合成氨工艺及设计计算
合成氨的工艺流程

合成氨的工艺流程
合成氨是一种重要的化工原料,广泛应用于化肥、医药、塑料等多个领域。
其工艺流程主要包括氮气和氢气的催化反应,下面将详细介绍合成氨的工艺流程。
首先,合成氨的工艺流程是通过哈伯-玻斯曼过程实现的。
在工业上,通常采用铁-铝催化剂进行合成氨的催化反应。
反应的化学方程式为N2 + 3H2 → 2NH3。
在反应过程中,氮气和氢气在催化剂的作用下发生反应,生成氨气。
其次,合成氨的工艺流程需要高温高压条件。
反应温度通常在400-500摄氏度,压力在100-200大气压。
高温高压条件有利于提高反应速率和转化率,从而提高合成氨的产率。
然后,合成氨的工艺流程需要进行氮气和氢气的预处理。
氮气通常来自空分设备,需要进行脱氧、脱水等处理,以保证氮气的纯度和干燥度;而氢气通常来自重整装置,也需要进行脱氧、脱硫等处理,以保证氢气的纯度和干燥度。
此外,合成氨的工艺流程还需要进行氨气的分离和净化。
合成
氨反应产生的氨气中通常伴随着少量的氮气、氢气、水蒸气和杂质气体,需要进行分离和净化,以得到高纯度的合成氨产品。
最后,合成氨的工艺流程还需要进行废气处理。
合成氨反应产生的废气中含有一定量的氮气、氢气和氨气,以及少量的催化剂粉尘和有机物,需要进行处理,以达到环保排放标准。
综上所述,合成氨的工艺流程是一个复杂的化学过程,需要高温高压条件下进行氮气和氢气的催化反应,同时进行氮气和氢气的预处理,以及氨气的分离和净化,最终进行废气处理。
这一工艺流程的稳定运行对设备的稳定性和操作技术都有较高要求,但合成氨作为重要的化工原料,其生产工艺的不断改进和优化将对化工行业的发展起到积极作用。
年产十万吨合成氨变换工艺和设备设计核算参考
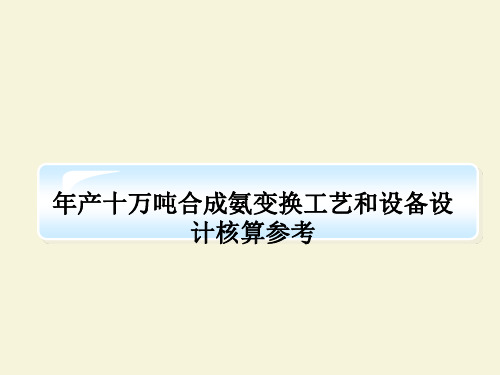
5、工艺流程
本设计主要是变换工序的工艺设计,所选流程为:
H2O
原料气
饱
和
热
水
塔
中
温 变
换热器
换
炉
低 变换气 温 变 换 炉
选用中串低工艺。从压缩工段来的变换气进入饱和
热水塔,在饱和塔出口加入水蒸汽使汽气比达3-5,以 后
再进入中变炉将转换气中一氧化碳含量降到3%以下。
再通过换热器将转换气的温度降到180℃左右,进入低
物量在设备里无物量的变化。
水带入热Q1=XCpT 变换气带入热Q2=nCpmT 同理求得变换气带出热Q3;水带出热Q4。 热量平衡:0.96×(Q1+ Q2)= Q3+ Q4 则X=288.305koml
中变炉一段催化床层的物料衡算
假设CO在一段催化床层的实际变换率为60% 求出在一段催化床层反应后剩余各组分的量 得到出中变炉一段催化床层的变换气干组分的含 进而求得出中变炉一段催化床层变换气湿组分含 量 出中变炉一段催化床层的变换气湿组分的含量 根据:Kp=(H2%×CO2%)/(H2O%×CO%) 计算得Kp,查出对应温度t
主换热器的物料与热量的计算
进出设备的变换气的量:190.97kmol 进出设备的水的量: Xkmol
变换气进设备的温度: 365℃ 变换气出设备的温度: 250℃
水进设备的温度: 水出设备的温度:
20℃ 90℃
变换气带入热Q1=nCpmT;水带入热Q2=XCpT 同理求变换气带出热Q3水带出热Q4 0.96×(Q1+Q2)=Q3+Q4
低变炉的物料计算
要将CO%降到0.2%(湿基)以下,
由CO实际变换率为:Xp=
Ya Ya
合成氨的工艺流程
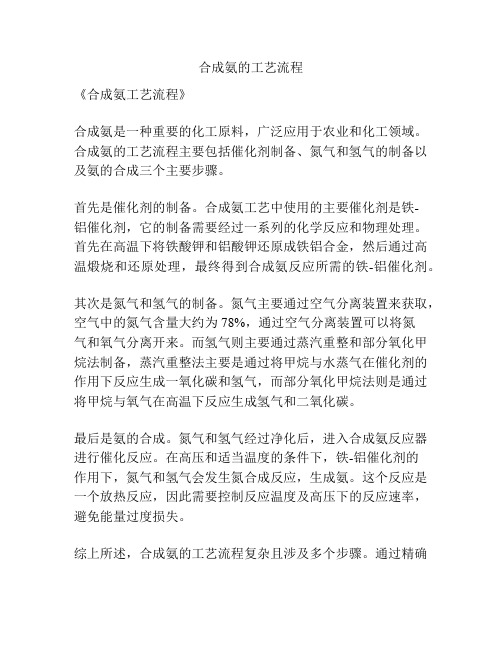
合成氨的工艺流程
《合成氨工艺流程》
合成氨是一种重要的化工原料,广泛应用于农业和化工领域。
合成氨的工艺流程主要包括催化剂制备、氮气和氢气的制备以及氨的合成三个主要步骤。
首先是催化剂的制备。
合成氨工艺中使用的主要催化剂是铁-
铝催化剂,它的制备需要经过一系列的化学反应和物理处理。
首先在高温下将铁酸钾和铝酸钾还原成铁铝合金,然后通过高温煅烧和还原处理,最终得到合成氨反应所需的铁-铝催化剂。
其次是氮气和氢气的制备。
氮气主要通过空气分离装置来获取,空气中的氮气含量大约为78%,通过空气分离装置可以将氮
气和氧气分离开来。
而氢气则主要通过蒸汽重整和部分氧化甲烷法制备,蒸汽重整法主要是通过将甲烷与水蒸气在催化剂的作用下反应生成一氧化碳和氢气,而部分氧化甲烷法则是通过将甲烷与氧气在高温下反应生成氢气和二氧化碳。
最后是氨的合成。
氮气和氢气经过净化后,进入合成氨反应器进行催化反应。
在高压和适当温度的条件下,铁-铝催化剂的
作用下,氮气和氢气会发生氮合成反应,生成氨。
这个反应是一个放热反应,因此需要控制反应温度及高压下的反应速率,避免能量过度损失。
综上所述,合成氨的工艺流程复杂且涉及多个步骤。
通过精确
控制每个步骤的条件和参数,可以确保生产安全高效地进行,从而满足氨的需求并为化工及农业领域提供丰富的原料。
合成氨的工艺流程
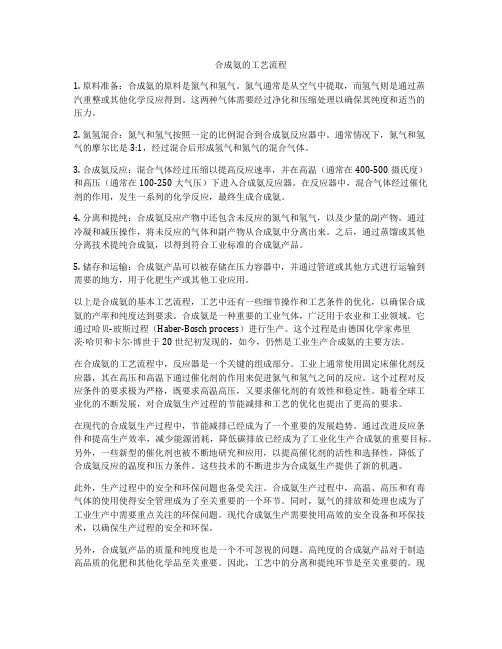
合成氨的工艺流程1. 原料准备:合成氨的原料是氮气和氢气。
氮气通常是从空气中提取,而氢气则是通过蒸汽重整或其他化学反应得到。
这两种气体需要经过净化和压缩处理以确保其纯度和适当的压力。
2. 氮氢混合:氮气和氢气按照一定的比例混合到合成氨反应器中。
通常情况下,氮气和氢气的摩尔比是3:1,经过混合后形成氢气和氮气的混合气体。
3. 合成氨反应:混合气体经过压缩以提高反应速率,并在高温(通常在400-500摄氏度)和高压(通常在100-250大气压)下进入合成氨反应器。
在反应器中,混合气体经过催化剂的作用,发生一系列的化学反应,最终生成合成氨。
4. 分离和提纯:合成氨反应产物中还包含未反应的氮气和氢气,以及少量的副产物。
通过冷凝和减压操作,将未反应的气体和副产物从合成氨中分离出来。
之后,通过蒸馏或其他分离技术提纯合成氨,以得到符合工业标准的合成氨产品。
5. 储存和运输:合成氨产品可以被存储在压力容器中,并通过管道或其他方式进行运输到需要的地方,用于化肥生产或其他工业应用。
以上是合成氨的基本工艺流程,工艺中还有一些细节操作和工艺条件的优化,以确保合成氨的产率和纯度达到要求。
合成氨是一种重要的工业气体,广泛用于农业和工业领域。
它通过哈贝-玻斯过程(Haber-Bosch process)进行生产。
这个过程是由德国化学家弗里茨·哈贝和卡尔·博世于20世纪初发现的,如今,仍然是工业生产合成氨的主要方法。
在合成氨的工艺流程中,反应器是一个关键的组成部分。
工业上通常使用固定床催化剂反应器,其在高压和高温下通过催化剂的作用来促进氮气和氢气之间的反应。
这个过程对反应条件的要求极为严格,既要求高温高压,又要求催化剂的有效性和稳定性。
随着全球工业化的不断发展,对合成氨生产过程的节能减排和工艺的优化也提出了更高的要求。
在现代的合成氨生产过程中,节能减排已经成为了一个重要的发展趋势。
通过改进反应条件和提高生产效率,减少能源消耗,降低碳排放已经成为了工业化生产合成氨的重要目标。
【最新版】年产20万吨合成氨合成工艺设计毕业设计

年产20万吨合成氨合成工艺设计The Process Design of 200kta of Synthetic AmmoniaSynthesis目录摘要 (I)Abstract (I)引言 (1)第一章综述 (2)1.1 氨的研究背景 (2)1.2 氨的用途 (2)1.3 氨的生产方法的选择 (3)第二章氨合成过程的步骤及工艺流程 (5)2.1 氨合成的步骤 (5)2.2 氨合成工艺流程简述 (6)第三章工艺计算 (9)3.1 原始条件 (9)3.2 物料衡算 (9)3.2.1 合成塔物料衡算 (9)3.2.2 氨分离器气液平衡计算....................... 错误!未定义书签。
