劳斯莱斯精益案例
某汽车公司精益生产改善案例

某汽车公司精益⽣产改善案例某汽车公司精益⽣产改善案例某汽车零部件公司⽣产现状及精益⽣产改善⽅案⼀、某汽车零部件公司⽣产现状某汽车零部件公司为提⾼职⼯的⽣活⽔平,每年进⾏调薪并提供各种福利。
近⼏年随着国际能源价格的⾛⾼。
原材料价格也持续提⾼,但该公司产品价格没能同步反应,这导致该公司运营成本上升,利润率降低。
共次在产品上的竞争愈演愈烈,导致该公司争取新业务时需要更具竞争⼒的价格,更加影响了本已不多的利润空间。
利润空间的减少需要通过节约运营成本,提⾼⽣产效率来加以弥补。
.通过该公司的调查发现其主要⾯临以下问题:1、⽣产⽅式落后,统⼀下发⽣产计划进⾏推动式⽣产使各车间成为“孤岛”。
现场、库房存在⼤量库存,占⽤⼤量空间和资⾦,同时带来质量隐患;2、设备管理粗放,很少关⼼设备利⽤率,设备停机、换模时间较长;3、现场管理松散,⽣产效率低。
该公司要想⽣存和发展就必须开始进⾏持续改进和成本控制,要达到这⼀⽬的该公司需要优化调配⼈员、设备、资⾦等资源,使它们发挥最⼤效益。
“没有⼀个国家可以在低廉的⼯资基础上在全球竞争中建⽴长时间的绝对优势,但可以通过精益⽣产和精益理念来维系优势”。
⼆、该公司精益⽣产改善⽅案借助价值流图析法分析,价值流是当前产品通过其基本⽣产过程所要求的全部活动。
这些活动包括增加价值和不增加价值两部分,简单地说包括从供应商到⼯⼚制造再到顾客交付的过程。
.⾸先确定实施精益⽣产⽅式的产品线,然后对选取的产品线进⾏研究。
收集数据,绘制现阶段的价值流程图。
通过对现有价值流程图的分析,找到需要改进的地⽅并运⽤精益的改善⼯具提出改进⽅案。
绘制未来改进后的价值流程图,实施精益⽣产⽅式,验证改进效果。
通过对该公司精益⽣产的探索和研究,共对打公司的⽣产管理⽅式做了如下改善:1、⽬视化管理为了更⽅便的掌握⽣产情况,对该公司进⾏⽬视化管理。
设⽴控制中⼼,将需要的信息集中展⽰。
按照管理层级的不同将控制中⼼分为:⽣产单元控制中⼼、⼯⼚控制中⼼,运营控制中⼼。
汽车行业五导向案例分析

•
有了新车的设计思路,福特的设计专家开始着手新车型 的设计开发。样机一再改进,最后确定了方顶、流线型、前 长后短、低矮大方的形状;整车显得既潇洒又矫健。 在命名上,用“野马”作为新型车的名字,显示出车的 性能和速度,使人产生飞驰的联想;同时有任君驰骋天地间 的狂放气魄,与美国人崇尚自由的性格不谋而合。 在价格设计上,公司在通过对52对有中等收入的青年夫 妇的消费心理的研究,最终艾柯卡把车价定在2368美元。 最后在汽车上市后,福特不惜投入重金,举办一系列的 宣传促销活动。 从产品设计、名称选择、价格制定到具体的促销活动, 福特公司的精心策划获得了巨大的市场回报。到1965年4月 16日,即野马诞生一周年之际,野马车已售出418812辆, 创下了福特公司的销售记录。野马车两年内即为福特公司创 造了11亿美元的纯利润。
• 同时因手工艺的繁多和客户的个性预订要求,劳斯莱斯几乎 不可能生产两辆一模一样的车。而为了迎合车主的尊贵感, 劳斯莱斯还严格控制新车的供给量,使想购车的美国人要在 预订半年甚至更长时间后才能拿到车。 • 在广告方面,劳斯莱斯广告成功的抓住了上层阶层重面子、 好显示自己的成功、地位和身份的欲望,触到了他们的痒处, 其尊贵的形象,怎能让他们不动心? • 该公司在英国的广告强调“买辆劳斯莱斯犒赏自己多年来的 辛勤工作”,一语击中了那些事业有成,家庭和睦,辛苦了 半辈子以后欲享受生活,显示身份地位的成功者的心。 • 在美国,广告则套用了亨利•詹姆士的名言“尽情享受,这 是一个不能不犯的错误”,恰与当时美国社会重享乐的风气 契合。
•
这一系列的营销策略,体现出了比亚迪关注客户体验的宗旨。 消费者切身体验到了的产品与服务价值,实现了有效价值, 带来公司价值提升。
五、推销(销售)观念—通用汽车危机管理
劳斯莱斯定理-概述说明以及解释

劳斯莱斯定理-概述说明以及解释1.引言概述部分的内容可以根据劳斯莱斯定理的背景和核心价值观来进行阐述。
下面是一个示例:1.1 概述劳斯莱斯定理是指劳斯莱斯汽车公司所秉持的一系列核心原则和价值观,这些原则和价值观贯穿于该汽车品牌的诞生、发展和成功之中。
劳斯莱斯定理的重要性在于它不仅仅是一种商业策略或品牌定位,更是一种对于卓越、质量和奢华的承诺。
劳斯莱斯汽车公司成立于1906年,创始人为查尔斯·斯图尔特·劳斯和亨利·罗伊斯。
从一开始,他们就以追求卓越和完美为理念,致力于打造出世界上最顶尖的豪华汽车。
劳斯莱斯的创始人们对技术和工艺的追求,使他们的汽车在当时就享有盛誉,并且成为当时英国贵族和富裕人士的首选座驾。
