压力容器制造、检验与验收
GB150-XXXX压力容器-制造、检验和验收

▪ (2) 与国际接轨和国际贸易的需要 ▪ 1997年欧盟颁布了PED,同时实施了以技术法规为基本
安全要求、协调标准为技术支撑的安全保障体系。 ▪ 后续发布的欧洲统一压力容器标准在技术上全面满足
PED的安全基本要求,全面提出了基于失效模式设计的理 念,在设计准则、计算方法、制造检验要求等方面引入了 现代技术研究的成果。对促进贸易和提高竞争力起到了重 要的作用。 ▪ 在美国、澳大利亚和其他国家也相继修订了原有的技术 标准体系。 ▪ 相应降低了安全系数,使我国面临国外压力容器产品的 冲击,需合理修订标准(如容器分类,设计与制造阶段的 风险评估与控制,材料复验,产品焊接试件要求等),提 高中国压力容器产品的质量和国际竞争力。
(3) 解决行业关注的突出问题的需要
▪
如给予失效模式的制造、检验,成型受压
▪ 元件的性能恢复,无损检测的时间与方法等……
(4) 技术发展的需要
▪
GB 150-1998《钢制压力容器》实施以来,
我国压力容器材料、设计、制造。检验水平大幅
度提高。
▪ ——新材料开发:增加新材料制造、检验、与验 收要求。
▪ 五、GB 150.4修订的主要变化
▪ GB 150.4主要变化的原因:
▪
1、为完善我国压力容器法规、技术标准体系,与
修订后的《固定式压力容器安全技术监察规程》相适应所
做的修订(该部分变化在下表中以★标识,共23处)。
▪
2、为适应技术发展,采用先进技术所作的修订
(该部分在下表中以●标识,共12处)。
▪ — 2011年7月征求WTO成员国意见并修改定稿
▪ 三98颁布13年来中国发生的技术和管理变化
▪ ——压力容器的大型化、高参数、长周期趋势(失效模式发 生变化)
压力容器制造检验及验收
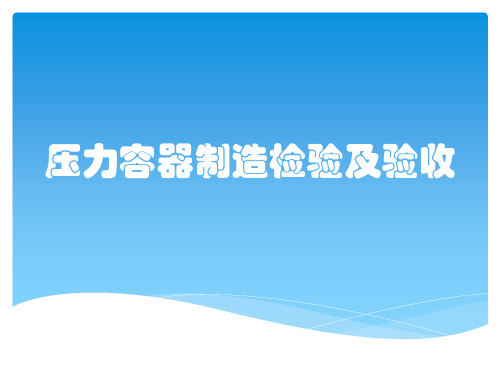
固定式压力容器的制造、检验及验收
四、 焊接
1. 焊前准备和施焊环境 a)焊条、焊剂及其他焊接材料的贮存库应保持干燥,相对湿度不得大于
60% 。
b)当施焊环境出现下列任一情况,且无有效防护措施时,禁止施焊: 焊条电弧焊时风速大于 10 m/s;
气体保护焊时风速大于 2 m/s;
相对湿度大于 90% ; 雨、雪环境; 焊件温度低于-20 ℃ 。 c) 当焊件温度低于 0 ℃ 但不低于 -20 ℃时,应在施焊处100 mm 范围内 预热到 15 ℃以上。
固定式压力容器的制造、检验及验收
4. 设计修改和代用 制造单位对原设计的修改以及对受压元件的材料代用,应事先取得原设计 单位的书面批准,并在竣工图上做详细记录。
二、 材料复检、分割与标识移植
1. 材料复检 1) 应对以下材料进行入库复检: a)采购的第 Ⅲ类压力容器用Ⅳ级锻件 b)不能确定质量证明书真实性或者对性能和化学成分有怀疑的主要受压 元件材料。 c) 用于制造主要受压元件的境外材料。 d) 用于制造主要受压元件的奥氏体型不锈钢开平板 e) 设计文件要求进行复验的材料 2)奥氏体型不锈钢开平板应按批号复检力学性能(整卷使用者,应在开
三、 加工成形与组装
1. 成形 制造单位应根据制造工艺确定加工余量,以确保受压元件成形后的实际厚 度不小于设计图样标注的最小成形厚度。 采用经过正火、正火加回火或调质处理的钢材制造的受压元件,宜采用冷 成形或温成形;采用温成型时,须避开钢材的回火脆性温度区。 2. 表面修磨 制造中应避免材料表面的机械损伤。对于尖锐伤痕以及不锈钢容器耐腐蚀 表面的局部伤痕、刻槽等缺陷应予修磨,修磨斜度最大为1:3。修磨的深度应不 大于该部位钢材料厚度δ的5%,且不大于2mm,否则应予焊补。
压力容器制造材料验收与复检

压力容器制造材料验收与复检发布时间:2021-08-30T09:00:38.886Z 来源:《中国建设信息化》2021年10期作者:张晓晨[导读] 在制造业中原材料的选用对成品有至关重要的影响,张晓晨中国石油天然气第一建设有限公司 471023引言:在制造业中原材料的选用对成品有至关重要的影响,尤其在设计承压产品时会按照相关承压标准设计规定原材料的性质。
所以原材料的验收和复验这二个步骤在压力容器制造中起到重要角色,本文就介绍一下上面二个步骤的重点事项。
