铸件质量检验和检测
铸件质量检验标准

铸件质量检验标准铸件是一种常见的生产工艺,广泛用于各个行业和领域。
铸件质量的好坏直接影响产品的性能和可靠性,因此进行铸件质量检验至关重要。
本文将介绍铸件质量检验的标准和方法。
一、铸件质量检验的重要性铸件质量检验的目的是确保铸件的尺寸精度、表面质量和机械性能达到设计要求。
一方面,铸件的尺寸精度和表面质量直接影响产品的装配和使用;另一方面,对于承受重载或高温等极端工况的铸件来说,其机械性能的好坏关系到产品的安全可靠性。
二、铸件质量检验的标准铸件质量检验的标准包括国家标准、行业标准和企业自身标准。
国家标准是根据相关法律法规制定的,具有强制性,是衡量铸件质量的重要依据。
行业标准是在国家标准的基础上,由行业协会或行业组织制定的,作为行业内铸件质量的参考指南。
企业自身标准是企业根据生产情况和需求制定的,用于规范和管理内部质量控制。
在铸件质量检验中,常用的国家标准有《铸造铁件技术条件》、《铸铝合金件技术条件》等,而行业标准包括《汽车铝合金压铸铸件技术规范》、《船用铸铁件技术条件》等。
企业自身标准则根据企业具体的生产工艺和要求制定,例如《XX公司铸件质量检验标准》。
三、铸件质量检验的方法铸件质量检验的方法主要包括外观检查、尺寸检测和性能测试。
1. 外观检查外观检查是铸件质量检验中最简单直观的方法。
通过肉眼观察铸件的外观,检查是否有裂纹、砂眼、气孔、夹渣等缺陷。
外观检查可以用目视检查或借助放大镜进行观察。
2. 尺寸检测尺寸检测是铸件质量检验中最常见的方法。
主要是测量铸件的外形尺寸、孔径尺寸和壁厚尺寸等。
常用的尺寸测量工具有游标卡尺、内径卡尺、外径卡尺、深度尺等。
尺寸检测可以帮助判断铸件是否满足设计要求。
3. 性能测试性能测试是铸件质量检验中最关键的方法,主要包括力学性能测试、化学成分分析和金相组织分析。
力学性能测试主要是测试铸件的拉伸、弯曲、冲击等力学性能。
化学成分分析可以确定铸件的材料成分是否符合要求。
金相组织分析可以观察铸件的金相组织结构,评估其机械性能。
铸件检验标准
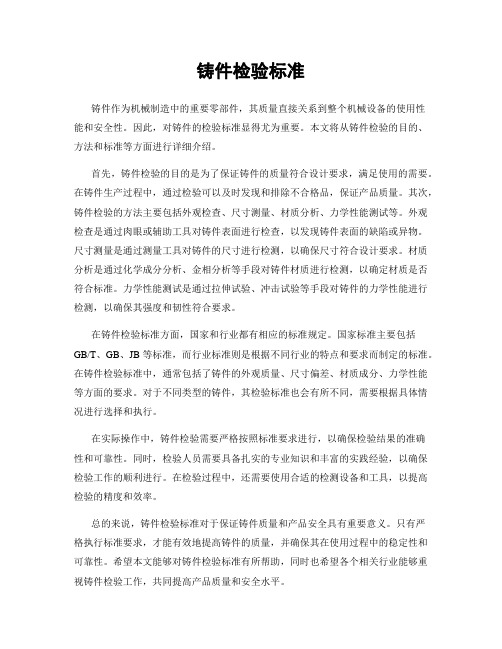
铸件检验标准铸件作为机械制造中的重要零部件,其质量直接关系到整个机械设备的使用性能和安全性。
因此,对铸件的检验标准显得尤为重要。
本文将从铸件检验的目的、方法和标准等方面进行详细介绍。
首先,铸件检验的目的是为了保证铸件的质量符合设计要求,满足使用的需要。
在铸件生产过程中,通过检验可以及时发现和排除不合格品,保证产品质量。
其次,铸件检验的方法主要包括外观检查、尺寸测量、材质分析、力学性能测试等。
外观检查是通过肉眼或辅助工具对铸件表面进行检查,以发现铸件表面的缺陷或异物。
尺寸测量是通过测量工具对铸件的尺寸进行检测,以确保尺寸符合设计要求。
材质分析是通过化学成分分析、金相分析等手段对铸件材质进行检测,以确定材质是否符合标准。
力学性能测试是通过拉伸试验、冲击试验等手段对铸件的力学性能进行检测,以确保其强度和韧性符合要求。
在铸件检验标准方面,国家和行业都有相应的标准规定。
国家标准主要包括GB/T、GB、JB等标准,而行业标准则是根据不同行业的特点和要求而制定的标准。
在铸件检验标准中,通常包括了铸件的外观质量、尺寸偏差、材质成分、力学性能等方面的要求。
对于不同类型的铸件,其检验标准也会有所不同,需要根据具体情况进行选择和执行。
在实际操作中,铸件检验需要严格按照标准要求进行,以确保检验结果的准确性和可靠性。
同时,检验人员需要具备扎实的专业知识和丰富的实践经验,以确保检验工作的顺利进行。
在检验过程中,还需要使用合适的检测设备和工具,以提高检验的精度和效率。
总的来说,铸件检验标准对于保证铸件质量和产品安全具有重要意义。
只有严格执行标准要求,才能有效地提高铸件的质量,并确保其在使用过程中的稳定性和可靠性。
希望本文能够对铸件检验标准有所帮助,同时也希望各个相关行业能够重视铸件检验工作,共同提高产品质量和安全水平。
铸件质量检验标准

铸件质量检验标准铸件质量检验标准铸件质量检验标准铸件质量检验标准铸件质量检验标准⼀、⽬的:为了确保外协⽑坯铸件、采购⽑坯铸件、标准铸件、成品铸件质量符合⼯艺、技术要求,为了满⾜产品特性,结合相关⽂件特制定本标准。
⼆、适⽤范围:本标准适⽤于我公司产品外协、采购、⽣产、装配过程中,全部铸件质量检验标准。
三、检验标准:3.1 铸件结构要符合设计要求或加⼯⼯艺要求。
⽆特殊要求时按铸件通⽤标准执⾏。
通⽤标准等级分为:交货验收技术条件标准;铸件质量分等通则(合格品、⼀等品、优等品)材质、检验⽅法;⼯艺和材料规格等⼀般性规则。