劳斯莱斯定理的核心可概括为三个方面:卓越品质、无与伦比的豪华和个性化定制。
首先,劳斯莱斯汽车以卓越品质而闻名于世。
他们对材料的选择、制造工艺的精益求精以及对每一个细节的极致关注,使得劳斯莱斯汽车成为卓越工艺和精湛技术的典范。
每一辆劳斯莱斯汽车都是由数以百计的工匠精心打造而成,每一辆都是独一无二的艺术品。
其次,劳斯莱斯汽车的豪华程度无与伦比。
从车内配置到选用的材料,从舒适性到驾驶感受,劳斯莱斯汽车都在追求极致的奢华体验。
豪华对于劳斯莱斯来说并不仅仅是外表的华丽或者贵重的装饰品,更多的是体现在对细节的极致追求和对驾乘者感受的深刻关怀。
最后,劳斯莱斯汽车以个性化定制而闻名。
他们始终坚持根据每一位客户的独特需求和偏好进行量身定制,以确保每一辆劳斯莱斯汽车都能真正体现车主的个性和品味。
无论是车身颜色、内饰材料还是个性化配置,客户都可以根据自己的愿望进行自由选择,使得每一辆劳斯莱斯汽车都成为独一无二的艺术品。
综上所述,劳斯莱斯定理是劳斯莱斯汽车公司所秉持的一系列核心原则和价值观,其以卓越品质、无与伦比的豪华和个性化定制为特点。
劳斯莱斯定理的确立和坚持,使其成为世界顶级汽车品牌之一,并且时至今日,劳斯莱斯汽车仍然继续引领着豪华汽车行业新的发展潮流。
莱斯莱斯定制版曜影
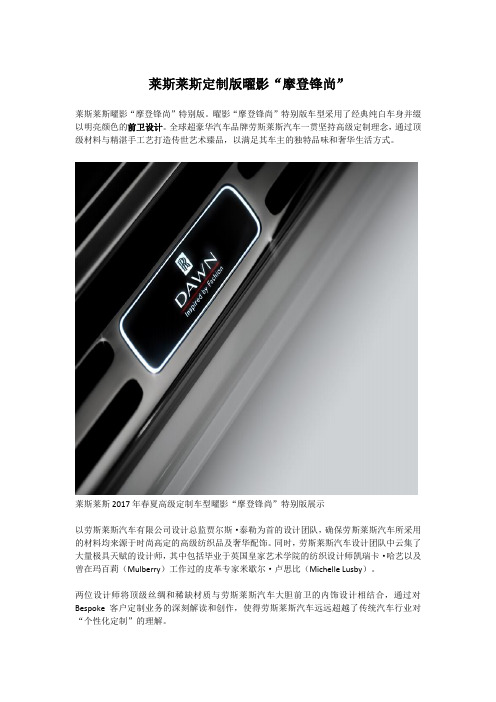
莱斯莱斯定制版曜影“摩登锋尚”莱斯莱斯曜影“摩登锋尚”特别版。
曜影“摩登锋尚”特别版车型采用了经典纯白车身并缀以明亮颜色的前卫设计。
全球超豪华汽车品牌劳斯莱斯汽车一贯坚持高级定制理念,通过顶级材料与精湛手工艺打造传世艺术臻品,以满足其车主的独特品味和奢华生活方式。
莱斯莱斯2017年春夏高级定制车型曜影“摩登锋尚”特别版展示以劳斯莱斯汽车有限公司设计总监贾尔斯·泰勒为首的设计团队,确保劳斯莱斯汽车所采用的材料均来源于时尚高定的高级纺织品及奢华配饰。
同时,劳斯莱斯汽车设计团队中云集了大量极具天赋的设计师,其中包括毕业于英国皇家艺术学院的纺织设计师凯瑞卡·哈艺以及曾在玛百莉(Mulberry)工作过的皮革专家米歇尔·卢思比(Michelle Lusby)。
两位设计师将顶级丝绸和稀缺材质与劳斯莱斯汽车大胆前卫的内饰设计相结合,通过对Bespoke客户定制业务的深刻解读和创作,使得劳斯莱斯汽车远远超越了传统汽车行业对“个性化定制”的理解。
一、设计理念:为了符合2017年春夏高定款风格,设计师们在设计曜影“摩登锋尚”特别版时,车身颜色采用了偏中性的帆布白。
另外可以自由搭配三种强调色:宝石红(Mugello Red)、藏蓝色(Cobalto Blue)和橘色(Mandarin),这些颜色完美融绘在曜影“摩登锋尚”特别版的内饰中。
当曜影“无声的芭蕾舞”缓缓打开时,仿佛阻挡一切外部纷扰、喷薄驶出,并划出一道炫美的色彩,吸引着大众的目光。
二、定制角度谈设计:最优秀的定制之美,总是展现在每一个细节之中。
开启曜影的马车式车门,经典的极地白(Arctic White)与黑色内饰色调巧妙搭配,并可从容搭配三种强调色:宝石红、藏蓝色和橘色,尽显超凡现代的装饰美感。
除了极地白皮质座椅搭配精心缝制的刺绣头枕及座椅缝线之外,工匠大师们对双色拼接方向盘的拼接处每一个针脚都进行了反复推敲,力求每一处细节都极致完美,其精湛技艺与世界顶级服饰所呈现的复杂工艺相比也毫不逊色。
品质管理的实践案例与成功经验

品质管理的实践案例与成功经验品质管理可以简单地定义为组织如何制定、实施和评估产品和服务的过程。
在现代商业环境中,许多企业都注意到品质管理的重要性,并将它作为其成功的核心策略之一。
本文将讨论几个品质管理的实践案例及其成功经验,并提供一些实用的建议和技巧,以帮助企业提高其品质管理水平。
实践案例一:Toyata汽车Toyata汽车是一个值得关注的品牌,因为他们以严谨的品质管理流程而闻名于世。
以下是Toyata汽车实践珂质管理的几个实例:1. 减少浪费:Toyata汽车通过推行精益生产模式以及“只生产客户订单”原则来减少浪费。
2. 持续改进:Toyata汽车通过实践Kaizen原则,不断改进生产流程,提高生产效率和精度,并确保产品品质。
3. 集中精力:Toyata汽车把员工培训和开展员工自我学习视为品质管理体系的重要组成部分,以确保员工的能力和素质与公司的要求相匹配。
4. 全面质量保证:Toyata汽车实行质量保证措施,从设计阶段开始到生产,到销售,再到售后服务的每个领域都掌握精准的控制方法,以确保每个环节都符合标准。
成功经验:Toyata汽车建立了一个系统化的品质管理流程,其中包括标准化操作程序(SOP) 、持续改进,以及员工培训和能力提升。
通过采取这些举措,Toyata汽车成功地实现了优质产品的整个产业链。
