转向器基础知识中英文
汽车转向系统英语词汇 汽车英语词汇
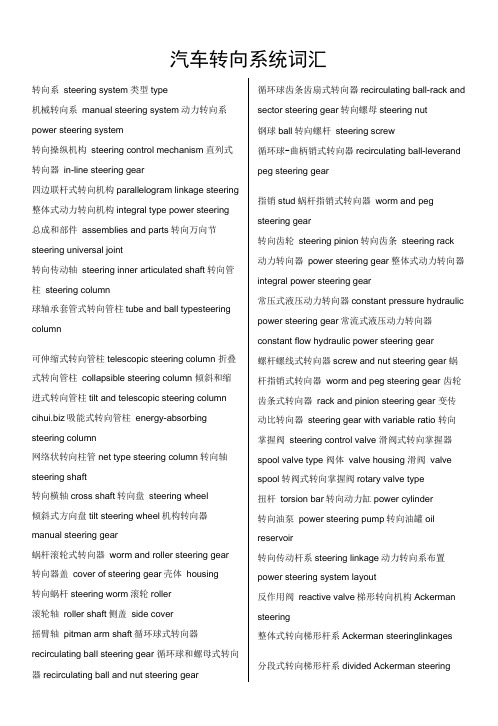
汽车转向系统词汇转向系steering system类型type机械转向系manual steering system动力转向系power steering system转向操纵机构steering control mechanism直列式转向器in-line steering gear四边联杆式转向机构parallelogram linkage steering 整体式动力转向机构integral type power steering 总成和部件assemblies and parts转向万向节steering universal joint转向传动轴steering inner articulated shaft转向管柱steering column球轴承套管式转向管柱tube and ball typesteering column可伸缩式转向管柱telescopic steering column 折叠式转向管柱collapsible steering column 倾斜和缩进式转向管柱tilt and telescopic steering column 吸能式转向管柱energy-absorbing steering column网络状转向柱管net type steering column转向轴steering shaft转向横轴cross shaft转向盘steering wheel倾斜式方向盘tilt steering wheel机构转向器manual steering gear蜗杆滚轮式转向器worm and roller steering gear 转向器盖cover of steering gear壳体housing转向蜗杆steering worm滚轮roller滚轮轴roller shaft侧盖side cover摇臂轴pitman arm shaft循环球式转向器recirculating ball steering gear 循环球和螺母式转向器recirculating ball and nut steering gear 循环球齿条齿扇式转向器recirculating ball-rack and sector steering gear转向螺母steering nut钢球ball转向螺杆steering screw循环球-曲柄销式转向器recirculating ball-leverand peg steering gear指销stud蜗杆指销式转向器worm and peg steering gear转向齿轮steering pinion转向齿条steering rack动力转向器power steering gear整体式动力转向器integral power steering gear常压式液压动力转向器constant pressure hydraulic power steering gear常流式液压动力转向器constant flow hydraulic power steering gear螺杆螺线式转向器screw and nut steering gear 蜗杆指销式转向器worm and peg steering gear 齿轮齿条式转向器rack and pinion steering gear 变传动比转向器steering gear with variable ratio 转向掌握阀steering control valve 滑阀式转向掌握器spool valve type 阀体valve housing 滑阀valve spool转阀式转向掌握阀rotary valve type扭杆torsion bar转向动力缸power cylinder转向油泵power steering pump转向油罐oil reservoir转向传动杆系steering linkage动力转向系布置power steering system layout反作用阀reactive valve梯形转向机构Ackerman steering整体式转向梯形杆系Ackerman steeringlinkages分段式转向梯形杆系divided Ackerman steeringlinkage中间转向杆intermediate steering rod转向摇臂pitman arm转向直拉杆steering drag link 中间转向联杆center steering linkages端部螺塞end plug球头销ball stud球头座ball cup压缩弹簧compression spring梯形机构tie rod linkage梯形臂tie rod arm转向横拉杆steering tie rod接头socket横拉杆端接头ti© rod end分段式梯形机构split tie rod type tie rod linkage摆臂swing arm动力转向power steering气压式动力转向air-power steering液压式动力转向hydraulic power steering 液压常流式动力转向hydraulic constant flow type power steering液压储能式动力转向hydraulic accumulator power steering慢速转向slow steering快速转向fast steering (quick steering)过度转向oversteering转向缺乏understeering转向系刚度steering system stiffness方向盘自由行程free play of steering wheel转向器转动力矩rotating torque of steering gear 转向力矩steering moment转向阻力矩steering resisting torque 转向力steering force转向传动比steering gear ratio (steering ratioO 恒定转向传动比constant ratio steering 可变转向传动比variable ratio steering 转向系角传动比steering system angle ratio 转向器角传动比steering gear angle ratio 转向传动机构角传动比steering linkage angle ratio转向器传动效率steering gear efficiency 正效率forward efficiency 逆效率reverse efficiency转向器扭转刚度torsional stiffness of steering gear转向盘总圈数total number of steering wheel turns转向器总圈数total turns of steering gear转向器传动间隙steering gear clearance摇臂轴最大转角max.rotating angle of pitman arm shaft转向摇臂最大摆角max. Swing angle of steering pitman arm转向器反驱动力矩reverse rotating torque of steering gear转向器最大输出扭矩steering gear max. Output torque最大工作压力max. Working pressure 额定工作压力rated working pressure 转向油泵理论排量theoretical displacement ofpump限制流量limited flow转向掌握阀预开隙pre-opened play of steering control valve转向掌握阀全开隙totally -opened play of steering control valve转向掌握阀内泄漏量internal leakage in steering control valve转向掌握阀压力降pressure loss in steeringcontrol valve转向器角传动比特性steering gear angle ratio characteristic转向器传动间隙特性steering gear clearance characteristic转向器传动效率特性steering gear efficiency characteristic转向力特性steering force characteristic 动力转向系灵敏度特性power steering system response characteristic转向掌握阀压力降特性steeringcontrol valve pressure loss characteristic 前桥front axle工字梁I-beam双工字梁twin I-beam非驱动桥dead axle转向节steering knuckle挂车转向装置steering system of trailer中心主销式转向装置central king pin type steering system无主销转向装置no king pin type steering system 全杆式转向装置all linkage type steering system 球销式转向节ball and socket steering knuckle 转向节止推轴承steering knuckle thrust bearing 前轮轴front wheel spindle转向盘轴steering spindle 转向节轴knuckle spindle转向节臂steering knuckle arm(转向节)主销knuckle pin(King pin)反拳式前桥reverse elliott axle反拳式转向节reverse elliott steering knuckle 叉式前桥elliott type axle叉式转向节elliott steering knuckle。
转向系英语词汇

转向系英语词汇摆臂 swing arm变传动比转向器 steering gear with variable ratio侧盖 side cover常流式液压动力转向器 constant flow hydraulic power steering gear常压式液压动力转向器 constant pressure hydraulic power steering gear 齿轮齿条式转向器 rack and pinion steering gear动力转向 power steering动力转向器 power steering stgear动力转向系 power steering system动力转向系布置 power steering system layout端部螺塞 end plug阀体 valve housing反作用阀 reactive valve分段式梯形机构 split tie rod type tie rod linkage分段式转向梯形杆系 divided ackerman steering linkage钢球 ball滚轮 roller滚轮轴 roller shaft过度转向 oversteering横拉杆端接头 tie rod end滑阀 valve spool滑阀式转向控制器 spool valve type机构转向器 manual steering gear机械转向系 manual steering system接头 socket壳体 housing可伸缩式转向管柱 telescopic steering column快速转向 fast steering (quick steering)类型 type螺杆螺线式转向器 screw and nut steering gear慢速转向 slow steeirng扭杆 torsion bar气压式动力转向 air-power steering倾斜和缩进式转向管柱 tilt and telescopic steering column 倾斜式方向盘 tilt steering wheel球头销 ball stud球头座 ball cup球轴承套管式转向管柱 tube and ball type steering column四边联杆式转向机构 parallelogram linkage steering梯形臂 tie rod arm梯形机构 tie rod linkage梯形转向机构 ackerman steering网络状转向柱管 net type steering column蜗杆滚轮式转向器 worm and roller steering gear蜗杆指销式转向器 worm and peg steering gear蜗杆指销式转向器 worm and peg steering gear吸能式转向管柱 energy-absorbing steering column循环球齿条齿扇式转向器 recirculating ball-rack and sector steering gear 循环球和螺母式转向器 recirculating ball and nut steering gear循环球-曲柄销式转向器 recirculating ball-lever and peg steering gear循环球式转向器 recirculating ball steering gear压缩弹簧 compression spring摇臂轴 pitman arm shaft液压常流式动力转向 hydraulic constant flow type power steering液压储能式动力转向 hydraulic accumulator power steering液压式动力转向 hydraulic power steerig折叠式转向管柱 collapsible steering column整体式动力转向机构 integral type power steering 整体式动力转向器 integral power steering gear 整体式转向梯形杆系 ackerman steering linkdage 直列式转向器 in-line steering gear指销 stud中间转向杆 intermediate steering rod中间转向联杆 center steering linkdage转阀式转向控制阀 rotary valve type转向不足 understeering转向操纵机构 steering control mechanism转向齿轮 steering pinion转向齿条 steering rack转向传动杆系 steering linkage转向传动轴 steering inner articulated shaft转向动力缸 power cylinder转向管柱 steering colum转向横拉杆 steering tie rod转向横轴 cross shaft转向控制阀 steering control valve转向力矩 steering mometn转向螺杆 steering screw转向螺母 steering nut转向盘 steering wheel转向盘自由行程 free play of steering wheel转向器盖 cover of steering gear转向器转动力矩 rotating torque of steering gear 转向万向节 steering universal joint转向蜗杆 steering worm转向系 steering system转向系刚度 steering system stiffness转向摇臂 pitman arm转向油泵 power steerig pump转向油罐 oil reservoir转向直拉杆 steering drag link转向轴 steering shaft转向阻力矩 steering resisting torque 总成和部件 assemblies and part。
中英文文献翻译—转向器的简单介绍
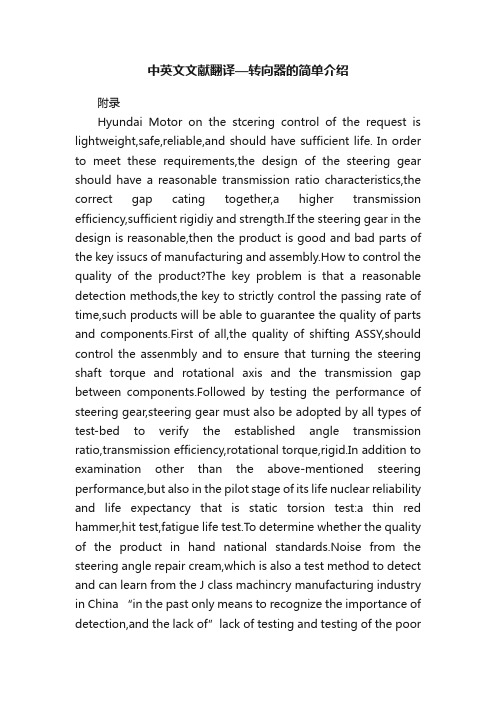
中英文文献翻译—转向器的简单介绍附录Hyundai Motor on the stcering control of the request is lightweight,safe,reliable,and should have sufficient life. In order to meet these requirements,the design of the steering gear should have a reasonable transmission ratio characteristics,the correct gap cating together,a higher transmission efficiency,sufficient rigidiy and strength.If the steering gear in the design is reasonable,then the product is good and bad parts of the key issucs of manufacturing and assembly.How to control the quality of the product?The key problem is that a reasonable detection methods,the key to strictly control the passing rate of time,such products will be able to guarantee the quality of parts and components.First of all,the quality of shifting ASSY,should control the assenmbly and to ensure that turning the steering shaft torque and rotational axis and the transmission gap between components.Followed by testing the performance of steering gear,steering gear must also be adopted by all types of test-bed to verify the established angle transmission ratio,transmission efficiency,rotational torque,rigid.In addition to examination other than the above-mentioned steering performance,but also in the pilot stage of its life nuclear reliability and life expectancy that is static torsion test:a thin red hammer,hit test,fatigue life test.To determine whether the quality of the product in hand national standards.Noise from the steering angle repair cream,which is also a test method to detect and can learn from the J class machincry manufacturing industry in China “in the past only means to recognize the importance of detection,and the lack of”lack of testing and testing of the poorlaw awareness.So have some of the parts is a qualified products I materials,and assembly of products from the pilot test proved to be defective,or:The test can verify the quality of products and design for the steering gear (1) the accuracy of parts of the foot only, finish second,two-phase the location of the elite“Measuring the content of L steering shaf t loaded journal bearings.Department feet inch accuracy and smoothness,anti-worm or worm-inch accuracy.smoothness and surface hardness and magnetic---for testing;steering vertical axis arm journal dimensional accuracy and smoothness, the worm wheel roller bearing of the journal center hole distance,wheel bearing and the journal” hole angle from the Chinese side,the block size,finish and degree of asymmetry;circulating ball tooth-type radial fan,big-law length,journal hardness,the magnetic;browser to Min Xuan cochlear aperture wheel size precision,smoothness,tooth surface roughness,intermediate thick teech,tooth,tooth degree ofasymmetry; ball rolling circle diameter,smooth,cylindrical roller Road”degree of accuracy and bias,raccway adjacent pitch error,cumulative error section of grass lines and sub-racj section from Rolling Road Center,rack section Road center line and the roll of injustice;carburizing layer thickness,hardn ess’magnetic flaw detection;ahift steering shaft shell aperture,roughness,different degree of heart;shift towards vertical axis aperture arm flying finish,different degree of heart;chaos and stecring shaft steering arm hole down the center distance,steering shaft-hole axes and steering arm hole down the center line of the non-verticality.(2) parts of cleanliness.Detection of the site is turning-browser shell surface and the surface parts.Detection method is to use cleaning fluid to clean parts,and then the cleaning fluid with impurities,and vacuum membranc leaching;further 120 weeks of petrol industrial solvents the menbranc will be washed with inpurities.To be volatile after the membranc cleaning fluid,together with the impurities from weighing with the magne cellophane packets are sorted in the iron impurities said the weight of a scrap-iro, The iron filings and then 40 times on the microscope with a disability in most dogs measured particle size.(3)assembly of the leakage.. Does not allow any leakage of the phenomenon of steering.Because of internal lubricants in the steering gear is used to turn parts lubricated friction pair,and if as a result of damage caused by leakng seals,lubrication will be affected; resulting in increased friction and wear parts and reduce the life span of steering gera;transminssion efficiency at the same time will lower.The use of conventional vibration and temperature 40 under the conditions of inspection,the shell and shell cap shaft oil scal joints as well as whether the spill.,and water to observe whether there are leakages.(4) after a good tune stecring assembly should check the technical requirements flexible and comfortable when turning the steering wheel,there is no axial gap I turn the steering wheel of the total value of the number required to turn around a few cars in line with the original request.Steering gear shife, also known as machine,machine,machine direction.which is steering the most important parts. Its role ie to increase the spread to turn steering wheel and transmission mechanism to change the direction of power transfer.Hydraulic Steering Hydraulic steering vehicles are windelyused in marine hydraulicsteering and rudder.Drivers can be used through its ability to manipulate smaller shift power to achieve greater control and performance of safe,reliable,flexible manipulation,light.The manipulation of steering is hydraulic,that is in the steering column and steering wheel there is no mechanical connection between the steering gear is between the fuel tank and steering hydraulic pipes or hoses link.When turning the steering wheel,steering wheel rotation in accordance with the relative proportion of transport fuel,the fuel tank directly into the corresponding control side,while the other side of the oil back to tank.BZZ steering is a switch-type full-hydraulic steering valve with the following characteristics:the elimination of mechanical linkage device,the host can reduce costs,provide a reliable,lightweight structures,manipulation of a flexible lightweight,safe,reliable,and can be very small continuous torque stepless control of rotation, provided to the control loop,as well as a wide range of host size choice,able to shift and a variety of pumps and hydraulic supply system.Steering by the structure can be divided into many types.History,there have been many forms of steering,there is currently more commonly used rack and pinion,worm means crank pins,recycling the ball-rack fan gear type,recycling the ball crank pins means,such as worm-type wheel.The second,fourth,respectively, is the first,the third form of the deformation,and the worm wheel is even more rare type.If the form in accordance with assistance,but also can be divided into mechanical(no help),and power-style(with help) two types of power steering which can be divided into pressure andmotivation,hydraulic-power, Electric power-type,electro-hydraulic power types of blocks.It is a rack and pinion of steering one of the most common.The basic structure is a pair of mutually meshing rack and pinon.Pinon steering drive shaft rotates, rack linear motion would be done. In some cases,directly driven by the rack cross-bar,you can make of steering wheel shift. So,this is one of the most simple steering. Its advantage is simple structure,low-cost,steering sensitivity,small size,can be directly cross-link.In widely used vehicle.It is a worm for the active parts,crank pin for the steering gear follower.Worm has a trapezoidal thread,referring to a finger-shaped pin with tapered bearings in the crank bearings,the crank shaft and the shift into one arm.Shifted through steering wheel rotating worm,helical worm embedded in the cone-shaped slot means the marketing side of the rotation,the crank shaft and the shift into one arm.Shifted through steering wheel rotating worm,helical worm embedded in the cone-shaped slot means the marketing side of the rotation,the side rocker shaft to do around the shifted are movement,thereby stimulating and steering crank arm swing down and then turning to make shift transmission wheel deflection.This steering is usually used to turn power on a larger truck.Circulating ball-type:This device is turned by the gear mechanism from the steering wheel to slow down the rotation of power,so that the rotation of steering wheel movement into rotary movement of the turbine worm,ball screw and nut holding the ball engagement,which Ball screw linear motion into rotary movement,with the fan-shaoed nut meshing gears,linear motion into rotary movement,with the fan-shaped nut meshing gears,linear motion into rotary movement,with the fan-shapednut meshing gears,linear motion into rotary movement again to shake the rod arm,link arm moving again so that even the bar and cross bar to do a straight-line movement to change the wheels direction.This is a classical institutions,most modern cars no longer have to use,but the way was the latest by the application of power steering device.It is equivalent to the principle use of nuts and bolts in the rotation process of relative movement,and in between the thread and thrend the ball into the folder to reduce the resistance,all the ball,both connected in a closed loop of the spiral curve rolling ball club is named after the cycle.Hydraulic rack and pinion steering gear is relative to the case of rack and pinion steering gear machinery, mainly to increase the steering pump,steering oiler,steering pineline, steering valve,steering components,suan as fuel tanks,with a view to improve the pilot hand,the purpose of increasing power steering of the steering device.After 10 years of internal development,has become a mature R&D and manufacturing technology manufacturers have Yubei Koyo Steering Gear Co.Ltd.and other enterprises.With the rapid development of automobile industry,as well as for comfort,safety and continuous improvement in performance,steering systems are also changing with the advance of technology.For the time being,electric power steering systems is turning the forefront of the industry rescarch projects,in accordance with its distribution of the form of string can be divided into power,gear Power,power rack,power bar,the form of electro-hydraulic power. Ago in some sci-fi movies of the unmanned aircraft can occur,such as unmanned acrial vehicle is now a reality,steering systems are moving in the direction of the development of more advanced,such as rescarch anddevelopment from Japan JTEKT advanced by the steer-by-wire systems.In this paper,choice-bassed recycling the ball GX1608A gear-steering rack as a research topic,its main contents are: knowledge of automotive steering gear,ball-type steering gear cycle of the main paramenters and design choices.Design also includes the shift rocker shaft,involute spline,fan gear shaft and screw shaft design and verification.According to its own independent study completed by the steering shaft and screw shaft rocker design and verification,in other parts of the network,as well as through the school library to collect relevant information and fax to the future,in the papers have used information the mark.The design has been through a total of about 16 Chinese and foreign-related literature,and learn from the relevant parts of which the essence of the final design of the times.Because of its limited ability to learn and,I urge teachers and experts have pointed out that less than one.中文现代汽车对转向器的要求是操纵轻便,安全、可靠、,并应具有足够的使用寿命。
重型卡车转向系统-中英文版-2015-11
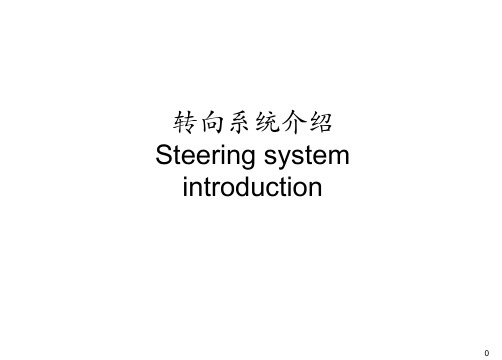
J 进油槽 radial groove K 进油槽 radial groove L 回油槽 return oil control grooves M 回油槽 return oil control grooves N 轴向槽 axial grooves O 轴向槽 axial grooves P 回油槽 return oil control grooves
>6.0
22.2-26.2 170±10
6479 7618 42
4
转向液压原理 Steering hydraulic principle
直线行驶 Linear driving 在发动机的驱动下转向泵向转向机提供所需的压力油。因 此,助力油在转向泵的作用下被从油壶吸出经过转向机后再 流回油壶。 The pump is driven by the engine to provide the required pressure oil to the steering gear. Therefore, the oil in the steering pump under the action of being sucked out from the oil reservoir after steering and returned to the oil reservoir .