一、原材料的进厂验收压力容器制造所需原材料主要为板材、管材、焊材、锻件、棒材和其他成品外购件。
因其原材料种类相对固定所以应制定验收控制程序,防止在验收时产生漏检、漏项等问题。
入场材料应均有特种设备制造许可证。
若有特殊境外材料验收时需要按照境外现行验收标准进行验收。
1)常规承压金属材料进厂验收原材料进厂时材料检验员应按图样要求、采购技术文件、材料标准等审核材料质量证明书,质证书内容应齐全、完整. 对材料牌号、规格、数量、供货状态、检验项目及数据、执行标准等进行核查,并由材料质控责任人给出材料检验编号。
原材料还需检查:外观质量。
材料表面没有裂纹、气泡、结疤、折叠和夹杂等缺陷。
材料的规格、几何尺寸。
凡需复验的原材料,应按项目要求进行复验。
2)焊材的验收压力容器产品受压元件之间的焊接接头质量对压力容器的安全性来讲是相对薄弱的环节。
尽管影响焊接接头质量的因素较为复杂,但为了保证其质量首要因素是确保焊接材料合格,施工中不错用、混用焊接材料。
a)用于制造压力容器受压元件的焊接材料,应保证焊缝金属的力学性能高于或等于母材规定的限值。
b)焊接材料进厂后,采购人员会同材料质控责任人对焊材质证书的项目、数据是否符合相关标准、订货技术协议、技术条件及特殊要求进行审查。
检验合格后,材料质控责任人给出焊材检验编号。
3)外购件、外协件的进厂验收对压力容器受压元件用的其它金属材料均按原材料的验收原则进行验收,但对压力容器用安全附件(安全阀、爆破片装置、紧急切断阀、压力表、液面计、测温仪表等)及其他辅助件(标准件、垫片等)还应按技术条件及相应标准的要求进行验收。
压力容器的设计、制造和检验

压力容器的设计、制造和检验一、压力容器概述1.压力容器规范化早在19世纪末就有了对锅炉和压力容器规范化的要求。
20世纪最初的十年,发生了近一万起锅炉爆炸,造成了约一万人的死亡和约一万五千人的伤残。
这些血的教训使人们对压力容器制造和安装的规范化有了更清醒的认识。
1907年,美国Massachusetts州继1905年和1906年两次灾难性的锅炉爆炸之后,提出了世界上第一部锅炉制造和安装的法规。
循着Massachusetts州的范例,美国其他州和城市也制定出了蒸气锅炉制造、安装和检验的不同形式的法规或条例。
不同州的技术规范缺乏一致性,使得制造者无法制造出其他州可以接受的标准锅炉。
制造出的锅炉不能运出州界,一个州的有资格的锅炉检验员也得不到其他州的承认。
要求订出蒸气锅炉和压力容器制造的标准规范的呼声越来越强烈,为解决这个问题,美国机械工程师协会于1911年成立了一个专门委员会,后来被称为锅炉规范委员会。
美国机械工程师协会非燃火压力容器规范对压力容器没有给出定义。
压力容器一般是指装有加压流体用于完成某项过程的封闭容器,例如贮罐、热交换器、蒸发器和反应器等。
规范规定压力容器的范围还包括容器外的管线,终止于管线端焊连接的第一条焊缝、螺栓连接的第一个法兰面、或类似连接的第一个有连接迹象的点或面。
美国非燃火压力容器规范的短评U-1列出了超出规范权限的一些例外。
这些例外是必须的还是已被解除,不同地区有很大的不同。
有关这方面的细节,需要查阅“锅炉和压力容器的法规和条例说明书”,或向有管辖权的地方管理机构咨询。
非规范压力容器是指不能满足设计、制造、检验和鉴定规范的最低要求的容器。
这些容器不打印规范代号,除非有特殊的裁定,不得在接受美国机械工程师协会规范的区域安装。
目前,许多国家都设置了压力容器规范的立法和管理机构,颁布了各自的压力容器规范。
在我国,原国家劳动总局1979年颁布了《气瓶安全监察规程》;1980年颁布了《蒸汽锅炉安全监察规程》;1981年颁布了《压力容器安全监察规程》。
GB150[1]制造检验与验收
![GB150[1]制造检验与验收](https://img.taocdn.com/s3/m/3aa6b2fa284ac850ad0242b8.png)
10制造、检验与验收10.1总则10.1.1本章适用于单层焊接、多层包扎、热套及锻焊压力容器。
对于设计温度低于或等于—20℃的容器,还应符合附录C(标准的附录)的规定。