实践案例二:苹果公司苹果公司是另一个成功实践品质管理的例子。
苹果公司以其优秀的用户体验和卓越品质而闻名于世。
以下是苹果公司实践品质管理的几个实例:1. 过程控制:苹果公司把控产品生产的每一个环节,从材料采购、生产到交付等环节,通过设置各种检验点和控制程序,确保每个产品都能符合用户的要求。
2. 不断挑战自我:苹果公司不满足于现有的标准和成就,继续探索和创新,推出不断涌现的创新产品和技术。
在坚持不断创新的同时,苹果公司保持其产品的稳定性和品质不变。
3. 严格管控供应商:苹果公司认为,如果想达到好的品质和服务,必须控制好整个供应链,苹果公司追求的要求就是选对好的合作伙伴,并对合作伙伴进行持续性的评估和监控。
莱卡,相机王国里的劳斯莱斯
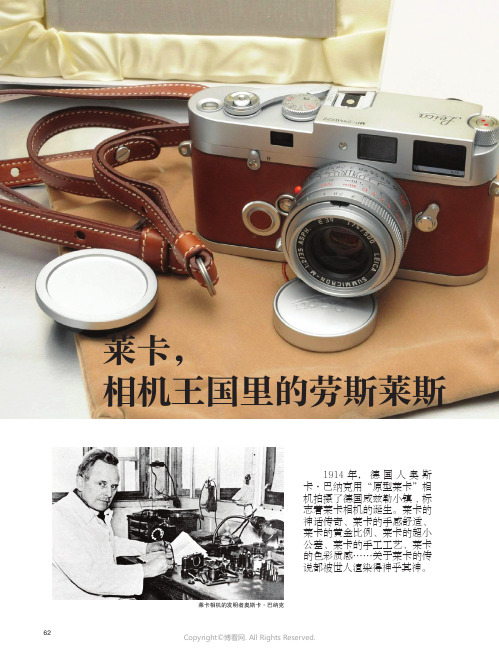
62莱卡,相机王国里的劳斯莱斯莱卡相机的发明者奥斯卡·巴纳克 1914年,德国人奥斯卡·巴纳克用“原型莱卡”相机拍摄了德国威兹勒小镇,标志着莱卡相机的诞生。
莱卡的神话传奇、莱卡的手感舒适、莱卡的黄金比例、莱卡的超小公差、莱卡的手工工艺、莱卡的色彩质感……关于莱卡的传说都被世人渲染得神乎其神。
Copyright©博看网. All Rights Reserved.63二战期间,盟军轰炸机不断地对德国的工业城市轮番轰炸,连柏林都难于幸免。
然而,位于德国中西部的工业重镇威兹勒,却被美国军方指定为唯一不被轰炸的城市,自始至终未落一枚炸弹。
原因是这里有一家著名的相机制造厂——莱卡(Leica)。
莱卡相机不仅是许多美军飞行员的挚爱,也是美国战地记者手中必备的工具,最重要的是,巴顿将军是莱卡相机的大“粉丝”。
凭借卓越的产品性能和完美的品质表现,莱卡相机赢得了包括巴顿将军在内的世人的青睐和尊重,并在战时获得同情,从而挽救了威兹勒这座城市。
“质量就是生命”这句格言,由莱卡相机赋予了更为深层的含义。
莱卡不是一台万能相机,但在它所擅长的领域,又是最好的。
选择莱卡还是不选择莱卡,是品位,是需要,是文化,是爱好,哪一个理由都行,无论哪一种理由都会牵扯很多的思考。
莱卡范儿想象这样的场景:穿着淡色休闲服,肩挎牛皮包,戴着毡帽,漫步在绿草丛中,脖子上挂着轻便的莱卡相机,据说在英国,一些绅士不拍照,身上也常挂一台莱卡,作为身份的象征。
从学术意义上来说,这是一样值得夸耀并显示主人懂行的标志;从物质层面上来说,这是一件饱含人文气质且透露着主人优雅腔调的饰品;从精神意境上来说,这是一种钢铁意志和精益求精结合的典范。
莱卡是光学和机械融合成像的黄金时代产物。
一位优秀的专业摄影师不一定拥有莱卡,但是对摄影略通一二的人士不会不知道莱卡相机。
对于现代的人们来说,它已不单纯的是一个品牌相机,而是近乎某种信仰,某种潜藏于内心梦想般的追求。
精益求精的案例
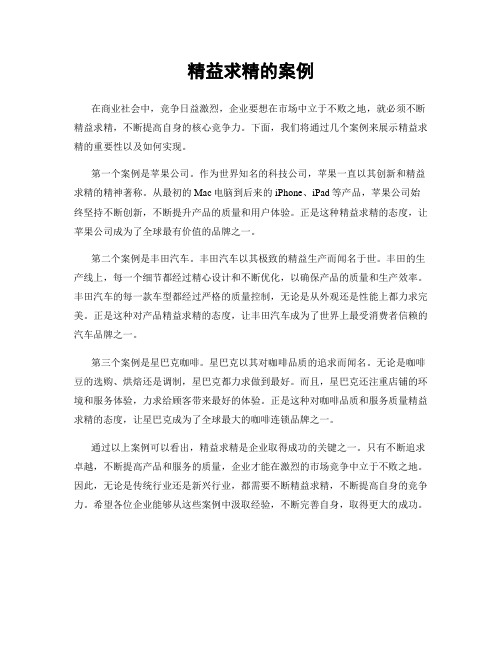
精益求精的案例
在商业社会中,竞争日益激烈,企业要想在市场中立于不败之地,就必须不断精益求精,不断提高自身的核心竞争力。
下面,我们将通过几个案例来展示精益求精的重要性以及如何实现。
第一个案例是苹果公司。
作为世界知名的科技公司,苹果一直以其创新和精益求精的精神著称。
从最初的Mac电脑到后来的iPhone、iPad等产品,苹果公司始终坚持不断创新,不断提升产品的质量和用户体验。
正是这种精益求精的态度,让苹果公司成为了全球最有价值的品牌之一。
第二个案例是丰田汽车。
丰田汽车以其极致的精益生产而闻名于世。
丰田的生产线上,每一个细节都经过精心设计和不断优化,以确保产品的质量和生产效率。
丰田汽车的每一款车型都经过严格的质量控制,无论是从外观还是性能上都力求完美。
正是这种对产品精益求精的态度,让丰田汽车成为了世界上最受消费者信赖的汽车品牌之一。
第三个案例是星巴克咖啡。
星巴克以其对咖啡品质的追求而闻名。
无论是咖啡豆的选购、烘焙还是调制,星巴克都力求做到最好。
而且,星巴克还注重店铺的环境和服务体验,力求给顾客带来最好的体验。
正是这种对咖啡品质和服务质量精益求精的态度,让星巴克成为了全球最大的咖啡连锁品牌之一。
通过以上案例可以看出,精益求精是企业取得成功的关键之一。
只有不断追求卓越,不断提高产品和服务的质量,企业才能在激烈的市场竞争中立于不败之地。
因此,无论是传统行业还是新兴行业,都需要不断精益求精,不断提高自身的竞争力。
希望各位企业能够从这些案例中汲取经验,不断完善自身,取得更大的成功。
kaizen改善案例

kaizen改善案例在大规模制造业领域中,日本的Kaizen改善方法以其持续改进和精益生产的理念而闻名。
它的主要目标是通过消除浪费和改善流程,提高生产效率和产品质量。
