精密注射模设计——崔杰
注射模设计任务书
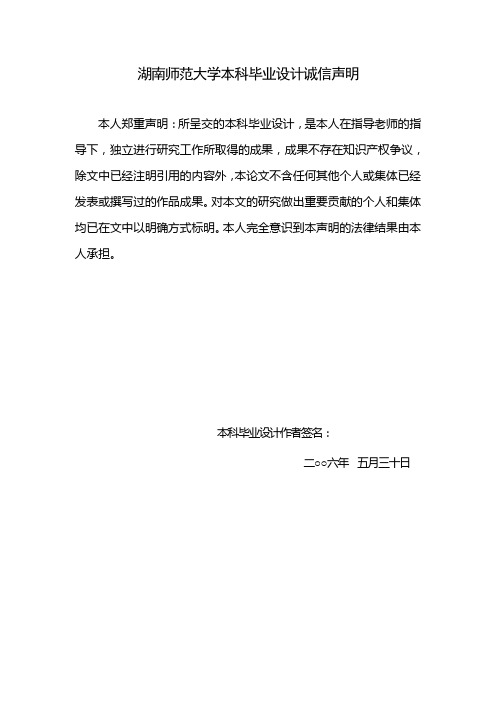
湖南师范大学本科毕业设计诚信声明
本人郑重声明:所呈交的本科毕业设计,是本人在指导老师的指导下,独立进行研究工作所取得的成果,成果不存在知识产权争议,除文中已经注明引用的内容外,本论文不含任何其他个人或集体已经发表或撰写过的作品成果。
对本文的研究做出重要贡献的个人和集体均已在文中以明确方式标明。
本人完全意识到本声明的法律结果由本人承担。
本科毕业设计作者签名:
二○○六年五月三十日
湖南师范大学本科毕业设计任务书
湖南师范大学
学院指导教师指导毕业设计情况登记表
湖南师范大学本科毕业设计评审表
优秀,80—89分记为良好,70—79分记为中等,60—69分记为及格,60分以下记为不及格。
优秀,80—89分记为良好,70—79分记为中等,60—69分记为及格,60分以下记为不及格。
湖南师范大学本科毕业设计答辩记录表。
【开题报告】10ml一次性注射器外套注射模具及成型工艺设计成型

开题报告10ml一次性注射器外套注射模具及成型工艺设计成型一、选题的背景和意义注塑模具是当今生产各种工业产品的重要设备,随着塑料行业的迅速发展,以及塑料制品在各领域的推广应用,塑料制品对模具的设计要求也越来越高,传统的模具设计方法已不能符合当今社会的要求. 与传统模具设计相比,计算机辅助工程(CAE)的技术无论在提高生产、保证产品质量,还是在降低成本和劳动强度方面,都有极大的优越性。
一次性注射器是注塑模具的主要一个体现,也是医疗机构中应用最为广泛的器械,是医护人员每天基本上必定会接触到的器材,我们很有必要对其历史知识作一些了解。
以前,医护人员会采用对体内直接用药的手段使药物快速被肌体吸收,但是由于条件的限制,必须先使用刀先在病人的身体表面划开口子,然后将装药的装置置于其内才能完成。
伴随着社会的发展,人类的文明程度提高,注射器的发展相应的也从15世纪开始进入了较为快速的发展时期,并经历了四个阶段。
第一阶段:15世纪到20世纪40年代,现代意义上的注射器的发明以及发展,出现了玻璃制的注射器;第二阶段:20世纪50年代到80年代,发明并且大量得制造一次性注射器;第三阶段:20世纪末至今,安全注射器的设计;第四阶段:注射器未来的发展趋势将会是发明发展大量的微型注射器技术,降低注射时的疼痛,提升药物治疗效果。
1955年,塑料首次被应用在注射器的设计中,全世界首个一次性塑料注射器问世,它不但降低了注射器的生产成本,而且使用起来更安全方便。
从此以后,塑料注射器不断地受人关注,不断出现新的、更安全的、性能更好的、更廉价的产品。
目前,无论是小型诊所或者大型医院,除了给患者开方立药予以内服外敷外,药液的静脉注射或肌肉注射无非是最快捷有效的,但是,药液要顺利的注入人体的表皮以内,需要依赖带有针头的注射器。
普通的一次性注射器由针筒、推杆、针头组成,针头插入人体的肌肉或皮下组织时,需要按住推杆往前推移,将针筒中的药液由针头注入人体。
MIM金属注射成型工艺

MIM金属注射成型工艺金属注射成型(Metal Injection Molding),简称MIM。
是一种将金属、陶瓷或复合材料通过粉末冶金工艺和塑料注射成型工艺相结合加工成型的先进制造工艺。
相对于传统的金属加工方式,MIM工艺具有高精度、高效率、低成本和复杂几何形状加工等优点。
MIM工艺的工作原理是先将金属粉末与绑定剂混合,形成可注射的糊状物。
然后,将糊状物充填进注射模具中,在高温高压的条件下,将糊状物注射成模具所需的形状。
经过烧结、退bind剂和后处理等步骤,最终得到高密度、高强度的金属零件。
MIM工艺的特点如下:1.高精度:MIM工艺可以制造出精度高的复杂零件,其精度可达到0.1mm。
与传统的金属加工方式相比,MIM工艺无需进行额外的加工,能够大大提高生产效率。
2.高效率:MIM工艺能够一次性完成复杂零件的成型,无需多次加工。
同时,每次注射可以注射多个零件,大大提高了生产效率。
3.低成本:相对于传统的金属加工方式,MIM工艺不需要额外加工,可以减少人工和设备投入。
另外,由于MIM工艺采用粉末冶金工艺,材料的浪费也相对较少。
4.适用范围广:MIM工艺适用于多种材料,包括不锈钢、钛合金、铁基合金、镍基合金等。