3.2.3 冷凝塔气液平衡计算......................... 错误!未定义书签。
3.2.4 液氨贮槽气液平衡计算....................... 错误!未定义书签。
3.2.5 液氨贮槽物料计算 (14)3.2.6 合成系统物料计算........................... 错误!未定义书签。
3.2.7 合成塔物料计算............................. 错误!未定义书签。
3.2.8 水冷器物料计算 (17)3.2.9 氨分离器物料计算 (18)3.2.10 冷凝塔物料计算 (19)3.2.11 氨冷器物料计算............................ 错误!未定义书签。
3.2.12 冷凝塔物料计算............................ 错误!未定义书签。
3.2.13 液氨贮槽物料计算.......................... 错误!未定义书签。
3.3 热量衡算 (26)3.3.1合成塔热量计算 (26)3.3.2 废热锅炉热量计算 (28)3.3.3 热交换器热量计算 (29)第四章设备的计算与选型..................... 错误!未定义书签。
年产70万吨合成氨脱碳工段工艺设计
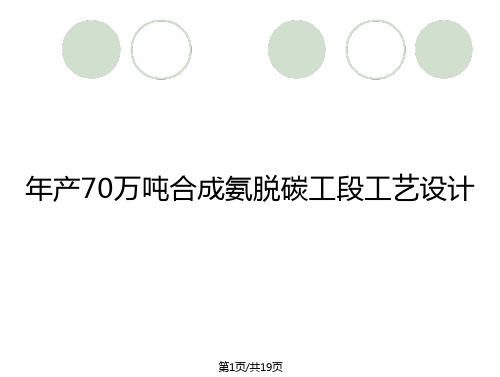
③低温操作性能好 ,溶剂损耗少:NHD低温不 分解 ,还能提高脱碳能力。
工业概况: 中国经过50多年的发展,合 成氨产量已跃居世界第1位 。掌握了多种原 料生产合成氨的技术 。2009年,我国共有合 成氨生产企业496家 ,产量已达5135万吨, 总体上 ,我国合成氨工业能够满足氮肥工业 生产需求 ,基本能满足农业生产。
第4页/共19页
发展趋势: 未来合成氨技术进展的主要 趋势是“大型化 ,低能耗,结构调整,清洁 生产 ,长周期运行 ”。产能分布的走势将是 向资源地转移 ,尤其是向煤炭资源地转移。
3 脱碳工段在合成氨中的重要作用
在合成氨装置前面工序产生的CO2气体 , 如果不除去将影响后续合成过程并使催 化剂 中毒。
为合成氨提供合格原料气; 为尿素合成提供合格的CO2气体。 从节能与环保方面考虑 ,脱除CO2 的洗涤液 要能够再生和循环使用。
第5页/共19页
二 国内外脱碳工艺发展
按照过程机理 ,合成氨装置脱碳工艺可分 为3大类。
MEA-T EA 双溶剂法, 同时使用MEA、T
EA 来脱除CO2, 既提高了吸收效率, 又降低 了再生能耗。 b 热钾碱溶液法中有:Davy Powergas 公 司开发的无毒 G-V 法,此法能耗低,CO2的 回收纯度 99% 左右,无毒;苯菲尔
第由8页于/共 页收
c 由 Eickmeyer & Associates 公司开发的催化 热钾碱法(Cata Carb 法)净化气中 CO2含量 为 50 µ L/ L 左右, 能耗与操作费用都不高。
天然气合成氨工艺流程
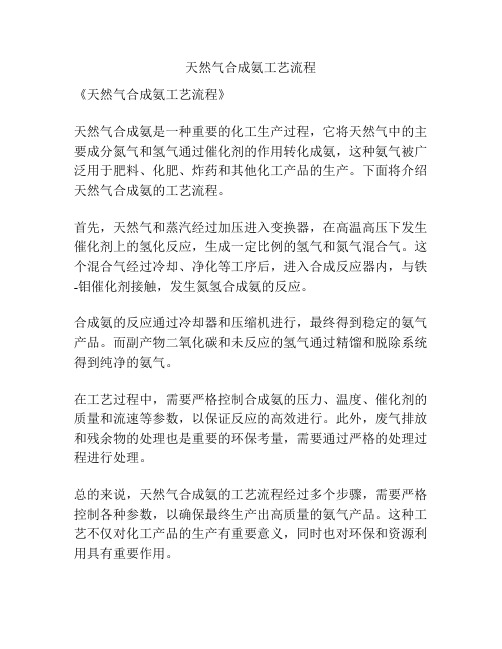
天然气合成氨工艺流程
《天然气合成氨工艺流程》
天然气合成氨是一种重要的化工生产过程,它将天然气中的主要成分氮气和氢气通过催化剂的作用转化成氨,这种氨气被广泛用于肥料、化肥、炸药和其他化工产品的生产。
下面将介绍天然气合成氨的工艺流程。
首先,天然气和蒸汽经过加压进入变换器,在高温高压下发生催化剂上的氢化反应,生成一定比例的氢气和氮气混合气。
这个混合气经过冷却、净化等工序后,进入合成反应器内,与铁-钼催化剂接触,发生氮氢合成氨的反应。
合成氨的反应通过冷却器和压缩机进行,最终得到稳定的氨气产品。
而副产物二氧化碳和未反应的氢气通过精馏和脱除系统得到纯净的氨气。
在工艺过程中,需要严格控制合成氨的压力、温度、催化剂的质量和流速等参数,以保证反应的高效进行。
此外,废气排放和残余物的处理也是重要的环保考量,需要通过严格的处理过程进行处理。
总的来说,天然气合成氨的工艺流程经过多个步骤,需要严格控制各种参数,以确保最终生产出高质量的氨气产品。
这种工艺不仅对化工产品的生产有重要意义,同时也对环保和资源利用具有重要作用。
产万吨合成氨工艺设计方案

《化工原理》课程设计题目名称:年产30万吨合成氨转变工序设计系别:化工与制药学院专业:制药工程班级:03制药工程<1)学生:蒋晟学号:2003063107指导教师<职称):<教授)摘要氨是重要的基础化工产品之一,在国民经济中占有重要地位。
合成氨生产经过多年的发展,现已发展成为一种成熟的化工生产工艺。
本设计是以天然气为原料年产三十万吨合成氨转变工序的设计。
近年来合成氨工业发展很快,大型化、低能耗、清洁生产均是合成氨设备发展的主流,技术改进主要方向是开发性能更好的催化剂、降低氨合成压力、开发新的原料气净化方法、降低燃料消耗、回收和合理利用低位热能等方面上。
设计采用的工艺流程简介:天然气经过脱硫压缩进入一段转化炉,把CH4和烃类转化成H2,再经过二段炉进一步转化后换热进入高变炉,在催化剂作用下大部分CO和水蒸气反应获H2和CO2,再经过低变炉使CO降到合格水平,去甲烷化工序。
本设计综述部分主要阐述了国内外合成氨工业的现状及发展趋势以及工艺流程、参数的确定和选择,论述了建厂的选址;介绍了氨变换工序的各种流程并确定本设计高-低变串联的流程。
工艺计算部分主要包括转化段和变换段的物料衡算、热量衡算、平衡温距及空速计算。
设备计算部分主要是高变炉催化剂用量的具体计算,并根据设计任务做了转化和变换工序带控制点的工艺流程图。
本设计的优点在于选择较为良好的厂址和原料路线,确定良好的工艺条件、合理的催化剂和能源综合利用。
另外,就是尽量减少设备投资费用。
关键字:合成氨;天然气;转化;变换;AbstractAmmonia is the most important one of basic chemical products, plays an important role in the national economy. Ammonia production after years of development, now has developed into a mature chemical production processes. The design is based on annual output of 300,000 tons of natural gas as raw material, the design of synthetic ammonia transformation process. In recent years, the large-scale industrial development soon ammonia, low energy consumption, the clean production of synthetic ammonia equipment development are the main direction of technical improvement, is to develop better performance of catalyst, reducing ammonia synthesis pressure, the development of new materials gas purification methods, reduce fuel consumption, low