下面是一些关于如何在制造业中应用Kaizen的改善案例。
1.价值流分析和流程改进价值流分析是Kaizen方法的核心。
它的目的是识别整个生产过程中的所有非价值增加活动,并找到解决这些问题的方法。
假设有一个汽车制造公司,该公司发现他们的装配线上的工人每天都要花费大量时间在获取所需的零部件和工具上。
通过进行一个价值流分析,公司发现工人们不得不走过很长的距离,从仓库中取零件。
为了改善这个问题,公司搬迁了仓库,将其放置在更靠近装配线的位置。
这样,工人们就不再需要走那么远的距离,并且能够更快地取得所需的零部件和工具,从而提高了生产效率。
2.设备维护和避免停机时间在制造业中,机器的损坏和停机时间是生产效率低下的主要原因之一。
一家化工公司发现他们的反应釜经常出现故障,并且停机时间很长。
为了解决这个问题,公司采取了预防性维护措施,定期检查和维护反应釜。
此外,他们还实施了一个定期培训计划,让操作员能够更好地了解和处理设备故障。
这些改进措施不仅降低了机器故障和停机时间,还提高了生产效率和产品质量。
3.标准化和员工培训标准化是另一个重要的Kaizen改善方法。
一家制造公司发现他们的不同工作站之间存在差异和不一致,导致了生产效率的下降。
为了解决这个问题,公司制定了一套标准作业程序,并确保每个员工都接受培训以遵循这些程序。
此外,公司还定期对员工进行技能培训,提高他们的专业知识和技能水平。
这些改进措施不仅提高了生产效率,还减少了错误和产品缺陷。
4.多功能和自主团队多功能和自主团队是Kaizen改善方法的核心理念之一。
一家制造公司发现他们的生产线上的工人只负责单个工作站,这导致了生产效率低下和工时浪费。
为了解决这个问题,公司进行了岗位轮换,并培养了一支多功能的工作队伍。
劳斯莱斯双R神话的背后故事
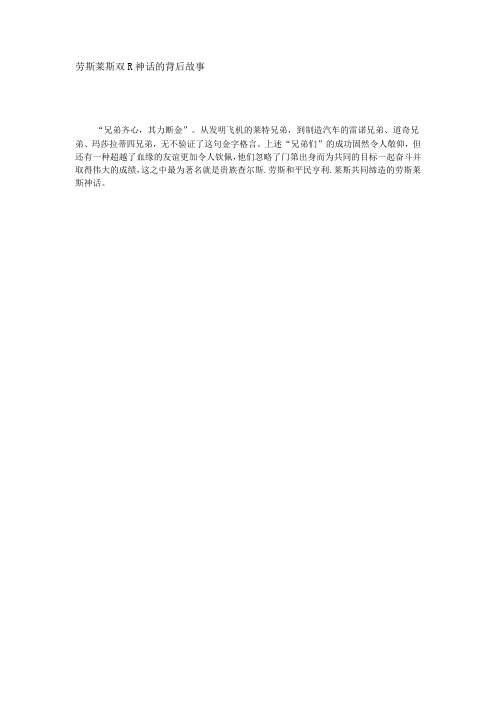
劳斯莱斯双R神话的背后故事“兄弟齐心,其力断金”。
从发明飞机的莱特兄弟,到制造汽车的雷诺兄弟、道奇兄弟、玛莎拉蒂四兄弟,无不验证了这句金字格言。
上述“兄弟们”的成功固然令人敬仰,但还有一种超越了血缘的友谊更加令人钦佩,他们忽略了门第出身而为共同的目标一起奋斗并取得伟大的成绩,这之中最为著名就是贵族查尔斯.劳斯和平民亨利.莱斯共同缔造的劳斯莱斯神话。
故事的主角查尔斯.斯图亚特.劳斯1877年出生在英国伦敦一个显赫的贵族家庭。
与只关心工厂和信贷收益的新贵族不同,这位贵族显然受到了当时科技大飞跃的时代影响,因而对科学表现出浓厚的兴趣。
在其念伊顿公学(中学)时候,劳斯便亲手安装了一台刚刚发明不久的发电机,而后他进入剑桥大学土木工程系学习,在此这期间,他迷上了新奇的汽车以及汽车运动,在他毕业的时候,他已成为一名赛车高手。
1903年,劳斯驾驶着一辆80马力的轿车在柏林创造了每小时150公里的汽车速度记录。
故事的另一个主角弗雷德理克.亨利.莱斯的身世与劳斯相比显然有着天壤之别。
莱斯1863年出生在一个贫困的磨坊主家庭,由于生活所迫,莱斯曾经上街卖过报纸,而后有在铁路公司当学徒。
尽管出身贫寒,莱斯却在机械方面表现了出人的天赋。
1904年,年过40的莱斯亲手设计制造了一辆2缸汽车,这辆车在当时堪称杰作,该车使用马达起动而非传统的摇柄,并且该车运行非常平顺,故障率很低。
恰巧莱斯的一名商业伙伴亨利.埃德蒙兹是英国皇家汽车协会的会员,他把这个这件事告诉给了同为协会会员的劳斯,没想到却让劳斯极感兴趣。
这样,境遇和背景完全不同的两个人被一件事连在了一起。
其实劳斯一直有一个愿望:找出一款能与外国汽车质量相媲美的英国本土汽车,并能用自己的名字命名这款汽车。
而作为工程师的莱斯志向与劳斯不谋而合:不计成本,设置制造质量最优良的汽车,并卖个识货的人。
正是有这种共同的志向,最终促成两人跨越门第的相识。
1904年5月4日,在亨利.埃德蒙兹的引荐下,两人在曼彻斯特的米兰德宾馆会面,并且一见如故。
非常好的精益生产案例值得借鉴

非常好的精益生产案例值得借鉴前言精益生产是一种专注于提高效率和降低浪费的经营管理方法。
通过消除不必要的步骤和资源浪费,精益生产可以帮助企业实现更高的产出和更好的质量,从而获得竞争优势。
本文将介绍一些非常好的精益生产案例,展示出这种方法的实际应用和可行性,以供其他企业借鉴。
案例一:丰田汽车丰田汽车是精益生产的经典案例之一。
丰田公司以“丰田生产方式”(Toyota Production System,TSP)闻名于世。
TSP 的核心思想是通过限制生产速度来提高质量,消除浪费和降低成本。
丰田将员工视为最重要的资源,鼓励员工参与改进流程,并不断学习和提高。
通过实施流程改进和标准化操作,丰田成功地降低了库存水平、缩短了交付周期,并提高了产品的质量。