3.2 铸件成品检验。
铸件成品检验包括:铸件的内部质量检验和外观质量检验。
铸件内部质量检验包括:化学成分、机械性能等。
铸件外观质量检验包括:表⾯质量、粗糙度、铸件尺⼨、重量等。
3.2.1 铸件内部质量检验①化学成分:表1牌号标准化学成分C Si Mn Cr P S Ni Cu MoWCAASTMA2160.25 0.60 0.70 0.50 0.04 0.045 0.50 0.30 0.20WCBASTMA2160.30 0.60 1.00 0.50 0.04 0.045 0.50 0.30 0.20WCCASTMA2160.25 0.60 1.20 0.50 0.04 0.045 0.50 0.30 0.20LCBASTMA3520.30 0.6 1.00 0.5 0.04 0.045 0.05 0.3 0.20LC1ASTMA3520.25 0.6 0.5~0.8 — 0.04 0.045 — — 0.45~0.65 LC2ASTMA3520.25 0.6 0.5~0.8 — 0.04 0.045 2~3 — —LC3ASTMA3520.15 0.6 0.5~0.8 — 0.04 0.045 3~4 — —WC6ASTMA217M0.05~0.201.50.04 0.045 0.5 0.5 0.45~0.65WC9ASTMA217M0.05~0.180.600.4~0.72.0~2.750.04 0.045 0.5 0.5 0.90~1.20C5ASTMA217M0.20 0.750.4~0.74.0~6.50.04 0.045 0.5 0.5 0.45~0.65CF3ASTMA3510.03 2.0 1.5 17~21 0.04 0.04 8~12 0.5CF8ASTMA3510.08 2.0 1.5 18~21 0.04 0.04 8~11 0.5CF3MASTMA3510.03 1.5 1.5 17~21 0.04 0.04 9~13 2~3CF8MASTMA3510.08 1.5 1.5 18~21 0.04 0.04 9~12 2~3CG3MASTMA3510.03 1.0 2.0 18~20 0.035 0.03 11~15 3~4CG8MASTMA3510.08 1.0 2.0 18~20 0.035 0.03 11~15 3~4②机械性能表2牌号标准⼒学性能σb(MPa) σs(MPa) δ(%) ψ(%)WCA ASTM A216 415~585 205 24 35WCB ASTM A216 485~655 250 22 35WCC ASTM A216 485~655 275 22 35 LCB ASTM A352 450~620 240 24 35 LC1 ASTM A352 450~620 240 24 35LC2 ASTM A352 485~655 275 24 35LC3 ASTM A352 485~655 275 24 35WC6 ASTM A217M 485~655 275 20 35CF3M ASTM A351 485 205 30CF8M ASTM A351 485 205 30CG3M ASTM A351 480 177 40CG8M ASTM A351 520 205 403.2.2 铸件外观质量检验①表⾯质量检验。
铸件检测报告

铸件检测报告
编号:2021-xxx
客户名称:XXX有限公司
检测日期:2021年5月20日
检测对象:铸造件(零件名称)
检测标准:GB/T 2828.1-2012
检测机构:XXX检测机构
检测人员:XXX
检测结果:
经过全面、细致的检测,铸件检测报告如下:
1.外观检测:铸件无裂缝、毛刺、气孔等缺陷,表面洁净无腐蚀。
2.尺寸检测:铸件尺寸符合客户要求,误差范围在允许范围之内。
3.化学成分检测:铸件化学成分符合客户要求,主要元素含量如下:XXX。
4.金相检测:铸件为均匀、致密结构,未发现内部缺陷、夹杂物等。
综上所述,铸件检测合格,符合客户要求。
备注:
1.检测报告内容仅针对该铸件,其他铸件严禁以此报告作为检测结果。
2.检测报告仅在检测日期及检测机构认证有效,如因使用不当、保存不当导致检测结果受影响,本机构概不负责。
3.如客户需要,可以提供原始记录。
检测机构联系方式:
联系人:XXX
联系电话:XXX
联系地址:XXX。
铸件质量检验标准

—
—
—
—
—
—
—
—
0.64
0.72
0.80
0.9
1.0
1.1
1.2
1.4
1.6
1.8
2.0
2.2
2.6
2.8
3.2
3.6
