重型车床刀具及切削用量的选择
重型车床刀具及切削用量

重型车床刀具及切削用量的选择1.引言重型机械加工行业的特点是被加工件的尺寸很大,重量很重(有的可达上百吨),因此重型加工用卧式车床的回转直径可达到6米,立式车床更可达到10余米。
与普通切削加工相比,由于重型切削加工具有切削深度大、切削速度低、进给速度慢等特点,因此其加工工艺与普通的机械切削加工工艺有很大不同,这些工艺问题包括刀具的选择、刀具的安装、切削用量的选择以及工件的装夹等各个方面。
本文对重型车床切削加工不同加工阶段的特点分别作如下论述。
2.刀具的选择机械加工中常用的刀具材料主要有高速钢、硬质合金、立方氮化硼(cbn)、陶瓷等。
由于重型切削的特点(切削深度大,余量不均,表面有硬化层),刀具在粗加工阶段的磨损形式主要是磨粒磨损。
由于切削温度高,尽管切削速度处于积屑瘤发生区,但高温可以使切屑与前刀面的接触部位处于液态,减小了摩擦力,抑制了积屑瘤的生成,所以刀具材料的选择应要求耐磨损、抗冲击,刀具涂层后硬度可达80hrc,具有高的抗氧化性能和抗粘结性能,因而有较高的耐磨性和抗月牙洼磨损能力。
硬质合金涂层具有较低的摩擦系数,可降低切削时的切削力及切削温度,可以大大提高刀具耐用度(涂层硬质合金刀片的耐用度至少可提高1倍)等优点,但由于涂层刀片的锋利性、韧性、抗剥落和抗崩刃性能均不及未涂层刀片,故不适用高硬度材料和重载切削的粗加工。
陶瓷类刀具硬度高,但抗弯强度低,冲击韧性差,不适用于余量不均的重型切削,cbn刀具同样也存在这个问题。
综合以上分析,只有硬质合金刀具适合于重型切削的粗加工。
硬质合金分为钨钴类(yg)、钨钴钛类(yt)和碳化钨类(yw)。
加工钢料时,由于金属塑性变形大,摩擦剧烈,切削温度高,yg类硬质合金虽然强度和韧性较好,但高温硬度和高温韧性较差,因此在重型切削中很少应用。
与之相比,yt类硬质合金刀具适于加工钢料,由于yt类合金具有较高的硬度和耐磨性,尤其是具有高的耐热性,抗粘结扩散能力和抗氧化能力也很好,在加工钢料时刀具磨损较小,刀具耐用度较高,因此yt类硬质合金是重型加工时较常用的刀具材料。
简述切削用量的选用原则。
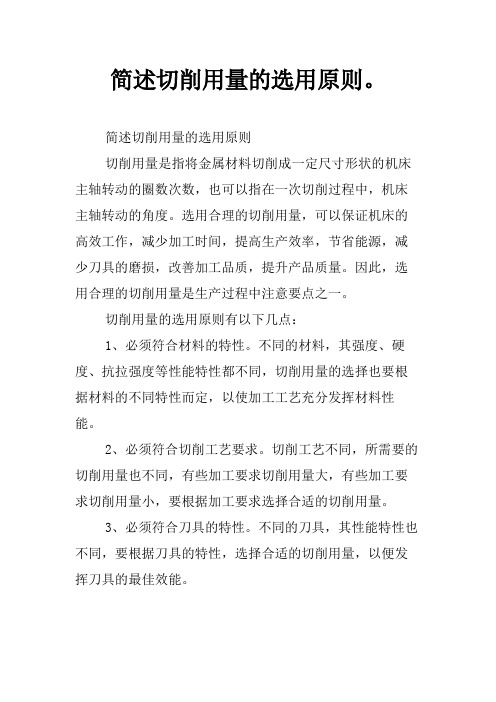
简述切削用量的选用原则。
简述切削用量的选用原则切削用量是指将金属材料切削成一定尺寸形状的机床主轴转动的圈数次数,也可以指在一次切削过程中,机床主轴转动的角度。
选用合理的切削用量,可以保证机床的高效工作,减少加工时间,提高生产效率,节省能源,减少刀具的磨损,改善加工品质,提升产品质量。
因此,选用合理的切削用量是生产过程中注意要点之一。
切削用量的选用原则有以下几点:1、必须符合材料的特性。
不同的材料,其强度、硬度、抗拉强度等性能特性都不同,切削用量的选择也要根据材料的不同特性而定,以使加工工艺充分发挥材料性能。
2、必须符合切削工艺要求。
切削工艺不同,所需要的切削用量也不同,有些加工要求切削用量大,有些加工要求切削用量小,要根据加工要求选择合适的切削用量。
3、必须符合刀具的特性。
不同的刀具,其性能特性也不同,要根据刀具的特性,选择合适的切削用量,以便发挥刀具的最佳效能。
4、必须符合机床的特性。
不同的机床,其转速、功率等性能特性也不同,切削用量的选择也要根据机床的特性来决定,以保证机床的最佳效能。
5、必须符合工件尺寸要求。
切削用量必须根据工件尺寸的大小来选择,如果工件尺寸较大,则切削用量越大,反之,切削用量越小。
6、必须符合加工精度要求。
当加工的精度越高时,切削用量就越少,而加工的精度越低时,切削用量就越大。
7、必须考虑切削方法的特点。
切削方法的特点包括:切削的深度和宽度,刀具的刃口形状,机床的转速,切削液的种类和流量等,这些都会影响切削用量的选择。
8、必须考虑切削液的特点。
不同的切削液具有不同的特性,要根据切削液的性质,选择适当的切削用量,以更好地发挥切削液的效用。
以上就是切削用量的选用原则的简介,要想使机床的加工效率达到最高,切削用量的选用是必不可少的,并且要根据不同材料、不同机床、不同刀具、不同加工工艺等多种因素,来确定适当的切削用量,以保证加工质量和加工效率。
刀具切削用量的选用
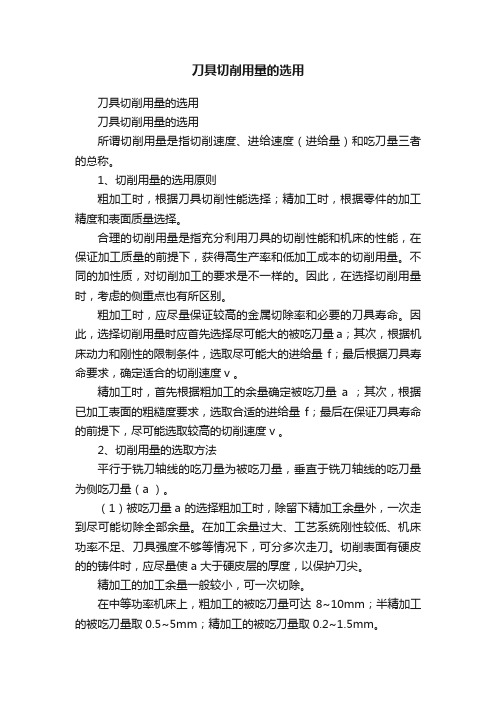
刀具切削用量的选用刀具切削用量的选用刀具切削用量的选用所谓切削用量是指切削速度、进给速度(进给量)和吃刀量三者的总称。
1、切削用量的选用原则粗加工时,根据刀具切削性能选择;精加工时,根据零件的加工精度和表面质量选择。
合理的切削用量是指充分利用刀具的切削性能和机床的性能,在保证加工质量的前提下,获得高生产率和低加工成本的切削用量。
不同的加性质,对切削加工的要求是不一样的。
因此,在选择切削用量时,考虑的侧重点也有所区别。
粗加工时,应尽量保证较高的金属切除率和必要的刀具寿命。
因此,选择切削用量时应首先选择尽可能大的被吃刀量a;其次,根据机床动力和刚性的限制条件,选取尽可能大的进给量f;最后根据刀具寿命要求,确定适合的切削速度v 。
精加工时,首先根据粗加工的余量确定被吃刀量a ;其次,根据已加工表面的粗糙度要求,选取合适的进给量f;最后在保证刀具寿命的前提下,尽可能选取较高的切削速度v 。
2、切削用量的选取方法平行于铣刀轴线的吃刀量为被吃刀量,垂直于铣刀轴线的吃刀量为侧吃刀量(a )。