流程改进丰田汽车通过实施精细的生产计划和精确的生产控制来改进流程。
他们使用所谓的“拉动式生产”(Pull Systems),这意味着生产进程只会在下一阶段需要材料和部件时才会启动,以此保持生产流程的稳定性。
这种方式可以防止过度生产和库存积压,并减少浪费。
标准化操作丰田汽车非常注重标准化操作。
他们制定了详细的作业指导书,确保每位员工都能按照标准程序工作。
通过标准化操作,丰田能够减少错误和变量,并提高整体生产效率。
标准化操作还使得员工之间可以互相替代,以应对人员变动和流程变化。
持续改进丰田汽车秉持着“持续改进”的信念。
他们鼓励员工积极参与改进流程,并通过小改进和创新来不断提高生产效率和质量。
丰田实行所谓的“就地解决问题”(Genchi Genbutsu),即员工应该亲自去现场了解问题并找到解决方案。
这种方法帮助丰田构建了一个持续改进的文化,使得所有员工都在努力寻找问题并付诸行动。
案例二:美国空军美国空军也是一个非常成功的精益生产案例。
空军一直致力于在各个领域实施精益生产,以提高效率、降低成本,并最大限度地满足任务需求。
下面将以飞机维修作业为例,介绍空军如何运用精益生产方法改进维修流程:改进维修流程空军通过改进维修流程来提高效率。
劳斯莱斯从起跑到起飞

劳斯莱斯从起跑到起飞一百一十年前,在大不列颠制造业有一对“R氏绝配”,一个叫查尔斯·罗尔斯(CharlesRolls),另一个叫亨利·罗伊斯(HeyRoyce)。
由“R氏绝配”支起的制造业,就是现在已享誉全球的劳斯莱斯(Rolls-Royce)。
“罗罗配”起跑作为最有影响力的发动机大帝,世界500强企业的常客,劳斯莱斯的标识为上中下结构,Rolls(罗尔斯)在上,Royce(罗伊斯)在下,双R叠合居中。
观图识义,一目了然,罗尔斯和罗伊斯作为劳斯莱斯的创始人,名字被彪炳于标识中,而双R意味着他们之间融洽、和谐的合作关系。
不仅于此,劳斯莱斯(也叫罗尔斯·罗伊斯)的企业名称,也是取于双R姓氏。
那么,罗尔斯和罗伊斯是如何打造劳斯莱斯——这支超级帝国基业的呢?这就要从他们相识说起。
亨利·罗伊斯(1863-1933)出身普通的工人家庭,14岁就开始在铁路工厂当学徒,凭着他高超的天赋和对汽车动力的潜心研发,不惑之年时已是曼彻斯特城一位不可多得的发动机工程师。
1904年,罗伊斯终于制成了三辆汽车。
这对当时尚无自己品牌汽车的英国来讲,本来是个好消息,但很遗憾,思想趋于保守的英国民众对尚未经权威认证的产品向来并不感冒,罗伊斯的成果没有给英国汽车行业带来震动。
英国皇家汽车协会会员、兼营汽车销售的赛车手罗尔斯知道这个消息后,事情才有了意外的结果。
查尔斯·罗尔斯(1878-1910)出身于名望贵族世家,他钟情于各种各样的冒险运动,尤其赛车更是他的最爱。
早在罗尔斯就读剑桥大学时,曾买下一辆豪华的标致轿车,并加入了大不列颠皇家汽车俱乐部。
当他从剑桥大学毕业时,已是一名出色的驾车高手,并创造了时速150公里的世界纪录。
1902年,罗尔斯注册了一家公司,开始从事汽车生意,并且很快成为英国最有实力的汽车经销商之一。
1903年底,莱氏兄弟的第一架飞机在美国试飞成功,受“飞行者一号”的鼓舞,罗尔斯的公司又开始涉猎航空运动领域。
鬼魅无他——劳斯莱斯古思特

作为劳斯莱斯家族中最年轻的四门轿车,古思特是家族鬼魅气质绝佳的承载者,它既可以像幻影那样载你去奢华的社交场合,也可以像魅影般衬托你的时尚触角,从欢庆女神的立标到尾排发出的每一声喘息,都在诉说着这个传奇品牌与众不同的传奇身世。
撰文/Stanley 摄影/乔治
鬼魅无他——劳斯莱斯古思特
rolls-royce
goodw ood
实际上,作为古思特的第二代车型,这辆配色低调的车相比前款的造型进化并不显著,每一个被奉为经典的设计元素都不该被拿来擅改。
仅靠大灯轮廓的调整、车身线条锋利度的收敛,古思特就能够在保持原有气度的同时,对属的black badge系列车款。
虽然“经典”是古思特打造的基调,
但尖端的科技同样是劳斯莱斯屹立于
金字塔尖上的立身之本。
LED照明技
术的最新成果被运用在古思特上,自
适应技术大幅增强了LED车灯功能。
劳斯莱斯 古思特加长版
诸葛嵩
3
5
6
7。
工匠精神精益求精的例子

工匠精神精益求精的例子工匠精神是一种追求完美、专注细节、注重品质的态度。
它是一种精神,一种工作态度,一种人生追求。
在现代社会中,工匠精神被越来越多的人所认同和追求。
而精益求精则是工匠精神的一种具体表现,它是对自己的要求更高、更严格,不断追求完美的过程。
下面就让我们看看一些工匠精神精益求精的例子。
1. 马自达的“魂动设计”马自达汽车的“魂动设计”是工匠精神的典范。