4.0
4.6
5
6
7
7
8
9
10
11
13
1600
2500
4000
6300
2500
4000
6300
10000
—
—
—
—
—
—
—
—
—
—
—
—
—
—
—
0.24
0.26
0.28
0.32
0.36
0.40
0.46
0.50
0.56
0.64
0.70
0.78
0.9
1.0
1.1
1.3
1.4
1.6
1.8
2.0
2.2
2.6
2.8
CF3M
ASTM
A351
0.03 1.5 1.5 17~21 0.04 0.04 9~13 2~3
CF8M
ASTM
A351
0.08 1.5 1.5 18~21 0.04 0.04 9~12 2~3
CG3M
ASTM
A351
0.03 1.0 2.0 18~20 0.035 0.03 11~15 3~4
检验铝铸件质量9大标准及处理方案-

检验铝铸件质量9大标准及处理方案-
1. 外观质量:检查铝铸件表面是否有气孔、夹渣、表面粗糙等缺陷,应采取去毛刺、打磨等方式处理。
2. 尺寸精度:检查铝铸件的尺寸是否符合要求,如存在尺寸偏差,可以通过机械加工或重新调整模具来处理。
3. 材质成分:通过化学成分分析检查铝铸件的材质成分是否符合标准要求,如有偏差,可以重新选择合适的材料。
4. 机械性能:通过拉伸、硬度等机械性能测试检查铝铸件的强度、硬度等机械性能是否达到要求,如不符合,可以进行热处理或调整合金配方。
5. 内部缺陷:采用X射线或超声波探伤等方法检查铝铸件的内部是否存在气孔、裂纹等缺陷,可采取疏松处理、补焊等方式。
6. 表面处理:对铝铸件进行表面处理,如喷漆、阳极氧化、电镀等,以提高铝铸件的耐腐蚀性和美观度。
7. 焊接质量:如果铝铸件需要进行焊接,需要检查焊接工艺和焊接质量,如焊接缺陷,可进行补焊或重新焊接。
8. 寿命、耐久性:通过模拟使用条件或实际使用过程中的试验,检查铝铸件的寿命和耐久性,如不符合要求,可采取增加材料厚度、改进结构等方式进行改进。
9. 环境适应性:根据铝铸件的应用环境,检查其对温度、湿度、腐蚀等环境因素的适应性,如不适应,可进行材质改进或表面处理等方式来提高适应性。
铸件质量控制及检验

铸件质量检验铸件质量检验是铸造生产的重要工序,其主要职能是:为铸件生产和管理部门提供质量信息;质量管理活动提出课题;保证产品质量。
铸件的检验主要包括铸件表面质量检验、铸件内在质量检验以及铸件质量的综合鉴定。
第一节外观质量的检验其中,铸件的表面质量包括铸件的表面缺陷、尺寸精度、质量偏差、表面粗糙度等。
铸件外观质量优劣影响后续加工工艺、后续加工的消耗,也影响铸件的使用性能。
所有铸件都要按照规定的标准进行外观质量检验。
这些检验又常常需要分多次完成。
例如,铸件铸出后的初检只能发现明显的表面缺陷,细小的表面缺陷则要用专门的设备才能发现。
外部尺寸不难直接测量,内腔的某些形状与尺寸,则要切剖铸件才能测出。
为此,对不同的铸件安排有不同的检验制度,载列于有关工艺文件巾。
本书将从铸件表面缺陷、表面粗糙度、质量偏差,尺寸偏差四个方面分别论述有关内容。
检验的依据是铸件的有关标准、技术条件和图样。
铸件的表面质量主要包括铸件的表面缺陷、尺寸精度、质量偏差、形状偏差、表面粗糙度和铸件表面清理质量等多方面内容。
一、铸件表面缺陷的检验铸件上的表面缺陷,应按具体技术要求分为3类。
(1)照技术条件允许存在的缺陷带有这类缺陷的铸件应视为合格。
(2)允许修复的缺陷包括可以铲除的多肉,可以焊补的疵孔,可以校正的变形和可以浸渗处理的渗漏等。
有这类缺陷的铸件,应按要求做好修复工作,然后再次检验。
(3)允许存在但不允许修复的缺陷有这类缺陷的铸件应子以报废。
(一)检验要求为保证铸件的表面质量,应规定每批(炉)铸件l00%的检验其表面缺陷。
检验要求一般规定如下。
①铸件非加工表面上的浇冒口应清理得与铸件表面同样平整,加工面上的浇冒口残留量应符合图纸规定,有色金属铸件一般允许高出铸件表面2~5mm,黑色金属铸件一般允许高山铸件表面5—15mm。
②在铸什上不允许有裂纹、通孔、穿透性的冷隔和穿透性的缩松、夹渣缺陷。
③铸件非加工表面的毛刺、披缝应清理至与铸件面同样子整。
铸件的表面和内部质量检测方法

铸件的表面和内部质量检测方法(图)铸件的检测主要包括尺寸检查、外观和表面的目视检查、化学成分分析和力学性能试验,对于要求比较重要或铸造工艺上容易产生问题的铸件,还需要进行无损检测工作,可用于球墨铸铁件质量检测的无损检测技术包括液体渗透检测、磁粉检测、涡流检测、射线检测、超声检测及振动检测等。
