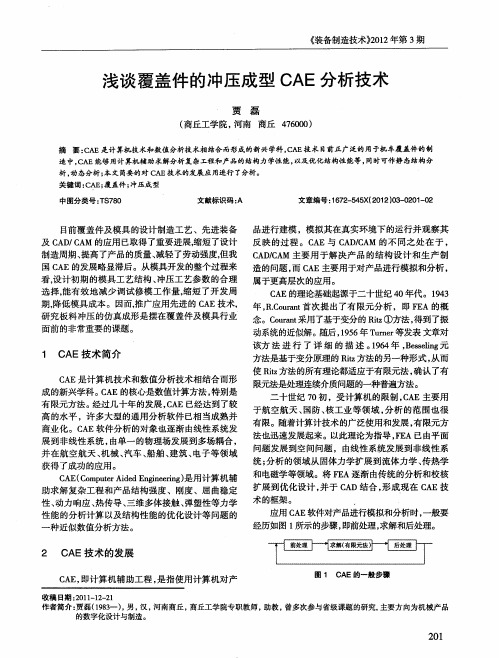
精确的接触摩擦模型, 有限元显式积分算法也开始应 传统 的产 品设计方法是产品设计完之后生产样 用 。2 世纪 8 年代, 0 0 板料冲压有限元数值模拟得 到 板 , 后 进行 测 试 , 主要 缺 陷 是在 已经 进行 大 量投 了迅速的发展。人们在 18 年开发出了一套预测板 然 其 92
面前 的非常 重要 的课 题 。
品进行建模 ,模拟其在真实环境下的运行并 观察其
反映的过程 。C E与 C DC M 的不 同之处 在于 , A A /A C DC M主要用于解决产 品的结构设计 和生产制 A /A 造 的问题 , C E主要用于对产 品进行模拟和分析 , 而 A 属于更高层次的应用。 C E的理论基础起源于二十世纪 4 年代。14 A 0 93 年 ,.or t RC ua 首次提出了有限元分析 ,即 F A的概 n E 念 。C u n采用了基于变分的 Rt①方法 , or t a i z 得到了振 动系统的近似解 。 随后,96 T re 等发表 文章对 15 年 u r n 该方 法 进 行 了详 细 的 描 述 。 94 ,es i 元 16 年 B s l g en 方法是基于变分原理的 Rt方法的另一种形式 , i z 从而 使 Rt方法的所有理论都适应于有限元法 , i z 确认了有 限元法是处理连续介质问题的一种普遍方法。 二十世纪 7 初 ,受计算机的限制 ,A O C E主要用 于航空航天 、 国防、 核工业等领域 , 分析 的范 围也很 有限。随着计算计技术 的广泛使用和发展 , 有限元方 法也迅 速发 展起 来 。以此理论 为 指导 ,E 已由平 面 FA
析。 动态分析 ; 本文 简要 的对 C E技 术的发展应 用进行 了分析。 A
关键词 : A ; 盖件 ; C E覆 冲压 成 型
端盖零件的冲压模具设计
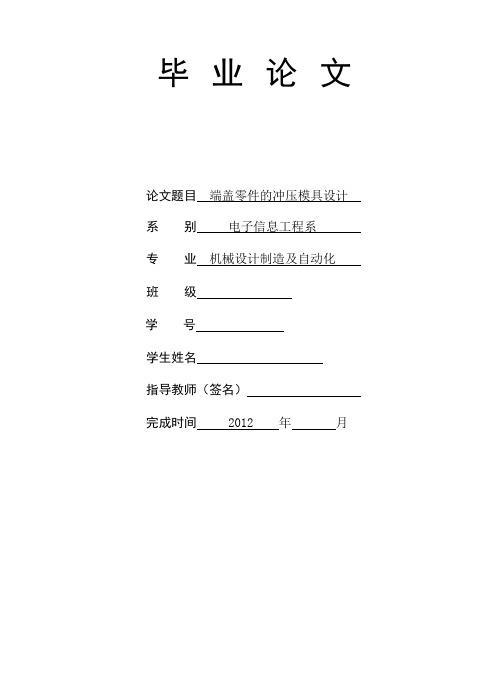
第四章 模具的结构设计..................................................................................................20 4.1 模具结构形式的选择.................................................................................... 20 4.2 模具工作部分尺寸计算................................................................................ 22
第一章 分析零件的工艺性................................................................................................4 1.1 分析零件的工艺性.......................................................................................... 4
端盖冲压工艺及模具设计

端盖冲压工艺及模具设计端盖冲压工艺及模具设计端盖是一种常见的零部件,广泛应用于机械、电子、汽车等领域。
端盖的冲压工艺是一种重要的加工方法,它可以通过模具将金属板材快速成形为具有一定形状和尺寸的端盖。
在端盖冲压过程中,模具是起着重要作用的工具,模具的设计和加工质量是决定产品质量的关键。
一、端盖冲压工艺流程端盖的冲压过程一般分为下料、模具调试、冲压成形、清洁、涂装等几个环节。
1. 下料:下料是冲压工艺的第一步,它是根据产品图纸,按照板材的尺寸进行的。
下料可以采用剪板机、切割机等设备进行,将整张金属板分割成具有所需形状和尺寸的板材。
2. 模具调试:模具调试是为了适应端盖的尺寸和形状要求。
模具调试包括刀模的套装、修正,以及调整模具中央孔的大小等。
调试完成后,需要进行冲压测试,以确保成形品的尺寸、形状、表面质量等达到要求。