转向液压原理 Steering hydraulic principle
左转方向 Left direction 当方向盘向左运动时,活塞将向左移动,在右侧动力腔内将建立 起压力。 When the steering wheel moves to the left, the piston will move to the left, and the pressure will be established in the right chamber. 此时转阀逆时针方向转动,油液通过打开的进油槽(J)进入到轴向 槽(O),然后达到右侧的动力腔。 At this point the rotation of the valve counter clockwise, the oil through the oil into the radial groove (J) into the axial grooves (O), and then to the right side of the power chamber. 左侧动力腔排出的油液经过滚珠丝杠以及打开的回油槽(L)流 回到转阀的回油槽(P),然后通过转阀及蜗杆上的中心孔流回到 油壶。 Left side power discharge cavity of oil through the ball screw and open back to the return oil control grooves (L) to flow back to the rotary valve return oil control grooves (P), and then through the turn back to the oiler center hole of the valve and the oil reservoir . J 进油槽 radial groove K 进油槽 radial groove L 回油槽 return oil control grooves M 回油槽 return oil control grooves N 轴向槽 axial grooves O 轴向槽 axial grooves P 回油槽 return oil control grooves
《汽车专业英语》Chapter 9 steering system

In the recirculating ball steering gear, the wormshaft is the input shaft. The wormshaft connects to the steering column in such a way that a mechanic can remove the steering gear or steering column independently of one another. The sector shaft (also called the pitman shaft) is like the output shaft of the steering gear. The main parts of the steering gear are the balls, ball nut, and the gear teeth on the ball nut.
转向横拉杆的长度同主销间的距离不相等,就可保证各前 轮以期望的角度旋转。转向横拉杆长度的设置要保证转向 横拉杆与转向节臂的连接点位于主销到后桥前端汽车中心 线上的点所形成的假想连线上。
Qu.4: List the main types of Steering Box. Qu.4: List the main types of Steering Box.
在循环球式转向器中,转向螺杆是输入轴。转向螺杆连接 着转向柱,这样修理工就可独立拆卸转向器或转向柱。齿 扇轴(也叫摇臂轴)相当于转向器的输出轴.转向器的主 要部件是钢球,球螺母和球螺母上的齿.
As the wormshaft turns, the balls move the ball nut up and down along the wormshaft. This turns the sector shaft, since the sector teeth mesh with the ball nut teeth. The sector shaft is connected through steering linkage to the front wheels.
转向器基础知识中英文

转向器基础知识中英文转向器基本原理介绍Fundamental Principles of Steering Gear 目录Contents一、汽车液压动力转向系统的组成I . Hydraulic power steering system二、循环球动力转向器基本原理II . Recirculating Ball Steering Gear三、齿轮齿条转向器基本原理III .R&P Power Steering Gear四、转向系统发展的先进技术IV . Advanced T echnology of Steering System五、我厂的技术优势及特点V . Our Advantages for developing Technology六、先进驾驶辅助系统ADAS Advanced Driver Assistant System汽车液压转向系统的组成Hydraulic Power Steering System汽车转向系统的组成Steering System汽车的跑、转、停是它的基本性能,他们中的一个重要机能则由转向装置来承担。
Basic capability of vehicle is to run, turn or stop. Turning device assumes this responsibility.机械转向系统Manual Steering Gear 动力转向系统Power Steering Gear汽车液压动力转向系统的组成Hydraulic Power Steering System 方向盘及管柱、中间轴Steering Wheel, Column and Intermediate Shaft转向器及摇臂Steering Gear and Pitman Arm 油泵Pump 油罐Reservoir 油管Pipe支架及其它附件Bracket and Other Accessories 拉杆系统Linkage 主销及车轮Pin and Wheels1-方向盘Steering Wheel 2-中间传动轴Intermediate Shaft 3-进油管Inlet Pipe4-回油管Outlet Pipe 5-油罐Reservoir 6-油泵Pump 7-转向器Steering Gear8-摇臂Pitman Arm 泵与油管组件Pump and Pipe Assembly 油泵Pump高、低压油管High and low Pressure Pipes 油箱Reservoir 回油管Outlet Pipe 油泵Pump循环油管Recycle Pipes 进油管Inlet Pipe R&P式油压动力转向器R&P Power Steering Gear转阀式循环球动力转向器基本原理Recirculating Ball Power Steering Gear转阀式动力转向器简介General Overview转向器是构成汽车转向系统的主要部件之一,由于特殊的作用,在性能和可靠性方面要求苛刻。
转向英文名词
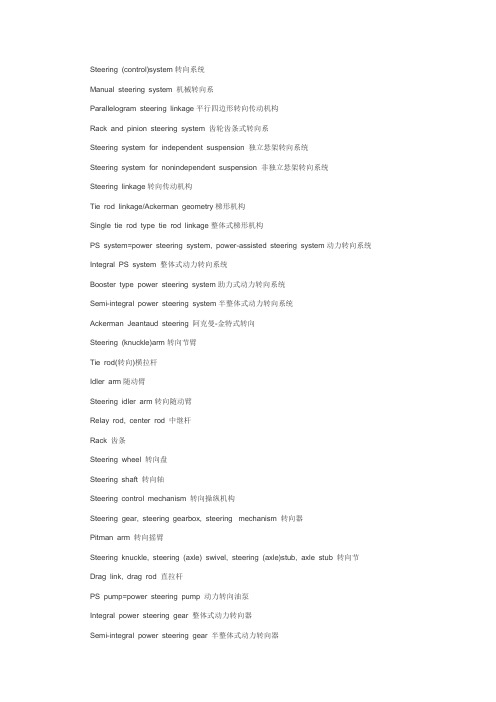
Steering (control)system转向系统Manual steering system 机械转向系Parallelogram steering linkage平行四边形转向传动机构Rack and pinion steering system 齿轮齿条式转向系Steering system for independent suspension 独立悬架转向系统Steering system for nonindependent suspension 非独立悬架转向系统Steering linkage转向传动机构Tie rod linkage/Ackerman geometry梯形机构Single tie rod type tie rod linkage整体式梯形机构PS system=power steering system, power-assisted steering system动力转向系统Integral PS system 整体式动力转向系统Booster type power steering system助力式动力转向系统Semi-integral power steering system半整体式动力转向系统Ackerman Jeantaud steering 阿克曼-金特式转向Steering (knuckle)arm转向节臂Tie rod(转向)横拉杆Idler arm随动臂Steering idler arm转向随动臂Relay rod, center rod 中继杆Rack 齿条Steering wheel 转向盘Steering shaft 转向轴Steering control mechanism 转向操纵机构Steering gear, steering gearbox, steering mechanism 转向器Pitman arm 转向摇臂Steering knuckle, steering (axle) swivel, steering (axle)stub, axle stub 转向节Drag link, drag rod 直拉杆PS pump=power steering pump 动力转向油泵Integral power steering gear 整体式动力转向器Power steering gear 动力转向器Power cylinder转向动力缸转向传动机构Steering Linkage(Mechanism) Parallelogram steering linkage 平行四边形转向传动机构Rack and pinion steering linkage 齿轮齿条式转向传动机构Boll joint 球节Steering (knuckle) arm 转向节臂Steering gear 转向器Pitman arm, drop arm, steering gear arm, steering lever转向节臂Inner tie rod 内横拉杆Inner tie rod end joint 横拉杆内接头Idler arm随动臂Bracket(所动臂)支架Mounting bracket 安装支架Relay rod, center link, centre link, connecting rod 中继杆Adjusting sleeve, adjusting tube(横拉杆)调节臂Outer tie rod 外横拉杆Outer tie rod end joint 横拉杆外接头Steering knuckle转向节Tie rod, tie bar, track横拉杆Steering tie rod 转向横拉杆Tie rod clamp 横拉杆夹Grease fitting 滑脂嘴Bearing 轴承Ball cup, ball socket, ball cap球碗,球头座Ball stud ,ball pivot, ball pin 球头消Full-ball stud 全球式球头销Joint housing 接头壳Compression spring 压缩弹簧Steering shock absorber 转向减振器转向操纵机构Steering Control(Mechanism) Intermediate shaft 中间轴Dust cover 防尘罩Universal joint 万向节Steering universal joint 转向万向节Steering column 转向管柱Upper column cover 管柱上罩Lower column cover 管柱下罩Combination switch 组合开关Steering wheel 转向盘4-spoke wheel 四辐条转向盘3-spoke wheel 三辐条转向盘Rim 盘缘,盘辐Spoke 辐条Ignition/starter switch 点火/起动机开关Air bag module 安全气囊组件Wheel pad with SRC airbag带安全气囊的转向盘盖Steering wheel pad, wheel pad 转向盘盖Upper bracket 上支架Key cylinder 钥匙筒 Column tube 管柱管Clamp 固定夹Bushing 衬套Main shaft 主轴Steering inner articulated shaft 转向传动轴可倾斜式转向管柱Tilt Steering Column Manual tilt手动倾斜Power tile 电动倾斜Upper column tube 上管柱管Lower column tube 下管柱管Main shaft (转向轴)主轴Pawl stopper 棘爪止动器Tilt lever retainer 倾斜度调整手柄保持板Tension spring 拉簧Tilt lever 倾斜度调整手柄Pawl wheel, ratchet wheel 棘轮Steering bolt 转向螺栓Compression spring 压紧弹簧Tilt switch 倾斜开关Tilt motor 倾斜电动机Tilt ECU 倾斜电子控制模块Unlock warning switch 锁开启警告开关Control gear assembly 控制机构总成车轮定位Wheel AlignmentSteering axis 转向轴线SAI=steering axis inclination 转向轴线内倾Kingpin inclination 主销内倾Vertical axis 垂线Central plane of the wheel 车轮中心平面Camber angle 车轮外倾角Positive camber angle 车轮正外倾角Kingpin offset, steering offset, scrub radius, swiveling offset, wheel offset 主销偏置距,转向轴线偏置距Positive scrub radius 主销正偏置距Kingpin caster angle 主销后倾角Caster offset, castor offset 主销后倾距Positive caster offset 主销正后倾距Toe in, wheel toe, toe 前束Toe out 后束,负前束基本转向器Standard Steering GearCam and lever steering gear, cam and peg steering gear 蜗杆指销式转向器Worm and roller steering gear, Gemmer steering gear蜗杆滚轮式转向器Rack and pinion steering gear 齿轮齿条式转向器Recirculating ball steering gear, ball and nut steering gear, ball nut type steering gear循环球式转向器Recirculating ball-rack and sector steering gear循环球齿扇式转向器Steering shaft 转向轴Steering worm 转向蜗杆Sector gear 齿扇Pitman arm shaft, sector shaft 摇臂轴,齿扇轴Stud, peg 指销Lever 曲柄Sector shaft adjusting screw 摇臂轴调整螺钉Roller 滚轮Pinion 小齿轮Ball guide 钢球导管Steering nut, ball nut 转向螺母Steel ball, ball 钢球Pitman arm 转向摇臂Drop arm, steering arm 转向摇臂齿轮齿条式转向器Rack and Pinion Steering GearLock nut 锁止螺母Dust cover 防尘罩Pinion shaft 小齿轮轴Steering gear input shaft 转向器输入轴Oil seal 油封Adjusting screw 调节螺母Plug 罗塞Bearing 轴承Steering rack 转向齿条Rack guide 齿条导块Rack support, rack retainer 齿条支撑Rack slipper 齿条滑履Steering gear housing 转向器壳Rack housing 齿条衬套Tie rod 横拉杆Rack boot 齿条防尘套Inner tie rod end 横拉杆内接头outer tie rod end 横拉杆外接头Tab washer, claw washer舌片止动垫圈齿轮齿条式动力转向器Rack and Pinion Power Steering Gear O-ring O形圈Oil seal 油封Spacer 隔套Bearing guide nut 轴承导向螺母Control valve 控制阀Valve/pinion assembly 阀/小齿轮总成Union seat 接头座Turn pressure tube 转向压力油泵Pressure line 压力油管Control valve housing 控制阀体Conical spring 锥形弹簧垫Cylinder end stopper 动力缸端止动器齿轮齿条式动力转向系Power Rack and Pinion Steering System Rotary valve type control valve 转阀式转向控制阀Rotary distribution cross-section 旋转分配器横断面Oil supply unit 供油装置Vane pump 滑片泵Power cylinder 动力油缸Rack housing 齿条壳体Steering pinion 转向齿轮Steering rack 转向齿条Torsion bar 扭杆Steering spindle, steering gear input shaft 转向输入轴Control port 控制口Control valve 控制阀,转向控制阀Rotary valve type control valve转阀控制阀Rotary distributor 旋转分配器Control valve housing 控制阀体Return line 回油管Oil reservoir, reservoir tank 储油罐Pressure and flow-limiting valve 压力和流量控制阀Pressure line 压力油管Vane-type pump 滑片泵Cylinder piston 油缸活塞循环球式转向器Recirculating Ball Steering Gear Ball guide 钢球导管Adjuster bolt 调节螺栓Preload bolt 预紧调节器Worm shaft 蜗杆轴Upper worm bearing 蜗杆上轴承Lock nut 锁紧螺母Adjuster plug 调节螺塞Worm bearing adjusterPitman arm 转向摇臂Worm thrust bearing 蜗杆止推轴承Lower worm bearing 蜗杆下轴承Ball nut 转向螺母Pitman shaft 摇臂轴循环球式动力转向器(转阀式)Power Recirculating Ball Steering Gear Steering limit valve stem 转向限制阀杆Drain plug 放油螺塞Dust cover 防尘罩Steering limit valve ball 转向限制阀钢球Ball nut 转向螺母,球螺母Hole for ball return guide, hole for guide 钢球导管孔Plug 螺塞Pressure relief [limiting]valve stem 卸[限]压阀杆Valve body 阀体Dust seal 防尘密封圈Retaining ring 卡环,挡圈Seal 油封Valve nut 阀螺母Ball bearing 球轴承Rotary valve assembly 转阀总成Side cover 侧盖Steering gear housing 转向器壳体Bearing roller 轴承滚子Sector gear 齿扇,扇形齿轮Adjusting screw 调整螺钉Pin hole 销孔Left-turn outlet 左转向出油口Valve outer element 阀门外侧元件Right- turn outlet 右转向出油口Fluid under pressure inlet 压力油入口Steering stop spline 转向限制器花键Return slot 回油槽口Return to pump 流回液压泵Spline to steering shaft 接转向轴花键Valve inner element 阀门内侧元件Torsion bar 扭杆循环球式动力转向器系Power Recirculating Ball Steering System Rotary valve type control valve 转阀式转向控制阀Rotary distribution cross-section 旋转分配器横断面Oil supply unit 供油装置Vane pump 滑片泵Housing 壳体Piston 活塞Ball nut转向螺母Torsion bar 扭杆Splined to steering shaft 接转向轴的花键Control valve/ worm 控制阀/蜗杆Rotary valve 转阀Sector shaft 齿扇轴Pressure limiting valve 限[卸]压阀Replenishing valve 供油阀,补给阀Inlet slot 进油槽口Return slot 回油槽口Axial groove 回油槽口Vane-type pump叶片泵Flow-limiting valve 流量限制阀Oil reservoir 储油罐车速感应式动力转向及转向油泵怠速提升装置Speed-Sensitive Power steering and Idle-Up De vice for Power Steering PumpSpeed sensitive power steering, power steering with speed-dependent assistance, variable poIdle-up device for power steering pump 转向油泵怠速提升装置Oil pump 液压泵Solenoid(acting)valve 电磁阀Electrohydraulic converter 电液转换器Steering housing 转向器壳体ECM=electronic control module电子控制模块Electronic speedometer 电子车速表Battery 蓄电池Air flow meter 空气流量计Throttle 节气门Surge tank 稳压阀Air control valve 空气控制阀滑片式转向油[液压]泵Vane Power Steering Pump Pump cover 泵盖O-ring O 形密封圈Cam ring 凸轮盘Vane 叶片Cam case 凸轮盘外壳Pressure hose connector[fitting]压力(油)软管接头Flow control valve 流量控制阀Spring 弹簧Outlet port 出口Pump body 泵体Seal 油封Spline to rotor 接转子的花键Pulley 带轮Pulley shaft 带轮轴Piston rod 活塞杆Plunger 柱塞Insulator 绝缘垫Snap ring 卡环Fluid inlet port 油液入口Dowel pin 定位销Crossover hole 穿过孔Spline to pulley shaft 装带轮轴的花键Rotor 转子Suction hose connector[fitting]进[吸]油软管接头Fluid passage 油液通道Fluid chamber 油液腔机械式四轮转向Mechanical 4WS*systemLayout 布置图Rear steering gear 后转向器Center shaft 中间轴Front steering gear 前转向器Stroke rod 行程拉杆Steering gear housing 转向器壳体Offset pinion gear 偏心小齿轮Offset shaft 偏心轴Internal gear 内齿轮Slider 滑块Guide 导轨Steering gear cover 转向器盖电子控制四轮转向系Electronically Controlled 4WS*System Layout 布置图Rear steering actuator 后转向执行器Main rear wheel angle sensor 后轮转角主传感器Sub rear wheel angle sensor 后轮转角副传感器Vehicle speed sensor 车速传感器Front main steering angle sensor 前主转向角传感器Rear wheel sensor 后轮传感器Rear sub steering angle sensor 后转向角副传感器Rear steering actuator 后转向执行器Rear steering gear 后转向器Rear main steering angle sensor 后转向角主传感器4WS control unit 四轮转向控制模块Front sub steering angle sensor 前副转向角传感器Steering shaft screw 转向轴螺杆Stator 定子Actuator housing 执行器壳体Return spring 回位弹簧Commutator 换向器Brush 电刷Rotor 转子Recirculating ball screw 循环球螺杆Magnetic rotor 电磁转子Integrated 集成电路MR element=magneto-resistive element 磁阻元件Tapered shaft 锥形轴Rear actuator spring cover 后执行器弹簧盖电子动力转向Electronic Power Steering System Interface circuit 接口电路Pinion shaft 小齿轮轴Steering sensor 转向传感器Torque sensor 扭矩传感器Rack 齿条Recirculating ball nut 循环球螺母Ball screw 球面螺杆Helical gear 斜齿圆柱齿轮Motor 电动机Electric assist steering gear 电动转向器Control unit 控制模块Battery 蓄电池VSS= vehicle speed sensor 车速传感器Torsion bar 扭杆Spiral groove 螺旋槽Guide pin 导向槽Wing 翼板Slider 滑动套Pinion gear 小齿轮Transformer 互感器Ball screw section 球面螺杆部电动液压式齿轮齿条式转向器Electric Hydraulic Power and Pinion Steering Gear Electric oil pump assembly 电动油[液]泵总成Return line 回油管Pressure line 压力油管Wire 线束Mount bracket 安装支架。
汽车英语04转向系统

It converts the rotational motion of the steering wheel into the linear motion needed to turn the wheels[3]. It provides a gear reduction,making it easier to turn the wheels.
知识拓展
什么事EPS
ESP是英文electronic stability program的缩写,中 文译成“电子稳定程序”。这一系统通常是支持ABS及ASR (驱动防滑系统,又称牵引力控制系统)的功能的。它通 过对从各传感器传来的车辆行驶状态信息进行分析,然后 向ABS、ASR发出纠偏指令,来帮助车辆维持动态平衡。ESP 可以使车辆在各种状况下保持最佳的稳定性,在转向过度 (over-steering)或转向不足(under-steering)的情形下效 果更加明显。
Recirculating-ball steering(Fig.4.3)is used on many trucks and SUVs today.The linkage that turns the wheels is slightly different than on a rack-and-pinion system. Essentially,the steering gear consists of two parts,a worm on the end of the steering shaft and a pitman arm shaft on which there is a gear sector[1].A nut rides on the worm gear and a sector,is engaged with this nut.
汽车转向系统英语词汇
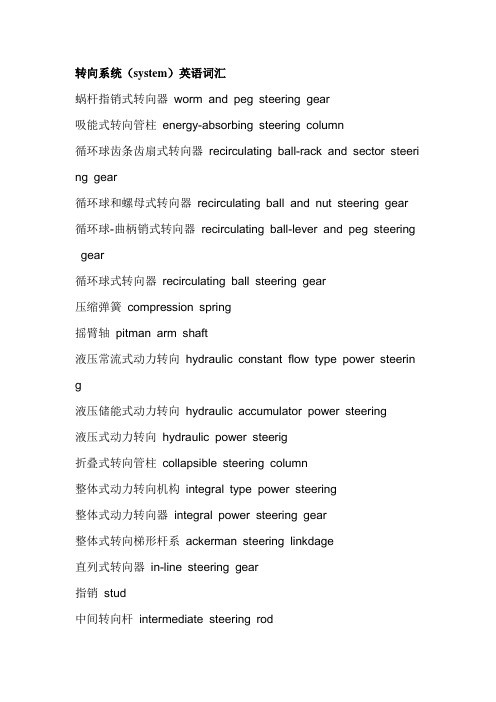
转向系统(system)英语词汇蜗杆指销式转向器worm and peg steering gear吸能式转向管柱energy-absorbing steering column循环球齿条齿扇式转向器recirculating ball-rack and sector steeri ng gear循环球和螺母式转向器recirculating ball and nut steering gear 循环球-曲柄销式转向器recirculating ball-lever and peg steering gear循环球式转向器recirculating ball steering gear压缩弹簧compression spring摇臂轴pitman arm shaft液压常流式动力转向hydraulic constant flow type power steerin g液压储能式动力转向hydraulic accumulator power steering液压式动力转向hydraulic power steerig折叠式转向管柱collapsible steering column整体式动力转向机构integral type power steering整体式动力转向器integral power steering gear整体式转向梯形杆系ackerman steering linkdage直列式转向器in-line steering gear指销stud中间转向杆intermediate steering rod中间转向联杆center steering linkdage转阀式转向控制阀rotary valve type转向不足understeering转向操纵机构steering control mechanism转向齿轮steering pinion转向齿条steering rack转向传动杆系steering linkage转向传动轴steering inner articulated shaft转向动力缸power cylinder转向管柱steering column转向横拉杆steering tie rod转向横轴cross shaft转向控制阀steering control valve转向力矩steering mometn转向螺杆steering screw转向螺母steering nut转向盘steering wheel转向盘自由行程free play of steering wheel转向器盖cover of steering gear转向器转动力矩rotating torque of steering gear 转向万向节steering universal joint转向蜗杆steering worm转向系steering system转向系刚度steering system stiffness转向摇臂pitman arm转向油泵power steerig pump转向油罐oil reservoir转向直拉杆steering drag link转向轴steering shaft转向阻力矩steering resisting torque总成和部件assemblies and parts摆臂swing arm变传动比转向器steering gear with variable ratio侧盖side cover常流式液压动力转向器constant flow hydraulic power steering g ear常压式液压动力转向器constant pressure hydraulic power steeri ng gear齿轮齿条式转向器rack and pinion steering gear动力转向power steering动力转向器power steering stgear动力转向系power steering system动力转向系布置power steering system layout端部螺塞end plug阀体valve housing反作用阀reactive valve分段式梯形机构split tie rod type tie rod linkage分段式转向梯形杆系divided ackerman steering linkage 钢球ball滚轮roller滚轮轴roller shaft过度转向oversteering横拉杆端接头tie rod end滑阀valve spool滑阀式转向控制器spool valve type机构转向器manual steering gear机械转向系manual steering system接头socket壳体housing可伸缩式转向管柱telescopic steering column快速转向fast steering (quick steering)类型type螺杆螺线式转向器screw and nut steering gear慢速转向slow steeirng扭杆torsion bar气压式动力转向air-power steering倾斜和缩进式转向管柱tilt and telescopic steering column 倾斜式方向盘tilt steering wheel球头销ball stud球头座ball cup球轴承套管式转向管柱tube and ball type steering column 四边联杆式转向机构parallelogram linkage steering梯形臂tie rod arm梯形机构tie rod linkage梯形转向机构ackerman steering网络状转向柱管net type steering column蜗杆滚轮式转向器worm and roller steering gear蜗杆指销式转向器worm and peg steering gear。
齿轮齿条转向器英语规范