(1)被吃刀量a 的选择粗加工时,除留下精加工余量外,一次走到尽可能切除全部余量。
在加工余量过大、工艺系统刚性较低、机床功率不足、刀具强度不够等情况下,可分多次走刀。
切削表面有硬皮的的铸件时,应尽量使 a 大于硬皮层的厚度,以保护刀尖。
精加工的加工余量一般较小,可一次切除。
在中等功率机床上,粗加工的被吃刀量可达8~10mm;半精加工的被吃刀量取0.5~5mm;精加工的被吃刀量取0.2~1.5mm。
(2)进给速度(进给量)的确定进给速度是数控机床切削用量中的重要参数,主要根据零件的加工精度和表面粗糙度要求以及刀具、工件的材料性质的选取,最大进给速度受机床刚度和进给系统的性能限制。
粗加工时,由于对工件的表面没有太高的要求,这时主要根据机床进给机构的强度和刚性、刀杆的强度和刚性、刀具材料、刀杆和工件尺寸以及选定的被吃刀量等因素来选取进给速度。
切削用量的选择原则

切削用量的选择原则
第一段:切削用量是不可缺少的切削参数,它需要用户根据切削要求,从许多切削可能量中进行选择,以使工件表面满足要求,并节约切削能耗。
本文旨在为熟悉切削用量的选择原则提供指导,以便于切削过程的有效控制。
第二段:切削用量的选择要根据工件材料、加工工艺、刀具结构和辅助设备等多种因素进行综合考虑。
首先,要考虑工件材料的加工性能。
材料的脆硬度、塑性弹性模量、耐磨损性、密度等参数,影响切削用量的选择,同样的材料,切削量的大小可能不同。
第三段:其次,要考虑加工工艺的不同,切削参数的选择要考虑加工的精度要求,especiallY对于高精度加工,比如微机雕刻,它要求切削误差极其小,切削用量需要减小,也就是说要使末端刀具和工件表面接触面积增加,以提高切削精度,但切向力也需要相应减小.第四段:接下来,要考虑刀具结构参数,尤其是刃口尺寸、形状和角度,它们直接影响切削刃的切向力、摩擦力和压痕深度等特性,从而影响切削用量的选择.比如对于高速钢加工,可以选择尖角度较钝的刃口,并采用更大切口尺寸,以降低切削刃的切入力,消除切削热.
第五段:最后,要考虑切削机床的驱动、辅助系统及其他因素,这些因素都会影响切削用量的选择.比如,利用液压机械手、磁浮支撑装置或向心力喷射装置等设备,可以减少刀具受到的横向切向力,从而提高切削精度,同时增大切削用量.
第六段:总之,切削用量的选择要按照工件材料、加工工艺、刀具结构和辅助设备等多种因素进行综合考虑,以确保加工工件的质量,确保切削过程的有效控制,以节约切削能耗.
第七段:由于切削用量对切削过程的控制有着至关重要的影响,因此需要用户熟悉切削用量的选择原则,才能做出正确的决定,以确保满足加工要求,同时节约切削能耗,提高切削效率。
切削用量的选择 1

切削用量的选择选择合理的切削用量,要综合考虑生产率、加工质量和加工成本。
一般地,粗加工时,由于要尽量保证较高的金属切除率和必要的刀具耐用度,应优先选择大的背吃刀量,其次选择较大的进给量。
最后根据刀具耐用度,确定合适的切削速度。
精加工时,由于要保证工件的加工质量,应选用较小的进给量和背吃刀量,并尽可能选用较高的切削速度。
(1)背吃刀量的选择粗加工的背吃刀量应根据工件的加工余量确定,在保留半精加工余量的前提下,应尽量用一次走刀就切除全部粗加工余量;当加工余量过大或工艺系统刚性过差时,可分二次走刀。
第一次走刀的背吃刀量,一般为总加工余量的2/3—3/4。
在加工铸、锻件时,应尽量使背吃刀量大于硬皮层的厚度,以保护刀尖。
半精、精加工的切削余量较小,其背吃刀量通常都是一次走刀切除全部余量。
(2)进给量的选择粗加工时,进给量的选择主要受切削力的限制。
在工艺系统刚度和强度良好的情况下,可选用较大的进给量值。
表1.4 为粗车时进给量的参考值。
由于进给量对工件的已加工表面粗糙度值影响很大,一般在半精加工和精加工时,进给量取得都较小。
通常按照工件加工表面粗糙度值的要求,根据工件材料、刀尖圆弧半径、切削速度等条件来选择合理的进给量。
当切削速度提高,刀尖圆弧半径增大,或刀具磨有修光刃时,可以选择较大的进给量,以提高生产率。
表 1.4 硬质合金及高速钢车刀粗车外圆和端面时的进给量注:1.加工断续表面及有冲击的加工时,表内的进给量应乘系数K=0.75~0.85。
2.加工耐热钢及其合金时,不采用大于1.0 mm/r 的进给量。
3.加工淬硬钢时,表内进给量应乘系数K=0.8(当材料硬度为44~56HRC)或K=0.5(当硬度为57~62HRC时)。
(3)切削速度的选择在背吃刀量和进给量选定以后,可在保证刀具合理耐用度的条件下,确定合适的切削速度。
粗加工时,背吃刀量和进给量都较大,切削速度受刀具耐用度和机床功率的限制,一般较低。
精加工时,背吃刀量和进给量都取得较小,切削速度主要受加工质量和刀具耐用度的限制,一般较高。
加工刀具和切削用量的选择

技师评审论文专业:数控车工浅谈数控加工中刀具选择和切削用量的确定姓名:刘胜华班级:074101学号:07指导老师:陈兵单位:江苏省盐城技师学院邮编:2240022010-3-17浅谈数控加工中刀具选择和切削用量的确定【摘要】:在切削加工中不仅要确定刀具的几何参数,还需选择切削用量的参数。
本文从加工零件的形状入手简单的讨论了数控加工中刀具的选择,从零件的加工质量和刀具的耐用度入手简单的讨论了切削用量的选择。