马自达汽车的设计师们追求的不是华丽的外观,而是一种简洁、流畅、有韵律感的设计。
他们注重每一个细节,每一条线条的流畅和比例的协调。
他们不断地打磨着每一个细节,直到达到完美的境界。
正是这种工匠精神,让马自达汽车成为了设计和品质的代表。
2. 苹果公司的“精益求精”苹果公司是全球知名的科技公司,它的成功离不开工匠精神和精益求精的精神。
苹果公司的设计师们注重每一个细节,从设计到生产再到销售,都要追求完美。
他们不断地改进产品,让它更加符合消费者的需求。
苹果公司的创始人乔布斯曾说过:“我们不是要让消费者告诉我们他们需要什么,我们是要告诉他们他们需要什么。
”3. 一位精益求精的厨师在餐饮行业中,有一位厨师因为他的工匠精神和精益求精的精神而被人们所称赞。
这位厨师在制作菜品的时候,注重每一个细节,从食材的选择到烹饪的技巧,都要追求完美。
他不断地尝试新的菜品,让菜品更加符合顾客的口味。
他的菜品因为精益求精的态度而备受顾客的喜爱。
4. 德国的“精益制造”德国是全球知名的制造业大国,它的制造业之所以能够获得如此高的声誉,离不开工匠精神和精益制造的精神。
德国的制造业注重每一个细节,从零部件的制作到产品的组装,都要追求完美。
他们不断地改进制造工艺,让产品更加符合市场的需求。
正是这种工匠精神和精益制造的精神,让德国的制造业在全球范围内都享有盛誉。
工匠精神和精益求精的精神是一种追求完美、追求卓越的精神。
它们不仅仅是一种工作态度,更是一种生活态度。
在现代社会中,我们需要更多的工匠精神和精益求精的精神,让我们的生活更加美好。
经营制胜智慧精要精益产品质量管理技术要诀
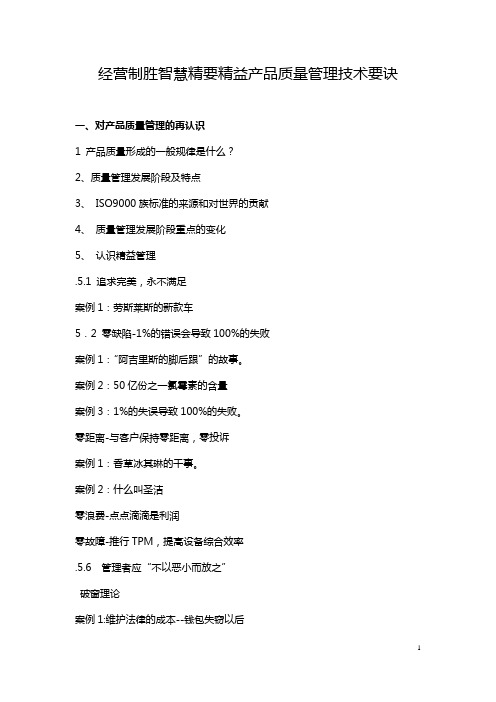
经营制胜智慧精要精益产品质量管理技术要诀一、对产品质量管理的再认识1 产品质量形成的一般规律是什么?2、质量管理发展阶段及特点3、ISO9000族标准的来源和对世界的贡献4、质量管理发展阶段重点的变化5、认识精益管理.5.1 追求完美,永不满足案例1:劳斯莱斯的新款车5.2 零缺陷-1%的错误会导致100%的失败案例1:“阿吉里斯的脚后跟”的故事。
案例2:50亿份之一氯霉素的含量案例3:1%的失误导致100%的失败。
零距离-与客户保持零距离,零投诉案例1:香草冰其琳的干事。
案例2:什么叫圣洁零浪费-点点滴滴是利润零故障-推行TPM,提高设备综合效率.5.6 管理者应“不以恶小而放之”破窗理论案例1:维护法律的成本--钱包失窃以后案例2:算了,差不多!执行过程不能打折扣5.7 精益质量管理的精髓5.8 精益质量管理过程5.9 精益质量管理的语言-----财务和PPM 5.9.1 质量成本的构成5.9.2挑战极限的6б管理--PPM5.9.3 6σ管理二、现场产品质量的精益管理1、现场产品精益质量管理总体框架2、现场精益质量管理关键策略3、作业标准化是现场产品精益质量管理的核心3.1 标准化操作3.2 标准化操作指导书3.3 操作员学练的标准化4、不合格产品控制5、钻石法1 –4 步6、快速反应程序6.1快速反应是这样一个系统:6.2 快速反应会议7、现场质量验证7.1 现场质量检验点设置7.2 现场质量检验点文件编制7.3 现场质量检验点资源配备7.4 检验点实施并检查7.5 检验点异常纠正7.6 检验点评价与改进8 质控点的设置和精益管理三、产品质量统计过程控制(SPC)1、SPC及特点2、制程控制系统3、SPC常用术语解释4、SPC--问题解决常用工具5、SPC--6步系统问题解决流程和持续改进模式6、各种类型控制图公式汇总四、防错技术的应用1、防错的概念2、出错的本质3、五种类型的错误防止方法4、防差错装置特点5、防错验证。
精益求精--二战中的劳斯莱斯

精益求精--二战中的劳斯莱斯在1936年,为了满足英国皇家空军(以下简称RAF)对新一代作战飞机的迫切需求,劳斯莱斯公司的梅林发动机(Merlin)被立刻提上了量产日程。
第一款由梅林驱动的飞机于1937年服役,在慕尼黑危机期间RAF就已经装备了97架飓风(Hurricane)和第一支喷火中队。
1940年梅林发动机开始被大量投入实战使用,例如在法国战场对抗德国人入侵的巴特尔轰炸机(Fairey Battle)...但这款设计落后的飞机很快便沦为了Me 109的猎物---仅在40年5月14号,71架出勤的飞机只有31架安全返航。
飞行中的巴特尔轰炸机在随后敦刻尔克上空激烈的空战里,德国人却也发现了飓风和喷火这俩难缠的对手,这两款机型也让德空在之后的不列颠战役中吃尽了苦头。
前线激烈的机械绞杀离不开后方的民众的辛勤劳动:虽然在敦刻尔克战役英国人损失了386架飓风和67架喷火,但6月份装备梅林发动机的战斗机数量又马上恢复到了600架,9月末更是到了700余架。