目录一零部件常用语 (1)二常用材料 (2)三热处理用语 (3)四公差符号与术语 (4)4.1 公差符号 (4)4.2 公差术语 (5)五标准件 (6)一零部件常用语齿轮pinion齿条rack壳体housing阀壳体valve housing阀套valve sleeve转向轴input shaft扭杆torsion bar液压缸cylinder tube液压油hydraulic oil防护套bellow/cowl活塞piston调整体support yoke调整体衬垫liner调整弹簧spring adjuster调整螺塞yoke plug/ adjuster plug中部球头节组件IBJ(inner ball joint)外部球头节组件OBJ(outer ball joint)大卡箍clamp小卡箍clip六角螺母hex nut支承套rack bush球轴承ball bearing滚针轴承needle bearing下端压紧螺塞end plug安装胶套mounting rubber安装座套silent blockO形圈O ring锁紧薄螺母special nut销子pin二常用材料防护套:1.聚烯烃弹性体POE=polyolefin elastomer(EPDM橡胶和聚丙烯混合物,即>EPDM+PP<)2.聚烯烃热塑弹性体TEO=Themoplastic Elastomer,Olefinic3.山都平Santoprene 103-40阀套密封环、活塞密封环: 1.聚四氟乙烯PTFE=Polytetrafluoroethylene[poli.tetrə.fluərə.eθili:n]O形圈:1.HNBR 2.NBR调整体:1.粉末冶金sintered iron[sintəd] SMF3030-JIS Z 25502. ZL107调整体衬垫:1. 复合材料钢板+铜基+PTFE涂层compound material:steel+copper+PTFE转向轴、阀套:S45C安装胶套:EPDM安装座套:1. 20 steel +NR2. 20 steel +NR/BR3. 20 steel +NR/SBR支承套:1.聚酯弹性体Polyester Elastomer2.HT250齿轮:1. 42CrMo 用于高频淬火2. SCM420(相当于20CrMo)用于渗碳淬火调整弹簧:VDCrSi活塞:20Cr大卡箍:1.不锈钢304 UNS S3042.SAE 1008/1010 hot-dip galvanized coating 热电镀涂层壳体:1. ZL1072. A13800 with 10% max silicon permissible齿条:1.S45C2.S45SC 屈服强度:560Mpa min,抗拉强度:814Mpa min液压缸:1. 20中部球头节组件: 内拉杆:40Cr内球壳:20外部球头接组件:外球壳:35球销:42CrMo防护罩:CR球碗:聚甲醛POM=Acetal resin, Polyoxymethylene三热处理用语carburized case depth 渗碳硬化层深carburizing 渗碳nitriding 氮化处理overheating 过热air cooling 空冷oil cooling 油冷hardening and tempering 调质induction hardening 感应淬火metallographic structure 金相组织shot blasting 喷丸(处理)sand blasting 喷砂(处理)grit blasting 喷钢砂(处理)spectrum analysis光谱分析inclusion 夹杂物stress relief 应力释放carbon content 含碳量temper brittleness 回火脆性die casting 压力铸造gravity casting 重力铸造mechanical properties 机械特性blueing 发蓝normalizing正火normalized steel 正火钢hardening/quenching 淬火hardened steel 淬火钢tempering 回火tempered steel 回火钢artificial aging 人工时效natural aging 自然时效四公差符号与术语4.1 公差符号以下符号来源于ISO 1101-1983:4.2 公差术语基本尺寸basic size实际尺寸actual size极限尺寸limits size最大极限尺寸maximum limit of size 最小极限尺寸minimum limit of size 偏差deviation上偏差upper deviation下偏差lower deviation公差tolerance公差带tolerance zone零线zero line标准公差standard tolerance公差等级tolerance grade基本偏差fundamental deviation配合fit间隙配合clearance fit过盈interference过盈配合interference fit过渡配合transition fit基孔制hole-basic system of fits基轴制shaft-basic system of fits间隙clearance螺纹thread外螺纹external thread内螺纹internal thread大径major diameter小径minor diameter螺距pitch of thread牙型form of thread旋向direction of turning右旋螺纹right-hand thread左旋螺纹left-hand thread头数number of thread导程lead粗牙coarse thread细牙fine thread螺旋线helix(line螺旋角helix angle螺栓bolt六角头螺栓hexagon head bolt六角头螺栓(全螺纹)hexagon head bolt-full thread 螺钉screw螺柱stud螺母screw nut垫片washer弹簧spring销pin圆柱销round pin圆锥销taper pin开口销cotter pin, split键key平键flat key半圆键half round key, woodruff key轴承bearing滚动轴承rolling bearing滑动轴承sliding bearing向心铀承radial bearing密封装置sealing equipment锁紧装置locking equipment扳手wrenches千斤顶Jack不合格品non-conforming products。
转向系统--中英文翻译
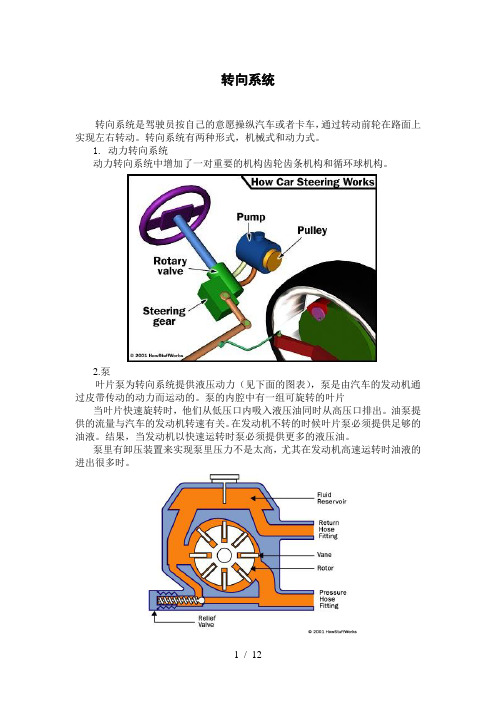
转向系统转向系统是驾驶员按自己的意愿操纵汽车或者卡车,通过转动前轮在路面上实现左右转动。
转向系统有两种形式,机械式和动力式。
1.动力转向系统动力转向系统中增加了一对重要的机构齿轮齿条机构和循环球机构。
2.泵叶片泵为转向系统提供液压动力(见下面的图表),泵是由汽车的发动机通过皮带传动的动力而运动的。
泵的内腔中有一组可旋转的叶片当叶片快速旋转时,他们从低压口内吸入液压油同时从高压口排出。
油泵提供的流量与汽车的发动机转速有关。
在发动机不转的时候叶片泵必须提供足够的油液。
结果,当发动机以快速运转时泵必须提供更多的液压油。
泵里有卸压装置来实现泵里压力不是太高,尤其在发动机高速运转时油液的进出很多时。
3. 滑阀驾驶员通过操纵动力转向系统来实现车轮的转向(仅仅当开始转动时)。
当驾驶员没有施加压力时,转向系统是不工作的。
滑阀时驾驶员在操纵中有路感。
旋转的关键是转向轴。
转向轴是一个金属杆,当对它施加扭矩时开始运动。
当驾驶员旋转方向盘时,转向轴传递扭矩到车轮,使车轮旋转。
驾驶员为了使车轮旋转的角度增大就需要有更大的扭矩。
转向阀关键是一根扭力杆。
扭力杆是细金属杆,在传递扭矩是运动。
扭力杆的顶端被连接到方向盘,而且它的底部被连接到齿轮或蜗杆上( 转轮子) ,因此,它传递的力矩跟驾驶员操纵方向盘所施加的扭矩相等。
为了是车轮的转动角度增大就需要增加扭矩。
从输入轴输入的扭矩部分进入伺服阀。
并且它连接到扭力杆的最底端。
扭力杆的底端连接到伺服阀的外部。
在其他的汽车转向中扭力杆也从转向传动装置输出, 连接到其他的转向齿轮或蜗杆上。
当扭力杆旋转时它是从伺服阀的内部向外部传递动力。
由于伺服阀的内部也连接在转向轴 ( 或直接到方向盘) ,在伺服阀的内部和外部之间的力矩大小以来于驾驶员作用于方向盘多少转力矩。
在伺服阀中的转动方向来自于方向盘的转动。
当方向盘没有被旋转的时候,两边的液体是相通的内部压力相当。
但是当它从一个位置旋转到另一个位置时,内部两端的压力将会改变。
GM中国转向器培训资料(英文)

GM China Engineering TrainingIntroduction toSTEERING SYSTEMSRack and Pinion Steering SystemsSection 5Participant’s Guide5. RACK AND PINION STEERING SYSTEM5.1 OverviewDelphi Saginaw’s first application for a rack and pinion gear was for Gran Prix of America in 1972. this gear was designed to fit into miniature race car and had a ratio of around 3:1. This was a manual gear only.The second application was for the AMC pacer. There were a power and a manual version. The gear had some very unique design features as well as some manufacturing processes. The pinion housing and the rack and cylinder assembly were injected together to set gear preloads and there was no adjustments on the gear. It had an automatic wear take up system. It also had formed pinion teeth created by a rolling process. These until were buit from 1975 to 1979.In 1976 Saginaw began building a more conventional manual gear for the Chevette. The gear was a refinement of an Opel design already in production. In later yearsof this program a power gear was added.In 1977-1979 Saginaw added additional power rack and pinion gear volume, doning a Chrysler gear for the OMNI and HORIZON in 1977, adding a SAAB application in1978, and adding GM “X” car in 1979. while these gears were more conventional than the Pacer gear, they were of a one piece aluminum housing design. This design had a number of process issues and was moved away from the 1982 models. The two piece design was introduced for this year model. It had a steel cylinder tube linked to an aluminum housing. This change was a cost saving with no mass penalty.From 1984 on a variety of applications have been added. A number of improvements and features have been added over the life of Saginaw gear programs including cast iron tophat, quiet valve, high temperature seals, hollow rack, variable ratio steering, SSS(Speed Sensitive Steering). Magnasteer, and a variety of process improvements. Today, rack and pinion systems are used on all front wheel drive models and some rear-wheel drive models.5.1.1. Basic Principle of Rack and Pinion GearFigure 5.1-1 shows the basic principle of rack and pinion steering. The steering shaft is attached to the pinion in the steering gear. The pinion, therefore, rotates with the steering wheel. Gear teeth on the pinion mesh with gear teeth on the rack. The rotating pinion moves the rack from side-to-side. The lateral action of the rack pushes and pulls the tie rods to change the direction of the vehicle’s front wheels.5.1.2. Rack and Pinion Design VariationsThere are two basic designs for Saginaw rack and pinion steering systems: end take-off and center take-off. Manual steering or power assist can be used on either design. The names indicate the location of the tie rods relative to the rack. On the end take-off design, the tie rods connect to the ends of the rack. The center take-off the rods connect the center of the rack. Figure 5.1-2 shows the basic differences in the two systems. Both designs have the same mechanical function. Choosing which version to use on a particular vehicular vehicle depends on the space. Weight, and other design considerations.5.1.3 Basic Rack and Pinion PartsThe turning motion applied to the steering wheel controls vehicles equipped with manual steering. When equipped with power assist system, vehicles only need reduced steering effort tocontrol their steering and, in some cases, reduced number of turns from lock to lock to improve emergency steering ability. Even if the power assist failure happens, a person can drive the vehicle but with increased steering effort.Since the design and operating principles of the manual gear are the same as the power gear, it is helpful to use the manual system to show the basic components common to all rack and pinion gears. Figure 5.1-3 shows the basic components of manual rack and pinion gears, which are also common to power-assist gears (which also include hydraulic-assist components).5.1.3.1. HousingThe housing is body-mounted or chassis-mounted, hollow metal body where the pinion and the rack engage.5.1.3.2. PinionThe pinion extends from the rack through an opening on top of the housing and attaches to the steering column or intermediate shaft. Gear teeth on the lower end of the pinion engage the gear teeth on the rack.5.1.3.3. RackThe rack is a long, around bar inside the housing. It has a cut gear surface where it engages the pinion. The inner tie rods are connected to the rack.5.1.3.4 Tie roadInner and outer tie rod connect the rack to the wheels to control the direction of the vehicle.◆End take-off (ETO): the tie rods connect to the ends of the rack and extend out fromopenings at each end of the housing.◆Center take-off (CTO): the tie rods connect to the center of the rack through a slot on thecenter of housing.5.1.3.5 Boot(s)Both the end and center take-off designs use flexible boots to cover housing openings and prevent internal damage and water intrusion.◆End take-off (ETO) (figure 5.1-2(a)): Boots on each end of the housing move back andforth with the rack; the boots expand and contract with the tie rods.◆Center take-off (CTO) (figure 5.1-2(b)): The center take-off design has a single, largeboot which surrounds the portion of the housing where the tie rods connect to therack. The boot expand and contract as the tie rods move back forth.5.1.4. Benefits of Rack and Pinion Steering SystemsThe benefits offered by rack and pinion steering systems include the following:◆Lighter weight for improved fuel economy.◆Space efficiency for tight design situations, particular for front wheel drive applications.◆Design flexibility to accommodate a wide rang of vehicle specifications.◆Compatibility with front-wheel drive vehicle design.◆Improved road feel, better handling, and more responsive steering.◆Durability. Compared to conventional steering systems, fewer things can go wrong with arack and pinion steering system.5.2. Manual Rack and Pinion Steering SystemThe figure 5.2-1 shows the assembly drawing of a manual steering gear. The pinion is supported in the rack and pinion housing by a lower bearing that is pressed into the housing. Typical manual steering gears utilize one-piece aluminum housing. Manual steering pinions are one-piece construction. The pinion is also supported by an upper bearing assembly that is positioned lengthwise on the pinion. The upper bearing assembly is held on the pinion by a retainer that is staked into a groove on the pinion. The upper bearing assembly slides into the housing with the pinion. Once the pinion is positioned in the housing, it is held firmly in place by a beveled retaining ring which fits into a groove in the housing. There is also a rubber lip seal which presses into the housing and seals between the housing and the pinion (figure 5.1-3 and figure 5.2-1).The rack is long round bar which has a number of gear teeth in a straight line. The gear teeth on the lower part of the pinion mesh with the gear teeth on the rack. Therefore, as the pinion rotates, the meshing of the gear teeth causes the rack to move back and forth sideways. Thus, the rotary motion of the steering wheel is converted by the steering gear into the lateral movement of the rack. The joint between the inner tie rod and the rack are protected from the environment by the boot seal.5.2.1. End Take-Off and Center Take-Off SystemsThe movement of the rack is transmitted by tie rod to the steering arms and wheels. There are two different ways tie rods connect to the rack: End take-off system and the center take-off system. Both designs have the same mechanical function. The systems’ names indicate the location of the tie rods relative to the rack. Choosing which version to use in a particular vehicle depends on the space, weight, and other design considerations. Refer to figure 5.1-2 to see the basic differences between the two systems.5.2.1.1. End Take-Off SystemThe Figure 5.2-1 shows the assembly drawing of a manual steering gear of end take-off design. On the end take-off system, the tie rods connect to the ends of the rack.The end take-off rack assembly is comprised of the following main components. A rack bushing is located in the housing and is held in place by a retaining ring. The steering rack then slides back and forth through the bushing (Figure 5.2-1 and Figure 5.2-2).A rack bearing slides into the housing and directly supports the steering rack. A spring is positioned between the bearing and an adjuster plug, which threads into the housing. The adjuster plug is secured in position by a locknut (Figure 5.2-2).The inner tie rod assemblies are threaded and staked to the steering rack. A shock dampener also snaps over each inner tie rod. The dampener minimizes noise at the end of rack travel and also determines the rack travel. Boots are secured to the housing with clamps. On some models the boots are also secured to the inner tie rods with clamps. The inner tie rod must be allowed to spin freely inside of the boots in order to adjust the vehicle toe. On other models, the boots fit tightly over the inner tie rods without requiring clamps. An outer tie rod assembly threads over each inner tie rod and is held in place with a locknut (Figure 5.1-3 and Figure 5.2-1).Figure 5.2-2 is an exploded view of a typical end tack-off rack and pinion steering assembly. The rack housing may be slightly different in some models from what is showm here, depending on the model and year vehicle.5.2.1.2. Center Take-Off SystemThe center take-off system functions in a similar manner to end take-off system, but is designed a bit differently. The center take-off tie rods connect to the center of the rack.Figure 5.2-3 shows the exploded view of a manual steering gear of center take-off design. This system has a bushing pressed into the housing through which the rack can slide. A rack bearing, spring and adjuster plug are positioned in this system the same way as for the end take-off system. Notice the front of the housing. It is not solid like the one used for end take-off, but rather has an open slot. This slot is often referred to as the window.When the rack is positioned in the housing, a rack guide is positioned in the front opening of the housing. A boot covers most of the housing, including the opening and the rack guide. The boot is secured to each end of the housing with clamps.The inner tie rod assemblies are connected to the rack at approximately the center of the housing where the opening is located. The bolts connecting the inner tie rods pass through and also connect the rack guide to the rack. The outer tie rod assemblies connect to the inner tie rods by a bolt, or stud, that threads into both the inner and outer tie rod. This is also an adjusting bolt that is used for toe adjustment during a front-end alignment.Except for the differences in some of their components, the center take-off and end take-off systems function the same.5.3. Power Rack and Pinion Steering SystemsDepending on the size and weight of a car and some other factors, including type of tires, tire pressure, gear ratio and road surface, the driver has to exert some amount of manual effort to turn the steering wheel. If the car is equipped with power assisted steering the driver does not have to exert as must effort to turn the wheel. Power rack-and-pinion steering systems are basically the same as mechanical systems, except for power assist components, as the manual rack and pinion. Therefore, if something happens to power assist, such as the pump belt breaking or the engine stalling, the driver can still maintain control and continue steering the car without the hydraulic assist.Basically, power steering is accomplished by adding a piston to the rack and sealing it within the housing. This, in effect, creates a hydraulic cylinder. When oil is sent under pressure from a pump and through a valve to one end of the hydraulic cylinder, it exerts a force that tends to push the rack in one directing. Directing the oil to the other end of the hydraulic cylinder pushes the rack in the other direction (Figure 5.3-1).5.3.1 Power Rack and Pinion Steering System Components5.3.1.1 End Take-Off systemFigure 5.3-2 is an assembly drawing of a typical power rack-and-pinion steering gear with end take-off. And Figure 5.3-3 is an exploded view of it. If you compare this with figure 5.2-1 and Figure 5.2-2, which is the manual rack and pinion gear with end take-off, you can see the difference between the two systems. As you’ll notice, the primary differences are in the housing, rack, and steering gear (pinion) because of the additional components for the power assist.In order for the power steering to work, a hydraulic cylinder is created in the rack-and-pinion housing.If the housing is a three-piece design, the cylinder tube, in conjunction with the piston acts as a hydraulic cylinder. The cylinder tube is pressed on to the rack housing and is secured by eitherdrive screws or by injecting plastic into the joint. The cylinder tube is typically made of steel.The valve housing (often referred to as the