在切削深度A p和进给量F c初步选定后,合理的选择切削速度对切削效率和加工成本也有很大的影响。
【关键词】:数控加工;刀具选择;切削用量等。
无论在普通车床加工还是在数控加工中,刀具选择和切削用量的确定不仅影响加工效率,而且直接影响零件加工精度和表面粗糙度。
现在我们使用的许多机械设计与制造软件都提供自动编程功能,只要选择好所用的刀具、切削用量等有关的加工参数,就可以自动生成程序并传输至数控机床完成其加工。
这与普通车床的加工形成鲜明的对比,也是最大的不同点。
因此,本文在数控编程中必须面对的刀具如何选择和切削如何用量确定问题进行了论述。
一、数控加工常用刀具材料的类型及性能数控加工刀具必须适应数控机床高速旋转、高效率的特点,还需有较好的工艺性、经济性。
工具钢还应具有比较好的热处理工艺性。
在选择刀具材料时,很难找到各方面都很好的,因为材料硬度与韧性之间、综合性能和刀具价格之间都是相互制约的。
㈠、数控刀具的分类有多种方法具体如下。
1、根据结构可分为:整体式、镶嵌式。
2、根据制造刀具所用的材料可分为:高速钢刀具、硬质合金刀具、金刚石刀具、陶瓷刀具等。
3、从切削工艺上可分为:车削刀具、钻削刀具、铣削刀具等。
各类常用刀具材料的物理力学能如表1:表1各类常用刀具材料的物理力学性能材料种类相对密度硬度H R C抗弯能力冲击韧度导热率耐热性切削速度大体比值碳素钢7.6-8.160-652.16-----41.87200-2500.32-0.4合金7.5-760-6 2.35----41.8300-0.48-0.6钢.957400高速钢8.0-8.863-71.96-4.40.089-0.5715.7-25590-6902.1-3.2钨钴类14.3-15.389-91.51.08-2.160.02-0.0675-87.9800 3.15-4.76钨钛钴类9.35-13.29-92.50.789-1.20.03-0.0720.9-629004-4.8人造金刚石3.47-3.5610000.21-0.48-----146.54700-80025㈡刀具材料还应具备如下的性能:⑴高硬度刀具材料的硬度应大于工件材料的硬度,常温硬度应在H R C68以上;⑵足够的韧性承受较大切削力、冲击力;⑶高耐磨性刀具材料硬度越高,耐磨性越好;⑷高耐热性刀具材料在高温下保持硬度、耐磨性、强度和韧度的能力;⑸良好的工艺性与经济性二、数控加工中刀具的选择实际生产中,应考虑清楚硬质合金适合车削的材料、高速钢车刀适合车削什么样的材料。
切削用量的合理选择

切削用量的合理选择(2008-07-13 15:37:22)标签:刀具寿命用量生产率切削性能杂谈分类:数控刀具技术切削用量不仅是在机床调整前必须确定的重要参数,而且其数值合理与否对加工质量、加工效率、生产成本等有着非常重要的影响。
所谓“合理的”切削用量是指充分利用刀具切削性能和机床动力性能(功率、扭矩),在保证质量的前提下,获得高的生产率和低的加工成本的切削用量。
一制订切削用量时考虑的因素切削加工生产率在切削加工中,金属切除率与切削用量三要素ap、f、v均保持线性关系,即其中任一参数增大一倍,都可使生产率提高一倍。
然而由于刀具寿命的制约,当任一参数增大时,其它二参数必须减小。
因此,在制订切削用量时,三要素获得最佳组合,此时的高生产率才是合理的。
刀具寿命切削用量三要素对刀具寿命影响的大小,按顺序为v、f、ap。
因此,从保证合理的刀具寿命出发,在确定切削用量时,首先应采用尽可能大的背吃刀量;然后再选用大的进给量;最后求出切削速度。
加工表面粗糙度精加工时,增大进给量将增大加工表面粗糙度值。
因此,它是精加工时抑制生产率提高的主要因素。
二刀具寿命的选择原则切削用量与刀具寿命有密切关系。
在制定切削用量时,应首先选择合理的刀具寿命,而合理的刀具寿命则应根据优化的目标而定。
一般分最高生产率刀具寿命和最低成本刀具寿命两种,前者根据单件工时最少的目标确定,后者根据工序成本最低的目标确定。
选择刀具寿命时可考虑如下几点:根据刀具复杂程度、制造和磨刀成本来选择。
复杂和精度高的刀具寿命应选得比单刃刀具高些。
对于机夹可转位刀具,由于换刀时间短,为了充分发挥其切削性能,提高生产效率,刀具寿命可选得低些,一般取15-30min。
对于装刀、换刀和调刀比较复杂的多刀机床、组合机床与自动化加工刀具,刀具寿命应选得高些,尤应保证刀具可靠性。
车间内某一工序的生产率限制了整个车间的生产率的提高时,该工序的刀具寿命要选得低些;当某工序单位时间内所分担到的全厂开支M较大时,刀具寿命也应选得低些。
如何选择刀具与确定切削用量,以及如何确定对刀点

如何选择刀具与确定切削用量,以及如何确定对刀点
数控加工中刀具的选择与切削用量及对刀点的选择是重要内容,下面介绍如何选择刀具与确定切削用量,以及如何确定对刀点
1.刀具的选择与切削用量的确定
(1)刀具的选择
数控加工的刀具材料,要求采用新型优质材料,一般原则是尽可能选用硬质合金;精密加工时,还可选择性能更好更耐磨的陶瓷、立方氮化硼和金刚石刀具,并应优选刀具参数。
(2)切削用量的确定
合理选择切削用量的原则是:粗加工时,一般以提高生产率为主,但也应该考虑加工成本。
半精加工和精加工时,一般应在保证加工质量的前提下,兼顾切削效率和经济性和加工成本。
1)确定切削深度t(mm)。