3. 冲压成形:冲压成形是将板材置于模具之间,施加一定的压力,使板材在模具的形状下变形,形成所需形状和尺寸的端盖。
在冲压过程中,需要对板材的表面进行保护,以免划伤或磨损。
4. 清洁:清洁是为了去除端盖上的铁锈、污渍等,制备好产品的表面。
清洁过程包括浸泡、刷洗、喷洒清洁剂等。
5. 涂装:涂装是为了提高端盖的容基性,增强其耐用性和耐腐蚀性。
涂装方式可以采用喷涂、浸涂、静电喷涂等。
二、端盖冲压模具设计1. 模具结构设计端盖冲压模具的结构设计要根据端盖的形状和尺寸进行模拟和分析。
具体的设计应该包括切口、冲头、冲模、定位、夹紧等结构。
切口、冲头和冲模是需要特别关注的部分,需要保证其准确度和可靠性。
定位和夹紧结构是为了保证制品的准确度和稳定性。
2. 材料选择模具材料需要具有足够的强度和硬度,以满足生产要求。
现在,常用的模具材料有高速钢、硬质合金、陶瓷、钢、塑料等。
需要注意的是,模具材料的选择要考虑到材料的性能、使用寿命、制造成本等因素。
3. 表面处理模具表面处理是为了提高其耐磨性和耐腐蚀性,延长模具使用寿命的关键。
密封端盖的冲压工艺及模具设计

密封端盖的冲压工艺及模具设计密封端盖是一种用于保护机器内部零部件不受外界影响和污染的重要构件。
它需要具有很高的密封性和机械强度保证,因此其冲压工艺和模具设计十分关键。
本文将就密封端盖的冲压工艺和模具设计进行讨论。
首先,从冲压工艺的角度来看,密封端盖的制作通常需要经过以下几个步骤:原材料准备,钣金冲裁,成形和叠焊。
其中原材料准备是冲压工艺的第一步,需要对板材进行剪切和横向拉伸处理,以使其具有适当的强度和韧性。
随后进行钣金冲裁,将板材按照盖子的形状和尺寸加工成所需的零件。
成形是冲压工艺的核心步骤,通过冲压模具对零件进行弯曲、拉伸等成形工艺,产生各种几何形状。
最后,使用叠焊工艺使所制成的零件焊接在一起,以保证组成的密封端盖拥有极高的可靠性和耐用性。
接下来,从模具设计的角度来看,密封端盖的模具设计主要关注以下两个方面:一是设计模具的结构、尺寸、材料和热处理工艺等;二是选择合适的成形工艺并进行有针对性的模具设计。
在模具结构方面,出于不同的需要和技术水平,模具可以分为开放式、半封闭式和全封闭式模具。
开放式模具结构简单、生产效率高,但制作过程中需要耗费大量人力和物力;半封闭式模具功能较完善,适用范围更广,但模具尺寸要求更高,生产成本也相对较高;全封闭式模具结构复杂,但可以实现高效率的生产效果,适用于大规模量产并且更加稳定的生产。
在设计模具尺寸和材料方面,还需考虑到成形工艺和密封端盖的设计要求。
成形工艺是设计模具时的重要关键,选择合适的成形工艺不仅需要注意模具自身要求,还需要充分考虑到成形工艺对材料的要求和操作难度。
尺寸设计方面,模具尺寸需要考虑到所要生产的密封端盖的尺寸和形状,确保模具能够精确制造符合要求的零件。
模具材料的选取要根据成形工艺和模具操作难度来综合考虑,常见的包括优质合金钢、高耐磨合金钢、硬质合金等。
总之,密封端盖的冲压工艺和模具设计十分关键,需要对制作过程、成形工艺、模具材料和尺寸等方面进行全面考虑和综合分析,以确保产品质量和生产效率的双重保障。
冲压成形cae标准
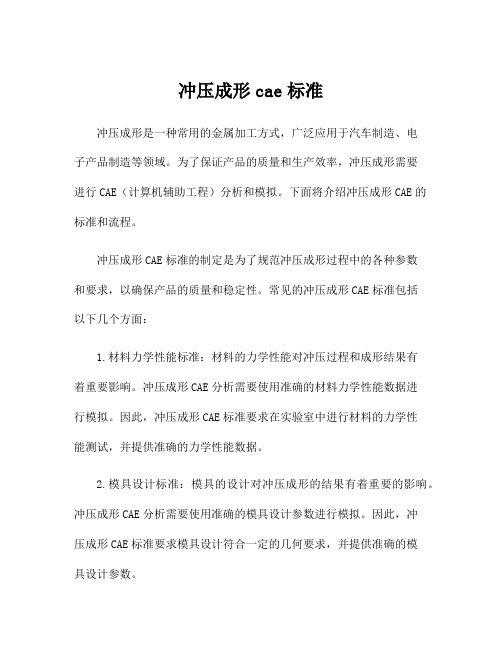
冲压成形cae标准冲压成形是一种常用的金属加工方式,广泛应用于汽车制造、电子产品制造等领域。
为了保证产品的质量和生产效率,冲压成形需要进行CAE(计算机辅助工程)分析和模拟。
下面将介绍冲压成形CAE的标准和流程。
冲压成形CAE标准的制定是为了规范冲压成形过程中的各种参数和要求,以确保产品的质量和稳定性。
常见的冲压成形CAE标准包括以下几个方面:1.材料力学性能标准:材料的力学性能对冲压过程和成形结果有着重要影响。
冲压成形CAE分析需要使用准确的材料力学性能数据进行模拟。
因此,冲压成形CAE标准要求在实验室中进行材料的力学性能测试,并提供准确的力学性能数据。
2.模具设计标准:模具的设计对冲压成形的结果有着重要的影响。
冲压成形CAE分析需要使用准确的模具设计参数进行模拟。
因此,冲压成形CAE标准要求模具设计符合一定的几何要求,并提供准确的模具设计参数。
3.工艺参数标准:冲压成形过程中的工艺参数对成形结果和产品质量有着重要的影响。