注:热套压力容器是指套合而经机械加工或不经机械加工,各层之间以过盈相互配合,其套合预应力须经热处理尽量消除的容器。
10.1.2容器的制造、检验与验收除应符合本章规定外,还应符合图样的要求。
10.1.3容器的制造单位应具有符合国家压力容器安全监察机构有关法规要求的质量体系或质量保证体系。
10.1.4容器的焊接应由持有相应类别的“锅炉压力容器焊工合格证书”的人员担任。
10.1.5容器的无损检测应由持有相应方法的“锅炉压力容器无损检测人员资格证书”的人员担任。
10.1.6容器主要受压部分的焊接分为A、B、C、D四类,如图10-1所示。
a)圆筒部分的纵向接头(多层包扎容器层板层纵向接头除外)、球形封头与圆筒连接的环向接头、各类凸形封头中的所有拼焊接头以及嵌入式接管与壳体对接连接的接头,均属A类焊接接头。
b)壳体部分的环向接头、锥形封头小端与接管连接的接头、长颈法兰与接管连接的接头,均属B类焊接接头,但已规定为A、C、D类的焊接接头除外。
c)平盖、管板与圆筒非对接连接的接头,法兰与壳体、接管连接的接头,内封头与圆筒的搭接接头以及多层包扎容器层板层纵向接头,均属C类焊接接头。
d)接管、人孔、凸缘、补强圈等与壳体连接的接头,均属D类焊接接头,但已规定为A、B 类的焊接接头除外。
D D D C CCB B B B BB A AA AA A AA A A图10-110.1.7凡制造受压组件的材料应有确认的标记。
在制造过程中,如原有确认标记被裁掉或材料分成几块,应于材料切割前完成标记的移植。
确认标记的表达方式由制造单位规定。
对于有防腐要求的不锈钢以及复合钢板制容器,不得在防腐蚀面采用硬印作为材料的确认标记。
10.2冷热加工成形10.2.1根据制造工艺确定加工裕量,以确保凸形封头和热卷筒节成形后的厚度不小于该部件的名义厚度减去钢板的负偏差。
GB1502011压力容器制造检验和验收

▲7、删去了对质保体系,人员资格的 要求。
◆1、修改了受压元件成 形后实际厚度的规定;
●2、修改了封头形状偏 差检查方法及合格要求;
●3、修改了简体直线度 检查方法;
●4、修改了筒节长度的 规定;
★5、提高了M36~M48的 螺栓、螺柱和螺母的要求。
GB150.4 《压力容器-制造、检验和验收》
五、GB 150.4修订的主要变化
▪ ——材料新能提升:减少材料的复验。
GB150.4 《压力容器-制造、检验和验收》
——“基于风险(失效模式)的压力容器设计、制造与检 验”技术的应用:制造过程中的失效预防与控制。 ▪ ——封头成形技术提升:限制褶皱,采用全尺寸样板检 查形状。 ▪ ——焊接技术与装备提高:提高焊接工艺评定要求,减 少产品焊接试件数量。 ▪ ——检验技术开发:壳体直线度检查、TOFD检测技术、 气液组合压力试验…… ▪ ——相关标准修订与进步:NB/T 47014《承压设备焊接 工艺评定》等
GB150.4 《压力容器-制造、检验和验收》
▪ GB150.4-2011 ▪
压力容器 ▪
第4部分:制造、检验和验收 ▪ 2012.03.11
GB150.4 《压力容器-制造、检验和验收》
▪ 二、修订过程
▪ — 2010年1月6日海口会议
▪
增列钢带错绕容器
▪ — 2010年3月合肥会议
▪
并入低温容器
PED的安全基本要求,全面提出了基于失效模式设计的理 念,在设计准则、计算方法、制造检验要求等方面引入了 现代技术研究的成果。对促进贸易和提高竞争力起到了重 要的作用。 ▪ 在美国、澳大利亚和其他国家也相继修订了原有的技术 标准体系。 ▪ 相应降低了安全系数,使我国面临国外压力容器产品的 冲击,需合理修订标准(如容器分类,设计与制造阶段的 风险评估与控制,材料复验,产品焊接试件要求等),提 高中国压力容器产品的质量和国际竞争力。
压力容器定期检验与验收标准

压力容器定期检验与验收标准一、引言压力容器是工业生产过程中不可或缺的设备之一,其作用是在容器内部施加压力,使其容纳液体、气体或其他物质。
由于压力容器在工作过程中承受巨大的压力,因此必须进行定期检验和验收,以确保其安全运行以及防止可能的事故发生。
本文将介绍压力容器的定期检验与验收标准,以提供参考和指导。
二、压力容器定期检验标准1. 检验时间间隔压力容器的定期检验时间间隔应根据容器的设计、工作条件、使用环境等因素进行评估,并遵守相关的法律法规和标准要求。