top hat) is pressed into the top of the rack housing and the joint is injected with plastic to secure it. The valve housing is usually made from cast iron, and the rack housing is usually made from die-cast aluminum.A piston is attached to the steering rack and slides back and forth in the cylinder. A Teflon ring acts as a seal between the piston and the cylinder a lip seal, called the inner rack seal, is pressed into the housing to act as a seal between the housing and the steering rack.An inner bulkhead fits into the housing and is located at the end of the cylinder. An outer bulkhead fits into the housing outboard of the inner bulkhead. The outer bulkhead has a lip seal pressed into it which provides a seal between the outer bulkhead and the rack (Figure 5.3-2). In addition, a rubber O-ring acts as a seal between the outer bulkhead and the cylinder tube. All these parts are held in place in the cylinder tube by a retaining ring which fits into a groove in the cylinder tube (Figure 5.3-2 and Figure 5.3-3).The rack is supported by a rack bearing that is positioned in the housing. There is a spring located between he bearing and an adjuster plug, which threads into the housing. The adjuster plug is secured in position by a locknut (Figure 5.3-3).Cylinder lines for the hydraulic oil are threaded into appropriate ports in the valve housing with O-ring seals providing the seal between the hydraulic lines and the valve housing. The cylinder lines are connected to the cylinder tube using flared end fittings. Just as with the manual rack and pinion steering system. The inner tie rod assemblies are threaded and staked to the rack. Boots are secured to the housing and, in some models, to the inner tie rods with clamps. The outer tie rod assembly threads over the inner tie rod and is secured in position with a locknut (Figure 5.3-4)There is one component in this area that is not provided on the manual rack and pinion. A breather tube is connected to the two boot seals for the inner tie rods (Figure 5.3-4). This breather tube is very important since it transfers air between the two boot seals as they collapse and extend. If a hollow rack is used, the air is often transferred through the middle of the rack, not requiring a breather tube. This tube is not necessary on a manual system since the transfer of air can occur inside the steering gear, which is not sealed like the one on the power system.It is also very important that the breather tube be installed at all times. If the tube is missing during operation of the rack and pinion. Dirt can be sucked into the boot seal hole where the tube should be positioned.The lower pinion components of the power rack-end-pinion steering system are illustrated in Figure 5.3-2 and 5.3-3. the lower pinion thrust bearing is pressed into the housing and is secured here by a retaining ring that fits into a groove in the housing. The upper pinion bushing and lip seal are also pressed into the housing. The pinion is positioned in the upper and lower pinion bearings. A nut threads over the bottom of the pinion and secures it firmly to the lower bearing. A dust cover is pressed into the lower part of the housing to shield the lower pinion components. On the upper part of the pinion is a retaining ring which snaps into a groove in the spool shaft. Above the retaining ring is an annulus into which the spool shaft bearing is pressed. A rubber primary lip seal and a dust seal are pressed into the upper part of the housing to provide a seal between the spool shaft and the housing. A retaining ring secures the two seals (Figure 5.3-2 and Figure 5.3-3)5.3.1.2. Center Take-Off SystemFigure 5.3-5 is an assembly drawing of a typical power rack-and-pinion steering gearing with center take-off. And Figure 5.3-6 is an exploded view of it. If you compare this with Figure 5.2-3, which is a manual rack and pinion gear with center take-off, you can see the differences between the two systems. As you’ll notice, the primary differences are in the housing, rack, and steering gear (pinion) because of the additional components for the power assist.Besides the differences associated with how the tie rods connect the rack, which manual gears have, there are distinct differences in the hydraulic cylinder and rack between power center take-off and end take-off systems. As can be seen in Figure 5.3-5 and Figure 5.3-6, the piston has different effective hydraulic areas at its different sides. In order to compensate the uneven power assist to one side and another, it is necessary to take certain measures.5.4. Basic Power Assist Operation5.4.1. Hydraulic PathsFigure 5.4-1 shows a typical hydraulic system in which a mechanical pump uses an internal vane rotor to generate hydraulic fluid pressure. The pump then forces fluid through a hydraulic hose to a valve assembly which is part of the steering gear.For power rack and pinion gears, the valve assembly is attached to the top of the pinion (see Figure 5.3-2, 5.3-3, 5.3-5, and 5.3-6).the valve directs the fluid to the appropriate parts of the system where hydraulic force is converted into mechanical movement.Figures 5.4-2 and 5.4-3 respectively shows typical system flow path and gear flow path of rack and pinion steering system. Hydraulic fluid from the power steering pump is delivered via the power steering hoses to the ports in the valve housing (or tophat). The power steering (rotary) valve then can direct available pump pressure to either side of the steering rack piston to assist the driver’s input as required. Fluid leaving the nonpressurized side of the piston flows through its cylinder line to the return passages of the valve and back to the pump reservoir. when no assist is required, the fluid flows internally within the valve and is returned to the pump. This open-center type system results in pump load when required.5.4.2. Rotary Valve Function5.4.2.1 Steering Gear Valve Body AssemblyThe steering gearing gear valve body assembly uses a spool valve to direct hydraulic fluid to the appropriate steering gear chamber. Valve operation is similar for both integral gears and rack and pinion gears. This section illustrates valve operation for rack and pinion systems. The valve assembly includes the following components (refer to Figure 5.4-4)◆Valve Body—The valve body provides a hydraulic interface between the gear housingand the spool shaft. Grooves and seal ring on the OD provide fluid path connectionsbetween pressure, return, and cylinder paths. Grooves on the ID interfacehydraulically with the spool shaft to direct fluid flow to provide the desired steeringassist.◆Spool Shaft—the spool shaft not only provides a mechanical connection with theIntermediate Shaft, but also directs fluid flow to provide the desired steering assist.Physical variations of the valving surfaces on the spool shaft dictate the ultimatesteering feel of the vehicle. These variations, such as groove width, flat width, angleand length, are performed on the spool shaft instead of the valve body since it ismuch easier to do.◆Torsion Bar—the Torsion Bar is nothing more than a spring which returns the valve to itsneutral position. The diameter of the bar dictates its torsional rate, and this is aninfluencing factor on valve effort. One end of the bar is retained in the pinion, andthe other end is pinned to the spool shaft as the valve is balanced.◆Drive Pin—The Drive PIN is the connecting link between the pinion and the valve Body.It is pressed into a heat treated portion of the pinion and rides in a hole in the valvebody. Since the valve body is the floating component in the rack and pinion valve, astraight-sided pin would tend to bind and lock the valve body if perfect alignment ofpin to hole is not achieved. Hence, the head of the pin is milk-bottle shapedproviding little more than point contact with the body hole ID. The top end of thepinion is attached to a valve assembly (see Figure 5.3-2, 5.3-3,5.3-5, and 5.3-6). Thevalve body rotates within the housing bore. There are annular grooves on the outsideof the valve body which connect with oil hold in the housing. The purpose of theseholds is for supplying oil from the pump and directing it to either end of the steeringcylinder bore. Teflon rings provide a seal between the valve body and the housing.There are also holes through the wall of valve body which connect the outsidegrooves with the longitudinal slots on the inside surface. These inner surface slotsform one-half of the valving interface (where the oil valving is done). (Figure5.4-4).A torsion bar is pressed and staked into the top end the pinion. There is also a drive pin in the head of the pinion which fits into a hole in the valve body. This then locks to the valve body, the lower end of the torsion bar and the pinion, allowing them to rotate as through they were one solid component (Figure 5.4-4).The spool shaft (input shaft) of the gear assembly is attached to the upper end of the torsion bar with a pin (Figure 5.4-4). This allows the spool shaft and the upper end of the torsion bar to rotate together as through they were one solid component.Longitudinal slots are cut into the outside diameter of the spool shaft and interact with the longitudinal slots on the inside surface of the valve body. This interaction forms the other half of the valuing interface.Holes that go through the spool shaft wall allow the oil to flow back to the pump. There are splines in the bottom of spool shaft which allow the spool shaft to fit loosely into splines in the top of the pinion (Figure 5.4-4) there is a certain amount of rotational movement available in the splines of the spool shaft and pinion. And this movement is called valve travel. The splines provide mechanical backup in the case of hydraulic failure.5.4.2.2 Vavling OperationThe amount of hydraulic assist that is provided in a power steering system is directly related to, and controlled by, the drive. This is because as the drive turns the steering wheel, he controls the operation of the steering gear valve. The valve, in turn, is a very important component in controlling the hydraulic response to the drive’s turning of the steering wheel. The actual operation of the valve is as follows.It has been shown that the spool shaft and upper end of the torsion bar rotate as one part. Thevalve body, pinion and lower end of the torsion bar act as another solid part. One part is then considered the action side and the other part is considered the resistance side. The torsion bar, which is a rotational spring, is the connection between the two parts (figure 5.4-5). When the diver turn the steering wheel, the action side of the steering gear, which is the spool shaft and upper end of the torsion bar, rotates with the steering wheel. The resistance side, which is the valve body, pinion and lower end of the torsion bar, does not move at first but does sense the resistance to turning at tires. Since the valve body is not rotating, valving begins to take place and oil is sent under pressure to the appropriate end of the rack cylinder.As the steering wheel and spool shaft continue to rotate, the oil pressure increases and the hydraulic force acting on the steering rack piston is large enough to overcome the turning resistance at the tires. When this happens the piston, rack, tie rods and tires start to move.If the drive continues rotating the steering wheel, the spool shaft will rotate within the valve body only as much as is required to overcome the turning resistance at the tires. The spool shaft will then maintain that position relative to the valve body, even though both parts, action and resistance, of the steering gear assembly are rotating within the gear housing.When the driver releases the steering wheel, the torsion bar unwinds and returns the spool shaft to a central position within the valve body. If the car is moving, the aligning forces from the tires help both the action and resistance sides of the steering gear assembly to rotate to the straight-ahead position.Figure 5.4-6 is a cutaway view of a valve is in a centered position, oil from the pump flows into the valve through four supply holes (ports) in the valve body. This valves is an open center valve, meaning that the oil is freely ported to both sides of the cylinder and to the return flow back to the pump.Figure 5.4-7 shows the valve in full right turn as performed in a parking maneuver. Again, input or pressure fluid enters the valve, but since the gaps to the left turn cylinder holes and closed, it enters the right turn cylinder holes since the gaps to return are also closed. Under these conditions, no flow from pressure to return takes place, the fluid is under extremely high pressure and maximum assist occurs. As the fluid actuates the hydraulic piston and motion occurs the fluid in the left turn side of the cylinder is forced out thru the cylinder lines and back to valve. Here it enters thru the left turn cylinder holes in the valve body, and since the gap to return is wide open, it flows out the return passages. Figure 5.4-7 shows two extreme positions of the valve. During normal steering, however, the valve seldom is fully actuated. Partial flow occurs to one of the sets of cylinder passages, and manipulation of the cross sectional areas thru which flow takes place and by selection of a desirable torsion bar diameter, the handling characteristics of the vehicle are determined and enhanced.5.4.3. Valve Plot TypesWhen a valve needs to be designed, and certain parameters must be met, it is desirable to depict these parameters graphically. Hence, two basic types of curves depict the functional characteristics of a certain valve. One is the pressure-effort curve, the other is the response curve. The pressure-effort curve shows the amount of steering effort required to build a certain steering assist pressure, and the response curve shows how far the valve has to rotate to build that pressure. Typical curves are shown in figures 5.4-8 and 5.4-9.One of the ways to change the shapes of those two types of curves is to change the diameter of the T-Bar (Torsion Bar). Figure 5.4-10 illustrates the effect of torsion bar diameter on valveeffort. The larger the T-Bar diameter, the bigger the amount of steering effort required to build a certain steering assist pressure.Using these two basic curves plus the data from vehicle evaluations, a valve is developed to meet certain customer specifications.5.4.4. Valve Balance and EffortWith the steering assembly mounted in an appropriate. Fixture, rotate the valve all the way to the right corner and read effort required to build a 0.69 Mpa differential pressure. Rotate the valve all the way to the left corner and repeat the reading. Valve effort in each corner at 0.69 Mpa to be within 0.46 N.m of each other and to be within the limits as specified on the appropriate valve and pinion assembly chart.5.4.5. Hardness of Valving SurfacesThe valve should be heat treated in order to meet the certain requirement for hardness of its valving surfaces. True, the valve will function the same whether its components are heat treated or not, but let us go one step further. The presence of foreign material in the steering system is virtually unavoidable. Whether in some isolated instances machining chips are left in the components or debris is introduced into the system thru service by the customer, it can and will happen. These foreign particles are capable of entering the valve. If the valving surfaces of a valve are not hard enough to chew up them, it may be caused to bind after a relatively shorter period of work. However, heat treated valving surfaces have the ability to chew up foreign particles and continue functioning.5.4.6. Quiet ValveThe original valve designed for rack and pinion steering was a down-size copy of the integral gear valve complete with its hiss characteristics. At that time, no consideration for hiss reduction was given to the design since adequate noise isolation was provided by the intermediate shaft. In the evolution of the American front-wheel drive automobile, ride stiffness became an important factor. On-Center compliance was partially reduced by stiffer compounds in the intermediate shaft pot joint. This had a tendency to degrade the noise isolation qualities of system, and hiss suppression became an issue to be addressed.Integral gear valve and early rack and pinion valves have velving surface arranged in such a manner that a three-step metering process is accomplished. This concept was incorporated into the integral gear valve to reduce valve squawk. As full actuation of the valve takes place and valving gaps are sequentially closed until just before final shutoff, two pressure gaps allow all the fluid to flow thru them at tremendous pressure and velocity. Studies at the time had shown that hiss is affected by fluid velocity, temperature and pressure. A valve with equal gaps, where fluid shutoff occurs simultaneously on all involved valving surfaces, was conceived and developed. Here final shutoff occurred thru all eight involved valving gaps, reducing fluid velocity thru a given passage thus reducing valve hiss. Implementation of this concept, however, proved to be cumbersome to say the least. In fact, subsequent experimentation revealed that in order for this concept to work, parts had to be made with unimaginable precision, virtually eliminating any tolerances at all.Another part of the problem also was that fluid metering took place over sharp edges.Further reduction in valve hiss was accomplished by having metering flats ground onto the。