冲压成形CAE分析需要使用准确的工艺参数进行模拟。
因此,冲压成形CAE标准要求工艺参数的选择符合一定的规范,并提供准确的工艺参数数据。
冲压成形CAE的流程大致如下:1.准备工作:确定需要进行冲压成形CAE分析的零件和工艺参数。
收集并整理材料的力学性能数据和模具设计参数。
2.建模:使用计算机辅助设计(CAD)软件对需要进行冲压成形CAE分析的零件进行建模。
根据模具设计要求,进行相应的模具设计。
3.材料建模:使用CAE软件对材料的力学性能进行建模。
根据准确的材料力学性能数据,进行相应的材料建模。
4.工艺建模:使用CAE软件对冲压工艺进行建模。
根据准确的工艺参数数据,进行相应的工艺建模。
5.分析和模拟:使用CAE软件对冲压成形过程进行分析和模拟。
根据材料建模和工艺建模的结果,进行相应的分析和模拟。
通过调整参数和优化设计,得到最佳的成形结果。
6.评估和验证:根据分析和模拟的结果,评估冲压成形的效果和质量。
端盖冲压工艺及模具设计说明书

端盖冲压工艺及模具设计说明书一、引言端盖是一种常用的金属制品,广泛应用于机械设备、汽车等领域。
端盖的生产过程中,冲压工艺和模具设计起着至关重要的作用。
本文档旨在介绍端盖的冲压工艺流程和模具的设计要点,以帮助读者了解并应用于实际生产。
二、冲压工艺流程端盖的冲压工艺流程主要包括材料准备、模具设计、冲压操作和零件加工。
1.材料准备材料准备是冲压工艺的第一步。
一般情况下,端盖的制作材料为金属板材,常用的材料有冷轧钢板、不锈钢板等。
在材料准备阶段,需要根据设计要求选择合适的材料,并进行切割、平整等处理。
2.模具设计模具设计是冲压工艺的关键。
模具的设计应根据端盖的形状和尺寸要求进行。
一般情况下,模具应包括上模、下模和导向装置。
上模和下模的设计要考虑到端盖的形状,确定冲模的凹线和凸线,以确保冲压过程中的精度和质量。
3.冲压操作冲压操作是将模具设计的零件在冲压机上进行加工的过程。
在冲压操作中,需要将材料放置在冲床上,并通过冲压动作将材料加工成端盖的形状。
操作时要注意材料的位置和冲压的速度、力度,以避免材料变形或断裂。
4.零件加工零件加工是冲压工艺的最后一步。
在冲压操作完成后,需要对端盖进行修整和整理,以达到要求的尺寸和表面质量。
同时,还需要进行表面处理,如喷涂、镀锌等,以提高端盖的耐腐蚀性能。
三、模具设计要点模具设计是冲压工艺的核心,合理的模具设计可以提高生产效率和产品质量。
以下是一些模具设计的要点:1.模具材料选择模具的材料应选择硬度高、耐磨损、耐腐蚀的材料。
常用的模具材料有合金工具钢、硬质合金等。
选择合适的材料可以延长模具的使用寿命,并提高模具的加工精度和稳定性。
2.模具结构设计模具的结构设计要简单、合理。
需要考虑到冲压力度和速度等因素,确定模具的构造强度,并确保模具的刚性和稳定性。
模具的上模和下模应配合良好,确保冲压过程中的精度和质量。
3.凸模和凹模设计凸模和凹模的设计要根据端盖的形状和尺寸要求进行。
在设计凸模和凹模时,需要考虑到材料的弹性变形和回弹等因素,以确保冲压过程中的形状和尺寸精度。
CAE技术在汽车覆盖件冲压成形中的应用
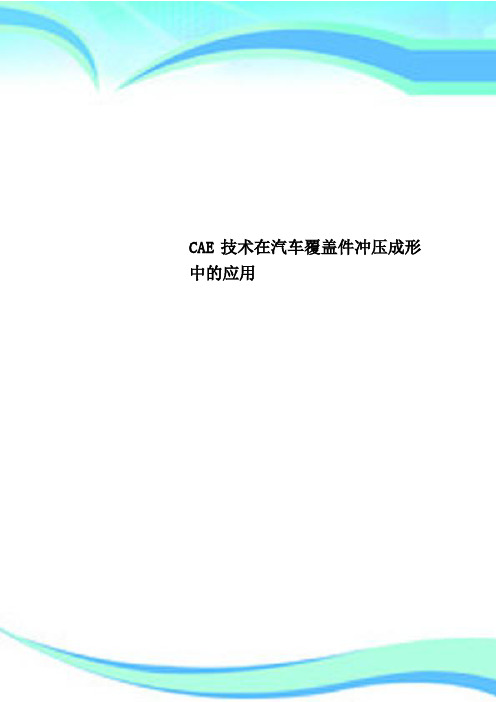
CAE技术在汽车覆盖件冲压成形中的应用————————————————————————————————作者:————————————————————————————————日期:CAE技术在汽车覆盖件冲压成形中的应用2007—1—17 14:13:00 进入论坛摘要:本文简述了CAE技术在汽车覆盖件冲压成形中的应用,通过对拉延工序进行冲压成形模拟分析,提前预知成形缺陷,并采取有效措施,进行工艺参数的调整与优化。
实践证明,分析计算缩短了模具制造周期,减少了模具调试次数,节约了生产成本.关键词:CAE技术;冲压成形;模具调试1 前言汽车覆盖件具有外形尺寸较大,材料比较薄,型面起伏复杂,尺寸精度与表面质量要求较高,在拉伸成形过程中容易出现拉裂、起皱现象。
模具调试过程中需要浪费大量的人力、物力和财力。
近年来随着计算机技术的不断发展,CAE(计算机辅助工程)技术目前已经在各大汽车模具厂广泛用于产品模拟分析、冲压板材成形过程分析。