轰炸机方面,同年秋季,双梅林的惠特利轰炸机(Armstrong Whitworth Whitley)和四台大力神(Hercules,并非RR产品)的哈利法克斯轰炸机(Halifax)展开了对德夜间轰炸行动。
41年初,一种更先进的轰炸机开始服役,它便是由两台秃鹰发动机驱动的曼彻斯特(Avro Manchester)。
曼彻斯特轰炸机,两侧发动机的外观就好像说着“我们不一样”秃鹰(Vulture),作为一款较为粗暴的X型24缸发动机,直接由两台红隼(Kestrel)并联(曲轴箱合成)而成,使用不可避免的冒出种种问题:发动机曲轴处与活塞连接部分(master rod bolt)经常出故障,以至于几乎将发动机切成两半,螺旋桨难以保持正常旋转。
狮鹫发动机,X型的气缸布局往往导致在一侧整流罩上就要安排两排排气管虽然进过一系列改进后(机构优化以及将发动机运转状态从+ 6磅@3000rpm更改为输出相同的+ 9磅@2850rpm以提高使用寿命)秃鹰的可靠性有所提升,但面对同时期竞争者(自家梅林,Bristol的半人马和Napier的军刀)相比并没有优势。
18创新不是扔骰子的事——柠檬车案例的类比说明

创新不是扔骰子的事——柠檬车案例的类比说明1、汽车制造是扔骰子的事吗?上一次坐进车里并担心汽车不能发动是多久之前的事了?好消息是,这个念头上一次闪过脑海的时间距离现在太过久远,你自己估计都想不起来了。
但即便是在20世纪80年代,情况还并非如此。
没错,当时的底特律的确生产了不少好车,但也生产了相当数量的无法正常运转的“笠檬车(1emonCar)1汽车技工虽然会对柠檬车的某个部件进行修理或替换,但问题总是接踵而至。
系统故障多次发生,人们怎么也无法把车完全修好。
这一情形,让生产者和消费者都手足无措。
一种观点认为,“柠檬车”如此常见并不奇怪。
一辆普通的汽车总共拥有将近30,000个独立的部件,其中发动机和座椅等很多部件都是预先做好的。
尽管如此,一条典型的汽车制造线,仍会从多达17个国家的几百个供应商那里收到大约2,000个独一无二的零部件。
从这么多不同的渠道获得这么多的部件,并将部件拼装为一辆可以行驶的汽车,这本身就是一个奇迹。
没错,多年来,人们对于汽车质量问题的解释便是生产过程本身具有随机性。
想要时刻保证万事不出差错是不可能的。
而这,基本上也是现今企业对于创新的看法。
2、试图解决,失败与成功【美国汽车制造商的失败解决】汽车制造商迎难而上,付出最大的努力想要解决这个问题。
他们增加了负责库存和检查的人员,并重新部署站台,对流水线无可规避的一切问题加以管控。
然而很不幸,这些解决方法使成本和装配复杂程度大幅增加,却只是缓解了问题,完全没有触及“柠檬车”出现的根本原因。
不仅如此,美国汽车制造商还在不经意间设计出了一套高效制造成本高昂、质量参差不齐,且不可靠的汽车生产流程。
(日本汽车制造商的成功解决】神奇的是,这种情况已是过去式。
20世纪七八十年代,在爱德华兹•戴明和约瑟夫朱兰的理论启发下,日本的汽车制造商对其生产的汽车进行了大幅改良。
答案就在理论之中。
日本人孜孜不倦她进行实脸,想要找出生产缺陷的原因所在。
他们相信,只要能够找到每个问题的根源,就能够设计出一套防止问题出现的流程。
劳斯莱斯精益案例

– Process parts that consistently meet the minimum customer requirements 100% of the time
Value Steam Mapping
9
#6 Transportation
Definition:
– Moving parts to unnecessary distances from one operation to another
13
Value Stream Analysis Process
Value Steam Mapping
1.0 Select Champion
and Initial Product Family
2.0 Gather, Map, and Analyze Selected Value Stream Data
Value Steam Mapping
• Identify who in your organization will fill these critical roles to support lean implementation – Executive Champion – Implementation Leader – Operations Manager – Technical Support – Other Key Roles?