同时,MIM工艺还能够制造涂层、多孔和镶嵌等复合材料,并且能够制造具有种类繁多的零件。
MIM工艺在多个领域得到应用,包括汽车、医疗设备、航空航天、电子等。
例如,汽车领域,MIM工艺可以制造发动机零件、传动装置零件等。
医疗设备领域,MIM工艺可以制造外科器械、植入器械等。
航空航天领域,MIM工艺可以制造航天器零件、航空发动机零件等。
电子领域,MIM工艺可以制造电子连接器、电子器件外壳等。
然而,MIM工艺也存在一些挑战和限制。
其中之一是材料选择的限制,因为不同材料的烧结温度和性能要求不同,这对生产过程的稳定性和成本有一定的影响。
另外,由于注射模具的制造和维护成本高,对于小批量生产和复杂形状的零件来说,MIM工艺的成本可能较高。
IMOLD在注射模设计中的应用

1 7
在 注 射 模 设 计 中 的 应 用
尚振 国 ,王 华 。 (. 1 大连水产学院 机械工程学院,辽宁 大连 162 ; 103 2 东北财经大学 实验教学中心,辽宁 大连 l62) . 105
摘要 : 介绍 了Sh 0 软件 中注射模设计插件 ⅣD [的主要功能。以喷墨打印机输纸滚轴为例, L) 阐述 了利用 D D进行注射模设计的几个 关键 步骤, 出了利用 Slv L 提 。d 分割线命令在 Ⅳ j 中手动创 i [ ) 建复杂零件分型线和分型面的方法,并介绍 了创建延伸曲面以及修补延伸曲面的过程及制作型芯和型 腔的步骤. 举例说 明了标 准模架参数化设计方法。 关键词 : 注射模; j ; [ 分型面; ) 型芯; 型腔 中图分类号 :C 11 l 文献标识码 : 文章编号 : 0 —26 (08 1 —0 1 —0 1 ;P 1 3 B l 1 182o)2 o7 4 0
A S at 1 【 man fl d n f .】 ,a pu 面 p c a e frijc o Ⅱ0 l e 运 . s l Wo k bt c :re i u c o s o 0 r h 1 lg a k g o ne n 1ud d sm m oi rs d
sf _e w r b f rsne . o e ky s p I d s o net n m u s fra pprfe 0ta ee l peet S m e t s i e蜘 fi ci o l o ae ed wr y d e 1 j o d
Ap l ai fI pi t n 0 MOL n ds n o Iet n mo ls c 0 D i ei fijci ud g l o
注射模浇注系统

分型面的形式
分型面可以是一个, 分型面可以是一个,也可以是多个 常见的形式有:平直分型面、倾斜分型面、阶梯分型面、 常见的形式有:平直分型面、倾斜分型面、阶梯分型面、 曲面分型面、 曲面分型面、垂直分型面
分型面的常见形式
水平分型面
斜分型面
阶梯分型面
曲面分型面
垂直分型面
组合分型面
分型面的设计原则
1 2
4qv ɺ γ w1 = 3 πR
6qv ɺ γ w2 = 2 Wh
根据切应力的定义,对于圆形和矩形通道, 根据切应力的定义,对于圆形和矩形通道,分别有
τw =
1
1 2
R∆p 2L
τw =
2
h∆p 2L
τ w 、τ w – 圆形和矩形管壁处的切应力(104Pa) 圆形和矩形管壁处的切应力( ) L – 管的长度(cm) 管的长度( ) ∆p – 熔体流经管长为L的通道时产生的压力降(104Pa) 熔体流经管长为 的通道时产生的压力降( ) 的通道时产生的压力降
由上面两式可知, 由上面两式可知,熔体的体积流量 qv 不仅与流 道长度L、 有关, 道长度 、流道截面尺寸 R 4 或者 Wh3 有关,还与黏 有关。这些参量彼此关联, 度 η 0 和压力降 ∆p 有关。这些参量彼此关联,当改 变其中一个参量时,其它参量也随之变化
流变参量的变化与选择
浇口截面尺寸
型腔数目的确定
按经济性确定型腔数目, 按经济性确定型腔数目,根据总加工费用最小的原则
模具费用
Xm = nC1 + C2
Xj = N Yt 60n
成形加工费用
型腔数目计算公式
NYt n= 60C1
N —— 需要生产塑件的总数 Y —— 每小时注射成形加工费,元/h 每小时注射成形加工费, t —— 成形周期,min 成形周期, C1 —— 每一型腔的模具费用,元 每一型腔的模具费用, C2 —— 与型腔数无关的费用,元 与型腔数无关的费用,