通过提前对产品可能出现的成形缺陷进行研究,预示汽车覆盖件冲压成形的可行性。
根据理论上的模拟分析结果,提高产品工艺补充设计的合理性,减少模具实际调试次数,近而达到缩短模具制造周期、降低生产调试成本,提高企业生产效能,保证新车型及时投放市场。
本文利用Dynaform分析软件,以公司G项目中的顶盖产品分析为例,介绍CAE技术在汽车覆盖件冲压成形的应用。
2 产品介绍图1所示为我公司最近开发G项目标准短轴距顶盖产品,其材料为SPCC,料厚t=0.9mm,整体来看,具有材料较薄,外形尺寸较大,端部型面极不规则,成形困难,冲压工艺补充以及后续模具设计比较复杂等特点。
图1 顶盖产品数学模型3 CAE分析工作流程CAE分析技术在汽车覆盖件冲压成形应用中的工作流程,见下图2所示。
图2 CAE分析工作流程图4 汽车覆盖件工艺补充设计注意要点(1)选定合适的冲压方向,保证凸模将工件一次拉伸到位,凸模两侧包容角尽可能保持一致,周边进料均匀,尽可能降低拉伸深度,并尽量深度均匀。
冲压成形工艺中的CAE剖析
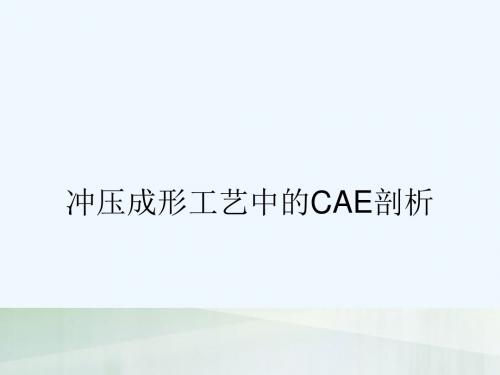
图1:交通工具遮盖件零件成形仿真剖析最后结果 长时期以来,我国交通工具 遮盖件生产模型的预设和制作是在过去经验的基础上,经过生产模型制作后期的反反复 复调整并最后完成的。这种凭经验和试着制做的办法不止使生产模型制作周期过长,并 且成本过高,品质总得不到保障。随着冲压产品的逐层复杂化以及对其精密度要求的不 断增长,树立一套科学的板材成形剖析系统来剖析、预先推测冲压件的变型状况和材料 流动行径并将其作谋生产模型预设时的根据是十分不可缺少的。 因为交通工具遮盖 件尺寸较大,式样复杂,且多为空间自由球面,所以其成形过程牵涉到数量多几何非线 性、材料非线性以及复杂的接触和磨擦等问题。随着非线性理论、有限元剖析办法和计 算机软硬件技术的迅疾进展,车身遮盖件冲压仿真技术渐渐如实验室走向工业实际应用 ,变成国里外交通工
具及其生产模型厂家缩减车身研发和生产模型制作周期的管用工具。 遮盖件成形仿 真剖析可以在各方面为公司的冲压出产供给有力量的支持:在预设办公的早期阶段名声 遮盖件及其生产模型预设、工艺预设的行得通性;在试冲试模阶段,施行故障剖析,解 决实际问题;在批量出产阶段施行欠缺剖析,以改善遮盖件出产品质,同时还可以被用 来调试材料等级,减低生产资本。 以有限应变弹范性有限元办法为基础的CAE技术 经过对交通工具遮盖件成形过程施行计算机摹拟来预先推测某一工艺方案成形的有可能 性以及有可能显露出来的问题,对增长遮盖件生产模型的加工精密度,缩减生产模型制 作周期起着十分关紧的效用。 我企业汽模工程部对板材成形有限元摹拟剖析技术施 行了深化研讨,并将其用于引导生产模型预设和出产实践:1、 板材成形过程摹拟的基 本流程。2、成形
整车项目局部零件剖析后,提出了产品预设问题,使预设部门趁早对产品施行了改进。
摹拟的基本过程。板材的成形摹拟普通需求通过多次反反复复计算能力获得比较满足的 最后结果。3、经过对多个零件的成形过程摹拟,并与出产实际施行相比较,总结概括 CAE软件应用的经验,积累有关的数值,形成总结概括报告陈述,施行评审。图2:板材 成形过程摹拟的基本流程经过上面所说的项目能技术纯熟运用有关的CAE软件,合理确认 冲压工艺参变量,并对摹拟计算最后结果做出准确的诠释,增长了对钣金成形机理的意 识,优化了冲压工艺预设。2、在科学研究和出产中,经过不断扩张CAE的应用领域,增 长了板材成形剖析的正确率,到现在为止正确率已达到70%左右。3、应用摹拟计算的 最后结果引导生产模型的预设和调短期工作,增长了生产模型预设品质、缩减了生产模 型制作周期,减低了成本。4、在对上汽某
手机后盖注射模具设计及CAE分析

Ab ta t B sdo h jc o o l eino G a dMod o n aigtemo i h n er oe s s c: ae ntei et nm udd s f n lf w a dtkn bl p o era vr r n i g U l h e c a
一
次试模 的成功 率 。 用 Mod o 软 件进行 仿 真模 拟分析 。 应 lf w l 分析 了浇 口、 道结 构和 成型 工 艺参 流