在机床、工件和刀具刚度允许的情况下,应以最少的进给次数切除待加工余量,最好一次切除待加工余量,以提高生产效率。
2)确定切削速度V(m/min)。
加大切削速度,也能提高生产效率。
但提高生产效率的最有效措施还是应尽可能采用大的切削深度t。
3)确定进给速度f(mm/min或mm/r)。
进给速度是数控机床切削用量中的重要参数。
主要根据零件的加工精度和表面粗糙度要求以及刀具与零件的材料性质来选取。
当加工精度和表面粗糙度要求高时,进给速度f应该选择得小些。
最大进给速度受机床刚度和进给系统的性能决定,并与数控系统脉冲当量的大小有关。
2.对刀点和换刀点的确定
选择对刀点的原则是:
(1)选择的对刀点便与数学处理和简化程序编制;
(2)对刀点在机床上容易校准;
(3)加工过程中便于检查;
(4)引起的加工误差小。
转发到朋友圈吧,你的朋友也在找这篇文章呢!。
切削用量选择的基本原则
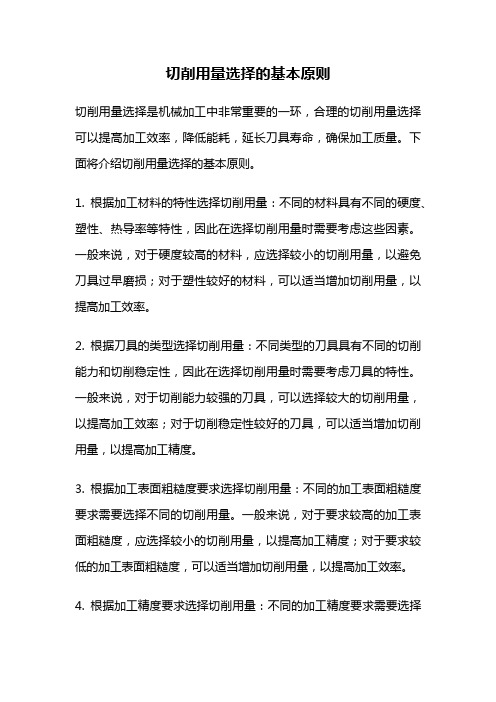
切削用量选择的基本原则切削用量选择是机械加工中非常重要的一环,合理的切削用量选择可以提高加工效率,降低能耗,延长刀具寿命,确保加工质量。
下面将介绍切削用量选择的基本原则。
1. 根据加工材料的特性选择切削用量:不同的材料具有不同的硬度、塑性、热导率等特性,因此在选择切削用量时需要考虑这些因素。
一般来说,对于硬度较高的材料,应选择较小的切削用量,以避免刀具过早磨损;对于塑性较好的材料,可以适当增加切削用量,以提高加工效率。
2. 根据刀具的类型选择切削用量:不同类型的刀具具有不同的切削能力和切削稳定性,因此在选择切削用量时需要考虑刀具的特性。
一般来说,对于切削能力较强的刀具,可以选择较大的切削用量,以提高加工效率;对于切削稳定性较好的刀具,可以适当增加切削用量,以提高加工精度。
3. 根据加工表面粗糙度要求选择切削用量:不同的加工表面粗糙度要求需要选择不同的切削用量。
一般来说,对于要求较高的加工表面粗糙度,应选择较小的切削用量,以提高加工精度;对于要求较低的加工表面粗糙度,可以适当增加切削用量,以提高加工效率。
4. 根据加工精度要求选择切削用量:不同的加工精度要求需要选择不同的切削用量。
一般来说,对于要求较高的加工精度,应选择较小的切削用量,以提高加工精度;对于要求较低的加工精度,可以适当增加切削用量,以提高加工效率。
5. 根据切削热量选择切削用量:切削过程中会产生大量的热量,如果切削用量选择不当,会导致切削热量过大,影响加工质量。
因此,在选择切削用量时需要注意控制切削热量,避免过热引起刀具磨损和工件变形。
6. 根据加工环境选择切削用量:加工环境对切削用量也有一定的影响。
例如,如果加工环境温度较高,应适当减小切削用量,以避免切削热量过大;如果加工环境湿度较大,应选择较大的切削用量,以提高切削稳定性。
切削用量选择的基本原则是根据加工材料特性、刀具类型、加工表面粗糙度要求、加工精度要求、切削热量和加工环境等因素综合考虑,选择合适的切削用量,以达到提高加工效率、降低能耗、延长刀具寿命和确保加工质量的目的。
切削用量选用原则

切削用量选用原则切削用量是指在加工过程中对工件进行切削时所使用的切削刀具、刀具材料、切削速度、进给量等参数的选择和调整。
合理选用切削用量是提高加工效率、保证加工质量和延长切削工具寿命的重要因素之一。
本文将从切削刃数、切削深度、切削速度、进给量和切削方式等方面介绍切削用量选用的原则。
一、切削刃数的选择原则切削刃数是指刀具上的切削刃数目。
切削刃数的选择应根据工件材料和加工要求进行。
对于硬度较高的材料,应选用切削刃数少、刀具强度大的刀具,以提高刀具的抗断裂能力和刀具寿命;对于材料硬度较低的工件,可以选用切削刃数多的刀具,以提高切削效率。
二、切削深度的选择原则切削深度是指刀具在每次切削中所能切削的最大距离。
切削深度的选择应根据工件材料、刀具强度和加工要求来确定。
一般情况下,切削深度应尽可能大,以提高切削效率。
但是,在选择切削深度时也要考虑刀具的抗断裂能力和加工表面质量,避免过大的切削深度导致刀具断裂或加工表面粗糙。
三、切削速度的选择原则切削速度是指刀具在切削过程中的线速度。
切削速度的选择应根据刀具材料、工件材料和加工要求来确定。
切削速度过高会导致刀具过热,影响切削质量和刀具寿命;切削速度过低则会降低切削效率。
因此,切削速度的选择应综合考虑切削质量、刀具寿命和切削效率的要求。
四、进给量的选择原则进给量是指刀具在单位时间内沿着工件表面移动的距离。
进给量的选择应根据工件材料、切削刃数和加工要求来确定。
进给量过大会导致切削力过大,影响加工表面质量和刀具寿命;进给量过小则会降低切削效率。
因此,进给量的选择应综合考虑切削力、加工表面质量和切削效率的要求。
五、切削方式的选择原则切削方式包括顺向切削、逆向切削和侧向切削等。
切削方式的选择应根据工件形状、切削刃数和加工要求来确定。
顺向切削适合于切削刃数少、工件表面平整度要求高的情况;逆向切削适合于切削刃数多、切削力大的情况;侧向切削适合于切削刃数多、工件形状复杂的情况。
切削方式的选择应综合考虑加工要求、切削质量和切削效率。
切削用量的选择原则、方法
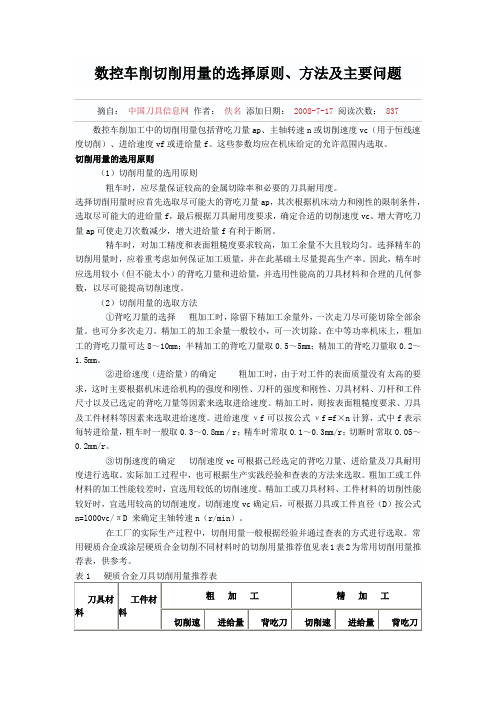