heat recovery and reasonable utilization, etc.The design process used in brief are: compressed natural gas after desulfurization and conversion into a furnace, the methane and hydrocarbons into hydrogen, through the Secondary reformer further transformed into the highly variable furnace heat exchanger, the great catalyst part of the reaction of carbon monoxide and hydrogen and carbon dioxide vapor, then through the low-temperature shift to reduce to an acceptable level of carbon monoxide to methanation process. The design review described some of the major domestic and international situation and the development of synthetic ammonia industry trends and technological process, parameter identification and selection, discusses the plant's location。
大型氨厂凯洛格工艺氨合成工序工艺设计计算毕业论文
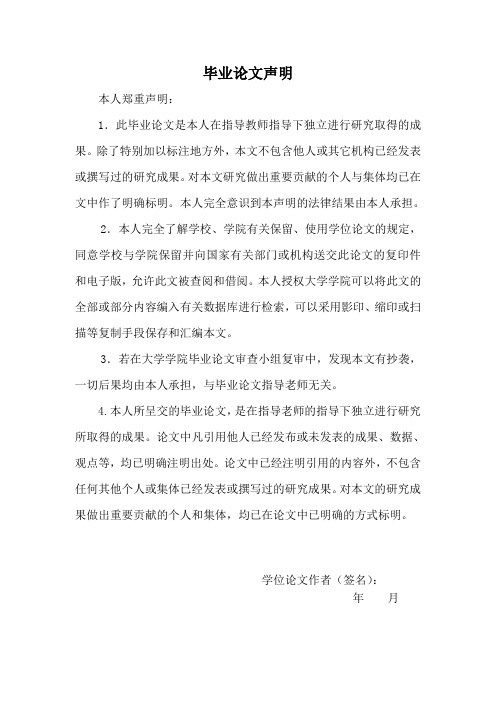
毕业论文声明本人郑重声明:1.此毕业论文是本人在指导教师指导下独立进行研究取得的成果。
除了特别加以标注地方外,本文不包含他人或其它机构已经发表或撰写过的研究成果。
对本文研究做出重要贡献的个人与集体均已在文中作了明确标明。
本人完全意识到本声明的法律结果由本人承担。
2.本人完全了解学校、学院有关保留、使用学位论文的规定,同意学校与学院保留并向国家有关部门或机构送交此论文的复印件和电子版,允许此文被查阅和借阅。
本人授权大学学院可以将此文的全部或部分内容编入有关数据库进行检索,可以采用影印、缩印或扫描等复制手段保存和汇编本文。
3.若在大学学院毕业论文审查小组复审中,发现本文有抄袭,一切后果均由本人承担,与毕业论文指导老师无关。
4.本人所呈交的毕业论文,是在指导老师的指导下独立进行研究所取得的成果。
论文中凡引用他人已经发布或未发表的成果、数据、观点等,均已明确注明出处。
论文中已经注明引用的内容外,不包含任何其他个人或集体已经发表或撰写过的研究成果。
对本文的研究成果做出重要贡献的个人和集体,均已在论文中已明确的方式标明。
学位论文作者(签名):年月关于毕业论文使用授权的声明本人在指导老师的指导下所完成的论文及相关的资料(包括图纸、实验记录、原始数据、实物照片、图片、录音带、设计手稿等),知识产权归属华北电力大学。
本人完全了解大学有关保存,使用毕业论文的规定。
同意学校保存或向国家有关部门或机构送交论文的纸质版或电子版,允许论文被查阅或借阅。
本人授权大学可以将本毕业论文的全部或部分内容编入有关数据库进行检索,可以采用任何复制手段保存或编汇本毕业论文。
如果发表相关成果,一定征得指导教师同意,且第一署名单位为大学。
本人毕业后使用毕业论文或与该论文直接相关的学术论文或成果时,第一署名单位仍然为大学。
本人完全了解大学关于收集、保存、使用学位论文的规定,同意如下各项内容:按照学校要求提交学位论文的印刷本和电子版本;学校有权保存学位论文的印刷本和电子版,并采用影印、缩印、扫描、数字化或其它手段保存或汇编本学位论文;学校有权提供目录检索以及提供本学位论文全文或者部分的阅览服务;学校有权按有关规定向国家有关部门或者机构送交论文的复印件和电子版,允许论文被查阅和借阅。
合成氨工艺设计
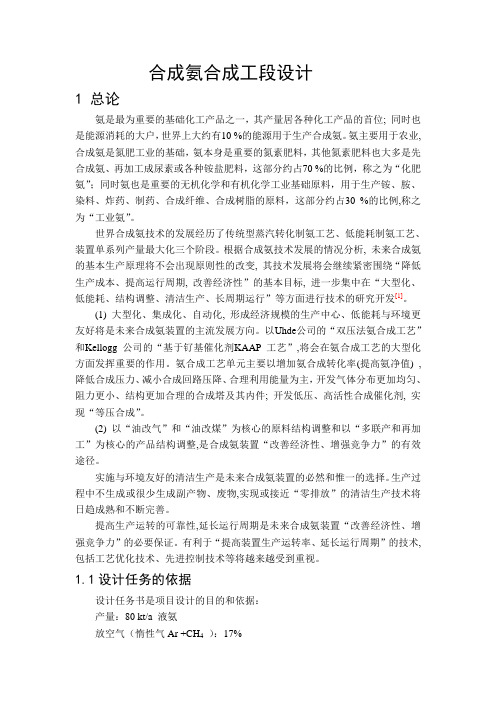
合成氨合成工段设计1 总论氨是最为重要的基础化工产品之一,其产量居各种化工产品的首位; 同时也是能源消耗的大户,世界上大约有10 %的能源用于生产合成氨。
氨主要用于农业,合成氨是氮肥工业的基础,氨本身是重要的氮素肥料,其他氮素肥料也大多是先合成氨、再加工成尿素或各种铵盐肥料,这部分约占70 %的比例,称之为“化肥氨”;同时氨也是重要的无机化学和有机化学工业基础原料,用于生产铵、胺、染料、炸药、制药、合成纤维、合成树脂的原料,这部分约占30 %的比例,称之为“工业氨”。
世界合成氨技术的发展经历了传统型蒸汽转化制氨工艺、低能耗制氨工艺、装置单系列产量最大化三个阶段。
根据合成氨技术发展的情况分析, 未来合成氨的基本生产原理将不会出现原则性的改变, 其技术发展将会继续紧密围绕“降低生产成本、提高运行周期, 改善经济性”的基本目标, 进一步集中在“大型化、低能耗、结构调整、清洁生产、长周期运行”等方面进行技术的研究开发[1]。
(1) 大型化、集成化、自动化, 形成经济规模的生产中心、低能耗与环境更友好将是未来合成氨装置的主流发展方向。
以Uhde公司的“双压法氨合成工艺”和Kellogg 公司的“基于钌基催化剂KAAP 工艺”,将会在氨合成工艺的大型化方面发挥重要的作用。
氨合成工艺单元主要以增加氨合成转化率(提高氨净值) ,降低合成压力、减小合成回路压降、合理利用能量为主,开发气体分布更加均匀、阻力更小、结构更加合理的合成塔及其内件; 开发低压、高活性合成催化剂, 实现“等压合成”。
(2) 以“油改气”和“油改煤”为核心的原料结构调整和以“多联产和再加工”为核心的产品结构调整,是合成氨装置“改善经济性、增强竞争力”的有效途径。
实施与环境友好的清洁生产是未来合成氨装置的必然和惟一的选择。
生产过程中不生成或很少生成副产物、废物,实现或接近“零排放”的清洁生产技术将日趋成熟和不断完善。
提高生产运转的可靠性,延长运行周期是未来合成氨装置“改善经济性、增强竞争力”的必要保证。
合成氨系统工艺设计及计算

种有机 煤 为原料 的部分 转化 , 根据 一氧化 碳变换 是 否采用耐 硫的 催化 剂脱硫的位 置。 ( 3 ) 气体C O , 精 制过程
.
合 成氨 的性 质及 用 途
经c O变 换l n c o , 脱 出后原 料 中长尚含 有少量 的 c o : f  ̄ c o , 为了防 止对 氨合成 催化剂 的毒害 , 规定 c o, i r c o , 总含 量不得大 于1 0 c m / m 分
础, 对 农业 增产起 着十分重要的作用 , 而 用化学肥料 是 农业增产 的有效
途径 。
二. 合成 氨 的 工艺 流程 ( 一) 合成 氨的工艺流程
卜 氨合成塔 t 2 一 水 冷器; 3 一 氨分离器 ; 4 一 循 环压缩机 , 5 一 滤抽 器;
( 4 ) 合成塔 进出1 : 1 气体中氯含量 : 进 口: 3 . O %; 出 口: 1 3 . O % ( 5 ) 放 空气中的惰性气体 ( C H + A ) 含量1 5 % ( 6 ) 计算基 准 : 物料 基准 : 1 5 0 0[ 公斤氨] ( 实际产 氯量 ) ; 基 准温
科技专论
合成氨系统工艺设计及计算
王慎国 黑龙江黑化集团有 限公司 1 6 1 0 4 1