数 对填 充 时间 、 熔接 痕 、 穴位 置的影 响 , 气 获得 了最佳 的 浇 口位置 和 流道 结构 , 化模 具 结构 , 优 指
导模 具设 计 . 并就 手机 外 壳常 用材 料 的选 用 、 型 面的创 建 、 分 注射设 备 的选 用、 抽 和推 出机构 设 侧 计 等做 了主要 说 明 , 后采 用 UG Mod zr 最 lwi d模块 构 建 最佳 设计 方案 , 成 2 工 程 图 , a 生 D 完成 手
机后 盖 注塑模 具 结构设 计.
关键 词 : 机后 盖 ; 料 注射 模具 : 手 塑 UG; od o M lf w l
中图分类 号 : H1 8 T 2
文 献标 志码 : A
D s na dC E a ayi o ls cijcinmo l ei n A n ls f at et ud g s p i n o
汽车端盖零件的冲压模具设计

汽车端盖零件的冲压模具设计孔炎;梁辰;赵蒙;聂爱琴【摘要】首先对端盖零件进行工艺分析,确定该零件成形工艺和模具设计的要点,并提出了最佳成形工艺方案。
重点描述了落料拉深冲孔复合模的设计过程,并解决凸凹模的设计,定位精度和冲裁孔拉深变形等问题,为薄壁零件浅拉深成形的模具设计提供参考。
%Automobile end cap is drawing component. The optimum forming project is achieved by determining the form-ing process and the die design based on the analysis to the component. The emphasis is onthe design of the compound die of blanking-drawing-piercing and the solution of punch-die design and positioning accuracy.【期刊名称】《精密成形工程》【年(卷),期】2012(000)006【总页数】3页(P129-131)【关键词】冲压工艺;复合模;凸凹模;模具设计【作者】孔炎;梁辰;赵蒙;聂爱琴【作者单位】合肥工业大学材料科学与工程学院,合肥230009;合肥工业大学材料科学与工程学院,合肥230009;合肥工业大学材料科学与工程学院,合肥230009;合肥工业大学材料科学与工程学院,合肥230009【正文语种】中文【中图分类】TG386.41复合冷冲压工艺是作为一种高效、优质、低耗的加工工艺,在塑性成形加工中占有十分重要的地位[1]。
端盖是汽车中必要的零件,数量多,其形状及尺寸如图1所示。
材料为优质碳素结构钢08号,板材厚度为1.2mm。
根据端盖的形状特征和尺寸结构,此零件属于拉深件,其基本工序有落料、拉深(2次)、冲孔、切边、精整。
试析CAE软件对冲压件结构设计的完善

试析CAE软件对冲压件结构设计的完善在对五金冲压模进行设计的过程中,要按照冲压件的结构,运用相关技术,从而能够设计出冲压件的成形模具,然后在试验的过程中还要对成形的模具进行修改,从而能够使冲压模具达到质量的标准。
在冲压件结构设计优化的过程中,可以运用CAE软件,这种软件运用计算机辅助技术,能够对冲压件结构设计过程中的数据进行运算,从而能够得到最准确的参数,提高冲压件设计的质量。
一、CAE软件的特征CAE软件必须准确的描述物体的形状特征,模具的工作部分都是根據零件的形状来制作的,因此,必须要明确模具的几何形状。
如果零件的几何形状不明确,程序则不能正常的运行,产品零件的几何特征也就不能进行输入。
在进行模具的加工时,必须要对刀具的轨迹进行准确运算,因此,也需要建立准确的几何图形来确定刀具的轨迹。
几何模型的建立是CAE软件使用过程中最核心的问题。
CAE 软件使用必须具备标准化的条件,模具的设计要遵循多元化的设计方案,为了更好的实现CAE软件的使用,减少数据消耗的存储量,在进行CAE系统的建立时,必须确保其设计的标准化,模具的零件也必须采用标准化的形状,模具的结构也必须有统一化的标准,在模具的设计过程中,可以选用标准的模具组合,实现模具零件的标准性。