●螺纹加工程序段中指令的螺距值,相当于以进给量f(mm/r)表示的进给速度vf。如果将机床的主轴转速选择过高,其换算后的进给速度vf (mm/min)则必定大大超过正常值。
●刀具在其位移过程的始终,都将受到伺服驱动系统升降频率和数控装置插补运算速度的约束,由于升降频率特性满足不了加工需要等原因,则可能因主进给运动产生出的“超前”和“滞后”而导致部分螺牙的螺距不符合要求。
进给量(mm/r)
背吃刀量mm
硬质合金或涂层硬质合金
碳钢
220
0.2
3
260
0.l
0.4
低合金刚
1800.23来自2200.l0.4
高合金钢
120
0.2
3
160
0.l
0.4
铸铁
80
0.2
3
120
0.l
0.4
不锈钢
80
0.2
2
60
0.l
0.4
钛合金
40
0.2
1.5
150
0.l
0.4
灰铸铁
120
0.2
2
120
粗车时,应尽量保证较高的金属切除率和必要的刀具耐用度。
选择切削用量时应首先选取尽可能大的背吃刀量ap,其次根据机床动力和刚性的限制条件,选取尽可能大的进给量f,最后根据刀具耐用度要求,确定合适的切削速度vc。增大背吃刀量ap可使走刀次数减少,增大进给量f有利于断屑。
精车时,对加工精度和表面粗糙度要求较高,加工余量不大且较均匀。选择精车的切削用量时,应着重考虑如何保证加工质量,并在此基础土尽量提高生产率。因此,精车时应选用较小(但不能太小)的背吃刀量和进给量,并选用性能高的刀具材料和合理的几何参数,以尽可能提高切削速度。
加工中刀具的选择与切削用量的确定

加工中刀具的选择与切削用量的确定在加工过程中,刀具的选择和切削用量的确定是非常重要的。
正确选择合适的刀具和确定合理的切削用量,可以提高加工效率、保证产品质量、延长刀具寿命,降低加工成本。
下面将从加工材料、切削参数和刀具选择等方面探讨加工中刀具的选择与切削用量的确定。
一、加工材料对刀具选择和切削用量的影响在加工过程中,加工材料是选择刀具和确定切削用量的重要依据。
加工材料的硬度、韧性、热导率等性质直接影响了刀具的选择和切削用量的确定。
1. 硬度:对于硬度较高的材料,如钢材,通常需要采用更硬的刀具,例如硬质合金刀具或陶瓷刀具。
同时,由于硬度高的材料切削时容易产生热量,因此需要相应地增加切削用量,以提高切削效率。
2. 韧性:对于韧性较好的材料,如铸铁,切削时容易产生切削力和切削温度较高。
因此,选择耐磨性好、抗冲击性好的刀具,以提高切削质量和刀具寿命。
3. 热导率:热导率高的材料在切削过程中很容易导致刀具温度的升高,因此需要针对这些材料采取相应的散热措施,例如降低切削用量、增加切削冷却液的喷射量等。
二、切削参数对刀具选择和切削用量的影响除了加工材料之外,切削参数也是选择刀具和确定切削用量的重要参考依据。
切削速度、进给量和切削深度等参数的选择直接影响了切削过程的质量和效率。
1. 切削速度:切削速度是切削工件单位时间内通过刀具的线速度。
切削速度的选择取决于刀具材料和工件材料等因素。
对于硬度较高的材料,切削速度较低;而对于韧性较好的材料,切削速度较高。
正确选择切削速度可以保证刀具和工件的寿命。
2. 进给量:进给量是刀具每转一周(或每行进一定距离)切削工件的材料数量。
进给量的选择与刀具的负荷和工件的表面质量有关。
过大的进给量容易导致切削力过大,影响刀具寿命;而过小的进给量则会降低切削效率。
3. 切削深度:切削深度是刀具在单位时间内切削工件的材料厚度。
切削深度的选择取决于工件的材料和加工要求等因素。
较大的切削深度可以提高切削效率,但也会增加切削力和切削温度,影响刀具的使用寿命。
简述选择切削用量的原则
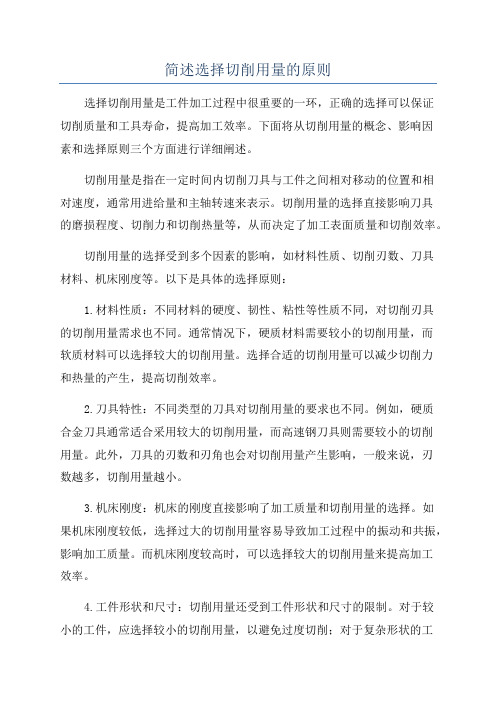
简述选择切削用量的原则选择切削用量是工件加工过程中很重要的一环,正确的选择可以保证切削质量和工具寿命,提高加工效率。
下面将从切削用量的概念、影响因素和选择原则三个方面进行详细阐述。
切削用量是指在一定时间内切削刀具与工件之间相对移动的位置和相对速度,通常用进给量和主轴转速来表示。
切削用量的选择直接影响刀具的磨损程度、切削力和切削热量等,从而决定了加工表面质量和切削效率。
切削用量的选择受到多个因素的影响,如材料性质、切削刃数、刀具材料、机床刚度等。
以下是具体的选择原则:1.材料性质:不同材料的硬度、韧性、粘性等性质不同,对切削刃具的切削用量需求也不同。
通常情况下,硬质材料需要较小的切削用量,而软质材料可以选择较大的切削用量。
选择合适的切削用量可以减少切削力和热量的产生,提高切削效率。
2.刀具特性:不同类型的刀具对切削用量的要求也不同。
例如,硬质合金刀具通常适合采用较大的切削用量,而高速钢刀具则需要较小的切削用量。
此外,刀具的刃数和刃角也会对切削用量产生影响,一般来说,刃数越多,切削用量越小。
3.机床刚度:机床的刚度直接影响了加工质量和切削用量的选择。
如果机床刚度较低,选择过大的切削用量容易导致加工过程中的振动和共振,影响加工质量。
而机床刚度较高时,可以选择较大的切削用量来提高加工效率。
4.工件形状和尺寸:切削用量还受到工件形状和尺寸的限制。
对于较小的工件,应选择较小的切削用量,以避免过度切削;对于复杂形状的工件,需要根据具体情况选择合适的切削用量,以保证加工表面的精度和光洁度。
5.加工方式:不同的加工方式对切削用量的选择也有影响。