注射模强行推出机构设计

3 常 见强 行 推 出的 模 具 结 构
1 )弹簧 、推杆 二次 强行推 出
如 图 2 示 为 盒 盖 塑 料 制 品 ,结 构 较 简 单 ,但 有 一 处 存 所 在 倒 扣 ,需 采 用 强 行 脱 模 。 强 行 推 出 的 模 具 结 构 工作 过 程 : 动 、定 模 打 开 后 ,在 弹 簧 5 用 下 推 动 顶 杆 6 而 推 动 型 芯 推 作 进
I
I
【凹 = qI a , 苹 --o ) 】 玎  ̄  ̄o %
2强行推 出应具备的条件
强行推 出应具备如下 条件 :
1 塑料制 品材 料 应为 软质 塑 料 ,如P ) E、 P P、 AB S、
P M 、软 质 P O VC等 。
f凹 分 = ×0 b l 率 1 ), 0 %
core s r ct r tu u e.
Ke r : lsi r d cs ltrl o v x c n a esr cu e ijcin mo d no c d ee t n ywo d P at p o u t;aea n e — o c v tu t r ;.e to l,e f re jci c c o
p r ii i he na ur o he l s i f m a i ha a t c pr duc s ha e ns e d of c a t utlz ng t t e f t e a tc de or ton t t pl s i o t v ,i t a om plc t d a x nsve l t r l r w i i a e nd e pe i a e a d a ng—
1 ~2 % , 同 时 ,有 侧 向 抽 芯 机 构 的 模 具 , 在 生 产 过 程 中 发 5 0
推杆直顶内抽芯结构注射模设计

无法实现斜 顶 内抽的情况下所 使用的一种结构 : 直顶 内抽 。 护壳 塑件如 图 1 所示 , 该塑
件 为 我 司 开 发 的 一 种 汽 车 连 接
器两线护壳 , 为 出 口塑件 , 对质
量 要 求 比较 严 格 。此 塑 件 外 形
简单 , 尺寸较小 , 内部有两个与 对插端 配合 的凸 台。由于是配 合 凸台 , 尺寸要 求 比较严格 , 并 《 模具制造) } 2 0 1 4 年第 l 2 期
wi t h i n t h e u s e o f a c o r e p u l l i n g s t r u c t u r e : t r a i g h t t o t h e t o p a n d i n w a r d c o r e — - p u l l i n g ; w i t h t h i s
a c h i e v e t h e c o mp l e t i o n o f t h e mi c r o p a ts r i n wa r d c o r e - p u l l i n g mo t i o n s a n d s mo o t h o u t o f t h e p l a s t i c , r e a l i z e d t h e a u t o ma t i o n i n p r o d u c t i o n
Ke y w o r d s : i n t e r i o r c o r e p u l l i n g ; t h e t o p ; l a t e r a l mo v e me n t ; s e c o n d a y r e j e c t i o n
1 引言
De s i g n o f I n j e c t i o n Mo l d wi t h P u s h Ro d
崔杰套锻法在生产中的应用

台阶 。在 锻造 生 产 中 , 同种 金 属 材 料 的 锻 件 就有 很 多 , 先 , 同种金 属 材料 工件 及 形状 、 首 对 尺寸 、 以及技
术 要 求加 以分 析 , 综合 起来 科 学 的制定 锻造 工艺 , 以
便 实 现省 工 、 省料 的 目的 。例 如 : 间在承 担一 批法 车 兰盘 和 圆环 锻 件 的生 产 任 务 , 料 质 量 分 别 为 6 1 下 .