CAE系统准则的制定是其使用的重要问题,模具准则的设计一般是以表格和线形图来呈现的。
二、冲压件形成的工艺分析(一)冲压件产品的主要特点以汽车的散热器罩为例子,在进行覆盖件的冲压过程中,尽量运用一道工序就可以完成任务,使覆盖件的轮廓清晰,如果覆盖件在两次工艺才成形的话,会导致成形不完整的问题,使覆盖件的质量降低。
当覆盖件的形状确定后,尽可能使覆盖件表面平滑均匀,使各个部位的变形程度能够达成统一,在不同的工序完成时,能够确保各个工序能够相互调整,使工序的状态良好。
(二)冲压件设计的结果和比较分析在传统的方法设计和有限元仿真基础设计出的成形的冲压件的制作工艺中,通过对两种方法设计出的冲压件进行分析,冲压件出现破裂和出现起皱问题的部分几乎是同一个部分,其仿真的结果也几乎一致,因此,如果能够在冲压件刚开始设计的时候,就采用有限元的方法进行模拟,从而能够对成形的冲压件进行分析,就能够提高冲压件开发的质量,使冲压件的设计更加符合规范。
筒盖零件冲压工艺CAE分析及冲压模具设计
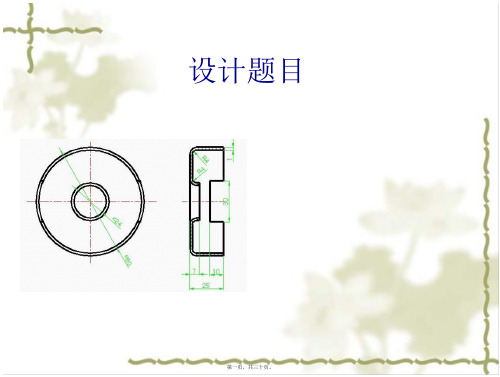
第二十页,共三十页。
第二十一页,共三十页。
拉深模具的设计
· 形状分析 (1)拉深件形状应尽可能简单、对称、避免急剧转角或凸台。 (2)深高度应尽可能小,以减小拉深次数,提高冲件质量。 (3)在保证装配要求的前提下,应允许拉深件侧壁有一定的斜度。 (4)需要多次拉深的零件,在保证必要的表面质量的前提下,应允许内、
立柱间距离(不小于)/mm
270
模柄孔尺寸(直径×深度)/mm
电动机功率/KW
2.2
第十一页,共三十页。
冲孔落料模具的设计
· 确定凸、凹模间隙及制造公差 · 冲孔时凸凹模刃口尺寸计算
· 弹性元件的选取与设计
由于橡胶允许承受的载荷较大,需要安装调整灵活方便。根据工艺 性质和模具结构确定采用较硬橡胶,形状是圆筒形,数量为4块
· 画出排样图
根据以上的内容,可以确定出制件的排样图
第八页,共三十页。
· 毛坯材料利用率的计算 · 材料的剪裁
查阅表1—13冷轧轧制薄钢板规格,拟用1mm×900mm×12000mm热轧钢板。 ①板料横向裁剪 裁板条数 n=900÷108=8(条),余36mm 每条个数 n=1200÷113.5=10(件),余65mm 每板总个数 80 ( 件) ②板料纵向裁剪 裁板条数 n=1200÷108=11(条),余12mm 每条个数 n=900÷113.5=7(件),余105.5mm 每板总个数 77(件) 由于计算可知横裁比纵裁的总个数多,而且送料方便考虑,我们可以采用横 裁。
防止设备超载,公称压力按总压力的1.3倍来计算
第十页,共三十页。
· 压力机的选择
公称压力/kN
250
滑块行程/mm
CAE分析在冲压成型中的应用

CAE分析在冲压成型中的应用
CAE分析在冲压成型中的应用
作者:于波;陈希娥
作者机构:辽宁曙光汽车集团有限公司;辽宁曙光汽车集团有限公司
来源:客车技术
ISSN:1006-6861
年:2008
卷:000
期:001
页码:24-26
页数:3
中图分类:U4
正文语种:chi
关键词:GAE;冲压成形;有限元;数值模拟;旋转拉深件
摘要:介绍了当前冲压数值模拟专用软件DYNAFORM的应用范围及概况,并以典型冲压件为例阐述了DYNAFORM在进行成形有限元模拟的一般步骤,即先由前处理器创建网格模型,再由求解器迭代计算出各个时间步的数据文件,最后由后处理器察看分析各处应力、应变等相关的参数分布.。
基于CAE的某加强件冲压成形工艺分析与方案的确定

【 摘要 】 通过 C E的平 台, A 对某典型汽车 内覆盖加强件的冲压成形工艺方案研 究, 出了一般大 得
型板料 冲压 成形 方案制 定 的方 法。 由于首 工序 成形 体现 整 个成 形 工艺方 案 思路 , 它是 整 个工 艺方案
的核心 。考虑 到装 配 、 制件 表 面质量 、 工成本 等 因素 , 加 重点论 述 了如何借 助 C E平 台实现对 冲压 工 A 艺方案 的 可行 性评 估 , 而在 多个 成形 工 艺方案 中选择 一条 优化 的工 艺路 线 。 从 关键 词 : 冲压 工艺 ; A 装 配 C E;
CHE NG n , I Ho g JANG B n — u ig h a