1 铸件表面及近表面缺陷的检测1.1液体渗透检测液体渗透检测用来检查铸件表面上的各种开口缺陷,如表面裂纹、表面针孔等肉眼难以发现的缺陷。
常用的渗透检测是着色检测,它是将具有高渗透能力的有色(一般为红色)液体(渗透剂)浸湿或喷洒在铸件表面上,渗透剂渗入到开口缺陷里面,快速擦去表面渗透液层,再将易干的显示剂(也叫显像剂)喷洒到铸件表面上,待将残留在开口缺陷中的渗透剂吸出来后,显示剂就被染色,从而可以反映出缺陷的形状、大小和分布情况。
需要指出的是,渗透检测的精确度随被检材料表面粗糙度增加而降低,即表面越光检测效果越好,磨床磨光的表面检测精确度最高,甚至可以检测出晶间裂纹。
除着色检测外,荧光渗透检测也是常用的液体渗透检测方法,它需要配置紫外光灯进行照射观察,检测灵敏度比着色检测高。
1.2涡流检测涡流检测适用于检查表面以下一般不大于6~7mm深的缺陷。
涡流检测分放置式线圈法和穿过式线圈法2种。
:当试件被放在通有交变电流的线圈附近时,进入试件的交变磁场可在试件中感生出方向与激励磁场相垂直的、呈涡流状流动的电流(涡流),涡流会产生一与激励磁场方向相反的磁场,使线圈中的原磁场有部分减少,从而引起线圈阻抗的变化。
如果铸件表面存在缺陷,则涡流的电特征会发生畸变,从而检测出缺陷的存在, 涡流检测的主要缺点是不能直观显示探测出的缺陷大小和形状,一般只能确定出缺陷所在表面位置和深度,另外它对工件表面上小的开口缺陷的检出灵敏度不如渗透检测。
1.3磁粉检测磁粉检测适合于检测表面缺陷及表面以下数毫米深的缺陷,它需要直流(或交流)磁化设备和磁粉(或磁悬浮液)才能进行检测操作。
铸造厂铸件质量检验管理制度

铸造厂铸件质量检验管理制度一、前言铸造厂作为生产铸件的核心部门,其质量检验管理制度是确保产品质量的关键。
本文将详细介绍铸造厂铸件质量检验管理制度及其实施细则。
二、质量检验组织架构为逐步提升铸件质量,铸造厂应设立专门的质量检验部门,建立健全的组织架构。
该部门应由质检主管领导,下设若干个质检小组。
每个质检小组应包括质检组长、技术员、质检员等人员。
质量检验部门与生产车间、技术部门等紧密合作,形成高效的质量管理体系。
三、质量检验流程1. 接受检验:在铸件送检之前,质量检验部门接收铸件并进行标识、登记和分类。
同时,对铸件的外观、尺寸、重量等进行初步检验,确保铸件符合基本要求。
如发现异常情况,应及时通知生产车间进行处理。
2. 检验方案制定:根据铸件的类型、规格和客户需求,制定相应的检验方案。
该方案应包含检验项目、方法、标准、设备及人员的要求等内容。
3. 检验执行:根据检验方案,质检小组对铸件进行全面检验。
其中包括外观检验、尺寸检验、材质检验等内容。
检验结果应详细记录,并及时汇总反馈给相关部门。
4. 不合格处理:对于不合格的铸件,应按照相应的处理流程进行处理。
即责令责任人进行整改,直至达到要求为止。
同时,应追踪不合格铸件的原因,并采取相应的纠正措施,防止类似问题再次出现。
5. 合格认证:对于符合要求的铸件,应进行合格认证。
认证结果应记录并保存,以备后续参考。
四、质量检验设备和工具铸造厂在实施质量检验过程中,应配备相应的检验设备和工具,以保证检验工作的准确性和可靠性。
如影像测量仪、硬度计、磁粉探伤设备、X射线探伤设备等。
同时,还需保养和维修检验设备,确保其正常运行。
五、培训与管理为了保证质量检验工作的高效和精确,铸造厂应开展相关人员的培训和管理。
培训内容包括质检操作规程、检验方法、仪器设备操作等。
通过培训和考核,提升质检人员的技术水平和专业素养。
同时,对质量检验工作进行全面管理,包括任务分配、工作计划、结果评价等。
铸造质量与检验

铸造质量与检验铸造是一种重要的制造工艺,广泛应用于汽车、机械、航空航天等行业。
铸造质量的好坏直接影响到制品的性能和使用寿命。
为了确保铸件的质量,铸造过程中需要进行严格的检验。
本文将探讨铸造质量与检验的相关内容。
一、铸造质量的影响因素铸造质量受到多个因素的影响,包括:1.原材料的质量:铸造过程中使用的原材料包括金属、砂型、熔剂等,它们的质量直接决定了铸造品的质量。
2.铸造工艺的控制:铸造工艺包括砂型制备、熔炼、浇注、冷却等环节,每个环节都需要控制参数,以确保铸件的完整性和性能。
3.铸型设计:铸型的设计需要考虑到铸件的形状、尺寸、壁厚等因素,合理的铸型设计能够降低铸件的缺陷率。
4.设备状态和操作技术:铸造设备的状态和操作技术直接影响到铸件的质量,如炉温控制、浇注速度控制等。
二、铸造质量的检验方法为了确保铸件的质量,需要采用适当的检验方法,主要包括以下几种:1.视觉检验:视觉检验是最常用的一种检验方法,通过目视观察铸件的外观,检查是否有裂纹、气孔、夹杂物等表面缺陷。