汽车转向结构中英文翻译
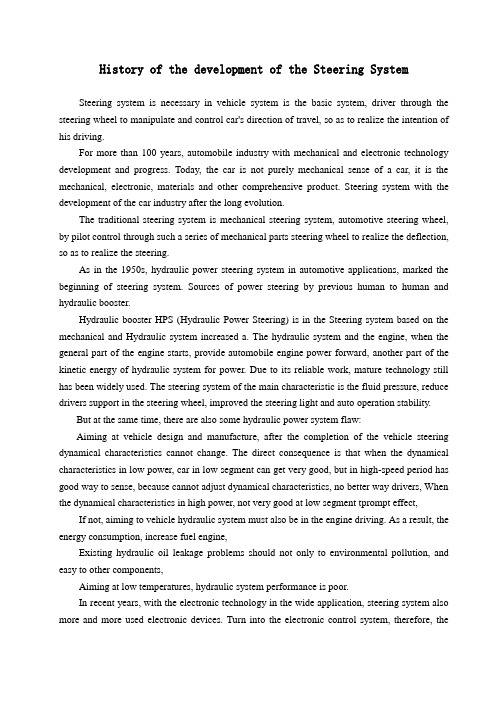
History of the development of the Steering SystemSteering system is necessary in vehicle system is the basic system, driver through the steering wheel to manipulate and control car's direction of travel, so as to realize the intention of his driving.For more than 100 years, automobile industry with mechanical and electronic technology development and progress. Today, the car is not purely mechanical sense of a car, it is the mechanical, electronic, materials and other comprehensive product. Steering system with the development of the car industry after the long evolution.The traditional steering system is mechanical steering system, automotive steering wheel, by pilot control through such a series of mechanical parts steering wheel to realize the deflection, so as to realize the steering.As in the 1950s, hydraulic power steering system in automotive applications, marked the beginning of steering system. Sources of power steering by previous human to human and hydraulic booster.Hydraulic booster HPS (Hydraulic Power Steering) is in the Steering system based on the mechanical and Hydraulic system increased a. The hydraulic system and the engine, when the general part of the engine starts, provide automobile engine power forward, another part of the kinetic energy of hydraulic system for power. Due to its reliable work, mature technology still has been widely used. The steering system of the main characteristic is the fluid pressure, reduce drivers support in the steering wheel, improved the steering light and auto operation stability.But at the same time, there are also some hydraulic power system flaw:Aiming at vehicle design and manufacture, after the completion of the vehicle steering dynamical characteristics cannot change. The direct consequence is that when the dynamical characteristics in low power, car in low segment can get very good, but in high-speed period has good way to sense, because cannot adjust dynamical characteristics, no better way drivers, When the dynamical characteristics in high power, not very good at low segment tprompt effect, If not, aiming to vehicle hydraulic system must also be in the engine driving. As a result, the energy consumption, increase fuel engine,Existing hydraulic oil leakage problems should not only to environmental pollution, and easy to other components,Aiming at low temperatures, hydraulic system performance is poor.In recent years, with the electronic technology in the wide application, steering system also more and more used electronic devices. Turn into the electronic control system, therefore, thecorresponding appeared electrohydraulic power steering system. Electrohydraulic Power Steering can be divided into two categories: electric Hydraulic Steering system (Electro Hydraulic Power - the EHPS) and electric Hydraulic Steering Electronically Controlled ECHPS Steering (Hydraulic Power Steering). Electric hydraulic steering system is in hydraulic power system on the basis of the development of hydraulic booster systems, and different is, electric hydraulic power system of power sources in the hydraulic system, but not by motor engine motor drive hydraulic system, save energy and reduce the engine fuel consumption. Electric hydraulic steering is in traditional hydraulic booster systems on the basis of the development, the difference is that the electric hydraulic steering system, electronic control devices increased. The electronic control unit can according to the steering rate, speed auto operation parameters of hydraulic system, change the size of the hydraulic booster at different speeds, so as to realize the change, dynamical characteristics. But under the motor drive hydraulic system, in turn, motor can stop turning, thereby reducing energy consumption.Although electrohydraulic power steering system of hydraulic steering overcomes the drawbacks. But due to the existence of hydraulic system, it exists the hydraulic oil leakage problem, and electrohydraulic power steering system, introduced motor drive system is more complex, costs and reliability.In order to avoid Electric hydraulic Steering system, Electric Power Steering system of Electric Power Steering (EPS) should now. It with all sorts of steering system, the biggest difference lies in the electric power steering system has no hydraulic system. Originally produced by hydraulic steering system by motor. Electric power steering system of general by the torque sensor and microprocessor, motor, etc. The basic principle is: when the driver turned the steering wheel drive shaft rotation, to install in the rotation axes of the torque sensor and torque signal into electrical signals to microprocessors, microprocessor based on speed and torque signal other vehicles running parameters, according to the set procedures in the treatment of that power motors booster direction and the size of the booster. Since 1988, the first in Japan suzuki Cervo car to equip the steering system, power steering system is widely recognized by the people.Steering system is mainly embodied in the following aspects:A power steering system can provide different at different speeds under the dynamical characteristics. In the low road, steering, to increase more light, At high speed reduced steering, even in order to improve the road are increased to damp.A power steering system only in steering motors to work, to provide power, so as to reduce energy consumption.A motor, so by battery-powered electric power steering system can not work in engine under the condition of the work.Electric power steering system should not hydraulic system, compared with hydraulic booster systems and automated assembly. And electric power steering system can change the booster program microprocessor algorithm, easy dynamical characteristics of the change.The development of science and technology is changing, the traditional steering system of steering control (wheel steering), and turn of transmission mechanism. But the thought of the spark can always bring surprise! Electronic Steering system SBW Steering (to the Wire) was changed to the traditional concept of three most with micro-controller, it was replaced By the Steering transmission mechanism, the three most into two parts. Electronic steering system is the most advanced and automotive steering system of technology. It mainly consists of steering control module, to execute module and micro controller three modules.Steering control module's main function is to torque sensor detection by the driver intention, and to detect signal (including rotation direction and rotational speed, etc) by bus to micro controller, and micro controller based on the signal, and speed feedback control module is a steering wheel to make drivers, can feel road. But this is the way, is the development of virtual according to test data of integrated, formed "experience", and by way of curing process in the form of micro controller. So it is with speed, turning to the size of the torque rate and some corresponding relation.Steering Angle sensor and actuator including steering motors, steering motor controller etc. It is the function of micro controller based on the control command, drive motor rotation Angle to execute, complete to action. Also the size of the rotation Angle sensor monitoring and feedback to micro controller, forming a complete accurate closed-loop control system, steering movement.Micro controller is the core of electronic steering system. It is receiving signal detection, processed send corresponding control signal.Due to the micro controller replaced steering transmission mechanism, thus mechanical connection between components of the system, reduce the response speed and the accuracy of the response. And to turn strategy, transmission control software programming any Settings, And other equipment, such as ABS, automatic navigation equipment. Transmission mechanism of reducing brings a bigger car interior space, give rides more fun. And turning behavior can be recorded, save in software that can help EEPROM after further perfecting the steering control strategy, even can provide evidence for the traffic accident.Auto safety question has been the focus of public attention. Steering system and lightingsystem can give at night traffic better security. Page shown above, the traditional lighting system is the vehicle to the front line irradiation, vehicles and pedestrians in corners if drivers will be hard to find in the corner, pedestrians traffic accidents. If the lighting system combined with the steering system, pictured above, when drivers in the steering wheel to the right of the steering wheel Angle, light with the right to change, the more wide illumination turn, lighting, so in a broader range of pedestrian road corner will easily be found. Currently the lighting technology has in the midrange Citroen triumph, Toyota camrys are used.At present, electronic steering system reliability and the cost is obstructed the development. If the micro controller is mainly manifested in the problem, steering system will complete failure, its not like electric power steering system and electric hydraulic steering system, in the motor or hydraulic system, also can appear when problems with human to control cars. The micro-controller electronic steering system malfunction, because no mechanical systems can be connected to the steering wheel and steering, therefore impossible to control of the car. But despite the electronic steering system is still the future development direction of steering system.汽车转向系的发展历史转向系统是在车辆系统是必要的基本制度,通过方向盘司机操纵和控制汽车的方向旅行,以实现他的驾驶意图。
汽车转向系统专业词汇

汽车转向系统专业词汇
Steering Linkages 转向拉杆
此装置是被用来连接前轮转向节和转向齿轮,使方向盘转动时,可使前轮由一边摆向另一边。
Steering Gear 轮向齿轮
固定在转向机轴下端的齿轮和装配在转向臂的齿轮总称。
可将方向盘的旋转动作,转换成拉杆的直线运动。
有二种基本的转向齿轮:回旋滚珠式和齿棒小齿轮式。
Recirclulating-Ball Steering Gear回旋滚珠式齿轮
此种转向齿轮,利用内部的循环珠,使螺母和螺杆之间的接触摩擦大大减少,让驾驶者操作方向盘轻巧方便。
Power Steering 动力转向
汽车所使用的动力转向系统,基本上是经修改的手动转向系统,主要的是增加一个助力器(Power Booster),以帮助驾驶者。
转向器 培训

4
CONTROL VALVE PARTS
1) TORSION BAR : 连接到I/S和P/S,转动方向盘时引起I/S和V/BODY之 间相对变位,通过控制STIFFNESS可改变P/V特性曲线。 2) INPUT SHAFT : I/S上加工有ORIFICE EDGE,转动方向盘时,利用与 V/BODY之间的相对变位形成缸体内压力差。 3) VALVE BODY : 通过连接到P/S来固定,当RACK BAR直线运动时开始 旋转,与I/S之间的相对变位形成压力差。 4) PINION SHAFT : 抑制V/B旋转方向的变位,通过与RACK啮合将 方向盘的旋转运动转换成直线运动。 5) VALVE HOUSING 支撑各个组件,防止油的外漏。
3
VALVE
转向时可以选用左右CYLINDER供应液压油
BELLOWS
防止水分渗透
FEED TUBE
连接VALVE和CYLINDER之间的油路
RACK & PINION GEAR
将方向盘的旋转运动转换为直线运动
CYLINDER
维持Piston的左右压差,通过液压油提供助力
MOUNTING BUSH
产品的结构功能technicalinformationshowncopiedreproduceddisclosedotherseitherpartwithoutpriorwrittenapproval转向器steeringgear抽油管suctionhose高压油管pressurehose回油管returntube储油壶reservoir方向盘steeringwheel转向柱steeringcolumn万向节universaljoint油泵oilpumpsteeringsystempartsnametechnicalinformationshowncopiedreproduceddisclosedotherseitherpartwithoutpriorwrittenapprovalvalve转向时可以选用左右cylinder供应液压油cylinder维持piston的左右压差通过液压油提供助力feedtube连接valve和cylinder之间的油路bellows防止水分渗透innerballjoint传递转向力tierodend将转向力传递给轮胎mountingbush安装到车辆吸收震动mountingclamp安装到车辆吸收震动rackpiniongear将方向盘的旋转运动转换为直线运动steeringsystemparts功能technicalinformationshowncopiedreproduceddisclosedotherseitherpartwithoutpriorwrittenapprovaltorsionbar连接到is和ps转动方向盘时引起is和vbody之间相对变位通过控制stiffness可改变pv特性曲线
汽车电动助力转向系统中英文对照外文翻译文献

汽车电动助力转向系统中英文对照外文翻译文献(文档含英文原文和中文翻译)原文:The auto electric power steering system researchAlong with automobile electronic technology swift and violent development, the people also day by day enhance to the motor turning handling quality request. The motor turning system hanged, the hydraulic pressure boost from the traditional machinery changes (Hydraulic Power Steering, is called HPS), the electrically controlled hydraulic pressure boost changes (Electronic Hydraulic Power Steering, is called EHPS), develops the electrically operated boost steering system (Electronic Power Steering, is called EPS), finally also will transit to the line controls the steering system (Steer By Wire, will be called SBW).The machinery steering system is refers by pilot's physical strength achievement changes the energy, in which all power transmission all is mechanical, the automobile changes the movement is operates the steering wheel by the pilot, transmits through the diverter and a series of members changes the wheel to realize. The mechanical steering system by changes the control mechanism, the diverter and major part changes the gearing 3 to be composed.Usually may divide into according to the mechanical diverter form: The gear rack type, follows round the world -like, the worm bearing adjuster hoop type, the worm bearing adjusterrefers sells the type. Is the gear rack type and follows using the broadest two kinds round the world -like (uses in needing time big steering force).In follows round the world -like in the diverter, the input changes the circle and the output steering arm pivot angle is proportional; In the gear rack type diverter, the input changes the turn and the output rack displacement is proportional. Follows round the world -like the diverter because is the rolling friction form, thus the transmission efficiency is very high, the ease of operation also the service life are long, moreover bearing capacity, therefore widely applies on the truck. The gear rack type diverter with follows round the world -like compares, the most major characteristic is the rigidity is big, the structure compact weight is light, also the cost is low. Because this way passes on easily by the wheel the reacting force to the steering wheel, therefore has to the pavement behavior response keen merit, but simultaneously also easy to have phenomena and so on goon and oscillation, also its load bearing efficiency relative weak, therefore mainly applies on the compact car and the pickup truck, at present the majority of low end passenger vehicle uses is the gear rack type machinery steering system.Along with the vehicles carrying capacity increase as well as the people to the vehicles handling quality request enhancement, the simple mechanical type steering system were already unable to meet the needs, the power steering system arise at the historic moment, it could rotate the steering wheel while the pilot to provide the boost, the power steering system divides into the hydraulic pressure steering system and the electrically operated steering system 2kinds.Hydraulic pressure steering system is at present uses the most widespread steering system.The hydraulic pressure steering system increased the hydraulic system in the mechanical system foundation, including hydraulic pump, V shape band pulley, drill tubing, feed installment, boost installment and control valve. It with the aid of in the motor car engine power actuation hydraulic pump, the air compressor