术
( c a i l e . h n d lc o Meh ncC l g ,h nd 10 1C ia Meh nc p C eg uE et — c a i ol eC e g u6 0 3 ,hn ) aD r e
图 1加 强 件 产 品 图
21方 案( ) . 1 的工艺 路线
落料一 形一 成 冲孔 ( 冲大异形孔和除 D处外 的另外三 圆孔 ) 一
冲 孔 ( D处 的 圆孔 ) 冲
2产品工 艺性分析与 冲压工 艺方案选择
图 1为某车型 内覆盖加强件产 品图的右件 , 左件与其对称 。
该工艺方案 的致命弱点 : 落料线难以调整 到较好状态。 目 从 材料为 S C , 厚为 l 。 由于该零件对车体起 到加强作用 , 前的 C E软件 的一步反求法(n t ) P C料 mm A o es p 算出的落料线精准度仍 e 功能上要求 : 刚性好 , 装配面( ) 边 制造精度高。 然难 以直接用于落料凹模 镶块 轮廓 的加工 ,绝大部分模具制造 该产 品 A、 曰均为翻边 , D凸包处有一圆孔。零件的装配 商最终仍然是依靠钳工试模调试 出凹模轮廓线。该方法周期较 在 要求是 ; C处 为搭接装 配 , A、 D处 圆孔 和另两个 大孔为 定位 装 长 , 且成形件的轮廓与模具的试模状 态关 系较大 , 它会直接影响 配。 因此在成形过程中要保证 A、 和 D处 圆孔及其余 装配孔 到落料线轮廓的制定。 c面 精 度要求 。 该零件从成形角度上来讲 , 以直接成 形。由于 D处 的圆 可 孔 与中部大异形 孔的边距太 近 , 4 m, 约 m 并且该孔 的法 向和大
冲压成形工艺中的CAE分析
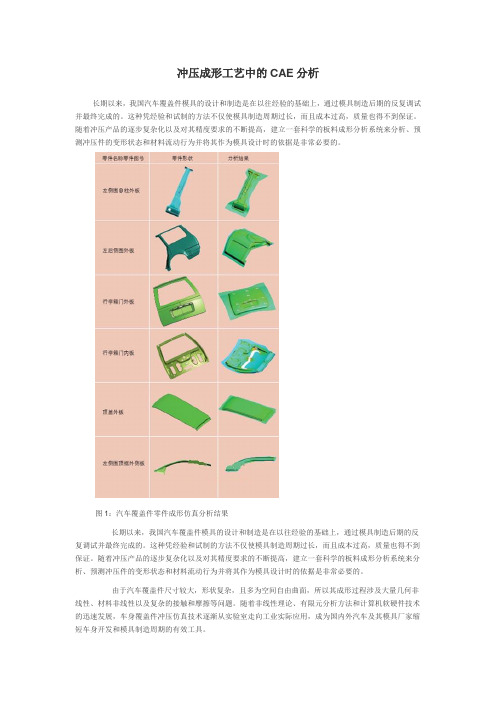
冲压成形工艺中的CAE分析长期以来,我国汽车覆盖件模具的设计和制造是在以往经验的基础上,通过模具制造后期的反复调试并最终完成的。
这种凭经验和试制的方法不仅使模具制造周期过长,而且成本过高,质量也得不到保证。
随着冲压产品的逐步复杂化以及对其精度要求的不断提高,建立一套科学的板料成形分析系统来分析、预测冲压件的变形状态和材料流动行为并将其作为模具设计时的依据是非常必要的。
图1:汽车覆盖件零件成形仿真分析结果长期以来,我国汽车覆盖件模具的设计和制造是在以往经验的基础上,通过模具制造后期的反复调试并最终完成的。
这种凭经验和试制的方法不仅使模具制造周期过长,而且成本过高,质量也得不到保证。
随着冲压产品的逐步复杂化以及对其精度要求的不断提高,建立一套科学的板料成形分析系统来分析、预测冲压件的变形状态和材料流动行为并将其作为模具设计时的依据是非常必要的。
由于汽车覆盖件尺寸较大,形状复杂,且多为空间自由曲面,所以其成形过程涉及大量几何非线性、材料非线性以及复杂的接触和摩擦等问题。
随着非线性理论、有限元分析方法和计算机软硬件技术的迅速发展,车身覆盖件冲压仿真技术逐渐从实验室走向工业实际应用,成为国内外汽车及其模具厂家缩短车身开发和模具制造周期的有效工具。
覆盖件成形仿真分析可以在多方面为企业的冲压生产提供有力的支持:在设计工作的早期阶段评价覆盖件及其模具设计、工艺设计的可行性;在试冲试模阶段,进行故障分析,解决实际问题;在批量生产阶段进行缺陷分析,以改善覆盖件生产质量,同时还可以被用来调整材料等级,降低生产成本。
以有限应变弹塑性有限元方法为基础的CAE技术通过对汽车覆盖件成形过程进行计算机模拟来预测某一工艺方案成形的可能性以及可能出现的问题,对提高覆盖件模具的加工精度,缩短模具制造周期起着非常重要的作用。
我公司汽模工程部对板料成形有限元模拟分析技术进行了深入研究,并将其用于指导模具设计和生产实践:1、板料成形过程模拟的基本流程。
- 1、下载文档前请自行甄别文档内容的完整性,平台不提供额外的编辑、内容补充、找答案等附加服务。
- 2、"仅部分预览"的文档,不可在线预览部分如存在完整性等问题,可反馈申请退款(可完整预览的文档不适用该条件!)。
- 3、如文档侵犯您的权益,请联系客服反馈,我们会尽快为您处理(人工客服工作时间:9:00-18:30)。
2 后端盖零件建模与材料 的选择
21 后端 盖零 件 三维 图 .