2 Teh oo yd p rme t Heln ja g H u a c iey C Lt Qiia r1 1 4 Chn ) . c n lg e at n , i gin a n ma hn r o, d, qh e 6 0 6, ia o
Ab t a t Thi a tce i to u e ic fs me p o u ti cu i g p o e s r f r n t e p a tc l r c s fb a k e sr c : s ril n r d c s a p e e o o r d c n l d n r c s e o mi g,h r c ia o e s o ln sr — p p o e sn n h o g h o c e e e a ls ea o a e h mp ra t me n n ft c n l g n o a i n t e u e e e g r c s i g a d t r u h t e c n r t x mp e , lb r t s t e i o t n a i g o e h o o y i n v t o r d c n r y o
一种无痕推出饰罩注射模设计

270mm,滑块处最长达到 505mm。经对注射压力、塑件
抽芯方式和模具体积情况,最终决定在 120t 注塑机上开
发 1 模 4 腔,如图 2 所示。
脱模结构设计
该模具采用二次分型方式:为保障二次分型顺利进
板与动模套板制件装有限位器,限位距离为 10mm。饰
罩塑件注射完成后动模进行第一次开模,动模镶块随动
比较好的耐高温性和防静电性能,其收缩率为 0.6%。
1.4
图1
塑料饰罩尺寸
《模具制造》2024 年第 1 期
·塑料注射模技术·
塑件尺寸公差与精度要求:该尺寸外形尺寸为长
62mm,宽 为 17.4mm 高 13.6mm,公 差 为 GB/T144862008 MT2 级。影响塑件公差的主要因素是模具制造误
此长的流程,在塑件成型时能够充填全是模具设计考虑
的重点之一。根据塑件的结构和表面要求,本设计采用
侧面潜伏式浇口,潜伏浇口与 Y 轴角度为 60°,浇口直径
为 ϕ1.2mm,塑件脱出时自动切断浇口,有利于实现自动
化生产,如图 5 所示。
用下开始分型向后运动。动模镶块固定在动模支撑板
上随之向后运动,与抽芯和定模镶块分离。此时饰盖塑
traceless ejection structure of the injection mold for decorative cover plastic parts. The mold adopts a
unique combination of secondary mold opening and secondary ejection structure, completely solving
后运动,直到把塑件全部从抽芯中脱离,饰罩塑件在重
注射模高光技术设计原理

注射模高光技术设计原理
宋德敏
【期刊名称】《模具制造》
【年(卷),期】2011(011)006
【摘要】结合录像机高光前面板的设计,简单介绍注射模高光技术设计原理,主要目的是对传统模具设计进行创新.
【总页数】2页(P45-46)
【作者】宋德敏
【作者单位】中国华录.松下电子信息有限公司,辽宁大连116000
【正文语种】中文
【中图分类】TQ320.66
【相关文献】
1.高光蒸汽注射模具设计的研究与应用 [J], 贾春燕;袁国强;黄汉福
2.基于制造工艺的注射模全镶拼结构设计原理 [J], 刘勇
3.镜面上盖高光注射模设计 [J], 吕永刚;张同斌
4.汽车高光格栅注射模设计 [J], 石波;郝加杰
5.打印机盖板针阀热嘴高光注射模设计 [J], 刘勇
因版权原因,仅展示原文概要,查看原文内容请购买。
底座注射模设计_职业学院机械工程毕业论
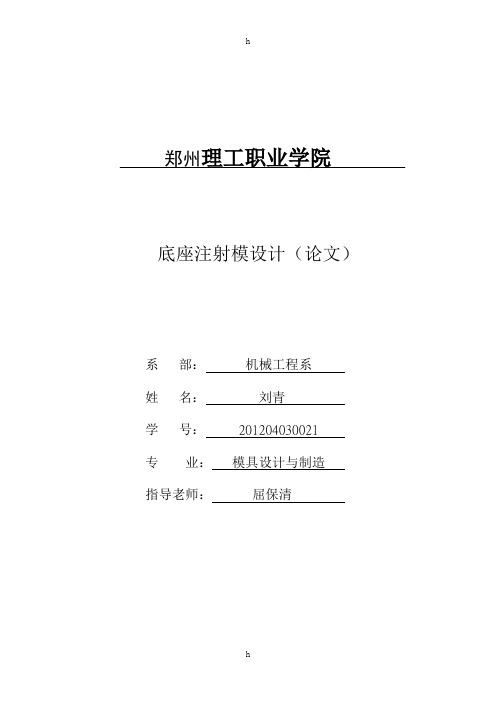
郑州理工职业学院底座注射模设计(论文)系部:机械工程系姓名:刘青学号: 201204030021 专业:模具设计与制造指导老师:屈保清摘要对塑料底座注射模结构采用中心浇口进料,采用一模一腔的模具结构,材料采用流动性能差的PC塑料,通过对塑件的分析,注射机的选定,浇注系统的设计,成型零件的设计计算,脱模推出机构的设计,以及冷却系统的设计和导向地位机构的设计,给出了生产底座的一个实际参考设计生产流程。