and the generator and so on, by the fluid strength, the physical strength or the electric power increases the pilot to operate the strength which the front wheel changes, enables the pilot to be possible nimbly to operate motor turning facilely, reduced the labor intensity, enhanced the travel security.The hydraulic pressure boost steering system from invented already had about half century history to the present, might say was one kind of more perfect system, because its work reliable, the technology mature still widely is applied until now. It takes the power supply by the hydraulic pump, after oil pipe-line control valves to power hydraulic cylinder feed, through the connecting rod impetus rotation gear movement, may changes the boost through the change cylinder bore and the flowing tubing head pressure size the size, from this achieved changes the boost the function. The traditional hydraulic pressure type power steering system may divide into generally according to the liquid flow form: Ordinary flow type and atmospheric pressure type 2 kind of types, also may divide into according to the control valve form transfers the valve type and the slide-valve type.Along with hydraulic pressure power steering system on automobile daily popularization, the people to operates when the portability and the road feeling request also day by day enhance, however the hydraulic pressure power steering system has many shortcomings actually: ①Because its itself structure had decided it is unable to guarantee vehicles rotates the steering wheel when any operating mode, all has the ideal operation stability, namely is unable simultaneously to guarantee time the low speed changes the portability and the high speed time operation stability;②The automobile changes the characteristic to drive the pilot technical the influence to be serious;③The steering ratio is fixed, causes the motor turning response characteristic along with changes and so on vehicle speed, transverse acceleration to change, the pilot must aim at the motor turning characteristic peak-to-peak value and the phase change ahead of time carries on certain operation compensation, thus controls the automobile according to its wish travel. Like this increased pilot's operation burden, also causes in the motor turning travel not to have the security hidden danger; But hereafter appeared the electrically controlled hydraulic booster system, it increases the velocity generator in the traditional hydraulic pressure power steering system foundation, enables the automobile along with the vehicle speed change automatic control force size, has to a certain extent relaxed the traditional hydraulic pressure steering system existence question.At present our country produces on the commercial vehicle and the passenger vehicle uses mostly is the electrically controlled hydraulic pressure boost steering system, it is quite mature and the application widespread steering system. Although the electrically controlled hydraulic servo alleviated the traditional hydraulic pressure from certain degree to change between the portability and the road feeling contradiction, however it did not have fundamentally to solve the HPS system existence insufficiency, along with automobile microelectronic technology development, automobile fuel oil energy conservation request as well as global initiative environmental protection, it in aspect and so on arrangement, installment, leak-proof quality, control sensitivity, energy consumption, attrition and noise insufficiencies already more and more obvious, the steering system turned towards the electrically operated boost steering system development.The electrically operated boost steering system is the present motor turning system development direction, its principle of work is: EPS system ECU after comes from the steering wheel torque sensor and the vehicle speed sensor signal carries on analysis processing, controls the electrical machinery to have the suitable boost torque, assists the pilot to complete changes the operation. In the last few years, along with the electronic technology development, reduces EPS the cost to become large scale possibly, Japan sends the car company, Mitsubishi Car company, this field car company, US's Delphi automobile system company, TRW Corporation and Germany's ZF Corporation greatly all one after another develops EPS.Mercedes2Benz Siemens Automotive Two big companies invested 65,000,000 pounds to use in developing EPS, the goal are together load a car to 2002, yearly produce 300 ten thousand sets, became the global EPS manufacturer. So far, the EPS system in the slight passenger vehicle, on the theater box typevehicle obtains the widespread application, and every year by 300 ten thousand speed development.Steering is the term applied to the collection of components, linkages, etc. which allow for a vessel (ship, boat) or vehicle (car) to follow the desired course. An exception is the case of rail transport by which rail tracks combined together with railroad switches provide the steering function.The most conventional steering arrangement is to turn the front wheels using ahand–operated steering wheel which is positioned in front of the driver, via the steering column, which may contain universal joints to allow it to deviate somewhat from a straight line. Other arrangements are sometimes found on different types of vehicles, for example, a tiller orrear–wheel steering. Tracked vehicles such as tanks usually employ differential steering — that is, the tracks are made to move at different speeds or even in opposite directions to bring about a change of course.Many modern cars use rack and pinion steering mechanisms, where the steering wheel turns the pinion gear; the pinion moves the rack, which is a sort of linear gear which meshes with the pinion, from side to side. This motion applies steering torque to the kingpins of the steered wheels via tie rods and a short lever arm called the steering arm.Older designs often use the recirculating ball mechanism, which is still found on trucks and utility vehicles. This is a variation on the older worm and sector design; the steering column turns a large screw (the "worm gear") which meshes with a sector of a gear, causing it to rotate about its axis as the worm gear is turned; an arm attached to the axis of the sector moves the pitman arm, which is connected to the steering linkage and thus steers the wheels. The recirculating ball version of this apparatus reduces the considerable friction by placing large ball bearings between the teeth of the worm and those of the screw; at either end of the apparatus the balls exit from between the two pieces into a channel internal to the box which connects them with the other end of the apparatus, thus they are "recirculated".The rack and pinion design has the advantages of a large degree of feedback and direct steering "feel"; it also does not normally have any backlash, or slack. A disadvantage is that it is not adjustable, so that when it does wear and develop lash, the only cure is replacement.The recirculating ball mechanism has the advantage of a much greater mechanical advantage, so that it was found on larger, heavier vehicles while the rack and pinion was originally limited to smaller and lighter ones; due to the almost universal adoption of power steering, however, this is no longer an important advantage, leading to the increasing use of rack and pinion on newer cars. The recirculating ball design also has a perceptible lash, or "dead spot" on center, where a minute turn of the steering wheel in either direction does not move the steering apparatus; this is easily adjustable via a screw on the end of the steering box to account for wear, but it cannot be entirely eliminated or the mechanism begins to wear very rapidly. This design is still in use in trucks andother large vehicles, where rapidity of steering and direct feel are less important than robustness, maintainability, and mechanical advantage. The much smaller degree of feedback with this design can also sometimes be an advantage; drivers of vehicles with rack and pinion steering can have their thumbs broken when a front wheel hits a bump, causing the steering wheel to kick to one side suddenly (leading to driving instructors telling students to keep their thumbs on the front of the steering wheel, rather than wrapping around the inside of the rim). This effect is even stronger with a heavy vehicle like a truck; recirculating ball steering prevents this degree of feedback, just as it prevents desirable feedback under normal circumstances.The steering linkage connecting the steering box and the wheels usually conforms to a variation of Ackermann steering geometry, to account for the fact that in a turn, the inner wheel is actually traveling a path of smaller radius than the outer wheel, so that the degree of toe suitable for driving in a straight path is not suitable for turns.As vehicles have become heavier and switched to front wheel drive, the effort to turn the steering wheel manually has increased - often to the point where major physical exertion is required. To alleviate this, auto makers have developed power steering systems. There are two types of power steering systems—hydraulic and electric/electronic. There is also ahydraulic-electric hybrid system possible.A hydraulic power steering (HPS) uses hydraulic pressure supplied by an engine-driven pump to assist the motion of turning the steering wheel. Electric power steering (EPS) is more efficient than the hydraulic power steering, since the electric power steering motor only needs to provide assist when the steering wheel is turned, whereas the hydraulic pump must run constantly. In EPS the assist level is easily tunable to the vehicle type, road speed, and even driver preference. An added benefit is the elimination of environmental hazard posed by leakage and disposal of hydraulic power steering fluid.An outgrowth of power steering is speed adjustable steering, where the steering is heavily assisted at low speed and lightly assisted at high speed. The auto makers perceive that motorists might need to make large steering inputs while manoeuvering for parking, but not while traveling at high speed. The first vehicle with this feature was the Citroën SM with its Diravi layout, although rather than altering the amount of assistance as in modern power steering systems, it altered the pressure on a centring cam which made the steering wheel try to "spring" back to the straight-ahead position. Modern speed-adjustable power steering systems reduce the pressure fed to the ram as the speed increases, giving a more direct feel. This feature is gradually becoming commonplace across all new vehicles.Four-wheel steering (or all wheel steering) is a system employed by some vehicles to increase vehicle stability while maneuvering at high speed, or to decrease turning radius at low speed.In most four-wheel steering systems, the rear wheels are steered by a computer and actuators. The rear wheels generally cannot turn as far as the Alternatively, several systems, including Delphi's Quadrasteer and the system in Honda's Prelude line, allow for the rear wheels to be steered in the opposite direction as the front wheels during low speeds. This allows the vehicle to turn in a significantly smaller radius — sometimes critical for large trucks or vehicles with trailers.Electronic power steering systemWhat it isElectrically powered steering uses an electric motor to drive either the power steering hydraulic pump or the steering linkage directly. The power steering function is therefore independent of engine speed, resulting in significant energy savings.How it works :Conventional power steering systems use an engine accessory belt to drive the pump, providing pressurized fluid that operates a piston in the power steering gear or actuator to assist the driver.In electro-hydraulic steering, one electrically powered steering concept uses a high efficiency pump driven by an electric motor. Pump speed is regulated by an electric controller to vary pump pressure and flow, providing steering efforts tailored for different driving situations. The pump can be run at low speed or shut off to provide energy savings during straight ahead driving (which is most of the time in most world markets).Direct electric steering uses an electric motor attached to the steering rack via a gear mechanism (no pump or fluid). A variety of motor types and gear drives is possible. A microprocessor controls steering dynamics and driver effort. Inputs include vehicle speed and steering, wheel torque, angular position and turning rate.Working In Detail:A "steering sensor" is located on the input shaft where it enters the gearbox housing.The steering sensor is actually two sensors in one: a "torque sensor" that converts steeringtorque input and its direction into voltage signals, and a "rotation sensor" that converts the rotation speed and direction into voltage signals. An "interface" circuit that shares the same housingconverts the signals from the torque sensor and rotation sensor into signals the control electronics can process.Inputs from the steering sensor are digested by a microprocessor control unit that also monitors input from the vehicle's speed sensor. The sensor inputs are then compared to determine how much power assist is required according to a preprogrammed "force map" in the control unit's memory. The control unit then sends out the appropriate command to the "power unit" which then supplies the electric motor with current. The motor pushes the rack to the right or left depending on which way the voltage flows (reversing the current reverses the direction the motor spins). Increasing the current to the motor increases the amount of power assist.The system has three operating modes: a "normal" control mode in which left or right power assist is provided in response to input from the steering torque and rotation sensor's inputs; a "return" control mode which is used to assist steering return after completing a turn; and a "damper" control mode that changes with vehicle speed to improve road feel and dampen kickback.If the steering wheel is turned and held in the full-lock position and steering assist reaches a maximum, the control unit reduces current to the electric motor to prevent an overload situation that might damage the motor. The control unit is also designed to protect the motor against voltage surges from a faulty alternator or charging problem.The electronic steering control unit is capable of self-diagnosing faults by monitoring the system's inputs and outputs, and the driving current of the electric motor. If a problem occurs, the control unit turns the system off by actuating a fail-safe relay in the power unit. This eliminates all power assist, causing the system to revert back to manual steering. A dash EPS warning light is also illuminated to alert the driver. To diagnose the problem, a technician jumps the terminals on the service check connector and reads out the trouble codes.Electric power steering systems promise weight reduction, fuel savings and package flexibility, at no cost penalty.Europe's high fuel prices and smaller vehicles make a fertile testbed for electric steering, a technology that promises automakers weight savings and fuel economy gains. And in a short time, electric steering will make it to the U.S., too. "It's just just a matter of time," says Aly Badawy, director of research and development for Delphi Saginaw Steering Systems in Saginaw, Mich. "The issue was cost and that's behind us now. By 2002 here in the U.S. the cost of electric power steering will absolutely be a wash over hydraulic."Today, electric and hybrid-powered vehicles (EV), including Toyota's Prius and GM's EV-1, are the perfect domain for electric steering. But by 2010, a TRW Inc. internal study estimates that one out of every three cars produced in the world will be equipped with some form of electrically-assisted steering. The Cleveland-based supplier claims its new steering systems could improve fuel economy by up to 2 