应用 ct 建立零件的三维实体模型 , aa i 如图 1 所示。
成形分析 , 单凭经验很难预先估计 , 致使模具设计 正
图 1 后端盖零件三维图
5 结束 语
核 心 的参 数化 标 准零 件库 的设 计 原 理和 结构 。该 方法 不需要 用到各 种复杂 的计算机 编程 语言 , 操作 简单 , 容易 掌握 , 常适 合模 具设 计 等工 程 技术 人 非
员应用 。
・
参
考
文
献
1 】 孙文学等编著.模具设计师 ( 注塑模 国家 二级) 国家 ( 本 文介 绍 了基 于 U X平 台 , GN 以参 数 驱 动 为 [ 李维 ,
【 摘要】 应用 D nFr ya o m对后端盖零件成形工序 进行仿真 , 究发现后端盖零件在成形过程 研
中, 受压边力影响显著 , 预设 的两种方案都不能达到满意效果。为 了解决没有压边力并改
善起 皱情况的问题 , 出拉伸兼整形的参数优化方案。 提 关键词 :y aom c E D nF r ; A 分析 ; 参数优化 ; 模具设计
《 具 制造} 02 第 3 模 2 1年 期
1
中国‘ , - N : W. UO I /t  ̄h J: : WW s t O I t l t. T
.
22 材 料 的选 择 .
从图 2 和图 3 以看 出 , 可 零件成形极 限在安全 区
厚度变 化在 1 1~ . 4 m, . 6 21 m 在允许 范围 内, 以 5 7 所 对零件进行 冲压 C E A 分析 , 首先要确定其使用的 内 , 对其进行精确 材料 。在 D n Fr y aom的材 料库 中 , 多数是 国外 的牌 理论上其成形是可行 的。在此基础上 , 大
ba k od r fre a d mp o ig w ike c n io rbe po oe rwig n s a i g ln h le o c n i rvn rn l o dt n p o lm,rp s d d a n a d h pn i
p r m e e so i iai n. a a tr ptm z to
【 bt c】 p l a o f ya o nt a cvr a s o i rcs s u t n Suy A s at A p ctno D nFr o er r oe pn r n poes i l i ,t r i i m h e fm g m ao d
f u d t a h e r c v r p ns d r g t e  ̄r n r c s . o r s e d e e fc p a e t 0 n h t t e r a o e a u i h n mi g p o e s C mp e s d e g fe t a p r n . P e e t s h me a n t c i v t e aif c o y f c . S i o d r o ov wi o t r s t wo c e c n o a h e e h s tsa t r ef t o n r e t s l e e t u h
为模具的合理设计 目前 , 板料 成形 在航 空 、 宇航 、 汽车 、 造船 、 电器 、 研究后端盖零件成形可行性方案 , 五金等工业部 门应用 广泛 , 板料成形过程是一个大挠 提供了依据。 度、 大变形 的塑性成形过程 , 涉及金属板在拉 伸和弯 曲的复杂应力状 态下塑性 流动 、 塑性 强化 , 及其 引起
淮安仕泰隆国际工业博览城
全 球招 商热 线 :5 8 2 9 9 01- 699 9 7
S T L
网址 : w. lpc m ww s e . t o
后 端 盖 零件 成 形 工序 C E分 析 及 冲压模 设计 A
叶丹 茜, 何俊 豪
中国矿业大学机 电学院( 江苏徐 州 2 10 ) 2 0 8
确性也难 以评价 , 问题只有在模具加工以后才能暴露 出来 , 给模具调试造成极大困难 , 甚至导致模具报废 。
所 以本文应用 D nF r yaom软件 , 以后端盖 为例 , 对
后端盖零件成形工序进行 C E A 分析 , 针对预先 的两种
方案 的不 足 , 提出拉伸兼整 形 的参数优化方案 , 对整
职业资格培训教程 ) 】 中国劳动社会保 障出版社 ,09 【. M 20.
【] 李金 友 , 2 张祥 林 编著.压铸 模 3 D设计 与计 算指 导【 .化 M】
学工业 出版社 ,0 0 21.
作者 : 孙文学, 17 年生 , 男,9 1 工程 师, 事产品设 从 计及模 具 C DC M技 术方 面 的研 究 工作 。 A /A ①
中图 分类 号 :P 9 .; G 8 . T 3 1 T 3 52 7 文献标 识 码 : B 文 章编 号 :0 2 O — 10 1 2 1一 10 — 0
Fo mi g P o e s CAE a y i n t mp n r n r c s An l ssa d S a ig Di sg fCo e r s eDe i n o v rPa t
Ke r s Dy a o m ; AE a a y i ; a a t r p i z t n; i e i n y wo d : n F r C n l ss p r me e so t mia i d e d sg o
1 引 言
个工艺流程进行 了数值模拟 , 并对其进行 回弹分析 。