2.尺寸检验:尺寸检验主要是对铸件的几何尺寸进行测量,以检查是否符合设计要求。
3.金相检验:金相检验是通过显微镜观察铸件的金相组织结构,以了解铸件的显微组织情况和组织均匀性。
4.硬度检验:硬度检验是通过硬度计对铸件的硬度进行测量,以表示铸件的抗拉强度和耐磨性。
5.化学成分分析:化学成分分析是通过对铸件材料进行化学成分测定,以验证其材料的成分是否符合标准要求。
6.无损检测:无损检测是利用超声波、射线等非破坏性的方法对铸件进行检测,以发现内部缺陷、裂纹等问题。
三、铸造质量控制与提升为了确保铸造质量,需要进行严格的质量控制与提升措施。
1.制定质量控制计划:在铸造过程中,制定详细的质量控制计划,明确每个环节的控制要点和控制方法。
2.培训操作人员:确保操作人员具备良好的专业知识和技能,能够正确地操作铸造设备和工艺,并严格遵守操作规程。
3.强化设备维护:定期检查和维护铸造设备,确保其正常运行,减少设备故障对铸件质量的影响。
铸件缺陷特征和检验标准

铸件缺陷特征和检验标准
铸件缺陷这事儿,其实就是铸造过程中不小心留下的“小毛病”,这些毛病会影响铸件的质量和使用。
咱们来聊聊常见的几种问题和怎么检查它们:
多出来的部分:就像做蛋糕时不小心多抹了一层奶油,铸件有时也会有些地方厚了或者不该有的凸起。
检查时,我们就得仔细瞧瞧,量量尺寸,看看有没有哪里鼓起来了,超出标准。
表面不平整:想象一下,如果你的新手机壳上有划痕、小坑或者脏东西嵌在里面,肯定不乐意。
铸件也一样,裂纹、小坑、杂质这些,得通过专业的“照妖镜”——磁粉检查或渗透检测来找,确保表面干净、光滑。
藏起来的小洞:气孔和针孔就像是面包里的小气泡,不过在铸件里可就不受欢迎了。
要用X光或者超声波这样的高科技手段,像给铸件做CT扫描一样,找出这些隐藏的问题。
缩水和疏松:就像冬天衣服没穿够会缩成一团,铸件也可能因为金属冷却时收缩,留下大洞或者密密麻麻的小孔。
得用水压测试或者高级的无损检测,确保这些洞洞不会让铸件“体质”变差。
脏东西留下的痕迹:渣眼就像是衣服上的污渍,得仔细找找。
通过破坏性检测或者非常精细的检查,把这些不干净的痕迹揪出来。
没填满的地方:冷隔和浇不足就像是倒茶时杯子没倒满,铸件里面或者表面也有没填满的情况。
还是得靠X光或超声波这些“透视眼”来发现。
性能不达标:铸件不仅要长得好看,还得结实能用。
通过拉拉扯扯的力学实验和化学分析,确保它既硬朗又成分合适,符合规定的“身体素质”。
每个国家或行业都有自己的标准,就像是老师给的考试大纲,告诉厂家铸件得达到什么水平。
厂家自己也会有一套更细致的检查办法,确保生产出来的铸件都是“优等生”。
铸件质量检验

铸件质量检验铸件质量检验模板一、引言好的铸件质量对于产品的性能和可靠性至关重要。
为了确保铸件质量符合设计和制造要求,需要进行全面的质量检验。
本旨在提供一个全面且详细的铸件质量检验模板,以供参考和使用。
二、质量检验目的铸件质量检验的主要目的是确保铸件的尺寸精度、材料质量和表面质量符合相关标准和要求。
通过进行严格的检验,可以提高铸件质量,降低不合格品率,确保产品的质量可靠性和性能稳定性。
三、质量检验流程1. 材料检验1.1. 检查原材料的标识和质量证书,确认材料符合规定要求。
1.2. 对材料进行化学成分分析,确保材料成分符合设计要求。
1.3. 进行金相组织分析,了解材料的显微组织情况。
2. 尺寸检验2.1. 使用适当的量具和测量仪器测量铸件的尺寸精度。
2.2. 检查铸件的几何形状是否符合设计要求。
2.3. 检查铸件的平面度、垂直度和圆度等参数。
3. 表面质量检验3.1. 检查铸件的表面是否平整、光洁,无明显缺陷和表面损坏。
3.2. 使用显微镜等设备对铸件表面进行放大观察,寻找微小缺陷和不良现象。
3.3. 使用硬度计测量铸件的硬度,确保硬度值符合要求。
4. 缺陷检验4.1. 通过目视和非破坏性检测方法检查铸件是否存在气孔、砂眼、夹杂物等缺陷。
4.2. 使用超声波、X射线等仪器进行进一步的缺陷检测,并对检测结果进行记录和评估。
4.3. 对检测到的缺陷进行分类和处理,决定是否接受或修复铸件。
5. 力学性能测试5.1. 进行拉伸试验、冲击试验等测试,评估铸件的力学性能。
5.2. 根据测试结果,对铸件的各项力学性能指标进行评定和判别。
四、质量检验记录1. 所有的质量检验活动都应记录在相应的检验记录表中,包括检验日期、检验人员、检验结果等信息。
2. 每项检验都应有相应的检验批次编号和铸件标识编号。
3. 质量检验记录应进行归档,以备查阅和追溯。