mpg, while enhancing handling. There are true bottom-line benefits as well for automakers by reducing overall costs and decreasing assembly time, since there's no need for pumps, hoses and fluids.Another claimed advantage is shortened development time. For instance, a Delphi group developed E-TUNE, a ride-and-handling software package that can be run off a laptop computer. "They can take that computer and plug it in, attach it to the controller and change all the handling parameters -- effort level, returnability, damping -- on the fly," Badawy says. "It used to take months." Delphi has one OEM customer that should start low-volume production in '99.Electric steering units are normally placed in one of three positions: column-drive, pinion-drive and rack-drive. Which system will become the norm is still unclear. Short term, OEMs will choose the steering system that is easiest to integrate into an existing platform. Obviously, greater potentialcomes from designing the system into an all-new platform."We have all three designs under consideration," says Dr. Herman Strecker, group vice president of steering systems division at ZF in Schwaebisch Gmuend, Germany. "It's up to the market and OEMs which version finally will be used and manufactured.""The large manufacturers have all grabbed hold of what they consider a core technology," explains James Handysides, TRW vice president, electrically assisted steering in Sterling Heights, Mich. His company offers a portfolio of electric steering systems (hybrid electric, rack-, pinion-, and column-drive). TRW originally concentrated on what it still believes is the purest engineering solution for electric steering--the rack-drive system. The system is sometimes refered to as direct drive or ball/nut drive.Still, this winter TRW hedged its bet, forming a joint venture with LucasVarity. The British supplier received $50 million in exchange for its electric column-drive steering technology and as sets. Initial production of the column and pinion drive electric steering systems is expected to begin in Birmingham, England, in 2000."What we lack is the credibility in the steering market," says Brendan Conner, managing director, TRW/LucasVarity Electric Steering Ltd. "The combination with TRW provides us with a good opportunity for us to bridge that gap." LucasVarity currently has experimental systems on 11 different vehicle types, mostly European. TRW is currently supplying its EAS systems for Ford and Chrysler EVs in North America and for GM's new Opel Astra.In 1995, according to Delphi, traditional hydraulic power steering systems were on 7596 of all vehicles sold globally. That 37-million vehicle pool consumes about 10 million gallons in hydraulic fluid that could be superfluous, if electric steering really takes off.The present invention relates to an electrically powered drive mechamsm for providing powered assistance to a vehicle steering mechanism. According to one aspect of the present invention, there is provided an electrically powered driven mechanism for providing powered assistance to a vehicle steering mechanism having a manually rotatable member for operating the steering mechanism, the drive mechanism including a torque sensor operable to sense torque being manually applied to the rotatable member, an electrically powered drive motor drivingly connected to the rotatable member and a controller which is arranged to control the speed and direction of rotation of the drive motor in response to signals received from the torque sensor, the torque sensor including a sensor shaft adapted for connection to the rotatable member to form an extension thereof so that torque is transmitted through said sensor shaft when the rotatable member is manually rotated and a strain gauge mounted on the sensor shaft for producing a signal indicative of the amount of torque being transmitted through said shaft.Preferably the sensor shaft is non-rotatably mounted at one axial end in a first coupling member and is non-rotatably mounted at its opposite axial end in a second coupling member, the first and second coupling members being inter-engaged to permit limited rotation therebetween so that torque under a predetermined limit is transmitted by the sensor shaft only and so that torque above said predetermined limit is transmitted through the first and second coupling members.The first and second couplingmembers are preferably arranged to act as a bridge for drivingly connecting first and second portions of the rotating member to one another.Preferably the sensor shaft is of generally rectangular cross-section throughout the majority of its length.Preferably the strain gauge includes one or more SAW resonators secured to the sensor shaft.Preferably the motor is drivingly connected to the rotatable member via a clutch.Preferably the motor includes a gear box and is concentrically arranged relative to the rotatable member.Various aspects of the present invention will hereafter be described, with reference to the accompanying drawings, in which :Figure 1 is a diagrammatic view of a vehicle steering mechanism including an electrically powered drive mechanism according to the present invention,Figure 2 is a flow diagram illustrating interaction between various components of the drive mechanism shown in Figure 1 ,Figure 3 is an axial section through the drive mechanism shown in Figure 1, Figure 4 is a sectional view taken along lines IV-IV in Figure 3,Figure 5 is a more detailed exploded view of the input drives coupling shown in Figure 3, andFigure 6 is a more detailed exploded view of the clutch showing in Figure 3. Referring initially to Figure 1 , there is shown a vehicle steering mechanism 10 drivingly connected to a pair of steerable road wheels The steering mechanism 10 shown includes a rack and pinion assembly 14 connected to the road wheels 12 via joints 15. The pinion(not shown) of assembly 14 is rotatably driven by a manually rotatable member in the form of a steering column 18 which is manually rotated by a steering wheel 19.The steering column 18 includes an electric powered drive mechanism 30 which includes an electric drive motor (not shown in Figure 1) for driving the pinion in response to torque loadings in the steering column 18 in order to provide power assistance for the operative when rotating the steering wheel 19.As schematically illustrated in Figure 2, the electric powered drive mechanism includes a torque sensor20 which measures the torque applied by the steering column 18 when driving the pinion and supplies a signal to a controller 40. The controller 40 is connected to a drive motor 50 and controls the electric current supplied to the motor 50 to control the amount of torque generated by the motor 50 and the direction of its rotation.The motor 50 is drivingly connected to the steering column 18 preferably via a gear box 60, preferably an epicyclic gear box, and a clutch 70. The clutch 70 is preferably permanently engaged during normal operation and is operative under certain conditions to isolate drive from the motor 50 to enable the pinion to be driven manually through the drive mechanism 30. This is a safety feature to enable the mechanism to function in the event of the motor 50 attempting to drive the steering column too fast and/or in the wrong direction or in the case where the motor and/or gear box have seized.The torque sensor 20 is preferably an assembly including a short sensor shaft on which is mounted a strain gauge capable of accurately measuring strain in the sensor shaft brought about by the application of torque within a predetermined range.Preferably the predetermined range of torque which is measured is 0-lONm; more preferably is about l-5Nm.Preferably the range of measured torque corresponds to about 0-1000 microstrain and the construction of the sensor shaft。
重型卡车转向系统-中英文版-2015-11
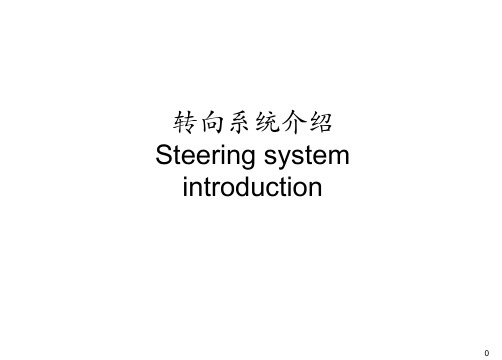
5
转向液压原理 Steering hydraulic principle
右转方向 Right direction 当方向盘向右转动时,活塞将向右侧移动,在左侧动力腔内将 建立起一个转向所需的压力。 When the steering wheel is turned to the right, the piston will move to the right, and the pressure will be set up in the left power chamber. 转阀顺时针方向偏转,进油槽(K)的开度变大,允许油液进入。 同时,进油槽(J)关闭,以防油液进入到轴向槽(O)。 The turning valve is in a clockwise direction, and the opening of the radial groove (K) is large, allowing the oil to enter. At the same time, the radial groove (J) is closed to prevent oil from entering into the axial grooves (O). 此时油液将通过进油槽(K)进入阀套上的轴向槽(N),然后刘 静滚珠丝杆进入左侧的动力腔。进油槽(J)关闭,以防油液流回 油壶,在左侧动力腔内建立起压力。 At this point the oil will pass through the radial groove (K) into the valve sleeve on the axial grooves (N), and then Liu Jing ball screw into the left side of the power chamber. An radial groove (J) closed, to prevent the oil into the pot, set up the pressure in the left power cavity. 右侧动力腔中的油液将被排出,通过打开的回油槽(M)流入转 阀上的回油槽(P),然后通过转阀及蜗杆上的油孔流回到油壶。 Right power cavity in the oil will be discharged, through the open back to return oil control grooves (M) inflow valve on the back of return oil control grooves (P), then transferred through the oil hole in the valve and the worm flows back into the oil reservoir .
汽车转向系统外文原文及翻译

本文摘于《Race Car Vehicle Dynamics》作者:William F. Miliken and Douglas L. MilikenSteering systemsIntroductionThis chapter begins with a discussion of steering geometry—casterangle ,trail ,kingpin inclination ,and scrub radius .The next section discuss Ackermann geometry followed by steering racks and gears .Ride steer (bump steer ) and roll steer are closely related to each other ;without compliance they would be thesame .Finally ,wheel alignment is discussed .this chapter is tied to chapter 17 on suspension geometry –when designing a new chassis ,steering and suspension geometry considerations are high priorities .19.1 steering geometryThe kingpin in a solid front axle is the steering pivot .In modern independent suspensions , introduced by Maurice olley at Cadillac in 1932,the kingpin is replaced by two (or more ) ball joints that define the steering axis .This axis is not vertical or centered on the tire contact patch for a number of reason .see figure 19.1 to clarify how kingpin location is measured .In front view ,the angle is called kingpin inclination and the offset of the steering axis from the center of the tire print measured along the ground is called scrub (or scrub radius ). The distance from the kingpin axis to the wheel center plane , measured horizontally at axle height ,is the spindle length .In side view the kingpin angle is called caster angle ; if the kingpin axis does not pass through the wheel center then side view kingpin offset is present ,as in most motorcycle front ends .The distance measured on the ground from the steering axis to the center of the tire print is the trail (called caster offset in ref .1 )Kingpin front view geometryAs mentioned in chapter 17, kingpin inclination ,spindle length ,and scrub are usually a compromise between packaging and performance requirements .Some factors to consider include :1.With a positive spindle length (virtually every car is positive as shown in figure 19.1) the car will be raised up as the wheels are steered away from center .The more the kingpin inclination is tilted from vertical the more the car will be raised when the front wheels are steered .This effect always raises the car , regardless of which direction the wheel is steered ,unless the kingpin inclination is truevertical .the effect is symmetric side to side only if there is no caster angle .See the following section on caster angle .For a given kingpin inclination ,a longer positive spindle length will increase the amount of lift with steer .2.The effect of kingpin inclination and spindle length in raising the front end ,by itself ,is to aid centering of the steering at low speed .At high speed any trail will probably swamp out the effect that raise ad fall have on centering .3. Kingpin inclination affects the steer –camber characteristic .when a wheel is steered ,it will lean out at the top ,toward positive camber ,if the kingpin is inclined in the normal direction (toward the center of the car at the upper end ). Positive camber results for both left– and right-hand steer .the amount of this effect is small ,but significant if the track includes tight turns.4. When a wheel is rolling over a bumpy road ,the rolling radius is constantly changing ,resulting in changes of wheel rotation speed . This gives rise to longitudinal forces at the wheel center .The reaction of these forces will introduce kickback into the steering in proportion to the spindle length .If the spindle length is zero then there will be no kick from this source .Design changes made in the last model of the GM “P ”car (fiero ) shortened the spindle length and this resulted in less wheel kickback on rough roads when compared to early model “P ”cars.5. The scrub radius shown in figure 19.1 is negative ,as used on front-wheel–drive cars (see below ) . driving or braking forces (at the ground ) introduce steer torques proportional to the scrub radius . If the driving or braking force is different on left and right wheels then there will be a net steering torque felt by the driver (assuming that the steering gear has good enough rev erse efficiency ).The only time that this is not true is with zero scrub (centerpoint steering ) because there is no moment arm for the drive (or brake ) force to generate torque about the kingpin .With very wide tires the tire forces often are not centered in the wheel center plane due to slight changes in camber ,road surface irregularities ,tire nonuniformity (conicity ),or other asymmetric effects .These asymmetries can cause steering kickback regardless of the front view geometry .Packaging requirements often conflict with centerpoint steering and many race cars operate more or less okay on smooth tracks with large amounts of scrub .6. For front drive ,a negative scrub radius has two strong stabilizingeffects :first ,fixed steering wheel –if one drive wheel loses traction ,the opposingwheel will toe –out an amount determined by the steer compliance in the system .This will tend to steer the car in a straight line ,even though the tractive force is not equal side-to –side and the unequal tractive force is applying a yaw moment to the vehicle .Second ,with good reverse efficiency the driver’s hands never truly fix the steering wheel . In this case the steering wheel may be turned by the effect of uneven longitudinal tractive forces ,increasing the stabilizing effect of the negative scrub radius .Under braking the same is true .Negative scrub radius tends to keep the car traveling straight even when the braking force is not equal on the left and right side front tiresome (due to differences in the roadway or the brakes).Caster angle and trailWith mechanical trail ,shown in figure 19.1,the tire print follows behind the steering axis in side view .Perhaps the simplest example is on an office chair caster–with any distance of travel ,the wheel aligns itself behind the point .More trail means that the tire side force has a large moment arm to act on the kingpin axis .This produces more self-centering effect and is the primary source of self-centering moment about the kingpin axis at speed .Some considerations for choosing the caster angle and trail are :1.More trail will give higher steering force .with all cars ,less trail will lower the steering force .In some cases ,manual steering can be used on heavy sedans (instead of power steering ) if the trail is reduced to almost zero .2.Caster angle ,like kingpin inclination ,cause the wheel to rise and fall with steer .unlike kingpin inclination ,the effect is opposite from side to side .With symmetric geometry (including equal positive caster on left and right wheels ) ,the effect of left steer is to roll the car to the right ,causing a diagonal weight shift .In this case ,more load will be carried on the LF –RR diagonal ,an oversteer effect in aleft-hand turn .The diagonal weight shift will be larger if stiffer springing is used because this is a geometric effect .The distance each wheel rises (or falls ) is constant but the weight jacking and chassis roll angle are functions of the front and rear roll stiffness. This diagonal load change can be measured with the car on scales and alignment ( weaver ) plates .Keep in mind that the front wheels are not steered very much in actual racing , except on the very tightest hairpin turns . For example , on a 100-ft .radius (a 40-50 mph turn ), a 10-ft. wheelbase neutral steer car needs only about 0.1rad .