一般情况下,压力容器的定期检验时间间隔不得超过两年。
2. 检验内容a. 容器外观检验检查容器表面是否有腐蚀、变形、泄漏等情况。
b. 材料检验对容器的材料进行检验,包括厚度测量、化学成分分析等。
c. 接口密封性检验检查容器连接部位的密封性,确保没有泄漏。
d. 阀门和安全装置检验对压力容器的阀门和安全装置进行检验,确保其正常运行和可靠性。
e. 强度计算和试验进行强度计算和试验,评估容器的承受能力和安全性。
f. 内部清洁和除锈清洁容器内部,并进行必要的除锈处理,防止腐蚀和生锈。
3. 检验记录和报告对于每次定期检验,应制作详细的检验记录和报告,记录检验的内容、方法、结果和建议等信息,并加盖检验单位的公章和签字。
三、压力容器验收标准1. 验收依据对于新建的压力容器,其验收应根据相关的法律法规和标准要求进行,包括国家标准《压力容器验收规程》等。
2. 验收内容a. 材料证明文件的检查检查容器材料的合格证明文件,包括材料合格证、化学分析报告等。
b. 容器外观检验检查容器表面是否完整,无腐蚀、变形等情况。
c. 容器安装检验检查容器的安装情况,包括支座、管线布置、阀门和安全装置的安装等。
d. 容器试压对容器进行试压,确保容器的密封性和强度。
e. 容器标志和铭牌检查检查容器的标志和铭牌是否齐全、清晰可见。
3. 验收记录和报告对于每次验收,应制作详细的验收记录和报告,记录验收的内容、结果、建议等信息,并加盖验收单位的公章和签字。
GB150.4制造与检验部分
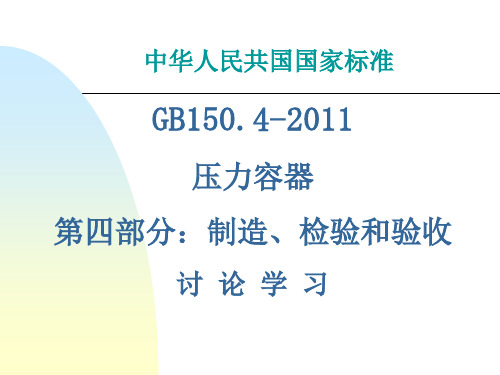
6.冷热加工成形与组装
6.1 成形 6.1.1 制造单位应根据制造工艺确定加工余量,以确 保受压元件成形后的实际厚度不小于设计图样标注 的最小成形厚度。 6.1.2 采用经过正火、正火加回火或调质处理的钢材 制造的受压元件,宜采用冷成形或温成形;采用温 成形时,须避开钢材的回火脆性温度区。
回火脆性 :是指淬火钢回火后出现韧性下降的现象。淬火 钢在回火时,随着回火温度的升高,硬度降低,韧性升高, 但是在许多钢的回火温度与冲击韧性的关系曲线中出现了两 个低谷,一个在 200~400℃之间,另一个在450~650℃之间。 回火脆性可分为第一类回火脆性和第二类回火脆性。
6.冷热加工成形与组装
第一类回火脆性又称不可逆回火脆性,低温回火脆性,主 要发生在回火温度为 250~400℃时, 1.特征 (1)具有不可逆性; (2)与回火后的冷却速度无关; (3)断口为沿晶脆性断口。 2.防止方法 避免这个温度范围内回火,没有能够有效抑制产生这种回 火脆性的合金元素。
6.冷热加工成形与组装
6.冷热加工成形与组装
6.5.2 在焊接接头环向、轴向形成的棱角E,宜分别 用弦长等于Di/6,且不小于300mm的内样板(或 外样板)和直尺检查(见图5、图6),其E值不得 大于(δs/10+2)mm,且不大于5mm。
压力容器验收记录
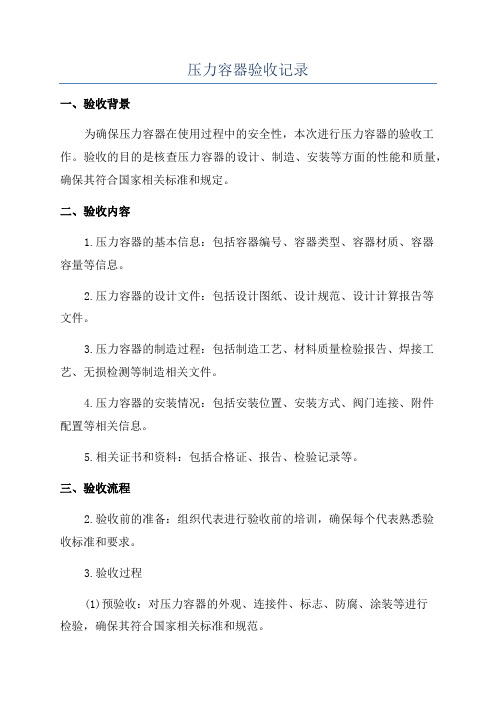
压力容器验收记录一、验收背景为确保压力容器在使用过程中的安全性,本次进行压力容器的验收工作。
验收的目的是核查压力容器的设计、制造、安装等方面的性能和质量,确保其符合国家相关标准和规定。
二、验收内容1.压力容器的基本信息:包括容器编号、容器类型、容器材质、容器容量等信息。
2.压力容器的设计文件:包括设计图纸、设计规范、设计计算报告等文件。
3.压力容器的制造过程:包括制造工艺、材料质量检验报告、焊接工艺、无损检测等制造相关文件。
4.压力容器的安装情况:包括安装位置、安装方式、阀门连接、附件配置等相关信息。
5.相关证书和资料:包括合格证、报告、检验记录等。
三、验收流程2.验收前的准备:组织代表进行验收前的培训,确保每个代表熟悉验收标准和要求。
3.验收过程(1)预验收:对压力容器的外观、连接件、标志、防腐、涂装等进行检验,确保其符合国家相关标准和规范。
(2)技术验收:对压力容器的压力试验、安全附件、泄漏检测、阀门测试等进行检验。
(3)焊接质量验收:对压力容器的焊接接头进行检验,包括焊缝的质量、外观、尺寸、无损检测等。