O 变 换反应 , 在不 同温 度下分 为高温 变换 以及低温 变换 。 将一 【 摘 要 1 从 能源危机至今 , 能源供应 紧张 , 价格越 来越 高, 世界各 先利 用C 国对环境保 护的要 求也越 来越 高, 严峻的形势迫使合成 氨生产企业实施节 氧化碳 含 量 降N o . 2 5 % 左 右。 因此 , 一氧 化碳 变换 式 原料 的制 造 的继 能降耗 技 术改造 。 合成氨是非常重要 的化 工产品之・ , 在 国民经济中起到 续 , 又是 净化过程 。 十分重要 的作 用。 合成氨工艺是最典型的化工生产工艺之・ , 它集原料前处 ( 2 ) 脱硫 脱碳过程 理、 反应 、 传热、 传质、 分离、 产品后处理等为一体 , 设备 多 , 流程长而复杂。 各种原料制 取的粗 原料 气, 都含有一些硫 和碳 的氧化物 , 为了防止 合成 氨还是一个消耗 原料、 燃料和动力 很 大的化工产品。 合成 氨生 产过程 催化剂 的中毒 , 必须在氨合成工序 前加以 脱碳 , 以天然 本文介绍了 合成 氨生产的用途、 工艺流程 、 工艺合成的方法及计算 , 并 气为原料 的 蒸气转化 法 , 第一 道 工序 是脱 硫 , 用以保护 转化催化 剂 。 一 进行 热量衡算和系统的物料衡算, 对合成氨的强化措 施以及设备 的工艺计 算。 【 关键 字i 合成氨; 系 统 工艺; 设计方法; 计算
合成氨工业设计及其计算

第一章合成氨的现状及发展概况1.1 概况氨是20世纪世界重要的基础化工产品之一,其产量居各种化工产品的首位;同时也是能源消耗的大户,世界上大约有10%的能源用于生产合成氨。
氨既是主要的最终产品,同时又是重要的中间体[6]。
按其提供反应氮用途分为“化肥氮”和“工业氮”。
氨主要用于农业,合成氨是氮肥工业的基础,氨本身就是重要的氮素肥料,其他氮素肥料也大多是先合成氨、再加工成尿素或各种铵盐肥料,这部分约占70%的比例,称之为“化肥氨”;同时氨也是重要的无机化学和有机化学工业基础原料,用于生产铵、胺、染料、炸药、制药、合成纤维、合成树脂的原料,这部分约占30%的比例,称之为“工业氨”[7]。
氨在21世纪世界经济中仍将占有十分重要的地位。
展望21世纪合成氨的发展,对于我们了解合成氨发展和变化规律,预测21世纪合成氨发展趋势,制定规划和促进社会经济可持续发展具有十分重要的现实意义。
1.2 世界合成氨工业概况1.2.1 氨的生产能力和产量合成氨是化学工业中产量很大的化工产品。
1982年,世界合成氨的生产能力为125Mt,但因原料供应、市场需求的变化,合成氨的产量远比生产能力要低。
近年,合成氨产量以苏联、中国、美国、印度等十国最高,占世界总产量的一半以上[8]。
1.2.2 消费和用途合成氨主要消费部门为化肥工业,用于其他领域的(主要是高分子化工、火炸药工业等)非化肥用氨,统称为工业用氨[9]。
目前,合成氨年总消费量约为78.2Mt,其中工业用氨量约为10Mt,约占总氨消费量的12%。
1.2.3 原料合成氨主要原料有天然气、石油、重质油和煤等。
1981年,世界以天然气制氨的比例约占71%,苏联为92.2%、美国为96%、荷兰为100%;中国仍以煤、焦炭为主要原料制氨,天然气制氨仅占20%。
70年代原油涨价后,一些采用石油为原料的合成氨老厂改用天然气,新建厂绝大部分采用天然气作原料[10]。
1.2.4生产方法生产合成氨的方法主要区在原料气的制造,其中最广泛采用的为蒸汽转化法和部分氧化法。
年产20万吨合成氨合成工段工艺设计

太原理工大学课程设计题目:年产20万吨合成氨合成工段工艺设计课程设计要求:设计采用中压两级分氨流程,年产20万吨合成氨合成工段的工艺设计。
设计配有设计说明书一份,图纸二张。
说明书内容:原料气来源、流程方案的确定、物料衡算、热量衡算、设备选型及设计计算、车间布置、三废”治理及综合利用。
二张图纸:1.带控制点的合成工段物料流程图; 2.中压合成塔的工艺装配图。
学生应交出的设计文件(纸质及电子版):1.设计说明书(首页附设计任务书)2.工程设计图(CAD版)(1)主要设备图(2)工艺流程图主要参考资料(电子版):一.手册1. 小合成氨厂工艺技术与设计手册(上册),化学工业出版社,1994。
2. 小合成氨厂工艺技术与设计手册(下册) 梅安华主编,化学工业出版社,1994。
3. 氮肥工艺设计手册气体压缩氨合成甲醇合成,化学工业出版社,1989。
4. 氮肥工艺设计手册理化数据分册,石油化学工业出版社,1977。
二.参考文献1中国环球化学工程公司编. 氮肥工艺设计手册[M].19852郝晓刚等编著. 化工原理课程设计. 北京:化学工业出版社,20093陈甘棠主编.化学反应工程[M]. 第三版.北京:化学工业出版社.1990(11)4黄璐. 化工设计. 北京:化学工业出版社,20005陈五平主编.无机化工工艺学.第三版. 北京:化学工业出版社,19856姜胜阶.合成氨工学【J】.石油化学工业出版社,1978(7)7湖北华工设计院.氨合成塔【J】.石油化学工业出版社,1977(12)8化学工业出版社组织编写.中国化工产品大全[M].第二版上卷.9司航主编.化工产品手册[M].第三版.北京:化学工业出版社.10李祥君著.新编精细化工产品手册[M].北京:化学工业出版社.1996.11万家亮曾胜年主编.分析化学[M].第三版. 北京:高等教育出版社.2001(6).12天津化工研究院编.无机与工业手册【M】.北京:化学工业出版,1988(2)13江寿建. 化工厂共用设施设计手册. 北京:化工工业出版社,200014时均等. 化学工程手册. 北京:化学工业出版社,199615赵国方. 化工工艺设计概论. 北京:原子能出版社,199016化工工程师手册编辑委员会. 化学工程师手册. 北京:机械工业出版社,2000 17陈敏恒等. 化工原理,上下册. 北京:化学工业出版社,198518吴志泉等. 化工工艺计算,物料、能量衡算. 上海:华东理工大学出版社,1992 18倪进方. 化工过程设计. 北京:化学工业出版社,1999专业班级化学工程与工艺0802班学生李林豪组别第四组组员李林豪李旭连文豪马楠宋路华要求设计工作起止日期2011.11.21~2011.12.16指导教师签字日期系主任批准签字日期前言《化工设计》课程设计是培养学生化工设计能力的重要教学环节,通过课程设计使我们初步掌握化工设计的基础知识、设计原则及方法;学会各种手册的使用方法及物理性质、化学性质的查找方法和技巧;掌握各种结果的校核,能画出工艺流程、各类塔结构等图形。
合成氨反应器及工艺流程的模拟计算
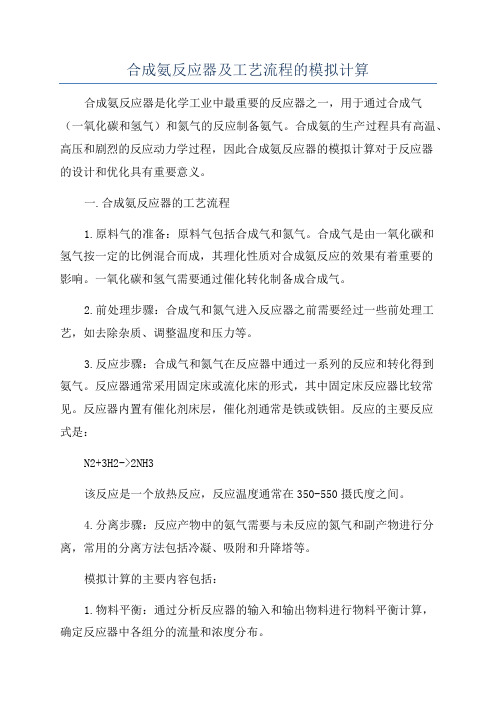
合成氨反应器及工艺流程的模拟计算合成氨反应器是化学工业中最重要的反应器之一,用于通过合成气(一氧化碳和氢气)和氮气的反应制备氨气。
合成氨的生产过程具有高温、高压和剧烈的反应动力学过程,因此合成氨反应器的模拟计算对于反应器的设计和优化具有重要意义。
一.合成氨反应器的工艺流程1.原料气的准备:原料气包括合成气和氮气。
合成气是由一氧化碳和氢气按一定的比例混合而成,其理化性质对合成氨反应的效果有着重要的影响。
一氧化碳和氢气需要通过催化转化制备成合成气。
2.前处理步骤:合成气和氮气进入反应器之前需要经过一些前处理工艺,如去除杂质、调整温度和压力等。
3.反应步骤:合成气和氮气在反应器中通过一系列的反应和转化得到氨气。
反应器通常采用固定床或流化床的形式,其中固定床反应器比较常见。
反应器内置有催化剂床层,催化剂通常是铁或铁钼。
反应的主要反应式是:N2+3H2->2NH3该反应是一个放热反应,反应温度通常在350-550摄氏度之间。
4.分离步骤:反应产物中的氨气需要与未反应的氮气和副产物进行分离,常用的分离方法包括冷凝、吸附和升降塔等。