通过本设计,可以对注塑模具有一个初步的认识,注意到设计中的某些细节问题,了解模具结构及其工作原理;为以后从事本行业打下了良好的理论基础。
此次设计的过程中查阅了大量的模具设计资料,通过模具的设计与应用,同原有的设计方法相比,模具的应用提升了产品的质量,模具整体设计的思路和要求符合现代设计潮流和未来的发展方向。
关键词: PC;一模一腔;中心浇口;模具设计ABSTRACTbase injection mould structure adopts center gate; Selected a mould for four cavity die structure, and selected the medium flow not well PC plastic for filling mold, improve the design compact and practical efficiency; PC Based on the analysis of the plastic parts, injection machine selection of the design of the shunt way, Lord, molding parts design calculation of mechanism design, stripping out, and the cooling system design and guide mechanism design, status are given a production of plastics base actual reference design of the production process. The mould designprocess .Through the design and application of the mold ,the processing technology ,compared with previous technology ,which increase the quality of the product. The overall design mentalityand request conform to the modern design tidal and development direction of the future.Keywords: pc; plastics base; center gate; mold design.目录一、塑件成型工艺性分析 (5)1.塑件的分析 (5)2.注射成型过程 (6)二、拟定模具的结构形式和初选注射机 (7)1.分型面位置的确定 (7)2.注射量的计算 (7)3.选择注射机 (8)三、浇注系统的设计 (9)1.浇注系统的设计原则 (9)2.分流道的设计 (10)3.冷料穴的设计 (10)四、成型零件的结构设计及计算 (11)1.成型零件的结构设计 (11)2.成型零件钢材的选用 (12)3.凹模深度尺寸的计算 (12)五、脱模推出机构的设计 (13)1.脱模力的计算 (13)2.推出方式的确定 (13)六、排气槽的设计 (15)七、导向与定位机构的设计 (16)1.导柱导向机构 (16)八、零件的加工工艺过程 (17)1.小型芯制造工艺过程: (17)2.型腔制造工艺过程 (17)九、设计小结 (20)参考文献 (21)致谢 (22)一、 塑件成型工艺性分析1.塑件的分析(1)外形尺寸 该塑件壁厚较厚,平均壁厚约为30mm ,结构较简单,对称度好,只需做几个型芯即可,塑件为热塑性塑料,流动性差,适于螺杆式注射机注射成型。
局部薄壁制品注射成型装置设计

局部薄壁制品注射成型装置设计
刘斌;吴晟霖;崔志杰;黄强
【期刊名称】《模具工业》
【年(卷),期】2018(44)10
【摘要】提出了一种适用于注射模成型制品局部薄壁的成型装置,由液压缸机构、型芯定位机构、限位机构和型芯组成,该装置解决了带有局部薄壁特征的制品成型时填充不满或成型质量较差的问题,通过设置可移动的型芯,实现了塑料熔体填充完成后再调整局部壁厚,避免填充不满现象的发生,提高了制品的成型质量。
【总页数】3页(P52-54)
【关键词】注射模;薄壁制品;液压缸机构;模具设计;注射成型
【作者】刘斌;吴晟霖;崔志杰;黄强
【作者单位】华南理工大学聚合物新型成型装备国家工程研究中心;欧唐科技(深圳)有限公司
【正文语种】中文
【中图分类】TG76;TQ320.66
【相关文献】
1.注射成型橡胶制品的自动脱模装置 [J],