(4)功能验收:对压力容器进行功能测试,包括泄漏试验、防爆性能测试等。
(5)文件验收:核查相关文件和证书的真实性、完整性、合法性。
4.验收结果:根据实际情况,结合检查结果,填写验收记录,并评定验收结果。
5.验收总结:对本次验收的过程进行总结,提出不足之处和改进意见。
四、验收结果及建议本次压力容器的验收结果如下:1.设计文件:设计文件齐全,符合国家相关标准和规范。
2.制造过程:制造过程符合相关标准和规范,各项制造工艺和材料质量达到要求。
3.安装情况:压力容器的安装位置、安装方式、阀门连接等均符合设计要求。
4.相关证书和资料:各项证书和资料齐全,真实有效。
根据以上验收结果,对压力容器的使用情况提出以下建议:1.在使用过程中,加强对压力容器的保养和维护,定期进行检查,及时发现和处理问题。
2.配备专业人员进行操作,定期进行技术培训,提高使用人员的安全意识和操作水平。
压力容器制造检验和验收

验收标准:根据国家相关标准 进行验收
验收内容:包括外观、尺寸、 材质、焊接质量等
验收方法:采用目测、测量、 无损检测等方法
验收问题:如发现质量问题, 应及时记录并采取相应措施进 行处理,如返修、更换等
PART FOUR
检验和验收是确保压力容器安全性 能的重要环节
检验和验收可以确保设备符合国家 标准和行业规范,提高设备性能
寸
焊接:将切割 好的材料焊接 在一起,形成 压力容器的主
体结构
热处理:对焊 检验:对压力
接后的压力容 容器进行检验,
器进行热处理, 确保其符合设
提高其强度和 计要求和安全
韧性
பைடு நூலகம்
标准
验收:对检验 合格的压力容 器进行验收, 确认其符合使
用要求
材料检验:包括化学成分、力学性能、 无损检测等
焊接检验:包括焊缝外观、焊缝尺寸、 焊缝内部质量等
PART THREE
检查压力 容器的外 观和结构 是否完好
检查压力 容器的焊 接质量是 否符合标 准
检查压力 容器的密 封性能是 否合格
检查压力 容器的安 全附件是 否齐全有 效
检查压力 容器的铭 牌和标识 是否清晰 完整
检查压力 容器的检 验报告和 合格证是 否齐全有 效
压力容器的制造和检验必须 符合国家相关标准和规范
汇报人:
尺寸测量:使用测量工具测量 压力容器的尺寸是否符合设计 要求
压力测试:使用压力测试设备 对压力容器进行压力测试,确 保其能够承受设计压力
泄漏测试:使用泄漏测试设备 对压力容器进行泄漏测试,确 保其没有泄漏现象
材料检测:使用材料检测设备 对压力容器的材料进行检测, 确保其符合设计要求
压力容器制造检验验收制度14
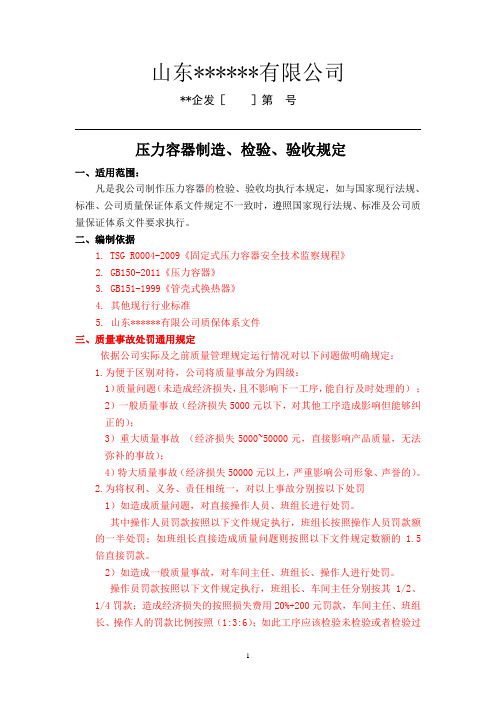
山东******有限公司**企发[]第号压力容器制造、检验、验收规定一、适用范围:凡是我公司制作压力容器的检验、验收均执行本规定,如与国家现行法规、标准、公司质量保证体系文件规定不一致时,遵照国家现行法规、标准及公司质量保证体系文件要求执行。
二、编制依据1. TSG R0004-2009《固定式压力容器安全技术监察规程》2. GB150-2011《压力容器》3. GB151-1999《管壳式换热器》4. 其他现行行业标准5. 山东******有限公司质保体系文件三、质量事故处罚通用规定依据公司实际及之前质量管理规定运行情况对以下问题做明确规定:1.为便于区别对待,公司将质量事故分为四级:1)质量问题(未造成经济损失,且不影响下一工序,能自行及时处理的);2)一般质量事故(经济损失5000元以下,对其他工序造成影响但能够纠正的);3)重大质量事故(经济损失5000~50000元,直接影响产品质量,无法弥补的事故);4)特大质量事故(经济损失50000元以上,严重影响公司形象、声誉的)。
2.为将权利、义务、责任相统一,对以上事故分别按以下处罚1)如造成质量问题,对直接操作人员、班组长进行处罚。
其中操作人员罚款按照以下文件规定执行,班组长按照操作人员罚款额的一半处罚;如班组长直接造成质量问题则按照以下文件规定数额的 1.5倍直接罚款。
2)如造成一般质量事故,对车间主任、班组长、操作人进行处罚。