例如,粗加工时应选择较大的切削用量,以快速去除材料;而精加工时需要选择较小的切削用量,以提高加工表面的质量。
总之,选择合适的切削用量是实现高效率、高质量加工的重要手段。
在实际应用中,需要综合考虑材料性质、刀具特性、机床刚度、工件形状和尺寸等因素,并根据具体情况进行调整和优化,以达到最佳的切削效果。
车削加工操作中切削用量的选择
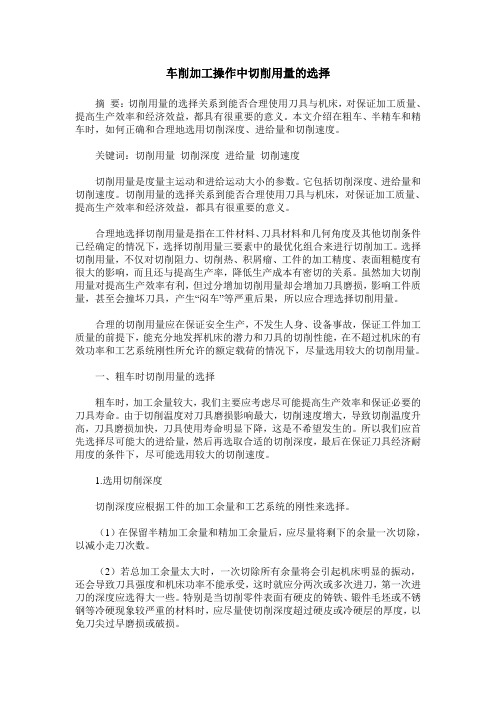
车削加工操作中切削用量的选择摘要:切削用量的选择关系到能否合理使用刀具与机床,对保证加工质量、提高生产效率和经济效益,都具有很重要的意义。
本文介绍在粗车、半精车和精车时,如何正确和合理地选用切削深度、进给量和切削速度。
关键词:切削用量切削深度进给量切削速度切削用量是度量主运动和进给运动大小的参数。
它包括切削深度、进给量和切削速度。
切削用量的选择关系到能否合理使用刀具与机床,对保证加工质量、提高生产效率和经济效益,都具有很重要的意义。
合理地选择切削用量是指在工件材料、刀具材料和几何角度及其他切削条件已经确定的情况下,选择切削用量三要素中的最优化组合来进行切削加工。
选择切削用量,不仅对切削阻力、切削热、积屑瘤、工件的加工精度、表面粗糙度有很大的影响,而且还与提高生产率,降低生产成本有密切的关系。
虽然加大切削用量对提高生产效率有利,但过分增加切削用量却会增加刀具磨损,影响工件质量,甚至会撞坏刀具,产生“闷车”等严重后果,所以应合理选择切削用量。
合理的切削用量应在保证安全生产,不发生人身、设备事故,保证工件加工质量的前提下,能充分地发挥机床的潜力和刀具的切削性能,在不超过机床的有效功率和工艺系统刚性所允许的额定载荷的情况下,尽量选用较大的切削用量。
一、粗车时切削用量的选择粗车时,加工余量较大,我们主要应考虑尽可能提高生产效率和保证必要的刀具寿命。
由于切削温度对刀具磨损影响最大,切削速度增大,导致切削温度升高,刀具磨损加快,刀具使用寿命明显下降,这是不希望发生的。
所以我们应首先选择尽可能大的进给量,然后再选取合适的切削深度,最后在保证刀具经济耐用度的条件下,尽可能选用较大的切削速度。
1.选用切削深度切削深度应根据工件的加工余量和工艺系统的刚性来选择。
(1)在保留半精加工余量和精加工余量后,应尽量将剩下的余量一次切除,以减小走刀次数。
(2)若总加工余量太大时,一次切除所有余量将会引起机床明显的振动,还会导致刀具强度和机床功率不能承受,这时就应分两次或多次进刀,第一次进刀的深度应选得大一些。
车床切削用量如何选择方案

在车削螺纹时,车床的主轴转速将受到螺纹的螺距P(或导程) 大小、驱动电机的升降频特性,以及螺纹插补运算速度等多种因素
影响,故对于不同的数控系统,推荐不同的主轴转速选择范围。 大多数经济型数控车床推荐车螺纹时的主轴转速n(r/min)为:
(3)按所用的刀具种类划分工序 以同一把刀具完成的那一部分工艺过程为一道工序,这种方法适
于工件的待加工表面较多,机床连续工作时间较长,加工程序的编制 和检查难度较大的情况。
如图4-19所示工件, 工序一:钻头钻孔,去除加工余量; 工序二:采用外圆车刀粗、精加工外形轮廓; 工序三:内孔车刀粗、精车内孔。
般采用二次进给车成,即第一次进给车槽时,槽壁两侧留精车余量, 第二次进给时用等宽刀修整。
车较宽的沟槽,可以采用多次直进法切割,并在槽壁及底面留 精加工余量,最后一刀精车至尺寸。如图4-29所示。
图4-29 切宽槽的走刀路线
小结:1. 数控车削切削用量的选择原则、方法及主要问题
2. 数控车削工序划分和加工顺序安排 3. 确定走刀路线的原则 4. 数控车床常用的走刀路线
4.5.4确定刀具的走刀路线
刀具的走刀路线:在数控加工中,刀具刀位点相对于工件的运 动轨迹和方向。即刀具从对刀点开始运动起,直至加工程序结束所 经过的路径,包括切削加工的路径及刀具切入、切出等非切削空行 程。
确定走刀路线的总原则:在保证零件加工精度和表面质量的前 提下,尽量缩短走刀路线,以提高生产率;方便坐标值计算,减少 编程工作量,便于编程。对于多次重复的走刀路线,应编写子程序, 简化编程。
作业:
21.刀具的选择和切削用量的确定

21.刀具的选择、切削用量的确定
加工刀具的选择,应尽可能选用硬质合金刀具或性能更好的更耐磨的带涂层的刀具。
铣平面轮廓用平头立铣刀,铣空间轮廓时选球头立铣刀。
选择刀具时要规定刀具的结构尺寸,供刀具组装预
调使用;还要保证有可调用的刀具文件;对选定的新刀
具应建立刀具文件供编程用。
切削用量的选择,数控机械加工的切削深度、切削
速度和进给量的确定原则与普通机械加工相似,也可根
据实际经验或查阅有关手册。
数控机床的使用说明书上
一般都会给出切削参数的推荐值。
有缘学习更多+谓ygd3076或关注桃报:奉献教育(店铺)
有缘学习更多+谓ygd3076或关注桃报:奉献教育(店铺)
合理选择工件的装夹方法、刀具和切削用量 :
在选用或设计夹具时应当遵循以下原则:
(1)尽量选用组合夹具,可调整夹具等标准化、通用化夹具,避免采用专用夹具。
(2)工件的装卸要快速、方便、可靠,采用气动、液压夹具,以减少机床的停机时间。
(3)零件上的加工部位要外露敞开,不要因装夹工件而影响刀具进给和切削加工。
数控编程时,合理选用刀具是数控加工工艺的重要内容。