模拟计算的主要内容包括:1.物料平衡:通过分析反应器的输入和输出物料进行物料平衡计算,确定反应器中各组分的流量和浓度分布。
2.能量平衡:考虑反应器中的能量转移和反应产生的热量,计算反应器的温度分布和热量平衡。
3.动力学模型:建立反应的动力学模型,描述反应速率和反应机理,确定反应速率常数和反应级数。
4.催化剂模型:考虑催化剂的物理特性和反应机理,建立催化剂活性和失活的模型。
5.反应器设计和优化:通过模拟计算,可以调整反应器的操作条件,如温度、压力、空速等,以实现合成氨反应的最佳效果和工艺参数。
三.模拟计算的应用和挑战然而,合成氨反应器的模拟计算也存在一些挑战。
首先,合成氨反应是一个复杂的多相反应过程,涉及多个物理和化学因素的相互作用。
其次,反应器中催化剂的活性和失活过程对反应效果和生产周期有着重要影响,但催化剂的性质和行为往往是难以确定和预测的。
合成氨计算说明书

安徽建筑大学毕业设计专业化学工程与工艺班级13化工(1)班学生姓名程爽学号***********课题年产30万吨合成氨合成工段工艺设计指导教师邵群2016年 3 月 1 日目录30万吨/年合成氨合成工艺设计 ...........................................................................第一章文献综述....................................................................................................1.1 合成氨项目简介 ...............................................................................................................1.1.1 合成氨物理性质 ........................................................................................................1.1.2 合成氨化学性质 ........................................................................................................1.1.3 合成氨市场预测 ........................................................................................................1.1.4 合成氨国内产能,消耗 ............................................................................................1.1.5 合成氨国外产能,消耗 ............................................................................................1.2生产规模及产品方案 ........................................................................................................1.2.1 产品方案 ....................................................................................................................1.2.2 生产规格 ....................................................................................................................1.2.3 产品质量 ....................................................................................................................1.3工艺技术方案的选择 ........................................................................................................1.3.1 工艺路线 ....................................................................................................................1.3.2 工艺路线的比较与选择 ............................................................................................1.3.3 本设计研究内容 ........................................................................................................第二章物料衡算....................................................................................................2.1 设计要求...........................................................................................................................2.2 工艺流程图 .......................................................................................................................2.3 全流程物料衡算 ...............................................................................................................2.4 单个单元的物料衡算 .......................................................................................................2.4.1 鼓风机物料衡算 ........................................................................................................2.4.2 混合器物料衡算 ........................................................................................................2.4.3 换热器1物料衡算 ....................................................................................................2.4.4 反应器物料衡算 ........................................................................................................2.4.5 换热器2物料衡算 ....................................................................................................2.4.6 闪蒸罐物料衡算 ........................................................................................................2.4.7 循环混合器物料衡算 ................................................................................................2.4.8 循环压缩机物料衡算 ................................................................................................第三章能量衡算....................................................................................................3.1全流程的能量衡算 ............................................................................................................3.2 单个单元的能量衡算 .......................................................................................................3.2.1 鼓风机热量衡算 ........................................................................................................3.2.2 换热器1能量衡算 ....................................................................................................3.2.3 反应器能量衡算 ........................................................................................................3.2.4 换热器2能量衡算 ....................................................................................................3.2.5 闪蒸罐能量衡算 ........................................................................................................3.2.6 循环压缩机能量衡算 ................................................................................................第四章设备的选型和计算....................................................................................4.1设备选型............................................................................................................................4.1.1 设备简述 ....................................................................................................................4.2 合成塔设计 .......................................................................................................................4.2.1 合成塔筒体设计 ........................................................................................................4.2.2 催化剂层设计 ............................................................................................................4.2.3下换热器 .....................................................................................................................4.2.4 层间换热器 ................................................................................................................1.4文献引用............................................................................................................................30万吨/年合成氨合成工艺设计摘要:氨是人体的基本元素之一,在粮食生产中占据着重要地位,是重要的基础化工产品,在国民经济中有重要地位。
合成氨的工艺流程

合成氨的工艺流程
合成氨是一种重要的化工原料,广泛应用于化肥、合成树脂、
医药等领域。
其工艺流程主要包括氮气和氢气的合成反应,以及合
成氨的分离和提纯过程。
下面将详细介绍合成氨的工艺流程。
首先,氮气和氢气通过压缩机分别被压缩至一定压力,然后经
过冷凝器降温至所需温度。
接着,氮气和氢气进入合成反应器,在
催化剂的作用下发生合成反应,生成氨气。
合成反应的温度、压力
和催化剂的选择对反应效果有着至关重要的影响,需要严格控制。
随后,合成氨气通过冷凝器冷却至液态,然后进入分离塔进行
分离。
在分离塔内,通过控制温度和压力,将未反应的氮气和氢气
重新回收利用,而将得到的合成氨气进行提纯。
提纯过程主要包括
吸附、脱附和冷凝等步骤,最终得到高纯度的合成氨。
在整个工艺流程中,需要严格控制反应温度、压力和催化剂的
选择,以确保合成氨的产率和纯度。
同时,还需要对氮气和氢气进