操作员罚款按照以下文件规定执行,班组长、车间主任分别按其1/2、1/4罚款;造成经济损失的按照损失费用20%+200元罚款,车间主任、班组长、操作人的罚款比例按照(1:3:6);如此工序应该检验未检验或者检验过程中未发现隐患,则检验员按班组长罚款数额执行罚款。
3)如造成重大质量事故,对生产部部长、车间主任、班组长、操作人、检验员进行处罚。
根据对公司经济损失的情况,按核实损失费用的20%罚款。
其中生产部部长、车间主任、检验员共同承担罚款总额的80%,其余班组长、操作人员承担。
压力容器的制造工艺要求与检验程序

压力容器的制造工艺要求与检验程序1. 引言压力容器是广泛应用于化工、石油、电力等工业领域的重要设备。
由于其承受高压力和容纳有害物质的特性,压力容器的制造工艺和检验程序至关重要。
本文将针对压力容器的制造工艺要求和检验程序进行探讨,旨在加强对该领域的认识和理解。
2. 材料选择与预处理在压力容器的制造过程中,材料的选择和预处理是首要考虑的因素之一。
常用的材料有碳钢、合金钢、不锈钢等。
选择材料时,需要考虑其耐压性能、耐腐蚀性能和可焊性等因素。
同时,材料需要进行预处理,如除油、除杂质等,以确保材料表面的清洁度和平整度。
3. 制造工艺要求制造工艺是确保压力容器安全可靠运行的关键。
首先是板料的切割和形状制作,要求精确度高、尺寸符合设计要求。
接下来是板材的弯曲成型和焊接工艺,需要保证焊缝的强度和密封性。
此外,还需要进行液压试验、气密性测试等环节,确保容器的耐压性能。
4. 焊接工艺与监测焊接是压力容器制造过程中最关键的环节之一。
焊接工艺的选择要根据容器的材料和设计要求确定,同时需要使用合适的焊接材料和焊接设备。
在焊接过程中,需要进行焊缝的监测和检测,如超声波检测、射线检测等,以确保焊缝的质量和完整性。
5. 表面处理与防腐压力容器的表面处理和防腐是确保其使用寿命和性能的重要环节。
表面处理包括除锈、喷砂、喷漆等过程,以保证容器表面的光洁度和耐腐蚀性。
防腐措施主要包括涂层、包覆材料等,以提高容器的抗腐蚀性能和稳定性。
6. 安全附件与连接压力容器的安全附件和连接部件是确保其安全运行和维护的关键部分。
安全附件如安全阀、压力表等可以监测容器的压力和温度变化,确保在超出设计范围时能及时采取相应措施。
连接部件如法兰、螺纹等也需要采用符合标准的材料和工艺,确保其牢固性和密封性。
7. 检验程序与质量控制压力容器的检验程序和质量控制是确保其安全性和可靠性的重要手段。
在制造过程中,需要根据国家标准和相关规定进行各种检验和测试,如焊缝检验、压力测试、泄漏测试等,确保容器符合要求。
压力容器制造检验与验收
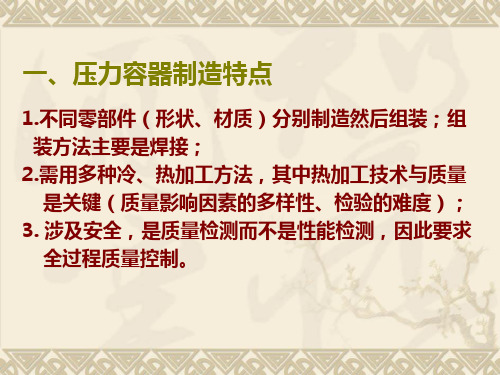
力学性能-焊接工艺评定、产品焊接试板 焊接缺陷-无损检测 外观质量-宏观检查
三、焊接
3.力学性能
焊接工艺评定 ➢ 作用-事先预防与指导;节约 ➢ 评定的做法与要求 产品焊接试板 ➢ 作用-事后检查 ➢ 制备条件与数量
➢ 制备要求-代表性 ➢ 检验-JB4744
三、焊接
4.焊接缺陷
缺陷的种类 咬边 ➢ 咬边的成因与危害; ➢ 咬边的检查-宏观检查;
一、压力容器制造特点
1.不同零部件(形状、材质)分别制造然后组装;组 装方法主要是焊接;
2.需用多种冷、热加工方法,其中热加工技术与质量 是关键(质量影响因素的多样性、检验的难度);
3. 涉及安全,是质量检测而不是性能检测,因此要求 全过程质量控制。
二、结构设计(选择)的重要性
1.结构是决定安全性与经济性的主要因素;结构是计 算的基础;应注意纠正轻结构重计算的倾向;
量;保证焊透;
二、结构设计(选择)的重要性
3.结构设计的若干实例
焊接结构 ➢ 焊接结构设计基本要求:方便施焊与检验;减少焊接工作
量;保证焊透; ➢ 焊接结构设计特点:与工人技术、习惯密切相关,属非强
制性要求。 对国外结构设计的思考 ➢ 球罐人孔的数量 ➢ 罐车安全阀的设置
三、焊接
1.焊接接头与母材的区别 2.焊接质量要素与对策
四、热处理
1.热处理(按目的)的分类
焊后(消除应力)热处理 ➢ 目的 ➢ 焊接应力产生的原因、特点及危害 ➢ 焊后热处理的条件
通用条件-厚度、材质与预热温度 特殊条件-图样注明应力腐蚀;盛装毒性极度、高度危害