编制程序时,常需要预先规定好刀具的结构尺寸和调整尺寸。
切削用量包括主轴转速(切削速度)、切削深度、进给速度(进给量)、切削宽度等。
对于不同的加工方法,需要选择不同的切削用量,并应编入程序中。
- 1、下载文档前请自行甄别文档内容的完整性,平台不提供额外的编辑、内容补充、找答案等附加服务。
- 2、"仅部分预览"的文档,不可在线预览部分如存在完整性等问题,可反馈申请退款(可完整预览的文档不适用该条件!)。
- 3、如文档侵犯您的权益,请联系客服反馈,我们会尽快为您处理(人工客服工作时间:9:00-18:30)。
4
刀具结构的选择
根据粗加工加工余量大、 切削余量大的特点 , 用 于粗加工的刀具应该具有很好的刚性。一般来讲, 整体刀具的刚性较好, 但重型刀具的结构笨重, 装卸 比较困难 , 所以发展方向应该是机夹刀具。机夹刀 具的刀片夹持结构及加工精度对于刀具的选择很重 要 , 实际加工中发现, 偏心销夹紧和勾头压紧式不适 合重型粗加工, 这是因为粗加工时的系统振动较大, 常使压紧机构松动 , 导致刀片损坏。而上压式结构 常因阻碍了切屑的流出造成压块的损坏。对机夹刀 具的制造精度要求也很高, 因为即使微小的误差 , 也 会使定位机构变成承力机构 , 由于重型切削的加工 过程中切削力巨大 , 就会造成刀具的损坏。经实际 加工验证 , 图 1 所示结构的刀具比较适于重型机械 加工的粗加工, 其优点在于 : 当刀块与刀体间有误差 时 , 可以进行修磨 , 从而保证装配精度; 压紧螺栓位 于后刀面上, 不容易被切屑损坏。板式刀架比较适 合重型切削, 因为它极大地增加了刀片受力方向的 刚度 , 可以使得在增加切削用量后 , 不会产生振动, 有利于生产效率和加工质量的提高。
Selection of Tool and Cutting Parameter in Heavy Lathe Machining
Wang Zhiyong
Abstract: The process problems in heavy lathe machining , such as the selection of tool materials, tool angles, cutting pa rameter, and the mount of tools are analyzed. The schemes of rough machining and finish machining are put forward combined with productive practice and the feasible schemes are useful reference to other practices of heavy lathe machining. Keywords: heavy lathe, cutting parameter,
收稿日期 : 2003 年 4 月
2 Cox J J. Space filling curves in tool path applications. Comput er Aided Design, 1994, 26( 3) : 215~ 224 3 Yuanshin Lee. Non isoparametric tool path planning by machin ing strip evaluation for 5 axis sculptured surface machining. Computer Aided Design, 1998, 30( 7) : 559~ 570 4 Chih Ching Lo. CNC machine tool surface interpolator forball
40 金材料时, 它的耐用度 下降很快 , 无法满足使 用要 求。如电站用机械产品工作于高温、 高压、 高转速的 环境中, 对材料 ( 如 26Cr2Ni4MoV、 Mn18Cr18) 机械性 能的要求非常高 ; 而一些高硬度轧辊, 表面硬度在淬 火后可达 Hs90, YT 类刀具 在加工此类产品时 就无 法胜任 , 在这种情况下应选用 YW 类刀具或细晶粒、 超细晶粒合金刀具( 如 643 等) 。细晶粒合金的耐磨 性好, 更适用于加工冷硬铸铁类产品 , 效率较 YW 类 刀具可提高一倍以上。 精加工阶段同样要求刀具耐磨损 , 但是精加工 阶段的磨损形式是以粘蚀磨损为主 , 这时的切削速 度虽然有了很大提高 ( 可达到 40m/ r) , 但由 于工件 材质等原因, 仍然会产生积屑瘤, 当积屑瘤增长到一 定高度时会从刀具上剥离, 将接触部位的刀具材料 带走一部分, 形成刀具的磨损。同时, 剥离的积屑瘤 会扎进工件表面 , 形成硬点, 降低加工表面质量。因 此, 如果精加工时仍然采用普通硬质合金刀具 , 则刀 具磨损非常快, 换刀次数增多 , 不仅影响加工效率 , 也易在工件表面形成接刀痕迹, 影响外观质量。解 决这个问题的办法就是改变刀具材料。在实际加工 中发现涂层刀具比较适合重型切削的精加工, 刀具 的涂层减小了切屑与刀面间的摩擦 , 减少了积屑瘤 的发生, 降低了刀具的磨损, 延长了刀具的寿命。实 际加工中, 我们采用瓦尔特公司的涂层硬质合金刀 片, 在加工 45Cr4NiMoV 支撑辊时 , 刀具耐用度提高 了一倍; 但使用陶瓷刀具未达到预期效果, 当切削速 度达到 100m/ min 时, 刀片的磨损显著加快 , 这是因 为陶瓷刀具与金属材料之间由于亲和作用加剧了刀 具的磨损。高速钢刀具在精加工阶段得到了广泛的 应用 , 由于高速钢刀具的锋锐性较好, 经常用于精加 工阶段的光整工序以去除微小余量 , 目前来看 , 其它 刀具还无法完全取代高速钢刀具的作用。