行预处理,去除其中的杂质和水分,以保证反应的顺利进行。
此外,对于合成氨的分离和提纯过程,也需要精密的设备和严格的操作,
确保产品的质量符合要求。
总的来说,合成氨的工艺流程包括氮气和氢气的合成反应,以及合成氨的分离和提纯过程。
在整个过程中,需要严格控制各项操作参数,保证反应的高效进行,最终得到高品质的合成氨产品。
这些工艺流程的细节和技术要点,对于合成氨生产工艺的优化和改进具有重要的指导意义。
天然气制合成氨 能耗计算
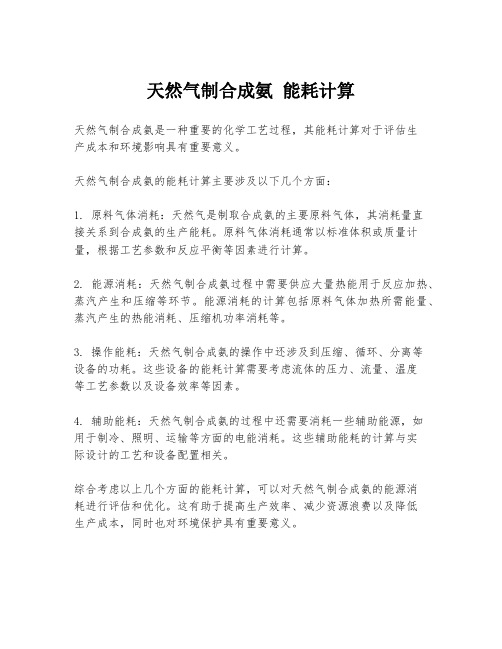
天然气制合成氨能耗计算
天然气制合成氨是一种重要的化学工艺过程,其能耗计算对于评估生
产成本和环境影响具有重要意义。
天然气制合成氨的能耗计算主要涉及以下几个方面:
1. 原料气体消耗:天然气是制取合成氨的主要原料气体,其消耗量直
接关系到合成氨的生产能耗。
原料气体消耗通常以标准体积或质量计量,根据工艺参数和反应平衡等因素进行计算。
2. 能源消耗:天然气制合成氨过程中需要供应大量热能用于反应加热、蒸汽产生和压缩等环节。
能源消耗的计算包括原料气体加热所需能量、蒸汽产生的热能消耗、压缩机功率消耗等。
3. 操作能耗:天然气制合成氨的操作中还涉及到压缩、循环、分离等
设备的功耗。
这些设备的能耗计算需要考虑流体的压力、流量、温度
等工艺参数以及设备效率等因素。
4. 辅助能耗:天然气制合成氨的过程中还需要消耗一些辅助能源,如
用于制冷、照明、运输等方面的电能消耗。
这些辅助能耗的计算与实
际设计的工艺和设备配置相关。
综合考虑以上几个方面的能耗计算,可以对天然气制合成氨的能源消
耗进行评估和优化。
这有助于提高生产效率、减少资源浪费以及降低
生产成本,同时也对环境保护具有重要意义。
小型合成氨凯洛格工艺实际
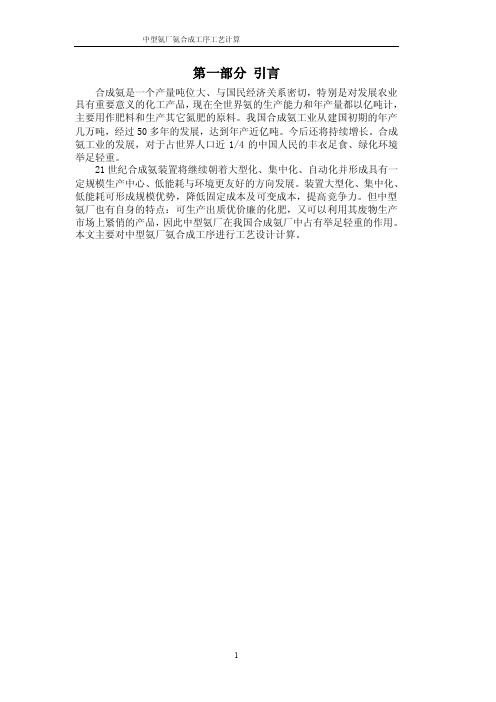
合成氨是一个产量吨位大、与国民经济关系密切,特别是对发展农业具有重要意义的化工产品,现在全世界氨的生产能力和年产量都以亿吨计,主要用作肥料和生产其它氮肥的原料。
我国合成氨工业从建国初期的年产几万吨,经过50多年的发展,达到年产近亿吨。
今后还将持续增长。
合成氨工业的发展,对于占世界人口近1/4的中国人民的丰衣足食、绿化环境举足轻重。
21世纪合成氨装置将继续朝着大型化、集中化、自动化并形成具有一定规模生产中心、低能耗与环境更友好的方向发展。
装置大型化、集中化、低能耗可形成规模优势,降低固定成本及可变成本,提高竞争力。
但中型氨厂也有自身的特点:可生产出质优价廉的化肥,又可以利用其废物生产市场上紧俏的产品,因此中型氨厂在我国合成氨厂中占有举足轻重的作用。
本文主要对中型氨厂氨合成工序进行工艺设计计算。
2.1合成氨工业在国民经济中的地位合成氨工业是基础化学工业之一。
其产量居各种化工产品的首位。
氨本身是重要的氮素肥料,除石灰氮外,其它氮素肥料都是先合成氨,然后加工成各种铵盐或尿素。
将氨氧化制成硝酸,不仅可用来制造肥料(硝酸铵、硝酸磷肥等),亦是重要的化工原料,可制成各种炸药。
氨、尿素和硝酸又是氨基树脂、聚酰胺树脂、硝化纤维素等高分子化合物的原料。
以其为原料可制得塑料、合成纤维、油漆、感光材料等产品。
作为生产氨的原料CO+H2合成气,可进行综合利用,以联产甲醇及羰基合成甲酸、醋酸、醋酐等一系列碳一化工产品。
以做到物尽其用,减少排放物对环境的污染,提高企业生产的经济效益。
已成为当今合成氨工业生产技术发展的方向。
国际上对合成氨的需求,随着人口的增长而对农作物增产的需求和环境绿化面积的扩大而不断增加。
据资料统计:我国1996年合成氨产量已达30.64Mt,2000年达36Mt, 专家预测2020年将增加至45Mt。
即今后20年间将增加到现在的1.5倍。
因而合成氨的持续健康发展还有相当长的路要走。
未来我国合成氨氮肥的实物产量将会超过石油和钢铁。
- 1、下载文档前请自行甄别文档内容的完整性,平台不提供额外的编辑、内容补充、找答案等附加服务。
- 2、"仅部分预览"的文档,不可在线预览部分如存在完整性等问题,可反馈申请退款(可完整预览的文档不适用该条件!)。
- 3、如文档侵犯您的权益,请联系客服反馈,我们会尽快为您处理(人工客服工作时间:9:00-18:30)。
第一章 物料与热量衡算已知条件:表1-1 原料气各组分的含量 Table 1-1 of the feed gas components in组 分 CO 2 CO H 2 N 2 O 2 CH 4 合计 含量,%9.6011.4255.7122.560.330.38100计算基准:1吨氨计算生产1吨氨需要的变换气量:(1000/17)×22.4/(2×22.56)=2920.31 m 3(标)因为在生产过程中物料可能会有损失,因此变换气量取2962.5 m 3(标) 年产12万吨合成氨生产能力(一年连续生产330天): 日生产量:120000/330=363.6T/d=15.16T/h 要求出中变炉的变换气干组分中CO %小于2%。
进中变炉的变换气干组分:表1-2 进中变炉的变换气干组分Table 1-2 into the furnace in the variable component of the transformation air-dry 组 分 CO 2 CO H 2 N 2 O 2 CH 4 合计 含量,% 9.611.4255.7122.560.33 0.38 100 m 3(标) 284.44 338.32 1650.41 668.34 9.78 11.26 2962.50 kmol12.696 15.103 73.67929.8370.4360.503132.25假设进中变炉的变换气温度为330℃,取变化气出炉与入炉的温差为35℃,出炉的变换气温度为365℃。
进中变炉干气压力为1.75Mpa.1.1水气比的确定:考虑到是原煤转化来的原料气,所以取H 2O/CO=3.5 故V (水)=3.5 V 水=1184.113m 3(标) ,n (水)=52.862kmol因此进中变炉的变换气湿组分如下:表1-3 进中变炉的变换气湿组分Table 1-3 into the furnace of transformation in the variable component wet gas组分CO2CO H2N2O2CH4H2O 合计含量% 6.86 8.16 39.80 16.12 0.24 0.27 28.56 100m3(标) 284.42 338.32 1650.42 668.34 9.77 11.26 1184.12 4146.61 kmol 12.69 15.10 73.68 29.84 0.44 0.50 52.86 185.121.2中变炉CO的实际变换率的求取:假定湿转化气为100mol,其中CO湿基含量为8.16%,要求变换气中CO含量为2%,故根据变换反应:CO+H2O=H2+CO2,则CO的实际变换率公式为:X p =X2/X1×100%式中X1、X2分别为原料及变换气中CO的摩尔分率(湿基)所以:Xp= 74%则反应掉的CO的量为:8.16×74%=6.04则反应后的各组分的量分别为:H2O%=28.56%-6.04%+0.48%=23%CO%=8.16% -6.04%=2.12%H2% =39.8%+6.04%-0.48%=45.36%CO2%=6.86%+6.04%=12.9%中变炉出口的平衡常数:K p = (H2%×CO2%)/(H2O%×CO%)=12查《小合成氨厂工艺技术与设计手册》可知Kp=12时温度为397℃。