介质;
无需进行的条件-奥氏体不锈钢
四、热处理
1.热处理(按目的)的分类
GB150-2011压力容器-制造、检验和验收

▪ 1.3 对于奥氏体型钢材质低温压力容器(设计温度低于196℃),有参与建造的各方协商规定附加的制造、检验 与验收要求,由设计单位在设计文件中予以规定。
▪ — 2010年6月北京会议
▪
处理网评意见211条,初步形成送审稿
▪ — 2010年11月
▪
处理送审意见78条,形成报批稿草稿
▪ — 2011年7月征求WTO成员国意见并修改定稿
GB150.4 《压力容器-制造、检验和验收》
▪ 三、修订背景
▪ (1)适应GB 150-1998颁布13年来中国发生的技术和管理变化
GB150.4 《压力容器-制造、检验和验收》
六、GB 150.4条文及释义
对应GB 150-1998条文 10 制造、检验与验收 10.1 总则 10.1.1 本章适用于单层焊接、多层包扎、热套及锻焊压 力容器。对于设计温度低于或者等于-20℃的容器, 还应符合附录C(标准的附录)的规定。
C1.1 本附录适用于设计温度低于或者等于-20℃钢制低 温压力容器(以下简称“低温容器”)的设计、制造、 检验与验收。
GB150.4 《压力容器-制造、检验和验收》
▪ 新增条款:主要变化或释义:
▪ 受益于我国压力容器行业整体技术水平的提 升,我国引入并开始实施先进的“基于风险的压 力容器设计、制造与检验”的理念和方法、该方 法的核心内容是:在压力容器设计使用年限内, 结合同类或类似容器曾出现过、或考虑容器全寿 命过程中动态服役条件下可能出现的各种失效模 式和损伤机理产生的风险对安全性与寿命的影响, 通过合理选材、改进结构设计,优化制造和检验 工艺等措施,在设计、制造过程中预先控制和降 低风险,使其安全服役到预定的使用年限。
GB150-2011压力容器第4部分:制造、检验和验收试题
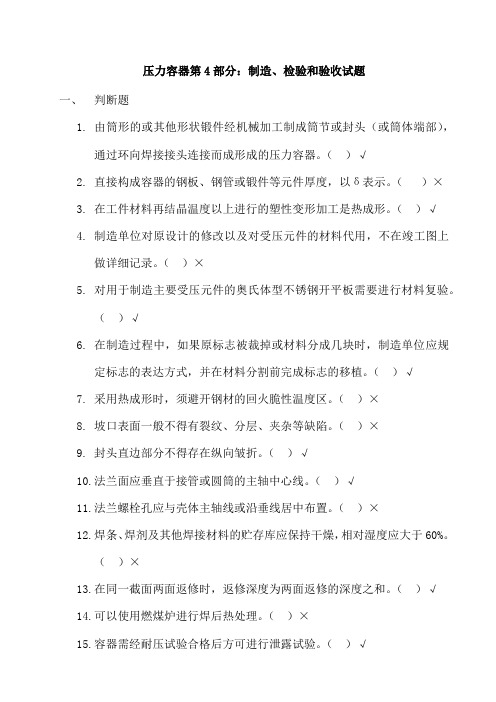
压力容器第4部分:制造、检验和验收试题一、判断题1.由筒形的或其他形状锻件经机械加工制成筒节或封头(或筒体端部),通过环向焊接接头连接而成形成的压力容器。
()√2.直接构成容器的钢板、钢管或锻件等元件厚度,以δ表示。
()×3.在工件材料再结晶温度以上进行的塑性变形加工是热成形。
()√4.制造单位对原设计的修改以及对受压元件的材料代用,不在竣工图上做详细记录。
()×5.对用于制造主要受压元件的奥氏体型不锈钢开平板需要进行材料复验。
()√6.在制造过程中,如果原标志被裁掉或材料分成几块时,制造单位应规定标志的表达方式,并在材料分割前完成标志的移植。
()√7.采用热成形时,须避开钢材的回火脆性温度区。
()×8.坡口表面一般不得有裂纹、分层、夹杂等缺陷。
()×9.封头直边部分不得存在纵向皱折。
()√10.法兰面应垂直于接管或圆筒的主轴中心线。
()√11.法兰螺栓孔应与壳体主轴线或沿垂线居中布置。
()×12.焊条、焊剂及其他焊接材料的贮存库应保持干燥,相对湿度应大于60%。
()×13.在同一截面两面返修时,返修深度为两面返修的深度之和。
()√14.可以使用燃煤炉进行焊后热处理。
()×15.容器需经耐压试验合格后方可进行泄露试验。
()√二、填空题1.冷加工是在工件材料再结晶温度以下进行的加工。
(塑性变形)2.介于冷成形和热成形之间的塑性变形加工称为。
(温成形)3.当采用其他方法消除压力容器及其受压元件参与应力时,应按照TSGR0004的规定进行。
(技术评审)4.有耐腐蚀要求的以及板,不得在耐腐蚀面采用钢印标记。
(不锈钢、复合钢)5.制造中应避免材料表面的。
(机械损伤)6.施焊前,应清除坡口及两侧母材表面至少20mm范围内的、、及其他有害杂质。
(氧化皮、油污、熔渣)7.螺孔的螺纹精度一般为精度,或按相关标准选取。
(中等)8.容器受压元件的组装中不得强力进行、等。
- 1、下载文档前请自行甄别文档内容的完整性,平台不提供额外的编辑、内容补充、找答案等附加服务。
- 2、"仅部分预览"的文档,不可在线预览部分如存在完整性等问题,可反馈申请退款(可完整预览的文档不适用该条件!)。