y c 正= Pz a ( L+ a) 3 EJ
2
( 3)
由式 ( 3) 和式 ( 2) 得到刀具反安装和刀具正安装 时的刀尖挠度值之差 :
y c正 = y c反 Pza2 L Pza2 = 3 EJ 3EJ ( 4) Pza2 ( L + a) 3EJ
6
结语
重型切削同普通切削相比, 其实际加工同理论 计算均有很大的区别。目前 , 重型切削的很多工艺 及刀具资料都是以普通机械加工为依据 , 并不完全 适用于重型机械加工 , 因此需要进一步专门深入研 究。
1
引言
择应 要求 耐 磨损、 抗 冲 击, 刀 具涂 层 后硬 度 可达 80HRC, 具有高的抗氧化性能和抗粘结性能, 因而有 较高的耐磨性和抗月牙洼磨损能力。硬质合金涂层 具有较低的摩擦系数 , 可降低切削时的切削力及切 削温度 , 可以大大提高刀具耐用度( 涂层硬质合金刀 片的耐用度至少可提高 1 倍) 等优点, 但由于涂层刀 片的锋利性、 韧性、 抗剥落和抗崩刃性能均不及未涂 层刀片 , 故不适用高硬度材料和重载切削的粗加工。 陶瓷类刀具硬度高, 但抗弯强度低 , 冲击韧性差, 不 适用于余量不均的重型切削 , CBN 刀具同样也存在 这个问题。综合以上分析 , 只有硬质合金刀具适合 于重型切削的粗加工。硬质合金分为钨钴类( YG) 、 钨钴钛类 ( YT) 和碳化钨类 ( YW) 。加工钢 料时, 由 于金属塑性变形大 , 摩擦剧烈, 切削温度高 , YG 类硬 质合金虽然强度和韧性较好 , 但高温硬度和高温韧 性较差, 因 此在重型切削中 很少应用。与 之相比, YT 类硬质合金刀具适于加工钢料, 由于 YT 类合金 具有较高的硬度和耐磨性, 尤其是具有高的耐热性, 抗粘结扩散能力和抗氧化能力也很好, 在加工钢料 时刀具磨损较小, 刀具耐用度较高, 因此 YT 类硬质 合金是重型加工时较常用的刀具材料。然而在低速 切削钢料时, 由于切削过程不太平稳, YT 类合金的 韧性较差, 容易产生崩刃, 而且在加工一些高强度合
end milling of free form surfaces. International Journal of Ma chine Tool and Manufacture. 2000( 40) : 307~ 326 5 Yuanshin Lee. Admissible tool orientation control of goug ing avoidance for 5 axis complex surface. Computer Aided Design, 1997, 29 ( 3) : 507~ 521 第一 作 者 : 刘 志峰 , 北 京 工 业 大学 机 电 系 CAD 中 心 , 100022 北京市
图 2 刀具反安装计算 简图
度降为 3m/ min 左右, 并采用煤油进行润滑。精加工 时 , 加工余量较小 , 从而切削深度也较小 , 对于形状 精度较高的表面, 应分多次去除余量 , 这样可以有效 消除残留的形状误差 , 这一点对于易变形的工件尤 其重要。
同理, 在刀具正 安装时, 由 于走刀抗力影 响较 小, 故计算变形时只考虑主切削力, 则有刀尖 C 点 挠度为
2003 年第 37 卷
10
39
重型车床刀具及切削用量的选择
王志勇
燕山大学
摘 要 : 对重型车床切削中的刀具材料、 刀具角度、 切 削用量的选择以及刀具安装 等工艺问题 进行了分 析。结 切削用量 , 机夹刀具 合生产实际 , 分别提出了粗加工和精加工工艺方 案 , 对重型车削加工的实际生产具有借鉴作用。 关键词 : 重型车削 ,
3
刀具角度的选择
图 1 机夹重 型车刀
由于在重型机械粗加工阶段刀具的工作环境比 较恶劣, 比如材料锻造后的氧化皮、 裂纹、 铲坑、 铸造 后的夹杂、 气孔等缺陷 , 都易导致刀具的损坏, 因此 应选择适当的刀具角度。用于重型切削的刀具一般 采用 0 ~ - 5 前角 , 10 ~ 15 后角 , 采用负的刃倾角 , 以增大工作前角和楔角, 提高刀刃的锋利性和刀尖 的强度。同时, 在主切削刃上开有 1mm 左右宽的负 倒棱、 R 2mm 左右的刀尖圆角以提高刀刃的抗冲击 性能。当然 , 这些角度还要根据实际加工情况进行 调整。
工 具技 术
精加工阶段以保证产品精度为主要目标。刀具 的锋利对切除微小的余量极为重要。这时选用的刀 具角度一般为 : 前角 10 , 后角 15 , 刃倾角 10 ; 当用 平刃刀片精光时, 前角达 25 ~ 30 , 后角 15 , 刃倾角 20 , 属斜角切削。刀刃在刃磨后 , 应该用金刚石砂 条或细目油石条进行研磨, 去除微小毛刺及微裂 , 增 强刀刃的锋锐性和强度 , 并用刀尺进行透光检查 , 保 证刀刃的平直度。
2003 年第 37 卷
10
41 重型机械加工的产品尺寸较大 , 所以很多产品