五、质量检验的结果处理1. 检验通过的铸件可直接进入下一道工序。
2. 发现不合格品的铸件应按照质量控制流程进行处理,包括退货、修复等。
铸件的表面和内部质量检测方法

铸件的表面和内部质量检测方法(图)铸件的检测主要包括尺寸检查、外观和表面的目视检查、化学成分分析和力学性能试验,对于要求比较重要或铸造工艺上容易产生问题的铸件,还需要进行无损检测工作,可用于球墨铸铁件质量检测的无损检测技术包括液体渗透检测、磁粉检测、涡流检测、射线检测、超声检测及振动检测等。
1 铸件表面及近表面缺陷的检测1.1液体渗透检测液体渗透检测用来检查铸件表面上的各种开口缺陷,如表面裂纹、表面针孔等肉眼难以发现的缺陷。
常用的渗透检测是着色检测,它是将具有高渗透能力的有色(一般为红色)液体(渗透剂)浸湿或喷洒在铸件表面上,渗透剂渗入到开口缺陷里面,快速擦去表面渗透液层,再将易干的显示剂(也叫显像剂)喷洒到铸件表面上,待将残留在开口缺陷中的渗透剂吸出来后,显示剂就被染色,从而可以反映出缺陷的形状、大小和分布情况。
需要指出的是,渗透检测的精确度随被检材料表面粗糙度增加而降低,即表面越光检测效果越好,磨床磨光的表面检测精确度最高,甚至可以检测出晶间裂纹。
除着色检测外,荧光渗透检测也是常用的液体渗透检测方法,它需要配置紫外光灯进行照射观察,检测灵敏度比着色检测高。
1.2涡流检测涡流检测适用于检查表面以下一般不大于6~7mm深的缺陷。
涡流检测分放置式线圈法和穿过式线圈法2种。
:当试件被放在通有交变电流的线圈附近时,进入试件的交变磁场可在试件中感生出方向与激励磁场相垂直的、呈涡流状流动的电流(涡流),涡流会产生一与激励磁场方向相反的磁场,使线圈中的原磁场有部分减少,从而引起线圈阻抗的变化。
如果铸件表面存在缺陷,则涡流的电特征会发生畸变,从而检测出缺陷的存在, 涡流检测的主要缺点是不能直观显示探测出的缺陷大小和形状,一般只能确定出缺陷所在表面位置和深度,另外它对工件表面上小的开口缺陷的检出灵敏度不如渗透检测。
1.3磁粉检测磁粉检测适合于检测表面缺陷及表面以下数毫米深的缺陷,它需要直流(或交流)磁化设备和磁粉(或磁悬浮液)才能进行检测操作。
铸造质量技术检验

一、铸件的检验 铸造生产中检验的对象: 生产过程中最初的、中间的和最后的产品的结果 铸造生产过程的各工序 技术检验的主要任务: 及时发现检验对象缺陷,防止生产出不合格铸件 技术检验类型 (1)原料检验——即对各工段所用原材料进行检验
(2)工序检验——每个工序完成后进行的检验 (3)验收检验——即对成品铸件的检验
3.金属液和铸型 影响金属液渗入的因素主要有液态金属的表面张力、
液态金属的压力和铸型工作表面砂粒的间隙
砂型铸 造
普通砂型 高压造型
压力铸造(有色金属)
表面粗糙度值Ra/μm范围 50~400 12.5~50 0.4~50
铸造方法 熔模铸造(铸钢) 低压铸造 金属型铸造
2.铸型表面粗糙度
表面粗糙度值Ra/μm范围 0.8~12.5 0.8~100 0.8~100
对砂型来而言,砂粒越粗,铸件表面粗糙度值越高
三、铸造表面粗糙度
铸造表面粗糙度是铸件表面上具有的较小间距和 峰谷所组成的微观几何ቤተ መጻሕፍቲ ባይዱ状特征
影响铸造表面粗糙度的因素:铸造方法的选择、铸 型表面粗糙度、金属液的化学成分和浇注温度以及金 属液与铸型表面的相互作用、清理铸件表面的方法
1.铸造方法的选择
表6-2 各种铸造方法所能达到的表面粗糙度值的范围
铸造方法
二、铸件尺寸精度控制
(一)影响铸件尺寸精度的因素 铸件最终形状及尺寸取决于: 一是铸型型腔的几何形状与尺寸 二是铸件在凝固冷却过程中膨胀和收缩的大小 影响铸件尺寸精度因素: 模样尺寸公差及模样在模板上的定位公差 芯盒尺寸公差及型芯在制造中的变形公差 型芯在下芯时的定位公差和铸件收缩公差
(二)提高铸件尺寸精度的措施 1.正确设计模样和芯盒的工作尺寸 2.严格控制工艺装备的制造和装配公差 3.控制型芯尺寸和下芯位置准确度 4.严格控制型壁的位移
铸件检验标准

铸件检验标准1.铸件质量检测仪:用于检测合金性能、组织、表面状态等铸件质量的仪器。
2.铸件公称重量检验:根据铸件图计算或根据供需双方认定合格的标准样品铸件的称重结果订出的铸件重量。
包括铸件机械加工余量及其他工艺余量。
3.铸件重量公差检验:用占铸件公称重量的百分比表示的铸件实际重量与公称重量之差的最大允许值。
与铸件尺寸公差对应的分为16个等级,以MT1-MT16表示。
4.铸件重量偏:铸件重量与公称重量之间的正偏差或负偏差。
5.铸件尺寸公差:铸件各部分尺寸允许的极限偏差。
6.铸件尺寸稳定性:铸件在使用和存放过程中保持原来尺寸不变的性能。