2.注射成型薄壁制品收缩与翘曲因素 [J], 董斌斌;申长雨;李倩
3.注射成型薄壁制品的结晶度 [J], 郑国强;王松杰;张响;申长雨
4.薄壁制品微结构充填注射压缩成型中关键因素分析 [J], 王鑫;杜林芳;李寒琪
5.基于实验设计法的圆筒形薄壁件注射成型收缩预测 [J], 袁甘林;辛勇
因版权原因,仅展示原文概要,查看原文内容请购买。
10ml一次性注射器外套注射模具及成型工艺设计成型【文献综述】
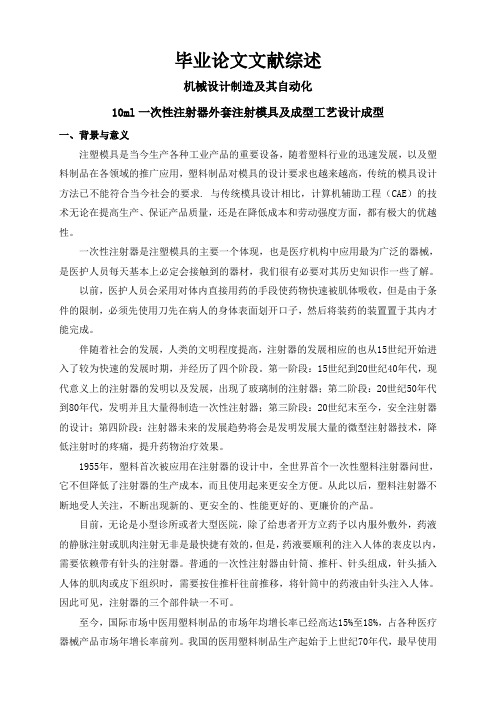
毕业论文文献综述机械设计制造及其自动化10ml一次性注射器外套注射模具及成型工艺设计成型一、背景与意义注塑模具是当今生产各种工业产品的重要设备,随着塑料行业的迅速发展,以及塑料制品在各领域的推广应用,塑料制品对模具的设计要求也越来越高,传统的模具设计方法已不能符合当今社会的要求. 与传统模具设计相比,计算机辅助工程(CAE)的技术无论在提高生产、保证产品质量,还是在降低成本和劳动强度方面,都有极大的优越性。
一次性注射器是注塑模具的主要一个体现,也是医疗机构中应用最为广泛的器械,是医护人员每天基本上必定会接触到的器材,我们很有必要对其历史知识作一些了解。
以前,医护人员会采用对体内直接用药的手段使药物快速被肌体吸收,但是由于条件的限制,必须先使用刀先在病人的身体表面划开口子,然后将装药的装置置于其内才能完成。
伴随着社会的发展,人类的文明程度提高,注射器的发展相应的也从15世纪开始进入了较为快速的发展时期,并经历了四个阶段。
第一阶段:15世纪到20世纪40年代,现代意义上的注射器的发明以及发展,出现了玻璃制的注射器;第二阶段:20世纪50年代到80年代,发明并且大量得制造一次性注射器;第三阶段:20世纪末至今,安全注射器的设计;第四阶段:注射器未来的发展趋势将会是发明发展大量的微型注射器技术,降低注射时的疼痛,提升药物治疗效果。
1955年,塑料首次被应用在注射器的设计中,全世界首个一次性塑料注射器问世,它不但降低了注射器的生产成本,而且使用起来更安全方便。
从此以后,塑料注射器不断地受人关注,不断出现新的、更安全的、性能更好的、更廉价的产品。
目前,无论是小型诊所或者大型医院,除了给患者开方立药予以内服外敷外,药液的静脉注射或肌肉注射无非是最快捷有效的,但是,药液要顺利的注入人体的表皮以内,需要依赖带有针头的注射器。
普通的一次性注射器由针筒、推杆、针头组成,针头插入人体的肌肉或皮下组织时,需要按住推杆往前推移,将针筒中的药液由针头注入人体。
- 1、下载文档前请自行甄别文档内容的完整性,平台不提供额外的编辑、内容补充、找答案等附加服务。
- 2、"仅部分预览"的文档,不可在线预览部分如存在完整性等问题,可反馈申请退款(可完整预览的文档不适用该条件!)。
- 3、如文档侵犯您的权益,请联系客服反馈,我们会尽快为您处理(人工客服工作时间:9:00-18:30)。
绪论本说明书是精密注射模设计的设计思路及详细分析。
本说明书主要阐述了此模具的设计思路与过程。
包括塑料件的工艺分析,塑件的成型方案分析,精密注塑模技术的介绍,注塑模总体结构的设计,注射机的选择校核,模具零件的设计与计算以及成型零件的制订等内容。
随着电子、电信、医疗、汽车等行业的迅速发展,对塑料制品的高精度、高性能要求与日俱增,精密注射成型要求制品不仅具有较高的尺寸精度、较低的翘曲变形,而且还应有优异的光学性能等。
注射成型是最重要的塑料成型方法之一,如何提高注射成型技术水平,生产出高精度的塑料制品,创造附加值高的产品,模具的设计是重要环节。
在精密注射成型设计中,除了应考虑一般模具设计事项外,还要特别考虑如下事项:1)为了得到所要尺寸公差的制品,要考虑适当的模具尺寸公差。
2)要考虑防止产生成型收缩率波动。
3)要考虑防止产生成型变形。
4)要考虑防止产生脱模变形。
5)要使模具制作误差最小。
6)要考虑防止模具精度波动。
7)要考虑维持模具精度。
这是近几年来发展得很快的一项新技术而国内,关于这项技术的报导开始增多,相信不久的未来将会得到普及。
此说明书,比较系统详细地介绍本次设计的各个步骤及精密注塑模具设计中的应用,并附上了大量结构零部件的设计简图。
毕业设计可以说是大学中最大的一次设计,时间跨度大,涉及内容多,是对个人模具设计与制造知识的全面检验。
本次毕业设计较以往的课程设计相比,要求个人对PRO/E 的运用更加熟练,所以具有一定的难度。