中变的平均温距为397℃-365℃=32℃根据《合成氨工艺与节能》可知中温变换的平均温距为:30℃到50℃,中变的平均温距合理,故取的H2O/CO可用。
1.3中变炉催化剂平衡曲线根据H2O/CO=3.5,与文献《小合成氨厂工艺技术与设计手册》上的公式X P = X2/X1×100%V=KP(AB-CD)U=KP(A+B)+(C+D)W=KP-1其中A、B、C、D分别代表CO、H2O、CO2及H2的起始浓度计算结果列于下表:表1-4 t-T-Xp关系Table 1-4 t-T-Xp relationst 300 320 340 360 380 400T 573 593 613 633 653 673Xp0.9012 0.8737 0.8424 0.8074 0.7687 0.7058表1-5 t-T-Xp关系Table 1-5 t-T-Xp relationst 420 440 460T 693 713 733Xp0.6859 0.6416 0.59631.4最佳温度曲线的计算由于中变炉选用C6型催化剂,最适宜温度曲线由式进行计算。
查《3000吨合成氨厂工艺和设备计算》C6型催化剂的正负反应活化能分别为:E1=10000KJ/Kmol,E2=19000 KJ/Kmol。
最适宜温度计算结果如下:表1-6 t-T-Xp组成Table 1-6 t-T-Xp compositionXp0.9012 0.8737 0.8424 0.8074 0.7687 0.7058T 526 546.8 564.2 581.5 598.8 624.5 t 256 273.8 291.2 308.5 325.8 351.5表1-7 t-T-Xp组成Table 1-7 t-T-Xp compositionXp0.67 0.64 0.61 0.58 0.55 0.52T 638.2 649.4 660.7 671 681.6 692.6 t 365.2 376.4 387.3 398 408.6 419.6表1-8 t-T-Xp组成Table 1-8 t-T-Xp compositionXp 0.49 0.45T 702.6 716.6t 429.6 443.61.5中变炉一段催化床层的物料衡算已知条件:进中变炉一段催化床层的变换气的温度为330℃进中变炉一段催化床层的变换气湿组分如下:表1-9 进中变炉一段催化床层的变换气湿组分Table 1-9 into the furnace section of catalytic change in the bed of wet gas componentstransform组分CO2CO H2N2O2CH4H2O 合计含量% 6.86 8.16 39.8 16.12 0.27 0.24 28.56 100 m3(标) 284.42 338.18 1650.41 668.34 9.78 11.26 1184.11 4146.61 kmol 12.69 15.10 73.68 29.84 0.44 0.50 52.86 185.121.5.1 中变炉一段催化床层的物料衡算假设CO在一段催化床层的实际变换率为60%假使O2与H2完全反应,O2完全反应掉故在一段催化床层反应掉的CO的量为:60%×338.318=202.9908 m3(标)=9.062kmol出一段催化床层的CO的量为:338.318-202.9908=135.3272 m3(标)=6.0414kmol的量为:故在一段催化床层反应后剩余的H21650.409+202.9908-2×9.776=1833.8478 m3(标)=81.868kmol的量为:故在一段催化床层反应后剩余的CO2284.4+202.9908=487.3908 m3 (标)=21.758kmol故出中变炉一段催化床层的变换气干组分的体积:=135.3272+487.3908+1833.8478+668.34+11.258 V总(干)=3136.1638 m3 (标)故出中变炉一段催化床层的变换气干组分中CO的含量:CO%=4.31%同理得:CO%=15.54%2%=58.47%H2CO%=15.54%2N%=21.13%2CH%=0.35%4所以出中变炉一段催化床层的变换气干组分如下:表1-10 出中变炉一段催化床层的变换气干组分Table 1-10 to change in the furnace section of the catalytic bed transform air-drycomponents组分CO2CO H2N2CH4合计含量%15.54 4.31 58.47 21.13 0.35 100m3(标) 487.39 135.33 1833.84 668.34 11.25 3136.16 kmol 21.76 6.04 81.87 29.83 0.50 140.01 剩余的H2O的量为:1184.113-202.9908+2×9.776=1000.6742 m3 (标)=44.6729kmol故出中变炉一段催化床层的变换气湿组分的体积:V总(湿)=135.3272+487.3908+1833.8478+668.34+11.258+1000.6742=4136.838 m3 (标)=184.68kmol故出中变炉一段催化床层的变换气湿组分中H2O的含量H2O%=24.19%故出中变炉一段催化床层的变换气湿组分中CO2的含量CO2%=11.78%同理可得:CO%=3.27%H2%=44.33%N2%=16.16%CH4%=0.27%所以出中变炉一段催化床层的变换气湿组分的含量(%)如下:表1-11出中变炉一段催化床层的变换气湿组分的含量(%)Table 1-11 to change in the furnace section of the catalytic bed transform components inwet gas (%)组分CO2CO H2N2CH4H2O 合计含量%11.78 3.27 44.33 16.16 0.27 24.19 100 m3(标) 487.39 135.33 1833.84 668.34 11.26 1000.67 4136.92 koml 21.76 6.04 81.87 29.83 0.50 44.67 184.681.5.2对出中变炉一段催化床层的变换气的温度进行估算:已知出中变炉一段催化床层的变换气湿组分的含量(%)如下:表1-12出中变炉一段催化床层的变换气湿组分的含量(%)Table 1-12 to change in the furnace section of the catalytic bed transform components inwet gas (%)组分CO2CO H2N2CH4H2O 合计含量%11.78 3.27 44.33 16.16 0.27 24.19 100 m3 (标) 487.39 135.32 1833.84 668.34 11.26 1000.67 4136.92 koml 21.76 6.04 81.87 29.83 0.50 44.67 184.68根据:Kp =(H2%×CO2%)/(H2O%×CO%)计算得K=6.6查《小合成氨厂工艺技术与设计手册》知当Kp=6.6时t=445℃设平均温距为35℃,则出中变炉一段催化床层的变换气温度为:445℃-35℃=415℃1.5.3 中变炉一段催化床层的热量衡算已知条件:进中变炉一段催化床层的变换气温度:330℃出中变炉一段催化床层的变换气温度为:415℃可知反应放热Q在变化气中含有CO,H2O,O2,H2这4种物质会发生以下2种反应:CO +H2O=CO2+H2 (1)O 2 + 2H2= 2 H2O (2)这2个反应都是放热反应。