7.铸件机械加工余量:为保证铸件加工面尺寸和零件精度,在铸件工艺设计时预先增加而在机械加工时切去的金属层厚度。
8.铸造表面粗糙度:铸造表面上由微小间距和峰谷组成的微观几何特征。
铸造工段铸件质量检验标准根据目前的生产情况,在初期对我单位的铸件检验制定了以下检验标准,随着以后生产和技术的进一步完善对此标准将逐步细化:1. *铸件外表面应平整,1000mm范围内的平整度(或变形量)不大于3mm(特殊要求例外),表面不允许存在高度长度大于3mm和直径大于3mm的铁瘤、脉纹;*不允许存在深度和直径大于3mm的孔洞类缺陷(砂眼、气孔、渣孔、缩孔、缩松等),如果此类缺陷存在面积大于150x150mm而失去修复价值视为废品,可以修复的必须经过焊补并打磨光洁后重新检验;*外型尺寸如有图纸要求公差的应严格按照图纸执行,未注公差的自由尺寸的偏差不能大于该尺寸的光洁度最低一级国家铸件标准规定;*铸件表面不能存在各种严重的裂纹缺陷,如果非加工表面存在长度不大于20mm的轻微裂纹,在请示技术部门后允许采用热焊补的办法进行修复;*铸件表面的粘砂必须清理干净,各种飞刺存在的面积不允许超过200x200mm,否则必须返工;2. *铸件水口冒口经过切割后不得留有高度大于2mm的根部,水口冒口根部的缩松、缩孔必须经过焊补,否则视为废品;*对比较重要的加工面,如果从外表发现各种皮下缺陷应及时反映到工段并对此铸件跟踪,一旦发现加工后存在大量气孔、渣孔、缩松等缺陷应立即将同类产品封存不得出厂并督促工段技术人员改进工艺;3. *每一批次铸件的材质要求单据在质监部门都应有存底,当炉次化验结果和要求对比后可以评判化学成分是否合乎要求;4. *对于用户在加工后发现的各种内在质量缺陷应及时核对并确定生产日期,作为考核数据重新对检验报告进行更改并及时建议工段技术人员改进工艺;5. *检验后发现问题比较严重的铸件只有在厂家提出强行发货要求,经过总经理及其授权人的书面同意后可以作为紧急放行件出厂。
铸件质量检验标准
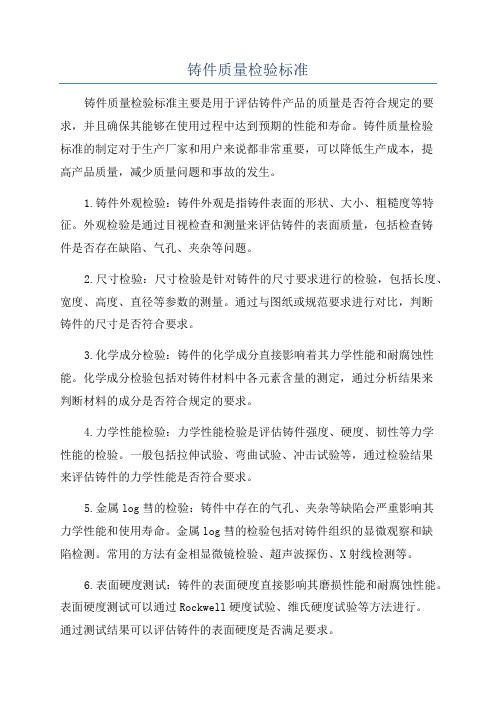
铸件质量检验标准铸件质量检验标准主要是用于评估铸件产品的质量是否符合规定的要求,并且确保其能够在使用过程中达到预期的性能和寿命。
铸件质量检验标准的制定对于生产厂家和用户来说都非常重要,可以降低生产成本,提高产品质量,减少质量问题和事故的发生。
1.铸件外观检验:铸件外观是指铸件表面的形状、大小、粗糙度等特征。
外观检验是通过目视检查和测量来评估铸件的表面质量,包括检查铸件是否存在缺陷、气孔、夹杂等问题。
2.尺寸检验:尺寸检验是针对铸件的尺寸要求进行的检验,包括长度、宽度、高度、直径等参数的测量。
通过与图纸或规范要求进行对比,判断铸件的尺寸是否符合要求。
3.化学成分检验:铸件的化学成分直接影响着其力学性能和耐腐蚀性能。
化学成分检验包括对铸件材料中各元素含量的测定,通过分析结果来判断材料的成分是否符合规定的要求。
4.力学性能检验:力学性能检验是评估铸件强度、硬度、韧性等力学性能的检验。
一般包括拉伸试验、弯曲试验、冲击试验等,通过检验结果来评估铸件的力学性能是否符合要求。
5.金属log彗的检验:铸件中存在的气孔、夹杂等缺陷会严重影响其力学性能和使用寿命。
金属log彗的检验包括对铸件组织的显微观察和缺陷检测。
常用的方法有金相显微镜检验、超声波探伤、X射线检测等。
6.表面硬度测试:铸件的表面硬度直接影响其磨损性能和耐腐蚀性能。
表面硬度测试可以通过Rockwell硬度试验、维氏硬度试验等方法进行。
通过测试结果可以评估铸件的表面硬度是否满足要求。
7.耐蚀性测试:铸件在使用过程中可能会接触到各种介质,耐蚀性是评价铸件耐久性能的重要指标。
耐蚀性测试可以通过浸泡试验、盐雾试验等方法进行,通过测试结果来评估铸件的耐腐蚀性能是否符合要求。
8.热处理性能检验:铸件由于制造过程中会经历冷却和加热等工艺过程,热处理性能对于铸件的组织结构和力学性能有很大影响。
热处理性能检验包括热处理工艺参数的测定和热处理后的铸件组织结构的观察与检测。
- 1、下载文档前请自行甄别文档内容的完整性,平台不提供额外的编辑、内容补充、找答案等附加服务。
- 2、"仅部分预览"的文档,不可在线预览部分如存在完整性等问题,可反馈申请退款(可完整预览的文档不适用该条件!)。
- 3、如文档侵犯您的权益,请联系客服反馈,我们会尽快为您处理(人工客服工作时间:9:00-18:30)。