大体上整个毕业设计的流程上安排如下:制品外观造型设计→查阅有关技术文献→确定模具设计方案PRO/E建制品实体→PRO/E建模→装配模具→由三维转为二维CAD图→撰写说明书。
由于本人的实践经验及理论水平有限,设计中不足和遗漏这处在所难免,敬请老师多多指教。
值此这际,本人向对本次设计提出宝贵意见和帮助的老师及同学表示由衷的感谢!第一章注塑产品设计1.1 通论产品设计是利用材料,经设计成为新创的外形或结构,以制成指定作用或目的的产品。
其所须具备之条件为:1)在功能上:要能符合使用者的需求。
2)在使用操作上:要能符合使用者的习惯与身份。
3)在外型上:要能合乎简单的制造原则并满足使用者的喜好。
4)材料应用与加工方法上:要合乎经济与合理的原则,并能求得最适化而降低成本。
即任何一新产品,从构思到生产,对一公司而言,其考量前题为以下所列各项:将来性:公司未来发展领域的配合,成长性。
技术性:与该公司现有技术之关系,原料设备获得之难易及技术上成功的可能性。
领先性:是否可申请或抵触专利及制品是否具独特性。
销售可能性:产品的展望,推出市场之难易,销售网的建立及有无商品特征等可能性。
经济性:研究经费人员的多寡,开发期间的长短,设备投资额之获得及获利率的大小。
其它如材料之选择、加工方式、模具的设计、二次加工方式及安全规范、法令等,皆须详加考虑。
通常塑料新制品产生的方式可分为三种:1)再设计(redesign):就是将现有产品的部分,做一些改变或修饰,使成为更具价值与流行的新产品。
现今市场上约莫80%,属于此类。
2)组合(combination):结合两种以上不同功能,发展而成之新制品。
例如PC制成的潜水镜再贴上防雾膜,而成为价值更高的新产品。
此类新产品约占10%。
3)创新(innovation):剩下的10%即为发明前所未有之新制品,此类产品由于须花费较长的时间在宣传及消费者的接受性上,所以通常这方面之设计比例较低。
塑料产品设计者与其它设计者最大的不同是,前者必须详加考虑塑料之各种物性,尤其是环境变化对物性之影响及在长时间负载下对产品之影响。
通常,塑料之物性数据是在实验室的环境下,依照美国标准测试方法(ASTM)而测得。
而所设计的塑料产品并不会正如测试样品在同样条件下成形或被加应力。
其它如:肉厚及形状、所加负载之速率及时间长短、玻纤之排列方向、缝合线、表面缺陷、成形参数。
以上这些;都会影响到塑料产品之强度及韧性。
设计时还须考虑到温度,湿度,阳光(紫外线),化学药剂等之影响。
所以了解其产品的最终目的而探讨相关的物性是非常重要的。
1.2注塑产品设计要点注塑产品设计的要点主要包括开模方向和分型线、脱模斜度、零件壁厚、加强筋、圆角和孔、抽芯机构及避免、塑件的变形、一体铰链、嵌件、气辅注塑、综合考虑工艺性和零件性能,等等。
1)开模方向和分型线每个注塑产品在开始设计时首先要确定其开模方向和分型线,以保证尽可能减少抽芯滑块机构和消除分型线对外观的影响。
a.开模方向确定后,产品的加强筋、卡扣、凸起等结构尽可能设计成与开模方向一致,以避免抽芯减少拼缝线,延长模具寿命。
b. 开模方向确定后,可选择适当的分型线,避免开模方向存在倒扣,以改善外观及性能。
2)脱模斜度a.适当的脱模斜度可避免产品拉毛(拉花)。
光滑表面的脱模斜度应≥0.5度,细皮纹(砂面)表面大于1度,粗皮纹表面大于1.5度。
b.适当的脱模斜度可避免产品顶伤,如顶白、顶变形、顶破。
c. 深腔结构产品设计时外表面斜度尽量要求大于内表面斜度,以保证注塑时模具型芯不偏位,得到均匀的产品壁厚,并保证产品开口部位的材料强度。
3)产品壁厚a.各种塑料均有一定的壁厚范围,一般0.5~4mm,当壁厚超过4mm时,将引起冷却时间过长,产生缩印等问题,应考虑改变产品结构。
b.壁厚不均会引起表面缩水。
c.壁厚不均会引起气孔和熔接痕。
4)加强筋a.加强筋的合理应用,可增加产品刚性,减少变形。
b. 加强筋的厚度必须≤(0.5~0.7)T产品壁厚,否则引起表面缩水。
c.加强筋的单面斜度应大于1.5°,以避免顶伤。
5)圆角a.圆角太小可能引起产品应力集中,导致产品开裂。
b.圆角太小可能引起模具型腔应力集中,导致型腔开裂。
c.设置合理的圆角,还可以改善模具的加工工艺,如型腔可直接用R刀铣加工,而避免低效率的电加工。
d.不同的圆角可能会引起分型线的移动,应结合实际情况选择不同的圆角或清角。
6)孔a.孔的形状应尽量简单,一般取圆形。
b.孔的轴向和开模方向一致,可以避免抽芯。
c.当孔的长径比大于2时,应设置脱模斜度。
此时孔的直径应按小径尺寸(最大实体尺寸)计算。