(5.7)of steer at the front wheels (with a 16:1steering ratio this is about 90degree at the steering wheel ).For cars that turn in one direction only , caster stagger (differences in left and right caster ) is used to cause the car to pull to one side due to the car seeking the lowest ride height . caster stagger will also affect the diagonal weight jacking effect mentioned above .If the caster is opposite (positive on one side and negative the same number of degrees on the other side ) then the front of the car will only rise and fall with steer ,no diagonal weight jacking will occur .3. Caster angle affects steer-camber but ,unlike kingpin inclination ,the effect is favorable . With positive caster angle the outside wheel will camber in a negative direction (top of the wheel toward the center of the car ) while the inside wheel cambers in a positive direction , again learning into the turn .In skid recovery , “opposite lock ” (steer out of the turn ) is used and in this case the steer–camber resulting from caster angle is in the “wrong ” direction for increased front tire grip . conveniently ,this condition results from very low lateral force at the rear so large amounts of front grip are not needed .4. As discussed in chapter 2, tires have pneumatic trail which effectively adds to (and at high slip Angles subtracts from ) the mechanical trail . This tire effect is nonlinear with lateral force and affects steering torque and driver feel .In particular , the fact that pneumatic trail approaches zero as the tire reaches the limit will result in lowering the self-centering torque and can be s signal to the driver that the tire is near breakaway .The pneumatic trail “breakaway signal” will be swamped out by mechanical trail if the mechanical trail is large compared to the pneumatic trail .5.Sometimes the trail is measured in a direction perpendicular to the steering axis (rather than horizontal as shown in figure 19.1) because this more accurately describes the lever (moment ) arm that connects the tire lateral forces to the kingpin . Tie rod locationNote that in figure 19.1 a shaded area is shown for the steering tie rod location . Camber compliance under lateral force is unavoidable and if the tie rod is located as noted ,the effect on the steering will be in the understeer ( steer out of the turn ) direction becomes much more complex than can be covered here .19.2 Ackerman steering geometryAs the front wheels of a vehicle are steered away from the straight-ahead position ,the design of the steering linkage will determine if the wheels stay parallel or if one wheel steers more than the other .This difference in steer Angles on the left and right wheels should not be confused with toe-in or toe-out which are adjustments and add to ( or subtract from ) Ackerman geometric effects .For low lateral acceleration usage (street cars) it is common to use Ackerman geometry . as seen on the left of figure 19.2, this geometry ensures that all the wheels roll freely with no slip Angles because the wheels are steered to track a common turn center . Note that at low speed all wheels are on a significantly different radius , the inside front wheel must steer more than the outer front wheel . A reasonable approximation to this geometry may be as shown in figure 19.3.According to ref .99, Rudolf Ackerman patented the double pivot steering system in 1817 and in 1878, Charles Jeantaud added the concept mentioned above to eliminate wheel scrubbing when cornering . Another reason for Ackermann geometry ,mentioned by Maurice olley , was to keep carriage wheels from upsetting smooth gravel driveways .High lateral accelerations change the picture considerably . Now the tires alloperate at significant slip Angles and the loads on the inside track are less than on the outside track . Looking back to the tire performance curves ,it is seen that less slip angle is required at lighter loads to reach the peak of the cornering force to a higher slip angle than required for maximum side force . Dragging the inside tire along at high slip Angles ( above for peak lateral force ) raise the tire temperature and slows the car down due to slip angle ( induced ) drag .For racing , it is common to use parallel steering or even reverse Ackermann as shown on the center and right side of figure 19.2.It is possible to calculate the correct amount of reverse Ackermann if the tire properties and loads are known . In most cases the resulting geometry is found to be too extreme because the car must also be driven (or pushed ) at low speeds , for example in the pits .Another point to remember is that most turns in racing have a fairly large radius and the Ackermann effect is very small . In fact , unless the steering system and suspension are very stiff ,compliance (deflection ) under cornering loads may steer the wheels more than any Ackermann (or reverse Ackermann ) built into the geometry .The simplest construction that generates Ackermannn geometry is shown in figure 19.3 fo r “rear steer ” . Here ,the rack (cross link or relay rod in steering box systems ) is located behind the front axle and lines staring at the kingpin axis , extended through the outer tie rod ends , intersect in the center of the rear axle . The angularity of the steering knuckle will cause the inner wheel to steer more than the outer (toe-out on turning ) and a good approximation of “perfect Ackermann ” will be achieved .The second way to design-in differences between inner and outer steer Angles is by moving the rack (or cross link ) forward or backward so that it is no longer on a line directly connecting the two outer tie rod ball joints .This is shown in figure 19.4. with “rear steer ” , as shown in the figure ,moving the rack forward will tend mo re toward parallel steer (and eventually reverse Ackermann ), and moving it toward the rear of the car will increase the toe-out on turning .A third way to generate toe with steering is simply to make the steering arms different lengths . A shorter steering arm (as measured from the kingpin axis to the outer tie rod end ) will be steered through a larger angle than one with a longer knuckle. Of course this effect is asymmetric and applies only to cars turning in one direction—oval track cars .RecommendationWith the conflicting requirements mentioned above , the authors feel that parallel steer or a bit of reverse Ackermann is a reasonable compromise . With parallel steer , the car will be somewhat difficult to push through the pits because the front wheels will be fighting each other . at racing speeds , on large-radius turns , the front wheels are steered very little , thus any ackermann effects will not have a large effect on the individual wheel slip angles , relative to a reference steer angle , measured at the centerline of the car .文献翻译摘自《Race Car Vehicle Dynamics》第19章转向系统序言:本章以转向几何参数的讨论为开始,包括主销后倾角,后倾拖距,主销内倾角,主销偏置量。
汽车相关词汇翻译(8)

汽车相关词汇翻译(8)转向力 steering force转向传动比 steering gear ratio (steering ratio0恒定转向传动比 constant ratio steering可变转向传动比 variable ratio steering转向系角传动比 steering system angle ratio转向器角传动比 steering gear angle ratio转向传动机构角传动比 steering linkage angle ratio转向器传动效率 steerign gear efficiency正效率 forward efficiency逆效率 reverse efficiency转向器扭转刚度 torsional stiffness of steering gear转向盘总圈数 total number of steering wheel turns转向器总圈数 total turns of steering gaer转向器传动间隙 steering gar cleanrance摇臂轴最大转角 max.rotating angle of pitman arm shaft转向摇臂最大摆角 max. Swing angle of steering pitman arm 转向器反驱动力矩 reverse rotating torque of steering gear热电偶高温计 thermocouple pyrometer转向器最大输出扭矩 steering gear max. Output torque最大工作压力 max. Working pressure额定工作压力 rated working pressure转向油泵理论排量 theoretical displacement of pump限制流量 limited flow转向控制阀预开隙 pre-opened play of steering contol valve 转向控制阀全开隙totally -opened play of steering control valve转向控制阀内泄漏量 internal leakage in steering control valve 转向控制阀压力降 pressure loss in steering control valve转向器角传动比特性 steering gear angle ratio characteristic转向器传动间隙特性 steering gear clearance characterstic转向器传动效率特性 steering gear efficeieny characteristic转向力特性 steering force characteristic动力转向系灵敏度特性power steering systme response characteristic转向控制阀压力降特性steeirn gcontrol valve presrue loss characteristtic前桥 front axle工字梁 I-beam双工字梁 twin I-beam非驱动桥 dead axle转向节 steering knuckle挂车转向装置 steering system of trailer中央主销式转向装置 central king pin type steering systme无主销转向装置 no king pin type steering system全杆式转向装置 all linkage tyep steering system球销式转向节 ball and socket steering knuckle转向节止推轴承 steering knuckle thrust bearing前轮轴 front wheel spindle转向盘轴 steering spindle转向节轴 knuckle spindle转向节臂 steering knuckle arm(转向节)主销 knuckle pin(King pin)反拳式前桥 reverse elliott axle反拳式转向节 reverse elliott steering knuckle叉式前桥 elliott type axle叉式转向节 elliott steering knuckle制动系 braking ssytem类型 tyep行车制动系统 service braking sytem应急制动系统 secondary (emergency )braking sytem 驻车制动系统 parking braking system辅助制动系统 auxiliary braking system自动制动系统 automatic braking sytem人力制动系统 muscular energy braking sytem助力制动系统 energy assisted braking system动力制动系统 non-muscular energy braking system 惯性制动系统 inertial braking styem重力制动系统 gravity braking sytem单回路制动系统 single-circuit braking system双回路制动系统 dual -ciurcuit braking system单管路制动系统 single-line braking system双管路制动系统 dual braking sytem多管路制动系统 multi-line braking sytem连续制动系统 continuous braking sytem半连续制动系统 semi-continuous braking sytemm 非连续制动系统 non-continuous braking system伺服制动系统 servo braking system液压制动系统 hydraulic braking sytem电磁制动系统 electormagnetic braking sytem机械制动系统 mechanical braking sytem组合制动系统 combination braking sytem基本术语 bsic terms制动装备 braking equipment组成部件 constituent elements制动力学 braking mechanics渐进制动 gradual braking制动能源 braking energy source制动力矩 braking torque总制动力 total braking force干扰后效制动力矩 distrubing residual braking torque总制动距离 total braking distance有效制动距离 active braking distance制动力分配率 braking force distaribution rate制动效能因素(制动强度) braking efficiency factro制动力 braking work瞬时制动功率 instantaneous braking power保护压力 rptection pressure报警压力 alarm pressure制动系滞后 braking system hysteresis制动效果百分数 percentage of the braking efficiency停车距离(制动距离) stopping distance充分发出的平均减速度mean fully developed braking deceleration (MFDD)制动反应时间 reaction time促动时间 actuating time初始反应时间 initial response time制动力增长时间 build-up time of braking force有效制动时间 active braking time释放时间 release time驾驶员反应时间 reaction time of driver机构滞后时间 mechanism hysteresis time增长时间 build-up time of braking force主制动时间 main braking time总制动时间 total braking tiem停车时间 stopping tiem开启行程 opening travel空行程 spare travel中间行程 mid-travel制动储备行程 reserve brake travel断油行程 cut-off travel行程损失 loss of travel缩小比(减压比) reduction ratio回缩 retraction两片法 two-plate method单片法 single-plate method热电偶高温计 thermocouple pyrometer含水量 moistrue content单轮控制 individual wheel control多轮控制 multi wheel control轴控制 axle control边控制 side control对角控制 diagonal control组合多轴控制 combined multi-axle control 可变选择 variable selection最低控制速度 minimum control speed传感器信号选择 sensor signal低选择 select -low高选择 select-high预定选择 predetermined selectin车轮选择 selection by wheel平均选择 average selecton分辨率 resolution rate控制周期 control cycle控制频率 control frequency控制力 control force作用力 control froce制动器效能因素 application force制动器材的滞后 brake hysteresis制动器输出力矩 brake output torque。
- 1、下载文档前请自行甄别文档内容的完整性,平台不提供额外的编辑、内容补充、找答案等附加服务。
- 2、"仅部分预览"的文档,不可在线预览部分如存在完整性等问题,可反馈申请退款(可完整预览的文档不适用该条件!)。
- 3、如文档侵犯您的权益,请联系客服反馈,我们会尽快为您处理(人工客服工作时间:9:00-18:30)。
转向器基本原理介绍Fundamental Principles of Steering Gear 目录Contents一、汽车液压动力转向系统的组成I . Hydraulic power steering system二、循环球动力转向器基本原理II . Recirculating Ball Steering Gear三、齿轮齿条转向器基本原理III .R&P Power Steering Gear四、转向系统发展的先进技术IV . Advanced Technology of Steering System五、我厂的技术优势及特点V . Our Advantages for developing Technology六、先进驾驶辅助系统ADAS Advanced Driver Assistant System汽车液压转向系统的组成Hydraulic Power Steering System汽车转向系统的组成Steering System汽车的跑、转、停是它的基本性能,他们中的一个重要机能则由转向装置来承担。
Basic capability of vehicle is to run, turn or stop. Turning device assumes this responsibility.机械转向系统Manual Steering Gear 动力转向系统Power Steering Gear汽车液压动力转向系统的组成Hydraulic Power Steering System方向盘及管柱、中间轴Steering Wheel, Column and Intermediate Shaft转向器及摇臂Steering Gear and Pitman Arm 油泵Pump 油罐Reservoir 油管Pipe支架及其它附件Bracket and Other Accessories 拉杆系统Linkage 主销及车轮Pin and Wheels1-方向盘Steering Wheel 2-中间传动轴Intermediate Shaft 3-进油管Inlet Pipe4-回油管Outlet Pipe 5-油罐Reservoir 6-油泵Pump 7-转向器Steering Gear8-摇臂Pitman Arm 泵与油管组件Pump and Pipe Assembly 油泵Pump高、低压油管High and low Pressure Pipes 油箱Reservoir 回油管Outlet Pipe 油泵Pump循环油管Recycle Pipes 进油管Inlet Pipe R&P式油压动力转向器R&P Power Steering Gear转阀式循环球动力转向器基本原理Recirculating Ball Power Steering Gear转阀式动力转向器简介General Overview转向器是构成汽车转向系统的主要部件之一,由于特殊的作用,在性能和可靠性方面要求苛刻。
Steering gear is an important part for steering system.Based on its special crucial function, rigorous limits are required in the field of performance and reliability.转向器的主要作用:Function:保证汽车能按驾驶员的意识进行转向行驶。
Make sure vehicle to drive and turn as driver controls.转阀式动力转向器简介General Overview一、转向器的主要分类I .Classification按阀的形式分1、转阀式动力转向器Rotary Valve Power Steering GearType of Valve 2、滑阀式动力转向器Slide Valve Power Steering Gear3、板阀式动力转向器Board Valve Power Steering Gear按助力方式分1、机械转向器Manual Steering GearAssistant Mode2、液压助力转向器Hysteristic Power Steering Gear3、电动助力转向器Electronic Power System(EPS)按结构进行分类:Classified as structure 转向器分类Classification循环球动力转向器Recirculating Power Steering Gear 齿轮齿条转向器R & P Power Steering Gear转向器的安装Installing of Steering Gear 输入轴Input Shaft 进油管Inlet Pipe回油管Outlet Pipe 输出轴Output Shaft 汽车大梁Frame 转向摇臂Pitman Arm拉杆Linkage 转阀式动力转向器简介Rotary Spool Valve Power Steering Gear1、传递运动Pass Motion2、传递力矩Pass Torque 总体拆分图Assembly Split Picture动力转向器结构剖视图(输入轴)Configuration View (Input Shaft)1、螺杆-螺母系统Rack Piston-Screw System2、螺母-齿扇系统Sector-Rack Piston System动力转向器结构剖视图(输出轴)Configuration View (Output Shaft)螺母-齿扇系统Sector-Rack Piston System上壳体组件Valve Housing Assembly 下壳体组件Housing Assembly转阀-螺杆螺母组件Rack Piston Screw Assembly 侧盖组件Side Cover Assembly摇臂轴组件Pitman Shaft Assembly 壳体尾部的调整Adjustment for Tail of Housing转阀工作原理Principle of Rotary Spool Valve 汽车直线行驶Drive Straightly汽车右转弯Turn right 汽车左转弯Turn left转阀的输入力矩-压力特性Input torque-pressure Characteristics 车低速行驶时LOW SPEED高速行驶时HIGH SPEED 规定力矩TORQUE 转向系统的组成Structure of Steering System管柱Column 拉杆Linkage 油箱Reservoir 回油管Outlet Pipe 循环管Recycle Pipe油泵Pump 高压油管High Pressure Pipe 动力转向器总成Assembly低压油管High Pressure Pipe 油箱Reservoir 油泵Pump 循环油管Recycle Pipe高压油管High Pressure Pipe 方向盘Steering Wheel 管柱Column 万向接头Universal JointR&P式转向器总成R&P Steering Gear Assembly齿轮齿条转向器的分类Classification of R & P Steering Gear·齿轮齿条式转向器R & P Steering Gear·机械齿轮齿条式转向器(RP-MS) ·动力齿轮齿条式转向器(RP-PS)齿轮齿条转向器的结构Structure of R&P Steering Gear防护套Bellows 油管Oil Pipe 壳体Housing 齿条Rack 活塞环Piston Ring 六角螺母Hex Nut安装支成套Bush 标牌Label 液压缸Cylinder Tube 齿条支承套Rack Bush 扭杆Torsional Bar阀壳体Valve Housing 调整体Support Yoke 调整螺塞Yoke Plug 锁紧薄螺母Special Hex Nut齿条Rack 配钻销Pin 输入轴Input Shaft 阀套Valve Sleeve 齿轮Pinion特殊六角螺母Lock Nut 下端压紧螺塞End Plug 流入油箱Feed into reservoir从油泵进Enter from pump 输入力矩Input Torque 扭杆扭动Torsional Bar twisted阀开始工作⇒油压进行换向Valve start to work ⇒Pressure deflect左右液压缸产生压力差Pressure Difference (产生助力)(Assist)齿条(IBJ部)的左右运动Rack Motion ⇒节臂Knuckle ⇒车轮转动(回转运动)Wheels turning齿条Rack 齿轮Pinion 中立状态时Neutral Position 扭杆Torsional Bar 输入轴Input Shaft阀套Valve Sleeve 转向系统发展的先进技术Advanced TechnologyC-EPS基本组成及原理Elements and Principle of C-EPS C-EPS系统组成Elements◆ECU控制单元ECU Control Unit ◆直流电机DC Motor◆吸能式转向管柱Suction Steering Column◆齿轮齿条机械转向器R&P Manual Steering Gear ◆中间轴Intermediate ShaftEPS技术特点EPS Technology Features可兼顾良好的高速路感和原地转向的轻便性With good road feel andEPS技术特点EPS Technology Features 基本性能Basic Performance计算机CAD中心采用三维立体软件进行设计,保证了新产品的开发进度和设计质量。
Our computer CAD center adopt 3 dimension solid software to design, and ensure the development of new product and the quality of design.技术中心Technology Center技术引进与合作Technology Introducing and Cooperation1993年引进美国德尔福(Delphi)循环球式动力转向器设计、制造技术。