• 1.2 涡流检测 • • 涡流检测适用于检查表面以下一般不大于6~7MM 深的缺陷。涡流检测分放置式线圈法和穿过式线圈法2 种。当试件被放在通有交变电流的线圈附近时,进入试 件的交变磁场可在试件中感生出方向与激励磁场相垂直 的、呈涡流状流动的电流(涡流),涡流会产生一与激励 磁场方向相反的磁场,使线圈中的原磁场有部分减少, 从而引起线圈阻抗的变化。如果铸件表面存在缺陷,则 涡流的电特征会发生畸变,从而检测出缺陷的存在,涡 流检测的主要缺点是不能直观显示探测出的缺陷大小和 形状,一般只能确定出缺陷所在表面位置和深度,另外 它对工件表面上小的开口缺陷的检出灵敏度不如渗透检 测。
1 铸件表面及近表面缺陷的检测
• 1.3 磁粉检测 • • 磁粉检测适合于检测表面缺陷及表面以下数毫米深 的缺陷,它需要直流(或交流)磁化设备和磁粉(或磁悬浮 液)才能进行检测操作。磁化设备用来在铸件内外表面 产生磁场,磁粉或磁悬浮液用来显示缺陷。当在铸件一 定范围内产生磁场时,磁化区域内的缺陷就会产生漏磁 场,当撒上磁粉或悬浮液时,磁粉被吸住,这样就可以 显示出缺陷来。这样显示出的缺陷基本上都是横切磁力 线的缺陷,对于平行于磁力线的长条型缺陷则显示不出 来,为此,操作时需要不断改变磁化方向,以保证能够 检查出未知方向的各个缺陷。
1 铸件表面及近表面缺陷的检测
• • • •
1.1 液体渗透检测
液体渗透检测用来检查铸件表面上的各种开口缺陷,如表 面裂纹、表面针孔等肉眼难以发现的缺陷。常用的渗透检测是 着色检测,它是将具有高渗透能力的有色(一般为红色)液体(渗 透剂)浸湿或喷洒在铸件表面上,渗透剂渗入到开口缺陷里面, 快速擦去表面渗透液层,再将易干的显示剂(也叫显像剂)喷洒 到铸件表面上,待将残留在开口缺陷中的渗透剂吸出来后,显 示剂就被染色,从而可以反映出缺陷的形状、大小和分布情况。 需要指出的是,渗透检测的精确度随被检材料表面粗糙度增加 而降低,即表面越光检测效果越好,磨床磨光的表面检测精确 度最高,甚至可以检测出晶间裂纹。除着色检测外,荧光渗透 检测也是常用的液体渗透检测方法,它需要配置紫外光灯进行 照射观察,检测灵敏度比着色检测高。
• 2.1 射线检测(微焦点XRAY) • • 射线检测,一般用X射线或γ射线作为射线源,因此需要产生射线 的设备和其他附属设施,当工件置于射线场照射时,射线的辐射强度 就会受到铸件内部缺陷的影响。穿过铸件射出的辐射强度随着缺陷大 小、性质的不同而有局部的变化,形成缺陷的射线图像,通过射线胶 片予以显像记录,或者通过荧光屏予以实时检测观察,或者通过辐射 计数仪检测。其中通过射线胶片显像记录的方法是最常用的方法,也 就是通常所说的射线照相检测,射线照相所反映出来的缺陷图像是直 观的,缺陷形状、大小、数量、平面位置和分布范围都能呈现出来, 只是缺陷深度一般不能反映出来,需要采取特殊措施和计算才能确定。 国际铸业网出现应用射线计算机层析照相方法,由于设备比较昂贵, 使用成本高,无法普及,但这种新技术代表了高清晰度射线检测技术 未来发展的方向。此外,使用近似点源的微焦点X射线系统实际上也 可消除较大焦点设备产生的模糊边缘,使图像轮廓清晰。使用数字图 像系统可提高图像的信噪比,进一步提高图像清晰度。
2 铸件内部缺陷的检测
•
• 对于内部缺陷,常用的无损检测方法 是射线检测和超声检测。其中射线检测效 果最好,它能够得到反映内部缺陷种类、 形状、大小和分布情况的直观图像,但对 于大厚度的大型铸件,超声检测是很有效 的,可以比较精确地测出内部缺陷的位置、 当量大小和分布情况。
2 铸件内部缺陷的检测
铸件质量检测方法
• 铸件的检测主要包括尺寸检查、外观和表 面的目视检查、化学成分分析和力学性能 试验,对于要求比较重要或铸造工艺上容 易产生问题的铸件,还需要进行无损检测 工作,可用于球墨铸铁件质量检测的无损 检测技术包括液体渗透检测、磁粉检测、 涡流检测、射线检测、超声检测及振动检 测等。
2 铸件内部缺陷的检测
• 2.2 超声检测 • • 超声检测也可用于检查内部缺陷,它是利用具有高频声能 的声束在铸件内部的传播中,碰到内部表面或缺陷时产生反射 而发现缺陷。反射声能的大小是内表面或缺陷的指向性和性质 以及这种反射体的声阻抗的函数,因此可以应用各种缺陷或内 表面反射的声能来检测缺陷的存在位置、壁厚或者表面下缺陷 的深度。超声检测作为一种应用比较广泛的无损检测手段,其 主要优势表现在:检测灵敏度高,可以探测细小的裂纹;具有大 的穿透能力,可以探测厚截面铸件。其主要局限性在于:对于 轮廓尺寸复杂和指向性不好的断开性缺陷的反射波形解释困难; 对于不合意的内部结构,例如晶粒大小、组织结构、多孔性、 夹杂含量或细小的分散析出物等,同样妨碍波形解释;另外,检 测时需要参考标准试块。