d.盲孔的长径比一般不超过4。
防孔针冲弯e.孔与产品边缘的距离一般大于孔径尺寸。
7)注塑模的抽芯、滑块机构及避免a.当塑件按开模方向不能顺利脱模时,应设计抽芯滑块机构。
抽芯机构滑块能成型复杂产品结构,但易引起产品拼缝线、缩水等缺陷,并增加模具成本缩短模具寿命。
b.设计注塑产品时,如无特殊要求,尽量避免抽芯结构。
如孔轴向和筋的方向改为开模方向,利用型腔型芯碰穿等方法。
8)一体铰链a.利用PP料的韧性,可将铰链设计成和产品一体。
b.作为铰链的薄膜尺寸应小于0.5mm,且保持均匀,c.注塑一体铰链时,浇口只能设计在铰链的某一侧。
9)嵌件a.在注塑产品中镶入嵌件可增加局部强度、硬度、尺寸精度和设置小螺纹孔(轴),满足各种特殊需求。
同时会增加产品成本。
b.嵌件一般为铜,也可以是其它金属或塑料件。
c.嵌件在嵌入塑料中的部分应设计止转和防拔出结构。
如:滚花、孔、折弯、压扁、轴肩等。
d.嵌件周围塑料应适当加厚,以防止塑件应力开裂。
e.设计嵌件时,应充分考虑其在模具中的定位方式(孔、销、磁性)10)标识产品标识一般设置在产品内表面较平坦处,并采用凸起形式,选择法向与开模方向尺可能一致的面处设置标识,可以避免拉伤。
11)注塑件精度由于注塑时收缩率的不均匀性和不确定性,注塑件精度明显低于金属件,不能简单地套用机械零件的尺寸公差应按标准选择适当的公差要求.我国也于1993年发布了GB/T14486-93 《工程塑料模塑塑料件尺寸公差》,设计者可根据所用的塑料原料和制件使用要求,根据标准中的规定确定制件的尺寸公差。
12)注塑件的变形提高注塑产品结构的刚性,减少变形。
尽量避免平板结构,合理设置翻边,凹凸结构。
设置合理的加强筋。
13)扣位a.将扣位装置设计成多个扣位同时共用,使整体的装置不会因为个别扣位的损坏而不能运作,从而增加其使用寿命,再是多考滤加圆角,增加强度。
b.是扣位相关尺寸的公差要求十分严谨,倒扣位置过多容易形成扣位损坏;相反,倒扣位置过少则装配位置难於控制或组合部份出现过松的现象。
解决办法是要预留改模容易加胶的方式来实现。
14)焊接(热板焊、超声波焊、振动焊)a.采用焊接,可提高联接强度。
b.采用焊接,可简化产品设计。
15)合理考虑工艺和产品性能之间的矛盾a.设计注塑产品时必须综合考虑产品外观、性能和工艺之间的矛盾。
有时牺牲部分工艺性,可得到很好的外观或性能。
b.结构设计实在无法避免注塑缺陷时,尽可能让缺陷发生在产品的隐蔽部位。
16)螺丝柱孔径与自攻螺丝直径的关系自攻螺丝螺丝柱孔径M2 1.7M2.3 2.0M2.6 2.2M3 2.517)支柱的设计原则:a.支柱尽量不要单独使用,应尽量连接至外壁或与加强筋一同使用,目的是加强支柱的强度及使胶料流动更顺畅。
b.支柱高度一般是不会超过支柱直径的两倍半。
因过高的支柱会导致塑胶部件成型时困气(長度太長時會引起氣孔﹐燒焦﹐充填不足等)。
c.支柱高度若超过支柱直径的两倍半,加强支柱的强度的方法”尤其是远离外壁的支柱,除了可使用加强筋外,三角加强块”Gusset plate的使用亦十分常见。
BOSS的形狀以圓形為主﹐設計在底部時取3個 (其它形狀則加工不易﹐且流動性也不好)。
d. 支柱的位置不能太接近轉角或外側壁,应与产品外壁保持一段距离。
e.支柱周圍可用除去部分肉厚(即开火山口)來防收縮下陷。
f.支柱的拨模角度:通常外取0.5°,内取0.5°或1。
第二章 工艺分析2.1 塑件分析手机已经成为现代生活中必不可少的通讯工具,各种各样款式都有,而且中国是世界手机保有量最大的国家。
本次设计的产品是索尼爱立信的K510型号手机,如图2.1_A 、2.1_B ;本次设计的模具是该手机的后电池盖部分,如图2.1_C 、2.1_D [8]:A BC D图2.1 索尼K510手机3D 造型效果图经分析,此塑件内侧有尺寸比较小的扣位突出,设置模具时需要采取斜顶出的装置;2.1_C 图塑件的右下方有两个突出,经分析有两种方案:1)此处采用滑块的形式;2)此处同样采用斜顶出方式的结构装置。
经过判定,采取第二种方案可以简化模具结构,使模具的设计和加工简单化,同时可以节省生产成本,符合设计思想。
在进行模具设计之前,首先对制品图及形状结构分析,其内容主要包括以下几个方面:(1)手机的后电池盖(见制件图)。
制品的几何形状:本次设计的制品形状为索爱K510c款式,平均壁厚为1.2mm,属轻质薄壁制品。
(2)制品的尺寸精度和表面粗糙度:塑料的尺寸精度主要决定于塑料收缩率的波动和模具制造误差。