n
Motio n
Trans Under-
Proceportat utilize5dSP-
ssing ion
eople Sort,Straighten,Sw
Waiti
eep,Standardize
ng
&Self Discipline
企业预测分析案例

企业预测分析案例
劳斯莱斯公司优化了维修计划
劳斯莱斯是全球最大的飞机发动机制造商之一,其正在部署预测分析工具,以有助于其大幅降低发动机的碳排放量,同时优化维修工作,以帮助客户延长飞机的飞行时间。
该公司的智能发动机平台会监控每台发动机的飞行情况、飞行条件以及飞行员使用发动机的方式。
劳斯莱斯公司将机器学习技术应用于这些数据中,以为每台发动机定制保养制度。
劳斯莱斯公司首席信息和数字官斯图尔特•休斯(Stuart Hughes)表示:“我们正在调整自己的保养制度,以确保充分利用每台发动机的使用寿命,而不是手册上所述其应具有的使用寿命。
”“将每台发动机视为一台单独的发动机,这真的是一个存在很多变化的服务。
”
休斯的建议是:专注于帮助您的客户。
分析工具正在帮助劳斯莱斯公司优化其所提供的维修服务,但最终的好处是客户获得了更少的业务中断,因为我们可以更好地预测何时需要维护,并帮助他们安排维护工作。
“劳斯莱斯公司至少20年来一直在监控发动机和每小时油耗,”休斯说。
“这方面的业务并不新鲜。
随着我们的发展,我们开始将发动机视为一个单独的发动机。
更侧重于每台发动机的个性化。
”。
汽车XX精益生产案例1通用

汽车精益生产案例1汽车精益生产案例“柔性化共线生产、精益制造技术”是人们在谈到通用先进的生产方式时经常提及的一点,但很少有人能真正明白什么是柔性化,什么是精益制造。
实际上,柔性化与精益生产不仅仅是通用生产制造的一个环节,更是从采购到销售整个企业流程运作的基本理念。
作为一条柔性化精益制造的生产线,它仅仅是整个GMS(GeneralManufactureSystem,通用制造体系的简称)系统中一个具体的工艺流程罢了。
假如把GMS看作是一架高速运转的机器的话,那么“标准化、缩短制造周期、质量是制造出来的、持续改进、员工参与”则是保证这部机器运转良好的最重要的5个环节,而实际上GMS就是以这5条作为其构成的最基本的原则,而这5条原则又是循序渐进,互为补充,互相促进,最终达到良性循环的效果。
万事有道:标准化应该说,标准化是整个GMS系统最基本的要素,这很好理解,作为一项精益生产方式,最重要的是要确立标准和规范,只有在确立标准的基础上才能实现大规模的精益生产,标准化是现代开端的标志。
同时标准化所设定的基准又是持续改进的基础,同时他能支持最佳的操作方法,更有助于解决问题。
看似简单的标准化实际上包含着众多方面,诸如工作场地布臵标准化、定额工时管理的标准化、标准化的作业流程以及简单明了的视觉标记的运用和管理。
工具、材料摆放在工位或者岗位的什么地方,是否能使操作的员工最直接、最有效、最便捷取用到相应的工具或者材料是工作场地布臵标准化所涉及的范围,一个经过科学测算并且经过不断改进的安全、清洁和安排有序的工作环境必然能带来准确的操作、效率和产品质量的提高,同时工时和**浪费减少到最小.定额工时的管理则是在确定一个基本产品操作完成时间的基础上,对产品的生产环节如手工操作时间、取料时间、行走时间和机器运转时间进行分析,以减少不必要(不增殖)时间浪费,进而提高工作效率的一种标准,但这个标准又可以是一个经过重新测定、持续改进之后的新的动态的标准。
- 1、下载文档前请自行甄别文档内容的完整性,平台不提供额外的编辑、内容补充、找答案等附加服务。
- 2、"仅部分预览"的文档,不可在线预览部分如存在完整性等问题,可反馈申请退款(可完整预览的文档不适用该条件!)。
- 3、如文档侵犯您的权益,请联系客服反馈,我们会尽快为您处理(人工客服工作时间:9:00-18:30)。
Value Stream Analysis Process
Value Steam Mapping
1.0 Select Champion
and Initial Product Family
2.0 Gather, Map, and Analyze Selected Value Stream Data
3. Define product families based on common processes and equipment
14
Value Steam Mapping
Leadership and Champions
Observations
Lean Aerospace Initiative
– A common factor in all observed successful lean implementations is one or more empowered Champions.
Goal:
– Put operations in order; minimize or eliminate the travel distance between them
Value Steam Mapping
10
#7 Waiting
Definition:
– a person or part(s) sitting idle while waiting for material, a supervisor, the next operation, etc.
Goal:
– Produce to Target Cycle Time then eventually produce all operations to Takt Time in the Future State
Value Steam Mapping
6
# 3 Inventory
Definition: material or parts that are stored for future use or shipment
Goal:
– Process parts that consistently meet the minimum customer requirements 100% of the time
Value Steam Mapping
9
#6 Transportation
Definition:
– Moving parts to unnecessary distances from one operation to another
Value Stream Mapp3in.0g
Design Future State
4.0 Implementation Planning and
Execution
1. Understand business goals and customer objectives
2. Select champion and value stream leaders based on proven criteria for success
16
Define Product Families
Value Steam Mapping
• Analyze Product-Volume Chart to separate high runners from low runners
• Analyze Product-Process Matrix to identify similar processing steps and common equipment
Goal:
– Eliminate the unplanned interruptions that occur due to inefficiencies
– Develop continuous flow wherever possible
– Convert waiting to valueadded work
8
#5 Processing (Over & Under)
Definition:
– Extra and/or unnecessary operations
– Standardization of operations not thorough enough
– Processing a part above specifications
Value Steam Mapping
Scrap/Rework
Over-production
Inventory
Motion
Processing
Transportation
Under-utilized People Waiting
(manpower, material, machine)
4
#1 Scrap/Rework
– Without the support of a champion, you should not attempt to implement lean practices and principles -- it is a recipe for disaster
15
Small Group be the role each person will have in supporting lean
• What can you do to get these people to successfully support your efforts
• Executive Champion • Implementation Leader • Operational Mgr
Value Steam Mapping
5
#2 Over-production (Under)
Definition:
– Producing more than is necessary, often causing WIP (Work In Process); working on parts ahead of schedule while delinquent parts wait
Definition:
– Any product that does not meet specifications and therefore either needs to be reworked or scrapped
Goal:
– 100% First Time Through Quality
Value Stream Mapping
The Value Stream - a definition
Value Steam Mapping
“All of the steps required to bring a product or service from raw state through to the customer”
Value Steam Mapping
11
#8 Under-utilized People
Definition:
– Skills untapped, Ideas not implemented and improvements not realized
Goal:
– Tap into the energies and unused improvement ideas from the workforce
– All the steps in the process, working back from customer demand to raw material
– The flow of both material and information and the effect they have on each other
– The distinction between value-added and non-valueadded activity (WASTE)
– The effect all of the above have on meeting the customer’s requirements
3
The 8 Wastes
Before
Value Steam Mapping
After
If you had only 30 seconds to find the unit… ...which storage system would you choose?
7
#4 Motion
Value Steam Mapping
Definition:
Value Steam Mapping
12
Value Steam Mapping
Exercise Worksheet
MANUFACTURING WASTES IDENTIFICATION SHEET
Dept: _______________
NO.
WASTE IDENTIFIED
ScrapOver /oRrekw(rUodnudcetri)ItoPnovryen
n
Motio n
Trans Under-
Proceportat utilize5dSP-
ssing ion
eople Sort,Straighten,Sw
Waiti
eep,Standardize
ng
&Self Discipline
John McLauchlin
Revision Date: 4/25/2000
– Excessive motion beyond what is needed to get the job done