- 3、如文档侵犯您的权益,请联系客服反馈,我们会尽快为您处理(人工客服工作时间:9:00-18:30)。
压力容器制造、检验与验收
一、压力容器制造特点
1.不同零部件(形状、材质)分别制造然后组装;组装方法主要是焊接;2.需用多种冷、热加工方法,其中热加工技术与质量是关键(质量影响因素的多样性、检验的难度);
3.涉及安全,是质量检测而不是性能检测,因此要求全过程质量控制。
二、结构设计(选择)的重要性
1.结构是决定安全性与经济性的主要因素;结构是计算的基础;应注意纠正轻结构重计算的倾向;
2.结构设计的基本要求:适用(满足使用要求);安全;经济性。
三者往往是矛盾的,好的设计在于求得辩证统一。
3.结构设计的若干实例
3.1 不等厚对接
3.2 倒圆、倒角
3.3 法兰螺栓通孔跨中均布
3.4 地脚螺栓孔的要求
3.5 焊接结构
a.焊接结构设计基本要求:方便施焊与检验;减少焊接工作量;保证焊透;
b.焊接结构设计特点:与工人技术、习惯密切相关,属非强制性要求。
3.6 对国外结构设计的思考
a.球罐人孔的数量
b.罐车安全阀的设置
三、焊接
1.焊接接头与母材的区别
2.焊接质量要素与对策
2.1 力学性能~焊接工艺评定、产品焊接试板
2.2 焊接缺陷~无损检测
2.3 外观质量~宏观检查
3.力学性能
3.1 焊接工艺评定
a.作用~事先预防与指导;节约
b.评定的做法与要求
3.2 产品焊接试板
a.作用~事后检查
b.制备条件与数量
c.制备要求~代表性
d.检验~JB4744
4.焊接缺陷
4.1 缺陷的种类
4.2 咬边
a.咬边的成因与危害;
b.咬边的检查~宏观检查;
c.标准对咬边的要求
5.外观质量
5.1 错边
a.错边的成因与防治:A类接头~对齐;B类接头~外圆周长;局部不圆。
b.错边的危害:厚度减薄;形状突变。
c.错边的测量:一般外壁;复合板内壁。
5.2 棱角
a.棱角的成因与防治~焊接变形
b.棱角的危害
5.3 焊缝余高
a) 余高的作用
b) 余高的危害
c) 标准对余高的要求
6.中外产品质量的主要差别~外观质量
四、热处理
1.热处理(按目的)的分类
1.1 焊后(消除应力)热处理
a.目的
b.焊接应力产生的原因、特点及危害
c.焊后热处理的条件
通用条件~厚度、材质与预热温度
特殊条件~图样注明应力腐蚀;盛装毒性极度、高度危害介质;无需进行的条件~奥氏体不锈钢
1.2 恢复力学性能热处理
a.冷作硬化的原因及危害
b.冷、中温卷筒热处理的条件
c.冷成形封头热处理(奥氏体不锈钢除外)
1.3 改善材料力学性能热处理
1.4 消氢处理
2.焊后热处理方法~整体炉内;分段炉内;局部;现场
3.焊后热处理工艺~进、出炉炉温;升、降温速度;炉内气氛;炉外冷却五、无损检测
1.不同方法的特点及选择
1.1 射线、超声、磁粉、渗透之特点
1.2 正确选择方法是设计者的责任
1.3 选择时建议考虑的因素
a.材质;b.结构;c.厚度;d.方法
2.A、B类焊接接头无损检测长度的选择
2.1 100%射线或超声检测的条件
a.厚度(P、D)~安全性、重要性、经济性
b.材质~可焊性、同一缺陷对不同材质的不同影响、重要性、经济性
c.产品的安全要求~事故后果的灾难性
d.结构的特殊性
2.2 局部射线与超声检测
a.局部检测的含义与目的
b.局部检测产品中应100%检测的部位(开孔、被复盖的接头、凸形封头拼缝、嵌入式接管、D≥250mm的接管对接)。
3.对局部检测的正确理介与执行
3.1 对制造方和使用方的要求
3.2 对P128中注的解释
4.关于不同方法的复探
5.设计者对无损检测的要求
六、耐压与气密性试验
1.耐压试验
1.1 目的
a) 内压~考核验证强度,检漏;
b) 外压(真空)~检漏。
1.2 液压、气压危险性的差异
a) 液压~能量(P×V)、金属碎片;
b) 气压~能量(P×V)、金属碎片、冲击波。
1.3 允许气压的条件
a) 因承重无法液压;
b) 液体无法排净吹干,生产不允许残留液体。
2.气密性试验
2.1 目的~检漏
2.2 需做气密的条件
a) 毒性介质不允许泄漏;
b) 生产工艺不允许泄漏。
2.3 试验压力与介质有关
2.4 气压合格后是否还需气密与介质有关
2.5 检漏方法与合格指标。